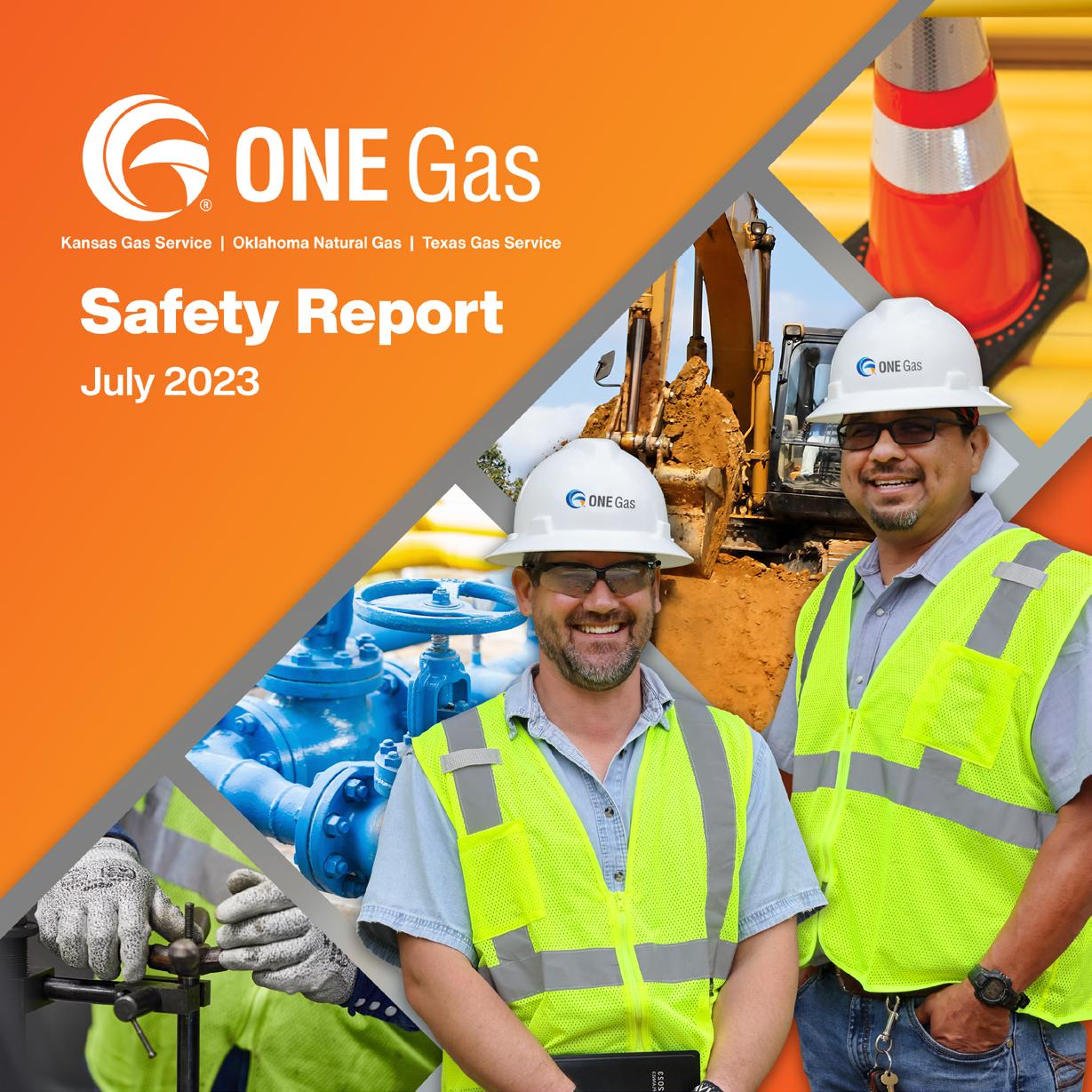
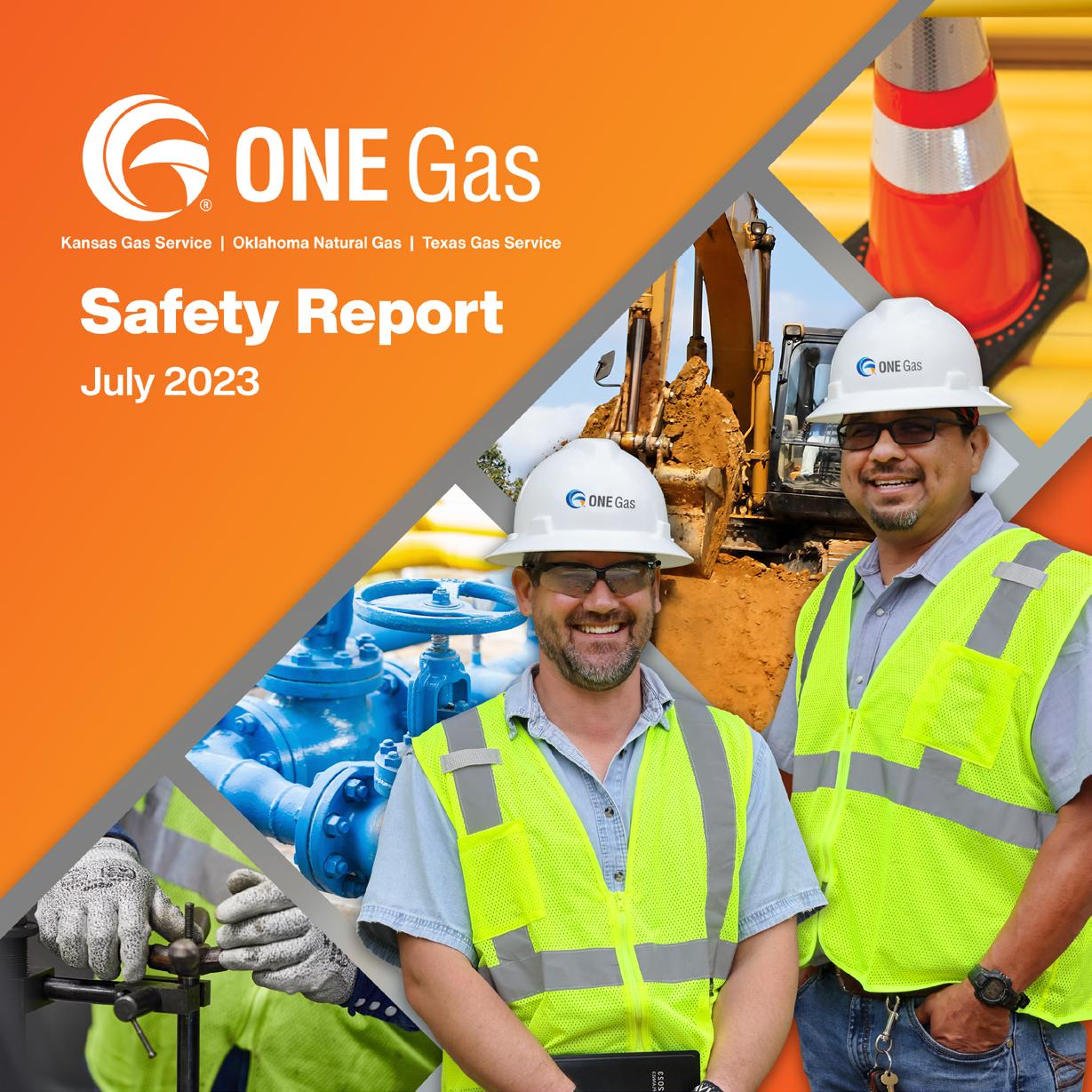
LEADERSHIP COMMITMENT
A Message from Sid
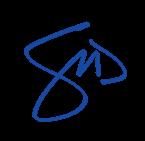
In the past year, our company has experienced exciting growth, in the number of customers we serve, co-workers we have onboarded and our safety culture. We expanded and enhanced initiatives that protect our people, customers, technology and facilities. I hope you enjoy reading about some of those advancements in this year’s report.
While innovation is exciting, we also recognize the value of focusing on the basics: working when safe and stopping when we’re unsure. Our Core Value of Safety drives our business strategy and decision-making. Safe driving, personal injury prevention and public safety remain essential aspects of our daily work.
For this year’s report, we again highlighted updates in the 10 elements of the ONE Gas Safety Management System (OSMS), our comprehensive and systematic approach to managing safety. Each area helps us further identify risks and opportunities for continuous improvement.
In addition to the many points of pride highlighted in this year’s report, we again received notice from the American Gas Association that ONE Gas had the lowest rate of significant injuries among our peers for the sixth year in a row. Our company would not be able to achieve our safety, reliability and growth goals without the dedication of each one of our more than 3,800 co-workers.
Thank you for your dedication to operating responsibly, caring for one another and living our Core Values as you serve our 2.3 million customers each day.
About OSMS
OSMS promotes a Plan-Do-Check-Act cycle. These four steps promote a continuous assessment and improvement culture.

• PLAN: Define the objectives/plan
• DO: Implement and control the plan
• CHECK: Monitor against the plan
• ACT: Improve performance of processes
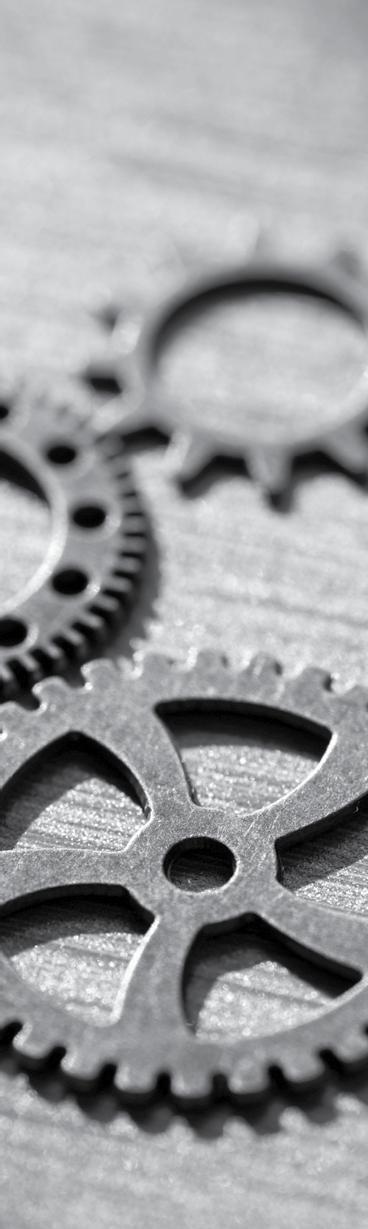
10 Elements of the ONE Gas Safety Management System
2022 Highlights
6th year
Recognized by American Gas Association for the lowest incident rate for DART (2017 to 2022) among mega-sized natural gas distribution companies.
Sid McAnnally President & Chief Executive Officer
More than
23,000 training hours
Logged for customer service, construction and maintenance training.
2nd Annual Safety Survey
Employees scored the safety-focused Gallup survey question 4.24 in 2023, compared to 4.18 in 2022.
1. Leadership Commitment
2. Risk Management
3. Operational Controls
4. Emergency Preparedness and Response
5. Incident Investigation, Evaluation and Lessons Learned
6. Safety Assurance
7. Documentation and Record Keeping
8. Management Review and Continuous Improvement
9. Competence, Awareness and Training
10. Stakeholder Engagement
Expanded the use of RADAR (Risk Assessment and Damage Reduction) to Kansas.
70 O-Net submissions with 65 successfully closed since implementation in 2020.
STAKEHOLDER ENGAGEMENT
Engaging our stakeholders is essential to identifying risks and opportunities for continuous improvement.
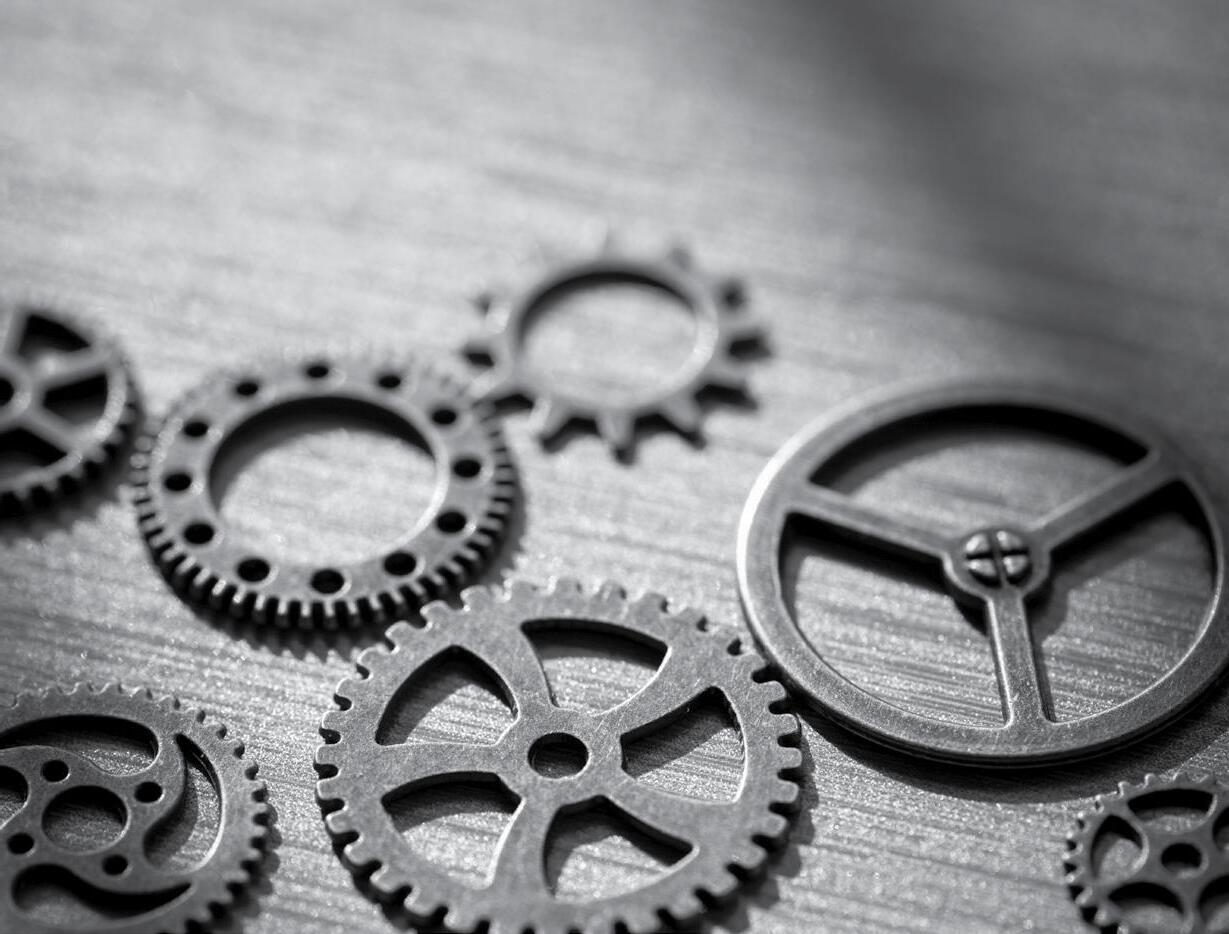
DART Historical Performance
AGA Safety Metrics Overview
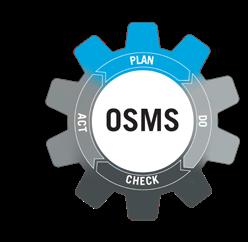
2022 Safety Metrics
Our safety metrics provide a snapshot of our ongoing efforts to keep each other, our customers and our communities safe. The safety of the public and our co-workers drive our vision. We strive to have employees leave work every day the same way they arrived — unharmed.
PVIR Historical Performance & Supporting Programs
Since 2014, we’ve enhanced our safety culture and improved our safety record in the following metrics:
44% 46%
reduction in our TRIR
Recognized for Safety Excellence
reduction in strains and sprains, the most prevalent type of injury
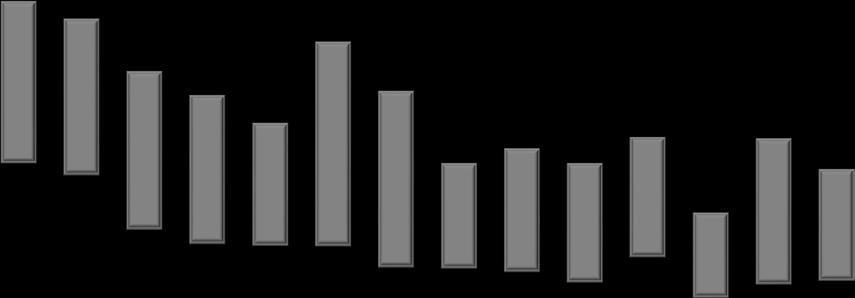
reduction in our DART 82%
In 2022, the American Gas Association (AGA) recognized ONE Gas for having the lowest incident rate for DART for the sixth consecutive year (2017 to 2022) among mega-sized natural gas distribution companies.
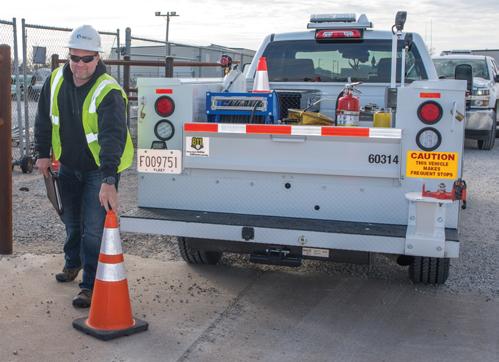
the percent
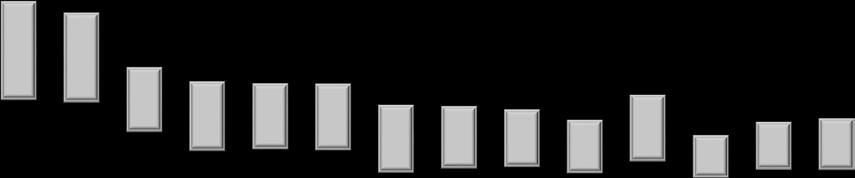

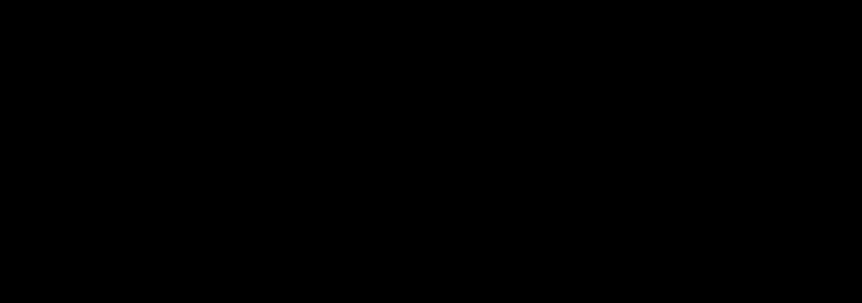
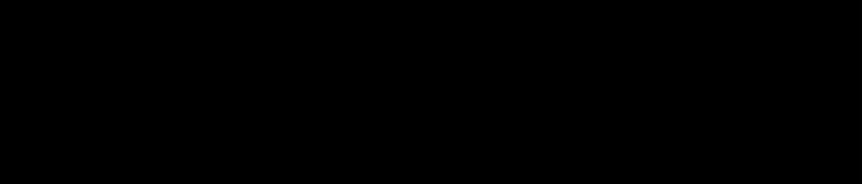

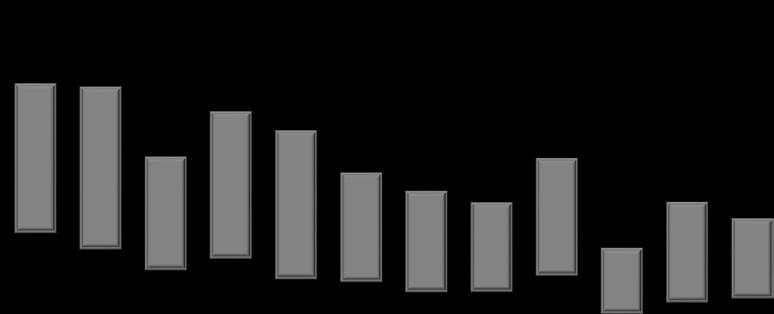
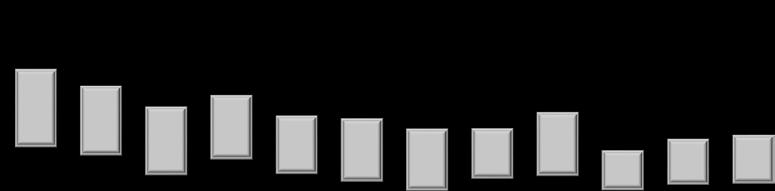

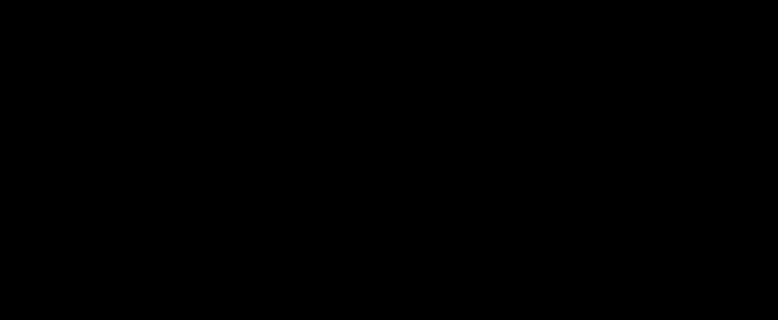

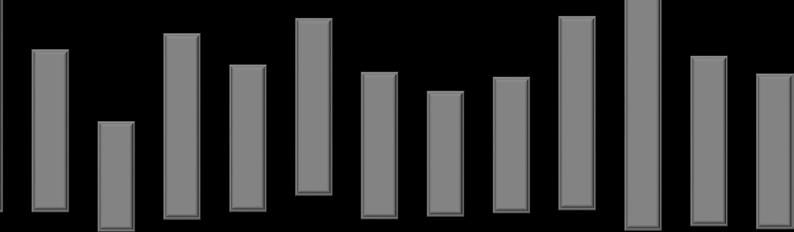
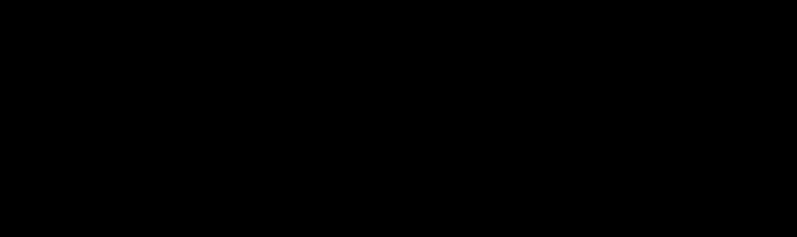
emergency orders where we safely respond on-site within 30 minutes after being notified of an emergency. The
does not maintain standardized Emergency Response Time data for peer comparison.
Leader in the Field
Our Leader in the Field program promotes positive, in-person conversations about safe work practices. Operations leaders observe work-related tasks being performed on-site and encourage open dialogue with their team members on how to improve safety outcomes.
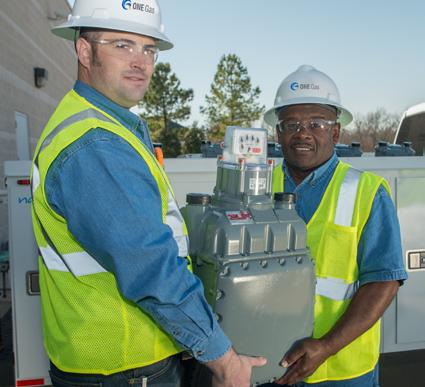

This program recognizes excellence in the field and identifies improvement opportunities that drive change. From March 2022, when the program began, to year-end, leaders logged more than 10,000 documented observations.
Safety Partners
Our Safety Partners program is an employee-driven committee that supports the growth of our safety culture. Volunteer committee members are non-managers and serve staggered terms of about three years. Members perform peer-to-peer job site safety observations, provide real-time feedback, give positive reinforcement and encourage safe behaviors.
The committee uses the information gained during observations to consider updates to our training, develop safety communications and select focus areas for safety meetings.
Learning Teams
Learning Teams were introduced to help us understand the complexity of the work we do and how work gets done in the field. These facilitated discussions engage the people that do the work, resulting in practical solutions. They help us identify potentially harmful situations and unexpected conditions that other tools may not detect to help us strengthen our safeguards and controls to keep people safe.
Gallup Employee Engagement Survey
Employee engagement is an important part of our culture. Research shows that organizations with highly engaged employees have fewer safety incidents, reduced turnover and increased productivity.
After receiving the survey results, managers create action plans with their teams. This begins with discussing areas of opportunity and identifying activities intended to enhance the team’s level of engagement.
What’s New :
• In 2022, companywide engagement scores increased for the sixth consecutive year.
• Engagement scores remained in the top quartile of both Gallup’s Utilities Benchmark and Overall Company Database.
• Our safety culture scores are on the rise. Employees scored the safety-focused Gallup survey question 4.24 in 2023, compared to 4.18 in 2022.
2023 Gallup Employee Engagement Results
What is RADAR?
RISK MANAGEMENT
Managing risk is essential to our Core Value of Safety and our dedication to providing reliable service.
Damage Prevention
Our Damage Prevention program focuses on enhancing public safety and environmental protection. We do this by preventing damage to our assets from excavation activities, such as digging, trenching, boring, backfilling or other ground-disturbing activities.
ONE Gas uses data to make improvements that lower the risk of damage during excavation.
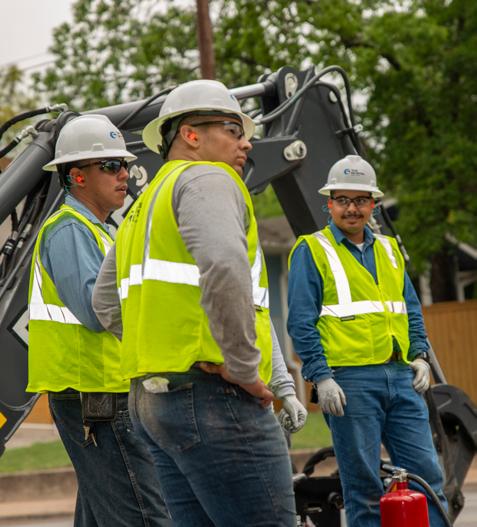
Advanced Leak Detection
ONE Gas uses a variety of advanced methods to monitor its system and detect leaks. Picarro is a mobile technology used to identify indications of methane in the air from various sources.
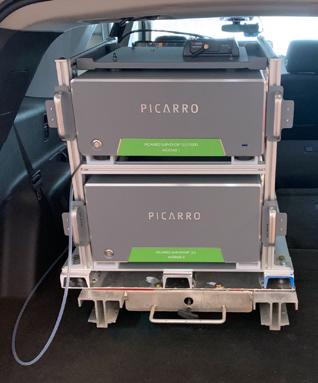
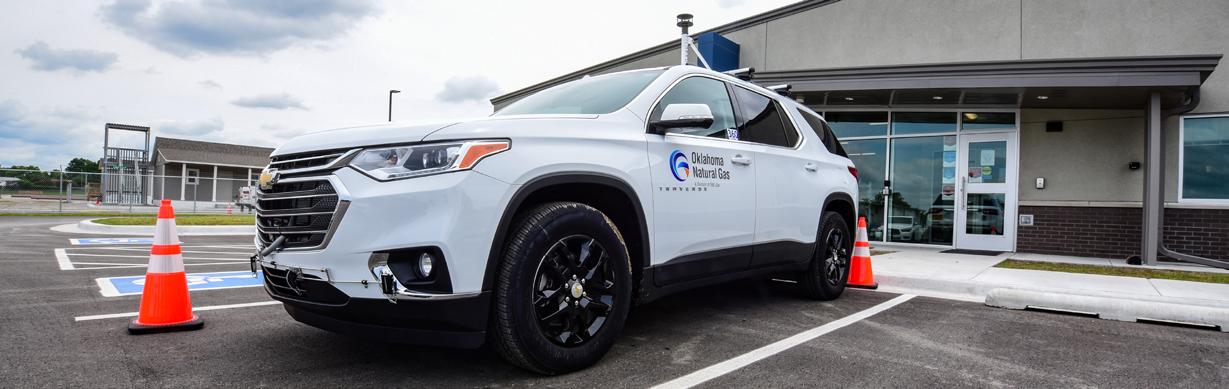
What’s New :
• Expanding the use of RADAR (Risk Assessment and Damage Reduction) beyond Oklahoma to Kansas (2022) and Texas (2023).
• Utilized the ONE Gas route work optimization platform to increase efficiency for line locating.

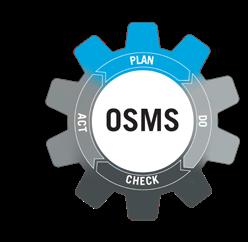
RADAR technology uses data from both public and internal sources to help us prioritize the probability of damage occurring due to excavation activities near our pipelines. As high-risk locations are identified, we can proactively connect with the excavator before work begins — and potential damage happens — to reinforce safe digging practices.
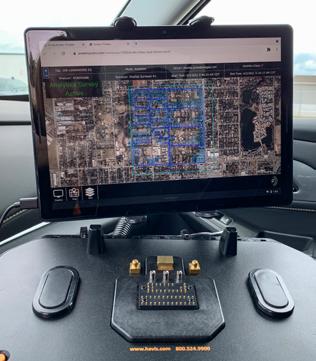
These indications are then investigated through traditional technologies such as Combustible Gas Indicators, Remote Methane Leak Detection and Flame Ionization Detectors.
Picarro is currently deployed in Austin, El Paso, Oklahoma City and Tulsa. We’re working with the Kansas Corporation Commission to implement the technology in Kansas soon.
Did You Know?
• In Oklahoma, Picarro currently surveys approximately 73% of the metro distribution footage and 45% of the total state compliance survey footage.
• In Texas, Picarro currently surveys approximately 88% of all compliance survey footage in the metro areas of Austin and El Paso and 51% of the total state compliance survey footage.
What’s New:
• Expanded the use of Picarro to the Rio Grande Valley summer 2023.
Infrastructure Modernization and Asset Management
Distribution Integrity Management Program (DIMP)
The DIMP team annually reviews our assets and leak information from our databases to identify and address threats to the distribution system. In 2022, the System Integrity team implemented a new risk model that better aligns Distribution Integrity Management and Asset Management through a single risk model that calculates the total risk for our assets while prioritizing and optimizing pipeline replacement projects. The model calculates how much risk is mitigated if a specific action is implemented, such as pipeline replacement as well as operational decisions. Risk results are shared across the company to help drive our programs that address threats.
Transmission Integrity Management Program (TIMP)
The TIMP includes integrity assessments of our transmission pipelines and resulting data-driven pipeline repairs and replacements to decrease risk.
How we reduce risk:
• Maintain traceable, verifiable and complete records for transmission pipelines
• Assess and inspect pipelines for conditions requiring repair
• Apply additional preventive and mitigative measures where appropriate
• Systematically reduce the operating pressures of our transmission pipelines in populated areas
ONE Gas has committed to infrastructure modernization and emissions reduction primarily through planned vintage pipeline replacement. The System Integrity team optimizes which vintage pipelines to replace for reliability and pipeline safety efforts. We use specialized software to predict pipeline risk and prioritize projects of the greatest value. We introduced a project management team, established vintage replacement objectives and key results, and established an emissions reduction short-term incentive safety metric to support these efforts.
Public Awareness
Our Public Awareness program provides helpful pipeline safety information to engage key stakeholders including, emergency responders, local public officials, excavators and customers. Our goal is to enhance public safety and protect the environment by increasing awareness of underground facilities in the communities where we operate.

Public Awareness Programs Include:
• 811 Call Before You Dig – Promote local damage prevention programs to increase awareness about safe digging
• Natural Gas Safety – Inform the public about how to detect a natural gas leak and what to do and not do if they suspect one
• Cross Bore Education – Provide cross bore awareness and safety measures to plumbing and excavating stakeholders (cross boring occurs when a natural gas line intersects another utility’s line)
• Social and Traditional Media – Leverage popular social media platforms and news media channels to raise awareness of safe digging
• Employee Engagement – Create safe digging employee advocates through educational materials, contests and trivia
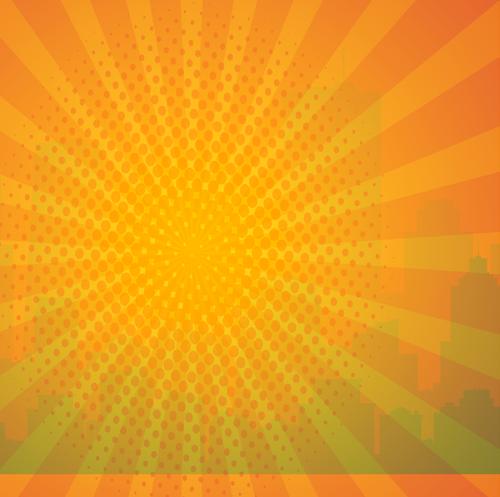
Raising Awareness
Our 2023 “Be a Dig Hero” campaign resulted in a 20% increase in Safe Digging Pledges over 2022.
Learn from Your Co-workers
OPERATIONAL CONTROLS
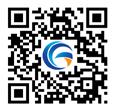
Operational controls set the framework for achieving safety throughout the organization.
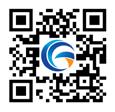
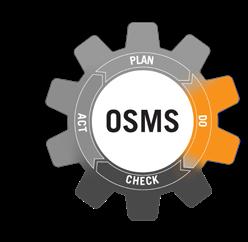
Operating and Safety Procedures
ONE Gas uses written procedures as controls to guide our operations. Our Operations and Maintenance Procedures and Safety Procedures define how we perform our daily tasks and remain compliant with pipeline safety regulations.
Work When Safe
We introduced Start When Safe in 2022 to encourage workers in all settings to think through what could happen before work begins and prepare for it rather than waiting to respond if something happens.
We’ve expanded this way of thinking to a broader Work When Safe concept to apply to any part of our jobs, whether in the field or the office. We urge our workers and contractors to have a safety plan before work begins and give them the authority to stop work if they perceive a hazard.
In alignment with the “Check” and “Act” stages of our continuous-improvement cycle, we monitor our regulatory requirements to develop, revise and improve our procedures.
What does it look like to Work When Safe? Check out these videos to learn how your co-workers incorporate safe practices into their daily work.

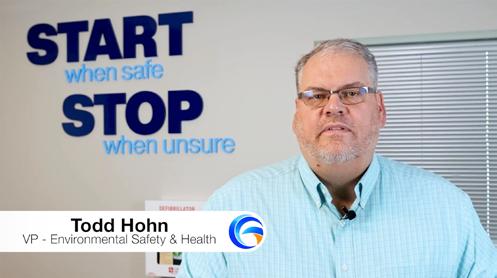
A Personal Story About Why It’s Important to ‘Start When Safe’ Scan
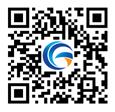
Employee’s Son Helps Him ‘Start When Safe’ Scan
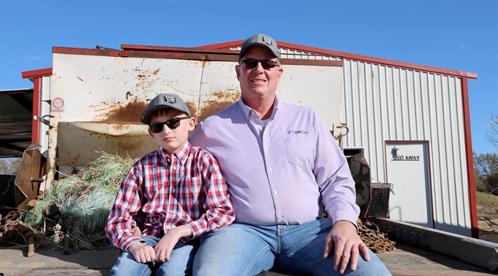
What’s New Safety Board Posters
The company is expanding the use of Work When Safe with safety board posters distributed companywide to enhance safety awareness. The safety boards capture important information, like locations of emergency exits, and assign roles for emergencies like a fire, severe weather or an active shooter.
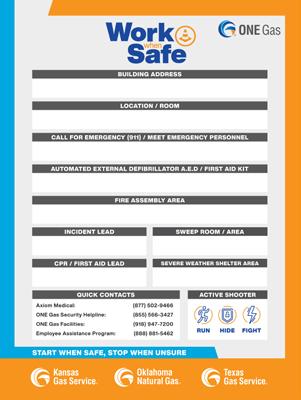
EMERGENCY PREPAREDNESS & RESPONSE
Training and preparation for emergencies help reduce the impact on people, property and the environment.
Pipeline Emergency Response Plan
Managed by the ONE Gas Emergency Preparedness and Response team, the Pipeline Emergency Response Plan, or PERP, is designed to promote emergency preparedness for pipeline operations to mitigate risk when an incident occurs. The plan requires emergency drills for each operating division and includes the participation of local emergency management personnel and public authorities.
Emergency Isolation
Valve Implementation
Rapidly isolating pipeline segments in the event of an emergency can expedite emergency response access to affected areas and mitigate consequences. To help with this effort, ONE Gas is installing remotely operable isolation valves along transmission pipelines routed through highly populated areas. Work began in 2022 to retrofit 14 transmission mainline block valves in Oklahoma and Texas with remote operation capability.
SAFETY ASSURANCE
Emergency Preparedness at ONE Gas includes:
• Annual crisis drills
• Crisis management plans
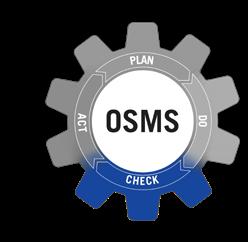
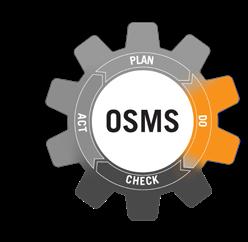
• Emergency fleet, equipment and tools
• Relationships with state and local emergency contacts
• Mutual aid relationships
• Coming soon — Mobile emergency command center
Emergency Monitoring System
Emergency Monitoring System (EMS) is a tool developed by ONE Gas that uses seismic activity recorded from the United States Geological Survey to outline the potentially affected areas in ONE Map, the online mapping application that employees use to view our pipeline systems. When the epicenter of an earthquake occurs near our pipelines, the data provided by EMS allows company decision-makers to prioritize work in areas with potential for damage.
Construction Project Inspection
ONE Gas and third-party inspectors monitor pipeline installation and replacement to verify the appropriate procedures, specifications and pipeline standards are met. Like anyone on our job sites, inspectors can stop work if they notice any unsafe situation.
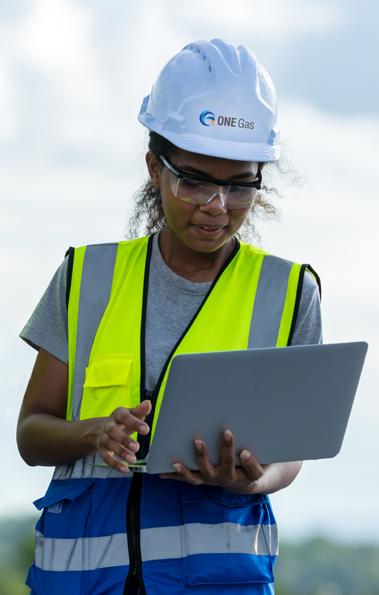
What’s New:
• LocusView, an automated job site tool designed to enhance our ability to track installed materials, is implemented in all three states for transmission and is rolling out to distribution main inspectors. LocusView will replace MobLite for construction field data capture, specifically for distribution mains projects. The distribution rollout has started in Kansas and will expand across Oklahoma and Texas later this year.
• Usage will expand further to include service lines later this year.
2022 Maturity Assessment
Our biennial maturity assessment compares our company safety practices against API RP-1173, an industry best practice document developed by the American Petroleum Institute for pipeline operators. It is intended to provide a framework to enhance our efforts for continual improvement of pipeline safety performance by making programs and processes more effective, comprehensive and integrated. On a scale of 10, our maturity rating increased from 7.1 in 2020 to 7.7 in 2022.
Assuring the safety of our co-workers and assets is instrumental in effectively managing risk and improving performance.
INCIDENT INVESTIGATION, EVALUATION & LESSONS LEARNED
Learning from experience helps us understand and build better processes to reduce the chance of incident recurrence.
Event Reviews
Conducting event reviews is a valuable part of continuous improvement. Our event review process looks at “what failed” versus “who failed.” We use our learning to implement systemic changes to how work is performed with the goal of safe, sustainable and repeatable performance. In addition to reviewing our incidents, we learn from our peers through discussions about their safety practices to determine if they can be utilized at our company to support better outcomes. We also follow investigations conducted by the National Transportation Safety Board and apply learnings to our own safety processes and procedures.
Materials Testing Lab and Failure Investigation
Located in Topeka, Kansas, the ONE Gas Materials Testing lab assists in evaluating and approving new materials and investigating failures or problems with existing pipeline materials, tools and equipment. These efforts improve the safety, system integrity, reliability, compliance and efficiency of the materials used. The Lab also performs tests to assist Field Operations in leak investigations.
DOCUMENTATION & RECORD KEEPING
Collecting and integrating data on our pipeline systems increases our system integrity. Knowledge of our pipeline construction, maintenance and operational experience drives decision-making, improves safety and aids in compliance.
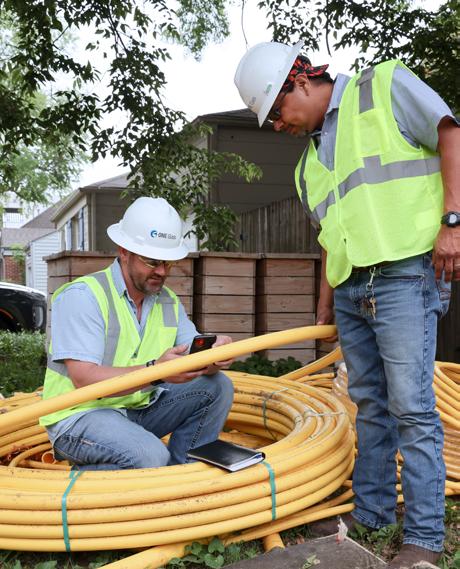
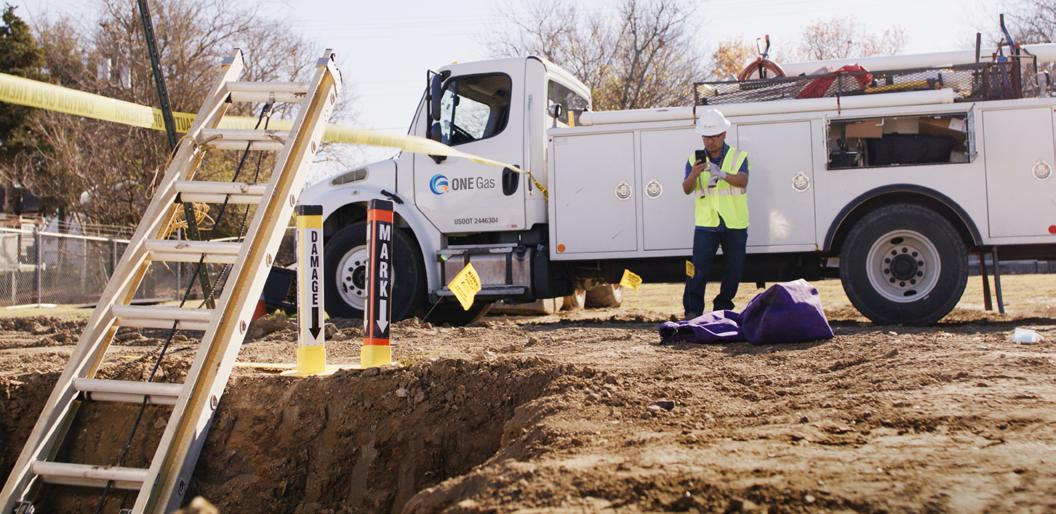
Benefits of LocusView
LocusView is a GPS-enabled mobile app that captures and displays detailed information about pipelines, installation dates, material types, fittings and pipeline locations to better inform actions.
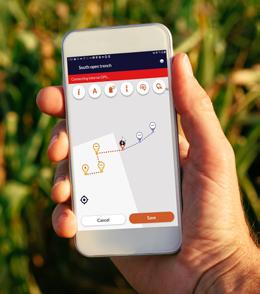
Our material failure investigation process helps us identify and correct pipe, fittings, equipment and tool failures. Various departments collaborate to investigate failures and identify steps to refine our processes and procedures to enhance the safety of our systems.
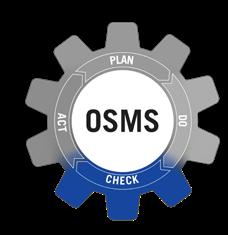
ONE Gas has fully deployed LocusView for our transmission and high-pressure distribution projects, and began deployment for distribution main projects in June of this year. The primary feature of LocusView to enhance our ability to track materials is its use of barcoding and GPS technology. This helps us be compliant while enhancing the user experience by reducing manual data entry, which in turn helps improve data quality. The LocusView application is fully integrated with both GIS, our mapping system, and Maximo, our asset management system.
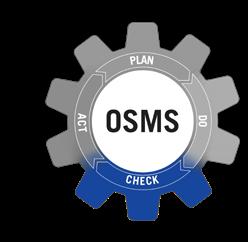
Work Management Systems
Our work management suite of software applications helps us effectively document, track, schedule and maintain pipeline assets. Many applications are integrated to create a more seamless user experience.
In 2022, ONE Gas began a multi-year project to upgrade our GIS database. As part of this upgrade, ONE Gas will also combine our Transmission and Distribution GIS systems into a single database, which is a vast improvement for GIS users and support staff who must utilize and support two separate applications today.
Application Purpose
• Maximo
• GIS database
Pipeline Safety Compliance
The Pipeline Safety Compliance team established the framework and processes to support our commitment to 100% compliance with safety and operational regulations and requirements to improve continuously. This team supports our commitment to safety and works alongside Field Operations to review procedures, records and documentation to verify compliance with our industry’s laws and regulations.
Call to A.C.T.
A.C.T. – being Accurate, Complete and Timely is a big part of the ONE Gas culture. It means doing our jobs in a safe and compliant manner. Working this way applies to all parts of our jobs, whether in the field or the office.
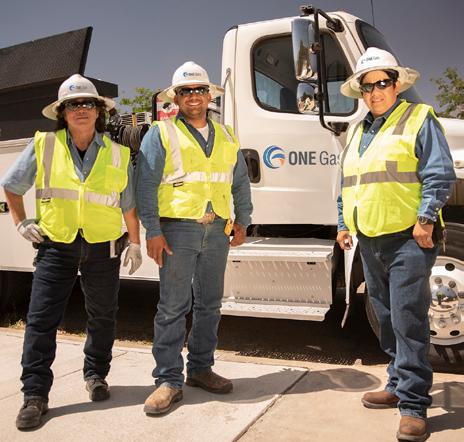
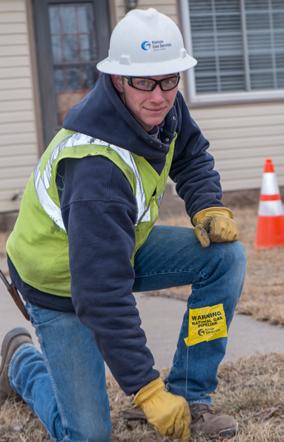
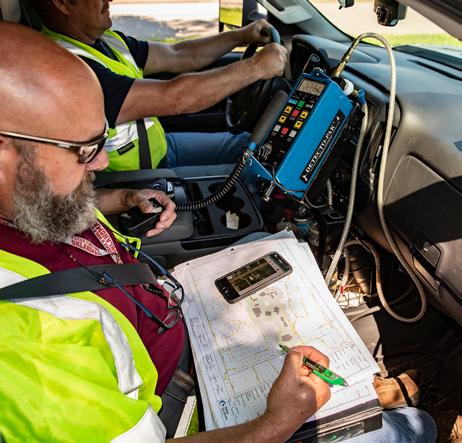
For example, being accurate and complete in record-keeping and information management can impact timeliness and safety when searching for a job order packet or records when planning a project. Proper records management means records remain authentic, accessible and reliable throughout creation, maintenance, retrieval, preservation and disposition.
• PragmaCAD/ MobLITE
• LocusView
• Asset Inspection
Digital systems of record for maintaining pipeline asset information required by pipeline safety regulations.
Used by the Engineering team to document technical designs and seek financial approval for projects.
Used by Field Operations to document construction and maintenance and compliance inspections.
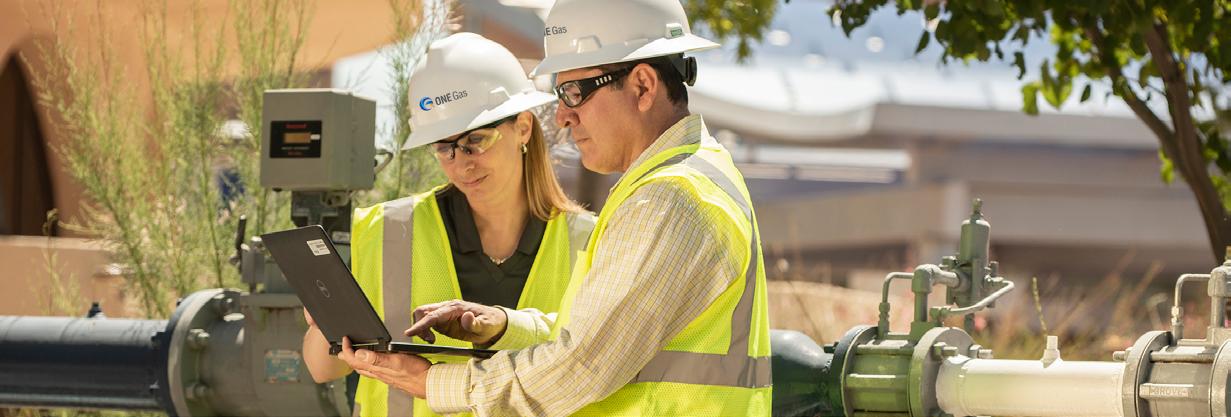
Operational Alignment Committees
MANAGEMENT REVIEW & CONTINUOUS IMPROVEMENT
Management establishes performance goals and objectives, manages resource availability and reviews performance based on continuous improvement efforts.
O-Net
O-Net is an easy-to-use application any employee can use to submit observations to enhance safety and promote continuous improvement. Users submit near misses, ideas for improvement and good catches. The application communicates with a database for retention, tracking, analysis and searchability. Since implementation in 2020, there have been 70 submissions with 65 successfully closed.
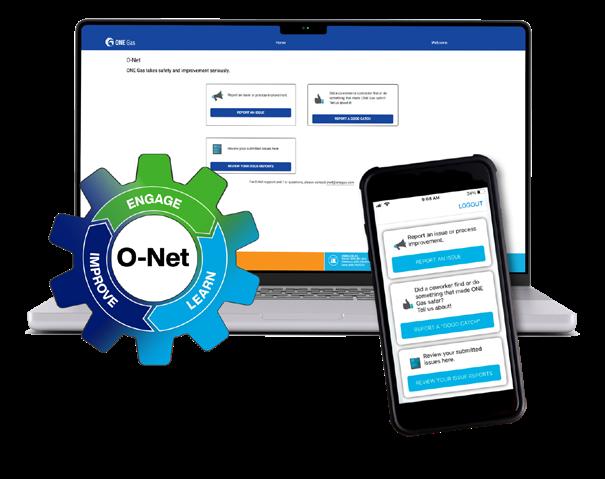
What’s New:
• Lessons Learned memo function added.
• Plans to expand access to the O-Net platform to contractors and service providers.


70 O-Net Submissions since implemented in 2020
ONE Gas operational alignment committees are crossfunctional groups charged with aligning our operations across the three states to drive safety, increase efficiency, centralize and standardize processes and share best practices for continual improvement.
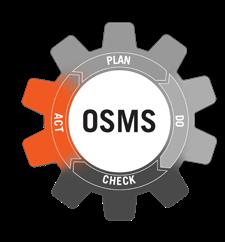
Committee Spotlight – Pressure and Measurement Committee
The Pressure and Measurement committee focuses on aligning and providing consistency for operating practices and equipment, materials and common approaches to policies, procedures, and enterprise applications related to pressure control and measurement.
The committee was instrumental in making process, equipment and reporting changes to adapt our organization to the new Transportation Safety Administration (TSA) requirements. Additionally, they’ve worked on deploying CNG trailers across the organization, evaluated emergency valve locations and developed a plan to expand electronic system monitoring.
Environmental, Safety, Health and Compliance Committee
Our Environmental, Safety, Health and Compliance (ESH&C) Steering Committee is chaired by our chief operating officer. This committee provides governance, vision, direction and oversight of our ESH&C programs and processes. They also oversee the implementation of the OSMS.
Learning from Others
ONE Gas participates in multiple information-sharing initiatives. Our participation in AGA’s Best Practice and Peer Review programs provides insights into improvement opportunities. We also review relevant events that the National Transportation Safety Board and other organizations report, supporting enhancements to operational and safety practices.

COMPETENCE, AWARENESS & TRAINING
We recruit and train highly experienced personnel to provide safe and reliable service to our customers – the foundation of an effective safety management system.
ONE Gas Training Center
The 17,000-square-foot training center in Tulsa, Oklahoma, is a hub for specialized, hands-on training for our Field Operations co-workers. Our training aligns with the B31Q, the industry safety and integrity standard published by the American Society of Mechanical Engineers (ASME).
In 2022, more than 23,000 training hours were logged for customer service, construction and maintenance training.
Coming Soon:
• Expanded training offerings to qualify steel welders and leak survey technicians
• Design begins for a new training center in the Austin, Texas area
• Launching a mobile training platform
• Launching the Trainer Excellence Program
Since the training center opened in 2021, more than 12,000 Operator Qualification Modules have been evaluated and 43,000 in-person-hours of training have been recorded.
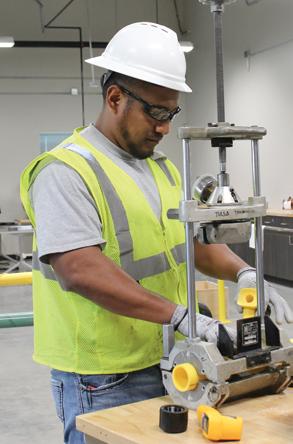
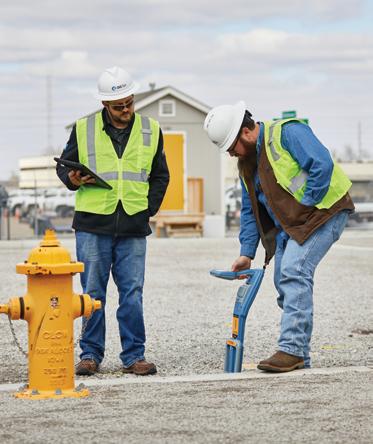
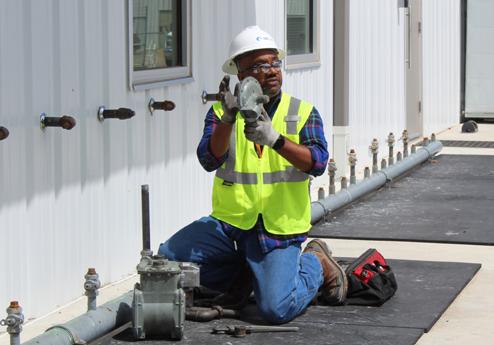
Engineer Training, Licensure and Capabilities Assessment
In 2022, ONE Gas developed the Engineering Training and Development Program (ETDP), a systematic approach to training and developing engineers. The program will provide engineers with consistent training across service territories and work groups. Implementation of phase one of three launched June 1, 2023.
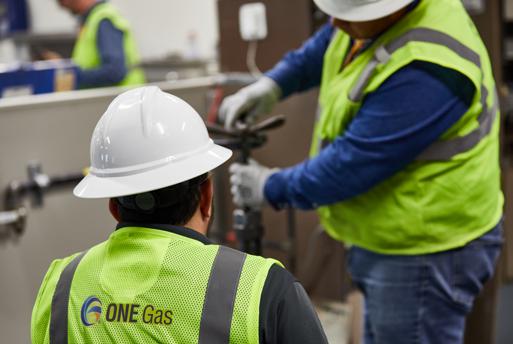
In Closing
Safety is — and always will be — our top priority. Our focus on continuous improvement through the Plan-Do-Check-Act cycle combined with our commitment to our Core Values remain the strong foundation for our success now and in the future.
For additional information, read our 2023 Environmental, Social and Governance Report at esg.onegas.com.
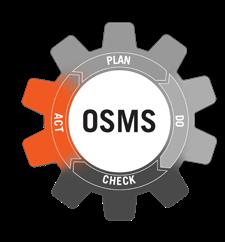