Root Cause Analysis:
Enhancing Safety in Chemical Processing Environments
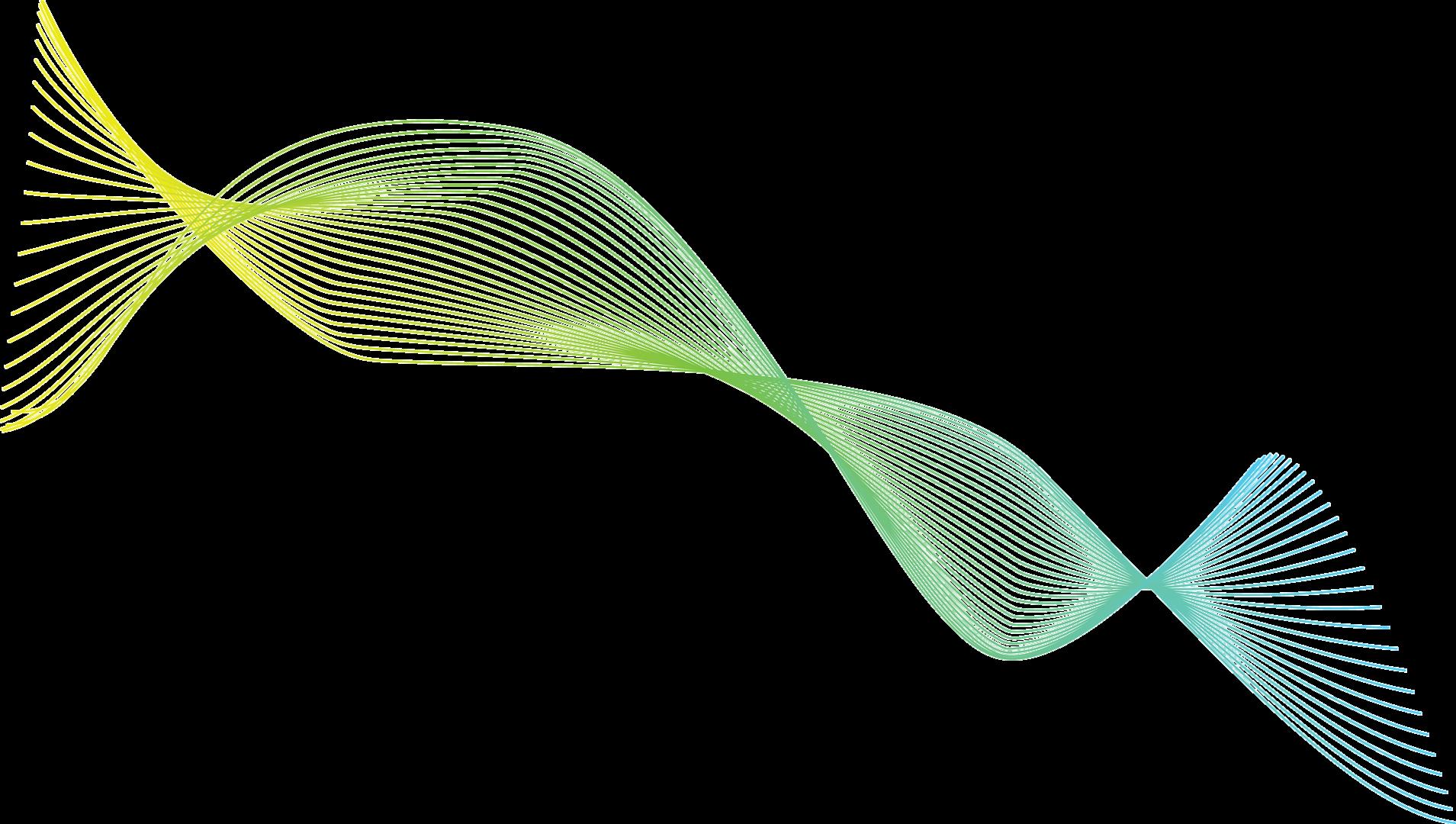
Noé Francisco Walls Longoria
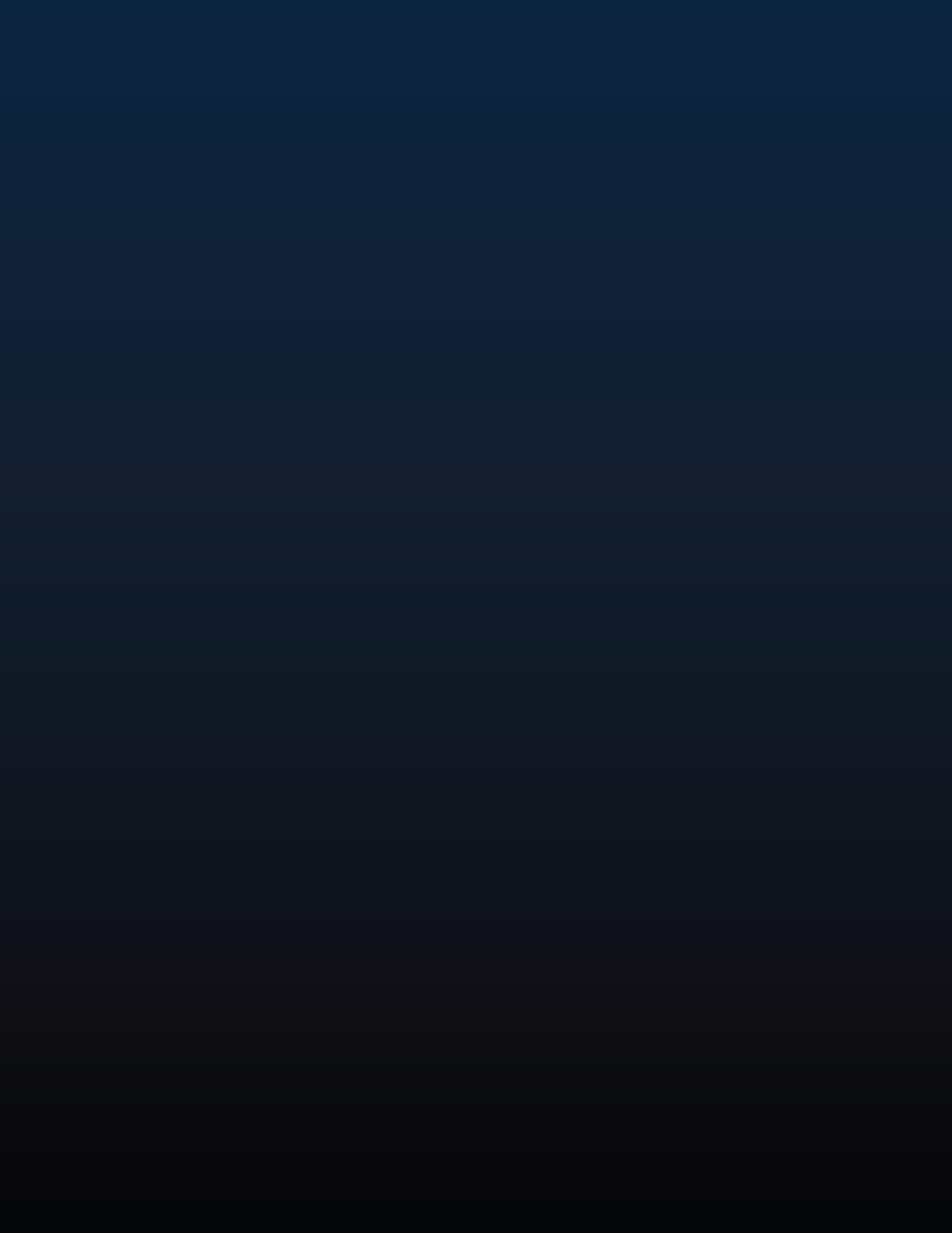
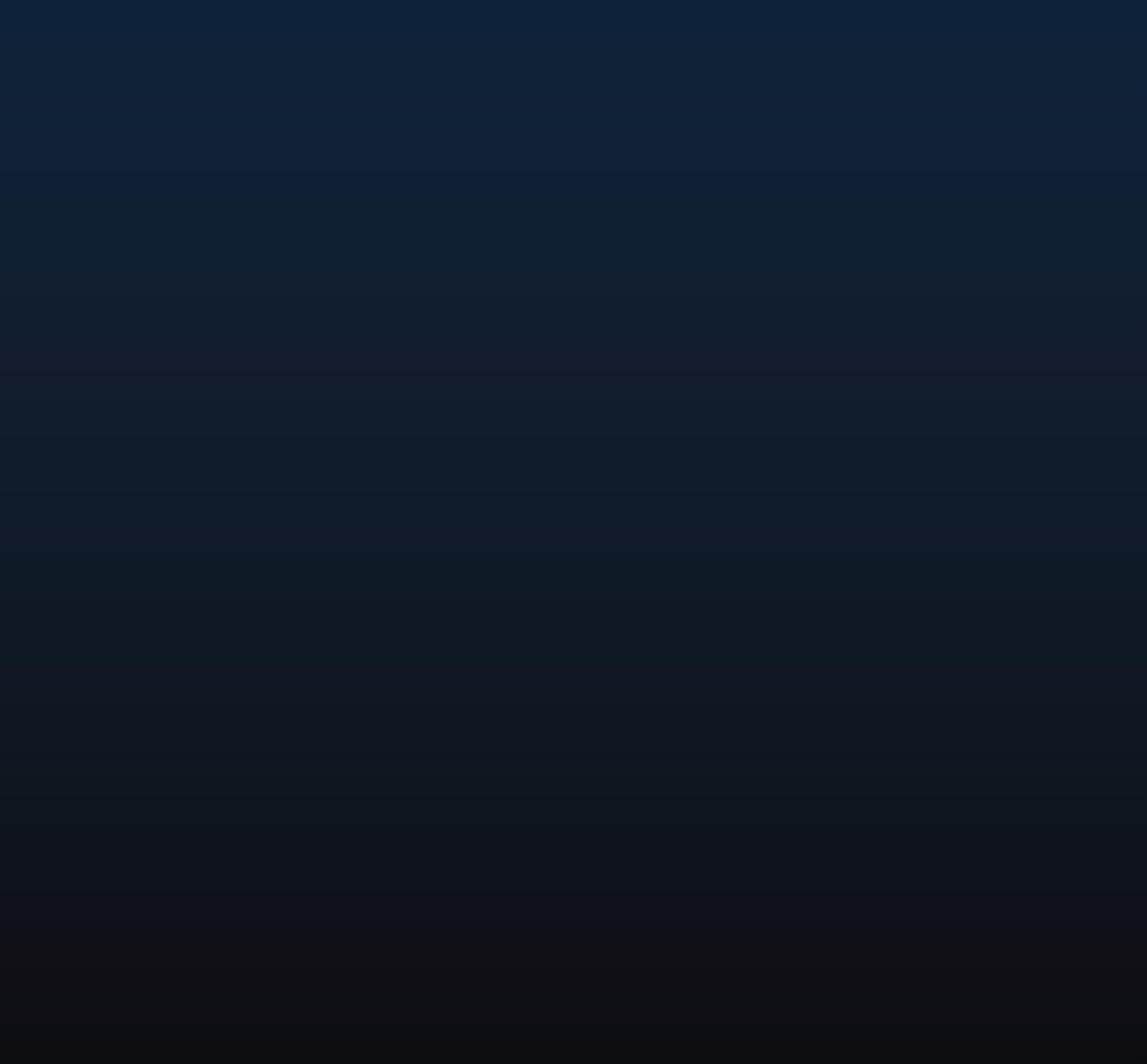
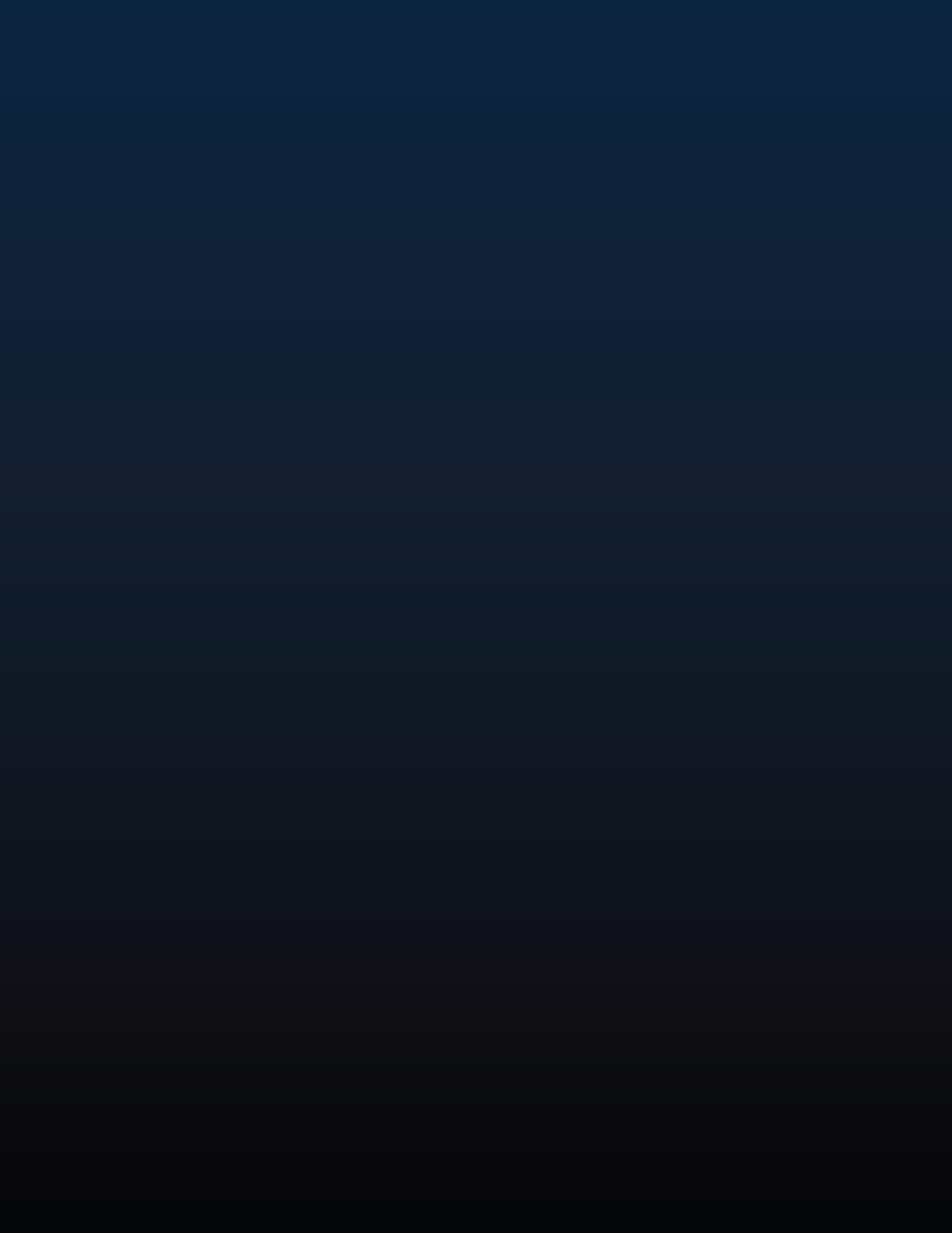
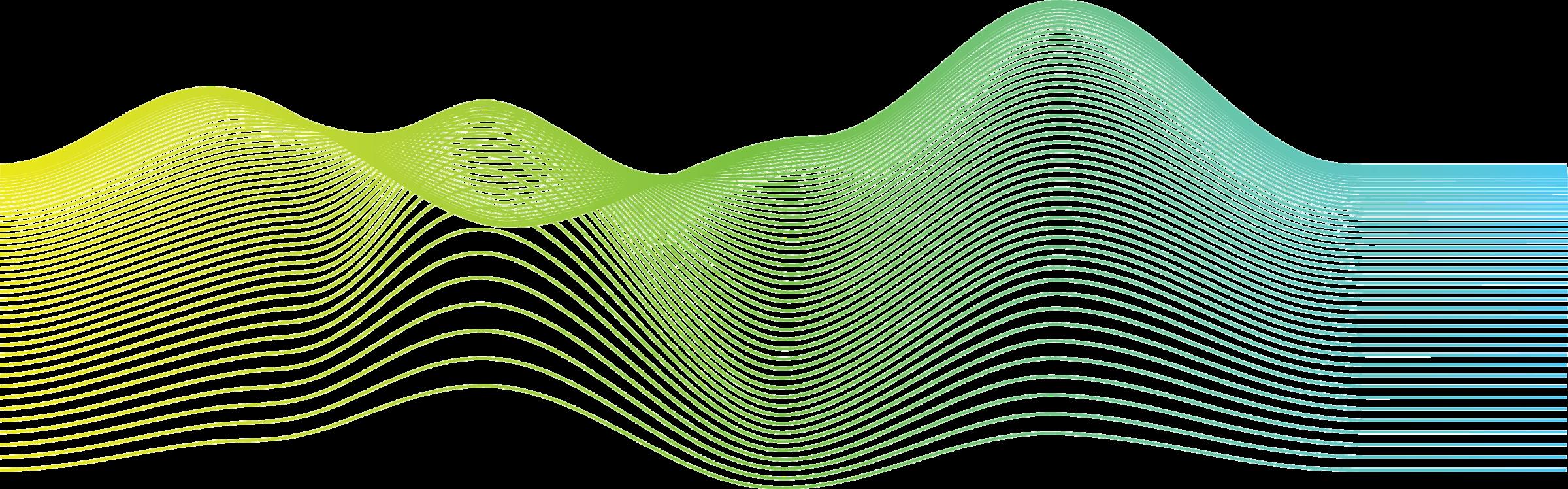
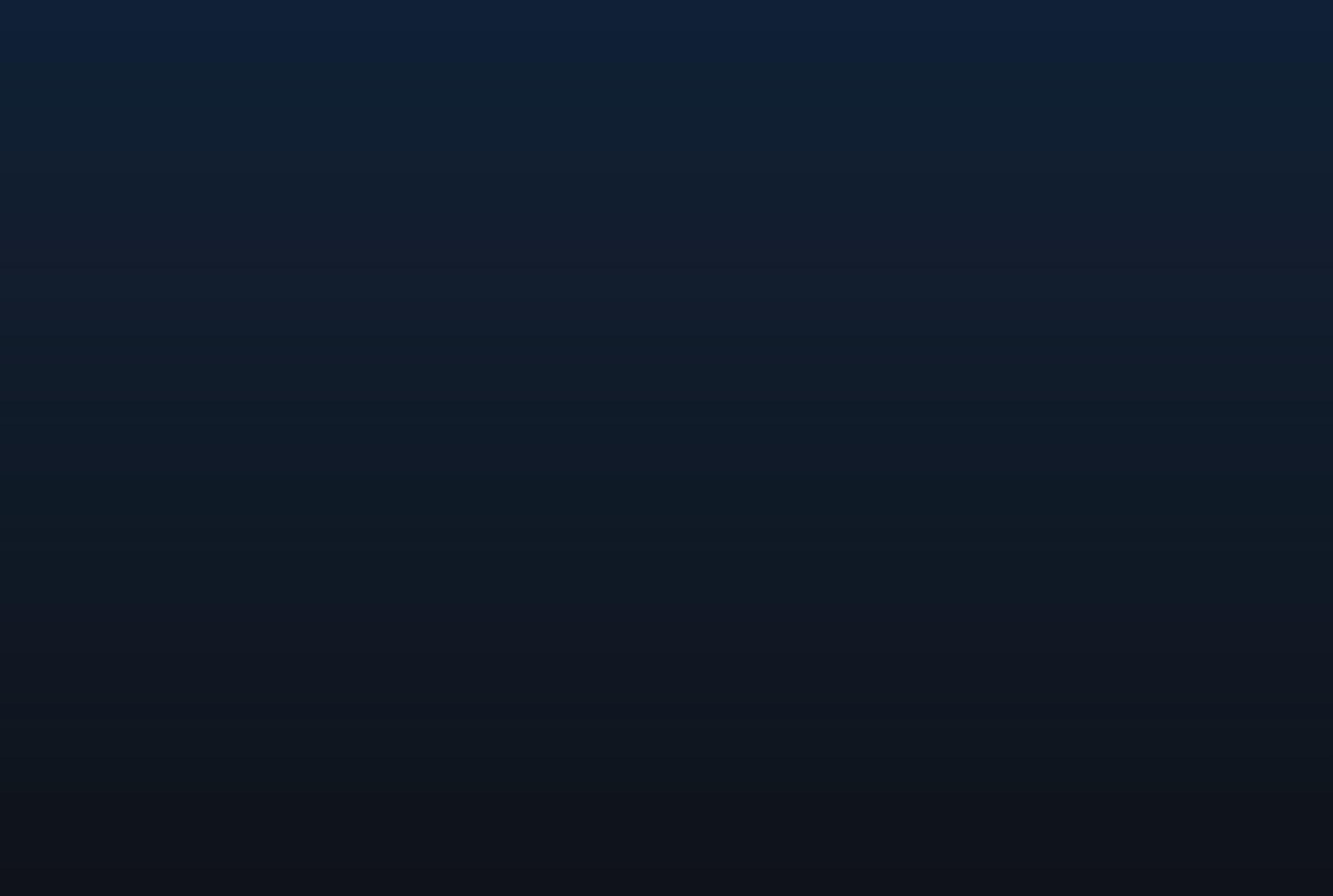
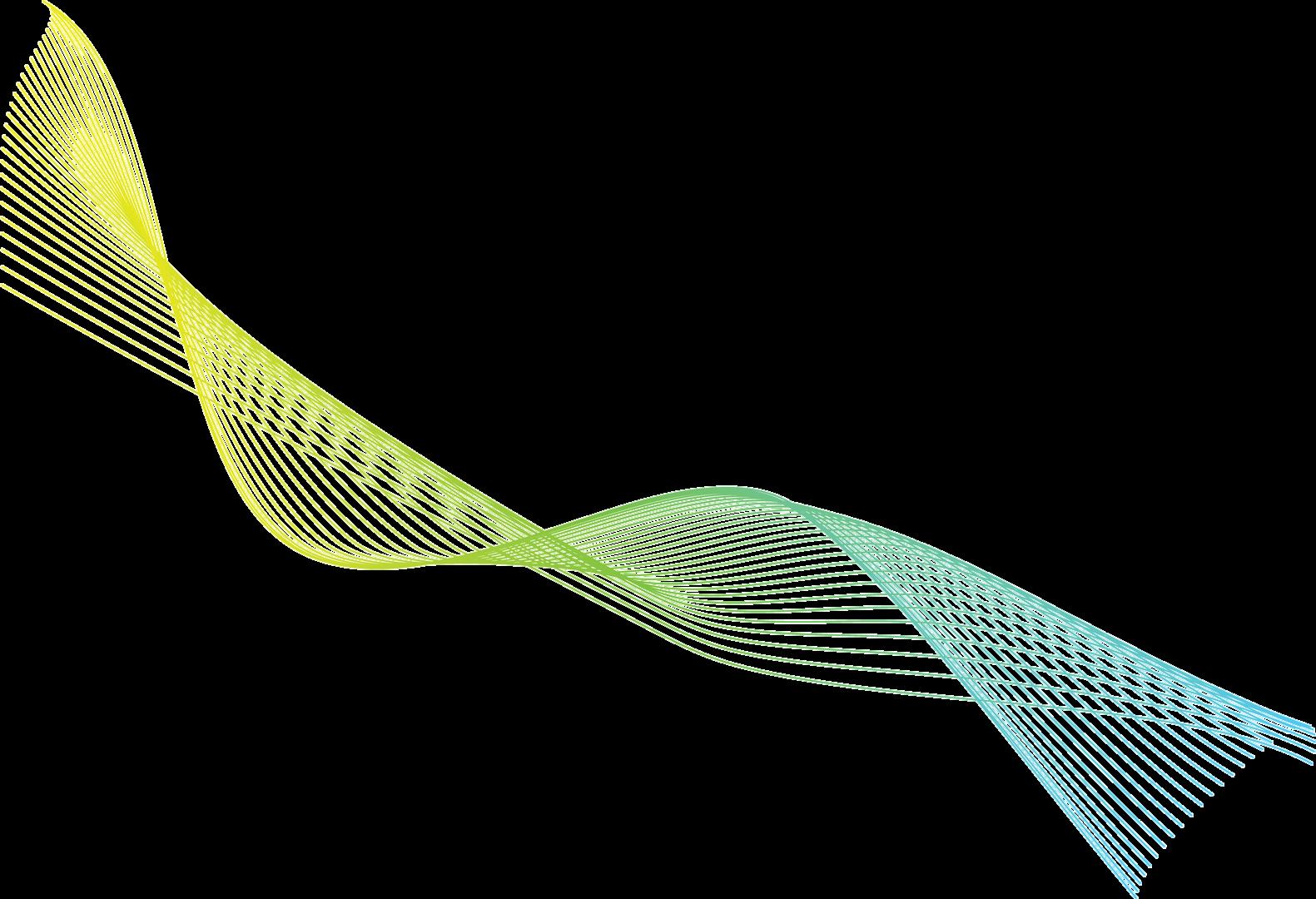
Noé Francisco Walls Longoria
Root Cause Analysis (RCA) is a systematic approach used to identify the underlying causes of incidents within chemical processing environments. It is an essential tool for enhancing safety and preventing future occurrences of similar events By focusing on the root causes rather than merely addressing the symptoms, RCA helps organizations develop effective strategies to mitigate risks and improve operational reliability. In the context of chemical plants, where the potential for hazardous incidents is significant, a thorough understanding of RCA is crucial for all employees involved in process safety incident investigations.
The RCA process typically begins with data collection, where relevant information about the incident is gathered This includes eyewitness accounts, operational data, and any documentation related to the event. It is crucial to ensure that this information is accurate and comprehensive, as the effectiveness of the analysis relies heavily on the quality of the data collected. Employees should be trained to document incidents meticulously and to report findings in a timely manner This foundational step sets the stage for a more profound exploration of the factors that contributed to the incident
Once data has been collected, the next step is to analyze the information to identify patterns and trends. This analysis often involves various tools and techniques, such as the “5 Whys” method or Fishbone diagrams, which help to visualize and categorize potential causes By asking “why” multiple times, employees can peel back the layers of the incident to uncover systemic issues that may not be immediately apparent. This analytical phase is critical for distinguishing between primary causes that require intervention and secondary factors that may simply be byproducts of the primary issues.
Following the identification of root causes, the implementation of corrective actions is essential. These actions should be designed to address the root causes effectively and prevent recurrence. This may involve changes to processes, updates to training procedures, or modifications to equipment. It is important that all employees understand their role in this phase and are encouraged to participate actively. By fostering a culture of continuous improvement and accountability, chemical plants can enhance their safety protocols and ensure that lessons learned from past incidents are integrated into future operations.
Lastly, the effectiveness of the implemented corrective actions should be monitored and evaluated over time. This ongoing assessment ensures that the measures taken are achieving the desired outcomes and that no new issues have emerged as a result Employees should be involved in this review process, providing feedback and insights based on their experiences. By maintaining a focus on continuous learning and adaptation, chemical processing environments can significantly enhance their safety culture, ultimately leading to a reduction in incidents and a more resilient operational framework.
Root cause analysis (RCA) plays a pivotal role in enhancing safety within chemical processing environments. By systematically identifying the underlying causes of incidents, RCA allows organizations to address not only the immediate issues but also the systemic weaknesses that contribute to recurring problems. In the context of chemical processing, where the stakes are often high due to the presence of hazardous materials and complex operations, the thorough application of RCA can significantly mitigate risks and enhance overall safety.
The chemical processing industry is inherently fraught with potential hazards, making it essential for employees to understand the importance of identifying root causes. Incidents such as leaks, spills, and equipment failures can lead to severe consequences, including injuries, environmental damage, and financial losses. By employing RCA, employees can develop a comprehensive understanding of how these incidents occur, enabling them to implement corrective actions that prevent future occurrences. This proactive approach not only protects personnel and the environment but also preserves the integrity of the facility.
Moreover, RCA fosters a culture of continuous improvement within chemical plants. When employees are encouraged to participate in the RCA process, they become more engaged and invested in safety practices This collaborative environment promotes open communication about safety concerns, leading to a more proactive stance on hazard identification and risk management. By involving employees in the analysis of incidents, organizations can leverage the collective knowledge and experience of their workforce, resulting in more effective and sustainable safety solutions.
Another critical aspect of RCA in chemical processing is its role in regulatory compliance. Regulatory agencies often require companies to conduct thorough investigations following incidents, and the documentation generated from RCA provides valuable insights into compliance efforts. By demonstrating due diligence in identifying and addressing root causes, organizations can better navigate regulatory requirements and avoid potential penalties. This not only helps in maintaining a good standing with regulatory bodies but also reinforces the commitment to safety and operational excellence
In summary, the importance of root cause analysis in chemical processing cannot be overstated. It serves as a fundamental tool for enhancing safety, fostering a culture of continuous improvement, and ensuring regulatory compliance. For chemical plant employees, understanding and implementing RCA is essential in creating a safer work environment and protecting both personnel and the surrounding community from the inherent risks associated with chemical processing operations By prioritizing RCA, organizations can achieve a significant reduction in incidents and cultivate a robust safety culture that benefits everyone involved.
The primary objective of this book is to provide chemical plant employees with a comprehensive understanding of root cause analysis (RCA) as it pertains to enhancing safety in chemical processing environments RCA is a systematic approach that identifies the fundamental causes of incidents to prevent recurrence By delving into the principles and methodologies of RCA, this book aims to equip employees with the necessary tools to analyze safety incidents effectively, thereby fostering a culture of continuous improvement and proactive safety management within their organizations.
Another key objective is to establish a clear connection between effective root cause analysis and the prevention of process safety incidents The book will demonstrate how a thorough investigation of incidents can reveal deeper systemic issues that contribute to failures in safety protocols. By highlighting case studies and real-life examples from the chemical processing industry, readers will learn how RCA not only identifies immediate causes but also uncovers underlying factors such as inadequate training, insufficient communication, or flawed procedures, which must be addressed to enhance overall safety
Additionally, the book aims to promote collaboration and communication among various stakeholders within chemical plants. Effective RCA requires input from multidisciplinary teams, including operators, engineers, safety professionals, and management This book will emphasize the importance of fostering a collaborative environment where employees feel empowered to report incidents and participate in investigations. By doing so, the book seeks to break down silos that often hinder effective communication and to encourage a unified approach to safety that leverages the diverse expertise of all employees.
Furthermore, this book intends to provide practical guidance on how to implement RCA methodologies within the context of chemical processing environments It will outline step-bystep processes, tools, and techniques that employees can utilize in their investigations. Special attention will be given to the integration of RCA into existing safety management systems, ensuring that employees have a clear understanding of how to apply these principles in their day-to-day operations. This practical approach aims to make RCA an integral part of the safety culture in chemical plants.
Finally, the book's objective includes fostering a mindset of resilience and accountability among chemical plant employees. By understanding the importance of learning from incidents and committing to continuous improvement, employees can contribute to a safer working environment. This book will encourage readers to view incidents not as failures, but as opportunities for growth and enhanced safety practices By instilling this mindset, the book aims to cultivate a culture where safety is prioritized, leading to a significant reduction in process safety incidents in the chemical processing industry.
Process safety is a critical discipline within the chemical processing industry, focusing on the prevention of incidents that can lead to catastrophic consequences. Key concepts in process safety form the foundation for effective risk management and are essential for ensuring the safety of personnel, the environment, and the facilities.
Understanding these concepts enables chemical plant employees to identify potential hazards, assess risks, and implement appropriate control measures
One of the core concepts in process safety is the identification and analysis of hazards. This involves recognizing potential sources of risk throughout the entire lifecycle of a chemical process, from design and operation to decommissioning
Employees must be trained to conduct thorough hazard analyses, using methodologies such as Hazard and Operability Studies (HAZOP) and Failure Mode and Effects Analysis (FMEA). These tools assist teams in systematically identifying risks associated with equipment, processes, and human factors, thereby fostering a proactive safety culture.
Another fundamental aspect is the concept of layers of protection This principle emphasizes the importance of multiple safety barriers to prevent incidents from escalating into serious events. Employees should understand the various layers, which can include engineering controls, administrative controls, and emergency response measures.
Each layer serves as a safeguard that reduces the likelihood of a failure, ensuring that if one layer is compromised, others will still function to protect against an incident.
The significance of a robust safety management system (SMS) cannot be overstated An SMS provides a structured approach to managing safety risks, integrating safety into everyday operations and decision-making processes
Employees must be familiar with the key components of an SMS, including policy development, risk assessment, performance monitoring, and continuous improvement. A well-implemented SMS promotes accountability and encourages a culture of safety, where employees feel empowered to report hazards and participate in safety initiatives
Finally, process safety is inherently linked to effective communication and training. The dissemination of safety information and the provision of training for employees at all levels are vital for fostering an informed workforce capable of recognizing and responding to potential hazards
Regular training sessions, drills, and safety meetings should be conducted to reinforce the importance of process safety concepts and ensure that employees are equipped with the knowledge and skills necessary to contribute to a safe working environment.
By prioritizing communication and training, chemical plants can enhance their overall safety performance and mitigate the risks associated with process safety incidents.
The regulatory framework governing chemical processing environments is crucial for ensuring safety and preventing incidents. Key regulatory bodies such as the Occupational Safety and Health Administration (OSHA), the Environmental Protection Agency (EPA), and the Chemical Safety Board (CSB) establish guidelines that influence operational practices.
These regulations encompass various aspects of chemical handling, from the storage and transportation of hazardous materials to the implementation of safety management systems. Compliance with these regulations is not merely a legal obligation; it is an essential component of a proactive approach to safety that can significantly mitigate risks associated with process safety incidents.
Central to the regulatory framework are standards that outline best practices for identifying, assessing, and managing hazards. Organizations like the American National Standards Institute (ANSI) and the National Fire Protection Association (NFPA) provide standards that are widely adopted within the industry.
These standards serve as benchmarks for safety practices and are often referenced in regulatory compliance audits. Employees in chemical plants must familiarize themselves with these standards, as adherence to them can not only enhance safety but also improve operational efficiency
Understanding the nuances of these guidelines helps foster a culture of safety that prioritizes risk management.
The implementation of process safety management (PSM) systems is a critical element of the regulatory framework. Under OSHA's PSM standard, facilities that handle highly hazardous chemicals must develop and maintain comprehensive safety programs
These programs include elements such as process hazard analysis, operational procedures, and employee training. Engaging employees in the development and ongoing evaluation of these programs ensures that safety becomes an integral part of the workplace culture.
Moreover, a robust PSM system can facilitate the identification of potential hazards before they result in incidents, making it an indispensable tool for chemical plant employees.
Investigating process safety incidents requires a thorough understanding of both the regulatory framework and the standards that inform investigation methodologies.
The guidelines provided by regulatory agencies often dictate the investigation process, including reporting requirements and the need for root cause analysis.
Chemical plant employees involved in incident investigations must be wellversed in these regulations to ensure compliance and the effectiveness of their findings.
This knowledge not only aids in the identification of root causes but also supports the development of corrective actions aimed at preventing future occurrences.
In conclusion, the regulatory framework and standards play a pivotal role in shaping safety practices within chemical processing environments. By understanding and adhering to these regulations, employees can contribute to a safer workplace, reduce the likelihood of incidents, and promote a culture of continuous improvement.
Engaging with the regulatory framework is not just about compliance; it is about fostering an environment where safety is prioritized and risk is managed effectively As the industry evolves, staying informed about changes in regulations and standards will be essential for maintaining high safety standards and protecting both personnel and the surrounding community.
Safety Management Systems (SMS) are an integral component in promoting a culture of safety within chemical processing environments. These systems provide a structured approach to managing safety risks, ensuring compliance with regulations, and fostering a proactive safety culture among employees.
By implementing an effective SMS, chemical plants can systematically identify hazards, assess risks, and implement control measures that significantly reduce the likelihood of incidents. It is essential for employees to understand the critical elements of SMS and their roles in maintaining a safe working environment.
At the core of an SMS is the identification and evaluation of hazards associated with chemical processes. This involves conducting regular risk assessments, which help in pinpointing potential sources of incidents, such as equipment failures, human errors, or external factors
Employees play a vital role in this phase by providing insights based on their day-today experiences and observations. Their participation ensures that the SMS is grounded in practical realities, allowing for a more accurate assessment of risks and the development of appropriate mitigation strategies.
Another key element of an SMS is the establishment of clear policies and procedures designed to govern safety practices. These policies should outline the responsibilities of all employees, from management to frontline workers, in ensuring safety. Training programs must be developed to educate employees about these policies, emphasizing the importance of adherence to safety protocols. When employees are well-informed and trained, they are more likely to engage in safe practices and report unsafe conditions or behaviors, thus contributing to the overall effectiveness of the SMS
Monitoring and continuous improvement are essential components of an SMS. This involves regular audits and inspections to evaluate the effectiveness of safety measures and compliance with established procedures. Employees should be encouraged to actively participate in these evaluations, as their feedback can lead to valuable insights for improvement Moreover, incidents and near-misses should be thoroughly investigated to identify root causes, enabling the organization to implement corrective actions that prevent recurrence. This continuous feedback loop is crucial for evolving the SMS and enhancing safety performance over time.
In conclusion, the implementation of a robust Safety Management System is paramount for chemical processing plants aiming to enhance safety and prevent incidents. Employees at all levels must recognize their role in this system, from hazard identification to policy adherence and continuous improvement. By fostering a culture where safety is prioritized and integrated into daily operations, chemical plants can significantly mitigate risks and safeguard the health and well-being of their workforce. Ultimately, a well-functioning SMS not only protects employees but also contributes to the overall efficiency and reliability of chemical processing operations.
Incident investigation is a critical component of process safety management within chemical processing environments. It serves as a systematic approach to identifying the underlying causes of incidents that occur in the workplace By analyzing incidents, organizations can uncover deficiencies in processes, equipment, and human factors that may contribute to safety risks.
The primary goal of incident investigation is not only to understand what went wrong but also to implement corrective actions that prevent recurrence, thereby enhancing the overall safety culture within the organization.
The incident investigation process typically begins with the immediate response to an event This includes securing the scene, ensuring the safety of personnel, and gathering initial information about the incident. A preliminary assessment is conducted to determine the scope and scale of the investigation needed
In chemical plants, where hazards can be significant, ensuring that the area is safe for investigators is paramount. This initial stage sets the groundwork for a thorough and effective investigation, allowing for a comprehensive understanding of the incident's context
Following the initial response, the investigation team engages in data collection and analysis. This phase involves gathering evidence, interviewing witnesses, and reviewing relevant documentation such as maintenance records, operating procedures, and training materials
The objective is to compile a detailed account of the incident, which includes timelines, contributing factors, and any deviations from established protocols. Utilizing various investigative tools, such as root cause analysis methodologies, enables teams to dissect complex scenarios and identify not only what happened but why it happened.
Once the investigation is complete, findings are documented in a detailed report that outlines the root causes identified during the analysis This report is crucial for developing recommendations and corrective actions aimed at mitigating risks.
It is essential that these recommendations are communicated effectively to all levels of the organization, ensuring that lessons learned from incidents are integrated into training programs, standard operating procedures, and safety practices.
This feedback loop is vital for fostering a culture of continuous improvement and reinforcing the importance of safety in the workplace
Implementing the recommendations from incident investigations is an ongoing process that requires commitment from all employees. It is not sufficient to merely identify causes; organizations must actively work to address them through changes in practices, equipment upgrades, and enhanced training.
Regular follow-up and assessments of the effectiveness of implemented changes are necessary to ensure that the organization continues to learn from past incidents.
Ultimately, a robust incident investigation framework plays a fundamental role in enhancing safety in chemical processing environments, safeguarding employees, and ensuring compliance with regulatory standards
Incident investigation in chemical processing environments is a critical component of ensuring safety and preventing future occurrences.
The first step in an effective investigation is to secure the scene of the incident This involves preserving evidence, restricting access to the area, and documenting the immediate conditions surrounding the event.
It is essential to gather information as soon as possible, while the details are still fresh in the minds of those involved This action not only protects the integrity of the investigation but also helps to identify any immediate hazards that may still be present
Once the scene is secured, the next step is to gather data. This includes collecting physical evidence, reviewing operational records, and interviewing witnesses. A systematic approach should be taken to ensure that all relevant information is obtained
This may involve creating a timeline of events leading up to the incident, which can help in understanding the sequence of actions and decisions made by personnel.
The data collected during this phase will serve as the foundational material for the analysis that follows, making thoroughness and accuracy paramount.
After gathering data, the investigation team must analyze the information to identify potential root causes. This process often employs various analytical tools and techniques, such as the "5 Whys" or fishbone diagrams.
The objective is to uncover not just the immediate causes of the incident, but also underlying systemic issues that may have contributed. It is important for the investigation team to maintain an open mind during this phase, considering all possible factors, including human behavior, equipment failures, and procedural inadequacies.
Following the analysis, the team should compile their findings into a comprehensive report This report should detail the investigation process, the evidence gathered, the root causes identified, and any contributing factors.
Additionally, it should include recommendations for corrective actions aimed at preventing recurrence.
It is crucial that these recommendations are actionable and tailored to the specific conditions and culture of the chemical plant, ensuring they are feasible for implementation.
The final step in the incident investigation process involves the communication and implementation of the findings This includes sharing the report with all relevant stakeholders, conducting training sessions, and establishing a follow-up mechanism to monitor the effectiveness of the corrective actions taken
Engaging employees in this process fosters a culture of safety and collaboration, emphasizing the importance of learning from incidents to enhance safety practices in chemical processing environments.
By systematically addressing the steps in incident investigation, chemical plants can significantly reduce the likelihood of future incidents, thereby protecting both personnel and the facility.
In the realm of process safety incident investigation, clearly defined roles and responsibilities are crucial for ensuring effective communication and collaboration among team members
Each participant in an investigation, from the incident investigator to the subject matter experts, plays a vital role in uncovering the root causes of incidents and implementing corrective actions.
Establishing these roles prior to an investigation not only streamlines the process but also enhances the overall safety culture within the chemical processing environment
The lead investigator is typically tasked with overseeing the entire investigation process. This individual is responsible for coordinating the investigation team, setting timelines, and ensuring that all relevant data is collected and analyzed
The lead investigator must possess strong leadership skills and a thorough understanding of both process safety principles and the specific processes involved in the incident. Their ability to facilitate discussions and encourage open communication among team members is essential for fostering a comprehensive investigation.
Subject matter experts (SMEs) play an indispensable role by providing specialized knowledge pertinent to the incident under investigation. These individuals may come from various disciplines, such as engineering, operations, or maintenance, and their insights are invaluable in understanding the technical aspects of the incident.
SMEs contribute by identifying potential failure points, evaluating existing safety systems, and offering recommendations for improvements Their involvement ensures that all relevant factors are considered, leading to a more thorough and accurate analysis of the root causes.
Another critical role in the investigation process is that of the data analyst This individual is responsible for gathering and interpreting data related to the incident, including operational records, maintenance logs, and safety audits
The data analyst must possess strong analytical skills to identify trends and anomalies that could contribute to incident causation. By presenting their findings in a clear and concise manner, they help the investigation team draw informed conclusions and develop effective mitigation strategies
Lastly, the involvement of frontline employees cannot be overstated. These individuals often have firsthand knowledge of the processes and systems in place, making their input essential to the investigation.
Encouraging open dialogue with frontline workers helps to identify potential hazards and contributes to a more comprehensive understanding of the incident
When employees feel their voices are heard and valued, it fosters a culture of safety and continuous improvement, ultimately enhancing the effectiveness of the investigation process and promoting a safer chemical processing environment.
The Fishbone Diagram, also known as the Ishikawa or cause-and-effect diagram, serves as a vital tool in root cause analysis within chemical processing environments. This visual representation allows employees to systematically explore the various factors contributing to a process safety incident
By delineating potential causes into distinct categories, the Fishbone Diagram helps teams organize their thoughts and focus their investigation efforts. This structured approach aids in identifying not just the immediate failures but also the underlying systemic issues that may have led to an incident
In a chemical plant, safety incidents can arise from a multitude of sources, including equipment failure, human error, and environmental influences. The primary categories typically include People, Processes, Equipment, Materials, Environment, and Management.
By categorizing potential causes in this manner, employees can ensure a comprehensive examination of all relevant factors This thorough analysis is crucial in a high-stakes environment where oversights can result in significant safety hazards or operational disruptions
The process of creating a Fishbone Diagram begins with a clear definition of the problem or incident at hand.
Employees should convene a diverse team that includes personnel from various functions within the plant, such as operations, maintenance, and safety.
As the team brainstorms potential causes, they populate the diagram with ideas, which encourages collaborative thinking and draws on the collective expertise of the group.
This collaborative effort not only enhances the quality of the investigation but also fosters a culture of safety and shared responsibility among employees.
Once the diagram is populated, the next step involves analyzing the identified causes The team should prioritize these causes based on their likelihood of contributing to the incident and the potential impact on safety and operations.
This prioritization allows teams to focus on the most critical issues, ensuring that resources are allocated effectively for corrective actions Importantly, addressing root causes rather than merely symptoms is essential for preventing recurrence, thereby enhancing overall safety in the chemical processing environment.
In conclusion, the Fishbone Diagram is an indispensable tool for chemical plant employees engaged in process safety incident investigations.
By facilitating a structured exploration of potential causes, it aids in uncovering both immediate and systemic issues that contribute to safety incidents.
The collaborative nature of its development promotes a cohesive safety culture, while the focus on root causes ensures that corrective actions lead to lasting improvements.
Adopting this method can significantly enhance the effectiveness of safety investigations and ultimately contribute to a safer working environment in chemical processing facilities.
The 5 Whys Technique is a fundamental tool in root cause analysis, particularly effective in the context of chemical processing environments where incidents can have severe consequences This technique involves asking "why" five times in succession to drill down to the core of a problem
By systematically questioning the reasons behind an incident, employees can uncover underlying issues that may not be immediately apparent. This process encourages a deeper understanding of failures and encourages a culture of continuous improvement, essential in maintaining safety and efficiency in chemical plants
In practice, the 5 Whys Technique begins with identifying a specific problem or incident. For instance, if a chemical spill occurs, the first question might be, "Why did the spill happen?" The answer could reveal that a valve was left open.
The next question would then address this answer, such as, "Why was the valve left open?" This iterative questioning continues, peeling back layers of the incident until the fundamental root cause is identified.
It is not uncommon for the initial answers to focus on superficial symptoms, which is why persistence in questioning is vital to reach the root cause
The effectiveness of the 5 Whys Technique lies in its simplicity and accessibility Employees at all levels of a chemical plant can utilize this method without requiring extensive training or specialized knowledge.
The informal nature of the technique encourages participation and input from various team members, fostering collaboration
By engaging everyone in the investigation process, organizations can benefit from diverse perspectives that may highlight different facets of an incident, leading to a more comprehensive understanding of the root causes.
However, while the 5 Whys Technique can be immensely beneficial, it is important to recognize its limitations.
This method is best suited for relatively straightforward problems.
More complex incidents may require additional tools and methodologies to ensure a thorough analysis. In such cases, combining the 5 Whys with other techniques, such as fishbone diagrams or fault tree analysis, can enhance the investigation and provide a more robust understanding of the failure.
Ultimately, the 5 Whys Technique serves as a vital component in enhancing safety in chemical processing environments
By encouraging employees to engage in critical thinking and analysis, organizations can create a proactive approach to incident investigation This not only helps in identifying and rectifying root causes effectively but also instills a culture of safety and accountability.
As chemical plants continue to navigate the complexities of process safety, employing such techniques will be crucial in preventing future incidents and ensuring a safe working environment for all employees
Fault Tree Analysis (FTA) is a systematic, deductive approach used to identify the various combinations of system failures that could lead to undesirable events, particularly in chemical processing environments
This technique serves as a critical tool for chemical plant employees engaged in process safety incident investigations
By mapping out the pathways that lead to failures, FTA allows teams to visualize how different factors interact and contribute to accidents or incidents. This understanding is vital for developing effective prevention strategies and mitigating risks within the plant.
The process of conducting a fault tree analysis typically begins with the identification of a specific undesired event, often referred to as the top event.
This could be a chemical release, equipment failure, or any incident that poses a risk to safety and operational integrity.
Once the top event is established, the analysis moves into a graphical representation of the various contributing factors, categorized as basic events and intermediate events.
Basic events are the fundamental failures that can lead to the top event, while intermediate events represent combinations of basic events or other intermediate events. This hierarchical structure illustrates the complexity of interactions within the system.
After constructing the fault tree, teams can evaluate the various paths that could lead to the top event This evaluation is conducted through qualitative and quantitative analyses, which assess the likelihood of each basic event occurring
By calculating probabilities, teams can prioritize their focus on the most significant risks and determine where to allocate resources for preventive measures. This data-driven approach enhances decision-making and enables chemical plant employees to target interventions that will yield the greatest safety benefits
In addition to risk assessment, FTA also supports continuous improvement within chemical processing environments. By regularly reviewing and updating fault trees in response to new data, incidents, or changes in processes, plants can ensure that their safety strategies remain relevant and effective.
This iterative process promotes a culture of safety, as employees become more engaged in understanding the risks associated with their work and the importance of adhering to safety protocols. Furthermore, involving employees in the FTA process fosters collaboration and knowledge sharing, which can lead to innovative solutions for reducing risk.
Ultimately, fault tree analysis is an indispensable component of a comprehensive approach to process safety incident investigation in chemical plants By systematically identifying and analyzing the failure pathways that can lead to incidents, FTA empowers employees to take proactive measures in preventing accidents.
As the chemical processing industry continues to evolve, integrating advanced risk assessment tools like FTA will be crucial in enhancing safety outcomes and ensuring the well-being of both employees and the surrounding community.
In the realm of process safety incident investigation, a variety of analytical tools complement traditional methodologies, enriching the understanding of underlying causes in chemical processing environments
These tools provide diverse perspectives and insights that can lead to more effective solutions and enhanced safety measures. By incorporating these additional analytical approaches, employees can develop a holistic view of incidents, ensuring that all potential contributing factors are considered. This comprehensive analysis is vital for fostering a proactive safety culture within chemical plants.
One prominent tool is the (FTA), which employs a top-down approach to identify potential failure points within a process. By mapping out the relationships between different failures and their effects, FTA allows teams to visualize how various factors can converge to cause an incident
This tool is particularly useful in complex systems, where multiple interactions can lead to unexpected outcomes. By systematically breaking down the events that lead to a failure, employees can identify not only the immediate causes but also the systemic issues that may need addressing to prevent future occurrences.
Another valuable analytical tool is the Bowtie Analysis, which combines elements of both risk assessment and incident investigation. This method provides a visual representation of how hazards can lead to unwanted events, delineating preventive and mitigative controls.
Human Factors Analysis (HFA) is another crucial analytical tool that focuses on understanding the role of human behavior in incidents HFA examines how organizational culture, communication, and decision-making processes influence employee actions and can contribute to safety breaches.
By investigating these human elements, chemical plants can unveil underlying issues that may not be immediately visible through technical analyses alone. Addressing these factors can lead to improved training programs, better communication channels, and ultimately a more robust safety environment
Lastly, Data Mining and Predictive Analytics harness the power of historical incident data to uncover patterns and trends that may not be obvious through traditional analysis. By utilizing advanced statistical techniques, chemical plant employees can predict potential failures before they occur, allowing for preemptive action This forward-thinking approach not only enhances safety but also improves operational efficiency by minimizing unplanned downtimes and associated costs. By illustrating the pathways from a potential hazard to an incident, Bowtie Analysis emphasizes the importance of both proactive and reactive measures Chemical plant employees can use this tool to assess existing safety controls and identify gaps that might expose the facility to risks, thereby enhancing overall safety strategies.
The integration of these analytical tools into the incident investigation process can significantly elevate the safety standards within chemical processing environments, ensuring a safer workplace for all employees
In the context of process safety incident investigations, various types of data are essential for conducting a thorough root cause analysis This data can be categorized into several key areas, each contributing to a comprehensive understanding of the incident. The primary categories include operational data, equipment data, human factors data, environmental data, and regulatory compliance data Collectively, these data types facilitate a systematic approach to identifying underlying issues and preventing future occurrences.
Operational data encompasses information related to the normal functioning of the chemical processing systems This includes production logs, process flow diagrams, and operational parameters such as temperature, pressure, and flow rates. By analyzing this data, investigators can establish baseline conditions and identify deviations that may have contributed to the incident Furthermore, operational data helps in understanding the sequence of events leading up to the incident, allowing for a clearer picture of what occurred during the process.
Equipment data is crucial in evaluating the mechanical and structural integrity of the systems involved in the incident. This type of data includes maintenance records, inspection reports, and specifications for the equipment used. Analyzing this information helps identify potential failures or limitations in the equipment that may have played a role in the incident. It is vital to assess whether the equipment was operating within its design parameters and whether any maintenance or operational lapses occurred prior to the incident
Human factors data focuses on the actions and decisions made by personnel during the incident. This includes training records, shift logs, and incident reports. Understanding human factors is essential, as many incidents can be traced back to errors in judgment, lack of training, or inadequate communication among team members By examining this data, investigators can identify gaps in training or procedural adherence that contributed to the incident, informing future training and operational improvements.
Environmental data includes information about the conditions surrounding the incident, such as weather conditions, site layout, and the presence of hazardous materials This data helps contextualize the incident within the broader operational environment. For instance, understanding how external factors may have influenced the incident can lead to insights about potential vulnerabilities in the process. Additionally, regulatory compliance data provides insight into whether the facility adhered to relevant safety standards and regulations, highlighting areas where improvements may be necessary to enhance overall safety and compliance in chemical processing environments
Data collection is a critical component of root cause analysis in chemical processing environments Effective methods for gathering data can significantly influence the quality of the investigation and the subsequent recommendations for safety improvements Various techniques can be employed, each with its specific advantages and considerations, depending on the nature of the incident being investigated. This chapter will explore the most commonly used data collection methods, emphasizing their relevance to process safety incident investigation in chemical plants
Interviews are one of the primary methods of data collection in incident investigations. Conducting structured or semi-structured interviews with employees who were directly involved in or witnessed the incident can provide valuable insights These interviews should be approached with care, ensuring that they are conducted in a non-threatening environment to encourage open and honest dialogue. It is crucial to ask specific questions that help to reconstruct the timeline of events and understand the decisions made during the incident. Capturing diverse perspectives can reveal discrepancies in understanding, which may lead to identifying systemic issues that contributed to the incident
Document review is another essential method for data collection. Investigators should gather and analyze a variety of documents, such as safety data sheets, maintenance records, operating procedures, and training materials These documents can provide context about the processes involved and highlight deviations from established safety protocols. Additionally, reviewing past incident reports can help identify recurring issues or trends that may not have been adequately addressed.
A thorough examination of documentation can illuminate factors that contributed to the incident and inform the development of corrective actions.
Observational techniques can also be valuable in the data collection process. On-site observations allow investigators to assess the physical environment, equipment conditions, and employee behaviors in real-time.
This method can help to identify unsafe practices, equipment malfunctions, or environmental factors that may have contributed to the incident.
Observations should be systematic, focusing on specific processes or activities relevant to the incident.
Additionally, using tools such as checklists or standardized observation forms can enhance the reliability and consistency of the data collected during this phase.
Surveys and questionnaires can serve as supplementary tools for data collection, especially when dealing with larger groups of employees. These instruments can be designed to gather quantitative data regarding employee perceptions of safety practices, training adequacy, and incident response.
Well-structured surveys can help to identify patterns or trends across different departments or shifts, providing a broader view of the organizational culture surrounding safety. However, it is important to ensure that surveys are anonymous to encourage honest feedback and to frame questions carefully to avoid leading responses.
In conclusion, the effective collection of data through interviews, document reviews, observations, and surveys is fundamental to conducting a thorough root cause analysis in chemical processing environments.
Each method offers unique insights and, when used in combination, can provide a comprehensive understanding of the factors that contributed to an incident By employing these methods thoughtfully, chemical plant employees can enhance the quality of their investigations, ultimately leading to improved safety practices and a stronger safety culture within their organizations.
In the pursuit of enhancing safety within chemical processing environments, analyzing data for root causes becomes a critical component of incident investigation
This process entails systematically examining data collected from various sources, including incident reports, operational logs, and equipment performance records.
By approaching data analysis with a structured methodology, chemical plant employees can identify patterns and anomalies that may signal underlying issues
Effective data analysis not only aids in understanding what happened during an incident but also assists in uncovering why it occurred, thereby providing a foundation for effective corrective actions.
The initial step in data analysis involves gathering relevant information from diverse sources. Employees should ensure that data collection methods are thorough and comprehensive, capturing all pertinent details surrounding the incident This may include interviewing personnel involved, reviewing maintenance records, and assessing environmental conditions at the time of the incident.
By compiling a wide array of data, the investigation team can create a holistic view of the event, which is essential for identifying potential root causes. Employees should be trained to recognize the significance of various data types, including qualitative insights from eyewitness accounts and quantitative metrics from operational performance
Once the data has been gathered, the next phase is to organize and analyze it systematically. Utilizing statistical tools and software can enhance the efficiency of this process, allowing for the identification of trends and correlations that may not be immediately apparent
For instance, employees can analyze historical incident data to determine if similar events have occurred under comparable circumstances.
This comparative analysis can reveal systemic issues within the plant's operations, such as recurring equipment failures or procedural deviations. By focusing on these patterns, the investigation team can identify potential weaknesses in safety protocols that may require immediate attention.
In addition to quantitative analysis, it is vital to incorporate qualitative assessments into the investigation. This includes examining the human factors that may have contributed to the incident, such as communication breakdowns, inadequate training, or lapses in adherence to safety protocols.
Engaging with employees through structured interviews or surveys can provide valuable insights into the organizational culture and how it influences safety practices. Understanding the human element is crucial, as many incidents can be traced back to decisions made or actions taken by individuals within the chemical processing environment.
Finally, synthesizing the findings from both quantitative and qualitative analyses allows for the formulation of targeted recommendations aimed at preventing future incidents. Employees should be encouraged to collaboratively discuss the results of the data analysis, fostering a culture of continuous improvement and shared responsibility for safety.
By documenting these findings and the rationale behind the proposed solutions, the organization can create a robust framework for ongoing evaluation and enhancement of safety measures. Through diligent data analysis, chemical plant employees can take significant strides towards identifying root causes and implementing effective strategies to mitigate risks in the workplace.
Human error is a significant contributor to incidents in chemical processing environments, often serving as a catalyst for failures that can lead to severe accidents
Understanding the role of human error requires a thorough examination of how operators interact with complex systems, the decision-making processes involved, and the environmental factors that influence behavior.
In many cases, human error is not merely a result of individual negligence but is rather a manifestation of systemic issues within the organization, including inadequate training, unclear procedures, and insufficient communication.
The factors leading to human error can be categorized into two main areas: active failures and latent conditions. Active failures are the unsafe acts committed by individuals, such as misjudgments during critical operations or lapses in attention. Latent conditions, on the other hand, are the underlying weaknesses in the system that create opportunities for active failures to occur. For example, poorly designed work processes or ineffective safety protocols may create an environment where human error is more likely Identifying these latent conditions is essential in the root cause analysis process, as it allows organizations to address the broader organizational and systemic issues that contribute to accidents.
Furthermore, the role of human error is closely linked to the concept of cognitive load, which refers to the total amount of mental effort being used in the working memory In high-stress environments like chemical plants, employees often face cognitive overload due to the complexity of tasks and the pressure to perform. This overload can impair decision-making and lead to mistakes. Implementing strategies to manage cognitive load, such as simplifying procedures, utilizing checklists, and encouraging regular breaks, can enhance operational safety and reduce the likelihood of errors
Training and continuous education play a critical role in mitigating human error by empowering employees with the knowledge and skills necessary to perform their tasks safely and effectively. Comprehensive training programs should not only cover technical skills but also emphasize the importance of situational awareness and decision-making under pressure Regular drills and simulations can help reinforce these skills and prepare employees to respond appropriately to unexpected situations. By fostering a culture of learning and improvement, organizations can reduce the incidence of human error and enhance overall safety.
Lastly, fostering an environment where employees feel comfortable reporting near misses and unsafe conditions is vital in understanding and mitigating human error Encouraging open communication and accountability allows organizations to learn from incidents and identify trends that may indicate systemic issues. This proactive approach to incident investigation not only enhances safety but also contributes to a more resilient organizational culture. By recognizing the role of human error and addressing its root causes, chemical processing facilities can create a safer working environment for all employees
Identifying human factors is a critical component of root cause analysis in chemical processing environments.
Human factors encompass the interactions between people, technology, and processes, and they play a significant role in the overall safety and efficiency of operations.
Understanding these factors is essential for chemical plant employees to prevent incidents and improve safety outcomes By systematically analyzing human factors, organizations can better identify underlying issues that contribute to accidents or near misses
One of the primary elements in identifying human factors is recognizing the influence of individual behavior on safety performance.
Employee actions can be affected by various factors including fatigue, stress, lack of training, and insufficient communication.
For instance, a worker under significant stress may overlook safety protocols or misinterpret critical information. Therefore, evaluating employee behavior in the context of these influences provides valuable insights into potential vulnerabilities within the safety system.
It is crucial for chemical plants to foster an environment where employees feel supported and are encouraged to communicate openly about challenges they face.
Another important aspect of human factors involves the design of work processes and environments. Poorly designed systems can lead to confusion, increased workload, and unintentional errors For example, if the layout of equipment is not intuitive, employees may struggle to follow standard operating procedures effectively.
Process safety can be significantly enhanced by involving employees in the design and evaluation of work processes. This participatory approach allows for the identification of potential hazards and the implementation of practical solutions based on firsthand experience
Training and competency are also vital in identifying human factors related to safety performance.
Comprehensive training programs that address not only technical skills but also behavioral and situational awareness can empower employees to make safer decisions Regular refresher courses and simulations can help maintain high levels of competency and readiness among staff
Moreover, organizations should consider adopting a just culture that promotes learning from mistakes rather than assigning blame, which encourages employees to report safety concerns without fear of reprisal
Finally, fostering a culture of continuous improvement is essential for identifying and addressing human factors in chemical processing environments. This involves regularly reviewing and refining processes, procedures, and training based on incident investigations and employee feedback.
Encouraging employees to actively participate in safety discussions and contribute to safety committees can lead to a more engaged workforce that prioritizes safety. By systematically identifying human factors and addressing them, chemical plants can significantly reduce the likelihood of incidents and enhance overall safety in their operations
Human error remains a significant factor in process safety incidents within chemical processing environments. To address this issue effectively, it is crucial to focus on the design of systems, procedures, and equipment that can mitigate the likelihood of errors occurring By understanding the principles of human factors engineering and applying them to the design processes, chemical plants can create environments that not only enhance safety but also improve overall operational efficiency.
An essential aspect of mitigating human error through design involves simplifying complex tasks When processes are streamlined and unnecessary steps are eliminated, employees can focus on critical activities without becoming overwhelmed This simplification can be achieved through clear, intuitive interfaces and controls that reduce cognitive load. For instance, employing standardized operating procedures and visual aids can help guide employees during their tasks, making it easier to follow protocols and reducing the chance of mistakes.
Another important design consideration is the implementation of fail-safes and redundancy By designing systems that can tolerate human error, chemical plants can prevent minor mistakes from escalating into major incidents. This may include the use of alarms, automatic shutdown systems, or interlocks that prevent unsafe operations. Such design features provide an additional layer of protection, ensuring that even if an error occurs, the consequences can be contained and managed effectively
Training and ongoing education are integral to the design approach aimed at mitigating human error. While effective design can reduce the chances of error, employees must also be equipped with the knowledge and skills necessary to operate systems safely Training programs should emphasize the importance of human factors and the role design plays in safety Regular drills and simulations can reinforce safe practices and encourage employees to engage critically with the systems they operate, fostering a culture of safety and accountability.
Finally, continuous feedback and improvement should be embedded in the design process. Engaging employees in discussions about their experiences and challenges can provide valuable insights into potential design flaws or areas for enhancement. Creating a feedback loop allows for the identification of recurring issues and the opportunity to implement design modifications that address these problems effectively By prioritizing employee input and fostering an environment of collaboration, chemical plants can enhance safety and reduce the likelihood of human error in their operations.
Creating effective action plans is a critical component of root cause analysis, especially within the context of chemical processing environments Action plans serve as a structured approach to address identified root causes of incidents and ensure that measures are put in place to prevent recurrence. A well-crafted action plan not only outlines the necessary steps for resolution but also assigns responsibilities, establishes timelines, and identifies required resources This clarity is essential for fostering accountability among team members and ensuring that corrective measures are implemented effectively. The first step in creating an effective action plan involves a thorough understanding of the incident being investigated Employees must review all relevant data, including incident reports, witness statements, and any existing safety protocols. This detailed examination will help in accurately identifying the root causes and contributing factors By involving multidisciplinary teams in this phase, the action plan can incorporate diverse perspectives and expertise, leading to more comprehensive solutions. Collaboration among different departments ensures that the plan addresses all potential implications across the facility
Once the root causes have been established, the next step is to develop specific, measurable, achievable, relevant, and timebound (SMART) objectives within the action plan Each objective should directly correlate with the identified root causes, ensuring that the planned actions will effectively mitigate risks. For example, if inadequate training was identified as a root cause, a specific objective might be to develop and implement a new training program within a defined timeframe By setting clear objectives, chemical plant employees can better track progress and measure the effectiveness of the implemented actions. In addition to outlining objectives, the action plan should designate responsible individuals or teams for each task Assigning clear ownership is essential for accountability and ensures that all team members understand their roles in the resolution process. This assignment should consider the expertise and availability of personnel to maintain efficiency Regular follow-ups should be scheduled to review progress, discuss challenges, and make necessary adjustments. This continuous engagement fosters a culture of safety and reinforces the importance of the action plan as a living document that evolves with ongoing operations
Finally, effective communication plays a vital role in the success of action plans All employees should be kept informed about the action plan's progress, changes, and outcomes. Engaging the workforce not only boosts morale but also encourages a safety-first mindset across the organization. It is important to solicit feedback and suggestions from employees at all levels, as they are often the first to identify potential issues and can provide valuable insights By ensuring that everyone is aligned with the action plan and its objectives, chemical processing environments can enhance their overall safety culture and reduce the likelihood of future incidents.
In the context of chemical processing, prioritizing recommendations following a root cause analysis (RCA) is critical to enhancing safety and preventing future incidents
Employees must understand that not all recommendations hold the same weight in terms of urgency and potential impact on safety. A systematic approach to prioritizing these recommendations allows for effective resource allocation and ensures that the most pressing safety concerns are addressed promptly. By focusing on high-priority recommendations, chemical plants can significantly reduce the likelihood of recurrence of similar incidents, thereby fostering a safer work environment
To effectively prioritize recommendations, it is essential to assess the risk associated with each identified root cause. This involves evaluating the likelihood of an incident occurring and the potential consequences should it happen. Recommendations that address high-risk factors, such as equipment failures or procedural inadequacies that could lead to catastrophic incidents, should be prioritized above those with lower risk profiles Utilizing a risk matrix can provide a visual representation of these risks, helping teams to categorize and prioritize recommendations based on both their likelihood and severity.
In addition to risk assessment, the feasibility of implementing each recommendation must also be considered. Some recommendations may require significant time, resources, or changes to existing processes, which could delay their implementation Evaluating the practicality of each recommendation allows teams to focus on those that can be executed efficiently and effectively. By balancing risk with feasibility, chemical processing facilities can develop a structured plan that addresses critical safety issues while also being realistic about the implementation timeline and resources available.
Moreover, involving a cross-functional team in the prioritization process can enhance the effectiveness of the recommendations. Collaboration between different departments, such as operations, maintenance, safety, and management, ensures that diverse perspectives are considered This inclusive approach not only aids in identifying the most impactful recommendations but also fosters a shared commitment to safety across the organization. Engaging various stakeholders can lead to a more comprehensive understanding of the challenges and potential barriers to implementing the recommendations.
Finally, it is vital to establish a followup mechanism to monitor the implementation of prioritized recommendations. Continuous evaluation and feedback loops allow chemical plants to assess the effectiveness of the actions taken and make necessary adjustments. Regular reviews of the status of recommendations help maintain momentum and ensure accountability within the organization This ongoing commitment to addressing root causes and implementing effective solutions is essential for cultivating a culture of safety and continuous improvement within chemical processing environments
Effective communication of findings and action plans is a critical component in the process safety incident investigation within chemical processing environments
When incidents occur, the primary goal is to identify the root causes and implement corrective actions that prevent recurrence.
Clear and concise communication ensures that all employees understand the findings and the steps necessary to enhance safety.
This communication must be tailored to diverse audiences within the plant, including management, operational staff, and safety personnel, to ensure that everyone is aligned in their understanding and response
The first step in communicating findings effectively is to develop a comprehensive report that summarizes the investigation's outcomes.
This report should include a detailed analysis of the incident, including the sequence of events, contributing factors, and root causes identified through methodologies such as the "5 Whys" or fishbone diagrams
It is essential to present this information in a straightforward manner, avoiding technical jargon that may confuse personnel not directly involved in the investigation. Visual aids, such as charts and graphs, can enhance understanding and retention of the information presented
Once the report is finalized, disseminating the findings to all relevant stakeholders is crucial. This can be achieved through meetings, presentations, or written communications, depending on the audience and the complexity of the findings.
Engaging employees in discussions about the findings fosters an environment of transparency and encourages feedback Employees should feel empowered to ask questions and express concerns, as their insights can provide additional context and may reveal overlooked aspects of the incident.
This collaborative approach not only enhances understanding but also promotes a culture of safety and continuous improvement
In addition to communicating findings, it is vital to outline the action plans that will be implemented as a result of the investigation. These action plans should be specific, measurable, achievable, relevant, and time-bound (SMART), ensuring that all employees know the steps being taken to mitigate future risks. Assigning responsibilities for each action item and establishing timelines for completion is essential to maintain accountability
Regular updates on the progress of these action plans should be communicated to all employees, reinforcing the organization's commitment to safety and demonstrating that lessons learned from incidents are being actively addressed.
Finally, evaluating the effectiveness of the communication strategy is essential for continuous improvement Gathering feedback from employees on the clarity and usefulness of the information shared can provide valuable insights into how communication processes can be enhanced.
Additionally, post-implementation reviews of the action plans will help determine their effectiveness in preventing similar incidents By fostering an environment where communication is prioritized, chemical processing environments can significantly improve their safety culture, leading to enhanced operational integrity and reduced risk of incidents.
Successful implementation of root cause analysis (RCA) in chemical processing environments requires a structured approach that integrates safety protocols into daily operations First and foremost, establishing a clear framework for RCA is essential This involves defining the scope of investigations, identifying key personnel responsible for conducting analyses, and outlining the necessary resources. Employees should be trained on the RCA process, emphasizing the importance of documenting findings and recommendations By fostering an understanding of the process among all team members, the organization can create a culture of accountability and proactive safety management
Incorporating a multidisciplinary team into the RCA process is critical for thorough investigations. Teams should consist of individuals with diverse expertise, including operations, maintenance, engineering, and safety This diversity enables the team to view incidents from multiple angles, leading to more comprehensive analyses Each member should contribute their unique perspective, ensuring that all potential causes are examined. Regular team meetings should be scheduled to discuss ongoing investigations and share insights from different areas of the plant, thereby enhancing overall safety awareness
Communication plays a pivotal role in the successful implementation of RCA strategies. Establishing clear communication channels among team members and across departments ensures that information regarding incidents is shared promptly and effectively Regular training sessions and workshops can help reinforce the importance of open dialogue and collaboration. Furthermore, utilizing digital tools and platforms can streamline communication, allowing teams to document findings and share updates in real-time This transparency fosters a greater sense of ownership among employees, encouraging them to actively participate in safety initiatives. Another essential strategy for effective implementation is the integration of RCA findings into the organization's safety management system. This involves developing actionable recommendations based on the analysis and ensuring that they are incorporated into standard operating procedures (SOPs) Employees must understand the relevance of these changes and how they contribute to overall safety. Furthermore, management should regularly review and update these procedures to reflect the latest findings and best practices, thereby reinforcing the commitment to continuous improvement in safety protocols
Finally, measuring the effectiveness of RCA implementation is vital for sustaining improvements in safety culture. This can be achieved through regular audits, reviews of incident trends, and employee feedback mechanisms. Establishing key performance indicators (KPIs) related to safety incidents and RCA outcomes provides a quantifiable means to assess progress. Recognizing and rewarding teams that demonstrate successful implementation of RCA strategies can further motivate employees to engage actively in safety initiatives By continuously evaluating and refining the RCA process, chemical plants can enhance their resilience against future incidents, ultimately safeguarding both personnel and the environment.
Monitoring and measuring effectiveness are critical components in the continuous improvement of safety protocols within chemical processing environments This subchapter emphasizes the importance of establishing robust metrics and monitoring systems to evaluate the effectiveness of root cause analysis (RCA) initiatives. By systematically tracking the outcomes of implemented safety measures, chemical plant employees can identify areas for further improvement, ensuring that safety standards evolve in response to new challenges and insights gained from past incidents A comprehensive approach to monitoring involves both qualitative and quantitative assessments. Quantitative measures might include tracking incident rates, near misses, and compliance with safety regulations, while qualitative assessments can involve employee feedback, safety culture surveys, and observations of safety practices on the shop floor Combining these methods provides a holistic view of safety performance, enabling teams to discern patterns and trends that may indicate the effectiveness of their RCA efforts Regularly scheduled evaluations of these metrics will help facilitate timely adjustments to safety protocols, ensuring that they remain relevant and effective.
In addition to tracking established metrics, it is essential to implement a feedback loop that incorporates lessons learned from previous incidents. This requires an open environment where employees feel empowered to share their insights and experiences regarding safety practices Encouraging discussions around RCA outcomes fosters a culture of continuous learning and improvement. When employees understand that their input is valued and leads to real change, they are more likely to engage in proactive safety behaviors and contribute to a safer workplace. Another vital aspect of measuring effectiveness is conducting periodic reviews of safety systems and procedures These reviews should analyze the implementation of corrective actions identified through RCA and assess whether they have successfully mitigated identified risks. By systematically evaluating these actions, chemical plants can ascertain whether the root causes have been effectively addressed or if further intervention is necessary. This iterative process not only enhances safety but also reinforces the commitment to a proactive safety culture within the organization
Ultimately, monitoring and measuring effectiveness in safety initiatives are ongoing processes that require dedication and engagement from all employees. By establishing clear metrics, fostering open communication, and conducting regular reviews, chemical plants can create a resilient safety culture that minimizes risks and enhances overall operational integrity. The commitment to continuous improvement in safety protocols is not only a regulatory requirement but also a moral obligation to ensure the well-being of employees, the community, and the environment in which they operate
Continuous improvement practices are essential in fostering a culture of safety within chemical processing environments. These practices focus on systematically enhancing processes, reducing risks, and optimizing operations to prevent incidents
By integrating continuous improvement into daily operations, chemical plants can create a proactive safety culture that prioritizes the identification and mitigation of hazards before they manifest as incidents
Emphasizing continuous improvement not only enhances safety but also promotes operational efficiency, making it a critical component of process safety management
One effective approach to continuous improvement is the implementation of the Plan-Do-Check-Act (PDCA) cycle. This iterative process encourages employees at all levels to engage in problem-solving and decision-making.
In the planning phase, teams identify safety issues and establish objectives.
During the "do" phase, solutions are implemented on a small scale to test their effectiveness.
The "check" phase involves evaluating the results against the objectives, and finally, the "act" phase entails standardizing successful practices or revising plans based on the evaluation.
This structured approach helps in embedding safety improvements into the organizational culture, ensuring that lessons learned from incidents are applied to prevent recurrence.
Another key practice in continuous improvement is the use of performance metrics and key performance indicators (KPIs) related to safety
By establishing clear metrics that track safety performance, chemical plants can identify trends and areas needing attention. Regularly reviewing these metrics allows teams to assess the effectiveness of existing safety measures and make informed decisions about necessary changes
Engaging employees in this process not only enhances their awareness of safety issues but also encourages a sense of ownership and accountability for safety outcomes. Metrics should be communicated transparently across all levels to ensure a unified commitment to ongoing safety improvements
Employee training and development play a crucial role in continuous improvement practices. Regular training sessions that focus on process safety, hazard recognition, and incident investigation equip employees with the knowledge and skills necessary to identify potential risks. Incorporating real-life case studies and lessons learned from past incidents into training programs can enhance understanding and retention
Furthermore, encouraging employees to participate in safety committees or improvement teams fosters collaboration and innovation. A well-trained workforce is better prepared to contribute to continuous improvement initiatives, leading to a safer working environment
Finally, fostering an open and communicative organizational culture is fundamental to successful continuous improvement practices. Employees should feel empowered to report safety concerns without fear of reprisal.
Establishing channels for anonymous reporting and conducting regular safety meetings can facilitate open dialogue about potential hazards and improvement opportunities.
Recognition programs that reward proactive safety behaviors further reinforce a culture of continuous improvement When employees are encouraged to participate actively in safety discussions and initiatives, the organization benefits from a wealth of insights and experiences that can drive meaningful change, ultimately enhancing safety in the chemical processing environment.
The analysis of historical incidents within chemical processing environments serves as a critical component in understanding the complexities and risks inherent in these operations By examining past events, employees can identify the factors that contributed to failures and mishaps, thereby gaining insights that are vital for preventing future occurrences. Historical incidents are not merely records of what went wrong; they provide a wealth of knowledge that can enhance safety protocols and improve overall operational reliability
One notable aspect of analyzing historical incidents is the identification of common patterns and root causes that often emerge Many incidents share similarities in terms of human factors, equipment failures, or procedural lapses. By systematically categorizing these incidents, employees can focus on trends that may suggest underlying systemic issues. For example, repeated failures in safety equipment or a high incidence of operator error may indicate a need for improved training programs or equipment maintenance schedules. This analytical approach allows for the development of targeted interventions.
Furthermore, studying past incidents fosters a culture of safety within the organization. When employees understand the historical context of safety failures, they are more likely to appreciate the significance of adhering to established protocols and guidelines
This cultural shift is essential for building a proactive safety environment where employees feel empowered to report unsafe conditions and suggest improvements Engaging in discussions about historical incidents can also enhance teamwork and communication, as employees collaborate to draw lessons from the past and apply them to current practices.
The role of regulatory agencies and industry standards in shaping the analysis of historical incidents cannot be understated. These entities often compile data from various incidents, providing benchmarks and guidelines that facilities can use to assess their own performance Employees should familiarize themselves with these resources, as they offer invaluable insights into industrywide challenges and best practices. By aligning internal safety measures with external standards, chemical plants can enhance their credibility and commitment to safety
Finally, the continuous analysis of historical incidents should be integrated into the broader framework of process safety management. This involves not only the investigation of past events but also the implementation of findings into everyday operations. Employees should be encouraged to participate in regular safety audits and reviews, ensuring that lessons learned are documented and disseminated throughout the organization This ongoing commitment to learning from historical incidents is crucial in fostering an adaptive safety culture that prioritizes the wellbeing of all employees and the integrity of the chemical processing environment.
In the realm of chemical processing, case studies serve as invaluable resources for understanding the intricacies of process safety and the implications of incidents that have occurred in the industry By examining these specific instances, employees can identify patterns and underlying factors that contribute to safety failures. Each case study presents a unique set of circumstances, yet common themes often emerge, revealing critical lessons that can be applied to enhance safety practices within their own operations
One key lesson learned from various case studies is the importance of thorough root cause analysis Incidents often arise from a complex interplay of technical, human, and organizational factors rather than a single cause. Employees must be trained to look beyond immediate symptoms and investigate deeper systemic issues. For example, a case study involving an explosion in a chemical plant highlighted that inadequate training and communication breakdowns were significant contributors to the incident This realization emphasizes the need for a culture of continuous improvement in training programs and communication strategies to prevent future occurrences.
Another critical takeaway from these case studies is the necessity of robust risk assessment processes. Organizations must regularly evaluate potential hazards associated with their operations and implement effective controls In one notable incident, a failure to recognize the potential for a chemical reaction led to catastrophic results This underscores the need for employees to actively participate in risk assessments and contribute their insights, as those working directly with processes often have the most relevant knowledge to identify potential risks and suggest improvements.
Moreover, the importance of fostering a safety-centric organizational culture cannot be overstated. Many case studies reveal that organizations with strong safety cultures tend to experience fewer incidents. Employees should feel empowered to report unsafe conditions and participate in safety discussions without fear of reprisal. For instance, in a case study where a nearmiss incident was reported, it became clear that open communication among staff led to the timely identification of safety issues, allowing for prompt corrective actions. Establishing trust and transparency within the workforce is essential for cultivating a proactive approach to safety.
Finally, the role of leadership in promoting safety is a recurring theme in case studies. Effective leadership is instrumental in establishing priorities around safety and ensuring that resources are allocated to support safety initiatives Leaders who visibly prioritize safety through their actions and decisions encourage a similar commitment among employees. A case study involving a leadership-driven safety initiative demonstrated a marked reduction in incidents, illustrating the profound impact that dedicated leadership can have on safety outcomes.
By learning from these cases, chemical plant employees can contribute to creating a safer work environment by embracing the lessons learned and implementing them in their daily operations
Root Cause Analysis (RCA) serves as a fundamental tool in enhancing safety within chemical processing environments. In realworld applications, RCA provides a structured approach to identifying underlying issues that lead to incidents, thereby enabling the development of effective corrective actions.
For chemical plants, where the stakes are particularly high, the application of RCA can significantly reduce the likelihood of future incidents, contributing to a safer workplace and improved operational efficiency
One notable scenario illustrating the application of RCA involved a significant chemical spill that occurred during the transfer of hazardous materials
Upon investigation, the RCA team employed the "5 Whys" technique to trace the incident back to its origin. Initial responses indicated that the spill was due to operator error; however, further questioning revealed that the operator had not received adequate training on the new equipment.
This insight prompted the implementation of a comprehensive training program, which not only addressed the immediate gap but also established a continuous education framework for all operators, effectively mitigating the risk of similar incidents.
Another practical example can be found in a case where equipment failure led to an unexpected shutdown of a critical process unit. The RCA team utilized a fishbone diagram to categorize potential causes, examining factors such as equipment design, maintenance practices, and operational procedures
This structured analysis revealed that a lack of regular maintenance checks had contributed to the failure. As a result, the plant implemented a revised maintenance schedule, integrating predictive maintenance techniques that improved equipment reliability and reduced unplanned downtimes.
In instances where human factors contribute to safety incidents, RCA plays a crucial role in understanding the interplay between personnel behavior and operational protocols. A case where a near-miss incident occurred due to inadequate communication between shift changes illustrated this point.
The RCA process highlighted the absence of standardized communication protocols, leading to misunderstandings about critical safety procedures. The corrective action involved developing a formal handover checklist that ensured all pertinent information was communicated effectively, thus fostering a culture of safety and accountability among employees
Ultimately, the application of Root Cause Analysis in chemical processing environments not only identifies immediate corrective actions but also promotes a proactive safety culture. By systematically addressing the root causes of incidents, chemical plants can enhance their safety protocols, improve employee engagement, and ensure compliance with regulatory standards
The continuous application of RCA fosters an environment where safety is prioritized, ultimately leading to more resilient operations and a stronger commitment to the well-being of all employees and the surrounding community.
Root cause analysis (RCA) serves as a foundational component in enhancing safety within chemical processing environments. It is a systematic approach designed to identify the underlying factors that contribute to incidents, allowing organizations to develop effective preventive measures By delving beyond immediate causes, RCA emphasizes the importance of understanding how various elements within the system interact and contribute to an incident. This holistic perspective is crucial for chemical plants, where complex processes and interdependent systems can lead to significant safety risks if not properly managed.
A key concept in RCA is the distinction between proximate and root causes
Proximate causes refer to the immediate reasons for an incident, such as equipment failure or human error. In contrast, root causes are the deeper, often systemic issues that allow these proximate causes to occur. Identifying root causes requires a thorough investigation that considers organizational processes, safety culture, training deficiencies, and equipment maintenance practices This distinction is essential for chemical plant employees, as addressing only proximate causes may result in recurring incidents and a false sense of security
Another important concept is the use of various analytical tools and techniques to facilitate RCA. Techniques such as the "5 Whys," fishbone diagrams, and fault tree analysis provide structured methods for dissecting incidents and uncovering root causes Each tool offers unique insights and can be tailored to the specific context of chemical processing environments. Employees should be trained in these methodologies to ensure a consistent and effective approach to incident investigations. Utilizing these tools not only enhances the accuracy of the analysis but also fosters a collaborative environment where employees feel empowered to contribute to safety improvements.
The role of organizational culture in RCA cannot be overstated A strong safety culture encourages open communication, reporting of near misses, and proactive engagement in safety practices. Employees at all levels must feel comfortable sharing information without fear of reprisal This cultural aspect is vital in ensuring that root causes are accurately identified and addressed. Chemical plants that prioritize a robust safety culture are more likely to implement successful RCA processes, leading to improved incident prevention strategies and overall workplace safety
Finally, the implementation of findings from RCA is critical for achieving lasting safety improvements. After identifying root causes, it is essential to develop and implement action plans that address these issues This may involve changes to policies, enhanced training programs, or upgrades to equipment and technology. Follow-up evaluations should be conducted to assess the effectiveness of these interventions.
Continuous improvement should be the goal, as safety in chemical processing environments is an ongoing endeavor that requires vigilance, adaptability, and a commitment to learning from past incidents. By embracing these key concepts, chemical plants can create safer working environments and reduce the likelihood of future incidents
The future of process safety in chemical processing environments is poised for transformative advancements driven by technological innovations, regulatory changes, and an evolving safety culture As industries grapple with complex safety challenges, there is a growing recognition of the need for robust frameworks that not only address current risks but also anticipate future threats
The integration of advanced technologies such as artificial intelligence, machine learning, and big data analytics is becoming paramount in enhancing predictive capabilities and improving incident response strategies
One significant trend in process safety is the increased reliance on data-driven decision-making. The collection and analysis of real-time data from various operations can lead to more informed choices regarding safety protocols and risk management.
By utilizing sophisticated algorithms and predictive modeling, companies can identify potential hazards before they escalate into serious incidents This proactive approach not only minimizes risks but also fosters a culture of continuous improvement, where employees are encouraged to engage in safety practices actively.
Furthermore, the implementation of automation and digital tools is reshaping the landscape of process safety Automated systems can monitor critical parameters and execute safety measures without human intervention, thereby reducing the likelihood of human error.
Additionally, simulation technologies allow teams to practice responses to hypothetical scenarios, enhancing preparedness for real-world incidents As these technologies evolve, the role of employees will also shift, emphasizing the importance of adaptability and ongoing training to effectively collaborate with these systems.
Regulatory frameworks are also evolving to reflect the changing dynamics of process safety. As regulatory bodies establish more stringent guidelines and standards, chemical plants must stay ahead by not only complying with these regulations but also embracing best practices that go beyond mere compliance.
This can involve adopting a holistic approach to safety management that integrates process safety with operational excellence, fostering a culture where safety is viewed as a critical component of overall performance.
Finally, the future of process safety will heavily rely on collaboration among industry stakeholders. Sharing best practices, lessons learned from incidents, and insights gained from investigations will enhance collective knowledge and drive innovation
By fostering partnerships across the industry, organizations can develop comprehensive strategies that address common challenges and elevate the overall safety standards within the chemical processing sector
Emphasizing collaboration will not only strengthen individual organizations but also contribute to a safer environment for all employees involved in chemical processing activities.
Encouraging a safety culture in chemical plants is vital for minimizing risks and enhancing the overall safety of operations. A robust safety culture encompasses shared values, beliefs, and practices that prioritize safety at all levels of the organization
It is essential for employees to understand that safety is not merely a set of rules to follow but a fundamental aspect of their work environment.
By fostering an atmosphere where safety is everyone ’ s responsibility, chemical plants can significantly reduce the likelihood of incidents and ensure a proactive approach to risk management
Leadership plays a crucial role in establishing and maintaining a safety culture. Management must demonstrate a commitment to safety through their actions and decisions This includes providing the necessary resources for safety training, implementing effective communication strategies, and encouraging employee participation in safety initiatives.
When leaders visibly prioritize safety, it sets a standard for all employees, reinforcing the notion that safety is integral to the company ’ s mission and values.
Engaging leaders in regular safety discussions can also reinforce their commitment and create a more open environment for addressing safety concerns.
Employee involvement is equally important in cultivating a safety culture Encouraging employees to participate in safety meetings, hazard assessments, and incident investigations helps create a sense of ownership and accountability.
When employees feel empowered to voice their concerns and contribute to safety discussions, they are more likely to identify potential risks and suggest improvements Moreover, recognizing and rewarding safe behavior can further motivate employees to prioritize safety in their daily tasks. This collaborative approach to safety not only enhances awareness but also fosters teamwork and communication among staff.
Training and education are essential components of a strong safety culture Regular training sessions should be conducted to ensure that all employees are knowledgeable about safety protocols, emergency procedures, and the specific hazards associated with their roles.
These training programs should be interactive and engaging, allowing employees to practice their skills in real-world scenarios. Continual learning opportunities, such as workshops and safety drills, reinforce the importance of safety and keep it at the forefront of employees' minds. A well-informed workforce is better equipped to recognize hazards and respond effectively to incidents
Finally, it is vital to establish a feedback loop that allows for continuous improvement in safety practices. Implementing a system for reporting near misses, unsafe conditions, or suggestions for safety enhancements encourages open dialogue about safety issues. Regularly reviewing incident reports and safety performance metrics can identify trends and areas for improvement
This data-driven approach not only helps to prevent future incidents but also demonstrates to employees that their input is valued and that the organization is committed to evolving its safety culture. By prioritizing these elements, chemical plants can create an environment where safety is embedded in every aspect of operations, ultimately leading to a safer workplace for all employees