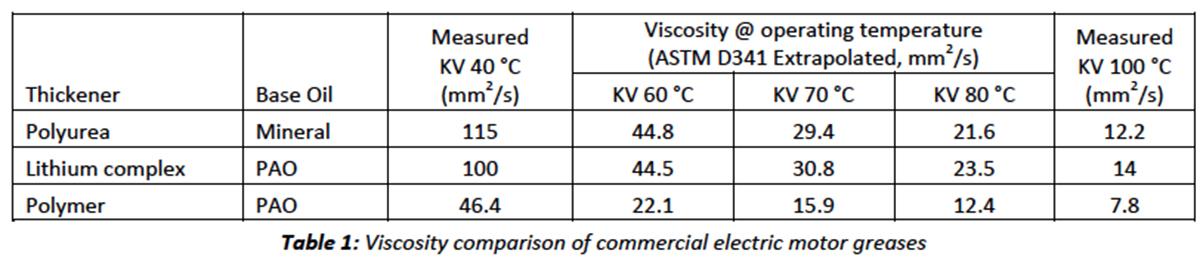
24 minute read
Development of Next Generation Electrical Motor Greases Offering Improved Frictional Characteristics
Development of Next Generation Electrical Motor Greases
Offering imprOved frictiOnal characteristics
John J. Lorimor1, Mihir Patel2, Brian Stunkel2, Rob Heverly2
1Axel Americas LLC • Kansas City, MO 2Vanderbilt Chemicals LLC • Norwalk, CT
ABSTRACT
The global recession and resulting decline in commodity prices have caused the mining industry to increasingly focus on energy efficiency measures. Electric motors are used extensively in every facet of mining including excavation, mineral preparation and material transfer, but energy efficiency gains in these motors through specific selection of lubricating grease have not been widely promoted.
Bearing grease exhibiting low friction performance may reduce energy consumption in electrical motors compared to grease offering the standard frictional performance. Novel grease thickeners based upon polymers have shown improvements in many functional areas over conventional grease thickener types, including low-friction performance.
The objective of this project is to characterize and improve upon the frictional performance of common commercially available electric motor greases. Once benchmarked, the work will focus upon the evaluation and use of friction reducing additive chemistries to develop novel polymer based grease formulations offering improved frictional performance. Experimental greases will be evaluated in both conventional bench testing and actual field trial versus their commercial counterparts as a potential new low-friction option for electric motor service. The results of experimentation and field trial will be discussed in detail.
INTRODUCTION
According to the International Energy Agency [1], electrical motors account for 45% of global electricity consumption. The efficiency of an electric motor can only be improved through a reduction in motor losses. Motor designs have improved resulting in energy efficiency gains, but grease selection specifically for energy savings potential has not been widely promoted. Grease components can be broken down into three major groups; base fluid, thickener, and additives. Energy efficient greases must have a designed approach to their formulation. In this designed approach, each component of the grease must be selected specifically for its ability to provide improvements in one of the three lubrication related conditions which influence energy efficiency. These three lubrication related conditions are churn, traction and friction.
Churn
The first lubrication related condition influencing energy efficiency in a mechanical system is churn under hydrodynamic lubrication. Under full-film lubrication, the surfaces are completely separated by lubricant film.
Energy is required to move mechanical parts (gears, bearing elements, etc.) through the lubricant medium. Churn is energy loss caused by the movement of these mechanical parts through the grease, and this energy loss is a function of the grease’s overall consistency and base oil viscosity.
Heavy grease consistency is a function of high thickener content, and is usually described as a beneficial characteristic in bearing lubrication. An example of this benefit is improved stay-in-place performance, providing a better seal to prevent contaminant ingress. Additionally, heavy grease consistency provides for a reserve of grease thickener that is gradually degraded during service, improving long term mechanical stability. In the formulation of energy efficient greases, the thickener type and amount needs to be carefully controlled to reduce churning losses in the formulation of energy efficient greases.
Polymer thickened grease compositions have been well described in the literature [2, 3, 4]. Leckner describes the polymer thickener as fundamentally different in its lubrication mechanism compared to regular soap based greases. Polymer thickeners have allowed the use of significantly different base oil viscosities compared to what is possible with soap based grease. Reducing viscosity can reduce churning losses. In his paper presented at ELGI, the energy savings obtained through the use of polymer thickened greases and reduced oil viscosity were described in detail through actual end user case studies.
During operation, churning losses can also be attributed to oxidative thickening of the grease components. In most cases, thickening and polymerization of conventional grease components exposed to high-temperatures results in an increased overall grease consistency. However, Polymer thickened greases have exhibited softening under these same circumstances. The theory of this mechanism is explained by Leckner to be the result of two opposing effects: As base fluid components oxidize and polymerize, the polymer thickener components slowly degrade into the lubricating fluid under high temperature exposure. This reduction in overall thickener content and consistency offsets the grease thickening effect of oxidation. This explanation was confirmed in testing by Westbroek, where aged conventional soap based grease became harder, while the consistency of polymer grease became softer. This influences the duration of the churning reducing effect, and improves the longevity of energy savings benefits.
A recent trend in the automotive segment for improving mechanical system efficiency has been to reduce the viscosity of the lubricant. Lower viscosity fluids seem to be more appropriate for energy efficiency because of the reduced churning losses. Unfortunately by reducing the viscosity, this also results in a thinner film and a move toward boundary lubrication and a potential increase in component wear. Under these conditions, grease will experience a high degree of shear and the thickener can be degraded. The degradation products of soap based greases do not actually participate in improving the fluid viscosity. However, polymer based greases have demonstrated the unique characteristic in that these degradation products can be absorbed into the lubricating fluid where they do contribute to improved fluid film thickness.
In general, the goal of bearing lubrication is to provide the minimum viscosity required at the expected operating temperature. At operating temperature, this minimum viscosity for proper lubrication of ball bearings has been determined by one manufacturer to be 13 mm2/s [5]. For most electric motors, the typical bearing operating temperature falls somewhere within the range of 60 °C to 80 °C [6]. Within this range, the typical electric motor grease provides a base oil viscosity
that is significantly higher than what is required for proper lubrication. The table below compares the base fluid viscosity of commercial electric motor greases, and calculates their actual viscosity under various operating temperature conditions.
When comparing two greases formulated with different base oil viscosity, the churning losses would be expected to be higher for the higher viscosity fluid. These increased churning energy losses would then manifest as heat. In this comparison the result should indicate that, all other properties being identical, the bearing lubricated with grease of higher base fluid viscosity will run at a higher temperature than a grease with a lower base fluid viscosity. Higher temperature exposure leads to faster grease degradation and a shorter grease life, in which case the lower base fluid viscosity can promote a longer grease life.
Traction
The second source of energy losses is traction under elastohydrodynamic lubrication (EHL) conditions. In this case, shearing in the EHL contact causes energy losses associated with the internal resistance of the lubricant to shearing. Under conditions of EHL contact, energy is required to shear the lubricant film between the sliding surfaces. Traction coefficient is a measure of this energy. The lower the traction coefficient, the less energy it takes to shear the lubricant film. Traction coefficient depends upon the molecular type and shape of each lubricant component. Traction is primarily a property of the lubricant’s base oil. It is generally not affected by additives; nor is it related to metal-metal contact. Since energy losses in lubrication are typically manifested as heat, traction behavior may be one indicator of operating temperatures in certain applications.
In the search for reduced energy loss potential, the type of base oil used in a grease formulation is therefore an important consideration. PAO’s have long been known for their reduced traction. Vinci [7] demonstrates that comparative traction profiles offer guidance in energy efficient base fluid selection, illustrating that at the same viscosity PAO offers a much lower traction profile compared to Group I and II base oils.
Traction coefficient can also be measured and used to differentiate the energy loss potential between greases. In recent work [8], polymer thickened greases have demonstrated the ability to achieve very low traction coefficients compared to lithium and lithium complex grease thickeners.
Friction
The final condition influencing energy efficiency in a mechanical system is friction under boundary or mixed lubrication conditions. In this condition, the lubricant film is not thick enough to fully separate surfaces. Under boundary and mixed lubrication conditions, metalto-metal contact occurs as surfaces slide by each other leading to friction and energy loss. Friction is a significant source of energy loss in mechanical systems, and all lubricants offer some degree of friction reduction. Energy efficient lubricants are differentiated from conventional lubricants in the degree of friction reduction observed.
When energy in a mechanical system is lost to friction, it typically is characterized by its conversion to heat. As a result, systems operating with increased friction are typically operating at an increased temperature, when compared to energy efficient lubricants. An increase in bearing temperatures means that the lubricant viscosity is lowered and film formation is made more difficult, leading to even higher friction and compounding further temperature increases [5]. High temperature exposure can also lead to
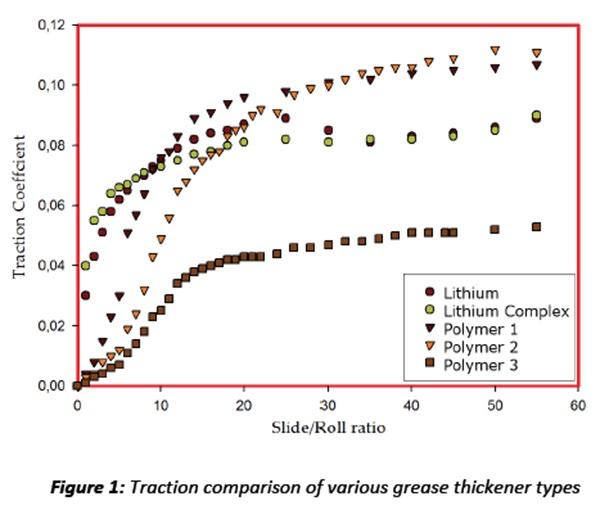
evaporation and oxidative thickening of the grease’s base oil component, and a resulting reduction in the amount of oil bleed that provides lubrication. As lubrication starvation occurs, the lubrication film thickness will decrease, resulting in increased friction. The increased friction creates more heat. [6]
Low friction grease can Influence the operating temperature of a bearing by reducing frictional heat generation. By lowering the operating temperature several additional benefits also occur. Grease degradation is commonly a major cause of premature bearing failure. As grease life is shortened by exposure to high temperatures, the grease can last significantly longer at reduced operating temperatures, promoting longer component life.
Experimental formulation
In designing energy efficient greases, the key to lubricant performance is a balanced formulation in which the energy loss reducing potential of each component is the selection criteria. We believe that by targeting the three lubrication conditions influencing energy losses, we can positively influence the energy consumption in an electric motor bearing application.
Thickener:
Polymer thickened greases are based upon four major components; base oil, polypropylene, elastomer/rubber and additives. The benefits of polymer thickened greases have been well documented [2] and include: • Non-ionic thickener system • Very good oxidation resistance • Excellent water resistance • Excellent resistance against process water, acidic and alkali solutions • Controlled oil bleeding • Long life • Mechanically stable • Good compatibility property with almost all greases • Recommended application temperature up to 120 °C
In a recent presentation at the ELGI [4] , Westbroek explained how polymer thickened greases have many qualities which make them very suitable for bearing lubrication, especially controlled oil release properties. In a rheometer equipped with rolling bearing assembly, Westbroek subjected commercially available test greases to a series of high temperature tests, including oil separation from a greased bearing. In his experiments, Westbroek identified oil loss having a significant role in the process causing bearing failure. Through this work he discovered that polymer thickened greases have a very controlled oil release, and are superior to the other thickener types tested.
Greases for electric motor bearing lubrication must be capable of maintaining their consistency even when subjected to the continuous rolling action of bearing elements. The polymer thickener provides a very shear stable structure, excellent grease life, controlled oil release properties, and outstanding low friction properties.
Base oil:
Based upon the known improved traction performance of the PAO fluids, and the operating viscosity requirements published by the major bearing manufacturers, an 8 mm2/s @ 100 °C viscosity PAO base fluid was selected for use in the experimental low friction grease formulation.
Additives:
In his paper at ELGI [9], Fish indicates that of the three major grease components, base oil, thickener and additives, each have different effects on grease performance, and that the additives were primarily responsible for friction reduction. Accordingly, we identified SRV® coefficient of friction within the operating temperature range as a key screening mechanism for these additive formulations. A discussion of the friction reducing additive chemistry is found in the results of experimentation. Greases emerging favorably from our screening program would then be considered for electric motor temperature and efficiency testing.
Reference Greases
The current state of the art grease technology has many differences when compared with novel blends based upon a unique polymer thickener. In order to demonstrate differences in energy efficiency between the author’s experimental grease formulation and the current products in service, reference greases were selected that were most representative of the electric motor grease technology in use today. The most common types of greases employed in electric motor bearing lubrication
are based upon the lithium complex and polyurea thickener types. These two grease thickeners are mechanically stable, and capable of resisting softening even upon exposure to elevated temperatures. In addition, they are typically formulated with antiwear, oxidation and corrosion inhibiting additives, to address the major performance requirements of the application.
As references in our testing program, we selected the following (Table 2) widely used commercial electric motor greases, each unique in their base fluid and additive systems. The mineral-based polyurea formulation is widely used for electric motor applications. The synthetic lithium complex grease is a formula recognized for reducing operating temperatures by utilizing a low friction additive system.
EXPERIMENTAL TECHNIQUE
In this work, the three different base greases were studied in rolling/sliding contacts. A standard mini traction machine (MTM) was used to measure rolling/ sliding friction. MTM uses two different motors to independently control different speed of upper and lower specimen thereby apply any slide/roll ratio for the experiments. The machine is computer controlled so that any required test routine can easily be programmed. Before the experiments both specimens (ball and disc) were cleaned thoroughly using n-heptane. A new ball and disc were used for each test, both of AISI 52100 steel. The root mean square (r.m.s.) roughness of the balls was 10 nm and their hardness 750 VPN. Smooth discs of 5 nm r.m.s. were employed with a hardness of 780 VPN. Rig was assembled and lubricant pot is filled with sufficient amount of grease. The applied load was 35N, corresponding to a Hertzian pressure of 1 GPa. Temperature was raised to 40 °C. Tests begin at entrainment speed of 3000 mm/s and end at 10 mm/s at specified intervals. The slide/roll ratio (SRR) was 50 percent. Slide-roll ratio is defined as the ratio of sliding speed to ub-ud mean speed, where ub and ud are speed
A comparison of the performance of each grease sample can be made by integrating the area under each Stribeck curve. The value of this integral, Traction CoF.log (u), is known as the Stribeck Friction Coefficient (SFC). Lower values of SFC indicate that less energy will be absorbed by the lubricant under mixed and boundary regimes. Lower values would therefore be expected to correlate with better performance in reducing frictional losses.
RESULTS AND DISCUSSION
The frictional property of polymer thickened grease was compared with two greases; LiCx-PAO and PU-Min using Mini Traction Machine (MTM) as shown in Figure 2. Typical Stribeck curves were generated at 50% slide-roll ratio where friction is measured over a range of entrainment speeds at a temperature of 40 °C. As the test time progresses friction increases when entrainment speed decreases for all three grease samples at 40 °C. The polymer thickened grease had the lowest coefficient of friction at all entrainment speeds compared to both greases LiCx-PAO and PU-Min. At a lower speed and a higher temperature, the Stribeck curve operates under boundary lubrication regime where an increased number of asperity to asperity contact occurs which leads to higher possibilities of wear and friction. However, a reduction in friction in the boundary lubrication regime indicates the formation of a friction reducing film by polymer thickened grease.
To understand the frictional performance at higher temperatures, Stribeck curves were also acquired at 120 °C for all three greases using similar test conditions mentioned above. As shown in figure 3, the Stribeck curve demonstrates noticeably different frictional behavior at 120 °C. Grease PU-Min exhibited higher
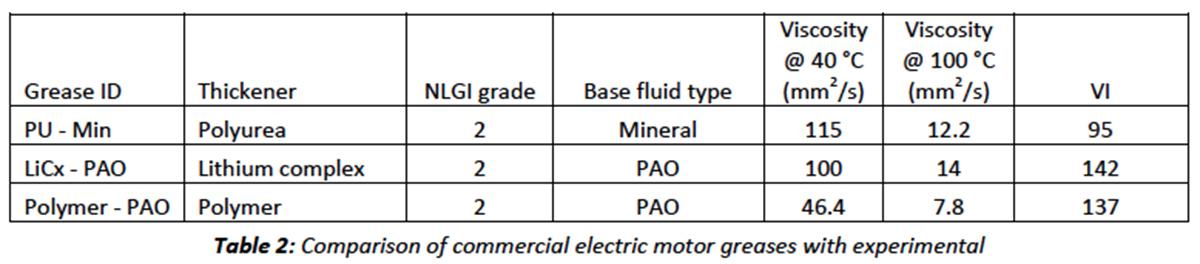
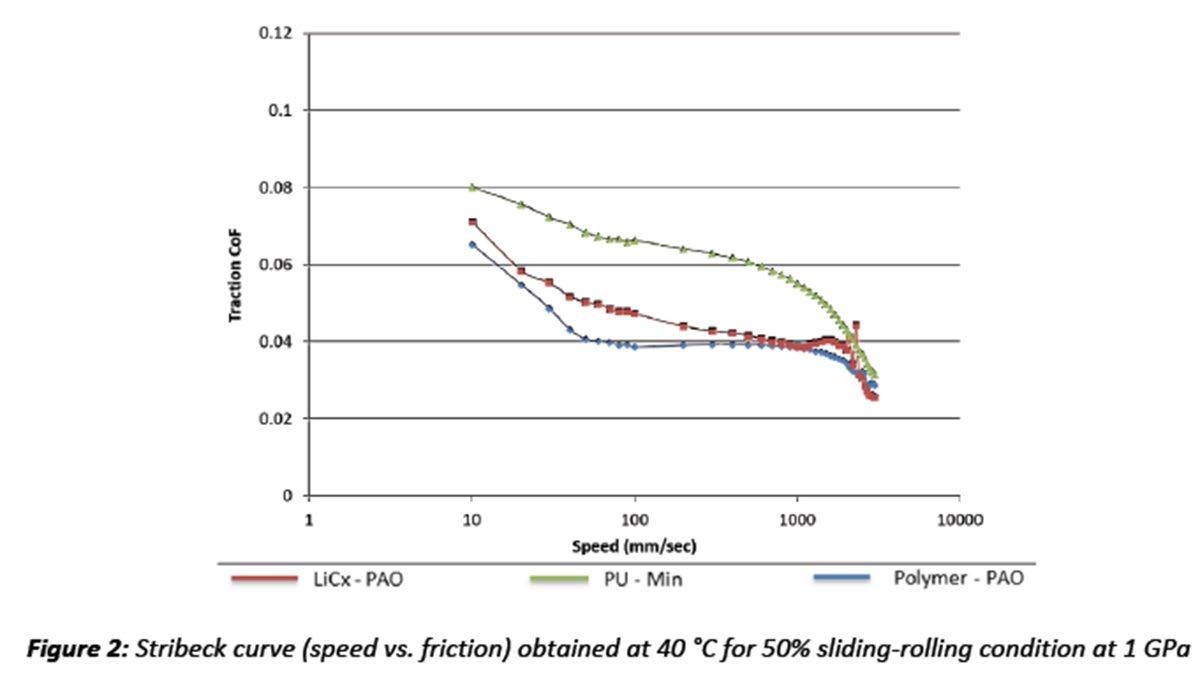
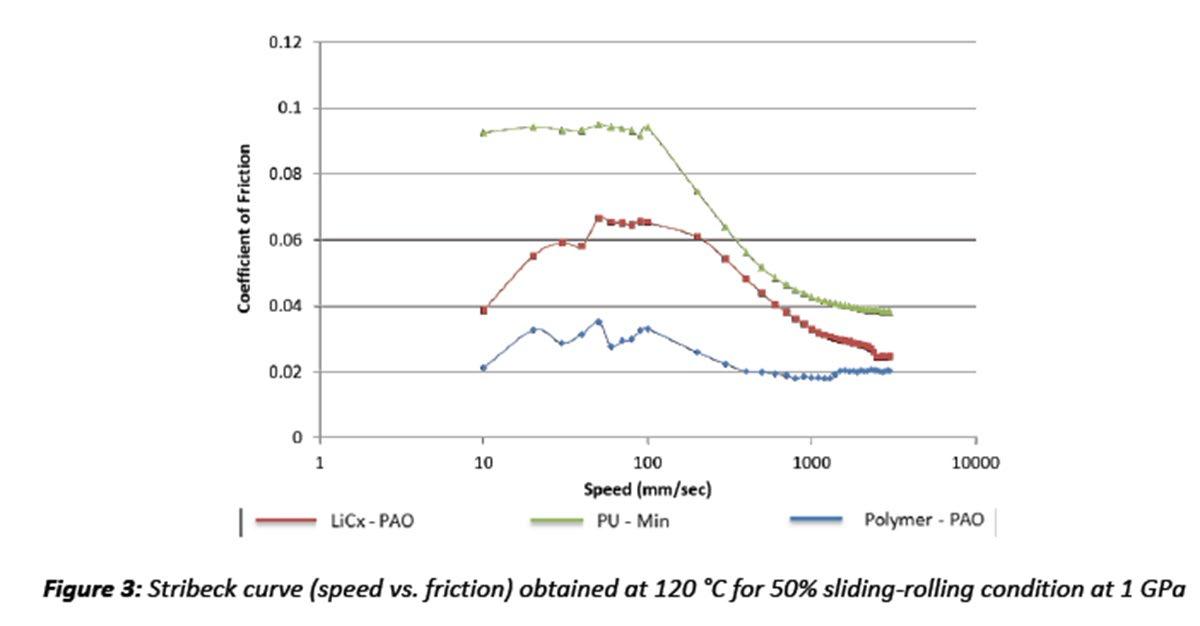
friction at 120 °C than at 40°C. Grease LiCx- PAO exhibited lower friction coefficient than grease PU-Min. On the other hand, polymer thickened grease exhibits lower friction coefficient at higher temperature of 120 °C than at 40 °C. All grease systems show different friction coefficients at different entrainment speeds; they also show downward trends or reduction in friction at lower speed.
Influence of Temperature on Frictional Energy Consumption
Stribeck friction coefficient (SFC) was calculated by computing the area under the Stribeck curve. Lower values of SFC indicate that less energy will be absorbed by the lubricant under mixed and boundary regimes. Lower values would therefore be expected to correlate with better performance in reducing frictional losses. SFC values were calculated for the curves acquired at 40 °C, 60 °C, 80 °C, 100 °C, 120 °C and plotted as shown in figure 4.
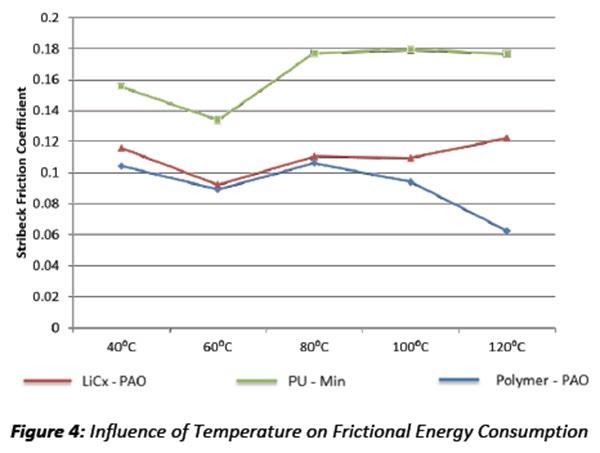
Figure 4 shows area under the Stribeck curve as a function of temperature. SFC values of grease PU-Min reduces as temperature increases from 40 °C to 60 °C. SFC value increases at 80°C and then stabilizes with higher temperature. Grease LiCx-PAO shows reduction in SFC values, followed by continuous increased in the SFC values. Polymer thickened grease exhibits reduction in SFC values at 60 °C, followed by increase at 80 °C. With further increases in the temperature, SFC values generated using polymer thickened grease exhibits continuous reduction in the SFC values.
Results indicate that greases LiCx-PAO and PU-Min consume different frictional energy with increasing temperature. Grease PU-Min seems to consume higher frictional energy during the test compared to grease LiCx-PAO. The polymer thickened grease shows lowest frictional energy consumption at all the temperatures. While after 80 °C, grease PU-Min maintained higher energy consumption while the polymer thickened grease exhibited reduction in the frictional energy consumption.
SRV® Testing
For some applications, particularly when studying the behavior of a lubricant under dynamic conditions, an oscillating motion is more representative than a continuously rotating disc. An SRV®3 test system from Optimal Instruments was used to measure friction and wear under pure sliding, boundary lubrication conditions. In this test, a 10.0 mm diameter steel ball is loaded downwards on the flat face of cylindrical disc. The disc is held stationary and ball reciprocates at given test frequency. The ball and disc are both of AISI 52100 steel. The ball is 10 mm diameter with a Rockwell hardness number of 60±2 on Rockwell C scale (HRC), 0.025±0.005-µm Ra surface finish. The lower disc (24-mmx7.85mm thick) is of the same hardness as the ball but with a surface finish between 0.5µm˂Rz˂0.650µm. The applied load was 50 N for 30 seconds as a break-in period followed by 200N for the duration of 2 hours. Ball was oscillating at 50 Hz for 1000µm stroke. Tests were conducted at 40 °C or 80 °C. Final coefficient of friction values were reported. Wear volume was measured using optical profilometer.
In this study, efforts were made to improve friction reduction and wear resistance properties of polymer thickened grease. A combinatorial approach using molybdenum friction modifier, sulfur chemistry and phosphorus chemistry were used to improve friction reduction and wear resistance.
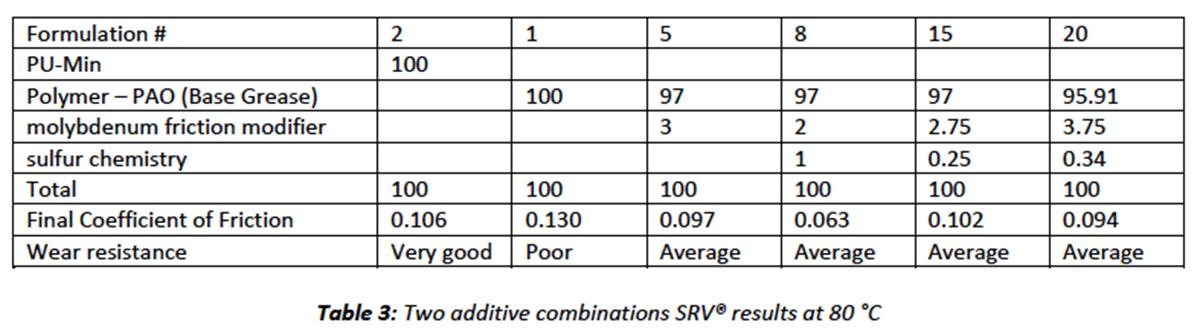
Grease formulations were prepared as shown in table above. All the tests were conducted at 80 °C. The base grease by itself shows very high friction and poor wear resistance in the pure sliding and reciprocating motion compared to polyurea based grease PU-Min. Formulation 5 shows the influence of the molybdenum friction modifier alone at 3.0 wt. %. Formulations 8 and 15 show the influence of sulfur chemistry maintaining 3.0 wt. % treat rate. Comparison of formulation 5, 8 and 15 indicates that addition of antiwear and friction modification improves both the friction and wear resistance performance of polymer thickened base grease over the base grease. Addition of molybdenum friction modifier at 3 wt. % (formulation 5) improved the friction reduction performance of polymer thickened base grease compared to poly urea based grease PU-Min but further improvement is needed to reduce wear compared to poly urea grease. Addition of sulfur chemistry at 1 wt. % while maintaining total treat rate of 3 wt. % (formulation 8) further improved the friction reduction properties compared to formulation 5 and polyurea base grease but antiwear properties deteriorate. Adjusting the treat rate of the combination of molybdenum friction modifier and sulfur chemistry does not exhibit significant improvement. Phosphorus chemistry was added to improve the antiwear properties of the two additive combination of molybdenum friction modifier and sulfur chemistry as shown in the table below.
As exhibited by formulation 24, addition of phosphorus chemistry maintains friction reduction properties of two way combination of molybdenum friction modifier and sulfur chemistry but further deteriorates the wear resistance properties. This phenomenon probably can be explained in terms of competition of additive for surface adsorption and hence formulations were further optimized by reducing treat rate of molybdenum friction modifier, i.e. formulation 27 and 28. Reduction in the molybdenum friction modifier treat rate and addition of phosphorus chemistry as antiwear shows significant improvement in the friction reduction compared to polymer thickened and polyurea base grease. This phenomenon probably can be explained in terms of competition of
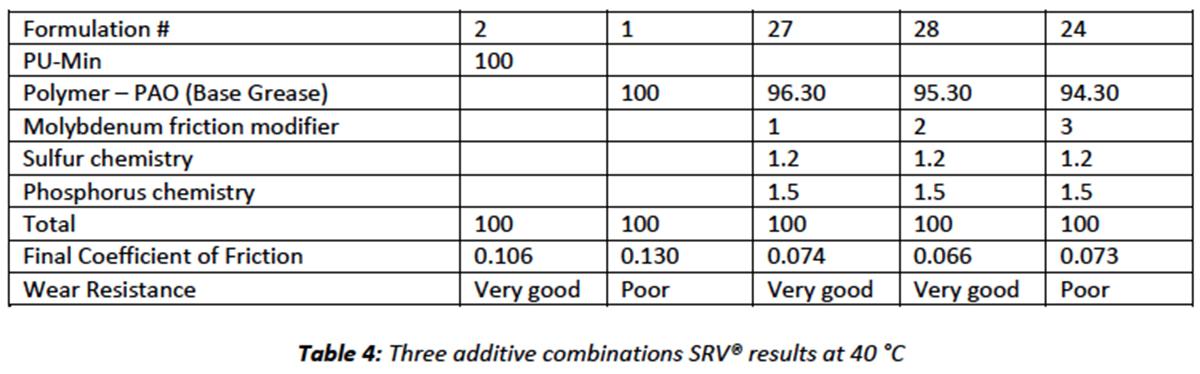
additive for surface adsorption or the balance between the friction modifier additive and antiwear additive surface coverage. The higher the friction modifier surface coverage, the better the friction reduction. Since both friction modifier and antiwear additives are competing for the same metal surfaces in relative motion, higher friction modifier additive surface coverage also means the lower the antiwear additive surface coverage. So when better friction modifier performance is achieved, wear often suffers. However, with the right balance of additives, desired performance can be achieved.
Similar formations were also evaluated conducted at 40 °C as shown in the table below. Interesting results were obtained. Formulation 27 was formulated at 1 wt. % of molybdenum friction modifier failed after 6 minutes due to extremely high friction that exceeded the set limit of the SRV® tester. Increasing the treat rate of molybdenum friction modifier to 2 wt. % passed the 2 hour test duration and maintained both the friction reduction and wear resistance properties as demonstrated at 80 °C. Further increasing the treat rate of the molybdenum friction modifier to 3 wt. % improves wear resistance but adversely affected the friction reduction at 80 °C. These phenomena may be explained by the activation energy each additive chemistry requires. In pure sliding and oscillating condition, molybdenum friction modifier typically activates at 60-80 °C temperature range to reduce friction by formation of lattice layer type MoS2 based tribofilm. On the other hand antiwear chemistries tend to activate faster than friction modifiers at lower temperatures. Hence an improvement in wear resistance at lower temperatures might be due to the more active role of antiwear additives compared to the molybdenum friction modifier. An improvement in the friction reduction and wear resistance at higher temperatures is due to activation of friction modifiers as well as due to optimization of additives.
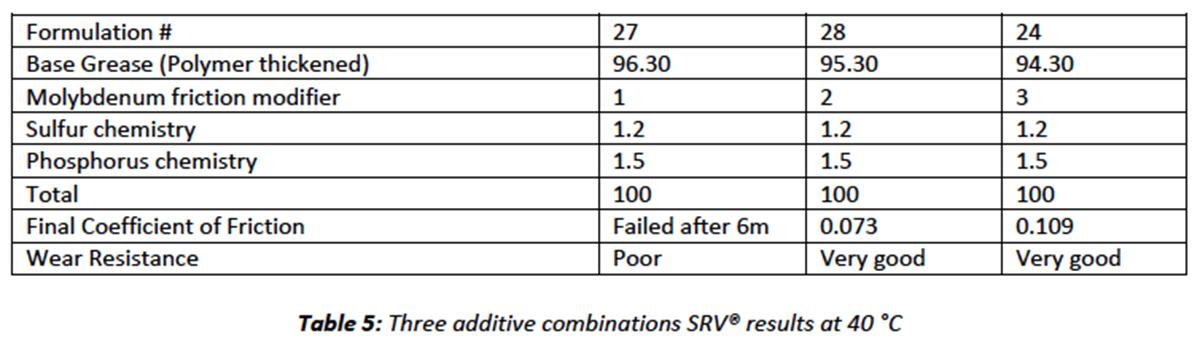
Motor trial results
To test the influence of lubricating grease selection on electric motor bearing operating temperatures and total energy consumption, a test rig was fabricated to perform a controlled comparison of author’s experimental grease with industry benchmark greases. The laboratory testing rig was fabricated utilizing a single phase AC powered 1/3 HP electric motor operating at a 1075 rpm shaft speed. To the shaft was mounted an 18-inch, four blade fan with 30-degree pitch. The fan blade provided a fully loaded state for the motor, allowing it to draw the maximum 3.3 Amp current from the 120V source.
In each test, the test motor was disassembled and two identical bearings, each containing the same test grease, were installed. A fixed 2.4 gram quantity of each test grease was applied to new 6203 size
deep groove ball bearings using a manual bearing packer. The quantity of grease required was calculated from published formulas [10] based upon the bearing dimensions. As per instruction by the bearing manufacturer [5] new bearings were not washed prior to grease application. The test bearings were then press mounted to the motor shaft using a hydraulic press. The test motor was reassembled, and each test run was conducted over a 48 hour interval to allow for break-in or running in wear and temperature stabilization.
The electric motor was modified to allow for direct contact temperature measurement of each individual bearing race by thermocouple probe. The temperature readings were captured by a 4-channel ONSET thermocouple data logger. The power supply to the electric motor was run through a data logging recorder for measuring and recording of power and energy consumption of 120V plug loads. The ONSET plug load data logger was used for determination of electrical current requirement during the course of operation, and has a measurement accuracy of 1-Watt (W). The results of the comparative evaluation are shown below.
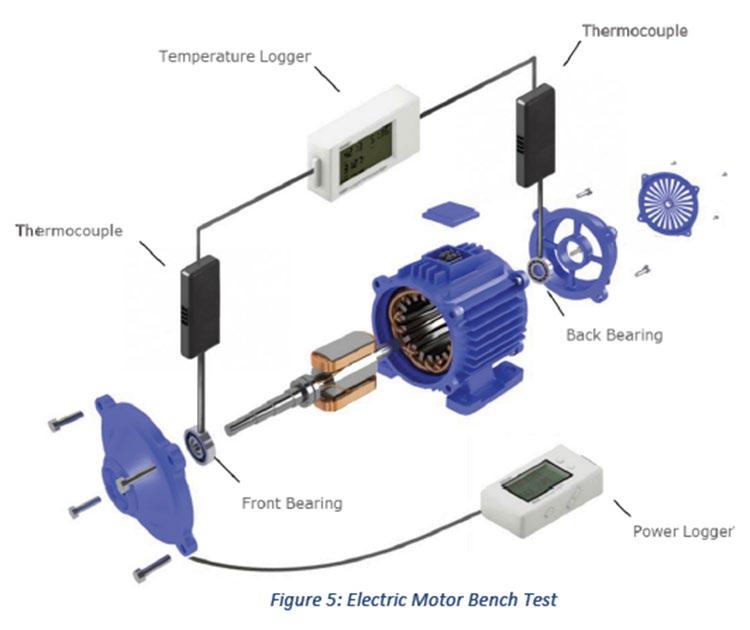
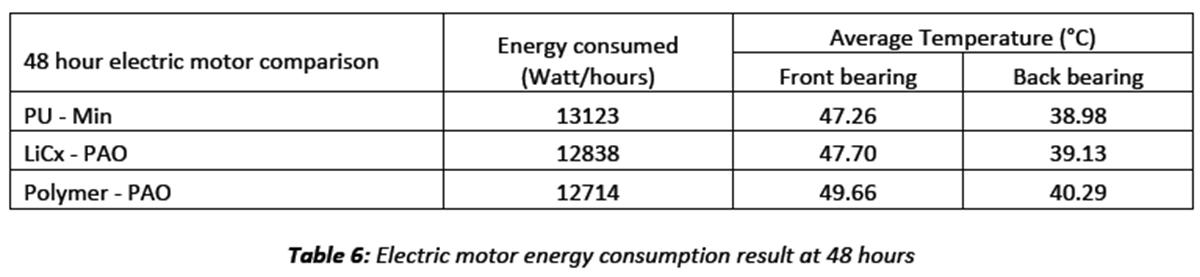
In the examination of the logged data, the commercial polyurea (PU – Min) electric motor grease had the highest resulting energy consumption measurement. The lithium complex (LiCx – PAO) energy consumption measurement was 2.17% lower than the baseline polyurea, which was expected due to its use of PAO base fluid and friction reducing additives. However, the lowest energy consumption was measured for the authors experimental polymer thickened grease (Polymer – PAO). In this final measurement, the resulting energy consumption was over 3.12% lower than the benchmark polyurea reference grease.
Unexpectedly, bearing temperatures remained fairly consistent over the duration of the test, and within a similar range for each of the three tested greases. Based upon this observation, we believe the bearings require more time than the 48 hours allowed to reach a steady state temperature. Once a steady state temperature is achieved, we believe the expected differentiation in operating temperatures among the test greases will be evident. This explanation is consistent with others findings, where bearing temperatures were found to be inconsistent for up to 20 days from the initial start-up [11].
SUMMARY AND CONCLUSIONS
Energy savings for electric motors can only be achieved through a reduction in energy losses. Three lubrication related conditions influence these energy losses, and they are churn, traction and friction. Greases can be specifically designed to influence these lubrication related conditions through the selection of formulating components with specific characteristics, including low traction, reduced viscosity, and low friction.
Differences can be observed between current technology commercial greases utilizing conventional thickener types and experimental polymer based greases in laboratory bench testing. These polymer thickened greases have unique characteristics which contribute toward friction and traction reduction, especially at higher temperatures. MTM and SRV® are versatile tools for measurement of a lubricant’s friction and traction reducing potential, and are therefore valuable for analyzing and optimizing grease formulations for this purpose. Greases for electric motor application based upon novel polymer thickeners have demonstrated in these tests that they can provide a very low coefficient of friction and low traction, resulting in low Stribeck friction coefficients. The Stribeck friction coefficient can be a valuable tool in screening greases for energy savings potential.
A laboratory rig based upon full-scale electric motor was successfully used to evaluate the energy consumption differences provided by the use of different greases. In this motor test rig, greases based upon novel polymer thickeners with low Stribeck friction coefficients have demonstrated they can positively influence the energy consumption of an electric motor. The energy and cost savings impact through use of this next generation technology is evident, and simple to apply today.
ACKNOWLEDGEMENTS
The authors would like to acknowledge the contribution of Doug Majors and Nathan Claycamp of Axel Americas LLC for their assistance in conducting the electric motor energy evaluation. Authors would also like to acknowledge Axel Americas LLC and Vanderbilt Chemicals LLC for their gracious support in conducting this research.
REFERENCES
1. P. Walde, “Energy efficiency policy opportunities for electric motor driven systems”, International Energy Agency publication, 2011 2. B. Jacobson, “Polymer thickened lubricant”, (Lubrisense White Paper 2007/07)
Axel Christiernsson 3. J. Leckner, “Energy efficiency and lubrication mechanisms of polymer thickened greases – Apples and oranges”, in ELGI 27th AGM, Barcelona Spain, 2015 4. R. Westbroek, “Upper Operating Temperature of Grease: Too Hot to Handle?,” in
ELGI 26th AGM, Dubrovnik Croatia, 2014 5. Anonymous, “SKF Bearing Handbook for Electric Motors,” SKF publication 140‐430, Version 11/2005 6. W.H. Detweiler, “Common causes and cures for roller bearing overheating” SKF
USA Inc., King of Prussia, PA 7. J. Vinci, “Developing Next Generation Axle Fluids: Part II – Systematic
Formulating Approach”, SAE publication 02SFL-‐ 154 8. Axel Christiernsson internal report 9. G. Fish, “”Grease additives for high temperature bearing applications”, in ELGI 26th AGM, Dubrovnik Croatia, 2014 10. Anonymous, “Mobil technical topic: Guide to electric motor lubrication”,
Exxon Mobil publication, 2009 11. G. Fish, “The development of energy efficient greases”, in ELGI 27th AGM,
Barcelona Spain, 2015