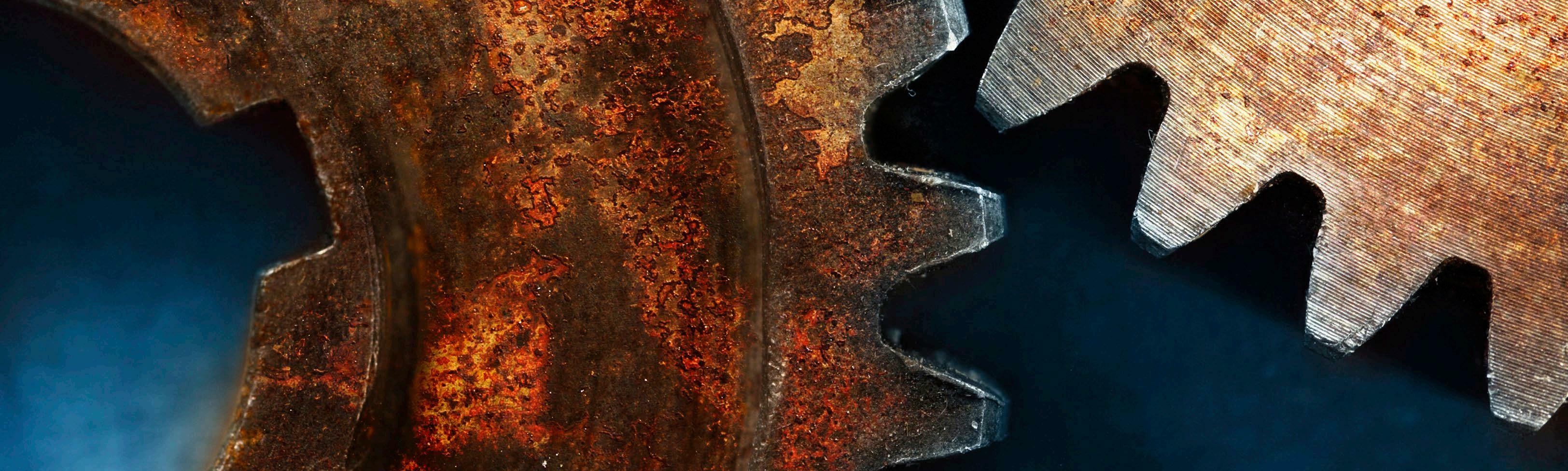
20 minute read
“Rust Never Sleeps” An Investigation of Corrosion in Grease Lubrication
Joseph P. Kaperick, Gaston Aguilar, Michael Lennon Afton Chemical Corporation • Richmond, VA
Abstract
Corrosion of steel or iron doesn’t just happen “out of the blue”. Rust causes damage to untold numbers of machine components not only through direct electrochemical erosion of the metal but through incidental increase in pitting and wear caused by the iron oxide particles. This can be of special significance in mining operations where the potential for exposure to wet or humid environments is extremely high. While grease itself can inhibit some corrosion by reducing ingress of moisture, the addition of rust or corrosion inhibitors is often needed to give additional protection. There is a wide variety of additive solutions as well as a number of different corrosion tests to screen their effectiveness. An overview of some common corrosion tests along with studies comparing the severity of the tests with various aqueous solutions and under different test conditions will be presented.
Introduction
A study on the cost of corrosion in the United States was conducted between 1999 and 2001 with support from the Federal Highway Administration (FHWA) and National Association of Corrosion Engineers (NACE). Their definition of corrosion was that it is a natural phenomenon which results in deterioration of a substance (usually metal) or its properties because of a reaction with its environment. This phenomenon affects everything from cars and appliances, to drinking water systems, to pipeline, bridges and public buildings. According to their statistics, over the past 22 years the U.S. has incurred total normalized losses of more than $380 billion (averaging $17 billion annually) from natural disasters such as tornadoes, hurricanes and earthquakes. In comparison, the direct cost of metallic corrosion is $276 billion on an annual basis which represents 3.1% of U.S. Gross Domestic Product (GDP). [1]
Mining uses a huge amount of water in its daily operations. According to the United States Geological Survey (USGS), roughly 4 billion gallons a day are used in the United States alone. “Mining water use is water used for the extraction of minerals that may be in the form of solids, such as coal, iron, sand, and gravel; liquids, such as crude petroleum; and gases, such as natural gas. The category includes quarrying, milling (crushing, screening, washing, and flotation of mined materials), re-injecting extracted water for secondary oil recovery, and other operations associated with mining activities.”[2] According to its 2005 study, 43% of the water used is saline. The use of saltwater or seawater is increasing in some areas as mines look to take advantage of convenient water sources for their needs. Just one example is BHP Billiton, an Australian-British mining company, whose chemical process needs large amounts of water pumped via pipeline from the nearby Indian Ocean. “Some of the seawater is used in its raw state to cool the bearings in all 152 pumps around the plant, while some is desalinated on site for the metallurgical process. Steam and acid are used to prepare the ore for the refining process.“[3]
The focus for the grease formulator, with respect to corrosion, is obviously on providing protection from the rust which often occurs in the presence of water and several studies have been documented by NLGI over the last couple of decades. Hunter and Baker [4, 5] evaluated different rust inhibitors and greases using the two versions of the traditional static rust test (ASTM D1743 and D5969) and the dynamic EMCOR corrosion test
(ASTM D6138). They mainly focused on the use of 5% synthetic seawater solution and showed good correlation between the tapered bearing static test and the EMCOR dynamic test. Hunter et al. also focused on ashless rust inhibitors in different grease thickeners in a study using the same tests in 2000. [6]
Experiment
The focus of this study was to examine in more detail three standard industry bench tests for testing grease with respect to steel corrosion – the dynamic EMCOR bearing corrosion test (ASTM D6138) and two “standard” bearing corrosion tests (ASTM D1743, D5969). There are several other types of corrosion tests for lubricants including salt spray corrosion (ASTM B117), humidity cabinet (ASTM D1748) as well as test to measure corrosion of copper and other metals, however, they are not included in this study.
Test Methods
ASTM D1743 “Standard Test Method for Determining Corrosion Preventive Properties of Lubricating Greases” [7]
This is often referred to as the “standard bearing” or “static corrosion” test. It utilizes a tapered roller bearing with a Timken bearing cone/roller assembly and cup which is packed, run in, exposed to water and let sit for 48 + 0.5 hours at 52 + 1˚C in 100% humidity. The water used in this method is restricted to distilled water.
ASTM D5969 “Standard Test Method for CorrosionPreventive Properties of Lubricating Greases in Presence of Dilute Synthetic Sea Water Environments” [8]
This test is identical to ASTM D1743 with two exceptions: it is only run for 24 hours and the water used is detailed as various dilutions of synthetic seawater (as specified in ASTM D665B).
ASTM D6138 “Standard Test Method for Determination of Corrosion-Preventive Properties of Lubricating Greases Under Dynamic Wet Conditions (Emcor Test)” [9]
This test is often referred to as a “dynamic corrosion” test. It employs a ball bearing (double row self-aligning bearing [30 by 72 by 19 mm], which conforms to 1306 K of ISO 15, with a steel cage. The referee bearing is SKF 1306 K/236 725 bearings but other bearings meeting this description can also be used. The bearing is packed and run in, then cycled for one week under specific conditions (8 hours on and 16 hours off for first 3 days, then sitting at rest for 4 days). The test rotating speed is 83 + 5 rpm and the rig is held at room temperature for the duration of the test. Distilled water, in addition to dilutions of synthetic seawater and sodium chloride, are allowed by the method.
Ratings for the D1743 rust test changed in 1987 to a pass/fail system under which a bearing with no spots larger than 1.0 mm in diameter is considered a pass and two out of three bearings must pass for the test to be considered acceptable. The old system attempted to show the extent of rust using a numbering system as shown in Figure 1. The EMCOR corrosion test still uses a numerical rating system with “0” indicating no visible rust while a “5” indicates more than 10% surface coverage and is the highest rating for the test. Typically, the EMCOR test is run in duplicate and numbers reported as “x/x”. Some specifications set limits that allow for some rust and therefore it is possible to see a performance target of “2/2” or even “3/3”. Alternatively, some older specifications will show a specification value of “1,1,1” for the D1743 test which is likely a holdover
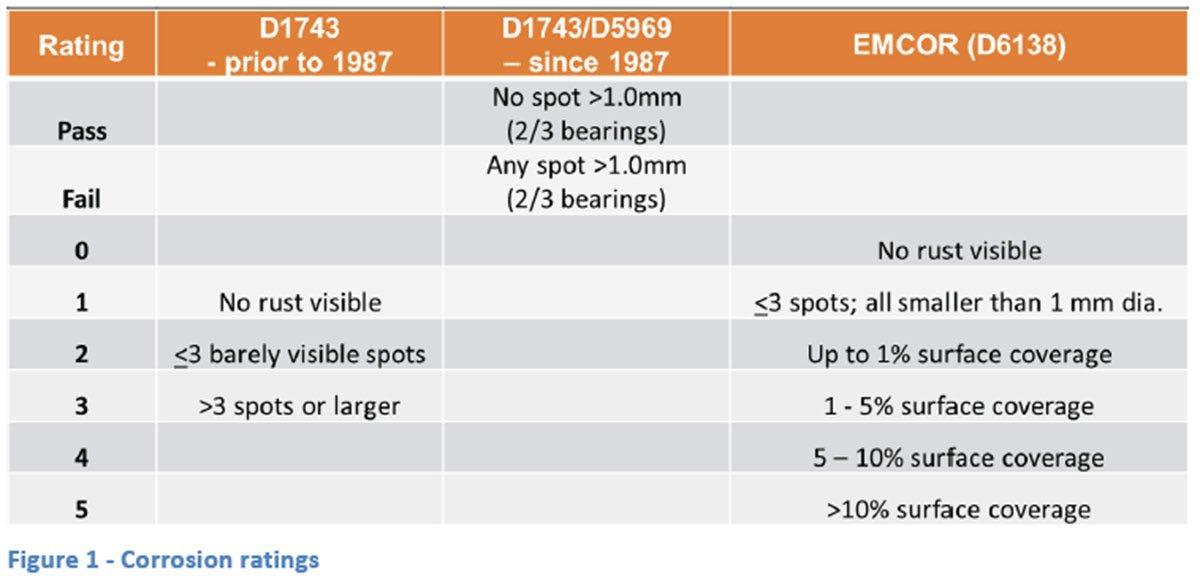
from the pre-1987 rating indicating three bearings with no visible rust.
Synthetic Seawater Solution
Grease Samples
The base grease used for the majority of the work done in this study (Base Grease #1) is a commercially-sourced straight lithium NLGI Grade #2 base containing Group I mineral oil. It was chosen for its moderate severity and response to additives so that better or worse results could be seen under the different conditions studied.
A second base grease (Base Grease #2) was also employed for part of this study. This base was made in the author’s facility using a lab scale kettle. It is a lithium 12-hydroxy stearate grease cut to an NLGI #2 grade and containing an ISO 150 Group I mineral oil blend. This grease was used to better understand the role of the thickener in protecting against corrosion.
The additive systems used were of two types. The first set was a group of packages that were formulated specifically for use in grease and contain combinations of rust inhibitors optimized for use in grease applications (Pack A, B, C). The second set was a group of packages that were optimized for gear oil applications (Pack D, E, F). These types of additive packages are often used in grease formulations because of desirable performance aspects that can be achieved.
The formulation for synthetic seawater (SSW) is shown in ASTM D665B, and is referred to in both D6138 and D5969 (see Figure 2). All dilutions used in rust testing are shown as some percentage of the “100%” formulation described in D665B.
Results
Initial testing was completed on Base Grease #1 alone and with 1.5 wt% of an EP additive blend. As can be seen from the results (Figure 3), the base grease by itself does a good job of protecting the EMCOR bearing in the presence of distilled water only but when a small amount of ionic character is added with a 5% mixture of SSW that ability disappears completely. Even the small amount of ionic material that was introduced with the EP additive system introduces some rust which hints at a tendency to break down that limited protection. Following this initial testing, Base Grease #1 was treated with Packs A thru F at various treat rates (Figure 4). Treat rates were chosen based on typical dosages and, for Packs D and E, two treat rates were used for each pack to be able to compare the effect of increased rust inhibitor on corrosion protection. The use of 5% SSW was decided on to give moderate rust results so that good comparison across different packages and rust inhibitor levels could be achieved. To
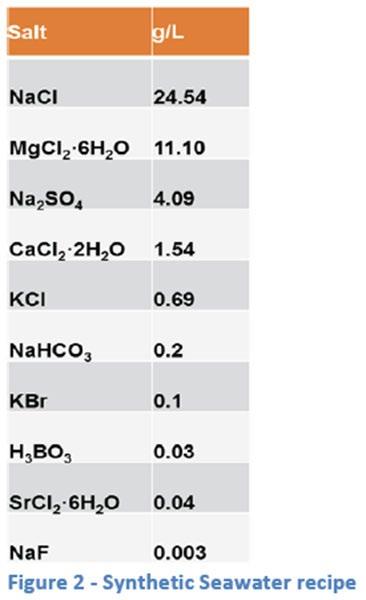

give a good comparison with a solution of pure sodium chloride (NaCl), it was decided to use the equivalent amount of salt on a weight percent basis. Using the SSW recipe, this was determined to be 0.212 wt% of NaCl in aqueous solution.
Examining the results in Figure 4, rough correlation can be seen between the severity of test results and the amount of rust inhibitor present. This is especially noticeable in comparing Packs A, B and C, as well as in looking at the different treat rates of both Pack D and E. The same trend is seen, generally, with both the 5% SSW and 0.212 wt% NaCl solutions although the NaCl solution appears to have a significantly milder effect on corrosion when compared head-to-head with the SSW solution. This milder effect also appears to reduce the level of differentiation in corrosion results seen with treat rate in the SSW solution. Based on the results seen in this general screening of different packages and rust inhibitor levels, it was decided to use Packs C and D-2 for further study.
The next stage of the study was an investigation of the effect of increasing salt water concentration using the SSW solution, as well as similar dilutions of NaCl (Figure 5). The effect of different salts was also studied by including magnesium chloride (MgCl2.6H2O) and calcium chloride (CaCl2). The practical reason to use these salts is that they often are used in de-icing solutions and therefore, automobiles, trucks and heavy equipment can all be exposed in colder climates. The dilution level of these additional salts was determined based on molar equivalents to the 0.212 wt% NaCl solution. It was obvious from these different ways of comparing salt solutions (weight percent versus molar equivalents) that a more universal way of comparing the solutions was needed. The ionic
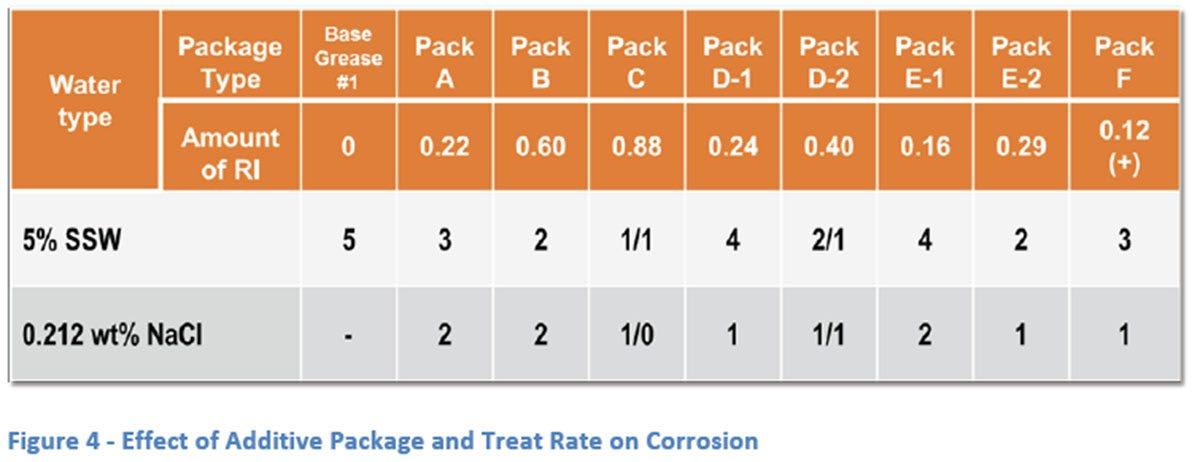
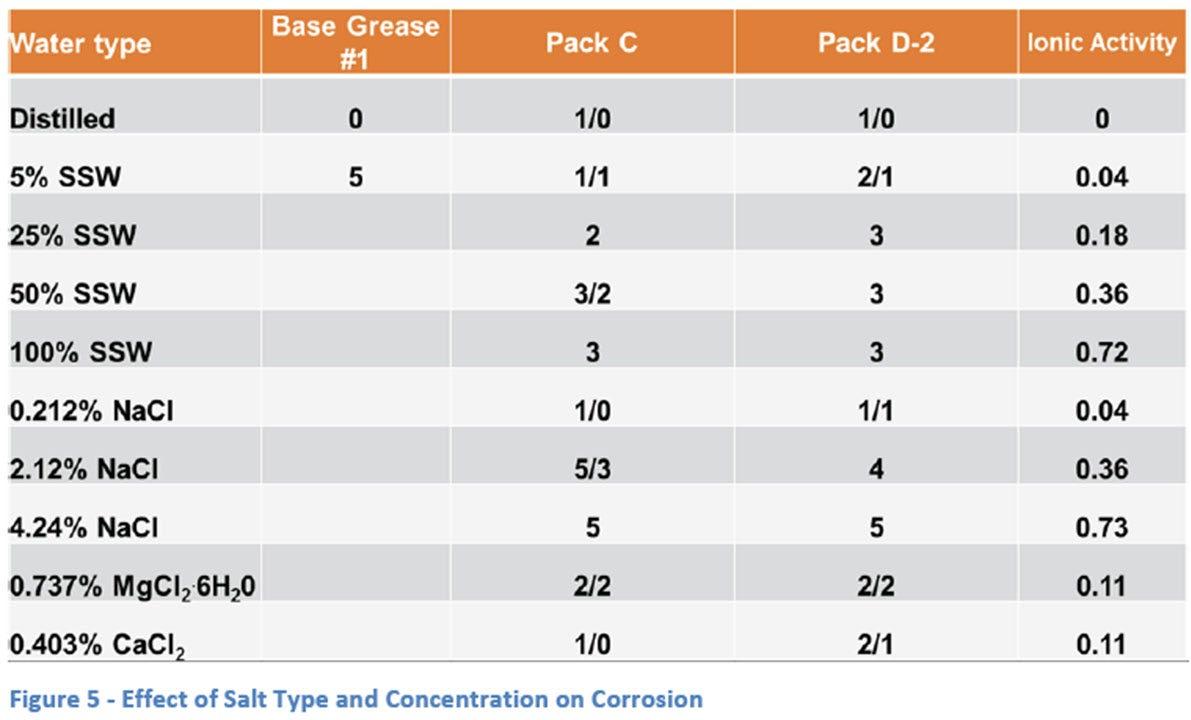
activity should have some effect on the amount of corrosion seen in a particular test, so these activities were calculated for each solution and are shown in Figure 5 as well.
As expected, the severity of the corrosion seen increases with the increase in concentration of the salt water solutions both in the case of SSW and NaCl solutions. As discussed earlier, there is a slightly milder effect seen when using 0.212 wt% NaCl versus the 5% SSW solution. However, as the concentration of the solutions was increase, a larger disparity between the two solutions was seen with the NaCl being more severe than the equivalent SSW solutions (2.12 wt% NaCl vs 50% SSW, and 4.24 wt% NaCl vs 100% SSW).
When looking at the additional salt solutions, the MgCl2 appeared to be more severe than either the CaCl2, the NaCl (0.212 wt%) or the SSW (5%) solutions with 4 bearings giving ratings of “2” while the other salts gave slightly milder ratings between “0” and “2”.
It is recognized that the concentrations of the different salt solutions may not allow an easy comparison due to different weight percents and molar equivalents being used. For this reason, a comparison was made with respect to the calculated ionic activity for each of the solutions (see Figure 6).
From the graph, a rough correlation is seen between corrosion and the ionic activity of the salt solution to which it is exposed. The effect seems to plateau at higher activities but this may well be due to the non-linearity of the EMCOR rating system which gives its highest rating of “5” to any bearing with corrosion on more than 10% of its surface. Another observation is that there appears to be better protection provided by Pack C at lower ionic activities (in the range of 0 to 0.2) but that same advantage is not seen at the higher levels of activity.
To compare the severity of the EMCOR “dynamic” corrosion test to the “static” corrosion test (ASTM D1743 and D5969), testing was carried out under similar conditions with a minor modification in the rating methodology. The tapered roller bearings of D1743 and D5969 are typically judged as “pass” or “fail” with two out of three “passes” needed for a successful test. For comparison purposes and to better judge the effect of different conditions and salt solutions, the EMCOR rating system was applied to the bearings in this portion of the testing yielding ratings from “0” to “5” for each bearing. Following the methodology of D1743 and D5969, three bearings were run in almost all cases. Additives used in the testing in this section were limited to Packs C and D-2 with the focus being comparison to the work done with the EMCOR bearings discussed above. Base Grease #1 was also used in this section for the same reason.
The results for Base Grease #1 with both distilled water and 5% SSW were very similar to those seen with the EMCOR testing (Figure 7). Again, a small increase in ionic activity showed a large increase in corrosion with ratings going from “2/0/0” to “5/5/5”. The same was seen with the additized greases with both Pack C and D-2 giving adequate protection of the bearings in distilled water while the presence of the 5% SSW solution caused significantly more corrosion in each grease (although less than the unadditized base grease).
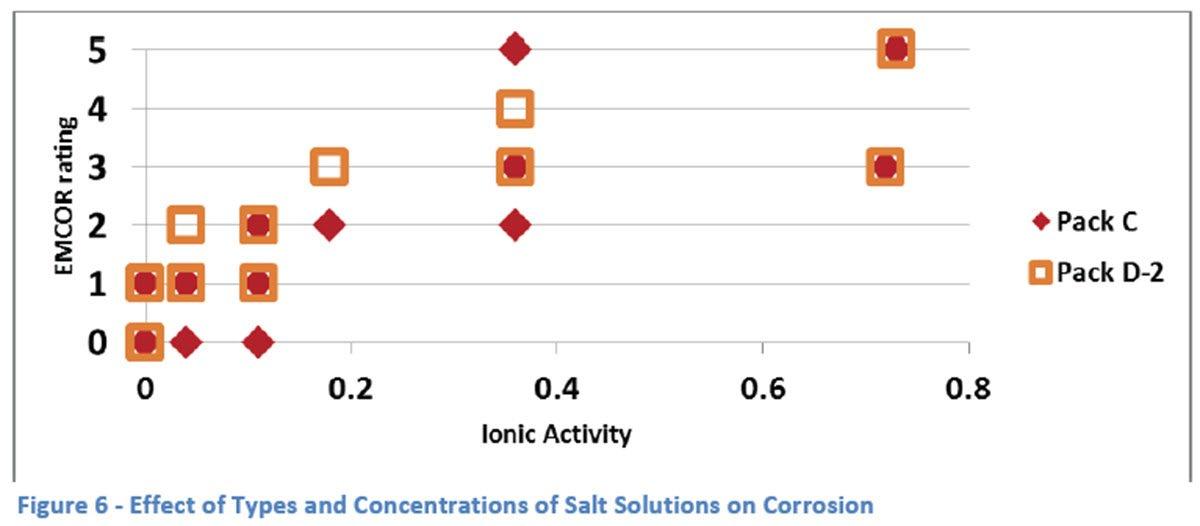
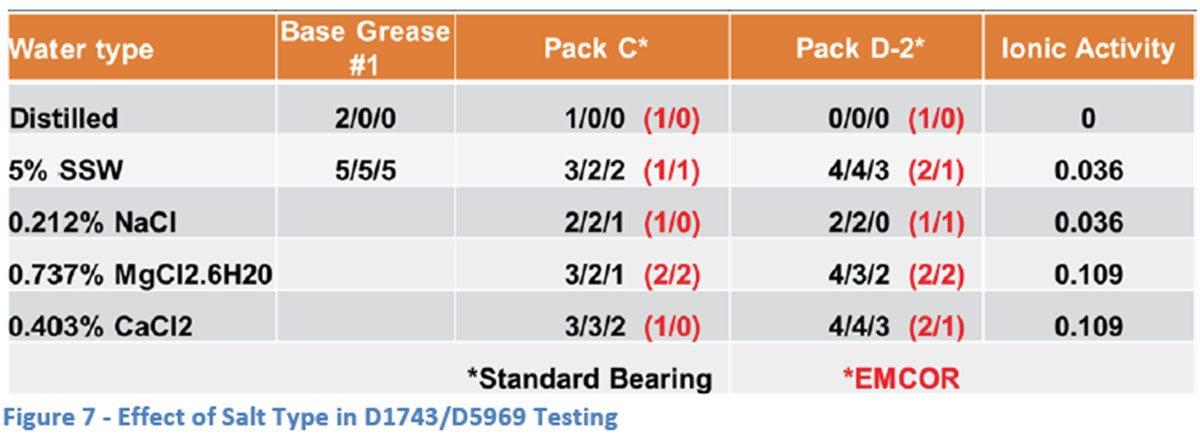
Comparison with the other salt solutions used in the EMCOR study, showed very little differences when using Pack C as the additive. However, Pack D-2 appeared to give better protection against corrosion in the presence of NaCl solution as compared to the other solutions. In general, Pack C provided better protection in all the salt solutions except for NaCl in which case there appeared to be no difference between the additive packages.
Interestingly, when compared to the results from the EMCOR testing (shown in red in Figure 7), the ASTM D5969 results appear to be more severe in each of the salt solutions regardless of the rust inhibitor system employed. This is in spite of conditions which would seem to make the EMCOR test more severe – longer time (1 week vs 24 hours) and environmental setting (dynamic rotation through water vs static exposure to humid atmosphere).
To further explore these differences, the ASTM D5969 test was modified to use the EMCOR bearing under the D5969 conditions. Sufficient water was used to raise the level, relative to the bearing, to the same height as the standard test and 30 ml was left in the container to provide the humid atmosphere necessary for the test. Several run-in conditions were used to judge the effect of this parameter (Figure 8). The standard EMCOR run-in procedure provides a total of about 2490 revolutions over a 30 minutes period whereas the D5969 procedure uses a much higher speed process which gives about 1750 revolutions in a minute. As can be seen from the results neither the amount of break in time or total number of revolutions seemed to have a significant impact on the results. Based on the data generated, it appears that the bearing itself is the main factor in the severity of the test. The first possible reason for this is that the tapered bearing configuration gives significantly more areas for rust to form with the linear geometry of the contact points with the outer race. The EMCOR ball bearing design only allows point contact with the outer race and therefore fewer overall opportunities for rust to occur. Another possibility is that the design of the EMCOR bearing somehow allows better distribution of the grease and less ingress of water.
The effect of time and temperature on extent of corrosion was also studied using the ASTM D5969 test method with 5% SSW solution. The standard test method calls for exposure to a humid atmosphere at 52 ˚C for 24 hours. The method was modified (as
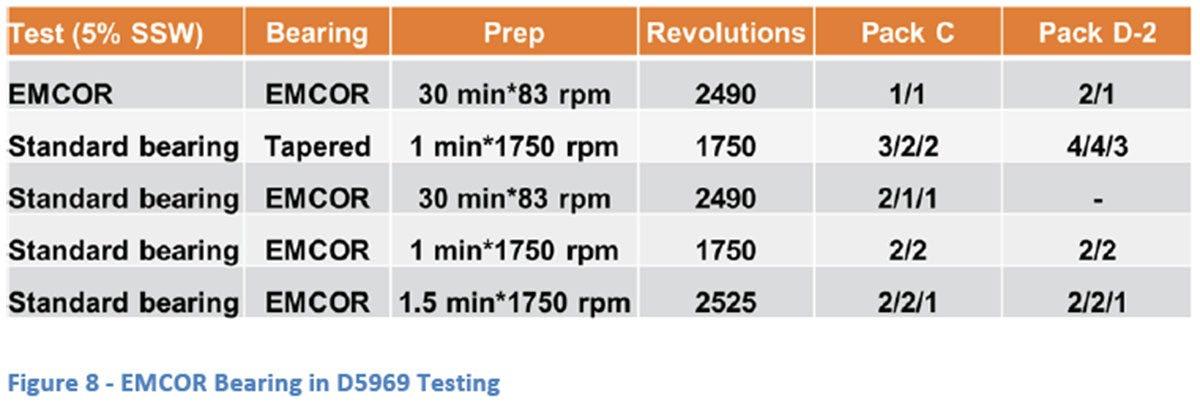
shown in Figure 9) to look at lower (room temperature – RT) and higher (70 ˚C) temperatures as well as an extended period of time (48 hours). The modified temperatures gave surprising results in that the lower temperature appears to give more severe results. Both additive packages gave better corrosion protection at the higher temperature than at the lower temperature even though at the standard test temperature Pack C was more effective. One possible explanation that is suggested in the literature [x] is that raising the surface temperature of the part may reduce the relative humidity at the surface and therefore reduce corrosion. Other possible explanations are that the softer grease gives better surface coverage at the higher temperature leading to better overall protection, or that the additives are more effective at higher temperature which might also explain the differences between the two packages at the standard temperature.
The longer time resulted, unsurprisingly, in more severe corrosion but this result does lead to the question of correlation of results of a 24 hour test to actual field conditions. How long does a grease that protects against moisture for 24 hours in the D5969 test actually protect against moisture in the field? The increase in severity seen with doubling the length of the test may indicate some need for additional study in this area.
A final aspect of corrosion was addressed by looking at the role that the grease itself plays in preventing corrosion. As was seen earlier in this study, base grease by itself supplies sufficient protection against rust in the presence of distilled water, but an increase in ionic activity quickly overcomes that basic protection. It is not clear whether the grease thickener system is protecting against rust, in part or in whole, by preventing water from getting to the surface, or if the additives in the grease are sufficiently surface active to protect the bearing from corrosion by themselves.
For this study, a lithium 12-hydroxy stearate grease made with an ISO 150 cSt Group I mineral oil blend (Base Grease #2) in the author’s lab was used. This allowed the separate study of the grease thickener/oil combination and the oil by itself. Both were additized with the same amount of Pack C and therefore the only difference between sample #2 and #3 was the presence of the grease thickener in sample #2. The samples were then tested in the standard EMCOR test using a 50% SSW solution (Figure 10). This had resulted in a medium rating of “3/2” with Base Grease #1 and the same conditions were used in order to see if there were any changes for better or worse.
As can be seen, there were no significant differences in the results for samples #2 and #3. While obviously based on a small sample set, this seems to indicate that the additive system itself is responsible for the corrosion protection under these circumstances and no additional benefit is seen from the presence of the grease thickener. It is in fact possible that the thickener has resulted in more corrosion although further study would be needed to confirm that with any statistical significance.
Summary and Conclusions
Under the conditions of the study, there does appear to be a rough correlation between ionic activity of various salt water solutions and the amount of corrosion seen in bearings. However, the type of molecule present in the salt solution does appear to have some effect separate from the overall ionic activity of the solution. This could indicate that the type of salt in the environmental water to which greases are exposed in the field could be important in formulating a grease for use in that application.
Higher concentrations of salt solutions as well as increased amounts of time exposed to them under test conditions increases the amount of corrosion seen. In addition, an increase in temperature of the test showed a
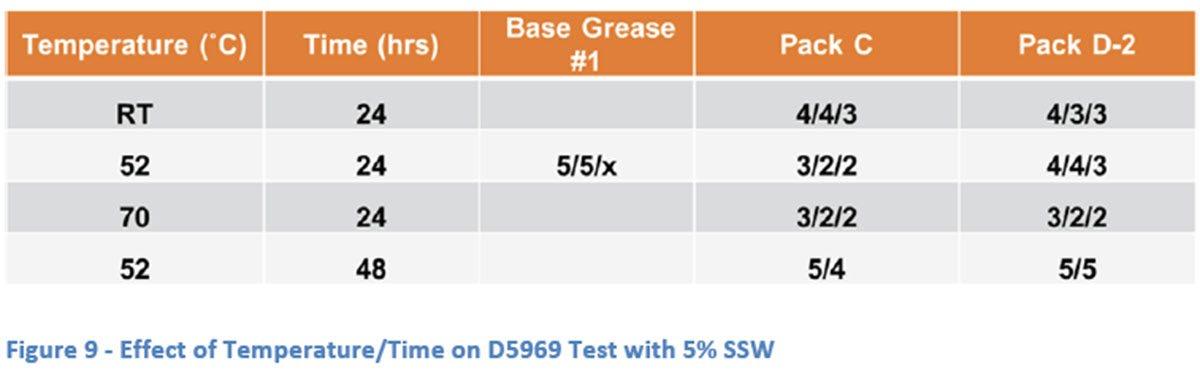
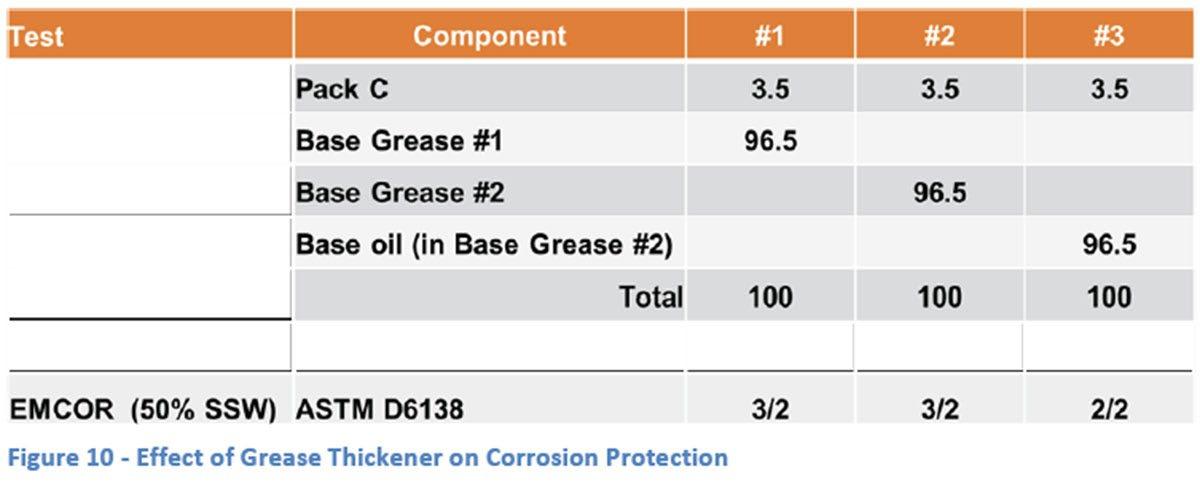
decrease in the amount of rust seen. These observations seem to indicate that reliance strictly on bench tests under limited conditions may not be sufficient to guarantee corrosion protection in environments that do not mimic these standardized conditions. Time and temperature seem to be especially critical and further study into the correlation of these two parameters in both bench and field testing would appear to be warranted.
The type of bearing was also shown to be critical with the tapered roller bearing giving more severe results than the EMCOR in almost all side-by-side testing. This was likely due to the larger number of contact points (and potential areas for rust to begin) seen with the tapered bearing. This indicates the importance of using the right bench testing to formulate for different bearing applications.
Finally, the importance of additive chemistry was seen with the severity of corrosion varying depending on the type of additive system and the treat rate of a specific additive system. The additive system can be optimized depending on the amount of corrosion protection needed and the environment to which the grease will be exposed. It was also seen, in limited testing, that the additive system by itself may be sufficient to provide the corrosion protection needed.
Additional study is indicated in a number of areas including the role of thickener in corrosion protection, the effect of temperature on rust formation and activity of corrosion inhibitors, and reason for differences in severity of different types of salt solutions. It is hoped that the information provided here will stimulate further investigation into these areas.
References
1. Koch, G.H., Brongers, M.P.H., Thompson, N.G.,
Virmani, Y.P., Payer, J.H. “Corrosion Costs and
Preventive Strategies in the United States” Publication
No. FHWA-RD-01-156. 2. Kenny, J.F., Barber, N. L., Hutson, S.S., Linsey, K.S.,
Lovelace, J.K. and Maupin, M.A., “Estimated Use of
Waater in the United States in 2005”, United States
Geological Survey, http://water.usgs.gov/edu/wumi. html. 3. Neil, M. “Overcoming Saltwater Corrosion”, Water and Waste Digest, Oct 2, 2009. http://www.wwdmag. com/pipe/overcoming-saltwater-corrosion. 4. Hunter, M. E. and Baker, R. F., “Corrosion-Rust and
Beyond”, NLGI Spokesman, Vol. 63, No. 1, March 1999. 5. Hunter, M. E. and Baker, R. F., “The Effects of Rust
Inhibitors on Grease Properties”, NLGI Spokesman,
Vol. 63, No. 12, 2000. 6. Hunter, M. E., Rizvi, S.Q.A., and Baker, R. F., “Ashless
Rust Inhibitors for Greases”, Presented at 67th NLGI
Annual Meeting, Asheville, NC, October 2000. 7. ASTM D1743-13 “Standard Test Method for
Determining Corrosion-Preventive Properties of
Lubricating Greases”, (2013) ASTM International,
West Conshohocken, PA. 8. ASTM D5969-11e1 “Standard Test Method for
Corrosion-Preventive Properties of Lubricating
Greases in Presence of Dilute Synthetic Sea Water
Environments”, (2011) ASTM International, West
Conshohocken, PA. 9. ASTM D6138-13 “Standard Test Method for
Determination of Corrosion-Preventive Properties of
Lubricating Greases Under Dynamic Wet Conditions (Emcor Test)”, (2013) ASTM International, West
Conshohocken, PA.