Inez Ow
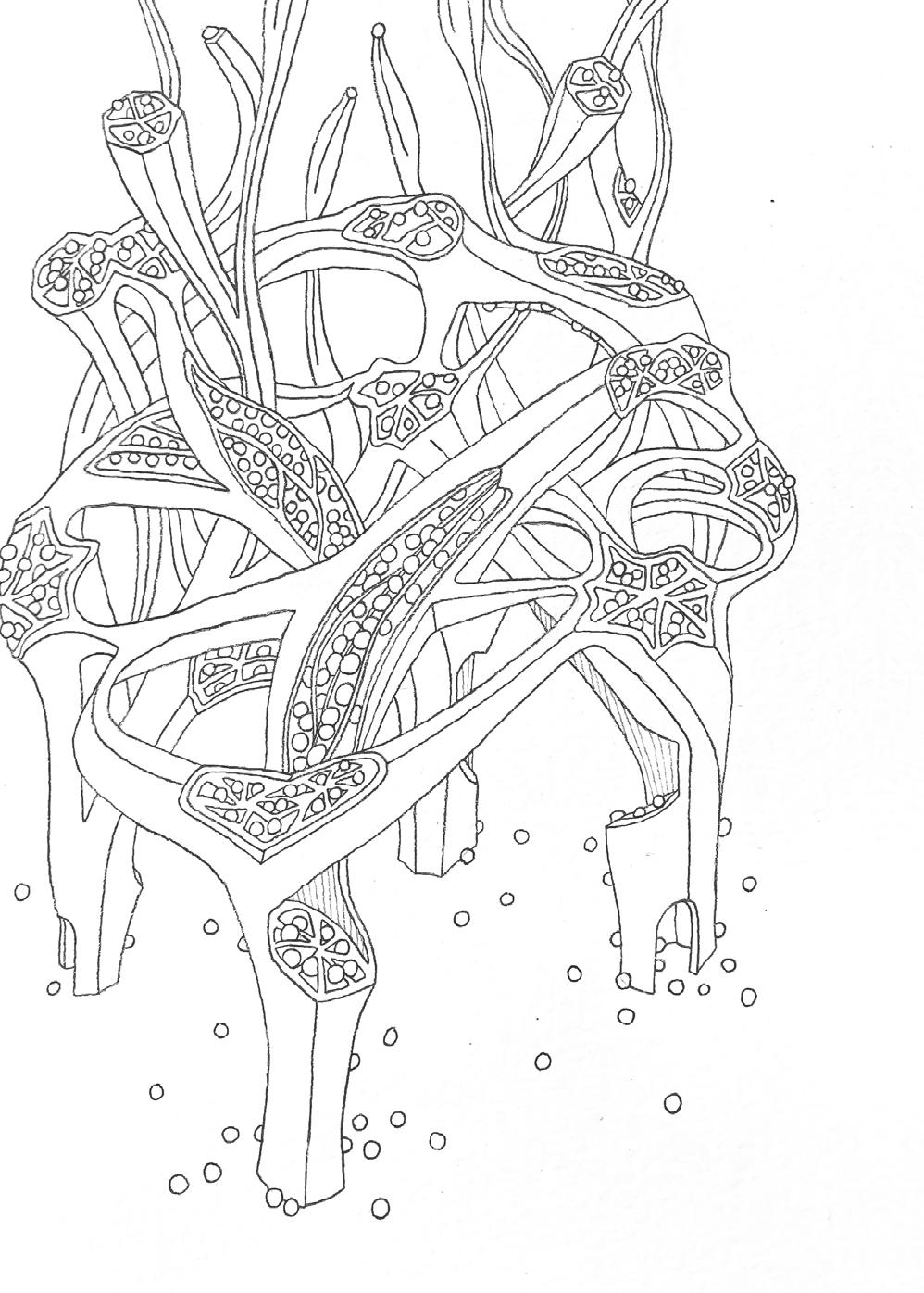
inezow@mit.edu Singaporean
3.5 years / 2018 – 2022
M.Arch, GPA 5.0/5.0
Joint Thesis – Seeing Labor: Fabrication Porn from Behind the Scenes
3.5 years / 2014 – 2017
Singapore University of Technology and Design
BSc.Arch, GPA 4.42/5.0
2 weeks / 2016 Aug
Architectural Association Pyongyang Visiting School Pyongyang, North Korea
10-day workshop with North Korean students, architects and policy makers, where we explored less common urban strategies for the DPRK such as adaptive reuse, while gaining a more nuanced understanding of emerging citizen aspirations.
2 months / 2022 Jan – Feb
MIT Urban Risk Lab Research Assistant / Cambridge, MA
Our team of 4 worked closely with Mass Audubon to design their upcoming exhibition space at Magazine Beach Park, integrating wildlife and ecosystem education into portable snack bars.
2 months / 2021 Jul – Aug
Research Assistant / Boston, MA
Our team of 2 designed and fabricated a series of 15 geometric models to investigate the intersectional space of constructive frictions between material systems and idealized complex geometry.
3 months / 2020 Jun – Aug
MIT BIPOC in the Built Project Research Assistant / Cambridge, MA
Our team of 12 researched, wrote and peerreviewed over 30 profiles of Black, Indigenous, and People of Color designers, to create a digital archive of their career trajectories and contributions to the built environment.
3 months / 2022 Mar – May BIG – Bjarke Ingels Group Design Assistant / Copenhagen
DD — Winter harbor bath and sauna extension in Copenhagen. In charge of 3D modeling construction details and conducting lighting scheme and material studies through iterative realistic renderings. [Rhino, Enscape, Photoshop, Indesign]
3 months / 2019 Jun – Aug Genome Architects
Architecture Intern / Singapore
Concept, SD — Semi-detached house. 3D modeling and rendering of exteriors and interiors.
DD — Co-working and co-living estate in Singapore. Assisted in detail drawings and schedule of furniture and finishes.
Concept — Holland-Bukit Timah District concept plan competition. Led the submission entry, was a shortlisted finalist.
[Rhino, AutoCAD, SketchUp, VRay, Photoshop]
6 months / 2017 Dec – 2018 May Venice Biennale 2018 Singapore National Pavilion Fabrication Lead / Singapore + Venice
Concept, DD — Prototyped acrylic modules and designed a streamlined fabrication process. Managed finances, material aquisitions, outsourcing and manpower. Resided in Venice for a month to oversee shipment logistics and assembly by local builders. [Rhino, Analog + Digital Fabrication]
9 months / 2017 Sep – 2018 May TakahashiLim A+D
Architecture Designer / Singapore
Concept, SD — Terrace house and good-class bungalow in Singapore. Physical and digital modeling. Joined meetings with clients, contractors and consultants. [Rhino, Photoshop]
6 months / 2018 + 2016 Jun – Aug Spatial Anatomy Architecture Intern / Singapore
Concept, SD — Adaptive reuse renovation of the Old Taman Jurong Cinema, and office extension for Public Utilities Board in Singapore. Drew plans, did physical and digital modelling. [Rhino, Photoshop]
2019 – 2022 MIT Merit Fellowship
2014 – 2017
SUTD Undergraduate Scholarship 2020
Longlisted Entry, Abu Dhabi Flamingo Visitor Center Design Competition
2015 – 2017 Head of Initiatives, SUTD Archi Society
2012 – 2013
Captain, Hwa Chong Women’s Touch Rugby Team
CAD / BIM Rhinoceros3D SketchUp AutoCAD
Autodesk Revit
2D Graphics
Adobe Photoshop Adobe Illustrator
Adobe InDesign Adobe PremierePro
3D Visualization
Enscape Twinmotion VRay
Autodesk 3DS Max Unity
Languages English Mandarin
Dear Reader,
Welcome to my portfolio! Here I have arranged projects along a loose spectrum from Imaginative to Technical to illustrate the range of architectural design modes that I have had the opportunity to operate in thus far, both in school and at work.
I have grown to value, on one hand, imaginative and refreshing solutions to briefs and constraints, and on the other, the technical rigor and agility required to realize them in innovatively feasible ways.
I look forward to continue pushing for the integration of these two qualities in an architectural career, ideally in teams with other creative and curious minds.
Thank you for browsing, and I’d be happy to discuss any questions you might have.
Inez,
How might we...
YMCA CENTER / New York
How might we extrapolate spatial logics embedded within existing objects to the building scale?
How might we design a house that helps to foster within its inhabitants an understanding of how it works?
ARTIST RESIDENCE / Madrid
How might we return the human scale to a site that has been dominated by a monolithic presence?
FLAMINGO VISITOR CENTER / Abu Dhabi
How might we elevate the potential of vernacular building techniques with geometric precision?
How do we discretize curved surfaces in a controlled manner to offer multiple spatial readings?
How do we make the most of frictions that exist between material systems and idealized complex geometries?
SINGAPORE PAVILION / Venice Biennale
How do we create an immersive space with a limited material inventory?
How do we...
Island,
Coney Island is New York City’s beachfront amusement park. Home to the famed Cyclone roller coaster, Wonder Wheel and the Mermaid Parade, the eccentric park holds a unique place in American history and in the nation’s imagination. It became a working-class symbol of the American democratic spirit because it was where the working class came to have fun.
The whimsical nature of this studio called for the design of a new YMCA center at Coney Island beginning with a found object , as a creative tool for approaching a project.
The object I had chosen was the okra, or “lady’s finger”. Detailed analysis, reconfiguaration and reinterpretion of the okra allowed for the extraction of its embedded intellegence. The architectural questions these spatial and organizational concepts in turn posed were then explored and challenged at a building scale.
Mariana IbañezWhen sliced in different directions, the okra reveals different spatial logics in the organization of the seeds — a radial distribution in the cross section, and a linear one in the longitudinal section. This poses the first architectural question — how do we enclose multiple and perhaps even contrasting spatial logics within a resolved, closed system?
Through imaginative drawings, the okra then underwent a process of repeated splicing, bifurcating, and rejoining. This resulted in the creation of organisms that morph from singular bases at the ground to a network of multiple terminating tips at the top, offering a rich diversity of spatial qualities in between. From this, a second architectural challenge emerged — what spatial techniques do we use to transition between singularity and multiplicity?
The programmatic brief for the YMCA at Coney Island provides a good opportunity for developing a design that tackles these architectural challenges. On one end of the spectrum it called for a few large, iconic program spaces such as the multipurpose hall, gymnasium, pool, and on the other end it required many small, granular program spaces in the form of residential units.
Rapid prototyping through masking tape models aided in the exploration of the different types and sizes of apertures in the curved form. Eventually, conics served as the fundamental geometry.
Illustration. “11 to 22”
3D Prints.
“The Teeth Series: Exploring seam conditions from Conic Booleans”
Masking tape model.
Iterative drawings served as the means of articulating, resolving and advancing the singularity-multicplity gradient. Eventually, we arrive at an architecture that expresses an oscillation between the catenary-like curvature in section, and the circular curvature in plan .
Such a spatiality seeks to facilitate larger-scale social congregation along the central continuous spine, as well as moments of respite and intimacy, for individuals who wander along the narrow spaces between the curved walls, that have peeled in from the exterior, or those that have punctuated from above.
First set of plans and section. RIGHT + NEXT PAGES
Final set of plans and section.
What makes a house, a home?
A house becomes a home when we understand how it works, just as we strive to understand how our own bodies work. Like that of a body, the anatomy of a house comprises organs, vessels, bones, and skin.
However, our estrangement from these vessels and organs of our houses have been preventing us from developing a relationship with them. We become reliant on others to diagnose, repair, and simply be concerned about the health of this very important space where we live, rest, recover, reflect, bond, aspire, and self-actualize.
Conceptualized during the peak of the pandemic when lockdowns and curfews were the norm, this project aspires for deeper connections between people and the spaces they inhabit.
This project was originally prepared in audiovisual format to adapt to pandemic-era virtual school. QR codes are available in the next few pages to access these videos.
RIGHT Systems of shophouses cast away to the back allies of Singapore.
Photo credit: Teemu Jarvinen @teemu.jpeg
To adapt to virtual school, the first exercise was to make physical experimental models using readily-available household materials...
...before translating them into digital models.
3mm Corrugated Translucent Polycarbonate
30mm Cellular Polycarbonate Roof Panels
150 x 150mm Base Jacks
48.6mm Ø Galvanized Steel Scaffolding Tubes
30mm Ø Galvanized Steel Tubes
Stainless Steel Scaffold Swivel Clamps Vessels
Sewage Pipes
Cold Water Ducts
Hot Water Ducts
Rainwater Drainage Pipes Electrical Wiring
HVAC Ducts Organs
Water Heater, Stove and Hood, Kitchen Sink, Refrigerator, Vertical Air Handling Unit, External Fan Coil Condenser, Laundry Machine, Bathroom Sink, Water Closet, Shower Cabinet, WiFi Router, Power Points
of back-end, support infrastructure, the anatomy of the home brings life to the space.
Study
Reading Area Laundry
Area W.C. + Sink Shower
AHU Kitchen Dining
Our home is nestled on the rooftop of an exitsing shophouse, gently tapping onto the existing supply and drainage network rising from the back alley down below.
The back alley is where all the systems of the shophouses have been cast away.
In our home, the anatomy of the house is put on display.
After all, recognition is the first step to understanding...
...how the air around you is being cooled...where your hot water is coming from...how your waste is carried away...
...and learning of the source of that constant but comforting low hum that you hear every night before falling asleep.
Located at the heart of Madrid’s oldest neighborhood is an unmistakable, colorful six-domed concrete structure — the 138 year-old Cebada Market.
At the start of the 20th century, the city council of Madrid had proposed the privitization of this piece of land for the construction of a shopping mall, resulting in the demolition of the adjacent sports complex in 2009. However, the economic crisis halted all plans, leaving a sunken area of 5,500 sqm beside the Cebada Market.
Taking things into their own hands, residents and initiative groups collaborated to reclaim this vacant space, setting up shared gardens and sports fields, and hosting various social and cultural events.
The brief calls for the conversion of the soon-to-be demolished market into an artist residence for 15 artists, with exhibition spaces, classrooms, a library and a cafeteria.
The People’s Plaza seeks to demonstrate how neglected industrial typologies might be converted into social condensors in a manner that respects the history and local politics of the site.
La Latina Madrid, Spain
Work 4.154 Option Studio 1 2020 Spring
To continue to encourage the spirit of citizen-led initiatives afforded by the plaza, it was decided that the new artist residence shall not assume the enclosed, monolithic form of the old market.
Instead, the structure of the original building shall be modified to allow typically consolidated program spaces to be fragmented and scattered around a sheltered central plaza, with the intention of reintroducing a sense of the human scale at the site.
Fully enclosed by concrete walls and bricks.
61 secondary reinforced concrete columns divide the space into 6 zones.
Expressed through speculative collages.
A substitution with deep Vierendeel steel trusses would allow a large column-free space.
How can we design fragments using the language of the surrounding context?
What if we began instead by pre-defining the sheltered plaza as a negative space?
How can we combine the fluid language of the surrounding context and the regularity of the program spaces?
Each artist studio opens up to a balcony area that serves as their personal exhibition space.
Each artist studio is connected by an internal staircase to a living space on the lower floor, that can be accessed from the central plaza.
1 Library 1 Shop
2 Classrooms
2 Restrooms
These larger programs are embedded in the ground, which is made up of a series of interconnected stairs and ramps that mediate the elevation differences at the boundary.
The Al Watheba Wetland Reserve in Abu Dhabi, a combination of natural and man-made mounds and water bodies, is famous for being the home and breeding grounds for over 5000 flamingos in the Arabian Gulf.
The brief calls for the design of a Flamingo Visitor Center with a exhibition and training spaces, a cafe, terraces and a carpark. Recognizing that Abu Dhabi positions herself as the high-tech hub of the Middle East while carrying with her a wealth of vernacular heritage, our response likewise aims to embody the spirit of blending the modern and traditional.
The Conoid Hut is a contemporary interpretation of the Areesh —the traditional desert house of the UAE built using different parts of locally abundant date palm trees. The Conoid Hut seeks to elevate the sustainable benefits and charm of this local construction technique by marrying it with a thoughtfully designed form that is geometrically complex, but not complicated.
Al Wathba Wetland Reserve Dhabi, UAE Group Competition 2020 June COLLABORATORS Tay Jing Zhi Kenneth Tung Lisa KoswaraThe building is a conoid, a 3-dimensional form with an embedded geometric dynamicism . This allows it to appear as a circle, triangle, and rectangle when viewed from different orthographic perspectives.
Echoing the undulating sand mounds of the surrounding wetlands, our enclosure emerges subtly from the ground, gently twisting and tapering inwards as it rises, terminating at a 35m-long rectangular skylight, which allows sunlight to flood the building’s interior.
The conoid is complex while being humble in its simplicity, referencing vernacular forms such as the pitched roof and rounded hut. 35m
S
E ES
W WN
Our building seeks to respond intimately to the site and its context. Its primary axis, as marked by the front and back entrances, as well as the skylight, are oriented to receive the prevailing Northwestern wind. Its perpendicular secondary axis, as marked by the side entrances, respect the direction towards Mecca.
Visitors enter the building from the northern drop-off point. Here, they are presented with two circulatory routes — the peripheral loop or the central ramp.
The 30m-long central ramp invites them to traverse the building’s primary axis. They ascend, eventually arriving at a viewing deck that draws them out of the building to take in the expansive views of the southern wetlands.
At the ground level, the roof gently lifts upwards at its eastern rim to allow trekkers returning from the wetland reserve walking trail to enter.
NFrom walking trail
QIBLAT 261° clockwise from true North
Beneath the roof superstructure, discrete rooms are arrayed along both sides of the central ramp. Folding and rotating glass door systems allow visitor activities to spill out of the rooms into the naturallyventilated peripheral spaces beneath the monolithic gesture of the roof. To walking trail
The operable roof is fitted with rotatable thatch modules made of compressed date palm fronds. Connected to a control-arm lever, users can manually vary the degree of natural ventilation, daylighting and thermal comfort to suit their changing needs.
After exploring the visitor centre and the wetlands, visitors conclude their experience with a cup of Gahwa, a popular traditional Arabic coffee at the cafe, as they enjoy a framed vista of nature and architcture coalescing harmoniously.
Ø15mm stainless steel handlebar
over-center tension spring mechanism
natural rubber control arm stopper
Ø100mm Borax-treated palm trunk post pole
60mm thatch sheet made of compacted date palm
12.5mm matte-coated plywood panel
Ø50mm Borax-treated palm trunk purlin pole
Ø100mm Borax-treated palm trunk rafter pole
Ø10mm stainless steel pipe with T-hinge and flange
Ø100mm aluminum pipe clamp attachment
Ø15mm stainless steel control arm lever
Beyond novel and iconic forms, the quality of buil ding massings and envelopes is largely dependent on the discretization and panelization of the base form. This discretization process not only has agency in preparing the base form to respond to available dimensions and natures of building materials, it also has significant potential in discovering an emergent aesthetic logic that becomes part of the architecture and spatial experience itself.
Two-in-One is a short exercise that explores the controlled discretization and panelization of a geometry based on the Hyperboloid of Revolution, a doubly-ruled surface. It seeks to maximize the richness of spatial qualities of a single object by designing it to embody two contrasting readings, woven together by a rhythm of sweeping blades.
Two hyperboloids of revolution were rotated, intersected and spliced to create a dynamic geometry with two contrasting readings from different angles. Object 1 was made using PLA filament 3D printing and piano wire inlay.
Construct two circles of 160mm diameter spaced vertically apart by 160mm. Construct isocurve of 135°.
Perform a 360° revolution of the isocurve to create a Hyperboloid of Revolution.
Duplicate the Hyperboloid of Revolution and rotate by 90° about the y-axis to form an intersection.
STEP 4 Perform a Boolean split to obtain a single module.
STEP 5
Mirror about the xy-plane to add a bottom module.
STEP 6
Rotate the bottom module by 90°.
STEP 7 (Plan view) Divide circular edge into 32 arcs of 11.25°, as it is a factor of the original 135° isocurve.
STEP 8
Extract the isocurves of the top and bottom modules at every 11.25° interval.
Isocurves are joined to form 3 loops and 2 open polylines with ends terminating at each of the 4 apices.
Each doubly-ruled segment was then panelized into one planar quadilateral and one triangle. These panels were trimmed against one another to achieve a zig-zagged rim. Object 2 was made with ZCORP 3D powder printing and CNC-ed aluminum sheet plating.
Reconstruct all curves into straight segments.
Delete clashing apex slopes to give a continuous, sweep in the shape of an “S”.
Use straight edge segments and isocurves to construct planar quadilaterals (white) and triangles (yellow).
Materials are assigned in an alternating fashion — yellow indicates where CNC-ed aluminum panels will be affixed to the ZCORP 3D powder print.
NURBS modeling softwares have granted our generation of designers the unprecedented ease of generating curved surfaces with infinite plasticity. While this has unlocked enormous sculptural potential in built architecture, what we also observe is a culture of designed geometries that are extremely complex but not necessarily controlled nor understood when it comes to its physical realization.
Such a lack of dexterity is observed in situations where fabrication is heavily reliant on highly-customized processes and parts, and consequently contingent upon the availability of time, money and labor — resources that when taken for granted leads to project setbacks and design failures.
In other situations, this lack of control is physically manifested as unintended, unresolved clashes between the idealized geometries and the realities of the material systems — a jarring edge condition, a discordant patterning, a material held in place at its breaking point...etc.
Constructive Collisions aspires to avoid such scenarios. It is a set of 15 studies that seeks out productive frictions between infinitely precise geometry and the real physical and spatial constraints of material and joinery tolerances. The solutions discovered are scalable and serve as a stepping stone towards a culture of geometric and material conscientiousness in our built environment.
We began by selecting a geometry each from five elementary surface families — Spherical , Toroidal , Ruled , Cylindrical and Conical . We intentionally selected geometries that were the advanced derivations of their elementary forms, as the new conditions created, such as edges or variations in isocurve directionalities, bring out the less familiar aspects of their geometric nature for us to confront.
We then selected three families of tectonic systems typical in architecture construction — Membrane (monolithic continuous surfaces), Plate (discrete surfaces) and Stick (linear members) systems.
Over the course of two months, we designed and prototyped parametric schemes for each of the 15 possibilities in the 5x3 matrix.
The Reuleaux Tetrahdron is the intersection of four spheres of equal radius, centered at the vertices of a regular tetrahedron. Unlike a pure sphere that has constant curvature and zero edges, the Reuleaux Tetrahedron has four spherical faces that join at six circle-arc edges.
A pure sphere would typically require triangular or polyhedral panelization, as seen in geodesic domes and Platonic solids. In these schemes, we explore alternative approaches for expressing spherical surfaces.
The bulge from the inflated ETFE pillows approximates the spherical surface.
The spherical surface is approximated into coursing lines and flat panels that flow across the edges in continuous loops.
Utilizing only small pieces, the overall complexity of the spherical surface is incorporated by the varying depths of joinery slots on individual stud members.
While a pure torus is the simple revolution of a circle about an axis, the Ring Cyclide is the surface generated by rotationally sweeping through a pair of circle cross sections of different diameters, bound by an external circular edge.
Like the torus, the surface of the Ring Cyclide shifts between positive and negative curvature, requiring uniquely flexible solutions from the materials.
The required flexibility is achieved by the deformation process, thus the entire geometry can be formed by just two pieces held together by a single binding barrel.
The pre-tensioned springback of coiled steel helps to achieve the circular profile in one dimension, but requires unique cut patterns in the other dimension to avoid collisions.
The flexibility of a thin strip of rattan expresses the entire surface as one continuously wrapped spiral.
Ruled surfaces are the the set of points swept by a moving straight line. The Conoid on the right is generated by sweeping a line through a vertical line and a quarter arc of a circle rotated 45 degrees from the line.
The challenges with the ruled surface of the conoid lie in the resolution of the changing angles. Each tectonic system reconciles the angle differently.
Crimps are used to set up regular pinch points, so that the angle variations are naturally subsumed into the stretching of the tensile fabric, made visible by the creasing pattern.
The standing seam joinery incorporates the angle changes into the custom profie of the unfolded panels, that are press braked into shape and slotted together.
The variations in angles are resolved through the varying density of twine-knot spacers between the wooden dowels.
The Tricylinder is the intersection of three orthogonal cylinders, giving it 12 cylindrical surfaces that join at 24 circle-arc edges.
As with pure cylinders, the unique challenge is maintaining constant curvature in one direction.
Chainlink as a membrane system effectively achieves linearity in one direction. However, slumping occurs at the center of the span due to the build up in tension from the stretched coils.
The linear grain of wood veneer creates rigidity across the span when locked taut with adjacent panels. Here, the regularity of the curvature depends on the regularity of the wood grain.
Linear members such as wooden louvers are especially conducive to this application, since they maintain clear rigidity in one direction.
The Sphericon is formed by cutting a bicone (two cones, with an apex of 90 degrees) in half and rotating one half by 90 degrees. This creates one continuous surface (as indicated by the loop) and only two semicircular edges.
In conical surfaces, the challenge lies in the material resolution of the convergence of isocurves at the apexes.
The canvas sailcloth scheme terminates before the apex, using a grommet joinery to cut the tip off of the cone.
In the shingles scheme, the convergence is subsumed into the narrowing profile of the cork panel, and its semi-flexibility allows for wrapping to fit the curvature.
Each physical study fits within a bounding box of approximately 8” x 8” x 8”. While we observe that certain material systems are naturally more pliant towards certain surface geometries, we learn that confronting discordant interactions can also lead to refreshing and suprising results.
As designers, we get to operate between two modes — we can either select more harmonious resolutions of geometry and material to ease the difficulties of construction, or, we can lean into the discord to produce new generative outcomes from standard material systems. Both approaches benefit from a strong grasp of geometry and material tectonics.
Arsenale, Venice, Italy
Singapore Team 2018 Venice Biennale 2017 Dec - 2018 May
No More Free Space, 2018 Venice Biennale
In response to the overall theme of the 2018 Venice Biennale, FREESPACE , the Singapore Pavilion was titled No More Free Space — alluding to the land scarcity and consequently resource scarcity that the city-state has been challenged with since its establishment. The pavilion sought to showcase the works of local architects that have dealt with these constraints in innovative ways to produce inspiring works of architecture. Our team wanted the centerpiece to embody this same spirit of creativity.
While Singapore lacks natural materials, synthetic ones are aplenty. One of such materials at our disposal were bundles of 2m-long, 12mm-diameter, clear acrylic rods. Our innovation challenge — how do we turn something straight, rigid and discrete into something fluid, interconnected and immersive? In 4 months, with over a hundred pairs of hands, we transformed 900 acrylic rods into a dreamlike “cloud” of 1414 handcrafted knots, suspended in the air at the Arsenale venue in Venice.
The first step was to come up with a heating and knotting logic. The main challenge lay in manipulating molten acrylic rods in a neat and controlled fashion.
Revisiting the knots that I learnt from Girl Scouts, the answer lay in the Reef Knot. Unlike most other knots that require multi-directional weaving motions, the Reef Knot could be achieved by linearly slotting together two identical parts. With 4 loose ends in each module, the natural spatial geometry to pursue was the tetrahedron, with its structural and spatial properties.
The cutting and lathe-drilling of acrylic rods for the dowel joints were outsourced to a local factory, while the hand-forming of the ~1500 tetrahedron acrylic modules was accomplished by a total of 100 students from NUS and SUTD, as well as a team of 20 construction site workers.
To maintain geometric precision during fabrication, two types of simple plywood jigs were designed — the Spoon Jig and the Tetrahedron Jig.
Last but not least, we travelled to Venice a month before opening day to oversee the installation of the acrylic modules and steel support structure by local builders. LED lights were affixed to every module in the topmost layer above the steel panels, so that colour could permeate the transparent constellation of acrylic knots.
steel hangar painted black anchored to timber structure
existing timber truss steel wire
50mm steel hollow section painted black
perforated ceiling panel steel frame structure