
6 minute read
Your go-to partner for food processing and packaging tech
In January 2020, Bosch Packaging officially stepped out of the Bosch brand and into its own identity – Syntegon Technology. Food Review looks at how 150 years’ experience in future-orientation and a premium technology portfolio has resulted in a reliable and flexible company.
With over 2 000 patented inventions, 6 100 employees and over 64 000 installed machines, Syntegon sets standards for others to follow when it comes to developing innovative packaging solutions. The company is focused on delivering tailored manufacturing processes designed to make high-quality products with the utmost reliability. Everything is available from a single source: from the 150m production line to the 0.5mm spare part.
A strong focus for Syntegon is its end-of-line packaging machines. The technology includes the Kliklok Cascade Loading system with direct-drop product timing and loading; the Kliklok new BEC entry-level endload cartoning machine and mid-range MEC endload cartoner. For case packing the following units round off the portfolio: Elematic 1001 (RSC), Elematic 2001 for the wrap-around case and high-speed toploader Sigpack TTM.
The Kliklok Cascade Loading system uses a rotor vane system to drop products on the product infeed conveyor flights of endload cartoners, such as the Kliklok MEC. It typically handles 113g or heavier bags of food and stands out for its hygienic stainless steel design, which is IP65-rated.
The independent design and computer logic of the Cascade Loading system support electronic indexing, to fill each flight of the cartoner’s infeed conveyor. With the cartoner operating at matching speeds and higher efficiencies, manufacturers will have less wear and tear due to “overrunning”. If one bagmaker is temporarily removed from operation due to reduced product availability or maintenance needs, the remaining units can be electronically reassigned to maintain full efficiency in filling every flight of the cartoner. Simple operation controls enable pocket rededication without disturbing the system’s ongoing performance.
The Kliklok MEC is designed to handle a wide range of carton sizes and packs up to 170 cartons per minute. “We’ve designed the unit to meet our customers’ needs for future-proof sanitary construction, ease of use and maintenance. It also stands out for its fast format changes and good access,” says Janet Darnley, product manager at Syntegon Technology.
The endload cartoner has full-length doors that allow walk-in access for easy changeovers and maintenance. Format changes are toolless, easily repeatable, and can be completed by just one operator in ten to 12 minutes. With its open-channel stainless steel frame and angled surfaces, the machine complies with stringent sanitary standards. The unit is IP65 washdown-rated, which makes it easy to clean. An additional feature is the optional open flap detection to prevent opened or partially opened cartons from exiting the machine, which ensures high product quality.
The dream of having an easy workday and a lot of flexibility in packaging comes true with the new Elematic 2001 case packer. The new machine offers a reduced footprint and maximum flexibility in terms of pack styles. Whether you require a full wrap-around, a tray with hood, tray without hood or ledge tray – everything can be packed on just one machine. The system offers high performance, a small footprint and quick changeover times.
The Elematic 2001 case packer impresses with its flexibility. The flexibility of this case packer means that all wrap-around pack styles, such as full wrap-around and trays with and without hood, can be packed on one machine. The unit can also handle different format sizes and packaging designs. “Up to 100 designs and more are possible. We understand the market of shelf-ready packaging and want the machine to pack a wide range of pack styles. Customer requirements for unique packaging designs and format sizes are always individual. Syntegon works closely with its customers to develop suitable solutions. The primary target is to create an attractive and transport-safe case design as well as the possibility to place it on the shelf in a time-saving and resource-saving manner,” she elaborates.
KEEP UP WITH RISING PRODUCTION DEMANDS
The Sigpack TTM was a new solution for one of the biggest key players in Latin America. Among their most popular product ranges are their chocolate and cereal bar brands. To keep up with rising production demands, the manufacturer was looking for a way of upgrading the previously manual secondary packaging process to a faster, automated and more reliable solution.
The cartoner had to be flexible enough to package bars of different shapes and sizes into cartons in packs of 6, 12 and 24 − without causing lengthy downtimes. Besides this, a high output would need to be realised within the compact layout of the existing production facilities.
During their search for suitable technology, the company was drawn to the Sigpack TTM toploading equipment from Syntegon. The TTM’s operator-friendly design with fail-proof, fast and fully-reproducible changeovers, as well as its flexible infeed possibilities, won over the Latin American team.
In close collaboration with Syntegon, a bespoke interface between the TTM and other upstream packaging equipment was developed. A feeding wheel copes with the high speeds that connect both elements of the line to ensure a smooth and harmonious production flow. The Sigpack TTM’s streamlined design meant installation and start-up was swift. With the launch of the new line, the changeover times for cereal bar production was reduced from one hour to just ten minutes.
At the factory, the new customised interface ensures that flow-wrapped cereal bars are delivered continuously and at even distances to the discharging conveyor of the toploader. Arriving lengthways, the flow-wrapped bars are then gently picked up by an FWV feeding wheel, which turns the products 90 degrees before placing them sideways into a PGR grouping unit, ready for cartoning.
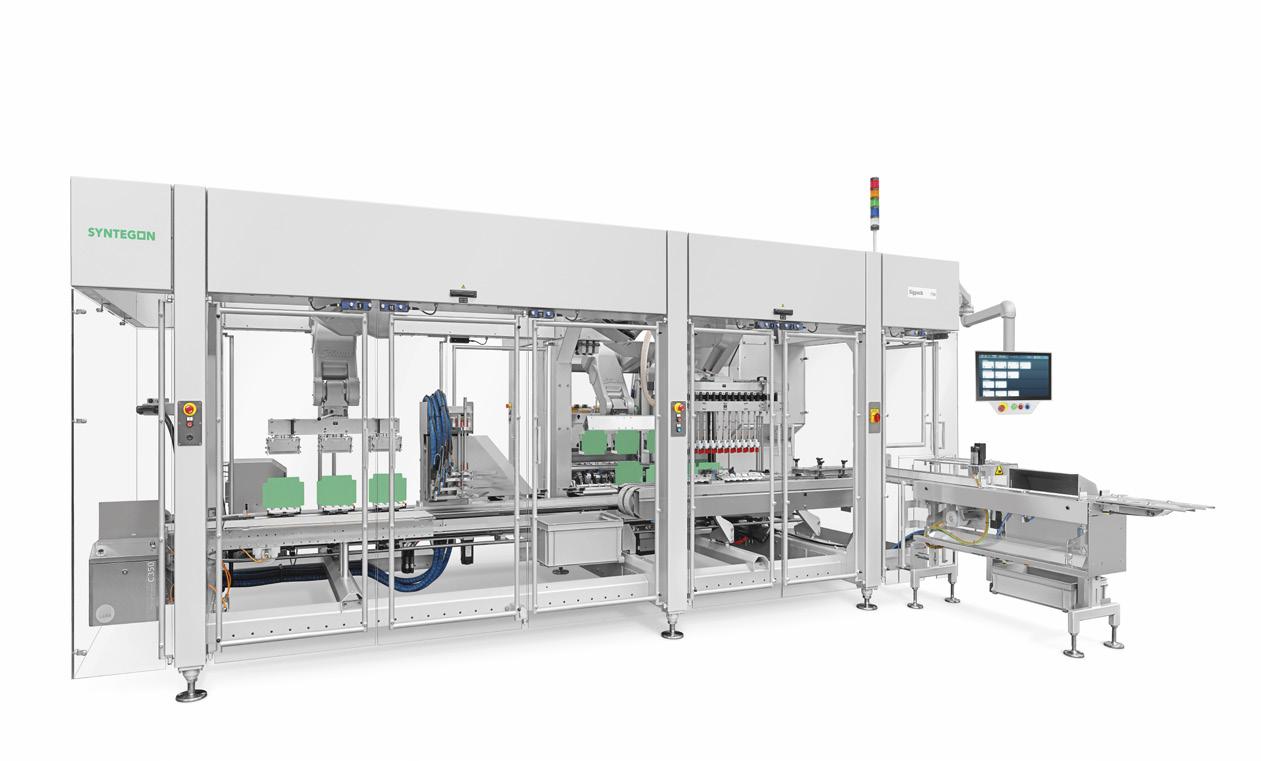
The endload cartoner has full-length doors that allow walkin access for easy changeovers and maintenance
Carton erection can be an Achilles heel in automated packaging solutions as it has the potential to slow down productivity. Difficult to handle carton materials and formats can decrease production output, result in faulty boxes and jam the production line. The Sigpack TTM is designed to eliminate these issues and achieve a reliable output with its quick-change format parts and fullyreproducible format settings and precise carton handling.
With its capacity to package bars of various sizes in four carton sizes using seven different configurations, the Sigpack TTM has been a resounding success.
The new topload cartoner has allowed the company to reach a level of flexibility and production output that they were not previously able to achieve with former manual efforts. The automated process, lightweight format parts and tool-free changeover mean that they have been able to speed up changes between products from 60 minutes down to just ten minutes. A single operator can now run, facilitate the changeover and clean the machine. •
Quote:
The Kliklok MEC is designed to handle a wide range of carton sizes and packs up to 170 cartons per minute. “We’ve designed the Kliklok MEC to meet our customers’ requirements for future-proof sanitary construction, ease of use and maintenance. It also stands out for its fast format changes and good access” - Janet Darnley is the product manager at Syntegon Technology.