Understanding Depyrogenation Tunnels: A Comprehensive Guide
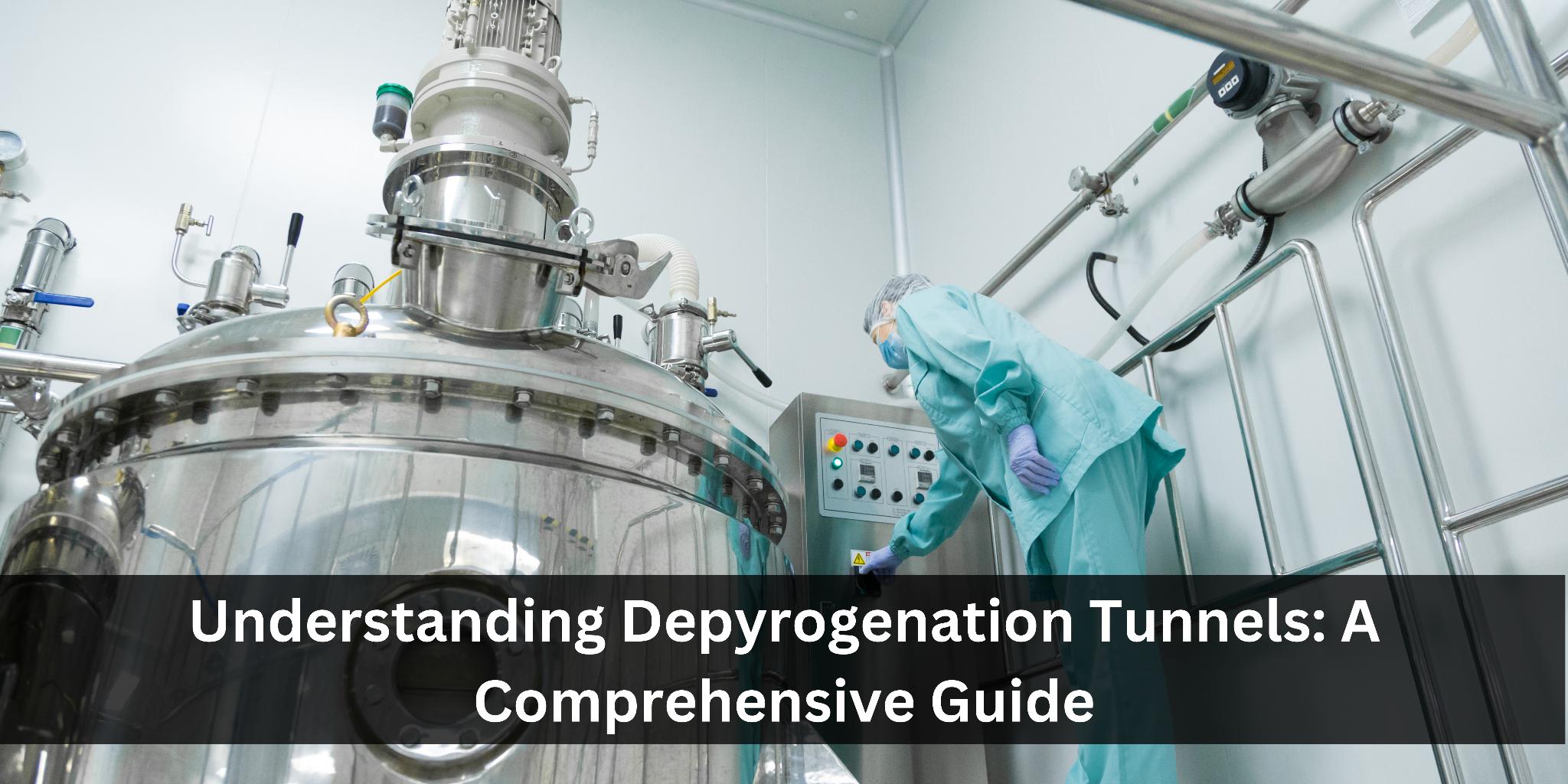
In the realm of pharmaceutical manufacturing, ensuring the safety and efficacy of products is of paramount importance One crucial step in this process involves depyrogenation, which refers to the removal of pyrogens – substances that can cause fever or other adverse reactions – from pharmaceutical equipment and containers. Depyrogenation tunnels play a pivotal role in achieving this outcome In this comprehensive guide, we delve into the world of depyrogenation tunnels, exploring their significance, functioning, and the key considerations when choosing a dependable depyrogenation tunnel manufacturer.
Introduction
Depyrogenation, an essential step in pharmaceutical production, ensures that medical equipment and containers are free from substances that could pose a health risk to patients. Depyrogenation tunnels play a pivotal role in achieving this outcome, making them a critical component of pharmaceutical manufacturing processes
What are Depyrogenation Tunnels?
Depyrogenation tunnels are specialized equipment used in pharmaceutical and biotechnology industries to remove pyrogens, which are fever-inducing substances, from glass containers, vials, and other equipment Pyrogens can originate from various sources, including water, raw
materials, and production processes These tunnels use high temperatures to eliminate pyrogens and attain the desired level of sterility.
The Importance of Depyrogenation
The presence of pyrogens in pharmaceutical products can lead to severe adverse reactions in patients. Fever, shock, and inflammation are potential consequences of pyrogen-contaminated products Depyrogenation ensures patient safety by eradicating these harmful substances and maintaining the efficacy of pharmaceutical products
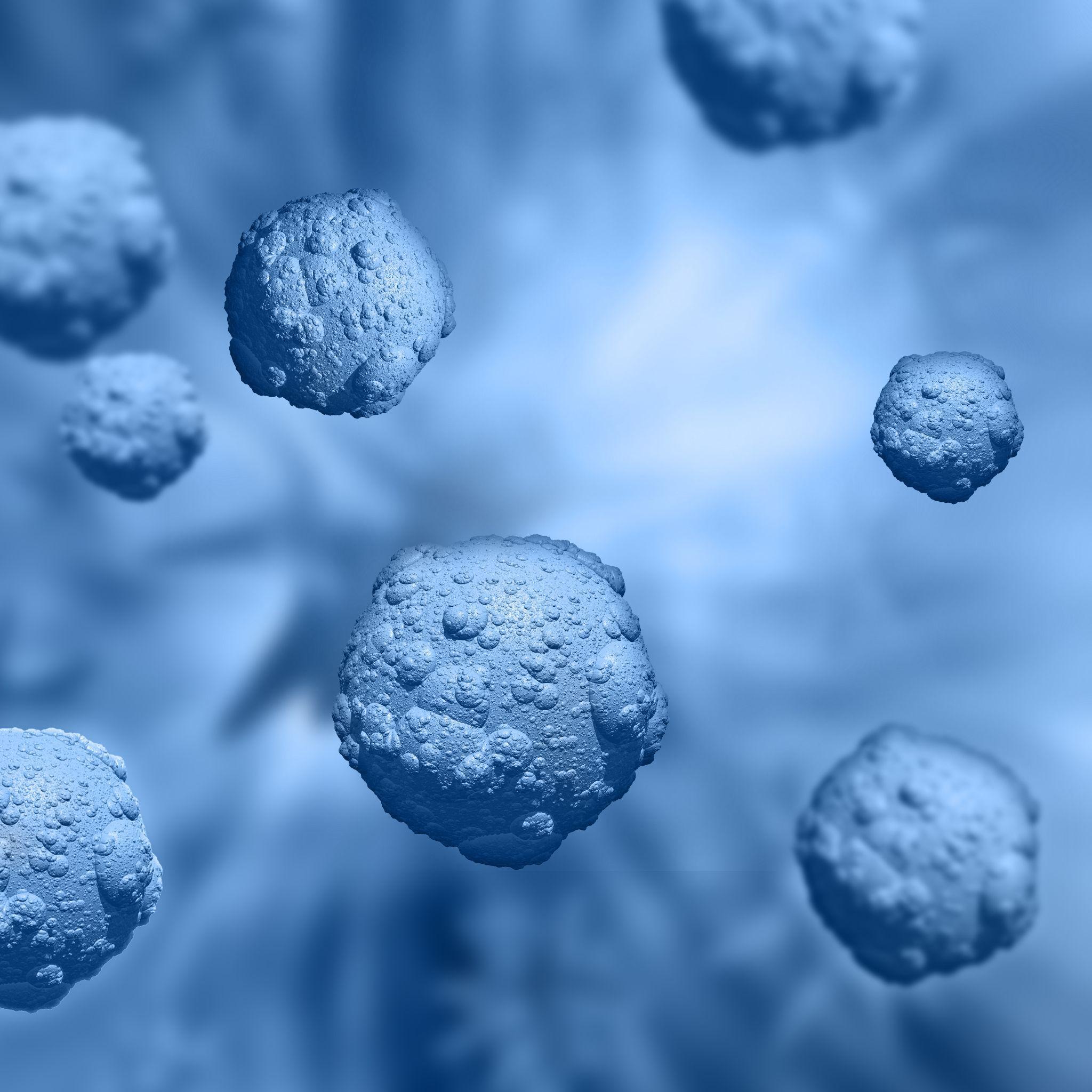
How Do Depyrogenation Tunnels Work?
Depyrogenation tunnels employ a combination of dry heat and a carefully controlled conveyor system to process pharmaceutical containers The containers pass through a heating zone, where high temperatures effectively break down and eliminate pyrogens The uniform distribution of heat within the tunnel ensures that all parts of the containers receive sufficient heat treatment
Types of Depyrogenation Tunnels
There are two primary types of depyrogenation tunnels: batch tunnels and continuous tunnels. Batch tunnels process a set quantity of containers in each cycle, while continuous tunnels offer a more streamlined and continuous depyrogenation process. The choice between these types depends on the production volume and efficiency requirements.
Factors to Consider When Choosing a Depyrogenation Tunnel
When selecting a depyrogenation tunnel manufacturer, several factors come into play The tunnel's size, heating capacity, conveyor speed, and compliance with regulatory standards are critical considerations Additionally, the manufacturer's reputation, customer support, and the tunnel's cost-effectiveness should also be evaluated.
Advantages of Using Depyrogenation Tunnels
Depyrogenation tunnels offer numerous advantages They provide a reliable and consistent method for eliminating pyrogens, ensuring product safety Their automated processes reduce the potential for human error, and they are versatile enough to accommodate various container sizes and types
Challenges in Depyrogenation Processes
While depyrogenation tunnels are effective, challenges can arise Achieving uniform heat distribution, preventing container breakage, and addressing particulate contamination are among the common challenges manufacturers face
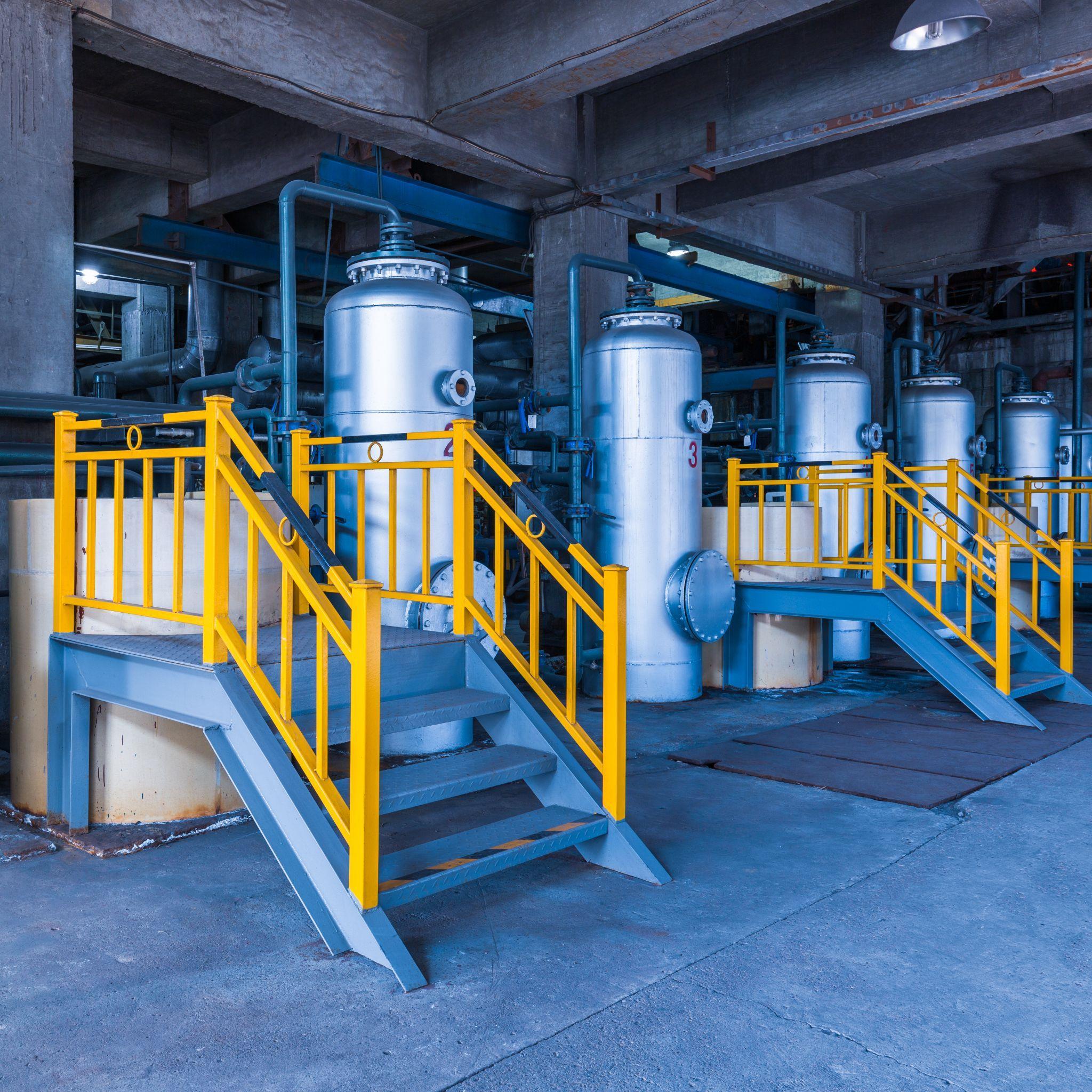
Maintenance and Validation of Depyrogenation Tunnels
Regular maintenance and validation are crucial to ensure the proper functioning of depyrogenation tunnels. Cleaning, calibration, and adherence to regulatory guidelines are essential to maintain their efficacy and compliance
Key Players in Depyrogenation Tunnel Manufacturing
The pharmaceutical equipment market boasts several key players in depyrogenation tunnel manufacturing These manufacturers offer a range of innovative solutions to meet the diverse needs of the industry
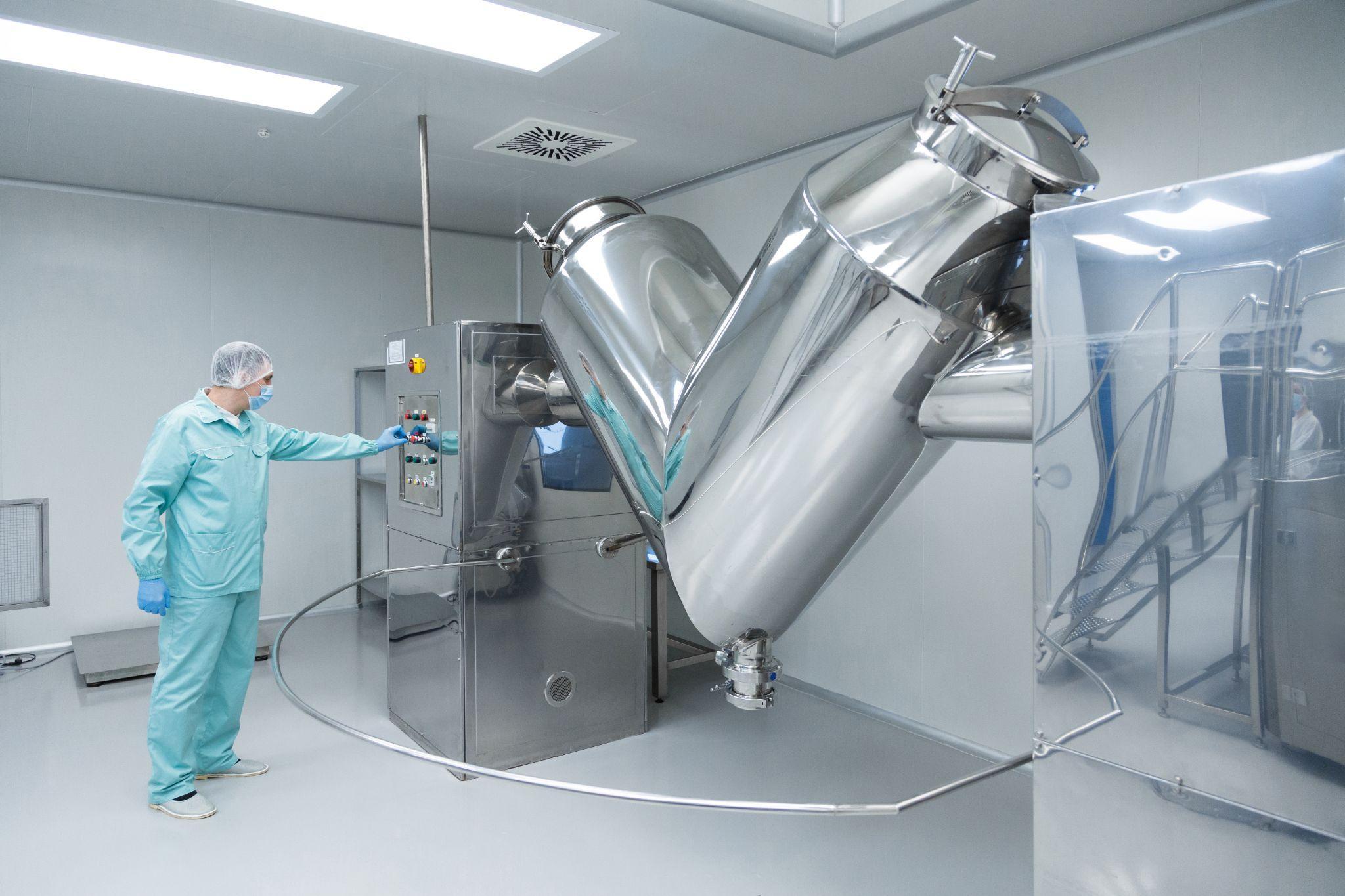
Comparing Depyrogenation Tunnels with Other Sterilization Methods
Depyrogenation tunnels have distinct advantages over other sterilization methods, such as autoclaving or chemical disinfection Their ability to achieve high temperatures without moisture makes them suitable for sensitive pharmaceutical products
Regulatory Guidelines and Compliance
Regulatory bodies like the FDA provide guidelines for the validation and operation of depyrogenation tunnels Manufacturers must adhere to these standards to ensure the safety and quality of pharmaceutical products
Innovations in Depyrogenation Technology
Advancements in technology continue to shape depyrogenation processes. From enhanced heat distribution mechanisms to real-time monitoring, these innovations further improve the efficiency and reliability of depyrogenation tunnels