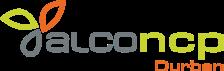
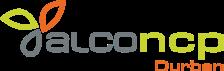
L A D UMA
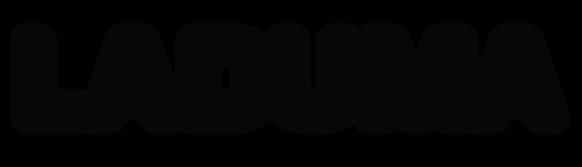

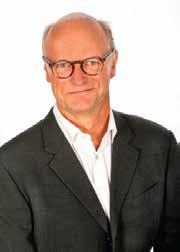
Peter Starling, Managing Director

Message from the MD
We set our 2024 goal to further improve operational efficiencies with stable, high levels of production with a focus on consistent performance, making the operating procedures required to achieve these performance levels routine and the “new normal”. Since our February shutdown we have made great progress in this regard, the complexity of our production operation means there are always issues but managing them is becoming less crisis management and more routine operation. The consistent supply of product requires a similarly consistent market in which to place the volumes and as we well know, markets tend to be unpredictable and volatile, especially when customers are spread throughout Africa. The breakbulk logistic constraints in Durban and other African ports, combined with regulation changes in some countries have put pressure on the marketing and distribution teams to keep pace with production. Subject to market prices we have now increased regular bulk shipments to Europe, this reduces storage and production limitations allowing the plant to operate at consistently higher rates. This stability supports continued efficiency gains and achieving the new normal. As we progress toward making plant operations routine, we must continually look to the future. Our ongoing value stream mapping initiatives are generating excellent results, the reduction in time and process steps for maize offloading and DDGS loading are great success stories. The focus is now on alcohol-loading procedures which will eventually be applied to every aspect of our business. These projects are not merely about examining our current methods; it's an opportunity to reimagine how we work. By questioning our processes and seeking improvements, we're positioning ourselves to be more efficient and responsive to market demands, making progress toward our value of Simplicity. Achieving simplicity is not easy, consider the iPhone, it appears easy to use, but the effort that went into making it that way is considerable, I encourage each of you to engage fully with these initiatives - your insights and ideas are crucial to their success. I recently attended the Alcogroup’s 35th anniversary celebrations and during the various presentations and events, I was able to reflect on AlcoNCP’s remarkable journey and the dramatic change we made by switching our business and operational model to processing maize. The opportunities this creates for future growth, efficiencies, volumes, sustainability, and new products are immense and made a little bit easier as we can follow the experiences of our European operations. I want each of you to feel the same enthusiasm for our future that I do. Whatever your role, you're contributing to something meaningful. We're not just manufacturing alcohol; we're inspiring the realisation of potential through relationships to achieve extraordinary outcomes.
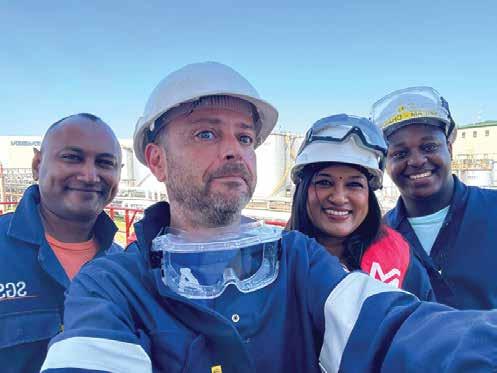
Seen during the loading of the Bow Gemini are (f.l.t.r) Deon Naidoo, SGS Surveyor, David-Taelman Hermans, Logistics Manager Alco Group, Lorraine Mudaly, Distribution and Compliance Manager, AlcoNCP and Senzo Mtshali QA/QC Technician, AlcoNCP. (Insert) Renisha Joseph, Customer Services Controller – Exports, AlcoNCP.
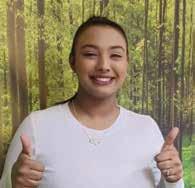
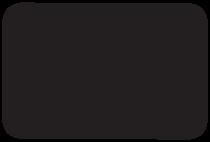
AlcoNCP recently completed its first bulk ethanol shipment for the year, marking a milestone. This export included sustainable fuel-grade ethanol and neutral ethanol, making its debut in Europe for cosmetic and pharmaceutical ts voyage to Durban, rerouted to Richard’s Bay due to port delays. After loading, the vessel arrived in Durban, and the process proceeded smoothly from May 6th to 9th. According to Lorraine Mudaly, Distribution and Compliance Manager, “This operation demonstrates AlcoNCP's commitment to excellence and effective teamwork, emphasising innovation and collaboration in achieving corporate goals.”
Cover: Kiara Premlall, Production Manager and Logan Naicker, Site Logistics Manager are all smiles thanks to Shalini Naidoo, the Process Engineer's excellent work on refining our Denatured Neutral Alcohol (DNA) process, ensuring high rates of on-spec product which eliminates the scramble for storage space for product that has to be reworked.
Gold for AlcoNCP
Monde Selection International Quality Institute
Since its first participation in 1969, AlcoNCP has been awarded Gold or Grand Gold Quality Awards over 55 years from Monde Selection.
This demonstrates our outstanding people and their commitment to continuously offering our customers the best quality product,” said Peter Starling, Managing Director at AlcoNCP.
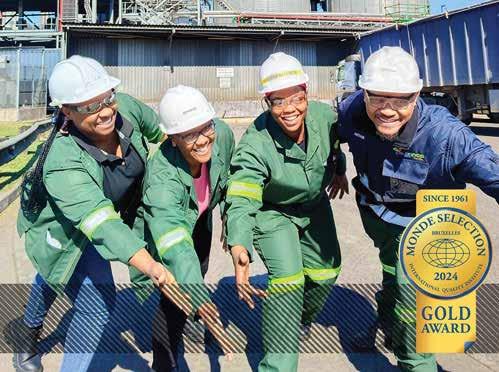
Embracing 6S for Enhanced Efficiency and Continuous Improvement at AlcoNCP
We recently caught up with Colin Mkhize, Instrument Superintendent, and Morgan Murefu, Engineering Manager, who have been at the forefront of this transformative journey. Here's a glimpse into how the 6S project is progressing and the impact it is having across our departments.
Progress and Achievements in the 6S Project
Since the integration of the 6S methodology into the Engineering Workshop, significant strides have been made. Weekly 6S audits reflect an impressive average score of 78%, just 2% shy of our 80% target. Colin and Morgan shared that t he use of a dedicated 6S board to log improvement opportunities and due dates has been instrumental in addressing crucial 6S matters efficiently.
The Genesis of 6S at AlcoNCP
The journey with 6S began in June 2023, inspired by training on Lean Manufacturing Fundamentals provided by Morgan and the Durban Chemical Cluster (DCC). Among the lean manufacturing tools explored, 6S stood out for its potential to increase efficiency, standardize operations, and boost productivity. Morgan recognised the benefits of this tool and spearheaded its implementation in the workshop.
Tangible Benefits of 6S Adoption
The adoption of 6S has brought about noticeable improvements in productivity, collaboration, and workplace culture. The Engineering Workshop, plant, and office environments have all benefited from enhanced organisation, streamlined processes, and a more engaged workforce.
Methodical Implementation Strategy
The successful rollout of 6S was achieved by dedicating a specific time each week for the team to focus on 6S activities. Emphasis was placed on embedding 6S into daily routines rather than treating it as a periodic task.
The implementation followed a structured approach, tackling each 'S' systematically:
1. Sorting: Identifying and removing unnecessary items from the workshop.
2. Setting in Order: Ensuring every item has a designated place.

3. Shining: Cleaning and inspecting equipment to identify defects.
4. Standardising and Sustaining: The current focus areas, are aimed at maintaining the achieved standards and creating consistent practices across the workshop.
6S aligns seamlessly with the company’s Sustainability Compass, fostering a culture of safety, efficiency, and continuous improvement. It promotes not only a productive working environment but also establishes sustainable practices that support our long-term goals.
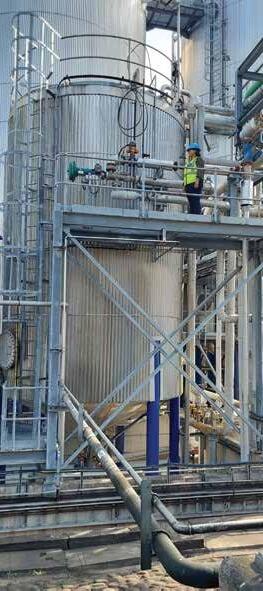
Sustainable Water Management
The jet cooker on the caustic tank is to be replaced with a heat exchanger to allow for the recovery of steam condensate.
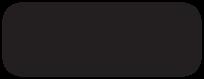
The initiative of using cooling water as seal water for evaps vacuum pumps was done and this flow rate.
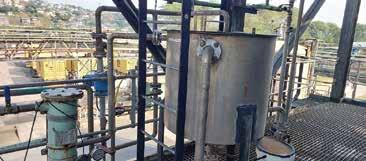
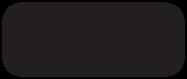

Water scarcity is a pressing global issue, and South Africa is no exception. In response, AlcoNCP has embraced sustainable water management practices. Louie Pillay, Utilities Manager at AlcoNCP comments, water-saving measures, we not only reduce our environmental impact but also ensure a reliable water supply for our manufacturing processes in the future.” Pillay provided us with a list of activities geared towards just
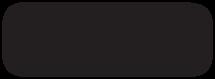
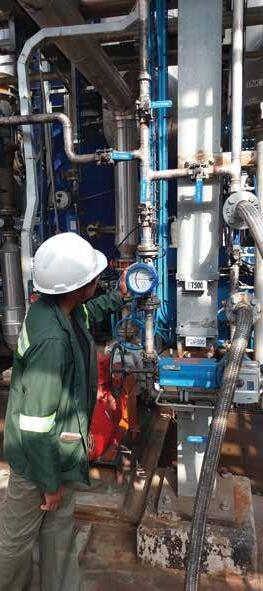
We’ve installed systems to reuse and recycle wastewater from manufacturing processes. This reclaimed water significantly reduces freshwater consumption.
We continuously review manufacturing processes to identify opportunities for water efficiency. Some of these projects include optimising equipment, adjusting production schedules, and minimising water-intensive operations without compromising productivity. Examples of such initiatives include demin water reduction at the distillery and boilerhouse by process optimisation and automation.
Fixing Leaks and Preventing Wastage:
We regularly inspect equipment and pipelines for leaks, drips, or malfunctions.
Investing in Water-Efficient Technologies:
We have upgraded some of our equipment and machinery to incorporate water-saving features. For example, installing low-flow faucets, utilising water-efficient equipment and installing steam traps and heat exchangers for condensate recovery can yield substantial water savings over time. New water treatment monitoring instrumentation and automation promises to deliver water and chemical savings.
Educating and Empowering Employees:
We continually raise awareness among employees about the importance of water conservation and encourage staff members to report leaks, suggest improvements, and actively participate in water conservation initiatives.
Engaging with Local Communities:
AlcoNCP has fostered a partnership with their local communities to address water-related challenges via Adopt-A-River, an NPO with a mission to clean riverbanks in KZN. The project has improved water literacy and enhanced the quality of water in the Umgeni River on which banks we operate.
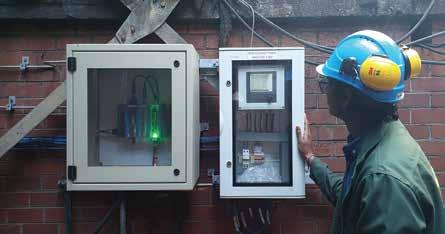
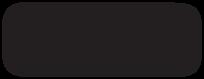

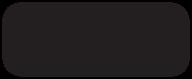

FIC500 was installed to accurately control the denim water supply flow rate to the vacuum pumps in the distillery.
A conductivity sensor was installed on the main cooling tower to control the blowdown pump. This has allowed for more accurate
Louie Pillay (left), Stanley Sijadu (centre) and Patrick Dladla (right) illustrate steam traps on the two-bar
Navigating Towards Success
Understanding our Sustainability Compass
AlcoNCP operates with a clear purpose and set of values, and central to this is the company’s Sustainability Compass. This tool directs AlcoNCP towards its goals and ensures ongoing success.
Let’s unpack the compass.
Purpose: AlcoNCP's aim is straightforward: to inspire the realisation of potential t through relationships, to achieve extraordinary outcomes.
Values: AlcoNCP upholds several core values essential to its operations. These include Passion, Collaboration, Excellence, and Simplicity. Passion drives dedication and belief, Collaboration fosters teamwork and partnership, Excellence sets high standards, and Simplicity seeks straightforward solutions.
What are the keys to our success?
AlcoNCP recognises three critical factors contributing to it’s success: Volume, Efficiency, and Quality. These elements are prioritised to ensure our operations are effective and sustainable in the long term. With these principles in mind, AlcoNCP continues its journey, focused on growth, innovation, and positive impact while remaining true to its purpose and values with competent committed people onboard.
On the topic of our sustainability compass Peter Starling, managing director comments, “At its core is the purpose and belief that true growth and achievement stems from the connections we build with those around us. These relationships are the catalysts that unlock our individual and collective potential. By fostering an environment of collaboration, we create a space where ideas can flourish, challenges can be overcome, and boundaries can be pushed. Together, we can achieve extraordinary outcomes that transcend what any one of us could accomplish alone. This sense of purpose has sustained AlcoNCP for 158 years, this significant outcome is more than its products, technology, leadership, and team at any given moment in its history. Through AlcoNCP, individuals can cultivate a career, get married, buy a house, and support their children's education. We have staff with 30-40 years of dedicated service, 3rd generation employees and have maintained enduring relationships with certain customers over 50 years.”
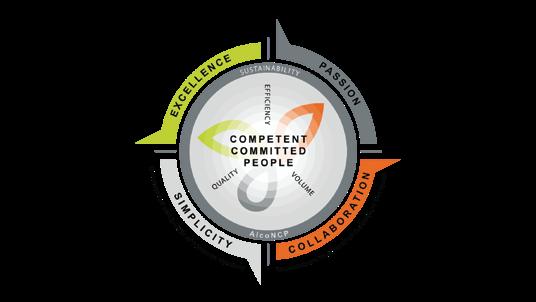
How does the sustainability compass guide employees in their day-to-day work? Laduma asked a few of our communication facilitators for their views.
Timothy Moodley, SHEQ and Fire Officer explains, “Our company’s compass aligns with Safety, Health, Environment, and Quality (SHEQ) standards. Safety is my priority and a clear company vision is important for setting goals. Our compass advocates sustainability as a means to secure a better future.”
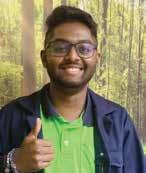
Nikita Ajodha, Procurement Officer emphasised the sustainability compass's role in streamlining operations and fostering accountability, with sustainability being crucial for future success and resource preservation.
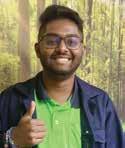
Zama Ngewu, SHEQ Intern underscores sustainability's importance in contributing positively to society and aligning efforts with the company's goals, securing a prosperous future for all.
Renisha Joseph, Customer Services Controller discusses how the company’s sustainability compass provides a clear vision that guides her team's efforts. “While sustainability is essential for our longevity it’s also addressing environmental impact and resource efficiency,” she says.
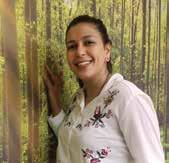
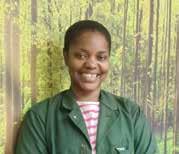
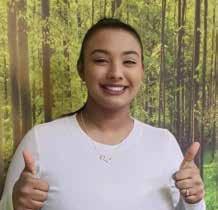
Rashina Munsamy, QAQC Technician says that the sustainability compass serves as a guide, which directs her focus while she works. “It also helps to ensure that everyone works towards shared goals. The clear direction of the sustainability compass helps me and my team prioritise tasks and resources, enabling efficient goal pursuit,” she says.
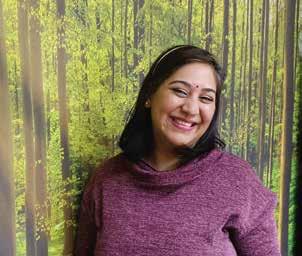
Ensuring Cyber Safety at AlcoNCP: An Interview with Shon Roopnarain,
Control Systems Engineer
Q: How has the evolving scope of AlcoNCP impacted the necessity for cyber safety training within companies?
SR: As our technology landscape evolves, encompassing both the Information Technology (IT) and Operational Technology (OT) realms, it becomes imperative to integrate cyber security into our modern work culture.
Q: In what specific ways have you observed companies such as AlcoNCP acknowledging the importance of cyber safety training as a business imperative?
SR: We view our employees as integral parts of our IT and OT systems defence mechanism. Regular training sessions, awareness campaigns, and practical exercises are some of the methods we've implemented to keep cyber safety at the forefront of our business operations.
Q: Can you highlight any recent trends or incidents at AlcoNCP that emphasise the critical need for robust cyber safety protocols in today's business landscape?
SR: About three months ago, we encountered several impersonation attempts targeting certain employees. This type of cyber threat is quite common and aims to deceive individuals into believing they are interacting with legitimate contacts.
Q: Considering the increasing complexity of cyber threats, how do you propose AlcoNCP integrate and prioritise cyber safety training within their overall business strategies?
SR: Integrating and prioritising cyber safety training has been challenging, but we've found success with a human-centred approach. For those who still didn't complete the training, implementing a more impactful measure—locking out user accounts—proved effective in getting everyone on board. It's crucial to treat cyber safety training as a fundamental safety policy, similar to our induction training for on-site safety.
Exploring Distillation at Alcohol School
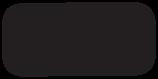

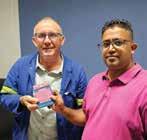
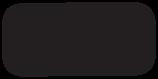
The Ethanol Technology Institute and Lallemand Biofuels & Distillery Spirits recently organised the Alcohol School in Saint Lucia, Caribbean, from 15 – 19 April 2024. Among the sessions, Kiara Premlall, Production Manager, delivered a seminar on Practical Distillation Troubleshooting named, ‘Ethanol Production: A symbiosis of science and art’. She shared insights into neutral alcohol production through case studies, discussing challenges and successes in the process. Reflecting on the event, Kiara Premlall emphasised its value in understanding global challenges, market trends, and networking opportunities within the industry. Such gatherings provide a platform for collaboration and knowledge sharing, essential for progress in alcohol production. “Alcohol School serves as a forum for professionals to discuss sustainability and efficiency in distillation, contributing to the industry's evolution. Through informative sessions and practical experiences, attendees are equipped to navigate the complexities of modern distillation practices. As the industry advances towards sustainability, events like Alcohol School offer guidance and inspiration for professionals seeking to improve their practices.”
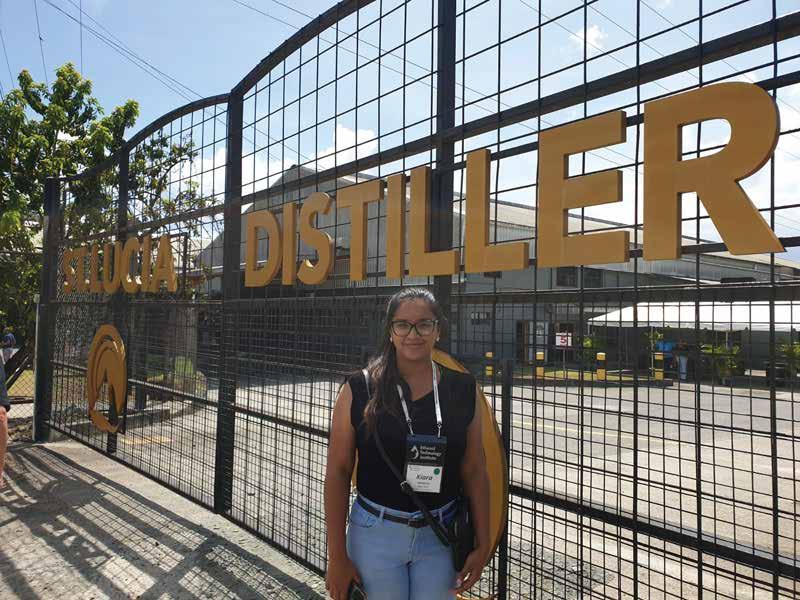

Louie Pillay (left) handing Avril Chetty (right) his cyber training spot prize
Ricardo Peters (right) handing Lance Ethell (left) his cyber training spot prize

At the 2024 Durban Chemical Cluster (DCC) Skills Graduation, AlcoNCP celebrated the achievements of its staff members who completed various programs within the DCC. Earning recognition for the achievements and seen here are AlcoNCP graduates (f.l.t.r.) Lucky Ntuli, Lance Ethell, Zinhle Mqadi, Siphokazi Majozi, Mervin Kullen, Lumeshni Pillay, Kaylin Govender, Morgan Murefu (supporting the team), Sihle Damini and Collin Mkhize. The group completed various courses which ranged from Lean Fundamentals, Executive Leadership Development Programme (ELDP), Training Leadership Development Programme (TLDP), and Problem Solving. During the event, AlcoNCP received an award for its commitment to skills recognition, highlighting the company's efforts in nurturing talent and promoting growth. Morgan accepted the award on behalf of AlcoNCP, reflecting the

Kaylin Govender (left) was nominated for the Trailblazer Award for his presentation on Increasing the Distillery Feed Rate, acknowledging his innovative approach and dedication
Lumeshni Pillay (right) received the Top ELDP Award, and the Mentor Recognition Award, recognising her exceptional leadership skills and mentorship contributions.
some action photos of Working at Heights safety training held at AlcoNCP on 30th April 2024. We asked Timothy Moodley, the company’s SHEQ and Fire Officer about the importance of regular safety training - especially the training for working at heights. “The Working at Heights Training is crucial for managing the risk of falling while conducting work on ladders, scaffolding and access platforms throughout AlcoNCP,” says Timothy. “In a manufacturing plant where staff and contractors regularly work at elevated levels and platforms, we have a legal duty to safeguard our workforce by training them regularly in the hazards and risks associated with their work.”
By providing comprehensive Work at Heights Training, AlcoNCP equips its employees and contractors with the essential knowledge and skills to utilise safe working load principles, fall arrest systems, safety harnesses and safe working procedures. This training not only reduces the likelihood of falls from heights but also enhances productivity by instilling confidence and building competence among all employees working at heights.

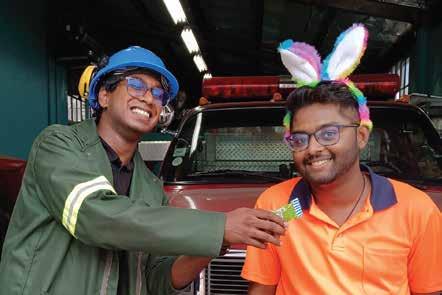
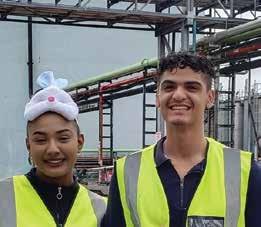
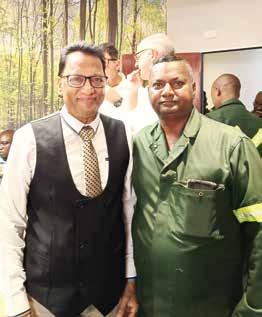

The 2024 Easter Egg Hunt at AlcoNCP kicked off with excitement and a hint of mischief as staff discovered chocolate marshmallow eggs hidden throughout the site. Teams eagerly searched their areas, and the competitive spirit led to some creative "meetings" in other departments. The engineering workshop was suspiciously quiet, with no eggs recorded—likely eaten on the spot—while the main control room buzzed with activity. Laughter and whispers filled the air as employees ducked under desks and peeked behind cabinets in search of eggs. In the end, the Projects Team emerged victorious with an impressive haul, making the hunt a morning of laughter, camaraderie, and unforgettable fun.
Farewell Vicky and Allan!
As we bid farewell to two of AlcoNCP’s stalwart employees, Vicky Singh, Shift Manager (left) on 1 February and Allan Pillay (right), Materials Handler on 14 May we reflect on their journeys and the positive marks they left on our company. Vicky and Allan were each honoured with heartfelt send-offs during their respective retirement functions, a testament to their significant contributions and the high regard in which they are held by their colleagues.
Vicky Singh devoted an impressive 32 years to AlcoNCP. His leadership, dedication, and unwavering commitment to excellence have been cornerstones of our operational success. Vicky was more than just a manager; he was a mentor, a problem-solver, and a guiding force, ensuring that every shift ran smoothly and efficiently. His illustrious career and achievements have set a high standard for all who follow in his footsteps.
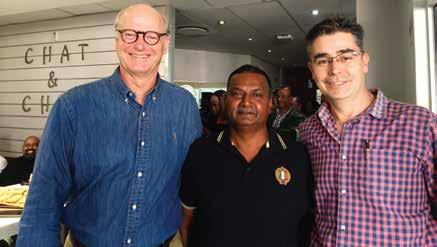
Allan, a hardworking materials handler in Site Logistics, served AlcoNCP for 32 years with diligence and a can-do attitude. His role, though often behind the scenes, was crucial to our day-to-day operations. Allan’s contributions were integral to his team’s success, and his presence especially at our year-end functions where he entertained us with his singing and guitar-playing talent will be sorely missed.
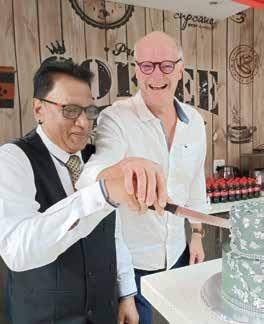
Photo: Vicky and Peter Starling sharing a laugh during his farewell.
Photo: Peter (left) and Steven Kitching (right) bidding farewell to Allan (centre).