
5 minute read
Searching for Sammy U: NATM Board of Directors Tour U-Haul Facilities › › › › › ›
Searching for Sammy U
NATM Board of Directors Tour U-Haul Facilities
By Meghan Ryan, NATM Assistant Director
In mid-October, U-Haul International®, Inc. opened its doors and welcomed the National Association of Trailer Manufacturers’ (NATM) Board of Directors to explore behind the scenes of a multi-billiondollar rental moving equipment company.
Marco Garcia, Director of Engineering Services for U-Haul, currently serves as the NATM Board Treasurer and invited the entire board to visit the facilities to share some insight as to what goes into running such a large company, as well as the differences in operations as a rental company compared to the sales focus of most NATM member trailer manufacturer companies.
“U-Haul Company’s hospitality for the board and NATM was overwhelming,” said NATM President Marty Lorick, President of Triple Crown Trailer. “It was great to tour two facilities and the wellness center to see how committed they are to the safety and health of employees. That same commitment shows in their products and services to the customers as well.”
The board first visited the Glendale Manufacturing Company (GMC) facility in Glendale, Ariz. Cedric Moore, plant president at GMC, lead the highly informational tour of the newer operations plant. The plant offers steel fabrication, welding, powder coating, and other operations that directly feed into the U-Haul production of trailers, tow dollies and U-Box® portable storage containers. Moore explained the importance and efficiency of vertically integrating nearly all steps of the steel fabrication, manufacturing, assembly and finishing under the umbrella of one parent company. Most impressive was the use of automation on the production floor which expedites the process and reduces the reliance on a limited workforce. Similar to all manufacturing industries, the company has struggled with the skilled workforce shortage. Automation has assisted in alleviating some of the challenges. The facility boasts two Salvagnini L3 Fiber Lasers offering computerized laser-cutting and automatic ordering of raw materials as stock runs low. It also works as a smart vending machine for all production material used in robotic welding and cutting. The facility also has six robotic units handling much of the welding workload while manual welding areas service more delicate assignments.
The board then visited the U-Haul Technical Center in Tempe and toured the R&D, test lab, and manufacturing floor. U-Haul has come a long way since its inception in the summer of 1945. U-Haul co-founders L.S. “Sam” Shoen and his wife, Anna Mary Carty Shoen, recognized a need for one-way trailer rentals and bought the first U-Haul trailers from welding shops, or secondhand from private owners. However, that strategy didn’t work. Many of the purchased trailers were unreliable, and there was no uniformity with repairs and general upkeep. So U-Haul quickly changed course and began building its own trailers – a process which it still follows to this day. U-Haul has grown to become the largest rental fleet in the do-it-yourself moving industry with more than 176,000 trucks, 126,000 trailers and 46,000 towing devices. With 77 years of experience in the trailer industry, U-Haul generously shared some of its expertise with the board.
While the board had fun looking for the small and elusive “Sammy U” logo, hidden within the large vinyl SuperGraphics® on the sides of the rental trucks and trailers, the attendees were focused on learning something new that they may be able to apply in their facilities or in their work as committee and board members.
On the engineering and testing floor, attendees observed the laser equipment used to measure coordinates of an object and produce a draft of the image digitally on the computer for research and reproduction. This same technology can be used as quality-control check for the consistency of parts.
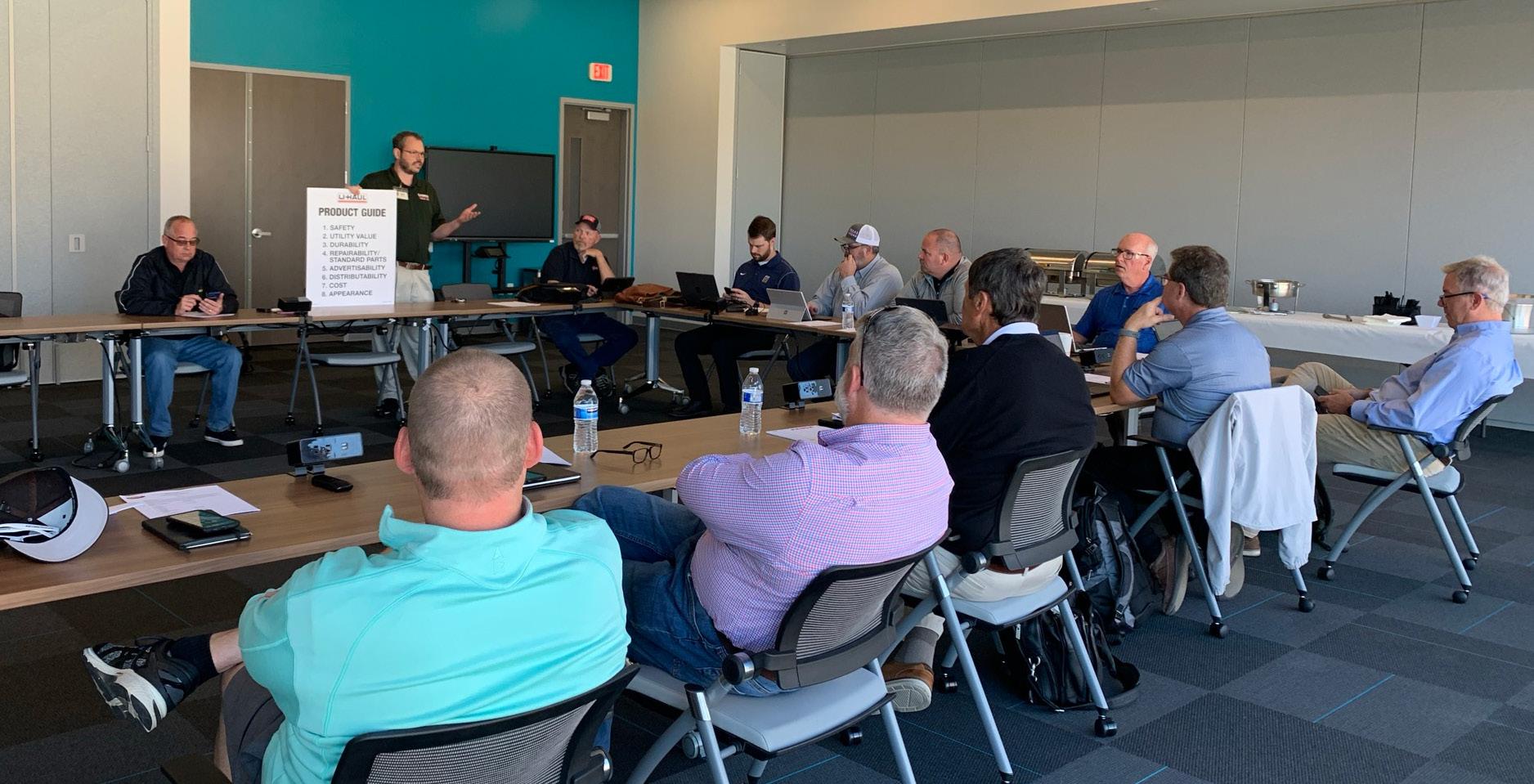
In order to quickly recreate an object with certain dimensions, the 3D printer was showcased. This technology was able to print objects with mobile parts – for example, a wrench with a working, adjustable worm-screw. The printer can be used in conjunction with software to create prototypes, redesigns, part fitment, and improve functionality of parts.
U-Haul staff demonstrated meeting SAE standards of the force necessary to pull a two-inch ball from a two-inch coupling. The machine pulled up to the rated mark of 10,000 lbs. and held for one minute, and afterward continued to increase force until the coupler failed and separated near 19,000 lbs. A load deflection test on a torsion axle also took place nearby.
The members also explored the manufacturing floor. As the company produces most of its own components, the floor was busy, productive and the workers diligent. The operation was impressive with its cleanliness and well-lit, organized floor that featured designated areas for all tools and materials. The efficiency was evident by the ease in which the trailer frames flowed smoothly throughout the many stages of production.
As a rental company, the operations go much deeper than the usual, basic manufacturing of goods. The maintenance process for the trailers, as well as trucks and other products, requires meticulous and thorough recordkeeping and scheduled maintenance. By checking and repairing any damaged components and refurbishing the trailers, U-Haul retains highly detailed documentation and information of past renters, damages inflicted, repairs and any alterations to the products in order to reduce risk and liability.
U-Haul hosted the NATM Board of Directors’ quarterly inperson meeting at their new Shoen Family Conference & Fitness Center at the U-Haul Midtown Campus in Phoenix. The U-Haul Midtown Campus was given a platinum-level Green Business rating from the City of Phoenix and was also recognized as a 2020 S&P Global Platts Energy Award finalist in the areas of Corporate Social Responsibility and Sustained Excellence – Green Initiative. For more information about U-Haul’s green initiatives, turn to page 39. Outfitted with modern virtual conferencing equipment and large windows offering natural light and views, the multi-million-dollar wellness facility was the ideal location to review NATM’s programming and goals. Opened in August 2021, the conference and fitness center is a 54,000 square-foot facility that includes a complete gym with weights, cardo equipment and resistance training, group fitness classes with professional instructors, a U-Haul Arena basketball court, golf simulator, and on-site medical clinic with a lab and physical therapy room. The board thoroughly explored and tested the new facility by shooting free throws and practicing layups on the court.
The board meeting in Phoenix was not only able to showcase one NATM member’s processes in place to manufacture trailers, but to share knowledge and increase engagement amongst members. ■
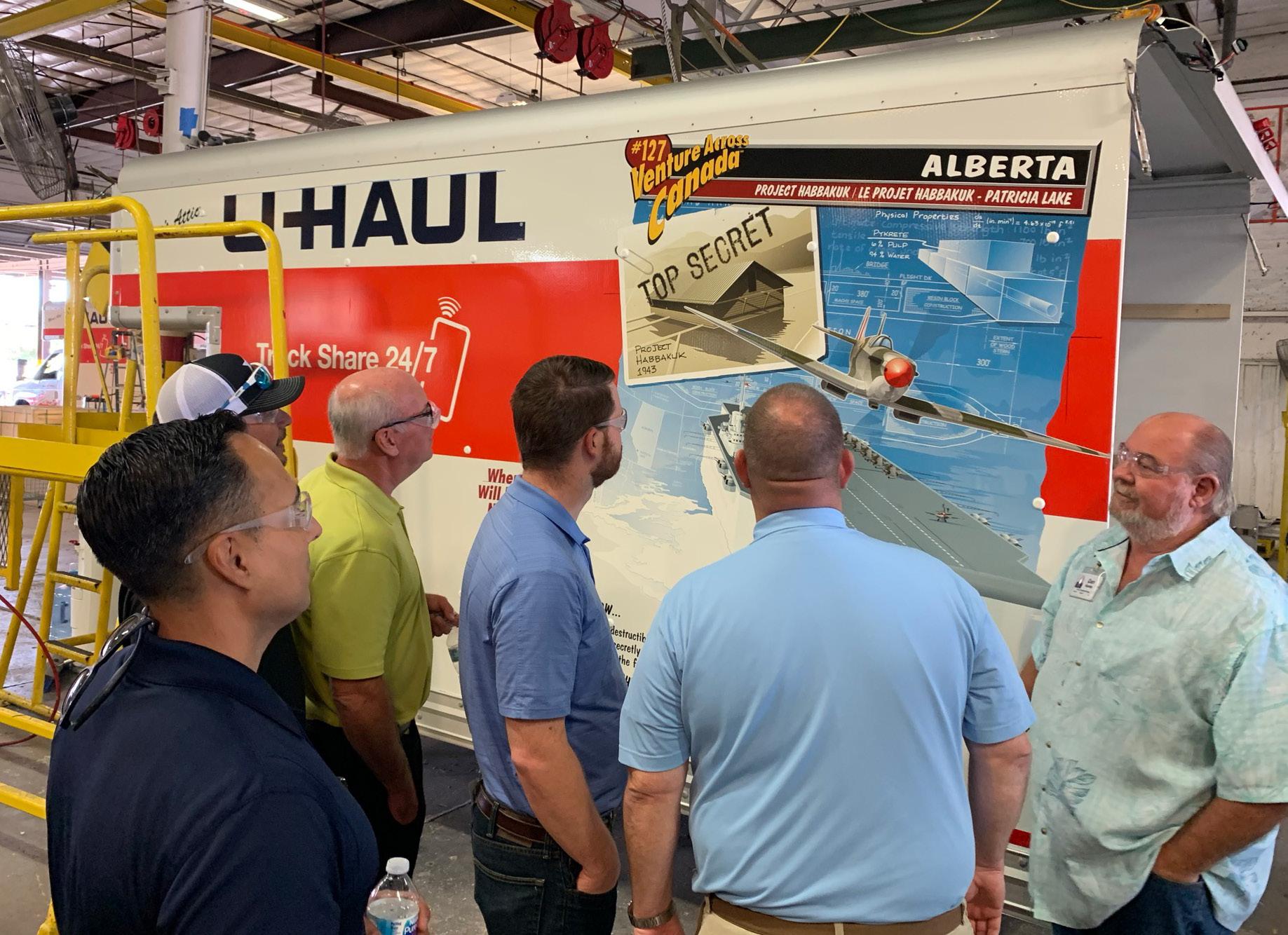
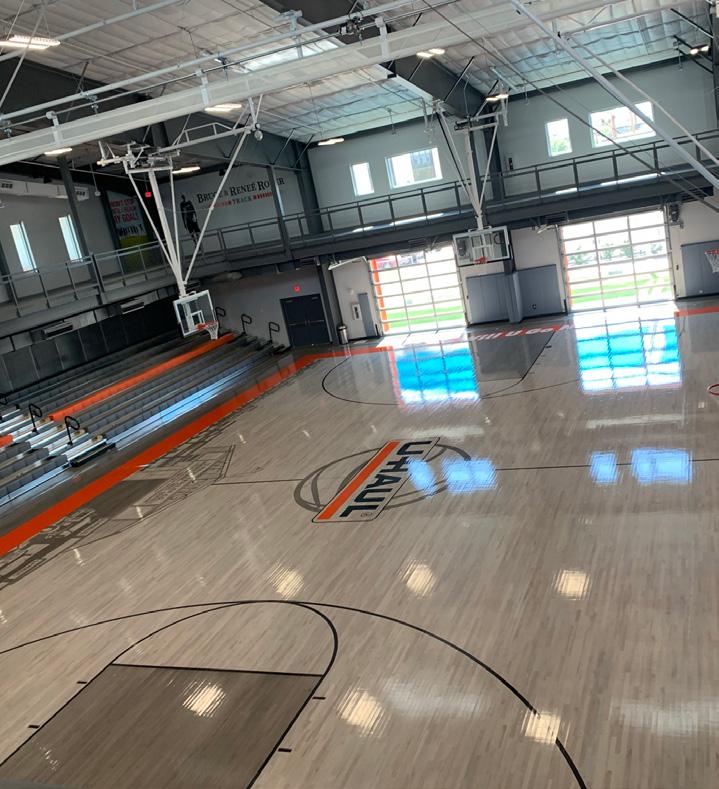
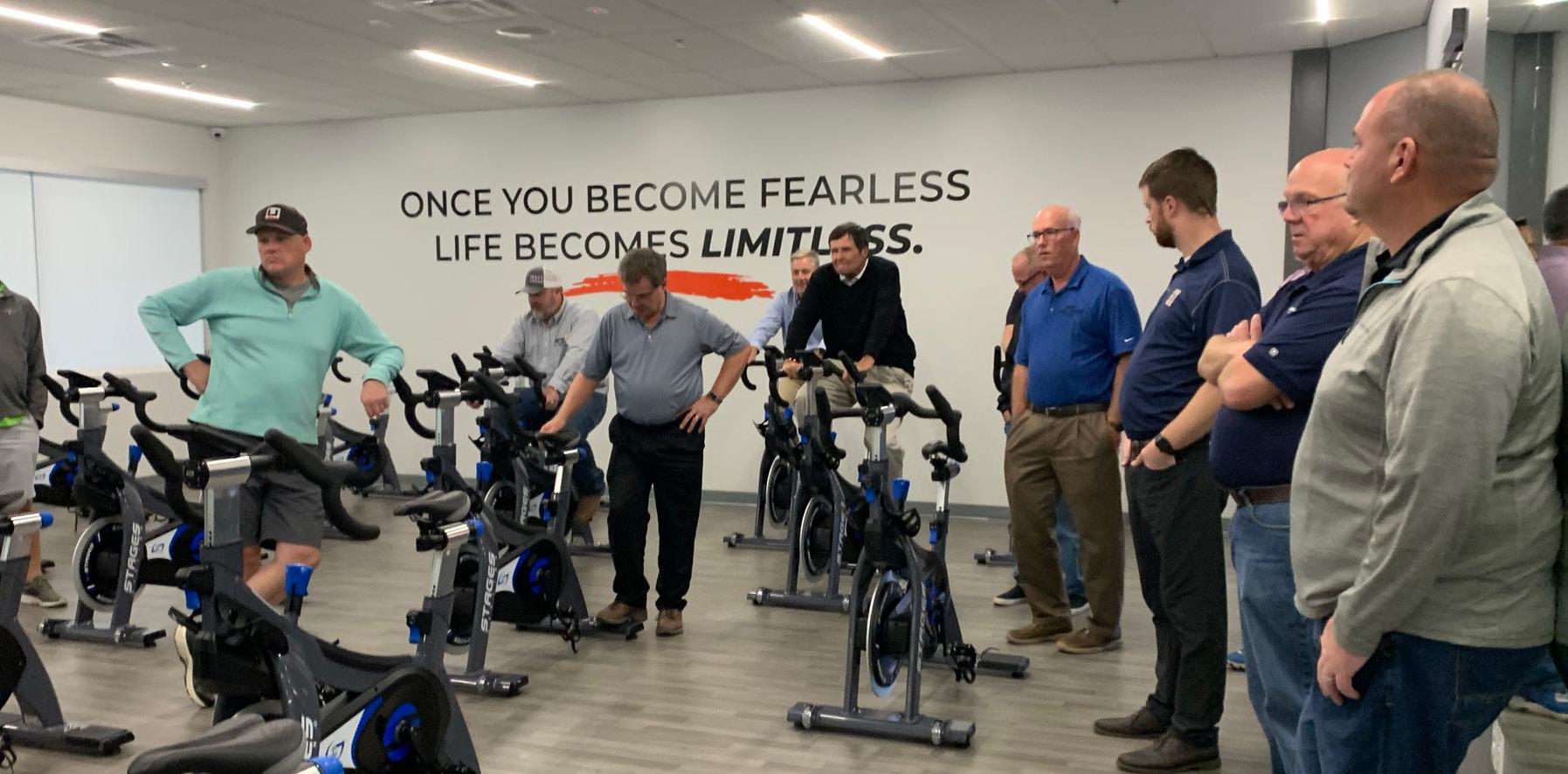
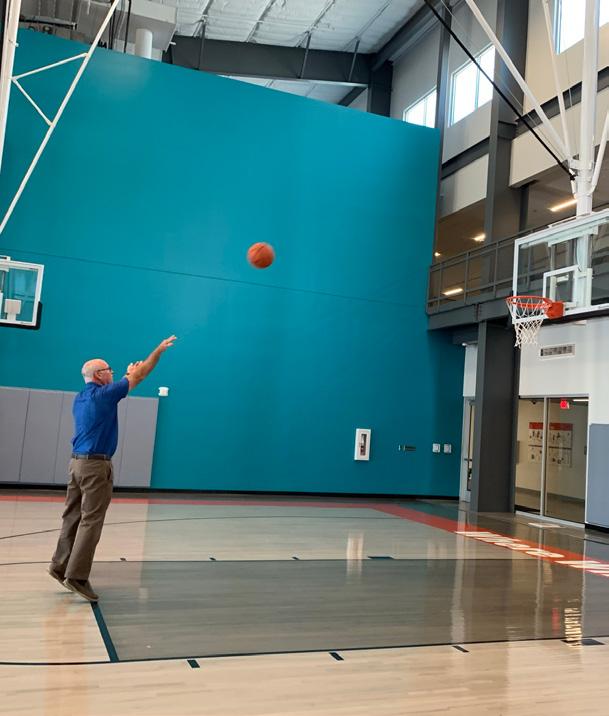
Interested in becoming more involved with NATM?
Contact NATM Executive Director Kendra Ansley at Kendra.Ansley@natm.com for information on becoming involved with NATM committees or serving on the board of directors.
Or call NATM headquarters at (785) 272-4433.