
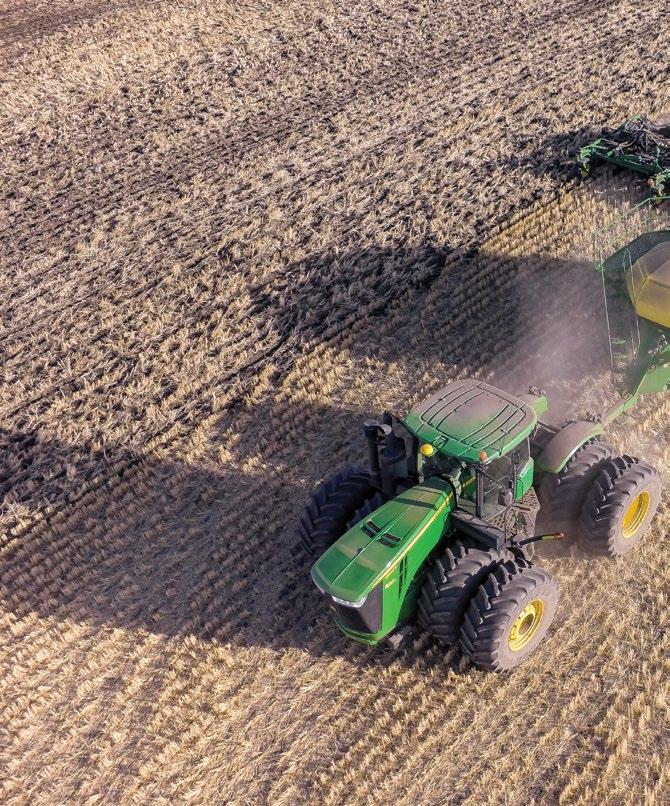
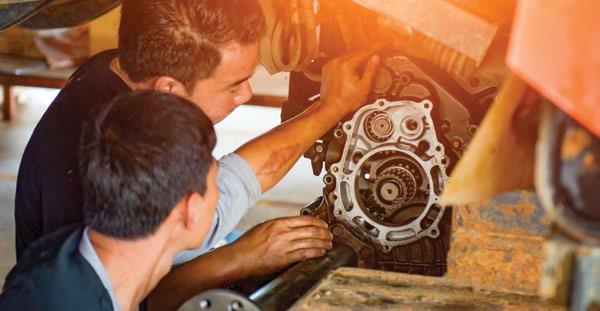
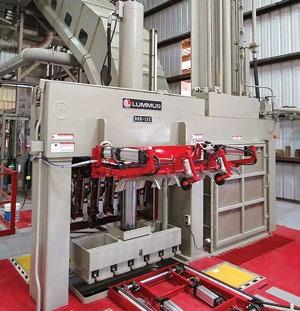
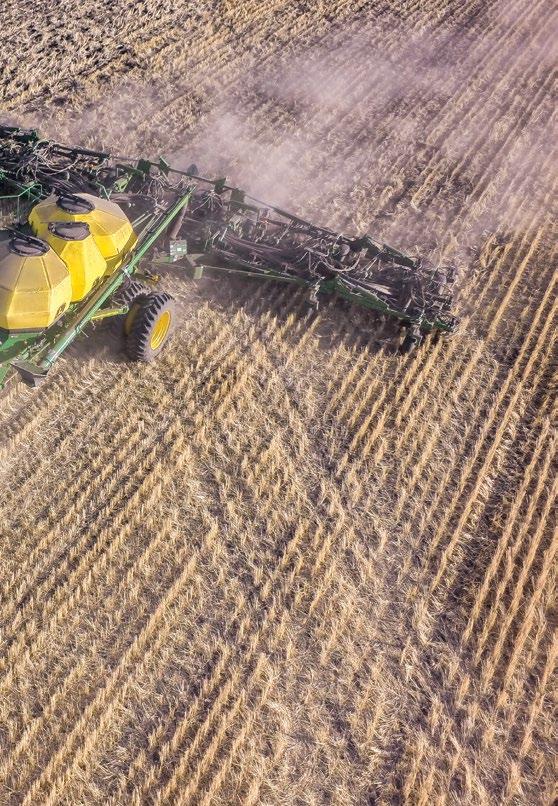
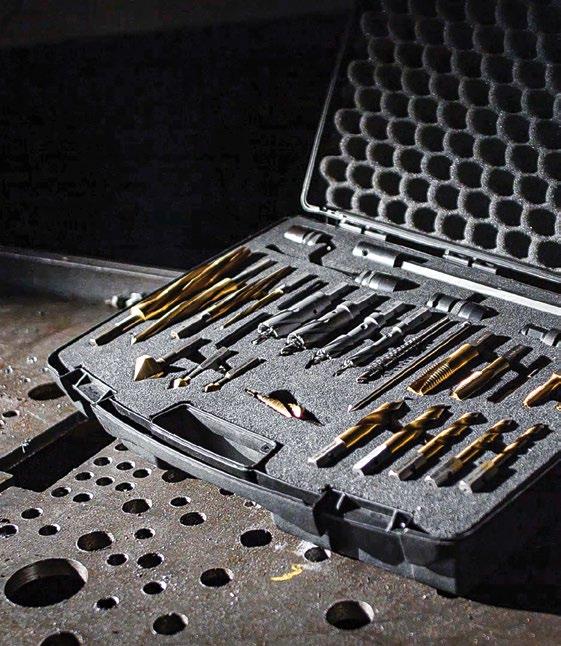
Russell Randal, National Business Development Manager - Agriculture. 25 Years at Motion Australia.
Russell is a passionate member of the Motion family and brings 25 years’ of knowledge and expertise to customers in the agricultural sector. He is responsible for the whole of the agricultural segment at Motion.
Russell has set up key supplier contracts with big factory traders in the US, attended many events including the World AG expo, and gets excited about how the latest equipment and technology solutions might help farmers back in Australia.
Russell’s key quality is that he listens to customers about their requirements and is able to provide solutions fit for their application.
What’s your favourite word?
Yes
If you could win an Olympic medal for any sport, real or fake, what would it be?
Marathon
If you could change your name, what would it be?
Maverick
What was your favourite subject in school?
Mathematics
What’s your hidden talent?
Getting of doing the washing
out of doing the washing!
To the tune of Paul Kelly’s famous refrain: from little things, big things grow. As the team at Motion looks out over the country’s illustrious farmland, they warmly welcome their customers, suppliers, and partners to a fresh start and a new year of sowing the seeds of success for Australian farmers.
Following a year marked by the challenges of flooding and climate change that impacted many of the country’s tight-knit rural communities, many Australians took time off over
the holidays to enjoy the fruits of their labour with friends, family, and loved ones. By ushering in the new year amongst kin, Motion, together with fellow Australians, are holding tight to the promise of new beginnings.
Mid-January to February is traditionally the time of year when Australian farmers begin dusting off their sowing and seeding equipment to gear up for planting crops for a new harvest season. For most people working in the agriculture sector, there
is a shared understanding that the only thing certain is that uncertainty is inevitable. A year in farming is likely to be impacted by fluctuating temperatures, unpredictable weather patterns, and the ebb and flow of native wildlife, insects, and of course, mice.
Typically, March through to late May is ideal planting season for wheat, barley, and canola in Australia, while at the same time, the season’s first cotton, almond, and walnut harvests also fall in the first half of the year. It is during these critical
months that the team at Motion set all systems to go, with engines firing on all cylinders, according to Motion’s National Business Development Manager for Agriculture, Russell Randal.
For Russell and his team at Motion’s Wagga Wagga branch, this means doing everything they can to ensure that Australian farmers have what they need to keep their equipment up and running. “We are very invested in ensuring success for our customers in the agriculture segment and we are heavily involved in the work that is done during seeding and sowing season, through to the harvest,” enthuses Russell.
“From stocking parts for critical pieces of agricultural equipment such as tractors, seeders, tillers, sprayer’s, headers and augers, to the design and implementation of food processing facilities, Motion is involved with every aspect of the farming industry.”
According to Russell, Motion’s approach to expected challenges this year has been manifold. “For one, we have increased the volume of our stock orders and ordered in bulk well in advance of the season to ensure that when the season starts our distribution centres are ready to deliver that same week,” he expounds.
“And another thing we have tried to do is localise some of our suppliers to Australian-owned and operated manufacturers, wherever possible. This eliminates the risk of grossly drawn-out lead times and supply chain issues with
importing from overseas,” he furthers.
“Additionally, we have leaned heavily on our strong relationships with suppliers and partners to negotiate priority stock and exclusive distribution rights within the Australian market,” he adds, noting that one key new offering will be specialised bearings for cotton picking equipment.
When dealing with lingering global supply chain challenges left over from the pandemic, Russell says that Motion’s vast network of supply partners, coupled with their substantial authority and influence in the field, has proven to be a crucial advantage when tackling the challenges of the last few years.
Motion provides a broad spectrum of products, services, and technical expertise to serve a diverse range of applications for farming and food production. This includes the supply of all the bits and pieces involved in the general upkeep of mobile equipment and farming machinery such as bearings, couplings, sprockets, belts, motors, and engine filters; as well as oils, greases, and fuel storage distributed through Motion’s CBC, BSC and WebsterBSC businesses.
Motion’s larger family of core businesses – SpecFast, Hardy Spicer, AIP, CRAM, Sealing Solutions and Waltersheid – offer speciality engineering products and services to the agriculture sector such as parts and components for engineering projects, custom driveline systems, pressure gauges, gaskets, mechanical seals, and hoses for hydraulic
pump assemblies.
For more niche products and applications, Motion’s offering also extends to the supply of safety equipment such as guards, backstops and lifting gear for conveyer lines, as well as food safe lubricants and filters for beverage producers like breweries and wineries.
“We really pride ourselves on being an industry leading industrial solutions provider and for us, it’s more than just selling products and signing off on supply orders. We like to get out to site as often as possible and learn everything we can about an industry so we can build relationships with our customers, partners, and suppliers,” says Russell.
“When it comes to solving engineering problems, we have the full spectrum of capabilities to offer solutions in the form of products and services, but we also like to leave no stone unturned. By this I mean, if there is a stone that is unturned, we will be sure to identify it and add it to our offering,” he concludes.
“We also try to keep ahead of the market and anticipate the needs of our customers. As a business, it’s our goal not only to be a one-stop-shop for industrial solutions, but to be a resource that people can rely on for insitu support, a well-connected friend that businesses can liaise with for networking purposes, garner insider information on new products and market trends, or just have a good yarn about day-to-day life.”
High-performance drive systems are crucial to ensuring farming equipment and machinery can endure the rigors of a harvest season. Australian harvesting conditions are particularly challenging for equipment operators due to the nation’s notoriously harsh climate conditions that include unruly weather, heavy rainfall, and extreme heat during the hotter months.
For this reason, manufacturers and suppliers of power transmission (PT) products and original equipment manufacturers (OEMs) of farming equipment and machinery invest heavily in the research and development of drive system products that can remain resilient under rugged and harsh operating conditions and effectively outlast a harvest season.
According to Motion’s Troy Markland, the key to a successful drive design is sourcing exceptional and genuine power transmission products that utilise the latest in PT technology for optimal drive performance. Over the course of his 40-year career, Troy has worked extensively with customers in the agricultural segment to deliver premium engineered power transmission solutions that support a variety of farming and food production operations.
“A big part of my role is liaising with clients, partners, and suppliers to establish what power transmission products are currently available to market and building and maintaining good relationships with
key stakeholders that can support our business goals and the service we offer to our customers,” says Troy. “The market is saturated with power transmission products, but the challenge is identifying those top tier companies that are experts in their field and can readily supply us with high quality product.”
Exemplary of these attributes is Australian Timken, suggests Troy. “Timken has a reputation for the design and manufacturing of a broad spectrum of premium engineered power transmission solutions, and their commitment to quality is evident in how their products such as the Diamond® Series Agriculture Roller Chain perform in equipment operations,” he explains.
According to Troy, the Timken Diamond® Agriculture Roller Chain offers superior resilience to wear and corrosion due to their shot peened surface finish which is resistant to sheer stress and compressive force. “Shot peening aids in mitigating fatigue failure when the part is exposed to repeated high loads,” he explains. “The Diamond® Chain also incorporates Timken’s proprietary ‘hot dip’ lubrication additives that provide uniform protection against the ingress
Features and Benefits INDUSTRY ADVICE
Timken Diamond® Chain Series Roller Chain
• Shot peened link plates and rollers
• Precision ground pins
• 30-40 percent greater wear life
• 20 percent greater fatigue life
• Initial lubrication with Timken proprietary ‘hot dip’ process at 125 degrees Celsius
• Pre-lubricant additives provide excellent corrosion protection
• Pre-loaded to up to 50 percent of their tensile strength to minimise stretch
• Specifically designed for use on agricultural applications
of contaminants and corrosion.”
For more than 130 years, Diamond® Chain has served the global industrial market and established itself as a firstclass manufacturer and supplier of power transmission products. Founded in 1890 as part of the Indianapolis Chain and Stamping Company, the company has a rich and storied history of pioneering power transmission solutions that have been part of ground-breaking and iconic projects, such as Ford’s first automotive drive system design and the Wright Brother’s first motorised aircraft.
Since being acquired in 2019, Diamond® has continued to trailblaze and make history as part of the global leading manufacturer and supplier of engineered parts, Timken. As a strategic supply partner to Motion, Timken has played a critical role in the design and implementation of drive systems for agricultural machinery with the supply of Diamond® Series Agriculture Roller Chain to farming equipment operators around the country.
Regional General Manager for Australian Timken Sean Young says the design of Diamond® Chain is the culmination of years of dedicated field research, and materials engineering and science that has seen continuous improvement over the years.
“The Diamond® Chain is constructed from precision-ground pins, shot peened rollers and link plates, and a seamless roller arrangement with protruding solid bushings,” he explains. “All of our Diamond® Chains are rigorously tested at the point of manufacture by our inhouse engineers and quality assurance officers. The chains are pre-loaded to 50 percent of their tensile strength to ensure the pins and bushings are securely seated in place for load bearing resilience on even the most demanding applications.”
The result is a significantly improved service life and extended life of the internal components. According to Sean, the Diamond® Chain offers a 30 to 40 percent greater service life on agricultural applications and are very versatile for use on different agricultural applications, compared to other standard roller chain solutions.
Australian Timken’s engineering services department and Motion
have enjoyed a successful working relationship for over 50 years, during which time both parties have shared the common interest of providing end-to-end engineering solutions and driving results for Australian industry.
“Our field engineers have always been proactive in supporting Motion’s technical specialists and we often perform joint site calls together as one unit to analyse drive system performance and oversee the
branches and product experts have been invaluable to us over the years. They have maximised our reach within the industrial market and have been instrumental in communicating the value of our products to customers as well as providing us with a host of feedback and recommendations that have come back from our endusers,” he concludes. “Much like our Diamond® Chain, our relationship with Motion has been built to last.”
One of the biggest challenges with operating hydraulic air seeding equipment is managing and controlling clumping and blockages that accumulate in the seeding hose from residue in the field. Weeds, soil, animal manure, and fertiliser can prevent an air seeder from releasing even pressure and dispersing seeds at a consistent rate and depth in the ground.
To deter the effects of residue and clumping blockages, many growers prefer to use disc seeders, rather than a more traditional tyne seeder machines, because they have a greater ability to handle heavy crop residues. However, according to Australian Government’s Grain Research and Development Corporation, one potential limitation to disc seeders is what is known as residue ‘hair-pinning,’ where residue is forced into the furrow by the disc opener resulting in poor seed to soil contact and a reduced ability to cut down residue.
Residue handling is particularly challenging in soft soil conditions, which can become quickly apparent to novice growers operating disc seeding systems. Consequently, controlling hair-pinning by minimising residue is critical to ensuring precision seeding and sowing processes and evenly
spaced rows of crops.
According to Fellipe Ramos, Category Manager at CRAM, one way this can be achieved is by ensuring disc seeder units are fitted with premium hydraulic down-pressure systems. In addition, they are fitted with dialled pressure control systems which can be gauged easier for better handling of residue materials and more precision air flow of seeds.
“The OEM standard for disc seeders is actually a static spring system that bounces up and down by way of a single push button system,” he says. “For this reason, it is imperative that farmers invest in adequate hydraulic down-pressure system upgrades for their disc seeders. This will allow them to achieve a smoother and steadier motion from the disc arms and achieve uniform pressure with every disc opener stroke toward the ground.”
CRAM’s Engineering and Design Services team specialises in the design, manufacture and maintenance of hydraulic equipment and fluid power systems, which includes custom engineered hydraulic solutions for equipment manufacturers within the agriculture sector such as hydraulic
pumps, cylinders, and manifolds. In addition to this, the CRAM Engineering and Design team can also provide hydraulic pressure valves and control systems to suit the requirements of a diverse range of agricultural applications.
Fellipe says that CRAM stepped in to assist one of CRAM’s local customers who specialises in upgrading OEM disc seeders with hydraulic down-pressure systems. CRAM assisted with the design and implementation of a custom pressure control system for their disc seeders which would allow remote access to the hydraulic circuits via the cabin of a tractor.
“Our engineering team visited the customer’s manufacturing facility to assess the hydraulic down-pressure systems and make calculations around the design of the pressure control system. What we discovered while doing this was that there were some glaring inefficiencies in the manifold at the back of the machine which was responsible for pressure control,” explains Fellipe.
“The pressure control manifold was located behind the disc seeder machine which is attached to a tractor during operation,” he elaborates. “So basically, to adjust the pressure of the valve, a farmer would need to stop the tractor,
and walk to the back of the machine. And even then, the system was limited to basically just a high, medium, mild, and off position for pressure control.”
The solution CRAM designed was a custom pressure control system valve that allowed a metered range of proportional pressure valve by using a electronic control system to dial the pressure up and down from inside the tractor cabin. The dial system displays the pressure and sends an electrical signal to the valves on the disc seeder machine through electrical cables, prompting the pressure valves to open and close proportional to the meter range.
“The valve we selected was electro-proportional based, meaning
that the operator would have full control of the hydraulic pressure at an increment of 0 to 100,” explains Fellipe. “For example, a farmer might want to just open the valve two percent or five percent, and our pressure control system will convert to pressure on the equipment side – allowing for full control of how much pressure they are putting into the equipment.”
The complete solution would provide operators with total control of the balance of the hydraulic downpressure system, which could quickly and efficiently be dialled to have more bounce or rigidity, depending on the specific requirements of the operation. The customer was very
happy with the result, recognising it as a great improvement to the standard fixed control system where previously operators could only control the flow of air going in and out of the seeder, but not the actual air pressure, according to Fellipe.
“By ensuring the hydraulic downpressure systems on disc seeders are fitted with a pressure control valve, farmers will have the ability to adjust the air pressure from inside the cabin of the tractor on a metered system for uniform and consistent pressure on air seeding applications,” he concludes. “The result is better seed to soil contact, and ultimately, a smoother and more precise flow of the seeds.”
The baling press is the last step in the cotton ginning process and therefore has a significant role. At the Australian Food and Fibre (AFF) cotton processing facility in Hay, southern NSW, the output target for their baler is 900 bales of processed cotton per day. Over a typical 16-week processing window the plant runs 24/7. So when the baler went down recently, Motion was called in to find the reason – and a quick solution.
The baling press at AFF Hay uses servo-controlled hydraulic cylinders to manipulate and control the movement of the lint (cleaned) cotton into the baling chamber. In operation, the lint cotton is forced into the baling chamber by a pusher cylinder and after each load a vertically-oriented tramper cylinder descends, roughly compresses the lint cotton and returns to its rest position ready to compress the next load of product pushed into the cylinder.
When the baling chamber reaches full bale weight – which usually takes around seven charges - a third cylinder pushes up from underneath and compresses the cotton into a 227kg high-density bale ready for despatch.
To meet the AFF Hay production target, a bale is produced every 90 seconds. Over the course of two days,
The piston had unscrewed from rod during operation, causing half to fall off, dislodging the seal, which then was carried back to the tank.
the operators of the baling machine noticed a deterioration in the operation of the pusher cylinder. According to the operators, sometimes the pusher was working fine, but at other times it wasn’t positioning properly and it just “wasn’t performing quite as we have come to expect.”
To investigate the problem a remote connection was established from a Motion diagnostic computer to a development computer at site. This allowed access to the motion controller that orchestrates the movement of the pusher and tramper cylinders. Having access to the controller allowed for control over machine parameters and trending of important values.
From the gathered trends and previous suspicions of oil contamination, the initial diagnosis was a faulty proportional valve. The AFF technicians on site changed the valve but the problem remained.
With the proportional valve eliminated, Motion engineers knew they had to dig deeper to find the cause. That would mean recording the oil pressures inside the cylinder by suspending the automatic operation of the cylinder and driving it manually with an open-loop signal.
Unfortunately, there was not any
suitable data logging equipment available on site. As an alternative, site technicians fitted a pressure gauge to a gauge point on the pusher cylinder, and a mobile phone was used to record video of the gauge as the pusher was driven remotely. The video was then sent to Motion where pressure data was extracted and timealigned with trends from the motion controller for analysis.
Plotting and analysis of the results revealed a high likelihood of significant oil leakage in the system. With the valve ruled out, the evidence was pointing to a significant fault inside the cylinder; most likely wear or damage to the piston seal. The recommendation from Motion was to change out the cylinder.
Although initially reluctant, AFF site technicians swapped out the malfunctioning pusher cylinder with the spare they had on site. The change out was completed in less than two hours, the symptoms disappeared, and the plant was up and running again.
The innovative use of getting information remotely in addition to Motion’s specialist understanding of the characteristics and operation of hydraulic cylinders meant the job was completed with minimum disruption to operations.
The baling press is the last step in the cotton ginning process. The output target for the baler at the AFF Hay (AFF) is 900 bales of processed cotton per day.
The pressure changes were recorded on video as the pusher cylinder was driven remotely. The video was then sent to Motion where pressure data was extracted and time-aligned with trends from the motion controller for analysis.
Waiting for an intermittent fault to shut down a vital piece of production equipment is not everyone’s idea of an exciting Saturday afternoon – but that was the scenario for two Motion specialist hydraulics technicians as they waited for a tramper to run to fault at the Australian Food and Fibre (AFF) cotton processing plant in Hay, New South Wales.
Cotton processing is a time critical operation. When downtimefree productivity is vital and a fault stops production, getting specialists to site and having the right people to quickly analyse the problem, devise a solution and get the plant back online is paramount.
During the six-month processing window, the Australian Food and Fibre cotton processing plant at Hay in southern NSW runs 24/7 to maximise productivity. Output is targeted at 900 bales of processed cotton per day. This is an achievable target but downtime is not an option.
The tramper is essentially the last stop on the production line. Used to compress the lint (cleaned) cotton into the baling chamber of a press box – to reduce the volume of the press box required – it is powered with a servocontrolled vertically oriented hydraulic cylinder.
In operation, lint cotton is pushed into the baling chamber by a second hydraulic cylinder in the tramper circuit. The tramper descends, compresses the lint cotton and returns to its rest position ready to compress the next bundle of lint cotton pushed into the chamber. On average, around seven compression charges are required to generate a 227kg bale ready for despatch - the acknowledged industry standard in Australia.
But when the tamper is impacted by an intermittent fault and does not descend as planned, productivity stops.
Each time the tramper did not work, the production crew would turn off the power then turn it back on to reset the tramper. This step worked –
sometimes for two hours, sometimes longer - but eventually the fault would reoccur. Given the power off / power on process was working, the decision was made to start the investigation at the servo valve controlling the cylinders on the tramper circuit.
To find the cause of the fault the Motion technicians used a combination of PLC diagnostics including an RMC Delta Controller to plot the operation and performance of the valve and also an HMG Data Logger to track the hydraulics and valve commands.
The diagnostics showed that the system had the necessary hydraulic pressure but at the wrong time. The more telling result was that the servo valve that controls the tramper cylinder had a stuck spool in it which would occasionally get jammed over, which meant hydraulic pressure to the cylinder when it was not required and vice versa.
With the problem identified, a solution was needed. The plant had an old servo valve available which was re-worked by the Motion technicians and installed in the circuit. With the old valve installed, operating speed was ramped up to the target 90 bales an hour which will allow the plant to finish their processing schedule on time. The faulty valve was refurbished by Motion and returned to the customer.
As it turned out the problem was inside the valve and the problem would not have been identified without the Delta Controller and HMG Data Logger. To access the valve the techs fitted a signal splitter to the loom of the valve so the diagnostic technology could analyse the signal in and out.
The combination of the right people and the right technology delivered the right result. Downtime was kept to a minimum and the plant quickly regained its target productivity schedule – at minimum time lost.
Soil ingress on equipment in agricultural applications can create significant problems for farmers in terms of machine performance and longevity. Bearings in particular are susceptible to failure from exposure to harsh conditions – and when every minute of uptime counts, it’s important to choose the right bearings for the job, says Tony Tormey, Motion’s Category Manager for Industrial Bearings.
“Soil ingression is an ongoing threat to harvesting equipment, particularly in Australia where farmers contend with extremely fluctuating weather conditions – from heat and dust to severe rain,” he explains. “This is why investing in bearings built to withstand those conditions is critical, particularly when there is huge demand for food product. No one wants to experience downtime in harvest season.”
According to Tony, the latest iteration of the Schaeffler FAG Black Series have features specifically built for harsh agricultural applications.
“The FAG Black Series of radial insert ball bearings and housing units from Schaeffler are robust, ready-tofit, self-contained units that provide simplified mounting, smooth running and high reliability,” he expands. “These bearings and housing units have superior sealing and corrosion protection. This is especially important as rust leads to flaking and premature failure. And bearing failure is one of the most common – and preventable – causes of
farming equipment breakdowns.”
The Schaeffler Black Series bearings take their name from their matte black surface coating.
“Their black coating is Schaeffler’s Durotect BS surface treatment formulated to inhibit rust, withstand temperatures from -20 to 120 degrees Celsius and other corrosive conditions,” explains Tony. “We recommend these for a number of agricultural applications –one that comes to mind is macadamia harvesting, where dust ingress is an ongoing issue and the hot and humid climate conditions that the trees grow in can be stressful on equipment componentry. These bearings will still perform well despite those conditions –they are durable and reliable.”
Moreover, the Black Series housing units conform to the standard JIS B 1559. They consist of graphite cast iron housings and concave seating where the insert bearing is located – this compensates for any misalignment of the shaft or assembly.
“They’re particularly suitable for applications with moderate to high radial loads,” says Tony. “The housing units also allow for relubrication to increase longevity of the bearings and prevent build up of dust, sludge and static contaminants that can slow down equipment.”
The Black Series radial insert ball bearings are available with two location methods and one type of seal. These units are matched to each other and
are available as pillow block housing units, flanged housing units and take-up housing units.
“Because of the way they are designed, they have reduced frictional torque, so they are more energy efficient and generate less heat which also extends grease life.” Tony adds.
The Black Series radial insert ball bearings are based on single row deep groove ball bearings and comprise a solid section outer ring and an inner ring extended on both sides. The bearings have plastic cages and are sealed on both sides by single piece seals with a vulcanised lip and outer flinger shield.
“Importantly, the ball bearings and housing units are particularly easy to install,” adds Tony. “Housing units are supplied with a lubrication nipple, integrated end cap for the lubrication nipple as well as an Allen key for bearings with grub screw lock.”
Tony recommends that customers call on Motion before changing over or installing bearings. This is because a local Motion branch can draw on the nationwide expertise of engineers and experts and provide highly localised service and support.
“If customers are having difficulties with their equipment and bearings, we’re here to help. Whether that’s about supplying the right bearing to their application, or questions about installation and best practices, we’re available around the clock.”
It can be a nutty time of year for those in the almond business, with harvest taking place between February and April in Australia. But as Russell Randal, Motion’s National Business Development Manager for Agriculture says, “Farming is an all year job, whether it’s spraying or pruning, agriculture doesn’t stop – but harvest is generally more intensive on machinery, which is why Motion works closely with farming communities to plan for what they need to perform adequate maintenance and keep their equipment in uptime.”
The almond harvesting process involves three main steps: shaking, sweeping and harvesting. In the first instance, a shaker machine enters the orchard, and makes the rounds with each and every almond tree.
“What these shaker machines do is that they fasten onto the trunk with a clawed type jaw and shake the almonds off the tree so they can be swept up and harvested – that’s the purpose of the machine,” explains Bryden Coote, Motion’s Branch Manager at Swan Hill, Victoria. “To do their job effectively, whilst not inflicting damage on the tree, the shakers need to be kept in good maintenance and we recommend using quality componentry such as heavy-duty Gates® v-belts on the shaker heads.”
According to Bryden, many OEMs exclusively use the Gates® Super HC™ PowerBand™ v-belts on their shaker heads.
“There are certain brands where the
Gates® belts come with the machine as they are specifically suited to these applications, and as partner to Gates® in Australia, Motion supplies these belts when they need replacing on the shaker heads,” says Bryden. “These belts, which include the 8V1600, 8V1800 and 8V2000, are especially reliable on these machines because they’re strong but narrow, basically combining the strength of a wrapped belt with the economy of a narrow section v-belt.”
Once shaken, almonds are typically left to bathe in the warm summer and early autumn sunshine. The drying time can span from 4 to 10 days, depending on weather and moisture content in the kernel and outer hull. Often a sample is taken from a part of the field to determine moisture content and whether the almonds are ready to be swept up.
“Once they’re adequately dry, the sweeping starts – farmers will navigate their sweepers up and down the orchard rows, and arrange them into lines for pick up,” says Bryden. “Again, these sweeping machines use Gates® v-belts due to their suitability to the application. They’re strong and narrow which is basically what the sweepers need to be too. The sweeping and lining up of the almonds is very important, as the harvesting machine – which comes next – has a limited area in which it can go into.”
After the rows have been swept and the almonds are neatly organised, a harvesting machine will follow, which picks all the nuts, discards additional soil
and debris, and essentially takes the nuts to be processed.
Since the region of northern Victoria has a lot of almond growers – which is where Bryden is based in Swan Hill – he has an understanding of the requirements farmers need. According to industry body Australian Almonds, there are over 15 million almond trees in Australia, and 78 per cent of these are located in New South Wales and Victoria. 1
“Almonds love the Mediterranean type of climate that we have up in the Riverina region where there is plenty of access to irrigation water,” says Bryden. “As the Australian appetite for almonds continues to grow, so does the economic importance of this crop to this agricultural community. As key suppliers to this community, I’m proud to be part of the Motion team to assist with machinery components, in addition to engineering and maintenance services to the farming sector.”
References:
1. Australian Almonds - https:// australianalmonds.com.au/
With around 1500 cotton farms in operation, across more than 150 regional Australian communities, Australia is the largest producer of raw cotton in the world. The regions with the most ideal cotton growing conditions can be found mainly in New South Wales and Queensland, with smaller operations located in Victoria, Western Australia, and the Northern Territory. But perhaps the most commendable aspect of the industry is that close to 90 percent of Australia’s cotton farms are Aussie owned and operated by families within these communities.
According to Australian Cotton1, the industry produces on average 680,000 tonnes of raw cotton annually. Approximately 90 percent of these cotton yields are exported globally each year to spinners and textile producers in Europe, Asia, and the Middle East. Following a bumper harvest season in 2022, Australian cotton farmers produced a recordbreaking six million bales, contributing
nearly $2 billion in domestic dollars to the Australian economy.1
Australian farmers are known to be amongst the most environmentally and socially responsible cotton producers on the planet. This is due to their conservative use of natural resources and low-impact operations that rely on the natural climate conditions that are ideal for cultivating and growing cotton. There are very few artificial or mechanical aspects to Australian cotton growing, and most local cotton farms are family farming operations where much of the labour is done manually by the farmers.
That said, cotton farmers still use the bare essential tilling, seeding, and harvesting equipment and machinery found on most modern farms. and Motion is heavily invested in supporting Australian cotton farmers, according to Russell Randal, Motion Australia’s Business Development Manager for Agriculture. Russell is based in the Wagga Wagga region, an area not too far away from many cotton operations, but he is also frequently on the road, visiting agricultural regions and meeting
with farmers across the Eastern seaboard and beyond.
Due to Motion’s broad range of industrial solutions and engineering capabilities, coupled with nation-wide supply networks and distribution channels, Russell enthuses that Motion is well positioned to serve the cotton industry. He explains that Motion has recently begun carrying an exclusive range of bearings specially designed for cotton planters and harvesting equipment.
“Cotton picking equipment requires a particular type of bearing that can be quite expensive and hard to source,” he explains. “But we have channels to source genuine bearings for these types of applications that are in line with OEM requirements. In addition to this, as an added advantage, we also have the ability to supply these bearings in bulk, at a reduced cost to our customers, because we were able to negotiate a very good rate with our supplier,” he continues.
Cotton harvesting can be very harsh on bearings because of the consistency of the raw material. The
dusty, dirty, and dry nature of cotton buds and blooms makes them one of the harshest materials on equipment in general, says Russell. “The cotton picker bearings we have arranged for procurement are well suited to cotton picking machines because they have a unique double triple lip, straight edged rubber sealing system built in that shrouds the bearing,” he explains. ‘Additionally, they come pre-filled with 80 to 100 percent bearing grease to ensure the bearings can remain sealed for their expected service life.”
Cotton is big business in Australia, and many cotton farmers have been impacted by floodwater challenges over the last year and require additional support as they recover from the damages, according to Russell. “On one hand, cotton thrives in high-heat, humid conditions with excessive rainfall and the cotton industry produced unprecedented yields last year, but in terms of quality of life, many cotton farmers are coming out of the trenches and require a bootson-the-ground approach to ready themselves for potentially another year of similar conditions.”
“For many of these communities and the cotton farming families living on the
rural land in these areas, the flooding was a double-edged sword. While their friends, families, and communities were being flooded out, they also had to worry about their crops, which their livelihood depends on at the same time,” he furthers. “It has been chaotic and overwhelming for many of us.”
In Australia, the cotton planting season begins in Spring in October, through to late November, in preparation for growth during the rainy season and the hot humid sub-tropical summer months. Then come March and April, when cotton harvesting season begins,
and the cycle continues.
Purportedly, Russell emphasises that cotton Australian farmers are “amongst the toughest and most resilient among us, and the cyclical nature of the farming industry means that they are somewhat used to contending with unpredictable weather and uncertainty. The upside to this is that with every new season comes the opportunity for a fresh start, new beginnings, and opportunities for further growth and expansion.”
References:
1. Australian Cotton – Industry Snapshot https://australiancotton.com.au/
There’s a reason Australian farmers choose Australian-made air seeder hoses – it’s because they’re built to last, says Jeff Mrak, Motion’s Marketing Manager for Customer Insights and Market Research.
“Farmers prefer the quality of the Australian-made products. They want to avoid changing out their hoses regularly, and have hoses that last longer than a season,” explains Jeff. “In which case they will opt for products that are made for Australian conditions, such as drought-ridden areas and regions subject to extremes in temperature and so on.”
Which is why Motion is wellstocked and ready to go with locallymanufactured air seeder hoses this seeding season.
“The hoses on an air seeder play a pivotal role in transferring product across primary and secondary lines, so you need a quality hose,” explains Russell Randal, Motion’s National Business Development Manager for Agriculture. “We have Australian-made air seeder hoses that have been tried and tested to
work in Australian agricultural conditions. This means they are lightweight, UVstablised and flexible so that they don’t get any kinks.”
Importantly, Russell points out that agricultural communities across Australia have access to these products through the Motion network of branches.
“We’ve prepared for the upcoming season with stock of air seeder hoses. On the back of the last couple of years and issues with supply chain, we’ve anticipated the needs of the agricultural sector by pre-ordering extra stock,” says Russell. “We understand the importance of having locally-made hoses available for seeding season. And we have air seeder hoses in our distribution centre, ready to go to any part of Australia when customers call for them.”
Jeff further points out that there will likely be a lot of seeding activity in the autumn months.
“Based on the moisture map of Australia, we understand a lot of areas of land will be seeded in the coming period and we have product available to support that program because a lot of places are
dry,” he expands. “We’ve had three good wet years – particularly on the eastern seaboard, but also in South Australia and Western Australia. So, in the context of that moisture map, the conditions are looking really good for agriculture over the next one to two years.”
Russell agrees but reiterates that farmers should always “hope for the best and prepare for the worst.”
As a leading supplier of all types of agricultural componentry, he adds that farmers can always rely on their local Motion branch for support.
“What our company has done as a whole has increased the volume of our orders and built on our relationships with local manufacturers and suppliers,” he says. “This enables us to overcome potential issues with supply. But of course, we always recommend to customers to have a chat with us about requirements so that we can better meet their individual needs.”
Likewise, while the Australian agricultural market has a preference towards Australian-made product, Jeff notes that Motion’s global reach means farmers have access to a wide range of specialty parts for air seeders – including brands from Global supplier locations.
“Farmers can always tap into our expert network for advice – as a company, we are truly invested in having solutions and expertise to service the agricultural community,” concludes Jeff. “We have a nationwide footprint of branches with an impressive amount of collective know-how.”
We know that each machine has its idiosyncrasies and that every farmer has their preferences.” This quote from agricultural powertrain specialist, Walterscheid, is indicative of why their solutions suit the needs of the Australian farming community.
“It’s German-made componentry and design, combined with the ability to custom-build and supply to customer needs that makes Walterscheid a leader in both power take-off drive shafts, tractor attachment systems and hitch systems,” explains Andrew Sawyer, Business Manager at Walterscheid. “The universal joints in the driveline are of an exceptionally high grade with superior seals that make them last longer in arduous Australian farming conditions as they keep the grease in and impurities out.”
Walterscheid has been dedicated to servicing Australia’s agricultural market since 1983, specialising in premium driveline systems and tractor attachments. As part of the Motion family, farmers across the country have access to the Walterscheid offering in addition to Motion’s technical expertise and national footprint of branches. One of the key advantages of this access is the fast turnaround of service.
“Not only do we tailor to customer requirements, we also do repairs on drivelines or tractor attachments and turnaround is very, very quick.” says Andrew. “Generally during harvest period time, we do say to people to get their componentry here early, and we will deliver it back fast. Additionally, we have a torque testing rig, so not only can we rebuild and refurbish overload clutches, we can test them as well.”
According to Andrew, Walterscheid is popular with farmers because the power take-off (PTO) driveshafts are reliable and come in a wide range that can support a multitude of agricultural attachments and implements.
“We have an extensive range starting from as little as ten horsepower, going up to 500 horsepower, which
means we can assemble to all sets of requirements, with multiple variations,” he adds. “Additionally, we have a number of safety devices, such as clutches that we can fit to these drivelines to ensure they do the job properly and safely. So for example, if something jams up the clutch will go off and protect everything around it.”
As part of its company ethos, the Walterscheid portfolio has evolved alongside modern farming practice to help farmers reap the best from their crops. An example of this can be seen through the Walterscheid three point linkage system or Tractor Attachment System (TAS), which has become an industry standard due to its simplicity and utility. The TAS gives the tractor more traction than it would ordinarily have with the same power, weight and fuel consumption.
“These TAS are commonly used for steering or towing mowers, ploughs, balers, and sprayers. The considered three-point design transfers the weight and resistance of an implement to the tractor’s drive wheel, catering to ongoing changes in farming practice such as increased farm sizes, crop diversity and longer machine operating times,” says Andrew. “We
offer rear attachment and front linkage systems through Motion to cover all requirements. This enables customers to experience the benefits of a ‘butterfly system’ – less fuel, less ground compaction underneath, and fewer passes necessary for a wide sweep.”
The Walterscheid linkage systems and combinations for mowers have been the fastest and highest selling products developed in their category. This is a trend Andrew attributes in part to increased rainfall and unprecedented demand for produce.
“Drivers can cover a wider distance, which means imprinting on the land less and having to do fewer passes of the field. You’re saving fuel by driving less distance overall, and whether you’re harvesting, mowing, or spraying, it’s a vastly more efficient process,” he concludes. “Importantly, these are all constructed with safety in mind. Drivers can operate the coupling and uncoupling mechanism directly from the tractor seat – saving time and mitigating the hazards of stepping outside the vehicle during service. The TAS lower link hook has a safety locking mechanism and the top link hook facilitates the safest possible connection between the vehicle and implement.”
Farming is one of the world’s oldest industries, and the relationship between soil and spade dates back to ancient times when early humans discovered cultivating the ground for growing plants was an effective way to foster abundance during the harsher months of the year, when food was in short supply and resources were scarce.
Ancient civilisations of nomadic hunters and gatherers scavenged the wild land to hunt and forage for survival, until around 13,000 years ago when Stone Age nomadic tribes began to cultivate small plots of land. However, the formal practice of domesticating plants and animals did not become widespread until approximately 10,000 BC, when families began permanently settling on land to establish farming communities. This was known as the Neolithic Revolution, and the first crops planted by these early settlers consisted of emmer wheat, einkorn wheat, peas, lentils, bitter vetch, hulled barley, chickpeas, and flax.
As farming progressed over centuries, farmers gradually gained an understanding of what practices were beneficial as opposed to detrimental to the soil on farmed field. In addition, they learned the science behind preparing the ground for seeding and sowing. Unless properly cultivated, soil has a finite amount of time that will be effective for planting before it loses its fertile properties. Therefore, cultivation is an important agricultural practice that involves breaking up depleted topsoil by mixing it with fertiliser and aerating seedbeds to restore the ground’s fertile properties.
“The purpose of cultivation, not to be confused with tilling soil, is to create the ideal seedbed for your crop because the quality of your ground at the start of planting season will determine the robustness of your yields during a harvest,” says Russell
Randal, National Business Development Manager for Agriculture at Motion.
“Cultivating soil turns over topsoil without penetrating too deeply into the ground. Whereas, tilling the soil involves digging deep down which is a subset method of cultivation used primarily for breaking new ground. However, this is typically avoided because it disrupted the natural biology of the soil and ultimately kills the ground,” he explains.
“Depleted topsoil is one of the biggest threats to modern industrial agriculture and the production of food and commodity farmed goods, which is why it’s important to have a strong working knowledge of the different types of cultivation tools that can be used on industrial and commercial farming operations.”
In Australia, there is a growing movement toward the practice of no-till cultivation as part of the effort to conserve natural resources and promote a more environmentally sensitive approach to industrial agriculture. In tune with this line of thinking, manufacturers of planting, seeding and tillage equipment have started to move away from antiquated machinery that disrupts and impacts the health of soil by gouging too far beyond the surface of the soil.
“Many of our partners and suppliers are on board with reducing tillage activities and interested in bridging the gap between growers and technology by upgrading and optimising the parts and components on cultivation equipment such as disc and tine harrows, chisel ploughs and rotary tillers,” says Motion’s Category Manager for Industrial Bearings, Tony Tormey. “Among these suppliers is leading global bearings supplier NSK who have developed an extensive range of bearings products geared toward agricultural equipment used in the cultivation of soil.”
In additional to concerns about their impact on soil health, agricultural applications are also harsh on
mechanical componentry, which means failures and breakdowns are common when machines must contend with the ingress of soil, moisture, and chemicals used in fertilisation. The soil bites back, so the challenge lies in fostering a balanced relationship between the soil and the spade.
NSK has risen to that challenge, according to Tony, with NSK’s Agri Disc Hub Double-Row Angular contact bearings. “The Agri Disc Hub bearing unit is ideal for disc harrows as well as a diverse range of other seeding and sowing applications,” he says. “In
most cases the bearings feature a protective O-ring seal that protects against contamination and moisture. A 5 lip cassette seal shields the internal components with the bearing itself also containing a double lip DDU contact seal to protect from contaminant ingress. This all helps maintain NSK’s high-performance long-life lubricant.”
The result is there is no need for regreasing the units throughout their service life and reliable protection against contamination such as clay, sand, dust, plant fibres, or fertilisers. “For
farmers, this equates to fewer bearing failures, reduced downtime, and savings on the cost of spare parts, repairs, and maintenance,” Tony explains.
“By improving the bearings technology used on farming equipment, we can improve the performance and efficiency of the machined parts and components, which ultimately will phase out legacy practices that have been detrimental to the environment.”
Although optimising cultivation equipment for reduced tillage is a relatively new area of interest for
industrial solutions providers, the agriculture industry has never shied away from a challenge in the past, and its unlikely to start, according to Russell.
“At Motion, we are on board with the evolution of farming and are keen to discover new technology to encourage healthier crops and better yields. Just as farming is one of the oldest and more enduring industries on the planet, farmers are among the most resilient. As long as we continue to help our farmers thrive, we can continue to rely on them to support our thriving communities.”
During seeding and sowing season, the use of cleaning chemicals and degreasers is common for maintaining equipment and removing soil build up and residue from fertilisers and contaminants that accumulate in the planting fields. The oils, greases, and lubricants used to improve the performance of machined parts and components inevitably require cleaning and degreasing once its service life has expired.
The primary role of degreaser is to safely remove built up dirt and debris accumulated on equipment and components without damaging the surface finish or components of what’s being degreased, explains Steve Keown, National Product Manager for Lubricants and Chemicals at Motion. However, with each power wash and rinse down using harsh degreasing chemicals, the run-off can eventually end up in local waterways and contributes to groundwater contamination and water pollution, he warns.
“For this reason, there has been a noticeable shift toward using more environmentally sound degreasing solutions over the last decade,” says Steve. “This is particularly true for those working within the agricultural segment because the industry’s core operations are intrinsically linked to the earth and the topography of the land, as well as the other elements – air, water, and fire – particularly where it pertains to preventing bushfires and the risks associated with flammable chemicals, oils, and gases.”
According to research conducted by Better Health in Victoria, supported by WorkSafe Victoria, common agricultural chemicals (agrichemicals) such as fuels, solvents, insecticides, herbicides, fungicides, fertilisers, and veterinary chemicals, can lead to serious longterm health effects. Data shows that prolonged exposure to agrichemicals absorbed through the skin or inhaled through mist, vapour, or dust, can result in respiratory illnesses, poisoning, chemical burns, birth defects and damage to the liver and kidneys.1
“Noxious agrichemicals pose a significant threat to the environment by contributing to global air pollution, the quality of ground water and drinking water, and dwindling biodiversity in terrestrial and oceanic ecosystems,” says Steve. “For many farmers, this research does not bode well. This is why most agricultural workers have become more proactive in seeking out environmentally safe solutions that will ensure safer, more sustainable working conditions and demonstrate that they are conscious in practicing responsible land ownership.”
For biologically safe cleaning and degreasing products, Steve defers to CRC Industries, one of Motion’s supply partners, who have demonstrated a keen interest in offering environmentally friendly industrial solutions through the introduction of their Eco Range of products to the agricultural market.
Business Development Manager at CRC, Ian Maguire explains that developing enviro-friendly cleaning products has become central to CRC’s business ethos in recent years, indicative of CRC’s evolution from “a pioneering chemical manufacturer’ to “a world leader in sustainable solutions”.
With the development of their Bio Degreaser formula, Ian says that CRC’s objective was to achieve a pH-neutral,
water-based degreaser that would not compromise the cleaning power of traditional degreasing products. “Our Bio Degreaser formula is non-toxic, biodegradable, and safe for use on all materials,” he enthuses. “During the parts cleaning process, Bio Degreaser’s patented ‘quick break’ formula forces the separation of the oil and grease contaminants from the degreaser to allow for the safe disposal of run-off contaminants.”
“By using CRC’S Bio Degreaser range of products, farmers can effectively reduce the environmental impact of their equipment and operations,” concludes Steve. “In addition to this, by practicing more responsible use of chemicals –that are in line with recent government regulations, environmental policies and guidelines – farmers can further improve their social license to protect the health of their families, friends, and colleagues.”
The CRC Bio Degreaser is available through any Motion branch in a 20-litre concentrated container, which can be diluted for use in a part washing basin or a portable 750-millilitre spray bottle for smaller parts such as bearings. Simply –spray, rinse, and go.
References 1. https://www.betterhealth.vic.gov.au/health/ healthyliving/farm-safety-and-handlingagrichemicals
In agricultural applications, the importance of heavy-duty, maintenance free couplings cannot be overstated, says Motion’s Branch Manager for Swan Hill, Bryden Coote.
“Downtime for anyone is painful but in the case of coupling failure, it can be particularly frustrating and costly –especially during harvest season – as standard couplings require you to pull apart the whole drive system of the application,” explains Bryden. “In the case of the Timken Quick-Flex® couplings, these are not only durable enough to cope with severe vibration and shock, they are designed with elastomeric inserts which means the couplings can be swiftly replaced without having to remove the hubs from the shafts.”
As Swan Hill is located in northern Victoria on the banks of the Murray River, Bryden mostly works with agricultural customers. The region – which is on the southern point of the Riverina – is renowned for its almond, grain, fruit and vegetable farming.
“These types of couplings are typically used in agriculture on irrigation pumps but also on harvesting machinery, such as almond harvesting machinery,” he says. “This is because they are known for being able to withstand tough conditions including extreme weather conditions.”
One of the key advantages of Timken QF couplings is their ability to accommodate misalignment. The flexible, elastomeric element allows for angular, radial, and axial misalignment between the shafts, which can help to reduce stress on the shafts and prolong their life.
“The QF couplings can absorb shock loads and vibration while accepting up to two degrees angular misalignment,” Bryden adds. “They can also handle high speed and very high torque of up to 188,000Nm.”
Due to the high torque capacity, the QF solution is often smaller than the coupling it has replaced, which reduces stress on other components and is a major weight-saving on the drive. Additionally, QF couplings do not need
lubrication and operate without metalto-metal contact. This means the metal hubs don’t wear and require little to no maintenance – only the urethane inserts will need replacing.
“Reducing maintenance is a huge time and cost saving for farmers and the fact that these couplings generally have the same life as the rotating equipment itself is a big win,” says Bryden. “Because you’re just replacing the inserts, it’s a big downtime saver. Instead of your equipment being offline for about 3 hours – which is the timeframe you’d expect with a standard coupling replacement – replacing these inserts takes just minutes.”
Moreover, Bryden reiterates the significance of the Motion and Timken partnership.
“The major benefit for farmers is that they can rely on us for support with this product range and other related solutions for harvesting equipment or pumps,” he says. “We are well-stocked with the QF couplings and can help customers choose the right coupling size and talk them through any questions they might have in regards to keeping spare inserts on site or what the QF installation and replacement involves.”
1. Significantly reduces downtime and replacement costs because Timken inserts can be replaced without moving the hubs or disassembling the driving or driven equipment.
2. Requires no lubrication and has no metal-to-metal contact so the hubs don’t wear, therefore eliminating maintenance.
3. Can accept misalignment up to 2 degrees.
4. Reduces inventory – the only spare part required is the urethane insert.
5. Can handle high speeds and high torque.
6. Durable in harsh conditions –design dampens transmitted torsional vibration and shock, extending life of the coupling and rotating equipment.
Thanks to the initiative of Motion, almond farmers now have access to premium harvest supplies from renowned Californian nut harvesting equipment manufacturer Coit and Hewes.
“This company specialises in nut harvesting equipment and manufactures original parts for OEMs such as Coe Orchard Equipment (COE), Flory Industries, Orchard Machinery Corporation (OMC), and Orchard-Rite – machinery brands that many local almond growers are familiar with,” explains Bryden Coote. “It’s great to be able to offer this to farmers here as the quality of Coit and Hewes parts is exceptional. Being Californian, they have a lot of experience with the nut-growing sector, especially in supplying quality almond harvest parts, which is a real growth industry here in Australia.”
The relationship with Coit and Hewes stemmed out of an initial phone call Bryden made. As he’s based up in Swan Hill in Victoria’s north, he works with a lot of almond growers and has specialist knowledge of their equipment requirements.
“As Coit and Hewes are such a bespoke company and make parts for many of the harvesting equipment our customers buy, I rang them out of the blue to see if they would be interested to work with us,” he says. “That initial conversation spurred further discussion down the line and the short version of that is Motion have the exclusive rights to distribute Coit and Hewes in Australia.”
According to Bryden, the Coit and Hewes parts are extremely popular.
“We made a commitment to Coit and Hewes with an initial purchase of stock in the vicinity of $400,000, but since then there have been several orders reaching into the millions – the parts are really sought after because they’re such high quality,” he adds. “As any farmer knows, good componentry will make a difference to the availability of your harvest machinery and its performance in the field. Spend more on the componentry upfront and you’ll likely to have saved money by the end of the season.”
Founded by Garry Coit and Leroy Hewes in 1988, Coit and Hewes manufactures and supplies a complete line of quality replacement parts for tree shakers, nut sweepers, harvesters, and carts. They are considered a leading source of nut harvest supplies in California.
“California is a leading global producer of nuts – particularly almonds – and Australian growers look to emulate the United States harvesting processes,” says Bryden. “Being the exclusive national distributor for this bespoke supplier is a big win for Motion and Aussie farmers. Coit and Hewes have been around for over 30 years, with one of the co-owners being a nut producer themselves, so they have a lot of firsthand experience and knowledge of the industry challenges and equipment requirements.”
The scope of equipment that Coit and Hewes provide is impressive, says Bryden.
“From tree shaker slings and pads to harvester chains and belts, the product range offers parts for every step of the harvesting process,” he explains. “Also, because they design and manufacture at their own site and have the industry experience, they’re innovative and building products that are durable and able to withstand the wear and tear of harvest. Built for rugged Californian conditions, this durability translates well to the almond-growing regions of Australia.”
The US is the world’s leading exporter of edible nuts – with statistics showing the country exported a total of 1.6 million kilograms of nuts in 2021. The state of California grows 90 per cent of the country’s nuts and almonds are its number one export. Comparatively, Australia is the largest producer of almonds in the Southern Hemisphere with over 17 million trees nationwide. The farmgate value of the almond industry is expected to exceed $1.3 billion by 2025.1-3
References
1. https://www.statista.com/topics/5954/nutindustry-worldwide/#topicOverview
2. https://www.almonds.com/almond-industry/ regulatory-and-trade/global-marketsoverview
3. https://www.austrade.gov.au/news/ success-stories/almonds-the-littlenut-that-cracked-the-big-exportgame#:~:text=Today%2C%20Australia%20 is%20the%20largest,exceed%20%241.3%20 billion%20by%202025.
Australia’s robust farming and food products industries are bolstered by locally owned and operated plantations and homesteads that produce a bountiful yearround harvest. From fresh fruits and vegetables; to nuts, seeds, and cotton; to corn, wheat, and a variety of staple grains, Australia is one of the most prominent cultivators and producers of agricultural goods in the world.
Behind the scenes of lush crops and harvested fresh foods, LOCTITE®’s liquid threadlockers have played a critical role in helping Australian farmers keep their equipment and machinery up and running and preventing downtime during critical times such as the cyclical planting and harvesting seasons.
Since world-renowned chemist and founder of LOCTITE Vernon Krieble first invented liquid threadlocker in the 1950’s, the practice of threadlocking fasteners to secure parts and components has become intrinsically linked to the farming industry, according to Motion’s Category Manager for Lubricants, Adhesives, Sealants and Chemicals, Michael Rowe.
“The most common problems with threaded assemblies on farming, agricultural equipment and machinery is loosening that occurs during operation. Although there are mechanical locking devices on the market, often these mechanical assemblies cannot maintain sufficient clamping force to lock a fastener in place,” says Michael.
“Threaded assemblies – such as double nuts, spring washers, tooth flanged bolts, and nylon insert nuts that hold important components in place – risk failure during operation when they must contend with the vibrational force, thermal expansion, fluctuating temperatures, bending and torque, and the ingress of external contaminants such as soil and fertilisers,” he explains.
In order to prevent the loosening of threaded assemblies on agricultural equipment, it’s important to ensure that they are reinforced sufficiently. This is where LOCTITE liquid threadlocker works
to fill in the gaps between threads and provide reinforcement against harsh operating conditions. Often imitated, but never duplicated, the iconic red bottles of the LOCTITE liquid threadlockers have earned their reputation as a premium range of anaerobic adhesives that can ‘lock tight’ fastener assemblies with reliable force.
Although, the idea behind liquid threadlocker may seem simple enough – it locks threads on metal fasteners in place securely – the science behind LOCTITE’s threadlocker compound is a little more complex. A threadlocker is an adhesive solution that forms a strong bond between the fastener, and it’s attached components using an airless, or anaerobic, curing process to secure interlacing threads and ensure load bearing capabilities.
When applied between two mating threads, LOCTITE threadlockers push the air between the threads out as the fastener is tightened. The anaerobic threadlocker resin is high viscosity and provides an instant, low-pressure sealing solution that cures on metal surfaces, even in an airless environment, to form a thermoset plastic that locks threads and joints in place. Depending on the role of a fastener, the LOCTITE threadlocker range comes in a variety of adhesive strengths to suit a variety of metals and applications.
For Australian farmers, this means fewer failures on critical pieces of farming equipment, reduced downtime on operations and cost savings on repairs, maintenance, and replacement parts.
INDUSTRY ADVICE FROM OUR EXPERTS
Features and Benefits
• Maintains the clamping force
• Prevents loosening under heavy external loads
• The elimination of all gaps guarantees a secure threaded connection
• Completely sealed and airtight
• Prevents leaks and reduces the effects of corrosion
• Engineers and designers can opt for the through hole design over the blind hole design for threaded assemblies
• All LOCTITE threadlockers have a broad temperature resistance of -65°F to 300°F (-18°C to 149°C), while some threadlockers are designed for high temperatures up to 650°F (343°C)
• One bottle of LOCTITE liquid threadlocker suits nuts and bolts of all sizes
For more information on where to buy LOCTITE threadlocker products, visit your local Motion branch today.
When the optimal window of time for seeding and sowing crops is short, and there’s plenty of ground to cover, Australian growers rely on high-performance seeding equipment to expedite their field planting processes and improve the quality of their yields. When choosing the right equipment for the job, Motion’s Russell Randal says it’s important for farmers to take into consideration the scale of an operation, the type of crop, the topography of the land, and what their budget is.
“Depending on these factors, there
are various types of planting machines that have different intended uses and advantages,” says Russell. “If the land requiring tilling in preparation for planting, traditionally tillage equipment such as a disc or a chisel plough can be used to turn the soil. However, with advantages in modern planting technology, no-till equipment has gained popularity.”
For example, Russell explains that no-till air drilling machines can be used in tow behind tractors for precise rapid planting that tills, by opening a slit in the soil, dropping in seed and closing the seed trench, all while managing
residue efficiently in the field. “Notill air drill carts are particularly economical and conveniently build healthier soil to reduce erosion while reducing money spent on fuel and labor.” he says. “And many of these machines include sensors and software now for monitoring seed to soil contact.”
For larger scale operations and equipment budgets, Russell says integrated planters and drawn row units will allow farmers to cover more acres with their massive, rowed arms that turn soil and use hydraulics and vacuum air to disperse seeds quickly
and efficiently.”
All these types of equipment require specialised parts, components and maintenance to run smoothly, which is where Motion comes in. “We carry a range of bearings and housing units that are specific to the agriculture segment which we supply directly to farmers or to equipment service and engineering companies that concentrate on maintaining and improving the performance of planting equipment,” says Russell.
Additionally, Motion and Japanese bearing manufacturer NTN’s longstanding joint venture has allowed them to get a greater understanding of bearing requirements for seeding applications, from a manufacturing standpoint. As a result, Motion has been able to provide expert engineering consult on the production and supply of bearings that go into seeding equipment.
According to Product Manager for Industrial Bearings at Motion, Tony Tormey, Genuine OEM approved bearings for the disc hubs on planter and drill wheels are in high demand due to the scarcity of suppliers who manufacture this particular type of bearing.
“While most bearing companies will carry a variation of this bearing that will suit wheel disc hubs, 90 percent of the time a double row ball bearing or angular ball bearing will be used, which after extended periods in field cannot handle the shock load of
heavy seeding and sowing activities,” says Tony.
He explains that the specific bearing type required for disc hubs is a double taper roller bearing and NTN is one of the only suppliers that carries this type of bearing and the appropriate sealing solutions for it.
“NTN’s Double Tapered Roller Bearings are designed so that the tapered vertex of the raceway surfaces on the inner and outer rings converge at one point on the
Features and Benefits
Optimised internal design
• Pressurised and tempered steel cage
• Hardened steel inner and outer rings
• Guided rollers
Improved performance
• 30% greater basic dynamic load rating
• 10% higher allowable speed
• Up to 3x longer service life
• Lower dimensional change
centerline of the bearing. This allows them to withstand dynamic loads. The tapered rollers are guided by the compound force of the inner and outer raceway surfaces which keep the rollers in place.” Furthermore, with the introduction of NTN’s next generation ULTAGE roller bearings technology, their Double Tapered Roller Bearings have an even greater load capacity, longer service life and greater allowances for misalignment and speed than ever before. The result is significantly improved service life of drilling and planting equipment and maximised productivity in the field.
“Our exclusive access to the best planter bearings available to the market through our joint venture with NTN is just another example of our capabilities as an industrial solutions provider,” concludes Russell. “When we identify an opportunity for improved service to the agriculture industry, we make it our mission to determine the best possible avenue to add that to our offering.”
“No-till air drill carts are particularly economical and conveniently build healthier soil to reduce erosion while reducing money spent on fuel and labor.”
Following engine oils, hydraulic oils are the most important lubricants on hydraulic farm machinery. To reap the benefits of hydraulic equipment in an agricultural setting, the correct use of hydraulic oils in maintenance is key.
Designed to go the distance Hydraulic oils – also known as hydraulic fluids – differ from other types of lubrication by serving multiple functions on hydraulic applications. These fluids are designed to protect hydraulic systems in the most demanding of agricultural applications. Besides serving as protection against wear, corrosion and the ingress of contaminants, they are also a medium for energy transfer – an important distinction to make between hydraulic oils and standard oil lubricants.
Hydraulic oils transfer power from the hydraulic pump motor to the hydraulic ram via a control valve. An important function is the transfer of heat and expulsion of trapped air. In addition to acting as a power transmission medium, the oils serve as a lubricant, sealant, coolant and eliminator of contaminants, to ensure all the driveline and all hydraulic system components are operating properly.
Basically, reliable quality hydraulic oils not only optimise the performance of hydraulic machinery but can extend its longevity and improve efficiency during working hours.
Gulf Western Oil – an Australian story
From the outset, Gulf Western Oil (GWO) have been producing oils specifically for the Australian market. That was the original goal when Peter Vicary founded GWO in 1988 with his two sons Andrew and Ben – from humble beginnings in Western Sydney, NSW – and it remains the focus of the lubricant specialists to this day.
With a unique understanding of Australian farming conditions, GWO has developed some of the most advanced and reputable hydraulic oil formulas available in their state-of-the-art facility.
As a premium partner to Motion, the farming community across Australia has access to the entire range of GWO hydraulic oils, greases and lubricants. The point of difference is quality and the fact that these are made by Aussies, for Aussies. To this day, GWO remains a family-owned and operated business. They are leaders in the field of hydraulic oils, and embrace globally-recognised programs such as API licensing (American Petroleum Institute) and ISO 9001 Quality Assurance Management Systems Certification.
An example of GWO’s local innovations in hydraulic oils is the SUPERDRAULIC anti-wear hydraulic oil range. These hydraulic oils have been formulated with Zinc Dithiophosphate additive technology, which enables them to resist liquid and air contamination with demulsifying properties and maintain perfect thermal stability. These features make them especially suitable for agricultural applications that are prone to extreme heat and humidity.
SUPERDRAULIC hydraulic oils give super performance
GWO’s SUPERDRAULIC range has been successful in the market because of its reputation for superior quality and performance. The hydraulic oils have consistently been given a high approval rating from OEMs in agricultural applications.
Why is SUPERHYDRAULIC preferred by farmers?
• Unmatched protection against wear and corrosion
• Decreased downtime on equipment
• Saves on equipment maintenance and/or breakdown
• Improved hydraulic performance
• Extended equipment life
• Longer fluid life
• Excellent filterability that prevents filter blockages even when contaminated
• Less filter replacements equals more cost savings
• Advanced low frictional characteristics prevent “stick slip”
• API (American Petroleum Institute) licensed
• ISO 9001 quality assured
• Superior protection against wear
• Exceptional filterability
• Exceptional seal and paint compatibility
• Available in ISO Viscosity Grades 15, 22, 32, 46, 68 and 100
hether it’s out in the field, or at a processing plant, onsite drilling and cutting processes are common practices for site engineers and maintenance, repair, and operations specialists. During peak harvest and planting seasons, MROs are kept busy with necessary maintenance and repairs to farming equipment and machinery –and time is always of the essence. Onsite drilling, hole-making, and threading can be a time consuming and arduous task that requires the right power tools to get the job done.
This is not just a tool, it’s a game changer
Introducing the Alpha VersaDrive – The world’s first modular quick-change cutting and drilling system. Specially designed for use on cutting and drilling tools across multiple tool platforms such as impact wrenches, drills and drivers, rotary drills, magnetic-based drills and pillar drills.
traditional work practices
Alpha has revolutionised onsite cutting and drilling processes with their range of Alpha VersaDrive sets, including impact starter kits, tapping kits and installation kits as well as imperial and metric sets that cater to a wide range of applications and industries. The non-slip 11.0mm hex shank design fits into all standard drill chucks and has three concentric lock positions allowing perfect alignment and accuracy when tooling with any of the modular adaptors.
costs. Save time. Increase productivity.
Investing in Alpha VersaDrive removes the challenges of onsite drilling, hole-making and threading in one easy system. Custom-engineered quick-change adaptors connect the tool platform to any one of the Alpha VersaDrive attachment tools. The high-grade steel tool attachments
We can guarantee that you have never seen anything like this before, Alpha has revolutionised onsite cutting and drilling processes. Imagine looking up at a communications tower knowing you need to drill some precisely aligned 4x14mm holes to attach a bracket. You need to climb up with a 12kg magneticbased drill, drill the hole and then work out how to thread it. It’s heavy and dangerous work. Then along comes the Alpha VersaDrive, and suddenly your job gets a whole lot easier, and quicker. When you get to the top of the tower with your Alpha VersaDrive kit you can now use your standard, portable power tools to get the job done fast and most importantly, safely.
have been specifically designed to outperform the closest comparable products on the market, producing up to 15 times faster results, longer life, and more holes per product.
If you are interested in learning more about the Alpha VersaDrive range, you can contact your local Motion branch to speak to a technical representative about purchasing or bulk ordering Alpha VersaDrive products. You can also view the full range of Alpha VersaDrive products at www.alphatools.com.au
What Alpha VersaDrive customers are saying
“We had a large fabrication project which required high precision with very low working tolerances. After processing and galvanising, a range of holes that required precise alignment fell outside of working tolerance. We were looking at a complete remake or arduous manual rework of the parts involved, which would have incurred substantial costs.
Thankfully, we came across the Alpha VersaDrive reamer bit that allowed us to open up the misaligned holes accurately and quickly to a point where they could function as intended.
The Alpha VersaDrive reamer changed a job that would normally take us a week into a job that took a day. We highly recommend this product for anyone in the metalworking industry who is looking for an efficient and speedy way to solve a problem.” – Alliance Metal Solutions
To meet market demand, the need to keep farming machinery well maintained and operating to its optimum is more critical than ever. Keeping productivity up, eliminating downtime on equipment and reducing the costs of maintenance is not just good business practice but can be the point of difference in farming profitability.
This is what the new Alemlube 630A 20V lithium-ion cordless grease gun has been designed to assist the farming community with. Newly released to the market and available through Motion, this mobile grease gun is lightweight and has built-in smarts to
Features and Benefits
• Adjustable delivery rates of 100g/min or 160g/min
• Maximum working pressure of up to 10,000psi/700bar limited to 7,250psi for operator safety
• Able to dispense up to 16 cartridges before battery recharge is required
• Backlit display provides real time battery level, grease level and grease dispensed feedback and information
• Battery recharge time of as little as 70 minutes
• Rubber supports free standing ground functionality
• Rugged corrosion resistant plastic moulded carry case provides protection
help grease equipment in an efficient, fast, safe and effective way.
Designed by Europe’s leading workshop lubrication equipment manufacturer, Samoa, the 630A cordless grease gun offers a drama-free high-pressure, high-volume greasing solution with dual flow rate modes delivering 100g/min or 160g/min and maximum grease pressures of up to 10,000PSI/700BAR.
The electric motor has also been engineered to increase the battery life, delivering more power and enabling greasing to occur even through blocked and dirty grease points. This minimises the time and effort required in an agricultural setting.
The unit is supplied with 2 x 2Ah lithium-ion batteries as standard which can dispense up to 16 x 450g cartridges of grease per battery charge. If greater output is required there is also an optional 4.0Ah battery that can dispense up to 32 cartridges before a recharge is needed.
Weighing at just 3kg, the lightweight and ergonomic 630A 20V Lithium-ion cordless grease gun is supplied with a 1,100mm long grease hose with steel spring protection, a heavy duty coupler and has the versatility of three way loading, 450g cartridge, bulk grease or filler pump. The 1.1m long flexible extension holster has robust rubber feet to provide stability on flat surfaces.
The pump is designed with quality componentry to ensure durability in harsh agricultural settings. It has overpressure and overload protection mechanisms built in the design to assist with longevity.
Additionally, the easy-to-see multifunction LCD screen gives users all the information they need to know about the gun itself and how much grease has been put into a pin, bush, seal, slide or bearing. Operators can see grease levels in the grease cartridge and battery levels and the gun has an LED work light included with its on/off control switch. Another feature of the grease gun is the LCD turns red when
The pump is designed with quality componentry to ensure durability in harsh agricultural settings.
there is a blocked lube point or another issue so users can quickly act to avoid any damage or waste.
The plastic moulded anti-corrosive carry case provided further helps to reduce contamination of ingress into farming equipment and machinery. It is supplied with a 2Ah spare battery, a battery charger which recharges the battery within 70 minutes and a shoulder strap to minimise user fatigue.
To give farmers peace of mind, the 630A 20V lithium-ion cordless grease gun comes with a 5 year warranty. To learn more about the Alemlube 630A 20V lithium-ion cordless grease gun and its suitability in an agricultural setting, readers can get in touch with their local Motion branch.
In the natural world, plants cannot seed themselves so they must rely on clever methods of transport to travel such as air, water, and by attaching to the fur of animals. The infamous dandelion is a great example of this with its lightweight feathery seeds that travel easier through the air and are often found attached to sweaters or tangled in hair.
In the industrial world however where large volumes of seeds are required for seeding broad acres of farmland and seasonal crops for food and raw materials, seeds must be transported more efficiently in long haul shipments using air freight cargo holds and heavily loaded palette trucks and trailers for long haul journeys.
In preparation for planting season, the logistics for seed transport for domestic producers requires considerable supply chain planning and freight capacity to ensure safe and effective delivery of seed bundles to rural sites. It also requires considerable lifting and rigging power to secure moving seed bundles in place.
This is also prime season for delivering bulk order seeding, sowing, and harvesting equipment to Australian farms as they ready their fleets for another year. With planting season around the corner, the team at Titan Lifting Technologies are similarly busy behind the scenes, supplying lifting and rigging equipment to Australia’s farming and transport industries.
Drawing on nearly half a century of industry experience and expertise, Australian owned and operated Allan Marketing developed its Titan brand of precision lifting and hoisting equipment to serve the Australian market and beyond. With a specialisation in chain blocks and lever hoists, Titan also produces load restraint equipment, lifting chain, shackles, ratchet straps, hooks, and wire rigging products.
The local supplier is well-recognised for their robust and durable stainless steel that is precision made and have a wide range of applications across the farming and food production sector.
According to Titan General Manager John Di Michele, “Considerable thought is put into every component the company supplies, with a focus on premium quality lifting and hoisting equipment that is rigorously tested from the point of manufacture through to the sale.”
“All of our products are designed and tested on Australian soil and compliant to all Australian Standards which means our products adhere to strict standards,” he explains. “Through the Lifting Equipment Engineers Association, we are a full member LEEAaccredited company which means our staff undergo comprehensive industry training. Additionally, all our stainlesssteel products are AISI 316 graded.”
For loading seed bundles for long haul transport, Titan offers a range of ratchet truck winches, tie down straps, and webbed synthetic slings for ensuring safe passage of the seedlings out to site.
For more information, visit www.titanlifting.com or contact your local Motion branch to speak to a product expert today.
Titan Flat Webbing Synthetic Slings
AS1353 Features:
• Manufactured with 100% high quality polyester
• Super strong stitching
• Double Thickness
• Protected Sleeved Eyes
• Colour Coded
• Safety Factor 8:1
• Complies to Australian Standard AS1353
• Tagged information
• Individually packaged
• Tests Certificate included
• WLL clearly marked on each sling
Titan Ratchet Truck Winches (clip on or slide on) Features:
• Handles and Hooks manufactured from high quality tensile steels
• Gold zinc plated anti-corrosion protected
• Standard or Reverse Handle options
• Types: Hook and Keeper; S Hook and J Hook
• Super strength high quality polyester webbing
• Protection Wear Sleeves on the Webbing Straps
• Various strap lengths available on request
• Complies to Australian Standard AS/NZS4380
• Tests Certificate included
• Lashing Capacity clearly marked on straps, handles and hooks
• ID Tagged
Titan Ratchet Truck Winches (clip on or slide on) Features:
• Manufactured to strict industry specifications
• Gold zinc plated anti – corrosion protected
• Bare Winch LC 3000kg
• 50mm Webbing Strap with Hook and Keeper LC 2500kg
• Protected Sleeved on the Webbing Strap
• Strap available 50mm x 9mtr and 11mtr
• Complies to Australian Standard AS4380
• Tests Certificate included
• Lashing Capacity clearly marked
The Timken Diamond® Agriculture Roller Chain offers superior resilience to wear and corrosion due to their shot peened surface finish which is resistant to sheer stress and compressive force.
The Gates® Super HC™ PowerBand™ Belt combines the strength of a wrapped belt construction with the economies of a narrow section v-belt. It is recommended for use on all industrial heavy-duty, narrow section v-belt drives. It has up to 300% capacity increase over classical belts.
The CRC Bio Degreaser offers nextgeneration high performance cleaning technology that is pH neutral, safe on surfaces, users and the environment. It is biodegradable, non-toxic, non-hazardous, non-flammable, pH balanced, and water soluble.
Specifically built for harsh agricultural applications, the Schaeffler FAG Black Series give easy mounting, smooth running and high reliability. The specially formulated black coating is Schaeffler’s Durotect BS surface treatment which is formulated to inhibit rust and withstand extreme temperatures.
Alpha VersaDrive is the world’s first modular quick-change cutting and drilling system. It allows cutting and drilling tools to be used across multiple tool platforms. Custom-engineered quick-change adaptors connect the tool platform to any one of the Alpha VersaDrive attachment tools saving time, money and increasing productivity.
Designed to improve reliability, eliminate failure, and boost productivity in operations. LOCTITE® threadlockers are singlecomponent liquid adhesives that secure nuts, bolts, and threaded fasteners. They are designed to eliminate air gaps that, combined with vibration and shock, that allow for loosening in threads.
With the introduction of next generation ULTAGE roller bearings technology, the NTN Double Tapered Roller Bearings have even greater load capacity, longer service life and greater allowances for misalignment and speed. These bearings are designed so that the tapered vertex of the raceway surfaces on the inner and outer rings converge at one point on the centreline of the bearing.
The Titan Flat Webbing Synthetic Sling is manufactured with 100% high quality polyester, has super strong stitching and comes in double thickness. It is colour coded and individually packaged for ease of use, and is perfect for the lifting and rigging required during planting season.
Typically used in agriculture on irrigation pumps and harvesting machinery, Timken Quick-Flex® couplings can withstand tough conditions including extreme weather. QF couplings can absorb heavy shock loads and vibration and can handle high speed and very high torque of up to 188,000Nm.
The Agri Disc Hub bearing unit is ideal for disc harrows as well as a diverse range of other seeding and sowing applications. The bearings feature a protective O-ring seal that protects against contamination and moisture. They are specially designed to be maintenance free and fit equipment for the exacting demands of agricultural use.
The Alemlube 630A mobile grease gun is lightweight and has built-in smarts to help grease equipment in an efficient, fast, safe and effective way. The electric motor has been engineered to increase the battery life, delivering more power and enabling greasing to occur even through blocked and dirty grease points. This minimises the time and effort required in an agricultural setting.
The GWO Superdraulic anti-wear hydraulic oil range is especially suitable for agricultural applications prone to extreme heat and humidity. New additive technology allows it to resist liquid and air contamination. It is preferred by farmers due to its unmatched protection against wear and protection, extended equipment life and excellent filterability.