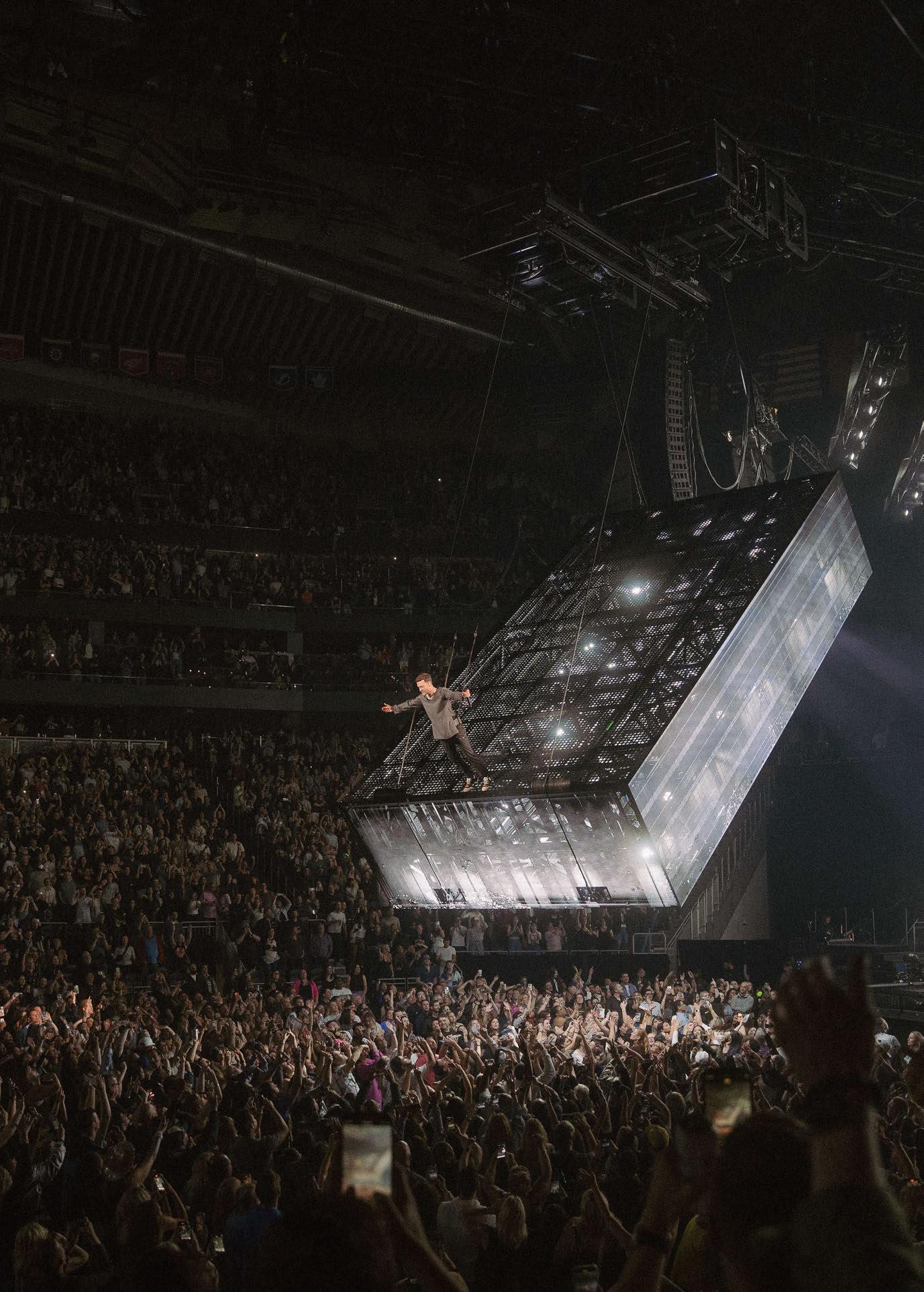
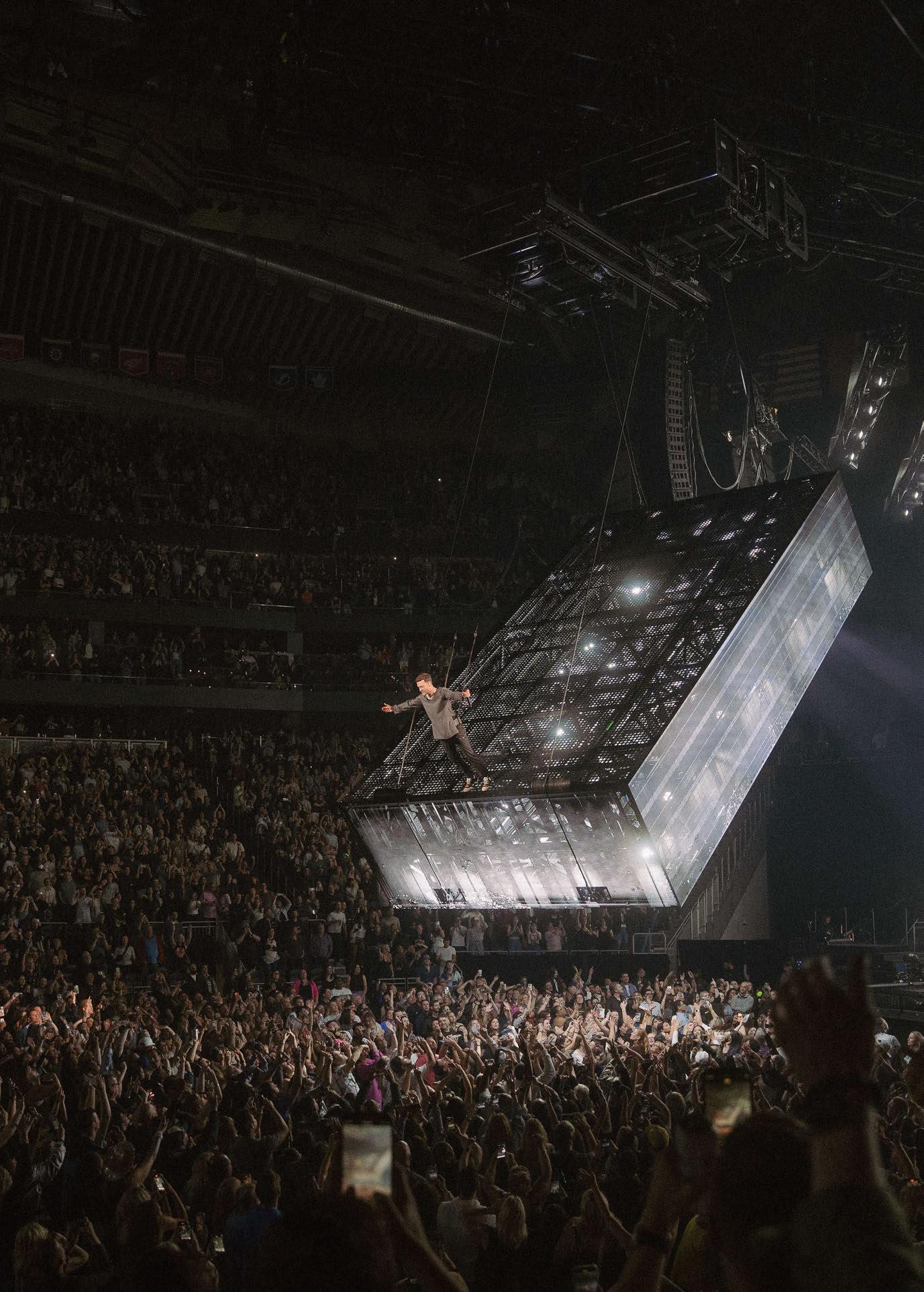
JUSTIN TIMBERLAKE: FORGET TOMORROW
Creatives,


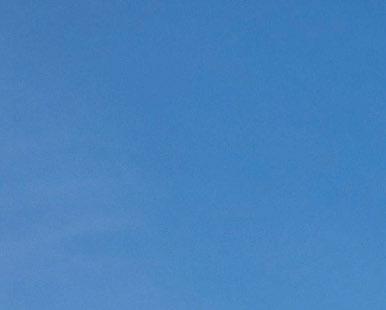

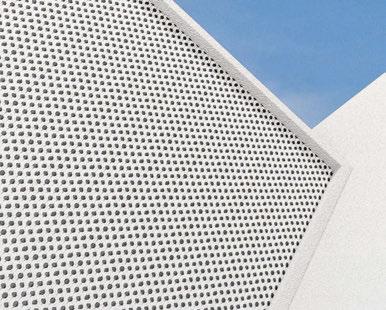
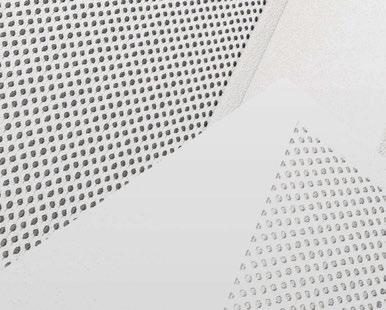
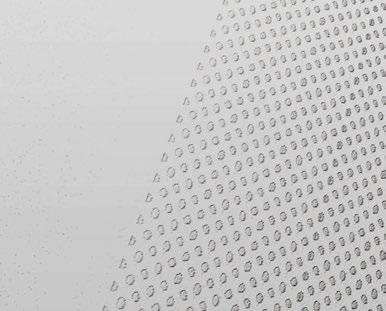
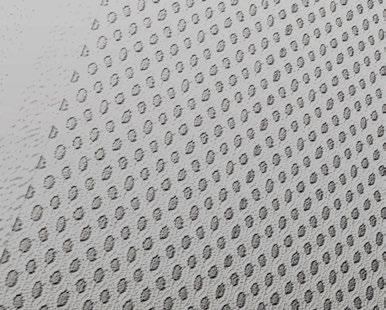
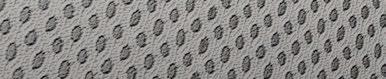
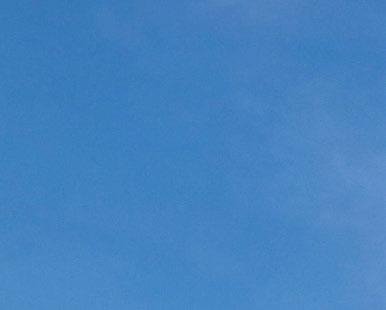
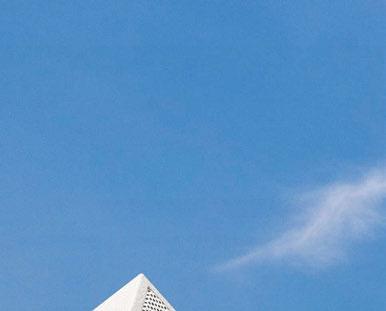
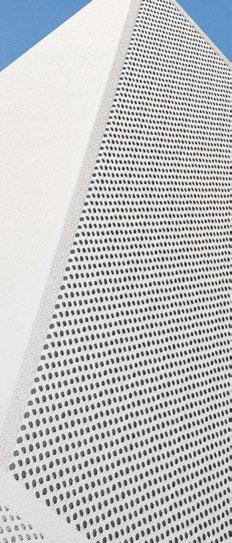
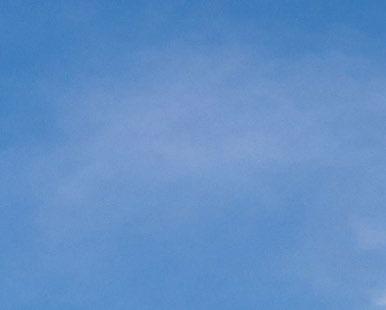

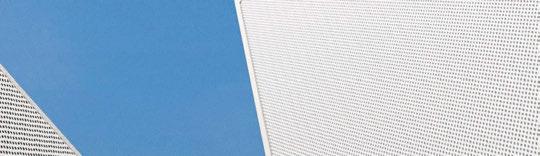
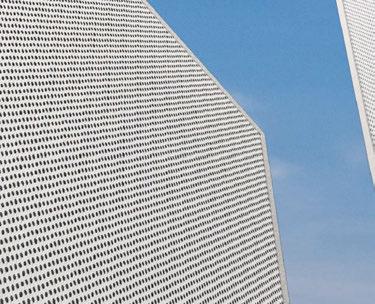
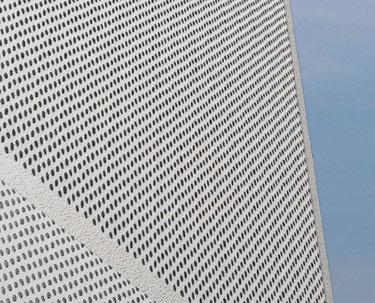
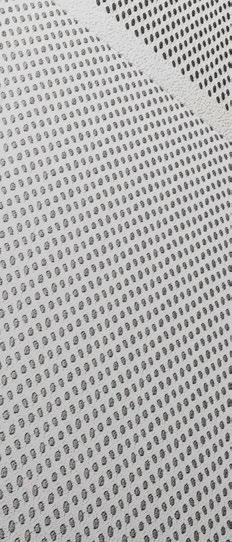
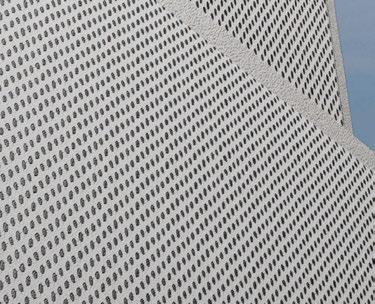
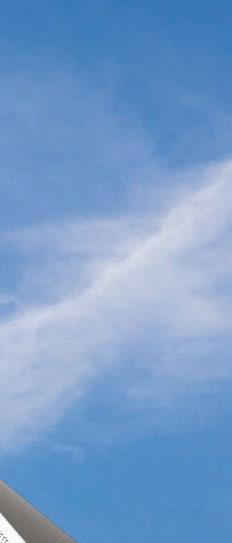
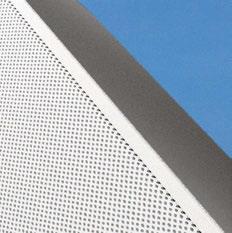
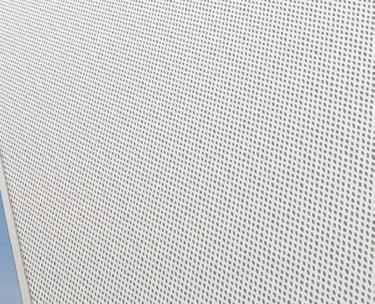
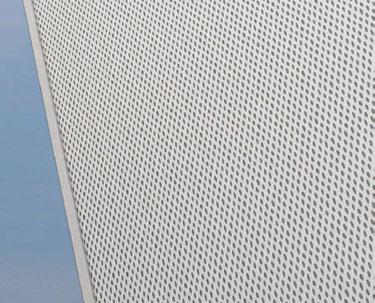
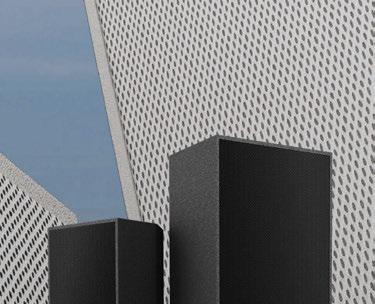

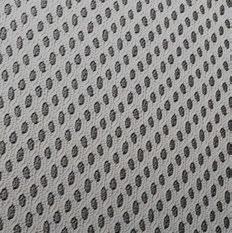
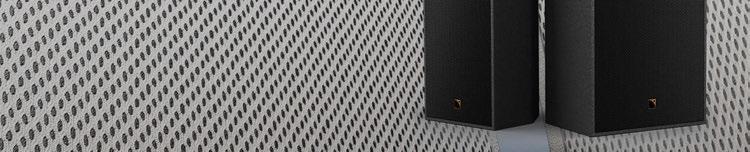
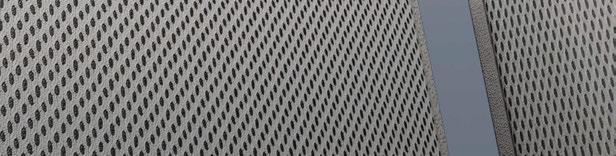
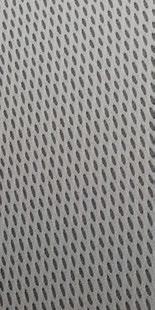
X6i
X8i

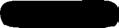
THE WASH BEAM FX
PROTEUS BRUTUS ™ 75000 lumens of cutting power!
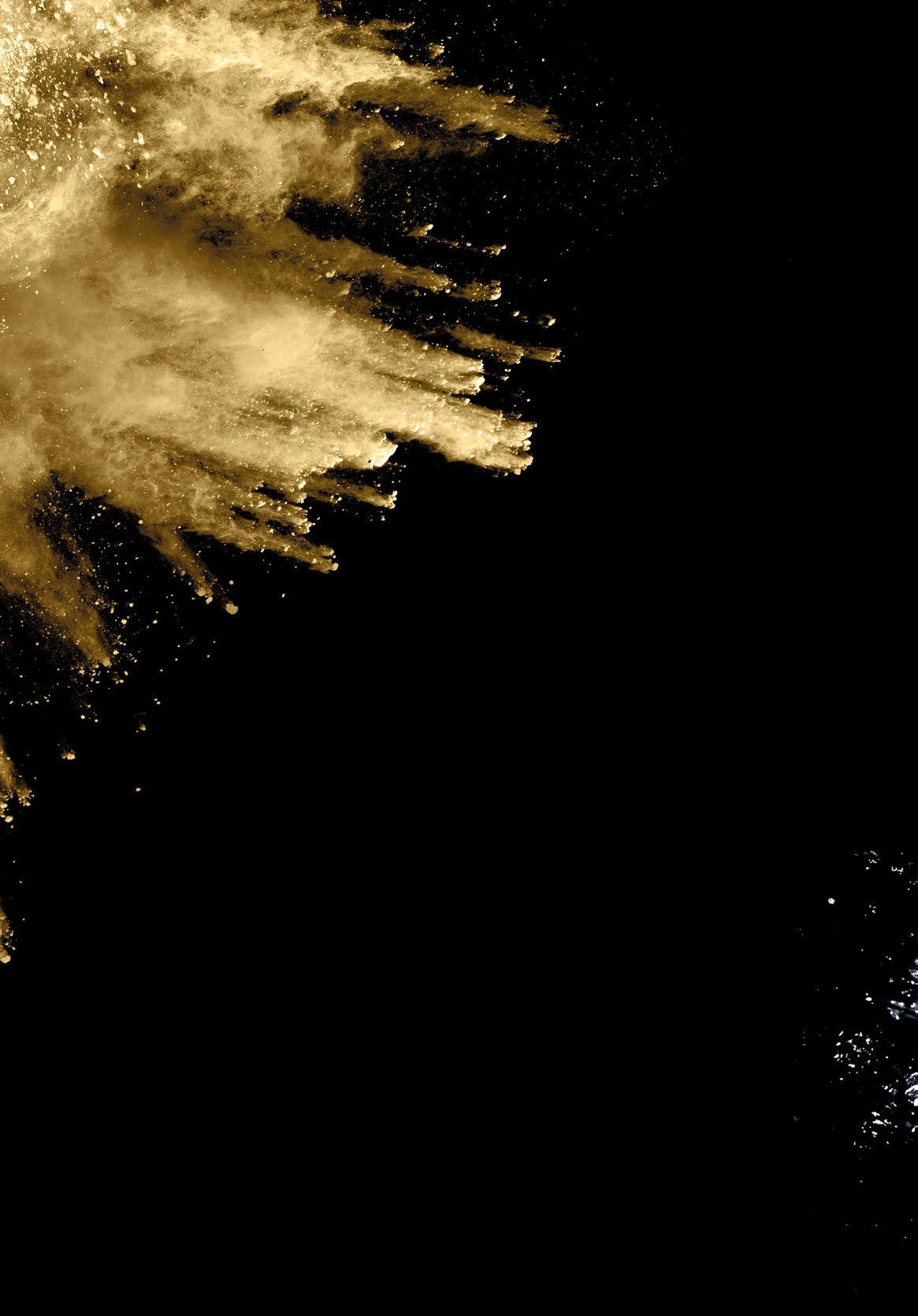
THE ULTIMATE POWERHOUSE PACKAGE FOR MAXIMUM IMPACT INDOORS OR OUT
!
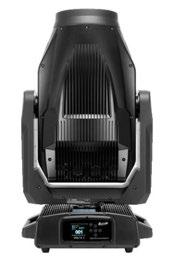
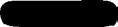
THE PROFILE
PROTEUS MAXIMUS ™ Market-proven all-purpose power luminaire!

THE BEAM
PROTEUS EXCALIBUR ™ Brightest IP65 full-featured beam fixture ever!

THE HYBRID
PROTEUS HYBRID MAX ™ Outperforms all other hybrids on the market!
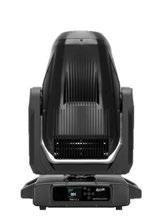
THE COMPACT
PROTEUS LUCIUS ™ Little but lethalthe Maximus mini-me!
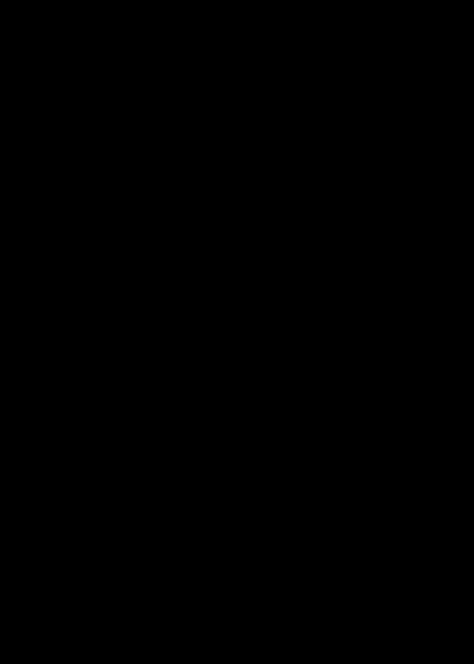
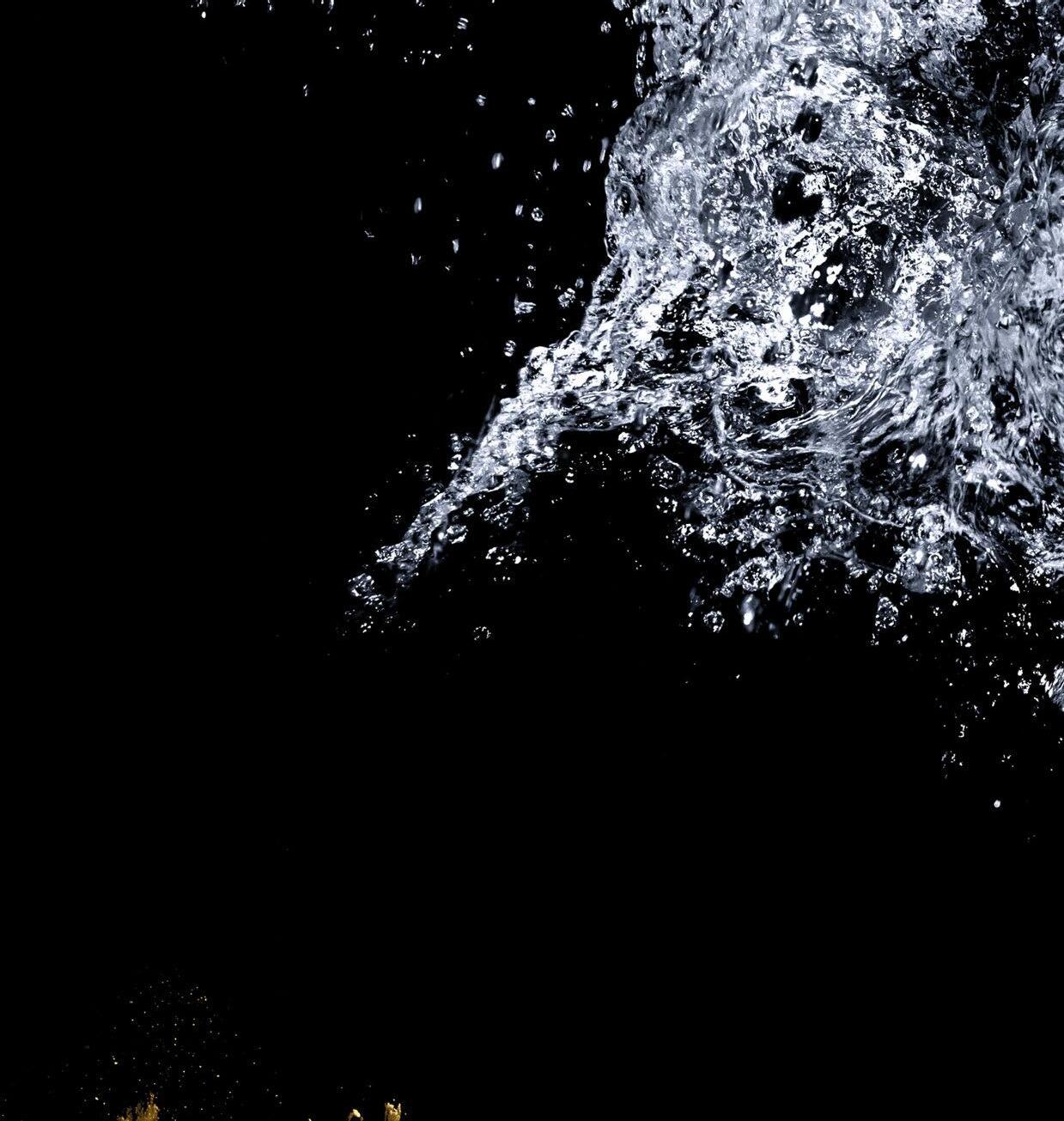
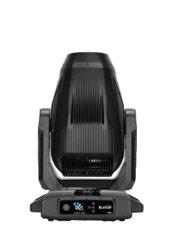
THE VARIABLE
PROTEUS ODEON ™ Industry´s first completely variable CRI LED engine!
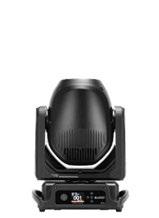
THE SOLID BEAM
PROTEUS RADIUS ™ Compact, high-intensity Beam FX!
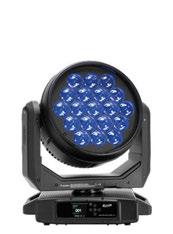
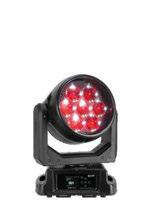
THE BEAUTY
PROTEUS RAYZOR ™ Beam, Wash, Sparkle. More than just a pretty face!
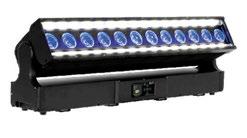
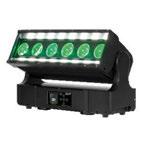
THE CREATIVE
PROTEUS RAYZOR BLADE ™ The market‘s most versatile FX bar!
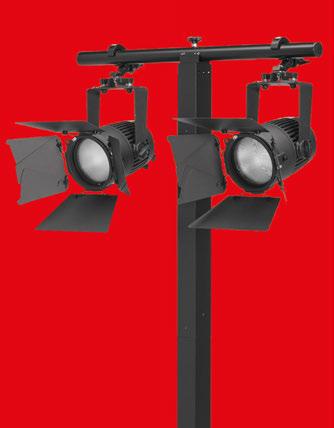
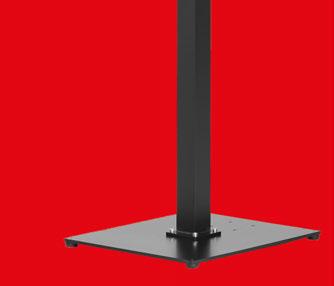
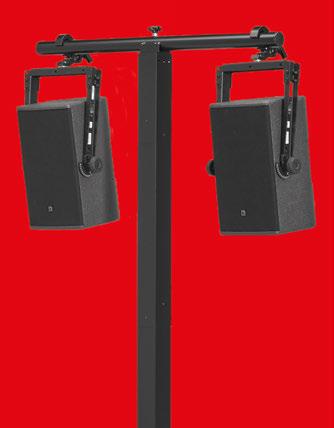
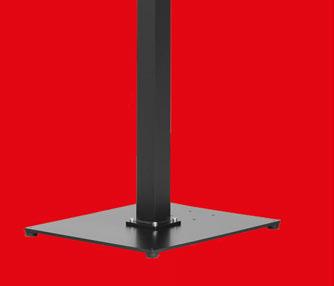
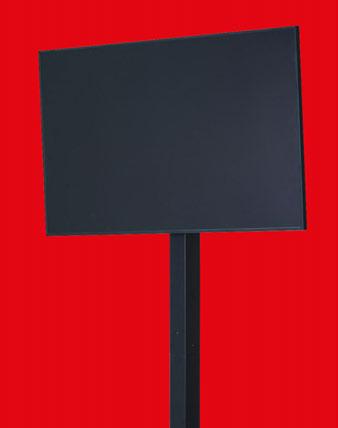

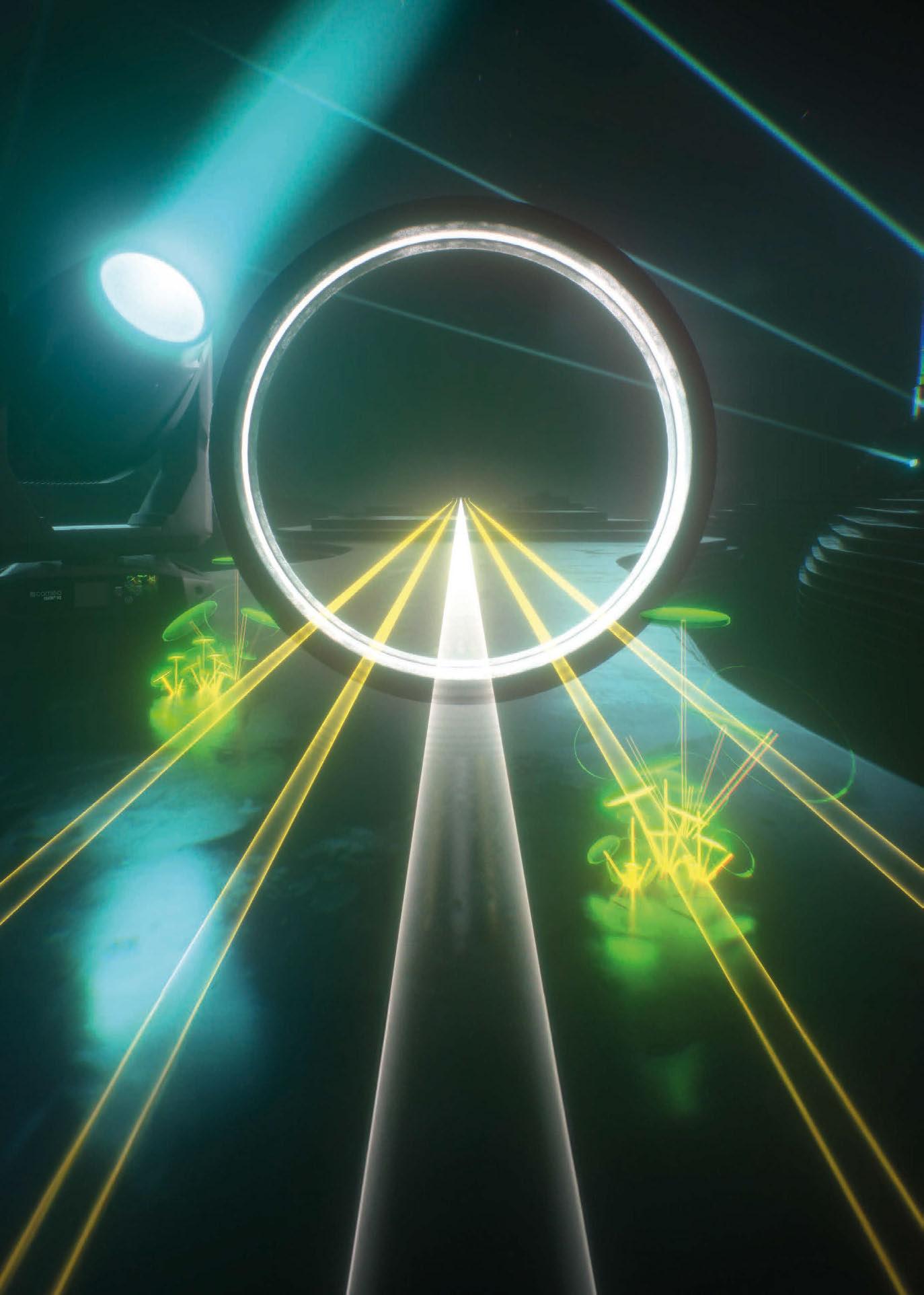
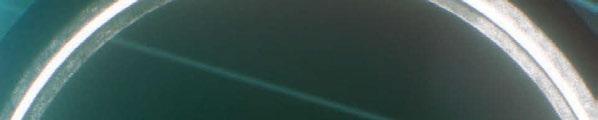
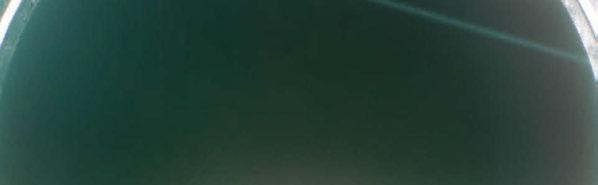
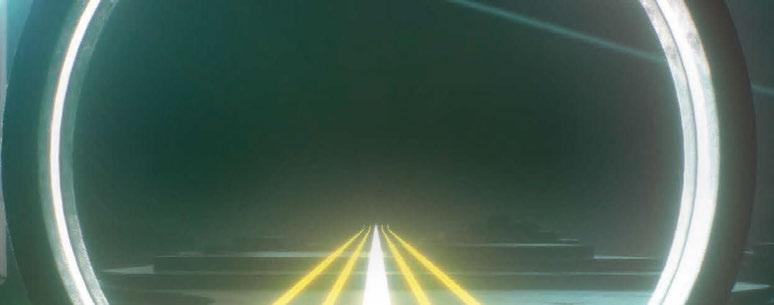

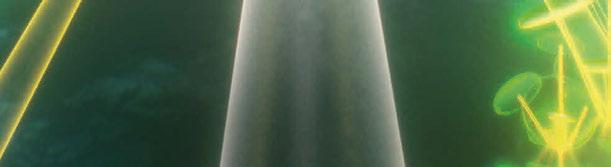

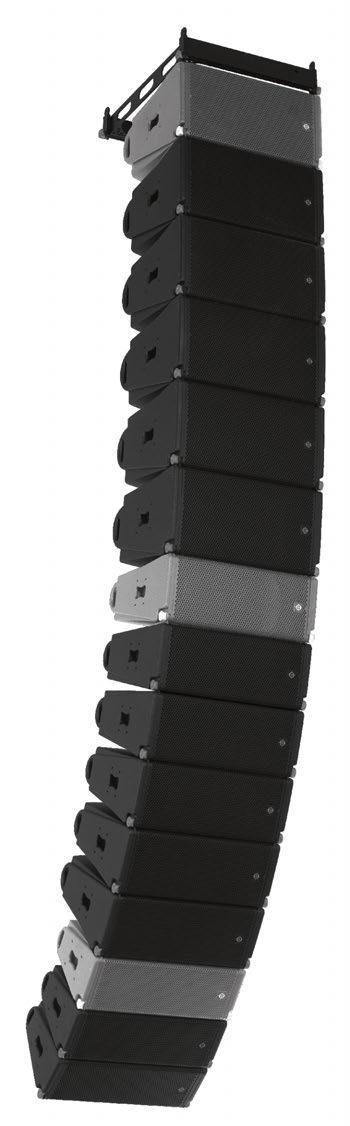
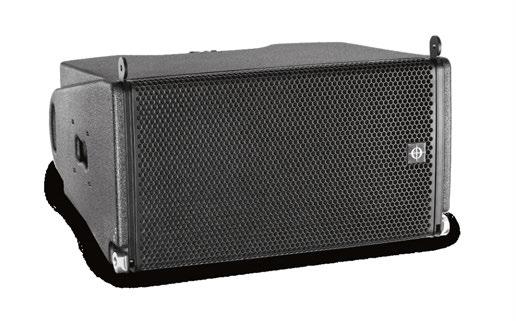

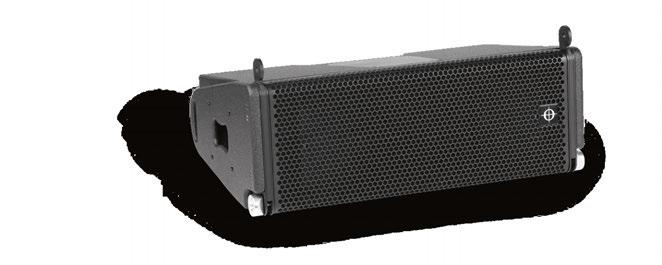
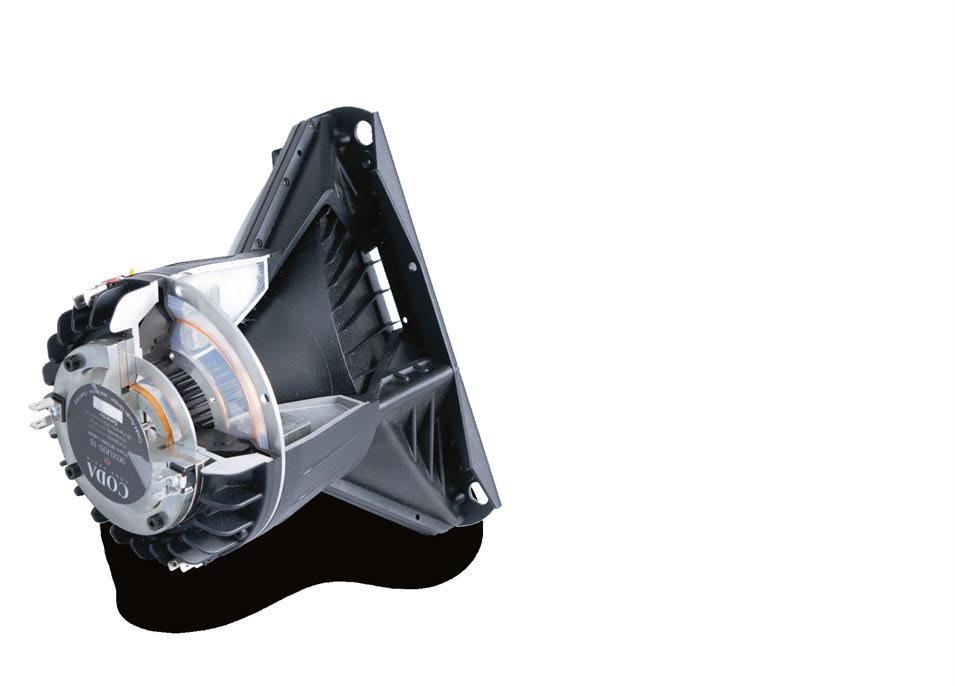
DDP Technology

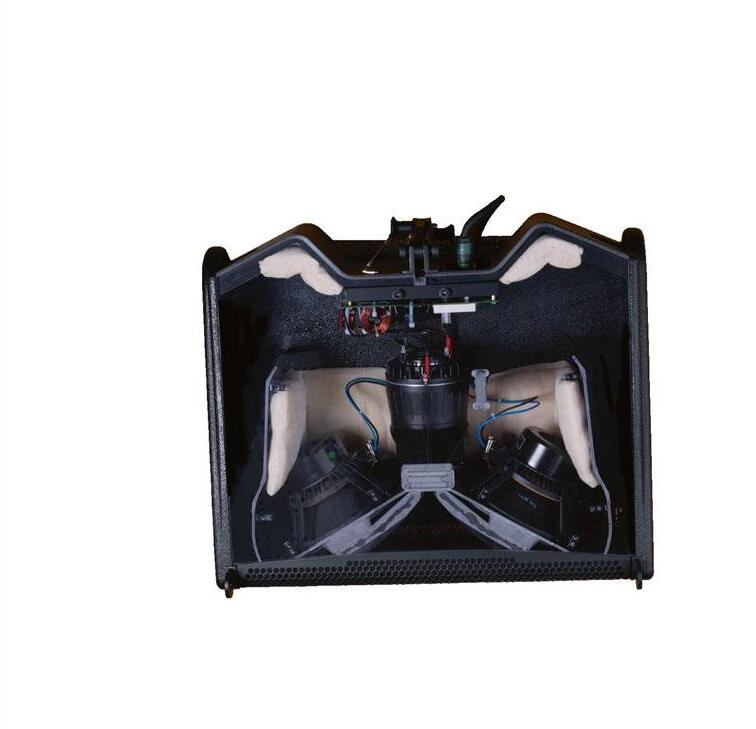
IN THE MAINSTREAM…
It’s the Monday before we go to print and the TPi office is alive with chat following Glastonbury weekend, with Alicia giving some first-hand accounts from the festival along with everyone trading their favourite highlights from BBC iPlayer. It’s always a weekend where the eyes of the world are firmly on the live events industry. More than just Glasto chat, the previous day’s Sunday Times has also dedicated a great deal of ink to live events, with an article exploring what it means to be ‘live’ following Dave Grohl calling out Taylor Swift live on stage, with our friends from ER Productions talking about how they survived through the COVID-19 pandemic, and a touching tribute to Fly By Nite’s late Dave Coumbe, who this edition of TPi is dedicated to [p12].
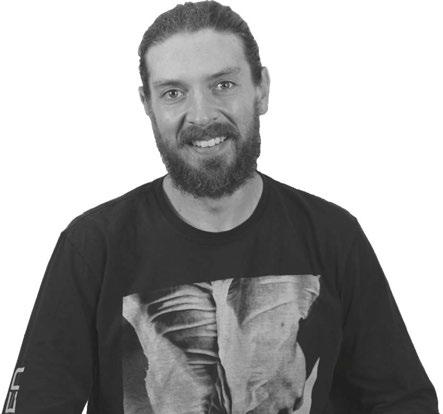
It ’s a great reminder of how privileged we are at TPi in getting a front row seat – or perhaps I should say a backstage pass – to the inner workings of the live events industry, and one which we’ve taken full advantage of in this bumper edition.
There’s a bit of a US theme running through this latest edition. This month’s cover story sees Jacob exploring the inner workings of Justin Timberlake’s latest North American tour – one of the most discussed productions of 2024, highlighted by an automated LED monolith that doubled as one of the more impressive flying elements seen this year [p42]. We also hear from the creatives of The Rolling Stones’ Hackney Diamonds tour [p20] along with the staging specialists responsible for Bad Bunny’s Most Wanted Tour [p26].
Continuing the American theme, Jacob headed to London’s O2 arena to catch Doja Cat’s first headline show at the famed venue in the midst of her European festival run [p58]. Meanwhile, Alicia covered two polar-opposite productions – from Elbow’s latest live offing that opened the brandnew Co-op Live in Manchester [p72], to speaking to the team behind High Lights, a new electronic dance festival in London featuring a jaw-dropping, brutalist overhead construction that defied expectations [p80].
Elsewhere in the issue, I tackle the topic of counterfeit products, speaking to the teams from MA Lighting and Avolites [p92] and draw insights from LIVE’s Powered by Freelancers – the Live Music Edition 2024 [p84].
Unt il next time, Stew Hume Editor.
Issue #282 July/August 2024
Editor Stew Hume Tel: +44 (0)161 476 8360 Mobile: +44 (0)7702 054344 e-mail: s.hume@mondiale.co.uk
Assistant Editor Jacob Waite Tel: +44 (0)161 476 8360 Mobile: +44 (0)7592 679612 e-mail: j.waite@mondiale.co.uk
Editorial Assistant Alicia Pollitt Tel: +44 (0)161 476 8360 Mobile: +44 (0)7508 441986 e-mail: a.pollitt@mondiale.co.uk
Commercial Director Fran Begaj Tel: +44 (0)161 476 8360 Mobile: +44 (0)7852 336728 e-mail: f.begaj@mondiale.co.uk
Account Manager Matilda Matthews Tel: +44 (0)161 476 8360 Mobile: +44 (0)7413 555978 e-mail: m.matthews@mondiale.co.uk
Account Manager Phil Tucker Tel: +44 (0)161 476 8360 Mobile: +44 (0)7522 130473 e-mail: p.tucker@mondiale.co.uk
Account Manager Sheelan Shah Tel: +44 (0)161 476 8360 Mobile: +44 (0)7401 690960 e-mail: s.shah@mondiale.co.uk
Digital Content Manager James Robertson Tel: +44 (0)161 476 8360 Mobile: +44 (0)7725 475819 e-mail: j.robertson@mondiale.co.uk
Marketing and Events Manager Alice Clarke Tel: +44 (0)161 476 8360 Mobile: +44 (0)7752 392465 e-mail: a.clarke@mondiale.co.uk
Editorial Director Peter Iantorno Tel: +44 (0)161 476 8360 Mobile: +44 (0)7763 233637 e-mail: p.iantorno@mondiale.co.uk
Chief Executive Justin Gawne Tel: +44 (0)161 476 8360 Mobile: +44 (0)7768 850767 e-mail: j.gawne@mondiale.co.uk
Accounts Lynette Levi / Sarah Miller: ar@mondiale.co.uk
Mondiale Group Chairman
Damian Walsh
Graphic Design & Production
Dan Seaton: d.seaton@mondiale.co.uk Jez Reid: j.reid@mondiale.co.uk
Cover Photo Justin Timberlake
Photo: Mark La Shark
Printed By Buxton Press • www.buxpress.co.uk
Annual subscriptions (including P&P): £42 (UK), £60 (Europe), £78/$125 (RoW).
Subscription enquiries to:
Subscriptions, Mondiale Media Limited, Strawberry Studios, Watson Square, Stockport, SK1 3AZ, UK. Tel: +44 (0)161 476 5580 Fax: +44 (0)161 476 0456 e-mail: subscriptions@mondiale.co.uk www.tpimagazine.com www.tpiawards.com
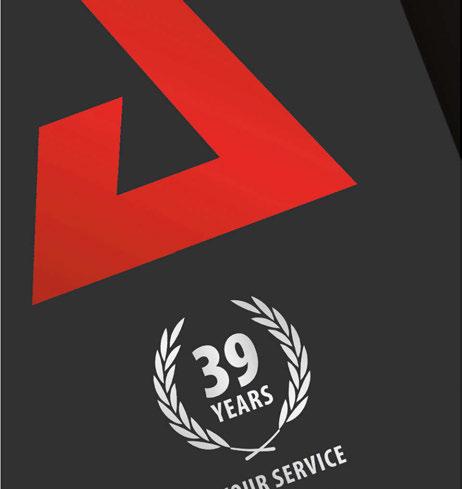
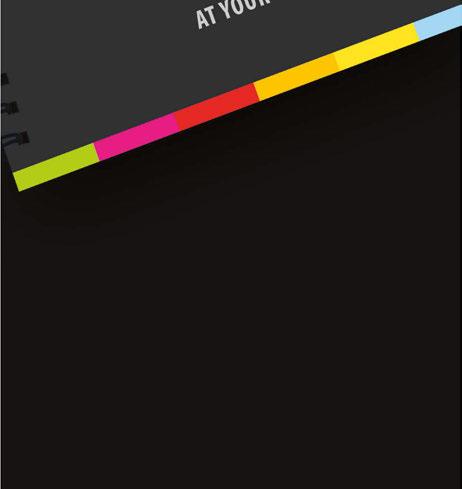
CHECK OUT THE LATEST AED CATALOGUE
ON THE COVER
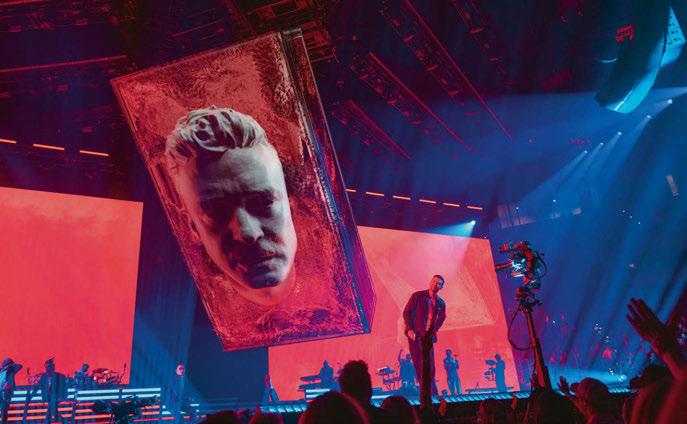
JUSTIN TIMBERLAKE
The singer-songwriter’s latest live offering lives up to his legacy of providing crowds with jawdropping moments.
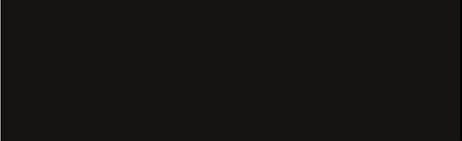
AED gives you access to the latest technology, without endangering your balance sheet. Use our business tools at your convenience to grow your business. or
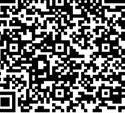
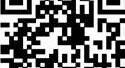
OBITUARY
12 Remembering David Coumbe.
EVENT FOCUS
14 The inaugural GTL Sessions.
20 Rolling Stones return to the US.
80 HIGH LIGHTS
A unique festival nestled among the trees of Barking Park.
INTERVIEW
84 Detailed insights from LIVE’s Freelancer Survey.
Please request your password here Already have a password?
AV BUSINESS TOOLS
RENT - SALES - LEASE - SECOND HAND - REPAIR - STORE
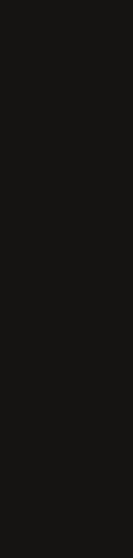
AED United Kingdom, Knaves Beech way, Loudwater, High Wycombe, Bucks HP10 9QZ
+44 1628 527 239 | info.uk@aedgroup.com
©2024 - AED group - www.AEDgroup.com
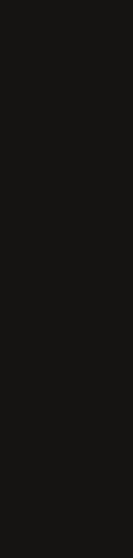
26 WICREATIONS and PixMob reflect on B ad Bunny’s latest tour.
30 Discover what it takes to host a festival on a public beach.
34 Creating visuals for the 68th Eurovision Song Contest
PRODUCTION PROFILE
58 DO JA CAT
Automated bridges, plasticcoated LED, and special effects make for a tour like no other…
72 ELBOW
The Manchester band return to arenas with a new-look show.
86 MAGIC FX previews sustainable solutions for live events.
88 Linking the worlds of CAD and acoustic simulation software with Vectorworks and L-Acoustics.
90 MA Lighting and Avolites highlight the issue of counterfeiting.
92 Claypaky’s Giovanni Zucchinali tackles the topic of innovation.
IN PROFILE
96 An inside look at Martin Professional’s redeveloped Hungarian factory.
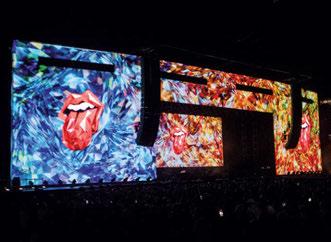
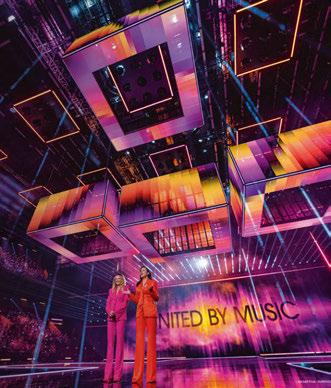





REMEMBERING: DAVID COUMBE
Fly By Nite’s Matt Jackson pays tribute to the legendary founder of one of the bestknown companies in the live events sector.
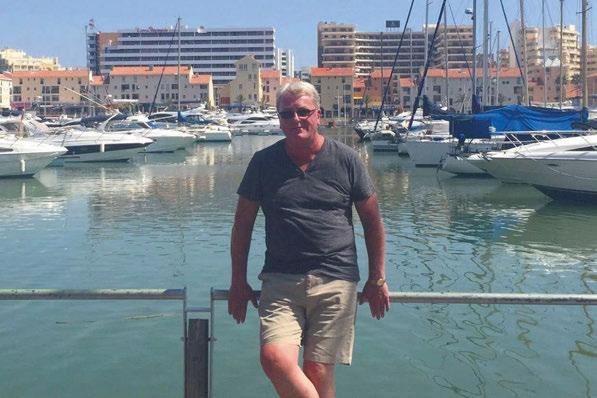
Last month, the live touring community received the shocking news that Fly By Nite’s David Coumbe had sadly passed away. Having established the company in 1989, Coumbe grew Fly By Nite into one of the world’s largest music production and logistics businesses, supplying specialised vehicles and dedicated drivers across the music, entertainment and exhibition industries. Coumbe led the company to achieve Favourite Trucking Company and Favourite Rehearsal Studios at the TPi Awards on many occasions and will be greatly missed by the entire industry. Matt Jackson, Fly By Nite’s Sales Manager, spoke to TPi about David’s legacy.
“W hat can I say about the great man... He was a legendary figure and a mainstay of FBN and the wider touring/events industry. David was a genius with an extraordinary ability to map things out in his head and retain an incredible amount of information, despite the fact that FBN had grown to its mammoth size by the time of his death. He had an incredible passion for the industry and an outstanding work ethic to match. He dedicated his life to building a successful business that started from nothing and drove its success personally. He set the highest of standards for others by the commitment he displayed on a daily basis.
“He was a man who was calm under pressure and always confident a solution could be found despite the circumstances. His knowledge and expertise of European logistics was unrivalled and he always remembered the best routes to take and borders to use, passing on that knowledge and expertise to those around him – including myself. I was incredibly fortunate to spend over a decade sharing an
office with him. I tried my best to get him to embrace technology but to no avail. He didn’t save any numbers in his phone, always relying on a folded up piece of A4 paper with numbers printed or written on. It was comical and at times you would scratch your head with him but at the same time, he could blow you away with an incredible piece of skill or knowledge.
“I recall most recently at an insurance renewal meeting at the end of last year, our Transport Manager Richard had stated the number of trucks now on the fleet following the latest batch of new vehicles being added. David was adamant that the number he had in his head was different but Richard seemed very confident in his figures. He left the room to check his records and while he was gone, Dave continued the meeting with the brokers based on his figures. ‘I know my figure is right as I remember signing the deals/finance for them’. Richard returned to the room and acknowledged the figures David had suggested were indeed correct. Richard is a very thorough person and keeps detailed records of everything but he had been upstaged by the brain of a genius, which was certainly no disgrace. For the rest of the meeting, the rest of the room were just in awe of the man and as such we struck a deal on favourable terms.
“David took the time to know his staff on a personal level. He loved the industry for the people it brought him into contact with – both staff and clients. He went out of his way to help others. He was a good man with a good heart.
“During COVID, we were still working in the office managing the general haulage work but it wasn’t as time consuming as our regular touring event work. So, to keep us occupied
we set up table tennis in the warehouse and we had some epic encounters. We were both ultra-competitive; Dave was a much better player than me but I had a deliberate tactic being almost 30 years his junior – I knew I would have a stamina advantage so I would keep him in a rally until he would get frustrated and try something risky and make a mistake. On the odd occasion he got the better of me, we wouldn’t hear the end of it for weeks on end.
“Dave was the boss, but he never made his presence known in an authoritative way. He liked others to have their say and I always found he would support our decisions and choices. He led by example, commanding respect from people with his personal and dedicated approach. I feel lucky to have known Dave so closely and to have learned so much from him. He was a mentor and inspiration, a big influence on my life and career. It’s difficult adjusting to life without him around and I still expect him to wander into my office for a chat about business or football. I will miss him dearly.
“Thanks for everything, boss. You were never one for accepting praise, but I hope you knew just how much you were loved and respected by your staff and the wider industry. You deserved every bit of success you had. It’s tragic you didn’t get to retire and relax after all your hard work, but I’m not sure that was your style anyway! We will keep the FBN flag flying high for you and build on your incredible legacy!
“Thank you to the entire industry for the love and support all of us at FBN have received. There have been some touching tributes and it has helped us all through this incredibly sad and difficult period.”
www.flybynite.co.uk
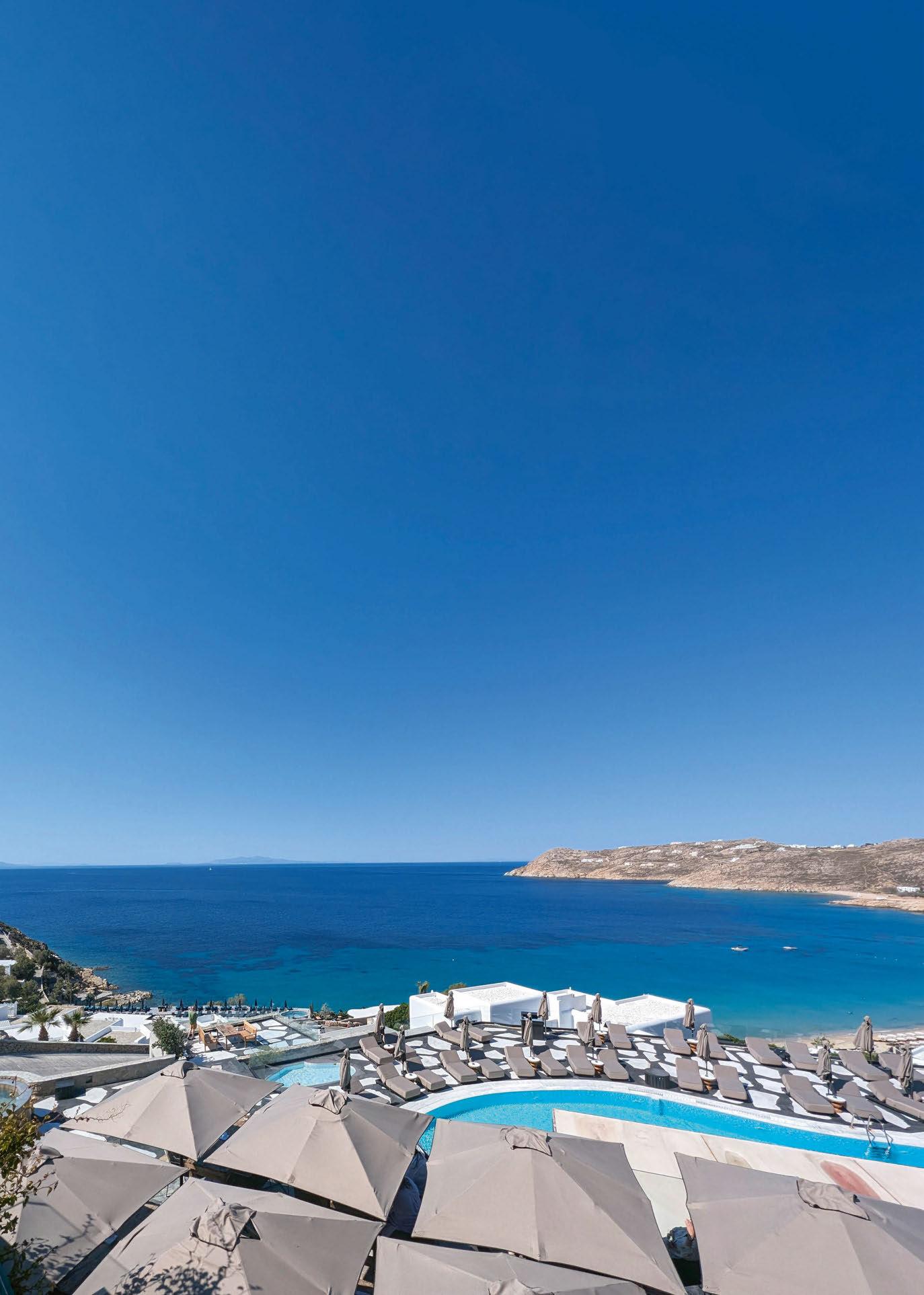
RETURNING TO MYKONOS MAY 2025
Register your interest here:
GTL SESSIONS
TPi launches a brand-new event designed to bridge the gap between tour managers and service providers, presenting attendees with an exclusive networking experience unlike any other...

Words: Stew Hume
Photos: James Robertson
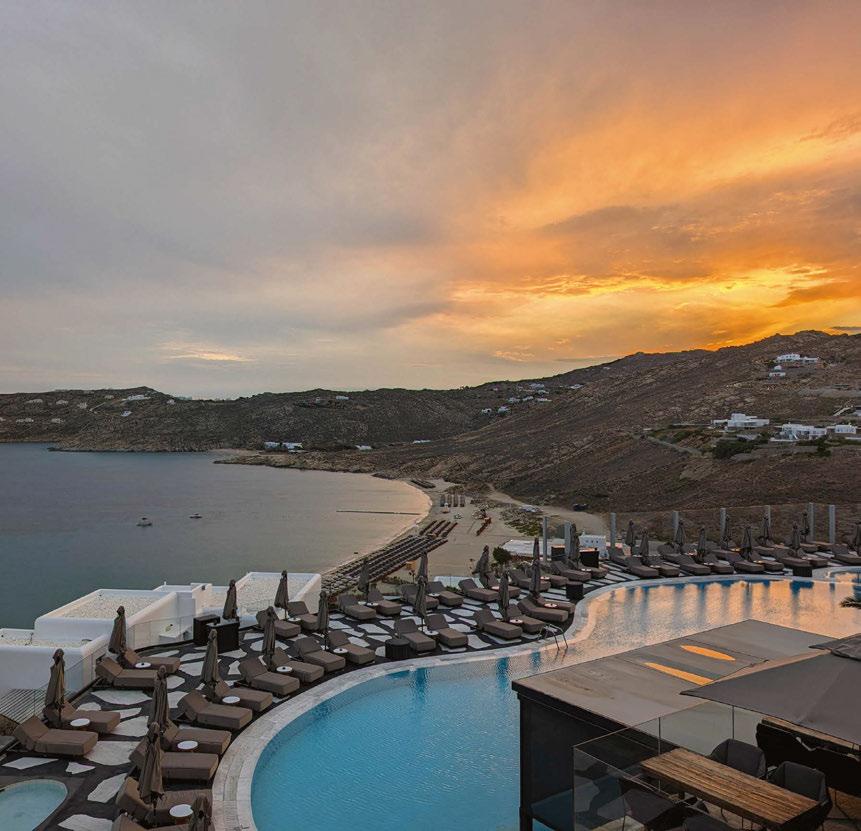
It was a surreal experience speaking to our esteemed guests in a welcome speech during the inaugural GTL Sessions on the balcony of The Royal Myconian Hotel in Mykonos, Greece. As the sun set on day one, I recalled the origin story of the event, which began in the far less spectacular surroundings of a Pizza Express in Manchester. Between slices, Fran Begaj, Alice Clarke and I plotted a brandnew event – one the likes of which had never been seen in the live events sector.
For years, countless companies have attend the TPi Awards with the main goal of connecting with tour managers – not an easy task when you’re trying to meet people within an audience of over 1,700. The companies in question came from a wide variety of backgrounds, from those that provide private transport to insurance. While they’re more peripheral suppliers than, say, audio, lighting or video rental houses, they still play an integral part of any touring machine. The question was, how do we connect these two camps of suppliers and tour manager? Thus, the concept of GTL Sessions started to take form.
Some 18 months later, TPi and a cohort of specially selected attendees descended on the island of Mykonos for three packed days of networking, relationship building and information sharing.
The main two days of the event took the form of a mixture of 10-minute meetings between tour managers and suppliers, which were broken up by talks covering a range of subjects from the importance of mental health
transform.engine
by fourieraudio
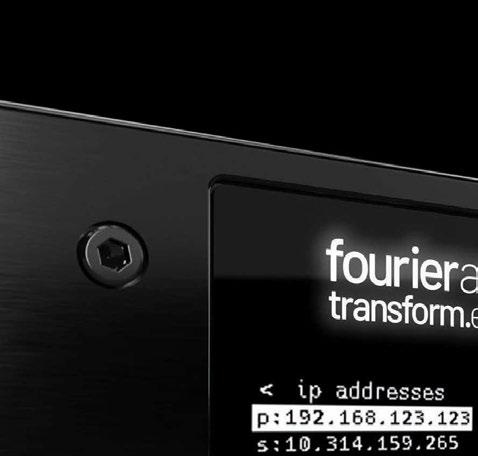
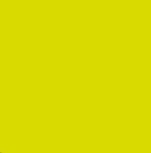

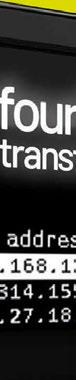
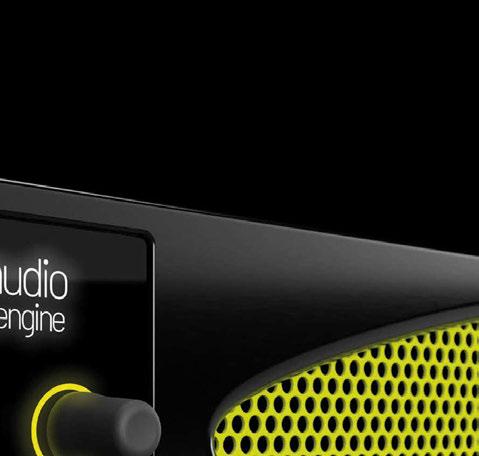
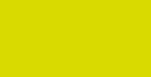


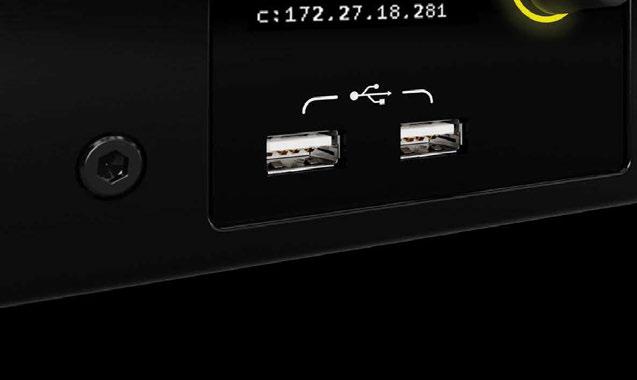
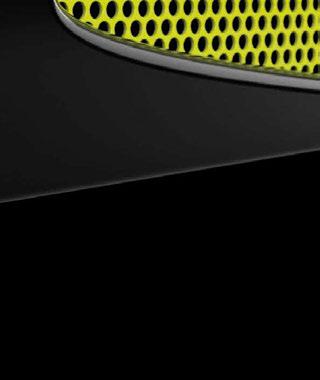
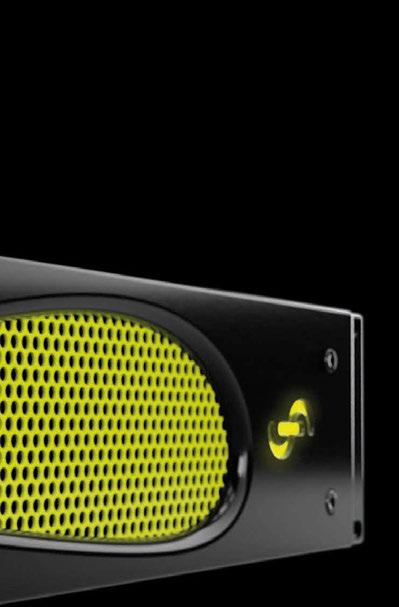

live plugin host.
64 channels. rock-solid reliability. ultra-low latency. DiGiCo integration now shipping:
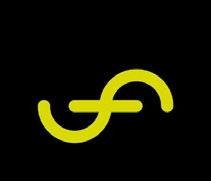

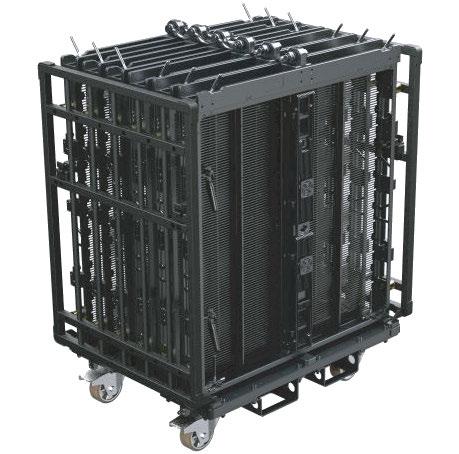
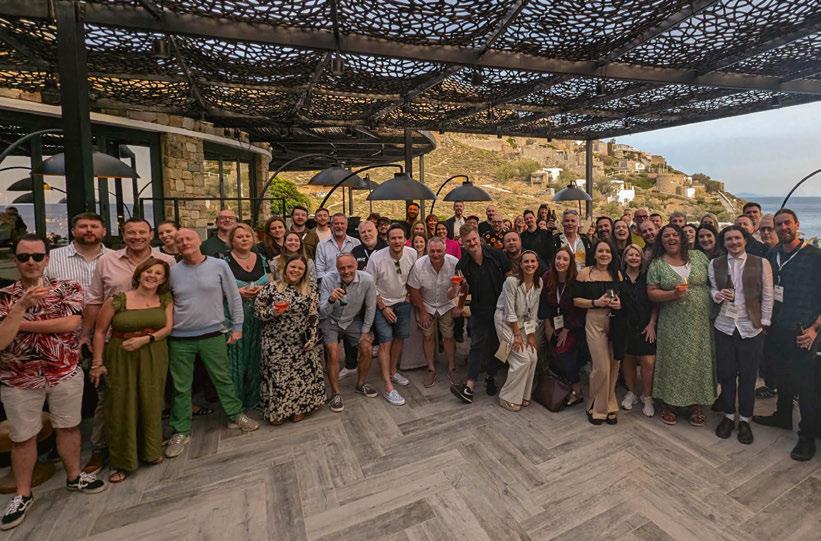
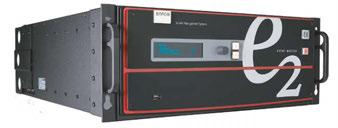
in the events industry to the new world of ‘virtual concerts’ such as ABBA Voyage and KISS’ transformation into avatars.
The meetings – dubbed Speed+Sync sessions – were set up in advance, with suppliers getting to select the TMs they were particularly interested in connecting with during the event. The meetings took place not in a stuffy windowless hall but on the upper floor of The Royal Myconian, offering stunning views over the cove.
Away from the scheduled meetings and talks, all attendees were given the late afternoon off to enjoy the facilities within the hotel or to continue their conversations from the day by the pool. Then each evening all guests gathered to break bread and, in the case of one evening, several plates – we were in Greece after all.
As for as the tour managers, the goal was to bring a wide selection of those within the industry – from TMs looking after stadium- and arena-level headliners to those representing more niche, up-andcoming artists. This led to a great spread of opinions from all areas of the industry. As was commented by more than a few tour managers throughout the duration of GTL, this must have been one of the largest gatherings of TMs in one place at one time where they were free to talk to one another.
“T his has been my favourite ‘industry event’ ever,” stated Ade Bullock, Tour Manager for The Smile and Radiohead. “It was intense but focussed and people
had plenty of time to get to know one another.” One of the more up-and-coming TMs in attendance was Samantha Simm (Everything Everything). “I wasn’t sure if I was in a place in my career where the top hoteliers and vendors would take me seriously, but I was very happy with the results of this trip. My confidence has been boosted massively and I’ve mingled with some fantastic people.”
The goal from the supplier’s standpoint was also to have a wide variety of companies represented at the event; from hoteliers, travel agents and insurance brokers to those offering specific products to tour managers.
One such company in this latter section was TourManagement.com and its founder, Roeland Veugelen, who also featured in one of the Symposia sessions during the week.
“T he inaugural GTL Sessions exceeded my expectations,” stated Veugelen. “It provided valuable insights and numerous networking opportunities with relevant tour managers. The organisation was seamless, and the sessions on tour life, mental health, and education were particularly engaging. It was a fantastic event, and I look forward to maintaining the connections made and participating again.”
The Symposia sessions kicked off with a presentation by 2024s TPi Industry Recognition Award winner, Tamsin Embleton, who shared her recent work researching the issues of mental health
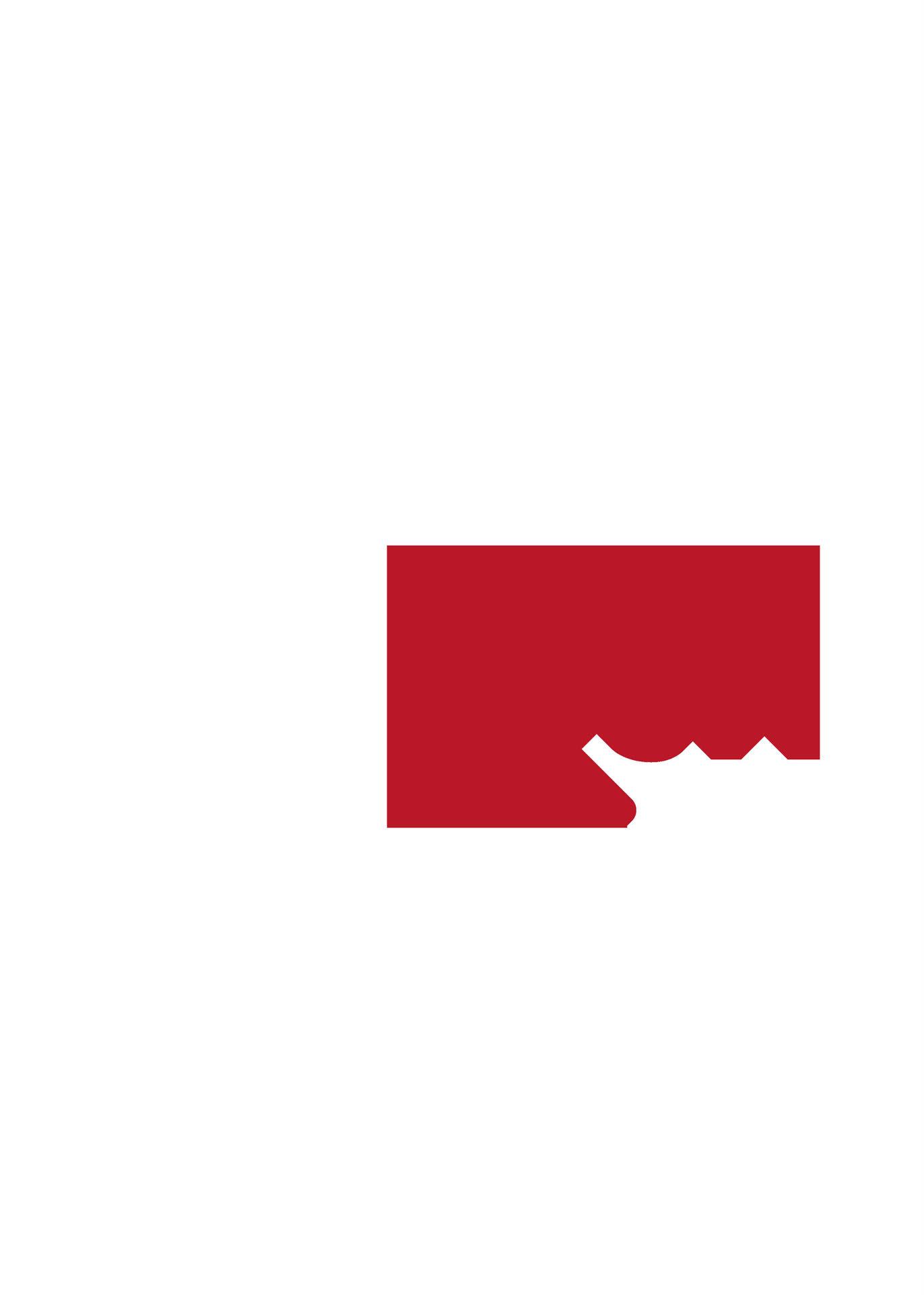
PUSH
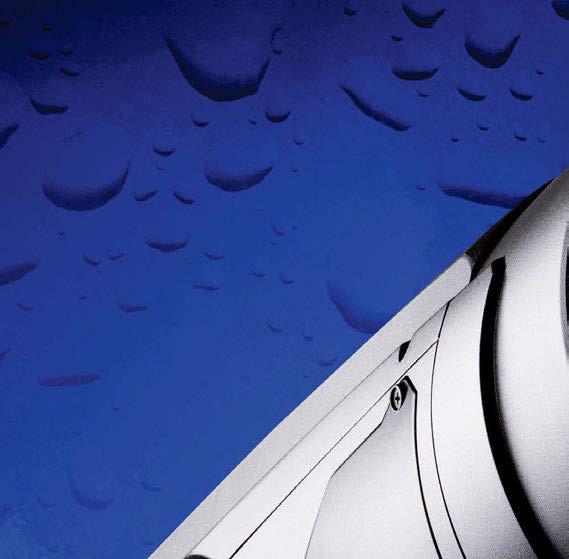
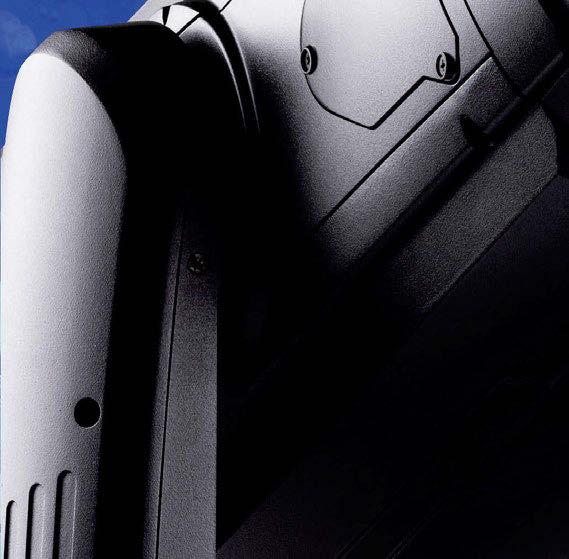

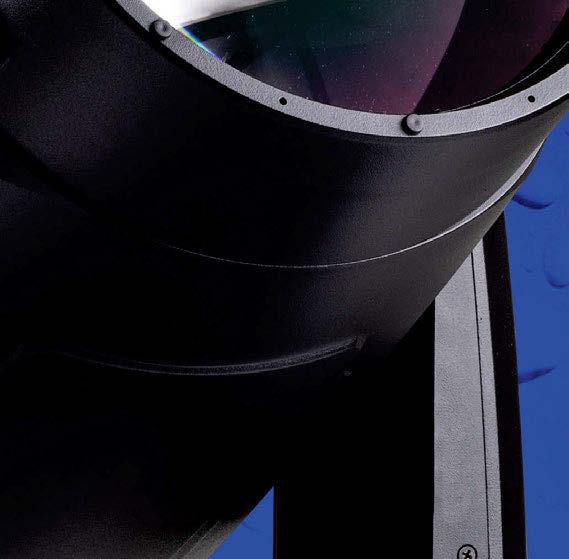

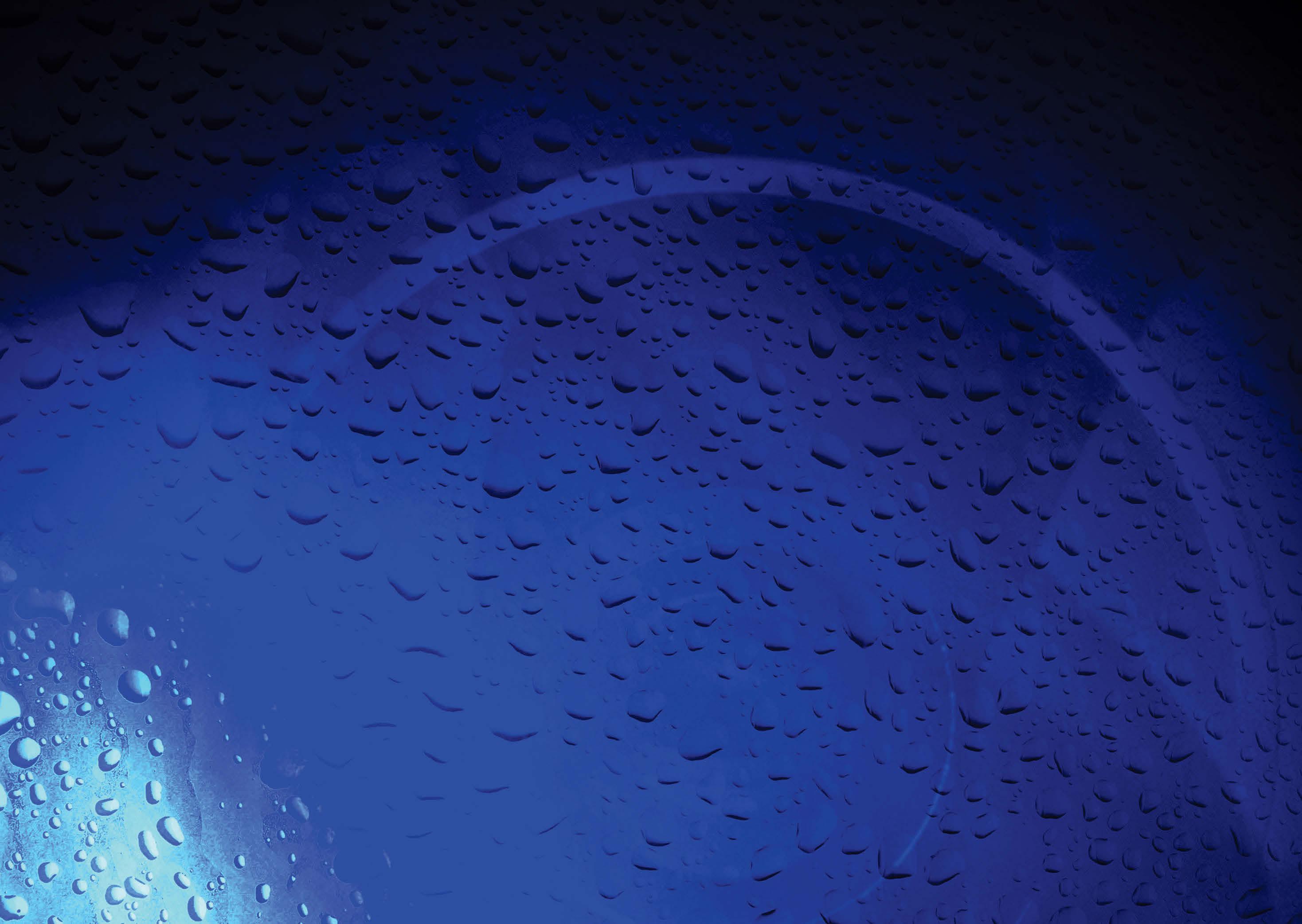
ALL WEATHERS OUR RELIABILI
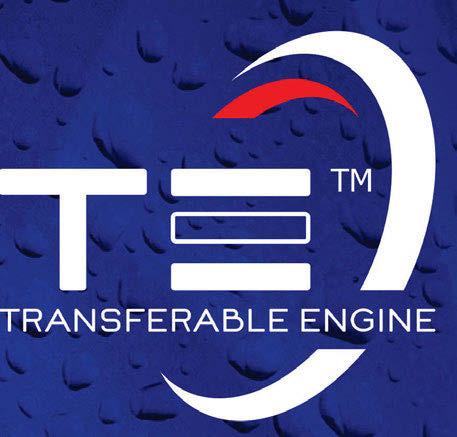
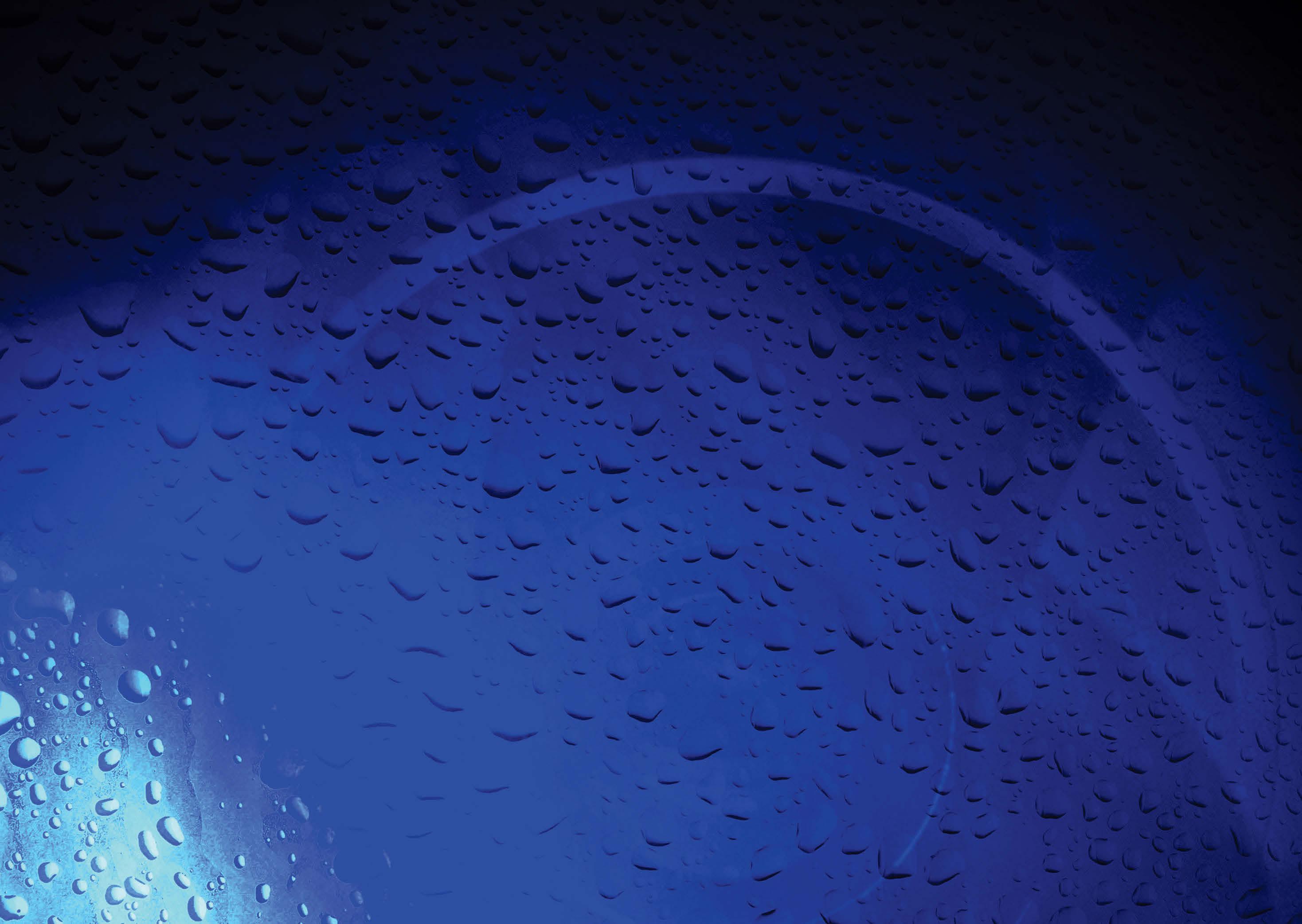




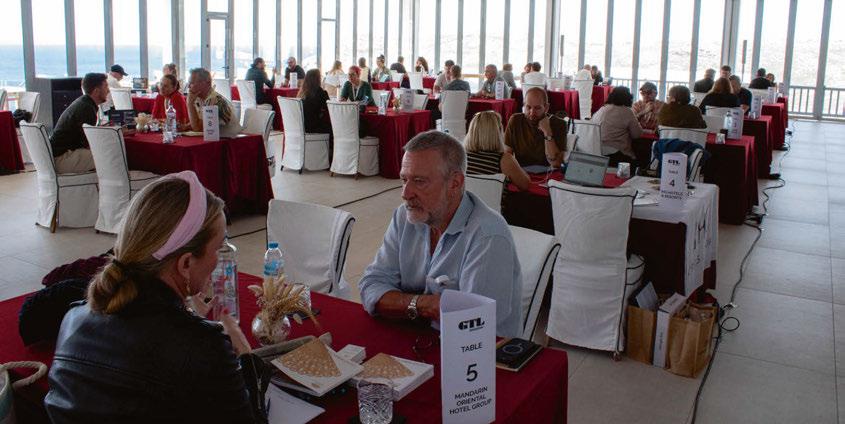
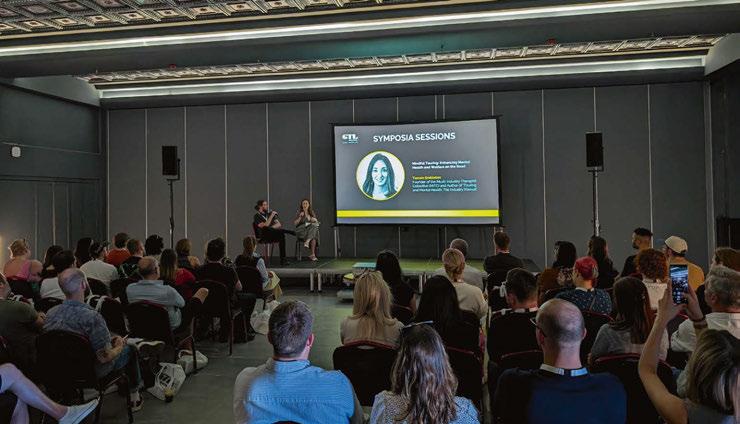
within the live events Industry, all of which is well-documented in her book Touring and Mental Health: The Music Industry Manual
GTL Sessions also welcomed Kyoto’s Glen Rowe to the stage to discuss education pathways within the sector and what those in attendance might be able to do to aid those looking to break into industry. During this session, AJ Sutherland shared his thoughts, highlighting the work of 3T and WILM along with Alice James who, among many hats, lectures at BIMM Institute London. Rock-it Cargo’s Chris Palmer closed out the first day’s talks, with an engaging panel on freighting for some of the world’s biggest artists.
On d ay two, Paul Jones reviewed key insights from LIVE’s much anticipated Freelancers Survey [p84]. Amid this impassioned talk, Jones detailed the realities and pressure points associated with life as a freelancer in the live events sector, backed up by data. He closed by suggesting solutions –from improving working conditions to diversity within the field.
In t he afternoon session, GTL Sessions welcomed Steev Tooth – KISS’ Tour Manager,
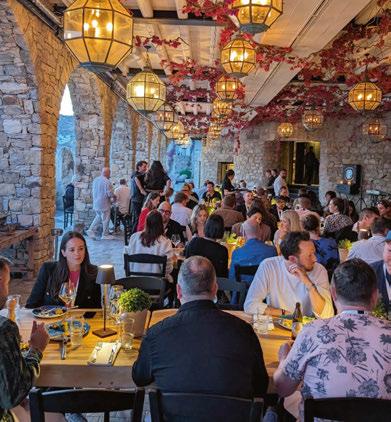
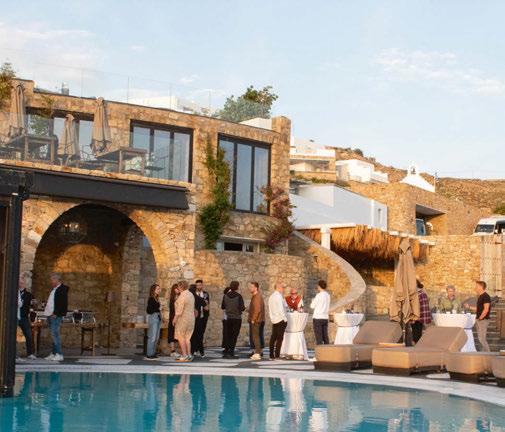
and Stu Phillips, Tour Manager for The Warning and owner of House of Tours Global to the stage. The duo shared their experience and involvement in transporting live events into a digital realm. From the legendary glam rockers’ transformation into avatars to Phillips’ company offering virtual studio solutions, it was certainly an interesting discussion.
Finally, Tour Manager, Roeland Veugelen of TourManagement.com, closed out the sessions, previewing some of the changing aspects of the tour management role, and sharing how his platform caters to the requirements of end users.
“L aunching a brand-new event is never a simple task, and although we had every faith in the concept, it’s safe to say that the end result far more than exceeded our expectations,” TPi Editor, Stew Hume commented. “In a world of endless email threads and scheduled Microsoft Teams calls, GTL Sessions underlined the importance of face-to-face interactions and in-person networking.”
GTL Sessions will return in 2025. Visit the website below to register your interest. www.gtlsessions.com
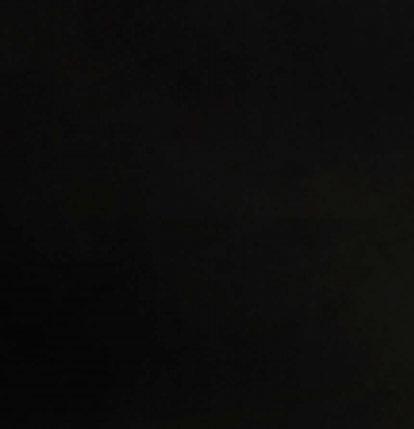

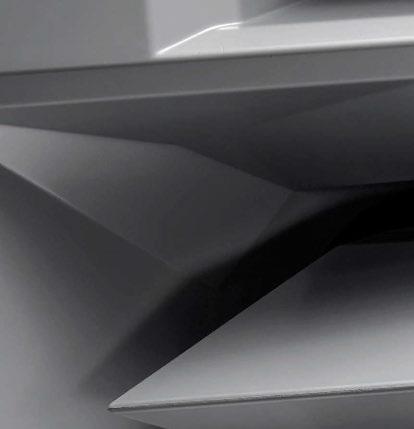
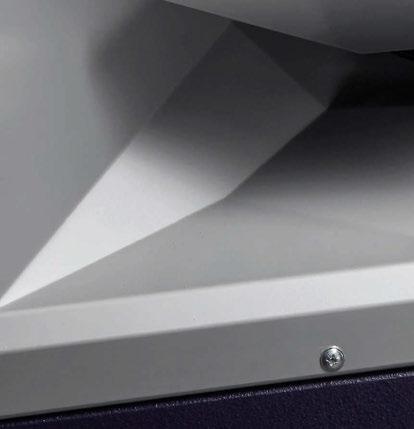
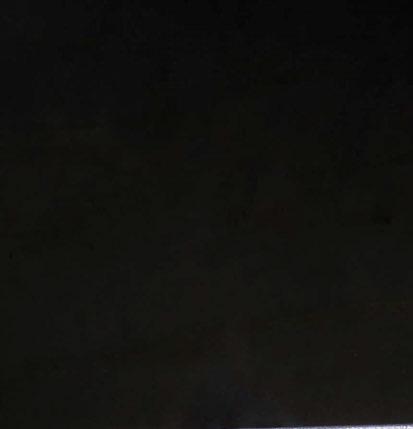
High Performance Loudspeaker Systems
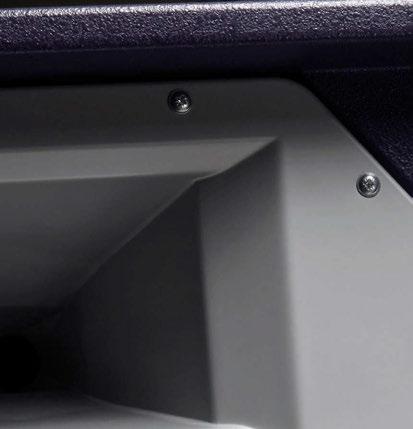
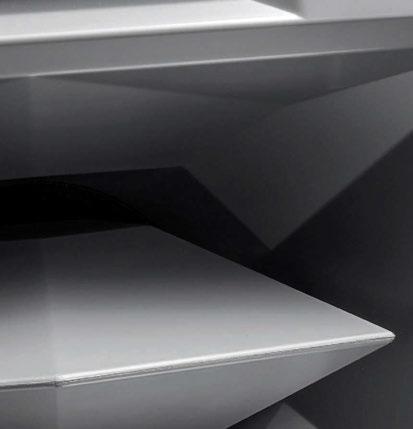
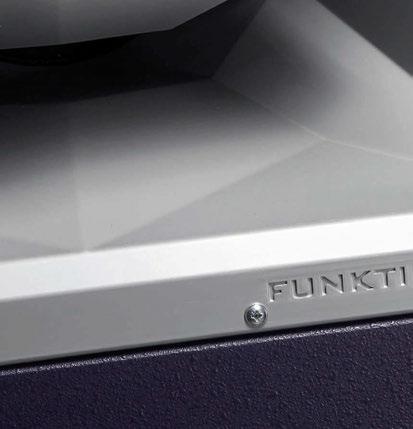
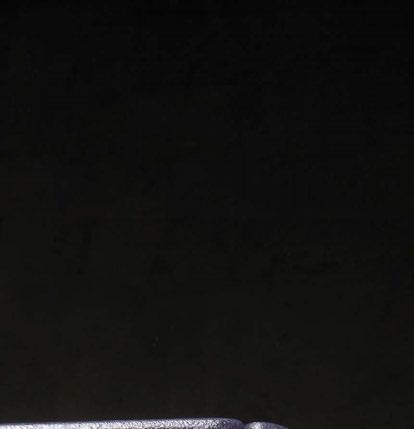
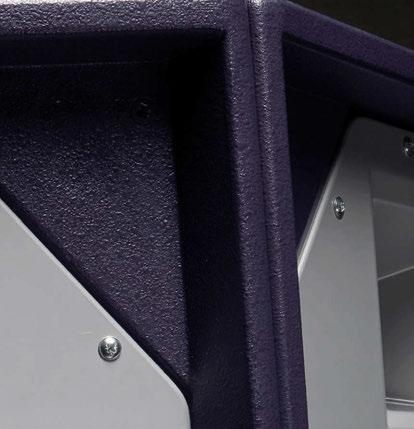
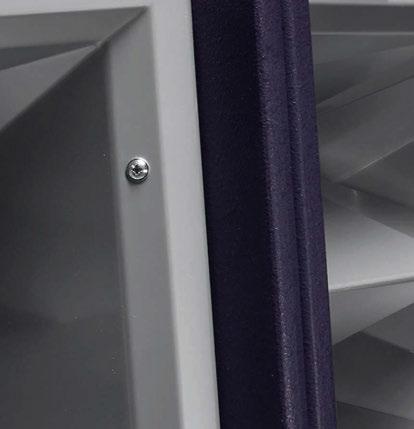
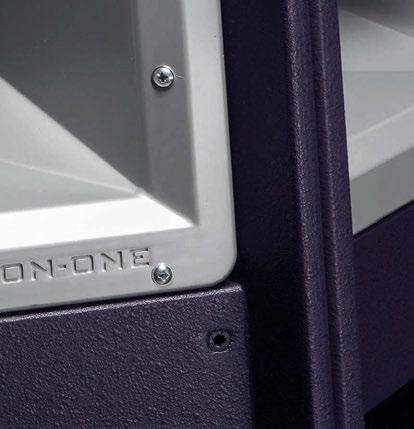
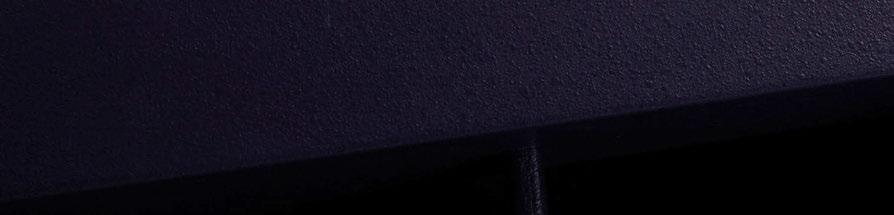
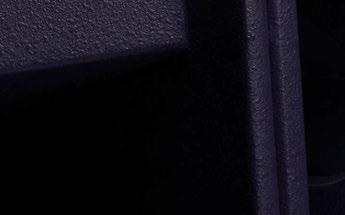
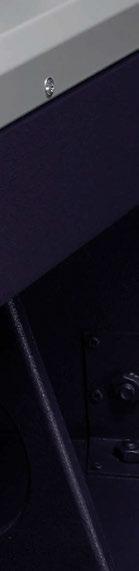
THE ROLLING STONES: HACKNEY DIAMONDS
The long-serving creative team behind the legendary rock band unite to create a new stage in support of The Rolling Stones’ 24th studio record – Hackney Diamonds. True to form, the team ensures a contemporary and modern feel with a greater use of LED and visual content than ever before.

Words: Stew Hume
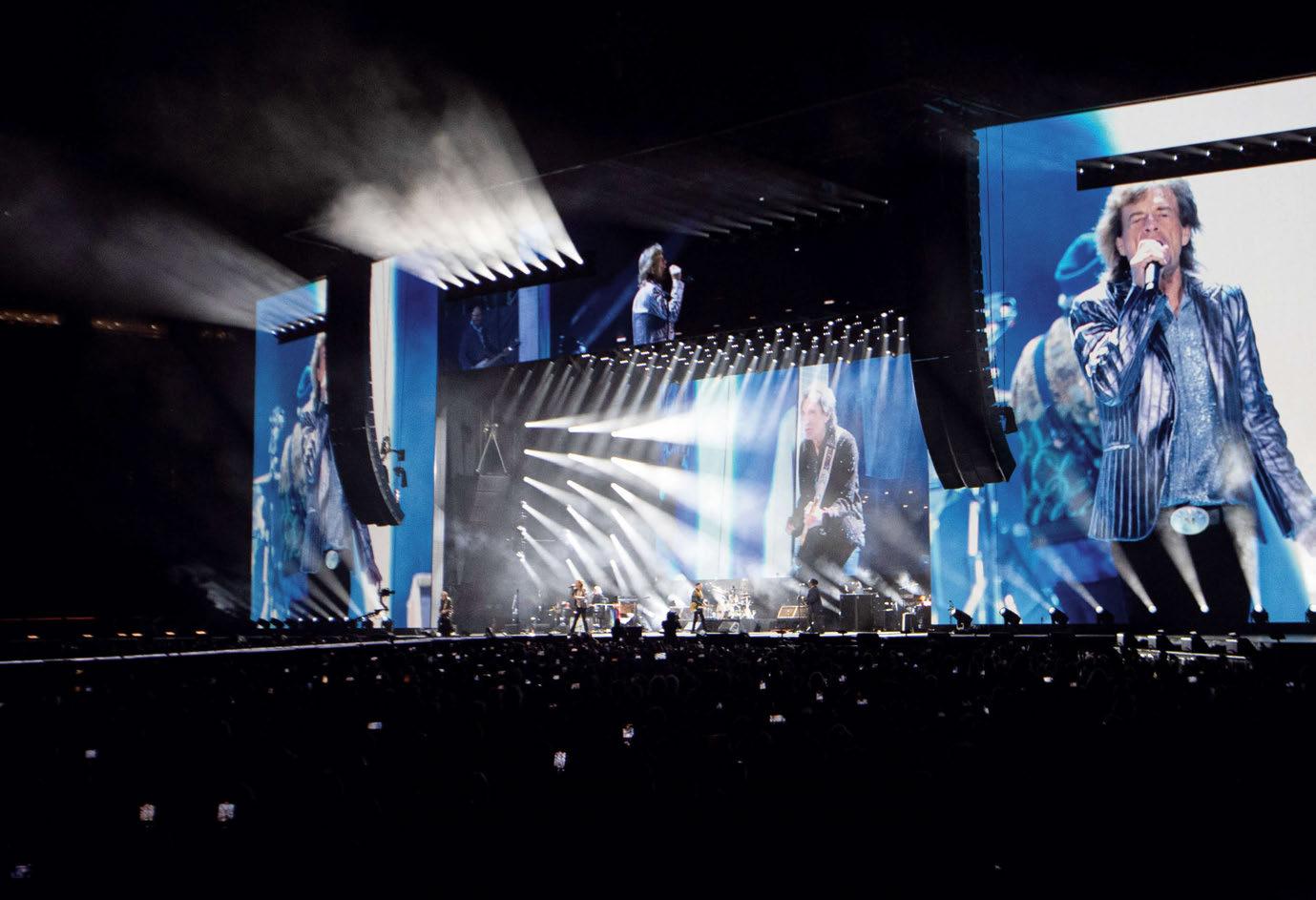
Entertainment Architects
“The Rolling Stones are always a band of the current time and not simply a nostalgia act. I’ve always seen them as a contemporary band,” stated Patrick Woodroffe, Creative Director for The Rolling Stones, as he spoke to TPi over the phone recounting his thoughts on the band’s latest touring production, Hackney Diamonds. Having worked with the group since 1982 on the Still Life tour, Woodroffe has been one of the key creatives responsible for establishing the high bar of production values over four decades alongside the late Mark Fisher. For this latest production, he joined forces once again with Ray Winkler and the team from STUFISH, alongside Lighting Designer, Terry Cook, content creators TREATMENT Studio and Screen Director, Roland Greil.
With all parties having multiple years of experience working with the band, they were all keen to bring something new and exciting for
the legions of fans. The result saw the creatives delve into the digital world with a stage set that built out a STAGECO roof and stage with a large LED configured to create real depth and perspective, allowing all involved to lean into architectural motifs and take the band to new realms throughout the two-hour set.
With a mentality of keeping this production “contemporary”, Woodroffe explained how he approached this show in the same way he would for any act promoting a new album.
“T hey have just released a new record [Hackney Diamonds], so it was only natural to want to give a modern stage set and to use whatever modern technology is around,” he said. “The difference is the band these days can only really commit to 19 show per run compared to the 60 of the past.”
This gave the creative team the challenge of ensuring the tour was financially viable for the number of shows while also living up to the high
bar the band has set over the years. “We went for a standard STAGECO roof meaning that the team at STUFISH had to deal with very specific geometry. We also opted against spending money on expensive scenery, instead using the LED as our stage set. This might not be an original idea but the way we created the show had a very architectural feel,” stated Woodroffe.
When it came to the suppliers of the US run, alongside the aforementioned STAGECO, the team brought on Nighthawk Video and Upstaging for lighting as well as the tour’s trucking needs. Also onboard was Wonderworks aiding as structural consultant.
“A lthough the festival roof provided some limitations, we approached this as an opportunity to try something challenging and create something new,” mused Ray Winkler of STUFISH. “Our approach was that this was an opportunity to bring in a high level of digital content in a way that hadn’t been done with the
Photos and Sketch: STUFISH
NO WORDS NEEDED
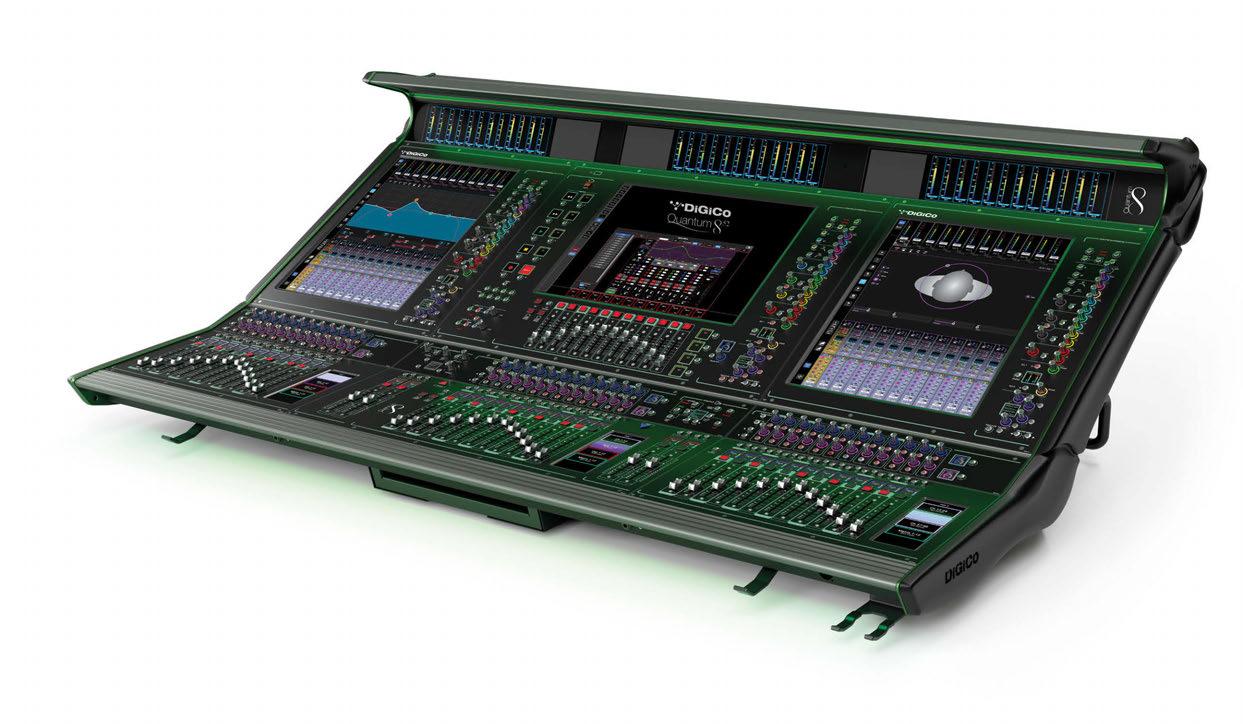
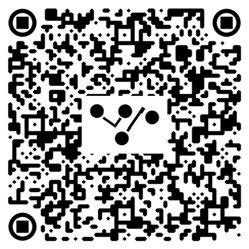
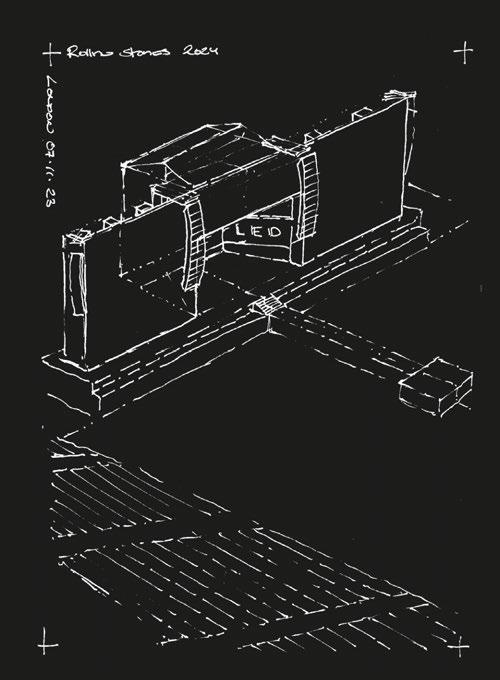
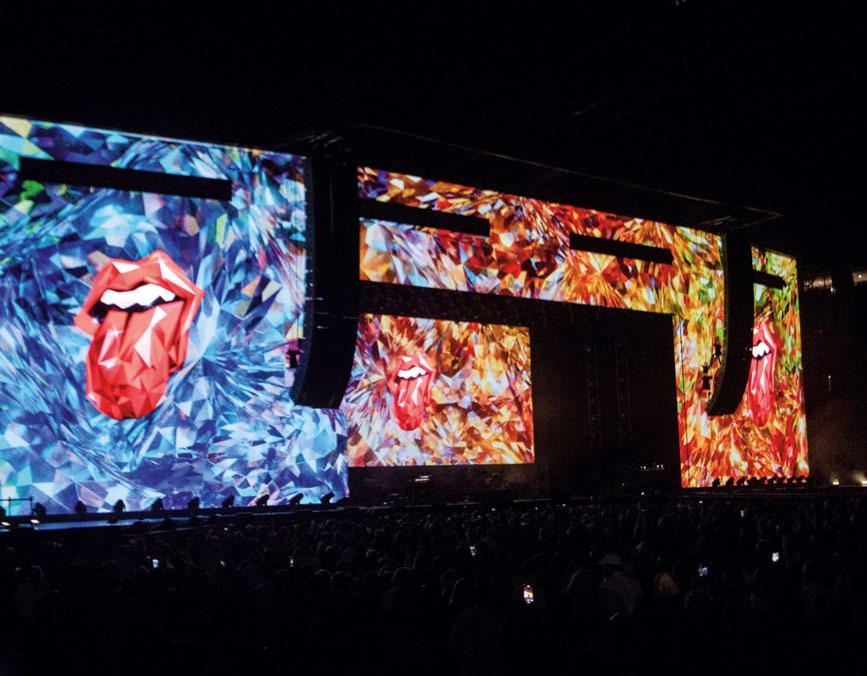
Stones. The huge amount of LED meant that we had the opportunity to make the staging structure behind disappear.”
In t he creation of the show, Winkler was quick to compliment Wonder Works. “Jeremy Lloyd from Wonder Works used to work at STUFISH so we have a good shorthand when we collaborate,” he revealed.
“T here is a real skill in maintaining the original design intent but still making it work with all the containing factors such as the number of trucks and people needed, and Wonder Works pull it off so well.”
Wonder Works Director, Jeremy Lloyd joined the conversation: “There was a lot of heavy equipment downstage, which meant that the rigging loads were concentrated on the downstage edge of the roof. The video header arequired additional structure for wind bracing. Working with the creative team we made some minor adjustments to transfer some of the loads. We then worked closely with STAGECO; Head Rigger, Antoin Patten and Nighthawk’s Ben Rader and came up with some creative rigging solutions and added some additional structure to wind brace the video header.”
Lloyd recounted an enjoyable experience working with The Rolling Stones creative team again. “We have been working together for more than 20 years, so we understand each other’s processes and there’s mutual trust between all of us.”
Winkler was also keen to extended praise to the team at TREATMENT Studio who had a great deal of pressure on their shoulders due to the dominant role of content in this production. Speaking to TPi about their involvement was Noah Campeau and Sam Brickman from TREATMENT Studio. “From conversations
with Patrick, it was clear that for this show they wanted more of a narrative arc to the show to give the audience a bit more structure to what they were hearing,” began Campeau. “This was my third time working on a Stones show. It is really great how they always want to add a modern twist to their show to have a contemporary feel.”
He continued: “We had an opportunity to use the architecture of the screen to frame the band in unique ways with the content. We sometimes used the content as dynamic animation and sometimes even just wallpaper.”
Br ickman added that the TREATMENT team also collaborated with several different creatives on the project, from illustrators to 3D artists. One of the duo’s highlights was during the track Sympathy for the Devil where they turned the screen into a palace. “That look came from an original sketch and idea and putting it into Photoshop, but it resulted in us illustrating the entire look and using stop motion to create the look of the whole song,” stated Campeau.
The content was shown via a large quantity of SACO 8mm screens supplied by Nighthawk Video, the tour’s longstanding video vendor. The supplier also provided the three Disguise GX 2c media servers to drive the content along with a full camera package.
“It’s always exciting when this band goes out on tour,” stated Nighthawk Video Tour Director, Ben Rader who also took on the role of Video Crew Chief. “The biggest reward for us is being involved in the early stages with the incredible design and production teams to then going out on the tour and executing the vision. This design screams video and is all about showcasing the rock legends they are.”
Once again taking on the role of Screens Director was Roland Greil. “I’m responsible for composing all of the beautifully commissioned content together with the live IMAG feeds from our Camera Director, Mike Duque,” stated Greil. “This means programming the media servers, set up as well as running the show live each night.” Greil ran the show with Sockpuppet control via the MA Lighting grandMA2 console.
The camera setup was a mixture of manned long lenses and handheld cameras, a jib as well as automated POV and robo cameras. “Keeping a balance between the two ingredients (IMAG and content) is the key to success – especially with this specific show,” stated Greil. “The goal is to create a visual narrative that works together with the lighting and also gives the audience enough moments to see what they really there for – The Rolling Stones.”
Despite being a key member of the Stones camp for some time, this tour marked the first production where Terry Cook took on the Lighting Designer role, having been an Associate Lighting Designer under Patrick Woodroffe for the past decade.
“W hen we had the framework of the video, both Partick and I began to work out how best we could enhance the show with lighting,” he explained. One of the key design discussions was the uniform lighting grid made up several Elation Proteus Maximus. “It’s a multifaceted LED fixture that we selected to cut through the LED. Having all the fixtures be the same meant we were able to create a unified look.”
This need to cut through the video also led to the decision to go for the ACME SUPER DOTLINE that were arranged on stage left and right. “We ended up using the battens for several ‘eye-candy’ looks, which we have never
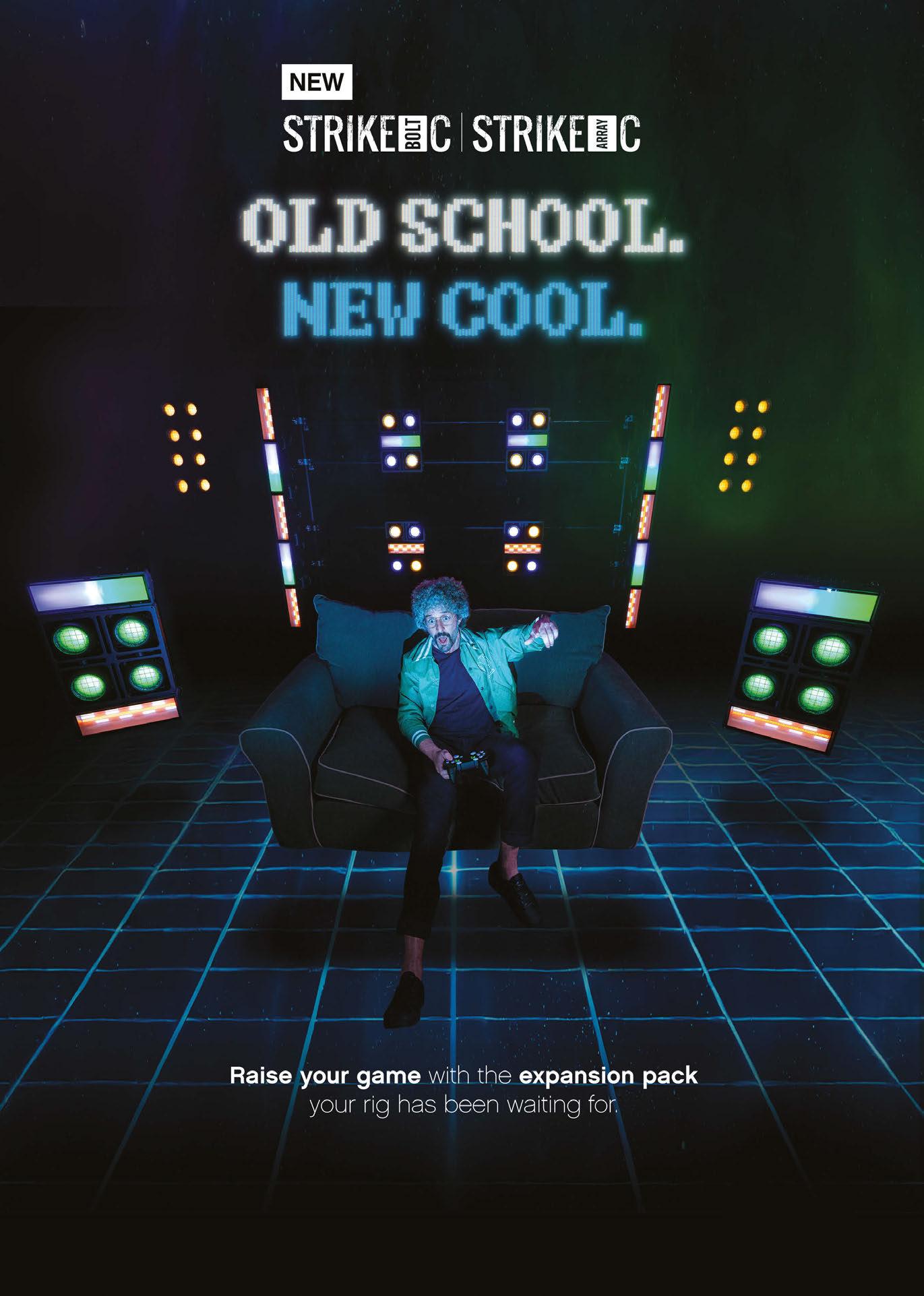
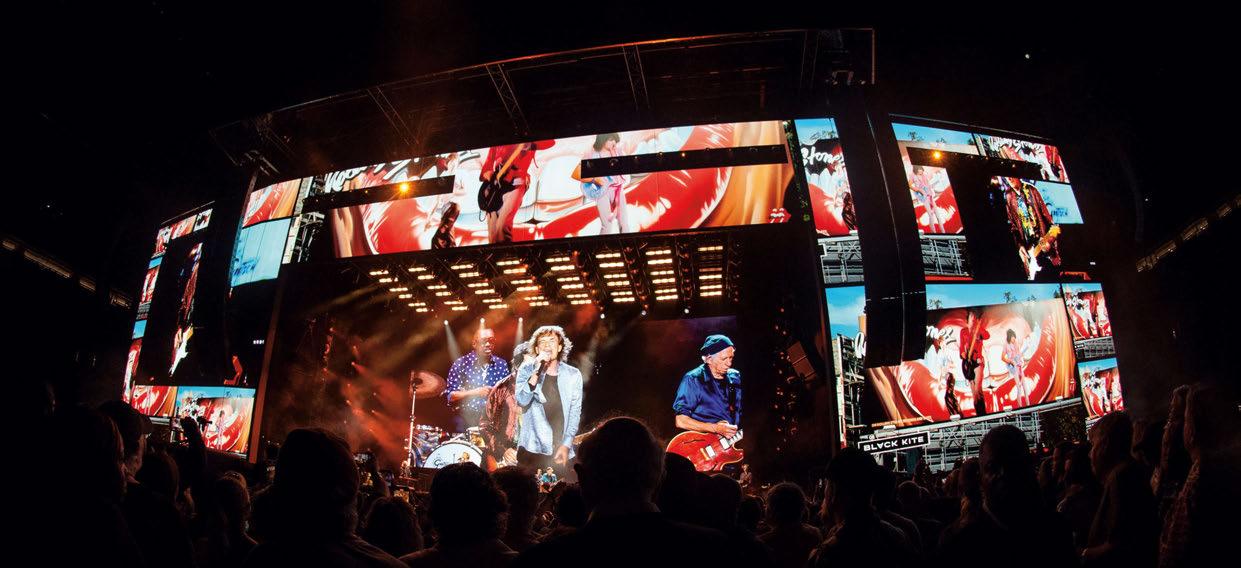
really done with the Stones before as it’s more of a ‘pop’ look. But it gave us a fun element to play with.” The battens were also used to extend looks within the screen content with Cook giving special mention to a sunrise scene during Gimme Shelter
Also on the rig were CHAUVET COLORado PXL Bar 16 that lined the thrust. For follow spots, the production selected Robe iForte LTX, with control coming via Follow-Me. While this was the second tour that Follow-Me was selected for, this time the lighting team utilised more of the software’s features to aid in the overall design.
“Using Follow-Me’s Proximity feature, we were able to program the CHAUVET bars on the thrust so when one of the band walks down the runway, the lights come on and follow them down, creating a great look for those higher in the stadium bowl.”
The Proximity feature was also utilised so that when Mick Jagger was close to the stage edge, the spots behind him would automatically dim for the sake of the cameras so the singer would not be silhouetted. “No audience member would even notice these
subtle elements, but it makes the show much cleaner and crisper which is really exciting for us,” enthused Cook.
Having these elements that could react to what the band was doing on stage fed into The Rolling Stones’ general rule where the visual show is reactive to the music. “It is always 100% live with no timecode,” asserted Cook.
“I always say we have Ethan-Code,” he chuckled referring to the band’s longstanding Lighting Director, Ethan Weber. “It’s beautiful to watch him keep time with all the tracks. Sometimes you can physically see the cue arrive from his knees to then travel through his body and to his shoulder.”
The show was controlled via an MA Lighting grandMA2 although Cook joked how he thought the original show file was originally crafted on a High End Systems Hog 1 more than 25 years ago.
“T here are many, many years of programming on this show file and we have over 100 songs programmed on the file. It’s always an interesting process during the setup of a Stones show. We begin programming some of the songs they are less likely to play
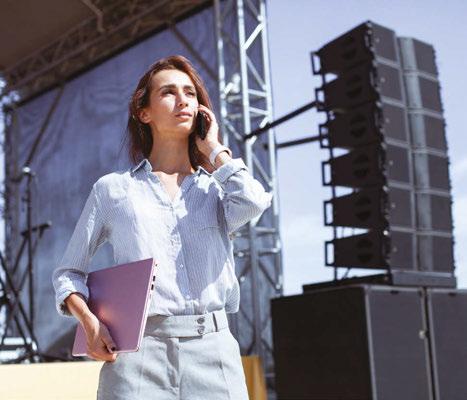
before moving onto the bigger hits such as Satisfaction and Sympathy for the Devil. This time round, several of the newer songs also needed to be programmed. The real magic is when we move into the stadium with the band. Being in an empty stadium with just us and the band is a truly surreal experience.”
This need to have so many songs in the chamber comes down to The Rolling Stones’ tendency to only decide on their set list a few hours before doors. “It’s Ethan and I’s job to be prepared for the show as much as we can be,” remarked Cook.
From speaking to numerous parts of the creative team, it was clear that all were satisfied with the result of this latest production and that they could all be part of another chapter of The Stones’ illustrious live career. www.rollingstones.com www.woodroffebassett.com www.stufish.com www.treatmentstudio.com www.upstaging.com www.nighthawk-video.com www.stageco.com www.wonder.co.uk
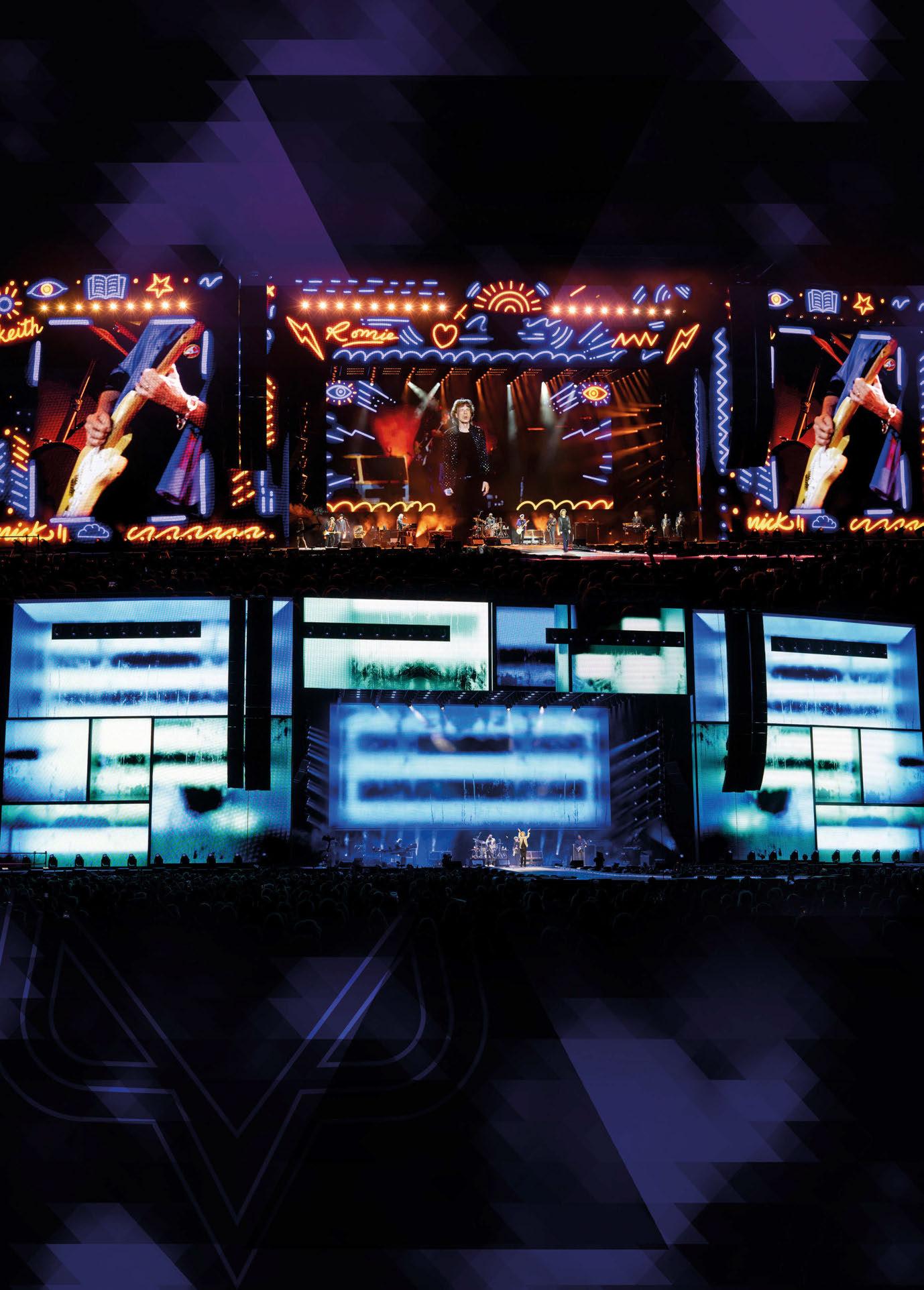
BAD BUNNY: MOST WANTED
Lifting the lid on some of the subtle themes explored in the dynamic stage design of the reggaeton star’s latest tour.

Words: Stew Hume
Photos: WICREATIONS
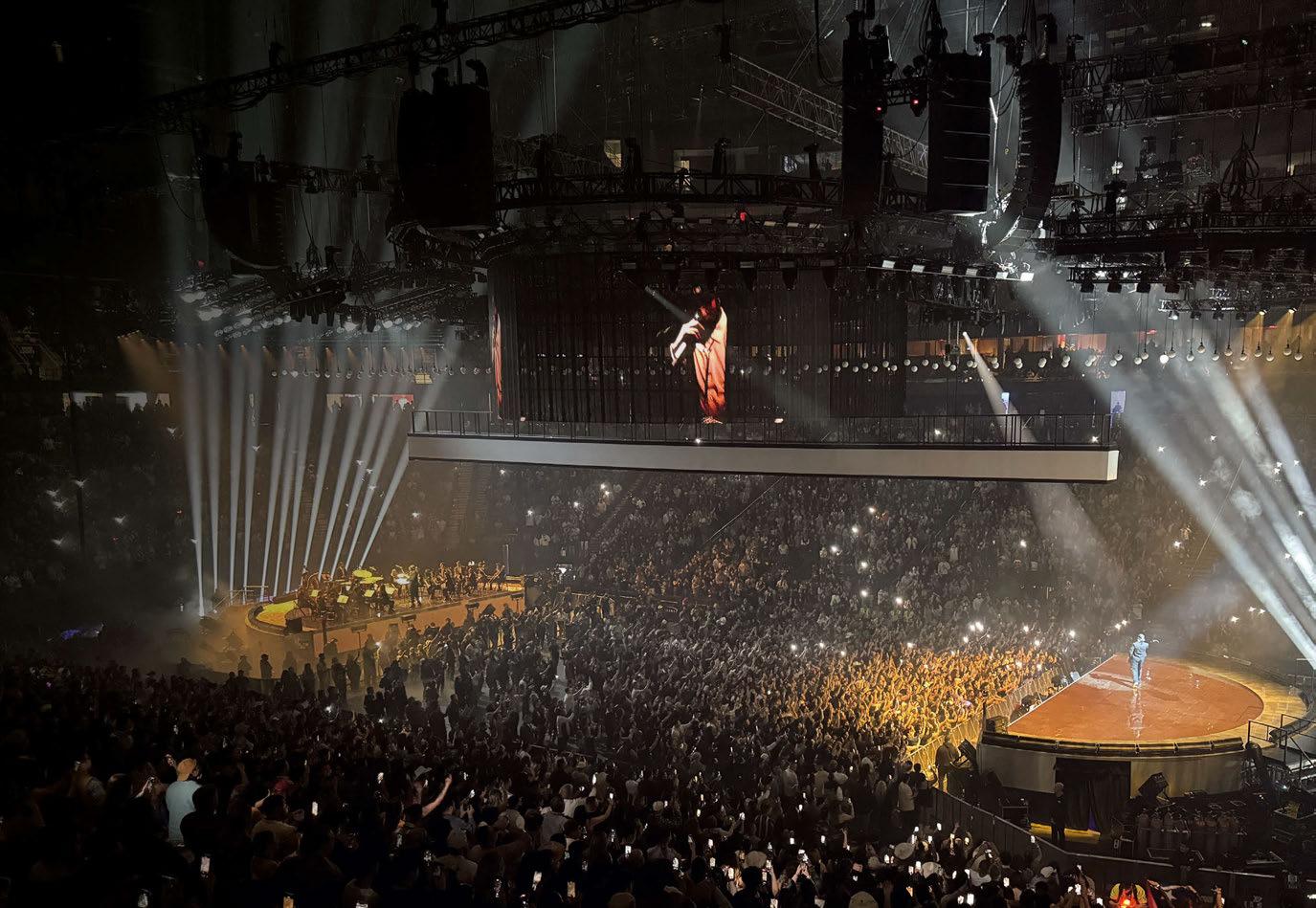
There has been a trend in recent years of Spanish-speaking artists playing to bigger and bigger audiences in the US. In fact, one such example was documented in TPi #278 – the stadium debut of Karol G in the United States. Another artist at the sharp end of this trend is Bad Bunny, whose collaboration with Drake and Cardi B saw him achieve a level of international notoriety that was previously considered unattainable for Spanishspeaking artists.
For his latest production, Most Wanted, the Puerto Rican had a clear vision to ‘bridge two worlds’, which manifested in a two-end stage show with an automated bridge connecting the two performance areas. Bringing in legendary show designer Es Devin to help realise this vision, it was an ambitious stage production with many highlights including the artist taking to the stage on a real horse.
Talking through the nuts and bolts of the two stages was WICREATIONS’ Raf Peeters. “We’d worked on his previous tour in 2021,” began Peeters, expressing his admiration for the artist and his work ethic. “During that first project I’ll admit I was not familiar with his work, but
it’s astounding how big he has become in the United States. He’s an authentic artist.”
Peeters spoke of one specific part of the design process where he and the wider creative team were determining how they could get the singer from the elevated bridge down to the second stage where a piano was stationed.
“It was about a 1.5m drop and while we threw out ideas of ladders and stairs, he decided instead to just jump down!”
In terms of the overall build, it was a tour of two halves with WICREATIONS handling all the floor packages and TAIT producing the automated bridge and flying element. “The split between the two companies really came down to a short timeframe to pull all the pieces together,” stated Peeters.
He continued to highlight the scale of this show, which filled 31 vehicles in the US. “Despite the size, the load-out took three hours on average,” he shared, praising the work of the touring production.
“Credit must go to Roly Garbalosa, Head of Production for the tour, who during rehearsals always programmed enough time to run through the load-in and -outs to ensure
everything was prepped for a quick load in –especially as this run’s schedule was busy.”
Looking after the WICREATIONS elements of the show was: Crew Chief, Greg Vervoort; Operator, Kim Bennett-Abbiss; Technician, Senne Diels; Carpenters, Lance Weaver, Kyle ‘Gweedo’ Smith and Jake Van Egmond.
WICREATIONS constructed two motioncontrolled semicircular stages positioned right in front of each other. The main stage – or King Stage – was set in motion by four WICREATIONS TP06 spiral lifts with a libera grid in between and a video floor above. The semicircle stage had a custom-brushed aluminium fascia. The stage is supported by 16 triple casters to allow to move it in proper alignment with the flown bridge by TAIT.
On t he downstage side of the arena, the Queen stage had a 4m by 2m moveable platform supported by a rectangular lift and four TP21 hoists powered by EVO PM030 drives. The deck system, a combination of standard and custom decks, was specially designed to create a semicircle with video floor on top. Just like the King Stage, it was also finished with custom-brushed aluminium.
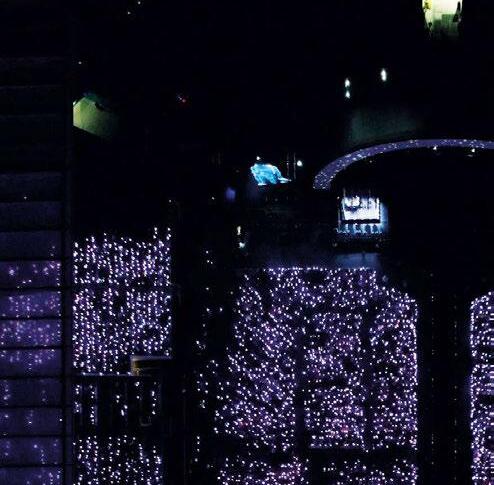
Fan euphoria MAY CAUSE

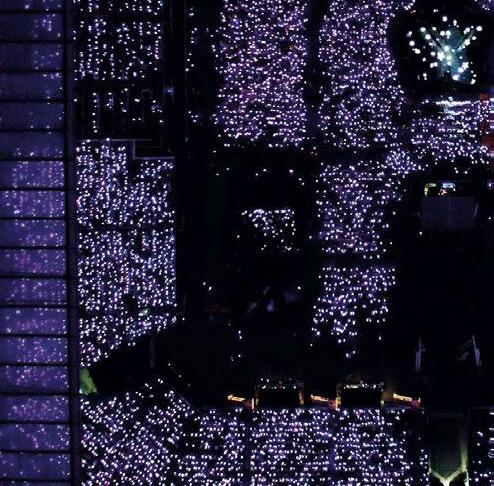



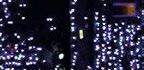






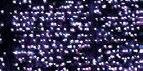
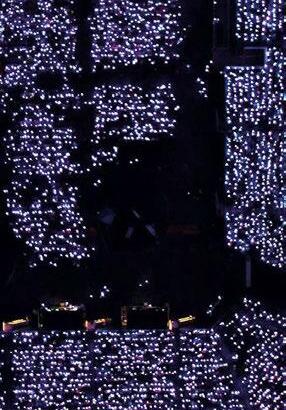
WE IMMERSE FANS IN THE LIVE EXPERIENCE WITH WEARABLE AND SEMI PERMANENT LIGHTING TECHNOLOGY. OUR PRODUCTS TURN UNLIT CROWDS INTO ACTIVE PARTICIPANTS OF THE SHOW, IGNITING COLLECTIVE JOY AND DEEPENING FANDOM.

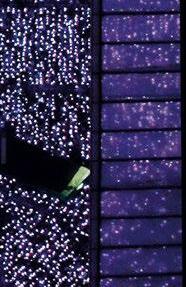
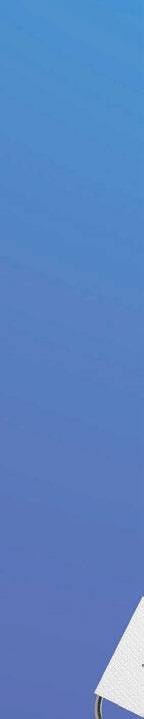


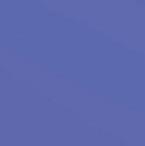

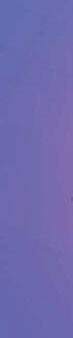

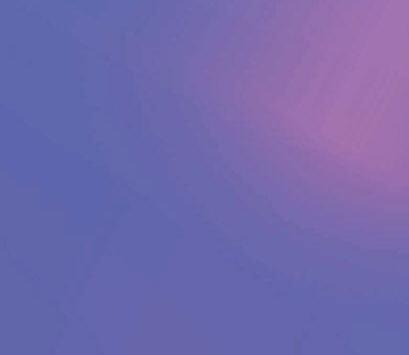




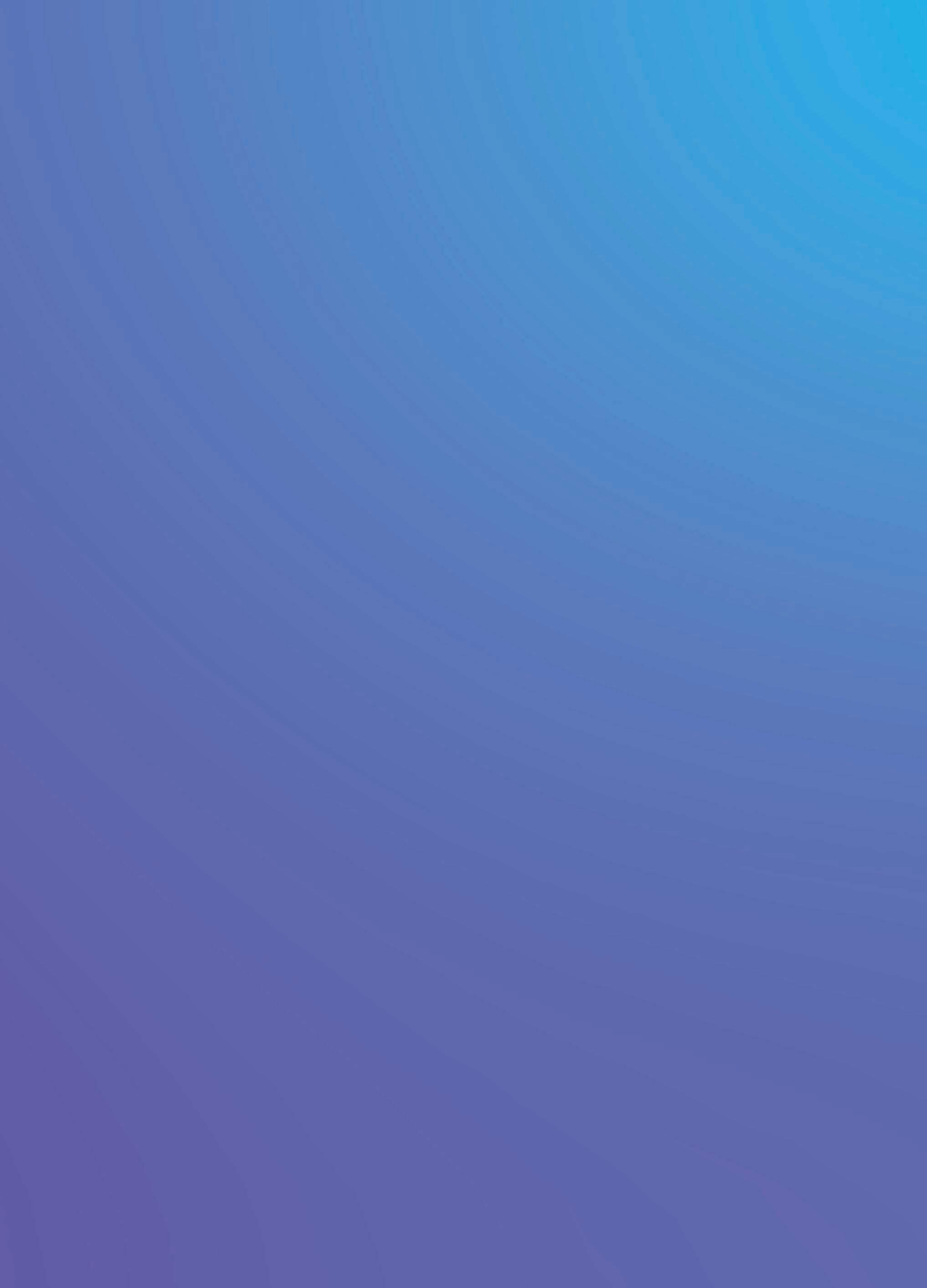
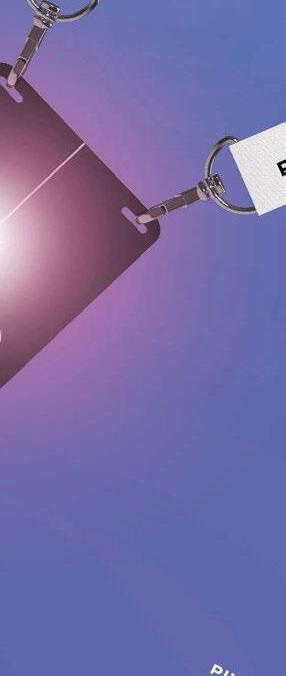
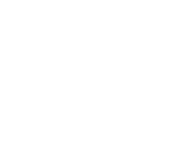



“During rehearsals, we made some big changes to the stage design due to the artist not being close enough to the audience,” Peeters commented, demonstrating not only how hands-on Bad Bunny is with his show design, but also how keen he was to have a close interaction with the audience.
Also aiding in this greater connection with the audience was PixMob, bringing its signature wireless LED technology – in this case in the form of a badge in the shape of a cowboy boot – to light up the audience.
“We’ve been working with Bad Bunny for six years,” stated PixMob’s Hila Aviran. “We brought our infrared moving head technology to arenas and used them to wirelessly program zones. With the LED badges the fans wore, jaw-dropping blasts of light swept through the audience.” Aviran further explained that the badges really “extended the stage lighting” into the crowd. “We’re thankful for Bad Bunny and his team,” he said. “They’re innovative and forward thinking and approaching things from a perspective that is 100 steps ahead.”
Peeters shared his final t houghts on t he collaboration: “He’s now one of the biggest artists worldwide and he continues to bring in new elements and genres with every new
album. As far as the show, the production is very deliberate when they use certain elements or gags. They never want to milk a look, making each moment very special for the crowd.”
www.wicreations.com www.pixmob.com
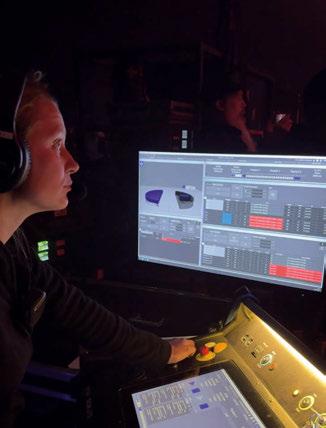
WICREATIONS Operator, Kim Bennett-Abbiss

CURATING MOGA CAPARICA
Discover what it takes to host a multifaceted festival on a public beach…

Words: Jacob Waite
Photos: Ines Machado and Angel Bambu
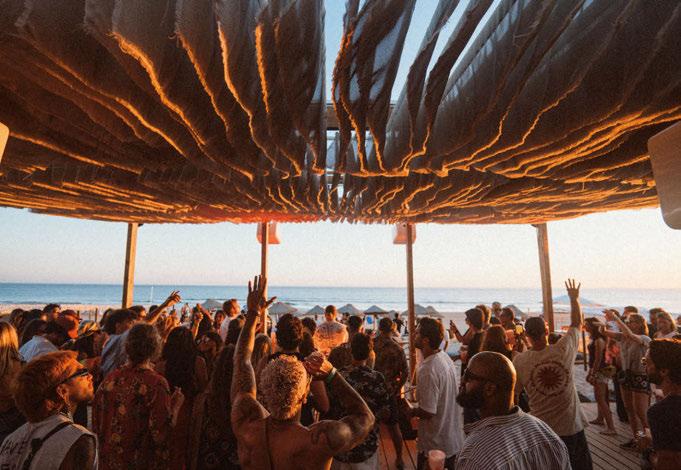
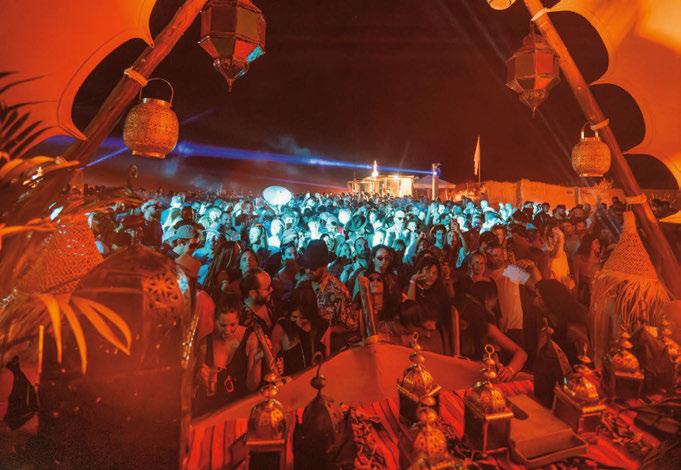
Taking place on the Costa da Caparica coast of Portugal from 29 May to 2 June, MOGA Caparica has become a mainstay in the Portuguese boutique festival calendar. This year, MOGA transitioned from a series of beach parties to a full-fledged beach festival with a single expansive site and three stages, while remaining a compact gathering for music and art lovers inspired by Atlantic vibes and aimed at connecting people from all over the world. As the sand settled on this year’s event, TPi sat down with founder, Matthieu Corosine and Executive Producer, Laura Seabra of Música no Coração to find out what it takes to host a multifaceted festival on a public beach.
“Taking the leap from a series of beach parties to a full boutique beach festival was a big step, but incredibly exciting. It was challenging to grow while keeping the intimate vibe our MOGA tribe loves,” Corosine said.
“At Praia da Morena, we now have two beach clubs forming one fantastic venue, offering more comfort. With three stages, chill-out areas, food trucks, and an on-site after-party club, we provide a complete, immersive experience in one of the most beautiful natural settings we’ve ever seen.”
Suppliers came in the shape of Portuguese outfits Matias for AV, Nuno Srl for stage design, Nuno Cruz for site operations (fencing and barriers) and US-based Natural Events for compostable toilets. “Portugal is a tiny market, so we knew or had worked with the suppliers in the past. We wanted to keep the pre-existing suppliers. It makes sense to maintain the structure; they have experience of this unique festival site and the challenges associated with it. The entire team has united to deliver a unique experience for festival goers,” Seabra said.
“It’s essential to work with local companies and champion the artistic and live events
sector in Portugal. We work with an international suppliers when it comes to the toilets because there isn’t a national supplier able to facilitate the number of compostable toilets required.”
Despite the growth of the festival, multiple stages helped distribute attendees evenly, preventing any feeling of overcrowding.
Corosine elaborated: “The safe access to the sea and the stunning surroundings creates a sense of intimacy and connection. We have designed cozy, engaging spaces where people can relax, enjoy the music, and connect with each other. This thoughtful setup ensures that even as we grow as a festival, we maintain the unique, close-knit atmosphere that makes MOGA special.”
Seabra added: “Although the suppliers and the bulk of the crew remain the same as prior iterations of the event, the festival offering has expanded with more stages, with more demand
Fantastic colours thanks to RGBL and iQ.Gamut technology


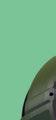
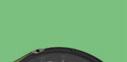


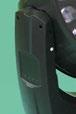

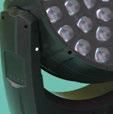



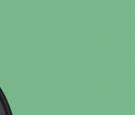
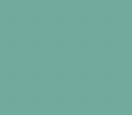
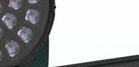





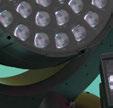
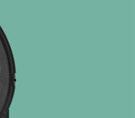

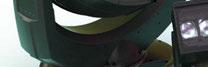


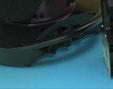





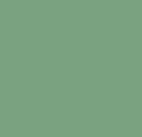
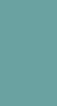
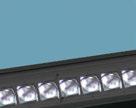
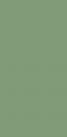
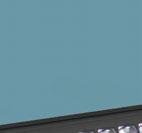
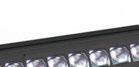


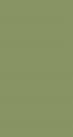






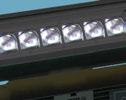
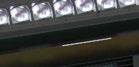
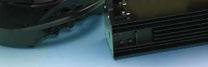



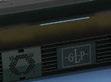
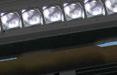



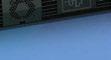
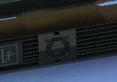

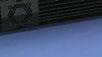




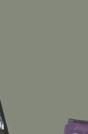

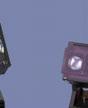


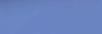
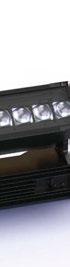
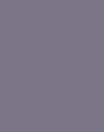

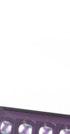
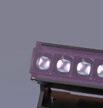
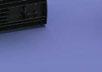
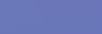
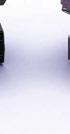
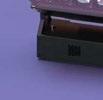




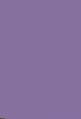

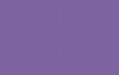
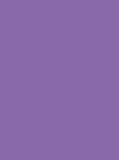


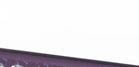
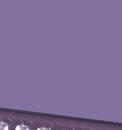
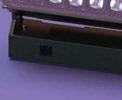
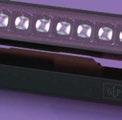
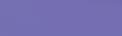
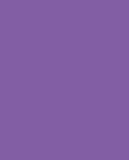



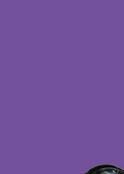

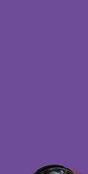

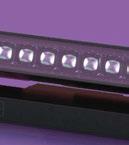







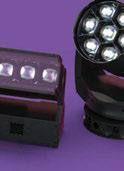
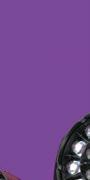
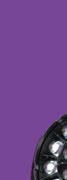
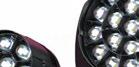
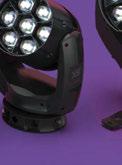
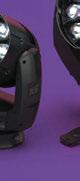
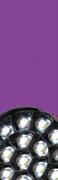
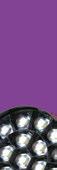

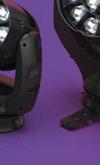

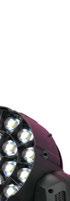
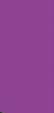
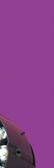
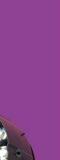



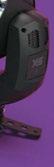
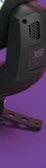

on crew, everything has been suitably upscaled, while maintaining the ethos of the festival. Seeing people happy is always my goal, from the moment the music starts until it ends.”
Music formed part of an exciting schedule of events at this year’s MOGA. Acid Arab (DJ set), Adassiya (live), Agoria, Francis Mercier, Mâhoud (live), Lee Burridge, Romain FX (live), Rui Vargas, To Ricciardi, Zengxrl and many more joined the likes of Acid Pauli, Dixon, Dekmantel Soundsystem, Jan Blomqvist (live) and Pachanga Boys on the stacked line-up.
In addition to the live electronic music and parties, the festival also aims to pay homage to the vibrant surf town of Costa Da Caparica, the festival’s OFF format featured free events at beach clubs, a boat party, a family friendly MOGA kids’ programme in the park, conferences and masterclasses, dinners with local fishermen, yoga sessions on the beach, street art performances, and more.
“In our effort to support local businesses, we’ve introduced a special hotspots programme, allowing festival attendees to explore and enjoy discounts or receive thoughtful gifts at various shops, restaurants, and bars,” Corosine explained. “The festival culminates in a spectacular beach event called IN at Praia da Morena, where attendees can revel in three days
of music and relaxation against the backdrop of a stunning sunset.”
According to Seabra, “nightmare” doesn’t begin to describe the headaches associated with hosting a festival on a public beach.
“T he sand, man… The sand!” she laughed. “Everything is an extra challenge. We do most of the load -in and -out either very early in the morning or overnight, focussing on small assembly points at a time. In Portugal, the entire coast is rightfully considered a public space; we want to keep it that way, so we don’t take up too much space and make sure that beachgoers aren’t impacted. With the right team and number of hands, anything is possible.”
Reflecting on the success of the fourth iteration of the festival, Corosine proudly reported: “After all these years of organising parties, the excitement of seeing people gathering around music is still intact. This entire experience attracts people from around the globe – representing 28 nationalities – who seek to nourish their ears, souls and bodies in the spectacular set up of Costa Da Caparica, all while making a positive impact on the local community. We’re looking forward to hosting MOGA Essaouira in October.”
mogafestival.com essaouira.mogafestival.com

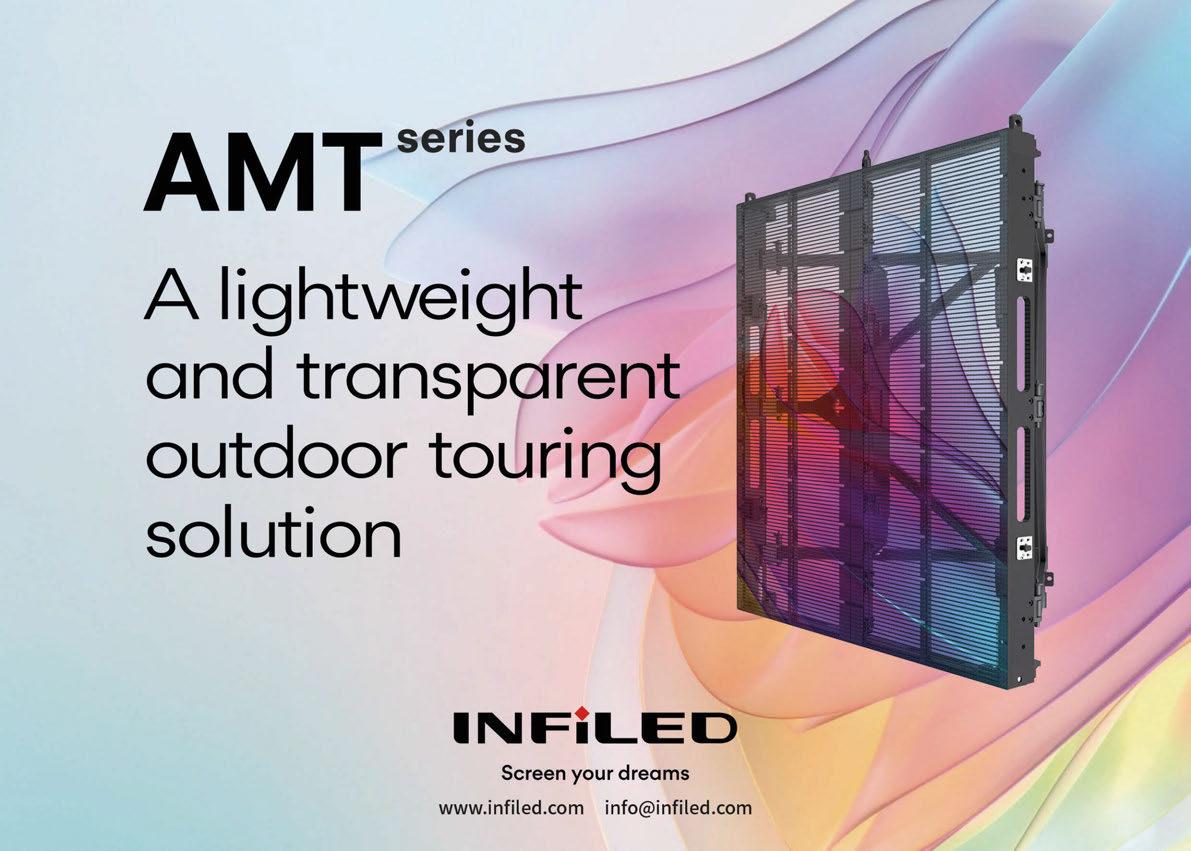

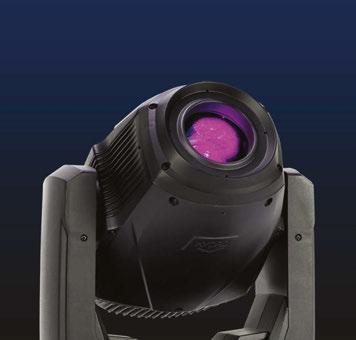

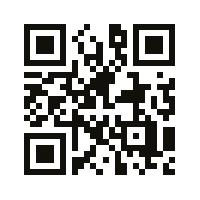
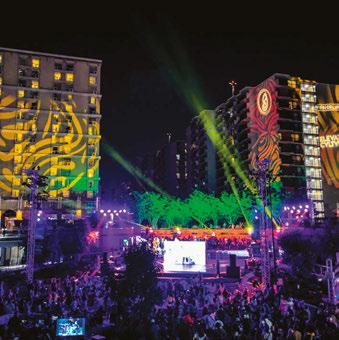
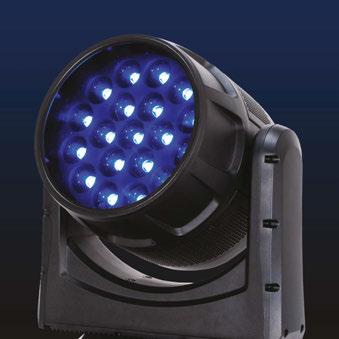
SCAN QR CODE TO DISCOVER THE HYDRO SERIES IP65-RATED MOVING HEADS
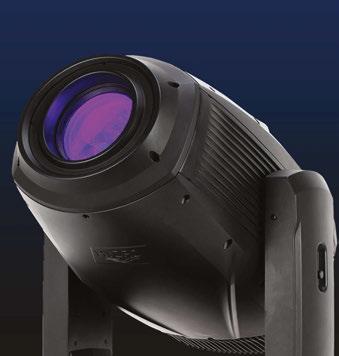
HYDRO PROFILE
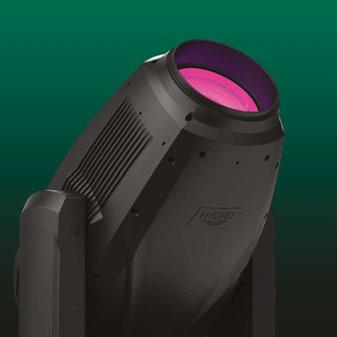

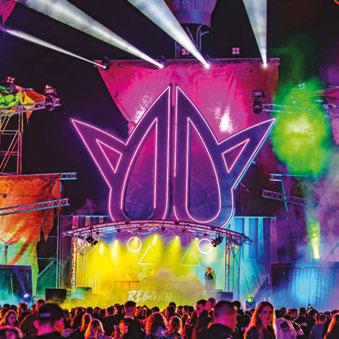
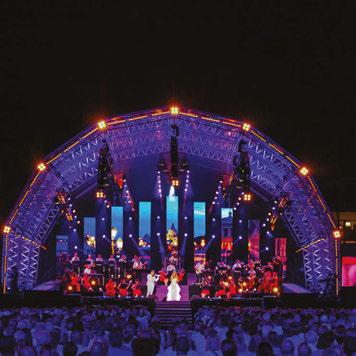
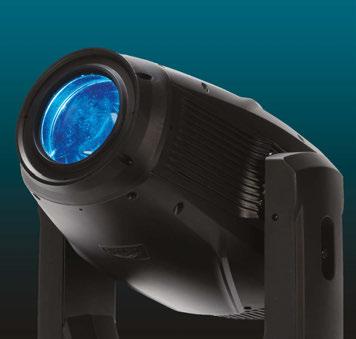
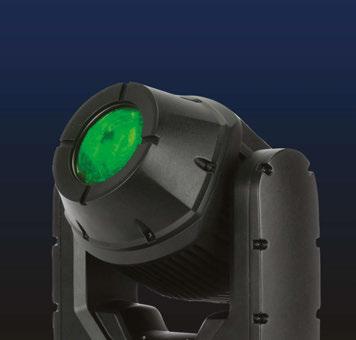
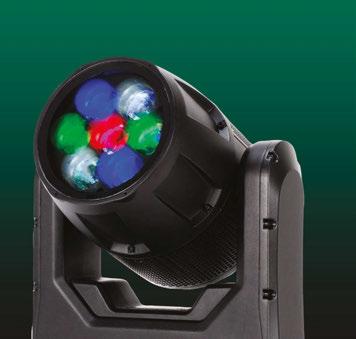

HYDRO HYBRID
HYDRO SPOT 2
HYDRO BEAM X12
HYDRO BEAM X1
HYDRO SPOT 1
HYDRO WASH X7
HYDRO
EUROVISION SONG CONTEST 2024
The creative and technical team powering the 68th Eurovision Song Contest tap into the capabilities of an all-LED rig to reach sustainability goals and ‘respectfully challenge the concept’ of the world’s most-watched music competition.
Photos: Ralph Larmann, Green Wall Designs and
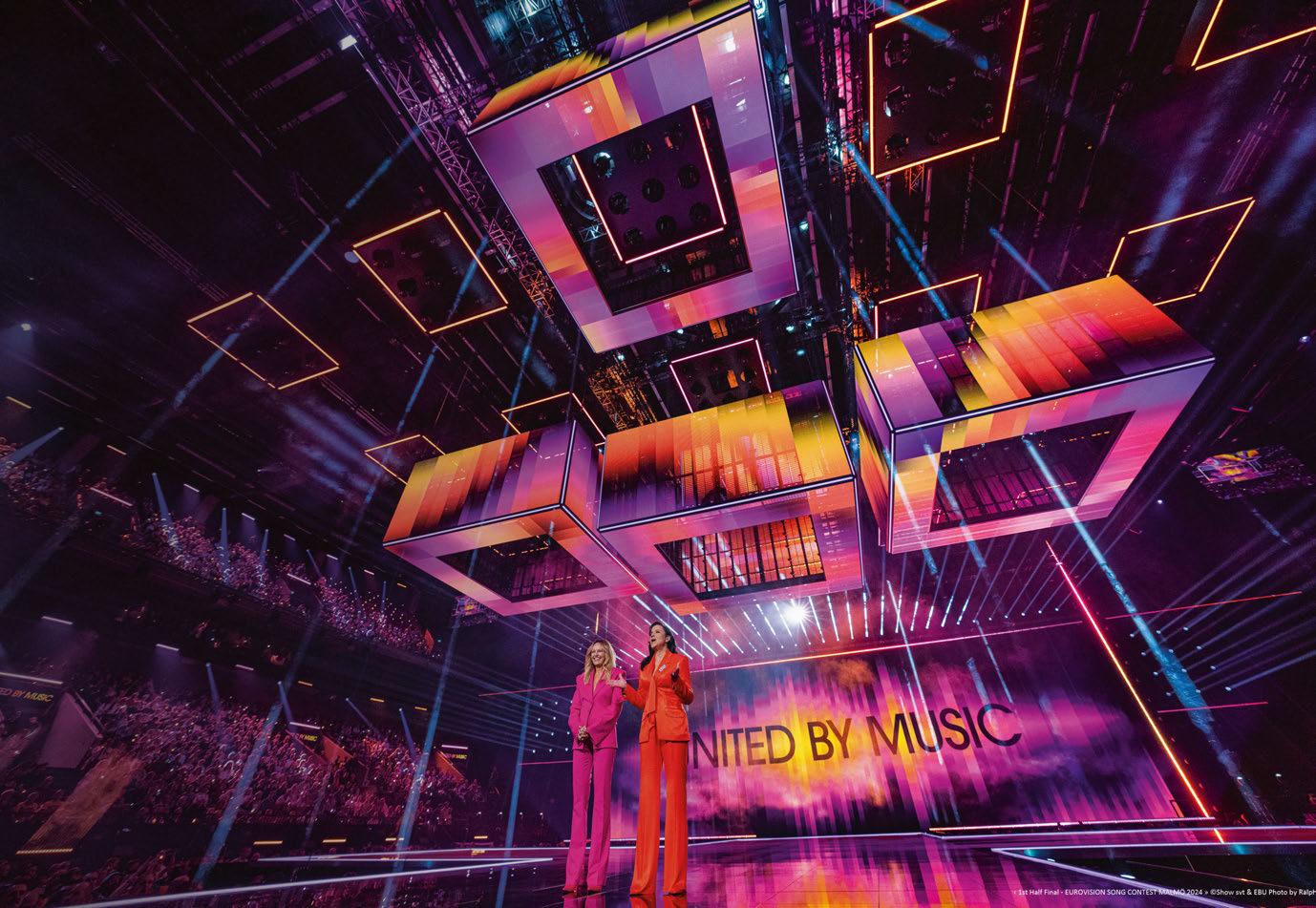
The 68th Eurovision Song Contest (ESC) was organised by the European Broadcasting Union (EBU) and host broadcaster, Sveriges Television (SVT), and was held in Sweden for the seventh time. Facing numerous challenges, the ESC’s official slogan, #UnitedByMusic, resonated not only with the artists and audiences but also with everyone involved. Producing a live broadcast of this scale – reportedly the largest live broadcast in the world – demands immense teamwork and cooperation over a long period, even before the artists take the stage.
Behind the scenes is no exception and under the experienced hand of Senior Technical Director, Ola Melzig; Production Designer, Florian Wieder; Lighting and Screen Content Designer, Fredrik Stormby of Green Wall Designs and the wider production team pulled out all the stops to produce a show befitting the high expectations.
“As this was the third time Sweden had hosted the ESC in the past decade, we set ourselves the challenge of doing something new and introduce a more large-scale concert tour feel to the familiar ‘studio show’ concept,” explained Stormby.
“Fans have quite high expectations when it comes to Sweden, given the country’s track
record of success at the competition, so we had to deliver.”
The load-in at Malmö Arena started on 3 April and was preceded by four days of technical preparation at Creative Technology (CT)’s warehouse in Malmö, which was also used as a production hub for all the equipment procurement and provisioning.
Drawing inspiration from Swedish music, songwriting and architecture, and a request from the producers to put the audience in shot for every performance, Stormby and Wielder developed a stage without any traditional scenic elements or shapes, based on in-theround layout and using light and video to shape the stage. Overhead, a dynamic rig on almost 200 automation hoists carried over 200 tonnes of equipment.
“Most of the lighting design was to work with strong lines of fixtures – not many types but densely used to give very strong expressions,” explained Stormby. “We could then use many combinations of these individually strong lines of lights and the many automated rig positions to create a very interesting palette.”
The ‘in-the-round’ experience saw a staging design shaped like an equilateral cross with moveable LED cubes, LED floors, lighting, video and stage technology creating an array of
visual variations for the artists. The centrepiece of the design was a video and light installation suspended above the stage.
The lighting and stage design had to support the very quick changes between acts, which allowed about 45 seconds for the crews to reset. The show was executed using only LED and laser light sources whose lower constant power consumption fit the event’s sustainability goals.
Claypaky Tambora Linear 100 LEDs and Skylos searchlights featured on the rig, supplied by CT with the support of Denmarkbased Motion Rental. “Claypaky lights are extremely reliable, and the ratio is very important for me: size, weight, output and power consumption. That’s critical when you’re trying to be sustainable; every watt and gram counts on a 210-tonne rig,” Melzig highlighted.
Wieder’s staging design featured straight lines in all directions with linear fixtures selected to outline and highlight the shape of the set. Automation enhanced the flown rig.
“Everything in the ceiling could move; the stage could constantly create new shapes and looks – it was a never-ending toolbox of toys,” Melzig remarked. Niclas Arvidsson of Interlite, Claypaky’s distributor in Sweden, introduced the lighting team to the Tambora Linears.
ROE Visual
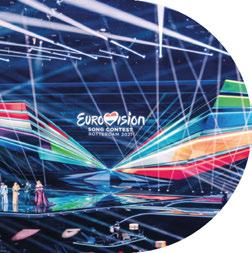
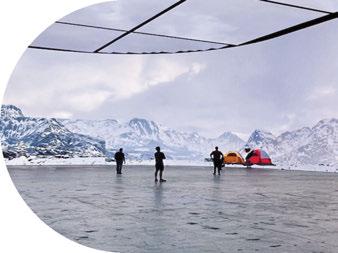
Technology
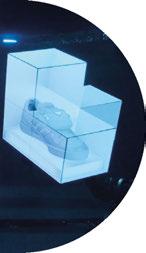
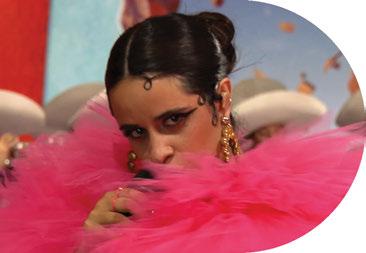


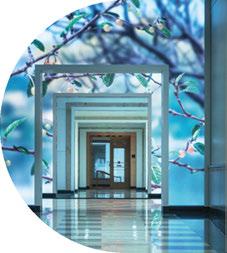
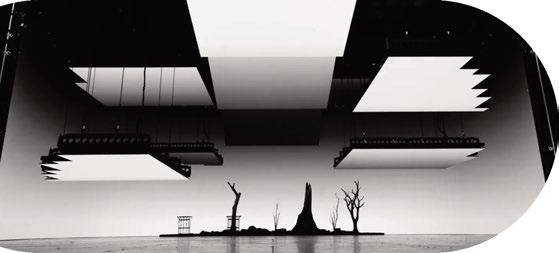
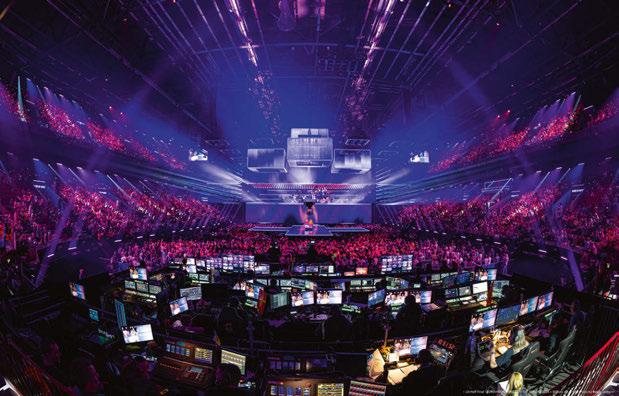


“He was great at helping us to source them since we needed 396 Tamboras mounted on the [overhead] LED cubes. They were perfect for this show!” Melzig enthused.
Stormby selected Tamboras for their look, features and size. “I needed a compact, lowweight, bright linear fixture in large numbers that could act as a graphic element outlining the flown pods, but also work as a strobe. In addition to this they were also fully mapped in the disguise server, allowing for video content to be played out over the lighting rig,” he explained. “The Tambora Linear, with the black ND lens, was a perfect combination for us, allowing them to blend in with the black cladding of our pods and set.”
On t he topic of Skylos searchlights, he said: “We ended up having them flown in an automated truss in front of the LED screen, that we could use in various heights, and flown along the sides of the stage over the bleachers. There were also five units positioned on the floor used for various specials. I’m most impressed with the pan and tilt speed. It’s superfast – like a Sharpy on steroids!”
Key to Stormby’s exclusively LED and laser-based design were 384 new Ayrton Rivale Profiles and 146 newly released Kyalami
fixtures, along with 32 Huracán Washes. “I like to approach my television designs using dedicated key light fixtures that have a certain quality of light to function well as key lights,” Stormby commented.
“I also like a single type of workhorse fixture throughout the rig that I can use for beam effects, mid-air effects, and to frame in on props or dancers, but can also support the key lighting to fill in as back or side lights.”
Around 20 automated ‘pods’ each carrying Rivale Profiles in a three-by-three configuration formed the main feature of the lighting design and allowed for a near-infinite number of aesthetic and practical positions. More Rivale Profiles were rigged in the audience trusses, above the stage and around the bleachers.
“I was looking for a workhorse LED fixture with shutters and good colours that was affordable in large numbers. I also wanted good light quality, a narrow zoom, gobos, shaper blades and all the traditional stuff,” said Stormby. “We needed to be careful of weight as there was so much hanging above the stage.”
Huracán Washes were rigged on front of house and audience trusses. “I wanted a wash instrument with shutters that I could use for audience lighting but be able to shutter off the
FOH at Eurovision Song Contest; Lighting and Screen Content Designer, Fredrik Stormby of Green Wall Designs and the ROE Visual team with CT Sweden back stage.

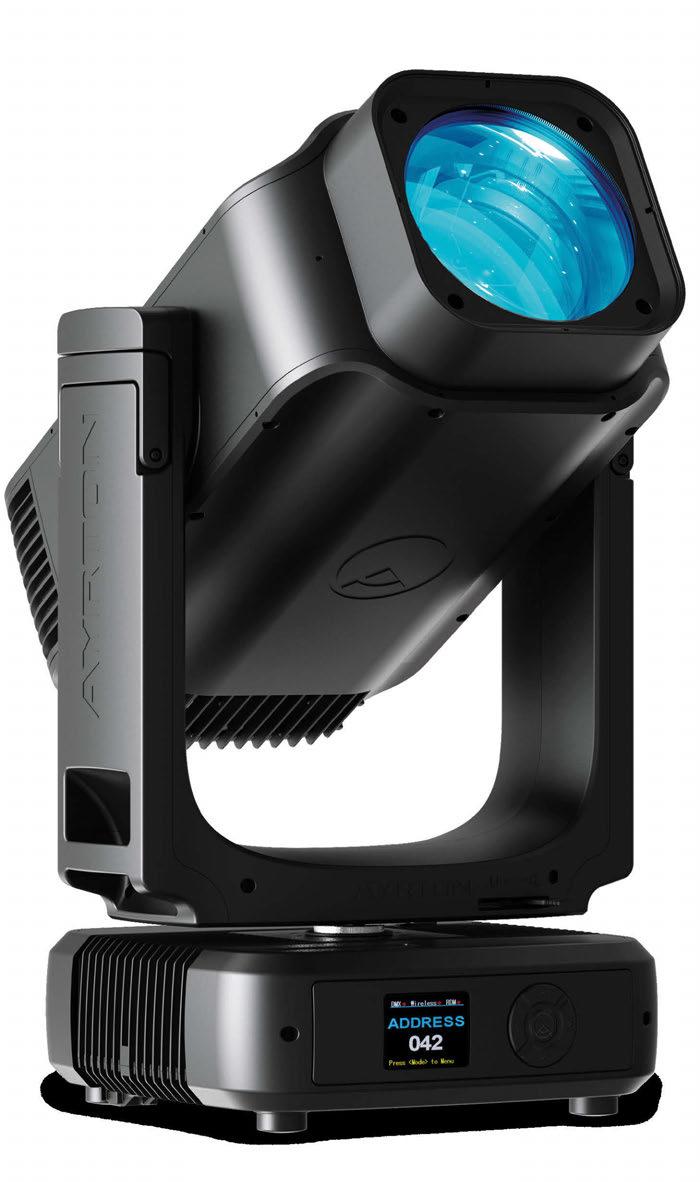
the ultimate revolution
RIVALE PROFILE is the first ultra-equipped luminaire in AYRTON’s brand new ‘ULTIMATE’ series, all models being perfectly homothetic and sharing common features, delivering previously unimaginable weight to output ratios.
Developed for mixed use indoors and outdoors, and in all conditions, RIVALE PROFILE, with its unique visual signature, is unparalleled on the market.
Weight determines performance, and RIVALE PROFILE weighs only 30.8 kilos.
To allow you more creativity and freedom in your lighting design, RIVALE PROFILE has been provided with continuous rotation of the pan and tilt movement.
RIVALE PROFILE, a unique projector that boasts performance, creativity, subtlety and power, is the most versatile fixture created by AYRTON to date.
A truly innovative luminaire with no equivalent on the market…
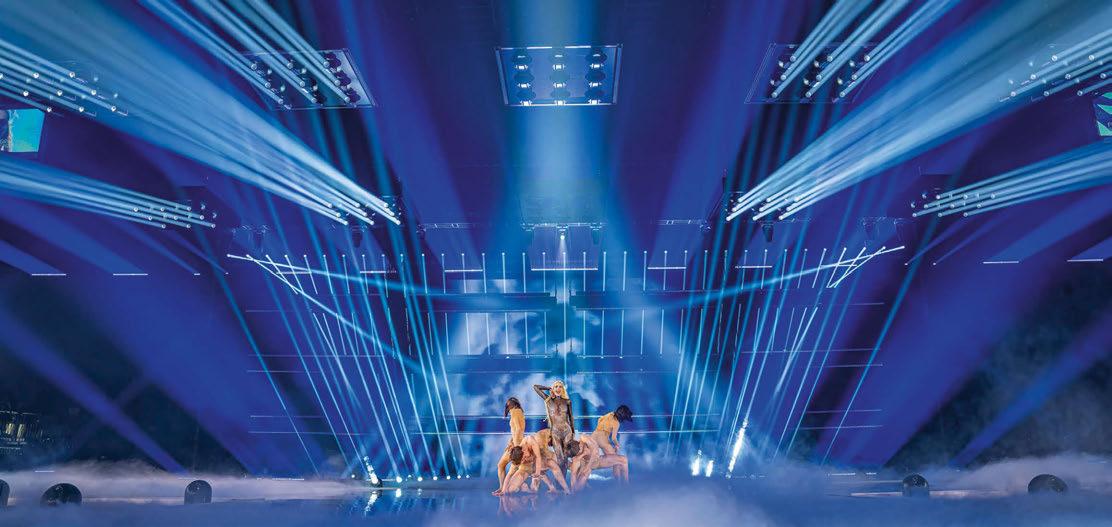
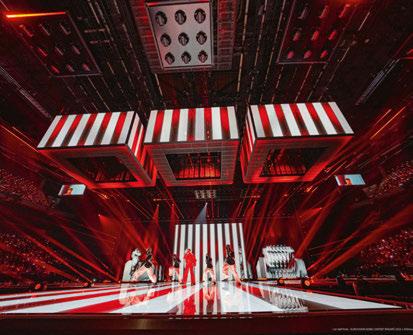
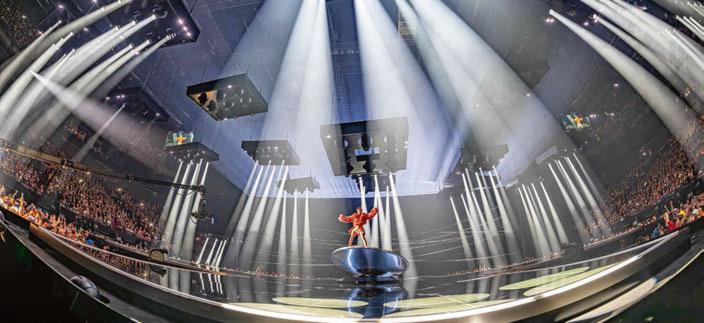
bleacher sections to avoid spill. It turned out to be a nice big powerful, traditional wash light with some extra features, which was exactly what I was looking for,” Stormby explained.
Looking for a fixture to outline the stage design in all dimensions, Stormby chose Ayrton Kyalamis, mounted on Wahlberg Motion Design Lifting Columns around the stage edges where they could be raised and lowered to define the shape of the stage as required.
Further Kyalamis were rigged in a long vertical line in each of the two 18m high towers that flanked the main video screen. Yet more were rigged on a 32m long truss using 62 universes alone which hung in front of the main video screen, completing a ‘football net’ effect with the side towers.
“Kyalamis on the truss and the towers could form a box of light for framing the back screen. We could also lower the massive truss right down to stage level so the Kyalamis could act as a floor package or raise it high to open out into very wide effects, and so many ways in between,” noted Stormby.
Around 52 Robe FORTEs, 57 T1 Profiles and 14 T2 Profiles were situated across the stage and green room to fulfil key lighting requirements. In addition, several FORTEs were
configured to run part of an extensive remote follow spotting system, so they could be called up and activated as needed.
“As with any broadcast show, key lighting is one of the fundamentals, so we were extremely pleased that Fredrik was happy to work with these Robe fixtures,” commented Emil Højmark, Head of Lighting at CT Sweden and Denmark.
Swedish distributor mLite, especially Mikael Uddh, played a key role in 170 ROXX CLUSTER S2 fixtures featuring on the CT lighting rig.
“Seeing our CLUSTER S2 fixtures contribute to the magical and vibrant ambiance of the show was a highlight of our professional journey,” ROXX’s Michael Herweg said. “It was a true honour to be part of an event that celebrates creativity and unity through music, and it reinforced our passion for pushing the boundaries of lighting technology.”
The result was a design with enough flexibility to create unique looks for each of the 37 participating countries’ very diverse performances, with less than a minute turnaround time between each song.
Stormby elaborated: “It was great fun working with this rig because we could position it in so many different places that, as well as giving us all manner of side light, backlight and low
lights, we could really play with the lighting and directions of lighting as well.”
The openness of the 360° stage allowed the team to invite the audience into the shots in a very natural way as part of the background.
“T his is when we had to rely on the skills of our programmers. If we were shooting from one side of the stage, we had to clean out all the lights hitting the bleachers on the other side to make it look good. We produced the show shot by shot to achieve the big clean cool rock concert looks yet were able to instantly cut to the hosts and back into Eurovision mode again,” Stormby explained.
The wider lighting team included: Associate Lighting Designers, Mike Smith and Michael Straun; Assistant Lighting Designer (Viewing Room), Louisa Smurthwaite; Followspot Caller, Per Hörding; Lighting Directors and Lead Programmers, Ishai Mika and Dom Adams; and Lighting Programmers, Leo Stenbeck, Linus Pansell, and Isak Gabre.
The production featured one of the largest MA Lighting grandMA3 control networks for lighting, playback video, lasers and LED wristbands to date, involving over 200,000 parameters of control across 682 DMX universes of output and 663 universes of Art-
Create the Maximum Experience
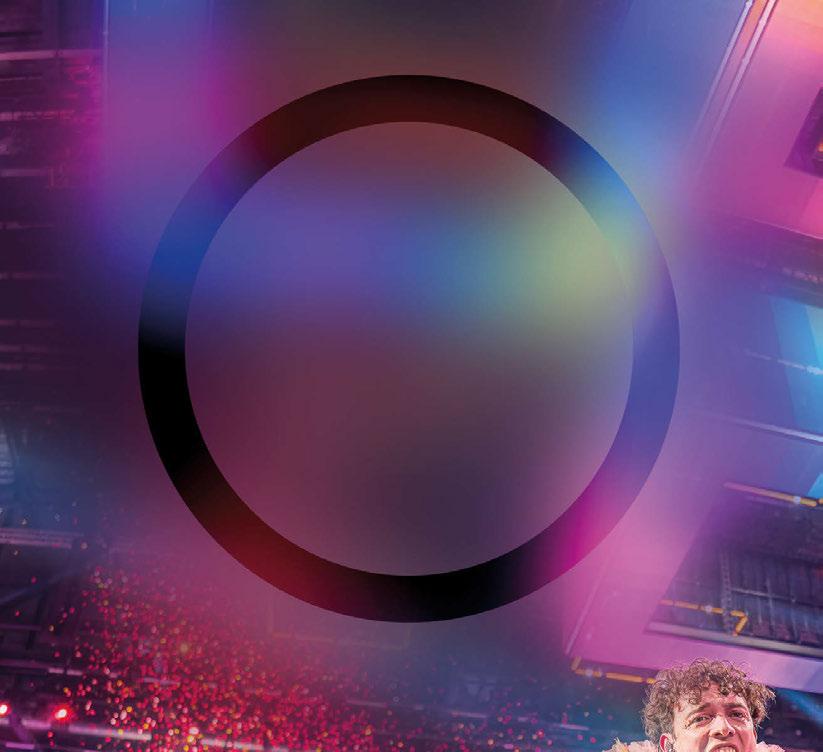
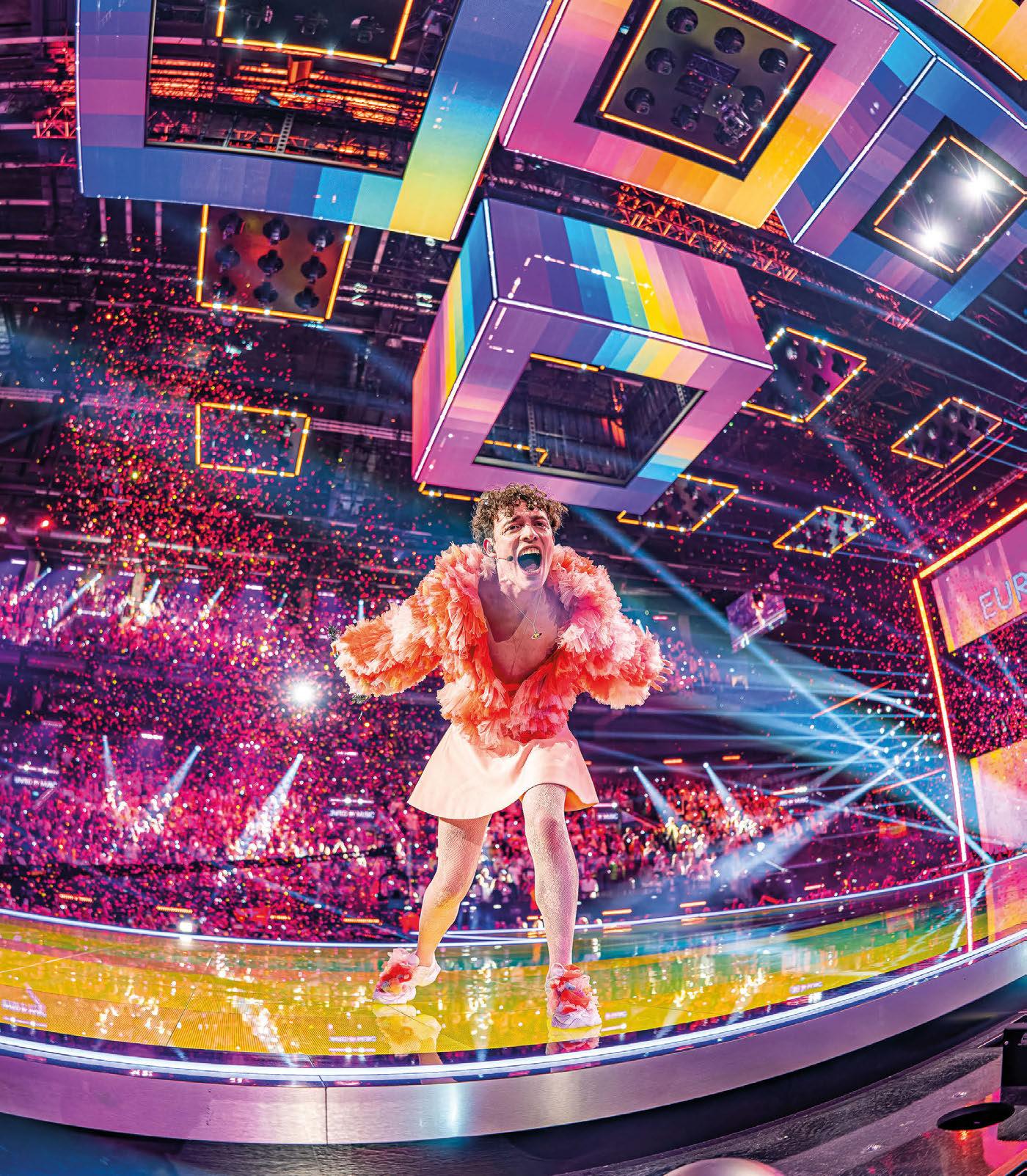
ROE Visual official event supplier
Premier choice LED products for Eurovision 2024
Your equipment must be reliable at all times. There’s no stopping the show, whatever happens. Eurovision Song Contest, renowned for its intricate production and spectacular designs, selected ROE Visual again to supply top-tier LED technology, including the Black Marble BM4 Floor, Vanish V8T cubes, over a kilometer of ROE Strip, and the stunning Black Quartz BQ4 main wall. Partnering with Creative Technology, ROE Visual’s cutting-edge LED products delivered a spectacular visual experience, enhancing the event’s global broadcast and live performances.
www. roevisual .com
Eurovision 2024, picture by Ralph Larmann
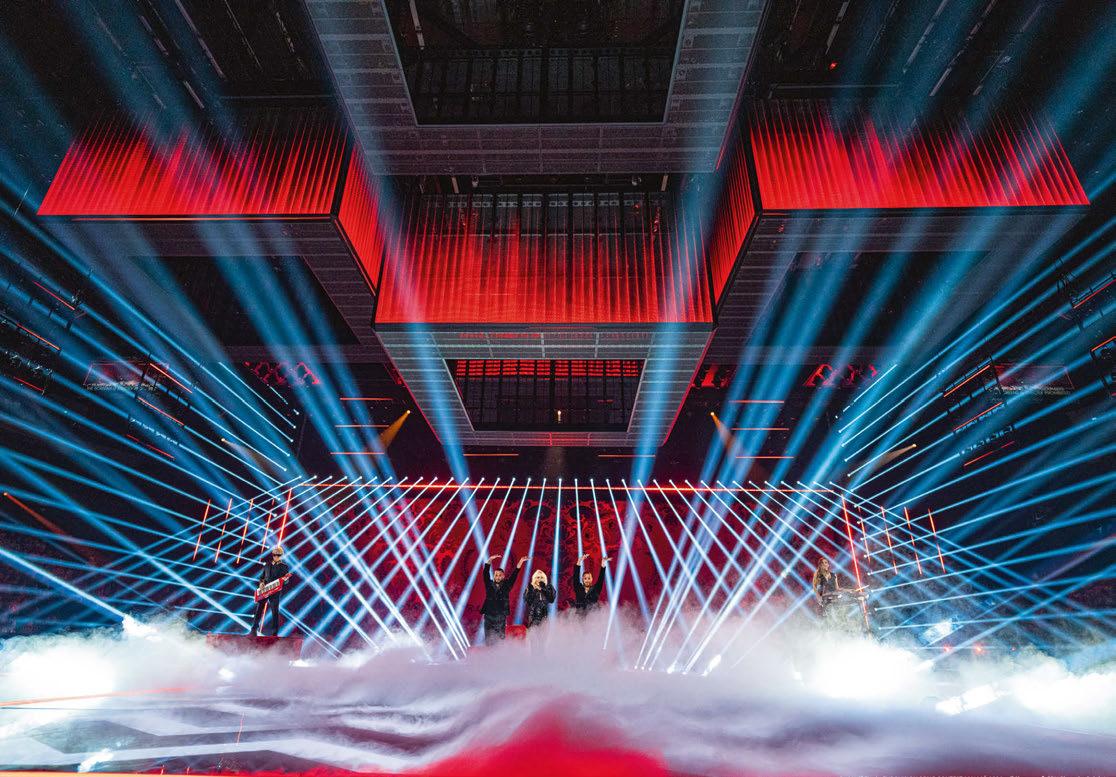
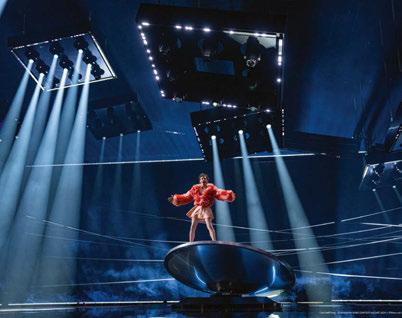

Net input from the Disguise media servers. Running all of this were up to 14 grandMA3 consoles and five main lighting show programmers all working in one session.
CROSS-SECTOR COLLABORATION
#UnitedByMusic went beyond the artists and creatives, and it took great teamwork between suppliers and distributors to bring the huge amount of equipment together.
CT collaborated with Danish-based VIGSØ to sub-hire the remainder of lighting fixtures. The fixture selection process was supported by Sweden’s TopStage who worked closely with the lighting designers to introduce, demonstrate and facilitate their choice of the new Ayrton fixtures and ensure everything was delivered and prepared in under 48 hours.
“It was very impressive,” Højmark said. “VIGSØ did what I’ve never seen before from a distributor to pull this together. All departments worked well together. It was hard work but good fun and all done in good spirit.”
TopStage’s Linnea Ljungmark added: “It was exciting to be involved in the decision-making process from the start. When Fredrik came to
me early in the process to discuss lights, it was clear to me that he was looking for a unique look – not a specific brand.”
Kenneth Jakobsen, Head of Sales at VIGSØ, commented: “VIGSØ was very happy to work with CT on this mammoth production. Everyone involved put in a huge team effort under challenging circumstances to collectively deliver the entire, massive project on time.”
Stormby added: “I think CT carried out an excellent delivery. With a rig designed like this with everything in straight lines, it really comes down to the finish of the build to make it look good and they really pulled that off.”
‘A PROJECT I’LL FOREVER REMEMBER’ Montreal-based PixMob provided RF equipment and LED wristbands to proceedings. The team harnessed technology to call all 9,500 wristbands to create multiple effects.
“Fredrik and I have collaborated on shows in the past, so he was aware of the creative capabilities of PixMob. I adjusted the colour and flow of the effects accordingly to match the visuals. We were working with RF, which made our setup as simple as a brick-sized node with
an antenna” Spain-based PixMob Operator, Eduardo Martin commented. “The PixMob wristbands we used at ESC only have two LED pixels, so sometimes it’s hard to compete in brightness with all the surrounding video and but thanks to Fredrik’s great keylight approach, our wristbands got to shine bright. The introduction of each performance, after the ‘postcard’ with the flash of the colours was the best demonstration of the creative capabilities of PixMob wristbands in enveloping the crowd in the lighting design,” Martin added.
“I really enjoyed working with PixMob and the audience with elements of the automated rig such as the infield pods in between, creating a layered effect of lighting in the back of shots,” Stormby commented.
“I was immediately impressed by the sheer level of production. I had Malmö Redhawks women’s team on site at Malmo Arena helping me prepare and distribute the wristbands for each rehearsal and live show. Almost 80% of the recyclable wristbands were returned postshow,” Rahel Feidler, PixMob Project and Pixel Manager, reported. “We are proud of what we have achieved and to play a small part in the
production with a fantastic team.” In closing, Martin shared his favourite moment from the show: “At the end of Slimane’s Mon Amour, he moves away from the microphone, and you can see our wristbands twinkle in the background, which was a special moment,” he enthused. “This was a landmark project and one I will remember forever.”
CUTTING-EDGE TECHNOLOGY
The cross-shaped stage featured 186 sq m of ROE Visual Black Marble BM4 LED panels; while 460 sq m of Vanish V8T transparent LED panels formed five moving squares, with each cube side highlighted with ROE Strip. A further 340 sq m Black Quartz BQ4 LED panels served as the back wall, including a spectacular opening sequence for the green room. “Over the years, we have noticed production trends and conventions come and go – from the heavy use of projection in past years to the increase of video surfaces,” Stormby theorised.
The technical setup included Helios LED processing and Disguise media servers. The production was timecoded meticulously, from camera shots to LED screen content, ensuring synchronisation. The team used Megapixel
Omnis and Faber FRM LED monitoring systems, logging data from all LED panels.
“O verall, the event utilised 1,100m of ROE Strip around all cubes and lighting pods, enhancing the overall visual impact,” Stormby highlighted. “The Black Marble LED floor allowed us to manage the rapid changeovers with accuracy using disguise digital markers to ensure that every prop was in place exactly when and where it needed to be,” he said. For the first time, the entire LED system operated on an SMPTE 2110 network. This setup utilised a two-core system with 42 100G connections.
The switch to fibre optic technology allowed for unprecedented data transfer rates. The production processed 1.2 terabytes of data per second, the equivalent of streaming 100,000 4K Netflix movies simultaneously. The entire fibre optic network made this monumental amount of data handling possible, surpassing copper cables’ limitations.
LED monitoring was conducted offline for cybersecurity reasons, with alerts sent via SMS to the technical team if a processor issue was detected. “Our advanced network and monitoring capabilities were crucial in delivering a flawless visual experience at
Eurovision,” commented Niclas Ljung, Chief Technology Officer, CT. “The transition to a full 2110 network and the redundancy measures we implemented ensured that the show ran very smoothly.”
ROE Visual Marketing Manager, Marina Prak praised the team for their “outstanding” work: “ESC showcases the power of cutting-edge LED technology and ROE Visual’s commitment to excellence, innovation, and collaboration. We are nothing but thankful for CT and the wider production team for delivering an impeccable and flawless showcase of technology and art.”
Over 163m television viewers tuned in to watch the finale with Switzerland’s Nemo crowned winner with their song, The Code
Summing up his experience, having spent months masterminding a different type of code, Stormby summarised: “It was 10 weeks of bonkers production but I’m proud of the result and we certainly ticked all the boxes in ‘respectfully challenging the concept.” www.eurovision.com www.ct-group.com www.greenwalldesign.com www.pixmob.com www.roevisual.com
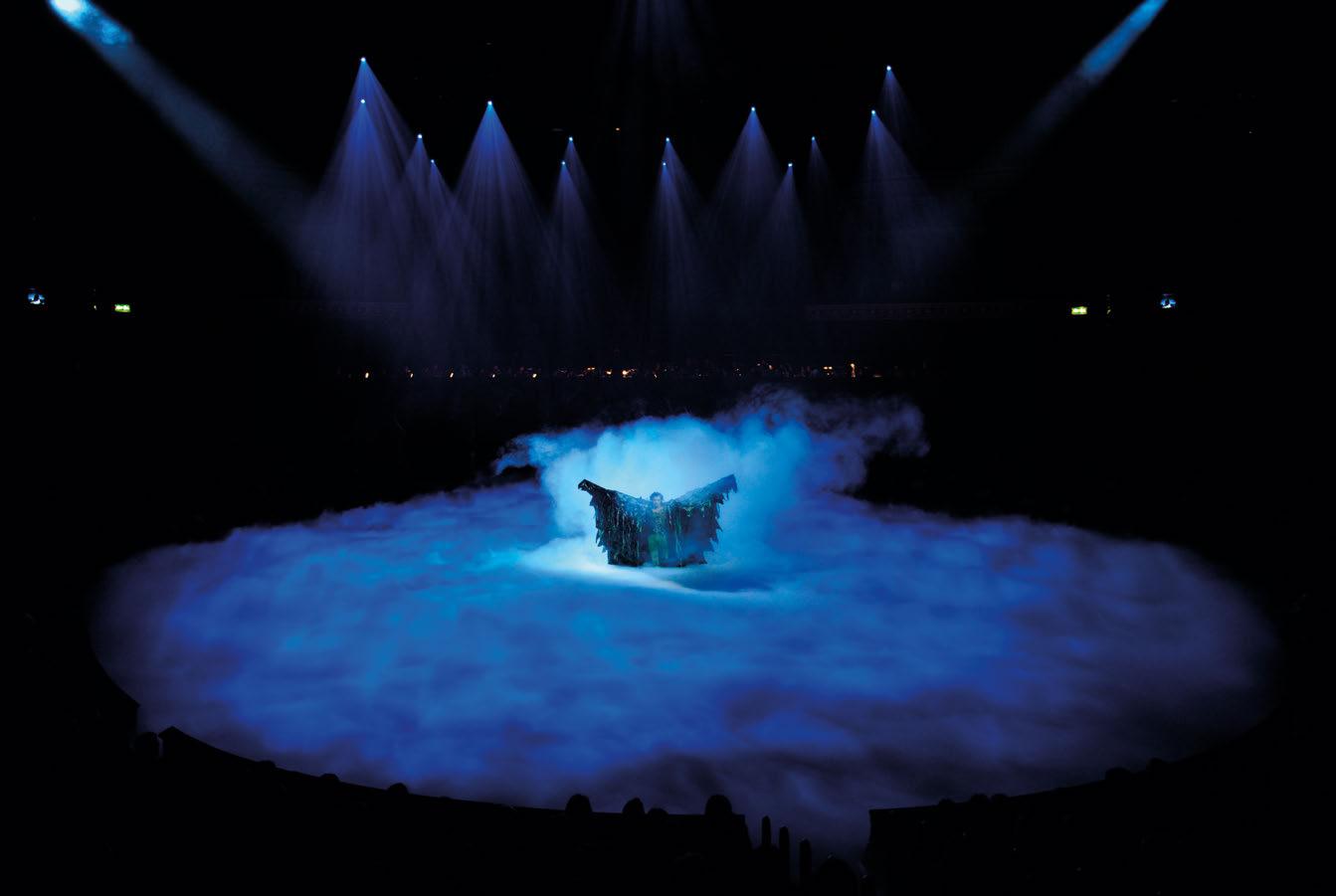

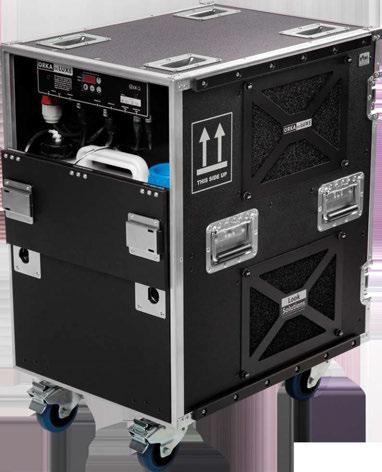
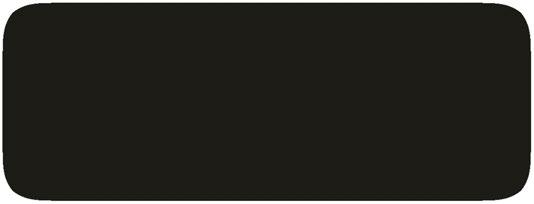
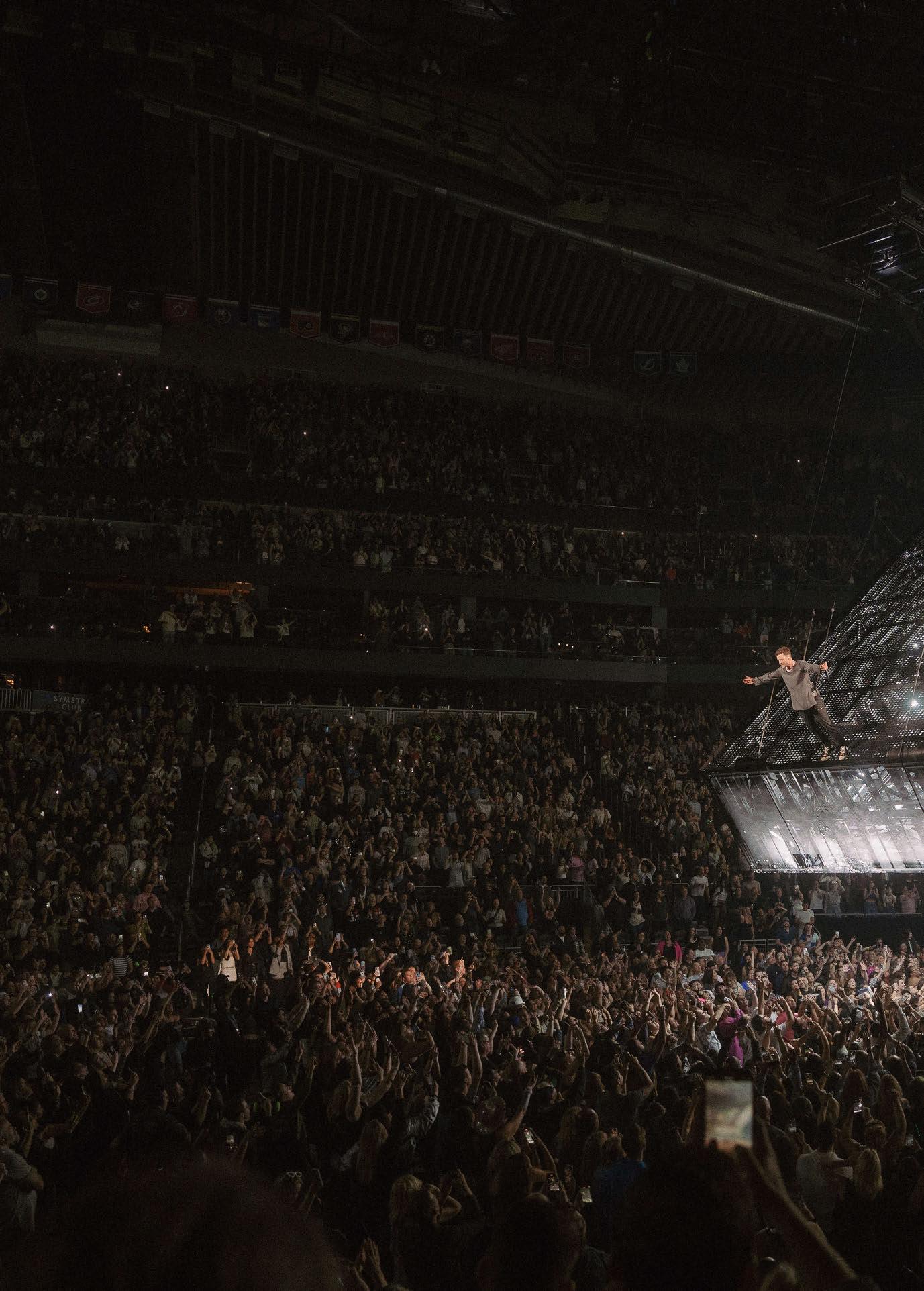
JUSTIN TIMBERLAKE: THE FORGET
TOMORROW
WORLD TOUR
The singer-songwriter’s latest live offering lives up to his unfaltering legacy of providing crowds jaw-dropping moments with creative teams behind the scenes working in tandem with technical and engineering specialists to craft an unmissable spectacle.

Words: Jacob Waite
Photos: Mark La Shark
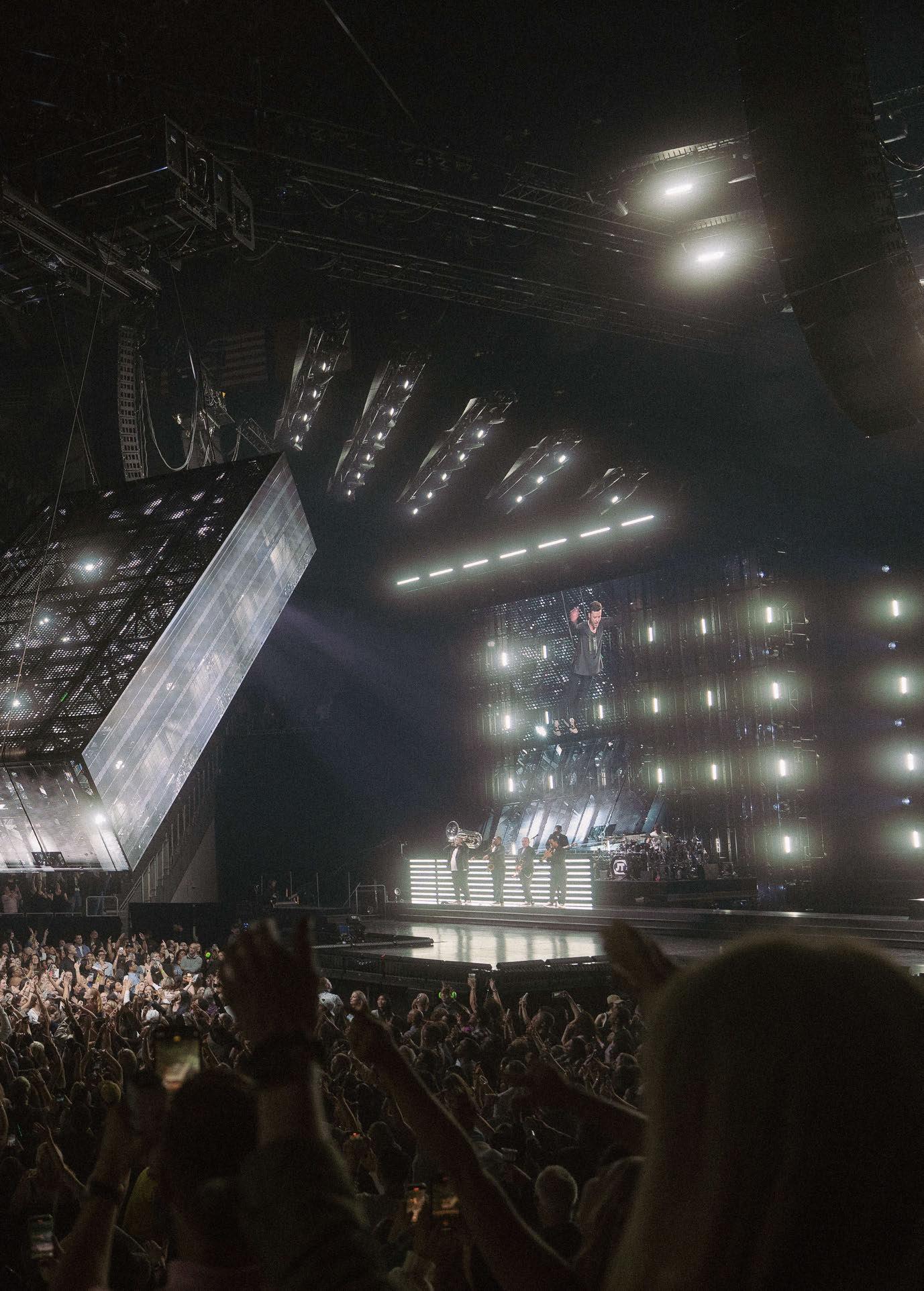
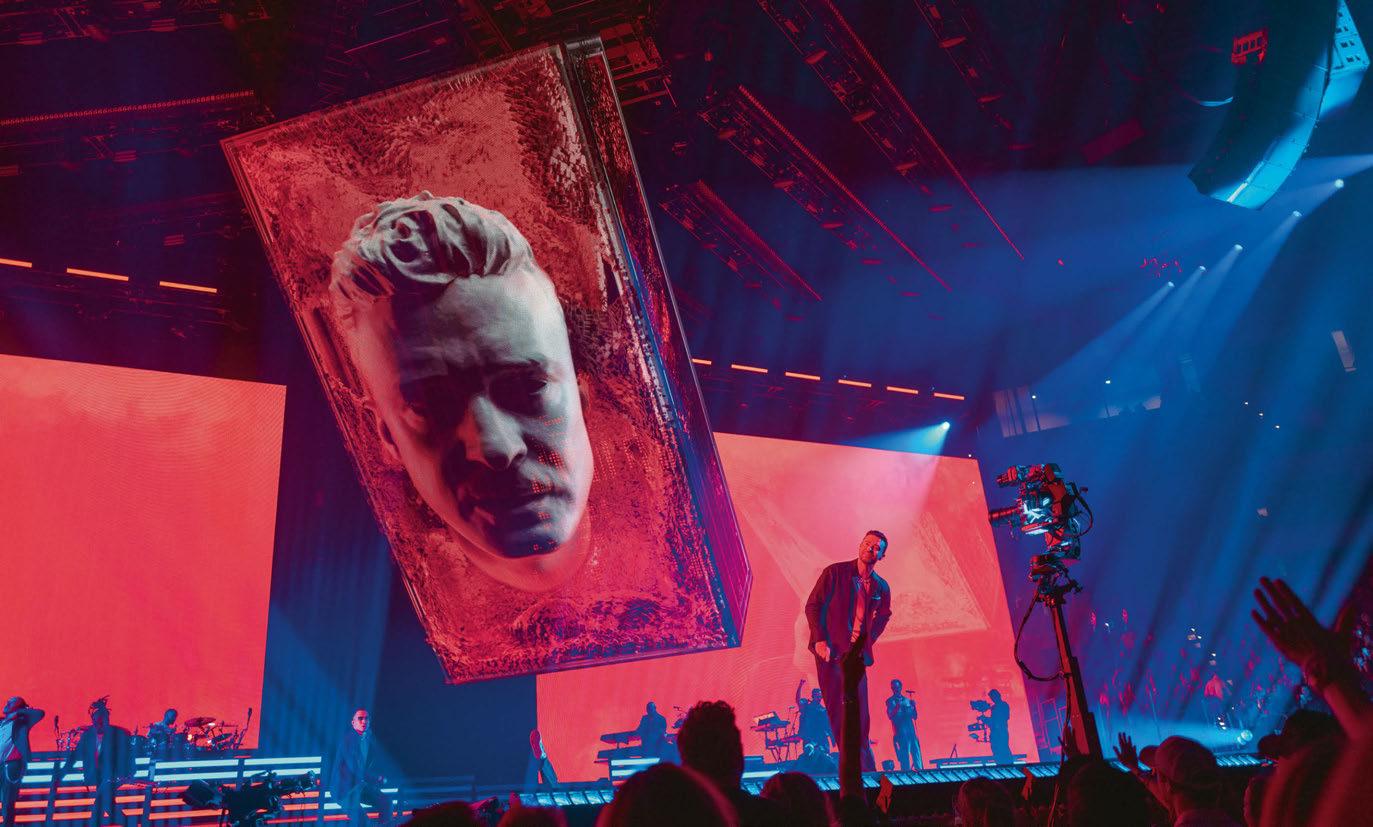
Marking Justin Timberlake’s long-awaited return to the touring circuit after a five-year hiatus, the Forget Tomorrow World Tour hit the road in Vancouver on 29 April to widespread acclaim and has turned the heads of those in live entertainment industry ever since. Behind the scenes, a talented troupe of creatives, technicians, engineers and support teams work tirelessly to transform an ambitious vision into a reality. Conceived and created by Justin Timberlake in collaboration with Production Director, Baz Halpin of Silent House, the 26-truck strong tour is a testament to the singer-songwriter’s enduring legacy of providing audiences with never-seen-before moments of performative art underscored by technical ingenuity.
Having built the foundation of the tour in tandem with Production Director, Robert ‘Hydro’ Mullin, Production Manager, Luke Larson – formerly stage manager on 2018’s Man of the Woods Tour – handled the advance, planning the logistics of moving this show from venue to venue. “My prior knowledge of the camp is helpful in the sense that I’m aware of the workflows,” he stated. “The attitude of the artist trickles from the top down on this tour. When we face challenges, we pivot to make the show happen regarding the intricacies of each venue without detriment to the overall vision.”
Speaking to TPi 15 shows into the cycle from Dickies Arena in Fort Worth, Texas, Larson recalled the embryonic stages of the project: “We initially hung half of the rig at Las Vegas’ MGM Grand Arena for a week in March to see how the show would piece together. We soon realised how heavy this show is, with a very concentrated load, which is demanding for a
lot of venues. For many dates, we are simply unable to load the show in its full capacity due to the sheer weight of the rig. We also spent a month in Vancouver with the show 100% together with the tech, choreography and musical direction before the first show.”
The technical suppliers of choice included TAIT (automation and staging), Solotech (audio, lighting, rigging and video), eps (barricades), Dreamliner (crew travel), Rock-it Cargo (freighting), and Truck’N Roll (logistics). “All our vendors are at the top of their game. On a show of this size and budget, we have the option to handpick the vendors we want to work with,” the PM remarked.
“From the inception to the delivery, with some complicated elements, we’ve put a lot of talented people on board to develop the custom elements of the show to handle the automation in line with TAIT. It’s quite a feat of engineering and the results speak for themselves,” said Lee Moro, Solotech Senior Vice President of Business Development.
“As this tour heads overseas, there are costs Solotech can offset using our vast network of global offices, compliant with the varying regional regulations and certifications; providing crew with information and resources before they need it. There is also a budget to be considered, so when you’re facilitating equipment for all departments, we concentrated heavily on the business and financials. There are efficiencies associated with a turnkey solution by centralising equipment, for example.”
A familiar face to the Justin Timberlake camp, having been a touring member of the team in his past life, Solotech Vice President
of Operations, John Flynn, added: “We know the high standard, speed and efficiencies they expect because transporting 26 trucks worth of gear into arenas isn’t easy. It’s ‘A-level’ touring. We have a lot of people intrinsically tied to the camp, which also helps with troubleshooting,” Flynn commented. “Putting so much weight in the roof means there are sacrifices made by all departments to create the most efficient show possible while also making the creative vision a reality. Uniting as a team instead of operating departments, collaborating with TAIT on things like cable management, load-in and -out processes, and combined rigging plots.”
The creative team behind the production included: Choreographer, Marty Kudelka; Musical Director and Programmer, Adam Blackstone of BASSic Black Entertainment; Lighting Designer, Cory FitzGerald of Silent House; Video Content Designer, Gabriel Coutu Dumont of Silent Partners Studios; Design Producer, Vincent Richards of Silent House; IMAG Executive Director, Sam Wrench of Good Cousin; Creative Consultants, Archie Lee Coates IV and Jeff Idehen of PlayLab, Inc. “Justin’s shows are renowned for unique use of entertainment technology; it’s become the cornerstone of his shows, and this one doesn’t deviate from that,” Larson noted.
BUILDING BLOCKY
Amid the show, Timberlake and his band, the Tennessee Kids, traverse the audience to a smaller stage at the back of the arena floor, performing eight tracks on the B-stage. The show concludes with Timberlake performing Mirrors on top of an automated floating stage
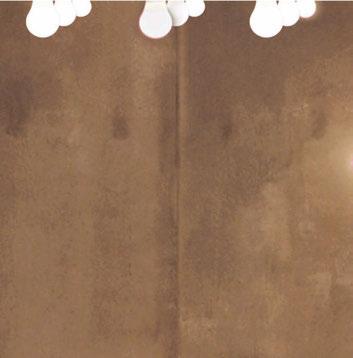
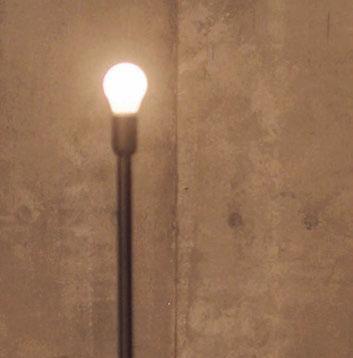


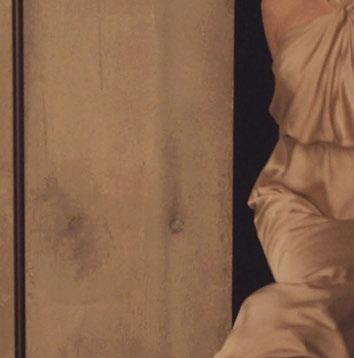
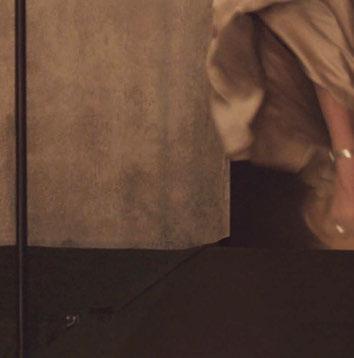

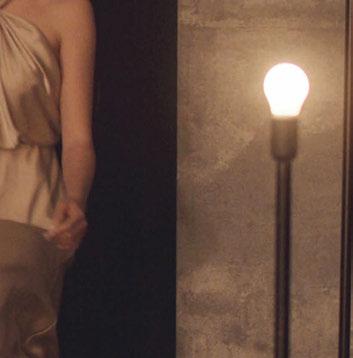
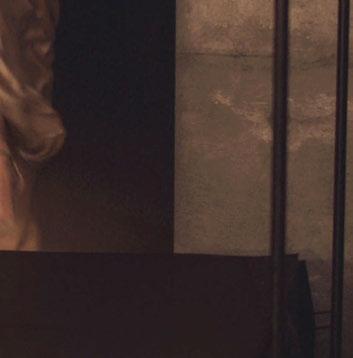
SET THE MOOD, SHAPE EMOTIONS
Discover endless creative possibilities without disrupting your workflow. From intimate gatherings to grand events, our solution o ers intuitive control via your smart device, remote, or console. Easily pair and manage with a simple remote via IR or the Astera App for seamless operation.
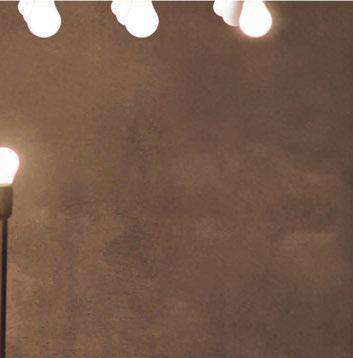

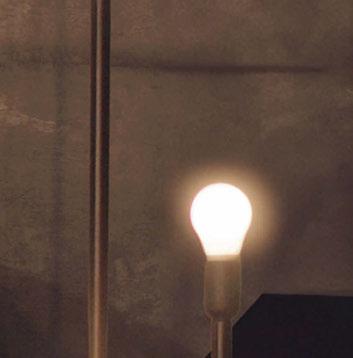
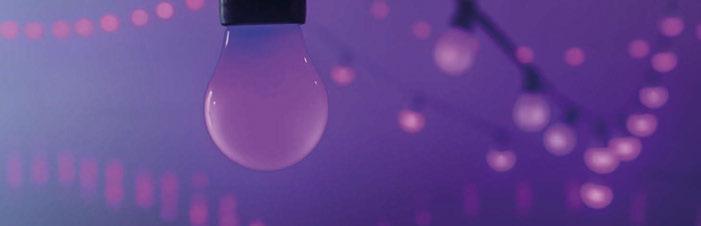
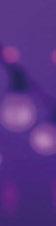
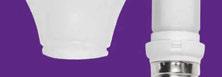
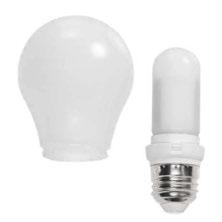
Classic to Slim Look
Choose between a classic and di used look or a slim and brighter hotspot.
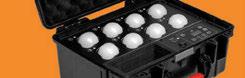
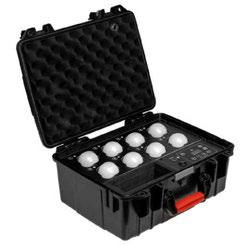
PrepCase Kit
The quickest way to set up 8 bulbs: assign DMX address, pre-configure dimming and color, pair them at once.
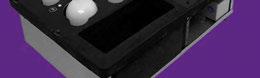

Preplnlay Kit
Simply add PrepInlays to your custom flightcase to use and prepare LunaBulbs in volume.

structure internally dubbed ‘the monolith’ and externally, by JT faithful, as ‘Blocky Timberlake’. Held safe by wires attached to a harness at his waist with his feet secured by straps to the deck, Timberlake rides the structure as it progresses above the crowd, turning from side to side in the arena. Toward the end of the song, as if bowing to the audience below, the stage angles forward in a way that tips Timberlake, his head extended well in front of his feet, almost onto the audience below.
TAIT provided the staging infrastructure for the main stage – including a performer lift in the downstage centre, 10 custom-built light lifters in the upstage half, which were part of the staging design but revealed themselves to be walls of lighting fixtures; above the light lifters were a further three large band lifts –each 10ft by 20ft – as well as the monolith and automation capabilities of the structure and side screens which bi-part revealing the monolith, plus the B-stage, VIP and bar area.
“Our relationship with Justin Timberlake goes all the way back to the NSYNC days,” TAIT Senior Project Manager, Logan Lower pointed out. “The design first made its way over to us in October 2023. Initially, the staging scope was straightforward – an arena tour with staging and multiple lifts. Then the idea of the monolith was floated under the guise of a ‘massive object that you don’t even know exists, which as it begins to reveal itself, can exhibit more tricks’,” he recalled. “Using this intel, we were able to help during the process of designing and engineering it in defining what those unique tricks would be.”
This project was a holistic effort between every department at TAIT, involving anywhere
from 200 to 300 people at the company’s Lititz campus – from the design and development teams crafting the initial conception of the artistic ideas alongside Silent House, through to the mechanical design department then taking that concept to the next level of detail with TAIT’s controls, design and mechanical engineering departments all helping contribute in figuring out how to technically execute what would become the monolith, and flesh out every last detail. On the production side, the project was also touched by everybody in TAIT’s vast machine shop, including its mechanical and controls fabrication floor, who also had a hand in making the creative vision become a reality.
The wider TAIT team featured Associate Project Manager, Jessa Grant; Technical Lead, Paul Sapsis; Project Design Lead, Nathan Poglein; Design Leads, Nick Bonsell, Dale Harris, Chris Norville, Steven Davis, Josh Sabo, Christine LemMon, and Andrew Hyatt; Mechanical Integration Lead, Tim Italiano; Control Integration Lead, David Alfano and Automation Programmer, Jason Shupe.
“A nything we designed and engineered had to be light enough to fit into any indoor arenasized venue in the world and easy to construct in a day. To ensure we the monolith was as light, configurable and tourable as possible, it was split into sections that could be assembled within hours on site,” Lower explained.
In collaboration with Solotech and ROE Visual, the production team utilised bespoke video products and mounting frames on the monolith. Even the winches, gantry truss, trolley and rotators were all designed and built from scratch in-house. “We knew the
monolith was going to be a unique gag but the personality that it has developed on social media as @blockytimberlake has been fun to follow,” Lower remarked.
With the monolith spanning 120ft into the audience, health and safety was vital. “Every system we build has top-to-bottom health and safety and risk assessment. The whole system is completely redundant. The lifting machines are 10:1 safety factor; they have redundant brakes inside of them,” Lower underlined.
Project timeline was also a key factor in TAIT’s involvement. “One of the reasons why customers come to TAIT to provide these services is to get it done in a tight timeframe. No other company in the world can make it happen as fast as we can,” Lower stated.
Harnessing its vast global network, TAIT not only designed, engineered and fabricated but also procured all the materials, motors and components required. Once all the designing and engineering work was done, a specialist team of programmers were piloted in to make the automation possible.
“Our automation platform, Navigator, is the star of the show, making sure that the monolith moves consistently and safety day in and day out,” Lower said, citing the support of Brian Levine and wider TAIT team. “Seeing everyone’s artwork transform into an amazing spectacle for thousands of fans each night is special. Collaborating with the production team and technical suppliers to develop the creative in tandem with the technical execution was a fantastic experience.”
Head Carpenter, Graham ‘Naylor’ O’Neill and Carpenters, Calvin Mosier, Nick Webber, Taylor Schmit, and William Koch – who was embarking
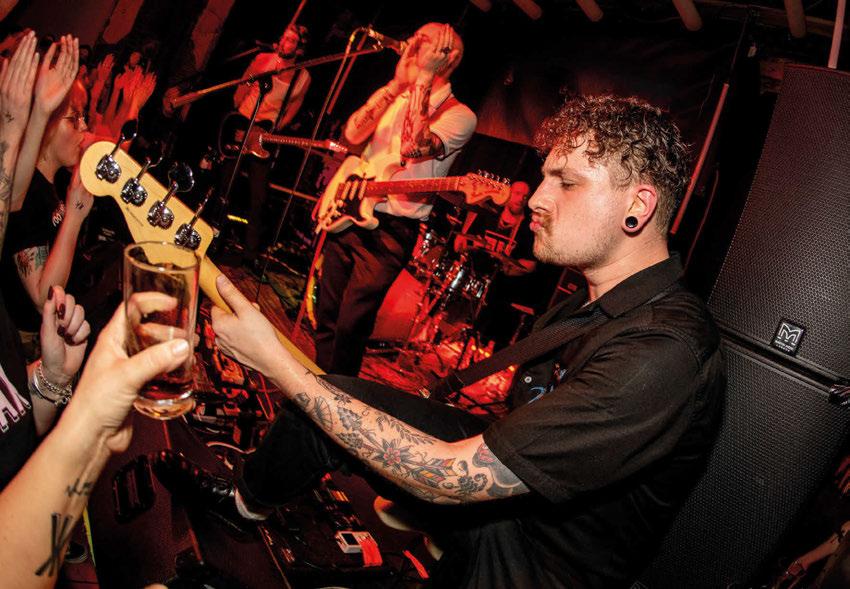

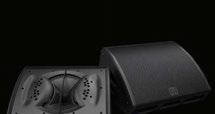
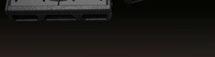
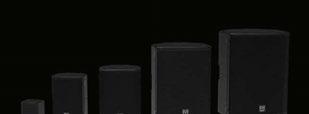





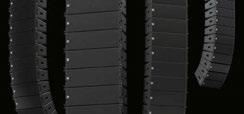

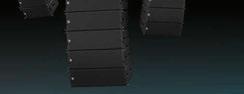
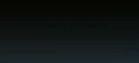
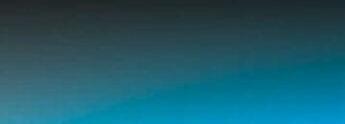
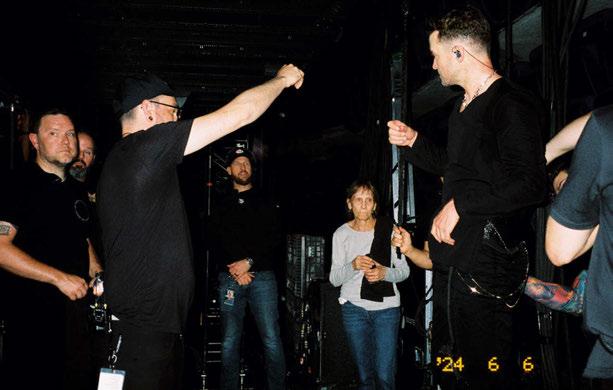

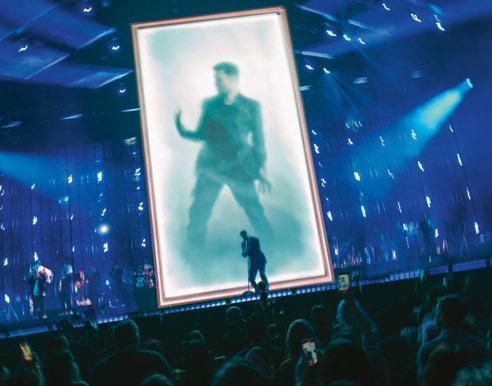
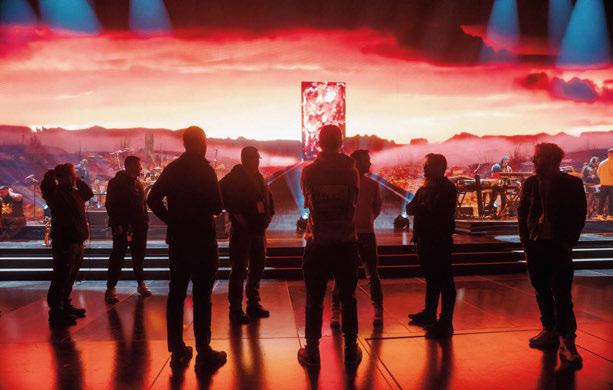
on his first tour – oversaw the complex stage build with 16 local stagehands.
“T he main stage gets built first in four sections. Three members of the team then construct the B-stage – putting together a bar for VIPs and curved runway for the band and dancers to perform on – which is a beast. Calvin and I jump in with the automation team and build all the band risers and light lifters on the main stage. Then we roll into place and get it all set and ready for the show,” Naylor explained.
The wider automation team featured TAIT Crew Chief, Nicholas Smith; Automation Operators, Brandon Davis, Didier ‘Didi’ Giraldo, Matthew Garrett, Daniel Evans and Takiya Cade. “TAIT kit and set is, as always, the best to work with, but the automation and moving parts are a step above anything I’ve seen from them before. They just keep breaking boundaries,” Naylor said. “Nevertheless, the gear is nothing without the crew, and on this tour, I’ve been blown away by their support on the road.”
Naylor explained how the support of the artist is key to the success of the show. “The rapport Justin has with all the crew sets the tone,” he reported. “What a lot of people don’t see is the camaraderie and banter that goes on behind the scenes. He seems to be enjoying performing and his band and dancers are
unreal! Our team are as good as it gets, making hard days easy. Overall, it’s been great so far and will only get better.”
‘VIDEO INFINITY’
“My very first tour was NSYNC’s Ain’t No Stopping Us Now. I was a camera operator and built projection screens,” Video Director, Bertrand Paré Jr recalled, reciting some of his favourite looks. “During the track, Infinity Sex we wanted to create ‘video infinity’ against the monolith. To achieve this, we have an ultra-wide lens on a Panasonic BS1H camera on top of our regular Luna Remote Systems camera and then we line up the shot perfectly with the monolith and JT does a dance number in front of the video wall and that creates multiples of himself and a dancer,” Paré explained. “He understood the concept immediately and within a few seconds had figured out how to time it just right so that whenever he moves, he lets the infinity multiply all the way to the end of the trail before moving again.”
The video rider comprised a Grass Valley Karrera video switcher, Panasonic UC 4000 and PLV 100 and BGH1 cameras with Tilta Nucleus controllers; Fujinon Duvo 24-300mm, 107 and 46 lenses; an inverted XL Tower, 3300 Tower and 3400 Tower camera on a Lizard dolly
track; a Steadicam Aero 30 stabiliser system; VZ-Snapcrane-16 with a Fujinon Cabrio 19-90 lense and a ABonAir wireless system.
Another “great moment”, according to Paré is a long take on a Steadicam, which goes from the main to the B-stage. “It’s a small miracle that wireless has come such a long way even in the past few years. It’s always fun to see all the hands getting in front of the lens and all the people reacting to him walking through the aisle all the way from one end of the arena to the other,” he said.
“A nother great shot is at the very end for the big moment when JT rides Blocky. Our inverted tower camera gets eye level with him, and you have a sense of height and scale with the audience below him that’s dramatic. Our pit camera, the Luna on tracks, gets to his eye line and JT plays directly to it several times during the show. It feels more direct and like a music video shoot.”
IMAG Executive Director, Sam Wrench of Good Cousin enlisted CuePilot during rehearsals to record and refine camera shots. After a few shows, CuePilot was used primarily as a reference tool, providing on-the-road flexibility. “All our features have been developed in line with user feedback,” CuePilot Business Development Manager, Danny Hodgetts,
RACCOON
✓ Ultra-bright strobe/wash combo
✓ 35 CW LEDs
✓ 420 RGBW LEDs
✓ Ten individually controllable sections
✓ High CRI (>92) 1 - 3 September 2024 STAND B23
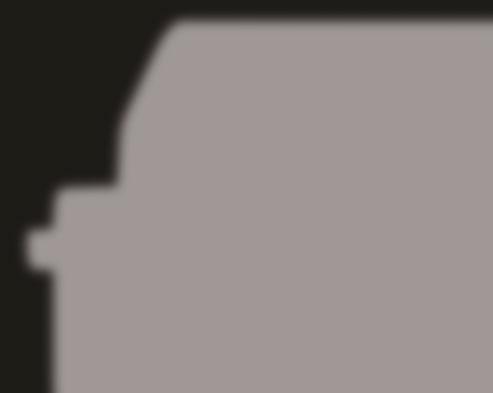
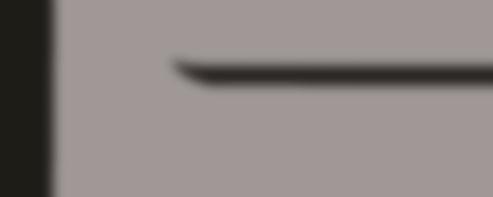

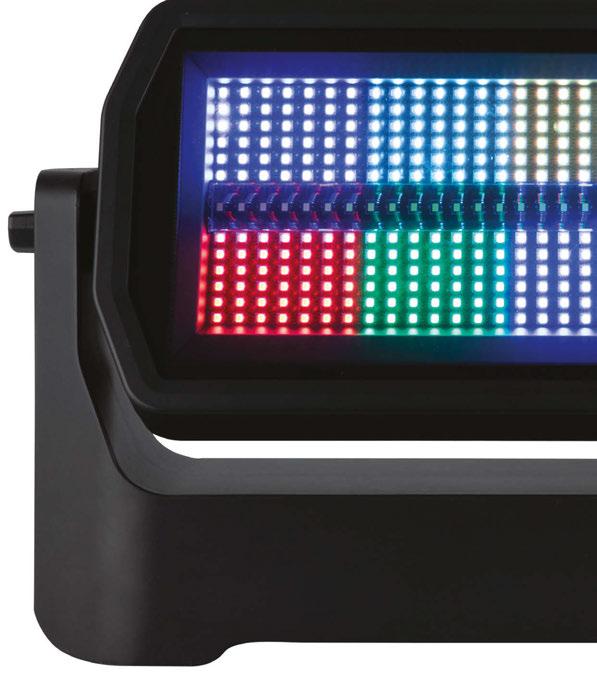

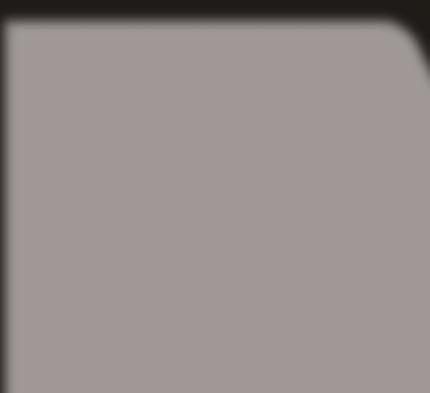

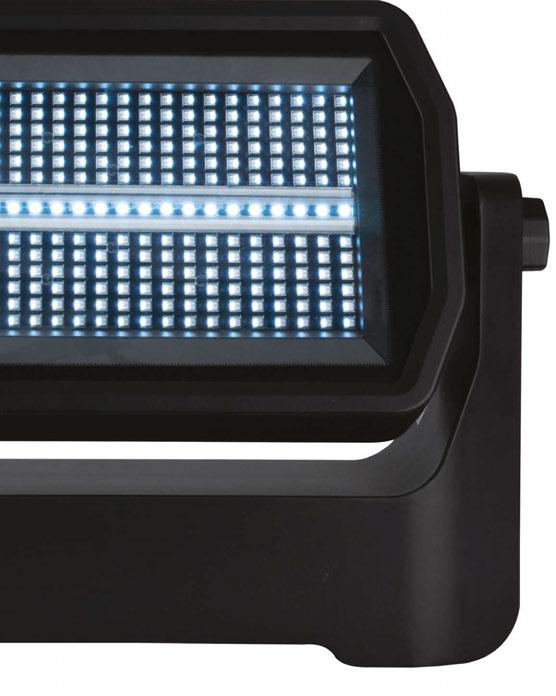

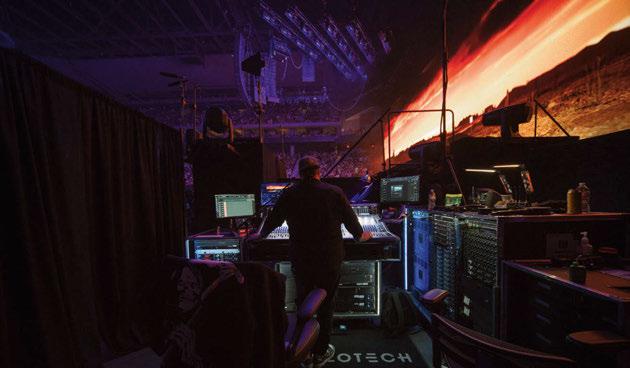
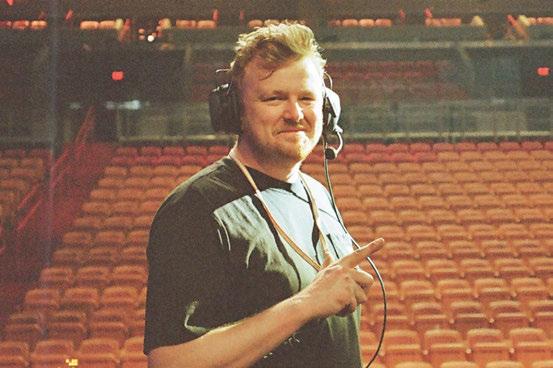
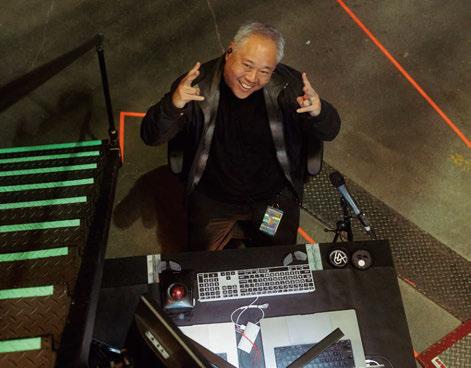
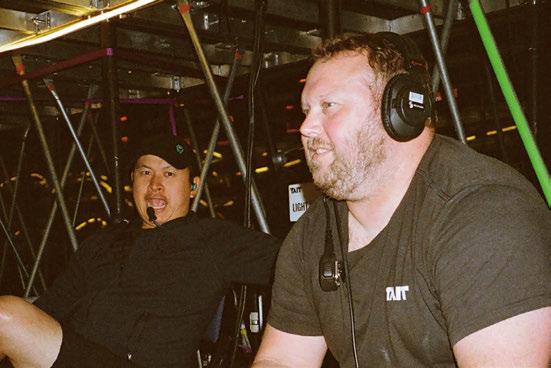
explained. “We were originally designed as a tool for the TV and broadcast market but now we’re now finding a lot of use in concert touring. There are slight differences in workflow which we’re adapting the system to accommodate.”
Network/Media Server Engineer and Operator, Ismael Alicea of ISH.TECH oversaw the installation of media servers during the load in, maintaining the network between servers and across entire video system.
“It’s been an amazing experience to witness how each piece of the design comes together,” he said. “Working with the most talented and experienced people in the industry to bring this performance to life has been spectacular.”
The show featured two tracking screens stage left and right, each 13m wide by 9m high made up of ROE Visual V8T LED tiles – a mixture of 108 touring panels and 18 custom touring panels. Both screens are assembled in a moving track that moves from upstage centre to upstage right and left with tracking data sent to the server via PSN for tracking the screen in real time.
The monolith comprised 101 V8T custom LED tiles, powered by a Brompton Technology SX40 processor with two XD boxes buried within the structure. “When the monolith joins the tracking screen, this gives us a spectacular 30m by 9m screen,” Alicea explained.
Measuring 5m by 9m, the monolith – clad with LED and lighting fixtures – was installed on a moving track that can move over the
audience down stage, rotate 360° and lean more than 90°. “To bring power and video data to the monolith, we use custom power and fibreoptic slip ring, letting us have power distro and XD distribution boxes inside the monolith to connect the LED panels and power,” Alicea explained. “We use three Disguise GX 3 media servers giving us more capacity in GPU and friendly use of the Notch blocks during the show. Silent Partners Studio and Earlybird Visual did a great job optimising the Notch blocks to not exceed the server GPU capacity and to have a smooth show each day.”
To control the show, the team harnessed two MA Lighting grandMA3 consoles operating in MA3 mode with custom macros to recall each song and timecode. The console sent commands via sACN to the disguise server, using sockpuppet to recall video layers and effects from the servers. Alicea also designed a custom BRIDE to run tests and control the system, which included a Dante rig, a custom server with GPU A6000, monitors and routing control for the entire system from FOH.
The network setup used Cisco switches, which Alicea dubbed the “most stable and reliable” switchers in the world. “I have two CORE switches in STACK MODE to give us fibre redundancy to all the switchers across the network in case of failures,” he remarked.
“It’s always a pleasure to work with Solotech and their amazing team. They always provide me with the right equipment to complete
Monitor Engineer, Jon Kooren; Pro Tools Playback Engineer, Danny Cheung; Lighting Technician, Kevin Chan with Automation Operator, Dan Evans; Network/FOH Lighting, Callum Humphries.
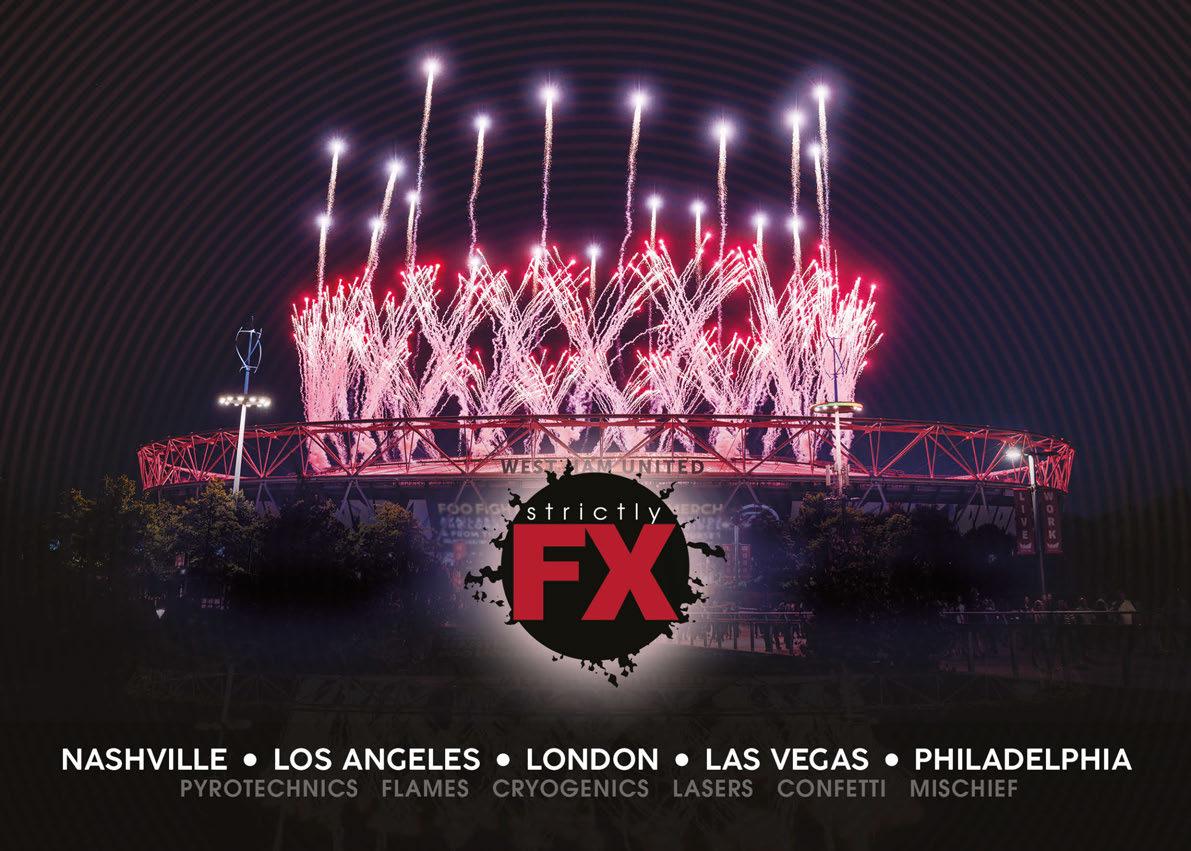
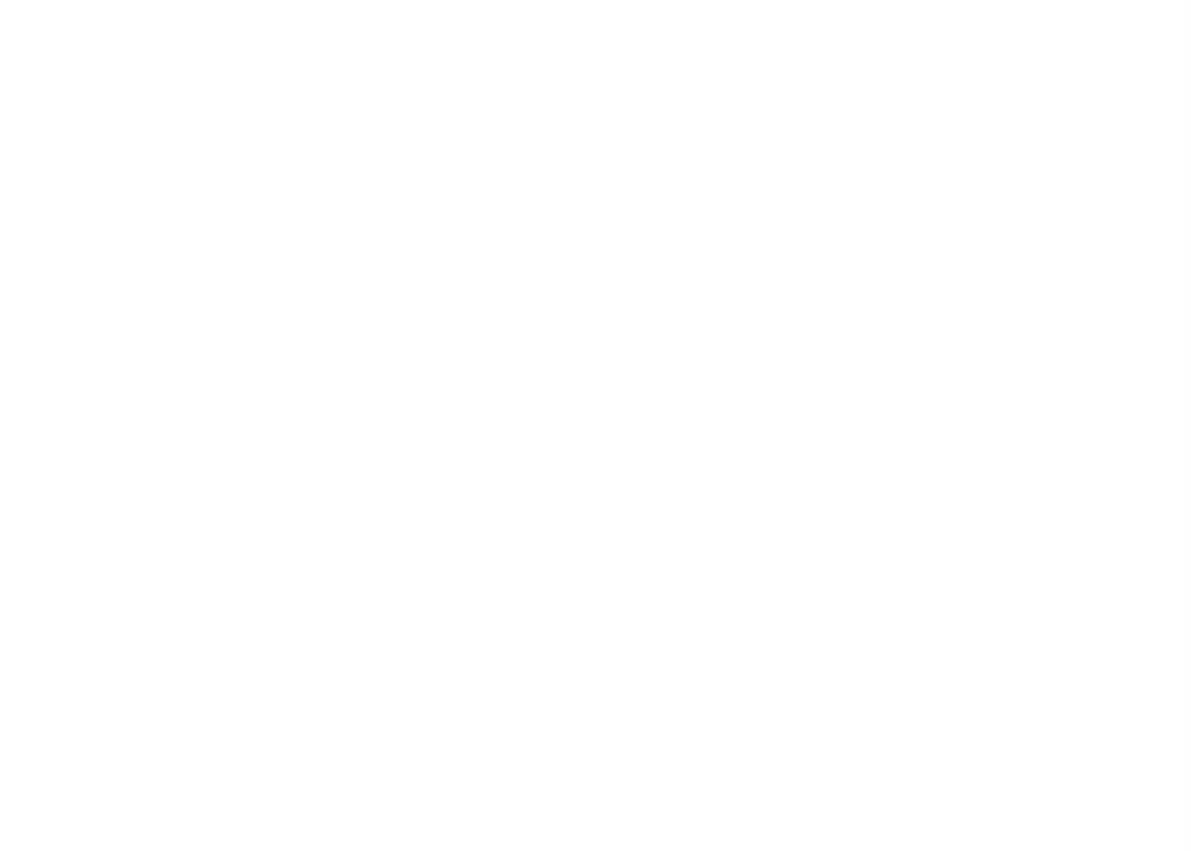
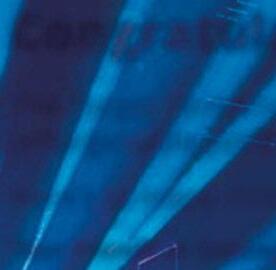
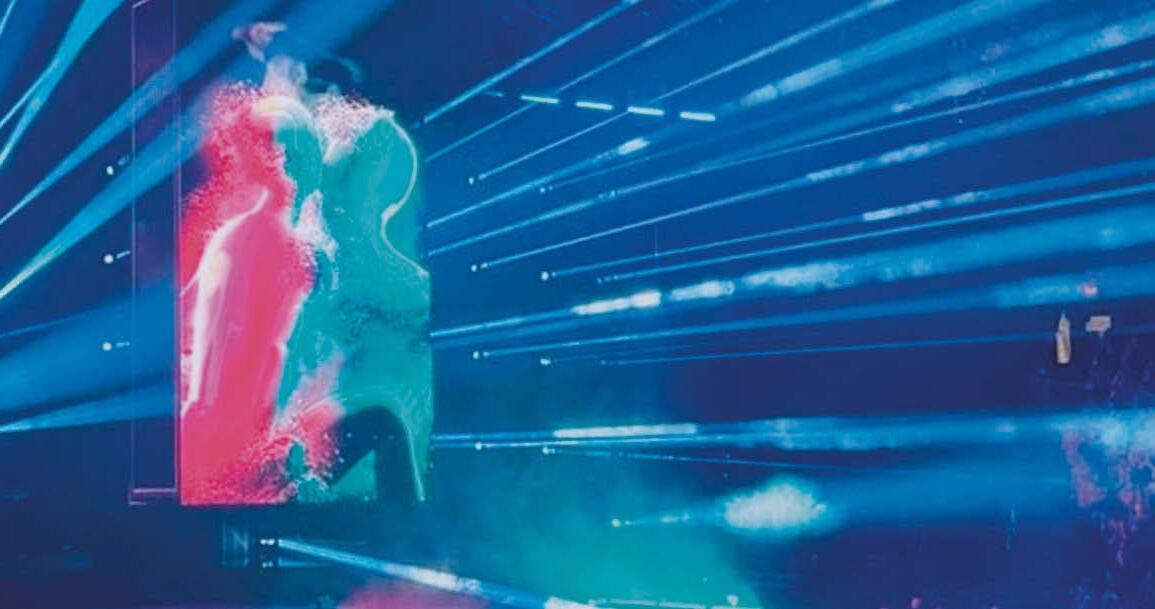
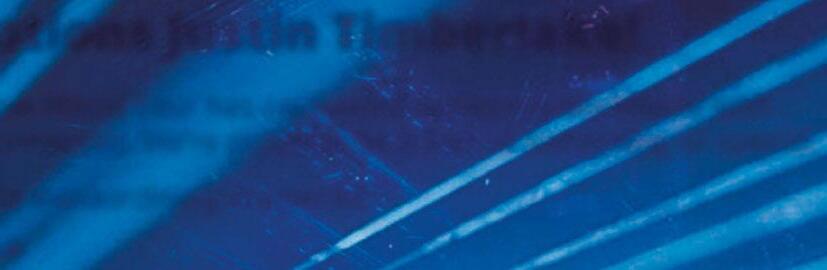
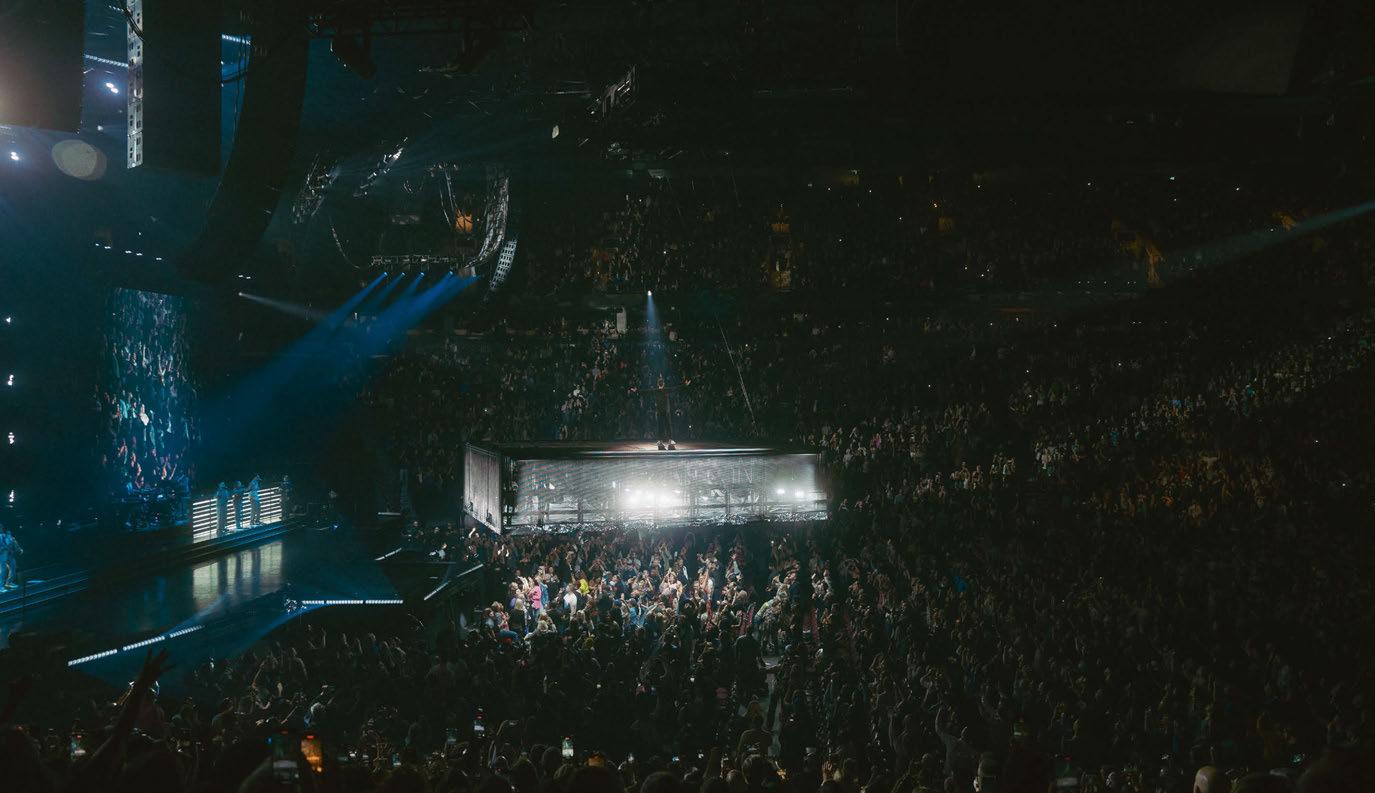
my job with the highest standards possible. My favourite moment of the show is the transition between Sanctified and Infinity Sex when the tracking screen opens, and the monolith comes in front of the audience. The perspective of the graphic effects and the movement of the monolith gives the audience an unforgettable visual moment.”
The show featured a variety of pre-recorded and pre-rendered content, using Unreal Engine to create virtual lighting – light data sACN captured during rehearsal and blended in the final render and live manipulated content using different Notch Blocks layers techniques in real-time. The video team built a scene within Unreal Engine of an underground, brutalist nightclub featuring virtual Claypaky Sharpyinspired lighting fixtures, tight beam lights, strobes and washes.
“We collaborated with the video team on where, realistically, the lights would be placed, how the light would emit from those fixtures and how it would look in a virtual world,” said Lighting Designer, Cory FitzGerald. “We were able to add hundreds of fixtures to the rig, purely digitally, adding depth to the show.”
The wider video team comprised: Crew Chief, Kimberly Hampton; LED Crew Chief, Reinder Vandersteene; Video Engineer, Briony Margetts; Camera Operator and Luna Remote Systems Technician, John Millman; Handheld Camera Operator and LED Technician, Jared Odom; Steadicam Operator and LED Technician, Zachary Rossi; Jib Operator and LED Technician, Jack Gurdon; Camera Operator and Projectionist, Olivier Tremblay.
“T his is one of the best tours I have worked on,” Alicea said. “The team makes everything way smoother and easy going.
Teamwork makes the journey more enjoyable and easier. The major challenge each day is accommodating our entire equipment despite space difficulties around the world and at the same time not compromising the safety of our team and the quality of the show.”
‘THE BEST IN THE BUSINESS’ “Baz and I don’t generally work on a lot of shows together, so this was a good opportunity to work together on a project from concept to creation, with integration with TAIT and Solotech,” Lighting Designer, Cory FitzGerald of Silent House stated. “Being involved from the ground upwards is integral in creating a creatively budgeted design, getting what we need out of the costs, and we can achieve our vision without having to sacrifice things, as we are part of the fund allocation process.”
FitzGerald started from scratch when it came to lighting design. “Lighting is an extension of his movement and the choreography on stage. We re-examined all the songs, old and new, on a song-by-song basis; refining the lighting design during the rehearsal process,” he said, adding that previsualisation was achieved using a variety of software –namely, Cinema4D, Rhinoceros, Vectorworks, Syncronorm Depence, and WYSIWYG.
Halpin and FitzGerald selected the “right fixtures for the right application” –typically, multifunctional fixtures that fit the requirements of good, fast and cheap. “We want to find the perfect mix; certain fixtures within the monolith had to be multifunctional, lightweight, and bright. Once we have quantities locked in, we work with weights, location, rigging, and pivot accordingly based on the density of our footprint with
automation,” FitzGerald explained. “We have received lots of complements about the ACME Pulsar S2 lights we used on the monolith. It is a super lightweight, fast, and bright fixture that has tonnes of functions for us to get a range of dynamic looks – it has all the bells and whistles required in a small package and is much brighter and more noticeable than I anticipated despite being buried between all the LED.”
CHAUVET COLORado PXL Curve 12s outlined the stage and lighting trusses. “Big shout out to CHAUVET for creating a unique tilt and zoom light – never have I had more compliments from every department on lighting fixtures. During the promo run we were able to travel with the first 16 in the US, and now they’re on some of the biggest tours on the planet,” FitzGerald said, extolling the virtues of the IP65-rated LED batten.
The wider rig also comprised CHAUVET Color STRIKE M; ACME PIXEL LINE IP; Robe MegaPointe, ESPRITE and iFORTE LTX, and Vari-Lite VL3600 lighting solutions, all which FitzGerald coined ‘reliable workhorse’ fixtures, controlled by an MA Lighting grandMA3 hardware on MA2 software.
“Given the synchronisation of visual and various automated, moving elements timecode backboned everything, we played on top of that, there are a handful of moments within the set which are triggered live,” FitzGerald said. “The MA2 software was great, and kept pace with all our changes, additions and swaps –connecting all the songs and transitions, huge swathes of data. We’re slowly transitioning to MA3, but it’s taking them a minute to compete with the speed in which we operate.”
The arrival of the monolith at the finale is the obvious watershed visual, however, FitzGerald
cited some additional moments during the Sexy Back section of the show, with a 3D scan of JT’s head captured in real-time, as well as the visuals for Summer Love, and the “epic” Cry Me A River as among his favourite looks.
“T he simplicity of the movement with the video encapsulates the emotion of the song with automation, as well as simple moments in FutureSex/LoveSounds with a up-light effect using Robert Juliat Dalias 864 footlights; those in addition to RobeSpots are instrumental for key lighting and finding ways to light Justin for camera that wasn’t just a white followspot in his eyes,” FitzGerald added. “It’s a cool show overall; the build and the dynamic sections of the songs are enjoyable. I’m not a fan of lots of video usually but this is the ideal balance of visual storytelling. This show wouldn’t be a success without Justin and Baz, creating, directing and driving the show. They helm the ship and it’s a pleasure to contribute.”
On t he topic of contributors, FitzGerald extended his gratitude to Lighting Programmers, Davey Martinez of Well Lit Productions and Lighting Programmer/ Director, Josh Beard of Sick Design. “During the
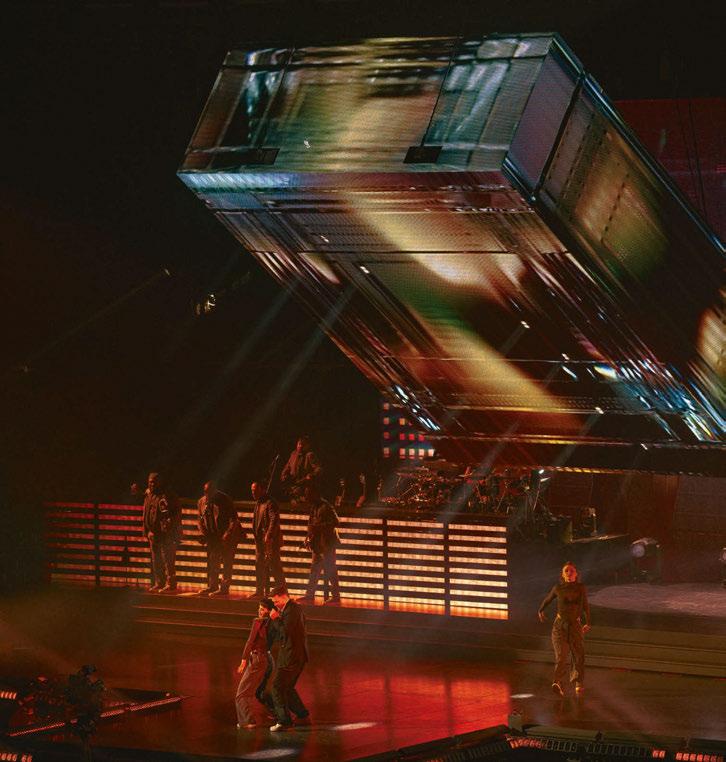
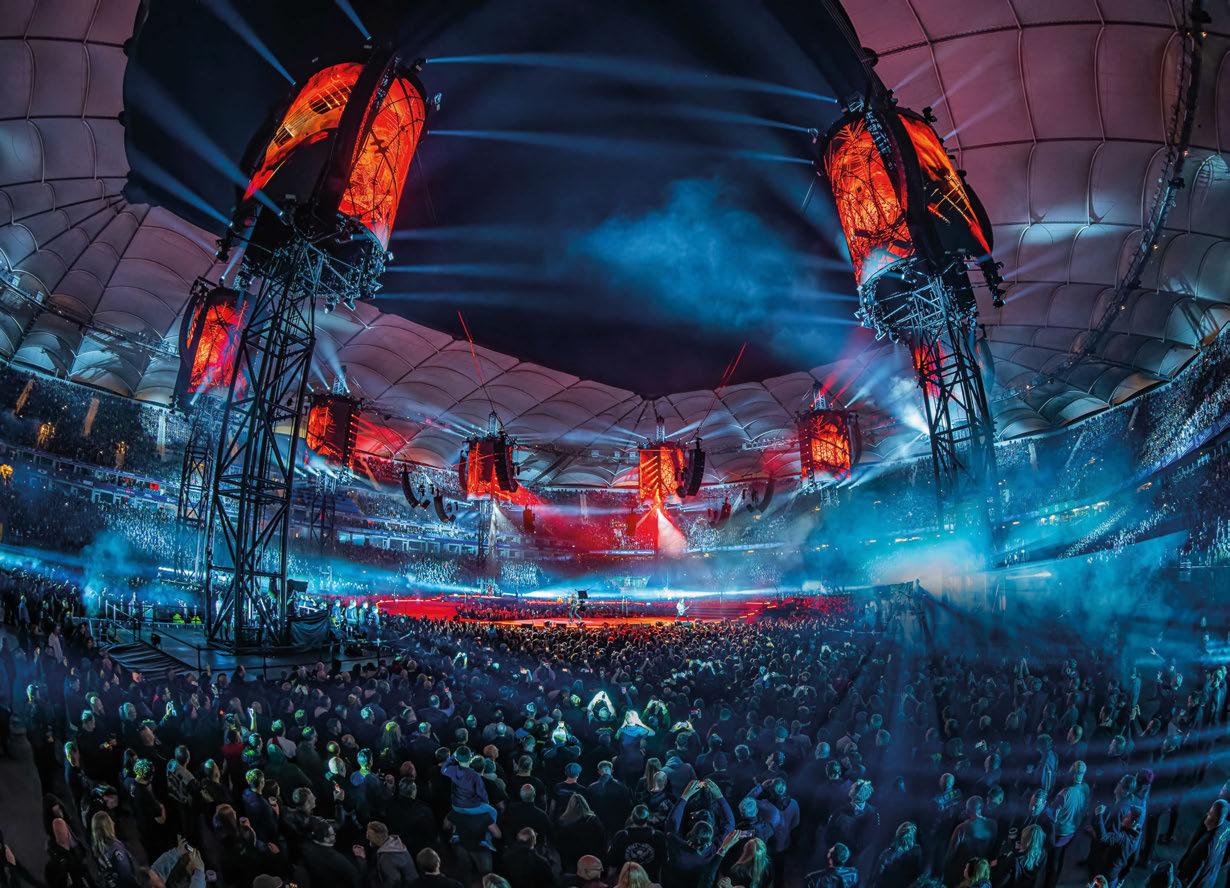

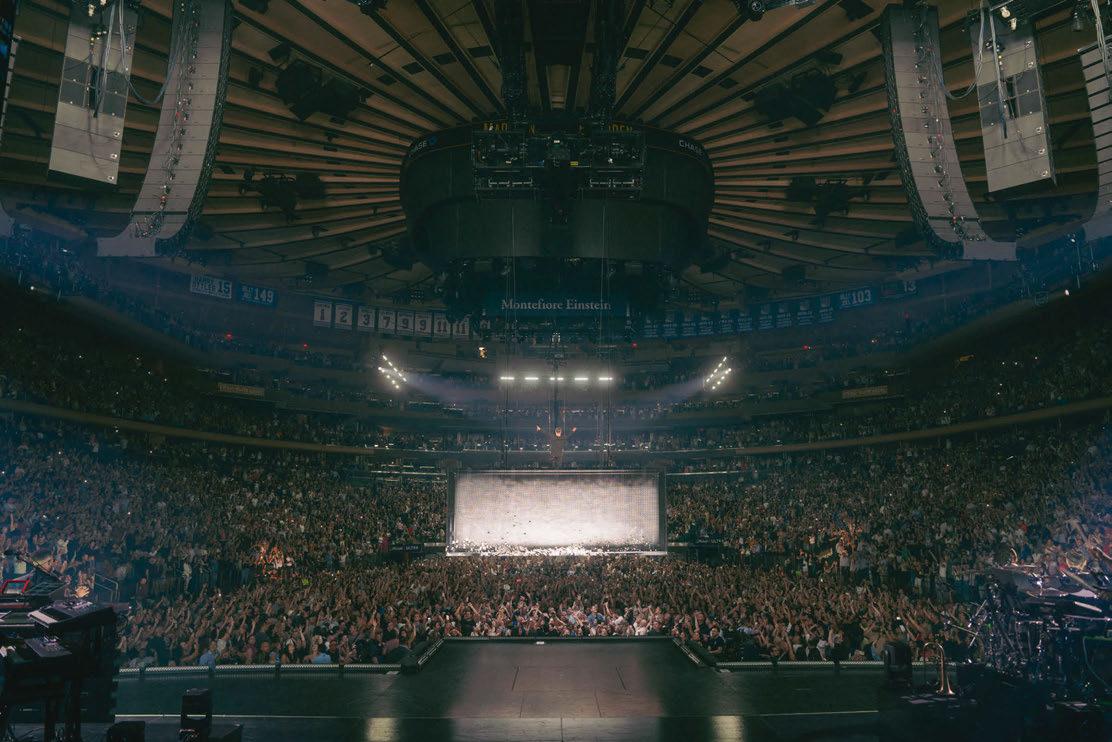
programming phase, no hit in the music went untouched,” Beard commented. “We spent weeks in previsualisation and rehearsal dialling things in,” he added.
“It is very impressive what Baz and Cory have come up with. We have found the right moments for video to pull back and let lighting take some hits. It is cool when a screen that size goes away for a moment, and you hit the crowd with something they weren’t expecting or didn’t know existed until that particular moment in the show.
“T here are also lots of moments where we are using screen and lighting at the same time and it’s just finding the balance of negative space in content versus what fixtures we are using where and when,” he continued. “You can find moments as well where we use the monolith to throw light or turning the screens off on the monolith and using the fixtures inside the monolith structure to show the depth and play with the crowd’s perspective.”
The team harnessed MA Lighting grandMA3 hardware – a main and a backup console at FOH – operating with MA2 software. A third desk was used for ‘ringing out’ the rig in the morning and remote focus on stage. A further 18 NPUs and 24 MA Nodes contributed to the vast MA Lighting network.
“I t ry to fit as much of the needed things into one show view, so I am not having to hop
around during the show. I like to minimise any distraction and things I don’t need during the show. I have plenty of views to get to things quickly if needed but I have a network / L2 at FOH if I am too busy to get to a fixture for resetting,” Beard explained.
Like FitzGerald, Beard spoke candidly about CHAUVET COLORado PXL Curve 12s. “It is an interesting fixture when you can get enough of them in a line. It provides lots of options of programming cool unique looks. Davey did a fantastic job in making some beautiful looks,” he said, citing Cry Me A River as a personal highlight of the show.
“T he PXL Curves played a huge role in bending light in a way that really captured the song. On the flip side, I think the most beautiful look in the show is the simplicity of Technicolor It starts as just back light from a couple of spots and a hint of side key with this beautiful black and white treatment on IMAG. The song then changes tempo and the PXL Curves come to life in this tasteful rainbow.”
The wider lighting team featured: Lighting Crew Chief, Corey Tom; Lighting Technicians, Scott Amiro, Cedric Vermette, Kevin Chan, Natasha Shaw and Natalie Oxenham as well as Network/FOH Lighting, Callum Humphries.
“It is a dream job to be able to work with Cory, Baz and the Silent House team. You can’t help but push yourself to operate at your best
when with them. These are people I’ve read about as a young programmer and designer,” Beard enthused. “I’m thankful to get to see how they work. They’re the best in the business.”
‘THAT YEAH MAN! FEELING’
“If I were to describe my mixing style, I would say it’s a ‘trust your ear’ approach,” FOH Engineer, James ‘Jaymz’ Hardy-Martin III said. “Outside of the console and reverb unit selection, I do not go into any situation with a preset EQ, compressor, or plug-in that I am absolutely going to use. I listen to the source in person, listen to it through the PA, then adjust what I think is needed to properly translate the music to the audience,” he articulated.
The ‘membrane’ of Jaymz’ mix is a DiGiCo 338 console. “DiGiCo is my first selection when it comes to consoles. I am more than capable of working on anything with a channel strip, but I prefer the DiGiCo because their desks have never limited me. Snapshots are crucial to the mix. What a snapshot allows me to do is preset EQs, FXs, pans, volume levels, delay times, etc. for specific songs and specific points within songs,” he explained.
“For example, the song My Love has an intro where I use huge verbs and delays. Once the song starts, I need to change the verb, the delay, and the levels of multiple instruments. Utilising the snapshot feature, I can preset

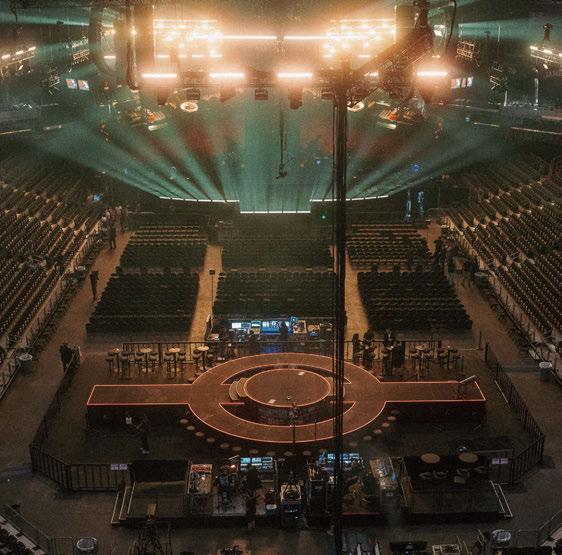

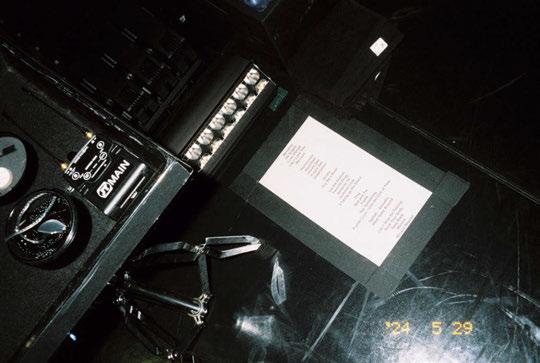
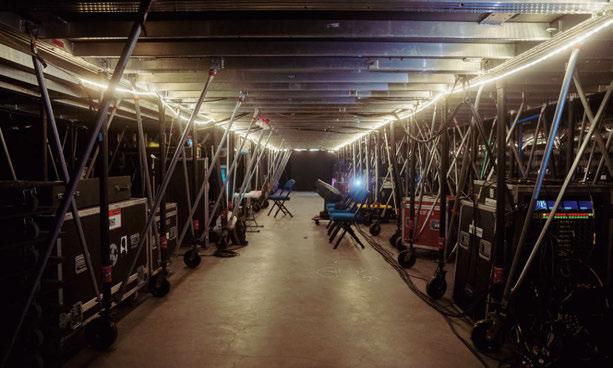
these settings and with one push of a button, all the changes I need happen.
Jaymz’ outboard rig included two Bricasti units – one for drums and another for vocals in addition to a Waves server for vocal effects. “I am using the PSE to help avoid feedback and keep the overall noise floor down. With 10 wireless microphones on stage, it could be a huge challenge obtaining a clean mix without the PSEs,” he reported.
The drum kit featured an array of Shure and Sennheiser microphones. “I’m not about all one brand because one brand doesn’t make the best overhead microphone and best kick drum microphone. Whatever sounds good and translates best is what I use. This can change from gig to gig. Currently, all the vocalists are on Shure SM58s,” Jaymz said.
The wider audio team featured Monitor Engineer, Jon Kooren; Pro Tools Playback Engineer, Danny Cheung; Audio Crew Chief and FOH Technician, Hilario ‘H’ Gonzalez; Monitor Technician, Nicholas Stover; PA Technicians, Adam Harris and Francis Lussier; Audio Technician, Mathieu Levesque.
“T his is my first time working with Solotech. It has been nothing less than great,” he added. “We are using an L-Acoustics line array and the team have been supportive. Being new to the gig, I rolled with what was provided.”
Jaymz cited Sexy Back as among his favourite moments of the set. “When we get to this point in the show and it has all gone smoothly, it’s a good feeling of a job well done
and the song slaps! JT has an awesome band, who know how to play the record.
“JT is a nice person who speaks to everyone and makes the environment comfortable when he is around. All personnel are pleasant to see on a daily. The management is professional, respectful, and shows their gratitude. These small but large things make the time away from home easier to cope.”
Having mixed studio and live for decades, Jaymz believes there is nothing outside of losing all power that prevents him from getting the job done, monolith or not. “The end-ofshow gag is not an issue because even though JT is in front of the PA, he is high in the sky. The boxes closest to him shoot much further out to the seats behind FOH up in the stands,” he commented. “It feels good when the first piece of low-end hits during Memphis at the top the show,” he added. “You have the crowd screaming with the band, lights and video on point. It feels good because all the logistical travel and preparation pay off in that moment and I get that ‘yeah man!’ feeling.”
The wider core The Forget Tomorrow World Tour team featured Tour Electrician, Paul Sadler; Backstage Coordinator, Amy Mills; Assistant Backstage Coordinator, Danny Carbajal; Head Rigger, Willy Williams; Riggers, Shawn Gibson, Simon MackwaynePagani and Terran Fernandez; Backline Crew Chief, Keyboard and Horn Technician, Okwa Amalemba; Guitar Technicians, Evan Bovee and Alfonso Urena Perez; Drum Technician,
Samuel Martin; Touring Director, Andre Person; Tour Manager, Dan Mcgee; Executive Assistant, Katherine Gallagher; Road Manager, Bianca ‘Bonkas’ Acosta; Tour Accountant, Kane Mcgee; as well as Ticketing and VIP Liaison, Brian Samuelson.
Gi ven the demand of the tour’s complex build, and conscious of overloading crew numbers , Larson underlined the importance of crew welfare and offsetting long working hours with redundancy in core departments – namely, Production Coordinators, Christine ‘Mama C’ Mullin, Malissa Harris and Brande Jackson as well as Stage Manager, Robert Hagedorn and Assistant Stage Manager, Charles ‘Chaz’ Phillips.
“T he wellness of our crew is important to us, so we try and focus on how we can prioritise health and rest by adding redundancy in some roles. I’m lucky enough to have multiple production coordinators and stage managers on this run, which allows one to rest in the morning, while the other rests at night, with split shifts,” he said, earnestly. “Thankfully, long gone are the 20-hour days. We are also seeing dividends – when we support our people better, we can provide a much better product.”
www.justintimberlake.com www.silent-house.com www.solotech.com www.taittowers.com www.eps.net www.trucknroll.com www.cuepilot.com

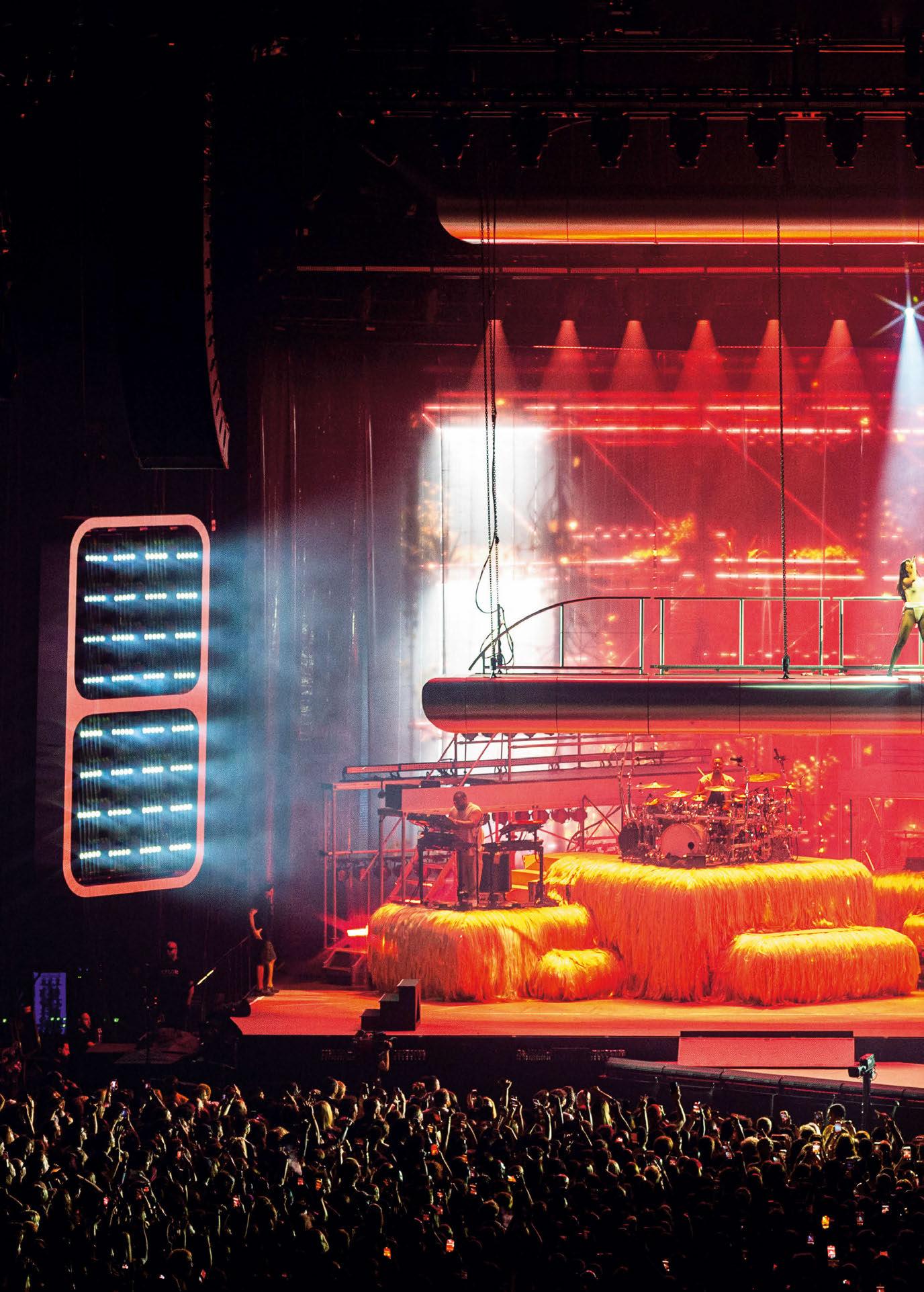
DOJA CAT: THE SCARLET TOUR
Automated bridges, hairy risers and microphone stands, plastic-coated LED screens, pyrotechnics, lasers and special effects aplenty make for a touring production like no other…

Words: Jacob Waite
Photos: Joe Okpako

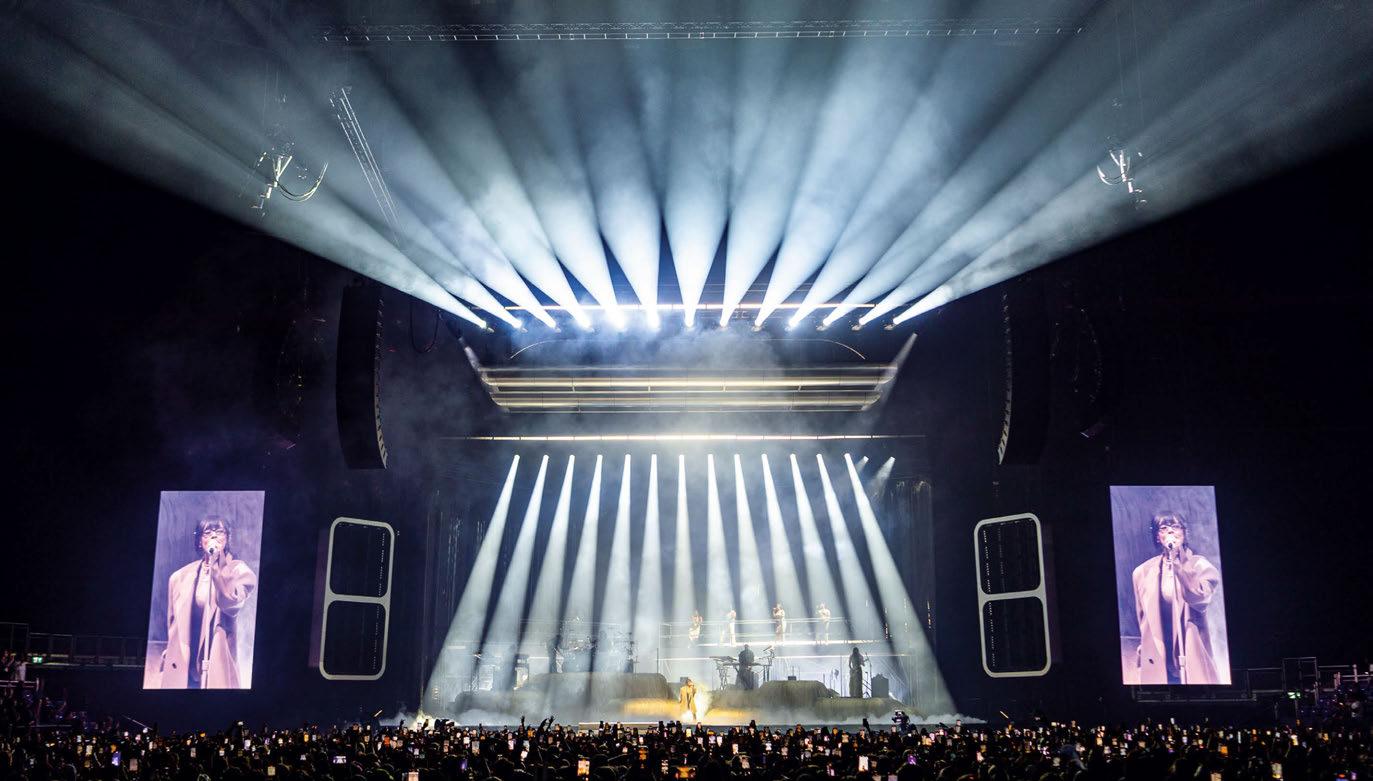
With previous production design iterations featuring everything from giant sprawling arachnids to roadie-powered dinosaur skeletons, hair monsters and a mud bath, Doja Cat’s long-awaited tour of UK and European arenas promised an unparalleled experience.
Following a successful, albeit typically rainy Mancunian festival welcome to the UK by way of Parklife, TPi tracked down the team behind the scenes during the second of two sold-out shows at London’s O2 arena to discover the innerworkings of the 18-truck tour.
“T his show is more of a representation of Coachella, with a bit more changing and adding of creative and technical elements along the way,” Production Manager, Aaron Draude began.
The tour’s vendors of choice included: BPM SFX and Image SFX (special effects and lasers), Brooklyn Sound and Glen Canyon Audio (playback), Dark Matter (media servers), Fly By Nite (logistics and rehearsals), Freight Minds (freighting), PRG (lighting, rigging and video), Sound Image – a Clair Global brand (audio), and TAIT (automation and staging).
“T hese are all companies I’ve worked with before and they provide great service and are aware of how to operate at this level on this continent,” Draude said, further highlighting the pressure points of this project.
“Bouncing from festivals to arenas is our biggest challenge on this run in addition to managing the time it takes to get equipment from one place to another. We sent a lot of gear to mainland Europe in advance, which subsequently travelled to the UK to be assembled at FBN Studios.”
Freight Minds Managing Director, Joseph Pacheco; Vice President Operations, Beverly
Aguiling and an additional team of ground staff oversaw the delivery of 20 airline pallets of equipment, shipped at different times for cost efficiency. Pacheco picked up the story: “This is the first time that much of the kit had been put on a flight, which meant that several of the pieces had to be reconfigured and arranged to fit in the aircraft. However, after some Tetris and extensive planning by our experienced team, it’s been smooth sailing since,” he reported. “We thank Aaron and the production team for their faith in us to deliver for the tour.”
Tour Manager, Tony Marino; Road and Tour Manager Assistant, Megan Rudd; Road Manager Assistant, Ali Hardaway; Production Coordinator, Cara ‘CJ’ McDaniel; PA, Tricia Engelbert; Venue Security Head, Simon Singh; Venue Security 2nd, Floyd Dahonick; and Tour Accountant, Jen Altermatt supported Draude with the daily operations.
“We wanted to showcase parts of the Coachella set in Europe. One large element that we changed was touring with a small choir instead of a spread of dancers, showcasing how much of a powerful performer Doja Cat is,” Marino commented. “Aaron and I have been working together for seven years, we understand each others workflows and have assembled a great team, which is the key to successful touring.”
BOH Coordinator, Sarin Moddle handled room allocations, offices, dressing rooms, and creating an atmosphere of general comfort for everyone living and working on the road. “It’s important to acknowledge that we don’t just create a home from home for the people on stage, but also for the crew. I like to provide people with the conditions they need to do their
best work. I also trust the process of delegation to the local crew and, like any department, having a strong relationship with the locals is very important,” Moddle said.
“We have a crew welfare hub that has everything you would need on a day-today basis as well as a touring nurse. I’m a big advocate of providing each room with warm adjustable lighting – the crew rooms are nap rooms for a lot of people, so having comfortable couches is also important. In terms of performers’ spaces, plants are essential in changing the entire tone of a space as well as soft, plush things.”
‘RIGGERS ARE AT A PREMIUM’
Head Rigger, Clay Hutson and Rigger, Ashlee Veghte were responsible for close to 100 points in each venue. “There is a lot of rigging involved given the sheer amount of automation and the fact that we’re switching from varying heights from venue to venue,” Hutson said. “The riggers in the UK have been fantastic. We’re typically done within two-and-a-half hours on a bad day.” Safety, of course, was paramount. “We conform to UK and EU standards, and everything is at least D8+ or C1-rated. The automated platforms weight in at 25,000lbs so that means a lot of weight in a concentrated area, which is a logistical challenge in addition to trim heights in venues like Birmingham’s Resorts World Arena and Newcastle’s Utilita Arena.”
The entire rig is weighed and analysed using Broadweigh load cell monitoring systems. “We have active load cell monitoring on the video wall and the grid. I think load cell monitoring should be commonplace on every gig,” he underlined. “After all, you can put tapes on any
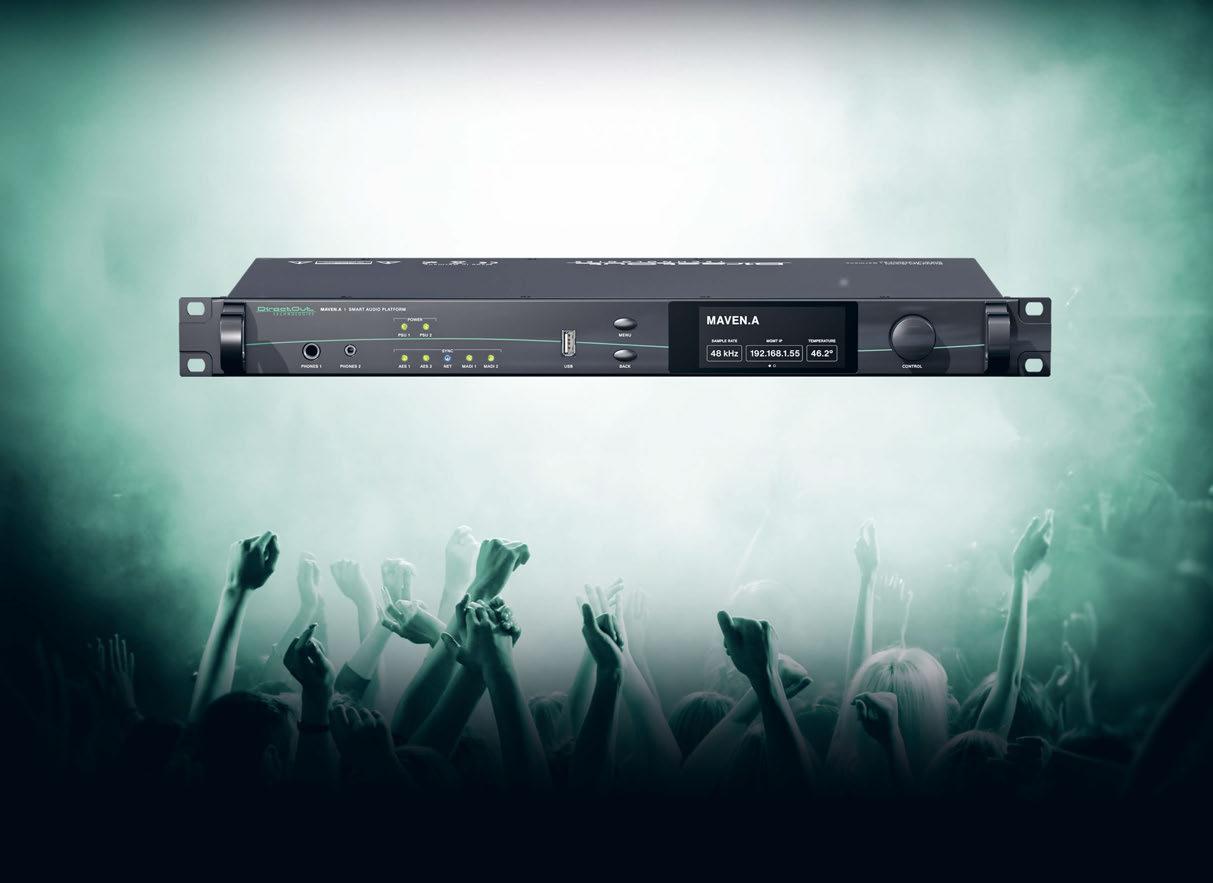

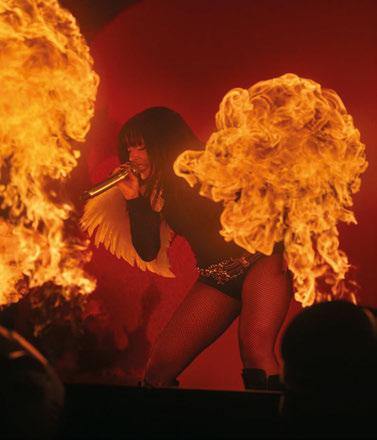
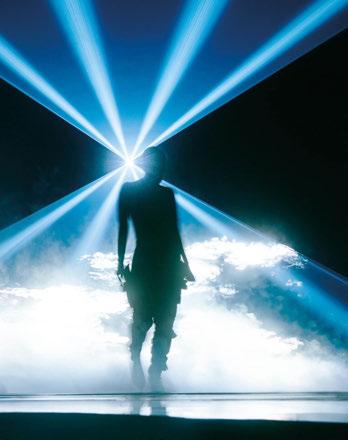
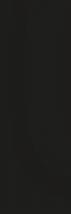
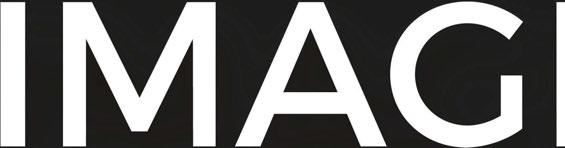
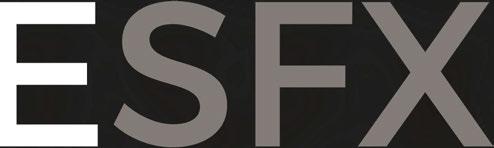

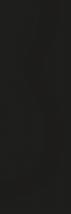
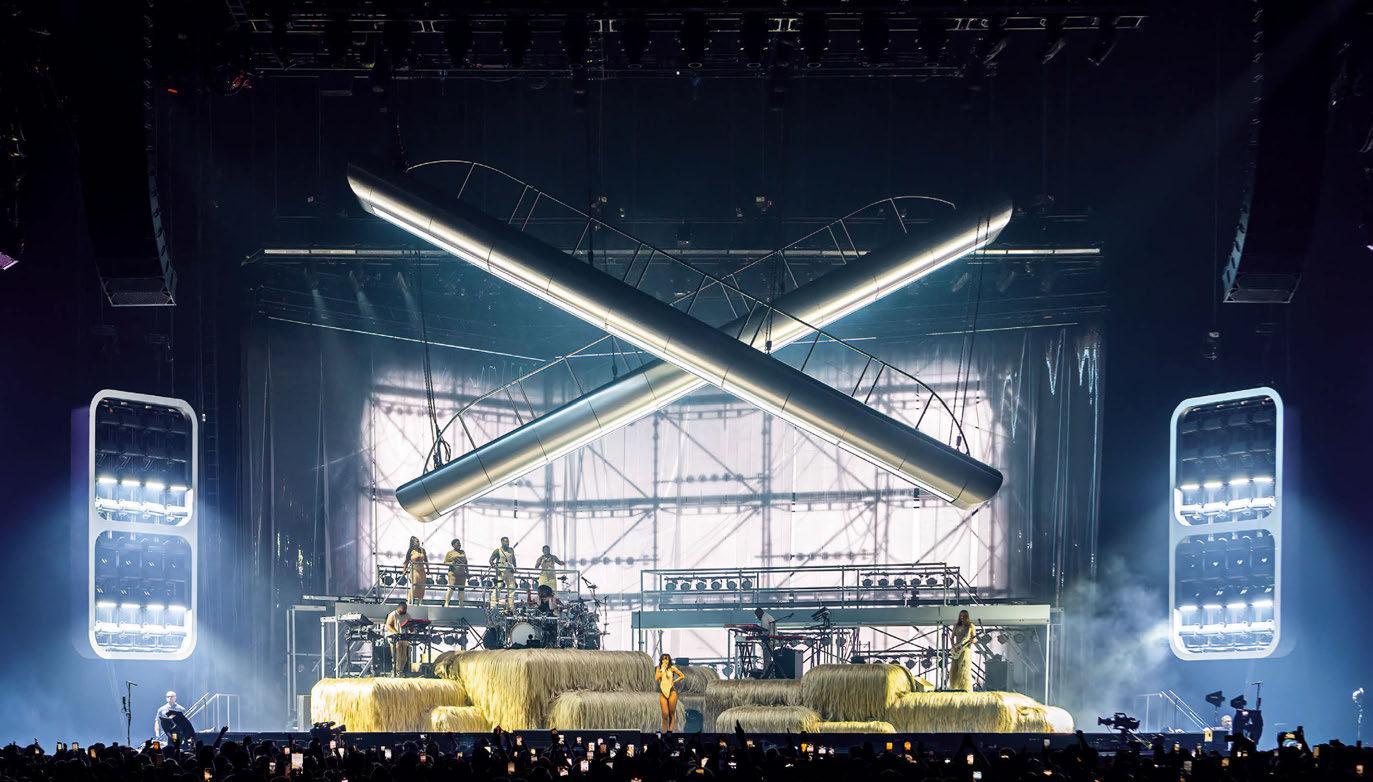
piece of truss and it looks perfectly level, but when you look at the load cell data, they tell you a very different story.”
Embarking on his 35th year as a touring rigger, Hutson was keen to encourage a new generation to take up the harnesses. “Our industry is really struggling with the influx of new people and the exodus of the ‘old timers’ post-pandemic. We are lacking the mentorship that used to be there and the training protocols to get people up to speed.
“The UK has been fantastic, however, shortstaffed because of the larger stadium shows currently on the road in addition to festival season,” he stated, earnestly. “Riggers are at a premium. I got into rigging during my freshman year in college and I haven’t looked back since... It’s what I love to do.”
Once the gear was rigged, the stage was eventually rolled into place. “We haven’t really stopped since Coachella,” said Stage Manager, Jack Dunnett of Backroom Limited, reflecting on a whirlwind year. “Learning three different shows with lots of differing stage cues has been challenging, however out of the three designs, this is the easiest for me.”
Using local crew chiefs as assistants in each venue, Dunnett typically arrived on site alongside Draude, Hutson and Veghte at 7am to mark out.
“I walk around with the promoter to find six trucks’ worth of storage around the building, which hasn’t been too bad. Today was the fastest we’ve ever assembled the show – we pushed the stage at 12.30pm, around five hours after loading in,” Dunnett stated proudly, citing the challenges he and Head Carpenter, Matthew Sperling and Carpenters, William
Cando, Jonathan Klose, Joshua Farrant and Josh Brooks faced.
“The fascia on the lighting pods is slightly heavier than expected, but we’ve managed to overcome that,” he added. “The biggest challenge, once the stage is pushed into place, is lining up sound check with a pyro and laser test within a tight time frame, while ensuring everyone’s expectations are met.” Backroom Limited also provided transformers for the pyro and automation. Summing up his experience, Dunnett said: “Doja Cat’s friendly, very funny and one of the nicest artists I’ve ever worked for... I’ve loved working with all the crew and suppliers on this tour.”
‘DYNAMIC MOTION’
In the air, 16 Kinesys APEX 1250 variable speed hoists suspended two platforms, eight per platform, paired into groups. “Around 90% of the moves in this show are on flat platforms, up and down, but the big opening sequence when everyone sees the platforms, they form a giant floating ‘X’ above everyone’s head on stage,” explained TAIT Automation Operator, Kiel Heerding. “We also have a single prop winch hidden in the rig, which is used for Demons and pulls up a hair braid that Doja Cat uses as a microphone stand and dances around with.”
All this, of course, was achieved using a TAIT Navigator system. “We have a standard complement of NAV:RS4 running all the safety control and the NAV:Polaris as our main console with NAV:Compass as our back-up console and main load-in console,” Heerding said, walking through his rig.
Automation was triggered in almost every song. “Each song has its own vibe,” Heerding
said, citing the evolution of automation in the sector. “Dynamic motion is becoming a big trend now, and we are seeing a lot more automation that moves continuously throughout the course of a show, with designers bringing dynamic looks to the stage instead of static looks per song. Paint The Town Red is a perfect example of this, as the automated bridges move up and down for the entire song, bouncing between looks to create different perspectives as the song progresses. Seeing her slowly rise behind the flame wall during Streets is one of my favourite moments.”
During the show, four choir members ride the platforms for a series of songs, with Doja Cat spending the closing segment of the setlist performing from the air. “For most of those songs, they’re moving up and down constantly,” Heerding reported. “We’ve been fortunate that most of the arenas we’ve visited have been able to achieve the creative vision. There was just one show at Birmingham’s Resorts World Arena, which we had to create a scaled-down show for due to it being 10ft lower on trim height. We still maintained the artistic vision and provide a dynamic show.”
Cr ucially, before hitting the road, TAIT performs a full hazard analysis on the equipment. “The NAV hoists that move throughout the show are C1 rated, which gives a 10:1 safety rating everywhere and meets the standards, specifically for Italy and France. We also have a full rescue team with us and a rescue kit with a rehearsed rescue plan. If the artist was to get stuck in the air for example, we have multiple avenues we could employ to recover her during the show or bring her down by hoists. If power were to go out in the entire

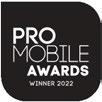
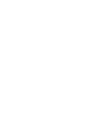
Intuitive layout inspired by music gear
• Up to 4 DMX universes
Reliable stand alone hardware • Color, Move, Beam and Flash FX
Music sync with mic and line in • 20 000 available fixtures
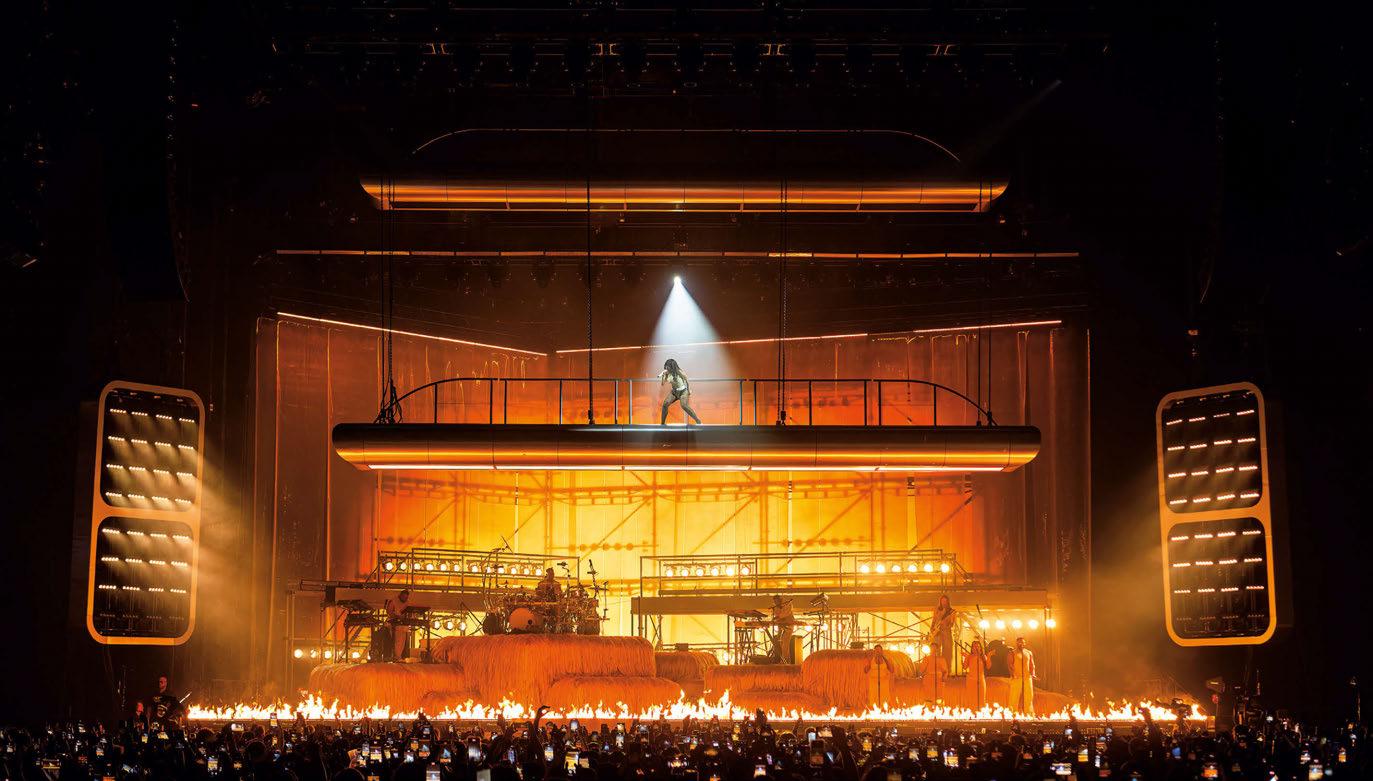
venue, we can also pick her off and lower her down safely,” Heerding added.
The wider automation team featured Automation Crew Chief, Benjamin Aaron Schiffer; Automation (Performer Flying Lead), Michael Gutierrez and Automation Technician, Darko Baez Paunovic. “Our team is equipped and staffed in such a way that we have a rescue plan for any scenario,” Heerding remarked.
While riding the automated bridges, the performers are in a fault-restraint, wearing a waistbelt which is tethered to prevent them from getting too close to the edge of the platform. “We physically clip them in and inspect them before any motion occurs. The performers have all gone through training seminars with TAIT to ensure they are comfortable performing at height. We validate the flight every day before they get on to inform them of any changes in speed and height, based on the venue,” Heerding reported.
‘CLEAN AND POWERFUL LOOKS’
“On each side of the stage, we have what we call our flown lighting ‘pods’, which are filled with ACME Lighting Geminis. They are our ‘special’ fixture of the show with LED on one side and white strips on the other. It’s the first time I have used them, and they look great and add a lot of depth and impact to the show,” commented Lighting Director, Anna Merritt.
“During the track, Rules, we use a certain effect on the Geminis and the ROE Visual LED CB8 LED panels underneath the bridge, which match seamlessly with the on-stage scaffolding to create this industrial vibe.”
Underneath all the hairy risers, upstage and
downstage truss were a complement of TMB Solaris Flares. ROE Visual CB8 LED panels were fixed under each of the automated bridges and run on full capacity to simulate industrial lighting. A clear, plastic tarpaulin-like material was draped over the back wall of video to extend the industrial aesthetic with Chroma-Q Color Force 72s lighting the way. Further VariLite 3600 fixtures were chosen as spots with vintage incandescent parcan lights providing a “retro, grungy” feel to proceedings.
The video content tied into idea of set extension, with virtual lights created to add depth to the lighting rig. “The video content extends the set and complements the lighting,” Merritt said, praising the vision of Lighting Designer, Parker Genoway of Silent House. “He is a lot different to other designers I’ve worked with. His looks are very clean and powerful, which makes for a beautiful and dynamic show.”
Merritt used Syncronorm Depence R3 for previsualisation and Vectorworks for all rigging plots. The LD operated the show using an MA Lighting grandMA3 console in MA3 mode. “I regularly update presets, making sure the overall look is locked in and aligns with the programming,” she said, citing some of her favourite looks. “We have a lot of low fog moments. Tia Tamera goes hard with the fire, which is sick. Lighting-wise, I also love Attention, which is a beautiful song and Streets, which is a very hot song to say the least.”
With four band members, four choir members and an energetic Doja Cat on stage, Merritt employed a Robe followspot system to track the action. The wider lighting crew featured Lighting Director, Mark Humphrey,
Lighting Crew Chief, Jamie Gorman and Lighting Technicians, James Tomlinson, Tim Saunders, Stevie Carty and Keira Clark. “PRG’s kit, crew and support has been great. It’s been a great run and I’m proud to be a part of it.”
‘AN
INDUSTRIAL LANDSCAPE’
The upstage screen and IMAG screens were made up of INFiLED AR 4.6mm LED panels running on NovaStar COEX processing. The plastic material, sprayed with a gradient to match the industrial and brutalist-inspired content, was used to diffuse the hard edges of the screen and provide a warehouse feel.
“T he video content extends this industrial and brutalist landscape,” said Media Server Operator, Eduardo ‘Eddy’ Dominicci of Dark Matter – who manned an active and back-up Disguise GX 3 media server setups to drive the prearranged content.
From FOH, Merrit was able to control the content and colours of the ROE Visual LED panels on the bridges via sACN provided by Disguise media servers.
“T imecode is crucial to synchronise the visuals and replicate a set extension of the lighting fixtures on the stage,” Eddy explained, citing the influence of Media Server Programmer, Adam Fontana of Dark Matter. “The closing song, Wet Vagina, in combination with the fireworks and pyrotechnics, is an impactful moment and a great crescendo for the show.”
Ensuring the action was captured, the camera package included two long lens cameras – one situated at FOH and another at the half arena position – a Furio head supplied
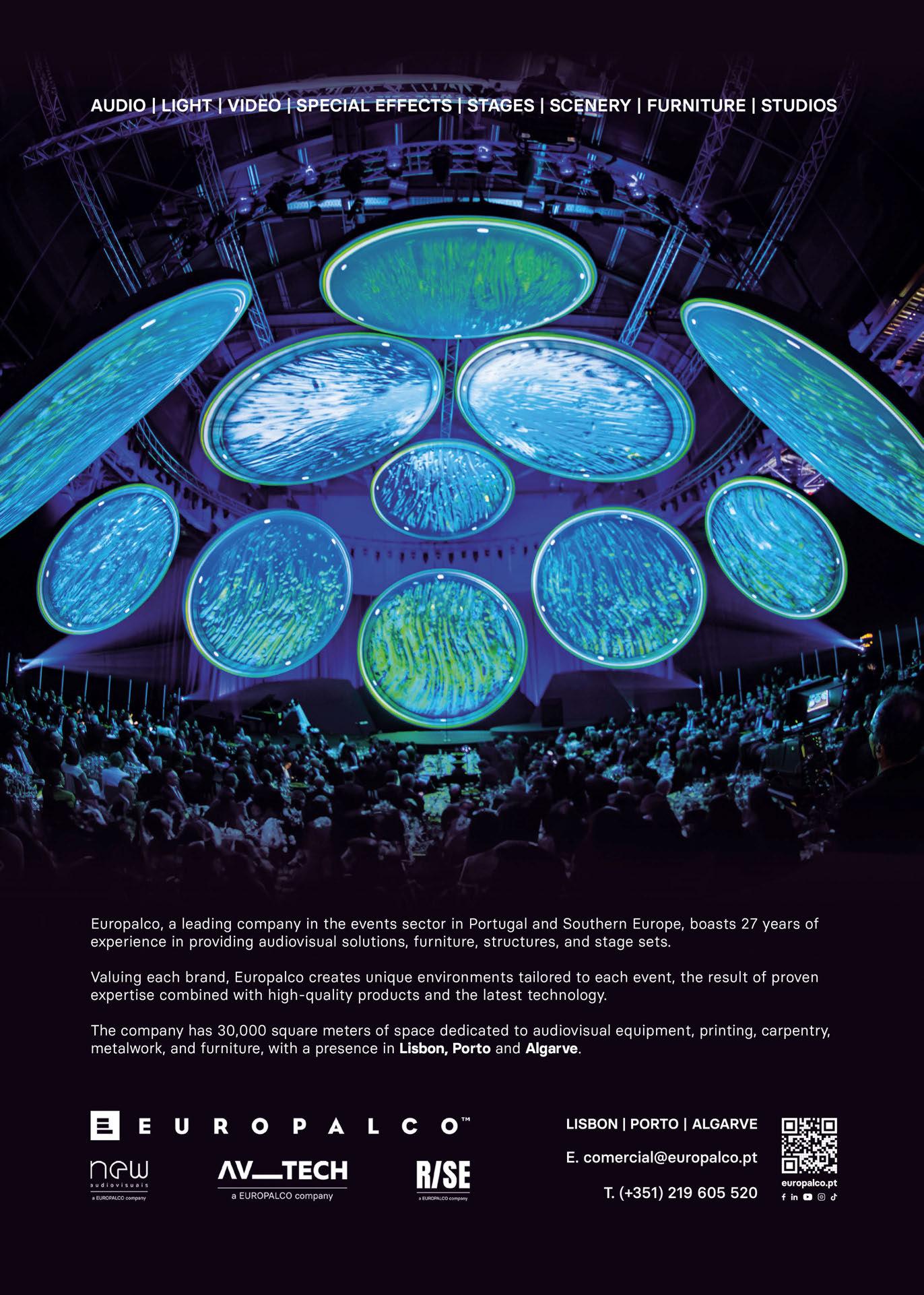

by Luna Remote Systems down the side of the angled thrust, a manned track dolly on stage left and a handheld camera on stage right.
There were also three PTZ cameras – one at the end of the thrust, one on stage and one on the follow spot truss to get an overhead shot – as well as a handheld RF camera used for a couple of key moments on stage. With a clean IMAG feed, there was an increased focus on direction of the cameras. Video Director, Jon Stutsman harnessed a Grass Valley Kerrera video switcher to select shots. “I’m a big fan of IMAG as image magnification to help enhance the artist for those at the back of the room,” Video Crew Chief, Jackson Warner said. “The placement and implementation of cameras in live touring is now getting more sophisticated, like adding the ‘slash’ camera and having a track and dolly instead of the handhelds.”
“W ith PTZ cameras, you can add a layer of intimacy and put them in places to get angles you would never be able to achieve on a handheld. For example, our camera seven gives us an overhead shot of when she walks down the thrust, lies down on the stage and pulls some shapes and contorts her body. We can add enhanced viewpoints and provide varying perspective to the crowd on the IMAGs, rather than having a hairy roadie running round on the stage,” added Video Engineer, Jon Priest.
“T his is our fifth show, so she’s playing with the cameras a lot more... To sell out one night here on your first EU/UK tour, and then come
back and do it again within a matter of days is a massive achievement.”
The wider video team featured LED Technicians, David Novak, Robert Daw, William Whitehead, Julie Mriouah and Steve Jones as well as Furio Operator, Tom Kelly.
‘250 PIECES OF PYRO PRODUCT’
“We are shooting over 250 pieces of pyrotechnic product, which means a lot of connections and six hours of loading boards. As the Fire Screens are on the effects tray, we’ve only got a couple of inches of space, so it’s taken some care to make sure everything is in its place and taken care of properly,” said SFX Operator, Joey Herring. “Pyrotechnics, lasers and automation kicks off the show. Special effects are featured throughout –our only low moment is running low fog for around 20 minutes. Wet Vagina is bonkers, with pyrotechnics and fire the whole time. It’s wonderful overall design by Nick Arnold!”
Laser and SFX Designer and Programmer, Nick Arnold of Image SFX, highlighted some of his favourite looks – from the teasing and interstitial pyrotechnics of What You Mean the long chases of slow burning flames of Tia Tamera and Streets intertwined with pyrotechnic chases through to the all-out, high-octane Wet Vagina
“I had a lot of fun programming this show. Streets is also a sexy, long-term burn look which is something you don’t often get away
with because of the duration of the flame,” he explained, citing the widespread usage of 25 Image SFX-engineered Fire Screens – 15 on the downstage edge and 10 on the upstage edge – to achieve these moments. “They are versatile, quick response and super fun to use because you can get a lot of different looks.”
The special effects package included four G Flame units and three LSGs, six lasers and additional fans to keep the air on the stage moving given the heat of the flames. “We are running an MA Lighting grandMA3 for master effects control,” Herring explained. “We output DMX to the flame systems, and network DMX to the laser system, which uses Pangolin BEYOND software. Our Galaxis pyro controller is also hardwired into the back of the console.”
In addition to flames and CO2, Arnold cited the “amber colour world” of the laser-laden track, Need to Know and laser-heavy Agora Hills as key moments. “Doja Cat is great at interacting with and framing herself between the pyro, lasers and special effects,” he said.
A high level of health and safety is standard operating procedure. “We have spotters everywhere; my line of sight allows me to watch her perform and see where she is on the stage in relation to any danger zones. With respect to automation, there are points in the set where we must dim the lasers as the bridges pass through the laser plane, to avoid any reflections and diffractions,” Herring added, noting the support of BPM SFX in the UK and Europe. The
PROFESSIONAL
CONTOUR X CX 210 LT
THE UNCOMPROMISING LONG THROW SYSTEM
The
compact point source for really big
sound..
• Impressive sound level, enormous throw by HK Audio MCT
• Perfectly matched Lab.Gruppen and Powersoft filter sets for arrays of 1 to 4 speakers
• Passive 24 db/oct. crossover - fewer power amp channels, more flexibility
• Linear phase FIR and IRR filters for latencycritical applications
• ICF - integrated single-point flying mechanics for single speakers and arrays
• Robust design for the daily use on the road „Made in Germany“
The perfect addition to the CONCERT SOUND CONTOUR X and COSMO series

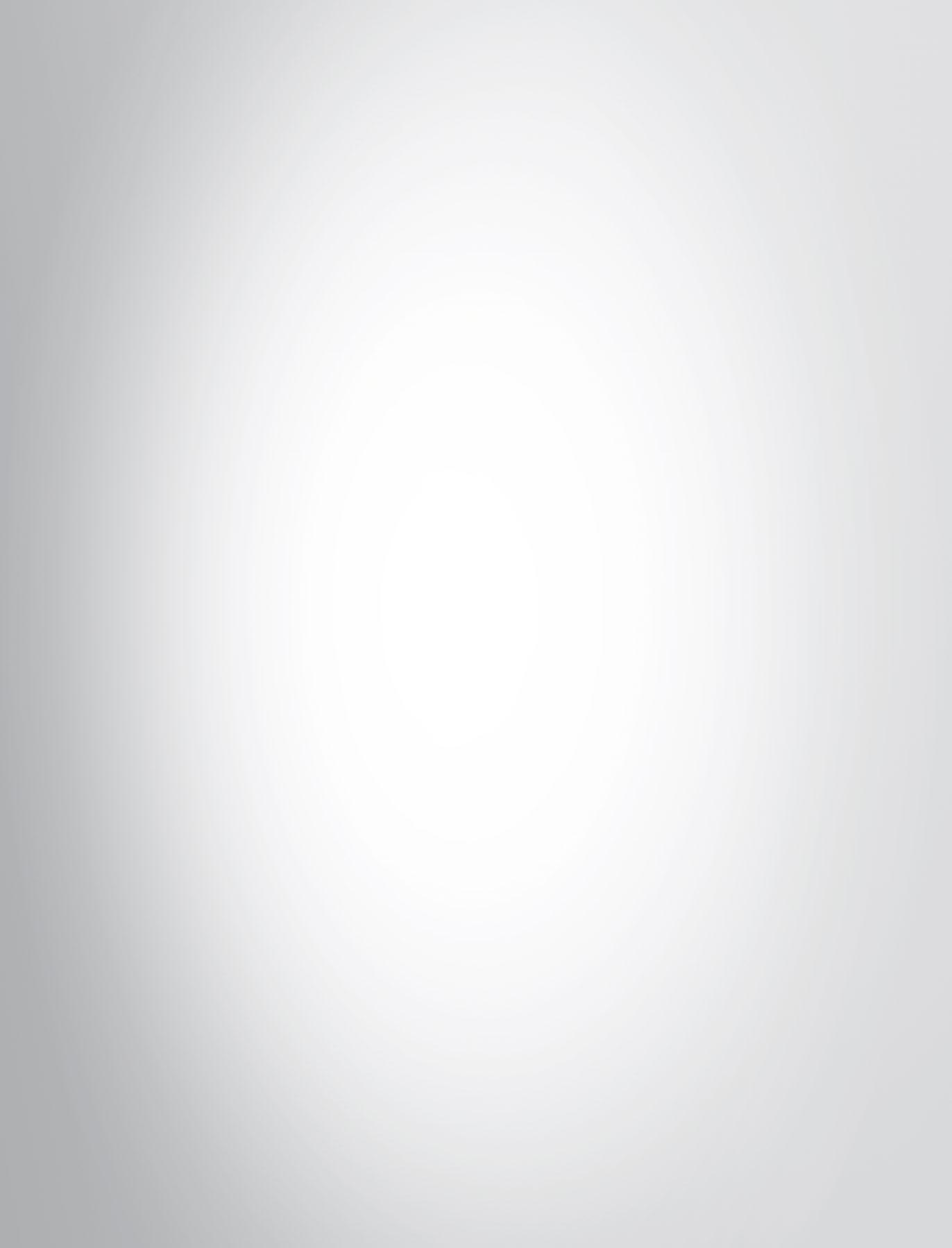

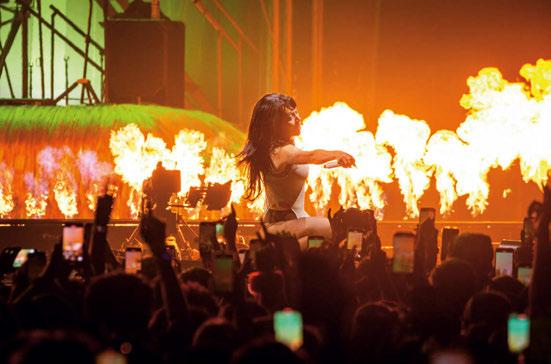

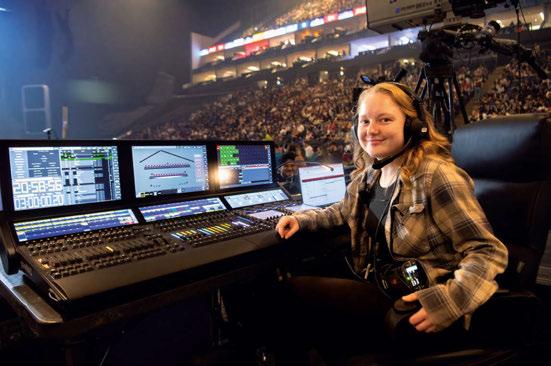
wider special effects and lasers team featured SFX Crew Chief, Tyler Scott; SPX Technician, Brandon Messersmith; SPX, Ehlana Godfrey; Laser Technician, Brian Andrews; Rehearsal Laser Technician, Will Brown.
“We are lucky to have a production team that understands special effects and the compliance requirements, they make the show a reality,” Arnold concluded.
‘MIXING WITH THE EARS’ FOH Engineer, Migui Maloles of Never Sleep Productions mixed on a DiGiCo Q852 console provided by audio vendor Sound Image, a Clair Global brand. “I’m loving the console so far,” he reported. “One of the coolest things about it is the visibility of everything and the way I can adapt the layouts to suit my workflow, having a master section for my matrix, group and aux outputs all easily accessible in one location on the board.”
Maloles described how he never leaves his VCAs “because I’m always riding those as I feel the sound coming out of the PA in the centre section, and my input channels are all on the left and right banks”.
He added: “Everything is available at my fingertips and there is a tonne of macros, so programming and customising it to our individual workflows makes us much more efficient. I also have a redundant console, a Quantum 5, firing snapshots on MIDI in case the Q852 goes down for any reason, I can
switch over and unmute the master and we’re off to the races.”
Preferring to keep everything within the console, Maloles’ only supplemented outboard gear came in the shape of a Universal Audio UAD-2 Live Rack for reverberation. “I love how everything sounds on the 825. The processing is awesome, and the way [Systems Engineer and Audio Crew Chief] Leon Fink has tuned the rig every day makes it easier for me to hear small, incremental differences of 0.5 dB on EQ, which is helpful. He is a brilliant systems engineer, so we have been collaborating to get the sound we want to the mix to translate from venue to venue,” Maloles said, noting that the aerial elements of the gig pose no problem to his mix. “Given the rejection on the backside of the PA, I find it better when she is performing on the bridge because I can get way more gain before feedback up there. It’s my favourite part of the set when she’s performing on the bridge with flames, the music mellows out and opens a bit to make the mix way more dynamic.”
The Cohesion PA system featured 16 CO12s on the main hang, 16 CO10s on the side hangs, 24 CP218s on the ground and eight CO10s as front fills.
Af ter 10 years of collaboration, System Engineer and Audio Crew Chief, Leon Fink, has joined Clair Global full time. “Having single feed control over the CP218s means we don’t have to push the boxes so hard, as there are so many, we can run them at a medium level
FOH Engineer, Migui Maloles with System Engineer and Audio Crew Chief, Leon Fink; Lighting Director, Anna Merritt.
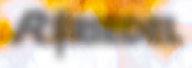
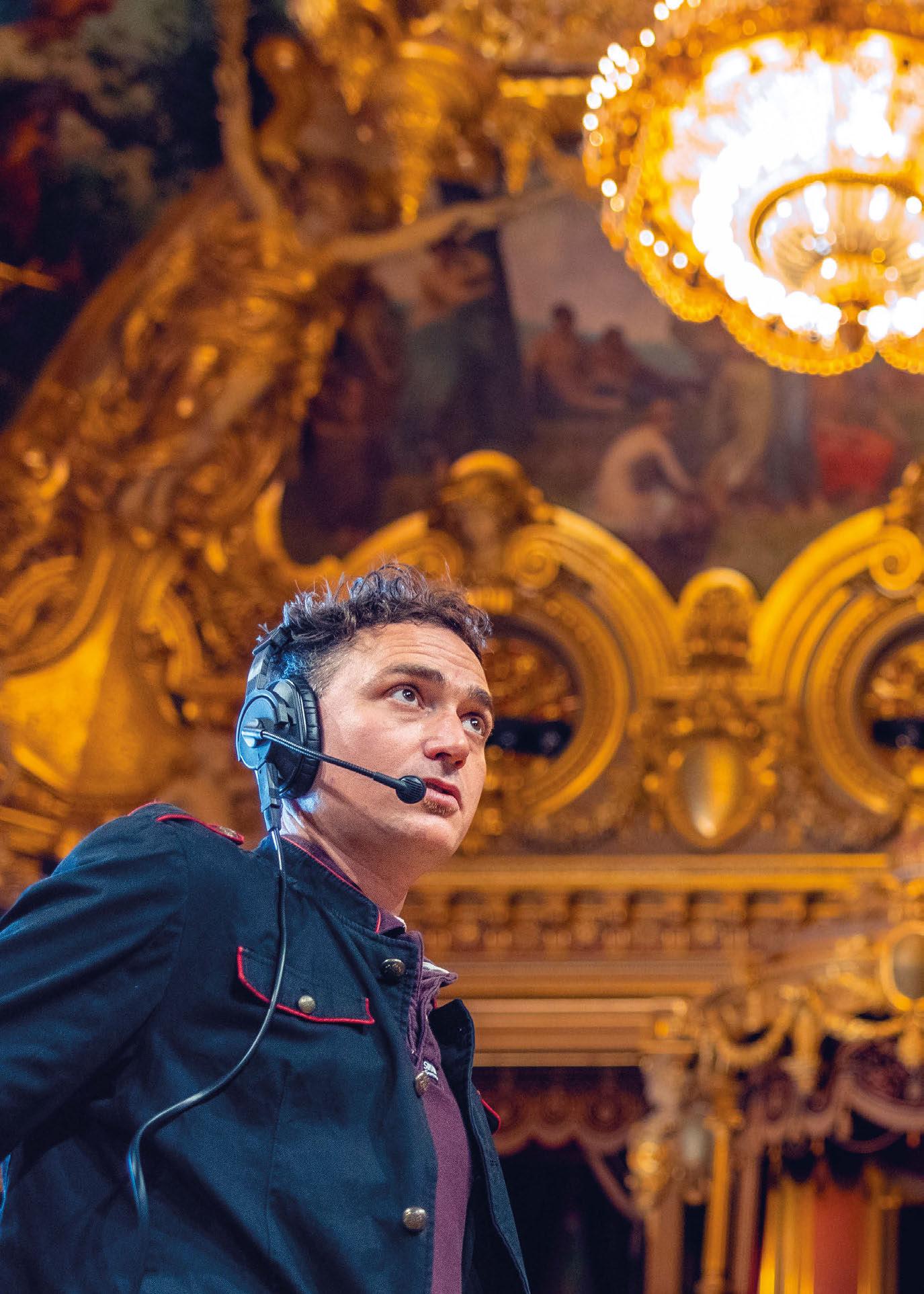
GREGORY CHOSSON
CEO AUDIOVISTA / FOUNDER MARCH ON MARS

To me it‘s all about creating a reliable and technically safe work environment for my customers as well as my teams.
Artist Intercom allows me to provide intuitive workflows and to onboard new team members swiftly.“ ARTIST INTERCOM
Professional and reliable live communications.
Seamless integration of Riedel‘s SmartPanel and Bolero wireless intercom.
Easily scaling from 16 to 1024 ports with flexible licensing.

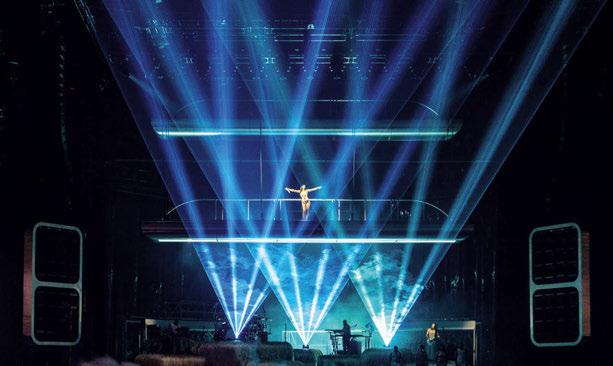
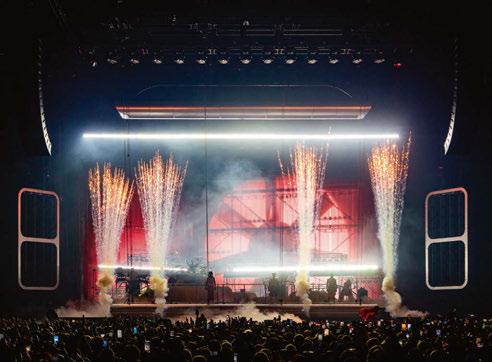

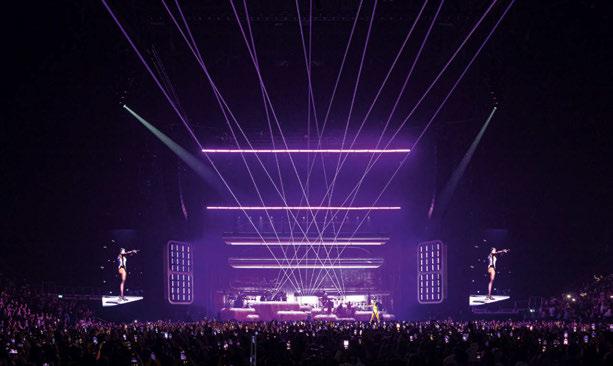
and still get all we need out of the system. As a hip-hop/pop show, the subs really get used and it’s nice that we don’t have to ride them at their limit. The single feed control allows us to adjust to every venue we walk into, without having to add a huge amount of delay time to open the arcs; in my personal experience, the more you must delay the subs to get even sub coverage, the less punchy it gets. This setup also means we don’t compromise the sound for those at the side of the stage,” Fink explained.
“At times we are so far back in the venue, we only really need the front fills to cover the first front row to get the image down and the rest of the crowd are far enough back to have a nice image and not feel like everything is hitting them from above. We worked on this during rehearsals at FBN and it works well.”
The Cohesion PA was driven by Lab. gruppen PLM 20K44s, which Fink mentioned as having “plenty of horsepower”. He elaborated: “Everything is Dante-driven with analogue fallback. We tie into house delays if we like the sound of them. However, given the nature of the rig, if we don’t like them – they’re not an essential ingredient.”
Something Fink believes is essential is his relationship with the FOH Engineer. “I haven’t worked with Migui before, and I always think the relationship with the FOH Engineer and System Engineer is crucial to the success of a great-
sounding PA system. Understanding what the FOH Engineer wants allows me to shape the sound of the PA to his and the artist’s tastes, especially in a field that is becoming increasingly technical,” he continued.
“We’re at a point now where I can pre-empt what he is thinking, adding or subtracting a filter here or there based on his reactions. Over the past couple of shows, we’ve tightened up the show, so he doesn’t need to do very much to his master file and at this point, it’s adding filters to counteract the room. Our tonal balance is pretty much set.”
At t he beginning of a tour, Fink likes to walk the room with the FOH Engineer. He elaborated: “We get to know what each other are looking out for and it builds trust. Migui is an amazing guy. He has got good ears and thinks musically rather than technically, which makes a difference to the mix.”
Despite visiting this venue earlier in the cycle, Fink purposely didn’t recall his show file. “Every show day is different and therefore, I start from scratch. Although the pinning didn’t change much, I tuned the system from the start because I don’t believe in a ‘copy paste’ approach in the touring world,” he said, praising Sound Image Account Executives, Jason Vrobel and Jeremy Peters; Communications and RF Technician, Nathaneal Marcheval; Patch Technician, Xavier Marcheval; Monitor
Technician, Thomas ‘Sometimes’ Lawn; and PA Technicians, Maciej Sliwinski and Anthony Dean. “The Newcastle show was good, and it felt like everything had fallen into place from then on,” he reported. “The rest of the technical team are proficient. During the load-out, the last speaker comes down 40 minutes after the walk out music finishes. We’re in a good groove, with all audio truck doors closed within an hour and five minutes. I’m fortunate to work with such a good team on this run.”
Monitor Engineer, Caleb James, inherited the gig from Jeremy Peters who mixed the US dates, and chose a DiGiCo Q852 with Waves plug-ins, sharing an Optocore loop with FOH and playback departments. “DiGiCo is my ‘goto’ console brand,” he revealed.
“T his is the first time Migui and I have used this desk – it’s their flagship model, which we inherited from Coachella and it’s really good. I love how much information you can see at the same time looking at the surface. You can personalise it to your workflow, and there are tonnes of macros now, so any function you want to get to quickly is easy to do. I’ve personalised my banks of faders to my muscle memory, lining things up to where I’m used to grabbing them,” he enthused.
For show communications, Sound Image provided a Riedel Bolero system. “I like being on this side of the Optocore loop – it’s the ‘hot
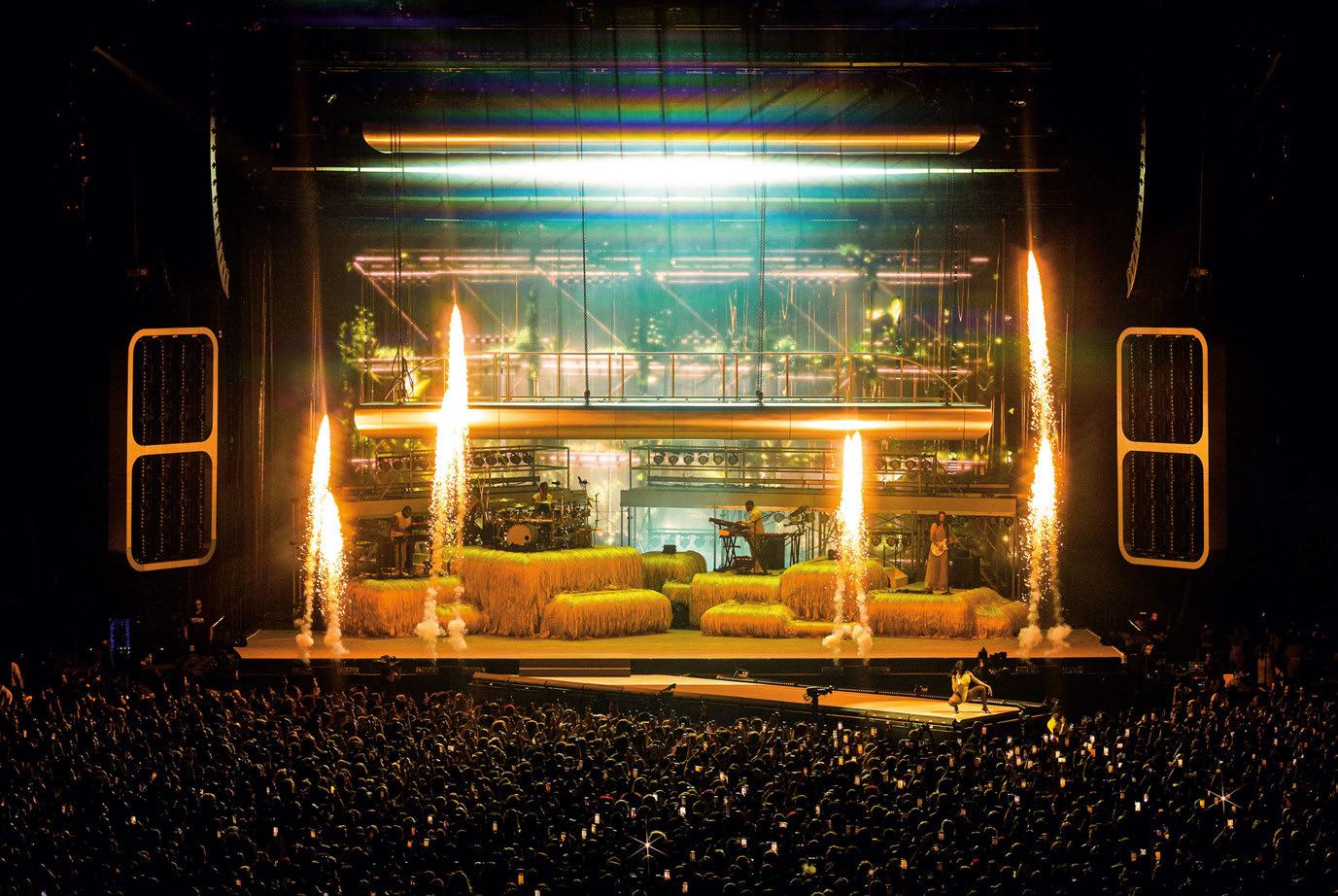
seat’ of the house. Overall, the thing I love most about mixing live is the fact that you must stay focussed and keep your head in the game; there is always something happening, and you must be quick to react and troubleshoot problems should they arise. Everybody on-stage is using talkback, so if they ever need something, I’m able to make it happen to keep the show going.”
James and Doja Cat both used Fir Audio Krypton 5 in-ear monitors. “I’ve been rocking with these for three years and they’re the best in-ear monitors I’ve ever had,” he reported. “The rest of the band are mostly using JH Audio IEM models, all on a Shure PSM1000 in-ear monitoring system.”
For main vocals, Shure’s new Nexadyne capsule was put through its paces on ADX2FDs, AD2 and AXT200s wireless microphones while the drums featured a mixture of sE Electronics microphones with Radial Engineering DIs chosen for guitars and AKG C414 and Sennheiser shotgun microphones selected to capture ambience.“My favourite moment of the set is the transition from 97 to Balut, where the drummer switches to his cocktail kit; it’s quite an intimate moment with the crowd,” he said.
“European crowds are loud. It’s been a good run. We started at Parklife, where we were rained on, but she was having a blast, kicking water around and having fun, and we’ve just been keeping that train going ever since.” On the
other end of the loop, Playback Technician, YS of Brooklyn Sound walked TPi through his rig, which he assembled in collaboration with Glen Canyon Audio.
“I have the DirectOut PRODIGY.MP with two network cards, 32-analogue out on the back, and MADI as well. I have a Universal Audio Apollo Twin X and a NetGear GS105 unmanaged port with three Apple MacBook Air M1s – one of which is the show computer running Ableton 11.3.22, which is ideal to switch around the setlist and do variations on the show when required,” he commented.
“I ’m routing Auto-Tune presets via MIDI over network, so A and B can interchange,” he added. “I also have this Oaktone controller to get through everything. DVS into the PRODIGY. MP, which pushes the stream and we’re going Dante into a DiGiCo Orange Box with primary and secondary networks just in case something happens. We’re running a redundant 32-channel show, 48K on this side, and 96K on the other to match up to the mixing consoles.”
YS described coming into the show with “most of the work already done in Coachella”. He added: “We’ve been tightening up on the road, which is a lot different than coming in and having to build it from the ground up, so it’s been a lot more relaxing, and it lets us focus on the fine details of everything,” he said, pinpointing some of his favourite tracks. “I love Agora Hills – it’s a
hitter for me, as well as Piss. This has been an amazing tour to be a part of. The schedule is friendly and we’re having fun.”
Th e Scarlet Tour was further supported by Wardrobe, Avila Alexis and Marisol Diaz; Caterers, Roy Bogle, Leigh Kelsey, Andre Allison, Carmen Wild and Trevor Bantin; Live Nation, Anthony Amor; Live Nation VIP, Mariachiara ‘Miki’ Paladino; Merchandisers, Arielle Gelb and Simon Harlock.
In closing, Migui highlighted the Streets, Ain’t Shit, Rules and Agora Hills portion of the show as his favourite part of the setlist. “The crowd really love it because she’s having fun on the bridge,” he remarked.
“European audiences have been great. Super receptive to the music and are loud and like to participate, singing along and dancing the whole time, and I know that if I see that, then I know I’m doing my job. Everybody feeds off her energy, so if she has a good show, we all do.” www.dojacat.com www.bpm-sfx.com www.clairglobal.com www.freightminds.com www.flybynite.co.uk www.glencanyonaudio.com www.imagesfx.com www.prg.com www.sound-image.com www.taittowers.com
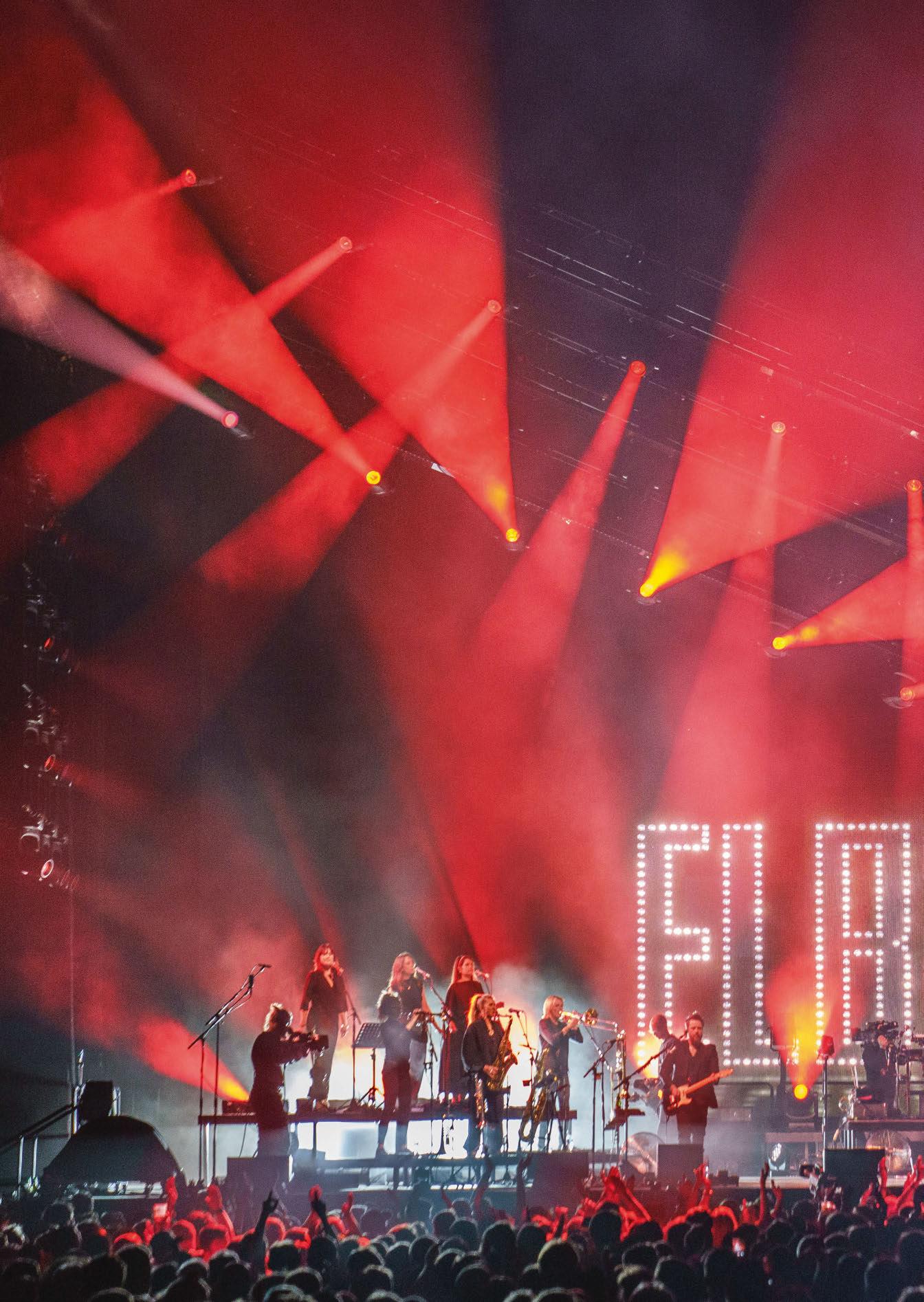
ELBOW: AUDIO VERTIGO TOUR
The Manchester band returns to arenas for the first time since the COVID-19 pandemic with a new production design inspired by their 10th studio album, Audio Vertigo. TPi catches up with the crew in Birmingham ahead of the band’s opening of the Co-op Live to find out more.

Words: Alicia Pollitt
Photos: Peter Neill (shootthesound.com)

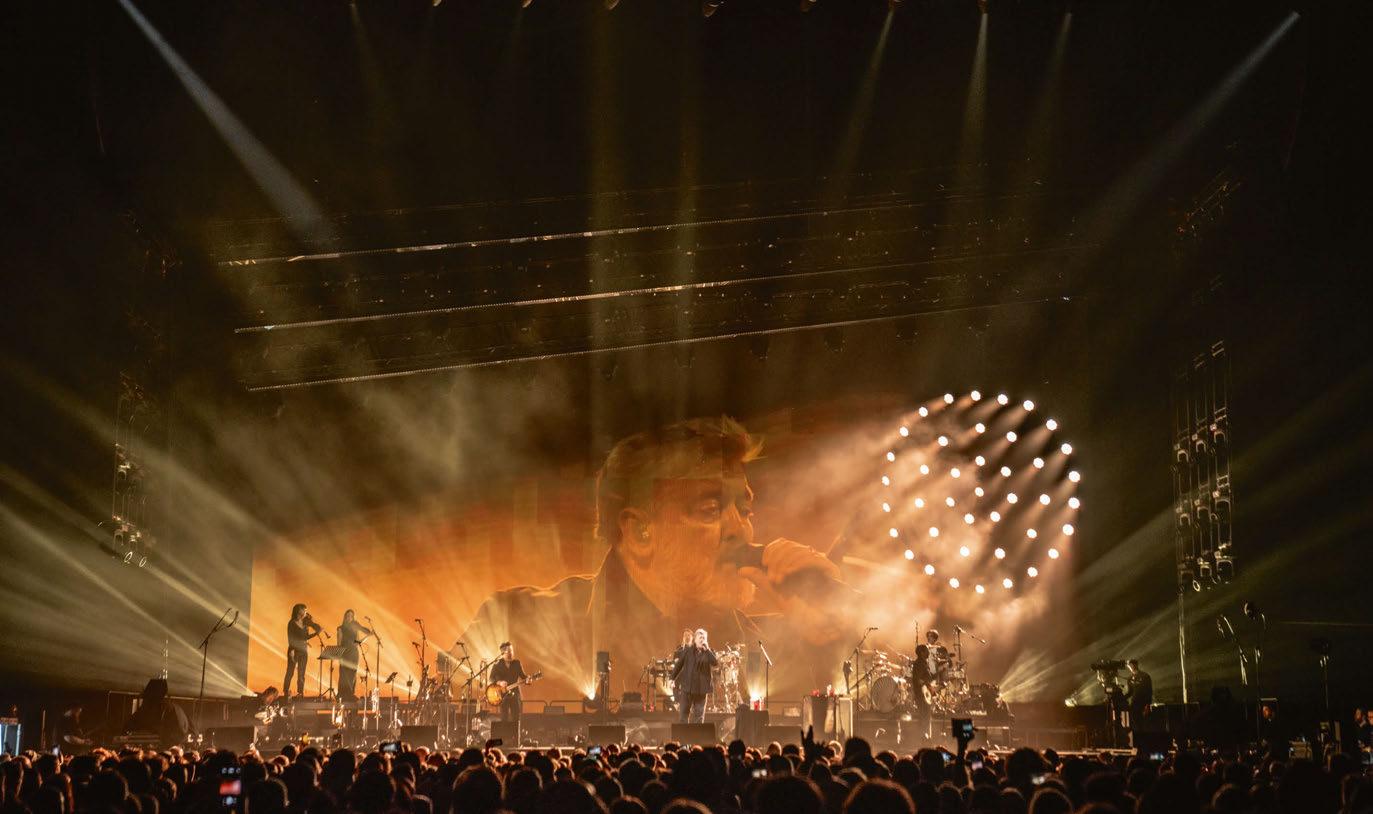
Alongside celebrating their 10th studio album, Audio Vertigo, Elbow’s latest live production marked the band’s first arena tour since the COVID-19 pandemic and, as fate would have it, provided the Manchester group the opportunity to be the official opening act for their home city’s new arena – the Co-op Live. Having not covered the band’s live shows since 2018, TPi made the trip to Birmingham’s Resorts World Arena catching up with the band’s long-standing crew and learn about some of the production goals for Elbow’s latest outing as well as why so many of their loyal crew dropped everything to jump back on their tour bus.
“It’s great to be back in arenas; we have the chance to do a proper arena show,” began Tom Piper, Elbow’s Tour and Production Manager. “On the arena tours, we have a crew that has done most, if not all of their shows, so it is like coming back to a family. It’s the reason I like working with these people who are all incredible professionals and great to be around.”
Piper, who has been with the band since 2000, is a picture of pride as he tours TPi around the backstage area with Show Designer, Cate Carter.
The suppliers for this show comprised Lite Alternative for lighting and rigging, Creative Technology for video, All Access Staging and Productions, lasers from ER Productions, audio from Skan PA, trucking from Fly By Nite, and Bittersweet Catering kept band and crew fed and happy throughout the seven-show run. Ensuring band and crew arrived venue to venue safely was Vans for Bands. “Elbow and their team are the loveliest group of people. We’ve
been working with them for 10 years now, and it is always the highlight of our year working for them,” Spadge, of Vans for Bands, commented. “We have longstanding relationships with all of our suppliers,” enthused Piper, once again highlighting the importance of loyalty within the Elbow camp.
On t he short but sweet tour, the production toured with seven trucks of kit. “The difference between playing The O2 arena at 20,000 capacity with seven trucks versus seven trucks at the Brighton Centre at 5,000 capacity is difficult but it means you’re not doing the same thing every day and the crew can build a fantastic show either way with the space, they will make it work,” Piper commented.
THROW THOSE CURTAINS WIDE
Carter began her working relationship with Elbow in 2008 as Lighting and Programming Operator under Bryan Leitch, who mentored Carter at the beginning of her career and eventually passed over the torch to her to be named Show Designer following Leitch’s retirement. Leitch passed in 2019 after a valiant battle with Non-Hodgkin’s lymphoma, and yet his legacy still lives on, especially within the Elbow camp. “He gave me and my friends great opportunities when we were younger,” Carter smiled. “He took me under his wing and mentored me and that included putting me on this show in 2008. To be still involved now is utterly fantastic.”
Beginning the design process in the autumn of 2023, Carter enlisted an extensive team to realise her design for the run, originally expecting the show to showcase snippets
from Elbow’s extensive discography. “We began design conversations before the album was even finished. The conversations were about it being a celebration of 10 albums, and we were going to pull in elements from each album. However, then the album came, and it was amazing and so strong that it needed to be about it alone,” Carted explained.
“I was then presented the artwork which was this extremely strong colour graphic direction and then that fed into a U-turn, and we made it all about Audio Vertigo and the sonic direction of the record. It’s the rockiest album Elbow have released in a long time.”
Fi ve out of the 19 songs on the setlist were from Audio Vertigo, which left time for the crew to give the new album its time in the spotlight.
ALL DISCO
Continuing with the ‘vertigo’ theme, the stage design consisted of skewed, sloping, slanted and kinetic lighting fixtures. “The lighting rig is automated and built from off-the-shelf lights and trusses,” Carter explained. “But we’ve configured it in a weird way to reference the album title so there are no straight lines. There are configurations that make you want to fall over, and that’s what we were going for.”
The lighting used on the tour consisted of 76 Ayrton Perseo Profiles, 59 Robe LEDBeam 350s and two iFORTE moving lights accompanied by 10 Martin Professional MAC Aura XBs, 22 CHAUVET Professional Color STRIKE Ms and 51 GLP impression X4 Bar 20s.
Directing the lights on this show was Kristof De Dycker, CEO of K-events, who worked alongside Carter in Belgium. “It’s such a cool
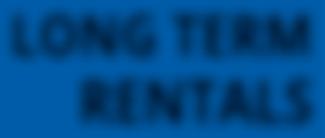
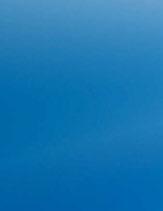









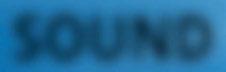
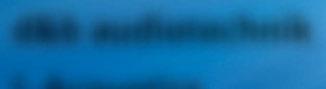
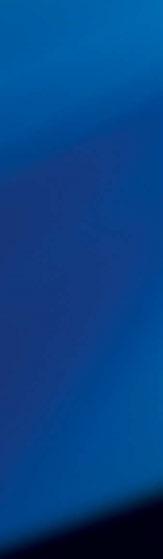
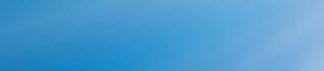
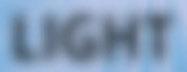

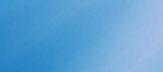
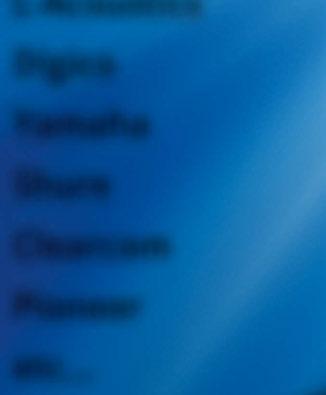
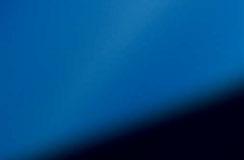

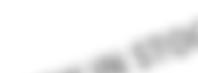










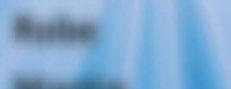
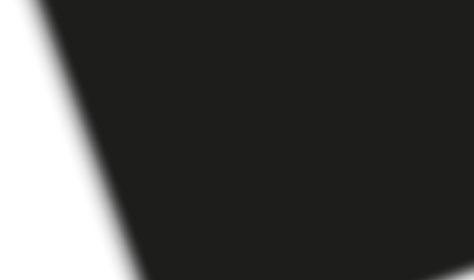

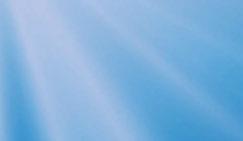



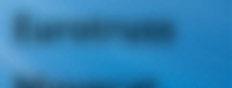
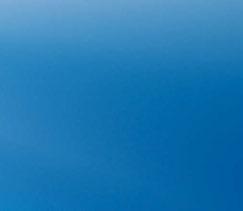
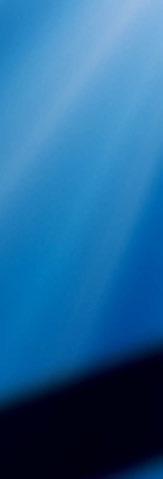


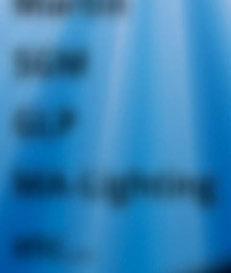
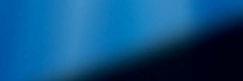



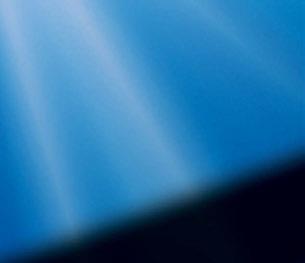









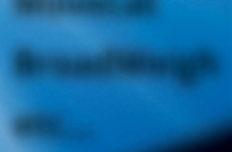

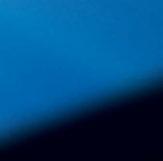

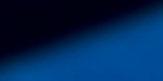
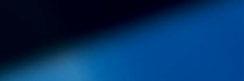
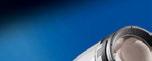

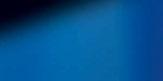
















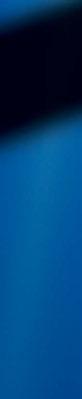
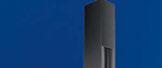



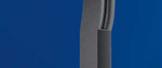
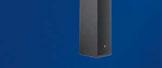
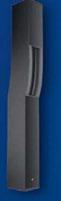




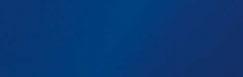

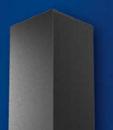
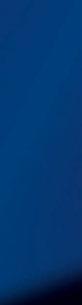
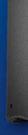










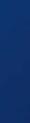

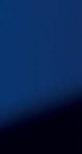



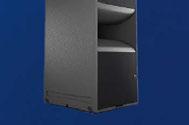
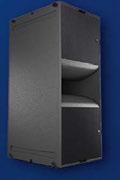
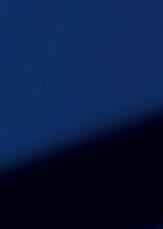










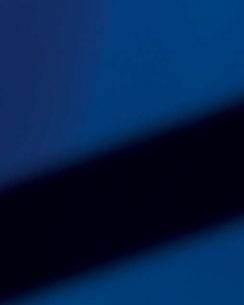





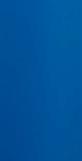




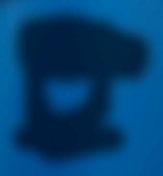


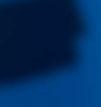

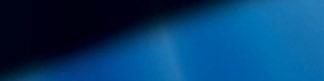



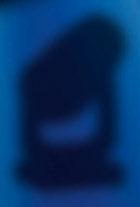








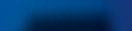
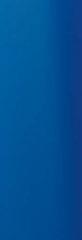


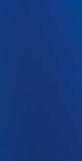
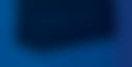


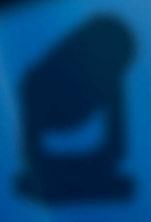

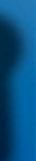

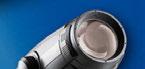
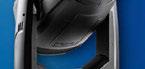
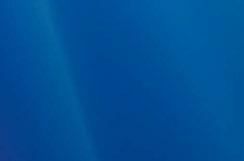

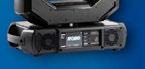




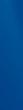
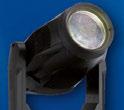


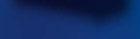

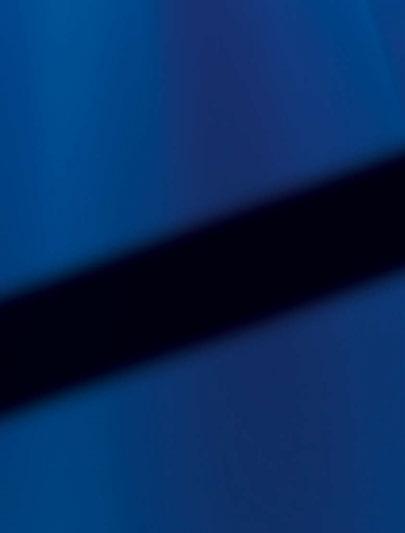






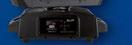


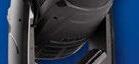


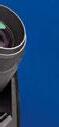
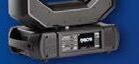


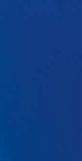





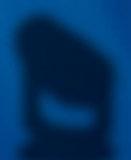




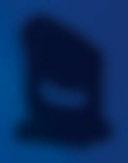


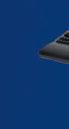

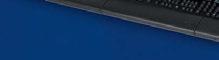
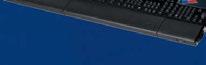
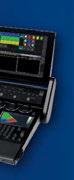
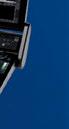
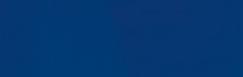

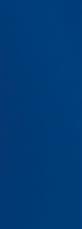
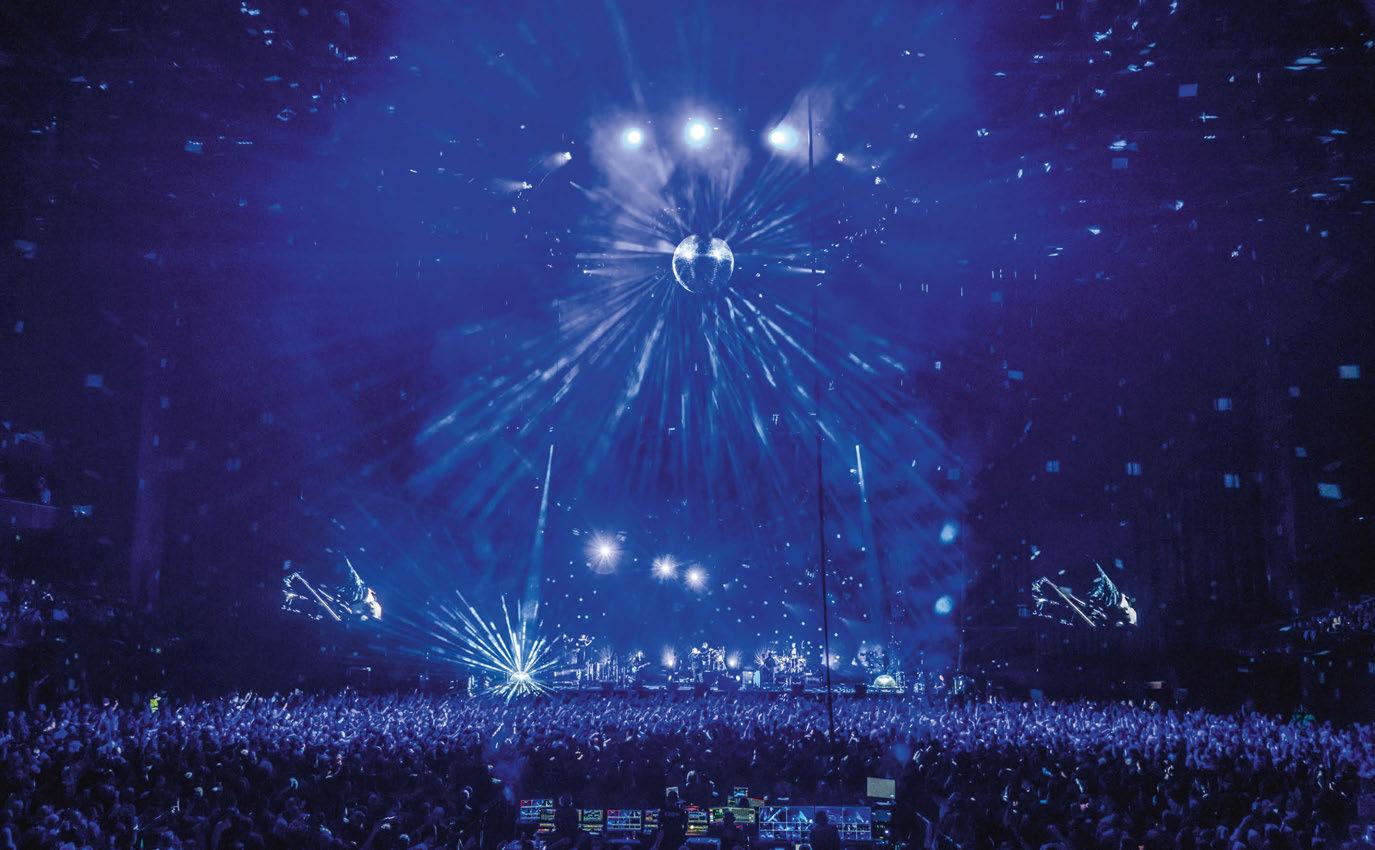
design to work with,” Dycker commented. “The beginning of the show is one of my favourite parts. It opens the show with an expectation of what you’re going to get for the next two hours and what the concept is.”
The designer ran the show on an MA Lighting grandMA3 full-size desk in MA2 mode. The decision to use this mode came from the preparation for the festival season in Belgium. “We have shows running in MA3 already, and I felt like it wasn’t necessary for this tour – especially because I was preparing for Belgium’s festival season at the same time as this,” Dycker added.
Dycker had been on the road with Elbow during last year’s festival season and was delighted to be welcomed back to the tight-knit camp for the UK arena run. “I remember having Elbow as one of my childhood artists. The Bones of You is such a pleasure to watch every night and I love it,” he reflected.
The GLP impression X4 Bar 20s existed on a Kinesys rig, so that both Carter and Dycker could use the automation to build different staging looks throughout the two-hour show including the finale, One Day Like This. The design created a circular light show on stage left that embodied the hopeful nature of the song, with the light shining down on the band and audience meant to resemble the sun, reflecting the lyrics ‘Drinking in the morning sun, blinking in the morning sun ’.
Carter’s stunning show design also included a bewitching moment where frontman, Guy
Garvey encouraged the crowd to beckon three mirrorballs, two downstage and one descending from the ceiling, using their twinkling fingers for the appropriately named song, Mirrorball
Carter told TPi that despite having several different elements, the show becomes a whole picture. “Having a good set and architecture gives you a cool thing to light,” Carter began. “On this show, we have lasers, video and lights and I don’t see them as individual things, which helps to make a better, bigger picture.”
Having had direct contact with the band when creating their show designs for years gone by, she told TPi an anecdote of how they had wanted to add lasers to the live show for a while. “The band have wanted to work with lasers for years and they’ve been promising me they would write an album that suits lasers for years and I think we finally had it with Giants of All Sizes and even more so with Audio Vertigo, though I don’t think we could ever go back to not using them now.”
The show had six AT20 Laser Heads from ER Productions’ ATOLLA range, with four of them situated on Wahlberg Motion Design columns upstage and the other two further downstage, the lasers were fired through Pangolin BEYOND by Cameron Dominey of ER Productions. Four Look Solutions Viper Deluxes and two Unique hazers were used for atmospherics.
“W hen I get to that moment where the AT20s are out during the show for the first time, I get a real buzz from it,” Dominey enthused.
The operator ran cues that triggered timelines due to the show being run live. “I think it makes me enjoy the show more. It makes me more engaged in the show.” With an increasing use of lasers in live events, TPi discussed the safety ramifications with Dominey.
“We have so many safety procedures in place that I can be certain when doors open, that I’ve marked all the lasers safely. There are things that can go wrong but provided that there are competent people who are aware of the dangers that can make it happen safely then they should absolutely be used.”
This is Dominey’s first tour with the camp, and he made it clear that he didn’t want it to be the last. “It’s nice to come into a team where they know each other so well,” he enthused. “I feel like I’ve been a part of it for some time now, which is an absolute credit to the crew.”
THE PICTURE
During the show Carter is situated at FOH, show-calling, directing automation and is sat with Dycker and Dominey, just in case the design team need her. With the show run completely live, the camp ran a tight ship, with eight people in the crew focussing entirely on cameras that filled the downstage 18m by 9m GLUX 10mm carbon LED screen and the two 5m by 5m IMAG screens which were also GLUX 10mm carbon LED screen which ran on GLUX VSP-F2L4 processing.
Creative Technology provided video, camera and server packages for the seven-
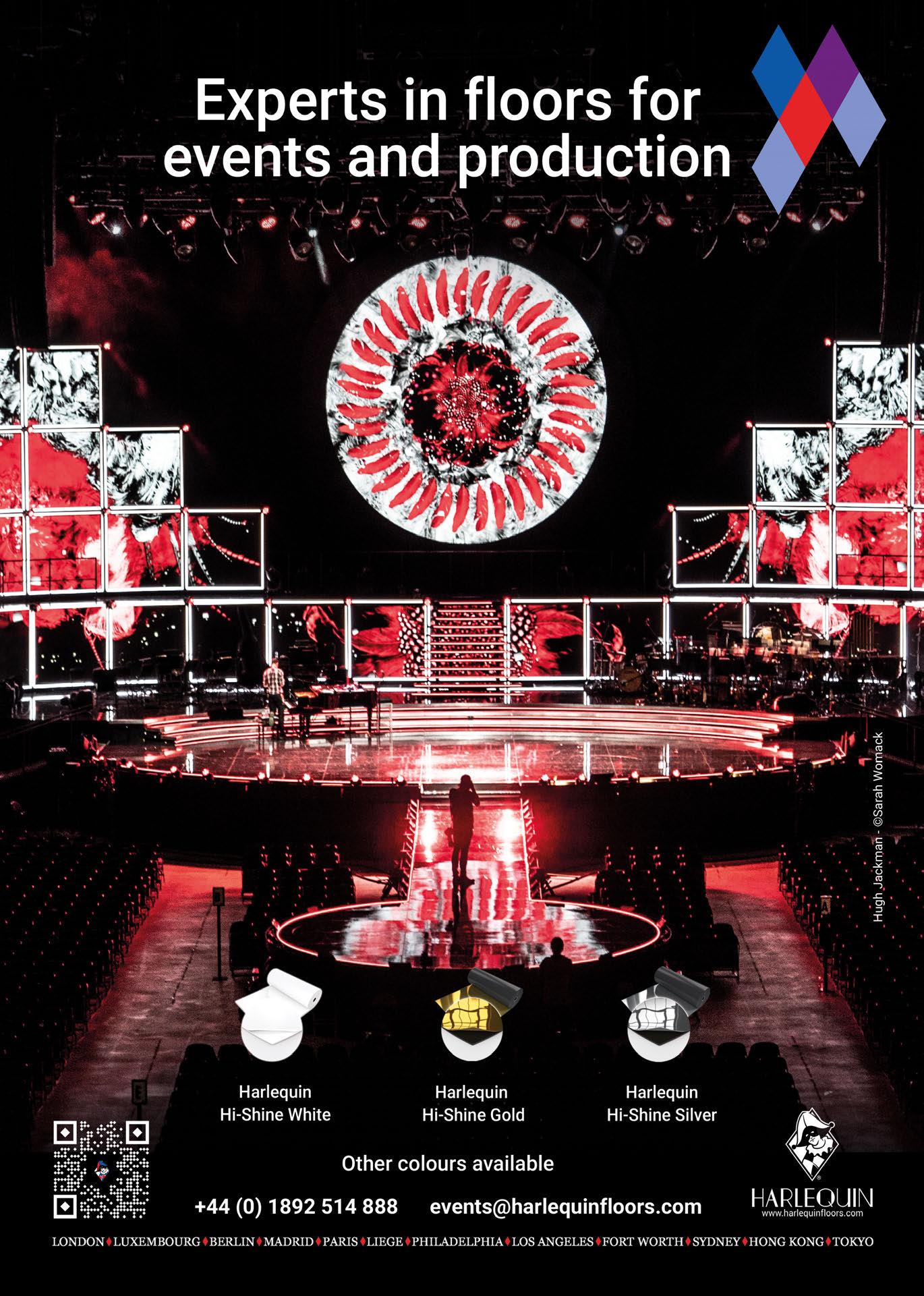
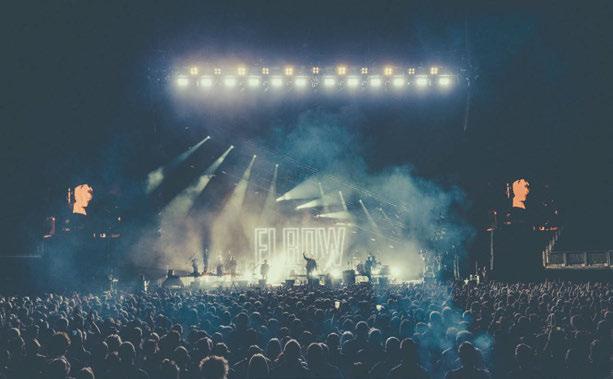
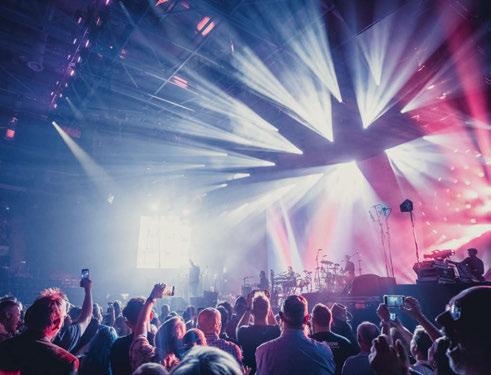

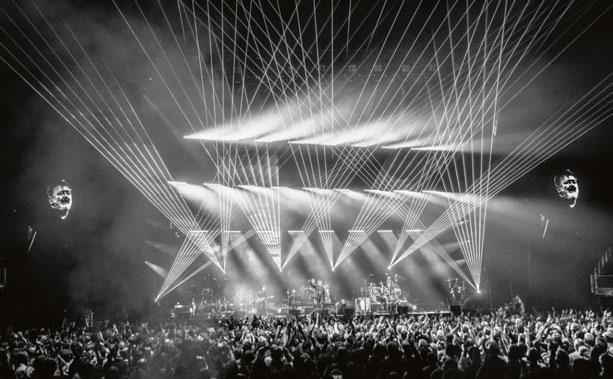
show run, with Arkadiusz Wegrzyn acting as Senior Project Manager with Jonny Clark on board within Creative Technology as the Head of Music and Touring. Taking control of Camera Director within the eight-person strong crew is Phil Woodhead, who has been on the road with Elbow four times before the Audio Vertigo tour. “It’s a nice situation to be in,” Woodhead commented. “We’re all working together so closely and it’s nice how you get close to people and how we’re in each other’s pockets.”
The production switcher on the show was a Grass Valley Korona 2ME, which controlled four Panasonic UC3000 4K cameras, four Panasonic AW UE100 PTZ cameras and three Marshall minicameras. The cameras had a variety of Canon lenses, including one HJ11 x 4.7B ENG lens, two Canon HJ22 x 7.6 ENG lenses and a Canon XJ95 x 8.6B Box lens with two of the cameras on an Osprey Elite S Pedestal that had a CARTONI C40 Dutch head and was situated on a VINTEN dolly.
Content creation was taken on yet again by Leo Flint of Studio Flint, which began the show by displaying ‘ELBOW’ in lights on the large video screen behind the musicians. “Leo has a team that works on the show and he works hand in hand with our Screens Director, Salvador,” Carter commented. “We’ve been creating a palette of different visual effects and layering cameras to try and tell a story.” The video processing saw Disguise GX 2c
media servers step up alongside a Riedel Communications MediorNet system to ensure smooth running of the live video footage that was then run through Notch to add different effects to the back video screen and the IMAGs at either side of the stage.
“The whole show is not on timecode, so we have to respond to it live,” Salvador Bettencourt Avila, Screens Director, commented. “It can be quite tricky in places when the band do things differently but every day we evolve the show more and more.”
With such a large video crew, it is no secret that the video elements of the show are of importance to the overall design and managed to echo the stage feel between the band and the long friendship they share.
“The band know each other so well, they’ve been friends forever,” Woodhead explained. “As the show goes on it is nice to capture the winks and smiles to each other, and it’s good for the audience to see that they’re having a good time on stage.”
TPi managed to walk around with the camera crew in the loading bay of Birmingham’s Resorts World Arena, as they enjoyed their first sun of the day at 5pm. Yet still, the crews were all smiles, telling tales of their relationship with Elbow as fans as well as an essential part of their crew. “I like the band and there are a couple of tracks that I really love,” Daniel Sheldon, Camera Operator, commented. “It’s
a lovely-looking show. I’ve done two or three tours with them now and it is nice to be back.”
Br uce Selkirk, Camera Operator, added: “This is probably one of the best tours I have done... The music helps but also the toy that I have on stage. I have a dolly and head that moves on a track and usually with rock ’n’ roll you get a skateboard as your dolly but on this tour, it is beautiful and smooth, it’s lovely.”
WHITE NOISE WHITE HEAT
Sounding out the two-hour show was a massive feat, with a collective crew of seven focussing on the audio. The team created a striking audio performance which included travelling with a d&b audiotechnik PA system.
The full audio system comprised main hangs of GSL, KSL side hangs, V Series as rear hangs, J Series ground subwoofers and Y Series side fills. Systems Technician and Audio Crew Chief, Scott Essen has worked with the camp for around 10 years and again, commented on the dynamic of the crew: “I’ve discovered that it is a tight-knit group. People have been here for years and years and it’s a nice family vibe.”
Essen began in the industry 25 years ago, consistently in audio and believed that the familial nature of the camp is what has kept him in the industry. “It has become such a part of my lifestyle that when I go home after being among so many people, it feels quiet and my
body has to adjust again,” he laughed. “I enjoy the show. They have their standout tracks but Danny Evans, our FOH Engineer, has a really nice mix and he knows it so well so it makes it a pleasurable show to work on and listen to.”
Evans has been within the Elbow camp for 25 years, not only acting as the FOH Engineer but also as the studio engineer for most of Elbow’s studio albums, including Build a Rocket Boys! Giants of All Sizes and recently, Audio Vertigo. “Some of the tracks on the first album ( Asleep In The Back ) were recorded in the studio that Tom and I had in the early days of working with the band,” Evans stated.
“We’re really fortunate to have an amazing crew that always do an excellent job. All of our crew are freelancers and despite Elbow not touring as intensively as other artists, they put the band as a priority and make themselves available for when they play. I think the reputation the crew has is excellent.”
Cate Carter joined the crew from a training opportunity in 2008 and worked her way up to becoming the show designer. This is just one example of the camp’s overall attitude to training the next generation as well as retaining current staff, as Evans elaborated: “Not only has the camp been a great training ground for crew who go onto bigger tours, but those
that have toured previously with Elbow often get in touch to let me know that they are keen and available should any opportunities arise to rejoin the crew,” he said.
With his mix highly regarded by the rest of the crew, Evans works on an Avid VENUE S6L with Julien Helme, Monitor Engineer, also on the same desk. “They’re great-sounding desks,” stated Evans.
“I love the flexibility of the routing, customisable fader layouts can be recalled with the snapshot/scene for each song, making it straightforward to mix a 50-odd channel show on a 24-fader surface. I like that there are a wide variety of Avid and third party effects/ plug-ins available, and I always specify the S6L with a Waves server.”
With SKAN PA Hire providing audio for this run, Helme told TPi that the band owned their own IEM systems, which were Shure PSM 900 Wireless transmitters and Shure P10R+ Diversity bodypack receivers: “It’s always a pleasure working with the SKAN crew, especially as we have worked with them for a long time,” Helme commented.
Evans highlighted the camp’s relationship with the audio supplier: “SKAN are very much the preferred and long-term audio suppliers for Elbow tours. It is a pleasure to work with a
state-of-the-art, best available system that makes for a super-efficient operation.”
Catching up with the crew in Birmingham, with the Co-op Live show on the horizon, Evans expressed his enthusiasm: “When news spread that Elbow would be the first to play, we received so many well wishes from previous crews and fellow tour managers and production members. We are very happy to be the first.”
The seven-show run concluded in Nottingham on 15 May. With a string of summer shows planned, Guy Garvey will continue to tell tales of their 10-album-strong discography. On the tour, the band also echoed The Trussell Trust’s mission, who are campaigning to end the need for food banks in the UK, with IMAG screens displaying donation links before the show. Supporting Elbow on its arena run was its unwavering crew that has taken the production to new heights. www.elbow.co.uk
www.allaccessinc.com www.bittersweet-catering.co.uk www.ct-group.com www.er-productions.com www.flint.studio www.flybynite.co.uk www.skanpa.co.uk www.vansforbands.co.uk
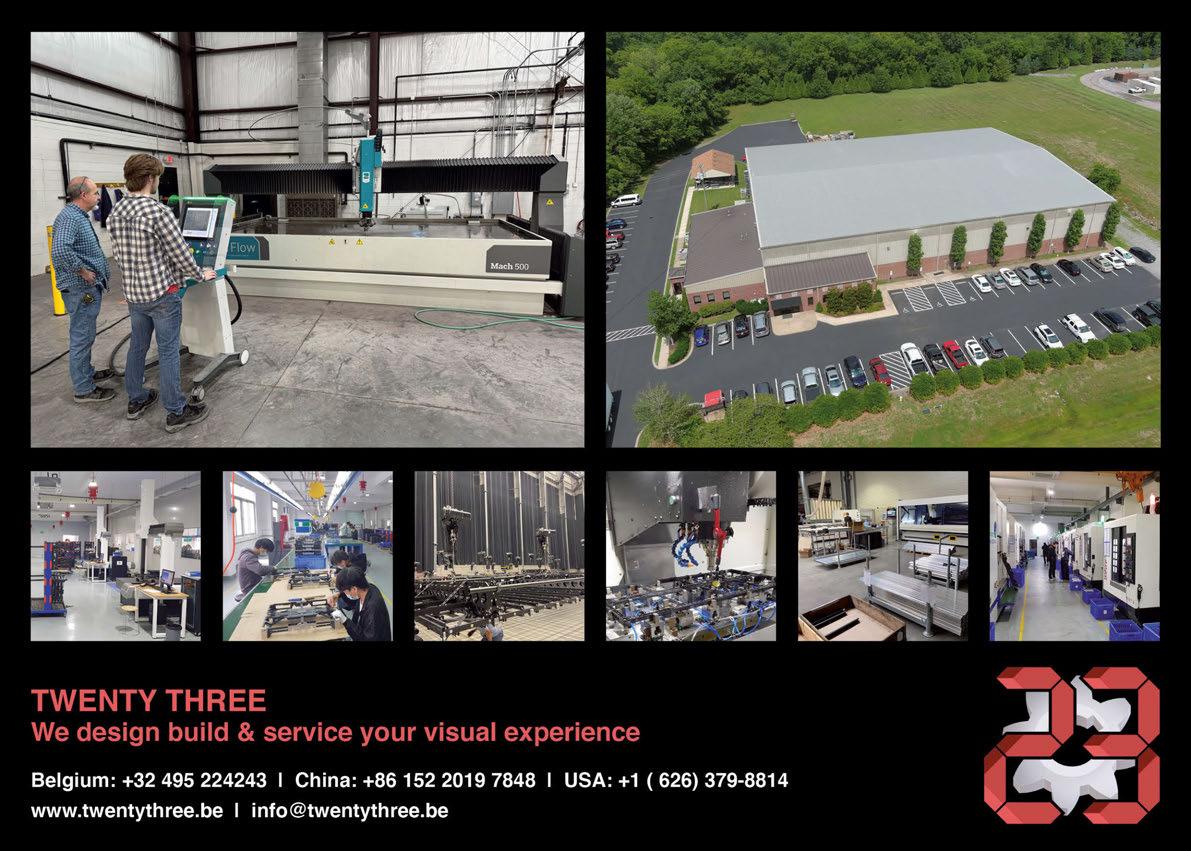
HIGH LIGHTS
Electronic dance music fans descend on London’s Barking Park for a unique, brutalist-inspired festival experience with creative engineering in abundance


Words: Alicia Pollitt
Photos: Jody Hartley, High Lights and Angelina Nikolayeva
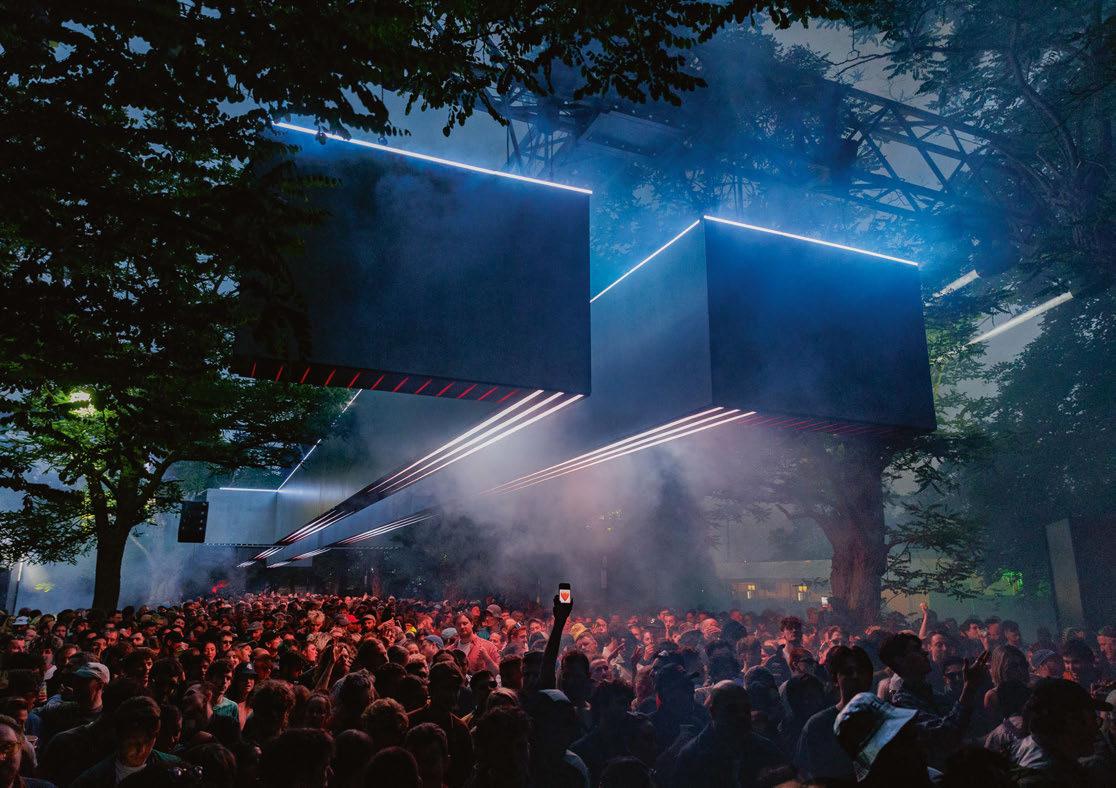
High Lights drew in a crowd of 7,000 during its inauguration at London’s Barking Park. London-based promoters Percolate enlisted design studio Lucid Creates to design and construct a ground-breaking events space that measured 60m long by 18m wide by 8m high, and saw electronic dance music heavyweights performing in and among the trees, kitted out with a d&b audiotechnik sound system.
“I don’t think there’s another location in London like it,” began Chris Carr, Director of Lucid Creates. “Fred [Letts, of Percolate] was set on the design working within the trees, so our design process began by having to work out how to actually design something that would look great and meet the design brief, as well as the very real and practical considerations of the structure fitting between the incredibly tight tree clearing.”
Coined the ‘Installation Stage’, the structure extended 60m into the crowd and consisted of a concrete façade that had distinctive geometric shapes that spanned the space in considered dimensions, shapes and proportions which provided a sense of surrealism. The suspended concrete blocks ‘floated’ in mid-air above festival goers and weighed an impressive 15 tonnes, with weight distribution handled by the substructure, which was another 15 tonnes.
The structure that held the weight of the set pieces and production is a unique truss system that Lucid have designed and developed over the past few years, which is all fabricated inhouse from its Kent workshop.
Daylight saw the sun filter through the trees, and onto the structure, this bleed of light cascaded down creating almost cathedral-like lighting. Ella Willis Nasseri, Project Manager
at Lucid Creates, elaborated: “Most of the festival was in the day; we only had one hour of darkness, so we wanted to work with the natural light rather than against it, when the sun shone, shafts of light would beam down onto and through the structure, as though it were natural light coming through the window in a cathedral, which felt magical.”
As t he show descended into darkness for the evening sets, an arsenal of lighting and video sprung into life, with custom-made content created by Lucid in partnership with long-time collaborator, Matt King.
“We didn’t want overly cinematic content because we wanted it to be purely about moving light through the dance floor and you get these blocks of light at different intervals, moments of pure darkness contrasting with the entire set being illuminated,” Carr commented. “We treated the video more as a light source, the way it interacted with the negative space and the angles we had created through the set looked amazing,”
A total of 70 sq m of ROE Visual CB5 MKII LED panels were accompanied by 20 Claypaky Sharpy Plus Aqua fixtures, 16 SGM Q-8s and 12 Q-7s, which worked in conjunction with 256m of Lucid’s LED strip, illuminated the sculpture, picking out each line, angle and detail.
Overhead structures are becoming somewhat of a signature of Lucid Creates’ design style, Carr told TPi: “There’s something extremely powerful about these overhead designs in open-air settings, which comes through in a lot of our designs and is something we love doing,” Carr explained.
“It means it doesn’t matter where you are standing, you can have that front of the crowd experience, whether you’re at the back, the middle, the side, wherever you decide, you’re
going to get a great, uncompromised dance floor experience.”
The bill included dance icons Max Cooper, Carl Cox, and London label FUSE, with the first night headline set from Max Cooper being a favourite of both Nasseri and Carr. “The first night was really special,” Nasseri commented. “It was raining, which I always think adds to the atmosphere, but the set was outstanding. Everything just came together, you could feel it in the air and in the crowd, it’s moments like that which make all the hard work worth it.”
With the festival describing itself as ‘club culture meets precision engineering’, Carr and Nasseri explained how the pressure was on to meet such a high-end brief. “Everything is so expensive, people are having to be more selective about where they are spending their money,” Carr commented.
“It’s important to be bold and to keep pushing creatively. You have to keep delivering something new and exciting because people will only buy tickets when they know it will be one hell of a show. We strongly believe that now really is the time to double down in that sense and do something that will stand out.
Fred (Letts) & Simon (Denby’s) dedication to delivering a wholly new experience for both artists and audiences is admirable and is of course, something we are fully onboard with.”
Pu tting on a production of this scale does not come without its challenges, but Carr explained how the team took the learnings from designing the LS23 Stage in 2022 at Leeds Festival when it came to working among trees.
“It’s a huge challenge,” he commented. “Getting a structure of this scale to fit between trees is complicated, but LS23 taught us a lot – mainly that we should be open to adjustment
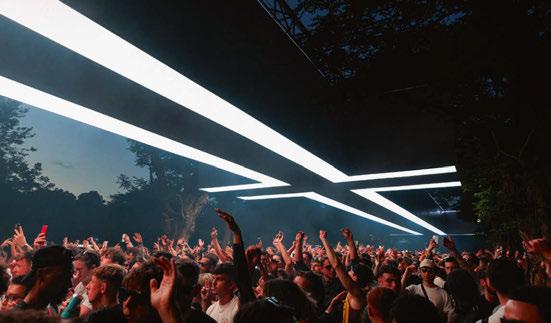

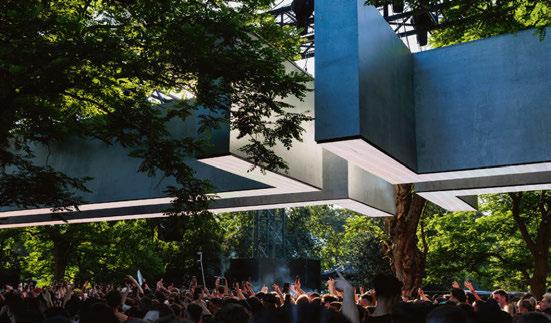
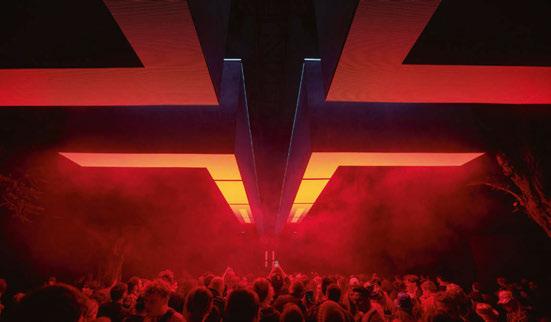
and spontaneity.” This flexibility was crucial to the demands of High Lights, as Nasseri highlighted: “Everything was equally spaced when we did LS23, but this wasn’t the case for High Lights as we had such a small area where the structure could go and the trees meant that the supporting towers could not be placed evenly apart - which increases the amount of structural engineering required by a considerable amount.”
Despite these challenges the studio, alongside the festival organisers, succeeded, while also protecting the park and the wildlife. “The site team did such a good job of looking after the park; it’s important for everyone to have done as well as they did in looking after the space, because we care about it but also because we all want to be back next year,” Nasseri commented. “The park is loved and used by a lot of locals so there are of course a lot of eyes on it, but people noticed the efforts we all went to protect the space.”
The ‘High Lights’ brand was always intended to call back to London’s industrial past and the warehouse music scene whilst also being in an outdoor setting. “The location of the stage actually changed in January to get better off-site levels for the sound,” Carr told TPi. “It meant a whole redesign, but the process happened very quickly. Of all the designs we had conceptualised, this was the one that complemented the space the most and we couldn’t be happier with it.”
Letts added: “Our vision to merge architecture with cutting-edge audiovisual design has been fully realised and we are overjoyed with the result.” Lighting was supplied by Ethix Management, 4Wall
Entertainment provided video screens, and Gaianova delivered video servers. Site management was handled by Eye Of The Storm Events, while structural calculations were managed by Momentum Structural Engineers.
‘THE SOUND WAS STRONG’
RSH Audio provided the sound system, which featured a combination of d&b audiotechnik products including KSL line array, SL-SUB, V-Series, and A-Series. A detailed model of the stage design was created using ArrayCalc, with NoizCalc utilised to consider the far field sound propagation beyond the immediacy of London’s Barking Park.
The sound design was then configured to use multiple delay and fill features to create a club-like intimacy to the festival. “The structure made the club feel and aesthetic,” commented Joe Haycocks, Director of RSH Audio. “We wanted to create a sound system that felt close. With extensive rigging already implemented, it meant we had options, but also had to fit within some defined constraints.”
RSH Audio has a long-standing relationship with d&b audiotechnik, having worked with the manufacturer since 2016.
“It’s great to see the ‘d&b philosophy’ working in action,” commented Jack Page, Artist Relations Manager at d&b audiotechnik. “Joe and his team can select the right product for the job, use all the tools available with a welloiled workflow, and deliver exceptional results, that are valued by not only the promoter and audience but the artists as well. This in no doubt contributes to why RSH has gained such a good reputation in the industry.” Haycocks added: “The quality of support
from d&b isn’t to be underestimated. Roy [Wimpenny, Education and Application Support at d&b audiotechnik] was doing training at RSH not long ago for several of our team and freelancers and it solidifies the major strength of the brand.”
For Dak Shah, Marketing Manager at Percolate the praise was crucial: “It can be a struggle to get the sound right, especially in such a busy part of London, but we’ve had such good feedback, with people saying it is the best sound they’ve heard at a London festival.”
Looking back on the festival, Shah reflected on its first year. “It was hard to envision the site and customer experience with it being a new festival, but once it was underway, it was really nice to see the site come to life and see people blown away by the production and sound, having a great time, and seeing the excitement for us to return,” Shah said.
With High Lights set to return to Barking Park in 2025, Lucid Creates is eager to get back onto the field with the new structure. “The feedback from the industry and the public has been incredibly positive, and we’re looking forward to developing the designs for both stages,” Carr concluded. “There is so much potential for festivals like this that are led equally by concept and design. We’re excited to see where it goes.”
www.thehighlights.space www.lucidcreates.co.uk www.dbaudio.com www.rshaudio.co.uk www.percolatemusic.co.uk www.ethixmanagement.com www.europe.4wall.com www.gaianova.co.uk

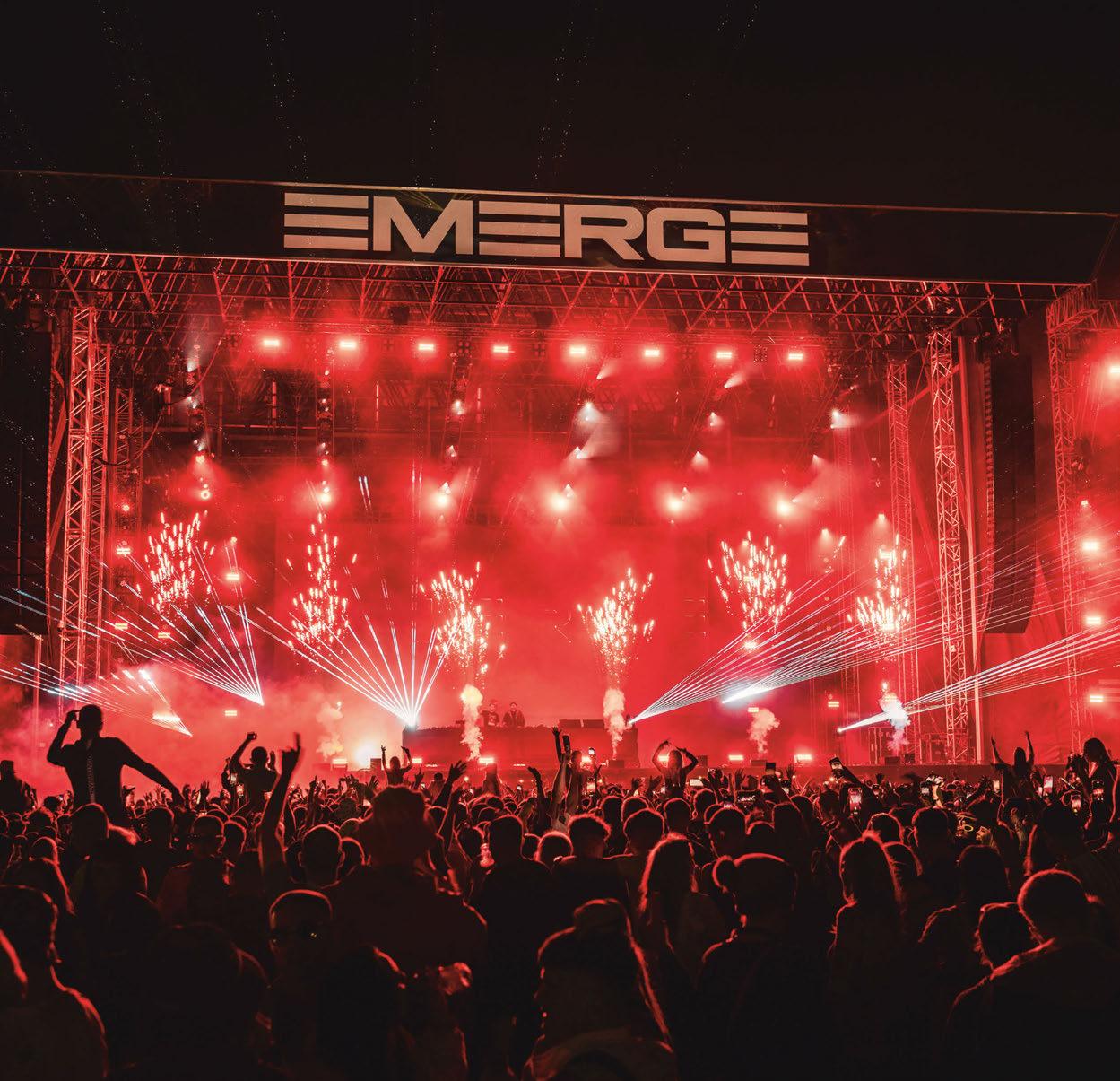
POWERED BY FREELANCERS
Authors of LIVE’s latest survey reveal key insights from the sector-wide paper, highlighting the challenges facing live events freelancers and how the industry can unite to overcome them.

Words: Stew Hume
Photos: LIVE
There were many takeaways from 2020 for the live events community, but one of the striking issues was the wider world’s lack of knowledge of what goes into live events – specifically, just how many people were now out of work due to the sudden closure of venues. One positive in these dark times was the number of communities that began to spring up online to foster a sense of support and a forum to share ideas. Two such communities that are still going strong are The Back Lounge, founded by Tour Manager, Suzi Green, and the UK Live Events Freelancers Forum, created by Ethix Management’s Paul Jones. Four years since their creation, both these forums have now played a key part in the Powered by Freelancers – the Live Music Edition 2024 – a study in collaboration with LIVE and Handle Freelance Solutions to quantify some of the hearsay within the live events industry and translate the most common points of discussion into hardcore facts.
Filled out by 1,281 freelancers and temporary workers, the survey looked to address several major concerns within the industry such as job satisfaction, security and pay rates, with the findings made freely available online throughout February 2024. “It
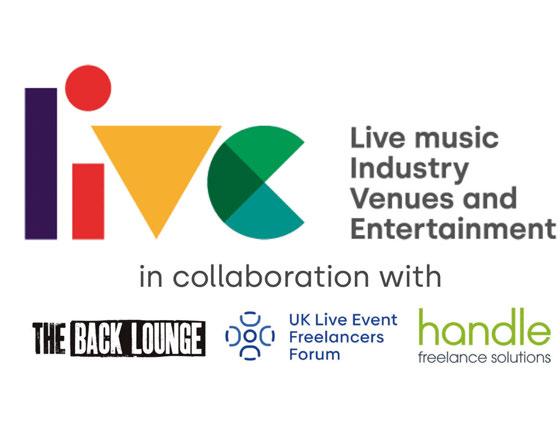
sets a benchmark for our industry,” writes LIVE CEO, Jon Collins, in the introduction to the report. “One we will use to measure progress over the months and years to come.”
LOVE OF THE INDUSTRY
Prior to the official publication of the survey, Paul Jones shared key insights at GTL Sessions [p14], highlighting one of the key “resounding positives” of the survey – that “the freelancer community is feeling optimistic about the next 12 months and many feel that the industry is a great place to work”.
Despite the positives, the report also highlighted the concerns of many participants who stated that they simply couldn’t solely work “for the love of the industry”. Reading through some of the statements in the report, many of the concerns seemed to echo those within the gaming industry, where passionate individuals’ mentality of completing a project would be seen as a given without adequate compensation or even realistic time off.
Job security was also a worrying stat, with 38% of participants stating they didn’t feel financially secure for the next six months. Equally concerning was that 56% either disagreed or strongly disagreed that it was easy
to secure a new freelance job, at the time of filling out the survey.
Although the survey was anonymous, respondents had the option to submit their race, gender and age. Although on all three markers around 46% preferred “not to say”, of those that did, 39% were men, 13.6% were women, 0.8% identified as non-binary and 0.2% were transgender. “We have a wide and varied workforce that has become more inclusive but there is a need to further embrace diversity and the entice more people from all walks of life into the sector,” stated Jones.
NO ONE IS AN ISLAND
With two of the key creators of the survey being forums that looked to build community and support one another, it was natural that some of the questioning would focus on wellbeing.
“You might wonder why a mental health support group would want to get involved in pay rates and the freelance experience,” stated Suzi Green within the report. “But a number of issues that we hear in the weekly meeting are played out both in the survey’s data and the comments regarding fair terms of employment.”
She went on to state that “pay security underpins everything” and that “it’s hard to
focus on self-care when you’re not sure if you can pay your rent long-term”.
Green was also keen to highlight that one interesting finding was that half of the respondents said that a “work-life balance was very important,” despite the inevitably inconvenient working hours for a freelancer working in the live events sector.
Security in pay extended to another focus of the report where participants were asked about the issue of show cancellations. It’s a topic that has garnered a lot of mainstream attention with A-list artists cancelling tours due to several reasons from ticket sales to issues with their mental health, but behind these headlines there is a workforce that are suddenly out of work.
Some of the standout figures were that 52% of participants had work cancelled with less than a week’s notice. Several anonymous applications also provided some rather shocking anecdotes such as several monthlong tours being pulled at the last minute while they were on the way to the airport without any warning, and in many cases, without a cancellation fee. The data also highlighted the lack of secure contracts for freelancers with only 5% of those asked saying they “always”
get a signed contract and 46% always getting email confirmation. In fact, 49% said they never get a signed contract.
This research “highlights a significant concern where late payments and a lack of formal contracts can often be normalised in the freelance community,” stated Darren Woolnough of Handle Freelance Solution. “From cancellations to the need to increase the ease and availably of job roles, there are no
simple fixes, but we hope that this survey also provided additional insight into the many things that can be controlled.”
RATES
The last major section of the survey focussed on the complex world of rates. From the outset of the section, the authors of the survey acknowledged that this was a complicated issue with multiple variables, but that it was vital
“It sets a benchmark for our industry. One we will use to measure progress over the months and years to come.”
Jon Collins, Chief Executive of LIVE
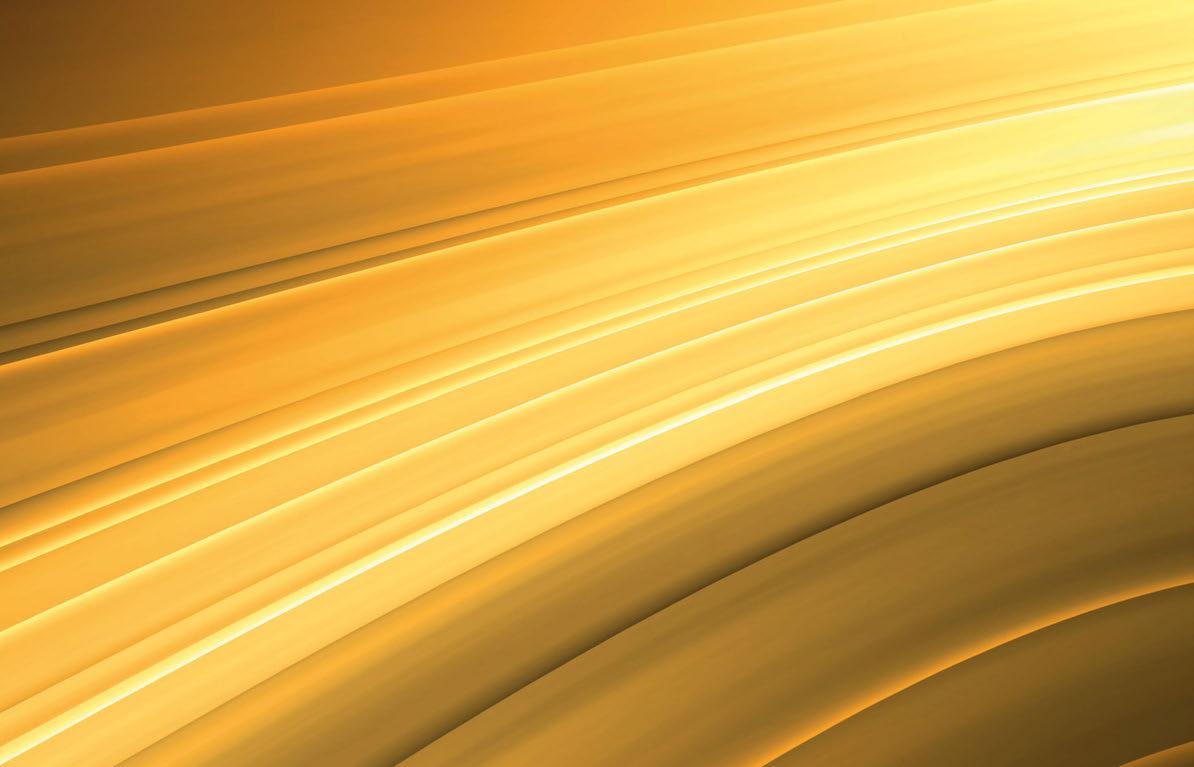
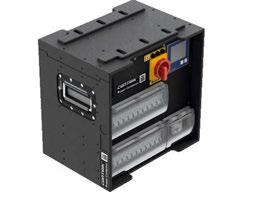

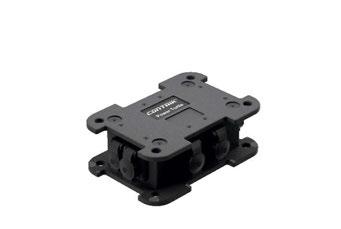
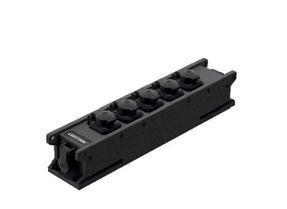

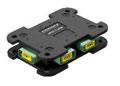
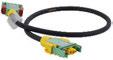

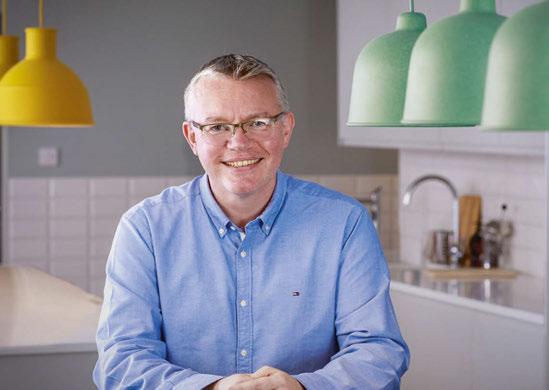
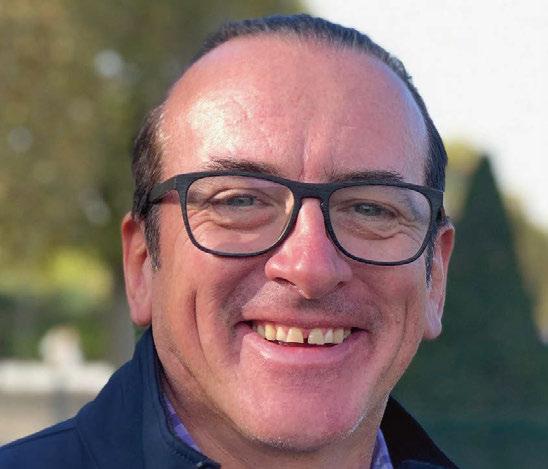
to have a more defined sense of what rates are being charged for various jobs.
In t he opening to the rates section, the authors spoke of the overall trends discussed in the market with the anecdotal conversions of rates increasing during the summer of 2022 due to the shortage of crew before plateauing in 2023 and 2024. “This could be down to a break in touring cycles, an increase in cancelled festivals or a steep rise in touring costs,” the authors suggested. “The reason to shine a light on the current rates is so that we can benchmark where we are as whole and enable us to track future fluctuation,” they stated. It also seems like a very valuable piece of research as the industry has been calling out for a need for younger generations to join the sector, and giving those looking for a career a realistic aspiration seems necessary. As well as giving a breakdown by position and sector in the market, the rates section also invited participants to discuss some of the terms of their employment. Interestingly, 24% said even when asked to get paid overtime that they never get paid for this work, while 30% never renegotiate if the job is bigger then expected.
NEXT STEPS
With such a great deal of information, the authors summarised three key areas that the community should be focussing on: contracts
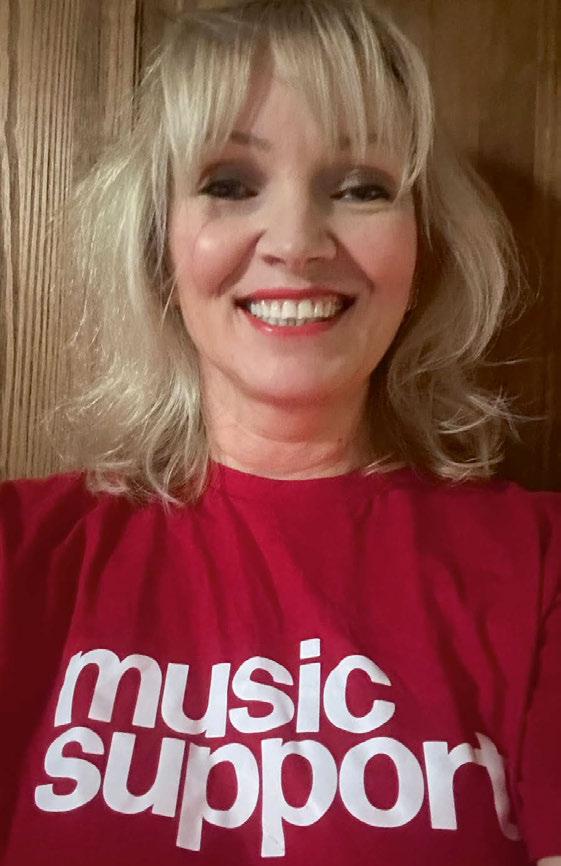
and cancellations; recruitment and securing job roles; and age and gender. “As a collective, we will be taking all the learnings from the report and funnelling them into the objectives of the LIVE Workforce,” the report concluded. The LIVE Workforce is a group of expert industry practitioners alongside ED&I and workforce specialists that looks to positively impact the current and future workforce of the industry. “Across this report, and with a focus on the three key areas identified, we will work as a collective to deliver positive resolutions to all.”
“T he report has certainly sparked a few ideas for the future,” stated Green, evaluating the lasting impact of the survey. “One is a possible charter for best practice and to create amendable terms and conditions that anyone can download and amend then share via email post verbal agreement of work.”
Reading through the paper, it was interesting to quantify so many parts of the live events industry that up until this point could only be garnered from hearsay. It makes sense that for the industry to move forward, certain assumptions are agreed upon. There is little doubt that as well as giving the authors something to work from, this report will also make some waves in the sector. Powered by Freelancers – the Live Music Edition 2024 is available to read at: www.livemusic.biz
LIVE CEO, Jon Collins; Founder of Ethix Management and the UK Live Events Freelancers Forum, Paul Jones; Tour Manager and Founder of The Back Lounge, Suzi Green
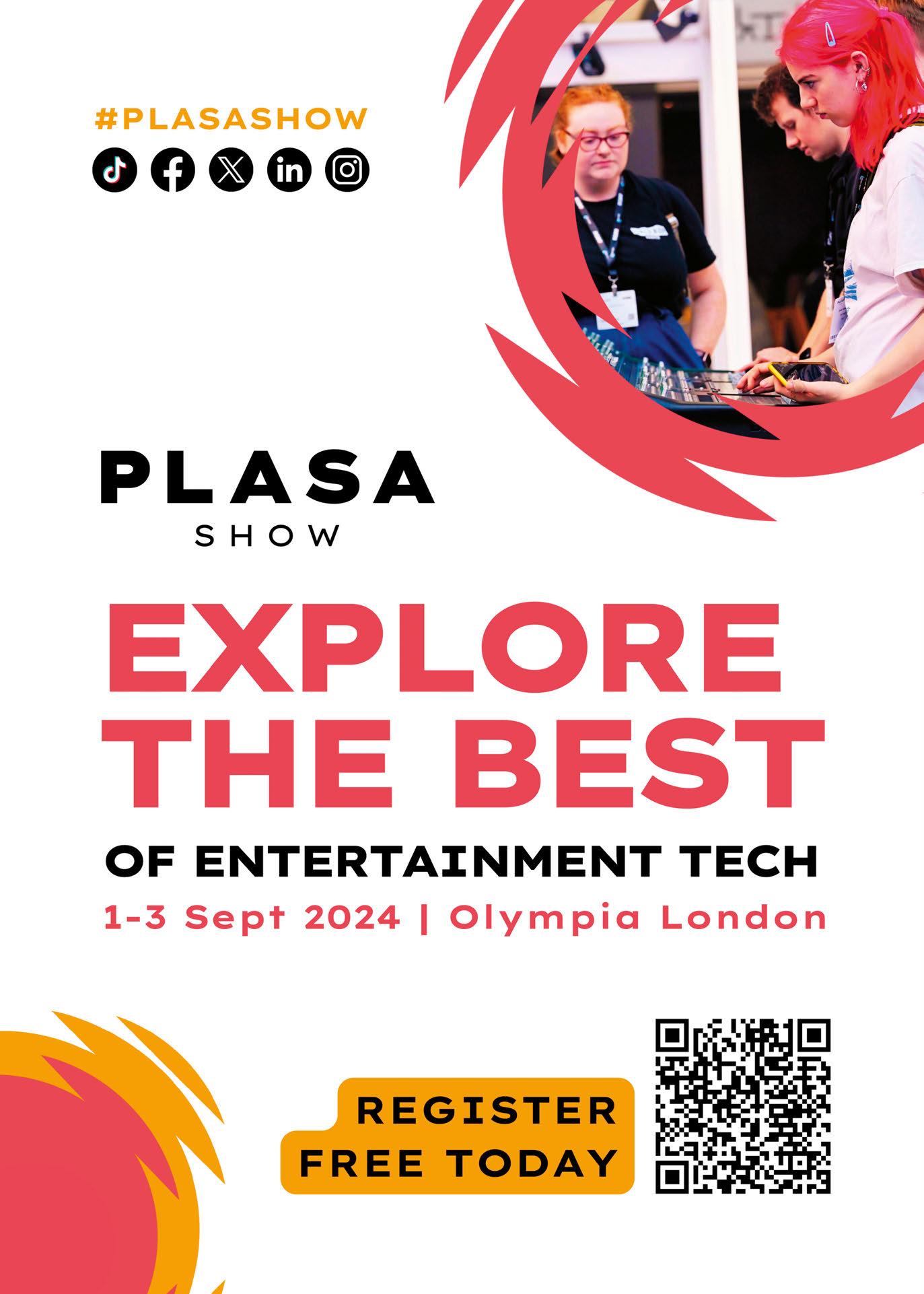
INTRODUCING: THE ECO2JET
Following the launch of a brand-new sustainable CO2 alternative for live events, TPi checks-in with MAGIC FX CEO and Founder, Bram Veroude to discover more.

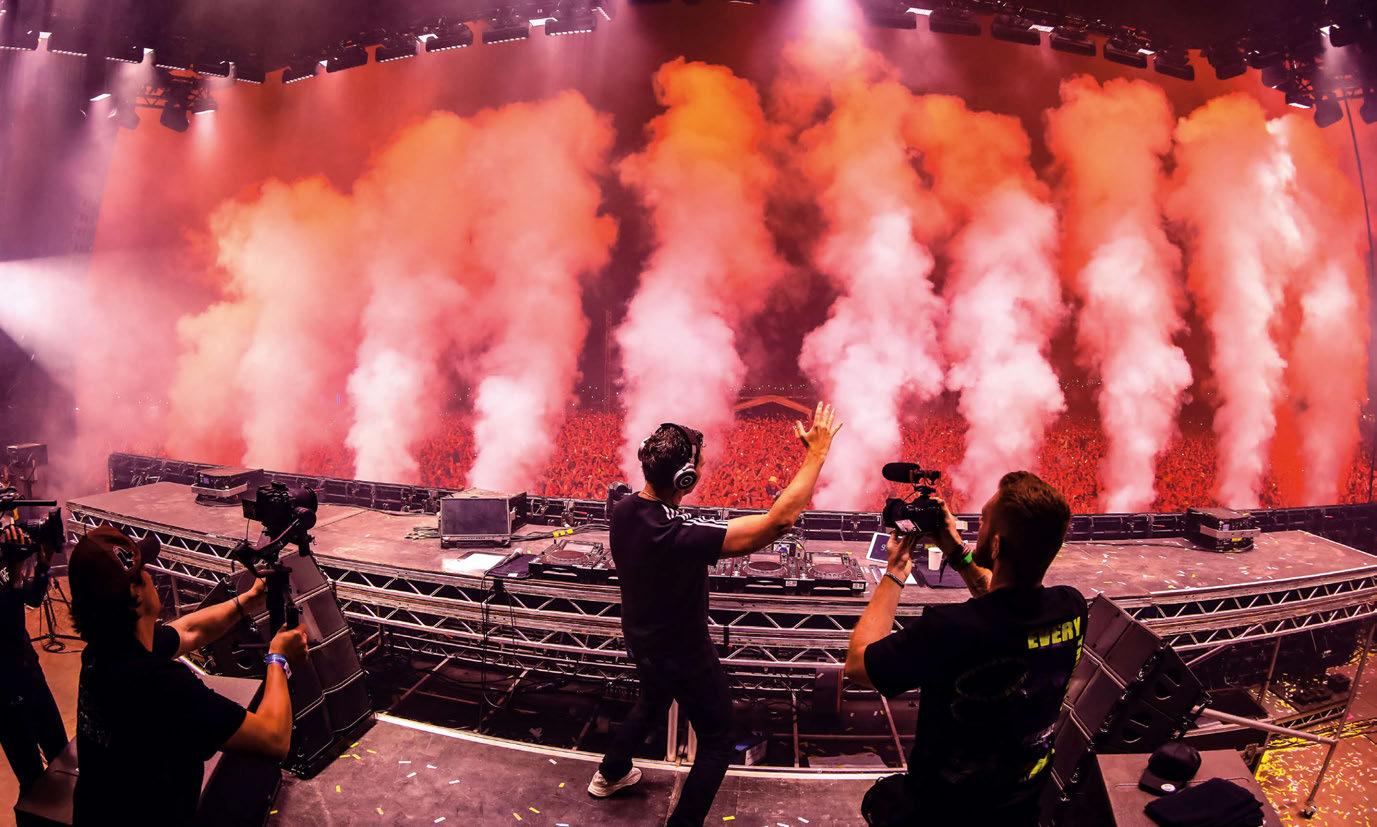
Despite becoming a very popular effect in live events from EDM to rock, the CO2 blast or cryo jet has been the subject of significant backlash due to its environmental impact and the rising costs of gas. To counteract this, the team at MAGIC FX has created a more environmentally friendly, cost-effective solution – the ECO2JET.
“Resistance to the use of CO2 has certainly increased and we know about the problems with space and installations around stages when using CO2 bottles,” began MAGIC FX’s Bram Veroude. “We’ve seen the popularity of the SMOKEJET grow as an alternative, but the smoke effect cannot compete with the speed and impact of CO2.”
With its compact size, the ECO2JET’s high-speed turbo fan and powered white smoke effect creates an authentic CO2 blast look. MAGIC FX has also developed two different fluid types – one for indoor and the other for outdoor use. “The special smoke liquid is created from distilled water and creates a thick white smoke effect that disappears quickly, just like CO2,” said Veroude. “One 5l can of fluid can create 13 minutes of effect – the equivalent to 13 large CO2 bottles,” he stated proudly, emphasising the cost-saving possibilities the ECO2JET offers.
“The other real innovation has been with the high-speed turbo fan combined with a custommade nozzle, which ensures the smoke is blown into the air at tremendous speed.”
According to Veroude, this ensures the effect is as powerful and explosive as CO2. “It’s what really sets it apart from other smoke machines on the market,” he stated. Veroude
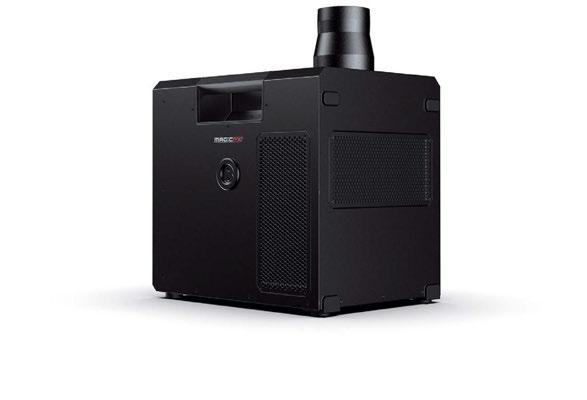
explained how the ECO2JET performs better in low humidity than CO2. “The smoke effect does not depend on humidity,” he stated.
“It’s consistent no matter the circumstances. For example, at an outdoor festival when the sun is shining, the smoke for the ECO2JET still reaches 12m compared to CO2, which would top out at 4m.”
Another advancement that has been cited by users who have already got their hands on the product has been the volume of the fixture. With a lower output noise of 95dB compared to a CO2 jet of an average 115dB, the ECO2JET “significantly enhances the overall show experience,” stated Veroude.
Before hitting the market, the ECO2JET was seen on some major stages including Tomorrowland, Creamfields, Lollapalooza and the Eurovision Song Contest. MAGIC FX has
certainly been pleased with the response. “The events industry has really welcomed this product with its revolutionary effects.”
The ECO2JET marks yet another product release highlighting MAGIC FX’s commitment to sustainable effects. “The ECO2JET is more environmentally friendly than CO2 and it eliminates the need for CO2 gas cylinders thereby reducing their contribution to the greenhouse effects,” stated Veroude.
“The product also eliminates the need for dangerous goods handling and heavy transport, leading to lower CO2 emissions. After introducing the world’s first TÜV-certified biodegradable confetti last year, this MAGIC FX product is a real game-changer for the events industry and the next step in making special effects more sustainable.”
www.magicfx.eu
Words: Stew Hume
Photos: MAGIC FX
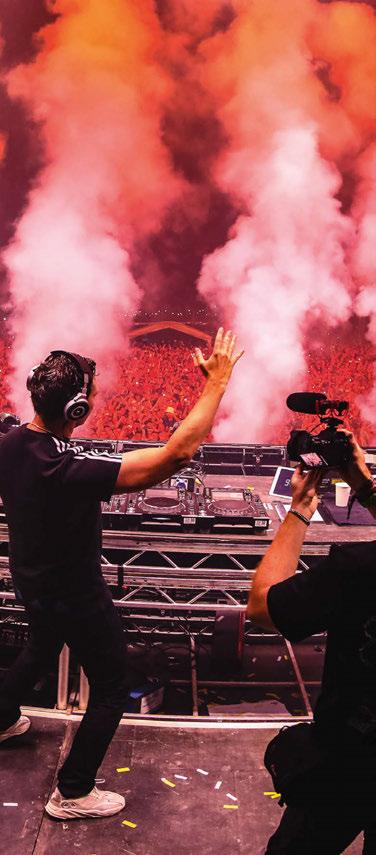
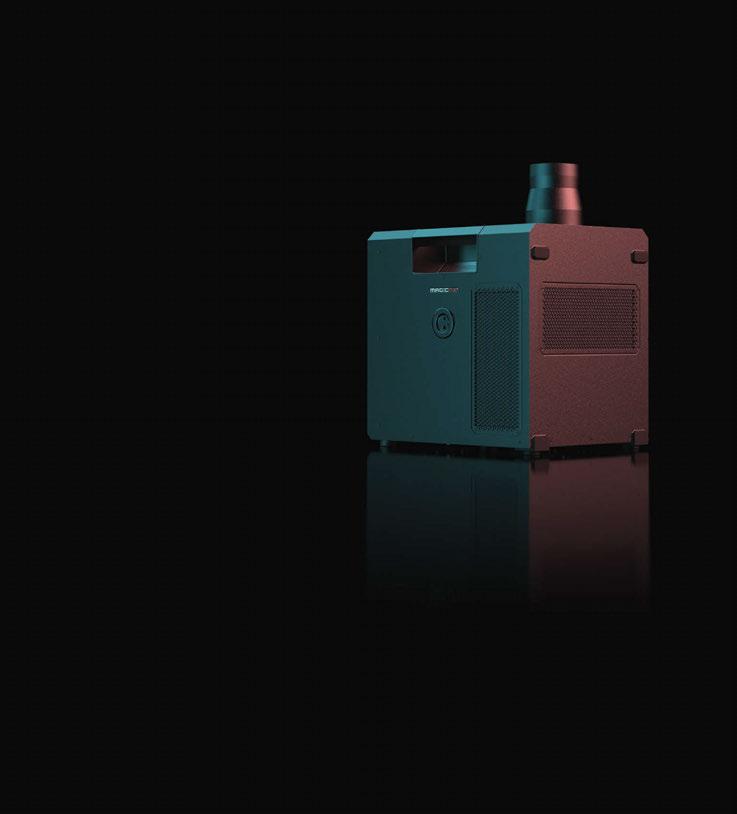
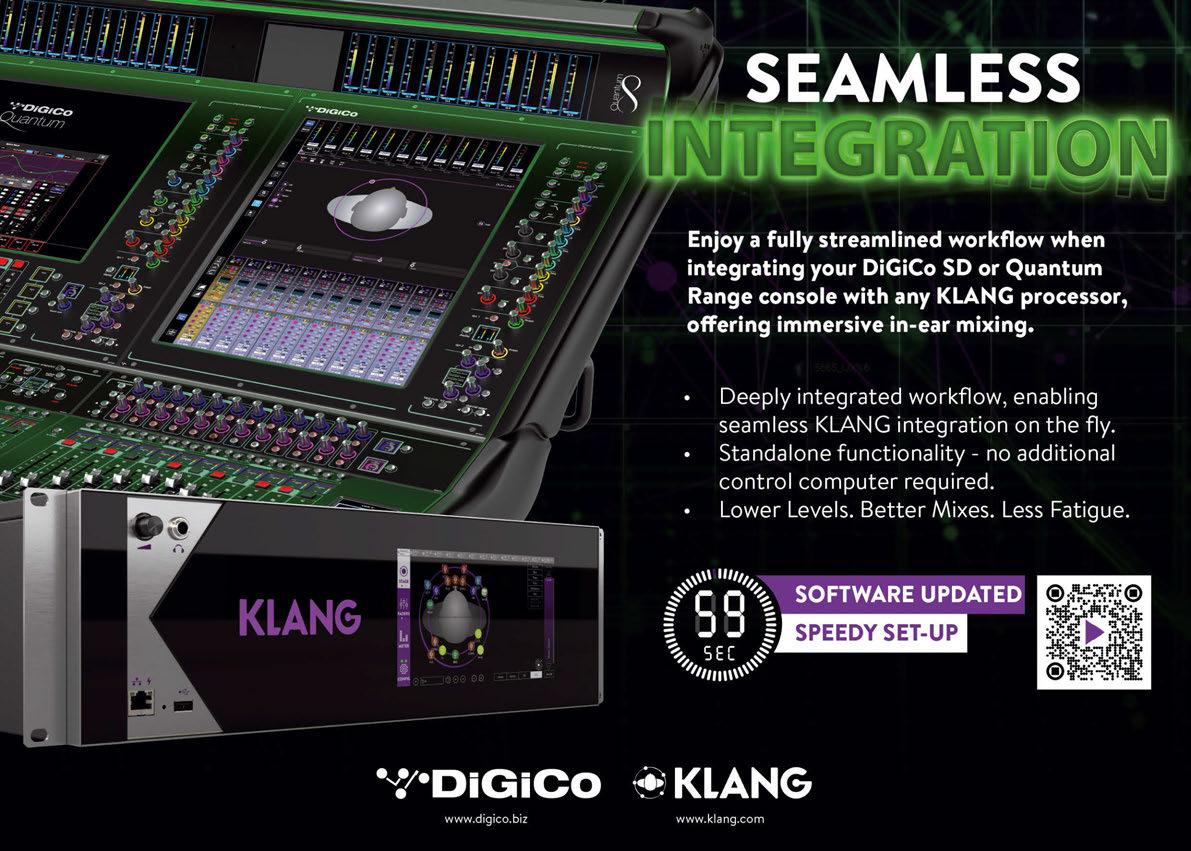
VECTORWORKS ENTERS THE WORLD OF AUDIO
Tom White from Vectorworks discusses the company’s latest collaboration with L-Acoustics to seamlessly link the worlds of CAD and acoustic simulation software for a more collaborative workflow.

Words: Stew Hume
Music, Film & TV



Too often, in the build-up to a show, once the designers and riggers have completed their tasks, the audio team will then go about remodelling CAD drawings to start their audio simulations. However, with Vectorworks 2024 Update 4, this process is going to be simplified thanks to a new collaboration with the team at L-Acoustics. With the Export to Soundvision feature, users can transport their models straight into Soundvision from Vectorworks in the latest version of the software.
Talking t hrough t his latest offering was Vectorworks Senior Solutions Specialist, Tom W hite. “ We’ve been speaking to several audio manufacturers for a long t ime to look at this t ype of integration w ith Vectorworks,” began W hite. “L-Acoustics was t he first company t hat began working on this and after just a few months had a working version.”
White went into a bit more detail about w hat t his collaboration means for end users. “Once you’ve got a f ull design w ithin Vectorworks, you c an export both simplified and extremely complex plots straight into Soundvision. This includes exact geometry, w hich leads to more exact calculations. ‘ Listening planes’ enable you to assign w here the audience at a show w ill be. You w ill soon be able to assign objects w ith a specific class’.”
The linking of t he t wo workflows also has a major benefit for t he designers using Vectorworks. “ You c an show the pictural renditions of t he SPL (sound pressure level) calculations t hat have been done in Soundvision, w hich is beneficial for show designers w hen determining w here audience members w ill be in a venue,” W hite noted. Although t his collaboration has been done w ith L-Acoustics, W hite explained t hat integration w ith other audio brands is very much on t he horizon. With many audio brands st arting to uniformly use MVR, it’s going to make integration with Vectorworks even easier.” T he team at Vectorworks have received very positive feedback f rom audio rental houses w ho have benefited f rom t his collaboration.
W hite was also keen to highlight some of its other latest developments, specifically w ith Vectorworks Odyssey – t he company’s v irtual reality v iewer app t hat allows users to ut ilise a headset to experience models and stage designs in immersive VR w ith bird’s-eye v iew and walkthrough modes.
“Admittedly, I t hought VR headsets might be a bit of a fad, but the perspective you c an experience w hen you’re dropped into a design is really impactful and a great way to solve problems before setting foot into a venue,” st ated White.
ww w.vectorworks.net
Photo: Vectorworks
Vectorworks’ Tom White
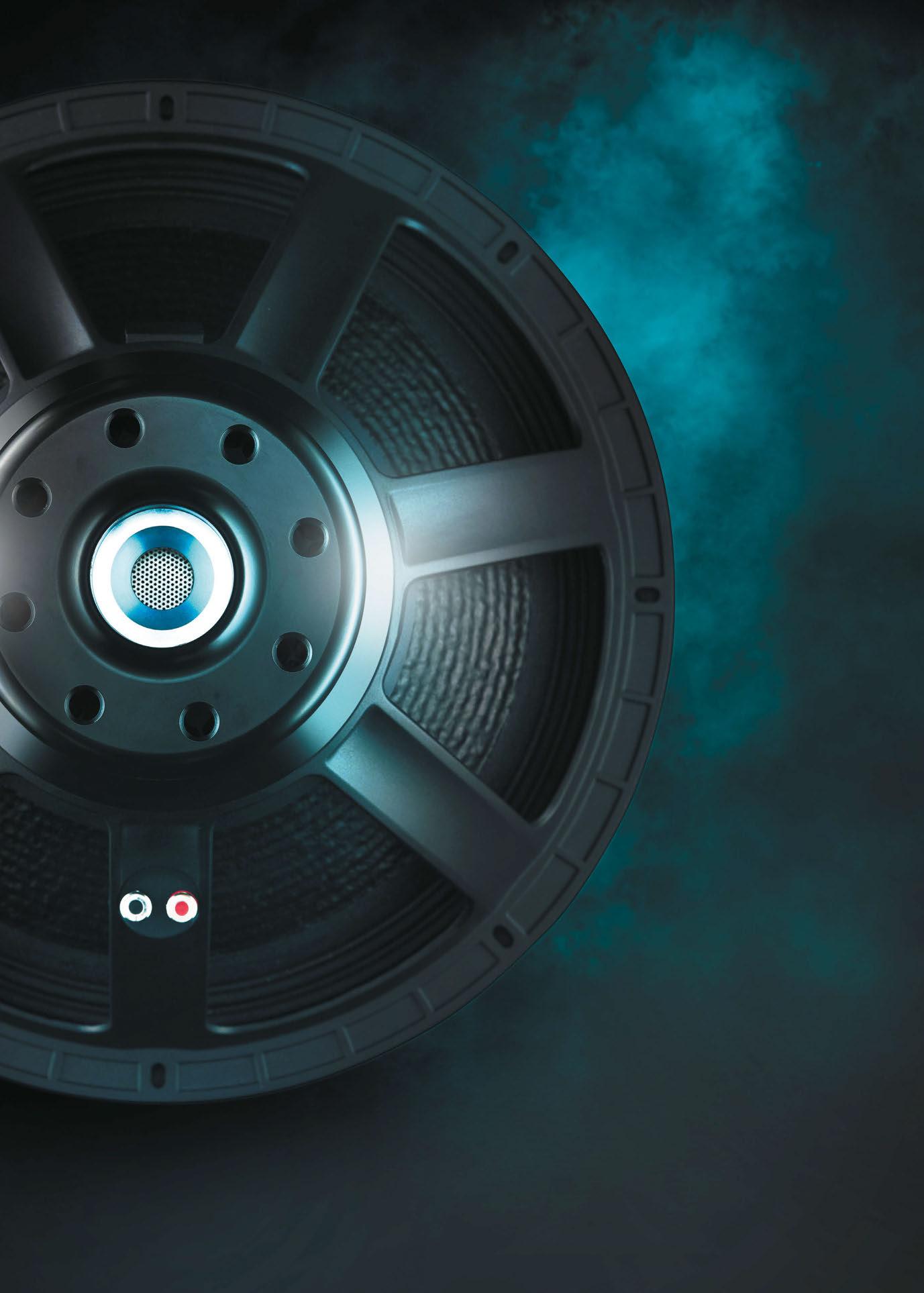
COUNTERACTING COUNTERFEITS
MA Lighting and Avolites underline the detrimental impact of counterfeit products.

Words: Stew Hume
Photos: MA Lighting and Avolites
In 2018, some of the biggest names in lighting control – MA Lighting, Avolites and MADRIX – announced that they were joining forces to tackle the ever-growing issue of counterfeit products. These efforts saw some immediate results, most notably from the Guangzhou Entertainment Technology (GET) exhibition of that year where counterfeit products were taken off the stands of exhibitors with the full support of the tradeshow organisers. This sent a clear message that this blatant wrongdoing was not going to be tolerated. However, six years on, the companies have expressed that this is still a troubling issue within the live events market, and in many respects, the practice of counterfeiting has worsened since the turn of the decade.
“The issue is getting much worse,” asserted Daniel Kannenberg, Brand and Product Management at MA Lighting International. “One of the main reasons for this is counterfeiters have new ways to spread their misleading messages about their copies via social media and other online sales tools.”
He went on to explain that this greater ability to mislead clients with confounding announcements to sell their online exacerbated the problem when the world began to come out of the COVID-19 pandemic and events started up again. “Straight after the pandemic when people were trying to get back on their feet, budgets were understandably smaller and so the low prices these counterfeiters were offering looked appealing at a very superficial analysis,” he explained.
Many of those buying these products did not realise they were not getting the genuine article. “For trying to clean the web from this fraudulent announcements that we’ve
employed an external company to reduce and, in some cases, delete adverts for social media that are promoting the sale of counterfeit products,” stated Kannenberg.
In fact, MA Lighting has a team of six fulltime employees continuingly tackling the complex issue of counterfeiting. “It’s offering an inferior product into the market at a lesser price and, in some cases, users don’t even know it’s a counterfeit,” explained Avolites Managing Director, Paul Wong. “That in turn affects us as that negative experience translates into what people think of the quality of Avolites products.”
Wong went on to explain that the company had spent a great deal of money in recent years to create a secure system for their software.
“It’s why I really make a point that counterfeit is theft,” stated Richard Salzedo, former Chairman of Avolites and now a consultant for the company. “It’s theft of everyone who bought a genuine console,” he added, referring to the investment people make into an Avolites desk that pays off the years of R&D and product innovation. “People also must realise that if they have a counterfeit desk, sooner or later something will go wrong with it and there is no support if it does.”
Having been at the forefront of the battle for a long time, MA Lighting Director of Business Development Franco Zaghini, based out of Singapore, spoke passionately about the juxtaposition between theses counterfeiters and legitimate manufacturers.
“First of all, those buying an MA counterfeit, they are inconsiderate, just basing on the cheaper price, not taking into consideration so many other factors, like poor quality of the hardware and instability of the software used on a counterfeited hardware, thus putting on
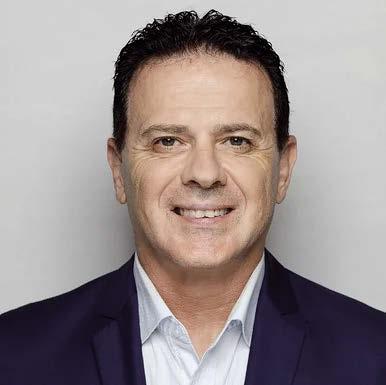
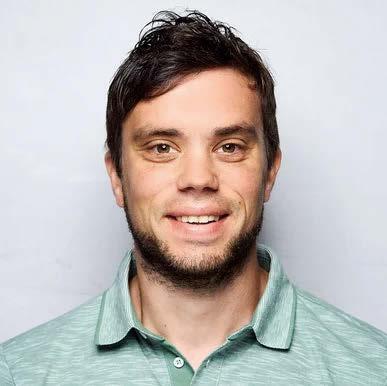
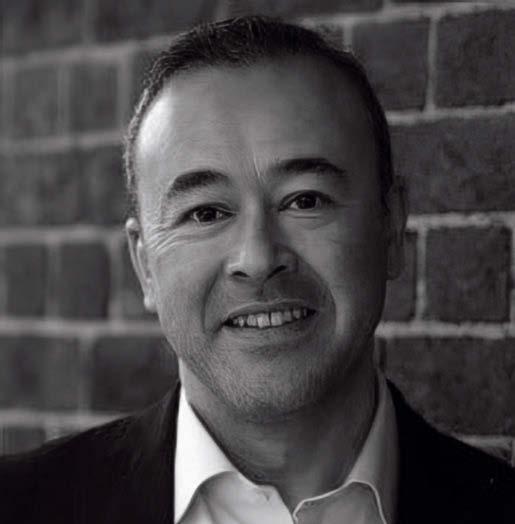
MA Lighting Director of Business Development, Franco Zaghini; MA Lighting Brand and Product Management, Daniel Kannenberg; Avolites Managing Director, Paul Wong.
serious risk the entire show along with the reputation of the lighting designer and the company in charge,” Zaghini said.
“The other aspect to consider is that counterfeiting is a crime worldwide and has no respect for any standard including human rights and child labour, not to talk about nature and environment, compared to companies like MA that have a strict code of conduct in compliance with International rules and laws.”
Zaghini also made the case that the value of a counterfeit desk is equivalent to zero with a significantly short lifespan and no support available when things go wrong. “We guarantee spare parts to be available five to 10 years after end of life of any desk along with 24/7 support for any buyers of legitimate MA Lighting desks.”
MA Lighting has been directing a lot of resources in spreading the awareness of counterfeit to both its distributors and end users. “This does not only affect us at MA or other manufacturers but first of all the users of these products and the entire industry,” he underlined. “You have people using these fake products and sometimes they don’t even know, which runs the risk of destroying the show.”
A lot of the interactions with this issue come through MA’s technical support team when
a user calls up with an issue with the desk and after several questions, it’s clear that the product they are using is not a genuine MA Lighting console.
“The first step in that scenario is to make that person aware of the situation and more often than not we will have success,” stated Kannenberg. On the other hand, he admitted that some end users might be more than aware they are using counterfeit products and, in that case, MA might consider legal action – again something the company has continued to invest in recent years.
Having united in the past on this topic, Avolites and MA Lighting agreed that collaborating with others in the field was one way in which the industry can take a stand against this rising tide. “The fight will be more efficient the more people are involved,” stated Kannenberg. “We would love to see more manufacturers join this active fight rather than just reacting.”
As far as advice to end users, according to Kannenberg, if you are ever unsure if a product you come across is counterfeit, contact your local MA support team. “All our distributors can help, and they will be able to explain the next steps. We also have a dedicated email address
– legal@malighting.com – where people can send over documents and queries about this very topic.”
Zaghini added: “We are extremely thankful to those lighting designers and operators who have been cooperating with us to limit this cancer in our industry.”
Wong commented: “In Europe and North America there has been a wide amount of support from users that will call out counterfeits. However, in Asia and South America, we often see the greater issue of fake products. The goal is to change the perception of counterfeiting, but it will take some time to turn that ship around.”
According to Avolites’ Andrew McKinlay, this ambitious mission will only be changed if everyone within the industry works together. “Manufacturers alone can’t do everything that is needed to fix this problem. The whole industry must want to get rid of them.”
In closing, Kannenberg explained that MA Lighting will be rolling out a campaign in the coming months to further highlight this issue in the industry, which will no doubt be a talking point for the autumn and winter trade shows. www.malighting.com www.avolites.com
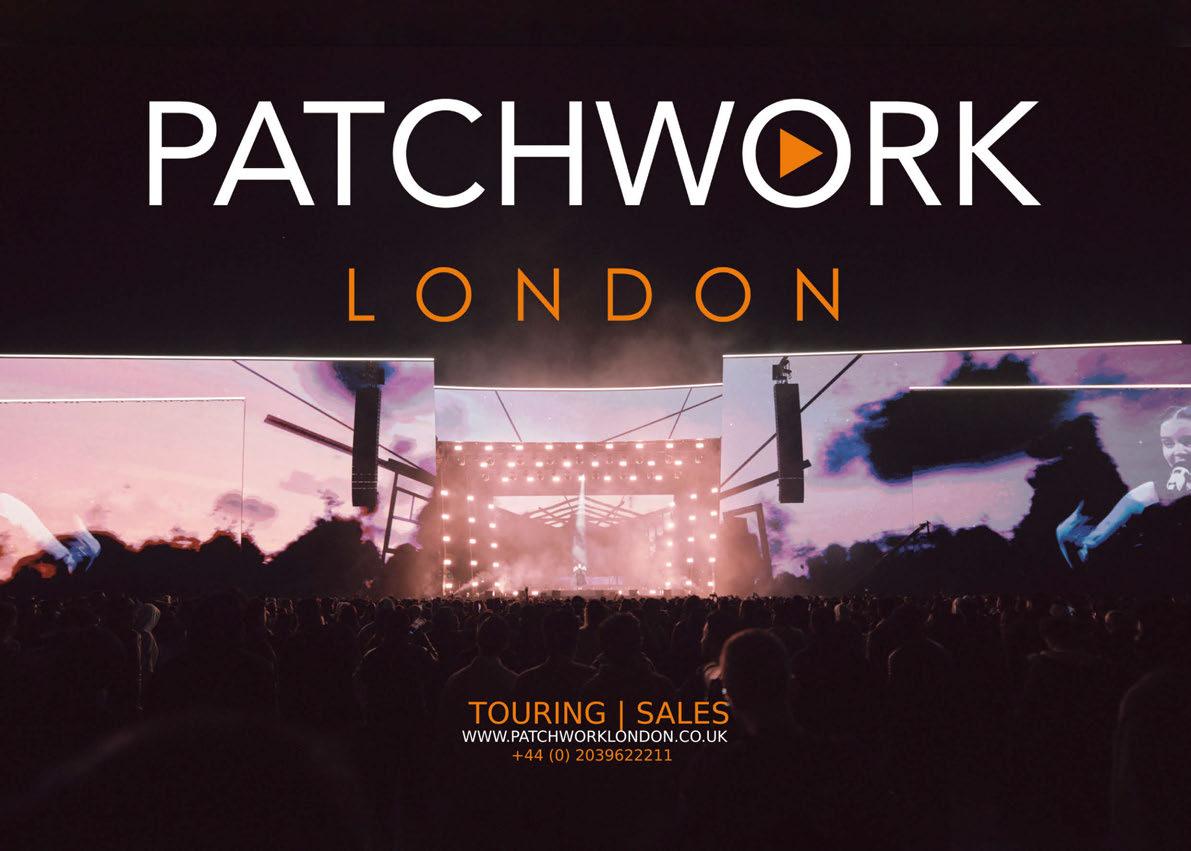
INNOVATION WITHIN LIGHTING
Claypaky Product Portfolio Manager, Giovanni Zucchinali tackles the topic of innovation and what the term means when it comes to product development.

Words: Stew Hume
Photos: Claypaky

The term ‘innovation’ is often thrown around in quite a blasé manner along with ‘highend’ and ‘cutting-edge’ on countless new product releases and at various tradeshows throughout the year. However, to the team at Claypaky, the term is taken very seriously. In fact, behind the walls of the manufacturer’s Bergamo HQ, Claypaky even has an entire team whose sole focus is innovation. To learn more, TPi caught up with Product Portfolio Manager Giovanni Zucchinali.
“M y role is all about market intelligence, analysing the market, innovation trends and gathering insights from customer feedback and requests. I’m the connection between R&D and our sales department,” he began, explaining the part he played in the Claypaky machine.
Having an intimate knowledge of the company’s product development, Zucchinali explained how innovation is integrated into the process of bringing new lighting fixtures to market. “For us, innovation is all about finding a solution for the market,” he mused. “Innovation when it comes to just a new technology is meaningless unless it is helping an end user – in our case a lighting designer or rental house.”
To give working examples of implementation of innovation, he looked back to 2010 and the release of the Sharpy – at the time a radical new concept that left a real impression on the industry, with the fixture using just 189W of power to produce an intense, laser-like beam, bright enough to rival far larger, higherwattage fixtures. “It changed how people began designing shows, with many designs focusing on the ‘beam’ look,” he recalled, noting that
much of the innovation came not only from the output and effects of the fixture but the level of control it gave.
“Take the B-EYE release in 2013,” he added. “It was not only the eye-candy effects it produced but the way we were giving control of the lights – a vital innovation due to the number of products that were deployed on show. With so many pixels, lighting designers need to be able to control things very quickly. It was this aspect that showed real innovation.”
Another highlight for Zucchinali which showed innovation in practice was the recent use of liquid cooling with its FLOW Technology. The use of FLOW reduces fixture size, lowers noise levels, and increases efficiency, making it an ideal solution for theatres and TV studios. This technology has already been implemented into the ORKIS CYC.
Although the Claypaky innovation team are continuingly working on new solutions, Zucchinali explained that the real trick was determining which of these innovations should be implemented into any new product. It’s where his personal role of being a middleman between market demand and R&D is so vital. We need to focus more on innovation alongside other services beyond just the production, including support, service and spare parts. It’s these key areas that differentiate Claypaky from other brands.”
It was clear from speaking to Zucchinali that staying ahead of the curve of imitation products is another challenge the company must deal with continually. “The Volero Wave was something special but then six months

Claypaky Volero Waves feature in an electronic music show designed by LD Christian Jackson; Claypaky Product Portfolio Manager, Giovanni Zucchinali.
later there were copies on the market,” he stated. “This raises the other hurdle with the challenge of protecting patent and the huge effort in pursuing any legal means on someone who has infringed on your patent.”
Looking to the future, Zucchinali predicted where some of the innovation department would be focussing their attention. “Lasers as a lighting source is one of the big conversations right now,” he stated.
Claypaky was first to market when it came the use of lasers within the moving head fixture with the Xtylos – a compact beam moving light that makes use of a tailor-made RGB laser source. “There was a lot of learning with the Xtylos with more safety considerations to bear in mind,” stated Zucchinali. “The cost of these types of fixtures will decrease in the years to come, which will lead to more conversations about the use of lasers over LED.”
Last year, Claypaky introduced the Skylos, a white laser light sourced fixture that comes from
the searchlight tradition but has an incredible list of features that make it versatile in every respect, also highly appreciated in the touring sector. With a maximum energy consumption of 900W, Skylos has the same light output as a 4kW xenon lamp, in line with the sustainability philosophy adopted by Claypaky.
He also explained that one of the other main considerations for his team is the firmware development as well as improving the mechanical capabilities of the fixtures.
“It’s all about matching up the roadmaps of the innovation department and the product development team,” he stated. “Claypaky must keep looking forward as this is where we’ve always been, and innovation is very much part of this conversation. We have already pushed LED to its limit in terms of output and that means focussing on other aspects such as more intelligent software – all of which will solve issues that are important to our customers. Just think of the work we have done on the
firmware of Sinfonya and Rhapsodya, two products designed specifically for the theater market: they both incorporate AccuTune, our in-house firmware algorithm, ensuring precise control over the multicolor LED engine. This delivers vibrant, high CRI, and high-TLCI light optimized for both stage and TV. The simplicity of operation saves valuable time ensuring the uncompromising quality.”
Claypaky has also entered the digital age, being the first company which introduced Internet of Things and Cloud-based services into the Entertainment Lighting industry - with CloudIO - a solution for the remote maintenance and Buddylight, a brand-new automated followspot system.
Claypaky has a dedicated tab on its website that focusses on the work of the innovation arm of the business, highlighting some case studies and product releases and presenting some innovative solutions for the end user.
www.claypaky.it/en/innovation
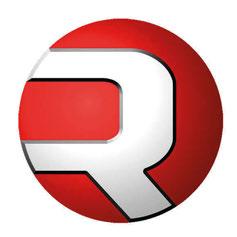

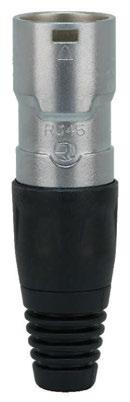
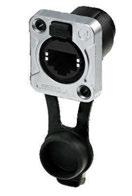

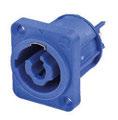
A NEW ERA FOR MARTIN PROFESSIONAL
An inside look at Martin Professional’s redeveloped Hungarian factory and how the lighting manufacturer is making leaps towards sustainability and gradually evolving its products…

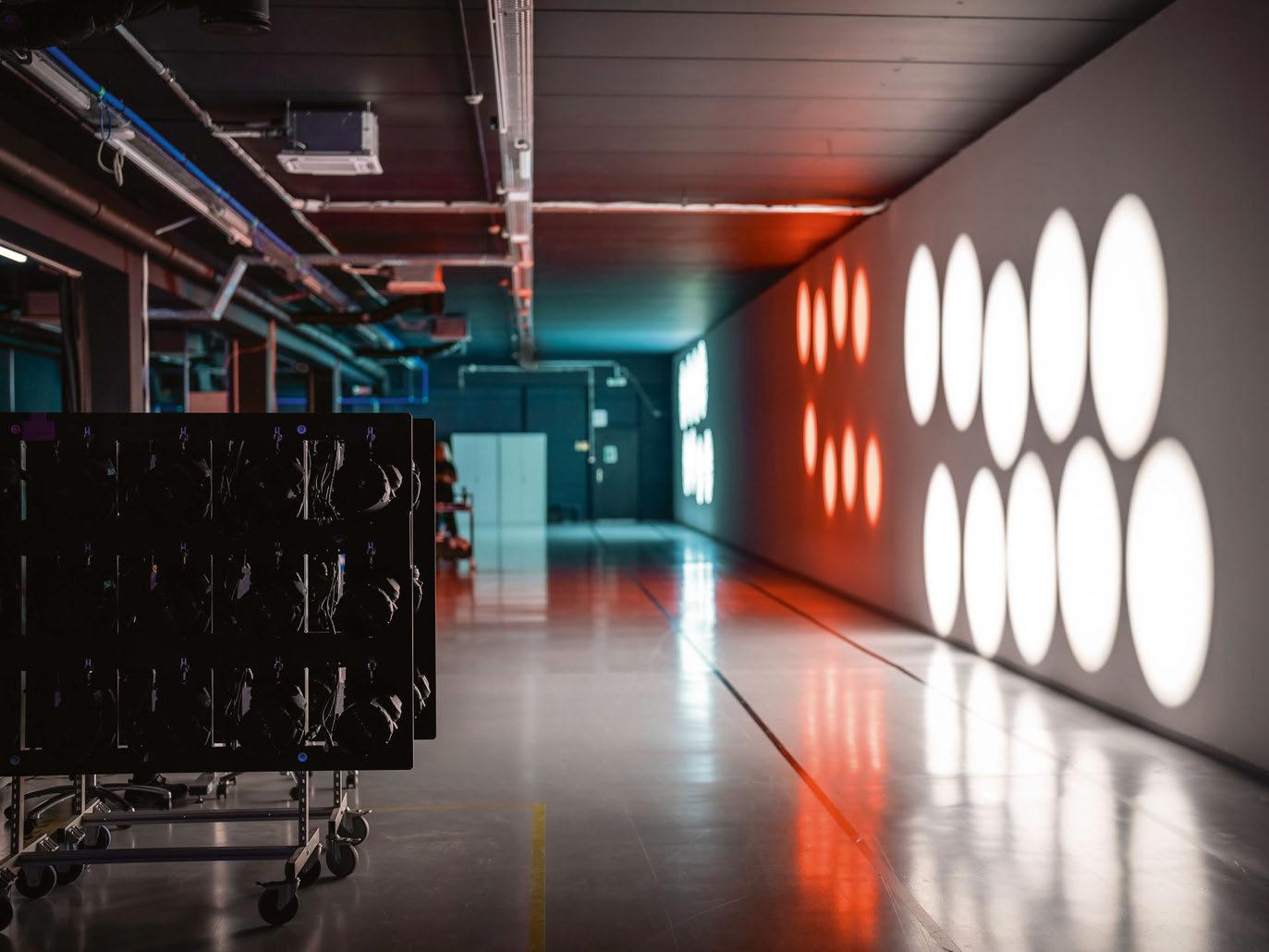
Following its complete renovation and reopening in November 2023, TPi was invited to Pécs, Hungary for a complete tour of Harman Professional’s dedicated Martin Professional space to get an insight into the freshly streamlined operation along with hearing how the company looks to reach its goal of carbon neutrality by 2040.
TPi was greeted by Martin Professional Senior Manager, András Dobre; Product Manager, Henrik Kristensen as well as EMEA Sales Director, Ben Payne, at the gates of the Pécs factory. The facility is situated over 100 miles from the Hungarian capital and has been the regional home for Martin Professional for several years. The factory’s facelift took eight months to finish and the facility now offers a streamlined operation, with the factory in full production during the visit. It’s also the only factory in the HARMAN Professional collective that focusses entirely on Martin Professional products and development.
BECOMING INCREASINGLY ENVIRONMENTALLY CONCIOUS
For the new factory, HARMAN modernised the more than 107,000 sq ft manufacturing facility to enable the lighting brand to heat and cool the facility with geothermal energy
using a water-to-water heat pump. Electricity for the whole facility will now be sourced via onsite solar PV panels, introduced in 2024, with the company anticipating a reduced electricity consumption of up to 15%, aiming to reach 100% renewable energy in all HARMAN factories by 2025.
“O ver the past six years, the Martin brand put into production more than 20 major LED lighting product SKUs with more new products being announced soon. It’s imperative that we not only create more space to meet demand but do so responsibly and in line with our corporate goals,” said Brian Divine, President, HARMAN Professional Solutions.
“The completion of this project is proof to our customers that we produce reliable products in technologically advanced facilities while doing so with reduced impact to our environment.”
Touring the factory, TPi discovered that 99% of the waste that the factory creates is used and recycled in the compression area with clear signposted bins for the 300 staff employed in the factory.
Sustainability is not a new topic for Martin Professional, with the company bringing in a third-party company to do a life cycle assessment of the MAC Aura XIP, which was released in 2022. This dedication to bettering
its practices was to ensure the company had access to more metrics surrounding sustainability, meaning that the data provided could then be used against all future products under the Martin Professional name.
Consistently striving to better its sustainability practices, HARMAN Professional has signed the climate pledge to meet the Paris Agreement 10 years earlier than outlined. The company is working toward shorter-term, measurable targets that aim to reduce its carbon footprint while being able to track the improvement due to small and often initiatives.
Operating under the HARMAN Professional umbrella, Martin Professional is contributing to its wider sustainability efforts and goals, especially within its new site in Pécs but as a whole with operational emissions decreased by 13% from 2019 to 2022, to which HARMAN commented: “Members of our manufacturing teams in our factories globally have been instrumental in reducing our impact.”
FURTHER PRODUCT INNOVATION
Significant effort has also been put into the hiring process for the Pécs factory, with recruits going through intensive training exercises that can take from six months to a year to ensure the standards that Martin
Words: Alicia Pollitt
Photos: Martin Professional
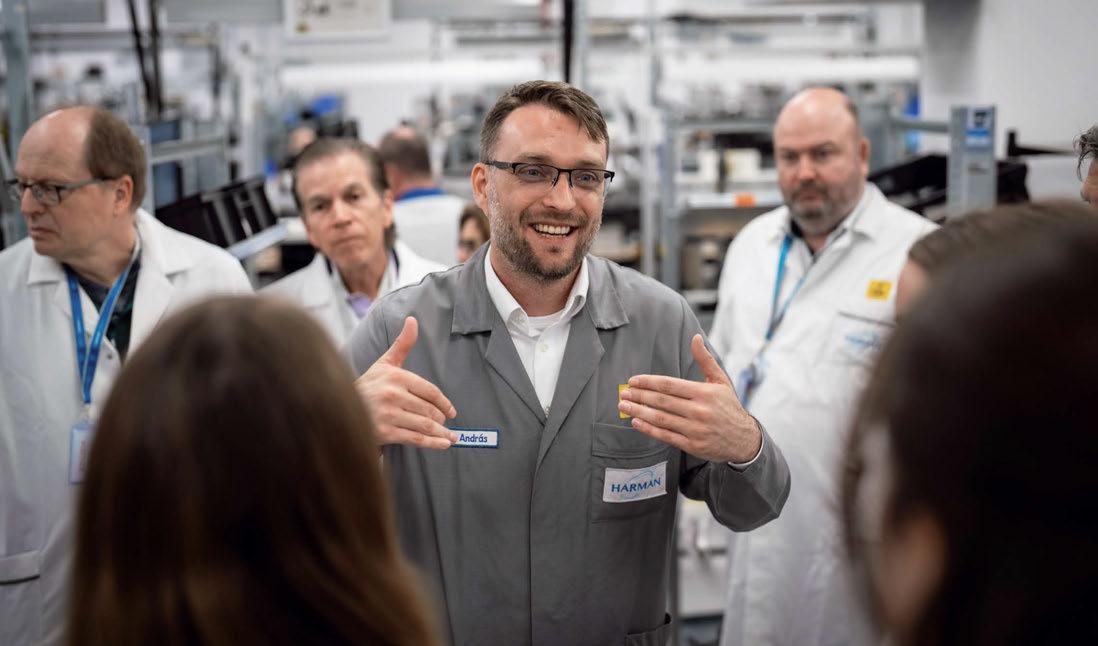
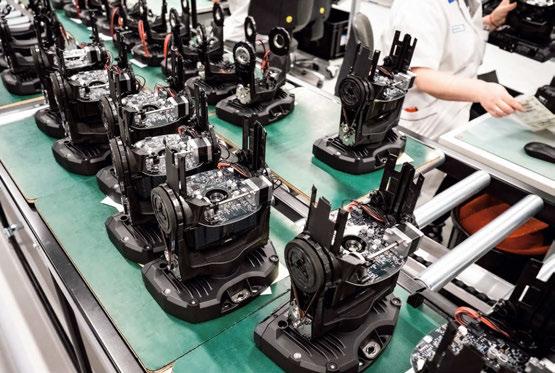

Professional sets for its fixtures are met. Dobre emphasised the importance of the conscientious training process: “We have to focus on the people to get the best performance – out of both the staff and the products,” he said.
The brand’s factory produces 5,500 products a month including its new MAC Viper XIP, which takes six-and-a-half hours to build. For each fixture that is created in the factory, 75 different compliance, reliability and performance verification tests are undertaken to ensure the longevity, safety and sustainability of the products manufactured; tests include extreme heat and cold climate tests to be able to battle with outdoor performances, EMC Emission compliance tests, electrical evaluation and field tests among many others.
With the new plant seeing a 40% increase in capacity from its previous site, it can hold 3,800 pallets of parts for its moving heads with ease, the entire refurbishment was finalised without any business interruption.
Focussing on the lifespan of its products, Martin Professional has made a significant effort in developing product features with the MAC Viper XIP, being its most feature-rich fixture yet. The XIP technology makes this
feature 1.5kg lighter than its predecessors and offers a reduced consumption of energy as well as fewer materials and resources.
Cr ucial to its development and dedication to less waste is the rigorous testing stages of the fixtures. Featuring three main test phases; burn-in, which sees each product feature be tested for 3.5 hours to check every mechanical function, and colour calibration, for uniformity between products and visual inspections where it is checked for a final time.
Finalising its process in the Pécs factory, the fixtures move to the shipment line where the products are shipped directly to customers and distributors worldwide in cardboard packaging that includes a SIP insert that can fit directly into a flight case, resulting in no waste and directly recyclable packaging.
With ambitious proactive sustainable missions, certainly Martin Professional is not slowing down its development when it comes to innovation with the Pécs facility being a clear example of this.
With a busy of summer of festivals a stadium shows, TPi is sure it will come across the Martin Professional brand on many a lighting plot in the coming months. www.martin.com www.pro.harman.com
András Dobre speaking to visitors amid the tour; Henrik Kristensen highlighting the varying elements of Martin Professional products.
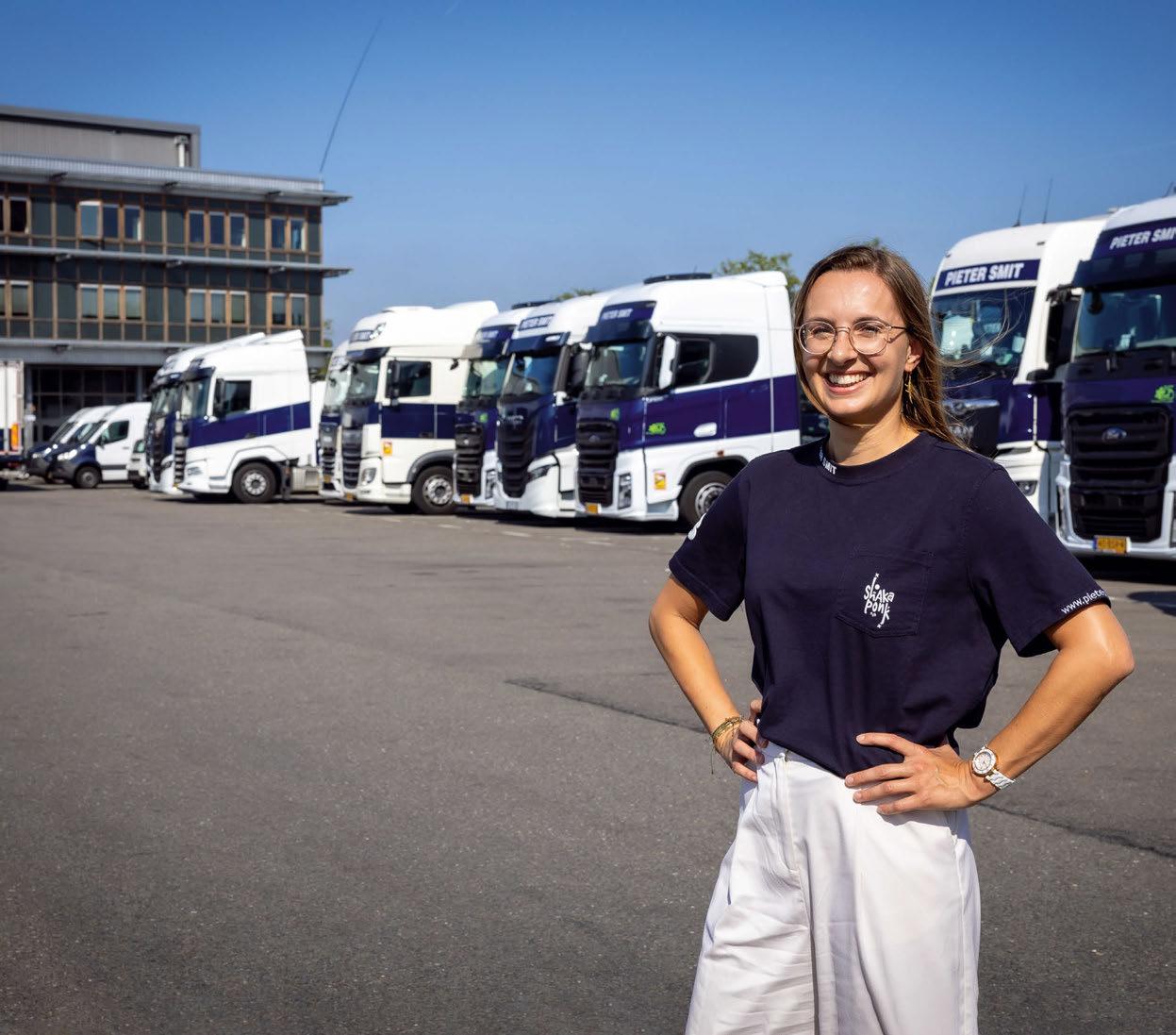
A NEW ERA FOR PIETER SMIT
Pieter Smit’s new CEO, Louise Smit, discusses taking over the reins of the family business and shares her plans for the future.

Founded back in 1980, Pieter Smit’s eponymous logistics business has gone on to be one of the most recognisable trucking companies within the live events sector. With bases throughout Europe including the Netherlands, Belgium, France, Germany, Portugal and Poland, the company has been responsible for ensuring that everything from theatre productions to stadium-sized tours get from and to venues on time. Although perhaps most known for its trucking solutions, the company also has a fleet of rental cargo, splitter vans and nightliner busses along with offering rehearsal spaces for academy-level acts and storage facilities for their equipment. In short, it’s a one-stop-shop for many a production’s needs.
Having dedicated over four decades to the growth and development of the company,
Pieter Smit has opted to step back from the top role to pave the way for his daughter, Louise Smit. TPi caught up with the newly appointed CEO to see how she’d been enjoying the first six months in the new role and how she hoped to continue her father’s legacy. “While I was studying law and thinking about my next move, I spoke to my father about spending some time working for Pieter Smit just to give me an idea of business,” reflected Louise.
“T he family company is the third child in the house, it is like having an older brother. So with my father getting older, it only seemed right to learn a bit more about the company, but five years later I’m still here,” she laughed, while speaking of how much she had enjoyed her time at the company. “My father has always been very entrepreneurial and free spirited. Although we had planned for a more gradual
Words: Stew Hume
Photos: Pieter Smit
Pieter Smit CEO, Louise Smit.
handover process, he essentially gave me free rein to find my feet,” she explained.
Despite the changing of the guard, Louise stated how one of her main goals was to maintain the “DNA” of the company. “We often speak about how everyone at Pieter Smit has a dark blue heart,” she revealed, making a reference to the company’s paint job on all its vehicles and logo. “We have many staff members who have been with us for many years resulting to the feeling of a family spirit.”
As such, Louise was pleased to keep the business in the Smit family to maintain this working culture. “At a recent seminar I learned that only 30% of businesses remain within a family and that percentage gets even smaller when it moves to the next generation, so I’m glad we’re somewhat of an exception.”
With the clear goal of keeping the company’s culture intact, Louise went on to explain some of her goals for the business – namely with a move to a more sustainable future. The company has been utilising HVO fuel for the past few years, but it is now seriously considering the future of electric vehicles. “We already have a number of electric vehicles for our smaller vans as they are able
to be charged quickly and charging systems are becoming more and more accessible,” she explained. “When it comes to the heavier, larger vehicles - like trucks - you need a completely different charging system. You cannot plug them on the same system as passenger vans or B-licence vans. We have to figure out how to make the specific charging requirements work and how to facilitate it both at our several yards and on the road.”
The CEO admitted that there were still several questions about the direction of electric vehicles, for example the issue of the life cycle of vehicles, which should be considered. “It’s imperative that we try to find solutions and share our findings and experience with our clients.”
The CEO also spoke of the potential growth of the company – specifically in the territories it already has bases. “The company has been very stable in the Netherlands for 45 years and my hope is that we’ll be able to get to the same level of stability in our other regions.”
Part of this development strategy has all the branches putting a real focus on local regional work. “Our origin within the Netherlands was in the theatre market and we’re pushing all of our
other branches to really consider their local markets, especially as these are less effected by the seasonality of the wider events market.”
There is also a real push internally to keep tabs on up-and-coming talent. “We have two rehearsal studios in Germany and Poland. Both are ideal for small to mid-level bands and therefore we put efforts to visit various festivals in the summers such as Eurosonic Festival to meet artists and let them know of our services.”
Louise Smit finds herself in an interesting position taking on her father’s legacy and maintaining the DNA of the company while also aiming to develop the brand in line with the wider demands of needing to consider sustainable practices.
“We are now moving the company away from being centred around my father, but we see this as a positive move as having a company centred around one individual could be very risky and instead, we can rework our structure to secure the company’s future and ensure that his vision lives on. We find ourselves amid succession and the energy transition. At Pieter Smit Group, we think in solutions and no challenge is too big for us.”
www.pietersmit.com
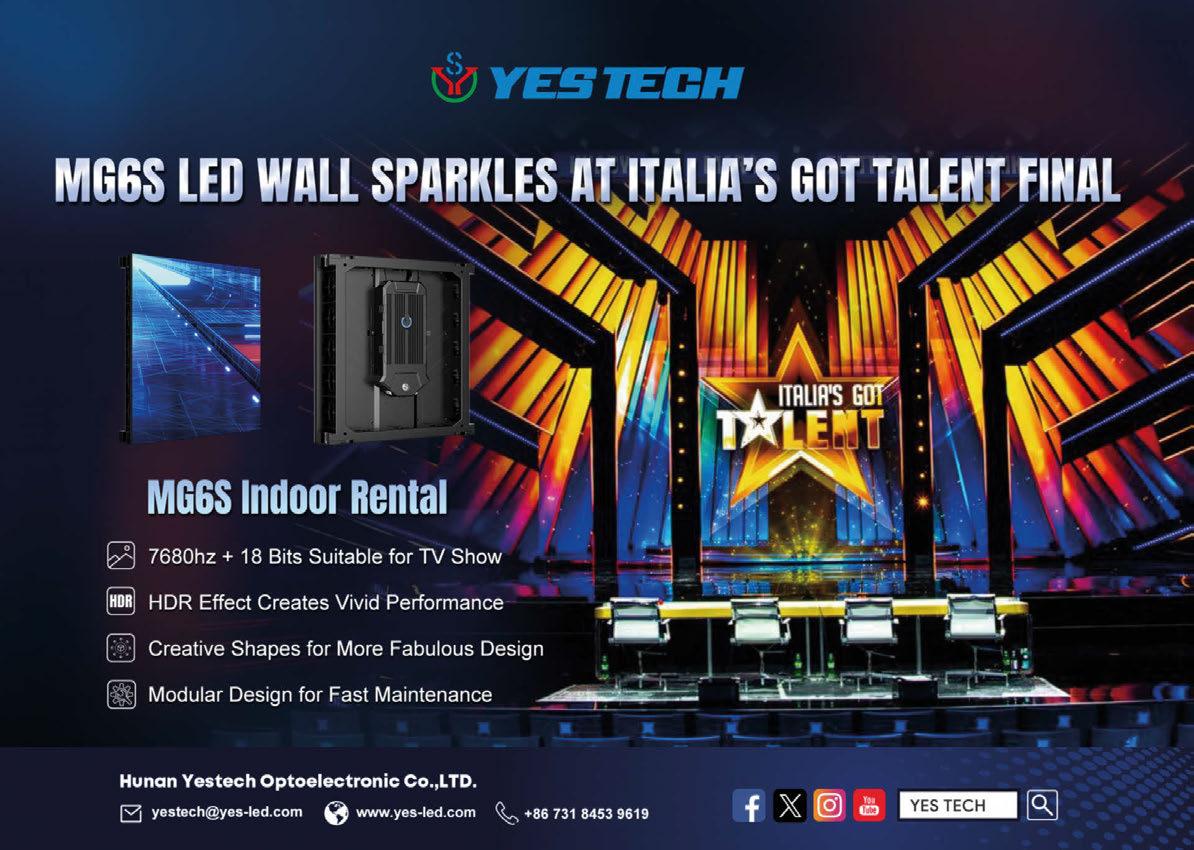
COLUMN POWERED BY
PF TALKS EXPANDS REMIT
Production Futures reveals new look studio space and launches the Breakthrough Talent Awards 2024.
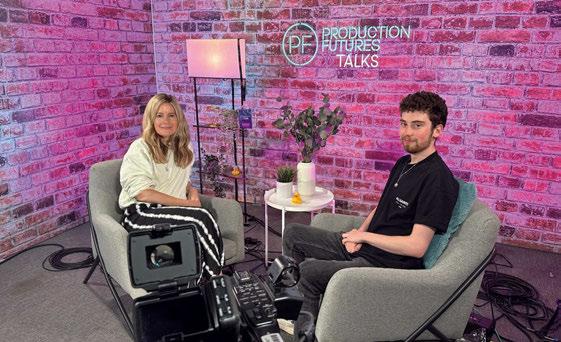
Following its launch in February, Production Futures has expanded the footprint of its PF TALKS studio with a new facility at the FIX8Group HQ, offering in-person interviews and a bigger capacity to facilitate its discussions with industry professionals with support from FIX8Group, Wavecast, ChamSys and CHAUVET Professional.
The original studio, situated at the iconic Strawberry Studios in Stockport, will be utilised for broadcasting remote interviews while the new studio provides space for visitors to attend PF TALKS live.
The new, larger set will also facilitate recorded chats with entertainment production industry professionals which will broadcast on Production Futures’ YouTube channel and can
accessed by those who aspire to work in the industry with guests providing a unique insight into what it takes to work in the events space. To enhance each interview, CHAUVET has supplied the PF TALKS Studio with five onAir Panel Min IP LED soft lights, two Ovation CYC 1 FC, and four COLORdash PAR H7X lighting solutions. “PF TALKS is a popular feature of all our live eventsIt is a hugely valuable resource for youngsters who are able to gain insights and receive answers to their questions from professionals who are seriously invested in helping to bring through the next generation, Production Futures CEO, Hannah Eakins commented. “The PF podcast is the next step to allow PF to connect with an audience wider than the successful PF ON TOUR events,”
EMPLOYEE OF THE YEAR
ENTREPRENEUR OF THE YEAR
APPRENTICE OF THE
Eakins continued. “This platform is going to enable industry-leading professionals to share insights about how they got started and how they see the industry progressing. By supporting the studio, we hope this new platform is going to help inspire more people to look at what we, as an industry, have to offer.”
Recent guests include Elliot Baines, who was awarded a Breakthrough Talent Award when he was just 15, and TPi Awardwinning Lighting Designer, Ed Warren. The Breakthrough Talent Awards will return later this year for its eighth edition with 21 categories, special guest judges and prizes. A ceremony will take place on 27 November at Production Park in South Kirkby. www.productionfutures.com
RIGGING
FESTIVAL PRODUCTION NEWCOMER OF THE YEAR
TOURING PRODUCTION NEWCOMER OF THE YEAR
VENUE PRODUCTION NEWCOMER OF THE YEAR
BROADCAST PRODUCTION NEWCOMER OF THE YEAR
AUDIO NEWCOMER OF THE YEAR
OUTSTANDING ACHIEVEMENT





Photo: Production Futures
PIONEER PRO AUDIO XPRS2
Federico Sidero, Marketing Executive at AlphaTheta EMEA, provides an insight into Pioneer PRO AUDIO’s latest innovations...
Photo: Pioneer PRO AUDIO
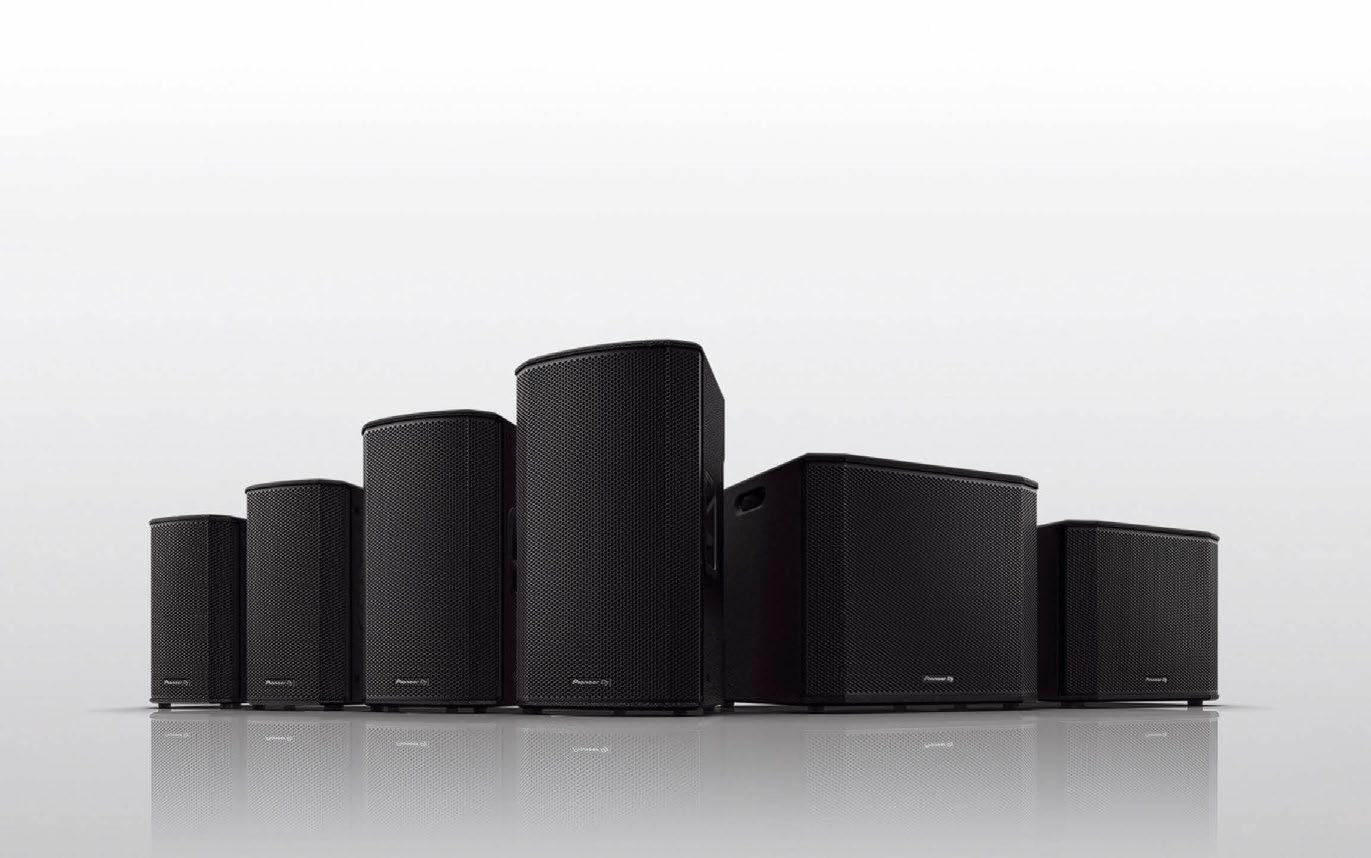
Where do the four new speakers fit into the existing XPRS2 Series line-up?
“The new eight-inch XPRS82 and 15-inch XPRS152 join the existing 10-inch XPRS102 and 12-inch XPRS122 speakers, while the two new active subwoofers – the 15-inch XPRS1152ST and 18-inch XPRS1182ST replace the two previous subwoofers in the range. Essentially, we’re providing our customers the widest possible choice, enabling them to choose speakers that align perfectly with the size and scale of their requirement.”
Who are these speakers aimed at?
“The XPRS2 series is perfect for any setting that requires premium sound from an easy-toset-up, intuitive, plug and play system. At either end of the range, the XPRS82 is perfect for music and spoken word, while the XPRS152 is ideal for DJ sets, live concerts, and for a variety of applications in difficult audio environments where room acoustics are not ideal.”
Which features will end users be excited by?
“ The units’ powerful Class D amplification delivers a premium audio for listeners and performers alike. The XPRS82 and XPRS152 full-range speakers feature Class D 2000W amplifications, while the XPRS1152ST and XPRS1182ST subwoofers offer Class D
4000W. Each model also features a sleek and protective all-black plywood cabinet for excellent performance in challenging indoor and outdoor environments.
“Durable handles (double handles on subwoofers) support easy system portability and handling during set up and take down, while rubber feet enhance separation and shock absorption between surfaces.
“X PRS1152ST and XPRS1182ST also feature a screw socket to accommodate a threaded pole. In common with the rest of the the series, each full range unit has onboard DSP modes, with XPRS82 and XPRS152 featuring four presets for Live, Music, Speech and Monitor.
“As well as the four presets, each XPRS2 full-range speaker includes 16 custom user DSP modes which can be saved with custom names, ensuring that EQ settings can be optimised for every scenario. The subwoofers offer three different preset modes – Boost, Normal, and Extend LF, to suit different listening environments.”
Why is it important for Alpha Theta and Pioneer DJ to include DSP settings?
“As well as being able to choose from different speaker sizes, the DSP settings add another layer of choice for users, giving them more flexibility for the widest range of applications.
The ease of plug and play is therefore complemented by four intuitive presets, and further enhanced by the ability to fine tune and name up to 16 custom user settings. This is extremely useful for DJs who are able to setup, name, and then return to EQs for specific rooms and venues.”
Where can we expect to see the XPRS2 Series in the coming months?
“The premium sound quality, versatility and extremely robust build, mean that XPRS2 is pretty limitless in its scope across a very wide range of applications.
“T he larger full-range units used in conjunction with the subs offer DJs and live bands a powerful performance tool – we have already seen XPRS2 deployed as DJ booth and stage monitoring in larger, prestigious settings, so expect more and more mobile DJs, clubs, and live performance venues to invest.
“X PRS2 isn’t just for DJs and bands, though. Interest from houses of worship, corporate and education settings is also bound to be strong. For rental companies that cater for diverse applications and are seeking high-quality audio from robust units that can cope with the rigours of daily use, XPRS2 is the perfect go-to system for them.”
www.pioneerproaudio.com
ROE VISUAL TOPAZ SERIES
Following a successful maiden outing at Integrated Systems Europe (ISE) 2024, ROE Visual Marketing Manager, Marina Prak and Technical Support Engineer, Jelle van Abbema retrace the origins of the company’s ‘road ready’ LED offering.

What was the inspiration behind the creation of the Topaz Series?
MP: “We wanted to bring a new, cost-effective product to the market. Design-wise, we drew inspiration from the integrated locks and sturdiness of the Ruby series, so we tasked our R&D team with creating an entry-level, rental product for mid-sized to larger rental companies, while maintaining the high-end quality associated with our product portfolio.”
How has the Topaz Series been developed to serve the live touring and rental market?
JvA: “With Topaz, there are many benefits for end users. Starting with the setup of the screen, we have corner protectors that make for quick and easy setup and helping to reduce damage during load-in and-out. Topaz uses modules made from magnesium – which results in a lightweight, rigid module with good heath dissipation. Better than the plastic modules used by most comparable products. Also, the Topaz curved LED panels use the patented OneLock curving system.
“Having integrated locks without the need for additional components when setting up the physical part of the screen allows you to implement the panel, engage the locks, and that’s it. From a hanging point of view, as with many of our products, there are magnets in the
top and bottom of the panels, which can hold the weight of a panel before it’s locked so you have both hands free to engage the locking mechanisms. In terms of servicing, panels of 0.5m by 0.5m consist of four different modules, so if the LED or drivers are damaged, you can easily remove one of those modules from either the front or back and sent it to one of our repair facilities.
“From an added servicing point of view, the power box, in addition to containing the power supply and connectors, also contains the hub board and receiver card, so if there is any technical fault, it is very easy to access using two pins to unlock the box, and replace and amend if required, which helps in a busy touring scenario when you have minimal downtime to troubleshoot any technical problems.
“If you are also tight for space on the backside, everything can be serviced from the front. With the combination of our Curve and Cube panels, customers are afforded a lot of creative options and the ability to interchange panels to fulfil modern requirements for exhibitions and live entertainment projects.”
How important is it to develop a cost-effective and malleable LED series?
MP: “It is very important, especially for rental companies that invest in multiple solutions
from the same line, so you don’t have any colour discrepancies. This also provides them with the freedom to mix and match to create them a flexible inventory to use for different applications. They all coexist and work together, regardless of their orientation, for multi-shape setup, providing a wealth of options with the curving lock providing an impeccable finish, which is a guarantee we provide when you invest in ROE Visual.”
What has the response been like since introducing the Topaz Series?
MP: “The response has been very positive. We introduced Topaz to the German market in November 2023, but we officially began shipping post-ISE in February 2024. We exhibited the entire range at ISE and Prolight + Sound, from the tilted cube to the straight and curved wall, from which we received a lot of favourable comments.
“Testament to the ease-of-use of the Topaz series is what happened to our crew at ISE. Our trucks were delayed due to labour strikes in France, so our inventory arrived midday on the Sunday morning before ISE, yet we were still able to fulfil the design brief in mere hours. Technicians really like our products due to their ease of use.”
www.roevisual.com
Photo: ROE Visual
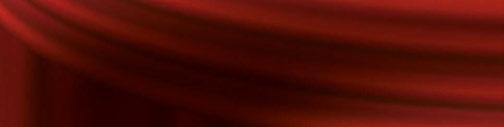
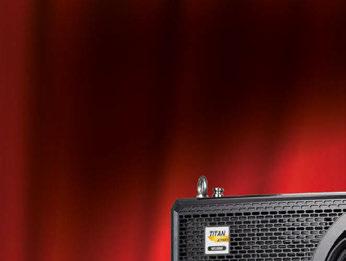










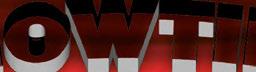

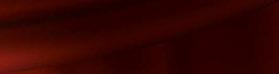
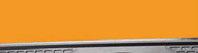
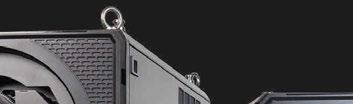

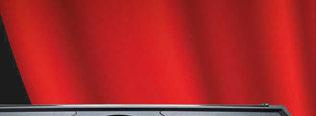
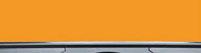
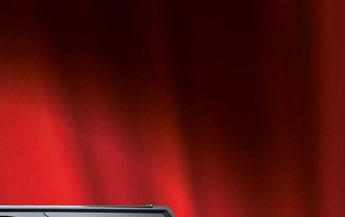
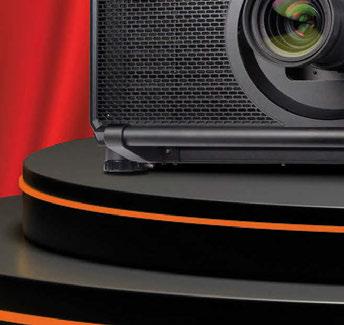

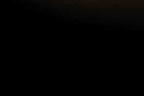
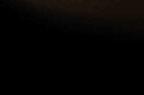


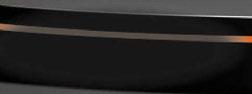

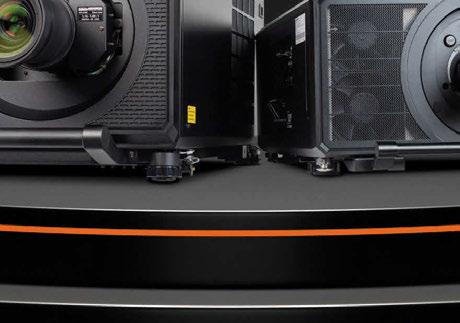
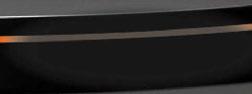

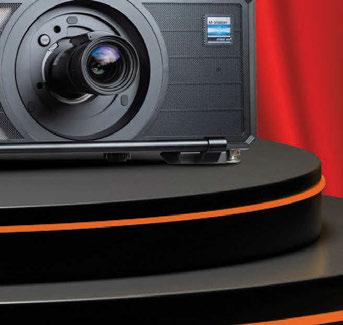

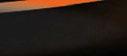





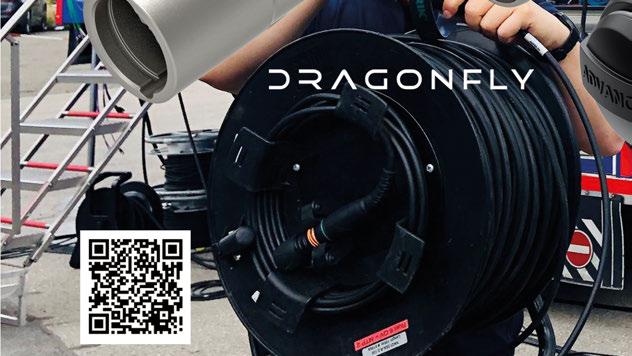
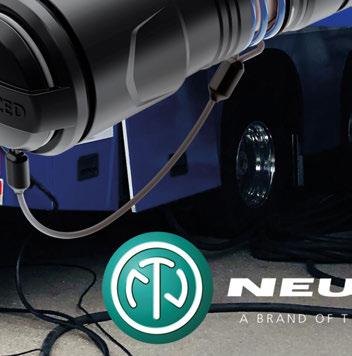
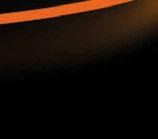

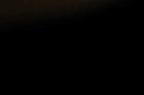

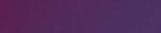
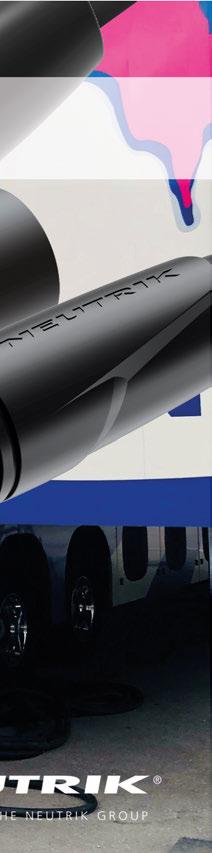
VARI-LITE VL2600 SE SERIES
Martin Palmer, Product and Marketing Leader at Signify, shares how VariLite harnesses the latest technological advancements to increase the output of its VL2600 SE Series without impacting business or the environment.
Photos: Signify
What were the primary goals when developing the VL2600 SE Series?
“The continual replacement of fixtures that we often see by others in the industry has a significant negative impact on sustainability –both environmentally and economically. The need to constantly swap fixtures with minor, iterative replacements lead to unnecessary cost for rental houses, as well as a large amount of waste that harms the planet, we all live in. With the VL2600 SE Series, we wanted to leverage the latest technology advancements and offer our customers more output without undue impact on their business or the environment. Existing fixtures can be upgraded, the parts and pieces of the fixtures remain the same, and they operate in the same way designers are already familiar with. They’re just a heck of a lot brighter.”
Can you elaborate on the process of upgrading from the existing VL2600 Series fixtures to the SE version?
“It’s quite easy to upgrade a VL2600 fixture to the new SE Series engine. There are six screws to remove and mount the assembly, along with a couple of wiring connections. Any trained service technician should be able to do it. We have instructions and a training video to make it even easier.”
What specific feedback or requests influenced the design and feature set of the VL2600 SE Profile and Wash fixtures?
“The feedback we get from the industry is that everyone is tired of the ‘flash and trash’
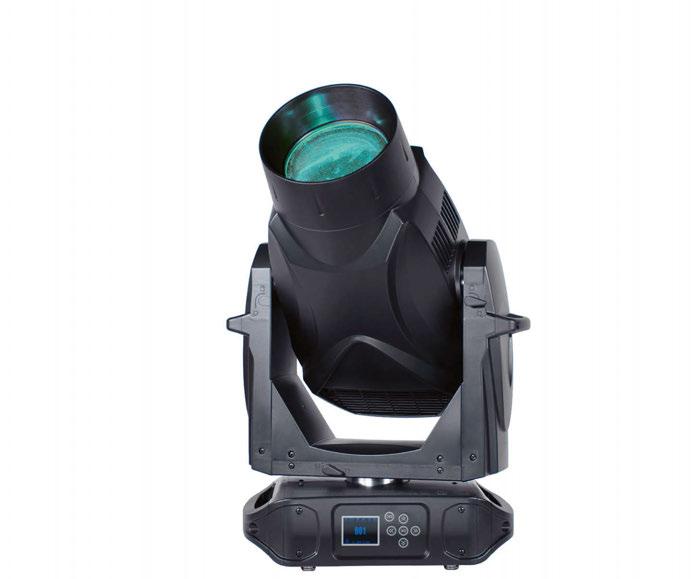
philosophy of iterative product upgrades. Customers want good, all-around workhorse products they can rely on for years. That’s been a core part of Vari-Lite’s DNA for decades. The VL2600 SE Series is the best workhorse on the market, and it now offers best-in-class output. It has a well-rounded feature set, a broad colour palette, and an excellent quality of light. It’s the reliable tool that LDs can trust in any design.”
Which features set the VL2600 SE Series apart from other lighting fixtures?
“The VL2600 SE Series is, at its core, a wellrounded fixture with great light quality and a broad range of colours. That’s why we call it a workhorse fixture. It’s a consistently and reliably high-quality luminaire that achieves most anything you ask of it. It’s not some special effect fixture that looks cool on a single production and then falls out of favour. It does the heavy lifting in the design, which is why the VL2600 is such a highly specified fixture.
“Designers trust the VL2600 Series because it has a track record of reliability, and the fixtures are available to rent on every continent on the planet. The SE Series just builds on that, with the goal of giving the fixture a 10-year life cycle at minimum.”
How does VL2600 SE Series align with VariLite’s commitment to environmentally friendly lighting solutions?
“Vari-Lite is part of our parent company Signify’s Brighter Lives, Better World programme with an aim to double our circular revenues company-wide by 2025. With
luminaries like the VL2600 SE Series that last longer and offer higher output at lower wattage, we extend the product life cycle. This ensures our users get new features without the waste.” www.signify.com www.vari-lite.com
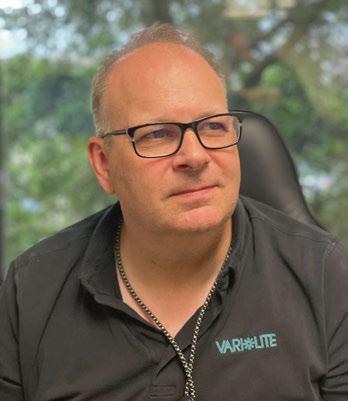
Martin Palmer, Product and Marketing Leader at Signify retraces the origin of the VL2600 Series.
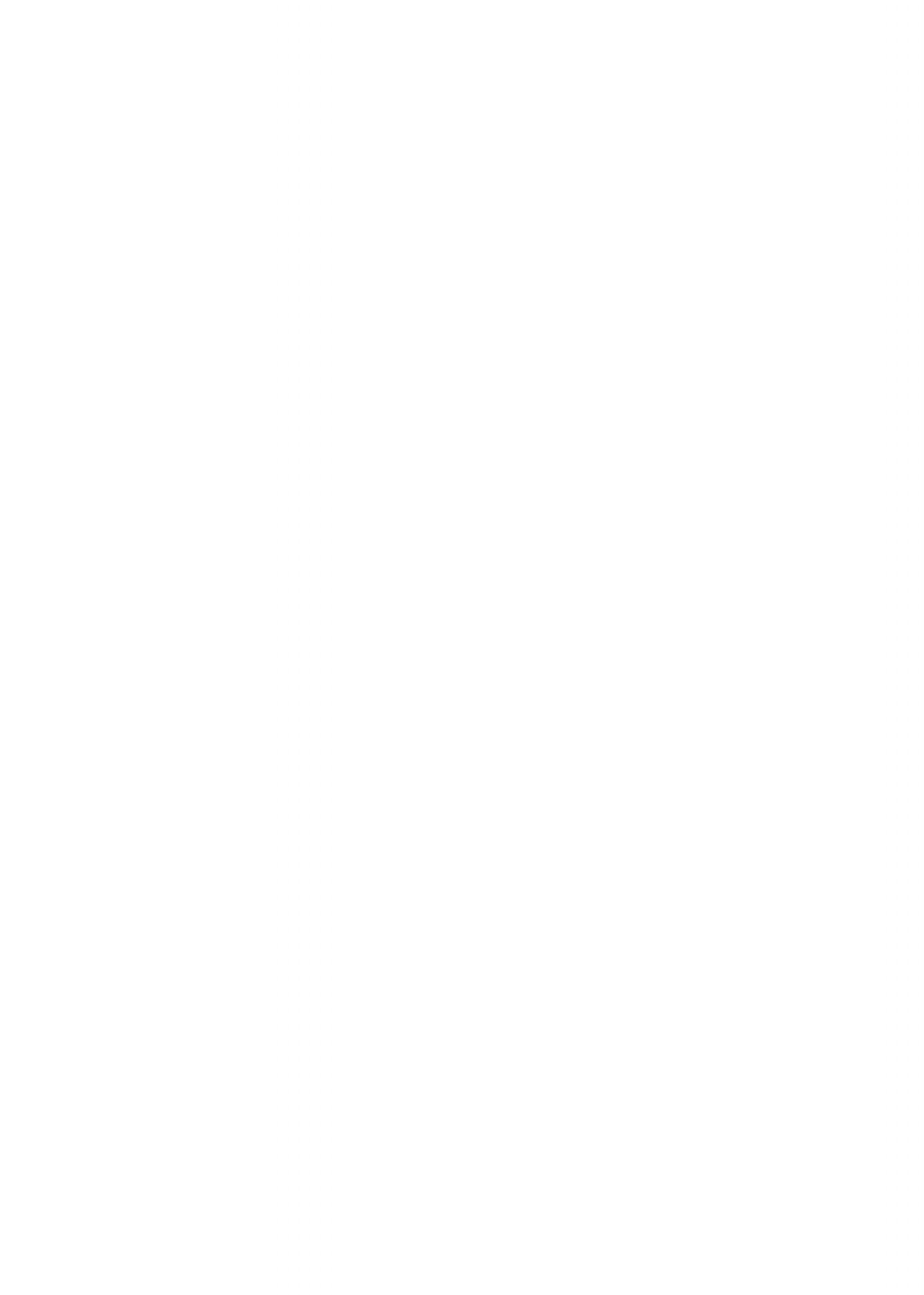
SHURE PRESENTS NEXADYNE
Introducing the latest addition to Shure’s impressive microphone portfolio…

On 30 April, Shure hosted TPi and other industry professionals at The Rose Shure Experience Centre in central London. This event provided an in-depth look at Shure’s latest innovation, the Nexadyne Dynamic Vocal Microphone, continuing the sound specialist’s longstanding legacy of excellence in the microphone industry.
After developing t he world’s first singleelement unidirectional dynamic microphone, the Unidyne, in 1939, Shure has become one of the most recognised microphones manufacturers worldwide; from the Unidyne to the SM58 which was developed in 1966 and is still used worldwide to this day.
In line with this legacy, Shure doesn’t aim to replace the SM58, but rather give options to its artists to choose from a range of microphones and the newest addition are the Nexadyne 8/C Dynamic Vocal Microphone and the Nexadyne 8/S Dynamic Vocal Microphone.
The former includes a cardioid pattern aimed at being utilised for professional live vocal performance, where the 8/S has a supercardioid pattern which is directed towards professional vocal performance.
Featuring Shure Revonic dual-engine technology, the Nexadyne is tuned for superior off-axis rejection w here t he Revonic c artridges are configured to work together to manage unwanted internal and external handling noise, with the Revonic two transducer design the microphone manages more acoustic signal processing without the need for traditional
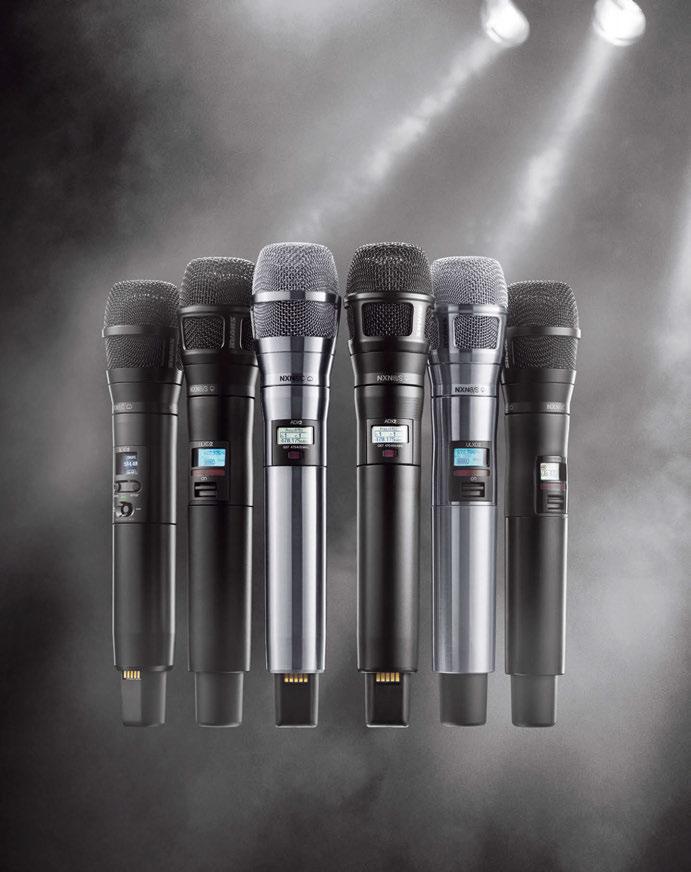
pneumatic shock mounting.
At t he launch event, attendees were treated to performances from Moonchii and Aaron A nderson, w ho were among t he first performing artists to test out microphones.
Production Manager, Chris Parker and FOH Engineer, Matteo Cifelli further provided insider insight, having debuted the microphones on the road prior to the launch.
With an increase in softer-spoken performing artists t aking to t he world’s largest stages, such as Billie Eilish, Dua Lipa, beabadoobee among others, Shure were aware of the challenge of creating a microphone that fits all professional vocalists.
TU G raz Professor of Acoustics, Kai Siedenburg analysed music from 1946 to 2020 and found that vocal levels generally decreased in pop music; to support this Nexadyne is a step forward in supporting artists which require additional amplification and support f rom their microphones. In addition to benefitting per formers and sound engineers, Nexadyne provides improved signal quality, delivering a clearer source for when it comes to the mixing process. Ultimately, the higher output of the microphone ensures engineers can reproduce and balance an artists’ vocals with less audio corrective processing.
The Nexadyne comes in wireless and wired formats for individual performers’ requirements, both available in black w ith t he wireless also available in nickel finish. ww w.shure.com
Words: Alicia Pollitt
Photo: Shure
Shure’s new Nexadyne Dynamic Vocal Microphone.
5 INDU-ELECTRIC
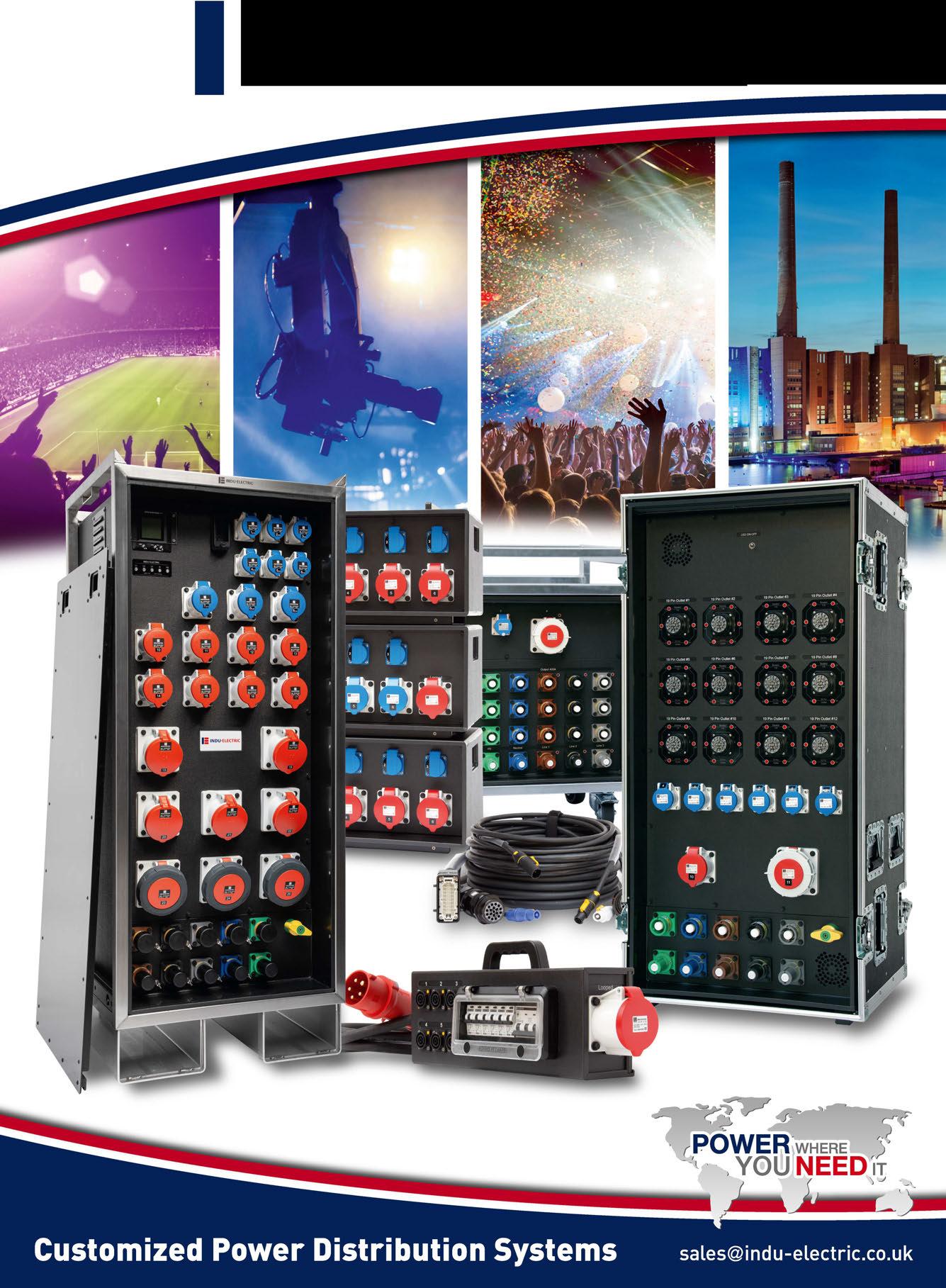
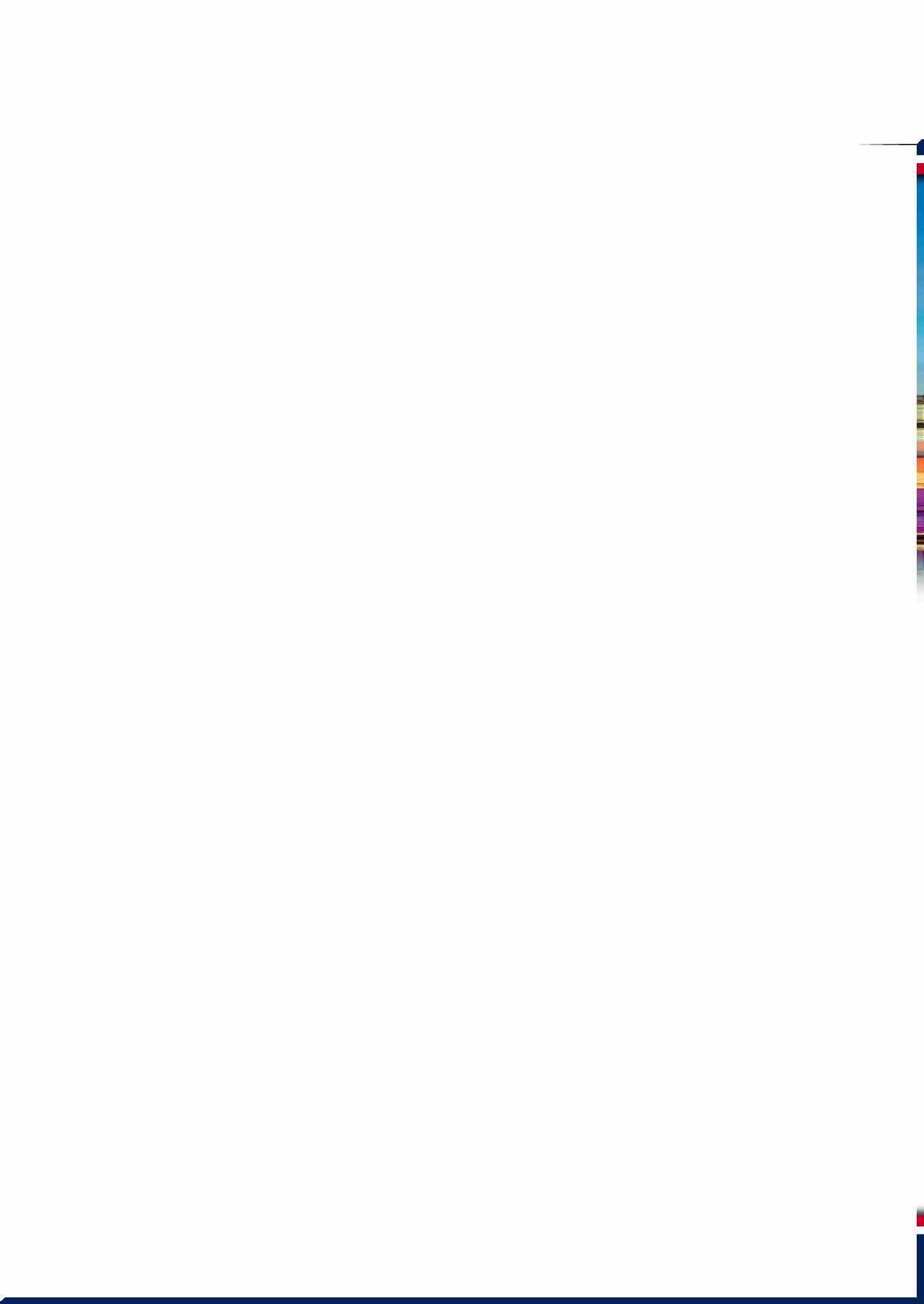
‘OUR INDUSTRY CAN TRULY MAKE AN IMPACT’
Robert Trebus, Director of Global Sustainability at d&b group, provides insight into the growing importance of sustainability within the global live event industry and introduces the company’s latest innovation – d&b SustainSymphony.

Words: Robert Trebus
Photo: d&b group
Sustainability has been a core focus for several years and is now a top priority for many companies. However, the tools and possibilities for driving change differ significantly across industries. The live event industry, in particular, faces numerous challenges and varying regional regulations. Increasingly, local communities and sponsors demand sustainability concepts for event funding. Additionally, sustainability is a key concern for millions of fans, festival-goers, sports enthusiasts, and tradeshow visitors.
With d&b SustainSymphony, our vision is to transform the event industry by putting sustainability and carbon neutrality at the heart of the business. It’s the first free normconform sustainability service tailored to the events industry, offering an easy-to-use platform for various stakeholders. Having spent years navigating the complexities of event planning, I was aware of the difficulties in sourcing equipment and services that met both high standards of quality and sustainability. The market for such environmentally friendly options was, and still is, very limited.
SustainSymphony is borne out of a desire to break down these barriers and create a more transparent, accessible, and sustainable future
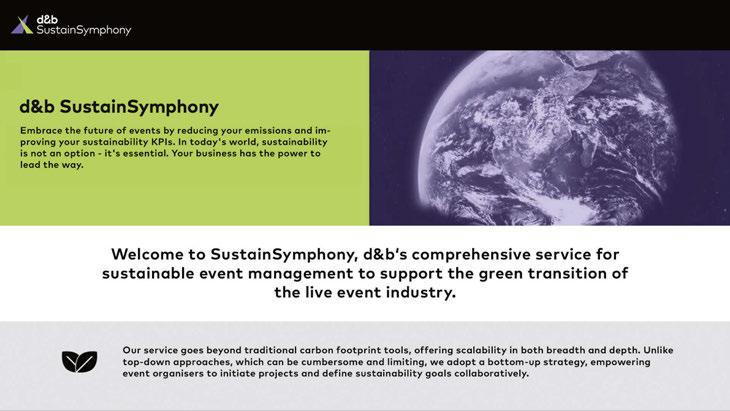
for the event industry. A key component of SustainSymphony is the Green Event module, a module designed to support event planners in making environmentally responsible decisions at every stage of their planning process. This module provides comprehensive guidance on a wide array of sustainable practices, from selecting renewable energy sources to opting for eco-friendly materials and efficient waste management solutions. It’s a one-stop resource aimed at reducing the environmental footprint of events and meeting the growing demand for sustainability across all sectors.
One of the most innovative features of SustainSymphony is the open supplier database. This is a game changer in the event industry, providing a platform for suppliers and manufacturers to list their sustainable products and services.
What sets this database apart is the detailed sustainability KPIs that accompany each listing. Suppliers provide information on metrics such as product carbon footprint, energy consumption, circularity, and residual waste. This level of transparency is unprecedented and incredibly valuable to event planners, enabling them to make informed decisions and promote sustainability.
Ensuring the credibility of the information in the supplier database is critical. Suppliers are required to upload product certificates to support their sustainability claims. This process builds a foundation of trust between event planners and suppliers, facilitating a more seamless and confident collaboration.
In addition, the ability to include accurate product information in the event’s sustainability report is invaluable. It provides tangible evidence of the efforts to deliver a green event, which is increasingly important to stakeholders and attendees who now prioritise environmental responsibility.
I am confident that d&b SustainSymphony will be of great benefit to event planners and the industry as a whole. It simplifies the process of identifying and verifying sustainable products and services.
The SustainSymphony platform provides the tools and transparency needed for sustainable event planning, promoting positive change and inspiring industry-wide transformation. In the end, we all share a common goal: to preserve our world for future generations and this is our chance as an industry, to truly make an impact. www.db.group
HARNESSING THE TECH OF TOMORROW
Pedro Magalhães, Europalco founder and CEO, highlights the company’s use of holograms, augmented reality (AR) and artificial intelligence (AI) to deliver immersive experiences.

Words: Pedro Magalhães
Photo: Europalco
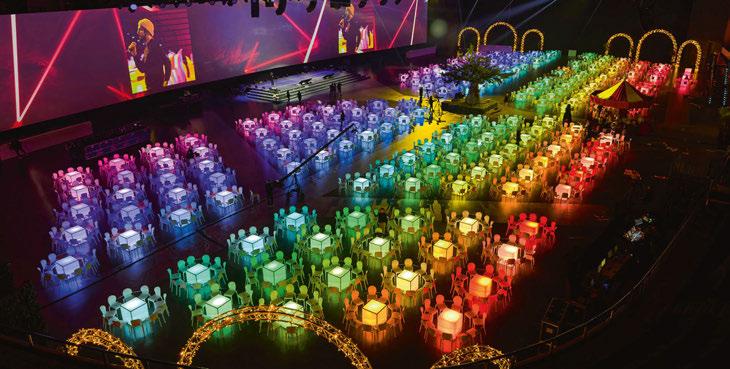
At Europalco, we are constantly engaged in research and development of new solutions. We strive to set trends and stay one step ahead of our competition with unique products and services. Our teams are continuously trained to maintain the highest level of expertise. We also work closely with several manufacturers to support the development of our solutions. We systematically listen to our clients, considering their feedback and ideas. Year after year, we invest significantly in acquiring the best equipment to provide our clients with unique, tailored solutions for their events. We also visit the major European technology trade shows to keep abreast of the latest developments from manufacturers and see what’s coming up.
Our clients increasingly seek immersive solutions for their events. When we talk about immersion, it’s not just about 360° projections; audio also plays a fundamental role, along
with other elements. Our mission is to develop unique solutions for each client, ensuring that every event is one-of-a-kind. Over the years, we have consistently achieved these goals by creating distinct solutions tailored to each event. In recent times, new holographic solutions have emerged for events. While small-scale holographic experiences are well-received by clients, large-scale events present a different challenge. Existing systems often fail to captivate clients because they require significant rethinking of the event’s scenic design, sometimes compromising the overall set design. In recent years, we have successfully integrated holograms into several events. With this experience and knowledge, we continue to seek out innovative solutions to meet our clients’ evolving needs.
When incorporating AR into events, it’s essential to proceed with caution, much like with 3D projection technology. AR should be used selectively and not forced into the event.
It can effectively capture participants’ attention in specific moments, such as when presenting a product that needs to be showcased in detail. AR allows us to highlight those details vividly. However, it’s crucial to use the technology sparingly and thoughtfully to avoid overuse. Our experience with AR was particularly strong during the pandemic period, and our teams are well-equipped to leverage this technology effectively. In the music and events industry, we often don’t have the same budgets for product development as other industries. Therefore, we frequently look to other industries for solutions that can be adapted for events, such as robots and AI. At Europalco, we actively seek alternative solutions from various fields, and we’ve invested in robots, which we now offer to our clients. However, investing in the product alone is not enough. We must also train our staff and develop the ability to envision how robots can be used creatively to offer unique experiences to our clients.
So far, we have used our robots to hold and move LED and LCD screens in the stage, creating a ‘wow’ effect amongst audiences. However, they can also be used to produce props and deliver captivating mobile and static stage designs. Their flexibility is fascinating, and the range of applications is limitless. Regarding AI, we cannot afford to ignore this technology. It is essential to start considering its applicability in events. At Europalco, we have dedicated teams and allocated budgets for AI development, ensuring that we remain at the forefront of innovation in the events industry. By integrating advanced technologies and continually seeking new solutions, we aim to provide our clients with cutting-edge experiences that set their events apart. www.europalco.pt
ROCK NASHVILLE
Lifting the lid on Rock Lititz’s plans for a major project to support Nashville’s dynamic live entertainment scene.

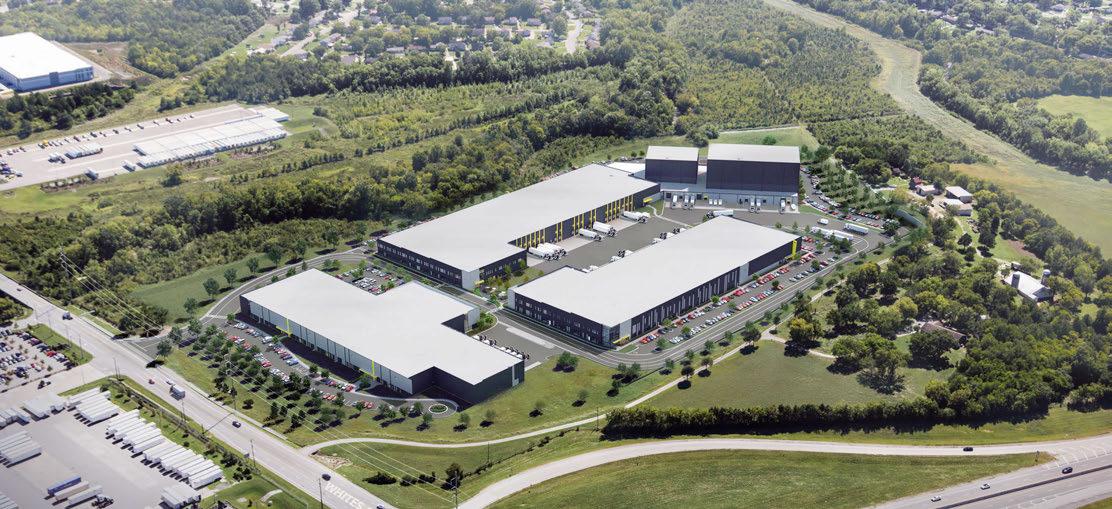
When it comes to touring acts, the performers on stage represent only a small portion of the team essential for its success. Behind the scenes, there are myriad technical workers – from lighting and set designers to sound engineers, videographers, choreographers, and production managers – all of who are artists. They rely on specialised software, equipment, and facilities to bring their creative visions to life.
Nashville has historically lacked a purposebuilt space tailored to the needs of these professionals. However, that’s about to change, thanks to the team behind Rock Lititz.
Andrea Shirk, President and CEO of Rock Lititz, reveals in an exclusive interview with TPi, the details of a large-scale development aimed at providing a home for Nashville’s vibrant live entertainment community...
What made Nashville an ideal location?
“Nashville is quickly growing into a global hub
of entertainment activity. Many strong live entertainment companies have a presence here, and the industry only continues to grow alongside the city. As country acts have gone global, the Nashville community has thrived.
“Ten to 20 years from now when people ask what the top music city in North America is, it’s going to be Nashville. Being able to offer the live entertainment industry a product that’s the calibre of Rock Lititz, in the hometown of so many in the industry, is great and is something we’re all thrilled to make happen. The Rock Nashville campus will provide community, resources, and a place to call home for this growing industry.”
How has the Rock Nashville team sought input from local live entertainment professionals to ensure the campus meets their needs?
“Rock Nashville was born from listening to the needs of the live entertainment community. We have a lot of respect for Nashville, its history,
and its roots. While we’re bringing something that is newer and more modern, we’re going to do it in a way that matches the current expectations of the environment while making sure we’re being a good partner.
“T his is why we have partnered with Soundcheck and Clair Global. They have a deep understanding of how the Nashville community works, with both playing active roles in the city for more than 30 years. We’re not trying to reinvent the wheel; we’re trying to support the natural evolution.
“Soundcheck is the nucleus of the upcoming Nashville campus – a space where all the other production companies come and physically collaborate in person with the artist and make their visions come to life. Soundcheck had this idea for a long time, but the Nashville live entertainment community is driving it all. We’re happier to be the facilitator in creating the centralised home for artists to imagine, build, and rehearse their shows.”
Words: Jacob Waite
Photos: Rock Nashville

How does Rock Nashville plan to support the growth and development of professionals in the live entertainment industry?
“We are committed to enhancing the live entertainment industry. That includes taking some of the education events that we have done in Lititz and bringing those to Nashville and working to grow the community there in the same way. Rock Lititz currently hosts annual conferences for youth ranging from high school juniors right through to young professionals to explore careers backstage in the live entertainment industry and has recently launched the Academy of Live Technology (ALT).
“Rock Nashville w ill offer educational opportunities to the local youth and has partnered with Blackbird Academy to bring education to the heart of the Nashville campus too. With collaboration at the heart of what we do, we will continue to support that same long-term vision for the next generation of live industry leaders and professionals by identifying spaces we can enrich and enhance the skills of industry professionals.”
How will Rock Nashville contribute to the cultural and artistic fabric of Nashville beyond providing rehearsal and production spaces?
“The Rock Nashville team is passionate about supporting the healthy development of the live entertainment community and helping raise awareness about careers and opportunities for interested individuals of all ages. We exist to serve the industry. We want to continue to be that facilitator and that listener so we can create connections in Nashville and expand our industry community even more.
“We want to create relationships, energy, and collaboration all year long for those who work within live entertainment. Rock Lititz, and now Rock Nashville, are about creating an environment and a space for the industry to do that. We care about the industry of today,
but we’re also looking forward to 30, 40, and 50 years from now and how we can support now what the industry is evolving into.
“Additionally, The SoundCheck team has a long history of partnering w ith local non-profits like the NashvilleRescue Mission and LastMinute Toy Storage to support the Nashville community. They plan to continue that spirit of giving during the transition and in their new location. The Rock Nashville project donated $25,000 to the District II scholarship fund earlier this year and plans to donate another $25,000 upon the completion of the project.
Rock Nashville will also engage with a local art non-profit to provide opportunities for local ar tists to participate in beautification projects.”
What wellness resources and support services will be available to professionals?
“At Rock Lititz we have Rock Med, a concierge medical service that focusses on the production community. For Rock Nashville, we are hoping to partner locally to bring Rock Med to this community as well. We have also established an incredible relationship with the team at Amber Health, who are on-site in Lititz frequently providing mental health support to our crews and offering t raining and resources to our team. We are excited to continue that relationship in Nashville.”
How does Rock Nashville intend to integrate sustainable practices into its operations?
“We are in the process of putting solar panels on the roofs of our buildings and adding geothermal capabilities and are on track to cover the electrical needs of the campus through alternative energy. We have also partnered with the Music Sustainability Association (MSA) to bring education and awareness to the community. Those same trainings and lessons learned will be part of the rock Nashville community as well.” www.rocklititz.com
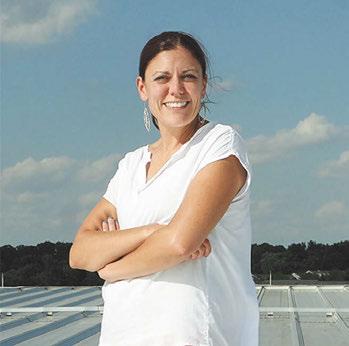
Rock Lititz President and CEO, Andrea Shirk.


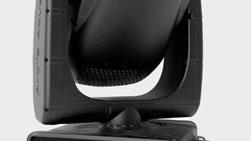

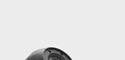

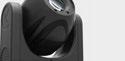


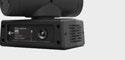
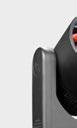



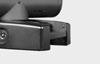
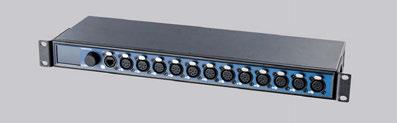
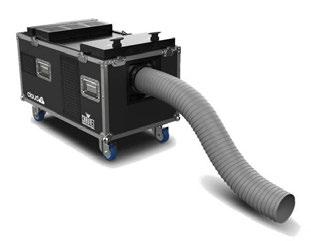







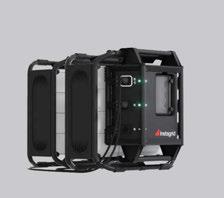
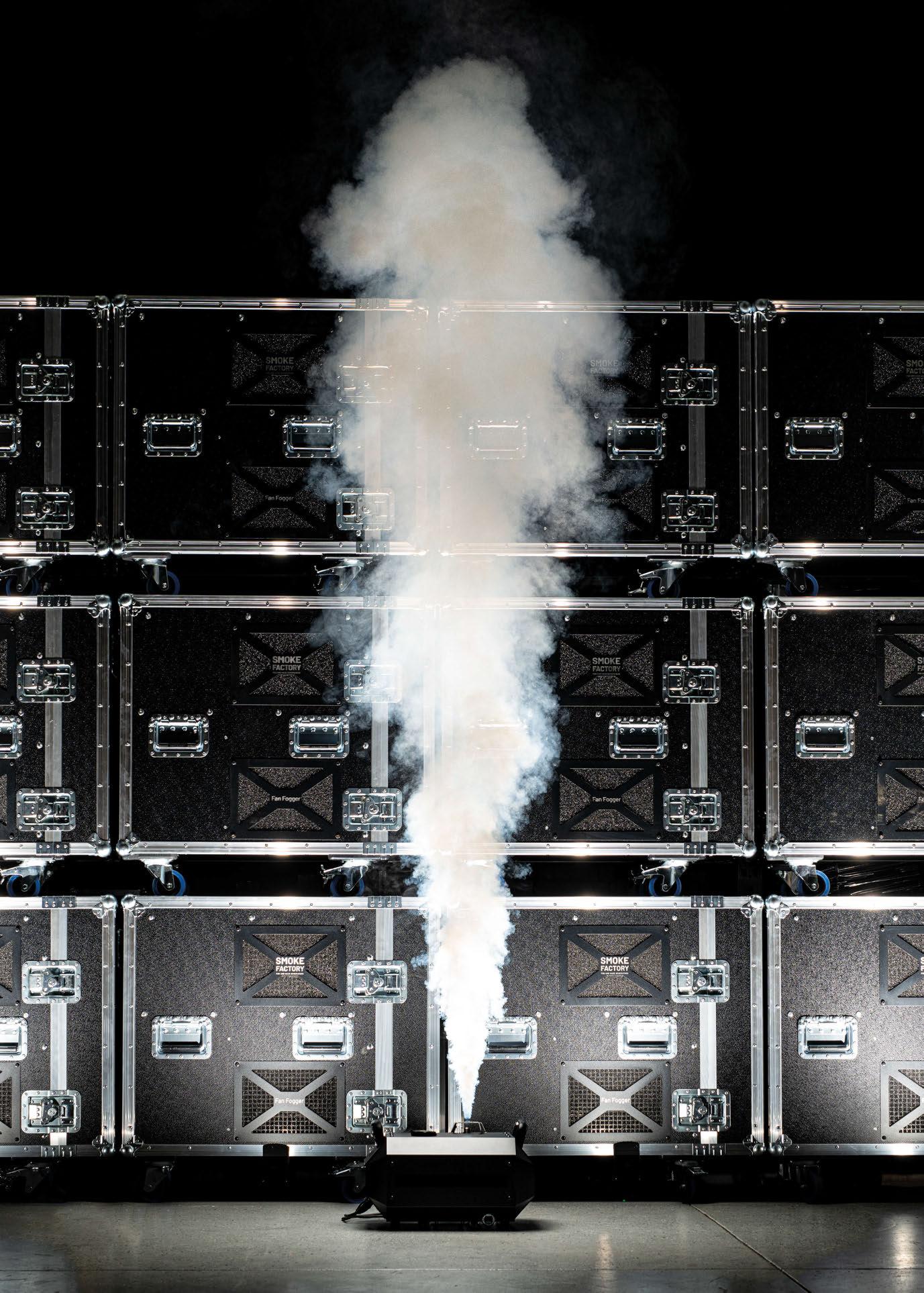

NEXT-GEN CONNECTIVITY FOR ENTERTAINMENT LIGHTING
KLSTR Commercial Sales Developer, Luke Edwards, discusses how networking is going to revolutionise lighting live shows in the future...

Which gap in the flourishing entertainment lighting market does KLSTR fill?
“Our goal is to make managing lighting fixtures simple for everyone. We created KLSTR.nano and KLSTR.one hardware that is built into the lighting fixture. Combining this with our KLSTR. ctrl application gives lighting technicians the tools they need to handle the complexities of modern fixtures and lighting rigs. Our vision starts with letting end users easily know and see the location of their fixtures based on their cable topology. Only assign a fixture ID, autopatch or upload a MVR file and your setup is completely configured.”
What is the vision behind the company’s various offerings?
“Our company was founded five years ago with a clear mission: to make networking technology accessible for everyone. Like many others in our industry, the COVID-19 pandemic had a significant impact on KLSTR. During this time, we came up with the concept KLSTR.nano, which is based on DMX and RDM and enables the same timesaving workflow. This innovation helped us complete our ecosystem.”
Why is networking an increasingly important factor to consider for lighting specialists?
“The complexity of lighting fixtures, different modes, and the number of channels per light make the 512 channels per universe limit increasingly restrictive. Transitioning to Ethernet networks seems logical, but it introduces many additional configuration steps and potential issues like IP addressing, sync problems, and other complex Ethernet settings. Setting up a show can become so
“Despite the advancements in technology, it’s surprising that we’re still addressing fixtures the same way we did 36 years ago. KLSTR brings us into the modern age.”
Luke Edwards, KLSTR Commercial Sales Developer.
complicated that it almost requires an IT technician. KLSTR eliminates all of this hassle. However, we believe DMX will always have a place in our industry due to its backward compatibility and cost-effectiveness. KLSTR. nano enhances the current technology without rendering it obsolete. We envision a future where both systems work together seamlessly and efficiently.”
How will KLSTR innovations benefit lighting specialists on the road?
“KLSTR is designed to help system technicians bring the lighting rig online much faster. This allows lighting designers to do what they are passionate about. The faster the lighting rig is online, the faster the designer can be creative and get the maximum out of their design.
As KLSTR is fully based on MVR and GDTF it enables a seamless workflow where KLSTR is
the missing link between visualisation software, the console and the real rig.”
Will this change the way lighting specialists approach their show designs?
“As KLSTR simplifies setting up lighting systems, manufacturers are also no longer bound when creating their new fixtures. This will result in even more exciting options and lights for designers. KLSTR therefore empowers designers to focus more on creativity and less on technical constraints, leading to more impactful and dynamic shows.”
Where are we likely to see KLSTR in the coming months?
“We will be active on several stages of Tomorrowland 2024, so follow our socials to discover more!”
www.klstr.tech
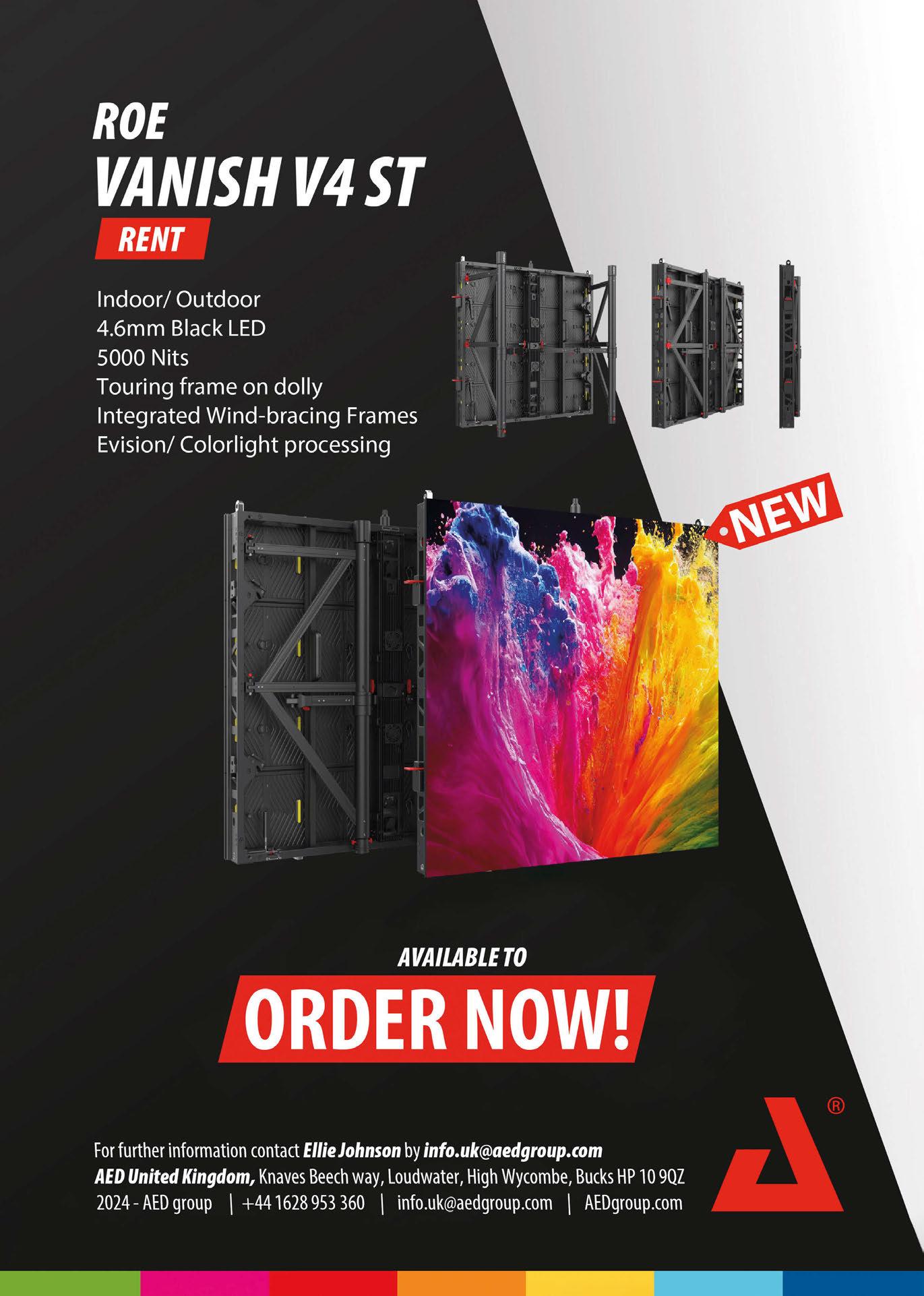
