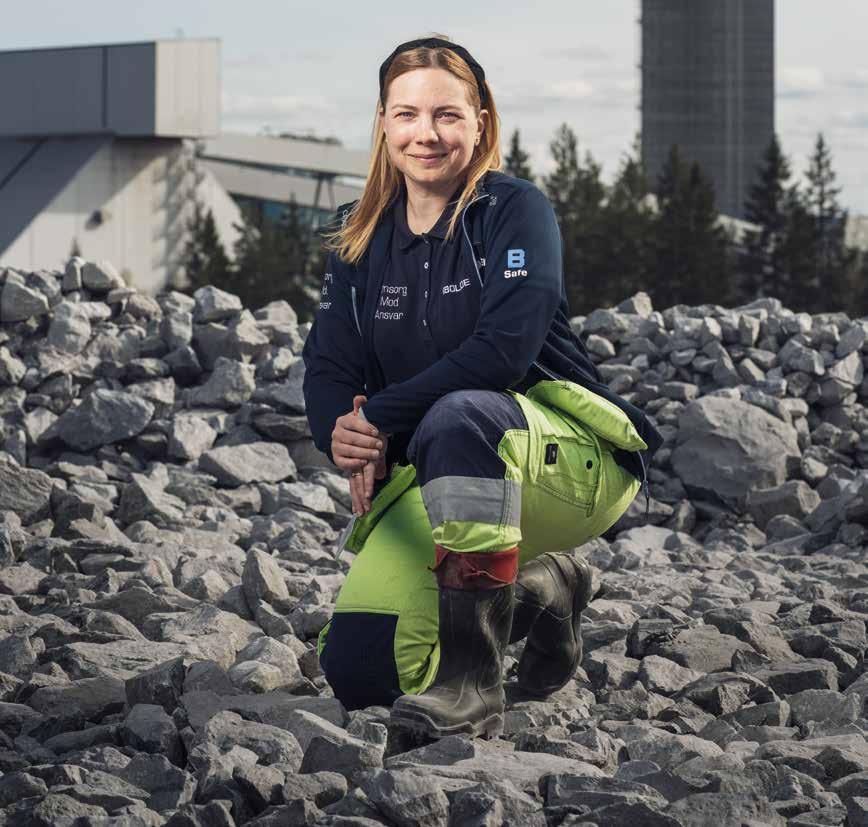
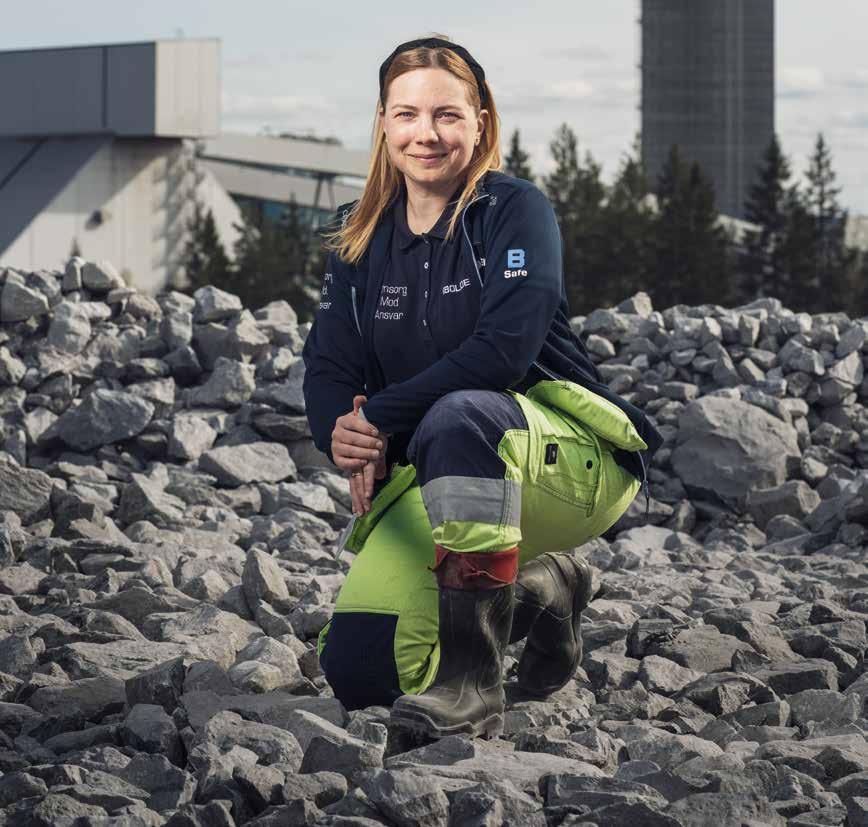
Explore the exciting world of exploration
DEAR CUSTOMER, the word “mining” typically conjures up images of dark underground tunnels or open pits where drills, loaders and trucks are hard at work extracting ore. But a mine’s life cycle typically starts with exploration drilling. With the global need for minerals steadily increasing, and gold, especially, recently reaching all-time high prices, exploration is now a hot area.
EXPLORATION IS ALL ABOUT gathering information. By drilling deep and bringing up rock samples, miners get clues that may lead to the discovery of valuable minerals. Exploration drilling can be divided into two main methods: core drilling, which produces a solid cylinder-shaped sample at an exact depth, and reverse circulation, also called percussion drilling, which produces a crushed sample from a somewhat more approximate depth. In addition, the drill hole
On my radar
Fortescue
In April we won our largest order contract ever, for a large fleet of electric and fully autonomous surface drill rigs to be used at Fortescue’s iron ore mines in Australia.
Geopolitics
All eyes are now on geopolitical developments such as tariffs, global trade, and the hope for peace in Ukraine.
can give supplementary important clues using so-called logging technology.
At Epiroc, we provide you with a range of drill rigs and advanced technologies to meet your needs for the most productive, accurate and safe exploration. Thanks to a combination of our organic offering and recent acquisitions, we cover all your exploration needs, including reverse circulation drilling, hyperspectral scanning, core photography and 3D laser profiling of drill core, rock chips and other geological samples.
One of our newest products is the Diamec Automated Rod Magazine, which trips out drill strings fully automatically to preset positions when used together with our Diamec drill rigs. Our technologies also include the semi‐automated OreSight™ platform, conventional multitool logging trucks, and a range of portable winches for remote and helicopter-supported operations.
Read more about the exciting world of exploration in this issue.

Helena Hedblom Epiroc President and CEO
Epiroc
At a glance
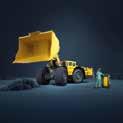
Epiroc is a vital part of a sustainable society and is a global productivity partner for mining and construction customers. We develop and supply innovative and safe equipment and offer world-class service and other aftermarket support, as well as solutions for automation, digitalization and electrification.
With Epiroc as a dedicated partner, you get a passionate team that supports you in a sustainable, efficient and safe way. No challenge is too big for our curiosity and persistence when it comes to increasing your productivity, safety or sustainability. We lift your competitive advantage through our continuous drive to make good things better – from highperformance equipment and service excellence to building the mining and construction industries of tomorrow.
Epiroc Group – get to know us better
What we strive for Accelerate the transformation
The world needs metals and minerals for the energy transition. And we need cities that can cope with a growing population in a sustainable way. To succeed, we need to speed up the shift toward a more sustainable mining and construction industry. We at Epiroc accelerate this transformation.
Epiroc Group 2024 in numbers
~ 19 000
Around 19 000 employees.
Customers in around 150 countries.
152 years of experience. Revenue: SEK 63.6 billion.
Speaking the same language
Digital integration enables holistic mining
Epiroc offers a wide range of interoperable, OEM-agnostic digital and automation solutions to help customers optimize operations, enhance safety, and improve productivity across various levels of operations.
Scalable
Extend your setup’s lifespan and expand operations with solutions that grow with your needs.
Global presence
Average employees
Flexible
Achieve smooth operations with solutions that adapt to various needs across different equipment brands.
Productive
Maximize output and optimize processes with tailored solutions that integrate your operations.
The urge to explore runs deep. Today, it’s also a necessity. How do we keep pushing forward – and where do we go from here?
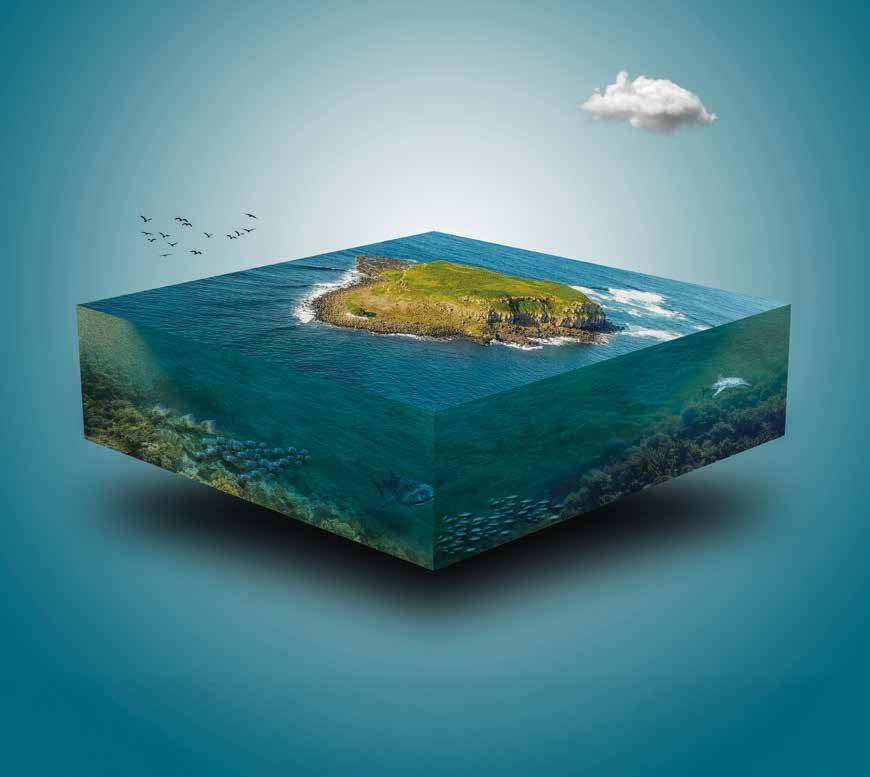
Committed to real change
Reducing emissions is pivotal in the mining industry. To advance the development of a battery-electric drill rig, Epiroc and Capital Limited joined forces – with great results.
WORKINGS
Hoseless boom design
The hydraulics of the Boomer M20 S face drill rig is contained within the booms, improving safety and efficiency. And there are lots of other features to love, as Stawell Gold Mines can testify.
SUSTAINABILITY
Circularity is at the core of Epiroc’s aftermarket services, spanning the entire machine lifecycle. Reusing materials enables costefficient solutions, benefitting both profitability and sustainability.
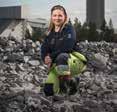
ON THE COVER Boliden wanted to modernize the procedure of logging the depth of drilled holes at its Garpenberg mine. Enter the Drill Tracker Solution from Epiroc. Emma Bjur, Head of Section Project Steering Mine, loves the way that it fits into Boliden’s ecosystem.
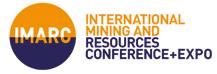
The next edition of the International Mining and Resources Conference (IMARC) will be held at ICC Sydney on October 21–23, 2025. The program features nine concurrent conferences covering the entire mining value chain, with more than 370 technical talks, panel discussions, and strategic keynote presentations taking place throughout the three days. www.imarcglobal.com
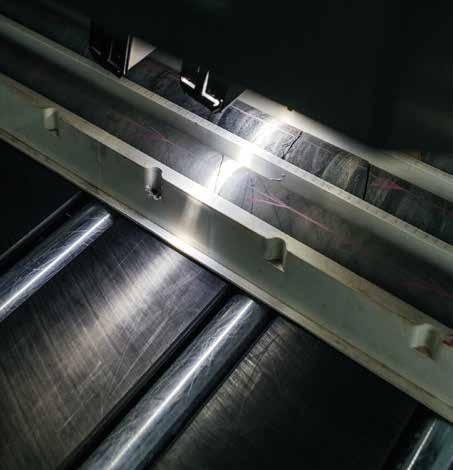
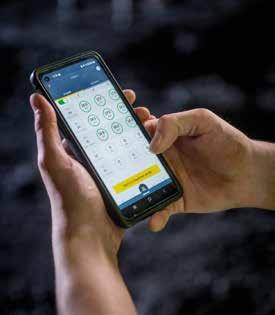
Betting big on exploration
Epiroc has made a series of game-changing acquisitions in exploration mining, taking charge of some cutting edge technology in the process.
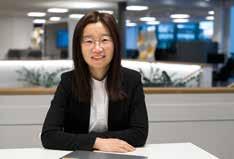
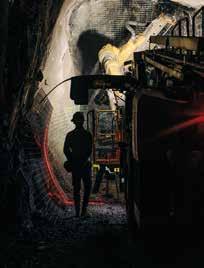
Mining & Construction is published by Epiroc. The magazine focuses on the company’s know-how, products and methods used for mining and construction worldwide.
Address:
Epiroc Rock Drills AB, SE-701 91 Örebro, Sweden
Web: epiroc.com
Phone: +46 (0)10 755 00 00
Publisher Ann-Sofie Andersson
Email: ann-sofie. andersson@epiroc.com
Editor Gustaf Höök
Email: gustaf@rubrik.se
Editorial Board
Ann-Sofie Andersson, Anders Bromsjö, Johan Bernström, Nurgül Atayer, Fredrik Ternström
Editorial Production & Art Direction/Layout
Rubrik AB, Masthamnsgatan 5, SE-413 29
Gothenburg, Sweden
Phone: +46 (0)31 719 06 00
Web: rubrik.se
Printed by Prinfo Welins, Sweden
Trademarks and reproduction of articles
All Epiroc product names (including but not limited to Pit Viper, Boomer, SmartROC, COP and Secoroc) are registered trademarks of one or more Epiroc companies. For questions regarding free reproduction of articles, photos or artwork in this magazine, please contact the editor or the publisher.
Selected highlights
06 EPIROC IN BRIEF
Keep tabs on what’s happening in the world of Epiroc.
14 FOLLOW-UP
Drill Tracker saves time and improves results for Boliden Garpenberg.
26 OUR CHALLENGE
The Powerbit X drill bit has transformed operations for Machines Roger at the Novanut site in Northern Canada.
44 MY WORK
Mary Zhu, Global Product Manager Small Loaders, embraces electrification.
48 BLAST FROM THE PAST
The Swedish method took the drilling world by storm. It all began in Stockholm in 1945.
50 AROUND THE WORLD IN BRIEF
Assorted news from the mining industry.
Safety first
Epiroc is committed to complying with or exceeding all global and local rules and regulations on personal safety. However, some photographs in this magazine may show circumstances that are beyond our control. All users of Epiroc equipment are urged to think safety first and always use proper Personal Protective Equipment (PPE) as required to minimize the risk of personal injury.
EPIROC IN BRIEF
Epiroc wins its largest contract ever
Epiroc has won a significant contract – the largest in Epiroc’s history – to deliver a major fleet of fully autonomous and electric surface mining equipment to Fortescue, a Perth, Australia, headquartered technology, energy and metals group.
The company, which is also one of the world’s largest iron ore producers, has ordered a fleet of Epiroc blasthole drill rigs; the cable-electric Pit Viper 271 E and the battery-electric SmartROC D65 BE. The equipment will be used at the company’s iron ore mines in the Pilbara region in Western Australia. The driver-less machines will eventually be operated fully autonomously, overseen from Fortescue’s Integrated Operations Centre in Perth more than 1 500 kilometers away. According to Fortescue, the machines will eliminate the need for around 35 million liters of diesel consumption annually.


“Fortescue is at the forefront of the mining industry in reducing emissions from operations and in using automation to strengthen safety and productivity, and we are proud to support them in this important effort,” says Helena Hedblom, Epiroc’s President and CEO. “Not only is this the largest contract we have ever received, but it is also a major step forward for our electric-powered surface equipment.”
Fortescue Metals’ Chief Executive Officer Dino Otranto says: “We’re thrilled to be joining forces with Epiroc to bring cutting-edge electric mining equipment into our operations. The deployment of this new fleet of elec-
tric drills will immediately start reducing our carbon footprint, cutting over 90 000 metric tons of CO₂ emissions annually once the fleet is operational.”
The Pit Viper 271 E rotary blasthole drill rig stands out with, among other things, its zero emissions and its patented cable feed system that prolongs component longevity and reduces operational costs. The SmartROC D65 BE is the new battery-electric version based on the well-proven SmartROC D65 drill rig. The new machine combines the invaluable experience gained from the development of Epiroc underground battery rigs with the many intelligent features of the original version.
Terrah Series: a brand-new product family
FOLLOWING THE ACQUISITION of AARD
Mining Equipment, Epiroc has successfully integrated a new product family of utility vehicles into its global mining and civil construction portfolio. The outcome is the Terrah Series – a hallmark of reliable, durable, and high-performance underground equipment.
With a heritage spanning over 30 years under AARD Mining Equipment, these ma-
chines have been developed and proven in the most demanding African mining conditions.
“The versatility of the Terrah Series is unlocking new opportunities, with strong demand already coming from customers outside of southern Africa. Built to last, the Terrah Series is a sustainable choice,” says Martina Ahlborg, General Manager for the production facility in Chamdor, South Africa.
Epiroc’s President and CEO Helena Hedblom and Fortescue Metals’ CEO Dino Otranto held a contract signing ceremony at Fortescue’s headquarters in Perth.
PORTIA
Gustaf Höök
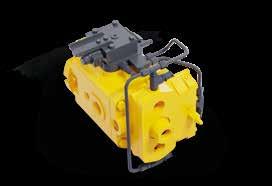
Pump nulling solution reduces line-of-fire
ORIGINALLY DEVELOPED for the Pit Viper 270 series and Pit Viper 291, the pump nulling solution virtually eliminates maintenance visits and reduces line-of-fire exposure related to service of the main pumps. Technicians do not have to manually “re-null” to limit the pressure difference, which eliminates unwanted motion of downstream hydraulic sub-assemblies.
The magazine can rotate the gripper arm, which makes the alignment toward the rig flexible and creates an easier setup.
EPIROC IS LAUNCHING the Diamec Automated Rod Magazine (ARM), a new product that will minimize operator fatigue, provide a safer work environment, and boost productivity. The magazine enables
5.64 million meters
AUTOMATED OPERATIONS offer several advantages to mining companies: savings on fuel, less carbon emissions, and less wear on the machine. Fully automated Epiroc equipment has removed 5.64 million meters of wasted over-drill in surface operations worldwide thanks to improved accuracies, resulting in efficiency and downstream effects of flatter benches.
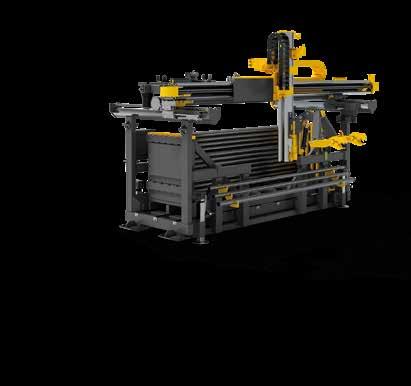
drill strings to be tripped out fully automatically to a pre-set position and tripped in with minimal input from the operator. The release goes hand in hand with Epiroc’s Live Work Elimination efforts.
Product news and innovation stories (choose country and click Newsroom): epiroc.com
Epiroc corporate press releases (click Media): epirocgroup.com
Epiroc dares to think innovatively: seeing possibilities and questioning the status quo.
How do you explore new ways of doing things?

Sandra Malm
Executive Management
Assistant, Rock Drilling Tools division, Sweden
“I strive to step out of my comfort zone to challenge the status quo. Experimentation and collaboration are key for trying new ways to do things, tracking results, and using learnings to improve. I surround myself with great colleagues who give me energy.”

Katrina Robinson
Global Product Manager, Parts and OreBody Solutions, Sweden
“Strong collaboration with multiple diverse departments and teams allows me the flexibility and opportunity to explore new ways of doing things and expand my understanding of new possibilities in the business by incorporating different aspects.”

Katherine Lee
Special Projects Engineering
Lead, R&D, Epiroc Electrification Solutions, Canada
“I try to look beyond the industry for ideas – to automotive, aerospace, and consumer electronics. Whether it’s a design approach, innovative technology, or smarter workflow, adapting proven strategies from different fields often leads to better, more practical solutions.”
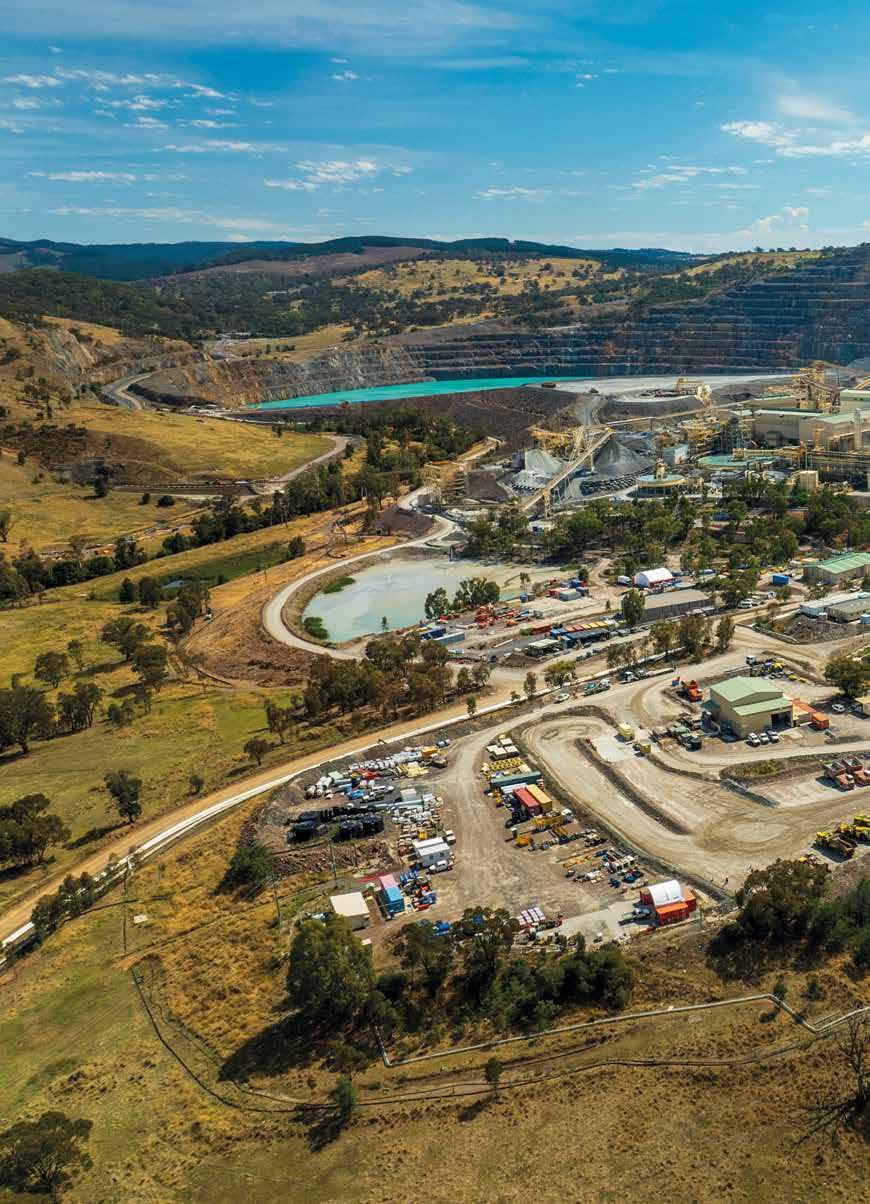
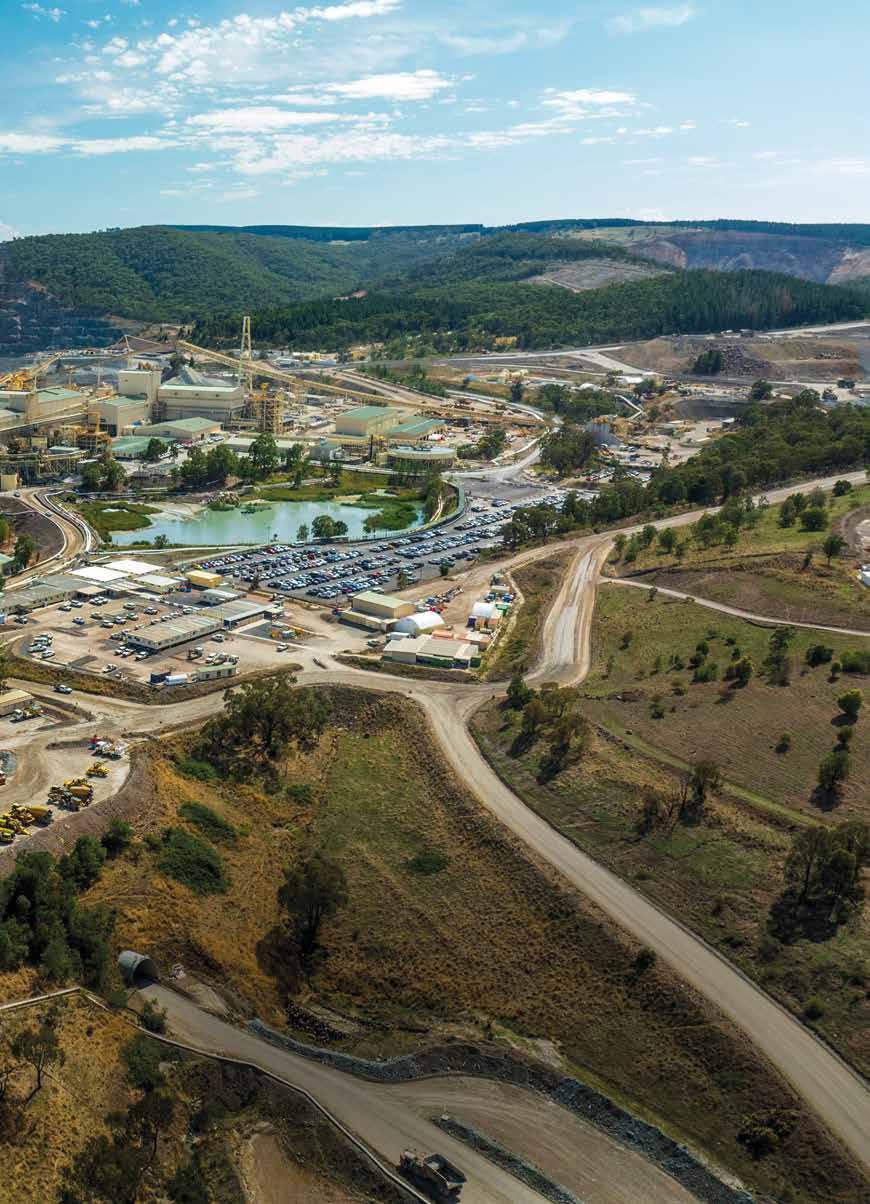
UNLOCKING THE UNMINEABLE AT NEWMONT CADIA
Automation is changing underground mining at its core, with improved safety for operators as one of the most obvious benefits. When Newmont Cadia, Australia’s largest gold mine, wanted to fully automate one of their production levels, they turned to Epiroc for a solution that could handle both loaders and auxiliary equipment – regardless of equipment manufacturer.
Marcus Måård Edwin Davis & Zach Walker
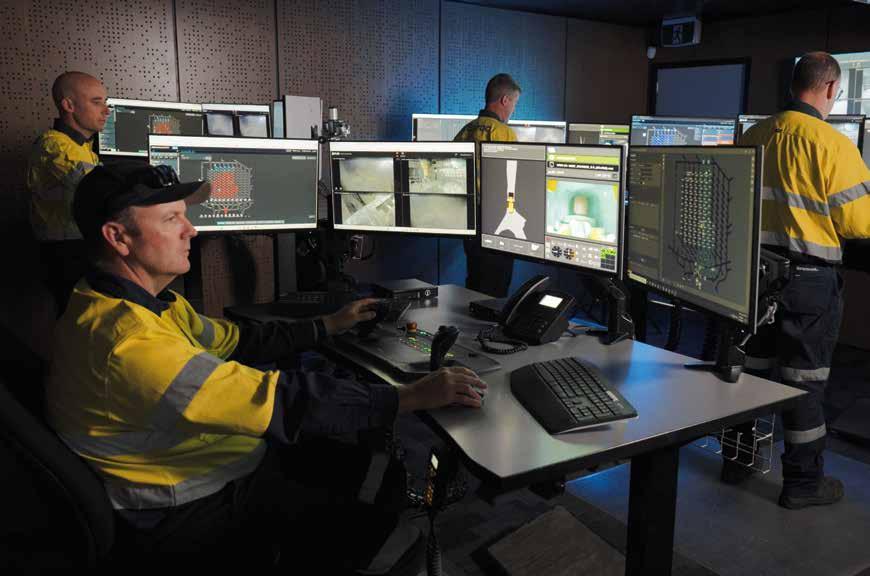
It’s early morning and the air is still cool outside Orange in New South Wales, Australia. The low sun casts long shadows and a soft glow over the rolling hills of the valley – the time of day photographers often refer to as the “golden hour” due to its ideal conditions for capturing dramatic and beautiful images. If you’re lucky, you might even spot kangaroos moving between the trees during the 25-kilometer drive from the city center to Newmont Cadia, one of Australia’s largest and deepest gold mines.
The mining history in the Cadia valley dates back to the mid-1850s and has since evolved from open pit operations to one of the world’s most advanced underground mines. Today, the mine consists of two main panel caves: PC1 and PC2, 1 200 meters and 1 400 meters deep, respectively, which
are mined using a block cave method where the ore body is undercut, causing it to gradually collapse under its own weight. The ore can then be extracted from a production level using underground loaders.
“Block caving gave us a method to mine the large ore body at a relatively low cost. And if we can mine at the right cost and keep our team safe – we can be here for decades to come,” explains Matthew Taylor, Head of Operations, Newmont Cadia.
EPIROC HAS BEEN present at the Cadia operation since 2005 when the development of a new section of the underground mine, Cadia East, was initiated. Since then, the operation has included a large number of Epiroc machines, including the development of the very first Simba E7C production drill rig,
one of Epiroc’s most popular production drill rig models to date. Cadia has also utilized the Boomer M20 face drill rig as well as multiple Scooptram ST18 underground loaders. Adding to this, there are currently about 20 Epiroc employees stationed at the mine, primarily working with service and maintenance of the fleet.
Safety is one of Newmont’s core values, which is reflected throughout its operations globally. Safety is also a big challenge in underground block caving due to the occurrence of inrush and seismic hazards. This was particularly a problem in Panel Cave 1, which motivated Newmont and Epiroc to initiate efforts toward an autonomous production level in 2017, based on a vision of having fully remote operations with no persons exposed to inrush risk.
While Epiroc provided automated
Mark Reynolds, along with other operators, orchestrates the underground machines in Panel Cave 1 from the surface control room using Deep Automation.
loaders for the production level, other types of equipment were needed in case a draw point became blocked by wedged rocks or boulders too large to haul out. This led to the necessity of developing an automation system also capable of handling secondary-break equipment from various equipment manufacturers – something that had never been done before.
The solution was Epiroc’s Deep Automation, a cutting-edge set of systems and applications used to orchestrate the underground material handling flow.
“Never before have we integrated other types of equipment in the same system so we can complete every activity in our extraction level autonomously – without putting people at risk,” says Taylor.
TODAY, THE PRODUCTION LEVEL is fully orchestrated from the surface using Deep Automation, with six to eight Scooptram ST18 loaders working simultaneously, hauling ore from draw points to the crusher. When needed, a rock breaker, a water cannon from MacLean Engineering, or an inspection robot can be navigated inside the production area using teleremote techniques – without interrupting the other machines.
“The development of Deep Automation and the integration of different OEMs and tasks into one system now form a unique capability that both Newmont and Epiroc have – and this can be used in many different mining environments and mining methods,” says Taylor.
Matthew Gibbons, Director of Technology at Newmont Cadia, has been deeply engaged in the development of the automation project during the past few years and sees the interoperability of Deep Automation as a crucial fea-
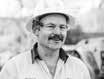
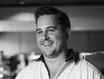
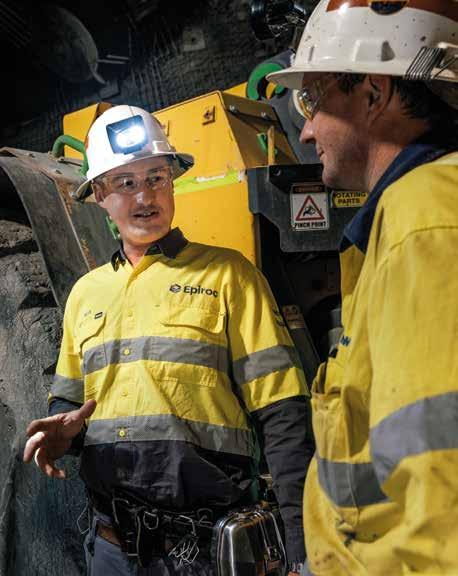
ture for forward-thinking mines with different types of equipment that need to work together.
Founded in 1921
Headquarter located in Denver, CO, USA
Leading producer of copper, silver, zinc and lead
17 managed operations spread across Africa, Australia, Latin America & Caribbean, North America and Papua New Guinea
The only gold producer listed in the S&P 500 Index
“The OEM-agnostic approach is vital for the future of technology in automation. Without Deep Automation at Cadia, we would not operate in Panel Cave 1,” says Gibbons.
THE SURFACE CONTROL ROOM at Newmont Cadia is far from the harsh setting often associated with underground mining. Multiple operator stations are lined up next to each other, while larger screens with dashboards provide a clear overview of the operation for all to see. Here, the operators can enjoy an air-conditioned office as well as a much shorter commute to and from work compared to working underground. Another benefit is the ability to keep the loaders working
Newmont Corporation
Matthew Taylor Head of Operations, Newmont Cadia
Matthew Gibbons Director of Technology, Newmont Cadia
Alex Diamond, Regional Sales Manager at Epiroc, and Michael Meek, Mine Technician at Newmont, in front of one of the automated Scooptram ST18 loaders.
“Without Deep Automation at Cadia, we would not operate in Panel Cave 1”
Matthew Gibbons Director of Technology at Newmont Cadia
over shift changes, unlocking additional hours of production and utilization.
And this is just the start. Epiroc and Newmont hold regular meetings to highlight technical and ease-of-use improvements, which has created a strong partnership over the years rather than a traditional supplier-customer relationship.
“The collaboration between Newmont and Epiroc has been great. We’ve put up some very ambitious challenges, and not once did Epiroc say that they couldn’t do it,” explains Gibbons.
PERHAPS IT IS the combination of cutting-edge automation solutions, open mindsets, and deep collaboration that has been the key to Newmont Cadia’s success – which is also reflected in the production records and the high utilization of the machines. Call it a golden hour for automation, with ideal
Newmont and Epiroc
conditions for brave new ideas to materialize.
With the development of Deep Automation, it certainly looks like the challenges along the way have only helped to strengthen the relationship between Newmont and Epiroc. Guided by their shared vision of pushing the boundaries of technology forward, both parties now remain firmly committed to advancing the future of productivity and safety in mining even further.
“I’ve seen the average performance from PC1 improve, and I’ve seen the record of daily tons increase as well. We hit a new record almost every month or every second month – and it’s really thanks to this great collaboration and great people that we’ve been able to do that,” says Taylor and concludes with a smile:
“The team should be incredibly proud.”
Newmont and Epiroc have a long history of collaboration on both surface and underground mining operations. With the acquisition of Newcrest in 2023, including the operations in the Cadia valley, Newmont has established itself as a pioneer within automation by successfully developing an automated production level where loaders and auxiliary equipment can work together seamlessly.
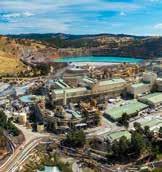
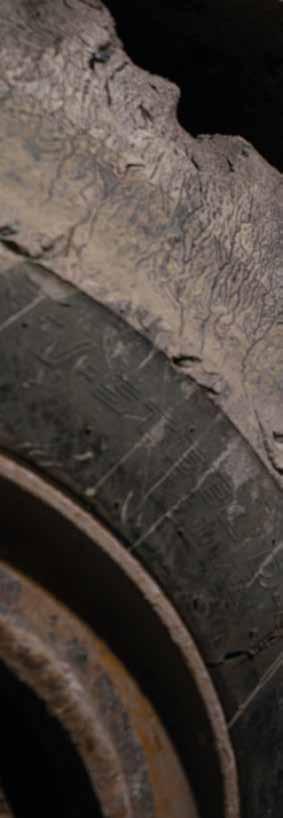
Cadia valley operations
The Cadia deposit was first discovered in 1992
One of Australia’s largest gold mining operations
Located 25 kilometers from Orange in New South Wales
Fully owned by Newmont Corporation
Current life of the mine is 25 years (2050)
Real improvement starts by listening to the customer. Michael Meek, Mine Technician at Newmont, shares firsthand insights with an Epiroc employee.
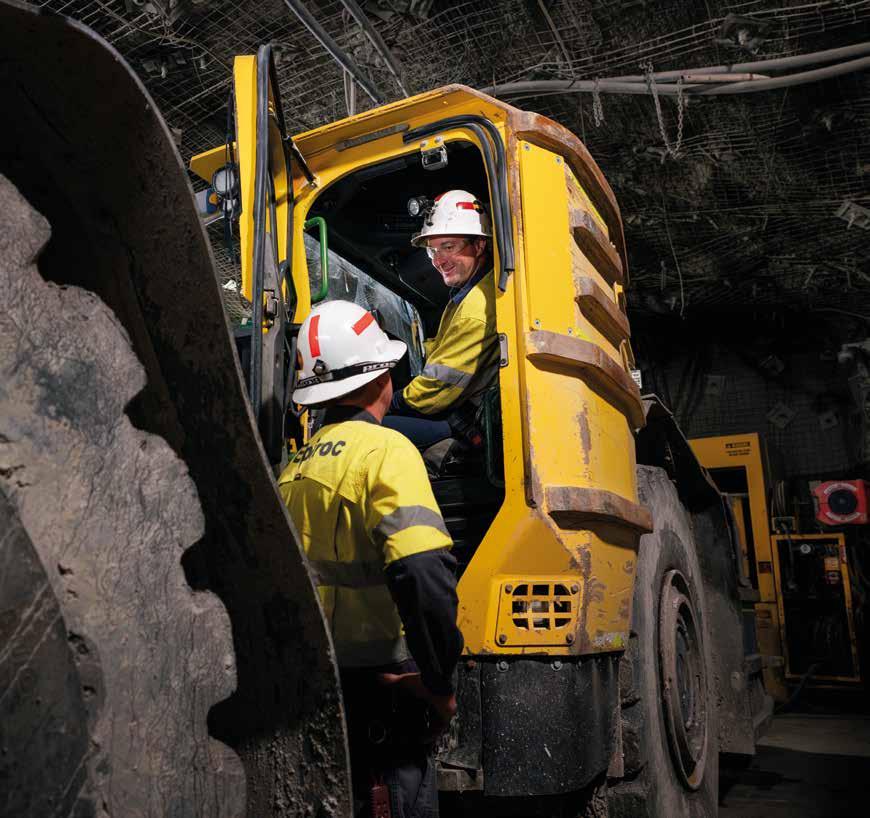
Five keys to success
Collaboration
Collaboration is the foundation of success when developing new solutions – it fosters an open dialogue, a positive and inclusive culture, and a shared commitment to overcoming challenges, driving innovation, learning, and mutual growth.
Ensuring that both parties are fully committed to the project, united by a shared belief in the value of the collaboration and the conviction that their combined efforts will lead to meaningful results and a significantly better solution.
Innovation is about challenging the status quo and daring to think differently. Just because something hasn’t been done before doesn’t mean it lacks value – it could be the breakthrough that drives meaningful change and propels the industry forward.
Recurring meetings that prioritize open dialogue and data-driven insights are essential for continuous improvement. Close collaboration ensures that solutions evolve in step with the operational needs, driving meaningful progress and delivering lasting value.
Open systems
Every mine operates with equipment from a variety of OEMs, making it essential for technology to be developed with compatibility in mind –ensuring seamless integration and reliable performance in a complex, mixed operational environment.
Tech Specs

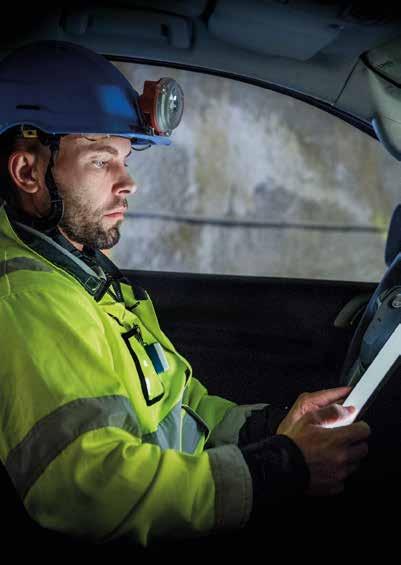
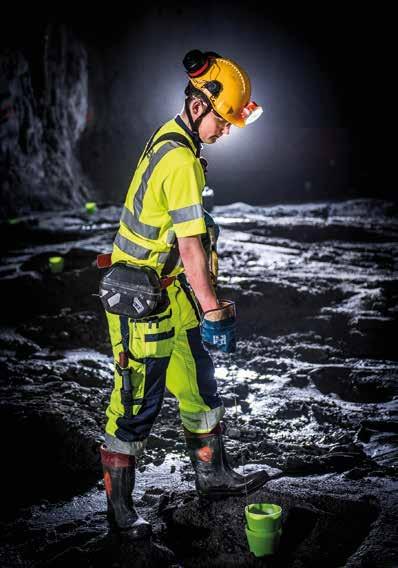
DIGITIZING DRILLING DEPTHS
By switching to a digital solution for registering drilling results, Boliden Garpenberg has saved both time and labor and benefited from improved accuracy in the logging process.
DRILL PLANS IN underground mining are critical for ensuring efficiency, safety, and accuracy in mining operations. The drill plans specify the locations, depths, and diameters of holes to be drilled for the placement of explosives. This ensures controlled rock fragmentation during blasting, which minimizes waste and optimizes ore recovery.
To log the depths of drilled holes, Swedish mining company Boliden traditionally used a manual, paper-based solution that involved keeping track of paper documents and ensuring that they remained dry and clean in the mine environment. To modernize the procedure, Boliden adopted the Drill Tracker solution from Epiroc. Drill Tracker provides operators with digital drill plan sheets on their smartphones, enabling them to track the progress of the drill plan execution. Switching to a digital tool was a necessary step, according to Emma Bjur, Head of Section Project Steering Mine at Boliden Garpenberg.
Why did you switch to a digital solution for logging drill results?
“Boliden Garpenberg is known for being at the forefront of technology, automation and autonomy. We think a lot about how we can improve
processes and routines, and the process of logging drill results definitely had room for improvement. The operators not only had to keep track of a piece of paper, sometimes over shift changes, but also keep the paper dry and clean. All this led to a loss of information at times. We saw a lot of potential with a digital solution, both in terms of saving time and improving results.”
You chose to implement Epiroc Drill Tracker. What are the major advantages of this solution?
“It fits well into the Boliden ecosystem. Now, the operators report drill results in an app on their smartphones, eliminating the problems of lost, damaged or illegible paperwork. The app is easy to work with. It saves time and labor and improves the quality of the results. We’re provided with a near real-time remote overview of the drilling progress, which increases transparency and allows for higher accuracy in planning. We also get better traceability, as it's easy to review past drilling data and identify issues.”
Do you have any advice for other mines looking to switch to a digital drill tracking solution?
“Involve the operators at an early stage, inventory their needs, and find out how you can make their work easier. It’s important to demonstrate that introducing a new solution solves an actual problem. Also, work closely with the developers to solve issues early in the implementation process.”
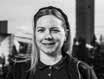
Emma Bjur Head of Section Project Steering Mine, Boliden Garpenberg
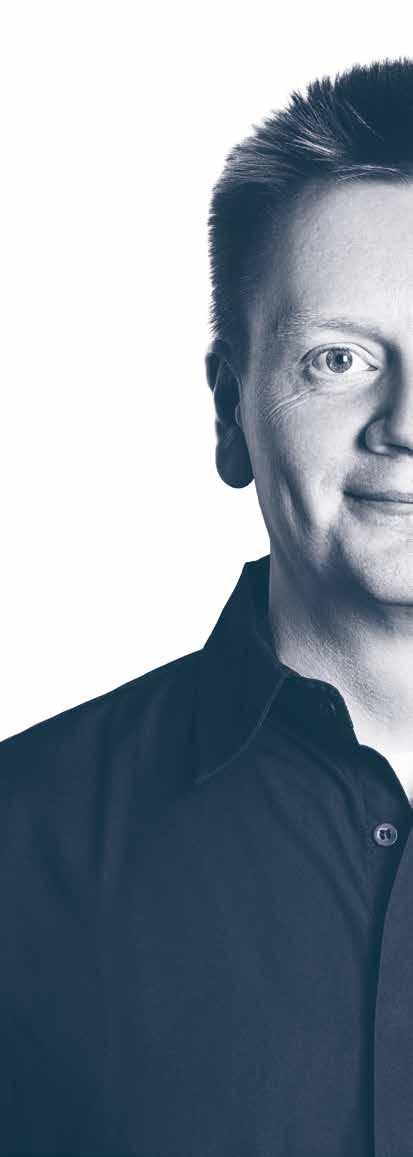
POWERING THE FUTURE OF MINING
Bringing advanced battery-electric drilling to the surface
Committed to decarbonizing their operations, Capital Limited and Epiroc fast-tracked a batteryelectric surface drill – leapfrogging market demand and shaping the low-emission future of mining.
CARL LAGER
Key Account Manager at Epiroc, based in Singapore
POWERING FUTURE MINING
IN AN INDUSTRY under pressure to reduce emissions, Capital Limited and Epiroc have accelerated development of a battery-electric surface drill well ahead of market demand. Their partnership on the SmartROC D65 BE demonstrator shows how a shared vision and urgency can overcome technical and logistical challenges. By stepping into uncharted territory together, they’re advancing equipment design and defining how mining companies will be able to transition to lower-emission operations globally. Tony Woolfe, General Manager, Assets and Supply Chain at Capital Limited, and Carl Lager, Key Account Manager at Epiroc, share how this collaboration came together – and why it’s setting the pace for what’s next.
How did this collaboration come about?
TONY WOOLFE: “We’ve used Epiroc equipment for a long time and were very aware that electrification was the future. Instead of waiting, we asked, ‘What’s on your roadmap? What’s coming next? And how can we help move it forward?’ That led to this collaboration.”
CARL LAGER: “Capital Limited didn’t wait for us to develop a finished product – they pushed us to move faster. They saw where things were heading and wanted to be part of the development, not just the end user. That made a huge difference.”
TW: “A big part of that was sustainability. Capital is moving toward lowering emissions, and we saw that Epiroc shared that goal – not just manufacturing electric rigs, but committed to real change.”

TONY WOOLFE
General Manager, Assets and Supply Chain at Capital Limited, based in Brisbane
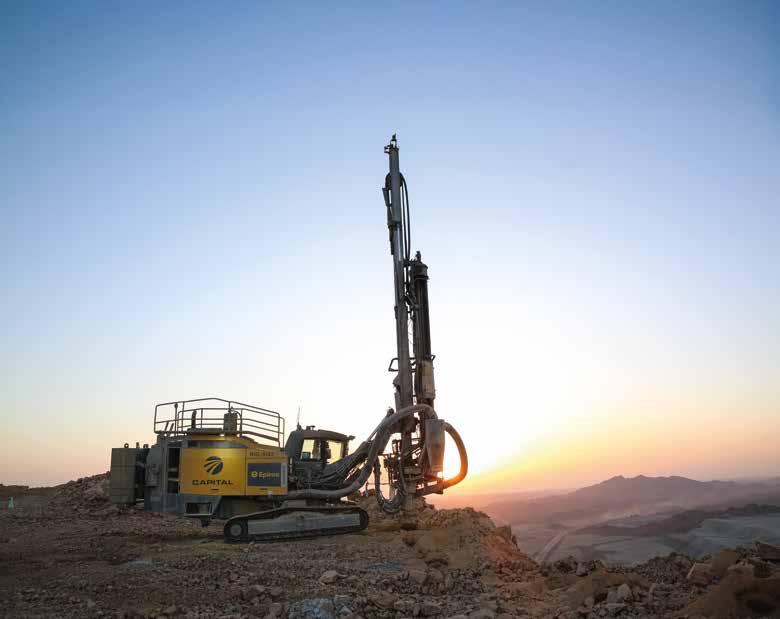
What were the biggest challenges?
CL: “The biggest challenge lies in the limitations of current battery technology. A drill of this size cannot depend solely on today’s batteries as it would require hourly charging. This makes a reliable power grid essential – something many mines are not yet equipped to provide.”
TW: “We had to convince people. There was initial skepticism – questions about operational challenges, power supply, and whether mines were ready for a battery-electric rig. Even within Epiroc, some doubted whether the timeline could be accelerated.”
How did you handle charging?
TW: “Initially, running a diesel generator felt counterintuitive, especially since we first explored connecting the onsite solar farm grid to the pit. However, it wasn’t feasible to install a grid for a single machine test, so in the end, we decided to focus on preparing and proving a battery-electric drill. We found that grid infrastructure for long-term operations could be the second phase. This test is about proving the drill’s readiness, even if it means using a generator while more sustainable options are developed.”
CL: “We also considered alternative fuels, but they either fell short on power delivery or are currently too costly to be viable. Moving to a plug-in electric rig seemed like the best decision, even if it means relying on a diesel genset at the start. This approach allows Capital Limited and their clients to explore using the future green power source that suits them.”
How were you able to move so fast?
CL: “Rather than designing a battery-electric rig from scratch, we retrofitted our proven SmartROC D65, which Capital Limited is already familiar with and trusts. This approach not only allowed us to deliver a working prototype quickly, but also enabled us to concentrate entirely on the power pack, as the rest of the machine was already reliable and well-tested.”
TW: “We weren’t passive – we pushed to move faster. While Epiroc weren't sure about the market readiness for battery-electric surface drilling on this scale and how it would be powered, we got involved early on, giving feedback and solving operational challenges.”
In Focus: Capital Limited
Capital Limited is a leading global mining services company providing a complete range of drilling, mining, maintenance and geochemical analysis solutions to customers within the minerals industry. With a commitment to sustainability and innovation, Capital Limited operates across several African and North American countries, delivering high-quality services that enhance operational efficiency and reduce environmental impact. Active projects include Sukari Gold Mine, Belinga Iron Ore Project, Nevada Gold Mines, Geita Gold Mine, Jabal Sayid Copper Mine, and many others.
How has this changed the way in which you work together?
CL: “Capital Limited sat down with us in Sweden and Vancouver, met the team, looked at the chassis mid-build, and helped shape final decisions. That level of collaboration sped development in ways we hadn’t expected. It’s definitely something I see continuing.”
TW: “People joke that I’m all Epiroc, and they’re right – because we trust their equipment, their team, and their commitment. That’s what makes this partnership work.”
Where’s the rig now?
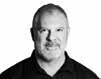
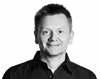
CL: “We’re working through a couple of small snags and conducting final testing in British Columbia, then it’ll be on to Capital Limited’s field trial at the Sukari Mine in Egypt.”
TW: “We chose Sukari because we have a strong technical team there and a great relationship and collaboration with our client, AngloGold Ashanti. Additionally, it’s one of the few mining sites with a large, operational on-site solar farm, which will be important long-term to truly make it an emissions-free drill rig.”
What’s next?
TW: “Once the rig is running at Sukari, we’ll apply what we’ve learnt to future deployments. The goal isn’t just one electric drill – it’s about integrating battery-electric technology across our operations and to actively contribute to moving the industry forward.”
CL: “Epiroc is committed to expanding its battery-electric offerings. By 2030, we aim to have a full lineup of emission-free surface equipment. Collaborations like this are how we get there.”
TW: “Of course, innovation costs. The first quotes for electric infrastructure were in the millions. That’s a hard sell for any company. But we knew that getting in early would set us apart in the long run, and we understood that the current hurdle for our suppliers was the lack of infrastructure strategy. So, we didn’t approach Epiroc with, ‘Build this and we’ll buy it’. Rather, we said, ‘We’ll help build the infrastructure; we’ll figure this out together. Let’s get this moving.’ This project will prove that battery-electric rigs work in real-world conditions, and that’s the first step to broader adoption.”
KEYS TO A SUCCESSFUL PARTNERSHIP 3
To achieve the best possible results when solving complex problems, it is important that everyone shares the same goal. Tony Woolfe (Capital Limited) and Carl Lager (Epiroc) define the success factors of the SmartROC D65 BE demonstrator project.
Communication and trust
Building a relationship based on clear communication and trust ensures long-term collaboration. Mistakes are frustrating and can be costly, but they will happen. By choosing to learn and grow, they also help us improve.
Shared vision and goals
A strong partnership thrives when both parties share common longterm objectives and work together to achieve them. In the end, when Capital Limited succeeds, Epiroc succeeds.
Always moving forward
There’s always room for improvement, so what worked well yesterday may not work best today. Everyone must be prepared to look forward and evolve to stay efficient.
Carl Lager Key Account Manager, Epiroc
Tony Woolfe General Manager, Assets and Supply Chain, Capital Limited
Capital Limited has 11 SmartROC D65 drill rigs operating in the Sukari Mine for AngloGold Ashanti.
EPIROC IN BRIEF
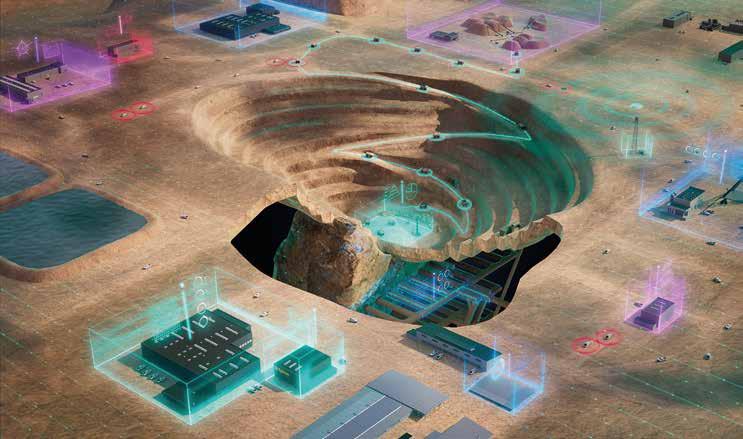
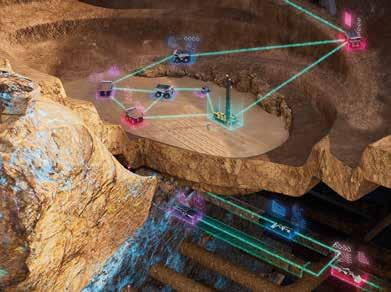
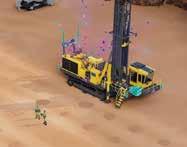
Epiroc’s Groundbreaking Intelligence solutions empower mining operations at machine, fleet, and mine levels for enhanced safety, efficiency, and sustainability.
Empowering mining operations on all levels
EPIROC IS REVOLUTIONIZING the mining industry with its innovative approach to digitalization and automation. Epiroc’s Groundbreaking Intelligence initiative focuses on enhancing safety and operational excellence through OEM agnostic and open technology. This allows mining operations to integrate various systems and equipment seamlessly, regardless of the manufacturer,
thus ensuring optimal performance and safety. By providing a flexible digital mine ecosystem, Epiroc enables effective data management and transforms the data into actionable insights. This empowers mining operations to make informed decisions, improve efficiency, and drive sustainable growth. At the machine level, Epiroc offers solutions that enhance machine utili-
Epiroc launches battery-electric loader for smaller drift sizes
THE NEWLY LAUNCHED Scooptram ST10 G brings Epiroc’s industry-leading benchmark in safety, productivity, and battery autonomy to smaller drift sizes. Built on well-proven technology from the field, this underground loader has been added to Epiroc’s leading electri-
fication portfolio and features a payload capacity of 10 metric tons – and up to four hours of drive time on a single battery charge. The battery can be swapped if needed or benefit from onboard opportunity charging through a standardized CCS charging interface.
zation and ensure a safe working environment. At the fleet level, Epiroc’s powerful scheduling solutions optimize mine plans and provide real-time insights into fleet position, health, and utilization. At the mine level, Epiroc’s integrated planning solutions optimize resource extraction, minimize environmental impact, and ensure regulatory compliance.
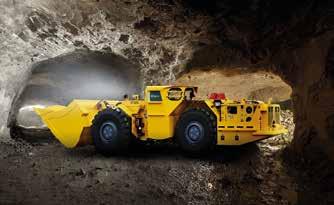
Gustaf Höök
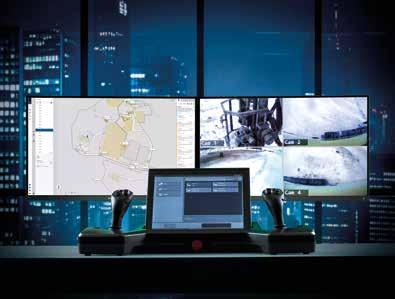
Common
Automation Panel now fully available
EPIROC IS PLEASED to announce the full availability of its Common Automation Panel (CAP) for both of its Rig Control System-based surface drill rig models – Pit Viper and SmartROC DTH MKII. With CAP, operators can control mixed fleets from a single ergonomic station, transforming the remote-control center into a more efficient, costeffective, and safer environment.
“CAP exemplifies our vision of an interoperable control room, allowing Pit Viper and SmartROC drills to be controlled by a single platform. Our customers need solutions that grow with them and adapt to their needs. CAP delivers by seamlessly connecting larger, mixed fleets with ease,” says Christopher Blignaut, Automation Manager at Epiroc Surface division.
EPIROC NEWS IN SHORT
02 03
Perfect your drilling game
Epiroc has launched the DTH 5 hammers, a revolutionary new range designed to maximize efficiency, boost profitability, and redefine versatility. The hammers, designed to excel in all drilling assignments, deliver an exceptional rate of penetration (ROP) and longer service life.
New e-commerce
Epiroc has launched a new e-commerce site (shop.epiroc.com) in Canada and the US, where customers and business partners can purchase a wide selection of original spare parts, rock drilling tools, and hydraulic attachments. The online shop will be rolled out to all countries by 2026.
MiningTAG wins award
Four employees at MiningTAG Powered by Epiroc were awarded with the 2024 Epiroc Safety and Health Award. They played a big role in MiningTAG completing the biggest project in the company’s history (an 8-year project at El Teniente mine) without any lost time incidents.
Want to keep track of what’s happening in the mining and construction industry? Visit miningandconstruction.com for links to industry news and other interesting reading.
Hello there! What's happening in Canada?
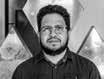
IN JUNE 2024, Epiroc acquired Yieldpoint Inc., a Canadian company that provides advanced ground support solutions that strengthen safety for mining and civil engineering applications. Yieldpoint designs, manufactures and sells advanced digital geotechnical instruments – primarily used for underground mining, tunnelling, and civil construction applications – and has customers worldwide. Daniel Bolivar, Production Manager, elaborates.
What’s new at Yieldpoint?
“We have secured a big order in Mongolia, one of our biggest ever. It involves more than 1 500 units of the d-Exto, a unique rod extensometer, and more than 1 500 Telemetry units. We already had a relationship with the customer, but closing the deal was easier thanks to Epiroc Mongolia. Also, we have been hiring, so the mood is very upbeat.”
Tell us more about the customer challenges you help solve.
“Yieldpoint’s solutions enable mining and tunneling projects to install digital geotechnical instruments and telemetry that can autonomously stream rich rock deformation datasets. These datasets will be analyzed using intelligent data management platforms to enable higher safety for personnel and better design and construction decisions.”
What’s on the horizon for the rest of 2025?
“Our main focus is to keep growing and to further the collaboration with Epiroc. I believe that we are only at the beginning of a very exciting journey together.”
The Common Automation Panel enables operators to control drills from anywhere in the world, offering flexibility, safety, and improved working conditions.
Daniel Bolivar Production Manager, Epiroc
UNIQUE BOOM DESIGN
What lies beneath
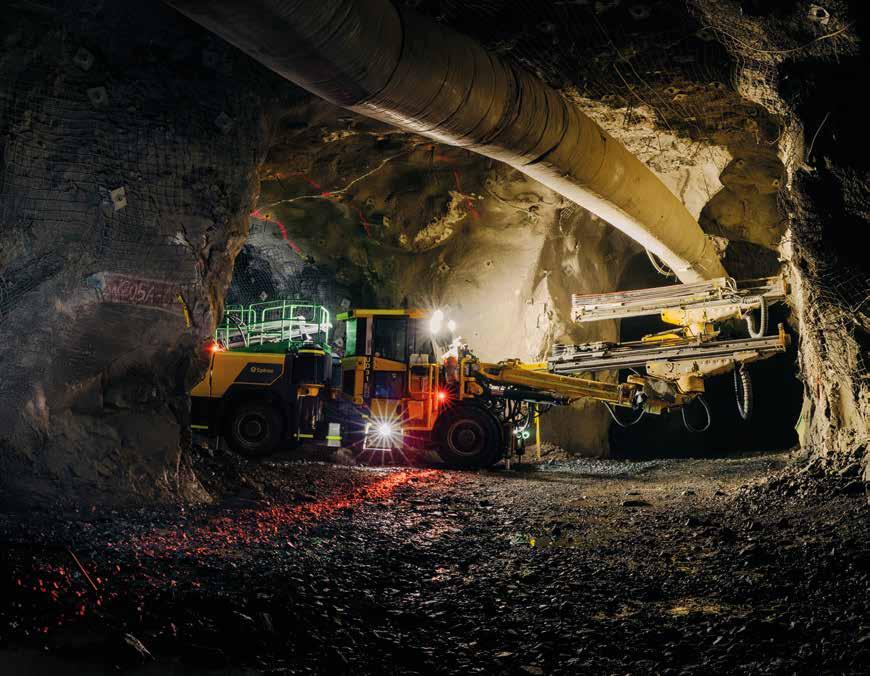
With an innovative hoseless design and its advanced Rig Control System, Epiroc’s Boomer M20 S jumbo drill rig is logging some staggering gains. We travelled deep underground in Australia to witness it in action.
TAWELL MIGHT LOOK like any other Australian regional center. There’s a town hall with a clock tower, a couple of menswear shops, and a pub.
But this small town 237 kilometers northwest of Melbourne is part of a historically rich gold province. In 1853, when gold was first discovered, it was simple alluvial operations. Now, it’s underground on the town’s eastern flank at Stawell Gold Mines – beyond its arch-shaped portal you’ll find 300 kilometers of tunnels that descend a kilometer below the surface.
To mine at these depths effectively, you need best-in-class equipment. Enter the Epiroc Boomer M20 S jumbo drill rig. Pass through the mine’s portal, and vivid Australian sunshine gives way to an
enveloping darkness. The headlights of Mobile Plant Maintenance Superintendent Jake McInerney’s LV kick in as we begin our descent.

After several minutes of negotiating a maze of intersections, the imposing backside of a Boomer M20 S begins to emerge from the darkness. Operator Glenn Walker is maneuvring the 14-meter-long rig to a towering mine face. Its two enormous booms unfold to begin the thunderous work of drilling, bolting and meshing.
PERFORMANCE RESULTS FOR the Boomer M20 S are staggering, the rig at one stage achieving 8 390 development drill-hole-meters-per-week and delivering an average 15 percent improvement in drill-hole-meters-per-hour over the mine’s ex-
Jake McInerney Mobile Plant Maintenance Superintendent, Stawell Gold Mines
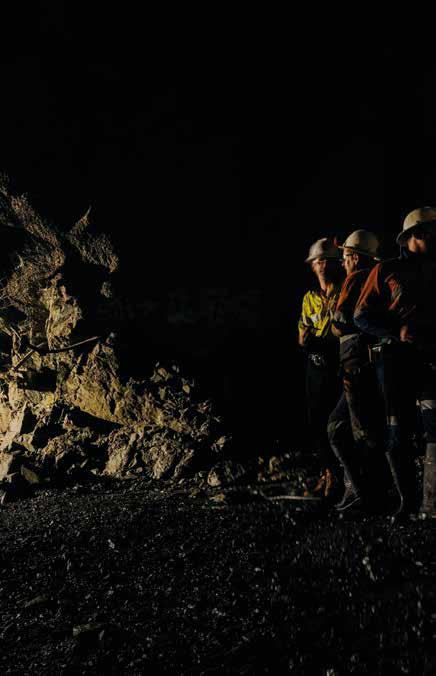
LEARN MORE // Boomer M20 S
Multipurpose rig
THE BOOMER M20 S combines high technology and productivity-increasing features with the benefits from a Rig Control System.
Enable higher precision drilling, better advance rate per round and a more precise tunnel profile. This means numerous synergies in the rest of the drill and blast cycle.
Dual-joystick control panel
Enables multitasking and quicker positioning. Equipped with dedicated modes for scaling, bolting and face drilling. Results in less scaling and overall higher tunnel quality. [ On Location ] Australia
3 meters isting jumbos. But seeing one in person is something else.
Its rockdrills drive into the ceiling seven meters above, oblivious to chunks of tumbling basalt. In the cab, Walker shifts between two touch screens, using the onboard Rig Control System RCS 5 to set the booms into a choreographed dance. It’s a stark contrast to the levered physicality of previous machines.
“Those gains are due to less time scaling and less time marking up,” McInerney says. “Operators get that nice profile because they have RCS 5 onboard to reference from.”
Then there’s the visibility. The Boomer M20 S boasts the world’s first hoseless design, with its hydraulics contained within the booms. Without looms of cabling on its front, there’s a clear view of the mine face, helping with safety and efficiency.
“Often if you see downtime on an older jumbo, it’s a damaged hose,” says Mining Superintendent Jeremy Sargent. “You spend a lot of time chang-
BUT M Pro booms Increases productivity thanks to higher speed and improves safety with better visibility. Easier to maneuver and position. Fewer breakdowns and unplanned stops thanks to internal hydraulics and hoses.
Multirole capabilities and safety features
Can be used for bolting as well as face drilling. Improves safety thanks to drill stop, boom isolation, and safe bolting platform.
www.epiroc.com/boomerm20s More
Operator Glenn Walker manoeuvres his cutting edge Epiroc Boomer M20 S jumbo drill rig deep underground at Stawell Gold Mines in Victoria, Australia.
Digital drill plans
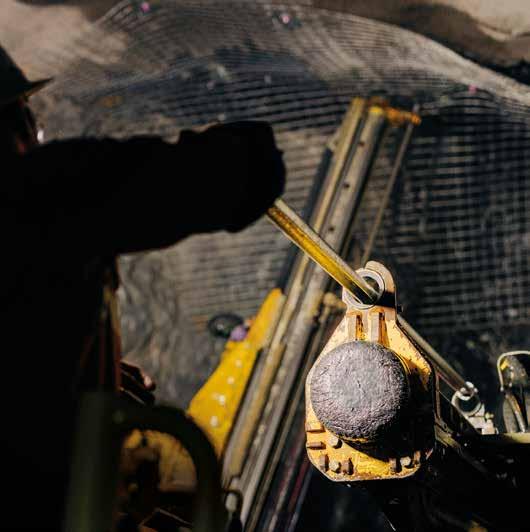
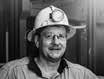
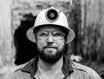
ing them or doing preventive maintenance.”
Not having hoses run into the cab also takes pressure off the Boomer M20 S rig’s air conditioning, helping with comfort.
“Everything is more reliable, consistent and predictable,” Walker says. “The rig simply makes your job more enjoyable.”
STAWELL TOOK DELIVERY of its first Boomer M20 S two years ago (it recently acquired a second) but McInerney says these gains are just a start, as Epiroc works with the mine to roll out its ABC Total automation software, which enables drilling of entire sequences of holes automatically.
“We’re up to 600 holes letting the machine do its own boom movements and find its drill position automatically,” McInerney says.
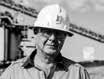
“That’s a small percentage of the total, but if the average rig is drilling 24 000 meters a month, we’re getting maybe 2 000 meters on top.”
“We ultimately want to run it over shift changes and get more of those free meters.”
“That has to do with Epiroc’s support,” Sargent adds. “Over those weeks, they’ve been here training operators and ensuring the rigs do what we expect.”
“It’s been a great journey with Epiroc over more than 20 years,” General Manager Troy Cole says. “They provide commercial support, and we reciprocate by enabling their products to be developed on site. They’re a huge part of what we do.”
Success factors
1. The COP MD20 rock drill – proven in field.
2. Internal hydraulics and hoseless design.
3. Optional batteryelectric driveline.
4. Optional safe bolting platform. No need for the operator to stand under unsupported rock when loading bolts.
wStawell Gold Mines
Stawell Gold Mines has operated since 1981. The site’s underground workings extend from the Magdala portal in a northwesterly direction underneath the town of Stawell.
The mine has been in continual operation since 1981, apart from a brief closure between late 2016 and early 2019.
The mine’s 300 kilometers of tunnels descend up to a kilometer below the surface.
It’s also home to the Stawell Underground Physics Laboratory, which conducts research into dark matter.
The Boomer M20 S features the world’s first hoseless design. That means a clearer view of the mine face, delivering big gains in safety and efficiency.
Glenn Walker Operator, Stawell Gold Mines
Jeremy Sargent Mining Superintendent, Stawell Gold Mines
Troy Cole General Manager, Stawell Gold Mines
THE NEXT-GENERATION DEVELOPMENT RIG
The BUT M Pro booms of the Boomer M20 S jumbo drill rig result in less unplanned downtime for hose repairs.
Stawell
Stawell (pop. 8 397) is located 237 kilometers northwest of Melbourne. With Bendigo and Ballarat, it forms the “Golden Triangle” – historically one of the world’s richest gold mining provinces.
Settled as Pleasant Creek in 1853, the town was renamed Stawell in 1864. Stawell is also known for the Stawell Gift, one of the world’s most prestigious foot races.
Stawell Gold Mines
Opened
Stawell Gold Mine has been in operation since 1981.
Gold
Stawell Gold Mines is located within the “Golden Triangle,” a region historically rich in gold.
Depth
Stawell Gold Mines operates along 300 kilometers of tunnels at depths close to one kilometer.
Due to the hoseless design, the operator has far better visibility from the cabin, which greatly improves operator safety.
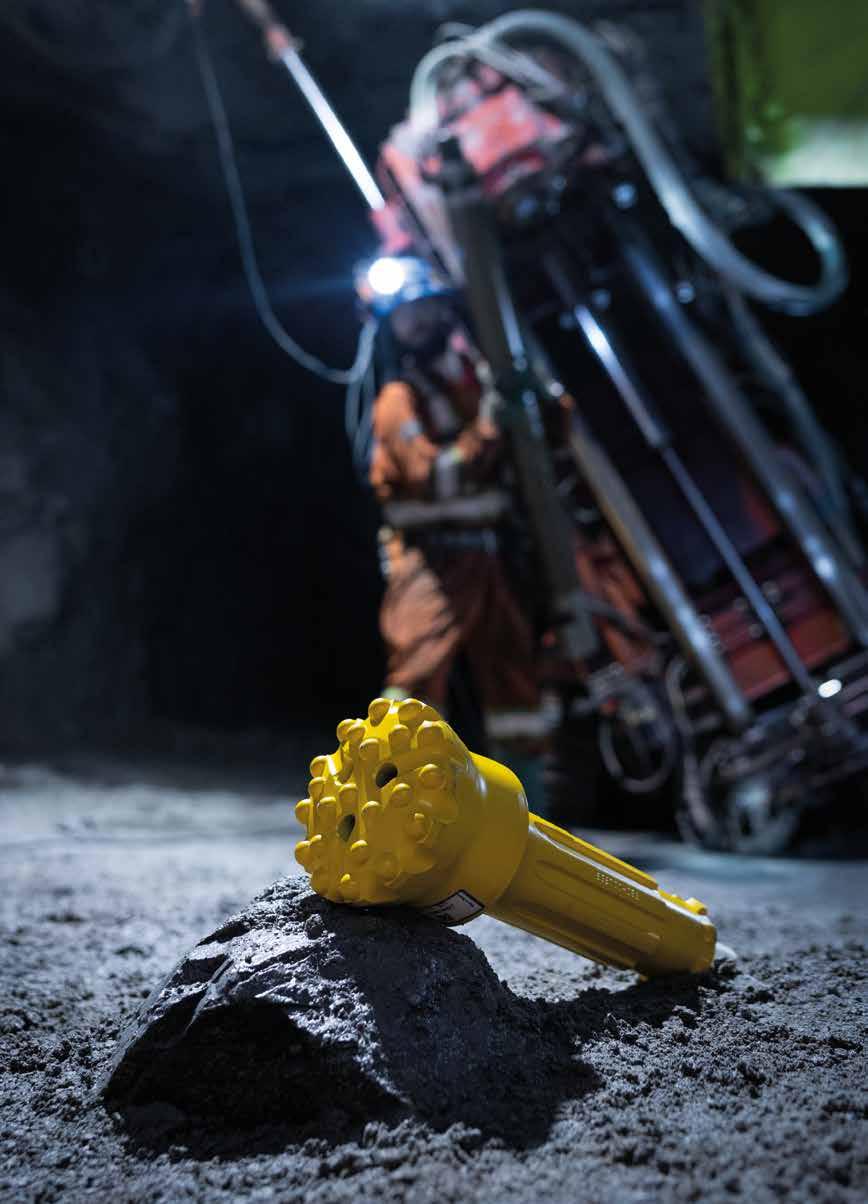
Protecteddiamondsby
After taking a chance on an innovative new drill bit, Machines Roger is saving money and exceeding its drilling targets in rugged northern conditions.
THE CHALLENGE 1
IT’S PROBABLY NOT surprising that drilling is no easy task in Nunavut, Canada’s largest northern territory, which borders the Arctic Ocean. Underground mining contractor and long-time Epiroc customer, Machines Roger International, experienced that firsthand while completing production drilling work for a mine in the territory.
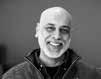
The hard and abrasive rock conditions at site forced drillers to change out or regrind the standard carbide drill
bits they were using every five to 10 meters, equating to seven-to-10-bit changes per shift. It was time-consuming, costly, and unproductive for the company – particularly given that the typical hole depth operators needed to make was 30 meters.
“In these conditions, the standard carbides will wear rapidly, and we don’t achieve the required depth to drill productively,” says Shakeel Khalfan, Manager Business Development & Technical Service at Epiroc.
THE SOLUTION 2
IN JULY 2023, Machines Roger began trialing eight Powerbit X drill bits from Epiroc in the harsh conditions at the Nunavut site. At first glance, the Epiroc Powerbit X has a similar design to a standard carbide drill bit, and a range of sizes from 45 millimeters to 115 millimeters covering face drilling and production drilling portfolios. However, it is manufactured with a protective polycrystalline diamond layer over the carbide, meaning a sintered-together mass of randomly oriented diamonds. The diamond mixture is applied to each button of the bit and exposed to high pressure and temperature to create a protective, durable structure. Powerbit X is built on Epiroc’s premium platform, sharing the same high-grade steel and advanced heat treatment process as our top-performing conventional drill bits.
“Those crucial differences allow operators using the bit to drill in hard or
abrasive rock for much longer periods before having to change out the drill bit,” says Khalfan. Not only does that improve productivity, allowing operators to hit their drilling targets more quickly during their shifts, but it also increases operator safety.
“It’s keeping them away from the face of the rock,” continues Khalfan. The Powerbit X also opens the door to greater use of automation. “What we’re striving for is autonomous drilling, that is the future – operators on the surface working their drills with a remote setting, or teleremotely from another location. That generates savings, not having to have someone underground changing bits.”
Additionally, longer-lasting drill bits with no need for replacement or regrinding can help to reduce the carbon dioxide emissions per drilled meter by up to 90%
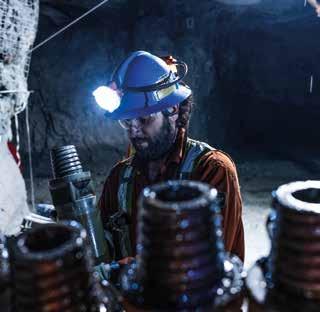
THE RESULT 3
MACHINES ROGER quickly saw the benefits of the Epiroc Powerbit X bits. The rugged diamond-protected bits exhibited an average service life during the trial of more than 400 meters per bit – a major productivity improvement that has allowed operators to not just meet their drilling meter targets but exceed them, and work for multiple shifts without needing to switch out a bit. The bits also demonstrated a consistent penetration rate and diameter, improving hole quality.
Working at a remote location comes with logistical challenges, including the complex and costly business of inventory management and transporting a year’s worth of drilling tools to the site. The Epiroc Powerbit X has been a game-changer in that regard: Machines Roger only requires about 12 bits per month, which can be easily transported to the mine on regular flights with mine personnel.
“Machines Roger has been using the Powerbit X in production drilling for the past year, where the bits have achieved an average 700-meter service life,” says Khalfan. Epiroc also tested the bits in mixed ground conditions at other sites for development drilling, where they achieved an astounding service life of more than 1 000 meters.
www.epiroc.com/powerbit-x
Shakeel Khalfan Manager Business Development & Technical Service, Epiroc
The driller must take multiple trips from drill rig to rack, which is approximately three meters away, handling tubes that are 1.8 meters in length and weigh 24 kilos each.
In Focus
EXPLORATION
ORIENTATION / ON SITE / PERSPECTIVE / SURVEY / SEVEN THINGS
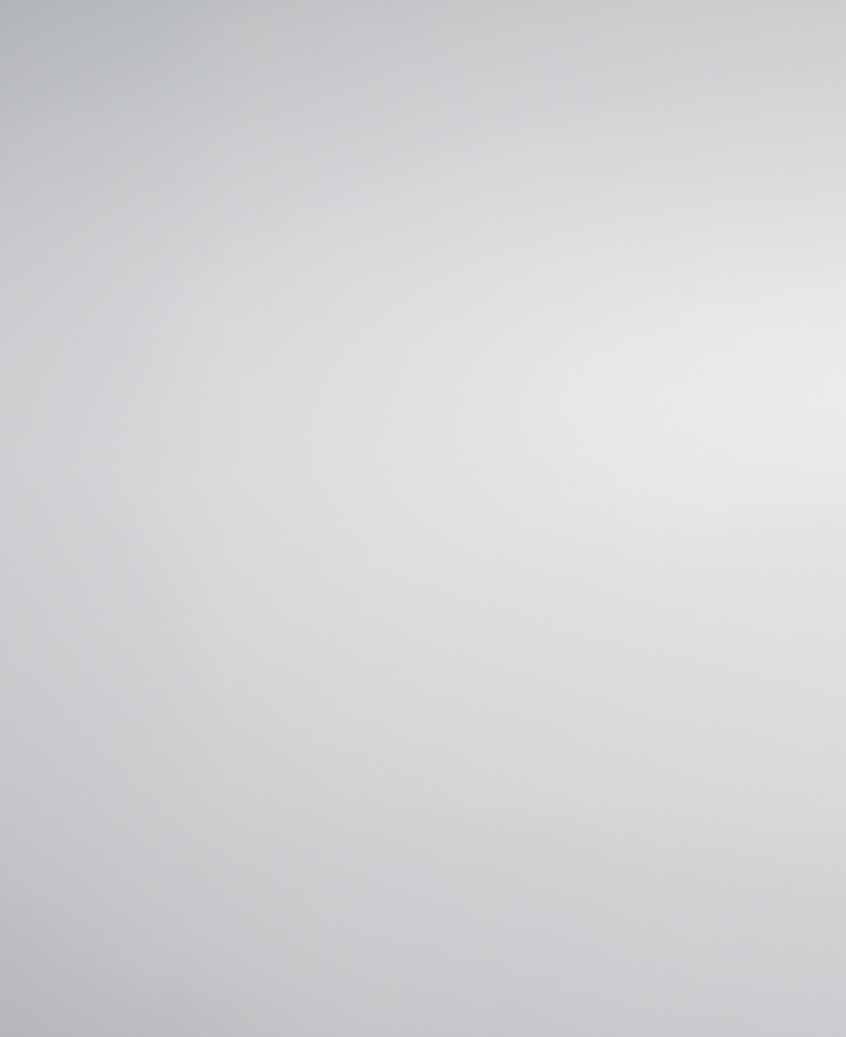
Exploration is a curious blend of instinct and industry – of ancient drives and cutting-edge tools. Whether it is space, the seafloor, or subsurface deposits, the world is opening up in new ways. In this issue, we look at what fuels the search, who leads it, and how we can explore even smarter.
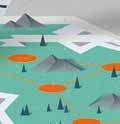
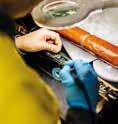
The demand for metals is soaring. But how do we find what’s hidden, buried deeper and in harder places?

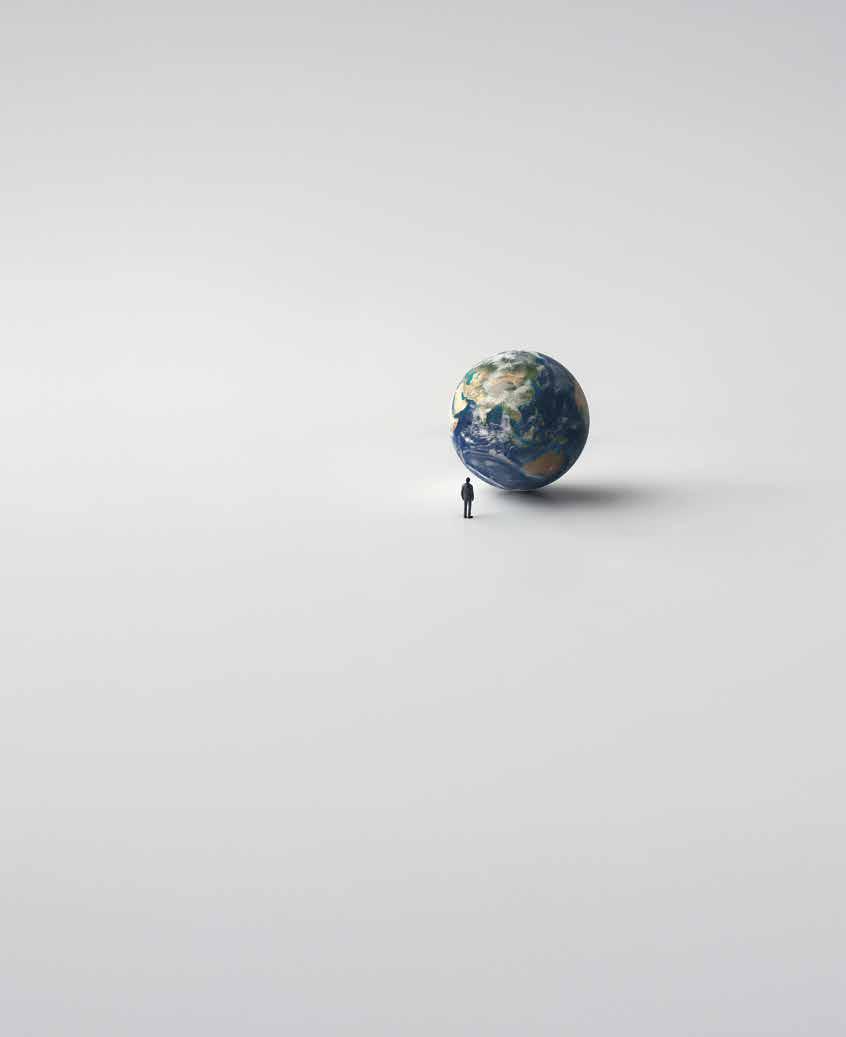
In Australia, Epiroc is building a new exploration powerhouse. It is a story of technology, teamwork and trust.
38
PERSPECTIVE A century of curiosity
The Explorers Club has a proud (and occasionally peculiar) history of championing curiosity. From Everest to the Mariana Trench, exploration means pushing boundaries – both scientific and human.
40
SURVEY
The next frontier
What is standing in the way of future exploration? Experts share their thoughts on depth, grade, geopolitics, and public trust – and how tech and transparency may be the key to a more resilient supply chain.
41
SEVEN THINGS
Hidden heroes of discovery
We have all heard of Magellan and Amundsen. But what about Xu Fu or Mary Kingsley? Here are seven explorers whose remarkable journeys have reshaped how we see the world – and what we value in it.

SCANNING THE DEPTHS
The need for new metals and minerals is increasing all the time, and to meet that demand, more focused exploration is required. How do we get there?
INFORMATION IS THE key to success. It’s something that Magnus Ericsson knows very well. In the 1980s, he was one of the founders of Råvarugruppen, which continuously collected annual reports from mining companies around the world, compiling everything in a unified database.
“It became a unique source of knowledge that enabled the industry to better plan for the future,” says Ericsson, who still runs the company, which is now called RMG Consulting.
The need for knowledge is at least as great today – and perhaps even more in-depth. Both visually and literally. Because what lies below ground needs to be discovered sustainably if the world is to cope with the future energy and material transition.
“You now need to go deeper to find deposits, because the most easily accessible high-value ores have already been mined, and you may have to work in areas that are completely different to the ones that have traditionally been a source of material. This makes the work both more difficult and more expensive,” says Ericsson.
Innovative prospecting is crucial to success, he says. And that’s precisely why the research he carries out, in his role as Professor of Mineral Economics at Luleå University of Technology, is concerning. Ericsson believes that exploration expenditure is rarely linked
to demand, but rather goes hand in hand with fluctuations in the price of metal during the previous year.
“When prices rise, more money is allocated to prospecting, and when prices fall, less. This isn’t an optimal approach. What you should do is look more at the actual future need for metals,” he says.
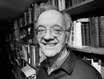
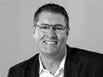
THE REASON FOR this is the challenges associated with prospecting. Costs are high and guarantees are few. According to Ericsson, more research and development is needed to make exploration both smarter and cheaper. Having fewer conflicts around the world would also help, as peace makes potential deposits more explorable.
“Ideally, there should be a clear upward year-on-year trend in investment. If not, it means that there is too little prospecting going on,” says Ericsson.
Errol Smart, former CEO Orion Minerals in South Africa, agrees. He de-
scribes the current situation as “a race to discover and develop new mines”, all at a time when the industry has experienced “decades of under-exploration”.
“Because of this, we find ourselves in a situation where the current supply of minerals cannot meet the world’s needs.”
Smart, whose former company focuses on mining operations in the northern Cape Province, believes that exploration in particular is a challenge for investors, as it requires them to invest money in something that takes a long time to get a return. If there even is a return.
INDUSTRY ORGANIZATION Minerals
Council South Africa, where Errol Smart is a board member, is doing its part to highlight the conditions facing mine operators.
“Investors need to know that they are investing money in a stable environment, where laws and taxes do not change overnight. Prospecting is stimulated by clear and reliable regulations where everyone knows what applies,” says Smart.
In his opinion, the fact that there is too little prospecting today is concerning, but does not constitute an insoluble problem. The world’s needs to speak up for an upturn in the industry, and new technology can help.
“Prospecting is largely a data-driven process,” says Smart. “You collect a lot
Magnus Ericsson Professor of Mineral Economics, Luleå University of Technology
Errol Smart Former CEO, Orion Minerals

“Exploration is the backbone of the minerals cycle”
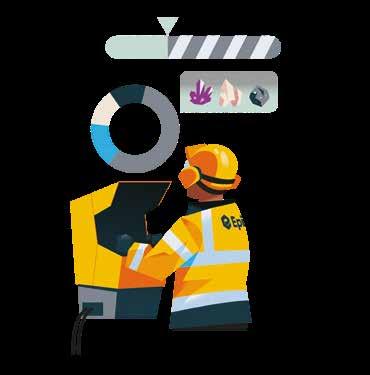
of information and the more data you have, the more analysis you need to perform. That’s good news, because the technology we now have at our disposal means that we can be much more efficient and accurate.”
ACCORDING TO Tatiana Aguilar, key responsible for the Mining and Metals Industry at the World Economic Forum (WEF), things are really taking off. When the organization launched two open innovation challenges during 2024–2025, aimed at start-ups and universities, many exciting ideas were presented. Several of these took advantage of AI.
“It is therefore fair to say that AI is already transforming mineral explo-
ration by enhancing efficiency, reducing costs, and improving decision-making,” says Aguilar.
This is necessary, because exploration is what she calls “the backbone of the minerals cycle”:
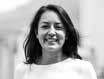
“High-quality exploration allows for better design of mining projects, leading to a more sustainable performance, greater efficiency, and a deeper understanding of the soil.”
Tatiana Aguilar would like to stress that the current situation with increased demand for new minerals and metals offers the industry an excellent opportunity to redefine its role, enabling it to take responsibility for a sustainable future.
Platform for collaborative action
SECURING MINERALS FOR the Energy Transition (SMET) is an initiative launched by the World Economic Forum in 2023. Among other things, it aims to facilitate political dialog, remove barriers, encourage innovation, and stimulate investment so that supply meets future demand for critical minerals. The latest report focuses on concrete innovations
as the way forward.
“It highlights that sustainable innovation enables the identification of deposits more quickly and cost-effectively, including high-grade and deep-seated deposits that might otherwise be overlooked,” says Tatiana Aguilar, Manager Mining and Metals Industry, World Economic Forum.
“By engaging transparently with civil society, policymakers, innovators and development institutions, the industry can strengthen trust and build long-term partnerships,” she says.
To succeed, global collaboration is essential. WEF assists in establishing such dialogs, with the aim of facilitating increased prospecting and even offers more concrete collaboration spaces.
“Collaboration is essential in addressing these challenges, as no single country can independently secure a stable and sustainable supply, and no single company can create a resilient value chain,” says Aguilar.
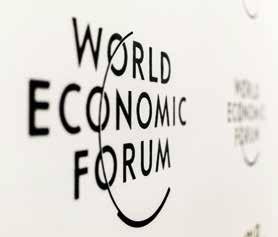
Tatiana Aguilar Key responsible for the Mining and Metals Industry, World Economic Forum
Tatiana Aguilar Key responsible for the Mining and Metals Industry, World Economic Forum
In Focus

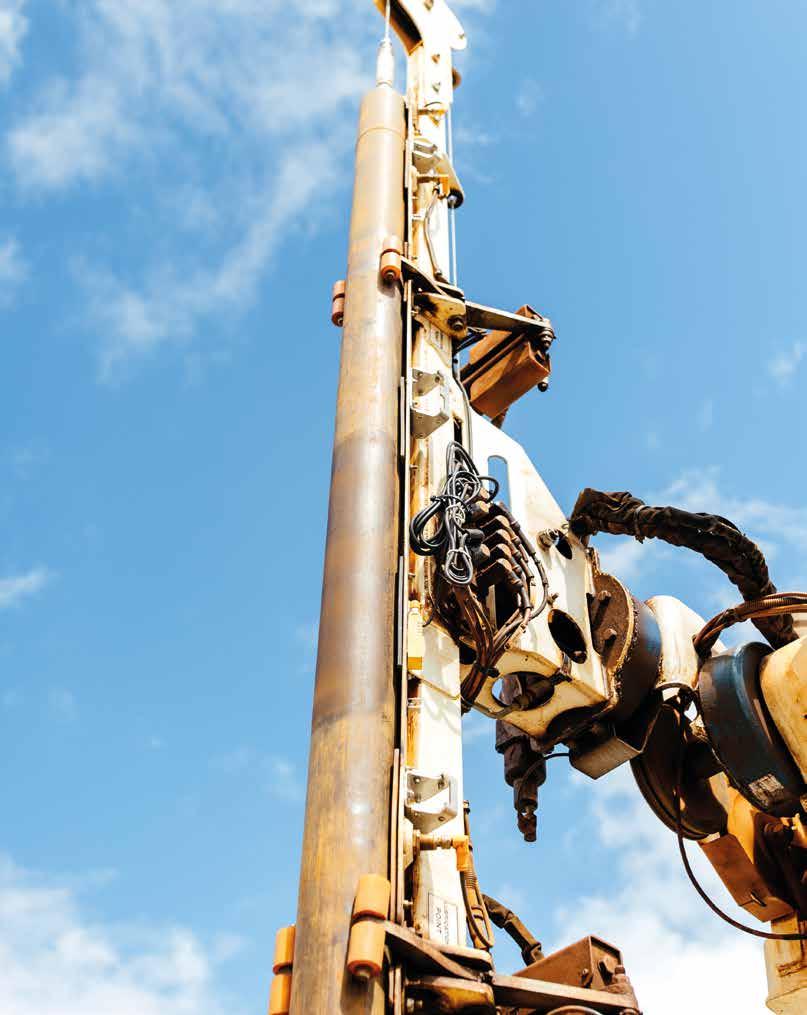
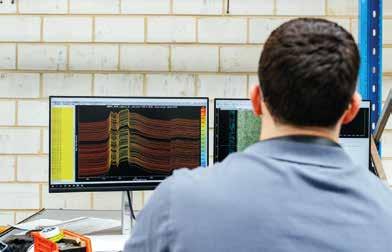
“Understanding what’s ore and what’s waste in near real-time has huge implications for mining and supply chain decisions.”
Penny Dent General Manager for Mining and Technology, Epiroc
Meet the explorers
Exploration is a traditionally tough sector in the mining business. But where others see adversity, Epiroc is utilizing the latest developments in technology to discover new and exciting opportunities.
EW ACQUISITIONS. Epiroc has made a habit out of them in recent years. Large-scale investments in automation, electrification and digitalization make immediate sense in the modern world. But exploration?
It’s the first question to ask Alex Grant while sitting in his office in an industrial park on the outskirts of Perth, Australia.
[ On Location ] Australia
Exploration is hard. Any miner will tell you that. Greenfield exploration can last anywhere from two to eight years, with limited guarantees of return on investment. And by nature it’s cyclical, with mining companies historically scaling back on exploration when times are tough.
Yet Epiroc is betting big on exploration and geosciences. You only need look at some of its acquisitions over the past five years.
There’s Schramm, for decades regarded as the industry leader in reverse circulation drills.
There’s Corescan, with its cutting edge Hyperspectral Core Imager (HCI) technology. And then there’s Kinetic Logging Services (KLS), where we are now.
Walk out of Grant’s coolly decorated office through a door on your left, and you’re inside an expansive workshop, engineers buzzing around different Fuso trucks. Some are brand new, others coated in dust from logging time in the Pilbara, their cabs decorated in artwork by indigenous children from the region. All are equipped with a sophisticated OreSight probe, developed in collaboration with French space optronics and neutron technology company Sodern.
Schramm, Corescan and KLS are all barely a five-minute drive from each other in Perth, but together they give Epiroc an enormous leg-up in exploration mining.

Penny Dent General Manager Mining and Technology, Epiroc
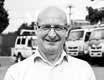
Alex Grant Vice President Marketing OreBody Solutions, Epiroc
“Exploration isn’t easy,” says Grant, Epiroc’s Vice President of Marketing in OreBody Solutions. “But new technologies are beginning to mature just at a point where, globally, we’re starting to exhaust that low-hanging fruit in terms of deposits.”
“We’re moving into a lower grade future,” agrees Huw Rossiter, Business Development Manager of Geosciences. “If you’re used to getting 4–5 grams per ton of copper, and now it’s 0.6 grams per ton, those deposits wouldn’t have stacked up as a business case 20 years ago. But with these advances in technology and geosciences, they can.”
BUT MUCH OF Epiroc’s investment in exploration and geosciences will be borne out on existing mine sites in brownfield usage cases. According to Grant and Epiroc’s General Manager for Mining and Technology Penny Dent, the potential gains are staggering.
“What surprised us is that a tier one or tier two producer can dig out the ore, get it on a ship, and there’s the potential they don’t know with a great degree of certainty what’s going out there,” Grant says. “That ship arrives at its destination and maybe they have to offload it and redo the blend to get, say, the iron content higher. Imagine how many millions it costs to fix that.”
Dent’s background before Epiroc was work-
Q&A
Marie Bergman, Product Line Manager, Epiroc Surface division
ing for a tier one mining company, lending her unique insight into these challenges.
“Epiroc was thinking of these technologies as an exploration tool,” Dent says. “But I thought, ‘There are millions of dollars in this as a production tool.’ Understanding what’s ore and what’s waste in near real-time has huge implications for mining and supply chain decisions.”
This is OreSight, KLS’s sophisticated downhole assay technology. Key to OreSight is a probe equipped with a pulsed neutron generator. Once initiated down a blast hole, the generator results in the emission of gamma photons from the surrounding elements, with each producing characteristic energies. Those energies are digitized, identified and quantified, and sorted into a spectrum that describes the chemical composition of the formation. The data is automatically transferred wirelessly to KLS’s real-time operations center.
It’s a highly automated system with the operator remaining in the air-conditioned comfort of the Fuso, meaning zero manual handling.
“There are other safety advantages too,” Dent says. “On a mine site there are material risks and hazards that we’re always proactively identifying to keep people safe. These tools can provide essential structural, geotechnical information about, say, pit wall stability, and that informs safety decisions.”

Bringing exploration into the Epiroc fold requires new ways of doing business. Mining & Construction sat down with Marie Bergman, Product Line Manager Capital Equipment, OreBody Solutions, to discuss how the company is tackling its expansion both in terms of products and customer support.
Q How does acquiring Schramm, Kinetic Logging Systems and Corescan benefit Epiroc customers?
A “It opens the door to more customers, but also provides more services to existing customers. We can tap our enormous network to provide better support and services, wherever our customers are in the world.”
Q Was it important to acquire all three of these businesses?
A “If we wanted to become number one in exploration we needed Corescan, we needed KLS, we needed Schramm – all of which provide very different technologies. Bringing them into the Epiroc family adds immensely to our portfolio, extending our offering to include exploration-to-port strategy.”
www.epiroc.com/exploration-orebody-solutions More
Q Is an exploration customer different to other customers?
A “They can be. If you have a customer only operating in exploration, they tend to be smaller family-owned companies, which means their needs are different. We need to provide them with the best aftermarket support, but we can also provide them with financing options through our Epiroc Financial Solutions arm.”
Q Epiroc has a fantastic reputation in terms of both its equipment and its aftermarket support. How do you maintain that while taking on this expansion into exploration?
A “Epiroc has the ability to grow this segment of the business due to extensive coverage from our customer centers globally. This enables us to reach most parts of the world, both when it comes to selling new equipment but also providing support for already delivered equipment.”
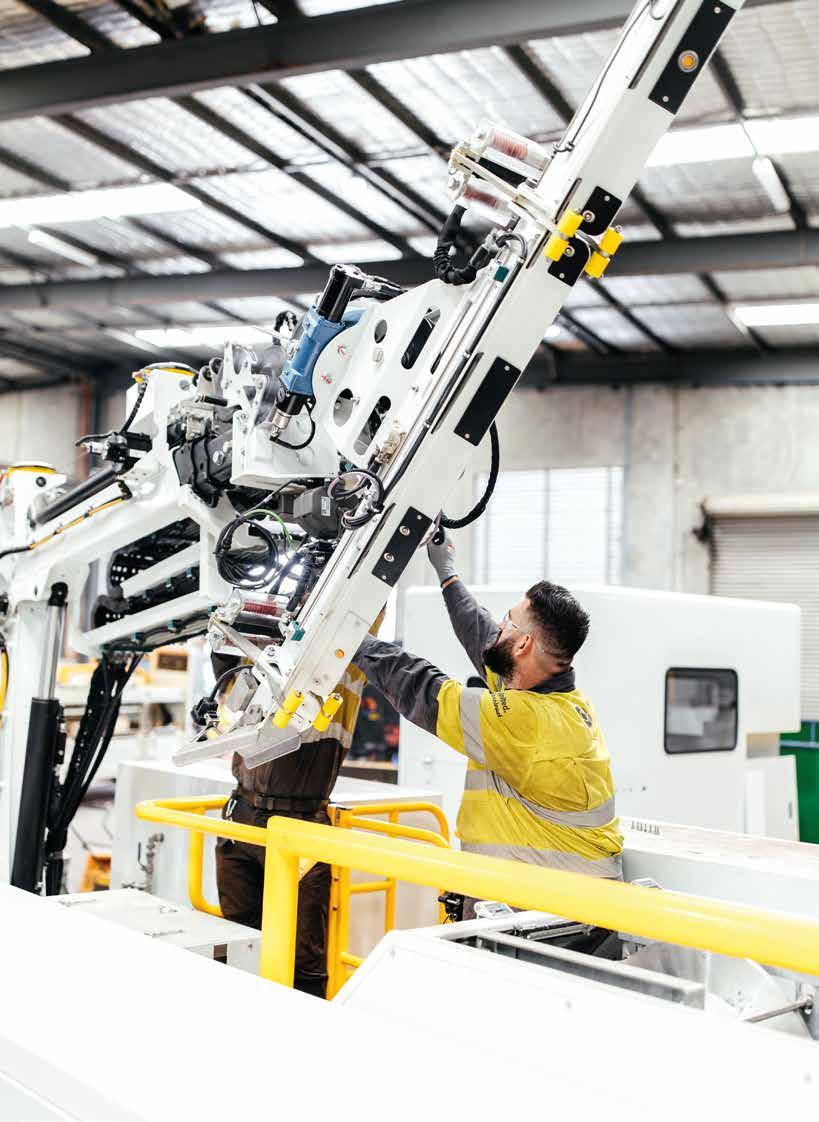
KLS’s OreSight downhole assay solution features a probe developed in collaboration with French space optronics and neutron technology company Sodern.

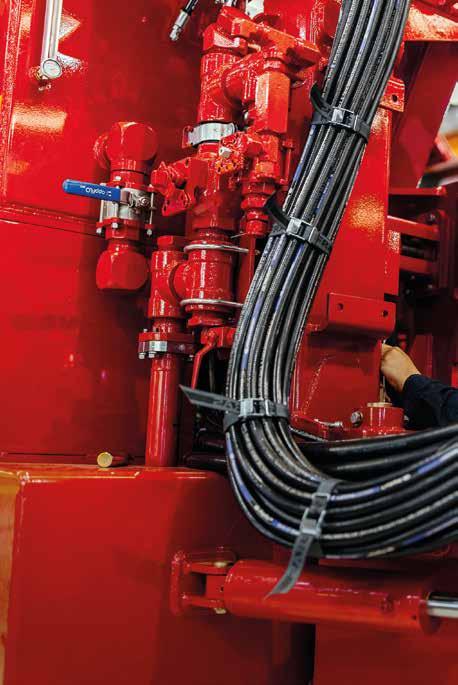
Oresight isn’t Epiroc’s only tech showstopper. Later, Dent drives us to an adjacent suburb and pulls up at an unassuming tree-lined warehouse. In its driveway is a shipping container detailed in Epiroc’s – and now Corescan’s – yellow and grey livery.
Walking past the container into the warehouse proper, we’re faced with shelves of timber pallets stacked high towards the ceiling. Dent slides open a pallet to reveal trays of precisely labelled core samples, each a few inches in diameter.
They’ve been shipped to Perth for analysis by Corescan’s HCI. A team of technicians takes a tray and loads it through a front window of the container onto a three-axis translation table. It whirs into action and runs the tray under an array with three sensors – a 25-micron pixel resolution RGB camera, a 3D laser profiler, and an infrared spectrometer – to produce a detailed analysis of each core sample, with the results appearing on twin LCD screens at the end of the container.
“Artificial intelligence is the next frontier, that’s really why we want to move into exploration more.”
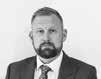
It’s impressive stuff, even if HCI was first developed by Corescan in the early 2000s. But what once took 60 minutes now takes around five.
“People can make decisions quicker in greenfield exploration, but also maximize quality from a production standpoint,” Grant says.
“There are sheds around the world with core waiting to be processed. We have the ability now to get this pushed through very quickly. It pretty much comes out of the ground and you can get results.”
THE FINAL PIECE in Epiroc’s new focus on exploration is Schramm. This company’s reputation in reverse circulation drilling by now speaks for itself and illustrates this round of acquisitions isn’t just about the cutting edge.
Not that its workshop is any less impressive. Schramm's engineers are in the final stages of assembling a T685 crawler rig. In its signature bright red paint job, with an enormous mast and powerful deck-mounted diesel engine, it’s an im-
Corescan’s Hyperspectral Core Imager (HCI) technology was first developed in the early 2000s. But what once took 60 minutes now takes little more than five.
Alex Grant Vice President of Marketing in OreBody Solutions, Epiroc
Huw Rossiter Business Development Manager Geosciences, Epiroc
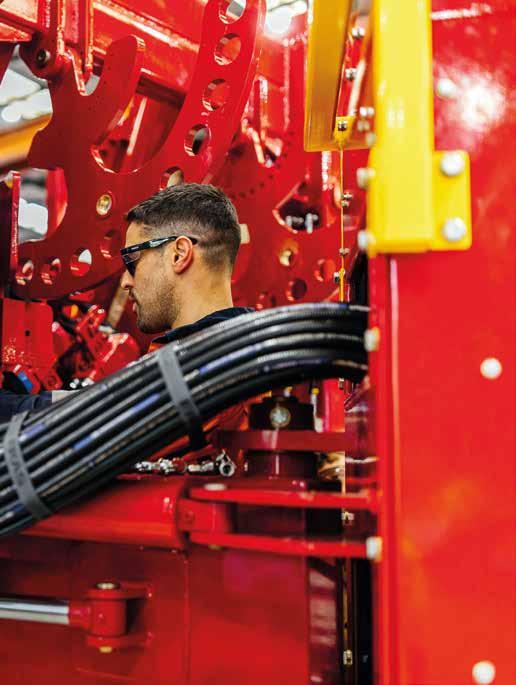
posing piece of kit, ready for the wide range of environments the company operates in globally.
“Schramm filled a hole for us with the reverse circulation market,” Grant says. “We’ve had a lot of customers say they’re pleased we’ve taken it on: it’s a great product, it integrates easily into our organization because it’s a drilling company, and it’s right in our wheelhouse. Epiroc can support existing and new rigs through our extensive aftermarket support network.”
BUT THIS NEW focus on exploration simply fits nicely into a wider Epiroc pivot toward a tech-driven future.
“AI is the next frontier,” Grant says. “That’s really why we want to move into exploration more, because we see a lot of opportunity for technology. It’s exactly where we need to be.”
“We talk at Epiroc about a pit-to-port strategy,” Rossiter adds. “But this is really about extending that to an exploration-to-port strategy. That’s where the future lies.”
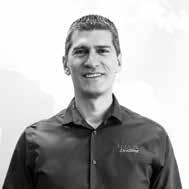
Marc Landry Chief Technology Officer, Major Drilling
How does Epiroc’s portfolio benefit your business?
Tell us about Major Drilling.
“Major Drilling is celebrating 45 years in business and is the largest specialized drilling company globally, with a fleet of more than 700 drills and over 5 000 employees.”
What’s your history with Epiroc and, in particular, its exploration portfolio?
“We’ve used many Schramm reverse circulation drills, mainly the T685 series, for decades, primarily because of the collaboration that we have together in technology and developing systems, seen today as our new TrailBlazer Rock5 drill data analytics system. Specialized drilling requires resources, expertise, and new technology that we can deliver with the underground Diamec Smart6 and Smart8 drills.”
Why do Schramm drills work so well for specialized drilling?
“Schramm drills perform when it counts, for sure. We chose Schramm because of product agility and their willingness to adapt to our needs. Our business model is focused on growth, so it’s a relationship we expect to improve with Epiroc.”
What are your thoughts on Epiroc’s acquisition of Schramm?
“If Schramm hadn’t continued with an appropriate owner, we might have revisited our standardization strategy. It made sense from our perspective to see Schramm become part of their portfolio, because we need that support and quality Epiroc guarantees.”
www.majordrilling.com
A Schramm technician works on assembling a new T685 crawler rig. The company’s reputation in reverse circulation drilling is second to none.
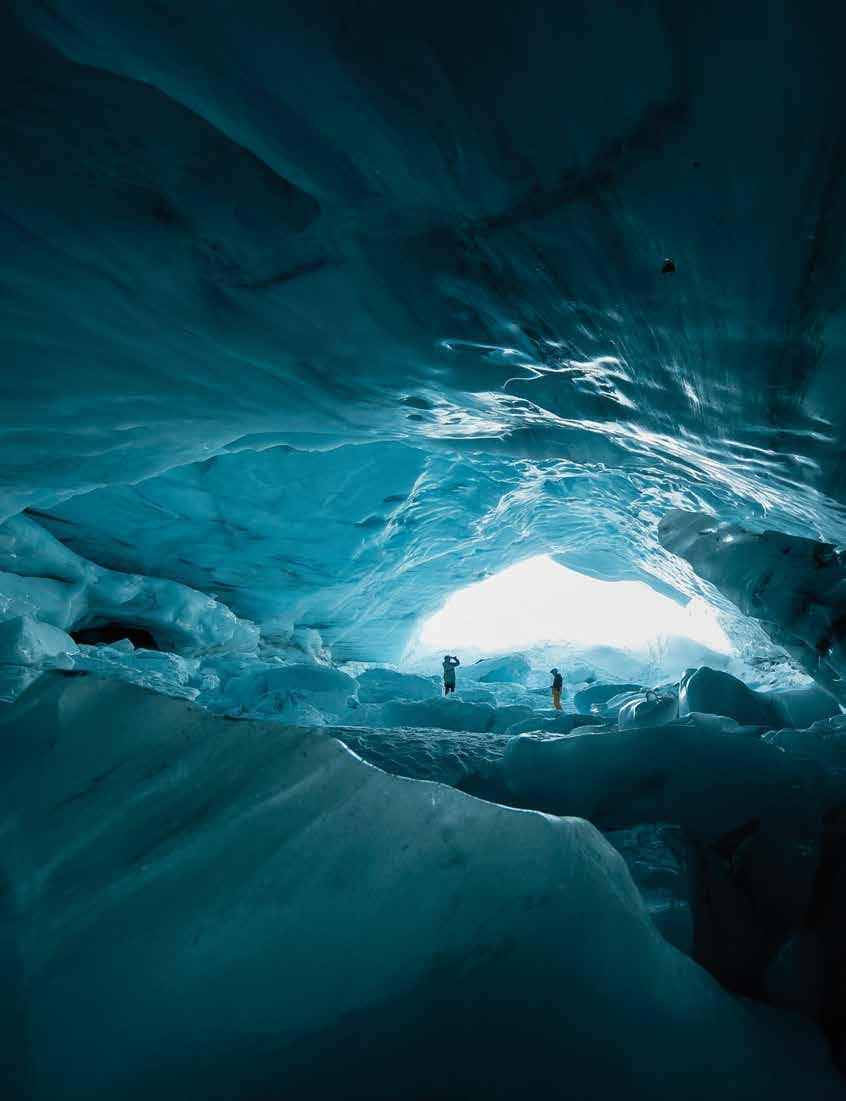
THE EXPLORERS CLUB
There are always things to be learned from other organizations and other industries. Here’s a look at how The Explorers Club promotes scientific exploration and field study.
THE EXPLORERS CLUB
Pushing the limits of the unknown
IF HUMANITY HAS a frontier, The Explorers Club has likely been there.
In 1904, a few daredevils got together in New York to found a club for the like-minded. Since then, it has served as a home for those with an urge to push the limits – climbing mountains, plumbing ocean depths, or exploring space. Its members have been at the forefront, pushing the boundaries of human endurance and scientific discovery.
The club’s roster reads like a roll call of history’s greatest adventurers. Sir Edmund Hillary and Tenzing Norgay, the first to summit Mount Everest, were members. So was Neil Armstrong. The wreck of the Titanic? Discovered by Explorers Club member Robert Ballard. Even the deepest part of the ocean – the Mariana Trench – has been visited by club affiliates, including Don Walsh and James Cameron.
Exploration is not only about grand achievements, though – it's also about scientific progress.
The Explorers Club has long supported research that advances our understanding of the planet and beyond. Its members have been involved in everything from archaeological excavations uncovering lost civilizations to climate studies tracking the impact of environmental change in extreme conditions. By funding grants, providing resources, and fostering collaboration between experts, the club ensures that exploration remains not only about discovery but also about expanding human knowledge.
ON A LIGHTER NOTE , the club also has a reputation for embracing the extraordinary. Nowhere is this more evident than at its legendary fundraising dinners, where guests have sampled exotic delicacies like fried tarantulas, scorpions on toast, earthworm stir-fry and goat eyeballs. Definitely food that calls for the adventurous mindset required for exploration.
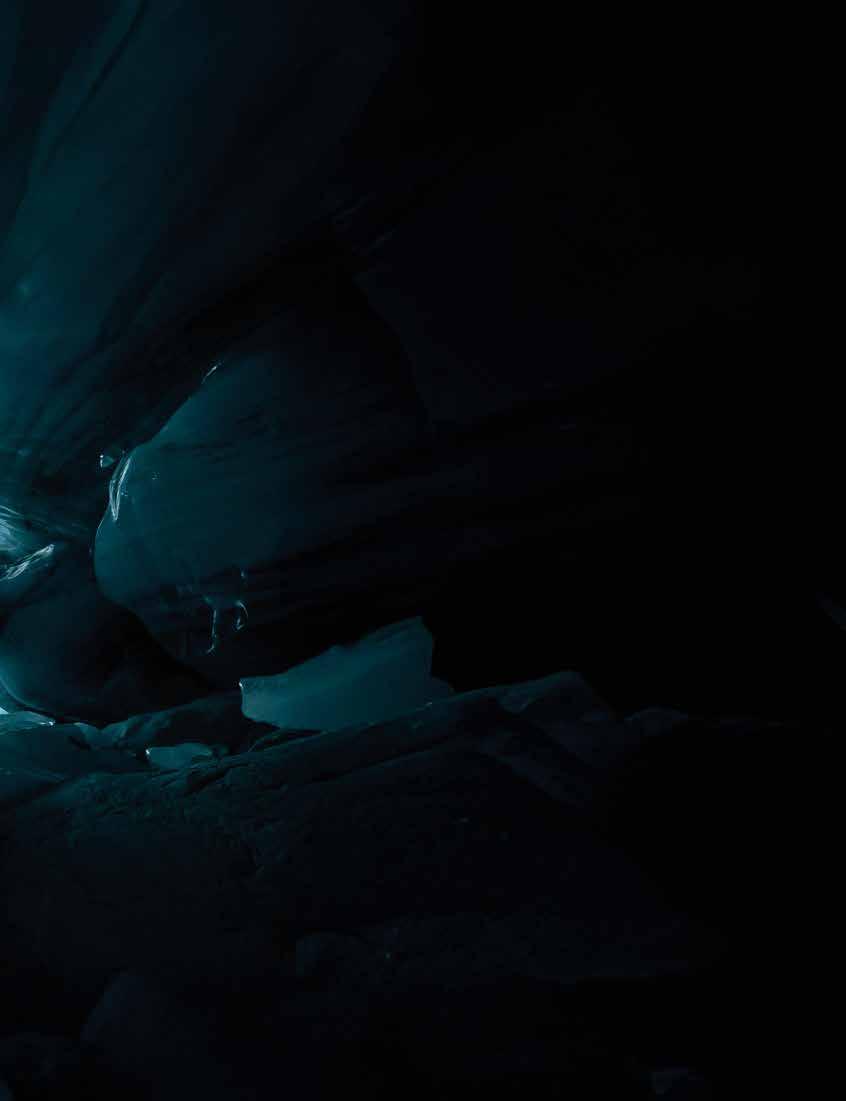
In Focus: The Explorers Club today
AS EXPLORATION EVOLVES, so does the club, remaining a driving force behind modern scientific discovery and global expeditions. With an increasing focus on environmental sustainability, the club actively supports research on climate change, biodiversity, and conservation. Collaborations with space agencies and
private enterprises push the boundaries of human presence beyond Earth, engaging in projects that explore Mars, deep-sea ecosystems, and the melting polar regions. The club’s headquarters in New York serves as a hub where scientists, adventurers, and innovators converge to share ideas and launch ambitious projects.
NEW WAYS TO EXPLORE
What are the main challenges for future raw material exploration?
How should these challenges be met?
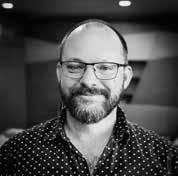
Tom Evans
Senior Research Fellow, Sustainable Minerals Institute University of Queensland, New Zealand
01
“For high-volume commodities (e.g. copper), the challenges are depth and grade. Finding a deposit at depth is the first challenge, and then economically mining and processing the deposit is the second. For lowvolume commodities (e.g. rare-earth elements), the challenges are both market-related and technical: access to downstream markets, price volatility, and costly processing methods.”
02
“The issues with highvolume commodities are surmountable by technology: new geophysical methods, efficient underground mass-mining methods, and energy-efficient processing that allow the economic treatment of low-grade ore. The issues with low-volume commodities can be mitigated through research into new processing methods and market intervention by governments.”
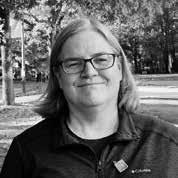
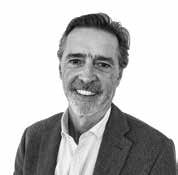
P.Geo, UBC, Bradshaw Research Institute of Minerals and Mining, Canada
01
“Raw material exploration operates within complex adaptive systems (CAS), where technical, environmental, and human factors can interact unpredictably. Deposits are increasingly obscured by cover, while rapid technological advancements outpace organizational adaptability. In addition, human biases and communication breakdowns can amplify risks, as explorers navigate volatile markets, regulatory shifts, indigenous rights, and workforce recruitment challenges.”
02
“Meeting these challenges requires a dual focus on technology and human systems that is rooted in the fundamentals of complex adaptive systems and operational excellence. Encouraging leaders and teams to be curious about active work experiences can surface hidden risks and opportunities.”
01
Australia
“Exploring isn’t getting any easier. Challenges include the ability to discover resources – genuine concern about how long some reserves can last, deeper ore bodies that are more expensive to extract, growing environmental concerns, geopolitical issues, and increasing public pushback against mining. At the same time, there is a significant push for cleaner, more sustainable methods to extract and process materials.”
02
“For the industry to thrive, it must embrace sustainability, innovation, and responsible mining. Success depends on new technology, better community engagement, and doing it all more efficiently. Mining is essential – the focus should be on doing it better.”
Brian Rudd
Executive Director Capital Drilling,
Janice Fingler
Curiosity is a human trait as old as time
Here is a list of lesser-known, though important, explorers often overshadowed by their more famous counterparts.
Louise Arner Boyd 1887–1972
Boyd inherited a fortune that enabled her to pursue her passion for polar exploration. She organized and led multiple scientific expeditions to Greenland and the Arctic, searched for missing explorer Roald Amundsen in 1928, and was the first woman to fly over the North Pole.
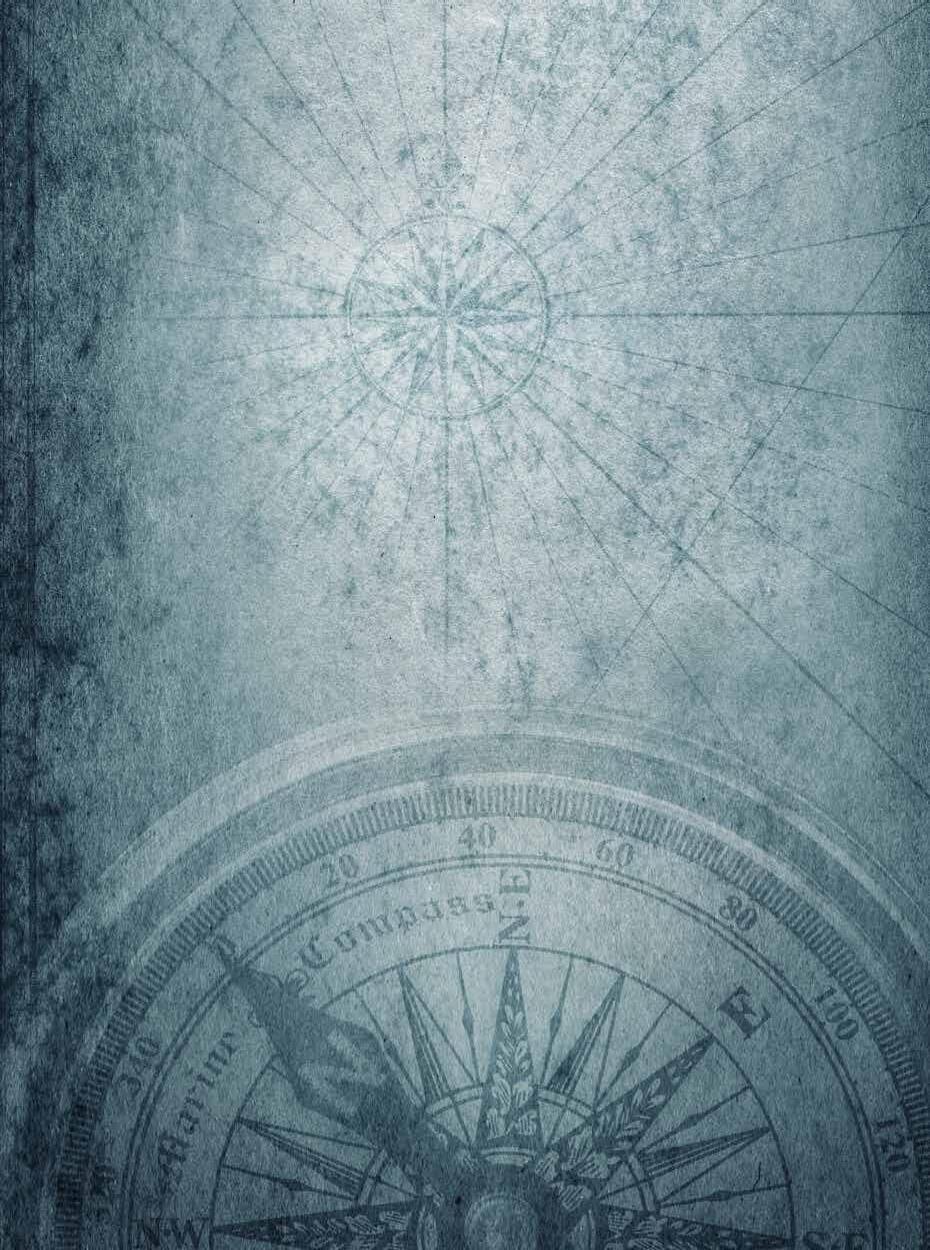
Isabelle Eberhardt 1877–1904
Swiss explorer who moved to Algeria in 1897, converted to Islam, adopted the male persona Si Mahmoud Essadi and immersed herself in Algerian society, writing extensively about her experiences. She survived an assassination attempt, only to die at the age of 27 in a flash flood.
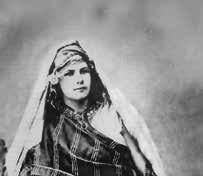
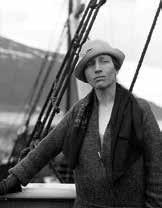
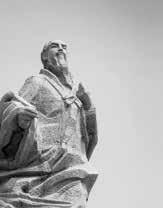
Xu Fu 255–195 BCE
As court sorcerer for Emperor Qin Shi Huang, he led two voyages to find the mythical Mount Penglai and the elixir of immortality. Although he failed in his mission, he is believed to have introduced advanced agricultural techniques to Japan, where he is still revered. Pytheas of Massalia 4th century BCE
Mary Kingsley 1862–1900
After her parents’ deaths, Kingsley set out on several expeditions to explore regions now part of Gabon, Congo, and Cameroon, documenting her experiences and observations along the way. Her work promoted a deeper understanding and respect for African cultures.

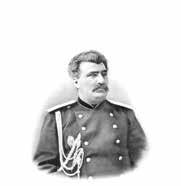
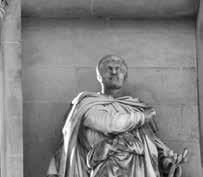
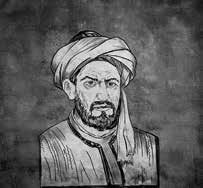
Pytheas is credited with being the first Greek to explore and describe the Atlantic coast of Europe and the first to circumnavigate the British Isles. He was also the first known explorer to reach the Arctic Circle and describe both polar ice and the midnight sun.
Ahmad ibn Fadlan 10th century
In 921, Baghdad traveler and writer ibn Fadlan was sent on a diplomatic mission to the Volga Bulgars. His detailed descriptions of the Rus –the Volga Vikings – and other peoples provide valuable ethnographic insights into the lifestyles and beliefs of these groups.
Nikolai Przhevalsky 1839–1888
An influential Russian geographer and naturalist who mapped vast parts of Central and East Asia. He led five expeditions that traversed Mongolia, Tibet, the Gobi Desert, and parts of China, advancing knowledge of the geography, flora, and fauna of these regions.
Before blasting, you have to know the drill. In next issue’s Feature, we take a closer look at trends and success factors that make drilling operations run the way they should.
Christian Tarras Ericsson Fanghong, Rvalette, Shutterstock,
MY WORK: GLOBAL PRODUCT MANAGER
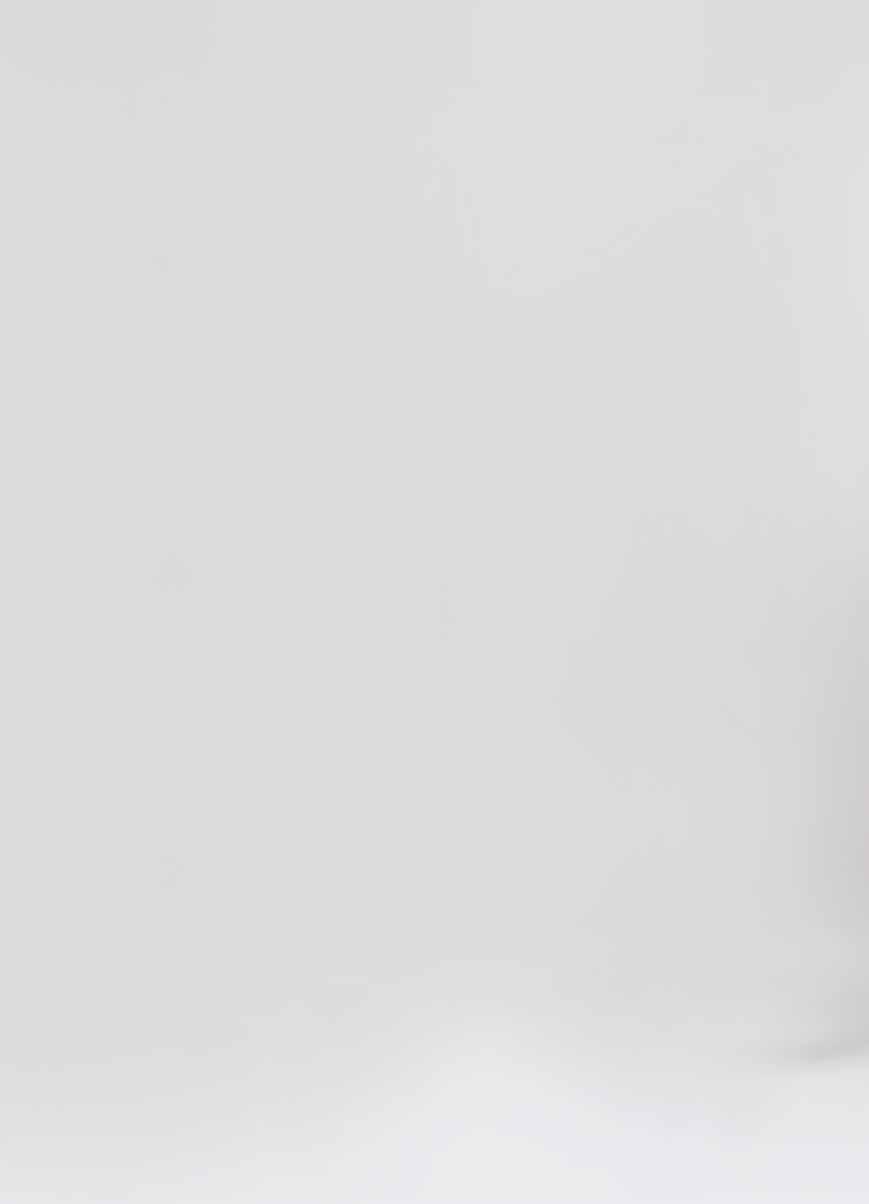
Epiroc’s greatest asset is our employees. We take pride in offering them an outlet for their creativity in order to provide the best possible value to our customers.
Maritha Arcos Andreas Hylthén
“There
are always opportunities to grab”
Mary Zhu was the first employee at the Project Office (R&D center) at Epiroc Nanjing, China. Now, she is the product owner of the Scooptram Small Loaders – and she's pushing the global market to adapt to China’s speed in electrification.
“My mission is to provide the best customer focus for the Small Loaders segment. I’m responsible for developing product strategies and roadmaps based on market analysis and customer needs. This involves initiating new projects, providing sales and after-sales support, handling orders (including special requests), and monitoring machine performance.
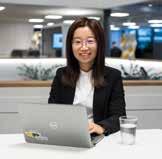
Age: 44
I WAS THE FIRST global product manager appointed outside of Sweden, which is a great honor. I enjoy the challenges and fulfillment my work brings. We have many products and many good ideas we want to achieve. My work presents opportunities to propose direction and guide the team in order to gain achievements. That’s a cool feeling.
Job: Global Product Manager – Small Loaders, Epiroc Underground division
Joined the company: 2012
Best part of the job:
“The collaboration and the feeling that I am making a real impact for our customers.”
Electrification is a priority for me and for Epiroc, and this is mirrored in the market demand of my portfolio. The speed of electrification in China pushes me to in-
novate and accelerate this transition. A project close to my heart was the release of the first battery-electric loader, Scooptram ST10 G, here at the production facility in Nanjing. We plan to have an electric version of every product in the future.
ONE OF MY PROUDEST achievements was initiating the ‘high lift’ option for our small loaders, which allowed us to capture market share in Peru. I was involved in every step of the project, from gathering customer feedback to reviewing designs. I recently traveled to Peru to see this function in action and gather insights for further improvements.
What I love about my job is the collaboration and the feeling that I am making a real impact. I work closely with colleagues across functions and countries, and I love to meet customer demands and bring new products to life.
I believe that if you don’t set limitations for yourself, there are always opportunities to grab.”
MARY ZHU
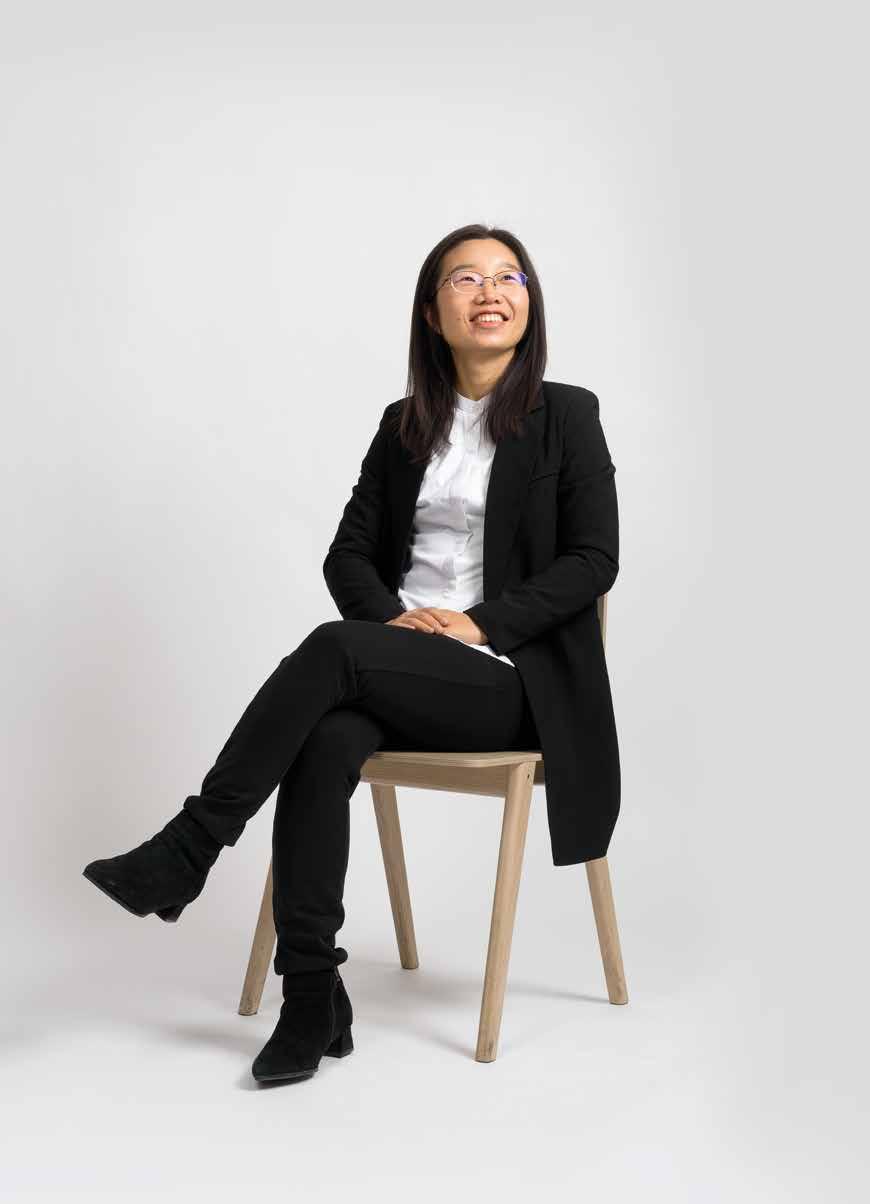
Mary Zhu traded software development for a career leading the global development of mining equipment, and she’s loving every minute of it.
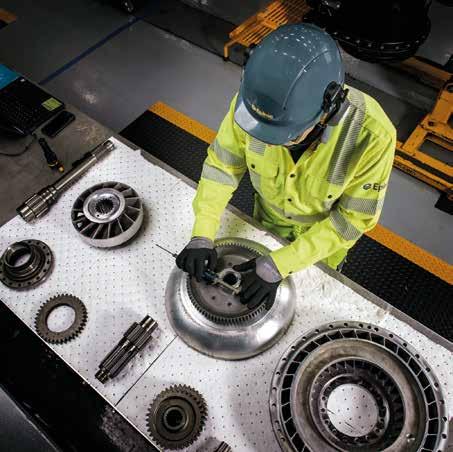
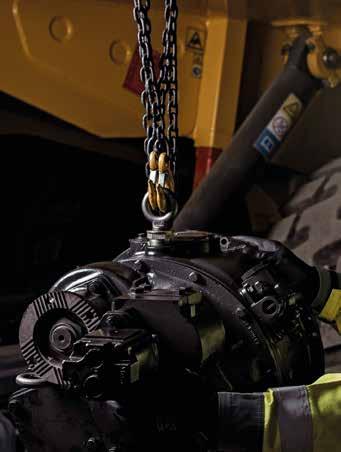
Closing the loop
Epiroc’s circular solutions demonstrate how innovative thinking and close customer collaboration can create value at every stage of a machine’s lifecycle.
IN A WORLD increasingly focused on sustainability, the mining and construction industries face the challenge of balancing operational efficiency with environmental responsibility. For Epiroc, part of the answer lies in a portfolio of circular solution services.
“Circularity is not new to us – it’s at the core of what we do in aftermarket services,” says Bodil Wiklund, Global Product Line Manager Service Solutions at Epiroc. “Our mission has always been to help customers get the most out of their machines, from the first day of operation to the very last.”
EPIROC’S CIRCULAR SOLUTIONS approach spans the entire machine lifecycle, from the design phase to service, maintenance, and component reuse. By maximizing the lifespan of existing machines and components, fewer new materials are needed, resulting in both cost savings and a reduced environ-
mental footprint. With the Repair and return service, for example, worn components are refurbished and returned to the customer. Service exchange, in turn, offers pre-repaired components for faster turnaround times.
“This is a win-win approach,” Bodil Wiklund explains. “By reusing up to 80 percent of the materials in some components, we can deliver cost-efficient solutions that benefit both the customer’s bottom line and the planet.”
Circular Component Offering
Repair and return
Local repair of customer owned components at one of Epiroc’s 75 workshops around the world. Service and rebuilds with the highest quality, returning the customer’s component to its original performance. Repairing components reduces cost of ownership as well as the environmental footprint.
Component exchange
Component exchange ensures minimal downtime by providing remanufactured components rebuilt to likenew condition. Epiroc supplies Reman and service exchange components, and the customer is required to return the core in exchange for a credit, resulting in a lower cost than new components.
Service agreements dedicated to prolonging the life of rock drills, ensuring optimal performance and minimizing unexpected downtime, taking all service parameters into consideration. Service intervals are based on impact hours for specific rock drill type, and an extended warranty is included.
Christian Tarras Ericsson James Hodgins
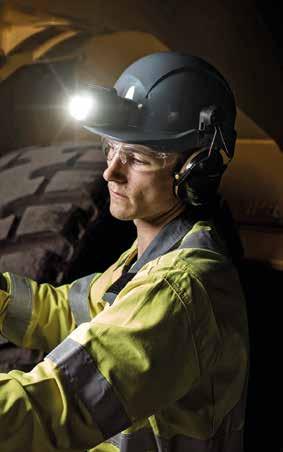

Fossil-free steel for reduced upstreams footprint
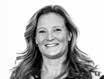
Central to circularity is collaboration. Epiroc works closely with customers to plan maintenance and component replacements at the right time – not too early, and not too late. Digital tools like asset management systems help monitor machine health and predict when interventions are needed, minimizing downtime and ensuring that components can be repaired rather than discarded.
Looking ahead, Epiroc is exploring how to quantify environmental benefits of circular solutions, with the potential to offer sustainability certifications.
“In the end, it’s about taking care of what we’ve already produced,” says Bodil Wiklund. “Circularity is good for business, good for uptime, and good for the planet.”
Epiroc has set long-term 2030 sustainability goals in line with the Paris agreement and the UN 2030 agenda for Sustainable Development. Manufacturing equipment with fossil-free steel is one example.
EPIROC HAS SET a number of sustainability goals for 2030 that further advance the Group’s ambitions on issues such as safety, climate change, and diversity. One of the sustainability initiatives is a partnership with Swedish steelmaker SSAB, to secure fossil-free steel for use in the production of Epiroc’s mining equipment. This fits well with one of the sustainability goals for 2030: halving Epiroc’s CO2e emissions.
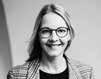
DURING 2024, Epiroc accelerated the green transition by offering SSAB Zero as an option on selected products. Officially presented at MINExpo in September, the bucket of the battery-electric loader Scooptram ST18 SG features virtually emission-free steel.
“By introducing SSAB Zero in our serial
production, we are taking action to reduce our upstream footprint,” says Carin Bergendorff Group Vice President Strategic Sourcing, adding: “Reducing emissions in the entire value chain is important to our customers, too, and the response to this new product has been very positive.”
SSAB Zero is made using recycled steel and fossil-free electricity and biogas, and Bergendorff stresses that the bucket on this batteryelectric loader is just the start.
“We are strengthening our purchasing organization to improve our steel quality worldwide. In the long term, we’ll be using SSAB’s HYBRIT steel, fossil-free steel made from virgin material, as soon as it’s on the market,” she says.
Epiroc’s 2030 sustainability goals help ensure that performance improves and that the organization is aligned to tackle important challenges and opportunities.
Carin Bergendorff Group Vice President Strategic Sourcing, Epiroc
The Epiroc Scooptram ST18 SG underground loader can be equipped with a bucket made with SSAB Zero, reducing CO2e emissions by 15 metric tons per bucket produced compared to traditional steel.
Repairing and returning parts to like-new condition prolongs the components’ life, minimizes the need for new materials, and reduces the cost of ownership.
Bodil Wiklund Global Product Line Manager Service Solutions, Epiroc
Gustaf Höök Johan Bernström
BLAST FROM THE PAST YEAR 1945
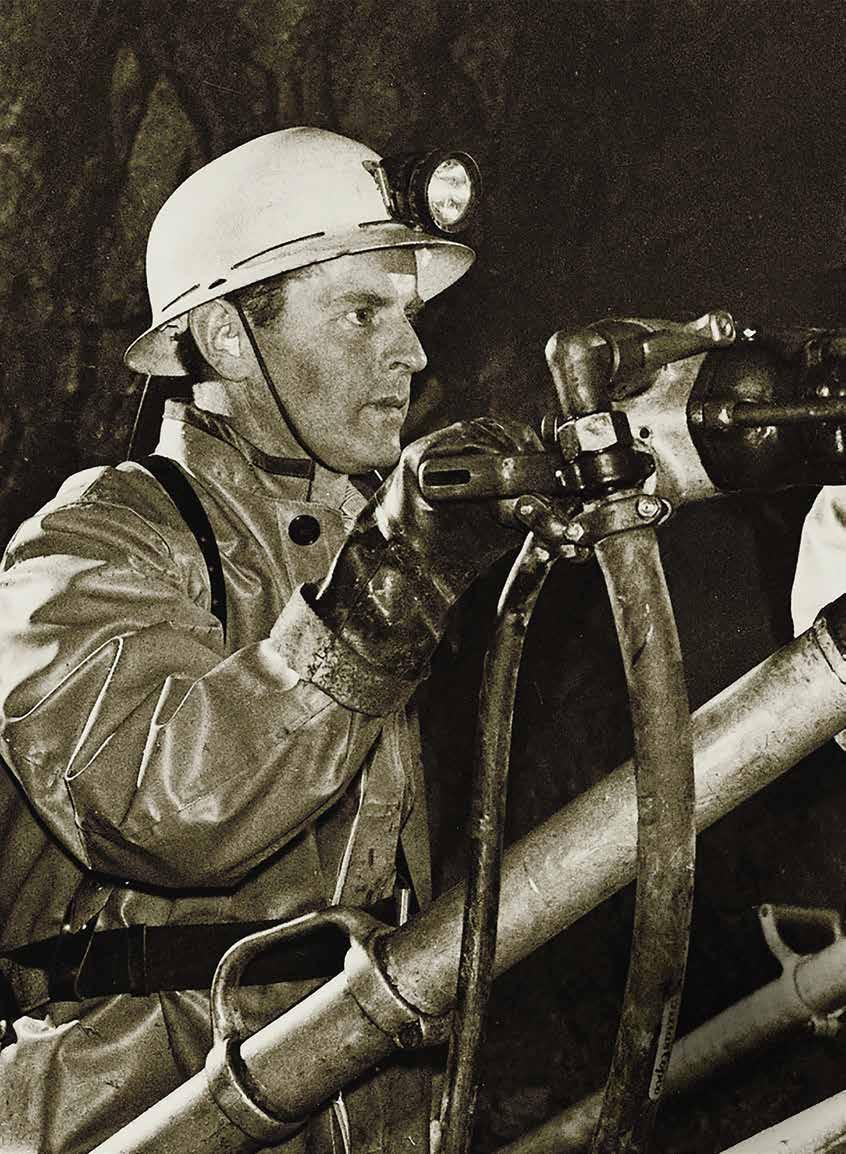
Innovative products and a wide array of customers: Epiroc is a new company with a long and rich history dating all the way back to 1873. In each issue of Mining & Construction, we look into the review mirror for a glimpse of the past.
The Swedish Method was used for the first time in the drilling and blasting of Stockholm’s new tram tunnel in 1945. This new rockdrilling method provided a unique opportunity for Atlas Diesel to establish itself on the global market.
Bodil Hasselgren Epiroc
AS TRAM LINE 17 was being extended and expanded in Stockholm in 1945–1946, a rock tunnel was drilled through Hägerstensåsen. This was the first full-scale use of a new working method, codeveloped by Atlas Diesel, that would come to be called the “Swedish Method” or “knämatade” RH-type drilling machines equipped with carbide bits.
more efficient than previous setups that required more labor. Carbide tips were another prerequisite for the new drilling method. These consisted of hard metal plate sintered from tungsten carbide and cobalt, and they had significantly higher wearresistance compared to regular steel.
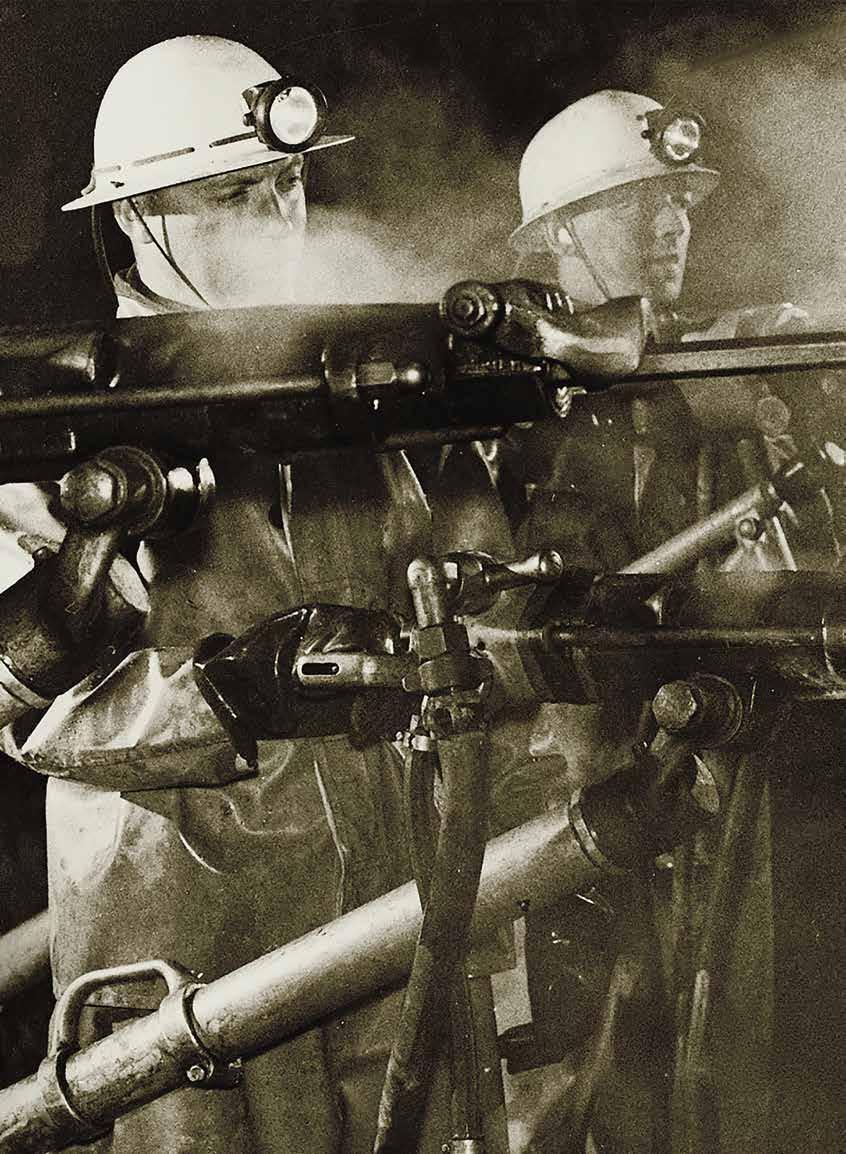
Thanks to the lighter and more portable equipment, drilling could be done by one man with one machine, which was significantly
of agents, then Atlas Copco CEO Walter Wehtje chose to sell the method through wholly owned subsidiaries. The combination of product, method, and sales strategy proved effective, and sales increased rapidly. Over the years that followed, a large network of subsidiaries was established. Between 1948 and 1958, the number of subsidiaries increased from 5 to 29. The Swedish Method formed the foundation of Atlas Copco’s international expansion. Portfolio:
THE SWEDISH METHOD quickly spread across the world. But instead of selling manufacturing licenses or expanding a network
AROUND THE WORLD IN BRIEF
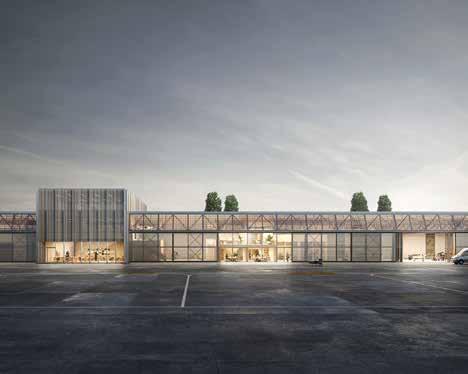
Innovative office space in 100-year-old air hangar
A BUILDINGS-IN-A-BUILDING renovation is underway at an historic airfield in the Swiss capital, Zurich, that will bring a cavernous, 100-year-old hangar back to life for modern purposes, Global Construction Review reports. Established in 1910 on the eastern outskirts of Zurich, Dubendorf Airfield is one of Switzerland’s oldest airfields, serving as the country’s main airport before Zurich Airport opened in 1948 Part of it is now being redeveloped into the
36-hectare Innovation Park Zurich.
One component of that is turning a historic, steel truss hangar built in 1925 for Swissair into a research and innovation hub for the Federal Institute of Technology (ETH) Zurich. The developer is HRS Real Estate and the concept has been created by architects KCAP. When complete at the end of this year, it will house offices for up to 200 ETH Zurich researchers working in robotics, mobility, aerospace, and advanced manufacturing.
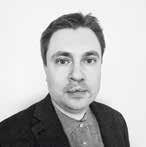
Akseli Mansikkamäki
Docent in Molecular Magnetism, University of Oulu, Finland
Viola MacMillan’s
rise and scandal in Canadian mining
ONE OF THE MOST fascinating stories in Canadian mining history is that of Viola MacMillan, who started out as a prospector in the 1930s and went on to achieve great success and fortune, and influence the development of mining. In the new nonfiction work, Windfall: Viola MacMillan and Her Notorious Mining Scandal, author Tim Falconer explores the trajectory of MacMillan’s life in mining, leading to the scandal and fraud of Windfall Oil and Mines.
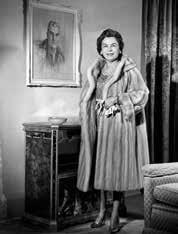
Your research group is developing new materials. Why?
“We want to find out if we can make elements do things they don’t normally do. In recent years, there has been a lot of discussion about critical raw materials, especially neodymium and other rare elements that we use to produce magnets. They have some very specific properties that are very useful for magnets, and, in principle, those properties are also found in other metals, such as lead, bismuth or tellurium. So I started wondering if there is some way to bring out those properties to produce magnetic materials. If so, this could have a huge industrial impact.”
What areas of use do you envisage?
“One application could be for the magnets used in electric cars or wind turbines. Another could be for molecular-sized devices used in quantum information processing. So it’s a rather wide field.”
When could we be seeing actual results?
“There is a huge amount of processing involved in an industrial application. The road from basic science to practical application is very long. It usually takes a decade, often more.”
The cavernous 150x20 meter building will be the new home to a plethora of researchers.
THE CANADIAN MUSEUM OF NATURE.
Pinpointed
1
Canada selects deep geological repository for used nuclear fuel Ignace, Ontario, Canada
On November 28, 2024, Canada’s Nuclear Waste Management Organization (NWMO) allotted a piece of rocky wilderness near the town of Ignace, Ontario, to bury 100 000’s of metric tons of toxic nuclear waste. Canada’s plan, which is similar to the plans of most other nations with used nuclear fuel, calls for this fuel, known as UNF, to be entombed at least 500 meters underground in a body of suitably stable bedrock for over 1 million years.
2
Merdeka Battery gets $1.4 billion loan for new nickel plant Fatufia, Indonesia
3
Indonesian nickel producer, PT Merdeka Battery Materials, has obtained a $1.4 billion loan to fund the construction of a plant located on Sulawesi island. The construction of the plant comes at a time when the nickel industry is grappling with weak prices and a tight supply of ores in Indonesia. The country now accounts for more than half of world’s nickel output and has been aggressively seeking investment for its domestic processing industry.
Want to keep track of what’s happening in the mining and construction industry? Visit miningandconstruction.com for links to industry news and other interesting reading.
4 Mammoet replaces bridges at Amsterdam Centraal station Amsterdam, The Netherlands
Heavy-lift specialist, Mammoet, has begun an amphibious operation to replace five crucial bridge decks at Amsterdam’s main Centraal train station that have reached the end of their design life, globalconstructionreview.com reports. Working with Dutch engineer-
ing company, Dura Vermeer, for client ProRail, Mammoet will replace four steel bridges and a concrete one on its eastern approach (Oostertoegang). It will take a year to replace each bridge – with large, prefabricated bridge sections – while the station remains open.
Torex begins copper production at Media Luna El Limón, Mexico
Toronto-based mining firm, Torex Gold Resources, has achieved a key milestone at its Media Luna project in Mexico, producing its first batch of precious metal-rich copper concentrate, miningweekly.com reports. “This milestone heralds the substantial completion of the project and the beginning of the next chapter in the evolution and growth of Torex as it becomes a gold and copper producer,” says CEO and President Jody Kuzenko.
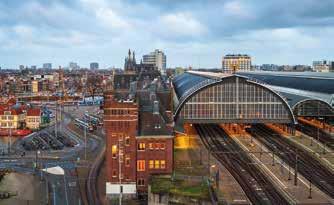
Vacuum heat
Vacuum hardening plays a vital role in enhancing the durability and performance of high-stress steel components.
Andreas Jansson, Heat Treatment Specialist at Epiroc, tells us more about this advanced process.
What is vacuum hardening?
“It’s a type of heat treatment where we harden steel components in a vacuum environment, free from oxygen and other reactive gases. The process involves heating the components to very high temperatures, up to 1200°C, and then cooling them in a controlled manner. The vacuum ensures that there’s no oxidation to minimize surface defects. It’s a highly controlled process that allows us to achieve consistent results across every batch.”
In what way does it improve upon traditional hardening processes?
“The big difference is in the level of control. We can precisely adjust the temperature and cooling rates. Different steels require different heating and cooling profiles to achieve the right combination of hardness and toughness. The vacuum furnace gives us the flexibility to fine-tune the process for

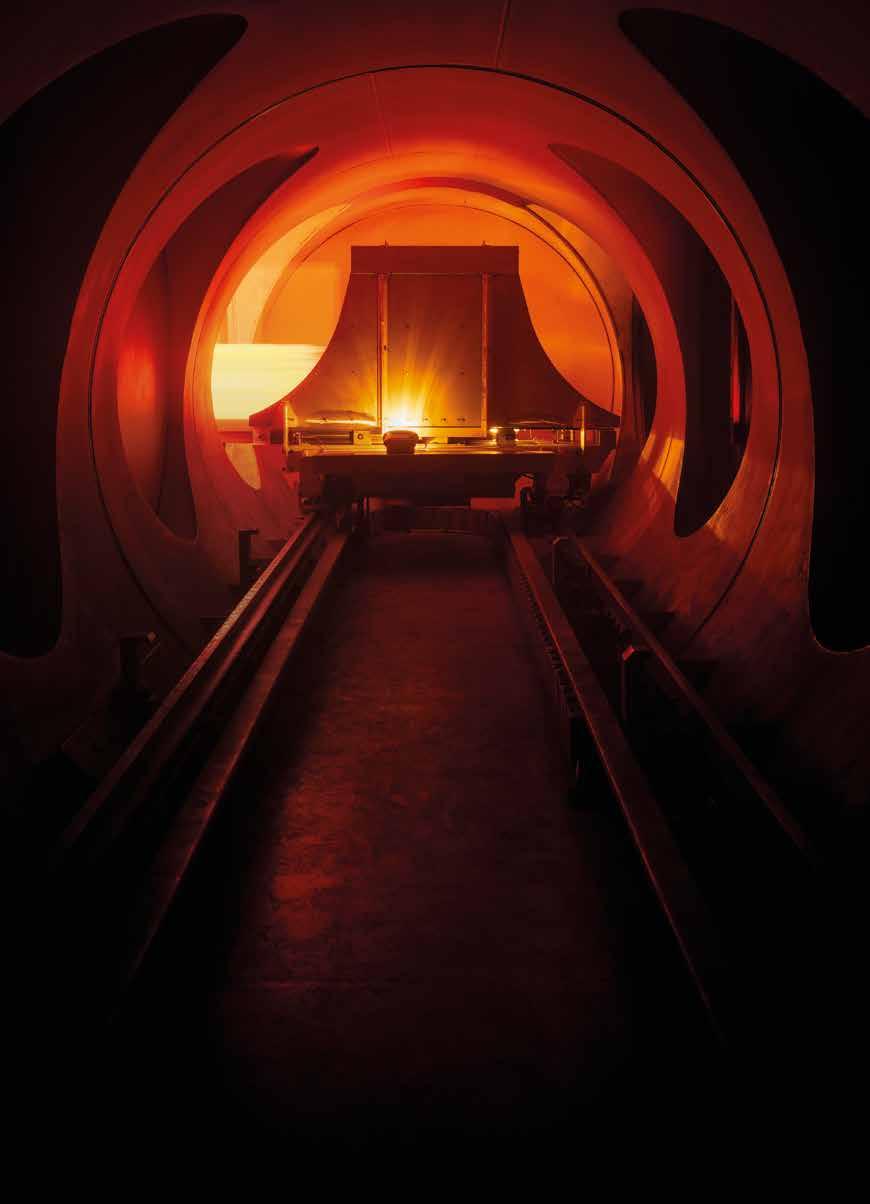
each material. Plus, the cooling is often done with gas quenching, which is much gentler than oil or water quenching, reducing the risk of unexpected distortion in the parts and eliminating the need for a washing.”
What advantages does vacuum hardening have for Epiroc customers?
“Vacuum hardening allows us to produce components with very consistent properties – the same hardness, toughness, and wear resistance every time. That translates into parts that last longer and perform more predictably in the field. There’s also an environmental aspect. For example, I’ve seen studies showing that vacuum carburizing with gas quenching can significantly cut CO2 emissions compared to traditional atmospheric carburizing methods.”
Component
benefits
Housing components that operate in extremely tough environments, exposed to, for example, corrosion, abrasive wear, and high stresses.
Gears benefit from less distortion caused by the heat treatment, and must have the ability to endure numerous load cycles without failure.
Flushing heads must withstand a combination of high stresses and a highly corrosive environment; this requires very controlled heat treatment operations.
Jansson
In a vacuum furnace, steel components are heat treated at extreme temperatures with precision, consistency, and no oxidation.
Christian Tarras Ericsson Andreas Hylthén & Magnus Wahrman