Making Your Own Grounded Pliers
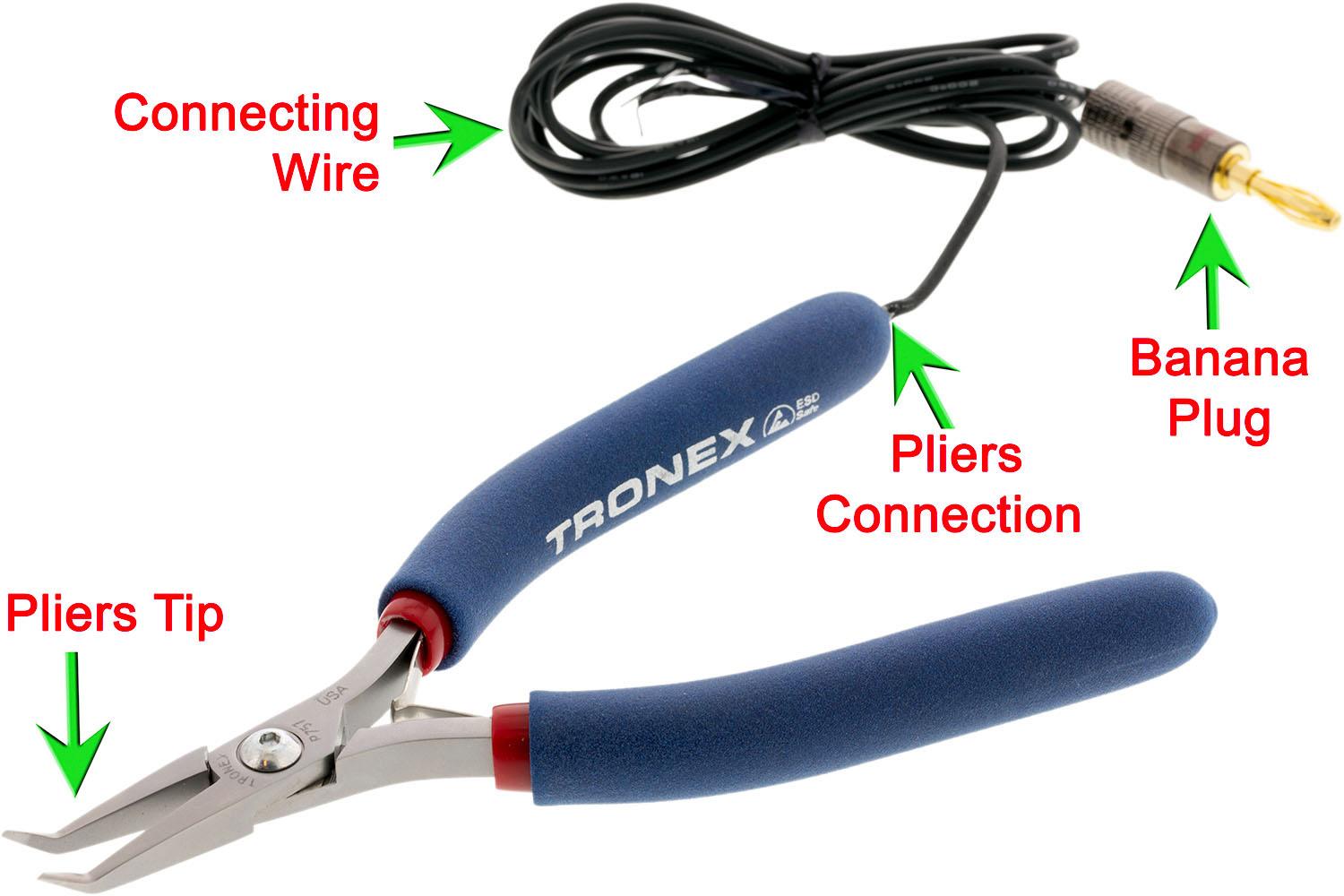

Let’s face it, making your own (DIY) grounded pliers for Permanent Jewelry Micro Welding is NOT rocket science. We all have different strengths and weaknesses, so this task may or may not be for you. Custom made or customizing tools is not a bad thing at all, I recommend it, you will end up having a tool that meets your specific needs/style of work.
There are multiple things to consider when making these pliers. Let’s start at the welder and work our way out to the pliers for this discussion.
Banana Plug
ALL Micro Welders that I have seen so far, be they Un-Branded, PUK or Orion, they ALL use a standard 4mm Banana plug for their grounding connection. I say standard, because this size of banana plug is crazy common, you can find them all over the internet. I have been using them for electronics test leads myself for over 45 years. Yes I’m an old fart.
They all work the same way, you push the pin “straight” into the hole. When removing, you pull them “straight” out. Some may be tighter than others but they all fit.
There are different styles of banana plugs but the majority attach to the wire (after it is stripped) with one or two screws. I prefer the style that uses 2 screws, 1 of these screws is tightened down on the stripped wire to make the connection and the second screw is tightened at a point where it goes against the insulation. The second screw is more about strength of the connection to help ensure that the wire is not pulled out of the plug.
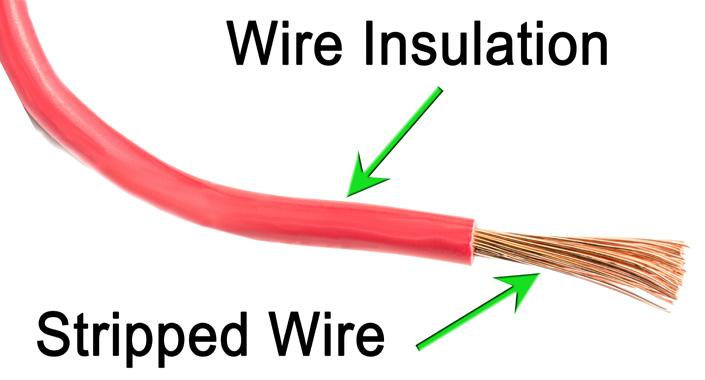
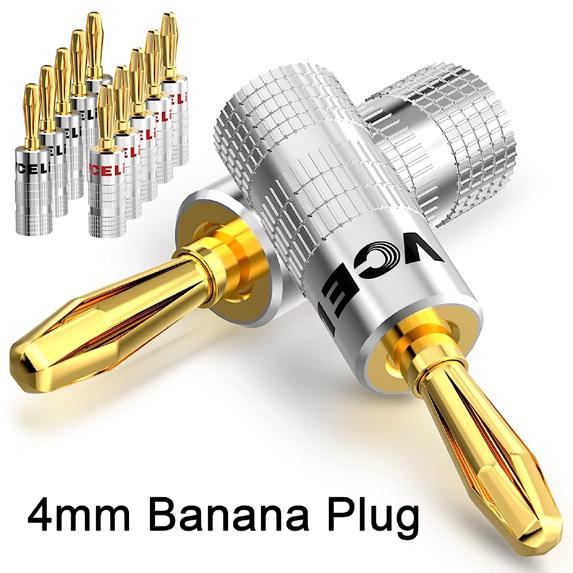
There are also stackable plugs that allow you to have multiple things plugged in at the same time. Molded plugs seem to be the strongest, but they are limited to whatever wire gauge and length that is already attached when you buy them.
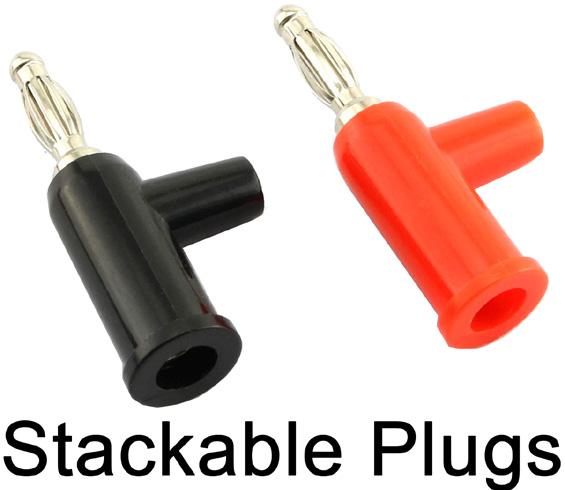
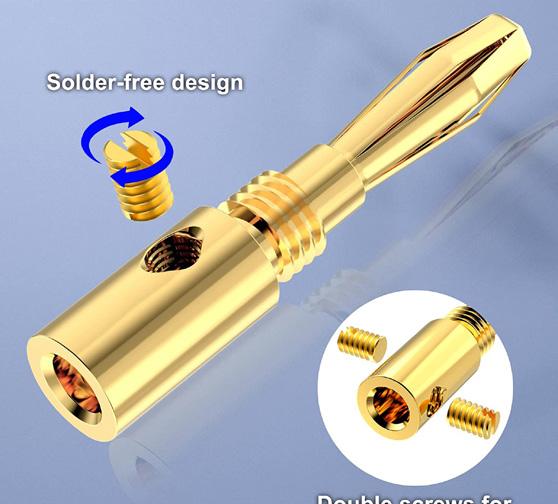
Connecting Wire
Length and wire gauge (thickness) are important factors. You have a lot of power that you are trying to get to flow to make a weld. Think of it like a garden hose compared to a fire hose and trying to fill up a pool. If you have a pump that will put out 100 gallons per minute, your garden hose is not going to be able to handle that flow as well as your fire hose. The longer your hose is the more loss in pressure you will have at the output due to friction (resistance). So, you want your wire to be at a minimum gauge and not too long.
The minimum gauge for a 5’ long or less grounding wire would be 18 gauge. 16 gauge would be better and 14 gauge better yet. The smaller the number, the thicker the wire and the less flexible it becomes. The thickness of the insulation is not included when measuring a wires gauge. 16-18 gauge seems to be a happy medium of not too stiff and not too thin. The thicker the wire, the less likely you are to break it. A 3’ length is usually quite sufficient for working on a table near the welder itself. Most people prefer 5’-6’ lengths to reach ankles.
You want to use a stranded copper wire as solid copper wire is too rigid and would not be flexible enough.
The wire insulation is also something to consider. An Ultra Flexible Soft Silicone Rubber insulated wire is the most flexible, and our wire of choice. PVC insulated wire will work but it is not nearly as flexible as the silicone rubber insulated wire.
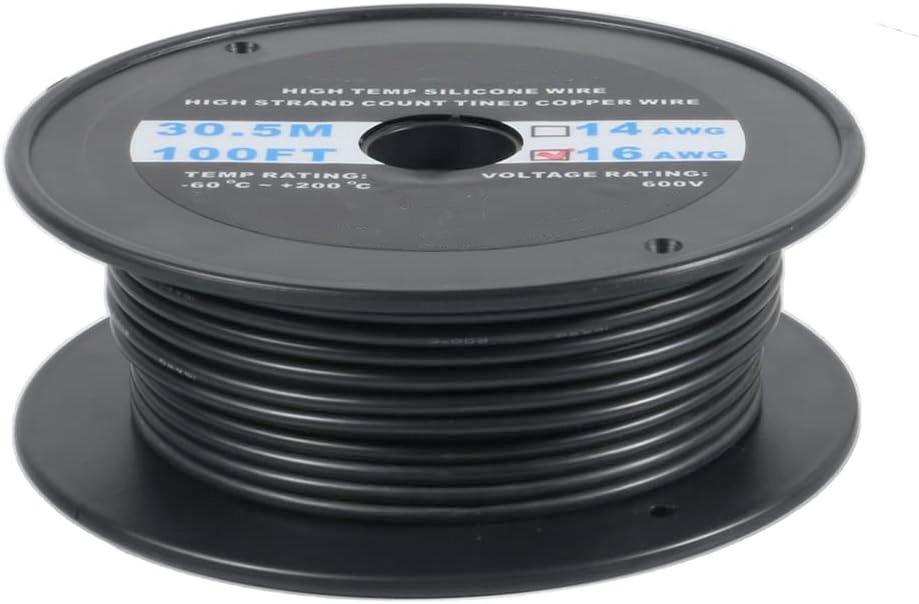
Pliers Connection
The method in which you connect the connecting wire to the pliers is going to be very dependent on the pliers themselves. The stripped wire must be touching and connected to the metal of the pliers by some form or fashion. You can do so with methods like soldering, eyelet with screw, riveting or even a banana plug welded to the handle. One very important thing to consider is that you need to secure the insulated part of the wire to the pliers too, this gives you a better chance of NOT breaking the wire while in use.
There are 3 common methods of securing the insulated portion of the wire to the pliers.
• Epoxy (needs to be an epoxy formulated for attaching these specific materials)
• Zip Tie
• Electrical Tape
You will want to make sure your connection wire to pliers’ connection is covered/insulated. Most of the time this is accomplished with heat shrink. The cruder your connection is, the more heat shrink you will need. You may very well need more than 1 layer of heat shrink.
The Xuron brand of pliers have grips that you can pull off with a little force and some holes already in the handles to mount the wire to. The Tronex brand of pliers have grips on them that must be cut off as they are epoxied on. We can get the cleanest installation using the Tronex brand of pliers as we don’t have to use heat shrink with our method.
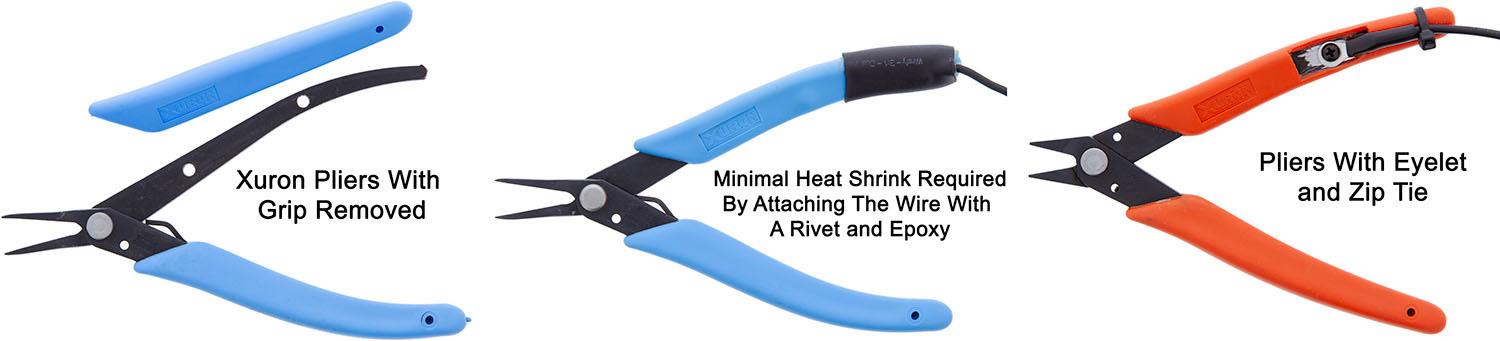
Our Method of connecting the wire to Tronex Pliers
1. Cut Off One Grip (Razor Knife)
2. Remove Spring
3. Grind Off Excess Epoxy from Handle & Spring (Foredom Right Angle Grinder)
4. Use New Grip and Drill Hole in The Bottom of It (3/16” 6” long Drill Bit)
5. Run Wire Through Hole in New Handle
6. Strip The Wire
7. Solder Wire to Handle (Heavy Duty Soldering Iron)
8. Epoxy Insulated Portion of The End of The Wire to The Handle (3M DP6310NS)
9. Epoxy Inside of The Grip and Slip Grip on The Handle with Spring Installed
10. Epoxy Inside of The Hole That You Drilled for The Wire to Go Through (Needle Tip on Epoxy Dispenser)
Selecting The Pliers
This is the part that gets so personal. It comes down to budget, functionality, and comfort. Why not throw the budget portion out of this equation? It doesn’t matter if you paid $10 or $100 for your pliers, most people would pay for them many times over in their first event/pop-up. They are going to last you a long time although I would recommend having a backup pair in case you break them somehow. It is much more important to have the best functionality and second is comfort.
ONLY use smooth jawed pliers. You want to stay AWAY from pliers and hemostats with serrated jaws. The serrations will scratch up and damage your work.
Although the Xuron 475 Short Stub Note is the most common pliers being grounded out there, there are other options. The Xuron 450BN Bent Tweezer Nose is another great option. Bent nose pliers give you the ability to get your hands and pliers out of the way while welding. Basically, you can ground any metal pliers. Find the shape of the tip that meets your specific needs/style of work.
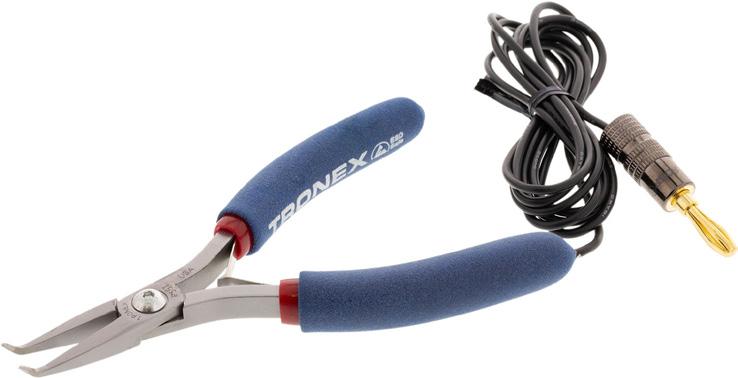
The Comfort of the pliers in your hand can make a big difference, especially the longer you use them. This again is a very personal choice as what is comfortable in one person’s hands may not be comfortable in the next person’s hands. The Tronex brand of pliers are some of the most comfortable pliers out there (to most).
Hemostats are another popular choice. The problem with hemostats is that #1 most have serrated jaws and #2 It is hard cleanly attach a grounding wire.
Weak Points
This is thin wire, it can break especially if one end is caught, and the other end is pulled. The wire can break at either end, it usually happens in the stripped area of the wire. The banana plugs can break if they are not pressed “straight” in. They can also break if a strong side force is applied while they are plugged in, this is an even bigger issue when you are using the stackable plugs with multiple items plugged in.
Banana plugs can be replaced, and wires can be re-attached to pliers. But you know if they are going to break, it is going to happen at the most un opportune time so that I why I recommend having a backup pair with you.
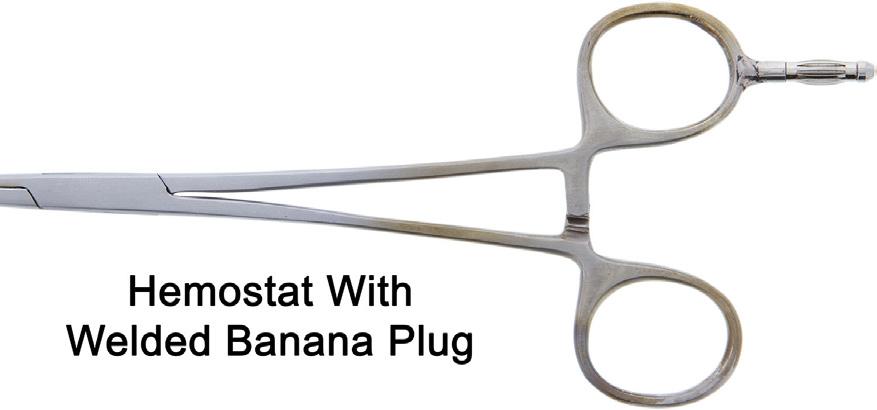
What is your time worth? Is it worth your time to make your own, or would you be better off buying a premade version?
By: Curt Fargo President of: Fargo Enterprises, Inc. dba www.Micro-Tools.com