Baby diapers: Market analysis, technologies, and trends
SUSTAINABILITY IN PACKAGING

A.Celli & PMT: The best choice for upgrading or converting your paper mills
B6-W Red
Your reference product, the most competitive

B6-W Red. Boost your sales while we mind your production
QUICK RETURN ON INVESTMENT
FROM BASIC TO PREMIUM PRODUCT
Thanks to the process solutions proven on our best-selling B8-W Red, this machine delivers baby diapers with cutting edge core technology and the option for permanent channels. It enables an optimal mix and distribution of fluff and SAP while minimizing raw material costs thanks to Zero Waste on both front and rear wings and the capability to run low gsm raw material.
B6-W Red, running at an actual speed of 600 ppm, is designed to last and ensures high reliability with stable performances and no stops. It is the answer to your needs of maximized production at an optimized cost supporting you and your growth ambitions in the Baby Diaper market.
Take advantage of all the benefits of a single source supplier from converting to primary packaging, combining it with our stacker & bagger SB50 Go
P.O.Box:
TURKEY SOUTH AFRICA
Europap Tezol Kagit starts up new tissue line
Europap Tezol Kagit started up a Toscotec-supplied AHEAD 2.2 tissue machine at its integrated production facility in Mersin, Turkey. The new high efciency line started producing high quality tissue immediately after start-up. The project also included two OPTIMA slitter rewinders, with the frst already in operation, and the second scheduled for installation soon. This is a repeat order for Toscotec who also installed a TT SYD Steel Yankee Dryer on their PM1 in 2012.
The AHEAD 2.2 line features a sheet trim width of 2,920 mm, an operating speed of 2,100 m/min, and an annual production capacity of over 40,000 tons. It is equipped with Toscotec’s upgraded design TT NextPress shoe press, a third-generation TT SYD, TT BulkyReel for optimal preservation of bulk and softness, and high efciency TT Hood with the automatic balancing system TT DryingEquilibrium.
The supply included the complete stock preparation system, Toscotec’s patented TT SAF® DD (Short Approach Flow system with Double Dilution) to ensure electrical consumption reduction, as well as electrifcation and controls, and dust and mist removal systems. Toscotec delivered a comprehensive service package with detailed engineering, erection supervision, commissioning, training, and start-up assistance.
Ahmet Senyasa, Factories Director at Europap Tezol Kagit, says, “The cooperation with Toscotec during the entire project was very positive. We are confdent that this state-of-the-art tissue line will allow us to meet the high quality standards of our customer base, especially in terms of the softness and hand feel of our super- prime brands.” Matteo Giorgio Marrano, Sales Manager at Toscotec, says, “The high energy efciency of this tissue machine is ensured by the combination of Toscotec’s latest generation design of TT NextPress and TT SYD with TT Hoods equipped with automatic balancing system. Europap Tezol will reap the benefts of this advanced technology both for energy savings and superior quality. With this successful project, Toscotec takes a further step in strengthening its presence in the EMEA market.”
Europap Tezol operates three tissue mills in Turkey with integrated converting, in Torbali-Izmir and in Mersin-Tarsus. The annual capacity is 93,000 tons and it will be increased to over 133,000 tons with this new line.

Toscotec starts up a tissue line at Jumbo Centre in South Africa
South African tissue producer Jumbo Centre has started up an AHEAD 1.8 tissue line supplied by Toscotec at their Johannesburg facility. This is a repeat order for Toscotec after the successful installation in 2020 of another complete tissue machine at the same mill.
The AHEAD 1.8 machine has a sheet trim width of 2,750 mm, an operating speed of 1,800 m/min and a production capacity of more than 30,000 tpy. It is equipped with a new generation design TT NextPress shoe press, a third-generation TT SYD Steel Yankee Dryer, and high-efciency TT Hood. The scope of supply covers the complete production line from the bale handling and stock preparation systems to the electrifcation and control system of the tissue machine. The associated services include detailed engineering, erection supervision, commissioning, training, and start-up.
Itzik Nikfard and Raf Nikfard, Directors of Jumbo Centre, said, “This investment marks a new important stage of expansion for our business. The choice of technology is key in supporting the continuous growth and success of our SnowSoft brand. Toscotec’s machines deliver premium tissue quality, high production efciency, and energy savings which equip us to succeed in the market.”
Matteo Giorgio Marrano, Toscotec Sales Manager, says: “Toscotec is proud to support Jumbo Centre in their decision to continuously upgrade their tissue making technology over the years to properly support their growth in the regional market. They moved from simple machinery to our energyefcient MODULO-PLUS machine and now to this state-ofthe-art AHEAD tissue line featuring Toscotec’s best-in-class energy efciency technology. An impressive journey in just a few years’ time.”

Tissue converting is now part of Valmet’s o ff ering
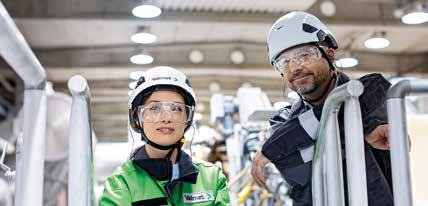
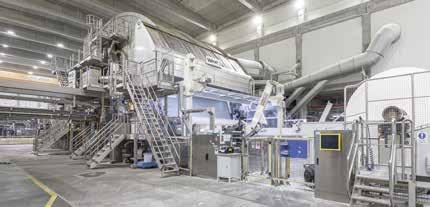
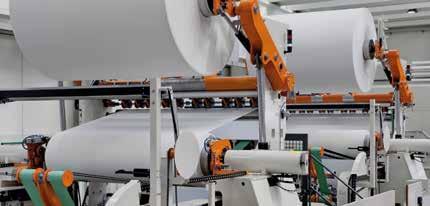
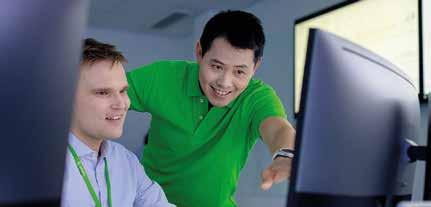
Valmet has acquired Körber’s Business Area Tissue, a global supplier of tissue converting and packaging lines. We are happy to welcome the market leader in tissue converting and close to 1,200 dedicated new colleagues to Valmet.
Together, we offer unique benefits for tissue producers through the combination of our technologies, automation solutions and services. We also have an opportunity to develop our tissue customers’ processes further by combining data from the tissue making and converting processes.
Our experts around the world are committed to moving your performance forward – every day.
Explore our combined tissue making and converting offering www.valmet.com/tissue
QATAR
Zain Paper Industry to start tissue business
Overmade has been commissioned by Zain Paper Industry to realize the new tissue production park in Doha, Qatar. The frst phase of the project includes the installation of two complete tissue plants for the production of high-quality facial tissue.
The project will be delivered on the basis of a turn-key supply: from virgin pulper to approach fow system, from hydraulic headbox to reel, from winding system to wrapping line, including all auxiliaries such as vacuum line, steam system, high efciency hood, mist and dust removal system.
The DCS (Distributed Control System), the QCS (Quality Control System), the Sectional Electrical Drives and the Electrifcation of the entire tissue mill are also part of the scope of supply.
The OVER CR C20 machines will produce each 30,000 tons of tissue per year at the speed of 2,000 m/min and a trim width of 2,750 mm. It will be equipped with a water treatment plant, a fber recovery plant and an advanced double dilution system to feed the headbox. The machines will be equipped with a DYNAFLO-C headbox on the OVER FORMER CR, capable to “OVER-perform” in the fber distribution at high consistency and to reduce the softwood needs in the paper. The delivery of PM1 has been already completed and the delivery of PM2 is in process. OVERMADE’s scope of supply includes all necessary services of engineering and erection supervision services as well as assistance at the start-up of both lines.
Elie Wanna, CEO of Zain Paper Industry, stated: “We are proud to announce the Zain Paper Industry Tissue Park Project in Qatar an important investment that is located on a plot of land exceeding 123,000 m2, which will be developed in multiple phases. In phase 1, we are already implementing the two OVERMADE lines, one tissue converting plant and one diaper plant. On top of that we are enthusiastic to announce that Zain Paper Industry has already activated the phase 2 project that includes the installation of two equal tissue machines and production lines. Further already programmed phases will be launched once phase 2 will reach an advanced stage of implementation. Having multiple equal lines, we dedicate each line for a single product. Production changes will be minimized to achieve the highest level of efciency and productivity, while saving in the spare parts and consumable management. We selected the OVERMADE lines mainly because of well-known quality of the product manufactured by the OVER CR tissue machines, and further because of the lowest proven production consumptions these lines have”.
POLAND
Velvet CARE acquired by Partners Group
Partners Group, a leading global private markets frm, acting on behalf of its clients, has agreed to acquire Velvet CARE, Central Europe’s fastest-growing consumer tissue producer from Abris Capital Partners and plans to build value through initiatives including expansion in Central Europe and beyond. New investor opens up global possibilities for Polish hygiene tissue producer.
Since 1996, Partners Group has invested USD 200 billion in private equity, private real estate, private debt and private infrastructure on behalf of its clients globally. The frm employs more than 1,800 diverse professionals across 20 ofces worldwide and has regional headquarters in Baar-Zug, Switzerland, Denver, USA, and Singapore.
Velvet CARE divestment by Abris Capital Partners takes place after fve years of dynamic growth.
In 2020 Velvet CARE acquired Moracell, Czechia’s largest producer of toilet paper and paper towels, giving the group a strong position on the Czech market. Further investments in production in Poland and Czechia have strengthened Velvet CARE’s position as the industry leader in Central Europe.
“Velvet CARE has a diversifed product portfolio and a strong market position in its core markets,” said Ralph Schuck, Managing Director, Private Equity Goods & Products Industry Vertical, at Partners Group. “The Company diferentiates itself through its superior production capabilities, best-in-class technology and deep relationships with retailers across multiple countries. We see Velvet CARE as a platform for further growth in Europe and look forward to working with the management team on our transformational value creation plan.”
Velvet CARE received B Corp certifcation, the globally recognized accreditation for businesses that demonstrate the highest standards of social and environmental performance, transparency, and accountability, earlier this year. Companies that are part of the B Corp community make commitments to uphold those priorities in their business model and work for proft, people, and planet at the same time. Earlier this year Velvet CARE also earned a Gold Medal from EcoVadis, the world’s largest provider of business sustainability ratings.
Velvet CARE’s products include toilet paper, paper towels, paper tissues and moist toilet paper. Its Velvet brand has enjoyed great popularity in Poland for the past 26 years, and the company also produces for private labels. Velvet CARE has two factories, in Klucze, Poland and Žabčice, Czechia, and sells its products on more than 30 markets, mainly in Europe.
SPAIN
Volpak partners with watttron to revolutionize Flexible Packaging through Digital Sealing Technology
Volpak, a Coesia Company specializing in horizontal formfll-seal solutions, has strategically partnered with watttron, a pioneering company in precision heating technology. This collaboration aims to integrate watttron’s intelligent digital sealing technology into Volpak’s state-of-the-art horizontal pouching machinery, marking a signifcant leap forward in the realm of fexible packaging.
In this joint efort, Volpak and watttron have crafted a revolutionary solution enhancing the precision, efciency, and sustainability of packaging processes. Notably, this advanced digital sealing solution is also designed for easy retroftting onto existing machines, enabling businesses to upgrade their technology seamlessly.
By integrating digital sealing technology, Volpak empowers its customers to achieve superior sealing quality, reduce material waste, and signifcantly contribute to environmental conservation.
Customers can also beneft from the strong technological collaboration within Coesia group, with R.A Jones, a sister company, providing integrated watttron digital sealing technology solutions on their ultra-high speed horizontal pouching machinery, running up to 2000 pouches/minute. Volpak and R.A. Jones have machines running successfully with watttron seal bars at major FMCG producers in Europe and the USA. Both Volpak and R.A Jones are already equipped with production-scale laboratory machinery, up and running with watttron technology, available for customer flm trials and testing.
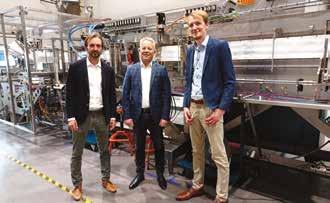
ANDRITZ to supply high-temperature Yankee hood and air system to Kartogroup
ANDRITZ has received an order from Kartogroup Espana S.L. to supply a new high-temperature PrimeDry Hood HT and an air system for a tissue machine rebuild at the mill in Burriana, Spain. Start-up is scheduled for the frst quarter of 2024.
The new gas-heated hood will enable Kartogroup to achieve a higher drying capacity with a hood design impingement temperature of 530°C, a higher heat transfer rate and a signifcant reduction of energy consumption per ton of paper produced.
The special set of advanced solutions for the drying section rebuild include optimized impingement distribution of the hood nozzle boxes, a heat recovery system, a state-of-theart burner management system and Yankee head insulation. Representing ANDRITZ’s latest developments in tissue drying technology, these solutions maximize the heat transfer rate, ensure higher safety, lower emissions and signifcantly reduce steam consumption.
This order refects the trustful relationship between the two companies, which started in 2020 with a turnkey order for ANDRITZ that included a steel Yankee with steam and condensate system, two dust removal systems, and an air-toair heat exchanger.
Pascual Gómez, COO Kartogroup, says, “We trust in ANDRITZ’s expertise to upgrade machines for a more efcient and sustainable tissue production. The innovative high-temperature hood perfectly meets our requirements for energy saving, high thermal efciency, and stable drying results. We look forward to continuing our collaboration with ANDRITZ on new R&D energy efciency projects next year.”
Kartogroup Espana S.L., a member of the Cominter Group, has more than 40 years’ experience in the tissue business. At its mills in Burriana and Hernani, Spain, the company produces high-quality tissue grades for household and industrial applications.

ITALY
A.Celli Paper’s SMARNIP®-T Tissue Shoe Press Open House a resounding success
A.Celli Paper successful “SMARNIP®-T Tissue Shoe Press” Open House event garnered widespread attention, and was attended by over one hundred guests from some of the world’s most prominent tissue and paper manufacturers.
The event held from October 11 to 13, 2023, at A.Celli Paper’s headquarters in Tassignano, Lucca, was met with overwhelming enthusiasm and curiosity from industry leaders. This open house was a testament to A.Celli Paper’s commitment to innovation and excellence in the feld of tissue paper production.
The primary focus of the event was the grand unveiling of the revolutionary “SMARNIP®-T Shoe Press.” This ground-breaking solution is meticulously crafted to bring the advantages of the shoe press concept to tissue paper production. The “SMARNIP®-T” promises to elevate efciency and performance while preserving the integrity of the fnal product and retaining its bulk and softness.
Throughout the Open House, A.Celli Paper provided a comprehensive showcase of its solutions, designed to empower tissue paper manufacturers of all scales to optimize their operations. The exhibited solutions included:
• “SMARNIP®-T” Pilot Line: A fully operational module featuring the exclusive Shoe Press and a Yankee Dryer section, both with a width of 0.5 meters. This module vividly demonstrated the tangible results and benefts of this Tissue Shoe Press”.
• “SMARNIP®-T” Application: A 3-meters wide Tissue Shoe Press in advanced state of assembly
• “R-WAY®” Solutions: A display dedicated to intralogistics, featuring a roll handling system and A.Celli’s autonomous guided vehicles (AGVs), demonstrating the seamless integration of A.Celli solutions into production logistics.
• “E-WIND® T200” Tissue Paper Rewinders: fnally, visitors were able to admire a T200 rewinder during the event, testifying to A.Celli’s wide range of oferings in the Tissue paper production sector.
The Open House event featured two daily sessions, ofering fexibility to accommodate the diverse schedules of attendees. Moreover, A.Celli Paper facilitated the convenience of access to the event by providing a private shuttle service directly from the MIAC 2023 exhibition.
In light of the resounding success of the “SMARNIP®-T Tissue Shoe Press”, Open House, Mr. Daniel Galli, General Manager of A.Celli Paper, expressed his satisfaction, stating, “We are incredibly pleased with the outcome of the Open House. The event’s success and the enthusiastic response from our industry peers underscore our dedication to innovation and our commitment to delivering cutting-edge solutions for the tissue paper and paper industry. We look forward to continuing our journey of excellence and to working collaboratively with our partners to shape the future of paper production.”
The event’s substantial turnout and the positive reception of the “SMARNIP®-T” further solidify A.Celli Paper’s position as a pioneer and leader in the tissue paper industry.
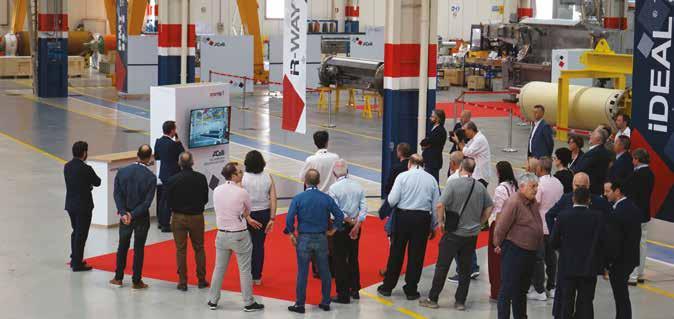
Join the USA’s largest tissue industry trade show in January 2024!
Tissue World Miami is back! Don’t miss your chance to reconnect with fellow tissue professionals, hear the latest insights, see new products, and network with leading fgures.
The conference theme, “All To Play for a VUCA World: Strategies for Winning With Tissue,” will showcase how leading companies not only survive but thrive in the current climate. Sign up now to secure your spot!

www.tissueworld.com/miami/en/home.html
tissueworldmiami@informa.com
FINLAND
Valmet has completed the acquisition of Körber’s Business Area Tissue
Valmet has completed the acquisition of Körber’s Business Area Tissue, the provider of innovative process technologies and related services for converting tissue jumbo reels into fnal tissue products. The closing of the transaction follows the agreement that was announced on July 7, 2023.
By combining the complementary ofering and competences of Valmet and the acquired business, Valmet creates the markets’ widest technology, automation and services ofering for the growing tissue industry covering the entire tissue value chain from fber to fnished products.
The new Tissue Converting business will operate as a business unit integrated in Valmet’s Paper business line. It focuses on delivering and serving converting lines for rolled and folded tissue products, packaging equipment and on providing digital solutions and services.
The acquired business enables Valmet to serve the tissue industry with wider expertise, process technologies and services covering end to end solutions including automation systems and fow control equipment.
Pasi Laine, President and CEO of Valmet: “Today we are happy to welcome the market leader in tissue converting and close to 1200 new dedicated colleagues to Valmet. The acquisition is a good strategic ft and complements Valmet’s tissue making ofering with strong expertise and complete solutions from tissue converting to packaging. By entering the tissue converting business, we take again a step forward with strengthened capabilities to serve our global customers even better.”
Oswaldo Cruz Junior, Head of Tissue converting business unit, Valmet: “Today marks the beginning of an important new chapter in our history, and we are very excited to be joining Valmet. Being part of Valmet will support the growth of our operations in the Tissue converting business and allow us to boost innovative projects. Now we can be even closer to customers as a one stop shop market leader”
The enterprise value of the acquisition is approximately EUR 380 million on a cash and debt free basis subject to ordinary post-closing adjustments.
The acquisition was completed on November 2, 2023.
Valmet estimates that the acquisition will bring sales, service, and cost synergies worth of EUR 8 million by the end of 2026. In Valmet’s reporting, the process technology part of the business will be consolidated to Paper business line and the services part to the Services business line.
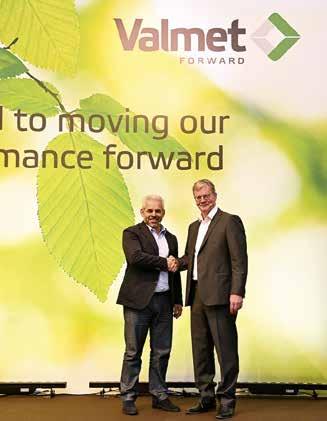
FINLAND
Valmet and Metsä Group to develop a joint sustainability model for industrial investment projects
Valmet and Metsä Group are jointly developing a comprehensive operating model to ensure sustainability in technology and maintenance investments. The model will address various aspects of sustainability related to the environment, social responsibility and governance (ESG). It will be used to verify the sustainability of the process technology projects delivered by Valmet to Metsä Group and the related supply chains. Valmet and Metsä Group have set up a joint working group to develop and deploy the sustainability model. The goal is to adopt the model by 2027.
“Valmet has consistently been developing its sustainability based on its comprehensive sustainability agenda. The company has been included in the Dow Jones Sustainability Index as one of the 300 global sustainability leaders for nine consecutive years. Our cooperation with Metsä Group in developing a sustainability model for investments contributes to both companies’ strong sustainability work and establishes tangible indicators for sustainability at diferent stages of investment,” says Anu Salonsaari-Posti, Valmet’s SVP, Marketing, Communications, Sustainability and Corporate Relations.
“As part of its strategic 2030 sustainability targets, Metsä Group is committed to ensuring that its supply network operates sustainably. Valmet is a large technology and service provider in the forest industry’s value chain, and its operations and procurement cover an extensive geographical area. By jointly scrutinising the chain’s sustainability in ever greater detail, we ensure that the forest industry’s positive impacts spread beyond the wood-processing value chain,” says Jari Voutilainen, Metsä Group’s SVP, Sourcing and Logistics.
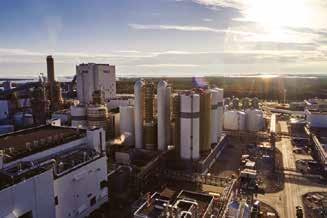
Runtech Systems renews its service ofering
Runtech Systems renews its service ofering by providing diferent service models, ranging from spare parts and basic bearing unit exchange to predictive and proactive maintenance. All service ofering is harmonized under RunCare name. RunCare Services ensure regular and correctly timed vacuum system maintenance and keep operational efciency at an optimum level. The cost of energy used by a vacuum system over its lifetime exceeds its purchase price many times over. Therefore, working at the optimum settings of a vacuum system is one of the most important economic factors in mill operation.
“Our aim is to provide our customers the easiest possible option to keep their vacuum system in optimum condition. At the mills manpower is often scarce. With RunCare, maintenance actions are planned and scheduled according to the mill’s production plan, requiring minimal time and efort from the customer’s organization”, says Mikko Virtanen, Production and Service Manager, Runtech Systems.
RunCare Services are categorized into four groups; Spare parts, RunCare Standard, RunCare Extended and RunCare Agreement. RunCare Agreement is the most comprehensive service model. It is a long term partnership, featuring extended warranty. With comprehensive reporting and feedback on the serviced equipment and 24/7 on-call assistance mills can be sure that the vacuum system is working at the optimum settings.
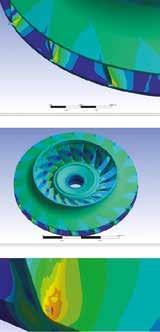
RunCare Agreement includes comprehensive reporting and recommendations, such as impeller crack test with a penetrant and impeller analysis.
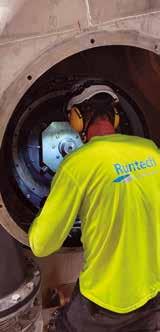
are economical to own and operate. But as with any other equipment, to assure trouble-free operation and long life, regular maintenance is recommended.
UKRAINE SWEDEN
Toscotec to supply a complete drying section rebuild to Rexcell in Sweden
Toscotec will supply a complete rebuild of PM1’s drying section to Rexcell Tissue & Airlaid at its Skåpafors mill in Sweden.
Toscotec will supply a customized solution designed to deliver substantial gas consumption reductions, as well as a signifcant increase in machine run-ability.
The scope includes a press section upgrade, a latest generation TT SYD Steel Yankee Dryer with new steam and condensate system, and a high efciency TT Hood with a complete air system. The latter features various steps of heat recovery and an advanced BMS (Burner Management System) to optimize combustion efciency through precise control of the combustion air, where the burners are ft to make an efcient use of LPG frst and biomethane in the near future. The hood plant is also equipped with TT Drying Equilibrium, a reliable system that automatically regulates the air balance in the hoods, thereby ensuring maximum drying efciency, faster basis weight changes, and a production increase.
The rebuild aims to considerably reduce PM1’s thermal energy consumption through the use of state-of-the-art drying technology designed for energy efciency, and to increase the machine speed and production capacity in the future. The project is planned for the second half of 2024. Lars Andersson, CEO at Duni Rexcell, comments, “At Rexcell we take global environmental challenges very seriously.
As a part of Duni AB, we share the same vision to be Net Zero 2030 along with considerable energy reductions. This machine upgrade is a strategic investment that perfectly fts into this vision. Toscotec’s energy efcient technology will take us a step closer to realizing maximum energy savings and minimal material footprint.”

A.Celli starts up its tissue line at Kochavinska Paper factory in Ukraine during war
Despite the extremely difcult situation created by the ongoing confict, A.Celli and Kochavinska Paper Factory teams managed to start up the new iDEAL® tissue line provided for the plant located in the Lviv region.
The difculties caused by the war posed a real challenge to the success of the project, leading to the search of new ways to complete the planned interventions. Thanks to this approach, A.Celli managed to install the plant and perform the commissioning and start-up with very few feld resources and intensive remote support, once again confrming itself as a company ready to be at its customer’s side in any situation.
The tissue paper production line supplied to Kochavinska Paper Factory includes an iDEAL® START 1.500 tissue machine, an R-WAY® roll handling system and a threeply E-WIND® T80S slitter rewinder.
The tissue machine is also equipped with the new A.Celli EVO-LOCK® Yankee Dryer, which in the present case features a 12’ diameter for a paper width of 2850 mm at reel.
This system further reduce the already low number of inspections required by a solution with a forged shell, and allows to achieve greater efciency and safety while maintaining the proven drying capacity of an A.Celli Yankee Dryer.
“I am very glad that the Embassy of Ukraine in Italy has succeded in facilitating this project, which made it possible to modernize the production of the Ukrainian Kochavinska Factory with the best Italian technologies and equipment” said Mr. Yaroslav Melnyk, Ukrainian Ambassador. “It is very important for us that the production in such socially important sector as paper continues and even develops during the war. I hope that many Italian businessmen will follow A.Celli’s extraordinary example of work and start their joint projects with Ukrainian partners in the near future.”
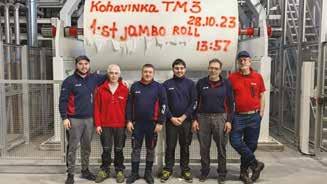
BRAZIL
Suzano selects ANDRITZ for major fuf pulp expansion project
ANDRITZ has received a follow-up order from Brazilian pulp and paper producer Suzano for a major conversion project at the Limeira pulp mill. The project will enable Suzano to increase its eucalyptus-based fuf pulp production capacity from 100,000 to 440,000 tons per year to meet the growing global demand for personal hygiene products. Suzano is the only company in the world producing fuf pulp from hardwood – based on ANDRITZ technology.
ANDRITZ will convert a pulp drying line for bleached hardwood kraft pulp (BHKP) into a line that can switch between BHKP and Suzano’s Eucafuf® pulp. With this project, Suzano continues to expand its highly successful Eucafuf business, which began eight years ago when ANDRITZ converted one of the company’s paper machines to produce fuf pulp from eucalyptus. This was the frst time fuf pulp was produced from hardwood, and the rebuilt machine has been running at full capacity ever since.
The Eucafuf brand is now well known in the hygiene market as an innovative and sustainable solution. It is approved for use in disposable care products that meet the strict criteria of the EU Ecolabel and the Nordic Swan label for high environmental standards throughout the life cycle of a product.
“The ANDRITZ solution allows us to expand our fuf pulp capacity using our existing production line. This meets our needs in terms of production capacity, cost efciency, and sustainability,” said Jean Moraes, Suzano’s Corporate Engineering Executive . “After the great partnership with ANDRITZ in our previous pioneering conversion project, we again chose ANDRITZ as a partner for our next major investment in fuf pulp production.”
Leonardo de Figueiredo, Sales Director for Pulp Drying at ANDRITZ, emphasized, “We will take care of the entire engineering, procurement, and construction process to transform an existing machine for fexible switching between fuf and market pulp grades. Having completed many projects in the past at several Suzano mills, we are very proud that Suzano has once again placed its trust in us.”
The equipment to be supplied includes a new state-of-the-art headbox, an extension of the former, a PrimeCal Hard hardnip calender, a PrimeReel, two winders, a new roll wrapping and handling line, and a core feeding system.
Production on the converted machine is expected to start in the fourth quarter of 2025.
Suzano to invest R$1.66 billion in new tissue paper mill
Suzano announced a series of projects aimed at expanding its installed production capacity and which will enhance its operational efciency. It will invest R$650 million in the construction of a tissue paper mill in Espírito Santo, it will also invest R$520 million to replace a biomass boiler at the same location. The company will also invest R$490 million to expand the supply of fuf pulp in São Paulo.
The total investment of R$1.66 billion, announced during the disclosure of the 3Q23 results, is aligned with Suzano’s strategic business avenues and underscores its commitment to constantly adapt its operations to evolving demand in Brazil and the global markets.
“Suzano’s competitive edge in the production of sanitary papers and fuf pulp, and the long-term growth of these markets driven by changes in consumption habits, underpin the strategy of strengthening our presence in these segments. We are the leaders in the Brazilian tissue paper market and pioneers in the production of fuf pulp from eucalyptus, which is why we must always be ready to serve our customers”, says Walter Schalka, CEO of Suzano.
The new fuf- and tissue-based products will reach the market by the end of 2025 and in 1Q26, respectively, and will add 340 thousand tons of fuf and 60 thousand tons of tissue to Suzano’s production capacity.
The third investment announced represents another phase in the process of modernizing its Aracruz Unit. The new biomass boiler will make the mill more efcient and stable, resulting in environmental gains for the operation. The boiler is slated to go operational in 4Q25.
The projects will be unveiled during Suzano Investor Day, to be held on October 27th when the company also will detail the 3Q23 results, which benefted from further improvements in the cash cost of production to R$861 per ton, at a time still marked by weak global pulp prices. Suzano reported adjusted EBITDA of R$3.7 billion and operating cash fow of R$1.9 billion. Pulp sales totaled 2.5 million tons and paper sales reached 331 thousand tons. Net revenue was R$8.9 billion. The company recorded net loss of R$ 729 million, impacted by the weakening of BRL during the quarter, which afected the portion of debt in USD and derivatives.
USA
ANDRITZ acquires NAF valve business
ANDRITZ has signed an agreement with Flowserve Corporation based in Texas, USA, to take over its NAF AB business.
NAF AB engineers, designs, and builds Flowserve’s NAF control valve portfolio. It is a leading supplier with longstanding experience in providing process control valves for pulp and paper and other related industries. With 50 employees at the facility in Linköping, Sweden, it has been a successful provider of process control valves for more than 100 years.
This acquisition further extends and strengthens ANDRITZ’s product and service portfolio in the feld of process control. The completion of the transaction is subject to approval by the respective authorities. The closing is expected to take place in Q1 2024. With this acquisition, ANDRITZ is adding control valves to its portfolio of process actuators, analyzers, and measurement equipment for the pulp and paper making process. For many years, ANDRITZ has successfully
equipped its production plant and equipment deliveries with NAF control valves.
This acquisition will further complement ANDRITZ’s capabilities to provide instrumentation, advanced process controls, as well as online process simulation and digital twins through its IDEAS digitalization platform, all from a single source. In addition, the NAF control valves will be seamlessly integrated into ANDRITZ’s Metris Asset Management suite, which provides automated monitoring of control valves to maximize plant uptime and process stability.
Jarno Nymark, ANDRITZ Executive Board Member responsible for the Pulp & Paper business area, says: “I look forward to welcoming the NAF AB team to the ANDRITZ GROUP. Their control valves are an important element for the operation and optimization of process plants and hence a valuable addition to our process control product portfolio. We are excited about the opportunity to expand NAF AB’s sales and service capabilities by leveraging our global presence.”
Sofdel invests in a new Valmet tissue production line
Sofdel America has decided to invest in Valmet’s Advantage DCT tissue line including an extensive automation package, fow control valves and Industrial Internet solutions to its Circleville mill in Ohio, United States. The target of the investment is to meet the American consumers’ increasing demand of high-quality tissue products with low environmental impact. The start-up is scheduled for the second half of 2025.
The new tissue line will have a design speed of 2,000 m/min and a width of 5,6 meters. The production line is optimized to save energy and deliver excellent paper properties. The line will have an annual production capacity of 70,000 tons. Valmet and Sofdel share a long history of partnership
CHINA
including eleven conventional tissue machines and four hybrid machines installed in various countries. The new Advantage DCT 200 (TM 3) line follows the two Valmet Advantage NTT lines installed at the Circleville mill in 2017.
“Sofdel has a strong focus on sustainable and high performing technologies that can fulfll our targets to increase capacity with as low environmental footprint as possible. The experience from recent Advantage ViscoNip rebuild projects has convinced us that it’s possible to achieve both energy savings and excellent paper properties under stable operating conditions. The industrial internet solutions will help us to further improve the performance,” says Simone Capuano, Executive VP, Operations and Supply chain, Sofdel America.
Sun Paper Group orders three Baotuo paper machines
Sun Paper signed a contract with Baosuo Enterprise Group for three Baotuo high-speed crescent former tissue machines. The machine model of this project is BC1800-2850, with a design speed of 1,800 m/min and a width of 2,850 mm.
Recently, the 300,000 tons/year household paper and converting project in the Nanning Park of Sun Paper’s Guangxi base was ofcially implemented, one year after two Baotuo paper machines were put into operation in the Beihai Park of Sun Paper’s Guangxi base.
Sun Paper’s household paper project in Nanning is planned to be constructed in two phases, mainly including production
workshops, post-processing facilities, warehousing, and other production auxiliary facilities. Among them, environmental protection disposal and thermoelectric energy rely on existing facilities in the “forest-pulp-paper integration” industrial park. The frst phase of the project is scheduled to be completed by the end of 2024.
Through the coordinated development of the three major bases, this project will create an optimal “forest-pulp-paper integration” whole industry chain system. The implementation of the new household paper project in Nanning Park will further enhance the household paper production capacity of Sun Paper’s Guangxi base.
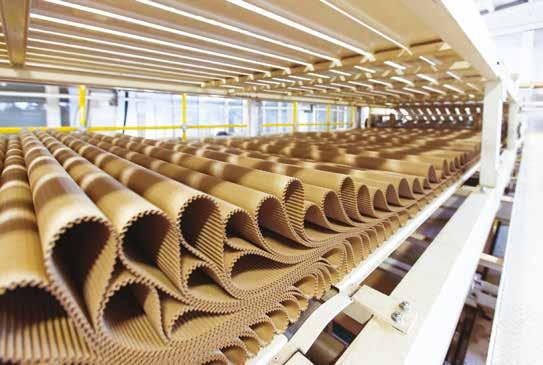
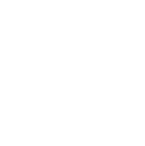
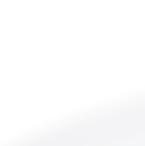
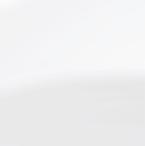

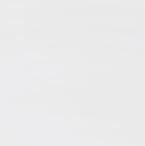
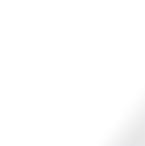
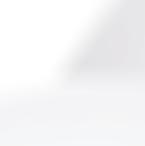

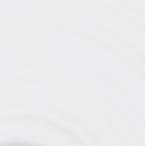



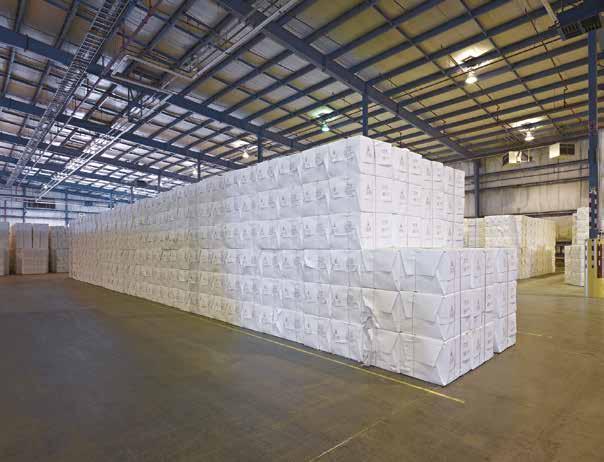

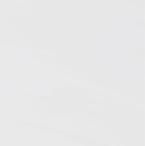
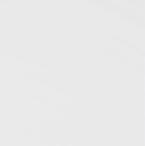
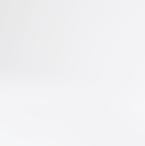
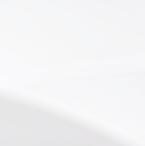
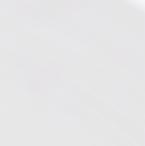


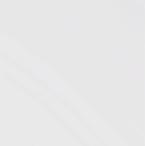
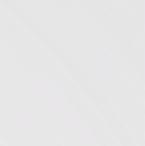

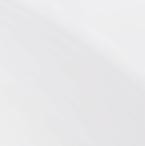
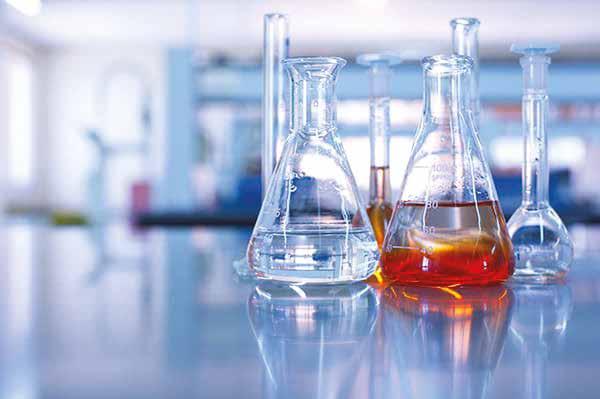




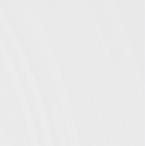

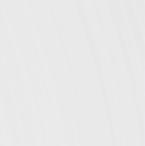




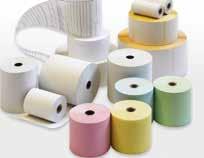
EDANA Sustainability Forum brings to a successful close a year of sustainability achievements
Sustainability is at the heart of everything we do today, from consumer purchasing choices to policy making, which is why, in November 2023 EDANA organized the frst edition of the EDANA Sustainability Forum. Established in Brussels, Belgium, this new event gathered over 150 nonwovens professionals to address issues from the future of value chain transparency to bioeconomy innovations.
Being held in the heart of the European Union (EU) ofered participants the unique opportunity to meet with EU ofcials. The three-day event included presentations from European Commission staf and culminated with a tour of the European Parliament.
This new conference evolved out of EDANA’s popular Circular Nonwovens Forum. The nonwovens industry has long been associated with progress, with providing society with versatile materials that touch nearly every aspect of our lives, from healthcare to hygiene and automotive to agriculture. The development of our products, however, comes also with a critical responsibility
for people, the planet, and prosperity. To achieve a truly sustainable nonwovens industry, we need to be responsible for the footprint that our innovations leave behind on our planet and this goes beyond circularity.
At EDANA we believe that bringing the nonwovens industry together at events is critical for our industry and can help to foster partnerships for progress, while still respecting confdential business information. This is why this year we revamped our events ofering to introduce new conferences including the EDANA Sustainability and Innovation Forums to discuss these issues and more. But this is just the beginning. Through responsible consumption and production, we can also help to meet other aspects of the United Nations Sustainable Development Goals, like climate change and biodiversity.
This led to EDANA reviewing and updating its sustainability vision, unveiling the new vision at the start of the forum. “Our previous sustainability vision was developed in 2018, and in this constantly evolving space no longer refected the improvements and investments that the nonwovens industry has made regarding environmental and societal aspects,” said Gil Stevens, EDANA’s External Relations & Sustainability Director.

Available on the EDANA website, the revised vision is split into three pillars addressing climate action, circular solutions, and a sustainable
value chain. These are all topics that were very much a part of the Forum programme and discussions.
Split into six sessions, the programme covered the crucial role that nonwovens play in society today, a lively panel discussion on how plastics can ft into a sustainable future, presentations on how to move towards a renewable economy, and more. EDANA is well placed to foster exchanges between the nonwovens industry and key stakeholders from European policymakers to NGOs and this was refected in the selection of 35 speakers, presentations, and panel discussions, including keynote speakers from the United Nations Environment Programme (UNEP) and the European Commission’s Environment Directorate General.
The session on end of life management of AHPs (Absorbent Hygiene Products), also presented an opportunity to share the results from EDANA’s AHP Waste to Resource Initiative. When it comes to AHPs consumers continue to favour single-use products over reusable ones, making research on recycling singleuse AHPs relevant. EDANA engaged the consultancy Ramboll to carry out a study – based on literature reviews and expert interviews – mapping existing technologies for collecting and recycling AHP waste. Felicitas Frick, Ramboll’s Senior Consultant Circular Economy and Resource Management who worked on the study, attended the forum to share the results with the attendees.
The report concluded that collecting and recycling AHP waste is very complex, and that no current initiative/ technology ofers a perfect technically and economically successful solution. This result proves that further investigation and research into AHPs and how to recycle them is needed and that industry engagement is crucial.
FOR REGISTRATION
24 > 25 January 2024
Jumeirah Beach Hotel ⁄ Dubai ⁄ UAE
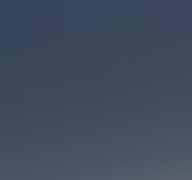



Back by popular demand, the eagerly anticipated MENA Nonwovens Symposium is designed for nonwovens professionals and business leaders operating within the Middle East and North Africa.
Join us in Dubai for expert discussions on:
� Consumer and market trends � Raw materials and circularity
� Construction and durables � Absorbent Hygiene Products

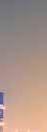



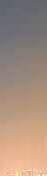
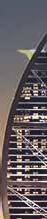

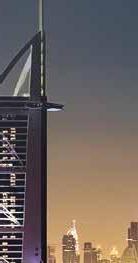
� Hygiene & Wipes � Nonwovens in health
Register early to secure your spot and benefit not only from reduced registration fees but also to guarantee a room at the hotel at a discounted conference rate. Spaces are limited.
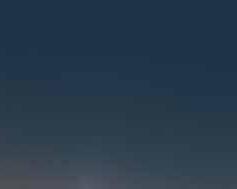
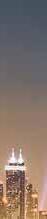

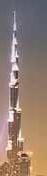
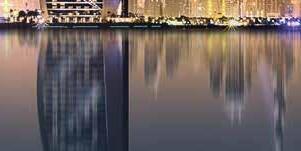
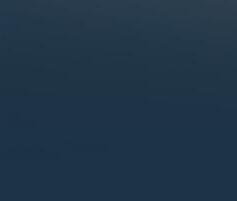
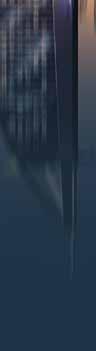
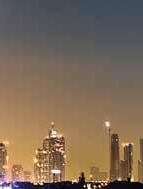

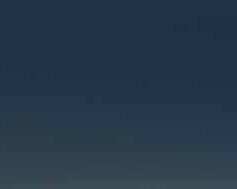
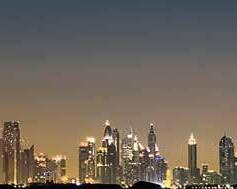
Sponsorship Opportunities

Ensure your company is at the forefront of attendees’ minds by sponsoring the fifth edition of this landmark event for nonwovens professionals working or doing business in the MENA region.

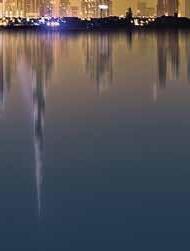

From brand visibility on charging stations and during networking breaks, to tabletop exhibitions and renting private meeting rooms, we have many options available to suit your needs. Contact us at mena@edana.org for more information.
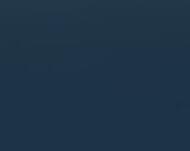
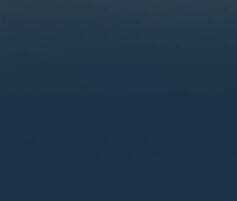


A.CELLI & PMT: The best choice for upgrading or converting your paper mills
The paper industry has been undergoing several changes and evolutions for some time now, caused by multiple factors, including growing environmental awareness, digitization, and a decrease in the use of paper itself in some areas of daily life.
On the one hand, there is an increased focus on sustainability and reduction of environmental impact (incidentally also demanded by consumers and regulatory bodies), which has led to greater use of recycled fber and renewable energy sources and the implementation of more efcient and cleaner production processes. On the other hand, increasing digitization has reduced the demand for paper in some areas, such as those of document production, printed advertising, and periodical publications. These events have prompted many paper mills to seek new market opportunities.
Being competitive today
To recover competitiveness and make production more efcient, it is possible to consider modernizing machinery or converting it to produce types of paper that are more proftable and in demand on the market, such as that used for packaging (which according to Assocarta today accounts for 52% of Italian paper production) or tissue paper.
In this regard, Assocarta points out that the turnover of the graphic papers segment in 2020 showed a 26.5 %

decrease nationwide compared to 2019, partly to be attributed to the lockdown and partly due precisely to the conversion of a major plant that was destined for the production of corrugated cardboard.
Within tissue, by 2030 Afry forecasts
6 % growth led by emerging markets, especially China (+4 %) and other Asian countries (+2 %), which together will account for 60 % of the increase in global demand. However, Afry points out, it will be a market with increasingly ferce competition, and in order to carve out its own space, it will be necessary to be able to optimize costs and have more efcient production processes.
PMT, a highly qualifed strategic partner
Cost containment, optimization, increased efciency, reduced consumption: these are the aspects that must be focused on today to be competitive in the world of paper production.
A.Celli’s mission, with the experience gained by PMT, is to help paper mills around the world achieve these goals, providing state-of-the-art services
and components and intervening on production machinery to reduce the use of raw materials, limit energy consumption and increase the efciency and reliability of the entire plant.
Through interventions such as the rebuilding or conversion of the machinery, A.Celli enables both maximizing the performance and safety of existing machinery and reacting to a changing market by seizing new business opportunities.
By joining the A.Celli Group in September 2020, PMT has brought in-depth expertise with the aim of providing efective and efcient solutions to players in the paper industry. By applying the technologies conceived and developed by PMT, A.Celli is able to optimize processes and improve production by intervening on the machinery in use (as we have seen) or introducing new ones where necessary.
An opportunity of absolute strategic value that takes on even more signifcance in a situation such as the current one, which is characterized by numerous companies in difculty. This is due in part to the aforementioned problems at the industry level, and in part to the rather frequent use of limited-performance machinery due to age or lack of optimization.
The cost aspect is particularly important at a time like today, marked by exponential increases in production expenses attributable to rising energy costs. Indeed, to avoid driving up prices for the end customer, the alternative is to improve and make the production cycle more efcient.
All the tools and support needed
As we have seen, interventions can be aimed either at improving an existing plant or converting it to other types of production. In either case, one of the indispensable steps is a prior analysis of the plant and the existing machinery to see if and how interventions can be made to achieve the desired result.
When the best choice for the company turns out to be a change of the
production type, thanks to PMT’s experience and numerous successful interventions worldwide, A.Celli is able to reconvert your plants ensuring excellent fnal results in line with the individual customer’s expectations.
To this end, A.Celli can provide technological solutions for every stage of the papermaking process, starting from the headbox, through various forming systems, energy- and paper quality-optimized pressing, to drying and reel winding.
In particular, the implementation of the Shoe Press (a concept introduced by Beloit and later developed for all paper grades by PMT) in the press section allows for a signifcant enhancement of the process efciency while improving paper characteristics.
To reduce consumption and increase efciency, PMT can also intervene on winders and rewinders, as well as in the stock preparation cycle. In addition to this, there are numerous services ranging from the maintenance and replacement of mechanical parts to the analysis of the installed equipment and feasibility studies for the re-engineering of the plant.
Finally, the synergy between PMT’s and A.Celli’s experiences makes it possible to provide solutions that are not limited to the paper machine alone but involve the entire production process, from the logistic management of raw materials and fnished product to the monitoring of production parameters through customized and user-friendly IT solutions.
In conclusion, by relying on A.Celli you will be sure to receive all the tools and support you need to make your paper mill highly competitive, regardless of the size of your plants and the age of the machinery used.
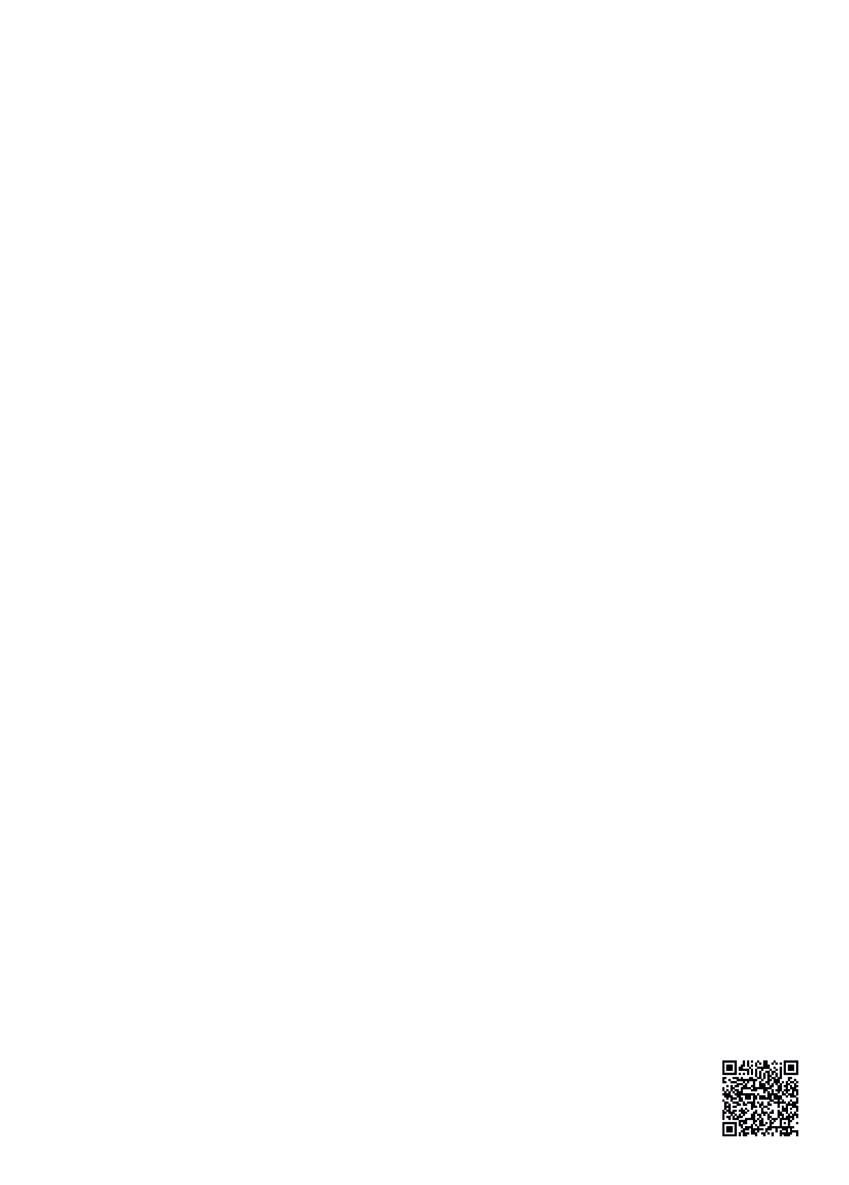
Cherel-Bonnemaison Associate partner, McKinsey
Alexia Letofe Analyst, McKinsey
Sebastien Leger Partner, McKinsey
David Feber Partner, McKinsey
Daniel Nordigården Partner, McKinsey
Sustainability in packaging: Global regulatory development across 30 countries
Sustainability regulations for packaging have become increasingly ambitious. A detailed understanding of the diverse regulatory landscape will be essential for companies to remain compliant.
Sustainability in packaging is a megatrend shaping the packaging industry, with consumers becoming increasingly worried about the environment and the impact of packaging leakage. In response, new, stricter sustainability regulations are emerging on multiple fronts with increasing frequency. However, regulatory focus and approaches vary considerably by region and diverge even further when viewed at the country or state level. This heterogeneity is making the fastchanging regulatory landscape complex to navigate on a worldwide basis. To better understand the recent developments, we have mapped regulations in 30 countries around the world. Our fndings reveal several common patterns of development that can be represented by four archetypes globally. To ensure they comply with the evolving requirements, packaging companies should stay tuned to regulation developments in sustainability packaging by tracking changes in their focus markets and implement processes to address future requirements proactively.
Increasing pace of regulatory development
Pressure to reduce packaging waste has increased dramatically in the face of global consumer sentiment aroused by visceral images of packaging leakage into oceans (Exhibit 1)—and regulators
are responding to address the public outcry. In recent years, we have seen a rapid increase in sustainablepackaging regulations well beyond a focus on shopping bags and selective food-service items. It is critical for companies across the packaging value chain to be aware of the accelerating pace of regulatory development, as noncompliance could lead to the imposition of tax increases or penalties.
However, understanding the developing regulations on a global scale is highly complex given the following factors:
• Regulatory maturity across countries is extremely heterogeneous.
• Established or aligned terminology is not in place globally—for example, the term recycling can have diferent meanings, leading to variable intensity of impact for the industry.
• What is in scope varies. For example, some regulations are focused on multiple categories, applications, end products, and materials, while others focus on specifc aspects—this creates potential overlap with diferent regulations covering a similar scope.
• Regulations are still in early stages of development, leading to uncertainty around undefned scopes, action plans, or targets.
• The geographical picture is complicated, as regulations can be developed at a federal, state, or even city level.
To better understand the developing picture, we have mapped current and proposed regulations in 30 countries around the world. This covers all regions: Europe and the European Union (eight countries), North America (three countries), Latin America (four countries), Asia (seven countries), and the Middle East and Africa (eight countries).
Mapping regulatory development across 30 countries
It is clear that there has been a general awakening on the issue given that 29 out of 30 countries studied have started to discuss and implement sustainable-packaging regulations.
As expected, these regulations are intended to enforce new requirements with the principal aim of limiting the negative impact of packaging on both the environment and on human health. Most regulations across the countries studied also tackle the following endto-end elements:
• packaging specifcations (such as composition, size, and weight)
• attributes of packaging (for example, recyclability and biodegradability)
• expected primary use of packaging (for example, labeling and traceability to promote customer empowerment)
• packaging chain, from raw-materials sourcing to disposal, including collection and sorting schemes and reuse or recycling target setting
Countries have mostly embarked on their sustainability journey by addressing the start and the end of the fow—that is, the restriction of certain materials and a focus on waste management via extended producer responsibility (EPR). More advanced countries have set up infrastructure to support lasting changes in design, recycling capabilities, and recycledcontent use (Exhibit 2):
• Twenty-eight out of 30 countries have collection, sorting, and EPR schemes and regulations in place or in development.
• More than 40 percent of the 30 countries studied already have an EPR scheme in place.
Packaging-waste management is subject to the highest number of regulatory measures worldwide (91 in total). In addition, there has been an increasing regulatory focus on more specifc areas of packaging, including the following:
Plastic packaging
In the past three years, sustainablepackaging regulations have tended to focus primarily on plastic packaging (versus other substrates). Eighty-three percent of the legal measures relating to sustainable packaging worldwide focus on plastics—with a total of 147 measures identifed. The European Union and Asia have the highest number of regulations focusing on plastics, with France and India being the top countries in this respect.
Beverage packaging Regulations worldwide tend to have a relatively higher focus on beverage packaging than on other categories such as food and home personalcare packaging. However, there are noticeable regional diferences:
• The European Union and North America focus more on beverages, with 50 to 60 percent of their regulatory measures having a specifc end-product scope targeting beverages.
• Latin America and the Middle East focus more on food packaging.
• In the European Union and Asia, an emerging trend aims to tackle packaging across multiple product categories, refecting a more holistic approach beyond a single focus area (such as beverages) to encompass a broader spectrum of end-use areas.
Primary
versus secondary
packaging Regulations tend to focus on primary packaging all over the world, but a focus on secondary and tertiary packaging1 is more prevalent in Asia:
• Worldwide, nearly 90 percent of legal measures with a specifc scope of packaging type tackle primary packaging alone or together with other packaging types (secondary, tertiary).
• China, India, Vietnam, and the Philippines are proposing regulatory
measures that focus on secondary and tertiary packaging, while India has the most measures focusing on secondary and tertiary packaging. China has also shown an increasing focus on regulations around e-commerce packaging to minimize waste and leakage.
Regulatory vehicle for change
Our mapping reveals that fnancial penalties (versus subsidies) represent the main and preferred regulatory vehicle for sustainability change in the packaging industry: approximately 45 percent of legal measures implying a defned fnancial fallout refer to penalties—and these are generally related to taxes, fnes, and fees. France uses incentives the most to encourage change in packaging sustainability (for example, via indirect premiums or indirect subsidies/funding).
Four archetypes identifed
Most countries are moving toward setting up regulations around sustainable packaging, though at diferent paces and in various depths (Exhibit 3).
In order to better understand the developments on a global scale, we have developed a methodology to map countries along four key dimensions covering national strategy on sustainability ambition, time, scope, and maturity (Exhibit 4).
This mapping and rating of national strategy has enabled us to categorize the world according to four archetypes, from the least mature countries to the leading countries—those that are defning what sustainable packaging means.
Archetype 1. Unclear strategy with no targets or milestones and unstructured mechanisms to support sustainable packaging. This archetype (seven of the 303 countries we mapped, mainly located in North Africa, the Middle East and Southeast Asia) represents countries with limited regulations on this topic and where sustainable packaging is not the principal concern. Regulations have started to emerge in these countries, but they focus mainly on packaging-waste management. These countries typically do not
present a holistic regulatory picture of packaging sustainability.
Archetype 2. Very high-level strategy with mostly generic targets, vague milestones, and unstructured mechanisms. This group represents countries in the early stages of sustainable-packaging regulation, mostly in the Americas. Their regulations are very immature, with numerous regulatory initiatives still under discussion or needing signifcant clarifcation and translation into more practical and concrete measures. Although they have demonstrated some willingness to make progress, the paths these countries will follow remain unclear. This category comprises seven countries.
Archetype 3. Clear strategy with generic/common targets (not by material type), with defned key milestones, incentives, and penalties. This archetype represents countries with a very recent but strong regulatory commitment to shaping the packaging industry in a more sustainable way. Prompted by business and public
concerns, these countries have already started to defne concrete plans of action and supporting measures. Eight mostly European and Asian countries comprise this archetype.
Archetype 4. Detailed, holistic strategy for at least one packaging type, with clear milestones supported by detailed targets, and structured mechanisms in place. This group comprises countries with developed economies and a very high packaging consumption, with market growth rates that tend to be slowing. Environmental considerations are not novel within the regulatory context of these countries. There is an advanced regulatory landscape covering packaging sustainability (for example, detailed target setting for recycling, as well as concrete incentives and penalties to support regulatory objectives). Seven of the 30 countries studied are in this archetype. This group consists mainly of European countries and a small number of countries in Southern Africa and Asia.
This national strategy ranking indicates that 40 percent of countries have high ambitions to take concrete actions, supported by a clear set of targets, by 2030. The remaining countries are committed to longer timelines and looser initiatives, or even lack visibility.
Questions to ask to stay up to date on development
The constant evolution of regulation will require packaging value-chain companies to keep track of changes in order to remain compliant. At the same time, they will need to develop capabilities to acquire an in-depth understanding of regulatory measures, scope, and application—as well as the implications for their own business and customers. This will also be important from an investment perspective. To get started, we propose three critical questions for packaging companies to consider:
1. Do we have a market intelligence taskforce in place within the organization to keep track of regulatory changes in our focus markets and to understand what other players along the value chain are doing?
2. Do we have agile processes in place internally to address current and future regulatory requirements quickly, and will we be able to change or adapt our business model in order to comply with the regulations?
3. What product- and technology-level investments should we be making regarding packaging as part of product sustainability? Here, it will be important to identify whether new packaging products will need to be developed to comply with the regulatory requirements (and if these products need to be diferentiated for specifc countries or focus markets). It will also be important to identify partnering opportunities for circular recycling, including renewable materials.
The sustainability regulation landscape is becoming ever more complex. The number of regulations, and the speed in which they can become efective, is increasing fast. In addition, 75 percent of the 30 countries mapped have implemented or intend to put in place penalties for regulatory noncompliance. A granular understanding of the regulations, therefore, is a must-have for all organizations along the packaging value chain.
1 “Sustainability in packaging: Investable themes,” McKinsey, March 26, 2021.
2 “Sustainability in packaging: Inside the minds of global consumers,” McKinsey, December 16, 2020.
3 David Feber, Daniel Nordigården, and Shekhar Varanasi, “Winning with new models in packaging,” McKinsey, May 9, 2019.
4 Primary packaging is typically the packaging closest to the product (sometimes referred to as consumer packaging). Secondary packaging is then used to promote, hold, and protect the primary packaging/product or packaging units. Tertiary packaging focuses on protecting and facilitating the transport of a series of products (sometimes referred to as transit packaging).
5 For example, funding of studies and experiments prior to investments, or premiums/bonuses granted to products that incorporate at least 10 percent of recycled postconsumer waste.
6 We studied 30 countries in total, with one country omitted from the archetypes because of incomplete sustainability regulation information.
7 “Sustainability in packaging: Investable themes,” March 26, 2021.
This article was originally published by McKinsey & Company, www.mckinsey.com. Copyright (c) 2024 All rights reserved. Reprinted by permission.
The authors wish to thank Claudia Barboza Hidalgo, Martijn De Meyer, Daniel Eriksson, Rachel Hao, Emily Roeper, Jingyu Song, and Christof Witte for their contributions to this article.
Conference May 13-14, 2024
Nanjing International Expo Convention Center

Exhibition May 15-17, 2024
Nanjing International Expo Center
The largest exhibition in the feld of tissue and disposable hygiene products in the world
An infuential platform for Chinese and overseas enterprises to exchange
● Tissue paper & disposable products manufacturers:
Tissue paper, wipes, sanitary napkins, pantyliners, baby/adult diapers, pet pads.
● Machinery manufacturers for tissue paper & disposable products:
Tissue machine, cylinder, felt and wire, converting machinery, disposable hygiene products machinery, machinery for airlaid and nonwovens, other related apparatus and fttings.
● Raw/auxiliary materials suppliers:
Fluf pulp, airlaid, nonwovens, flm, adhesive tape and release paper, hot melt adhesive, SAP, chemical actives, elastic band, package materials.
● Agents, distributors
Organized by
Contact person: Register
Ashley (Ms. Wang Juan) Mobile: +86-15810334780
Alice (Ms. Zhang Yuan) Mobile: +86-15108406885
Tel: 86-(0)10-64778184/8197
E-mail: cidpex@cnppri.com Http://cloud.cnhpia.org/

ALL YOU NEED TO KNOW ABOUT BABY DIAPERS: Market analysis, technologies and trends

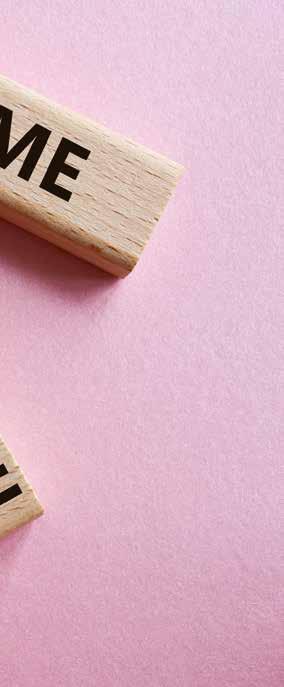
Owing primarily to declining birth rates, the baby diaper market is going through a period of stagnation in North America and Europe, where consumer awareness and market saturation are at an all-time high. However, it is not all doom and gloom, as demand for Disposable Hygiene products is gaining momentum in developing countries in Asia and on the African continent, where rapid urbanization is driving progress.
Despite the increase in demand in some countries, Euromonitor recorded a drop in the overall volumes of baby pants and baby open products sold over the past three years. Nevertheless, the market segment was valued at 47.3 billion dollars in 2022, making it a very lucrative opportunity for brands and manufacturers in the Disposable Hygiene industry.1
In addition, two key trends have stood out this year: consumer awareness and price sensitivity 1 In 2023, consumers are looking for products from sustainable materials that guarantee them convenience of use (in terms of shape and design), an afordable yet premium ft and excellent performance. To meet these consumer needs, manufacturers are looking for baby diaper machines that give them a competitive edge.
GDM’s solutions for Baby Diapers segment
In recent years, product developments have taken the form of machine upgrades that prevent leakages, improve performance and reduce thickness. To achieve the latter, eforts have focused primarily on the absorbent core of diaper products. GDM has engineered the Core Plus solution that allows manufacturers to stand out from the crowd. This new technology thins down the absorbent core, improving product performance, ft and wearability while keeping costs to a minimum. Thanks to this new solution, the products produced by GDM’s baby diaper manufacturing machines guarantee:
• a core weight variation vs the target weight of diapers of less than 1.5%
• improved core integrity, thanks to the redistribution and combination of SAP and fuf to ensure a better liquid spread and protection against leakage
• the prevention of sagging, thanks to a reduction in the quantity of fuf used in baby diapers and the even distribution of weight
And if all that wasn’t enough, Core Plus technology implicates the use of 40% fewer core materials, allowing manufacturers to save up to 800k € a year (internal estimation).
A closer look at GDM’s babypant and open diaper machines
GDM’s machinery portfolio benefts customers across several Disposable Hygiene segments, but nowhere is this better demonstrated than GDM’s baby pant and baby open portfolio, where two machines in particular can guarantee manufacturers premium quality, ease of use and sustainable products.
The BP6-Red baby pants manufacturing machine produces premium-quality, H-type baby pants. This fully automatic machine is equipped with the technology to produce Core Plus, thus allowing manufacturers to reduce the sagginess and bulkiness of baby diapers. GDM’s innovative BP6 baby pant machine boasts an intuitive and easy-to-use interface and excellent benefts in terms of operations and handling. Moreover, the BP6 production machine guarantees energy savings of up to 30% thanks to its improved ability to control and tension raw materials; it also streamlines production and product costs by leveraging cuttingedge technical solutions.
Meanwhile, the B8-W Grey is a highspeed baby open diaper manufacturing machine that guarantees fexibility and a fast changeover when manufacturing products with front and rear wings.
Upgrade Kits: the smart way to improve your existing production lines
The Disposable Hygiene market is showing promising signs of growth in both volume and value across all segments, with Adult Inco, Baby Pants and Sanitary Napkins leading the way.2
The past two years have seen a faster increase in value compared to volume, mainly due to higher prices. However, experts predict that prices will continue to increase over the next fve years, driven by infation, raw material shortages, and the introduction of new premium products.
The Baby Open and Lady Sanitary Protection segments, being the more mature, are the most critical contributors to the Disposable Hygiene market in terms of volume, and unit prices.
Against this backdrop, consumer awareness and cost orientation in diferent regions are impacting investments in new machinery and related obsolescence.
Consumers in regions such as Europe and North America are mature and aware of their diferent product options. Meanwhile, in the Middle East, Turkey and India, manufacturers are more cost-oriented and therefore make fewer investments. In light of these trends, upgrading existing production lines with cost-efective upgrade kits can help manufacturers remain competitive while optimizing production and equipment costs.
Upgrade Kits: GDM makes business easy
Upgrade kits are becoming an increasingly popular option for businesses looking to remain competitive and optimize their production and equipment costs. At GDM, we have over 30 years of experience and proprietary know-how in the Disposable Hygiene market, and we ofer upgrade kits that are tailored to meet the specifc needs of our clients thanks to our 360-degree Business Made Easy approach.
Our upgrade kits are designed to improve existing production lines in four key areas:
• Speed - Upgrade kits can increase the number of Baby and Adult products manufactured per minute, helping to maximize Overall Equipment Efectiveness (OEE) while minimizing unitary product costs. The investment payback timeline for these kinds of kits is typically 12-18 months, and installation can take as little as three-to-four weeks.
• Products - Upgrade kits ofer several benefts for the Adult and Baby segments, including premium features that improve comfort ft and softness while also optimizing costs. For example, GDM’s in-line laminated waistband and 3D topsheet lamination kits have been developed in order to make premium diapers. Moreover, upgrading to in-line raw material lamination instead of buying prelaminated RMs can also contribute to savings on materials.
• Safety - This is an important topic for industrial environments and is the focus of strict and evolving local directives. In this context, we have developed several diferent kinds of kits, such as protection doors to reduce noise and specifc changeover tools to improve safety while moving plates and materials.
• Modernization of commercial components - By modernizing OEM components sufering from physiological obsolescence (typically motion and remote connection system components), you can improve process performance and extend the life of your existing machinery while minimizing downtime.
Moreover, as an added bonus, the modular concept of GDM-branded machines allows for easy installation of upgrade kits, making it a cost-efective solution that extends the life of existing machinery while keeping up with the latest industry developments.
To learn more about how GDM Upgrade Kits can help you save money and improve your business operations, please contact info.it@gdm-spa.it
1 Global Baby Nappies/Diapers/Pants Update: Balancing Afordability and Premium Innovation. Euromonitor. https://www.euromonitor.com/globalbaby-nappies-diapers-pants-updatebalancing-afordability-and-premiuminnovation/report
2 Retail Tissue and Hygiene: HalfYear Update H1 2023. Euromonitor. https://www.euromonitor.com/ retail-tissue-and-hygiene-half-yearupdate-h1-2023/report
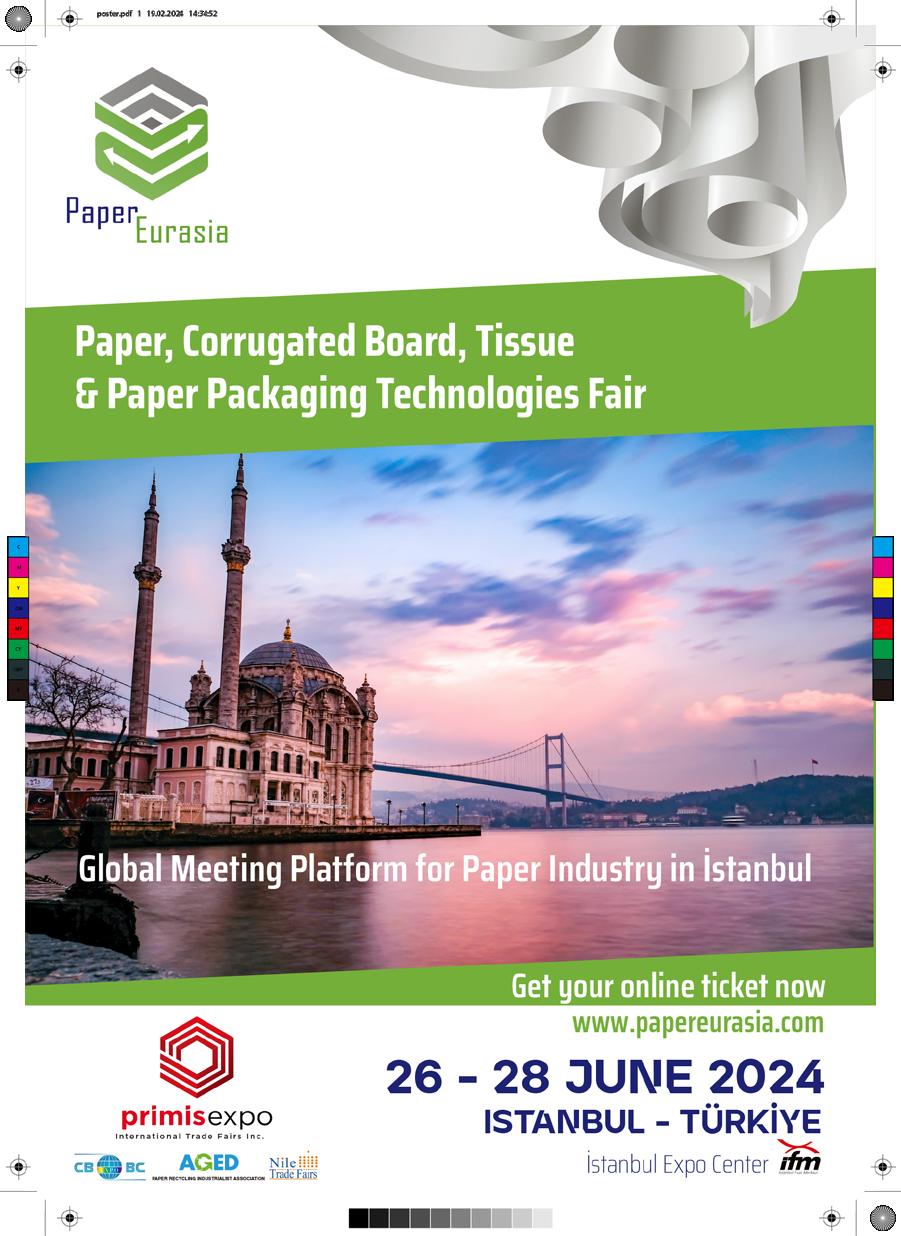
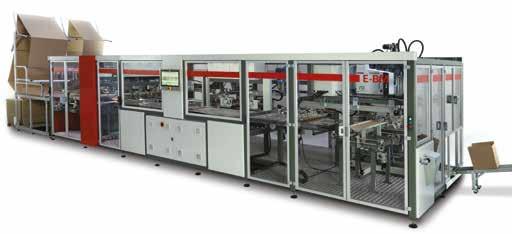
COESIA
MOVES INTO E-COMMERCE WITH A NEW BOX MAKING SOLUTION FROM EMMECI
Emmeci, a Coesia company leader in the design and manufacturing of machines and systems for the production of premium packaging, launches E-BM, a complete ft-tosize box making solution for the e-commerce sector.Water use in the industrial sector at large is one of the most important topics of debate; in particular, in paper production this natural resource is an essential component for fbres transportation, equipment cleaning, lubrication, cooling and in the achievement of high tissue quality.
The ideal packaging is ft-to-size, compact and robust With e-commerce, the packaging must follow the object’s dimension, to ensure its integrity frst and foremost. E-BM produces extremely robust packs: the base of the pack comprises a single piece with no bottom closure, and the corners are reinforced with a double layer of material. The result is an improved resistance to protect items during delivery and a better customer experience. The E-BM is engineered to integrate seamlessly with warehouse control and management systems, enabling the dimension of the packaging to be adapted automatically to end product, on-demand. The ability to produce right-size packaging means up to 40% smaller packaging sizes (compared to the standard shipping boxes commonly used on the market) and less raw material, saving on paper. Fit-to-size boxes are also more manageable in the downstream phase of the supply chain, facilitating handling and space as well as transport optimization during shipping or delivery,
resulting in reduced emissions and inventory footprint.
The bar is ever higher, but Coesia is up for the challenge Logistics hubs primarily need systems capable of handling, sorting, and packing an increasing number of products of diferent shapes and sizes. That is why using a partner combining long-term experience in developing rigid box packaging solutions like Emmeci with the strength of a leading industrial automation group like Coesia is crucial. Emmeci and Coesia have created E-BM; a packaging machine specifcally designed for the e-commerce sector. E-BM packs into boxes a wide range of goods from sectors such as electronics or fashion, including tablets, PCs, clothing, and many other everyday items.
Flexibility and customization
E-BM fexibility allows not just to automatically adapt the box to the dimensions of the product to be shipped, but also to customize the packaging in many diferent ways, including tape closure. It also ofers numerous options for printing codes and labels to assist in package control and traceability processes.
The benefts of having a single partner
Choosing Coesia as a single partner in the e-commerce industry ofers infnite advantages, frst and foremost that of having an end-to-end solution provider. Coesia seamlessly guides its clients through every leg of their e-commerce automation journey, spanning from box making and flling, through inline printing, up to palletizing.
Coesia’s e-commerce solutions revolve around three key domains, fnely tuned technologies to elevate operations and ensure customer satisfaction.
Firstly, Coesia pack automation solutions redefne wrapping, box making, box flling and inline printing for the e-commerce industry. Tailored to perfection, these solutions cater to the need for right-sized, customized package, ensuring a superior customer experience.
Secondly, the E-Fulfllment solutions usher in a new era of process automation, meticulously crafted to address the ever-evolving challenges faced by e-commerce players. From conveying solutions to ground-breaking sorting equipment, the portfolio is designed to optimize every facet of their operations.
Lastly, Coesia advanced robotics capabilities ensure secure handling of a diverse array of products, boxes, and cases, for a seamless journey from picking systems to palletizing and depalletizing equipment.
In the dynamic world of e-commerce, Coesia shines as a pioneer in cuttingedge technology and customer-focused solutions. Innovation and userfriendliness are at the core of highly advanced technological solutions, all geared towards delivering agility, fexibility, and efciency.
A sector experiencing double-digit growth
The e-commerce packaging sector is worth around 60 billion dollars globally and is more dynamic than ever. According to forecasts, it will grow by 13.8% over the next fve years to over USD 115 billion in 20281. E-commerce is now the preferred sales channel for a wide range of goods, including consumer goods, food, hi-tech and fashion. The sector’s expansion involves more than logistics and transport; the related packaging world is also experiencing growth and change.
1 https://www.mordorintelligence. com/industry-reports/e-commercepackaging-market
MICROLINE PARTNERS WITH DI MUCCI D.O.O. TO DEVELOP ENVIRONMENTALLYFRIENDLY FILMS
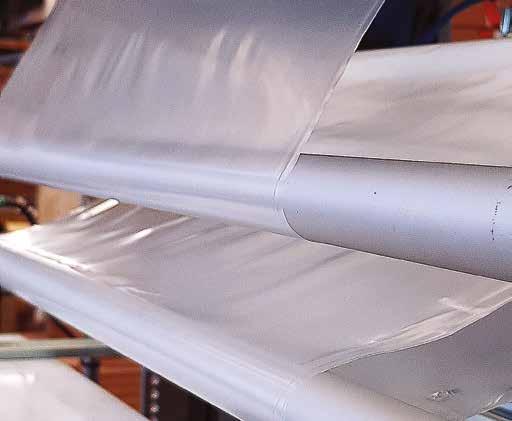
Based in Anzola dell’Emilia, near Bologna, Italy, Microline specialises in the design and marketing of complete conveyor and packaging systems for the Tissue sector and secondary packaging machines for the Food and Cotton sectors. With its frm commitment to sustainability, the company manufactures machinery that afords signifcant waste reduction and optimised energy consumption. Microline also believes strongly in the use of new environmentally-sustainable materials. For this reason, it has partnered with Slovenian company Di Mucci d.o.o., an undertaking that boasts consolidated know-how in the development and manufacture of compostable flm for packaging applications. The purpose is to study the machinability of the materials on machines intended for packaging.
The project: testing use under production conditions
As part of Microline’s commitment to research and development it works with a number of technological partners, including companies that design and manufacture packaging flm. As the issue of sustainability becomes increasingly important to consumers and, consequently, to manufacturers, the Bologna-based company decided to run a series of tests on its machines aimed at verifying the handling and performance of environmentally-friendly
packaging products. The project is part of the environmental policy that the company has been implementing for several years and that has allowed it to develop machines with a far lower environmental impact than the competition. As a matter of fact, Microline’s wrappers and bundlers do not generate trimmings, thus eliminating wrapping material wastage, translating into savings of between 20% and 30% compared to its competitors. Microline therefore chose Di Mucci, a leader in the development of compostable flms with vast potential for use in the packaging sector, to develop a series of tests under diferent production conditions.
New materials as the frontier of sustainability Materials research is one of the frontiers of packaging, particularly since environmental sustainability has become of paramount importance. In the specifc case of compostable flms, they have the advantage of not damaging the environment.
The project considered two flms:
Vincentius-SuperPower: with OK HOME COMPOST certifcation issued by TÜV Austria, this is a revolutionary flm that replaces conventional PE flm in many applications. Derived from natural resources, such as sugar cane, cassava and corn, it decomposes into
biomass, carbon dioxide and water under ambient conditions (30 °C) and can be disposed of with organic waste. In addition, it is also compostable in open-air landflls under ambient conditions (30 °C), without requiring a dedicated composting system. This characteristic makes it unique in the sector.
Vincentius-POF is certifed for industrial composting and replaces conventional shrink-wrapping polyolefn (POF) and polypropylene flm. It too is derived from natural resources such as sugar cane and farming waste. It is disposed of through anaerobic digestion, a biological degradation process that takes place in the absence of free oxygen. Degradation is caused by bacteria that obtain the oxygen required for their vital functions from biomass. The flm’s biodegradation takes place in under three months, converting it into excellent natural compost, without leaving any residues or chemical substances harmful to the soil or human health.
Vincentius SuperPower and VincentiusPOF are perfectly compatible with the machines, thus guaranteeing a lower environmental impact.
As a matter of fact, the results were far more encouraging than expected: when tested for the packing and overpacking of diferent product ranges, including individual AFH-type rolls and bundled bags of cofee, the flms proved to be perfectly compatible with Microline’s machinery range, with performance on a par with the equivalent plastic products in terms of mechanical strength, pack quality and the performance obtained. It was not necessary to make any hardware changes to the Microline machines, which only require a simple change of parameter settings on the HMI panel to be able to use the compostable flms. This paves the way for the massive use of this type of flm in the consumer packaged goods sector, and that of Tissue products for consumer or industrial use, and many more besides. Increasingly deeper knowledge of materials and their behaviour enriches the company’s know-how and can be an important aspect to be shared with customers.
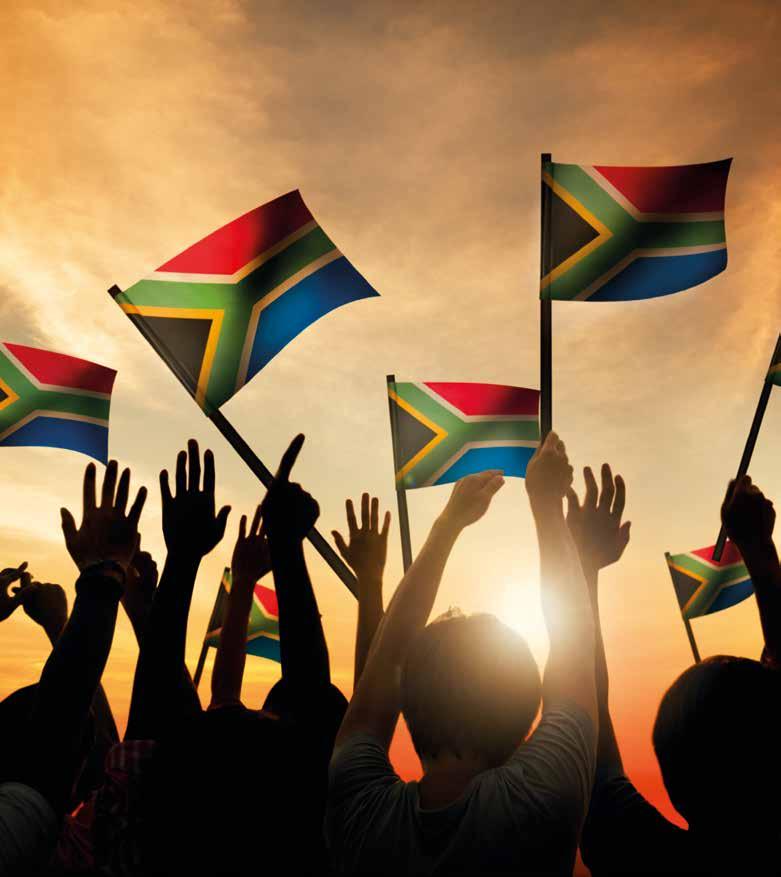
proven technologies long-lasting maximum performances high speed best paper quality energy saving flexibility customized and optimized design new generation software integrated end-of-line solutions
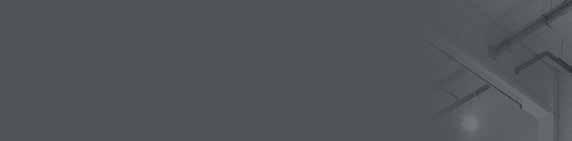
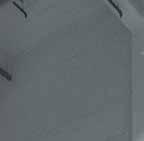
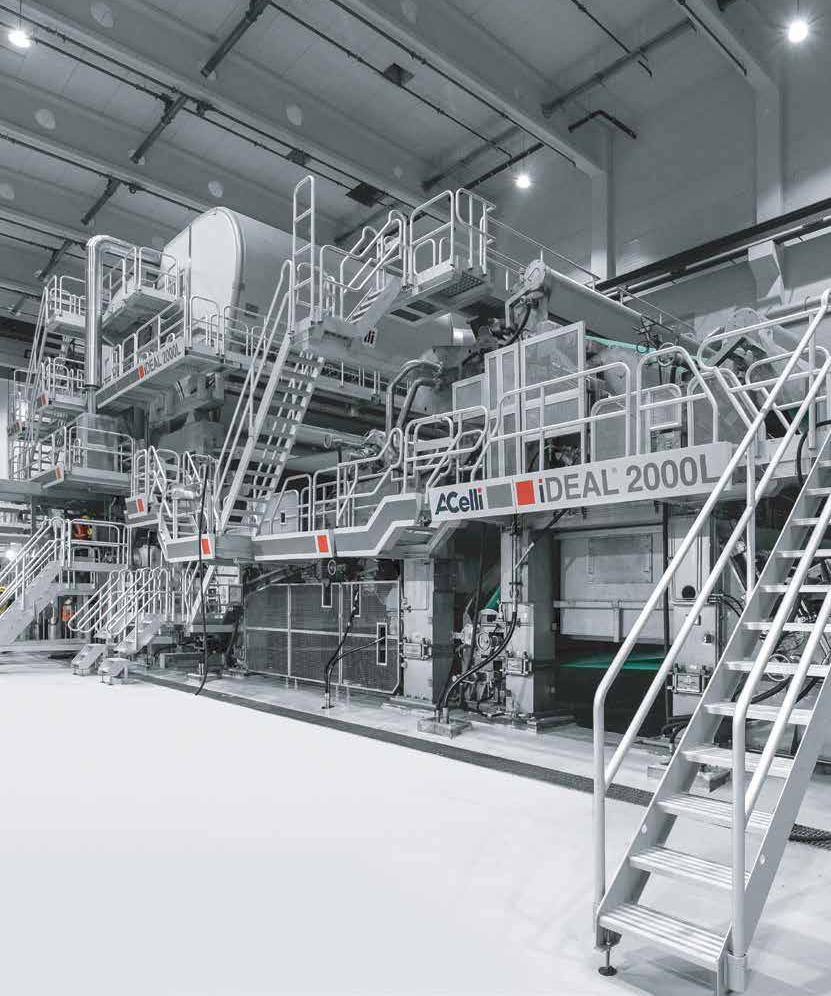
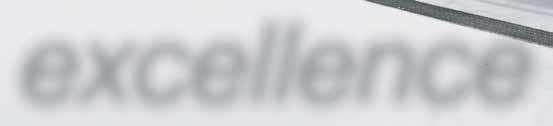

A.Celli has long-standin g, proven expertise in the construct ion of complete tissue plants Basic and detail engineering, electr cation and automat ion are performed by inter nal engineer teams to optimise the overall plant performances All activities are oriented to offer proven and granted solutions through extensive research and development activit ies that, since the foundat ion, have been of strate gic importance for the company