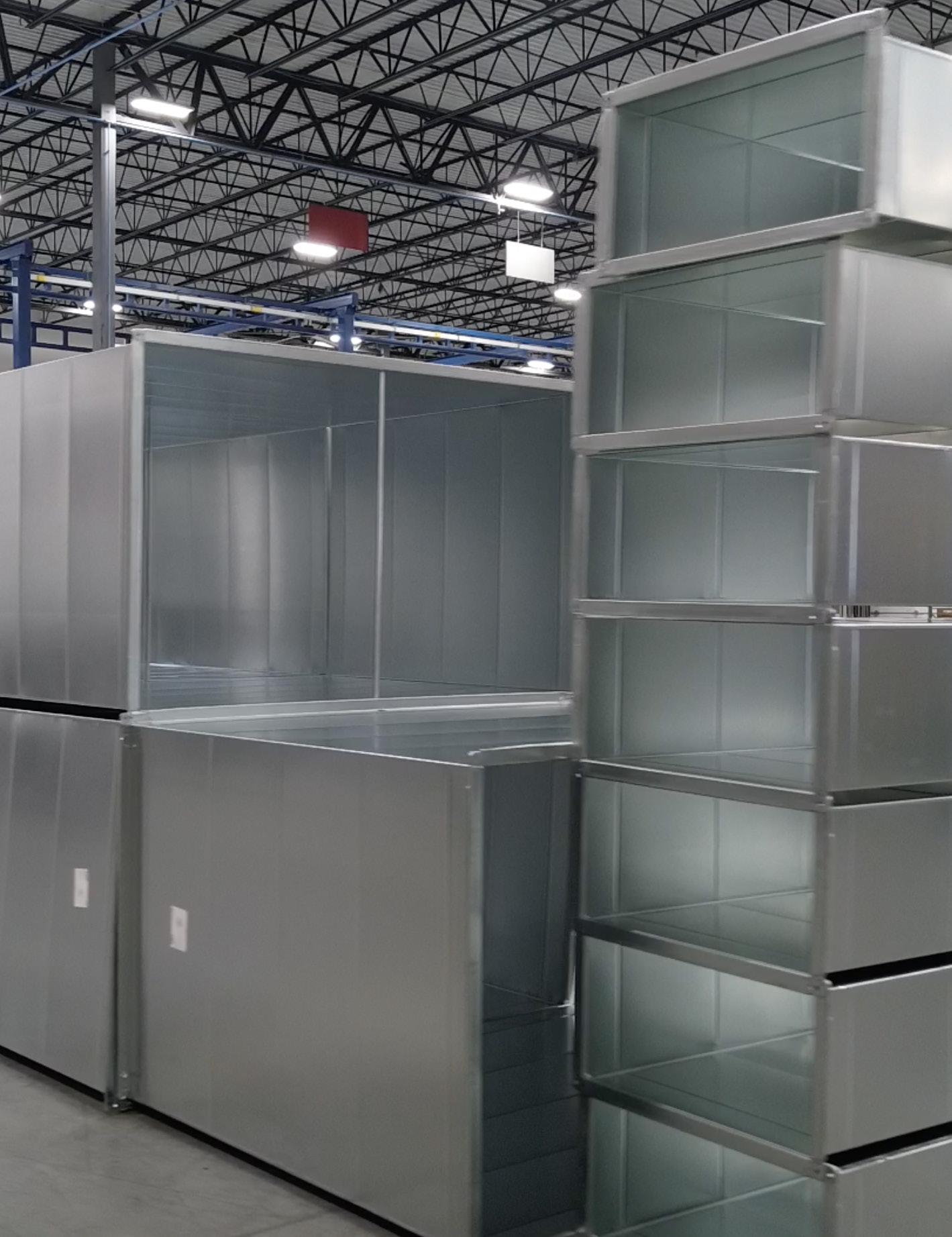






Mestek Machinery is pleased to provide you with the latest edition of our product catalog. On the following pages you’ll find the industry’s widest range of high-performance Heating, Ventilation and Air Conditioning (HVAC) machinery and equipment, built to a standard of quality that’s second to none. For your convenience we’ve listed as many details as possible about each piece of equipment including videos and other helpful links throughout. If you would like additional information, if you have any questions, or if you'd like a quote on any machinery, please don't hestitate to reach out — simply click on one of the question mark or calculator icons in the lower part of any page throughout the catalog.
Mestek Machinery is the industry-leading designer and manufacturer of the most complete, productive, and innovative metal forming solutions for the fabrication of HVAC sheet metal ductwork and fittings. Our family of brands — Lockformer, Iowa Precision, Engel, and Roto-Die — have decades of experience addressing every facet of the HVAC duct industry. The result is a combined knowledge and experience that develops cutting edge, precision technologies and automated manufacturing equipment that saves sheet metal contractors and fabricators time and labor while ensuring the highest-quality finished ducts and fittings.
Mestek Machinery offers you much more than the industry’s finest machinery and equipment – we also offer an unrivaled level of service and attention to detail AFTER the sale. When you partner with Mestek Machinery, we dedicate a broad range of experienced resources and expertise to you, making sure that you receive the maximum return on your investment.
Whether you have a maintenance request, want to upgrade your hardware or software, or just need a question answered, our experienced team of qualified professionals is always there to assist.
Should you need a spare part, we’ll get it to you quickly – even if you don’t know the serial number of the machine or part. What’s more, Mestek Machinery has a knowledgeable group of dealers around North America which means that you are assured of ongoing local support.
Invest in Mestek Machinery and see for yourself why we set the standard for product quality, performance, customer service and integrity – the standard against which every equipment manufacturer in the HVAC industry is judged.
Mestek Machinery is dedicated to keeping your operations running smoothly. No other company in the industry delivers the level of service and support that Mestek Machinery provides. Whether it’s a replacement part, troubleshooting an existing machine or process, operator training, or optimize your shop layout and workflow, our experienced team of engineers and technicians is here to help keep your operation running at peak performance.
Mestek Machinery is committed to supporting its customers with genuine OEM parts for all our machinery in order to keep your machinery and business operating. Learn More
Mestek Machinery can help streamline your shop workflows and activities by assisting your business with a professional shop layout review and design. Learn More
Mestek Machinery has the largest service network in the industry to support your sheet metal forming and fabricating needs. Keep your essential machinery and equipment running with help from Mestek Machinery. Learn More
Mestek Machinery offers many services to bring older equipment back to life to meet modern with services including rebuilds, retrofits, and reconditioning. Learn More
Mestek Machinery offers pre-owned, affordable equipment for sale that can be offered as-is, upgraded with new controls and tooling, or retrofitted with add-ons. Purchasing pre-owned Mestek Machinery equipment allows you to save money while acquiring the world’s leading sheet metal forming and fabrication machinery. Learn More
Mestek Machinery offers remote assistance and self-diagnostics services, modern digital tools that can improve the effectiveness of the equipment assembly and maintenance. Learn More
Trust the Mestek Machinery professionals to properly train and educate your staff in order to operate our machinery in a safe and efficient manner. Learn More
Mestek Machinery offers installation services with highly trained technicians that are able to install, relocate, and reinstall new and existing machines quickly, safely, and efficiently in order to get your business back up in running in a timely manner. Learn More
Mestek Machinery is committed to supporting its customers and offers the most comprehensive coverage and benefits to protect your machinery investments. Learn More
Mestek Machinery offers one of the best warranties available in the industry on the best sheet metal forming and fabrication equipment and machinery in the market. Learn More
Mestek Machinery can design, program, and build complete replacement control systems for your older Lockformer, Engel, or Iowa Precision equipment and coil lines. Each new control we supply is quality checked to meet rigorous standards. Rather than a complete machine tool re-build, a CNC control retrofit is just what the doctor ordered to get an older, well-maintained Vulcan®, Pro-Fabriduct®, or Compact II® system performing like new again. That older machine may be very capable mechanically for years to come, but aging electronics can make it impossible to keep that machine in top operating condition. A control retrofit can give new life to that valuable asset.
• HMI/PLC interface touch screen controller
• Plug and play control system
• Compact flash platform for hard drive (solid state)
• No moving parts: fans and hard drives continually running of systems
• No changes necessary for Vulcan® software or the interface
Contact Lockformer for more information
• Solid state components with industrial grade touch screen
• Intuitive user interface provides at-a-glance operational assessment
• Status messages prompt user for required information
• Graphical job processing flow information
• New operator manual and complete electrical drawings
• Designed to NFPA 79-Standards for industrial machinery
Contact Iowa Precision for more information
• Solid state components with industrial grade touch screen
• Intuitive user interface provides at-a-glance operational assessment
• Status messages prompt user for required information
• Graphical job processing flow information
• New operator manual and complete electrical drawings
• Designed to NFPA 79-Standards for industrial machinery Contact Engel for more information
Since 1938, Lockformer has been the most recognized name in the sheet metal machinery industry. Lockformer has led the world in the production of HVAC roll forming machinery (such as our Lockformer Pittsburgh Machines) and Vulcan cutting systems, plus the Transverse Duct Connector (TDC) roll former revolutionized the HVAC ductwork industry around the world. Lockformer sets the standard for product quality, performance, and service — the standard against which every other equipment manufacturer in the HVAC industry is judged.
The Vulcan® Fiber Laser is the next evolution in cutting systems from Lockformer. Using over 30 years of sheet metal cutting experience, we’ve designed the Lockformer® Vulcan® Fiber Laser Cutting System to meet the specific needs of sheet metal fabricators to help take your operation to the next level. Faster, more precise cutting, better quality parts, coil feeding capability, quicker access to cut parts (no enclosure) and many more features all designed to improve the productivity and profitability of your fittings operation while setting the standard for safety (accession number and coveted Class 1 safety rating from the Food and Drug Administration).
• Cut speed up to 1,200 inches per minute (28 m/min) on 24ga mild steel
• Cut speed on 10ga to 26ga mild steel up to 3X faster than a conventional plasma cutter
• Cut quality like that of a high definition plasma cutter on mild steel and stainless
• Uses less heat than plasma so edges are not hardened leading to less wear and tear on other machinery
• Standard 5’ x 10’ zoned exhaust cutting table with an option of 5’ x 20’ produces minimal exhaust — can be sheet fed or coil fed
• Exclusive patent-pending open architecture design (no enclosure) provides access to parts directly from the table, eliminating the need for a pallet shuttle system and allows for easy integration into existing workflows — FDA Accession Number and coveted Class 1 Safety Rating
• Patented shroud design further elevates its operational safety and cutting precision, ensuring high-quality results while mitigating hazardous risks
• Equipped with a Windows 10 ® Professional PC with 19” Monitor and Printer, the Fiber Laser can be integrated with most CAD to CAM software systems for maximum shop productivity and seamless connectivity with other machines throughout your operation
With 30 years sheet metal cutting experience, the Fiber Laser Cutting System is the next evolution in Vulcan® cutting systems
Exclusive patent-pending open architecture design (no enclosure) received an accession number and a coveted Class 1 safety rating from the Food and Drug Administration (FDA)
CNC Mach III and Color Graphic Mouse Driven Control 2D x 3D Tool Path & 3 Axis X1-X2,Y,Z
All rack and pinion 4-Axis (2-Y, 1-X, 1-Z) controlled Z is servo driven with automatic torch height control.
The fiber laser can be coil fed with the Iowa Precision Coil Feed Machine with with 60" or 48" coil stock with capacities from 14 gauge to 26 gauge.
The Lockformer Vulcan Fiber Laser Cutting System can be coil fed with 60" and 48" coil stock with maximum 26 gauge to 14 gauge. The Iowa Precision Coil Feed Machine is comprised of a drive motor and a series of rolls to feed and remove coil set from the material. The operator uses an on/off switch attached to an electrical cable to advance the material. This allows the operator to feed the material to the proper location along the fiber laser table. Drive is by way of entry and exit pinch rolls and straightening is accomplished with a fifth roll, which is located between the entry and exit rolls. This straightening roll is controlled by a hand wheel to vary the amount of flattening. Cut-off of the sheet length is standard and an optional shear cut-off system is also available. CLICK TO LEARN MORE
Cutting Unit
1.5kW& 2.okW fiber laser resonators available
Cutting Speed
Maximum cutting speed up to 1,200 inches per minute (28 m/min) with maximum positioning speed up to 1,400 inches per minute (35.56 m/ min)
Cutting Area / Table Capacitiy:
Standard: 5'x10' (1.5 m x 3.0 m)
Optional: 5'x20' (1.5 m x 6.0 m)
Cutting Capacity
10ga to 26ga Mild Steel based on Laser Resonator selected
Machine Control
Mach 3 & Color Graphic Industrial Touch Screen
Software / Computer System
MACH III Windows 10 Based Control System accepting of Autodesk CAM Mep, Trimble Fab Shop, Practi Cam, Shop Data Systems and others upon request.
Dimensions
Length: 168” (4270 mm)
Width: 96" (2438 mm)
Height: 63" (1600 mm)
Weight: 3,200 lbs. (1450 kg)
The Lockformer® Vulcan® 1600 Water Jet Cutting System automates the slow, costly, and inexact manual process of cutting insulation delivering an unrivaled level of quality and efficiency. The machine will cut fiberglass or foam insulation as well as gasket rubber and many other types of insulation products up to 4" thickness at a maximum positioning speed of 2,000 inches per minute. Whether you require precise insulation shapes for square to rounds, radius elbows or transitions, the Lockformer Vulcan Waterjet Cutting System can fabricate insulation fittings for about one-tenth of what it costs to buy them or one-tenth the time it takes to cut them by hand.
The Lockformer Vulcan Waterjet Cutting System can be integrated with the most CAD to CAM Software systems for maximum shop productivity and seamless connectivity with other machines throughout your operation. The software optimizes the cut pattern to maximize the pieces that can be cut from a single sheet of insulation — and, unlike a laser or plasma, the precision of the Water Jet can cut right to the edge of a previous cut for a zero scrap factor — that’s zero waste from part to part. The software also streamlines your fittings operation by matching the cut insulation to the corresponding metal blanks. And the precision quality of each cut is unmatched in the industry — from the simplest of shapes to the most complex, the Lockformer Water jet can handle them all.
The unsurpassed engineering excellence of Lockformer integrated with the operating software from QuickPen, a leading software supplier to the mechanical construction industry makes the Lockformer® Vulcan® 1600 Waterjet Cutting System the most complete solution in the industry.
Insulation can be more costly than sheet metal and cutting it manually is inefficient and wasteful. The Lockformer Vulcan 1600 Water Jet Cutting System can help you virtually elminate your scrap and increase your profitability. The operating software optimizes the cut pattern to maximize the pieces that can be cut from a single sheet of insulation. And unlike a laser or plasma, the precision of the Water Jet can cut right to the edge of a previous cut for a zero scrap factor — that’s zero waste from part to part. Your cut parts will fit perfectly into your metal blanks completely eliminating trim cuts and the re-fabrication which can bottleneck your operation — allowing you to work smarter and more efficiently.
The new trend in the HVAC industry is for specifying engineers to replace fiberglass duct liner with open or closed cell elastomeric foam. This foam insulation has no mold issues or potential to break down and get into the airstream. The Lockformer Vulcan 1600 Water Jet Cutting System will cut fiberglass or foam insulation as well as gasket rubber and many other types of insulation products up to 4" thickness at a maximum positioning speed of 2,000 inches per minute.
The Lockformer Vulcan 1600 Water Jet Cutting System can be integrated with the most CAD to CAM Software systems for maximum shop productivity and seamless connectivity with other machines throughout your operation. One software tool for all applications and all systems — PLC, drives, communications, operator interface, programming, and diagnostics — integrated with robust hardware made for the industry — no moving parts, no fans, no hard disks, plus a high ambient temperature specification.
Components made by the manufacturer, not outsourced. This control of components allows Lockformer to provide components for the long haul.
Central program storage to all components in the system and field replacements without programming for servo drives, HMIs, etc. Excellent drive diagnostic features — ACOPOS software oscilloscope.
CPUs have the highest performance in the PLC industry and the fastest hardware — PLCs, inverter, trigger inputs, etc. Complex functions are programmable in high-level languages. Scalable for quick development with saleable and compatible hardware. Software can easily be adapted to different hardware configurations and machine applications.
Note: Configurations vary based upon equipment and options selected
Overall:
• 60" x 120" effective cutting area
• 60" x 240" optional cutting table size
• Up to 3,000 IPM positioning speed depending on the material type and thickness
• Cutting Speeds up to 2,000 IPM with a safety standard of 1,200 IPM
• 4" maximum cutting thickness
• +/- 1/32" positional accuracy
• All Premium "plug-in" components
• Unitized, fixture-welded, 3" x 3" steel tubing framework for strength and stability
• Stand-alone control console
• All axis home positioning using motor torque measurement
• 8" x 8" steel table leg pads with leveling feature
Table:
• 1/4" steel plate perimeter
• “Gull Wing” table design to protect the machine’s drive system and reduce the footprint size
• Complete stainless steel table lining for rust-free performance longevity
• Rectangular exhaust plenum at the back end of the table for easy access connection
• Strategically located Emergency Stops [1 = controller; 1 = x-axis carriage]
Drive:
• Dual precision Y drive
• Double deck, 24 strand steel, precision reinforced radial timing belts
• HIWIN® linear x-axis bearing and way
• 3" diameter x 128" long, turned, ground snd polished, heavy duty Y-axis guidance rail — Armaloy surface coated
• Precision cam followers
• X-axis brush guard
• Steel enclosed housing for X-axis servo drive motor
• Y-axis drive house enclosed and integral to the machines frame
• SNC® brand - vertical dual cylinder pneumatic torch lifter with adjustable up/ down pressure
Machine Control:
• Lockformer 759 CNC-TS control system with 15" color graphic industrial touch screen with leveling feature
• Digital drive devices
• Manual speed increase/decrease override
• Kerf compensation
• Auto home sense to set 0/0 automatically
• Automatic corner slow down
• Brushless AC servo motors with resolver feedback
• Remove safety stop switches and current limiting devices for safety
The cutting power of the Lockformer® Vulcan® 1600 Water Jet Cutting System comes from the Steamline® SL-VI Waterjeft Intensifier from KMT.
System:
• Cutting power delivered via a horizontal whip that can be installed in most any fab shop, regardless of the height of the ceilings
• Pneumatic valve cutting head with .007 diamond office
• Intensifier cycles a maximum of 8 times per minute to reduce pressure fluctuations and improve component life
• Designed for non-abrasive pure water cutting only
• 55,000 PSI maximum continuous cutting pressure
• Maximum 3 GPM of water with 80 GPM inlet pressure
• Full amp load = 52A; Circuit Breaker = 80A
• Motor is totally enclosed & fan cooled
• Pump footprint is 59'L x 42"W x 41"H
• Machine CNC Control: 230 Volt, Single phase, 60 Hz (Dedicated circuit)
• High Pressure Water Pump: available in 208, 240, or 480 Volt, Three phases, 60 Hz
Water:
• Customer’s water supply may need to be softened or treated. Please refer to proposal for manufacturer minimum water quality
• 90 PSI low volume (less than 5 SCFM). The machine requires an Air Compressor to supply 99.997 percent dry compressed air at 5.0 SCFM @ 90 PSI. An Air Compressor is not included in the machine price. We recommend the purchase of the Air Filter and Dryer (option) to insure a clean, dry air supply for the water jet pump
The Lockformer® VulcanPlus® Plasma Cutting System is the industry benchmark in plasma cutting systems. Loaded with features for unmatched accuracy and precision, this system will perfectly cut 3/8"- 1/2" mild steel with a maximum positioning speed of 3,000 in/min — the fastest cutting, positioning, and traversing times in the industry. Faster, more precise cutting, better quality parts, coil feeding capability and many more features all designed to improve the productivity and profitability of your fittings operation.
• Maximum positioning speed of 3,000 in/min — the fastest cutting, positioning, and traversing times in the industry
• Premium “plug-in” components — virtually indestructable
• Fixture welded, 3" x 3" steel tubing framework — ensures the frame will be as perfectly aligned today as it will be years from now
• Three (3) servo motors, planetary gears, and single-shaft belt — the most accurate in the industry
• Equipped with a Windows 10 ® Professional PC with 15" Monitor and Printer, the VulcanPlus Plasma can be integrated with most CAD to CAM software systems for maximum shop productivity and seamless connectivity with other machines throughout your operation
CLICK TO SEE WHAT OUR CUSTOMERS HAD TO SAY ABOUT THE LOCKFORMER VULCANPLUS PLASMA CUTTING SYSTEM
• B&R Machine Controller built for demanding industrial duty applications
• Lockformer 759 CNC-TS control system with 15" color graphic industrial touch screen
• Windows 10 VS Control software architecture
• Digital drive devices
• Manual speed increase/ decrease override
• Kerf compensation
• All axis home positioning using motor torque measurement
• Auto home sense to set 0/0 automatically
• Automatic corner slow down
• Brushless AC servo motors with resolver feedback
• Remote safety stop switches and current limiting drives for safety
Table:
• Available in 10' and 20' table configurations to meet your operational needs
• 1⁄4" steel plate table perimeter
• 3" x 16 ga. CRS, multidirectional X or Y sheet support slats
• Slats can be configured for either “side-load” or “endload”of the table
• Exclusive Gull-Wing table design
• Rectangular exhaust plenum at the back end of the table for easy access connection
• 10" x 12" table exhaust ducting of 20 gauge galvanized TDC four bolt connector
• Strategically located Emergency Stops [1 = controller; 1 = x-axis carriage]
• 3 surface milled “L” bracket sheet stops
• 8" x 8" steel table leg pads with leveling feature
• Dual Y drive
• Double deck, 24 strand steel, precision reinforced radial timing belts
• HIWIN® linear x-axis bearing and way
• 3" diameter x 128" long, turned, ground & polished Y-axis guidance rail
• Precision cam followers
• Steel enclosed housing for X-axis servo drive motor
The Lockformer Vulcan Fiber Laser Cutting System can be coil fed with 60" and 48" coil stock with maximum 26 gauge to 14 gauge. The Iowa Precision Coil Feed Machine is comprised of a drive motor and a series of rolls to feed and remove coil set from the material. The operator uses an on/off switch attached to an electrical cable to advance the material. This allows the operator to feed the material to the proper location along the fiber laser table. Drive is by way of entry and exit pinch rolls and straightening is accomplished with a fifth roll, which is located between the entry and exit rolls. This straightening roll is controlled by a hand wheel to vary the amount of flattening. Cut-off of the sheet length is standard and an optional shear cut-off system is also available. CLICK TO LEARN MORE
Hypertherm® PowerMax45:
• 50% duty cycle at 65 amps with Hypertherm Powermax 65 Sync Technology
• Solid-state inverter power supply with output variable from 20 to 65 amps optimum performance on thickness from 28 gauge to 1/4" metal
• Conical Flow nozzle increases arc energy density for superior cut quality with little dross
• Patent Pending shield reduces dross buildup and enables smoother drag cutting for a better cut.
• Hypertherm-shielded nozzle design to increase consumable life
• Universal power supply at single phase 208 Volt and three phase 480 Volt
• CNC Interface and Fast Connect Torch Connection increases versatility
PowerMax65 available as an option
• Power-cool design cools internal components more effectively for greater system reliability and improved uptime
• Full 3 year power supply warranty and a 1-year torch warranty
• 3/8" Maximum cutting ability
Software & Computer Includes:
• Rectangular, drop cheek, square to round
• Round & oval complete
• Super & manual segmenting
• Automatic shape nesting and rotational nesting for minimum scrap
• Holes cutting in fittings / rounds / slot / square / oval
• 3D picture preview and flat pattern layout
• Rod reinforcing holes cut in fitting
• Insulating cutting software
• Vulcan Parts (special shape CAD program)
• Two user input station license
• Easily create and customize, color coded labels and reports
• Microsfot Windows 10 OS
• Two printers
The family of Lockformer® Vulcan® Cutting Systems has been the HVAC fabrication industry standard for plasma, laser, waterjet cutting solutions for over 30 years. Central to the machines’ ability to increase your shop’s productivity and profitability, is the integration of the equipment with the Vulcan FabShop Software.
Vulcan FabShop has set the bar for cutting software with its unique combination of innovation and powerful, intuitive technology. Easy-to-use input screens let your operators enter duct and fittings quickly and accurately. The comprehensive fitting library within Vulcan includes thousands of fittings of all shapes and sizes which can be used in projects ranging in size from residential projects to large industrial applications, while tools such as the automatic segmenting and shape nesting tools help to drive efficiency. Vulcan FabShop Software makes you work more productive whether you have five or fifty people in your shop.
Increase your shop’s productivity and profits with software that has been the industry standard for 30 years. Vulcan FabShop Software makes you work more productive whether you have five or fifty people in your shop. Fitting input is quick, simple, and non-repetitive. Create customized, color-coded labels and reports easily.
• Comprehensive Fitting Libraries
• Automatic Shape Nesting
• Customized Color Labels
• Accessories
• Automatic Segmenting
• Manual Segmenting
• Dampers
• Reinforcing
The CAD providers we are currently open in architecture with are:
• Autodesk Fabrication CADmep
• Trimble SysQue
• Trimble DuctDesigner 3D
• Trimble EC-CAD
• Bentley
• Orange Technologies CADPipe
• DrawTech
• SDS Shop Data Systems
• BuildCentric: a Webduct Systems, Inc. Company
• Practi Cad
Hardware and Software solutions are the ultimate answer for the HVAC contractor looking to tackle projects from residential to commercial while meeting tight deadlines and maintaining profitability on a project.
As an MEP Contractor, you have enough point solutions that do not talk to other solutions across your business. We understand your business and the MEP specific challenges you face. This appreciate and understanding drives our goal of connecting your design and fabrication processes for a seamless, 21st century business environment.
Spec-driven labor and material estimating software are ideal for HVAC and sheet metal estimators. Leverage pre-built assemblies, automatic fitting generation, and integration with CAD detailing solution, estimating software is a go-to solution for large and small sheet metal contractors alike.
For years, Vulcan has set the bar for cutting software with the best mix of innovation and usability. At the core of its success is the unique combination of powerful, intuitive technology. Easy-to-use input screens let your operators enter duct and fittings quickly and accurately. The comprehensive fitting library within Vulcan includes thousands of fittings of all shapes and sizes which can be used in projects ranging in size from residential projects to large industrial applications, while tools such as the automatic segmenting and shape nesting tools help to drive efficiency.
Extend the integration of Design and Fabrication to Installation with Field fitting input, providing contractors, fabricators and their installers a way to capture sheet metal fitting information in the field simply, seamlessly, and accurately.
Gain additional productivity with the optional Trimble Mobile Pro for iPad, the most efficient and easiest way to enter sheet metal fitting information in the field and transfer it to the office for import into your Vulcan Cutting System CAD | CAM | MEP Software. Whether you are looking to do a small residential or large commercial project, Trimble Mobile Pro covers you with a comprehensive fitting library for most any situation. Additionally, Trimble Mobile Pro provides your organization with 97% of the Vulcan Cutting System CAD | CAM | MEP Software library of fittings. Trimble Mobile Pro allows contractors to keep each project separate, and keep floor and drawing information separate within each project. Contractors are able to enter every dimension as well as the type of metal, gauge, insulation and liner thickness, and seam data. Reduce errors and rework while increasing productivity and return on investment.
The Pittsburgh lock revolutionized the HVAC industry in the late 1940’s and is still used today for its strength and ease in assembling ductwork. And for nearly that long, the Lockformer Pittsburgh Lock Roll Formers have set the standard for product quality and performance. Available in six (6) different configurations with varying capacities, configurations, and forming speeds to fit your specific operational needs, all Lockformer Pittsburgh Lock Roll Formers feature industrial motors, precision bearings, heavy 3/4" chassis plate, case-hardened and ground roll shafts, and arc-welded steel stands protected with Lockformer’s top-quality primer and paint finish.
The Lockformer Pittsburgh Lock Roll Former Model 24 features a 24-28 gauge capacity and has 5 forming stations and 1 inboard forming position. With a forming speed of 30-35 ft/min, this machine is compact, lightweight, and can easily be taken to the job site!
CAPACITY
• 24–28 gauge
DEPTH OF POCKET / SIZE
• 5/16”
• Uses approximately 1” of material
OTHER
• Width of hammer-over edge adjustable up to 3/8”
FORMING STATIONS
• 5 forming stations and 1 inboard forming position
SPEED
• 30–35 ft/min
MOTOR / VOLTAGE
• 1/3 hp, 115/230 volts, 60 cycle, single phase, A.C. 1,800 RPM.
• Other motors available upon request
DIMENSIONS / WEIGHT
• Length - 30”
• Width - 13.5”
• Height - 20”
• Weight - 175lbs.
The Lockformer Pittsburgh Lock Roll Former Model 20 and Model 20 Super Speed have 5 forming stations with 2 forming positions. One inboard forming position forms the Pittsburgh lock and one auxiliary or outboard forming position has the capability of forming 1 of 3 different profiles. While the Model 20 features a forming speed of 25 ft/min, the Model 20 Super Speed delivers 75 ft/min.
• 24–28 gauge
CAPACITY DEPTH OF POCKET / SIZE
• 1/2"
• Uses approximately 1-3/8" of material
MOTOR / VOLTAGE
• 1/3 hp, 115/230 volts, 60 cycle, single phase, A.C. 1,800 RPM.
• Other motors available upon request
DIMENSIONS / WEIGHT
MODEL 20:
• Length - 36"
• Width - 16.5"
• 5 forming stations and 1 inboard forming position
SPEED
MODEL 20:
• 25 ft/min
MODEL 20 SUPER SPEED:
• 75 ft/min
OTHER FORMING STATIONS
• Width of hammer-over edge adjustable up to 3/8"
• Height - 41"
• Passline - 32"
• Weight - 450lbs.
MODEL 20 SUPER SPEED:
• Length - 48"
• Width - 24"
• Height - 42"
• Passline - 34"
• Weight - 450lbs.
Available as an optional component for both the Model 20 and Model 24 Lockformer Pittsburgh Lock Roll Formers, this flanging attachment will automatically follow any edge – straight, inner, or outer radii — while forming a 7/32 (outside) flange height. No change over is necessary between Pittsburgh Lock and flanging operations… just turn up a starting flange in the table slot, feed materials into the rolls and let go. Handles radii down to 3-1/4" or 1-3/8" manually at speeds of 16-18 ft/min.
Auxiliary Rolls
Flange
• Auto-Guide/Power Flanging Attachment (Model 24 and Model 20 only)
• Option for Model 24 Pittsburgh Stand
• Option for Model 20 Only, 3-phase control
• Option for Model 20 Super Speed Only, 230/1/60 control
Lockformer Pittsburgh Lock Roll Former Models 14, 16, and 18 have seven forming stations with two forming positions. One inboard position forms the Pittsburgh lock; and one auxiliary or outboard position has the capability of forming 1 of 8 different profiles depending on which auxiliary roll set is ordered.
CAPACITY
MODEL 14
• 14–16 gauge
MODEL 16
• 16–20 gauge
MODEL 18
• 18–22 gauge
DEPTH OF POCKET / SIZE
• 5/16”
• Uses approximately 1” of material
SPEED
MODEL 14:
• 35 ft/min
MODEL 16:
• 40-45 ft/min
MODEL 18:
• 40-45 ft/min
FORMING STATIONS
• 5 forming stations and 1 inboard forming position
OTHER
• Width of hammer-over edge adjustable up to 3/8”
MODEL 14:
• 5 hp, 230/460 volts, 60 cycle, 3 phase, A.C. 1,800 RPM.
MODEL 16:
• 3 hp, 230/460 volts, 60 cycle, 3 phase, A.C. 3,600 RPM.
MODEL 18:
• 2 hp, 230/460 volts, 60 cycle, 3 phase, A.C. 1,800 RPM.
• Other motors available upon request
• Length - 58.5”
• Width - 24”
• Height - 41”
• Passline - 34”
• Weight - 750lbs.
Special 2-in-1 Rolls & 2-Step Gauge
• 3-in-1 Perforating—Notching Arrangement
• 2-in-1 Perforating—Notching Arrangement
• Complete set of Drive Cleat rolls and Slitting-Cutting device
• Slitting-Cutting device only with conversion parts for existing Drive Cleat rolls
• Option for single-phase wiring
With Lockformer Transverse Duct Connector (TDC) Roll Formers, you can roll form your own seal-able flanges on transverse duct joints during the fabrication process for both fittings and straight duct applications
Introduced in 1982, the original Lockformer TDC Roll Former produces flange on the machine’s left-hand side auxiliary. The work horse in the industry for over 40 years, it continues to be the only transverse duct connector machine on the market that produces rollformed flanges certified to have passed all the functional criteria tests from 1/2" W.G. to 10" W.G. to comply with SMACNA Duct Construction Standard (DCS) T-25a. Today the Lockformer TDC T25A Roll Former is available in the original standard configuration with a capacity of 1826ga steel at a speed 60 ft/min and our latest model which has a capacity of 1626ga steel at a speed of 70 ft/min with optional inboard and outboard roll sets.
CLICK TO TO SEE THE LOCKFORMER TRANSVERSE
DUCT CONNECTOR ROLL
FORMER IN AN OPTIMIZED SQUARE FITTINGS FABRICATION
SHOP FLOOR LAYOUT
The revolutionary Lockformer Spiral Tube Formers combine the most advanced technology with one of the smallest footprints in the industry. Unlike other compact models, the Lockformer Spiral Tube Formers will not sacrifice speed, power, or technology, and are the most affordable in their class with unsurpassed features and reliability make them the best value.
The only compact units in the industry that are fully automatic, Lockformer Spiral Tube Formers produce pipe from 3" to 100" in diameter from 14 to 28 gauge steel at speeds of up to 344 ft/min. Our user-friendly Spiral Smart Technology™ control system takes the guesswork out of machine setup for proper operation — operators simply choose the diameter, tube length, and length on the easy-to use touch screen. The system can also be integrated with the most 3rd party CAD to CAM Software for maximum shop productivity and seamless connectivity with other machines throughout your operation.
All Lockformer Spiral Tube Formers feature a flying slitting device for silent and precise cutting of tubes 4″ diameter with a maximum material thickness of 16 gauge without burs and sparks as well as a 10’ standard run-off table and either vertical or horizontal pallet decoiler.
Included features of all Lockformer Spiral Tube Formers
• Self-diagnostics and digital length control
• Spiral Smart Technology™, userfriendly control system takes the guess work out of set-up and pressure settings for proper operation.
• On-the-fly slitting device for silent cutting tubes of 4" diameter and maximum material thickness of 20 gauge
• Unbeatable customer service offering technical support and parts
• Only compact unit in the industry that is fully automatic
• Ergonomically friendly to the operator
• 10' standard run-off table
• Vertical or horizontal pallet decolier
• Mestek Key Performance Indicator Technology
• Smart Sense Control Software
Lockformer Spiral Tube Formers are available in two models to meet your operational needs:
• Model 1.2: Our most popular model produces spiral pipe up to 18 gauge (1.25 mm) thickness with a maximum speed of 241 ft/min (87 m/min)
• Model 2.0: Our workhorse model offers both high speed and heavy gauge capacities producing spiral pipe from 28–14 gauge (0.50–2.0 mm) thickness with maximum speeds of 287–375 ft/min (84-114 m/min) depending on gauge.
Specifications:
MODEL 1.2
CAPACITY
• 28–18 gauge galvanized steel
• 28–22 gauge stainless steel
DIAMETER RANGE
• 3"–64" (80–1600mm)
MAX STRIP SPEED (GALV. STEEL)
• 241 ft/min
MOTOR / VOLTAGE
• 230V or 460V/3ph/60Hz Special voltage available
DIMENSIONS / WEIGHT
• Length - 72"
• Width - 68"
• Height - 62"
• Weight - 3,000 lbs.
MODEL 1.2
MODEL 2.0
• 28–14 gauge mild steel
• 3"–100" (80–2500mm)
• 287–375 ft/min
• 460V/3Ph/60Hz Special voltage available
• Length - 72"
• Width - 78"
• Height - 62"
• Weight - 3,200 lbs.
MODEL 2.0
Lockformer Spiral Tube Formers are available with either a vertical or horizontal pallet decoiler. The horizontal pallet decoiler design allows a quick change over time and serves to cope with thick material. This unique decoiler holds a maximum of 3 coils at 2,200 lbs. each with speeds up to 328 ft/min and performs perfectly in line with the Spiral Tube Former at maximum speed on any duct size.
The new QuickStitch 2.0 Rotary Stitch Welder from Lockformer® was desgined to meet the needs of today’s duct fitting fabrication. The QuickStitch 2.0 optimizes your welding production output by giving the operator a controlled and consistent longitudinal weld from end to end with a minimal overlap. With a new operator-friendly touch-screen control panel wth a memory feature for ease of production, the operator can choose from a continuous or stitch weld that provides an excellent solution for welding of both galvanized and stainless steel straight tubes and round fittings. A manual welding pressure system is also included for welds and changeovers. The system also features digital temperature switches for chiller temperature and water flow adjustments. The QuickStitch 2.0 produces air-tight weld seams with an adjustable weld speed from 3 ft/ min to 49 ft/min for maximum productivity and efficiency. The QuickStitch 2.0 is available in three (3) models to meet your operational needs allowing you to create longitudinal seams of 2" - 40", 2" - 50", or 2" - 60" respectively.
Specifications:
MODEL 40"
MODEL 50"
GALVANIZED STEEL MATERIAL THICKNESS RANGE
• 30 gauge to 18 gauge (0.012" to 0.048")
• 30 gauge to 18 gauge (0.012" to 0.048")
STAINLESS STEEL MATERIAL THICKNESS RANGE
• 30 gauge to 22 gauge (0.012" to 0.032")
DIAMETER RANGE
• 3" to 40"
• 30 gauge to 22 gauge (0.012" to 0.032")
• 3" to 40"
LONGITUDINAL SEAM LENGTH
• 2" to 40"
• 2" to 50"
STANDARD OVERLAPPING (Special on Request)
• 0.236" (1/4" nominal)
POWER | STITCHWELDER
• 460VAC, 3PH, 60Hz, 125A
POWER | CHILLER
• 120VAC, 1PH, 60Hz, 10A
COPPER WIRE
• 0.078" round (optional 0.070" round)
• 0.315" (5/16" nominal)
• 460VAC, 3PH, 60Hz, 125A
MODEL 60"
• 3 ft/min to 49 ft/min
WELD SPEED DIMENSIONS / WEIGHT
• Length: 115"
• Width: 45"
• Height: 69"
• Machine Weight: 1,323 lbs.
• Copper Wire Coil Weight: 44 lbs
• 120VAC, 1PH, 60Hz, 10A
• 0.078" round (optional 0.070" round)
• 3 ft/min to 49 ft/min
• Length: 115"
• Width: 45"
• Height: 69"
• Machine Weight: 1,356 lbs.
• Copper Wire Coil Weight: 44 lbs
• 30 gauge to 18 gauge (0.012" to 0.048")
• 30 gauge to 22 gauge (0.012" to 0.032")
• 3" to 40"
• 2" to 60"
• 0.315" (5/16" nominal)
• 460VAC, 3PH, 60Hz, 125A
• 120VAC, 1PH, 60Hz, 10A
• 0.078" round (optional 0.070" round)
• 3 ft/min to 49 ft/min
• Length: 115"
• Width: 45"
• Height: 69"
• Machine Weight: 1,389 lbs.
• Copper Wire Coil Weight: 44 lbs
Lockformer’s Dual Head Gore-Locker is your quality, efficient and costeffective solution to the production of elbows, reducers, end caps and offsets. Lockformer’s operator friendly Dual Head Gore-Locker provides the power to fabricate quality standing seam fittings in-house. On a single machine platform, the Dual Head Gore-Locker offers the ability to flange/ swage on one end, while simultaneously closing the seam at the other end. The Dual Head Gore-Locker allows operators to modify controls when flanging/ swaging, providing complete control of production speeds. After closing on the second station and creating a standing seam, the Dual Head Gore-Locker delivers an airtight seal, eliminating the need for sealing or painting. Using minimal power and floor space, the Dual Head Gore-Locker handles a variety of materials and thicknesses – up to 16 gauge (1.5mm) – to produce standing rib diameters from 4"–60"(100–1500mm) with included tooling and can produce standing rib diameters from 4" and 50"–60" with additional tooling.
Offset Fitting End Caps Galvanized Steel Elbow Reducer
CAPACITY
• 16 gauge
DIAMETER RANGE
• Included Tooling: 4"–60"
• Additional Tooling required for 4" and 52"–60"
MOTOR / VOLTAGE
• 460V/3ph/60Hz
DIMENSIONS / WEIGHT
• Length - 106"
• Width - 32"
• Height - 44"
• Weight - 2,310 lbs.
The Lockformer® Flanger 2.7 produces either straight angle or flared angle round and oval flanges for a variety of applications including ring connectors for HVAC spiral duct. The machine takes angled stock of up to 12 gauge material to create single-wall, double-wall, and oval spiral ring connectors from 8" to 100" in diameter for standard 90˚ flange.
The Lockformer Flanger 2.7 also features operator-friendly touch screen PLC controls for easy operation and the ability to save and recall round and oval parameters for fast and easy production of duplicate parts.
While the Lockformer Flanger 2.7 can accept angled stock from a press brake, its impact on shop productivity comes when it’s used in conjunction with the Lockformer Angler 1.6 — which produces 90˚ angled stock from coil stock up to 16-gauge for the production flat oval and round flanges. The combination of the Lockformer Angler 1.6 and Flanger 2.7 truly maximizes shop productivity when producing spiral ring connectors.
Specifications:
• Up to 12 gauge (consult factory —exact capabilities vary depending on material and thickness)
DIAMETER RANGE
• 8" - 100" for standard 90˚ flange
AIR CONSUMPTION
• 1 CFM @ 100 PSI
• 13 HP (2 motors) | 460V/3 PH/60 HZ
• Length - 74"
• Width - 40"
• Height - 81"
The Lockformer® Angler 1.6 produces 90˚ angled stock from coil stock up to 16-gauge for the production of flat oval and round flanges. The machine will bend coil stock with a raw edge on one side and a transverse duct connector (TDC) bend or hem on the opposite edge for safety — 1", 1-1/2", or 2" for single or double wall production. But the key advantage of the Angler 1.6 is its ability to punch pilot holes for screws and cut the angled stock to a desired length. Unlike a press brake which can only produce 10 ft. sections for a maximum 30-inch diameter ring, the Angler allows you to produce precisely the angled stock you need for any diameter rings — even larger than 30-inch round — without a secondary cutting or punching operation. The Lockformer Angler 1.6 also features operator-friendly touch screen PLC controls for easy operation.
The impact of the Lockformer Angler 1.6 on shop productivity is maximized when used in tandem with the Lockformer Flanger 2.7. The Lockformer Flanger 2.7 takes the angled stock produced by the Angler 1.6 and forms either straight angle or flared angle round and oval flanges for the production of single-wall, double-wall, and oval spiral ring connectors from 8" to 100" in diameter for standard 90˚ flange. The combination of the Lockformer Angler 1.6 and Flanger 2.7 truly maximizes shop productivity when producing spiral ring connectors.
Specifications:
• Up to 16 gauge
LENGTH
• 20" - 200"
AIR CONSUMPTION
• 5 CFM @ 100 PSI
• 7.5 HP | 460V/3 PH/60 HZ
MOTOR / VOLTAGE DIMENSIONS / WEIGHT
• Length - 99"
• Width - 42"
• Height - 47"
The Lockformer® Button Punch Cheek Bender machine provides any shop with a complete work center for fabricating fittings from 20 gauge or lighter metal. One side of the dual purpose bending die bends and punches the cheeks for button punch snap lock 90-degree fittings. Flip the die over and you have a 20 gauge power cheek bender for making right-angle flanges for Pittsburgh fittings. Features a self-contained hydraulic system.
CAPACITY
• 20 gauge or lighter
HEIGHT OF RIGHT ANGLE MALE FLANGE
• 1/4" or 3/8"
• Self-contained hydraulic system
• 1-1/2 HP, 115/230 volts, 60 cycle, single phase, A.C. 1,800 RPM
OTHER MOTOR / VOLTAGE DIMENSIONS / WEIGHT
• Length - 24"
• Width - 28"
• Passline - 34"
• Weight - 200 lbs.
The Lockformer® Manual Cheek Bender is a two-way trunnion that keeps the bending bar in position at the starting point to assure perfect bends throughout the entire length. Mounting bolts are included. 20 gauge maximum with a 1/4″ – 3/8″ male right angle flange height for Pittsburgh seams on square duct fittings and a max bend length of 293/4″. The double-sided operation allows for bend angles 1° to true 90°.
CAPACITY
• 20 gauge or lighter
RIGHT ANGLE MALE
PITTSBURGH BEND HEIGHT
• 1/4"–3/8"
MAXIMUM BEND LENGTH
• 29-3/4"
• Double-sided operation
• Bend angles 1˚to true 90˚
OTHER DIMENSIONS / WEIGHT
• Length - 34"
• Width - 8-1/2"
• Height - 4"
• Weight - 95 lbs.
The Lockformer® Model 1836 Cleat Benders are designed for high speed folding or bending of drive cleat edges, standing seams, hems, drip edges s-cleats or right angles. With a capacity of 18 gauge or lighter, these presses are available in various configurations to suit your needs.
1836-0
18 gauge and lighter
Cleat bender only. Fixed back gauge, preset at 7/16" or 1/2" with a bend angle preset at 180˚
1836-1 18 gauge and lighter
One (1) position back gauge, preset at 1" or 5/8" or 7/16" with 3 bend angles preset at 180˚, 90˚, and 45˚ (other settings available)
1836-2
18 gauge and lighter
1836-3
18 gauge and lighter
Two (2) position back gauge, preset at 1" and 5/8" or 7/16" with 3 bend angles preset at 180˚, 90˚, and 45˚ (other settings available)
Three (3) position back gauge, preset at 1", 5/8", and 7/16" with 3 bend angles preset at 180˚, 90˚, and 45˚ (other settings available)
The all new Ovalizer 2.0 from Lockformer is the latest advancement in spiral pipe-forming technology. The Ovalizer 2.0 features a 10' boom which can produce pipe up to 20' lengths, as well as tooling with a Minor axis ranging from 6" to 36" to produce pipe with a Major axis ranging from 18" up to an impressive 96". The Ovalizer 2.0 uses the latest technology in combination with a wedge style boom to make stretching oval duct easy, reliable and repeatable — resulting in a more efficient production process for your operation.
The Ovalizer 2.0 offers a full touch screen programmable logic controller (PLC) giving the operator the ability to save and recall parameters for fast, easy, and automatic set-up for production of duplicate parts. The PLC also features a restretch function that allows the operator to measure a finished part and simply input a dimension on the screen to automatically re-stretch the part if required.
• 18 gauge
DIAMETER RANGE
• 6" to 36" Minor Axis
• 18" to 96" Major Axis
MATERIALS
• Galvanized Steel Stainless Steel
• Mild Paint-Grip Coated Steel Aluminum
LENGTH
• Up to 20'
MOTOR / VOLTAGE
• 25 HP (32 Full Load Amps @ 460/3/60)
• 460/3/60 Standard (Others available upon request)
DIMENSIONS / WEIGHT
• Length - 230"
• Width - 48"
• Height - 70"
The Lockformer® Pneuma-Wrap Pneumatic Brake Press is the ideal machine for forming L, flat, wrap, transverse duct connector (TDC), transverse duct flange (TDF), and slip & drive duct. The tooling has been redesigned to accept any size duct from 7” up to standard 60” without adjustment and the beam has also been redesigned to clear pins on lined duct. With rugged, welded steel construction and maintenance-free bearings and guides, the Pneuma-Wrap Brake also features pneumatic drives for clamping and folding beams with automatic returns as well as pneumatic operated pedal control, dial-adjustable bend angle 0 to 90˚, automatic transverse duct connector (TDC) or transverse duct flange (TDF) notch locator, front-adjustable support apron, and safety interlock controls.
DEPTH OF POCKET
• Pneumatic drive or the clamping beam with pneumatic return
AIR CONSUMPTION
• 11 CFM @100 PSI
DIMENSIONS / WEIGHT
• Length - 58-1/2"
• Width - 24"
• Height - 41"
• Weight - 3,500 lbs.
CLICK TO TO SEE THE LOCKFORMER BUTTON PUNCH SNAP LOCK SEAM ROLL FORMER IN AN OPTIMIZED SQUARE FITTINGS FABRICATION SHOP FLOOR LAYOUT
The Button Punch Snap Lock Machine forms a two piece seam that greatly simplifies ductwork assembly. The male seam is a button, the female seam is a lock and the two snap together for a flush corner. These machines can form 20 to 26 gauge sheet metal into female locks on one side and button punched right angle flanges on the opposite side at speeds of 60-65 ft/min and are available in seven and nine forming station machines. Not only do these locks assemble twice as fast as traditional methods but, because the two pieces nest, they are easier to transport too.
Standard with Lockformer quality construction, these machines have industrial motors, high precision needle-type bearings, heavy 3/4" chassis plate, case-hardened and ground roll shafts, and arc-welded steel stands protected with Lockformer’s top-quality primer and paint finish. Alternate fittings are easily accessible from a main transmission bearing lubrication panel.
CAPACITY
• 20–26 gauge
DEPTH OF POCKET / SIZE
• Uses approximately 1-3/4" material
PROFILE
SPEED MOTOR / VOLTAGE
• 60 - 65 feet per minute
• 3 HP, 230/460 volts, 60 cycle, 3 phase, A.C. 3,600 RPM.
• Other motors available upon request.
DIMENSIONS / WEIGHT
• Length - 58.5"
• Width - 24"
• Height - 41"
• Passline - 34"
• Weight - 725 lbs.
Auxiliary Rolls
5/16" Pittsburgh Rolls
Seam Rolls (Type“L”)
The flexible Lockformer Triplex Cleat Former is designed for super high productivity of inboard cleats. The triplex design has two (2) inboard and two (2) outboard forming positions allowing bearing support on both sides of the profile. The top plate and roll assembly are split into three zones with each having special design details like knurled rolls and angled guides to keep material moving through the machine in a straight line.
With nine (9) forming stations, the Triplex Cleat Former can form multiple gauge sheet metal into “S” and drive cleats on the inboard forming positions and up to twelve (12) auxiliary roll set profiles on the outboard forming positions at speeds averaging 100 ft/min.
Standard with Lockformer quality construction, this machine has a 5 hp industrial motor; high precision needle-type bearings; heavy 3/4" chassis plate; case-hardened and ground roll shafts; and an arc-welded steel stand protected with Lockformer’s top-quality primer and paint finish.
CAPACITY
• 22–28 gauge for “S” cleat profile and 20–26 gauge for drive cleat profile
DEPTH OF POCKET / SIZE
• “S” cleat width 1-1/16" Drive cleat width 1-1/8"
• Extended shafts for mounting auxiliary rolls
DIMENSIONS / WEIGHT
• Length - 60"
• Width - 24"
• Height - 40"
• Passline - 32-1/2"
• Weight - 850lbs.
SPEED PROFILE
• 100 feet per minute
MOTOR / VOLTAGE
• 5 HP
• 230/460 volts, 60 cycle, 3 phase, A.C. 1,800 RPM.
• Option for 230 volt, single-phase wiring
Drive cleat rolls inboard 20–26 gauge
“S” cleat inboard 22–28 gauge
• Combination “S” and Drive Cleat Cutter Attachment
• 3-in-1 Perforating — Notching Arrangement
• Optional 20 gauge male and female Snap-Lock Rolls
• Optional 20 gauge female Pittsburgh Rolls
• Optional Right Angle Flange Rollsets
AUXILIARY OPTIONS Lockformer Triplex Cleat
“S” Cleat inboard profile Drive cleat roll profile
“S” and drive cleat scrap cutter attachment
Plate housing
Form Roll Configuration
Special 2-in-1 Rolls & 2-Step Gauge
Snaplock with Button Punch Rolls Male/Female
Beading is a cost-conscious way to stiffen ductwork. It is 5 times faster than the old method, cross-braking, and uses only one operator. Designed to meet the requirements of SMACNA, the Lockformer 6016 Beader produces 5 beads on 12" centers and is adjustable to 3/16" depth. A convenient hand-wheel raises or lowers the top roll assembly to set depth of bead. The top and bottom rollers are kept parallel with adjustable screw and pillow block assemblies connected by a link chain. Individual adjustable screw and pillow block assemblies connected by a link chain. Individual collared beading rolls are replaceable. Feed rolls are self-compensating over the entire gauge range. Double entrance feed bars are provided so that material can be gauged from either left or right side.
With Lockformer quality construction, this machine has an industrial electric motor; precision bearings; turned, ground, and polished steel forming rolls and roll shafts; and an arc-welded steel stand protected with Lockformer’s topquality primer and paint finish. Lubrication fittings are located on each bearing.
CAPACITY
• 16–30 gauge
• 3/4 HP
SPEED MOTOR / VOLTAGE DIMENSIONS / WEIGHT
• 115/230 volts, 60 cycle, single phase, A.C. 1,800 RPM
• Max Width - 5'
• Weight - 1,650 lbs.
In just one pass, form a shape that combines a conventional “S” cleat with a standing seam for greater strength and rigidity. This seam is adaptable in fabrication of large trunk or branch lines in industrial and commercial heating and ventilating ducts. Included are doubleextended auxiliary shafts for a variety of choices for optional rollform tooling. The design integrity and quality construction of its 10-station configuration will provide years of trouble-free service.
CAPACITY
• 20–26 gauge
DEPTH OF POCKET / SIZE
• 1-1/8" pocket
• Uses approximately 6-1/4" material stretch out inboard
SPEED
• 60–70 ft/min
MOTOR / VOLTAGE
• 5 HP
• 230/460 volts, 60 cycle, 3 phase, A.C. 1,800 RPM
DIMENSIONS / WEIGHT
• Length - 84"
• Width - 30"
• Height - 37"
• Passline - 33"
• Weight - 1,700 lbs.
Combination
Effortlessly roll single-direction curves to a minimum radius of 3-1/2" on the inside or 5" on the outside, with minimal manual adjustment, providing significant time savings and enhancing the overall efficiency of your fabrication process. These precisely punched, right-angle flanged curves are engineered for maximum precision, ensuring a perfect fit into the receiver formed on both the Lockformer 20 gauge and 24 gauge Button Punch Snap Lock systems. This seamless integration eliminates the need for additional modifications, streamlining the workflow and reducing the likelihood of errors. With their high-quality construction and exacting standards, these curves are designed to maintain durability and consistency throughout the duct fabrication process.
CAPACITY
• 20 gauge maximum
• Working range 20–28 gauge
RIGHT ANGLE FLANGE HEIGHT
• 5/16" or 7/16"
SPEED
• 18 feet per minute
MOTOR / VOLTAGE
• 3/4 hp, 115/230 volts, 60 cycle, single phase, A.C. 1,800 RPM
DIMENSIONS / WEIGHT
• Length - 24"
• Width - 24"
• Height - 34"
• Weight - 250 lbs.
The Lockformer Auto-Guide Flanging Machine | Model 16 automatically follows any edge – curved or straight — and uses the convenient table slot to automatically turn up a right angle flange. A calibrated dial can be set for radii as small as 3-1/4" (or 2" when auto-guide is deactivated). Automatically flange 16 to 26 gauge material at speeds of 18 fpm. A non-releasing type head is suitable for open-end fittings, straight and irregular curves. Standard with Lockformer quality construction, this machine has an industrial electric motor, and an arc-welded steel stand protected with Lockformer’s top-quality primer and paint finish.
CAPACITY
• 16 gauge maximum
• Working range 16–24 gauge
RIGHT ANGLE FLANGE MALE
• 3/8" or 1/4"
• 18 feet per minute
LEG HEIGHT SPEED MOTOR / VOLTAGE DIMENSIONS / WEIGHT
• 3/4 hp, 115/230 volts, 60 cycle, single phase, A.C. 1,800 RPM
• Length - 24"
• Width - 24"
• Height - 34"
• Weight - 225 lbs.
The Lockformer® Roto Notcher Notching Machine is designed for highefficiency metal fabrication, allowing you to effortlessly create precise dovetail notches in 24 to 30 gauge galvanized steel with just a single pass. Whether you’re working with pre-cut sheets or utilizing scrap material, this machine provides a fast, reliable solution for your notching needs. Simply cut your metal blanks to the desired width and length, or use scrap material, and adjust the machine to accommodate either 3" or 6" width blanks. The intuitive design and straightforward adjustment process make the Roto Notcher a must-have tool for improving productivity and ensuring consistent, high-quality results on every job.
CAPACITY
• 24–30 gauge
SPEED
• 30 feet per minute
MOTOR / VOLTAGE
• 3/4 HP
• 115 volt, single phase
• Drive - V-belt
DIMENSIONS / WEIGHT
• Length - 20"
• Width - 23"
• Height - 36"
• Weight - 300 lbs.
Save time and money by combining notching, beading, crimping, and rolling into a single operation with the Lockformer® Collar Maker. This efficient machine performs all four tasks in one go, streamlining your workflow and reducing the need for multiple machines.
Ideal for creating complete round starting collars from 3" to 14" in diameter out of 24–30 gauge galvanized steel, the Collar Maker handles everything in just one pass. Simply cut material to width and length, or use scrap—this machine works with 3" or 6" wide blanks. Adjusting the crimp roll is quick and easy, ensuring fast setup and minimal downtime. The Lockformer® Collar Maker increases productivity, reduces waste, and delivers consistent, high-quality results every time.
CAPACITY
• 24–30 gauge
OTHER
• Tab-notch depth 5/8" standard, adjustable to 3/4"
• Optional depth available upon request.
• Tab-notch spacing approx. 3/4" center
• 30 feet per minute
SPEED MOTOR / VOLTAGE DIMENSIONS / WEIGHT
• 3/4 hp, 115 volt, single phase Drive - V-belt
• Length - 20"
• Width - 22"
• Height - 36"
• Weight - 300 lbs.
The Lockformer Duct Spin Collar Maker Machine allows you to make your own spin collars in minutes. Just cut galvanized stock (24 gauge and lighter) to width and length, set the diameter from 4″ to 16″, and push the blank against the automatic stop. A synchronized die notches the lead edge for easy spin-installation on the job site. The notched piece is then pushed past the stop, feeding the part into the roll former and finally into the automatic crimping and curling operations.
Two models are available:
• Model 6: 2" to 6" wide collars
• Model 12: 2" to 12" wide collars
CAPACITY
• 24–30 gauge
CURLING DIAMETER
• 4–16"
COLLAR WIDTH
• Model 6: 2 – 6"
• Model 12: 2 – 12"
SPEED
• 40 ft/min
MOTOR / VOLTAGE
• 3/4 HP
• 1,725 RPM, 115 Volt, Single Phase
DIMENSIONS / WEIGHT
• Length - 22-1/2"
• Width - 42"
• Height - 37-1/2"
• Weight - 400 lbs.
The Lockformer Easy Edger Manual Flanging Machine turns perfect flanges on elbows or other curved fittings as fast as you can notch them. No gauge to set. Hand clamps to any bench. Available with or without stand. Maximum capacity —20 gauge.
Iowa Precision is the global leader in custom-designed and manufactured automated solutions for the HVAC sheet metal ductwork fabrication industry. With over 75 years of experience, Iowa Precision has established itself as the industry leader in advanced equipment for duct forming, seam closing, corner insertion, and coil processing. Innovative technologies including the Fabriduct®, Pro-Fabriduct®, Ductomatic®, Pro-Ductomatic®, Cornermatic®, Whisper-Loc®, and Adjustable Elbow Machine deliver unmatched performance and quality. These field-proven systems ensure higher quality products with fewer defects, longer run times, and enhanced safety standards, making them the preferred choice for rectangular and spiral ductwork fabrication. Whether meeting specific production goals or optimizing operations, Iowa Precision advanced machinery is designed to help outperform even the most demanding expectations.
The Pro-Fabriduct Full Coil Line from Iowa Precision is the most advanced complete coil line in the HVAC industry today. The line leverages footprint, speed, and production rates along with tolerances that no other HVAC coil line can match. But perhaps most importantly, the Pro-Fabriduct Full Coil Line helps contactors produce finished duct with a full-width longitudinal seam which significantly reduces the chances of leakage in the corners of the duct’s transverse joint (up to 25%). With the Pro-Fabriduct Full Coil Line, you can produce a better product (one with tangible benefits for your customers) while reducing your postproduction labor costs - that’s a competitive advantage you can take to the bank.
Prefabrication continues to be the growing trend across the country. Pre-assembling ductwork in a controlled environment prior to shipping leads to better quality, just in time fabrication, less inventory on the job site, and a significant reduction in labor costs. The innovative Pro-Fabriduct Full Coil Line from Iowa Precision was designed with this trend in mind. First, the ProFabriduct is the only HVAC coil line in the industry with a true full-width ”X” ”Y” cutting bed In-Line Plasma Cutting System. The system includes built-in download capabilities from most CAD/CAM systems and BIM modeling acceptance from Autodesk, Trimble, Practi Cam, Shop Data Systems and others, enabling the cutting of access doors, taps, and more for duct prefabrication on the line.
The sytem also features a new Insulmatic insulation rotary cut off and pinning system. Either Duro Dyne or Gripnail Pinners between 1/2” - 2” cut most all material types, including fiberglass, Arma Cell Elastomeric, Ductmate Poly Armor, Owens Corning, Johns Manville, Certainteed, Knauff, with speed and accuracy. The system is also compatible with the New Johns Manville RC-IG Water Based Insulation which only requires water and eliminates the need for glue.
Most HVAC duct leakage occurs at the notch hole that is produced at the top and bottom of a duct section at the transverse duct connection to the fan or the unit. The Iowa Precision Pro-Fabriduct Full Coil Line has undergone a combination of modifications to the processor, transfer system, and hydraulic servo wrap brake that allow it to produce ProDuct™ — a finished duct with a full-engagement longitudinal seam which substantially reduces the chance of leakage in the corners of the duct’s transverse joint. Full-width longitudinal seam production can substantially reduce the chance of leakage with a greater deliverable thereby producing greater output with less input creating less chance of human error. The Full-width longitudinal seam production is applicable to our 5’ line, with 4’ or 5’ stock, and can be either Large-Pittsburgh and Small-Pittsburgh or Large-Pittsburgh and Snaplock.
The notch profile is altered to leave more material on the male side of the notch, allowing the male seam to extend to the edge of the duct. Dual steppermotor controlled notching die positioning eliminates an operator from needing to adjust the notchers for coil width or notch type; precise positioning is handled through the control system. The 90˚ male lock is formed after the roll forming of the connecting flange, avoiding the full length male flange from being deformed as it passes through the roll former. The servo wrap brake is altered to include locating pins to accurately locate the part parallel to the bending beam. Positioning of the leading raw edge gives very accurate and precise locations for the subsequent bends. Computer controlled leaf tooling gags have been added allowing the brake to bend the full engagement male lock seam without deformation.
• Wireless pendant control system for decoil and recoil of each coil station
• Hydraulically-powered, gear-driven uncoilers, hold downs, and an in feed ramp for smoother coil loading
• E-Z load coil drum assemblies allow for quick spool changeover
• Heavy-duty nylon pockets eliminate mechanical wear and tear items
• Standard 16 gauge processor with optional 14 gauge processor systems available
• When choosing the 14 gauge system, the hydraulic hold down on station 1 is fully powered and an extra set of hydraulically actuated pinch rolls are also included to assist material into the straightening rolls
• Male seam is made on system’s re-engineered hydraulic servo-driven wrap brake
• The notch profile has been altered to allow the male seam to extend to the edge of duct
• Dual stepper-motor controlled notching dies automatically position to eliminate the need for an operator to adjust the notchers for coil width or notch type as precise positioning is handled through the control system
• The servo wrap brake also includes locating pins to accurately locate the part parallel to the bending beam, and the positioning of the leading raw edge gives very accurate and precise locations for subsequent bends
• Computer controlled leaf tooling gags have been added, allowing the brake to bend the full engagement male lock seam without deformation
• The 90˚ male seam lock is formed after the roll forming of the connecting flange, avoiding the full length male flange from being deformed as it passes through the transverse duct connector (TDC) or transverse duct flange (TDF) roll former
• When choosing Female Seam Type from the HMI Input, the hydraulically rafted female roll former automatically moves into place for either Large Pittsburgh Lock, Small Pittsburgh Lock, and/or Snaplock — this also greatly improves the cold sealant program.
• An 18 gauge Dual Head TDC or TDF forming system is standard, with a 16 gauge option available — includes automated go-to positioning from the pendant when coil widths are not a true 60 inches in width
• True full-width ”X” ”Y” cutting bed In-Line Plasma Cutting System with built-in download capabilities from most CAD/CAM systems and BIM modeling acceptance from Autodesk, Trimble, Practi Cam, Shop Data Systems and others, enabling the cutting of access doors, tabs, and more for duct prefabrication on the line — the only HVAC coil line in the industry with a this feature
• Insulmatic insulation rotary cut off and pinning system — either Duro Dyne or Gripnail Pinners between 1/2” - 2” cut most all material types, including fiberglass, Arma Cell Elastomeric, Ductmate Poly Armor, and many more, with speed and accuracy. Also compatible with the New Johns Manville RC-IG Water Based Insulation which only requires water and eliminates the need for glue.
• Punchmaster tie rod hole program not only punches the tie rod holes based on scopes and specs but also provides damper hole capabilities
• Hydraulically-actuated dual head cleat roller produces cleats while attached to coil for squareness
• Within the HMI input, the coil width and automated servo driven notching dies will position automatically for lead and trail, TDC or TDF, and/or ”S” and Drive based on input of coil width
• When Full Width Longitudinal Seam Production is not chosen, a Shear Brake System is included for male leg production for large and small Pittsburgh Lock or Snap Lock seams
• The 10 ft transfer system is standard with optional 12 ft and 14 ft systems available for larger ductwork
• System supports welded duct programs for 1/2”, 3/4”, and 1” straight right angle flange (SMACNA recommends a 1/2” leg height) — welded duct program for 18 gauge stainless steel is also available as needed
• B&R Automation control software supports machine intelligence capabilities as well as Mestek Machinery Key Performance Indicator Technology, which provides on-demand insights including machine uptime, material usage, parts per hour, and pounds per hour
• Remote self diagnostic capabilities and control software features including Auto Batch Control, an Insulation Detection System, Crop Cut Technology, and Bead Roll Up Technology.
The Iowa Precision® Pro-Ductomatic® Front End Coil Line was designed, engineered, and built to efficiently and precisely produce finished duct sections. This front end coil line will dramatically reduce your material, labor, and storage costs and will increase overall profits. The controls and processing features are designed, built, and serviced by Iowa Precision, providing total system support.
The Pro-Ductomatic Front-End Coil Line System provides the fastest feed rate in the industry and the most economical footprint in the world. Every ProDuctomatic Front-End Coil Line System has been designed to maximize return on investment by delivering years of reliable production. This system was designed for light to heavy duty commercial applications and allows future additional components to make this system a complete automated duct line. The Pro-Ductomatic is the start of a complete Pro-Fabriduct® Full Coil Line.
• Fabrication from coil feed material — instead of sheets — to increase ROI
• E-Z load coil drum assemblies for quick coil changeover (no lifting devices to add to your lift truck)
• Hydraulically-powered gear-driven decoiler system on each coil station with low friction UHMW shaft pockets
• Multi-grid skate roll system for support of every coil station
• Powered multi-station coil select for hands-free material feeding into the system processor
• Industrial designed solid block die construction for a 25 year die life
• The industry’s toughest and most stable frames — structured steel tube construction — maintaining structural strength allows accessibility for maintenance, clean up and service
• Shear head squaring system designed for tool-free adjustment
• Industrial, solid-state PLC touch screen operating system controller with storage recall
• State-of-the-art control designed, manufactured, and serviced by Iowa Precision
• Full-width contact feed rolls for positive accurate movement
• Engineered with heavy-duty left/right synchronization to stabilize cutting action and give the lowest moving mass — reduces shock and vibration during the cutting stroke
• Quiet operating system — sound level less than 67 DB
• Soft start motors for long life
• Breaks the blank into L, U, or fully wrapped sections
• The system drives material off the coil to flatten, bend, bead, notch, forms the slip and drive cleat, produces the male Pittsburgh or snap lock seam —from coil to straightening
COIL GAUGE CAPACITY
• 16-26 gauge mild steel
• 14 gauge mild steel optional
COIL WEIGHT CAPACITY
• Standard: up to 12,000 lbs.
• High Capacity Option: up to 20,000 lbs — heaviest in the industry
COIL WIDTH CAPACITY
• 60” width with optional 72” width
PROCESSING SPEED
• Feed rates up to 75 feet per minute
PART LENGTH TOLERANCES
• +/- .020”
• Individual hydraulic gear driven soft start motors
• Individual hydraulically actuated hold down rolls
• Wireless jog pendent technology
• Hydraulically actuated infeed ramp for better feed of material to coil processor
• Line hydraulic notching dies for TDC, TDF, Slip & Drive, Pittsburgh, and Snap Lock
• Combination shear brake for male leg production of both Snap Lock and Pittsburgh
• Hydraulically actuated dual head cleat roller
• One electrical connection
• Industrial, solid-state PLC touch screen operating system controller with storage recall
• Solid State B&R True Machine Tool Control and remote self-diagnostics
• Decoiling feed system supplies each coil station with it’s own hydraulic motor drive and feed up path, allowing for hands off coil selection and feeding by selector switch and push button
• Punchmaster
• Center and end hole punch for 5/16” and 7/16” diameter cross-tie installations
• Tie-Rod Punching, male button lock, and slitting
• Damper Program
• Cleat roller, roll forms 180˚ hems for drive cleats, and Snap Lock Button Punch
• Comes in two standard models known as Short Frame or Long Frame. Frame type is determined by options chosen.
The Iowa Precision Fabriduct line continues to be the most efficient and productive automated duct line ever built — over 800 machines have been delivered worldwide. The Iowa Precision Fabriduct Infinity Full Coil Line is the next evolution — improved to allow automated production of rectangular straight ducts either to coil width/standard duct length or to any duct length from 32” up to 118”. This new configuration allows HVAC duct fabricators to optimize the production of special length straight ducts and greatly reduces labor costs and production lead times.
CLICK TO WATCH ADDITIONAL VIDEO OF THE IOWA PRECISION FABRIDUCT INFINITY COIL LINE
Specifications:
GAUGE CAPACITY
• 16 gauge to 25 gauge
MINIMUM DUCT SIZE SPEED COIL CAPACITY
• 8” x 10”
DUCT LENGTH CAPACITY
• 32” to 118”
• Up to 75 feet per minute
• 12,000 lbs each 20,000 lbs available on request
• 25 to 16 gauge
• Minimum Duct Size 8”x10”
• Capable of producing any duct lengths from 32” to 118”
• ”L”, ”U” & Full Wrap duct type capability
• Up to 75 FPM
• Touch screen Human Machine Interface (”HMI”) with comprehensive diagnostic system
• Up to 12 Coil stations with fast change over 12,000 capacity each (20,000 lbs available on request)
• Underfed Multi-Grid hydraulic powered driven uncoilers
• EZ-Load coil spools, for one man safe and easy coil loading
• Heavy Duty Hydraulic Hold Down Rolls to prevent clock spring effect and allow hands off coil handling
• Automated Coil Selection with powered feed rolls
• Heavy Duty Straightener and Beader
• Heavy Duty Hydraulic Notchers for Slip & Drive and Transverse Duct Connector (TDC) Flange
• Heavy Duty Hydraulic Shear
• Two seam types available (1/2” or 5/16” Pittsburgh or Button Punch Snap Lock)
• Wrap Brake 14’9” available with straight line configuration; 9’10” with L shaped line
• Download option available
• Heavy Duty construction, all hydraulic activation guarantees a very long life time and low maintenance
• Maintenance friendly design allows easy access to valve banks and drive components
• User Friendly Industrial PLC control system
• Servo motor system guarantees long life and consistent part qualityFour (4) sets of tooling can be installed on the Model HB-825.
• Optional Slitter Attachment on the HB825 cuts scrap metal to the correct width for producing ”S” and Drive cleats.
The Iowa Precision Coil Feed was designed for the decoil and recoil of Plasma and Fiber Laser Cutting Systems. This highly integrated system is equipped with wireless capabilities to eliminate the need to load material by hand. The Coil Feed system is comprised of a drive motor and a series of rolls to feed and remove coil set from the material. The material is advanced by the operator using a wireless pendant. This allows the operator to follow the material to proper location along the cutting table. Drive is by way of entry pinch rolls and exit pinch rolls. Straightening is accomplished with rolls located between the entry and exit rolls, which are controlled by way of a hand wheel for depth penetration. Length of feed is at the operator’s discretion, as the machine does not measure the material. Plasma or laser cut-off of the sheet length is standard, optional sheet cut-off system is available.
• E-Z Load system for ease of use when loading coils
• Complete hands-off technology once coils are loaded
• Productivity and savings can be increased with the addition of beading
• Down-bead or up-bead patterns are available
• One-man operation system that reduces material handling
• Instead of storing material on racks, coil stations are ready to feed cutting tables
• Small footprint saving valuable shop floor space
• Reduction in scrap material
• Reduced material costs with coil versus sheet stock production
• Labor savings when decoiling coil stock vs. handling sheet stock
• Material utilization completely optimized when cutting from coil especially when operating a 20’ table
MAXIMUM WIDTH CAPACITY
• 72” (1829 mm)
MAXIMUM GAUGE CAPACITY
• 16 gauge with option for 14 gauge
PASS LINE HEIGHT
• 32.5” (826 mm)
ROLL DIAMETER
• 4.167” (105,7 mm)
MATERIAL JOG SPEED
• 35 FPM (10,7 MPM)
ELECTRIC MOTOR SIZE
• 3 HP (2,3 kw)
MOTOR / VOLTAGE
• 5 HP | 230/460 volts, 60 cycle, 3 phase
DIMENSIONS / WEIGHT
• Length - 13' 4” (for 2 uncoilers)
• Height - 26' 8” (for 4 uncoilers)
• Width - 77”
• Weight - 3,900 lbs. (for 2 uncoilers)
• Weight - 7,800 lbs. (for 4 uncoilers)
Down-Bead or Up-Bead pattern is rolled into the material as it is being fed onto the cutting table. The bead pattern is produced by bead rings that ride in grooves machined into a pair of pinch rolls with the the bottom roll powered and the top roll adjustable up and down by means of a hand wheel. The bead pattern is not intended to be a half radius, but more of a rounded shallow vee to form a cross-break in the material for stiffening.
BEAD PATTERN SPACING
• 12” (304,8 mm) centers 6” (152,4 mm) from edge
MINIMUM GAUGE
• 28 gauge (0,5 mm)
BEAD PATTERN HEIGHT
• 0.060” (1,5 mm) – 0.120” (2,5 mm) adjustable
MAXIMUM GAUGE
• 16 gauge with option for 14 gauge
IOWA PRECISION® COMBINATION
CORNERMATIC II WHISPER-LOC PRO
CLOSING MACHINE
AUTOMATED CORNER INSERTION AND PITTSBURGH LOCK SEAM
The Iowa Precision Cornermatic II Whisper-Loc Combo is a unique, innovative machine that not only inserts and crimps corners into both ends of ductwork but also closes longitudinal Pittsburgh seams on the same ductwork when required. This design allows the operator to accomplish both corner insertion and seam closing on one machine without having to handle the ductwork between processes. The system will close the Pittsburgh seam on any ductwork that uses the duct flanges conforming to T25-a or T25-b under the SMACNA Duct Construction Standards. It will also close the Pittsburgh seam on ductwork that uses the raw edge or slip and drive method as well as slip-on flange type ductwork.
• Designed for ductwork corner insertion and seam closing without having to handle the ductwork between processes
• Pneumatic operation automatically inserts corners into both ends of ductwork that use the transverse duct connection (TDC) or transverse duct flange (TDF) method of joining and crimps them securely and permanently into place in seconds
• Corners are inserted square and fully crimped — no need to change the crimping adjustment when inserting corners in 16 to 26 gauge fittings
• Electric motor and gearbox with variable frequency drive powers the seam closing operation
• Works with SMACNA-conforming, T-25a and T-25b flange and many other flanged duct systems without changing settings
• Will also close the Pittsburgh seam on ductwork that uses the raw edge or slip and drive method as well as slip-on flange type ductwork
The Iowa Precision Cornermatic II Whisper-Loc Combination Automated Corner Insertion and Pittsburgh Seam Closing Machine will operate with all widely available Genuine Cornermatic ® Corners, Ductmate ® Cornermatic ® Strap-Pak ™ and RapidMate™ Corners, and revolutionary DuroDyne ® EZ Connector® Corners for ”C” and ”F” flanges. For best results use in conjunction with Lockformer® Transverse Duct Connector (TDC) Roll Formers and Engel® Transverse Duct Flange (TDF) Roll Formers.
LEARN MORE
Iowa Precision Cornermatic II Whisper-Loc Combo
Specifications
CAPACITY
• Mild Steel: 16 to 26 gauge for automated corner insertion
• Mild Steel: 16 to 26 gauge for seam closing
• Stainless Steel: up to 20 gauge
• Galvanneal: All gauges
• Aluminum: All gauges
FLANGE TYPE FOR INSERTION
• Transverse Duct Connector (TDC) or Transverse Duct Flange (TDF)
Customer to Specify
SPEED
• Approximately 2.5 seconds per corner
AIR
• 9 CFM @ 100 psi
MOTOR / VOLTAGE
• 460/3/60 2.3 Full Load Amps
Other 3 phase voltages available
DIMENSIONS / WEIGHT
• Length - 30 1/2”
• Width - 34”
• Height - 96”
• Weight - 1,800 lbs.
The Dual Head Cornermatic Classic Automated Corner Insertion Machine automatically inserts and crimps specially designed transverse duct connector (TDC) and transverse duct flange (TDF) style corners in seconds. Allows you to install all eight (8) corners, fully crimped on a duct section in about 45 seconds with virtually no physical exertion. Compared to other methods of hand insertion and crimping, it’s a saving of 3 to 6 minutes per section of ductwork depending on size and gauge. The Adjustable Dual Head Cornermatic Classic adds the feature of automatically adjusting the upper crimping head to handle duct from 38″ to 72″ in length.
• Corners are inserted square and fully crimped
• No need to change the crimping adjustments when inserting corners in 18 to 26 gauge ducts
• 16 gauge capacity optional
• Engage ductwork and the dual head automatically and simultaneously installs all eight corners and crimps the corners top and bottom. Rotate ductwork three (3) times for completion of all eight (8) corners
• For cut joints, disengage the top head and utilize the bottom head for automated cornering
• Standard model handles 60” duct
• Adjustable model automatically adjusts the upper crimping head to handle duct from 38″ to 72″ in length
The Iowa Precision Dual Head Cornermatic Classic Automated Corner Insertion Machine will operate with all widely available Genuine Cornermatic ® Corners, Ductmate ® Cornermatic ® Strap-Pak ™ and RapidMate™ Corners, and revolutionary DuroDyne ® EZ Connector® Corners for ”C” and ”F” flanges. For best results use in conjunction with Lockformer® Transverse Duct Connector (TDC) Roll Formers and Engel® Transverse Duct Flange (TDF) Roll Formers.
LEARN MORE
CAPACITY
• 18 gauge to 26gauge Mild Steel Only
16 gauge capacity available
FLANGE TYPE FOR INSERTION
• Transverse Duct Connector (TDC) or Transverse Duct Flange (TDF)
Cutomer to Specify
• 110/1/60 (Single Phase)
MODEL CM3-DH
Dual Head Cornermatic Classic
• Length - 24 1/8”
• Width - 24 1/8”
• Height - 116”
• Weight - 1,400 lbs.
MODEL CM3-DHA
Adjustable Dual Head Cornermatic Classic
• Approximately 2.5 seconds per corner
AIR SPEED
• 85 to 100 PSI (5.5 - 7 Bar)
• Length - 35 3/4”
• Width - 35 3/4”
• Height - 127”
• Weight - 1,800 lbs.
The Iowa Precision Cornermatic Plus Automated Corner Insertion Machine was specifically designed for the fabrication of duct FITTINGS — from standard fittings to odd fittings like tight square throat elbows, flex connectors, offsets down to 2″ throats, and even the toughest inside or outside angle off-set transition fitting from 16-26 gauge. Sitting at an ergonomically comfortable table height, the Cornermatic Plus can handle any transverse duct connector (TDC) or transverse duct flange (TDF) fitting assembled on a bench and automatically and effortlessly completes eight (8) transverse duct connector (TDC) or transverse duct flange (TDF corner inserts — square and fully crimped — in approximately 20 seconds.
• Specifically designed for the fabrication of duct fittings from 16-26 gauge — from standard fittings to odd fittings like tight square throat elbows, flex connectors, offsets down to 2″ throats, and even the toughest inside or outside angle off-set transition fitting
• Operator friendly above ground, table height setting is ideal for fabricating small fittings — adjustable legs to match most bench heights
• Heavy gauge switch for 16-18 gauge performance and light gauge switch for 20-26 gauge performance enhances the Crimping process — slows the Cornermatic down for heavy gauge and speeds it up for light gauge
• Fully automated — no switches or foot pedals — just push in and Cornermatic does the rest
• Completes eight (8) corner inserts in seconds = Floor Level
• Corners are inserted square and fully crimped — no need to change the crimping adjustment when inserting corners in 16 to 26 gauge fittings
• Corners feed from below the worksurface allowing a clean, unobstructed work area
• Light bar indicates when the material has fully engaged on the right or left side of the infeed guide clamps — green light = Go, red light = No
• Light bar also indicates empty corner magazine
• Works with SMACNA-conforming, T-25a and T-25b flange and many other flanged duct systems without changing settings
• Each quick loading box holds eigthy (80) corners and loads in ten (10) seconds
Specifications
CAPACITY
• Mild Steel: 16 to 26 gauge
• Stainless Steel: up to 20 gauge
• Galvanneal: 16 to 26 gauge
• Aluminum: 16 to 26 gauge
FLANGE TYPE FOR INSERTION
• Transverse Duct Connector (TDC) or Transverse Duct Flange (TDF)
Customer to Specify
AIR
• 85 to 100 PSI (5.5 - 7 Bar)
MOTOR / VOLTAGE
• 230/3/60 (Single Phase)
DIMENSIONS / WEIGHT
• Length - 32”
• Width - 36”
• Height - 34”
• Weight - 600 lbs.
SPEED
• Approximately 2.5 seconds per corner
The Iowa Precision Cornermatic Plus Automated Corner Insertion Machine will operate with all widely available Genuine Cornermatic ® Corners, Ductmate ® Cornermatic ® Strap-Pak ™ and RapidMate™ Corners, and revolutionary DuroDyne ® EZ Connector® Corners for ”C” and ”F” flanges. For best results use in conjunction with Lockformer® Transverse Duct Connector (TDC) Roll Formers and Engel® Transverse Duct Flange (TDF) Roll Formers.
The Cornermatic Plus Versa is the most flexible unit for production available. Similar to the Cornermatic Plus, the Cornermatic Plus Versa was designed for the fabrication of duct FITTINGS — from standard fittings to odd fittings like tight square throat elbows, flex connectors, offsets down to 2″ throats, and even the toughest inside or outside angle off-set transition fitting from 16-26 gauge. The Cornermatic Plus Versa features the same above ground, ergonomic table height setting as the Cornermatic Plus, but also adds a floor level setting which allows for sliding over larger, heavier fittings and cut duct sections (machine goes from in-ground to above ground in less than 1 minute with a simple push of a button).
• Specifically designed for the fabrication of both small and large duct fittings from 16-26 gauge on one machine — from standard fittings to odd fittings like tight square throat elbows, flex connectors, offsets down to 2″ throats, and even the toughest inside or outside angle off-set transition fitting
• Operator friendly above ground, table height setting is ideal for fabricating small fittings — adjustable legs to match most bench heights
• Floor level setting allows for sliding over large duct sections and fittings to automatically insert the corners
• Heavy gauge switch for 16-18 gauge performance and light gauge switch for 20-26 gauge performance enhances the Crimping process — slows the Cornermatic down for heavy gauge and speeds it up for light gauge
• Completes eight (8) corner inserts in seconds
= Floor Level
• Fully automated — no switches or foot pedals — just push in and Cornermatic does the rest
• Corners are inserted square and fully crimped — no need to change the crimping adjustment when inserting corners in 16 to 26 gauge fittings
• Corners feed from below the worksurface allowing a clean, unobstructed work area
• Light bar indicates when the material has fully engaged on the right or left side of the infeed guide clamps — green light = Go, red light = No
• Light bar also indicates empty corner magazine
• Works with SMACNA-conforming, T-25a and T-25b flange and many other flanged duct systems without changing settings
• Each quick loading box holds eighty (80) corners and loads in ten (10) seconds
Specifications
CAPACITY
• Mild Steel: 16 to 26 gauge
• Stainless Steel: up to 20 gauge
• Galvanneal: 16 to 16 gauge
• Aluminum: 16 to 26 gauge
FLANGE TYPE FOR INSERTION
• Transverse Duct Connector (TDC) or Transverse Duct Flange (TDF)
Customer to Specify
SPEED
• Approximately 2.5 seconds per corner
AIR
• 85 to 100 PSI (5.5 - 7 Bar)
MOTOR / VOLTAGE
• 230/3/60 (Single Phase)
DIMENSIONS / WEIGHT
• Length - 32”
• Width - 36”
• Height - 34”
• Weight - 600 lbs.
The Iowa Precision Cornermatic II Whisper-Loc Combination Automated Corner Insertion and Pittsburgh Seam Closing Machine will operate with all widely available Genuine Cornermatic ® Corners, Ductmate ® Cornermatic ® Strap-Pak ™ and RapidMate™ Corners, and revolutionary DuroDyne ® EZ Connector® Corners for ”C” and ”F” flanges. For best results use in conjunction with Lockformer® Transverse Duct Connector (TDC) Roll Formers and Engel® Transverse Duct Flange (TDF) Roll Formers.
LEARN MORE
All Iowa Precision Cornermatic Automated Corner Insertion Machines will operate with all widely available Genuine Cornermatic® Corners, Ductmate® Cornermatic® Strap-Pak™ and RapidMate™ Corners, and revolutionary DuroDyne® EZ Connector® Corners for ”C” and ”F” flanges. For best results use in conjunction with Lockformer® Transverse Duct Connector (TDC) Roll Formers and Engel® Transverse Duct Flange (TDF) Roll Formers.
Genuine Cornermatic® Brand Corners
Available from Ductmate®, DuroDyne®, CL Ward® and other approved manufacturers, these corners are precision designed to be strong and easy to use, are available in a variety of gauges, and are designed for a 3/8” Carriage Bolt. These corners come oriented and stacked in the shipping carton (250 corners per carton) for quick and easy loading into the 80 corner magazines feeding the top and bottom crimping heads on all Iowa Precision®Cornermatic® Automated Corner Insertion Machines.
DuroDyne® EZ Connector® TDC / TDF Corners
Corner system that allows the contractor to make duct joints with a super-fast locking bolt using a power drill — saving up to 50% installation costs in duct joint construction work:
EZ Connector® corners from DuroDyne® feed from all Iowa Precision Cornermatic® Automated Corner Insertion Machines with new presser blocks with simple modification — specify ”C” or ”F” for new presser block. It’s Patented EZ ”tear-drop” connector and clenching holes with matching patented extra high drive head with built-in washer serve as pilot guide for EZ assembly with the most versatile and lightest screw-guns. They also reduce the need for drift pins – thanks to its selfpiloting screw tip. Stronger connection for EZ connector duct assembly can ship multiple ducts in connected assemblies. They allow the contractor to fasten duct joints with a super-fast locking bolt using a power drill. No more fumbling for washers, nuts and bolts — it’s magnetic adapter holds screw to the drill for onehand use… even with gloves on. Lastly, it complements new EZ Hanger® as a quick method of securing the corner in place.
Ductmate® Cornermatic® Strap-Pak™ Corners
The Strap-Pak from Ductmate consists of 80 double-strapped Cornermatic® Brand corners which can be quickly loaded into the magazine on all Iowa Precision Cornermatic® Corner Insertion Machines directly from the shipping carton eliminating the need to sort and orient the corners before installation and keeping them properly aligned to reduce corner loading jams. Reload at least three times faster than traditional corner packaging, reducing both loading time and lost production time. Each carton contains five (5) Strap-Paks.
Ductmate® Rapidmate® TDC / TDF Corners
Rapidmate® TDC / TDF Corners are a universal corner and screw system designed to feed from all Iowa Precision Cornermatic® Automated Corner Insertion Machines providing an alternative method of efficiently assembling, aligning, connecting, and securing commercial rectangular HVAC duct systems. The system consists of precision-stamped 16-gauge corners for TDC and TDF flange systems with 3/8” – 12, ASME B18.6.3 Type AB screws which simplifies connection and reduces installation time in the field. Advanced bridge design replaces standard tabs, providing even loading and smoother corner insertion. Beveled gasket plate guides gasket placement at the corner for improved seal. Unique raised spacer plate ensures proper corner spacing and gasket compression. Fits all automatic corner insertion machinery and is also available in specialty alloys. Available pre-stacked in standard 250/box packaging.
Ductmate® Rapidmate® Strap-Pak™ Corners
The fastest, most efficient way of reloading Iowa Precision Cornermatic® Automated Corner Insertion Machines in the HVAC industry. Rapidmate Strap-Pak Corners reload at least three times faster than traditional corner packaging, reducing both loading and lost production time. Strap-Paks contain 80 Rapidmate® TDC / TDF Corners per strap versus the traditional 25 per stack. Each carton contains five Strap-Pak 80 magazines (400 corners).
The Iowa Precision® Whisper-Loc® PRO-XVI Seam Closing Machine closes Pittsburgh seams – whether transverse duct connector (TDC), transverse duct flange (TDF), or slip and drive type duct work – in a fraction of the time. Equipped with push button motor controls for quick-change duct lengths and chain driven, the micro-processor motorized control moves the clamp and slide block, as a unit, for faster set up (one handed) and greatly reduced noise levels. Adjustable from 18″ to 72″, the Whisper-Loc PRO-XVI requires minimal hammer over top and bottom — unlike competitive models that require extensive manual hammer over in Pittsburgh and full length hammer over of at least 45° in slip and drive. Seams from top and bottom to the middle to avoid run out and incomplete seaming of full-travel models. Features low maintenance 220 V, single phase, 3 HP, selfcontained 10-gallon (38 liter) hydraulic unit and requires minimal floor space.
• 16 gauge
• 3 ft (914mm)
• 4 ft (1,219mm)
• 5 ft (1,524mm)
• 6 ft (1,829mm)
• 3 HP - 220/1/60
• Length - 96”
• Width - 35”
• Height - 32 1/2”
• Weight - 1,500 lbs.
The Iowa Precision Whisper-Loc is the quiet, automated way to close Pittsburgh seams in less than six seconds. Eliminate hammering to close ductwork seams, greatly reduce noise levels, and speed up duct seam closing in your shop or at the job site. The Whisper-Loc will also close both insulated and reinforced ductwork seams from top and bottom to the middle to avoid run out and incomplete seaming.
CAPACITY
• 18 gauge
DUCT LENGTH
• 3, 4, 5, 6 ft (914/1219/1524/1829mm)
• 2 HP - 220/1/60
MOTOR / VOLTAGE DIMENSIONS / WEIGHT
• Length - 96”
• Width - 35”
• Height - 32 ½”
• Weight - 2,400 lbs.
The Iowa Precision Automated Furnace Pipe Rolling System produces oval or 3” to 14” diameter round pipe from 2’ to 10’ in length out of 24 to 30 gauge galvanized steel with the turn of a dial. Just feed blank material into the 9-station duplex rollforming machine where male and female configurations are formed.
The blank is then delivered to a two-stage conveyor where it’s oriented and fed in a perfect 90° angle to the pipe rolling machinery. That’s all there is to it! The pipe is finished and ready for packing into shipping bundles.
CAPACITY
• Pre-curl 24-30 gauge
SIZE
• 2 ft to 10 ft lengths
• 4” to 14” diameters
SPEED
• Variable
MOTOR / VOLTAGE
• 9.5 H.P. (6 motors)
• 230/460 volts | 60 cycle, 3 phases
/ WEIGHT
• Length - 192”
• Width - 84”
• Height - 48”
• Passline - 33”
• Weight - 5,400 lbs.
The Iowa Precision® Tube-Matic™ elbow blanking line provides highly accurate punched, crimped, beaded and rolled blanks ready for processing and is an ideal companion line for the Iowa Precision Adjustable Elbow Machines. Tube-Matic models permit automatic production of elbow blanks in diameter ranges of 3 to 16 inches or 3 to 24 inches (high speed model) with rates up to 3,150 per hour. A programmable controller maintains batch counts and blank cut-off lengths. All cut-off shears are made of premium quality, high carbon/high chrome D2 tool steel for exceptional long-life. With Tube-Matic, the entire fabrication line is easily managed by a single operator, reducing labor requirements. Plus, all Tube-Matic lines are backed by the Iowa Precision one year guarantee.
CAPACITY
• 20 gauge or lighter
DEPTH OF POCKET/SIZE
• Variable
OTHER
• Self-contained hydraulic system
• 3” diameter (76,2mm) = 1200 PPH
• 4” diameter (101,6mm) = 1120 PPH
• 5” diameter (127mm) = 1050 PPH
• 6” diameter (152,4mm) = 990 PPH
• 7” diameter (177,8mm) = 940 PPH
• 8” diameter (203,2mm) = 890 PPH
MOTOR / VOLTAGE
• 1-1/2 HP, 115/230 volts, 60 cycle, single phase, A.C. 1,800 RPM
DIMENSIONS / WEIGHT
• Length - 24”
• Width - 28”
• Passline - 34”
• Weight - 200 lbs.
• 9” diameter (228,6mm) = 845 PPH
• 10” diameter (254mm) = 805 PPH
• 12” diameter (304,8mm) = 735 PPH
• 14” diameter (355,6mm) = 675 PPH
• 16” diameter (406,4mm) = 625 PPH
MODEL AEMTM 3-16
CAPACITY
• 3” to 16” diameter
MODEL AEMTM 3-24
MODEL AEMTM-HS 3-24
• 3” to 24” diameter
• 3” to 24” diameter
• Up to 1,200 tubes / hour
SPEED MATERIAL
• .030” max x 24” wide
UNCOILER CAPACITY
• 3,000 lbs.
• Optional: 6,500 lbs.
• Up to 1,200 tubes / hour
• Up to 3,500 tubes / hour
• .030” max x 32” wide
• .030” max x 32” wide
• 5,000 lbs.
• Optional: 8,000 lbs.
UNCOILER MAX DIAMETER
• 54”
• Optional: 60”
UNCOILER ID RANGE
• 15” to 21”
• Optional: 13” to 17”
MOTOR / VOLTAGE
• 7.5 hp, 220VAC, 14/7 amp, 3 phase
DIMENSIONS / WEIGHT
• Length - 120” / 205”
• Width - 60”
• Height - 51”
• Weight - 4,450 lbs.
• 60”
• 5,000 lbs.
• Optional: 8,000 lbs.
• 60”
• 13” to 17”
• Optional: 14” to 18”
• 13” to 17”
• Optional: 14” to 18”
• 7.5 hp, 220VAC, 14/7 amp, 3 phase
• 7.5 hp, 220VAC, 14/7 amp, 3 phase
• Length - 120” / 205”
• Width - 60”
• Height - 51”
• Weight - 4,450 lbs.
• Length - 120” / 205”
• Width - 60”
• Height - 51”
• Weight - 4,450 lbs.
All Iowa Precision Tube-Matic models are capable of making tapered or straight tubes. Interal large end tube diameters are held to a 0.005”.
Iowa Precision Automatic Adjustable Elbow Machines produce high quality 2-piece 30˚, 3-piece 60˚, or 4-piece 90˚ articulated adjustable elbows from galvanized steel tube blanks for tube diameters anywhere from 3” to 24”. The tubes are manually inserted in the machine by the operator who then presses the cycle start button and the machine automatically performs all the operations necessary to form the elbow.
Iowa Precision Automatic Adjustable Elbow Machines incorporate a programmable logic control to handle the sequence logic required for machine operation and a servo control along with a brushless DC servomotor to position the elbow for the individual gores. The operator enters elbow data into the control system via an operator terminal; simply entering the starting point on the tube, the spacing between each gore and the breed distance for each gore. When the machine is placed in the run mode, the push tube automatically moves to the starting point for the elbow, the operator then places the tube over the tooling in the proper orientation and presses the cycle start button to make the elbow.
• Tube position controlled by two highspeed servo motor driven ball screws for accuracy and consistency
• Head assembly for smooth operation
• High/low speed valves with controls and operating program provide soft start and stop of head motor for longer drivetrain life without affecting production stages
• Tool steel used in clamp plates and cut ring for longer life
• Electric lube pump and resevoir to automatically lube each gore
• New lubricator to handle a wider range of viscosities of oil
• Hydraulic power unit is mounted externally for easy service and maximum cooling
• Suitable for B vent off sizes
• Control panel is angled for easy operator use
• Light curtains with safety cage
• Wiper seals in push tube and arbor enclosed to protect bushings
• Push tube connected to push plate by sealed large diameter bearing and eclosed gears
MODEL EMPH 3/4/5
MATERIAL THICKNESS
• 0.0125” to 0.020” (0.32mm to 0.51mm)
MODEL EMPH 4/5/6
MODEL EMPH 5/6/7/8
(Galvanized steel or aluminum. Stainless steel available upon request unless otherwise noted)
• 0.0125” to 0.024” (0.21mm to 0.6mm)
• 0.0125” to 0.024” (0.32mm to 0.6mm)
DIAMETER RANGE
• 3” to 5” (76.2mm to 127mm)
MOTOR / VOLTAGE
• 5 HP - 220V or 440V/3/60
AMPERAGE
• 17.5 (22V) or 9.7 (440V)
DIMENSIONS / WEIGHT
• Length - 60”
• Width - 36”
• Height - 50”
• Weight - 1,550 lbs.
• 4” to 6” (101.6mm to 152.4mm)
• 5” to 8” (125mm to 200mm)
• 5 HP - 220V or 440V/3/60
• 5 HP - 220V or 440V/3/60
• 17.5 (22V) or 9.7 (440V)
• 17.5 (22V) or 9.7 (440V)
• Length - 60”
• Width - 36”
• Height - 50”
• Weight - 1,550 lbs.
• Length - 60”
• Width - 36”
• Height - 50”
• Weight - 2,700 lbs.
MODEL EMPH 6/7/8
MATERIAL THICKNESS
• 0.0125” to 0.024” (0.32mm to 0.6mm)
MODEL EMPH 9-16
MODEL EMPH 10/24
(Galvanized steel or aluminum. Stainless steel available upon request unless otherwise noted)
• 0.013” to 0.025” - 9”, 10”, 12” (0.33mm to 0.64mm)
• 0.015” to 0.025” - 14”, 16” (0.38mm to 0.64mm)
DIAMETER RANGE
• 6” to 8” (152.4mm to 203.2mm)
VOLTAGE
• 5 HP - 220V or 440V/3/60
AMPERAGE
• 17.5 (22V) or 9.7 (440V)
DIMENSIONS / WEIGHT
• Length - 60”
• Width - 36”
• Height - 50”
• Weight - 1,550 lbs.
• 9” to 16” (228.6mm to 406.3mm)
• 0.021” to 0.027” - 10”, 16” galvanized steel riveted or stitch welded, no stainless steel
• 0.021” - 0.027” - 18” - 24” stitch welded tubes only, no stainless steel
• 10” - 24” (254mm to 406.3mm)
• 10 HP - 220V or 440V/3/60
• 10 HP - 220V or 440V/3/60
• 32.0 (220V) or 18.0 (440V)
• 32.0 (220V) or 18.0 (440V)
• Length - 48”
• Width - 58”
• Height - 67”
• Weight - 5,200 lbs.
• Length - 74”
• Width - 65”
• Height - 93”
• Weight - 8,000 lbs.
The Iowa Precision® Collar-Matic Automated Duct Collar Production System takes the handwork out of collar production for collar/boot assemblies. The system uses convenient 2-1/8″ drive cleat coil stock, .013” to .015” thick, to form hemmed collars. An integral parent metal locking joint eliminates the need for collar rivets or staples. The line’s roll former hems the collar’s exposed edge while maintaining the required inside diameter. The Collar-Matic Automated Duct Collar Production System automatically produces and places the collar into the beading die, ready for collar/boot assembly. Available with various pallet or motorized type decoilers.
Parent metal locking joint eliminates the need for rivets or staples. Optional hemming produces a finished edge and adds to collar’s strength.
Collar-Matic’s die components are accessible for tooling changes and servicing. Simply remove outer overs and fold down bead die plate.
Collar-Matic automatically produces and positions collars into the beading die. Adjustable table aligns the boot. Foot pedal control activates beading.
CAPACITY
• .013” - .018” galvanized steel
COLLAR WIDTH
• 2-1/8” wide if hemming
COLLAR DIAMETER
• 4”, 5”, 6”, 7”
COLLAR WIDTH
• 2”
MOTOR / VOLTAGE
• 1-1/2 HP @ 240 (6 Amp) / 3 / 61
DIMENSIONS / WEIGHT MODEL
• Length - 38”
• Width - 47”
• Height - 76”
• Weight - 1,000 lbs.
• .013” - .018” galvanized steel
• .013” - .018” galvanized steel
• 2-1/8” wide if hemming
• 3” wide if hemming
• 5”, 6”, 7”, 8”
• 5”, 6”, 7”, 8”
• 2”
• 3”
• 1-1/2 HP @ 240 (6 Amp) / 3 / 61
• 1-1/2 HP @ 240 (6 Amp) / 3 / 61
• Length - 40”
• Width - 48”
• Height - 78”
• Weight - 1,100 lbs.
• Length - 40”
• Width - 48”
• Height - 78”
• Weight - 1,100 lbs.
OVERALL LINE DIMENSION
• 3 ft. wide x 16 ft. long x 7 ft. high with hemming unit
• 3 ft. wide x 9-1/2 ft. long x 7 ft. high without hemming unit
• 80 PSI minimum AIR
OVERALL LINE MOTOR / VOLTAGE
• 10 Amps @ 230 VAC, 3 Ph., 60 Hz
Hem Former
• 10 Amps @ 115 VAC, 1 Ph., 60 Hz
Uncoiler
• 5 Amps @ 115 VAC, 1 Ph., 60 Hz
The Iowa Precision Colatch Duct Collar Attaching Machines — field-proven and multi-functional — form a bead for the collaring operation in producing boots and other furnace fittings. The machines can expand the boot or take-off and also groove the collar (as well as the boot or take-off). It will also stabilize the collar to the boot or take-off. The three-legged design facilitates precision leveling and there are three (3) different models for 4″ through 20″ diameters.
MODEL B48
MAXIMUM CAPACITY
• 26 gauge
STANDARD DIES
• 4”, 5”, 6”, 7”, 8”
COLLAR WIDTH
• 6” Machine
COLLAR DIAMETER
• 4” through 8”
MODEL C814
• 24 gauge
• 8”, 9”, 10”, 11”, 12”, 14”
MODEL D1420
• 22 gauge
• 14”, 16”, 18”, 20”
• 6” Machine
• 6” Machine
• 8” through 14”
• 14” through 20”
• 220V, 1 Ph, 60 Hz
POWER DIMENSIONS / WEIGHT
• Length - 41”
• Width - 49” with legs
• Height - 23” without legs
• Weight - 725 lbs.
• 220V, 1 Ph, 60 Hz
• 220V, 1 Ph, 60 Hz
• Length - 52”
• Width - 55” with legs
• Height - 35” without legs
• Weight - 1,350 lbs.
• Length - 60”
• Width - 58” with legs
• Height - 38” without legs
• Weight - 1,500 lbs.
Whether you use 1/2”, 3/4” or 1” EMT, keeping HVAC ductwork quiet is reliable, cost-effective, and easy with the Iowa Precision Tie Rod Crimper. Using commonly available hardware, this machine crimps hex-bolts or hex-nuts into the tie rod end tight enough to survive a 3,000 lbs. pull test. Changeover from inserting hex-bolts to hex-nuts takes just a few seconds. Rubber grommets prevent air leaks, vibration and noise.
CAPACITY
• 1/2”, 3/4”, and 1”
AIR REQUIRED
• 85 PSI min. (5 to 6 BAR)
• 3 HP, 208 – 230/3/60
MOTOR / VOLTAGE DIMENSIONS / WEIGHT
• Length - 21”
• Width - 47”
• Height - 41”
• Weight - 800 lbs.
Since 1949, Engel has been recognized as one of the leading manufacturers of quality sheet metal forming machinery. For over seventy years, Engel has designed and built heavy-duty, practical, and cost-effective HVAC coil Lines and roll formers — including the Transverse Duct Flange (TDF) Roll Former— providing the best value in machinery and support that customers have come to depend on.
Combining equal parts evolution and innovation, the Engel Compact II Starter Coil Line was developed specifically for the HVAC industry and is built to last longer, produce more and deliver the highest levels of quality and value. Expandable to a full coil line, this fully hydraulic unitized compact coil line has earned the reputation as one of the most accurate and reliable machine available. The system come standard with a direct hydraulic drive with hydraulic hold downs and low friction pockets which eliminates labor intensive and expensive wear items. This coil line also features a unitized structural steel frame with a low profile design and stress relieved welded construction for low maintenance and long life. Comes standard with an industrial, solid-state PLC touch screen operating system controller, remote self diagnostics, and storage recall.
• State of the art B&R PLC based control system
• Electric servo drive motor that utilizes 4-1/4″ ground and polished rolls with heavy-duty bearings and inner races capable of removing coil set from both overfed and underfed coils
• Ring type beader with five (5) beading rings (16 ga. capacity) preset to SMACNA standards of 12-inch increments
• Notching unit includes two (2) ”V” dies and two (2) ”Lock” dies for use with both TDF and S/ DC type duct. Each pair of dies is independently adjustable for variations in notch depth and width of material
• Twin cylinder hydraulic shear has four-sided high carbon/high chrome blades capable of shearing 16ga. mild steel
• The self-contained 10 HP hydraulic pump system is located between the solid steel side plates of the coil line.
Hydraulically-Powered, Gear-Driven, Multi-Grid Feed Uncoiler:
• The coil is mounted on two drum collars, one being adjustable for various coil width
• Each coil drum assembly has the E-Z Load lifting system
• A hydraulic drive motor is provided for each coil station
• A manual 90° turn ball valve is used to select each motor, located at each motor
• Hydraulically powered hold down wheel for safe band removal and positive feed
• The linear support rails create a multigrid feed system, separating the material vertically as its being used
• Coil capacity is 12,000 lbs.
• Powered drive wheel to feed the material up the ramp and into the pinch rolls
• Hand wheel for easy adjustments to width variances of material
• Standard hydraulic lift for easy vertical adjustment of infeed guide
To include air cylinders located on the ”V” dies for notch depth offset from S/DC to TDF with respect to the ”Lock” dies. This allows for fast notch offset by means of a toggle switch on the Compact II Coil Line.
This unit is designed to provide tie rod holes on the center and at the ends of each leg of duct. Hole placement is programmable to meet SMACNA standards. Hole placement is entered into operator console and is automatically located through the units computerized controls for correct hole location. No manual adjustments are required.
The Engel Compact II Full Coil Line was developed specifically for the HVAC industry and is built to last longer, produce more, and deliver the highest levels of quality and value. An extension of the Compact II Starter Coil Line, this system includes many additional features including a direct hydraulic drive standard on every station with hydraulic hold downs and low friction pockets which eliminates labor intensive and expensive wear items. The unitized structural steel frame with a low profile design and stress relieved welded construction delivers low maintenance and long life. And that’s just the beginning — there are tons of features in this coil line combining equal parts evolution and innovation.
CLICK TO WATCH VIDEO OF THE ENGEL COMPACT II STARTER AND FULL COIL LINES
• State of the art B&R PLC based control system
• Electric servo drive motor that utilizes 4-1/4″ ground and polished rolls with heavy-duty bearings and inner races capable of removing coil set from both overfed and underfed coils
• Ring type beader with five (5) beading rings (16 ga. capacity) preset to SMACNA standards of 12-inch increments
• Notching unit includes two (2) ”V” dies and two (2) ”Lock” dies for use with both TDF and S/ DC type duct. Each pair of dies is independently adjustable for variations in notch depth and width of material
• Twin cylinder hydraulic shear has four-sided high carbon/high chrome blades capable of shearing 16ga. mild steel
• The self-contained 10 HP hydraulic pump system is located between the solid steel side plates of the coil line.
• Hydraulically-powered, gear-driven, multigrid feed uncoiler
• The coil is mounted on two drum collars, one being adjustable for various coil width
• Each coil drum assembly has the E-Z Load lifting system
• A hydraulic drive motor is provided for each coil station
• A manual 90° turn ball valve is used to select each motor, located at each motor
• Hydraulically powered hold down wheel for safe band removal and positive feed
• The linear support rails create a multigrid feed system, separating the material vertically as its being used
• Coil capacity is 12,000 lbs.
• Powered underfed infeed guide assembly featrures powered drive wheel to feed the material up the ramp and into the pinch rolls
• Hand wheel for easy adjustments to width variances of material
• Standard hydraulic lift for easy vertical adjustment of infeed guide
• Quick set die adjustment (MM-QS) to include air cylinders located on the ”V” dies for notch depth offset from S/DC to TDF with respect to the ”Lock” dies. This allows for fast notch offset by means of a toggle switch on the Compact II Coil Line.
• Punchmaster unit with damper hole is designed to provide tie rod holes on the center and at the ends of each leg of duct. Hole placement is programmable to meet SMACNA standards. Hole placement is entered into operator console and is automatically located through the units computerized controls for correct hole location. No manual adjustments are required.
• A direct hydraulic drive standard on every station with hydraulic hold downs and low friction pockets — eliminates labor intensive and expensive wear items
• Unitized structural steel frame with a low profile design and stress relieved welded construction for low maintenance and long life
• Fast, accurate squaring 3-table transfer system with auto mode for continuous batch runs
• Quick and easy changeover from Pittsburgh to Snap Lock — no tools required when changing
• Industry proven roll former with positivepush transfer into cleat edge former and arms that index part via chain to Transverse Duct Flange (TDF) roll former
• SMACNA tested and approved T-25B four bolt connector roll forming system
• Automatic insulation applicator with no need for manual adjustments on varying material thicknesses, plus lead and trail placement of insulation is made from the service screen
• Patented Rotary Cut-Off Insulation Cutting System is standard for cutting both fiberglass and elastomeric foam insulation
• Consistent and accurate welded frame front-gauging hydraulic wrap brake
• Industrial, solid-state PLC touch screen operating system controller
• Remote self-diagnostics and storage recall
• AVAILABLE OPTIONS:
• PLC controlled Tie-Rod Hole Punching
• Cold Sealant System
• Weld Duct Companion Flange
• Coil line Download
The Engel ValuePLUS2 Front End Starter Coil Line effortlessly delivers the power and precision that today’s HVAC companies demand. Innovative ideas are all over this affordable workhorse — ideas that will save you time and money.
CLICK TO WATCH
• Expandable to full line
• In-line footprint fits well in many factory layouts — saving valuable space
• One man operation — run in automatic or on demand mode using a convenient foot switch
• Belt drive or hydraulic drive uncoilers from 12,000 lbs. or 20,000 lbs. capacity available
• From 2 to 10 stations available
• Multi-grid feed systems available for easy threading
• Quick coil changeover — extra coil drum assemblies available for fast changeover of even more coil inventory
• Straighten, bead, notch, and shear (all standard) and cleat edge former or tie rod punching (both optional) all on one compact frame
• No infeed guide assembly required — equipped with built-in entrance guides
• Quick change Notcher and CEF heads
• Electric Servo Drive for faster, more accurate positioning
The Engel ValuePLUS2 Full Coil Line has been engineered to effortlessly deliver the power and precision that today’s HVAC duct fabrication companies demand. Innovative ideas are all over this affordable workhorse that can produce 16″ x 16″ wrap in 60 seconds.
CLICK TO WATCH ADDITIONAL VIDEO OF THE ENGEL VALUEPLUS2 FRONT END AND FULL COIL LINES
• In line footprint fits well in many factory layouts – saving valuable space
• One man operation — run in automatic or on demand mode using a convenient foot switch
• Belt drive or hydraulic drive uncoilers from 12,000 lbs. or 20,000 lbs. capacity available
• From 2 to 10 stations available
• Multi-grid feed systems available for easy threading
• Quick coil changeover — extra coil drum assemblies available for fast changeover of even more coil inventory
• Straighten, bead, notch, and shear (all standard) and cleat edge former or tie rod punching (both optional) all on one compact frame
• Patent pending positioning and retention conveyor assures superior seam profile from the Pittsburgh Roll Former
• Notching dies include clearance holes for use with EZ Connector® system
• Roll former comes standard with 1/2″ Pittsburgh and Snaplock rolls
• Transverse Duct Connector (TDC) or Transverse Duct Flange (TDF) Roll Former available
• Lin-O-Matic / Pinspotter available
• Wrap brake produces 4 sided, ”L”, ”U” and full wrap duct
• No scrap between jobs run from the same coil
• Accepts downloaded jobs from many popular software applications
• User friendly touch screen control
• Low maintenance
• Modular construction — any option can be added later so you can expand your capabilities as your business grows
With Engel Transverse Duct Flange (TDF) Roll Formers, you can roll form your own seal-able flanges on transverse duct joints during the fabrication process for both fittings and straight duct applications. Engel TDF T25b Rollformers feature patented TDF Rolls that produce the TDF flange with unique buttons for snapin corners on the machine's left-hand outboard side.. Optional rolls are also available for the clip. These are the only transverse duct flange machines on the market certified to comply with SMACNA Duct Construction Standard (DCS) T-25b based on actual laboratory tests across the full range of water gauges. The original Engel TDF T25b Rollformer has a capacity of 18-26 gauge mild steel and operates at a speed of 75 ft/min. Our newest model has a capacity of 16-24 gauge mild steel at a speed of 50-60 ft/min.
MODEL TDF T25b 18ga
MAXIMUM CAPACITY
• 18 gauge to 26 gauge mild steel
NUMBER OF FORMING STATIONS
MODEL TDF T25b 16ga
• 16 gauge to 24 gauge mild steel
• 16 • 16
SHAFT DIAMETER
• 1-1/8”
VERTICAL CENTER DISTANCE
• 3-1/2”
HORIZONTAL CENTER DISTANCE
• 6”
SPEED
• 75 ft/min
MOTOR / VOLTAGE
• 7.5 H.P.
• Standard: 230 V / 3ph /60 Hz (22 Amps) 3 Phase
• Optional: 460 V / 3ph /60 Hz (11 Amps) 3 Phase
• Single Phase not available
DIMENSIONS / WEIGHT
• Length - 141”
• Width - 32”
• Height - 45”
• Weight - 3,000 lbs.
Transverse Duct Flange (TDF) Profile
• 1-1/8”
• 4”
• 6”
• 50-60 ft/min
• 7.5 H.P.
• Standard: 230 V / 3ph /60 Hz (22 Amps) 3 Phase
• Optional: 208 V / 3ph /60 Hz (24 Amps) 3 Phase
• Optional: 460 V / 3ph /60 Hz (11 Amps) 3 Phase
• Single Phase not available
• Length - 141”
• Width - 32”
• Height - 45”
• Weight - 3,000 lbs.
Transverse Duct Flange (TDF) Profile with Optional Clip
Optional Rolls
Standing Seam Rolls 1-1/8” Standing Seam Rolls 1-1/4” Standing Seam Rolls 1-1/2” Standing Seam Rolls All 20 gauge
TDF Clip Rolls
Combination
Right-Angle Flange
Seam
1-1/8” Standing Seam Rolls
1-1/4” Standing Seam Rolls
1-1/2” Standing Seam Rolls All 16 gauge
Standing ”S” Cleat
Standing ”S” Bar Slip
1-1/8” Standing ”S” Cleat 20 gauge
1-5/8” Standing ”S” Bar Slip 20-22 gauge
ENGEL® SLIP & DRIVE ROLL FORMER
The industrial grade Engel Slip and Drive Roll Former is built to last longer, perform quieter, and deliver the highest levels of quality and value. This innovative design from Engel features inboard tooling for ”S” and Drive and comes standard with extended outboardroll shafts for mounting auxiliary rolls and there are no opening rolls required — four (4) sets of tooling can be installed. The unit also features eight (8) stations, 2” vertical centers, 5” horizontal centers, and polished 1” spindles. An optional slitter attachment cuts scrap metal to the correct width for producing ”S” and Drive cleats.
MODEL HB825
CAPACITY
• 18-26 gauge
DEPTH OF POCKET
• 1-1/16” for Slip
• 1-1/8” for Drive
FORMING STATIONS
• 8 stations
VERTICAL CENTER DISTANCE
• 2”
HORIZONTAL CENTER DISTANCE
• 5”
SPEED
• 90 ft/min
• 5 HP
• 230/460 volts, 60 cycle, 3 phase, A.C. 3,600 RPM
Other motors available upon request
• Length - 48”
• Width - 24”
• Height - 42”
• Passline - 34”
• Weight - 1,000 lbs
The Pittsburgh Lock revolutionized the HVAC Industry in the late 1930’s and is still used today for its strength and ease in assembling ductwork.
The Engel 800 Series Pittsburgh Lock Roll Formers have eight (8) forming stations with two (2) outboard forming positions. One forms the Pittsburgh Lock and one auxiliary has the capability of forming 1 of 8 different profiles.
MODEL HB-800P-20
CAPACITY
• 20-26 gauge
• 5/16”
• Uses approximately 1” of material
MODEL HB-800P-18
• 18-22 gauge
• 16-20 gauge
• 8 stations
FORMING STATIONS SPEED
• 90 ft/min
MOTOR / VOLTAGE
• 115/230 volts, 60 cycle, single phase, A.C. 1,800 RPM
Other motors available upon request
DEPTH OF POCKET DIMENSIONS / WEIGHT
• Length - 60”
• Width - 24”
• Height - 37”
• Passline - 34”
• Weight - 950 lbs
• 1/2”
• Uses approximately 1-3/” of material
• 1/2”
• Uses approximately 1-3/” of material
• 8 stations
• 8 stations
• 90 ft/min
• 50 ft/min
• 230/460 volts, 60 cycle, single phase, A.C. 1,800 RPM
Other motors available upon request
• Length - 60”
• Width - 24”
• Height - 37”
• Passline - 34”
• Weight - 950 lbs
• 230/460 volts, 60 cycle, single phase, A.C. 3,600 RPM
Other motors available upon request
• Length - 60”
• Width - 24”
• Height - 37”
• Passline - 34”
• Weight - 950 lbs
Engel 800 Series Pittsburgh Lock Roll Formers
1/2” 3/8” 5/16” 14 & 16 gauge 18 gauge 20 & 24 gauge
Engel 800 Series Button Punch Snap Lock Roll Formers form a two piece seam that greatly simplifies ductwork assembly. The male seam is a button, the female seam is a snap lock and the two snap together for a flush corner. These machines are available with eight forming stations. Not only do these locks assemble twice as fast as traditional methods, but because the two pieces nest, they are easier to transport too.
CAPACITY
• 24-28 gauge
DEPTH OF POCKET
• 1/2”
• Uses approximately 1-13/16” of material
• 20-26 gauge
• 1/2”
• Uses approximately 1-13/16” of material
• 18-24 gauge
• 1/2”
• Uses approximately 1-13/16” of material
• 8 stations
FORMING STATIONS SPEED
• 90 ft/min
MOTOR / VOLTAGE
• 5 HP
• 230/460 volts, 60 cycle, single phase, A.C. 3,600 RPM
Other motors available upon request
DIMENSIONS / WEIGHT
• Length - 60”
• Width - 24”
• Height - 37”
• Passline - 34”
• Weight - 950 lbs
• 8 stations
• 8 stations
• 90 ft/min
• 90 ft/min
• 5 HP
• 230/460 volts, 60 cycle, single phase, A.C. 3,600 RPM
Other motors available upon request
• Length - 60”
• Width - 24”
• Height - 37”
• Passline - 34”
• Weight - 950 lbs
• 5 HP
• 230/460 volts, 60 cycle, single phase, A.C. 1,800 RPM
Other motors available upon request
• Length - 60”
• Width - 24”
• Height - 37”
• Passline - 34”
• Weight - 950 lbs
For over 45 years, Roto-Die’s unique hydraulic sheet metal bending brakes have been regarded as an industry standard in HVAC and metal fabrication shops throughout the United States. Each sheet metal brake is a versatile, economical, productive tool satisfying a wide range of sheet metal bending and forming needs. With heavy-duty hydraulics and a complete line of OEM Roto-Die replacement parts — genuine parts made specifically for your press brake —Roto-Die makes your bending operations quick and easy – today and for decades to come.
The patented Roto-Die Hydraulic Sheet Metal Brake Presses have been a fixture in thousands of sheet metal shops for over 45 years. As simple to operate as a hand brake – but with infinitely more production capacity — Roto-Die Hydraulic Sheet Metal Brake Presses form full length ducts, gravel stops, standing lock seams, flashing and hemming operations accurately, economically, with just one handling by one operator —reducing abor costs and maximizing shop productivity.
As simple to operate as a hand brake with infinitely more production capacity
• Merely by rotating the selections lever, one operator can perform all basic sheetmetal forming operations — no dies to change
• Forms full length ducts, gravel stops, standing lock seams, flashing and hemming operations accurately and economically
• The compactness inherent in the cylindrical die design permits acute reverse bends not possible with conventional wide-bend machines
• Indexes quickly and accurately to all forming stations — automatic detention assures positive die alignment
• Centerline machined upper dies are instantly interchangeable in all openings without special stops or adjustments
One handling by one operator for most
• All basic sheet metal-forming operations can be made without die change or major adjustments — infinitely variable speed control for easy selection of ram speed
• The ram may be jogged, stopped or returned to “up” position at any point of the stroke — it may also be inched for accurate positioning of the work, reducing material loss and gauge adjustment time
• Disappearing pins are conveniently located for fast one-person positioning in cross-braking (stiffening) and rectangular duct forming — pin gauges are easily removed and relocated
Engineered to reduce labor costs while increasing shop productivity
• The patented Roto-Die principle reduces setup time by as much as 70%, compared with other power forming equipment — gauge and clearances are adjusted more quickly than on conventional hand brakes
• One-man operation cuts labor requirements in half on virtually all handbrake operations
• Simple adjustments permit operating speeds up to 50 strokes per minute for maximum production output
• Multiple handling of sheet stock is kept to a minimum — this allows you to fabricate most commercial ventilating jobs, including the TDC duct system, in the Roto-Die in one-fourth the time ordinary benders require
MODEL 5
MODEL 10
BENDING CAPACITY (* = 7/8” die opening with angle insert)
• 60” x 16 gauge
• 3”
LENGTH OF STROKE STROKES PER MINUTE (* approximate)
• 20 to 50
DIE CLEARANCE
• 2-1/8”
DIE SPACE
• 7-1/2”
DIMENSIONS / WEIGHT
• Length - 94-1/2”
• Width - 22”
• Height - 63-1/2”
• Weight - 3,300 lbs.
• 120” x 16 gauge
• 72” x 10 gauge*
• 3”
• 20 to 50 • 2-1/8”
• 7-1/2”
• Length - 145”
• Width - 22”
• Height - 63-1/2”
• Weight - 5,700 lbs.
MODEL 15
MODEL 15/12
BENDING CAPACITY (* = 7/8” die opening with angle insert)
• 120” x 14 gauge
• 120” x 10 gauge*
LENGTH OF STROKE
• 144” x 14 gauge
• 144” x 10 gauge*
• 3” • 3”
STROKES PER MINUTE (* approximate)
• 20 to 50
DIE CLEARANCE
• 2-1/8”
DIE SPACE
• 7-1/2”
DIMENSIONS / WEIGHT
• Length - 150-1/4”
• Width - 22”
• Height - 73”
• Weight - 8,950 lbs.
• 20 to 50
• 2-1/8”
• 7-1/2”
• Length - 174”
• Width - 22”
• Height - 73”
• Weight - 10,000 lbs.
Business owners who use Roto-Die Hydraulic Brake Presses are responsible for the safety of each person that operates these hydraulic benders. In accordance with all documented safety guidelines, business owners are responsible for ensuring that safeguarding is provided, installed, maintained, and used. The Roto-Die Light Curtain Safety System not only meets ANSI B11.3, but can also be retrofitted to your existing Roto-Die Hydraulic Bender.
• Main control panel including lockout/ tagout requirements
• 18” Category 4 Light Curtain offers maximum protection above the upper die and below the lower die
• Muting function 1/4” die opening
• Redundant (primary and secondary) proximity sensors and electric sonenoid valves
• Push-button operator station
• Front fixed-guard for added safety in the die area
• New piping, high-pressure fittings and installation hardware
• Manual jog of upper die remains intact
Back Gauge Manual Operation
Rear Operated (RD00900)
Front Operated (RD00975)
Single Station Ajustment system
Permits depth-of-stroke adjustment from one side of machine (RD900001)
Foot Pedal Conversion Kit
Converts oldstyle “Treadle Pedal” to an OSHA-Approved covered foot pedal (RD93012)
Merely by shifting the selections lever, one operator can perform all basic sheet-metal forming operations. No dies to change.
Roto-Die Hydraulic Brake Presses form fulllength ducts, gravel stops, standing lock seams, flashing, and hemming operations accurately and economically.
All Roto-Die Hydraulic Brake Presses include tooling for five (5) basic forming operations:
• One (1) #37 Roto-Die® with 7˚ crossbraking groove, 85˚ die opening 3/8 ” wide, 85˚ die opening 7/8 ” wide, 30˚ die opening 1/2 ” wide
• One (1) #1 Forming Die 85˚
• One (1) #24 Hemming Die 30˚
• Six (6) sheet support arms with clips
• Six (6) #52 gauging blocks
• Six (6) #53 disappearing spring-pin gauges
Additional Available Dies
All models are equipped with depth-of-stroke adjustment with indicators, length-of-stroke adjustment, motor and controls for 230/460 Volts, 3 Phase 60 HZ. (Other 3 Phase voltages also available.) ] ]
A — #24 Hemming Die B — #1 Forming Die
C — Gravel Stop Adapter Die
D — #49 Adjustable Damper Die
See next page for more information on dies
E — Narrow #1 Forming Die used with TDC Conversion Die
F — TDC / TDF Conversion Die
G — Heavy Gauge Angle Insert
H — #5 Gooseneck Die
A. Forming
B. Open Hemming (B) Forming and open hemming bends are accomplished with standard 30° upper die and No. 37 Roto-Die. Following these sequences, a standing lock seam may be formed without die change or multiple handling of the sheet.
C. Blade Forming
Many degree-of-bend combinations are quickly and easily formed by bottoming and air-bending.
D. Heavy-Gauge Forming
Machined inserts increase bender capacities up to 120” of 10 gauge materials for heavygauge or large-radius forming.
E. Box Forming
Depths to 1-3/4” may be formed with standard dies.
F. Architectural Gravel Stop Adapter Plate
This combination die will form 120” of 24-gauge gravel stop with a 3/4" rise. Easy removal of the rear forming section converts the die to acute-angle forming and hemming operations.
G. Channel-Forming
90° gooseneck dies (with or without angle inserts) simplify forming light and heavygauge channels.
H. Multi-Forming
Damper blades and V-rib shapes may be formed in one stoke in 20 gauge galvanized steel up to 120” long. Shorter lengths may be formed in heavier gauges. Die is adjustable for metals with springback.
Custom Dies to Increase Your Capabilities
As you develop creative uses for your Roto-Die Hydraulic Brake Press, adding a custom die set will increase your capabilities and your profitability. To the right are a few custom dies we have manufactured to customer specifications. These are available by special order or we can have a die made to fit your unique application.
Contact Roto-Die to learn more
Roto-Die® will remanufacture your machine to the latest specifications or sell you a remanufactured machine. Remanufactured machines carry the same full one-year warranty as our new machines.
Have your old machine completely remanufactured into a brand new machine. Everything is replaced on the machine except the original bed, ram, and side plate weldment. All new dies are included.
Have questions about our machinery and equipment? Looking for help on a unique application? We’d love to help.
Need help with a budget estimate to determine overall equipment costs? Looking for a firm or detailed quote for your equipment needs? We’d be happy to help.
Request a 1-on-1 Consultation with a Mestek Machinery Technical Advisor to address your specific application.