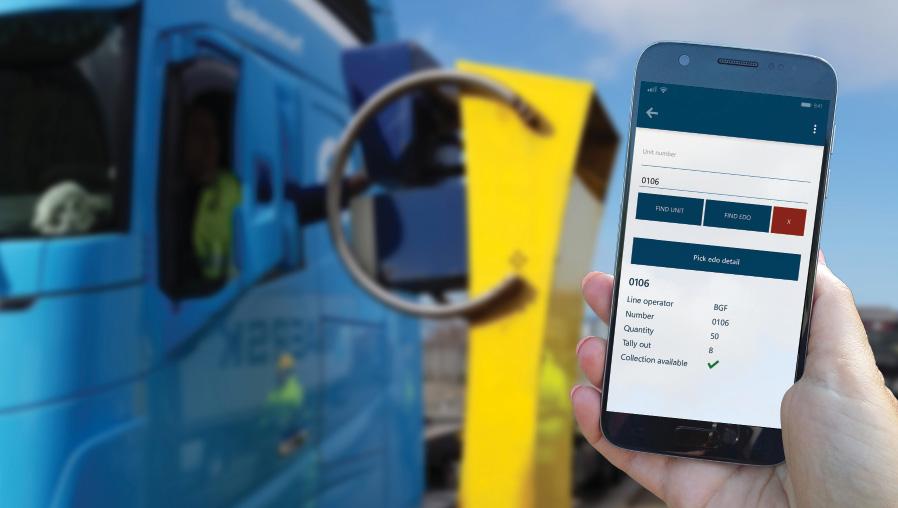
8 minute read
Terminal VBS
MAKE AN APPOINTMENT WITH VBS
A number of parties suggest the full benefi ts and unfolding powers of the modern Vehicle Booking System are not fully recognised until post system implementation. John Bensalhia reviews the innovative supply sector
Norbert Klettner, Managing Director, RBS EMEA, says that a major benefi t lies in the data delivered before trucks arrive. “Gate automation coupled with slot booking will drive gate effi ciency because you can allocate the required resources much more effi ciently. This,” he says, “is good for productivity as well as for a reduction of environmental impact. Matching equipment to a known workload delivers these and other benefi ts.”
Drivers today have the possibility to register themselves prior to the arrival at the terminal, minimising waiting time through a reduction of queuing time and completing other formalities associated with container pick-up/drop off.
“Systems nowadays are more and more integrated with Terminal Operating Systems (TOS)/Port Community Systems which facilitates efficient data interchange between parties involved with the operational process as well as other local interests,” explains Daniele Labate, DSP Team. “Also,” he elaborates, “terminal customers and trucking companies have more visibility of what is happening in a real-time manner, allowing bookings and planning of the next phases quickly.”
Jan Bossens, CEO, Camco Technologies, concurs that the main changes happening today are taking place upstream of terminal gates – the processes before gate access, typically involving truckers’ apps and vehicle booking systems (VBS). “Truck appointment systems,” he notes, “allow upfront registration of bookings, increasing terminal efficiency on a broad scale.”
He too points out the linkage of such systems to TOS as a mainstream driver of terminal efficiency, citing many of the afore mentioned advantages but also the ability to flatten out peaks in terminal traffic and on the trucking company side the ability to achieve better fleet management, expedited truck turnround and for the driver less hassle overall.
Rok Štemberger of the Port of Koper, Slovenia, confirms the usefulness of VBS to flatten out traffic peaks and generally better handle high traffic flows. “In the Port of Koper,” he explains, “we are handling around 330.000 trucks annually and managing this traffic flow is very important for the internal logistics of the port, terminal productivity and to relieve the roads around the city. Our Vehicle Booking System (VBS) is an online platform, developed by Luka Koper, for making truck appointments, checking cargo status and scheduling plans, recording truck entries in the port and reviewing the validity of annual permits for port entry.”
SYSTEM EVOLUTION
System supplier 1-Stop Connections, says that the very nature of what a port vehicle booking system (VBS) is, has evolved over the last few years. “Historically, a VBS is seen as an appointment or time slotting system – which couldn’t be further from what a true VBS is today. 1-Stop’s VBS,” the company explains, “has turned into a fully-fledged capacity management tool that matches terminal resources with landside demand and ultimately drives efficiencies across the Supply Chain. A true VBS,” 1-Stop emphasises, “is a solution that interconnects the entire Supply Chain from the Quay Line to a customer’s door by improving efficiency and creating more certainty.” The company further points out that vehicle booking systems have evolved to cover all cargo types, not just containers as they have typically been used for in the past. 1-Stop is another party to tick the boxes of VBS in terms of its ability to improve yard productivity, optimise yard planning, streamline gate processes, and even create paperless exchanges. It underlines, however: “The most significant benefit a VBS implementation creates is the ability
8 More innovation
is expected in the use of smartphones, apps and VBS – standardisation is also an issue
to match a facility’s resources with the landside demand; this generates a higher asset utilisation and increases efficiencies across the entire Supply Chain while reducing costs.”
Also in terms of benefits, John Lund, Sales and Marketing Director (Global), Visy Oy, another system supplier, makes the point that: “A VBS is one of those tools that operators may not appreciate until they actually have it in use. On paper,” he suggests, “it may seem abstract, but in practical terms it is a critical part of operations.”
“For Visy,” he further notes, “the VBS is a module that can be added to our gate operating system (GOS) – with the two systems complementing each other very well. The VBS,” he points out, “provides an additional suite of access and area control tools to help operators save time and money on every transaction. It will allow operators to create scalable, repeatable, predictable, and ultimately more profitable operations,” he says.
SYSTEM DETAIL
Explaining the Visy VBS in detail, Lund notes that it offers a wide variety of features. These include: booking and time slot allocation administration; a web page for customer booking and terminal visit management; seamless integration with Visy Access GOS, terminal operating systems and warehouse management systems plus editable booking monitors to automatically report exceptions such as terminal visits that are too slow. Mandatory data fields can be managed by administrators and there are no limits to the number of customers or users.
The Visy VBS also features an SMS/App messaging for truck drivers, such as created bookings and allocations or changes for time slots as well as dynamic list views of current bookings to be shown on info’ displays, tablets and mobile devices. These views can typically be all trucks inside the terminal, waiting area or due for arrival within the next two hours.
SIMPLIFICATION - KPIs
“The VBS provides benefits by automating (and therefore simplifying) a workflow,” says Lund. “Some of the benefits are obvious, some less so. The types of benefits one would expect from a VBS include: more predictable operations, the ability to make appropriate staffing requirements and increased visibility.” However, Lund adds that the Visy VBS also provides tools for measuring KPI’s such as truck turnaround times and creates alerts if a vehicle has spent too long on the terminal. “The ability to track KPI’s allows operators to measure and therefore, truly improve operations,” he says. “After all, if you can’t measure the changes to your operation, how do you know that you’re making improvements?”
The VBS, Lund continues, provides a scalable platform that collects and shares data with relevant parties such as terminal administrators, truck drivers, and cargo owners. “For example, we use SMS text messaging or an app to communicate with drivers in real-time about the status of their work order. Changes happen in terminal operations, so the platform allows operators to immediately notify drivers that a booking was created or that a time slot was allocated or even changed. Ultimately, we’re trying to save every party time on each transaction and ensure that the right assets are in the right place when they should be. It’s a natural extension of the gate operating system which in many ways is concerned with similar functionality but from a slightly different perspective,” he explains.
Bossens notes that an issue with today’s app technology is that port authorities can’t get various terminals on one common and single VBS and truckers app, which he says “must be a nightmare for truckers frequenting different terminals.
“As an enabler of gateless gates, one expects a future,” he argues, “for BYD (Bring Your Own Device) instead of truck reception kiosks. This means that kiosks will be replaced with a ‘gate app’ on a smartphone. “Technically,” he elaborates, “it’s not a big challenge to extend the current truckers app, the problem is the security related procedures. Biometrics as fingerprint isn’t available on all smartphones, face recognition is an alternative but the main issue is that security procedures are running on a device not owned and controlled by the terminal.”
“We had RFID seal readers installed with some customers but we can’t speak yet of a real breakthrough, which is remarkable as RFID seals are not that more expensive than standard seals.”
BUILDING FOR THE FUTURE
Daniele Labate concludes that automation goes together with quality data. Knowing in advance the information about the traffic and peaks, container terminals can handle congestion proactively and smarter.
“The comparison between the received data and what is currently showing up at the gate triggers the next action into the gate process flow automatically. OCR recognition behaves as human eyes and identifies the physical information about the unit and its position as well as the truck related info. Sensors and automatic weighbridge enrich the dataset with specific information on the weight and trailer composition.”
The Port of Koper along with other ports and terminals worldwide plans to build on what it has achieved to-date with its VBS. Rok Štemberger comments: “We plan to further digitalise all the processes to offer trucking companies, forwarders, agents and customs a complete paperless system. Our container terminal is currently in an advanced stage of this development,” he notes.
Meanwhile, VBS companies are also working on innovations. “We’ll continue to develop new tools to make communication between stakeholders easier and faster,” says Lund. “We currently have an intuitive web interface and tools for mobile devices and tablets. The speed and accuracy of information exchange is critical in terminal operations and helps terminals differentiate themselves from one another. We’ll continue to look for new ways to make that happen for our customers.”
“There are endless opportunities for the future of the VBS,” suggests 1-Stop: “These include the prospect of using geofencing technology, smart apps, and even API/AOT/ Blockchain system integrations.”
“The more innovation with VBS, the more connected and stronger supply chain efficiencies will become for all parties and assets involved.”

8 A typical
workfl ow presented in the Visy system
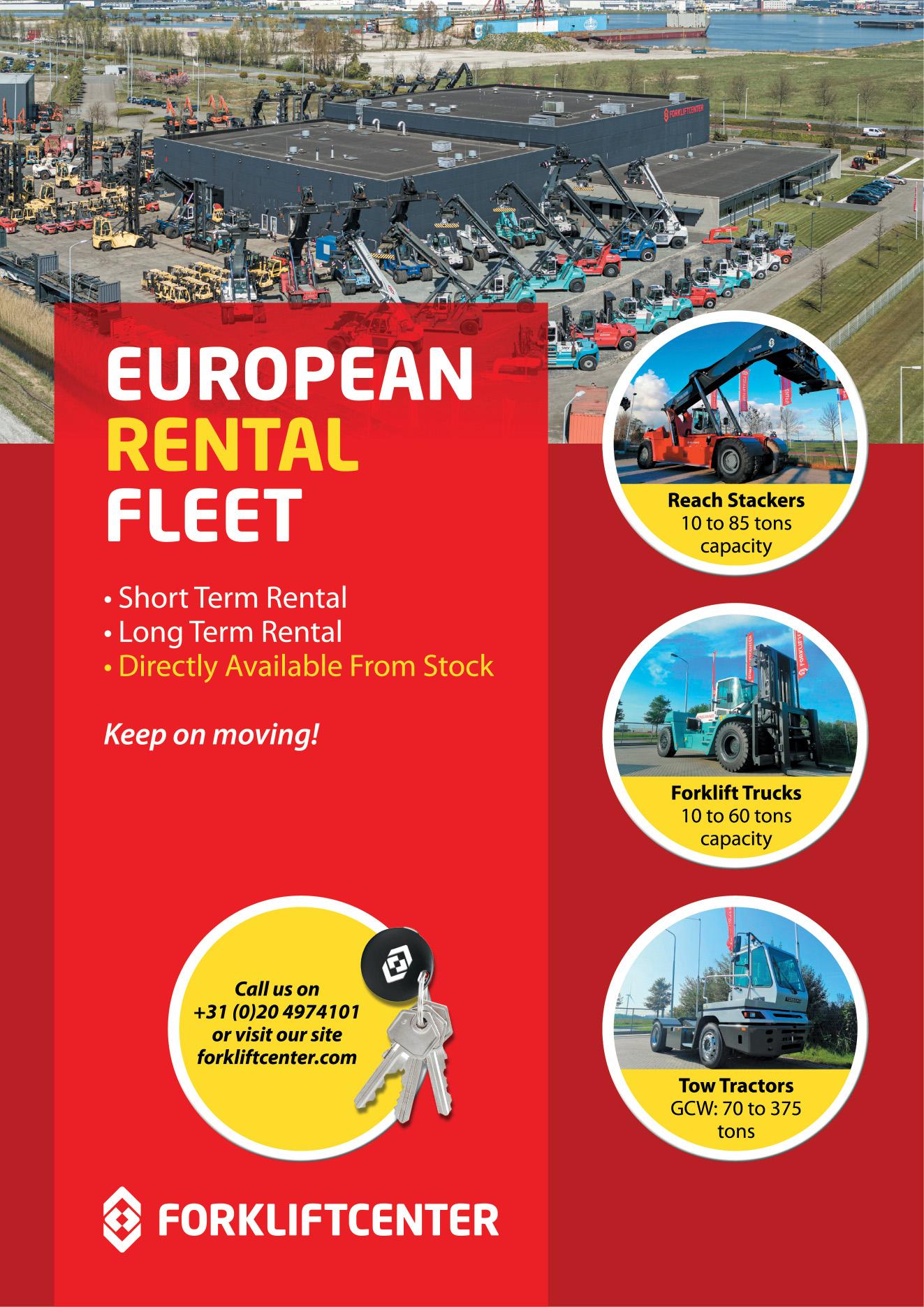