
22 minute read
Shifting boundary conditions
SOLVING THE CLEAN-UP CONUNDRUM
Two-stage turbocharging has been around for quite a while, but there's recently been a resurgence of interest. However, the targets diff er from those of automotive applications which focus on dynamic behaviour, writes Stevie Knight
Firstly, as Michael Willmann of ABB Turbocharging points out: “Any step that helps to minimize the engine footprint, such as increasing the power density through the use of higher receiver pressure, is desirable.”
But it's broader than that: for marine's medium-speed engines, “concern centres rather more on efficiency and peak pressure”, says two-stage turbocharger development lead for PBST, Sebastian Spengler. Here, it's not just an enabler for high power densities, it's also aimed at NOx and SFOC reduction.
However, there's a conundrum: “A greater mean effective pressure in the engine requires more mass coming through the air intake,” says Johannes Kech of Rolls-Royce's Power Systems business unit. This doesn't necessarily sit well with combustion clean up techniques aiming to meet IMO Tier III and EPA Tier 4 NOx requirements (which this year reached the Baltic and North Sea ECAs). All of which puts yet more demand on the turbos.
Take Exhaust Gas Recirculation: this diverts some of the exhaust flow back into the intake manifold, diluting the charge, reducing available oxygen, combustion temperature and NOx formation on the flame front. However, large engines require considerably higher EGR rates to achieve the same NOx reduction level as their smaller automotive counterparts - the fraction sometimes reaching over 50%. Therefore, the EGR can be asking for more while the turbo itself might be feeling the pinch.
Another technique is playing with the timing to change the combustion characteristics: on a Miller cycle, the charge is limited by either late or early intake valve closure. This can be tweaked to reduce the work required by compression, stretch out the intake charge to cool combustion temperatures from NOx-formation levels, and harvest more energy from the cycle.
While a turbo can mitigate the consequent power loss, stronger Miller timing necessary to meet advancing NOx requirements also means “there's much less time for bringing the air through into the cylinder”, explains Kech.
He adds that even relatively straightforward particulate filters “put a higher back pressure on the exhaust system, so to ensure the exhaust flows out of the cylinder, again you need more pressure on the intake side”.
Initially, EGR, filter pressure and Miller cycle demands were supported through single-stage turbochargers. These are comparatively simple and cost-effective, so they've gained a good slice of development: ABB's product has lifted the pressure ratio ceiling from 6.0 to 6.5, while PBST has been investigating how to move towards 7.0 with package, cost and performance benefits for medium speed and high speed gas engines.
But these single-stage units have shortcomings. While they can deliver emissions savings, above a pressure ratio around 5 or 5.5, “the topological map of the compressor tends to narrow, and in this situation, the engine's overall performance becomes rather limited”, says Kech. In other words, it can be set up either for a wide speed range or a high boost pressure - but there's generally a trade-off between the two.
Just adding another TC for increased speeds will fix a number of issues. “A sequential system means starting the engine with one turbocharger: accelerating to a higher power triggers a second, then a third and so on,” he explains.
That in turn allows more boost at low engine speeds and faster transient response. However, sequential turbocharging has a different focus: broad performance maps and greater surge margins remain the highest priority for compressor development. But as these systems still operate within the confines of single-stage TCs, Kech points out “this setup can't reach the pressure ratios required for emission reduction technologies”.
Instead, the answer lies in two-stage TC arrangements
Image: ABB Turbocharging 8 Both power
density and emissions are concerns

which can push the pressure ratio into double figures. Here, the inlet air is speeded up and compressed, first by one or two low-pressure turbines in parallel, giving it a leg up. It's then cooled to make it denser before it's transferred to a high-pressure stage and possibly another intercooler, explains Willmann. However, he adds that the load distribution between the lower and upper stages “influence both the system efficiency and its size”.
That means that for OEMs like Rolls-Royce - currently working on a new two-stage offering for its mtu series 4000 marine four-stroke - the effort is not merely to get the highest peak pressure rise out of the individual turbines. Instead, it's to tailor their highest efficiency regions to their operating position on the now combined, two-stage compressor map.
But for manufacturers like ABB Turbo and PBST, the focus is adaptability, offering matching combinations between a variety of high and low pressure turbines. Spengler adds that even inside these stages, different fuel type or application requirements can change the arrangement.
Therefore, tailoring each stage isn't easy. Firstly, “the load split between HP and LP is typically defined by static matching,” he says, with parts like nozzle rings and diffusers being modelled to meet the engine's most common demand.
Further, operational points outside this area can be so diverse as to require changing the balance. Variable geometries (used onboard MAN's 51/60 GTS engine) and other devices have their place: Rolls-Royce, for example, is incorporating a valve or flap mechanism to alter the flow with a bypass that allows the LP side to pick up more of the load as speed rises and it also acts as a wastegate to protect the HP side at very high flow rates.
It opens up the possibilities but also creates another level of complexity, and more, “any methods need to be closely linked to the engine control and operation”, adds Spengler.
Still, the (often iterative) matching process may be somewhat eased by further turbine developments.
Radial - centrifugal - designs have been the general go-to choice for single-stage compression. These work by hurling out the gas at an angle: it then flows through the spiral chamber where the velocity gets converted to pressure. While radial units can maintain overall efficiency across the rpm range and deliver a considerable step-up in pressure ratio in one hit, the limits are blade size and impeller stresses from supersonic gas speeds.
Recently, two-stage solutions have opened the door to axial compressors. These typically have a set of rotating blades - more like propellers - which accelerate the gas directly along the flow path to a stator, which converts it to pressure. They make a better job of handling large volumes than radial types, but two features have held back take up: they don't yield as big a jump in pressure, and their efficiency isn't that even, generally rising with speed.
Despite that, axial flow's characteristics are still attractive for larger four-strokes, and some marine manufacturers may be considering them for the initial, low-pressure stage.
For example, although Kech underlines Rolls-Royce's development decisions aren't set in stone, he says “the advantage of an axial turbine is its low momentum of inertia compared to a radial turbine, achieving higher agility”. ABB Turbo also appears to be contemplating their advantages, as Willmann notes: “With increasing airflow, the classical tradeoff between radial - high-pressure ratio - and axial - high mass flow - machines may lead to consideration of axial turbines for large-bore marine engines.”
Interestingly, as part of its modular approach, PBST is already offering its new, axial TCT series as its smaller, lighter design makes it suited for the LP turbo in two-stage systems.
However, the HP side “is generally more physically demanding,” says Spengler. Here, radial versions have their advantages, as they have a very robust, well proven and compact design while covering all efficiency requirements. But he adds: “The blade vibration is higher, forces on the bearings are more powerful - and nearly all the components are subject to more stress .”
So it has taken effort. Both RollsRoyce and PBST have been working on geometry; PBST's radial TCX has recently benefited from smoothing the internal flow alongside tweaks such as channelling water-cooling toward higher temperature areas and thicker walls in certain regions.
Further, some of the designs also offer ramp-up support: for example, the TCX has a Jet Assist which blows high-pressure air onto the compressor blades, assisting TC acceleration.
Finally, two-stage turbos have enough potential to support all kinds of clean-up technology. “It is a big enabler for Miller timing,” says Spengler: “If you deliver very high pressure to the cylinder, you can afford to lose a bit, and you still have enough power density in the cylinder afterwards. That's the key.” While there is still a trade-off, tests demonstrate that with a strong Miller cycle, you can drop NOx or SFOC significantly compared to single-stage TCs.
There's still a world of possibilities. Rolls-Royce's initial two-stage model for the mtu 4000 marine engine looks likely to have twin LP turbines running in parallel - while other installations could offer two HP compressors. But as Kech points out, imagination is limited: it all has to fit into nothing much larger than the envelope presented by earlier single-stage designs.
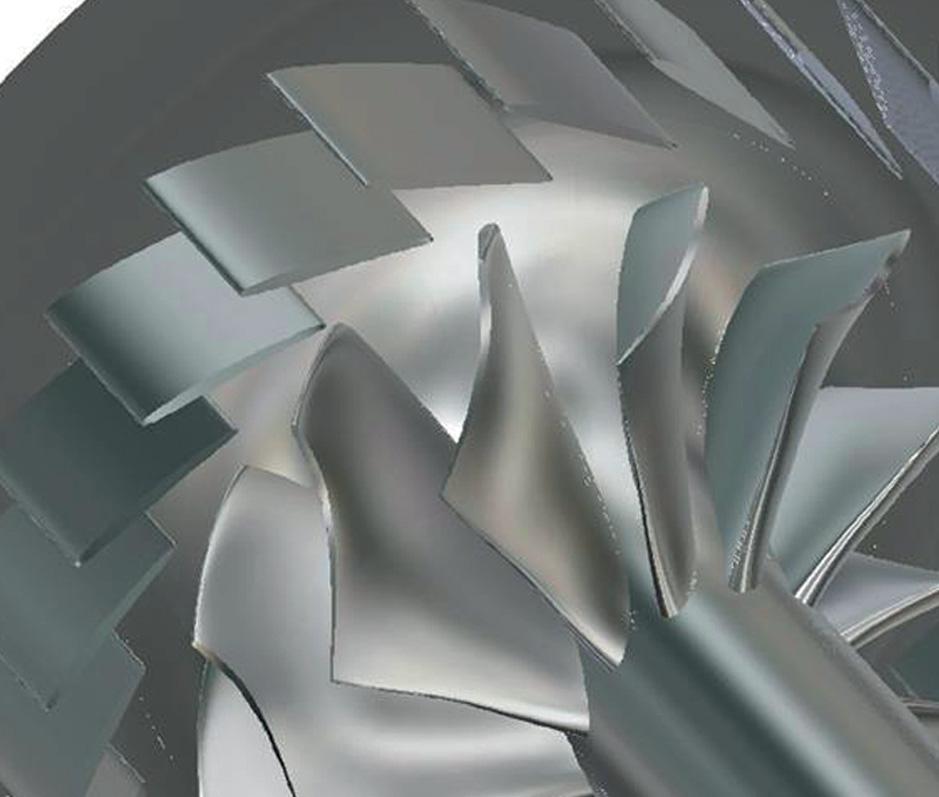
8 The needs of
the high pressure side of two-stage turbochargers may still be best met by radial fl ow compressors
8 Two-stage TC's
have potential to support a variety of clean-up technologies
UECC PUSHES LIMITS TO TEST NEW TECHNOLOGIES
United European Car Carriers (UECC), the Norway based company that operates a fl eet of 16 pure truck and car carriers in intra-European trades, is upping its game to meet client expectations
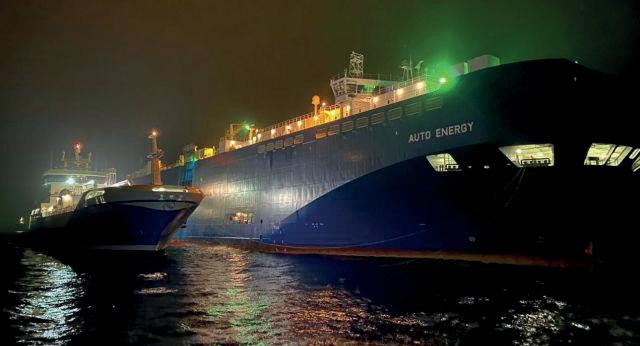
Credit: UECC
Early in 2020, the company appointed Daniel Gent as Energy and Sustainability Manager to add momentum to its green drive. The company's ambitions to exceed minimum GHG reduction targets have led it to becoming an early adaptor of new technologies, although it means accepting a sharp learning curve that follow from this. Gent added that the greatest change had been in terms of corporate mindset.
“In 2010-12, I would probably have asked how could LNG technology work, it was an oil mindset,” he told The Motorship.
It is unlikely that Gent would have envisaged working with dual-fuel battery-hybrid PCTCs in 2010. However, UECC is waiting to take delivery of the first of a series of three 3,600 car equivalent unit (ceu) capacity LNG-fuelled battery-hybrid PCTCs before the end of 2021. The vessels were ordered in March 2019 at Jiangnan shipyard, and are expected to be delivered by early 2022. "We are investing in the future," said Glenn Edvardsen, CEO of UECC in a statement at the time, adding: "Our solution will take us beyond IMO's target for a 40% reduction in carbon intensity by 2030”.
The combination of an energy storage system with WinGD 6RT-Flex50DF main engines offers specific peak shaving efficiency advantages, Gent noted. But extending the use of the battery technology will have to wait for further advances in battery technology in the coming decades. Perhaps a new pack can be installed in the future that can offer possibilities that are not available at the present moment, Gent mused.
Turning back to the present, UECC has also acted as an early adopter with liquefied biogas (LBG). In December 2020, its Auto Energy, bunkered gas containing 90% LNG and 10% LBG at sea outside Gothenburg from Gasum's bunkering vessel Coralius.
Dual fuel engines can and have run smoothly on bio oil, bio gas and LNG blends, Gent noted. Finding the supplies of bio oil and gas, however, is an entire different matter. This is sourced from waste treatment plants, mainly in Scandinavia, that produce bio methane or bio oil from discarded cooking oil.
The supplier network is therefore fragmented and localised, which marks a sharp contrast to the historical global supply chain of fossil oil and gas. However, high grade bio gas is very clean burning and, like bio oil, is much greener than fossil fuel sources, which makes the search for supplies worthwhile.
“With green energy, we will see an increasing a shift to local production and relatively local consumption. We look at renewable sources to make bio methane - it can be produced by using green hydrogen and we believe this is an exciting pathway to investigate. It is important to draw on our experiences and to show the market a vision of sustainability,” Gent continued.
ADVANTAGES OF LINER SERVICES
The UECC fleet operates in regular liner service in an extensive pan-European network, which is an important and helpful feature of its business. It makes it a lot easier to e.g. look for local suppliers of bio fuels and to set up the necessary infrastructure compared to vessels that operate in tramp trades.
That said, Gent expressed the ease at which the company adapted to using biofuel: “Our seafarers are amongst the best there are and we managed to take a pioneering fuel onboard our vessel and make a success of it. Many of our seagoing personnel have been with us for a long time which adds continuity to the training and high standard we are renowned for.”
8 UECC's Auto
Energy and LNG bunker vessel Coralius in December 2020
“Understanding fuel characteristics and handling them appropriately is key to a successful transition to carbon neutral transport. This can be replicated on any seagoing vessel with the right technical expertise.”
This became apparent in 2016-17, when the company introduced its first LNG power ships. The bunkering infrastructure was not readily available in each port. UECC developed their vessel in parallel with the LNG bunker vessel Green Zeebrugge and as years passed, the infrastructure across Europe has gradually expanded.
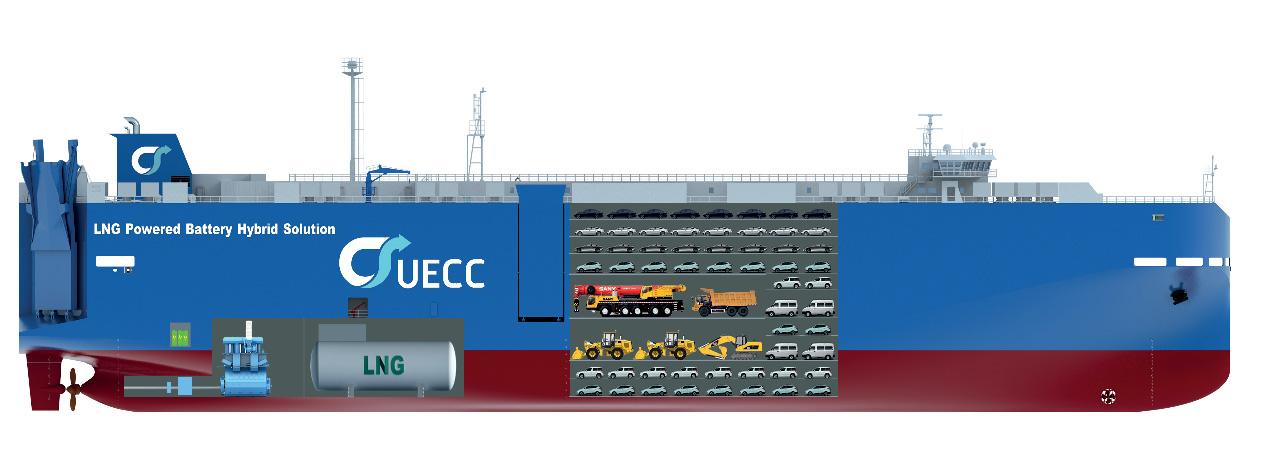
EEXI AND CII
Despite UECC's green credentials, Gent noted that the introduction of EEXI (existing ship energy index) and CII (carbon intensity indicator) rules at the IMO poses specific challenges for companies like UECC, whose ships are volume rather than dwt critical in their operations.
“On our vessel Autosky, we have demonstrated that carbon-neutral sea logistics are possible with the implementation of biofuel. Our commitment to biofuel in 2020 saw a reduction of over 20 million kilograms of CO2. We need carbon calculus that accurately capture these remarkable improvements,” Gent said.
“The index as proposed does not work at all for vessel that max out on volume: a brand-new ship can be deemed inefficient due to the current proposed methodology. Using gross tonnage as the base of the index for such ships would make more sense,” he said. “We have seen that exceptions exist in other maritime sectors and we strongly support IMO looking again at ours.”
Gent mentioned a case regarding CII, in which a ship sailing between two ports at 15 knots can perform worse than one that covers ten times the distance at 13 knots, because of the impact of slower speeds on index calculations.
“IMO holds the key and bureaucratic processes are slow. Once legislation has been passed, it has hardly ever been revised, so it is important to get everything as right as possible from the start,” he continued. The planned legislation is due to take effect in 2023 and time is passing quickly.
Any revision to the proposed legislation should really be made this year to take into account the slow decision making at IMO. “We are in the future now. We need to talk,” Gent said.
UECC, which is jointly owned by Wallenius of Sweden and Nippon Yusen Kabushiki Kaisha (NYK) of Japan, regards itself as a pioneer in efforts to make shipping greener and more sustainable. The nature of its business makes it well positioned to explore new technologies, but it is its willingness to make bold investments and to learn from each step that it takes what makes progress on that path possible, Gent highlighted.
2
4TO
NOV 1 Hamburg Germany
CALL FOR PAPERS
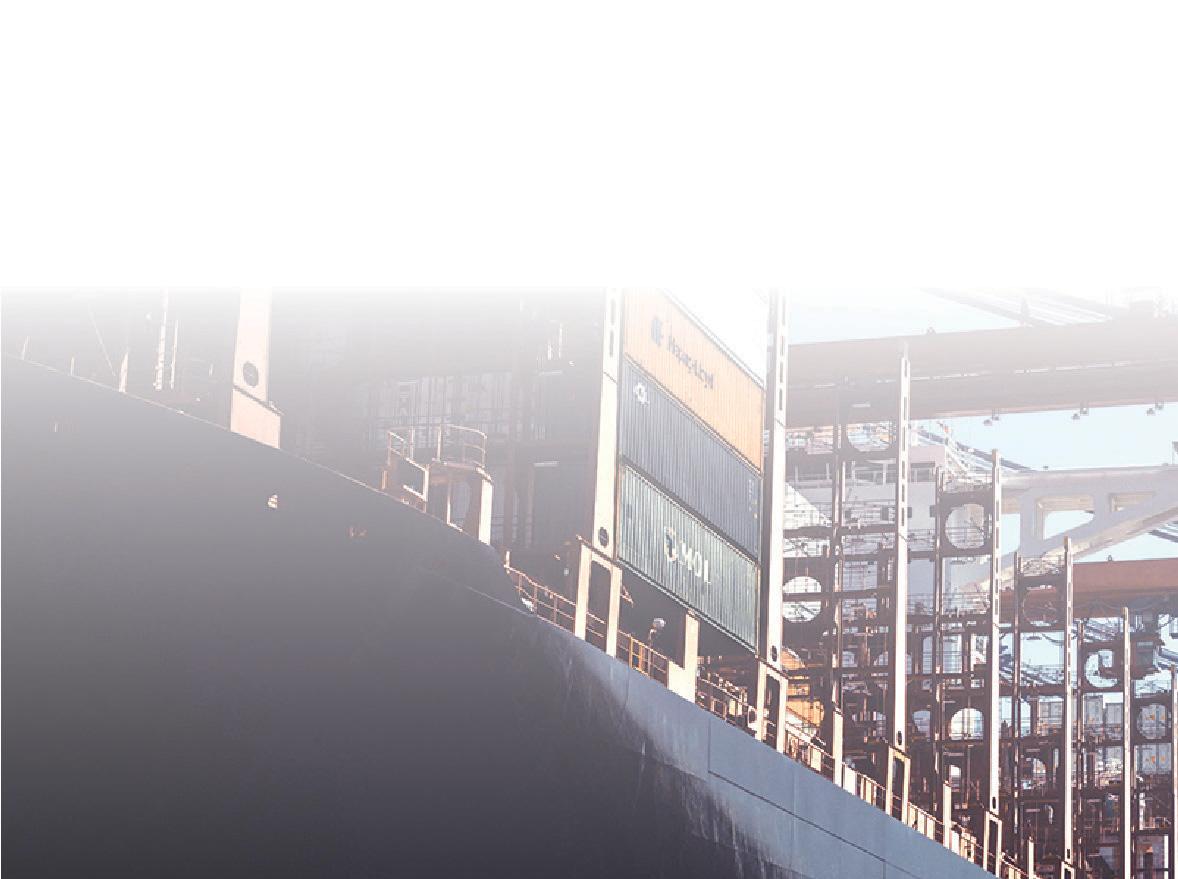

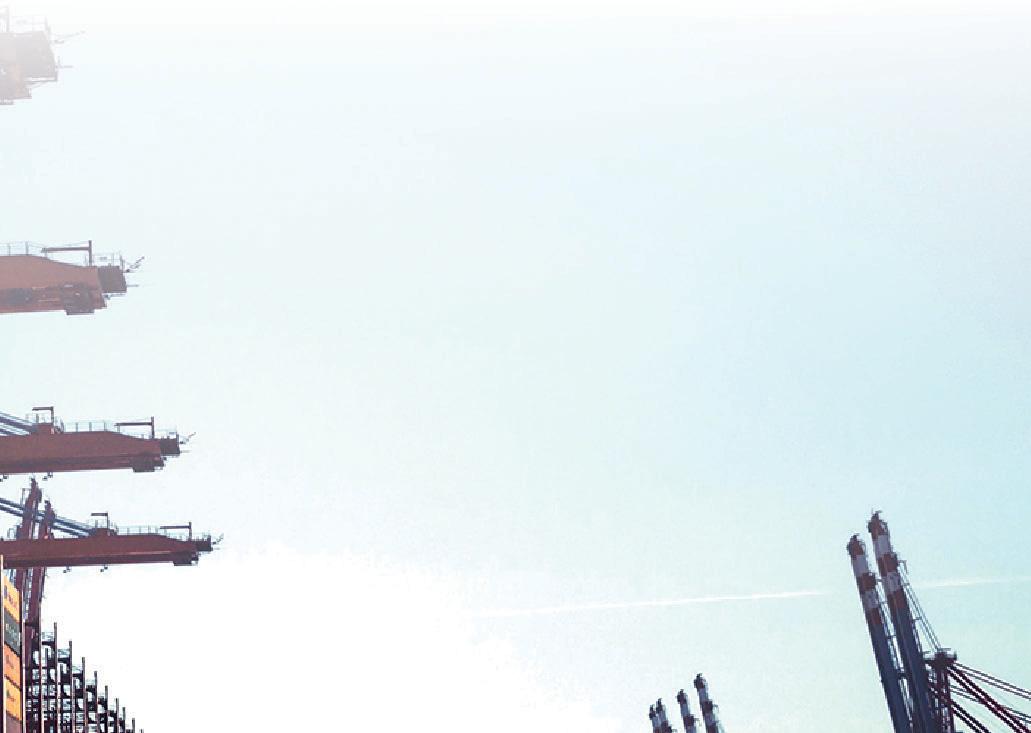
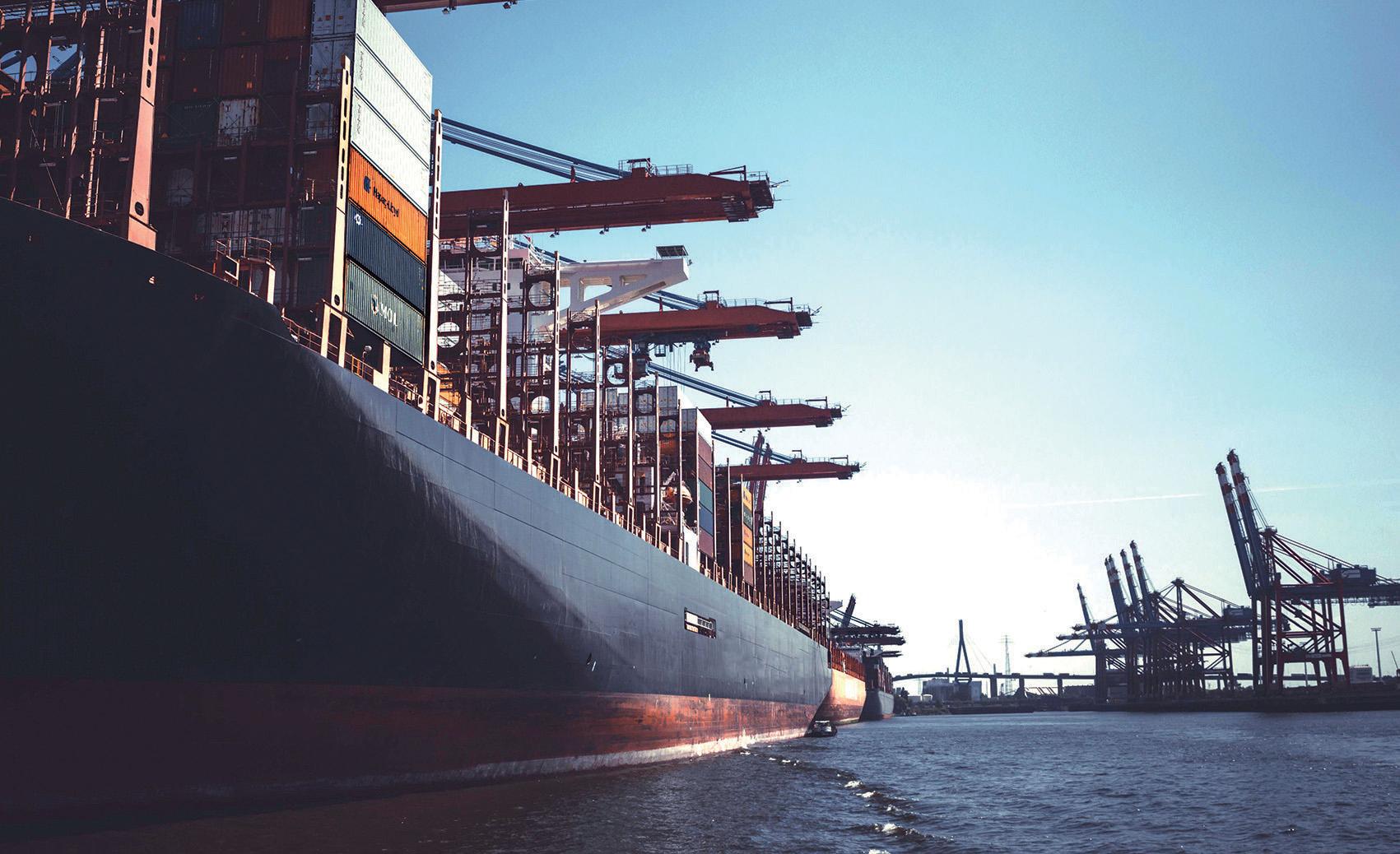
8 Integrating an
ESS and shaft generator into the hybrid dual-fuel PCTC design allows the vessel to reduce the number of auxiliaries to two
Submit your abstract on:
6 6 6 6 6 6 6
Abstracts of 250 words with speaker biography, headshot photo and company logo to be sent to conferences@ propulsionconference.com by 5 April 2020. For further details on sponsorships or attending the 42nd Motorship Propulsion & Future Fuels Conference please contact Brand manager Toni Sibley tsibley@motorship.com or call +44 1329 825335.
#MotorshipPFF
Sponsored by:
SILVER SPONSOR
Supported by: Organised by:
MOTORSHIP
INSIGHT FOR MARINE TECHNOLOGY PROFESSIONALS
FIRST DEMONSTRATION OF MAN LOW-PRESSURE ME-GA ENGINE
Engine designer MAN Energy Solutions held a public demonstration of its new low-pressure dual-fuel engine platform at its Copenhagen Research Centre in mid-March 2021
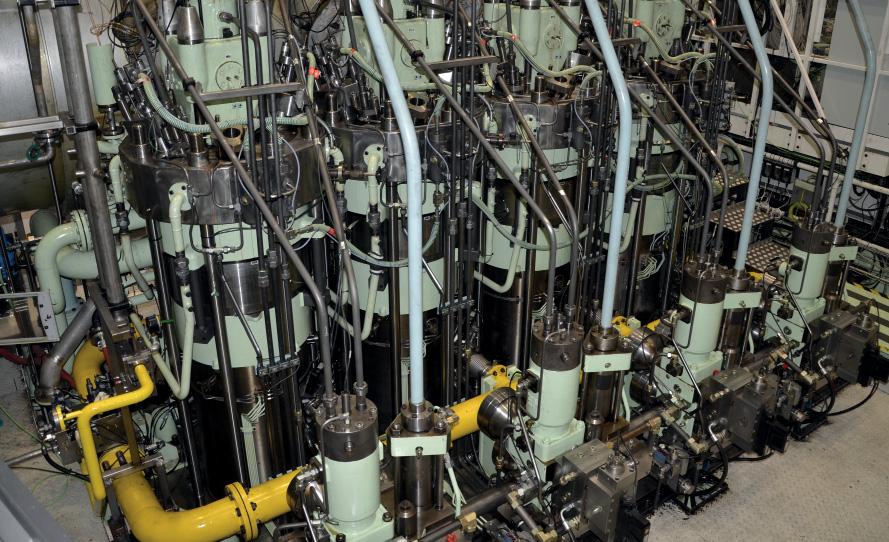
The demonstration, which was held remotely to comply with Covid-19 public health requirements, was accompanied by the announcement of the fi rst orders for the company’s new Otto Cycle engine platform.
Bjarne Foldager, Senior Vice President and Head of TwoStroke Business, revealed the ME-GA engine had already been specified in several LNG carrier newbuilding projects. The details of the first of the projects will be revealed by mid-April.
The timeline for the commercial launch of the Otto Cycle engine has remained largely unchanged, despite the disruptive effects of the Covid-19 pandemic on collaboration with engine licensee HHI-EMD and with Hyundai Heavy Industries' shipyard division.
The testing of the first, commercial ME-GA design is expected to begin by the end of 2021, with the first engine delivery following in early 2022.
The response from other shipyards in Korea and East Asia had also been encouraging, Foldager noted.
This was no surprise, as the new engine platform had been designed with commercial as well as technical requirements at its heart. The 700mm bore design retains the same outline and footprint as a G70ME-C10.5 engine. The five cylinder version of the 700mm bore G70ME-C10.5-GA is explicitly aimed at the LNG carrier market, where twin five-cylinder 700mm bore engines are frequently specified.
Shipyard considerations were also reflected in the choice of a high-pressure EGR solution. The solution could be integrated into existing engine-room designs, while the EGR unit itself does not change the engine footprint.
However, the MAN B&W ME-GA engine is also being aimed at other vessel types and applications, where low capital outlay is a priority. These include Aframax tankers, for example. The company plans to add a 500mm bore version of the engine - S50ME-C-GA - to its engine programme alongside its existing 700mm bore G70ME-C10.5-GA and 600mm bore G60ME-C10.5-GA options.
However, Wayne Jones OBE, Chief Sales Officer, confirmed to told The Motorship that the company was considering developing other engine sizes.
Foldager noted that the company had no plans to develop a larger 950mm bore version of the ME-GA. The technical challenge of developing a 950mm-bore Otto Cycle engine was significantly greater than simply scaling up a 700-bore engine. He added that as MAN ES’s ME-GI high-pressure dual-fuel engine was frequently specified by shipyards for ultra large container vessels newbuildings, there was little commercial demand for such a development.
TIER III COMPLIANT OPTIONS
The presentation confirmed many of the details released during earlier stages of the product development cycle. As previously reported, the engine will be Tier III compliant in gas mode without emissions abatement equipment.
Meanwhile, specifying the exhaust gas recirculation (EGR) option would ensure the engine met Tier III requirements in both fuel oil and gas modes without additional aftertreatment. The exhaust gas recirculation aftertreatment option would lower the engine’s methane emissions by between “30-50%”.
8 The MAN B&W
ME-GA engine (pictured) at MAN Energy Solutions’ Research Centre Copenhagen
The company reports that EGR will enable the ME-GA to reduce specific gas consumption by around 3%, and specific fuel-oil consumption by 5%.
The EGR aftertreatment option offers particular advantages for fuel consumption at part-loads within the load range.
Thomas S. Hansen, Head of Two Stroke Promotion & Customer Support, noted that this improvement was seen in the engine for both specific fuel oil consumption and for specific gas consumption. Hansen cited the MAN B&W MAN B&W G70ME-C10.5-GA, which lowered SFOC by 7.4g/kWh to 170.1g/kWh at 50% load in Tier II mode, compared with the low-pressure SCR version. A similar reduction of 5.6g/kWh was seen at 75% load.
Comparable reductions in SGC were seen, with gas consumption lowered by 6.8g/kWh to under 134g/kWh at 50% load in Tier II mode, compared with the low-pressure SCR version. A similar reduction of 5.1g/kWh was seen at 75% load.
One particular area of focus has been the pilot fuel oil consumption, given its connection with NOx emissions in gas mode for Otto Cycle engines. In gas mode, the ME-GA engine required no more than 0.5% pilot fuel consumption.
The ME-GA design also included a microbooster system, which allowed high sulphur fuel oil to be used for pilot fuel injection in Tier II gas mode, Hansen confirmed during the presentation. Hansen that several of the ME-GA’s design features offered opportunities to bear down on CAPEX costs during the newbuilding process. He gave the example of the separation of the Gas Valve Unit from the Gas Regulating Unit within the design. By locating the GVU outside the gas safe area, this eliminated the need to install a cofferdam box in the engine room, as the unit did not need to be specified to comply with gas safe area rules.
Hansen also identified the ME-GA’s purging concept as an area where the application of ME-GI concepts led to CAPEX reductions. Rather than injecting nitrogen from the GVU, the nitrogen is applied at the engine end, and the purged volume is carried along existing piping. The simplified solution reduced the amount of pipework and components, and significantly lowered the volume, reducing nitrogen consumption, Hansen noted.
Hansen noted that the engine also employed a safe gas admission valve, placed on the manifold and exhaust side of the cylinder. By being located close to the cylinder, it minimises the potential volume that could enter under the piston case in case of a release. The valves also have a window valve function.
Hansen confirmed that the standard 3 piston-ring package used on ME-GI engines was being applied to the ME-GA design. MAN had gained considerable experience with the CERMET coated ring pack concept in service on existing G70 engines.
Hansen noted that the ME-GA engine was expected to have similar cylinder oil requirements as the existing ME-GI engine. While MAN ES would recommend the use of a BN40 Category II cylinder oil as soon as one became available, a BN100 Category II cylinder oil.
Engine
Bore
MAN B&W G70ME-C10.5-GA MAN B&W G60ME-C10.5-GA
700mm 600mm
Stroke
Stroke/bore ratio
3,256mm 2,790mm
4.65 4.65
Power per cylinder, L1 rating 2,830kW @78rpm 2,080kW @91rpm
Power/cyl, L2 rating
Power/cyl, L3 rating
2,260kW @78rpm 1,660kW @91rpm
2,400kW @66rpm 1,760kW @77rpm
Power/cyl, L4 rating
1,920kW @66rpm 1,410kW @77rpm
Mean effective pressure, L1 rating 17.4 bar 17.4 bar
Engine versions, cylinder numbers 5, 6 5, 6, 7, 8
Power range(SMCR), 5cyl model 9,600-14,150kW 7,050-2,080kW
Power range(SMCR), 6cyl model 11,520-16,980kW 8,460-12,480kW
Power range(SMCR), 7cyl model
9,870-14,560kW
Power range(SMCR), 8cyl model
11,280-16,640kW
8 Principal
particulars - MAN B&W ME-GA engine
Putting the market at the heart of MAN ES’ programme
Speaking just after the fi rst demonstration of MAN Energy Solutions’ new low-speed, two-stroke Otto Cycle engine platform on 18 October, Wayne Jones OBE, Chief Sales Offi cer, discussed the ME-GA project and wider market trends.
“Speaking as an engineer by training, technology and R&D is the lifeblood of a company like MAN Energy Solutions,” Mr. Jones said. However, bringing new engine platforms like the ME-GA to the market represents a significant investment in terms of time and resources.
The company had 150 engineers working on the project and conducted over 800 tests at the Research Centre Copenhagen.
This connection with the market comes from MAN ES’ strong partnerships and relationships, with shipyards, with engine licensees, and with shipowners in pilot projects. But it also comes from the company’s own connections with the market, which extended well beyond the commercial side of the business.
Mr. Jones said that it was a source of pride that MAN’s high-quality engineers were all grounded in commercial realities. “Our R&D is not internally focused but client-led.”
This outward-facing approach was an integral part of the ME-GA project from its initiation in late 2017 when demand for a lower-cost alternative to the ME-GI engine, primarily from the LNG carrier market, began to make itself felt. elt.
As such, Jones took as much pride in es took as much pride in announcing that MAN ES’ new Otto Cycle t MAN ES’ new Otto Cycle engines had been specified in multiple en specified in multiple newbuilding projects as in the successful ojects as in the successful public demonstration of the engine itself. tration of the engine itself.
This market-led approach was more ed approach was more important than ever as the industry ever as the industry undergoes what Mr Jones called “an ultimate t Mr Jones called “an ultimate change”. Decarbonisation and digitization are bonisation and digitization are set to transform the industry. The changes of m the industry. The changes of the energy transition were also being felt in sition were also being felt in individual trades, with the expansion of s, with the expansion of existing trades such as methanol. such as methanol.
Mr Jones concluded by noting that the cluded by noting that the delivery of the latest addition to MAN ES’s dual-fuel portfolio demonstrated the company’s ability to deliver technically-challenging solutions that meet client needs. “We didn’t see anything that surprised us [during the ME-GA development],” Mr. Jones concluded.
A reassuring thought, as many of the solutions to the industry’s decarbonisation challenges lie in the hands of companies challenges lie in the hands of companies like MAN ES. like MAN ES.
