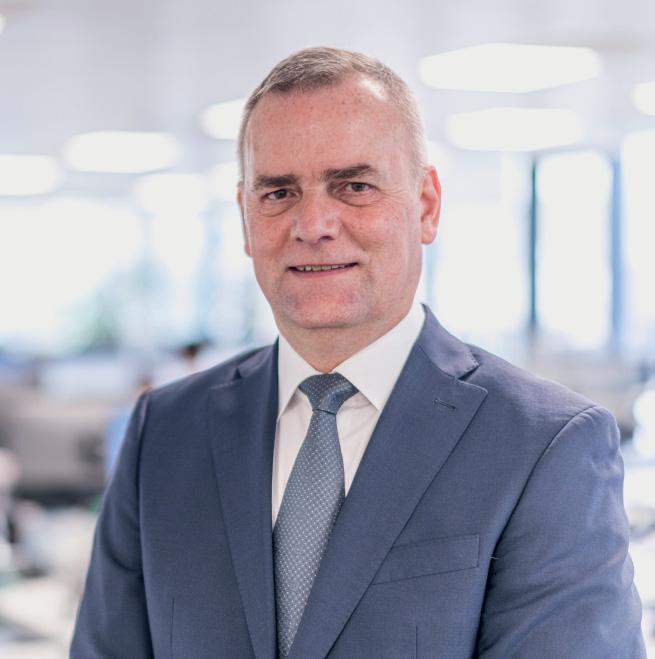
45 minute read
Caveat operator
VLSFO MAY STILL ADD TO NEW FUELS' DISRUPTION
More problems are anticipated with VLSFO this year, adding to the potential of new fuels to “disrupt” the industry ahead of 2030 and 2050
“There will be very exciting years to come,” says Søren Høll, CEO of marine energy services provider KPI OceanConnect. “We have now overcome the 2020 mountain, and we can see the 2030 mountain and 2050 mountain ahead of us.”
However exciting the future though, he warns that the 2020 mountain may not be completely behind us yet. Through 2020, only 55 cases of 0.50% compliant fuel being unavailable had been reported in IMO's Global Integrated Shipping Information System, and there have been fewer quality issues than many analysts predicted. However, potential issues may have been partly masked by the pandemic and depressed oil prices. More challenges may arise once the world starts to recover from Covid-19 and distillate demand and prices increase in other industries besides the bunker industry - and if unscrupulous suppliers start using cheaper components for blending, says Høll.
Bharath, Technical Manager for Singapore-based bunker testing house Maritec, says that around 95% of VLSFO samples tested on a monthly basis are within ISO standards. “Of late, there are quite a number of cases where the fuel, despite meeting ISO specifications, is still found as unstable due to the nature of the blend or chemical contaminants/ deleterious substances that were detected. For the latter it is worrying to the vessel operator, as there are few countermeasures available to combat the issue.” He says one option is to dilute the fuel with a suitable bunker. “We have seen vessels suffer excessive wear to fuel injection components, total breakdown of fuel purifiers, sludging of fuel system filters and pipes, to name a few. In worst case scenarios we have seen the vessel debunker the fuel.”
MEPC75 has clarified the 0.5% sulphur cap by defining the sulphur limit according to the specific sampling location. The MARPOL delivered sample will continue to have a sulphur test result limit of 0.50% maximum. “Due to the inherent variance in the test results, suppliers now need to have a lower blend target with respect to sulphur content (ideally below 0.47% m/m),” says Bharath. There is a leeway to the in-use and on board samples to have the sulphur test result limit of 0.53% maximum.
“We advise not to accept any argument from suppliers with regards to the 95% confidence boundary of 0.53% when tested sulphur content of lab samples sourced at the manifold exceed 0.50% m/m,” says Bharath. “Your MARPOL delivered sample may very well be above the limit when it is from the same primary source during future verifications by the administration. Moreover, a higher sulphur content at the manifold inlet will raise the probability of in-use and on board samples testing above the 0.53% limit.”
NOT JUST VLSFO
Bharath foresees potential challenges with microbial growth and the oxidative and long-term stability of biofuels. “Biofuels may require a cleaner environment and to be kept away from moisture sources (of which there is plenty at sea.) There might be a need to periodically test the fuel as long as it is in storage to check its viability either by onshore lab tests or onboard test kits.
“Like any clean fuel, biofuels have the tendency to flush out the previous fuel in use, and this will be an issue when changing over the plants. It has a higher wax forming temperature than conventional diesel oil which might pose some risk to the fuel gelling at lower temperatures. Due to the acidic nature of the fuel, there might be compatibility issues with the materials used throughout the fuel systems. Specialised tank and pipeline coating might be required. Fuel injection and combustion equipment materials will need to be assessed if they can sustain long term contact with the fuel.”
THE GOOD NEWS
Dirk Kronemeijer, CEO at sustainable biofuel company GoodFuels and sustainable supply chain advisory GoodShipping, says there have been only a few filter clogging problems during fuel switchover in the last couple of years, and the root cause is linked to the fossil fuels used before. “Once the fuel system is clean, no sediments can be soaked off anymore and no problems will occur.”
Regarding higher wax forming temperature, he says that some biodiesels have cold flow properties that meet the winter quality requirements of certain countries, for example the Netherlands. Meanwhile, some biodiesels have cold flow properties that are well above zero degrees Celsius.
8 Søren Høll, CEO of marine energy services provider KPI OceanConnect
Fuel injection and combustion equipment materials will need to be assessed to ensure they can sustain long term contact with the fuel. “There are indeed compatibility issues with some materials. However, this is not per se linked to the acidic nature of biodiesel. The acidity of biodiesel can even be lower than the acidity of mineral diesel. The parts in the fuel system that are incompatible with biodiesel are often small components like rubber seals. Most of our customers did not have to replace anything in their fuel system to be compatible with biodiesel.”
Typically, when using GoodFuels' biofuels, the CO2 footprint of a voyage is reduced by between 80-90% (wellto-propeller). The biofuels are not considered to be 100% carbon neutral as the calculation includes emissions generated by the transport and production of the biofuels, according to the Intergovernmental Panel on Climate Change's definition. GoodFuels uses waste and residue streams that would be otherwise burnt as feedstock.
“As we produce biofuels that are sustainably sourced and completely derived from sustainable waste and residue products, we continue to work to scale up biofuel production. We are confident that with targeted growth, we can ensure that the maritime industry has all of the sustainable biofuel that it needs, as part of an alternative fuel mix towards decarbonisation,” says Kronemeijer.
“It's a genuine triple-win for shipowners at the moment, as biofuels are the fossil-free equivalent and virtually sulphur free (therefore offering compliance for IMO 2020),” he says. They are competitively priced and eliminate carbon thereby setting up shipowners/operators to meet the 2030 and 2050 targets. “Other future fuels are important, but advanced biofuels are a 'today' fuel, allowing instant decarbonisation impact.”
EYES ON AMMONIA
Carbon Neutral Consulting (CNC) has said it believes ammonia is a game-changer for the maritime industry. Principal Milton Bevington says: "In game theory, a 'dominant strategy' is a strategy that leaves you better off no matter what your competitors do in response. Dominant strategies are rare in business contexts because we're usually faced with options that have an upside if our competitors react one way and a downside if they react in another. Right now, for companies in the maritime sector, an ammonia-oriented action plan comes very close to being this kind of 'dominant strategy,' a business plan that enables commercial success across a period of intense disruption regardless of the actions of your competitors.”
Like LNG, ammonia is a good transition fuel in that it meets all current IMO2020 requirements for emissions and is priced competitively with cleaner burning distillates like MGO, says Bevington. “Once IMO-mandated emissions tighten, electrolytic ammonia can be produced using carbon-free renewable energy (wind, solar, hydro), and vessels equipped with ammonia propulsion systems can simply switch from conventionally produced ammonia to green ammonia without any further capital investment or risk of stranded assets. Ammonia has the singular virtue of being both a viable transition fuel and a long-term zero-emission solution, and investing in it early protects the asset value over its full economic life, which can be 30 or more years in many cases.”
Availability is already being increased. In February 2021, Yara International signed a Letter of Intent with Statkraft and Aker Horizons to establish Europe's first large-scale green ammonia project in Norway. The partners will target green hydrogen and green ammonia opportunities within shipping, agriculture and industrial applications by electrifying Yara's existing ammonia facility in Porsgrunn.
Shipping currently accounts for 2% of global GHG emissions, of which long-distance shipping represents 80 percent. Yarra anticipates that converting all long-distance shipping to ammonia would require approximately 500-600 million tonnes of ammonia annually, 3-4 times the current world production.
Integrated energy company, Mabanaft is ramping up its stake in ammonia as a future marine fuel. The company will be marketing 500,000 metric tons ammonia per year from a production plant in Texas. “We see ammonia as the best zero carbon fuel in shipping, building on existing infrastructure and existing merchant ammonia trade flows. There is not enough biomass and not enough e-fuels production capability soon enough to play a role for ocean transportation,” says Oleksandr Siromakha, Head of Sustainable Fuels.
“The availability of green ammonia (produced from renewable electricity) will substantially increase in the future. However, already today grey and blue ammonia (produced from natural gas, and in case of blue ammonia carbon emissions are captured and stored) represent a feasible alternative to substantially reduce the emissions from shipping and to speed up the decarbonization of ocean transportation.”
Yet, challenges remain. A panel discussion held by the Ammonia Energy Association late last year acknowledged that ammonia users face relatively high fuel costs and a lack of infrastructure in the short-term. Despite this, when polled, the audience and panellists expected rapid development of the fuel resulting in around 30 ammonia-powered vessels being in operation by 2030.
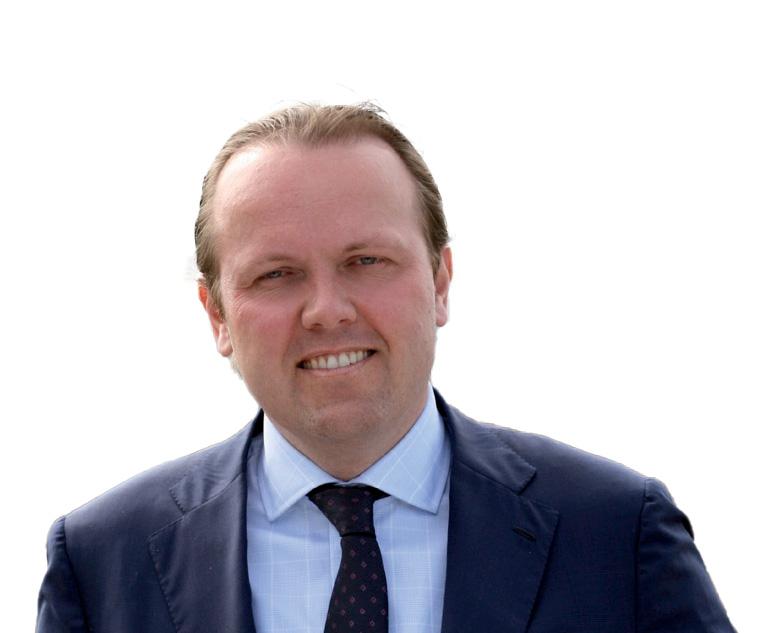
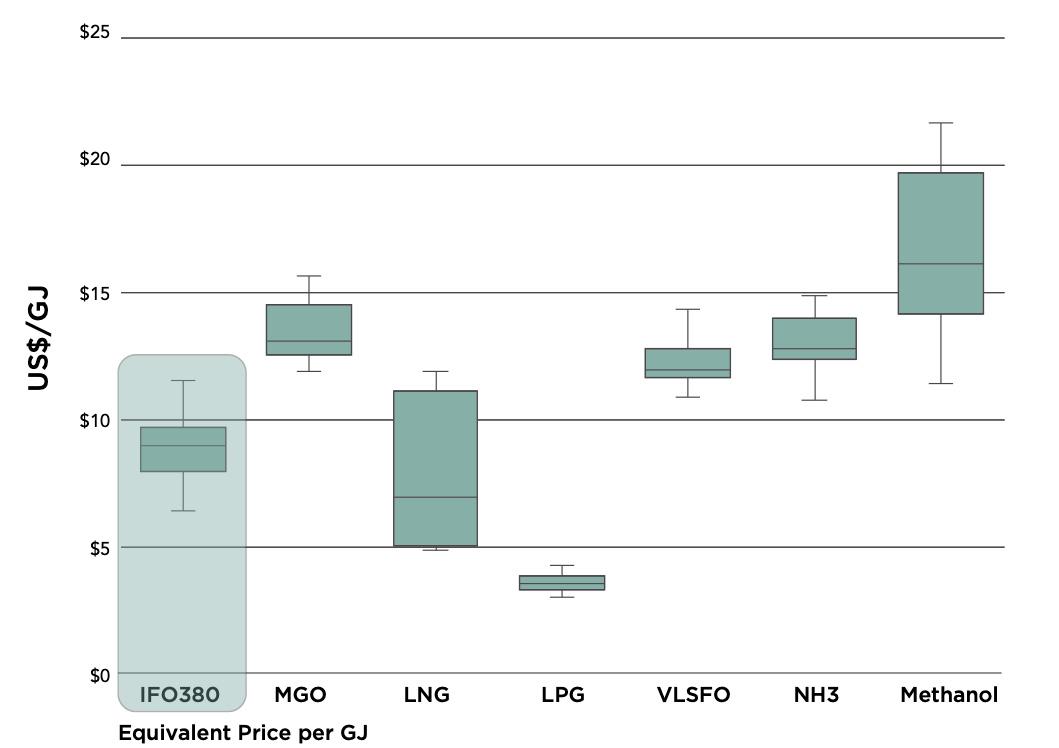
nd stored) represent a feasible ly reduce the emissions from e decarbonization n. A panel monia Energy knowledged elatively high rastructure in this, when nd panellists ment of the d 30 ls
8 The Ammonia Report Fuel Price Comparison Chart
For the three years (2017-2019) preceding the coronavirus outbreak, the strike price of various bunker fuels strongly suggests that ammonia can be competitive with low-sulphur options currently under consideration
8 Dirk Kronemeijer,
CEO at sustainable biofuel company GoodFuels
CYLINDER LUBRICATION DELIVERY FLEXIBILITY FOR TWO-STROKES
The shipping industry's ambitions for reducing CO2 emission are likely to follow several technological pathways, so a more fl exible and modular lubrication system is now available, says Dr Rathesan Ravendran, Technology and Innovation Specialist at Hans Jensen Lubricators
There is a paradigm shift underway that aims to make the maritime industry more environmentally friendly. As part of this, the drive towards higher effi ciency has led to design changes in slow speed two-stroke marine diesel engines, the most signifi cant being the application of the electronical-controlled, supercharged and long-stroke engine, which allows more fl exible usage and higher combustion pressure.
There is a paradigm shift underway that aims to make the maritime industry more environmentally friendly. As part of this, the drive towards higher efficiency has led to design changes in slow speed two-stroke marine diesel engines, the most significant being the application of the electronicalcontrolled, supercharged and long-stroke engine, which allows more flexible usage and higher combustion pressure.
These changes in engine design as well as the way engines are being run have led to challenges when it comes to cylinder condition and lubrication, because the lubrication systems and methods delivering cylinder oil to lubricate piston rings and cylinder liner have remained largely unchanged.
LUBRICATION CHALLENGES WITH LOW SULPHUR FUELS
A large majority of the vessels made the transition to lowsulphur fuel well. However, as anticipated, a number of issues was observed on several vessels. High cylinder liner and piston ring wear, severe scuffing, heavy deposits and piston rings sticking leading to heavy blow-by/ring breakage, were some of the issues occurring just a few days after changing over.
The lower lubricity of low sulphur fuels has been made up for by cylinder lubrication oil, distributed correctly on the cylinder liner. Using a low 15-40 BN cylinder oil is currently the most widespread countermeasure adopted. However, using low BN oils creates new and other challenges, since the cleaning ability of the cylinder oil is not sufficient to keep the cylinder and piston clear of deposits, which potentially can lead to increased wear, bore polishing and scuffing.
A common procedure when observing high wear rates is to increase the cylinder lubrication oil feed rate, but this is not always the right solution. Increasing the dosage of lubrication oil does not mean less frictional losses and wear. It can be as damaging as low oil dosage, as calcium deposit formation (unused BN additives), is naturally increased with the lubrication oil consumption.
Operators are also advised that higher BN cylinder oils are needed to keep the cylinder clean from deposits, but attention must be paid to secure against cylinder liner bore polish. When using a high-BN cylinder oil, the risk of top land calcium deposits increases. The calcium deposits may polish on the cylinder liner surface and cause polished areas which can initiate a cylinder liner scuffing.
To improve the cylinder condition in terms of cleanliness and deposit control, a number of tools have been recommended by OEMs and lubricant suppliers. Coated piston rings have become standard for every engine types. The coatings have higher melting temperature and hardness compared to standard aluminium coated piston rings, which ensures an increased safety margin against scuffing as well as low wear of the coating. Engine designers also recommend changing the piston configuration to three piston rings in order to minimize the deposit build-up between the rings.
New cylinder oils have been introduced by lubricant supplies, which have improved their formulations with ashless additives increasing the dispersancy for better cleaning ability. A less practical approach for improving the cleanliness with traditional cylinder oils is manual alternation between low and high BN oils. This method is proposed to create a balance between the limited neutralization of sulphuric acids and having a sufficient deposit control. As an alternative to the manual BN alternation, an automatic cleaning sequence has been incorporated in lubrication systems which periodically increases the cylinder oil feed rate to facilitate better cleaning of the cylinder. For short periods, the additional oil is injected into the piston rings in order to react with and flush out deposited particles.
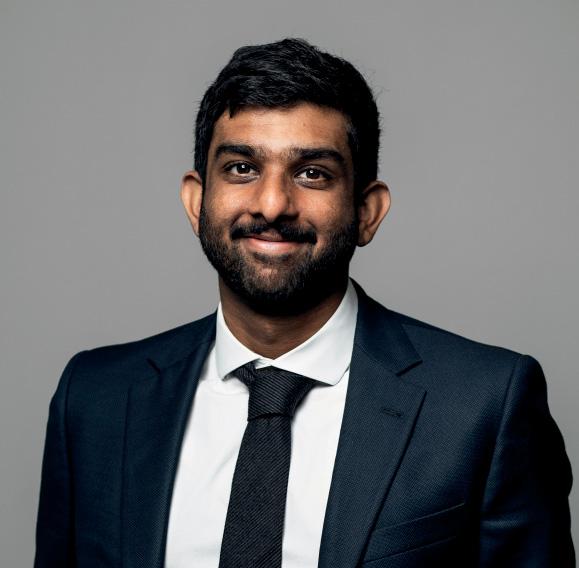
8 Dr Rathesan
Ravendran, Technology and Innovation Specialist at Hans Jensen Lubricators
THE GROWING IMPORTANCE OF SERVICING
Lubricating two-stroke marine diesel engines has become more complex over the years, as the engines are operating
under more demanding conditions and must be capable of using different fuel types. About 54% of vessels in operation today are not optimally lubricated, which could have a longterm impact on the engine’s lifespan, components and drydocking intervals. Selecting the optimal cylinder oil type and the feed rate is not easy, as it depends on multiple factors e.g. fuel quality, engine type, size and operating conditions. Furthermore, a large variety of different lubrication oil formulations have been introduced, which may be difficult to navigate through. This places a great challenge and burden on engine operators, as they must ensure good main engine condition as well as reduce operational expenses.
Lubrication systems have become more flexible over the years, but this also creates more complexity for the endusers. Firstly, there is added complexity with the possibilities of the system. Experienced and trained crew are required to operate the system, which is today a challenge on the majority of the vessels.
Secondly, there is also added complexity in terms of more advanced parts and critical components. This sets a great challenge of proper operation and service. A survey conducted by The Swedish Club has shown that most main engine claims are as a direct and indirect result of incorrect maintenance. Numerous cases have been noted where damage occurs shortly after the engines have been overhauled by ship or shore staff. This emphasizes the importance of correct training and maintenance. The lack of training and planned equipment maintenance is often the issue, when vessels are not achieving the full potential of the lubrication system with regards of optimal lubrication performance and minimum lubrication oil consumption.
Today, the recommended minimum lubrication oil consumption is 0.60 g/kWh. However, practical studies by Jensen et al. (2016) have shown that the minimum oil dosage can be reduced to a new minimum using the HJ SIP lubrication system. Such low lubrication oil dosage has not previously been recommended and used in practice. The studies showed that the recommended minimum could be reduced to a feed rate of 0.30 g/kWh, and at the same time even lower wear rates could be maintained. It is therefore believed that there is room of optimization of lubrication oil consumption, and that the limits will be pushed with newer lubrication technologies and injection methodologies.
A NEW PARADIGM IN LUBRICANT FLEXIBILITY
Today’s changes in engine design and operation due to the environmental legislation are just the tip of the iceberg, and further optimization will be seen in the maritime industry. New technologies and methods for achieving optimal cylinder condition will be introduced. Digitalization and condition monitoring will be an important information source for early machine failure detection just like the role of the human blood sample testing in order to perform disease detection. The condition of lubrication oil and its circulation system reflect the health status of the machinery and its components. Furthermore, more flexibility and modularity in the lubrication system will be added to deal with the constantly changing engine operation and the availability in a variety of carbon-free fuels.
Beyond the 2020 requirements, the future direction of new fuels for the shipping industry is largely insecure. There is an ambition to reduce CO2 emissions, but there are several technological pathways to achieve this. It is therefore necessary to have a flexible and modular lubrication system, that is able to handle different situations. This has led to the introduction of a new approach for delivering the cylinder oil, which is currently the most flexible system available compared to all other current systems and making it compatible to all engine configurations and operations (scrubbers, LSFO, LNG, other).
The system is HJ Smartlube 4.0, which is invented by Hans Jensen Lubricators. The system consists of a solenoid valve controlling the opening and closing of the valve. The hydraulic system comprises a frequency-controlled motor pump unit to build the common rail pressure and a pressure sensor to maintain correct pressure level of the cylinder oil. The electrical control system uses an Ethernet protocol for all signal communication, ensuring a thoroughly standardized and robust network with high bandwidth and low latency.
With the possibilities of advanced control such as multitiming on individual valves, optimal utilization of the cylinder oil is achievable, which will lead to less cylinder oil consumption and better cylinder condition. Direct control of the valves means more accurately timed injections as there is minimal hydraulic delay from signal to injection. This gets the cylinder oil to the intended target and will lead to a higher utilization of the cylinder oil.
Very small amounts can be injected while maintaining good spray quality. This makes the system able to deliver oil every revolution, or even multiple times per revolution (multi-timing). Multi-timing allows cylinder oil to be placed both on the liner surface above the piston and between the piston rings in the same revolution. The quantity can be adjusted between injections, enabling advanced multi-timing control.
CONCLUDING REMARKS
In recent years, changes in engine design as well as the way an engine is being run have led to challenges when it comes to cylinder condition and lubrication. Today, it is necessary to pay more attention to the cylinder lubrication system’s operation and service to achieve optimal cylinder condition, and the introduction of a new approach for delivering the cylinder oil has now been developed by Hans Jensen Lubricators.
Feed rate [g/kWh]
1.2
1
0.8
0.6
0.4
0.2 Recommended feed rate
Possible reduction?
0 1990 1995 2000 2005 2010 2015 2020 2025 2030 Year
8 History of
the minimum recommended feed rate for two-stroke marine diesel engines and the possibility for optimization
8 The development
in lubrication technology

SHIPYARD INERTIA SLOWING WATER LUBRICATION UPTAKE
Shipowners want to return to a water lubricated propulsion arrangement, but shipyards are preventing the wider take up of the environmentally sustainable solution, writes Patrik Wheater
That was the opinion of some of the panellists speaking at an online webinar hosted in late February in which representatives from oil supplier Gulf Marine Oil, polymer bearings pioneer Thordon Bearings and shipmanager Delta Corp Shipping discussed the merits of oil lubricated and water lubricated propeller shaft.
All three representatives appeared to agree that the water lubricated approach represented a better solution, although there were differences of opinion when it came to technical performance and pollution data.
Gulf Marine Oil's technical director Don Gregory, for instance, was sceptical of the statistics, dismissing data compiled by New York-based Environmental Research Consulting that found 240 million litres of operational oil escape from ships annually.
Gregory offered a lower estimate of the amount leaked: 10 litres per month per ship, he claimed. Clearly, more research into sterntube oil consumption and pollution is needed. But even based on Gregory's trickle, it amounts to yearly 6 million litres of oil spilling into the marine environment, based on 50,000 ships in the commercial shipping fleet.
Quantity aside and admitting that oil losses do occur from
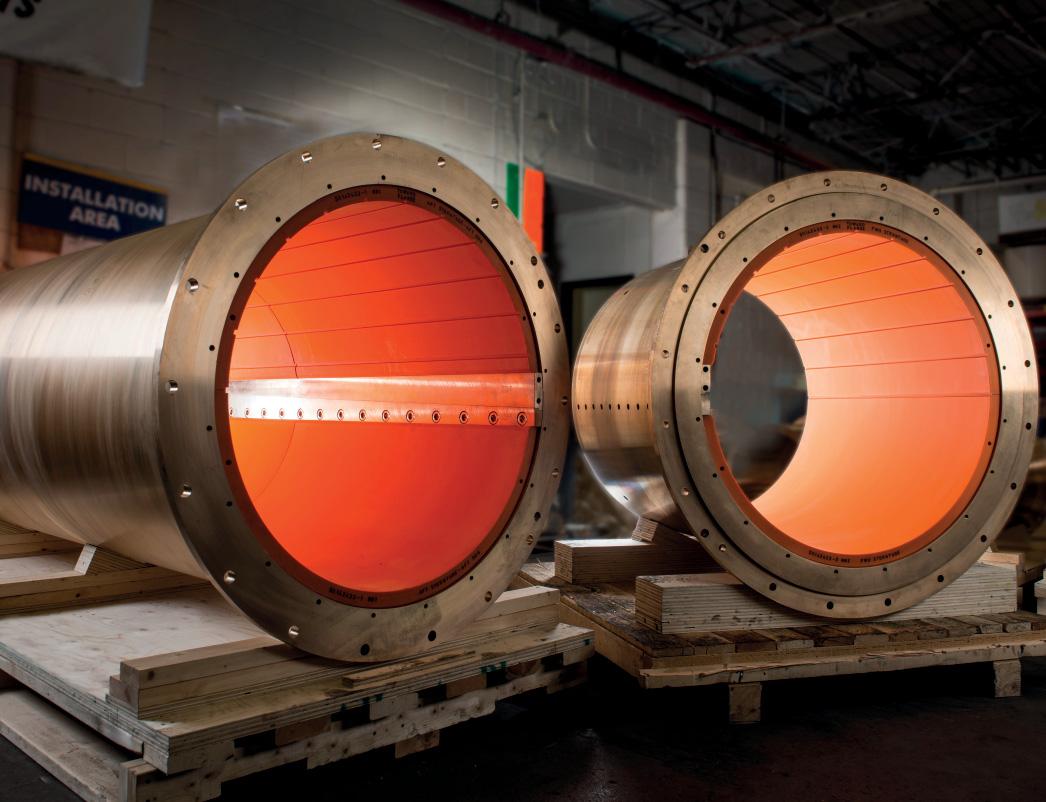
Credit: Thordon Bearings
stern seals with the “flexing of the shafts”, Gregory, said water lubricated propulsion is gaining ground. “Costs seem to be driving the sterntube more to water lubrication. It appears water lubrication is turning back history,” he admitted.
All parties agreed there are technical merits to both solutions, largely dependent on the type of vessel and the operational profile - whether it is slow steaming, for instance.
Caroline Hout, Senior VP Shipmanagement, Delta Corp Shipping - a company with more than 50 vessels under its charge - acknowledged the possible long-term operational cost benefits of water lubricated propulsion but asked about the technical complexity involved in the transition from oil to water.
“Until now I have only experienced an oil lubricated system [but] I am interested to know about the shipyards proposing this technology. The question is when you look at water lubricated shafts, are the guarantees sufficient?” she asked.
While Chinese yards are successfully delivering water lubricated newbuilds, George Morrison regional manager, Thordon Bearings, suggested that on the whole shipbuilders are blocking the wider return to water lubricated propulsion - a solution common to most ships until the 1950s.
8 Composite
bearings and housings
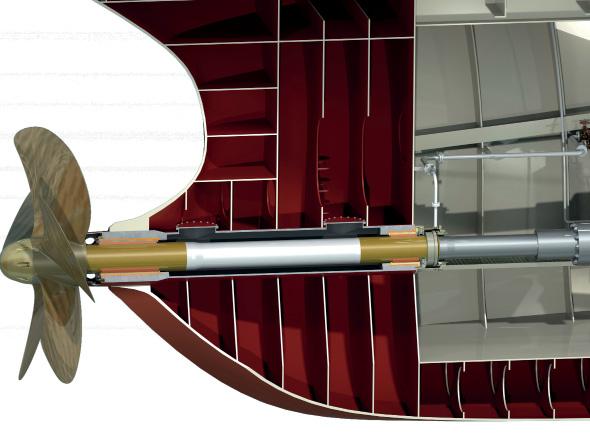
“You touched on the relationship with the shipyard. That is one of the biggest challenges we have, because shipyards are used to producing standard ships, with oil lubricated systems.
“The shipyard, as a business entity, largely speaking, doesn't care about the environment or the through life costs of the vessel.”
Morrison referred to what he called “the unholy alliance” between the shipyards and oil-lubricated bearing manufacturers, of which the latter, he suggested, supplies bearings to the yards at cost, happy to squeeze the shipowner later on through frequent maintenance, repair work, after sales and spares.
Morrison said when shipowners approach yards for water lubrication, some shipyards respond by lifting the price above the cost of the installation. “They say, okay, you can have it for an extra US$250,000. In reality, the difference in the build cost is pretty much zero. I would argue it is even lower. A lot depends on the balance of power between shipowner and shipyard.”
The scales of power currently tip in favour of the yard, according to Morrison. “The shipyards are saying to their customers here is a standard vessel filled entirely with local equipment. Here's the price. Take it or leave it. That's essentially what's going on.”
Morrison intimated that substantially more ships would be operating water lubricated shaft lines today if shipbuilders took a more pragmatic approach to not only protecting the marine environment but also their customers' bottom line.
“Shipowners are concerned about the environment, but also cradle to grave costs of the ship right through to the disposal. And they are the other ones that are more interested in trying to push forward with this technology.”
There's also the cost of the lubricant itself. A typical “sealed” oil lubricated sterntube system is filled with about 1500 litres of mineral or synthetic oil. Despite this being considered a closed system, frequent propeller shaft seal oil leakage and topping up of the head tank is viewed as normal operational consumption and acceptable.
Questioning the technical differences between oil and water as a lubricating medium, Caroline Hout asked how the condition of water lubricated shaft is monitored, “considering the shaft is one of the most important elements for safe navigation?”
“If you're measuring a high temperature, it's probably already too late,” said Morrison. “The reason is these materials are largely insulators. The basic principle is that you measure the quality of the inputs, so if you're supplying appropriate water at appropriate temperatures and appropriate flow rates, then you can have absolute confidence that the system is operating correctly. Through life measurements of bearing wear rates also provides information on what the bearing is doing.”
Another point raised was that water is better than oil in terms of removing heat. And when a water lubricated sterntube is operating within its design parameters, at full power and speed and at lower RPM, the system “operates hydrodynamically,” the same way as an oil lubricating system.
Morrison then alluded to something called the “Thomson Stern Space” - a concept that could create a cavity in the sterntube so that bearings can be inspected and changed from within the vessel.
“One of the problems with a sterntube is that it is inaccessible, so this is a brilliant idea,” said Gregory. “As soon as you have access, you have a totally different scenario and you can water lubricate, you can oil lubricate, you've got choices.”
Despite some differences, the speakers believed the industry has to take collective responsibility in dealing with marine pollution no matter the source.
“We need to think about who is accountable,” said Gregory. “We have been going through 30 to 40 years of shipbuilding and optimising costs and you buy something off the rack, and you trade it, and that's that, but we're into a future now, where, as George says, we don't want to be discharging oil or we don't want to be increasing CO2 emissions. There's a number of different questions that we need to answer. And who's going to take responsibility for that. The shipowner? The shipyard? Somebody's got to take responsibility, otherwise, we're going to come to a dead stop.
“We really need to start thinking about what the problems are we are trying to solve. And if we take a singularity view on it, say, we just try to solve oil leakage, I think we miss a lot. The shipping industry doesn't seem to be moving along in that direction whatsoever. It all seems to be driven by cost and I think this needs to change, if we are going to advance,” he said.
We really need to start thinking about what the problems are we are trying to ‘‘ solve. And if we take a singularity view on it, say, we just try to solve oil leakage, I think we miss a lot. The shipping industry doesn't seem to be moving along in that direction whatsoever. It all seems to be driven by cost and I think this needs to change, if we are going to advance
8 The COMPAC
open water lubricated stern tube arrangement
THE LIFE OF CRANES, AND HOW THEY LEARN
What place does machine learning have in the world of cranes?
Both welded structures and machinery have a design lifetime that's exhausted not by the calendar, but by work cycles, weighted against load. There are established calculations (and an ISO standard), but while analyses based on previous cycles are all well and good, utilisation patterns can change and since it's onboard a ship, the foundation beneath the crane is inherently unstable, adding dynamic lifting moment.
Further, there's an exponential increase in failure rate at the end of the design life, complicated by the fact that at this point, not all parts of the crane will age at the same rate. Notably, rotating machinery can develop issues faster than structural elements - and their failure curve will typically be that much steeper.
So what can AI and in particular, machine learning (ML) add to the mix?
Firstly, there's been a change in thinking. While a 24/7 support service provide a go-to when things are amiss, “this is a reactive solution” says Joerg Peschke, MacGregor's Director of Drives and Controls.
However, since MacGregor has delivered cargo and load handling equipment onboard thousands of ships, preventative maintenance and real-time indication of potential trouble is far more efficient for both the operator and the company.
There's a problem. “You can't rely on high density data transfer when a ship is out at sea,” Peschke points out. So, MacGregor started to evolve an edge computing solution which keeps the bulk of the data crunching onboard.
Here's where things get interesting: there's a lot of information to process spanning a wide number of sources, from load, pressure and heat sensors to those measuring position, speed and direction. And it doesn't stop with multiple feeds from each element or component, these also need to be tied in with vessel motion and weather.
To try to wrap machinery health predictions up with written code would probably take decades especially given the wildcards of sea and air; further, it's likely it would require massive updates to take advantage of new, more accurate information.
The other approach is to feed neural networks with labelled data sets. Then, those labels are applied to anything with similar characteristics - a numerically weighted response is applied to 'train' the brain. As a result, ML can be used to find hidden features and relationships, utilising them to flag up suspicious sensor patterns. Moreover, it can continue refining and updating these associations.
For MacGregor, ML's ability to identify equipment malfunction is an “enabler”, says Peschke: it yields an ongoing condition-based check of the equipment, with real-time projections of the health and lifetime of both structural and power machinery, including hydraulic and electrical loads.
First and foremost, “continuous observation of the sensor data minimizes the risk of equipment breakdown during planned operations” he says, making sure that the weather windows can be fully utilised. Importantly, this works alongside other, more traditionally defined automation systems which have their own version of 'smart', being able to adjust the crane operation envelope to wind and waves and warn of inappropriate manoeuvres.
With the ML distilling data down to manageable packets for transmission (ship to shore transfer being developed in collaboration with Kongsberg Maritime), landside offices can benefit from a near real-time web-page view, updated with a lag of only a few seconds. As all parties access the same information at pretty much the same moment, crew, operation centres and third parties such as MacGregor can collaborate on the immediate situation.
“Monitoring and analysing crane performance data that is streamed directly from the vessels will enable us to make better-informed decisions and reduce problem solving time,” says Yannis Voulgaris of Load Line Marine, one of MacGregor's OnWatch Scout service customers.
However, crew are still on the front line of lifting operations; with that in mind, there's been a demand for a straightforward appearance to the interface. “We probably underestimated the work it would take to make it look simple,” admits Peschke “But we've managed it.” He explains the 'old school graphs' are still available, but an overview schematic shows 'OK' checkboxes at various points covering the main jib, knuckle jib, slew, tugger winch and so on. “If there's a critical message or warning, you can push the resolve button, this will display the error description and step-by-step, explicit, actionable instructions with links”, he says: “You don't have to search for anything - not even spares which you can push straight into the shopping basket.”
He adds, “Our customers are not left alone with the sensor data, but are given the conclusions.”
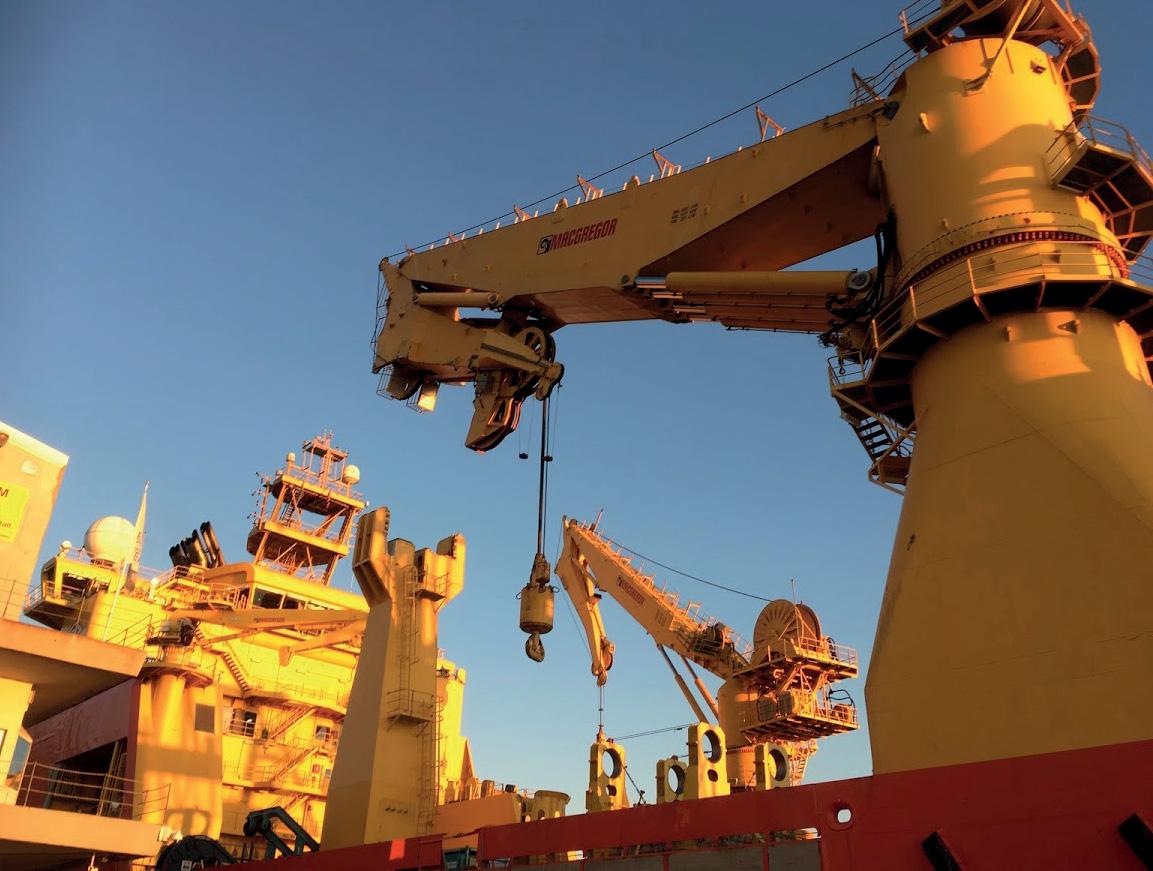
8 For MacGregor,
ML's ability to identify equipment malfunction is an "enabler", yielding an ongoing condition-based check of the equipment in real-time
Onboard cranes have other uses for machine learning.
Although there's rising interest from commercial shipping, Optilift has so far been focused on the offshore sector. Unmanned operations are already being realised in the field, underlines CTO Torbjørn Engedal, the goals being lower OPEX, better asset optimisation - though arguably, most significant is reduced risk. Despite safety initiatives, stubborn peaks keep appearing in onboard lifting incident figures: for example, a 2019 report from the Norwegian offshore industry revealed they'd doubled in just a couple of years.
But development faces a similar challenge to crane health monitoring: the bandwidth isn't up to sustaining a high density, long distance connection. So again, there has to be some onboard intelligence to fill in the gaps.
This slots in nicely with the stepwise evolution toward full autonomy through 'assistance' modules: anti-pendulum, antisway and anti-collision are fairly familiar features by now, though ML adds further 'recognition' capabilities. However, Optilift has also developed a complete auto-lift and soft landing module. Watching the demo it seems unremarkable: the crane can pick up the load, position it over a deck and bring it down gently while compensating for heave. However, it's a little more difficult than it appears, requiring the crane “to have eyes as well as a brain”, says Engedal. Both lift and landing are timed based on relative velocities and measured tension of the wire to make sure there's no re-entry. The anticollision automatically adapts to structural changes on the landing or pickup site, the cruise control follows the vessels horizontal movement during sea lifts and pauses for the right moment to act. Interestingly, it can also release a specially designed hook by itself, with no intervention.
But this iterative model toward autonomy requires it to work alongside humans. That's caused hesitancy around adoption of many 'intelligent' systems although here, the potential benefits of ML are more obvious: instead of attempting to define an image by code, train the brain on hundreds of thousands of pictures till it can recognise crew and prevent the load crossing above, or worse, hitting them with cargo or hook.
But despite ML's buzzword status, it needs to be enclosed within more traditional calculations “that will use physical laws or models to carry out sanity checks” on the outcomes explains Engedal. That's because neural networks are “defined by what they're fed” - not by the kind of logic a human would, or could, follow. Further, he adds you can't go in and “tweak or fix the underlying cause of an 'illogical' decision”, so the biggest challenge remains “to select and tune the training data to cover all possible use-cases”.
This is very hard work. For example, MacGregor already had ten years of historical sensor data - terabytes of it - which was made available to project partners. Despite that, examination found “there were gaps”, admits Peschke. A crystal ball would have come in useful as “most of the information was process oriented - we had the error messages and conclusions, but years ago, we didn't think it necessary to store background data, indications from the accelerometer or pressure sensors”, he explains. Therefore, an amount of back-working of the information was necessary.
But as Peschke explains, bringing ML onboard will likely trigger changes that go well beyond the machinery. There was a need for collaboration “as we realised we couldn't do it all ourselves”, he says. Further, everyone has had to adapt to a new way of working: “Before, the sales team could lay out a well-known list of options,” he says: “Now, there's more questions to be asked... and our clients are far more involved in development.”
Finally, ML has another layer of possible uses: it can also learn how sensor signals themselves degrade, warn, and potentially recalibrate to take up the slack. A technical paper by Yokogawa Electric reports 'slight differences in patterns .... which indicate the deterioration in the performance of the sensor caused by changes in the electrode' were spotted by ML. So, in future there should be less wondering if an anomaly is sensor failure - or if it's really signalling the beginning of trouble.
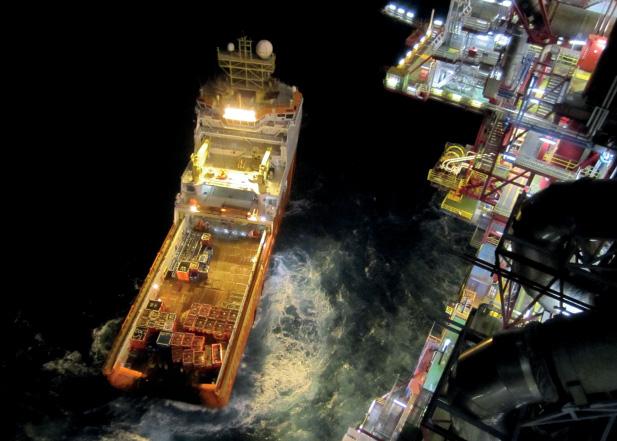

Photo: Optilift
8 In future there should be less wondering if an anomaly is
sensor failure - or if it's really signalling the beginning of trouble
8 Despite ML's
buzzword status, it needs to be enclosed within more traditional calculations that will use physical laws or models to carry out sanity checks on the outcomes
DOING MORE WITH LESS
Increasing a ship's remit isn't altogether easy, especially if it demands extra capabilities that don't fi t into either onboard space - or power parameters
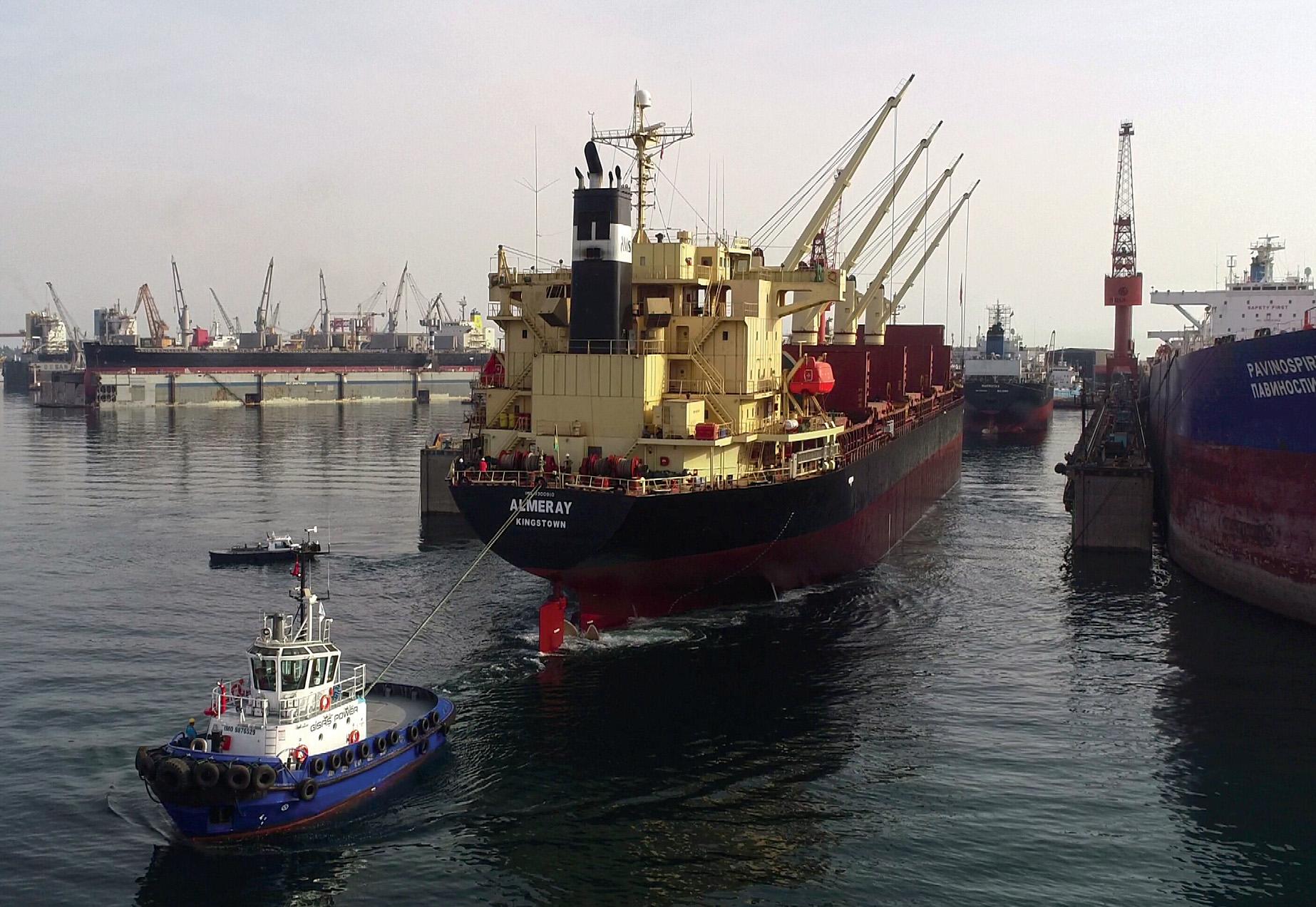

Photo: Navtek
The HES880 from ABB could make all the diff erence for e for vessels changing their work pattern and needing extra extra deck kit - whether winches, cranes, LARS or cable-laying aying units - but fi nd they've got no space left for the drive below. elow. As product manager Vesa Kajander explains this simplifi es plifi es things as “it doesn't require an additional cabinet or et or electrical room installation”.
Originally developed for landside HEVs and propulsion for on for small vessels, its character as a self-enclosed module “also “also makes sense for smaller mission equipment, the kind that's that's sometimes used for offshore installation or distributed buted systems where space is cramped”, says Daniel Olsson, sson, marine sales manager for Drives in ABB Motion. “For that you t you from some kind of local energy source or hybrid combination, might want temporary capabilities just for the duration of the of the potentially bringing together batteries, supercapacitors and campaign.” And ideally, “you also want it to come in a single, plug and play package”.
Importantly, the drive, available in 350A, 600A or 900A modules, is ruggedized to IP67, “so it could be fitted on or in the base of a crane or other mission equipment without squeezing it into an existing e-room - and with a lot less cabling”, he explains, adding the requirements also extend to boxed kit: “We've had a few projects with containerised solutions since these don't always have the same climate control that you get in the electrical room.” A drive that can cope with damp, salt air, water ingress and so on can really simplify such concepts.
However, where it gets particularly interesting is that with a HES880 in DC-DC configuration you could run the extra kit from some kind of local energy source or hybrid combination, potentially bringing together batteries, supercapacitors and fuel cells with other solutions as yet on the horizon. Moreover, if utilised with active heave compensated equipment it can be used to regenerate otherwise wasted energy, pushing it back into the local ESS or main bus. As a result, a ship might be able to expand its power profile. A lot of work has also gone into making the HS880 not only robust, but as flexible as it can be: one hardware module has the options of three different firmware flavours: a motor/ generator inverter, DC/DC converter and supply converter control. Usefully, good support is also available: remote monitoring and diagnostics allow engineers to resolve issues in realtime and it is backed by the same service network as all ABB marine products.
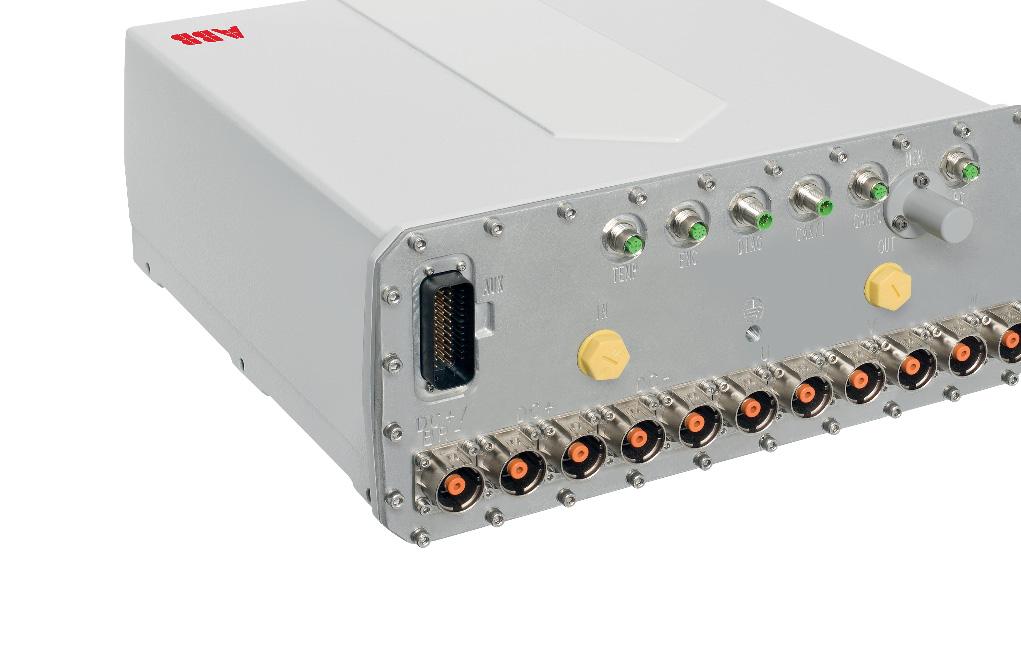
8 Originally
developed for landside HEVs and propulsion for small vessels, its character as a self-enclosed module also makes sense for smaller mission equipment
8 The HES880 The
from ABB in DC-DC from A confi guration config can run mission can ru equipment from a equip local energy source local such as batteries, such supercapacitors or super fuel cells fuel c
So, with something that flexible, how easy is it to commission?
The topology should be familiar to anyone acquainted with ABB's other drives, says Olsson. However tying it into the same family has been “challenging”, admits Kajander: “The main idea has been to use the same software so the interfaces and tools look the same - even though the hardware is very different”.
Those physical differences are significant: the HES880 has been designed from the ground up for a service-free life in extreme conditions “so it's not just a familiar drive in a more robust box,” underlines Kajander. For example, it's fully liquid cooled, withstanding -40 to +85°C temperatures even in warm seas and it has 4G continuous vibration and 30G shock tolerance.
When designing for maintenance-free operation in rough environment, “a lot of the work is about intense heavy-duty testing from component level up to complete pilot projects with our partners - that's one of the most critical processes to ensure it lives up to the high reliability standards expected from all ABB products even in such harsh conditions”, says Olsson.
For the HES880, development required avoiding moving parts such as fans, “and starting with components able to withstand higher temperatures” Kajander explains, as well as paying attention to small, practical details such as using larger PCBs with a greater number of fixing points: these give the assembled drive far better vibration and shock survival.
However the final frontier has been “making it all fit in a very small box” concludes Kajander. The biggest, 675kW module measures just 430mm by 180mm by 525mm.
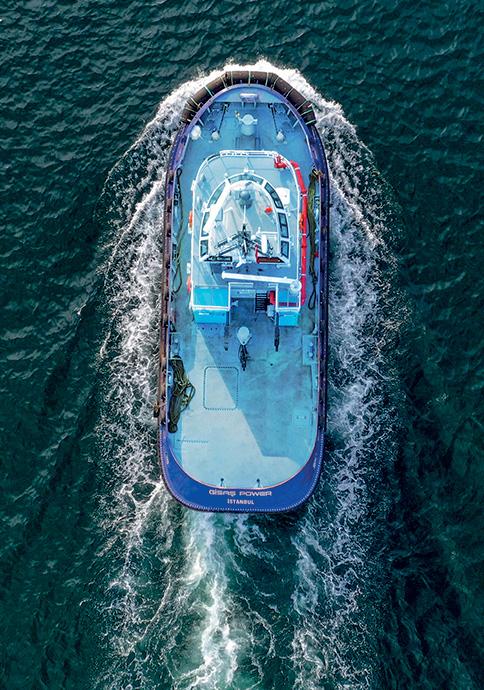
8 The HES880 from
ABB could make all the diff erence for vessels changing their work pattern and needing extra deck kit
Photo: Navtek
SUBSCRIBE NOW
to receive your three month free trial
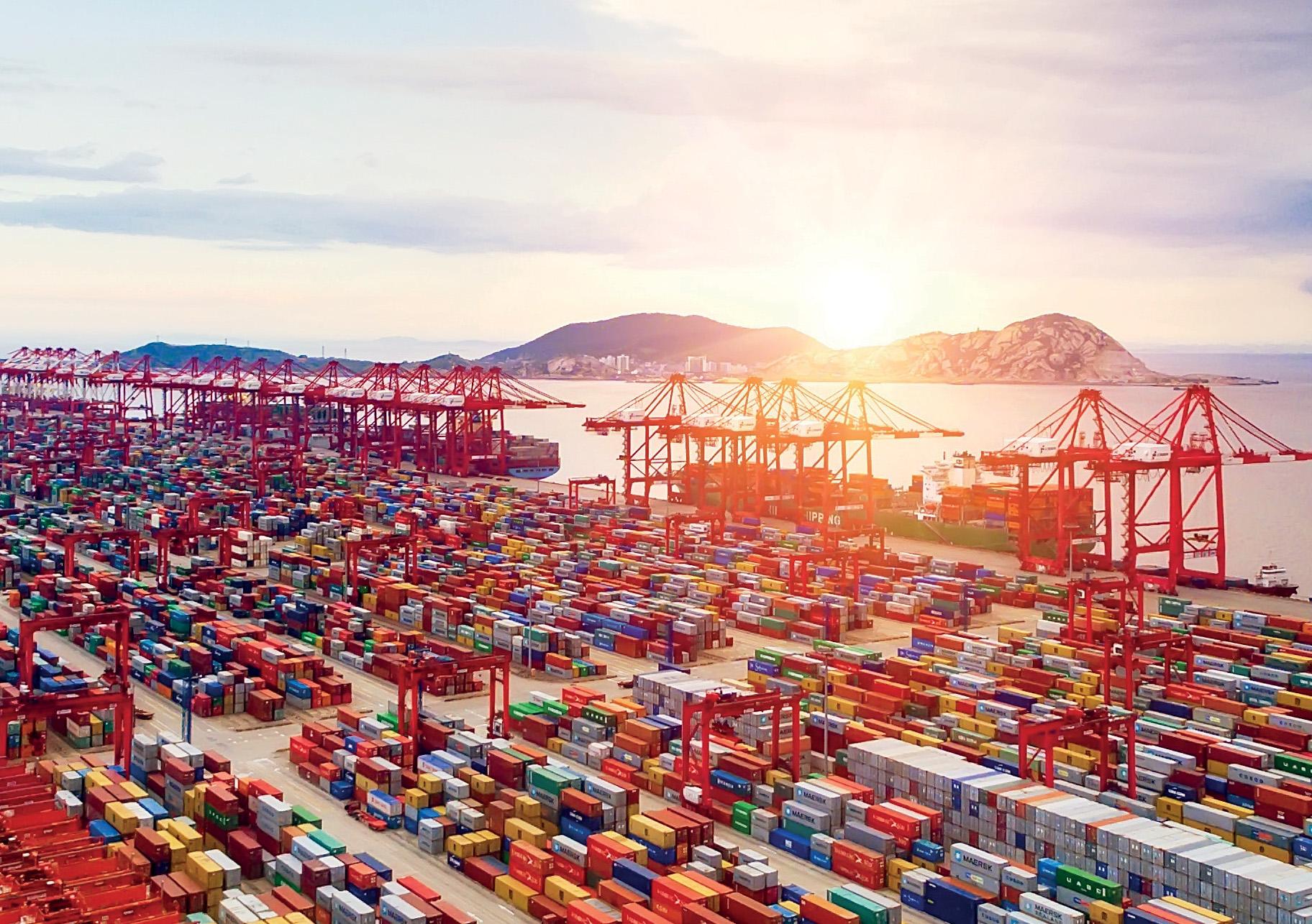
•Instant access to industry news •Expert opinion •Monthly features •Weekly eNewsletter and port maintenance industries.
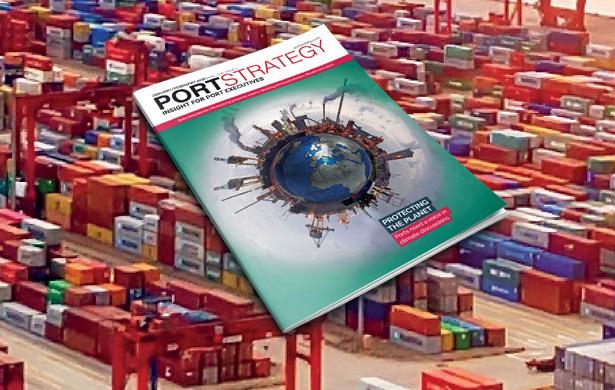
Informing over
port and terminal professionals around the world
portstrategy.com
WALLENIUS SOL RAISES ITS GAME IN BALTIC TRADE
Sweden's shipping industry is set to introduce the largest ro-ro freight vessels that combine the highest ice class rating with LNG-fuelled propulsion, writes David Tinsley
As a coalition of two august names in Swedish shipping, Wallenius SOL is poised to implement a new stage in the development of capacity to serve year-round industrial traffi c between the northern Baltic and European markets.
Four dual-fuel trailerships in the 'mega' size category under construction and on order at a Chinese yard have been specified to Finnish/Swedish ice class 1A Super standard, so as to ensure access throughout the winter period to icebound ports in the Gulf of Bothnia.
At a length of 242m, and accommodating 5,800 lanemetres of freight on a deadweight capacity of about 27,000t, the design tops the scale in terms of Baltic ro-ro traders. Long-term agreements with pulp and forestry product groups will underpin the vessels' employment.
The newbuild programme was landed by Yantai CIMC Raffles Offshore, consolidating its drive in the ro-ro sector, and Wallenius Marine is superintending the project on behalf of the shipowners. The concept was developed by Danish naval architectural consultancy Knud E. Hansen, entrusted with contract and basic design. Input has been provided by the shipbuilder's Offshore Engineering Institute(OEI) and by the CIMC Group's Gothenburg subsidiary Bassoe Technology.
The lead vessel is expected to enter service during the autumn this year, to be followed at three-to-four month intervals by the sisterships.
The Wallenius SOL combine's route network entails a nineport itinerary, calling for flexibility and rapidity in loading and discharge. The type of goods brought out of the northern Baltic also poses an additional hydrodynamic challenge, since the vessels will typically have up to 2.5m more draught on the southbound voyage than on the return trip.
Each vessel has been specified with a pair of WinGD twostroke, LNG-capable dual-fuel main engines and in-line PTI/ PTO permanent magnet (PM) shaft generators. The primary power concentration will be just over 21,000kW, and direct drive will be made to twin, controllable pitch propellers, for a service speed of 20 knots.
Notwithstanding the considerable expansion of the dualfuel offering from engine makers and licensors over the years, in both the low-speed and medium-speed categories, Wallenius SOL has opted for models of the first design of two-stroke, low-pressure DF propulsion machinery, the RTflex50DF. Originally a Wartsila product, in turn born out of the Sulzer RT low-speed diesel series, the RT-flex50DF is wellproven, and remains competitive as regards consumption and power output in relation to dimensions and weight. In gas mode, Tier III emission requirements are met without the need for external exhaust gas aftertreatment.
The installation in each of the Swedish newbuilds will comprise two RT-flex50DF units in eight-cylinder format, at a contractual maximum continuous rating (CMCR) of 10,500kW at 117rpm. The continuous service output, denoting the intended, efficient transit setting, equivalent to 60% of CMCR, is 6,300kW at 98.7rpm. At its nominal MCR, the 8RT-flex50DF can deliver 11,520kW on a crankshaft speed of 124rpm.
The Chinese yard contracted Ingeteam of Spain to develop and supply the hybrid electric propulsion element, featuring two Ingedrive LV400 multidrive frequency converters, and the two Indar PM generators. In PTO mode, the latter will deliver 2,200kW at 85-122rpm, and produce 1,000kW at 122rpm in PTI mode. The system has been prepared, in terms of space, wiring and ventilation, for future adoption of battery hybrid arrangements and incorporation into the vessel energy management system.
During port calls, the intention is that the ships will primarily draw energy from the shoreside electric grid, while the alternative reliance on gensets will also chime well with environmental edicts and expectations since the nominated engines are of LNG dual-fuel type.
Each of the two auxiliaries will be based on a nine-cylinder
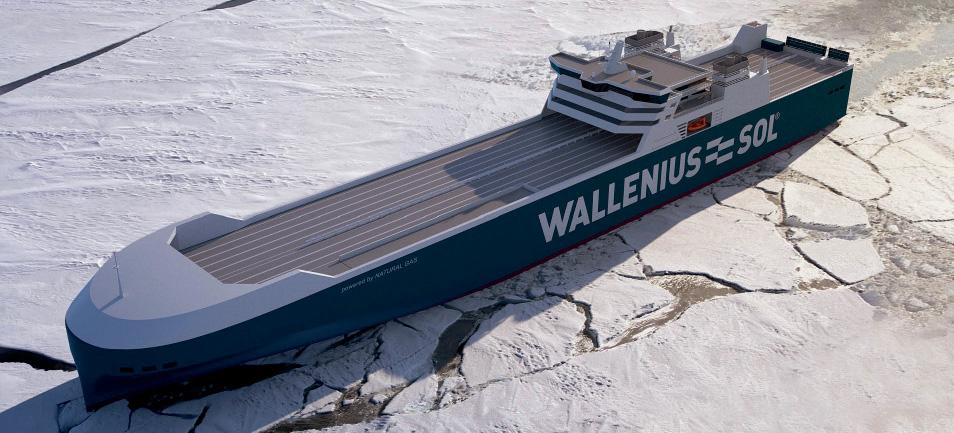
Credit: Knud E.Hansen 8 The fi rst of the
record-breaking generation for Wallenius SOL is due in the northern autumn
model of L28/32DF design from MAN Energy Solutions. The latter's subsidiary MAN Cryo is providing the complete LNG fuel gas supply systems, embracing each shipset of two 685m3 Type C vacuum tanks, including tank connection spaces with LNG fuel pumps, plus bunker stations with a capacity of 500m3 per hour, and automation, emergency shutdown and gas detection arrangements.
MAN Cryo claims that the tanks mounted under-deck with air locks will minimise the amount of ambient air drawn into the tank rooms. This is an important consideration in the tough winter conditions to which the ships will be exposed, whereby the amount of very cold air introduced needs to be kept to a minimum.
Wallenius SOL commissioned the Swedish Environmental Research Institute (IVL) to quantify the advance in energy performance and emission curtailment promised by the nascent tonnage. A comparison was made with the 2006-built, 190m Thuleland, which plies the Baltic/Continent /UK route and is ranked best-in-class as regards environmental impact.
While the newbuild type's significantly higher energy efficiency reflects upscaling with a greater load capability, design measures including the hydrodynamic characteristics of the hull, the design arrangement, weight reduction solutions and choice of machinery have enhanced efficiency to a similar degree. Despite embodying four cargo decks, the centre of gravity has been lowered, reducing the amount of water ballast needed. It was found that fuel consumption per freight unit will be halved, greenhouse gases will be reduced by 63%, sulphur and particulate emissions will be negligible, and NOx will be cut by 85%.
Finnish paperboard company Metsa Board's shipping agreement with Wallenius SOL entered force at the beginning of 2021. The producer's goals for the next 10 year include fossil-free mills and 100%-sustainable supply chains, such that it was attracted to the environmentally-sensitive transport concept offered by the shipowners.
Other long-term industry customers include paper and packaging maker StoraEnso, and Wallenius SOL has recently included Vaasa in its regular liner network, to serve the logistic needs of industrial firms located there.
PRINCIPAL PARTICULARS - Wallenius SOL ro-ro
Length overall 241.70m Length bp 234.25m Breadth, moulded 35.20m Depth, to main deck 11.10m Draught, summer 8.70m Draught, design 8.50m Deadweight, maximum c.27,000t Ro-ro freight capacity 5,800 lane-m Container capacity 800TEU Propulsion system Dual-fuel two-stroke Main engine power 2 x 10,500kW Speed, service 20kn Class LR Class notations +100A1, Ro Ro Cargo Ship, Container cargoes on weather deck, ShipRight (SDA, CM, ACS[B]), Ice class 1AS FS, IWS, L1, +LMC, LFPF(GF, NG), UMS, NAV 1, IBS
SUBSCRIBE NOW
to receive your three month free trial
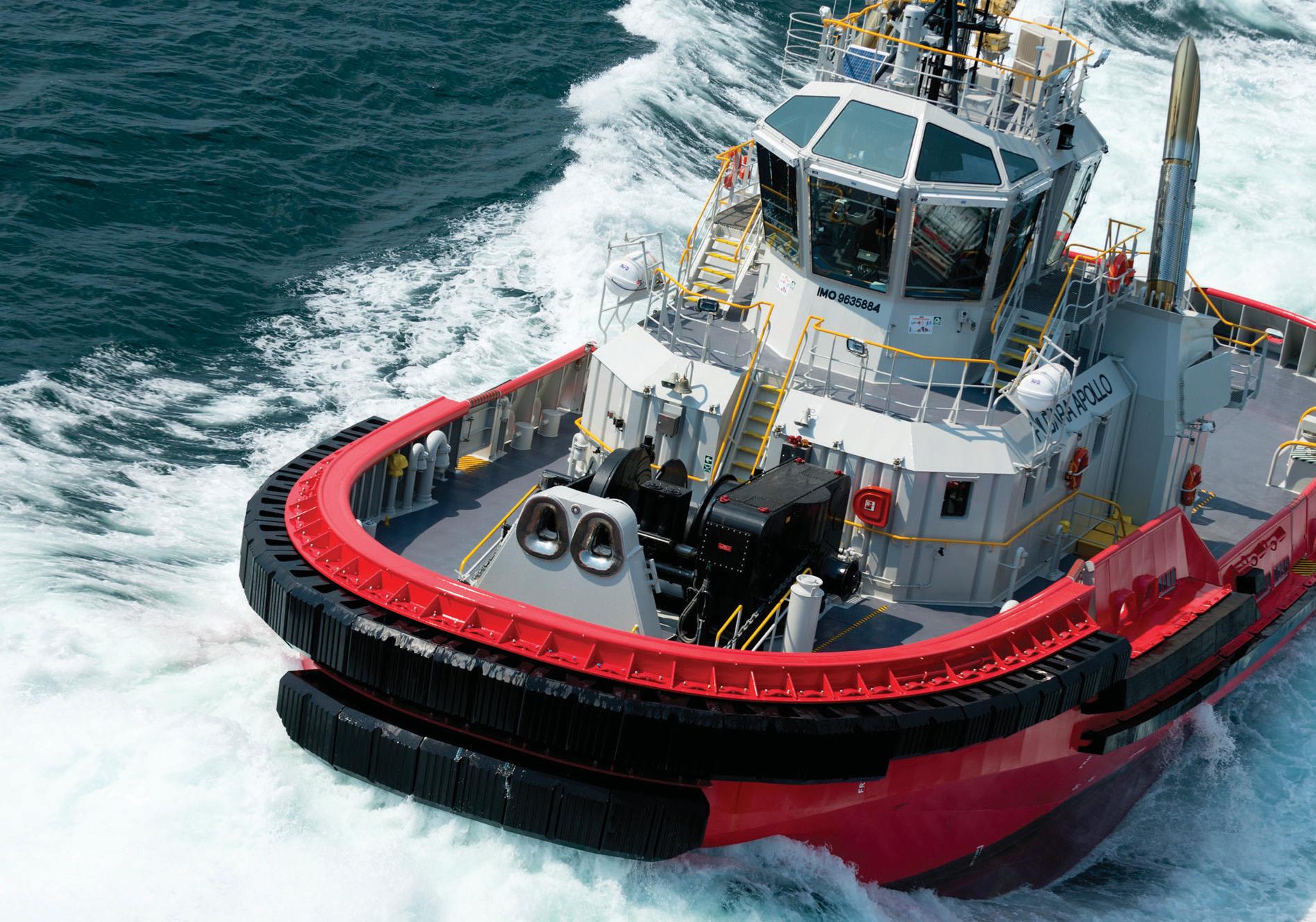
•Instant access to industry news •Expert opinion •Monthly features •Weekly eNewsletter Maritime Journal is relied upon by marine zone and short sea commercial maritime businesses.
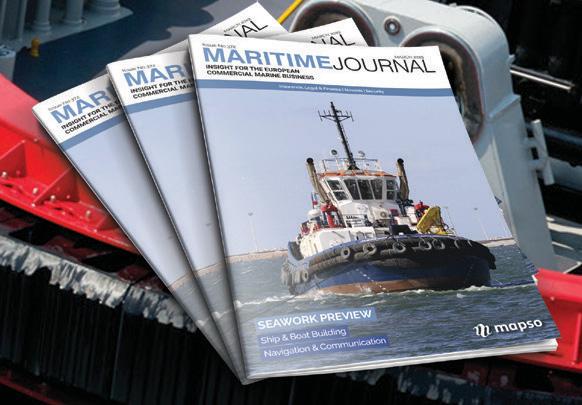
Informing over
maritime professionals across Europe
TO SIGN UP FOR YOUR THREE MONTH FREE TRIAL
maritimejournal.com
EMERGING FUTURE TRENDS
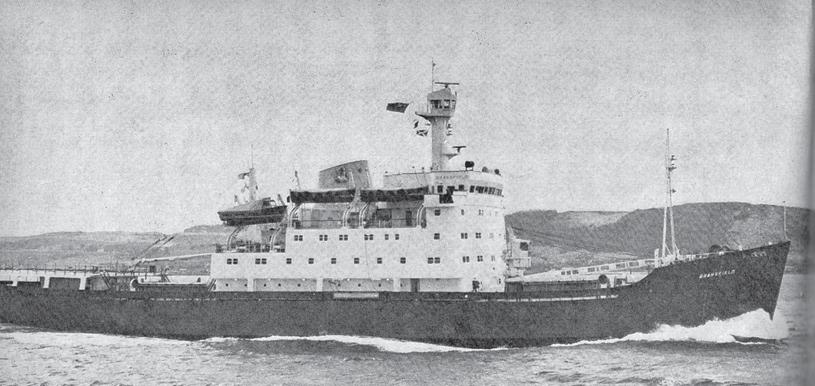
In March 1971, The Motor Ship reported that the shipping industry was poised to benefi t from the oil majors waking up to the reality that the world demand for oil could not be met by the current supply of tanker vessels.
So, an industry that -with the possible exception of Japan - was depressed through lack of orders, was about to see a worldwide rush for building berths. Not only did our predecessors foresee a boom for European yards, but they expected Taiwan, Brazil and Peru to emerge as major shipbuilding nations.
A somewhat more accurate prediction came later in the lead editorial feature, discussing automation. “Perhaps,” they wrote, “the time is now approaching when marine engine builders will feed all relevant information into a computer against which all performance data from ships with such machinery can be related. The ship will transmit the symptoms and available data and the engine works will prescribe the remedial measures.” Which was, after all a rather verbose forecast of remote assistance and predictive maintenance, which now applies to all the ship's systems, not only the engines. But with cheap and reliable satellite communications some years away, such a comment probably seemed far-fetched at the time.
A twin-engine medium speed propulsion plant for a mid-size bulk carrier sounds rather an unlikely choice today, but such was the strength of debate about the merits of large low-speed versus multiple medium-speed engines that the idea must have seemed well worth trying in 1971. In this case, it was a series of 23,655 dwt vessels from Haugesund in Norway, the second of which, Lyle Shipping's Cape Horn, received a detailed description.
Apart from the twin side-by-side funnels, the vessel looked like any other bulker. The reasoning behind the choice of machinery, though, was that it offered a potential 15% gain in cargo capacity compared with the normal single large engine. The prime movers here were a pair of 12-cylinder Ruston AOM diesels, each rated 6000 bhp at 450 rpm. Unusual in being trunk-piston engines operating on the two-stroke cycle, the units fitted to these vessels incorporated modifications to an earlier design which had been fitted to a general cargo ship and a ferry,
8 The diesel-electric icebreaking research
vessel Bransfi eld
but had proved troublesome. The faults were expected to be cured with changes to the fuel system and cylinder covers, enabling the Ruston Paxman company to offer a comprehensive warranty. The main engines drove a single CP propeller, while Ruston also supplied the two auxiliary gensets. Another novel feature was the way that waste heat from the engines was utilised, meaning no boilers were required in the machinery room.
Another pointer to future trends could be found in the second ship description - an ice-breaking research and supply vessel for the British Antarctic Survey, with diesel-electric propulsion. The Scottish-built Bransfield was powered by twin Mirrlees K8M engines burning diesel oil driving a pair of 1975kW DC generators, supplying power to a single electric motor driving a SMM CP propeller. The configuration had been chosen to enable the power to be used most effectively at low speeds in ice conditions. As befits a research ship, there was a high degree of automation employed, with full control available through no fewer than four separate conning stations.
Automation was obviously important in 1971, with a separate supplement covering the subject, as well as a look forward to computerised navigation, via Sperry Rand's 'integrated bridge' system. Another glimpse into the future came with an in-depth technical discussion on the design of membrane-type tanks for gas carrying ships.
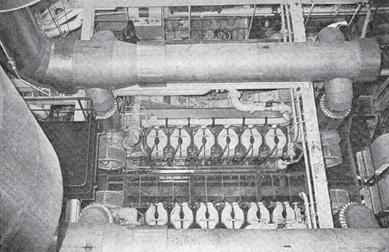
8 Looking down at one of the two-stroke medium
speed Ruston engines for bulker Cape Horn
MOTORSHIPTHE
INSIGHT FOR MARINE TECHNOLOGY PROFESSIONALS
The international magazine for senior marine engineers
EDITORIAL & CONTENT
Editor: Nick Edstrom editor@mercatormedia.com
News Reporter: Rebecca Jeff rey rjeff rey@mercatormedia.com
Correspondents
Please contact our correspondents at editor@motorship.com Bill Thomson, David Tinsley, Tom Todd, Stevie Knight, Wendy Laursen
Production
Ian Swain, David Blake, Gary Betteridge production@mercatormedia.com
SALES & MARKETING t +44 1329 825335 f +44 1329 550192
Brand manager: Toni-Rhiannon Sibley tsibley @mercatormedia.com
Marketing marketing@mercatormedia.com
EXECUTIVE
Chief Executive: Andrew Webster awebster@mercatormedia.com
TMS magazine is published monthly by Mercator Media Limited Spinnaker House, Waterside Gardens, Fareham, Hampshire PO16 8SD, UK
t +44 1329 825335 f +44 1329 550192
info@mercatormedia.com www.mercatormedia.com
Subscriptions
Subscriptions@motorship.com or subscribe online at www.motorship.com Also, sign up to the weekly TMS E-Newsletter 1 year’s magazine subscription Digital Edition: £GBP173.00
© Mercator Media Limited 2021. ISSN 2633-4488 (online). Established 1920. The Motorship is a trade mark of Mercator Media Ltd. All rights reserved. No part of this magazine can be reproduced without the written consent of Mercator Media Ltd. Registered in England Company Number 2427909. Registered offi ce: Spinnaker House, Waterside Gardens, Fareham, Hampshire PO16 8SD, UK