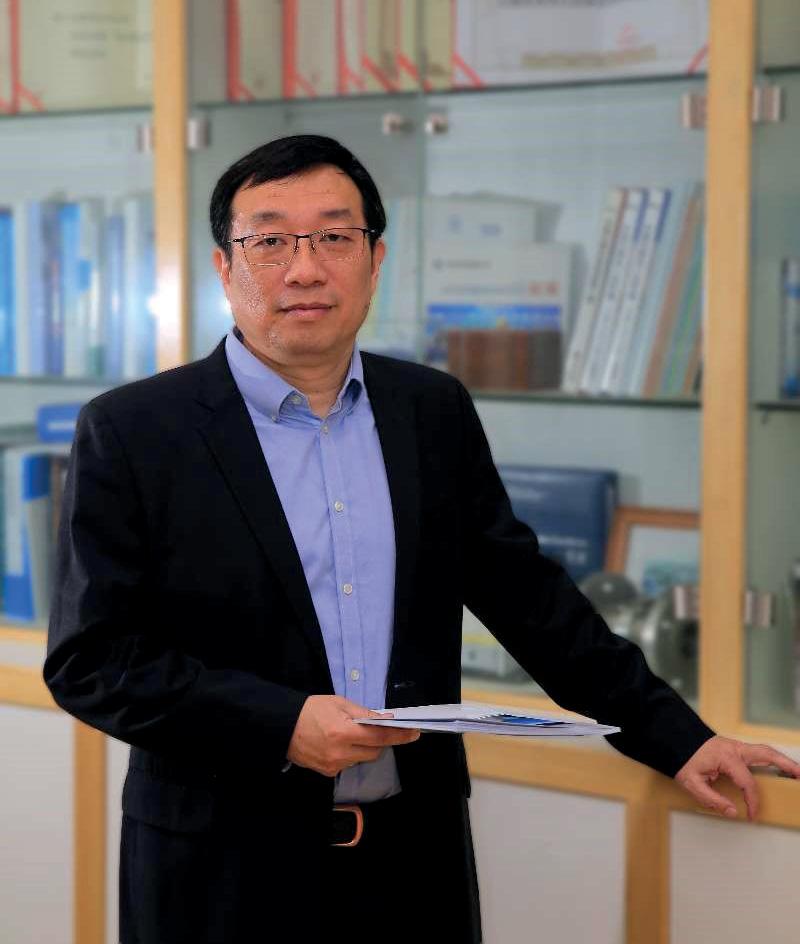
28 minute read
Pearl River hydrogen trial
CHINA UPS PACE IN DRIVE TOWARDS ALTERNATIVE FUELS
In line with China's aim to reach carbon neutrality before 2060, and to focus on ensuring its greenhouse gas emissions peak in the next decade, China Classifi cation Society (CCS) Wuhan branch is stepping up its focus on alternative fuels.
Earlier in 2021, CCS Wuhan branch awarded China's fi rst certifi cate of type approval for a marine fuel cell product to Wuhan-based PEM fuel cell supplier Troowin Power System Technology Co. This will provide a "new channel" for the application of hydrogen fuel cells on ships.
This is just part of its work towards a zero-carbon future in line with President Xi's announcement, to the United Nations in September 2020, that China will reach carbon neutrality before 2060 and ensure its greenhouse gas emissions peak in the next decade. "The Chinese government has established a long-term goal to become a carbon neutral country by 2060," said Jia Siqing, General Manager of Industrial Products for CCS Wuhan branch. “We must also reach the peak of carbon emissions before 2030. As the marine industry is one of the major sources of these emissions, it must make its share of the contribution to this inspiring target."
CCS had been actively researching low or zero emission fuels long before these new targets were announced. For example, as far back as 2013, CCS was already exploring hydrogen and seeking to quantify its potential in everything from powering fuel cells to how to tackle a hydrogen-fuelled fire. At the same time, its researchers were also evaluating a host of alternatives, such as liquified natural gas (LNG), various alcohols, bio-fuels, ammonia and renewable electricity from wind and solar. They also looked at how these could be harnessed more efficiently with better power management systems. Even once a new technology is proven, CCS goes further, running exhaustive tests to decide if the application would be practical. "Take the use of bio-fuel," said Siqing's colleague, Luo Xiaofeng, Director of CCS Rules & Research Institute in Wuhan. "With China having such a large population, we need all the available farmland to feed our people. This means biofuel isn't a solution for us - we can't grow crops for powering our ships."
THE RISE OF HYDROGEN
By contrast, hydrogen is abundant and is an ideal candidate as a zero-emission fuel in internal combustion engines. Hydrogen can also react with a catalyst to create electricity in a fuel cell, and so power an electric drive train. CCS published its first reliable guidelines for harnessing hydrogen as a commercial marine fuel as long ago as 2015, 'Guidelines for Application of Fuel Cell System'. In 2017, this was followed by 'Guidelines For Ships Using Alternative Fuels'. These guidelines were updated in 2020. The detailed research found a hydrogen-enabled ship could be as safe as one powered by conventional fuels such as diesel. However, this comes with caveats. "No fuel is absolutely safe by nature," said Jia Siqing. "Only good management can ensure that level of safety. We think that hydrogen has some very distinctive characteristics which make it easy to manage. So, in that sense, it is inherently safe." Jia Siqing also supports the policy of allowing leaking gas to easily escape to atmosphere, rather than forming a gas cloud between decks. "The marine environment has issues very different from land-use hydrogen," he said. "These include vibration, high and low temperatures, tilting and swinging, damp and other stressors that need to be tested for verification. Hydrogen fuel cells are usually installed in a small engine space. We protect this space with an enclosure, and then discharge any leaked
8 Luo Xiaofeng,
the Director of CCS Rules & Research Institute in Wuhan
Hydrogen is clearly the future. In China, we are asking all our stakeholders to ‘‘ help us to achieve the zeroemission solution for shipping, and no later than 2060
hydrogen through a ventilation system. Working with CCS approved companies, we have seen a lot of improvements, such as metal pipes for hydrogen, with all joints either welded or connected with gas-tight fittings. All the materials used should be resistant to hydrogen embrittlement and corrosion. We have specified that a seamless steel pipe should be used for transporting fuel, and the materials used should be made from austenitic stainless steel."
CHALLENGES OF STORAGE
The main downside of hydrogen is its low energy density and the challenges of storing enough of it to take a ship on a protracted voyage. To this end, CCS is researching the most cost-effective ways to store the gas in large quantities, and in how to combine it with other fuel sources to extend its range. "Since hydrogen is the lightest natural element, more space is needed to store it," said Jia Siqing. "We are looking at methods to create hydrogen at sea, such as the use of methanol or ammonia, which can be easily and cheaply transported. However, this still requires the addition of a fuel reformer for conversion. Methanol as a fuel is still accompanied by the production of carbon dioxide. Ammonia itself is corrosive and toxic, but as a zero-carbon fuel, it will have a wide range of applications in the future."
Instead, the main focus is on carrying bulk hydrogen, enough for an entire voyage. "We think liquid hydrogen may be a good contender," Jia Siqing explained. "Alternatively, hydrogen can be stored in some organic compound in liquid form, but there may be some other issues with this technology. At present, in terms of storage methods, we still consider high-pressure gas cylinders as a viable solution."
TESTING THE THEORY
CCS is planning a series of real time tests on a purpose-built bulk carrier of 2,100DWT. The ship is currently at the design stage but is expected to be powered by four 130kW hydrogen fuel cells. A large bank of Li-ion batteries will also act as an energy reservoir. Once completed, the ship will be trialled along the Pearl River in Guangdong province, where it will carry operational cargoes. Reinforcing the data from these tests will be feedback from other sectors, such as the burgeoning Chinese electric automotive sector, as Luo Xiaofeng explained. "Today's car technology is tomorrow's ship technology," he said. "Hydrogen is a hot topic in China, so we work with other hydrogen-use sectors and universities to share the research. Breakthroughs elsewhere can help the marine industry. The safety of a new hydrogen system is the base line, then we develop the theory and economics of the various technologies, and soon we will be able to test them thoroughly in the Pearl River project."
Luo Xiaofeng is realistic about the future, and appreciates that while the zero emissions target is achievable, in the short-term trans-ocean hydrogen technology will still need to be supported with low-carbon and hybrid systems for propulsion. He also feels that new hydrogen systems should be installed in brand new ships rather than trying to retrofit the existing fleet. Once again, safety is the main consideration, as this can be optimised in the design. "Hydrogen is clearly the future," Luo Xiaofeng concluded. "In China, we are asking all our stakeholders to help us to achieve the zero-emission solution for shipping, and no later than 2060. Throughout history, the human race has always found solutions to its problems, and our new knowledge of hydrogen systems will help Chinese shipping to meet the current climate challenges."
DEVELOPMENT OF DOMESTIC REGULATIONS
In addition to conducting research on various forms of marine hydrogen fuel storage technology, CCS has also jointly carried out special research on the application of hydrogen fuel on ships with China State Shipbuilding Corporation. The research included risk assessment, ventilation, fire-fighting, as well as other areas which are essential to the safety of hydrogen fuel-powered ships. Some of the other aspects of a marine fuel cell system included the storage of hydrogen as a fuel, the bunkering and fuel gas supply system and hydrogen piping.
The above studies were aimed to evaluate the feasibility, reliability and safety of hydrogen fuelled ships and provide support for the simultaneous development of relevant technical regulations. At the same time, CCS is now authorized by the China Maritime Safety Administration to research and develop the first domestic technical regulations for ships using hydrogen fuel, and it will be released at end of 2021.
" he ther rch. The we ous hem ates the eed for ould rofit ion, ded. s to ater ways e of the
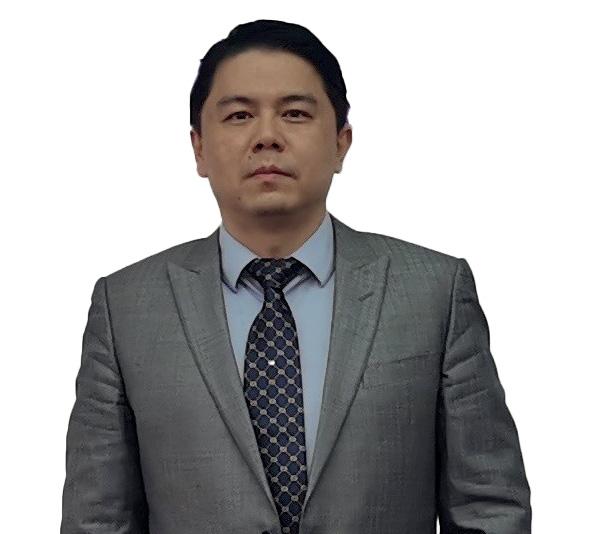
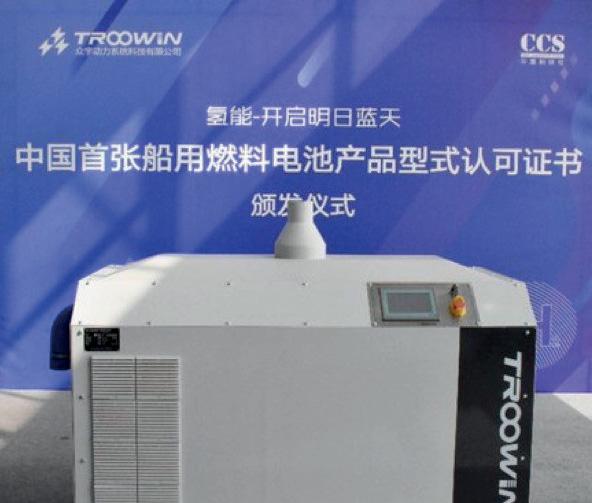
8 Wuhan-based
Troowin Power System Technology Co.'s PEM fuel cell received the fi rst type approval for a hydrogen fuel cell from China Classifi cation Society (CCS) Wuhan branch earlier in 2021
8 Jia Siqing,
General Manager of Industrial Products for CCS Wuhan branch
HOLISTIC DESIGN PLATFORM TO COMBINE LOW-EMISSION TECHS
A new design platform being developed as part of the EU CHEK project will initially be used to design a near-zero emissions bulk carrier and a cruise ship, but it is also expected to expand holistic design concepts to other vessel types.
The three-year deCarbonising sHipping by Enabling Key technology symbiosis on real vessel concept designs (CHEK) project will get underway in June 2021. It is being undertaken by a consortium consisting of the University of Vaasa, Wärtsilä, BAR Technologies, Cargill Ocean Transportation, Climeon, Deltamarin, Hasytec Electronics, Lloyds Register, MSC Cruises, Silverstream Technologies and the World Maritime University.
The project will design a Kamsarmax bulk carrier that will use wind energy and a Meraviglia-class cruise ship that will operate with a Wärtsilä engine running on hydrogen fuel. It is estimated that by combining these and other technologies, including batteries, heat recovery, air lubrication and new anti-fouling technology, greenhouse gas emissions can be reduced by 99%, energy savings of up to 50% can be achieved and black carbon emissions can be cut by more than 95%. Several key enabling technologies will be demonstrated in practice on actual operational ships.
“Shipping of the future must combine emerging technologies into a systemically symbiotic entity,” says CHEK project coordinator, Dr. Suvi Karirinne, who heads VEBIC, University of Vaasa's energy and sustainability research platform. To support this, the project will develop the FutureProof Vessel Design Platform to provide a way of combining new technologies as favourably as possible. It is expected to then also be applied to other vessel types, such as tankers, container ships, general cargo vessels and ferries.
MULTI-OBJECTIVE OPTIMISATION
A central challenge will be identifying how each solution contributes to overall CO2 emissions reductions. Mia Elg, R&D Manager at Deltamarin, says the company will use its digital design tools including energy simulations as a starting point to resolving what she considers will be very complex, multi-objective optimization problems.
“Many of the ships we design today will still be in operation in 2050, so it's exciting to be an engineer today!” However, she says that it is also important to remember that the best fuel savings are actually the result of having a smart operational strategy as well as an optimized design and new technologies. There's still much to be saved by simple operational optimisation such as slow steaming, minimising port times and weather routing. For some ships, this can lead to savings of around 20%, although in others, shipowners believe that they've done all they can, says Elg.
Another important component is the vessel design optimisation including hullform, maximising cargo capacity and the combination of technologies such as waste heat recovery, batteries and wind power. A third path to decarbonisation is zero or low-carbon fuels.
Elg emphasises the growing importance of teamwork, not just designer, shipowner and yard but also, increasingly, technology and data providers. Deltamarin has been building capability to facilitate this. A previous research project resulted in the company being capable of analysing larger amounts of data, faster, for its energy models and simulations. They can now also be run in a cloud environment.
“It's really important to establish the savings claimed by technology providers,” says Elg. “But how do we actually, technically, do that? How do we actually get enough data to simulate the energy savings, because, for sure, we are not going to be sharing all the relevant, detailed models protected by IP. We have to establish good ways of sharing the data so that we can all have our own IP protected while being able to simulate, together, what the combined result is of all the technology and operational design choices we're making.” She notes that many of the partners have already worked together extensively and is positive about the project's success.
WIND ASSISTED BULKER
Consortium partner BAR Technologies aims to achieve annualised savings of up to 30% via its solid wing sail array, WindWings, for the Cargill Kamsarmax bulk carrier. The vessel will also feature energy storage, waste heat recovery, air lubrication and an automated, optimised vessel routing system to take advantage of prevailing and forecast wind conditions.
Wärtsilä's contributions to the bulk carrier concept will include system integration, including hybridisation, energy storage and shore power connections. The company will also be developing a compact and modular fuel-flexible 4-stroke powertrain for reduced fuel consumption and optimum efficiency.
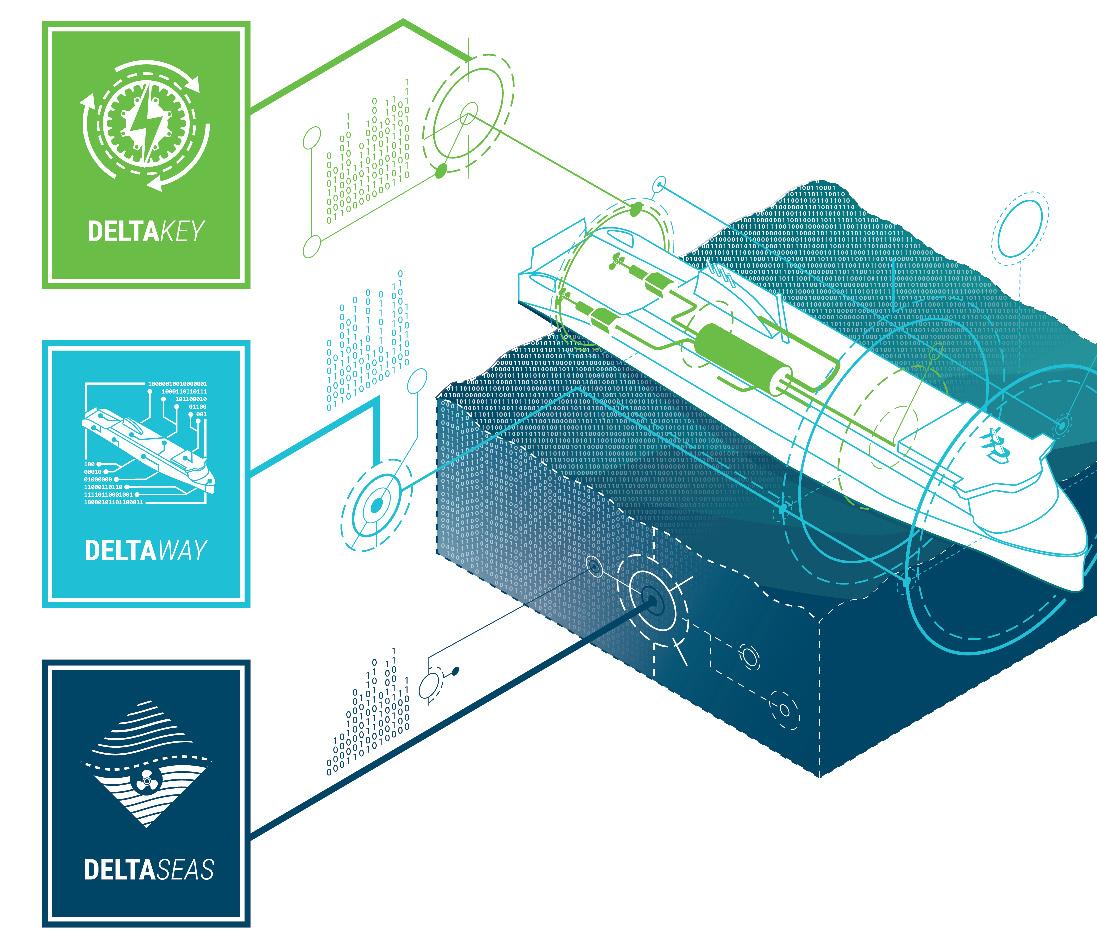
8 Deltamarin's
digital design tools include energy simulations to address "highly complex, multi-objective optimization problems"
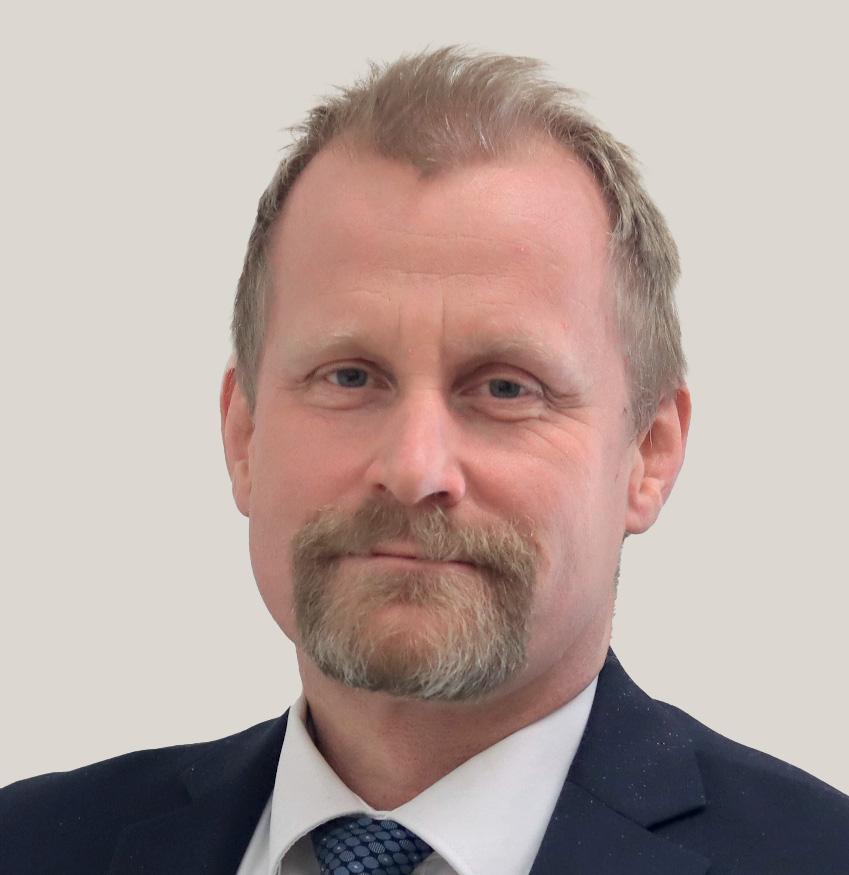

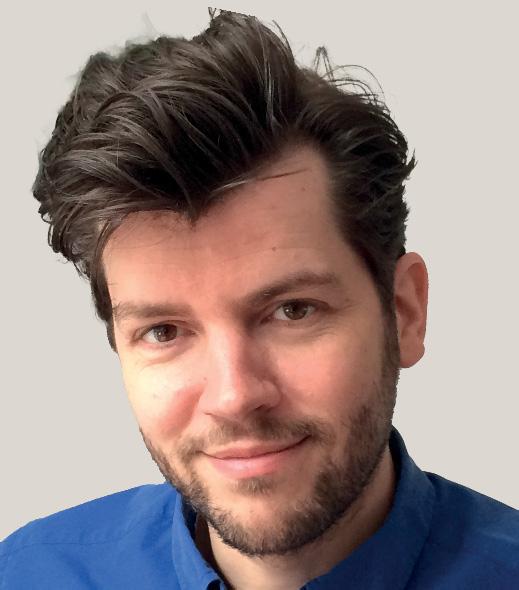
An increasing amount of wind assist means the engine load decreases for the same service speed, so more output flexibility is needed from the powertrain. Wärtsilä will focus on medium speed engine designs to provide this flexibility, as the classic two-stroke and controllable pitch propeller layout may no longer be the optimum solution.
Sebastiaan Bleuanus, General Manager for research coordination and funding at Wärtsilä, notes that traditionally these bulk carriers would sail at 12.5 knots, but it is now typically 10 knots. With around 30% of propulsive power provided by the WindWings, the engine load will be even lower. “We need a lot more operational flexibility,” he says. “We're sure the conventional layout is not optimum, so one of our major development items here is to determine what the best power train would actually be. Would it be one single engine, driving a single propeller through a gearbox? Would it be diesel-electric? Would it be two engines, one twin-in, single-out gearbox driving a single propeller? And on top of that, we will be working on route optimization to take maximum advantage of anticipated wind conditions.”
A gate rudder system, consisting of a rudder either side of the propeller rather than behind it, offers enhanced manoeuvrability and better efficiency and is expected to reduce fuel consumption by around 10%. With the rudders situated beside the propeller, the total propulsion train is reduced in length, freeing up more space for cargo or passengers. The actual savings will be modelled using CFD techniques rather than at full-scale. “Quite simply, if you want to test all of these technologies at full-scale, you will run out of money,” says Bleuanus. “The gate rudder can be done quite well using CFD, and by doing it virtually, we free up funds for other things, like the sails, which we were very keen on to demonstrate in practice.”
HYDROGEN FUELLED CRUISE SHIP
The cruise ship will operate with a gate rudder system and a Wärtsilä designed engine running on hydrogen fuel. Wärtsilä is doing the engine development including injection technology, with the University of Vaasa responsible for the fuel system, piping, pressure controls and bunkering stage. Wärtsilä has already demonstrated its current internal combustion engines can operate on LNG mixed with 20% hydrogen. The goal now is pure hydrogen which could take two years of development, leaving the third year of the project for lab-based demonstration.
Senior Project Manager, Kenneth Widdel, who will lead Wärtsilä's participation in CHEK, emphasises that the project will look at the vessel designs from a total cost of ownership perspective. “We're not just stacking on different technologies. Rather, we are seeing how they work and interact together and how to get the best out of that interaction.” He says that optimising system integration, energy flows and waste heat recovery will be key components, particularly for the cruise ship design effort.
The CHEK project dovetails with Wärtsilä's extensive investments in developing an ecosystem of co-creation including the company's Smart Technology Hub in Vaasa. “There is no silver bullet to meeting the challenge of combating climate change,” says Jonas Åkerman, Director of Research and Technology Development at Wärtsilä. “You need to exploit a number of parallel paths, and that's exactly what we are doing together with our partners here. What makes the project so exciting is that we are stretching what is economically viable to be done.”
RULE DEVELOPMENT
In February, Lloyd's Register (LR) released its Guidance Notes for Fuel System Risk Assessments, Hazard Identification - Hydrogen, and the project will contribute towards LR's work to build on the guidance to develop Rules to ensure that the risks of using hydrogen as a fuel are mitigated. “The work being undertaking on this project on design, risk assessment and testing of the hydrogen engines will be a useful in strengthening the Rules and our understanding of the safety aspects of hydrogen as a fuel,” says Chris Hughes, LR's Global Lead, Shipping Markets.
“For several of the technologies included in the project, we are starting from a relatively strong point in terms of existing rules and experience. For some of the newer technologies, there are safety challenges that need to be considered, and the project includes work packages that investigate these and assess the risk of the solutions developed.”
WHAT THE INDUSTRY WANTS
LR's scope also includes work on modelling the efficiency gains, assessing infrastructure requirements beyond the ships and development of new commercial models that will facilitate the uptake of the solutions developed. Hughes says having end-users such as Cargill and MSC Cruises involved ensures that the technology solutions developed are practical, viable and what the industry ultimately wants. sks of using hydrogen as a fuel are being undertaking on this project on nt and testing of the hydrogen eful in strengthening the rstanding of the safety as a fuel,” says Chris ead, Shipping Markets. echnologies included in tarting from a relatively s of existing rules and of the newer technologies, nges that need to be roject includes investigate risk of the
WANTS
cludes the ssing ments and new at will facilitate ons developed. nd-users such uises involved technology are practical, he industry
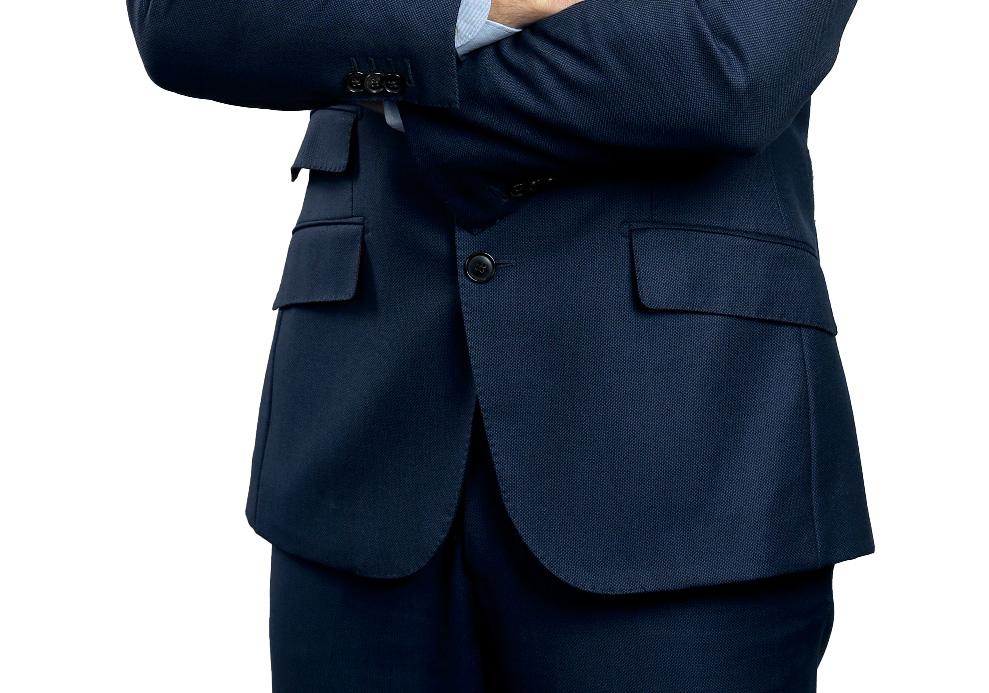
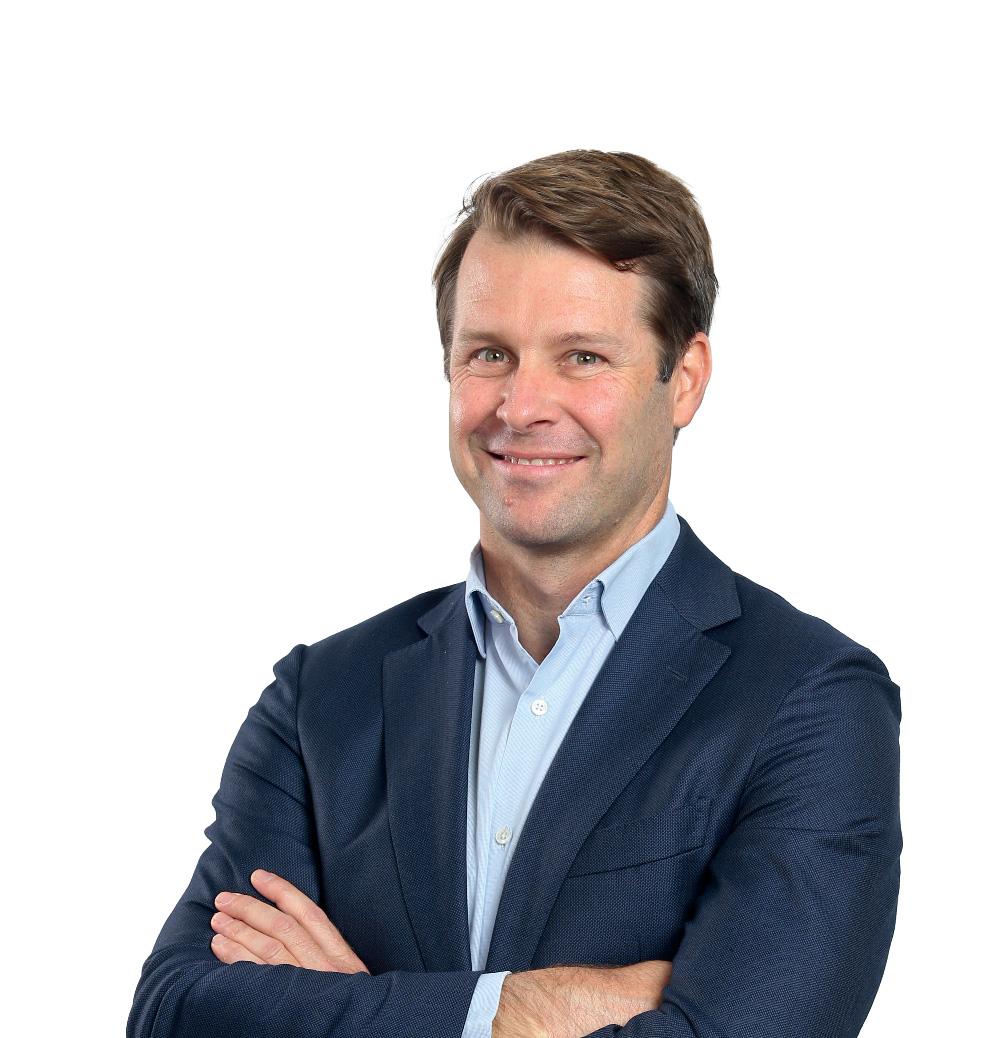
8 From left to right:
Kenneth Widdel, Senior Project Manager at Wärtsilä; Mia Elg, R&D Manager at Deltamarin and Sebastiaan Bleuanus, General Manager for research coordination and funding at Wärtsilä
8 Chris Hughes,
Lloyds Register's Global Lead, Shipping Markets
GREENER METHANOL SUPPLY TO MEET RISING SHIPPING DEMAND
Green methanol is establishing itself as a contender in the 2050 bunker fuel market, with the chemical industry motivated to go green and new production facilities and new ships raising optimism around the world
The pricing of sustainably produced methanol means that its uptake as a bunker fuel will likely need the social and political mandate that is already building towards 2030 and 2050 deadlines. A technology transition will also be required for greener methanol, and it will be required at scale. A recent report, Innovation Outlook: Renewable Methanol by the International Renewable Energy Agency (IRENA) and the Methanol Institute recognises this but maintains a positive outlook because of the many benefi ts methanol has over competing future fuels.
As a marine fuel, methanol emits no sulphur, very low particulate matter and, according to data from MAN Energy Solutions, it results in carbon dioxide emissions around 20% lower than conventional marine fuel oil. To meet IMO NOx Tier III requirements, methanol can be blended with water, negating the need for expensive exhaust gas after treatment. It is also miscible in water and readily biodegradable, characteristics that the Methanol Institute says make it ideal for use in polar waters.
“Methanol provides considerable retrofit potential as an IMO compliant bunker, being very close to a drop-in fuel for most 2 or 4-stroke marine engines. As such, some vessels may be cost effectively repurposed, extending their useful lives in the process,” says Chris Chatterton, COO of the Methanol Institute. “Methanol's share of the marine market may be difficult to predict today, but it seems that it will steadily increase the closer we move to 2030 as experience with it as a compliant fuel is shared, pricing visibility is maintained and availability is proven up.”
The cost of producing fossil-fuel based methanol is

Credit: Methanex
currently in the range US$100-250, and it is already a competitive option, at least for Emission Control Areas, states the IRENA/Methanol Institute report. By 2050, the cost of bio-methanol (produced using waste biomass streams) could be US$220-560, and the cost of e-methanol (produced using green hydrogen and CO2 captured from renewable sources) could be between US$250-630 per tonne.
It's still not clear how methanol prices will compare to key competitors such as hydrogen and ammonia, but it is likely to be cheaper to move, store and to repurpose existing infrastructure to accommodate its use as a bunker fuel. Ammonia is likely to take five to 10 years to be cost competitive and available at scale for shipping. For hydrogen, it will probably take 15 to 20 years.
SUPPLY/DEMAND BALANCE
Current global demand for methanol at close to 100 Mt per year and growing. The report estimates that by 2050, there could be 135Mt of methanol produced from biomass, 250Mt produced from green hydrogen and captured CO2 and 115Mt from fossil fuels. Demand from land and marine transport will be a key driver for the production of renewable methanol due to increasing regulation of GHG emissions.
The top five methanol producing countries are China, Saudi Arabia, Trinidad and Tobago, Iran and Russia. Methanol (CH3OH) is typically produced from fossil-fuel based natural gas by reforming the gas with steam to produce syngas (hydrogen and carbon monoxide) and then converting and distilling it to produce methanol (steam methane reforming).
Less than 0.2Mt of renewable methanol is produced
8 Methanol has
been produced at Methanex's Motunui plant in New Zealand since 1999
annually, mostly as bio-methanol. Green production alternatives include using the pyrolysis of biomass to produce the syngas, the use of electrical heating from renewable power sources for the energy-intensive reforming step or the auto-thermal reforming of methane where an extra exothermic step, typically partial oxidation, is used to generate the necessary heat to complete the reformation.
Producer BASF, for example, is now producing methanol as a biomass balanced product, replacing the fossil resources needed with biogas or bionaphtha. This means that BASF reduces greenhouse gas emissions by at least 50% compared to methanol produced from fossil raw materials.
Methanex, the world's largest producer of methanol, is currently involved in a number of green methanol initiatives including in Iceland where the company has invested in Carbon Recycling International (CRI). CRI operates the world's first renewable methanol plant which uses emissions-toliquids technology, converting renewable energy and recycled CO2 emissions to renewable methanol. In Canada, Methanex produces low-carbon methanol through sequestration and injection of CO2 into the production process.
GREENER PRODUCTION ROUTES
A study led by the University of the West Indies evaluated the cost and sustainability of multiple different future technologies for producing methanol. The researchers found that both pyrolysis and auto-thermal reforming (ATR) were the premiere climate-smart choices for production when based on circular CO2 utilisation and storage. ATR proved to be the least energy demanding technology, mainly due to the high energy recovery from the partial oxidation that powers the reformation.
Solar-powered electrolysis was also a sustainable solution, but one that was determined to be significantly less profitable than pyrolysis. “The problem with renewables is the economies of scale issue,” says Dr Keeran Ward, study coauthor. “Although the technology is getting cheaper, it can't compare with large scale or even normal scale production capacity. For example, a 5,000 MTPD methanol plant requires about 50 tonnes/h of hydrogen while large scale electrolysis can produce 50 tonnes/day.”
He foresees a gradual transition away from cheaper, nonsustainable fossil fuel-based production, although ATR technologies are already mature enough for new projects. “And it has been shown that ATR is cheaper than steam methane reforming at large scale production capacities (5,000MTPD and higher), so logically it will be the winner.”
Methanex also considers it the most economically viable technology when there is excess hydrogen from the purge gas of its existing steam methane reforming plants. The company is developing a project in the US based on ATR.
Construction of a growing number of renewable and biomethanol plants have been announced globally including in China, the US and numerous EU states, and for e-methanol, new production can be readily sited close to renewable power capacity, with access to both water and CO2.
This significantly broadens the potential for new production hubs. For example, in January, Germany-based energy and chemical provider Mabanaft and Chile-based Highly Innovative Fuels (HIF) announced a Memorandum of Understanding in relation to the purchase and sale of up to 500 million litres of carbon neutral e-fuels per year from HIF's projects located within Chile including a project that will use wind power to produce hydrogen which will be combined with CO2 extracted from the atmosphere to produce methanol. The methanol will then be converted into gasoline.
Swedish energy supplier Övik Energi is providing access to one of its biofuel-based energy facilities to Sweden-based Liquid Wind so that the facility's carbon dioxide emissions will be captured and combined with renewable hydrogen to form methanol using wind power. Once operational in 2024, the fuel facility will upcycle 70,000 tons of CO2 into 50,000 tons of carbon neutral fuel annually and make it available as a shipping fuel.
Liquid Wind's plant will include technology from partners such as Axpo, Carbon Clean, Haldor Topsoe and Siemens Energy. Having secured crowdfunding partners in Europe, Liquid Wind is now crowdfunding in Canada, a country it says could be a prime location for e-fuel production, as it is growing in both hydrogen and carbon capture industries. Liquid Wind is planning 500 facilities by 2050, providing 25 million tons of fuel.
Haldor Topsoe has announced the construction of a facility to produce solid oxide electrolyzers (SOEC) with a total capacity of 500MW per year with the option to expand to 5GW per year. With Topsoe's SOEC electrolyser, more than 90% of the renewable electricity that enters the electrolyser is preserved in the green hydrogen it produces, compared to around 70 % for alternatives such as PEM and alkaline electrolysis technologies. The high operating temperature of SOECs offers more favourable thermodynamics and faster kinetics, and the technology uses abundant raw materials such as nickel, zirconia, and steel.
The SOEC technology can be thermally integrated with a range of chemical synthesis processes enabling the efficient production of future fuels such as methanol and ammonia. The company says that electrolysis technologies play a central part in power-to-X solutions, and to meet the future needs for decarbonization globally, electrolysis technologies must be deployed at a massive scale.
METHANOL AS MARINE FUEL
Methanol is already available in around 100 ports around the world and is being used on around 20 large ships. There is more coming, with Proman Stena Bulk expecting to take delivery of a methanol-fuelled 49,900dwt vessel in early 2022. Waterfront Shipping Company, a wholly-owned subsidiary of Methanex, has announced eight new methanol fuelled dualfuel ships to be built at Hyundai Mipo Dockyard and delivered between 2021 and 2023 in partnership with Marinvest, NYK, Meiji Shipping, KSS Line and Mitsui O.S.K. Lines.
Fredrik Stubner, Director Ship Management at Marinvest Shipping, says it is difficult to predict the future economics of
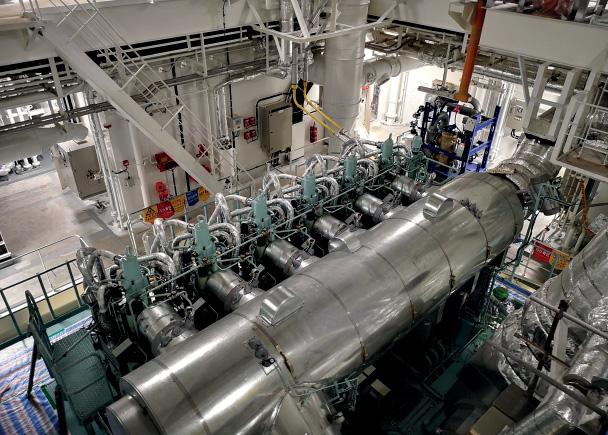
8 The interior of
the engineroom of Marinvest's methanol-fuelled tanker, Mari Couva
using bio-methanol and e-methanol. “What will the carbon taxes be? What incentives will contribute towards paying a premium for de-carbonized fuels? With stricter regulations and the cost to comply with them, it is expected it will tilt the balance in favour of greener solutions.”
He says that LNG is a cheaper fuel source, but the cryogenic technology required is expensive compared to methanol, a stable liquid at ambient temperature that is easy to store onboard. “I can't say methanol will be a winner, but it is definitely one very good alternative. One has to keep in mind that the alternative greener fuels have less energy value, meaning larger amounts are required to meet the required cruising range for a specific vessel type and trade. So how to store the fuel whilst maintaining an equivalent cargo volume as before needs to be considered.”
A white paper from Chevron Marine Lubricants notes that a vessel would need to burn about twice as much methanol to produce the energy equivalent of MGO. This raises concern about the size of bunker tanks, but as it is biodegradable, methanol can be stored in ballast tanks in some cases. As a low flashpoint fuel, there are fuel system design requirements such as double-walled piping to the engine, but the white paper concludes that the premium for upgrading a newbuilding to be dual-fuel methanol is typically less than five percent.
MAERSK'S METHANOL-FUELLED LINER
A.P. Moller - Maersk is accelerating its efforts to decarbonise with the planned launch of the world's first carbon neutral methanol-fuelled liner in 2023 - seven years ahead of its initial 2030 ambition. However, a spokesperson for the group says: “At the moment, there is no at-scale production of carbon-neutral e-methanol or sustainable bio-methanol with net-zero emissions across the lifecycle. There are a number of pilot projects and projects under development, and we are engaging with these projects so that they can advance to ensure we have carbon-neutral fuel available by the start of the feeder operation.”
One project is a partnership with Copenhagen Airports, DSV Panalpina, DFDS, SAS and Ørsted for the development of a hydrogen and e-fuel production facility in Copenhagen which could start producing hydrogen by 2023 and methanol by 2027. When fully scaled-up by 2030, the project could deliver more than 250,000 tonnes of sustainable fuel annually. Production would potentially be based on a total electrolyser capacity of 1.3 gigawatts, making it one of the world's largest facilities of its kind, and a large-scale supply of renewable electricity could be obtained from offshore wind power produced at Rønne Banke off the island of Bornholm.
Investing in the methanol feeder is anticipated to stimulate development further. “If we - through commitment from customers - can create a real market at a reasonable price point, we believe that the combined effort and collaboration of developers, manufacturers, financers and carriers can accelerate the supply quite fast.”
For Stuart McCall, Head of Global Marine Fuel, Market Development at Methanex, it too early to tell what production volumes from new sources will be in 2050 with any degree of certainty. “All we can say at this stage is that the green methanol market, like most alternative fuels, is small but growing.”
The most important future development, he says, “is simply to encourage the shipping industry to use the dualfuel technology we have today to start the transition to a lower-carbon economy. We can't let perfect get in the road of good. Conventional methanol will immediately offer up to a 15% reduction in in-sector CO2 as well as complying with the strictest air emission standards in place today. Methanol dual-fuel technology is proven; it's globally available; it's cost-competitive with conventional fuels and is lower emission. We just need regulations to encourage the use of cleaner fuels. Methanol is also future-proofed as it offers a clear pathway to 2050 decarbonization goals.”

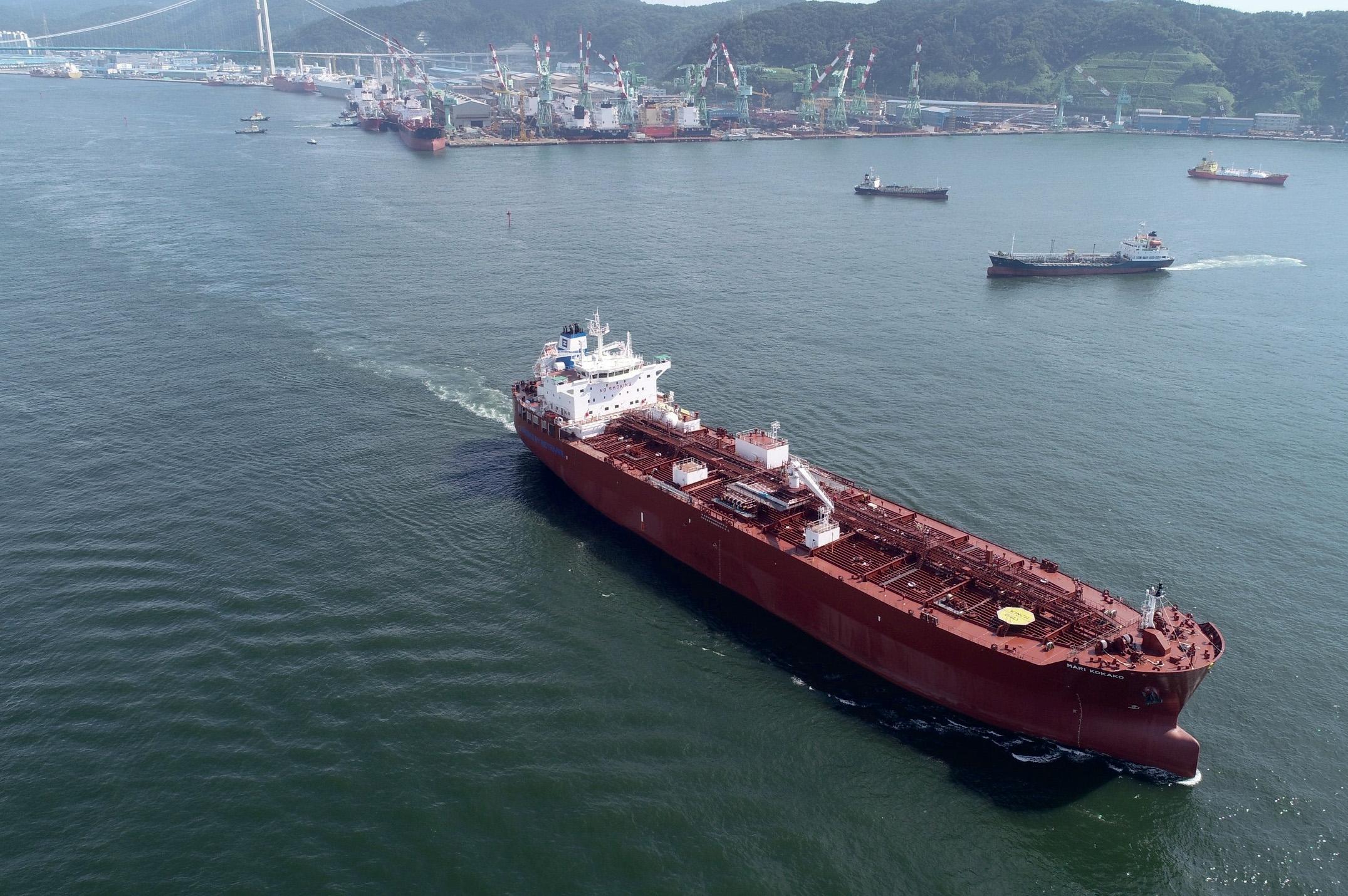
Credit: Marinvest
l metha anol will reducti tion o in plying w with it t andards in dual-fuel globally ive with emission. encourage anol is also ar pathway to
8 Mari Kokako is
fi tted with a six-cylinder 500mm-bore MAN B&W ME-C9.5 LGIM main propulsion engine
8 Chris Chatterton,
COO of the Methanol Institute
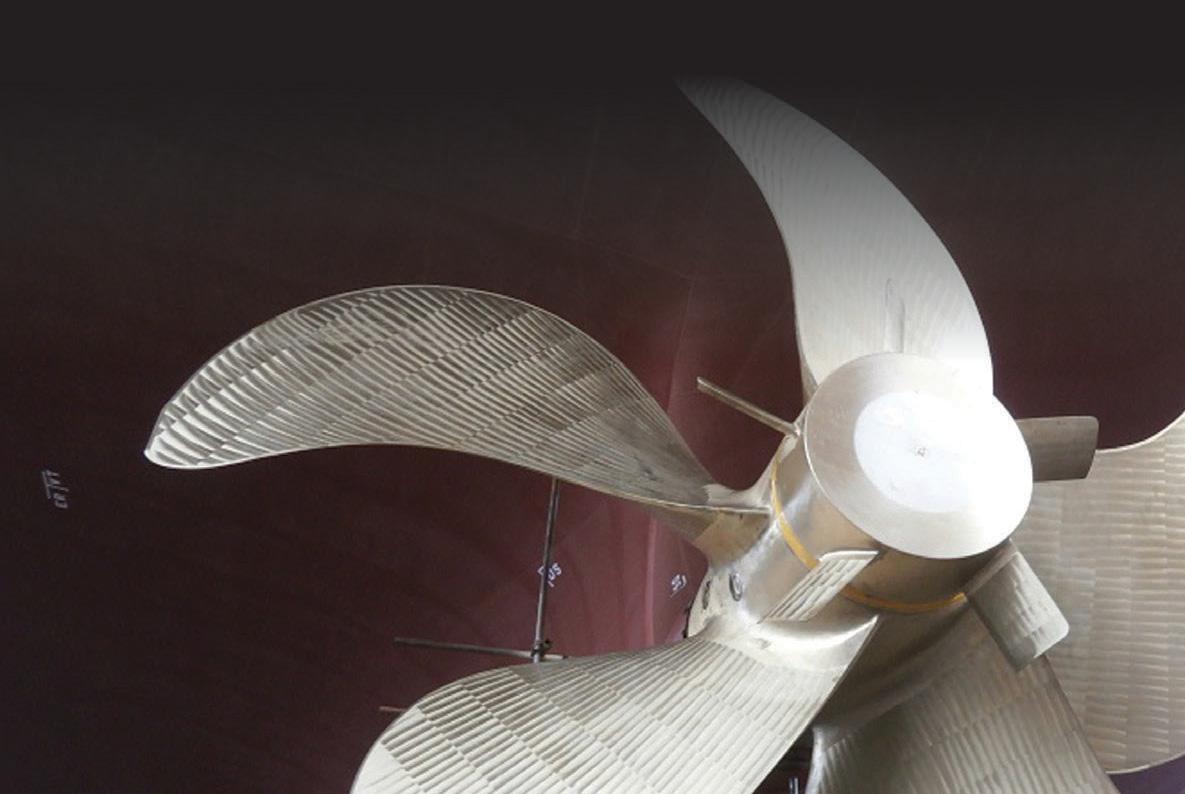
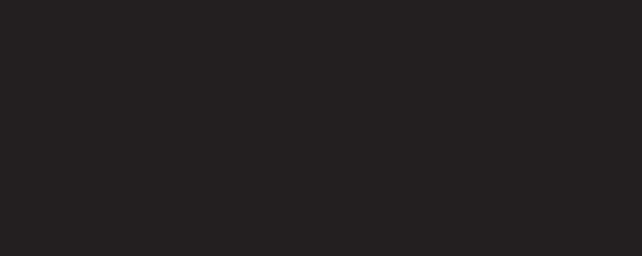
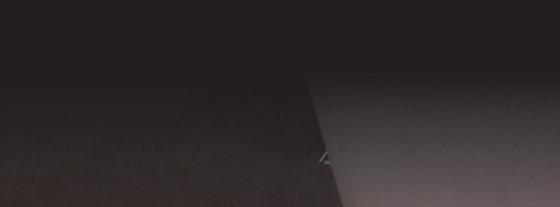



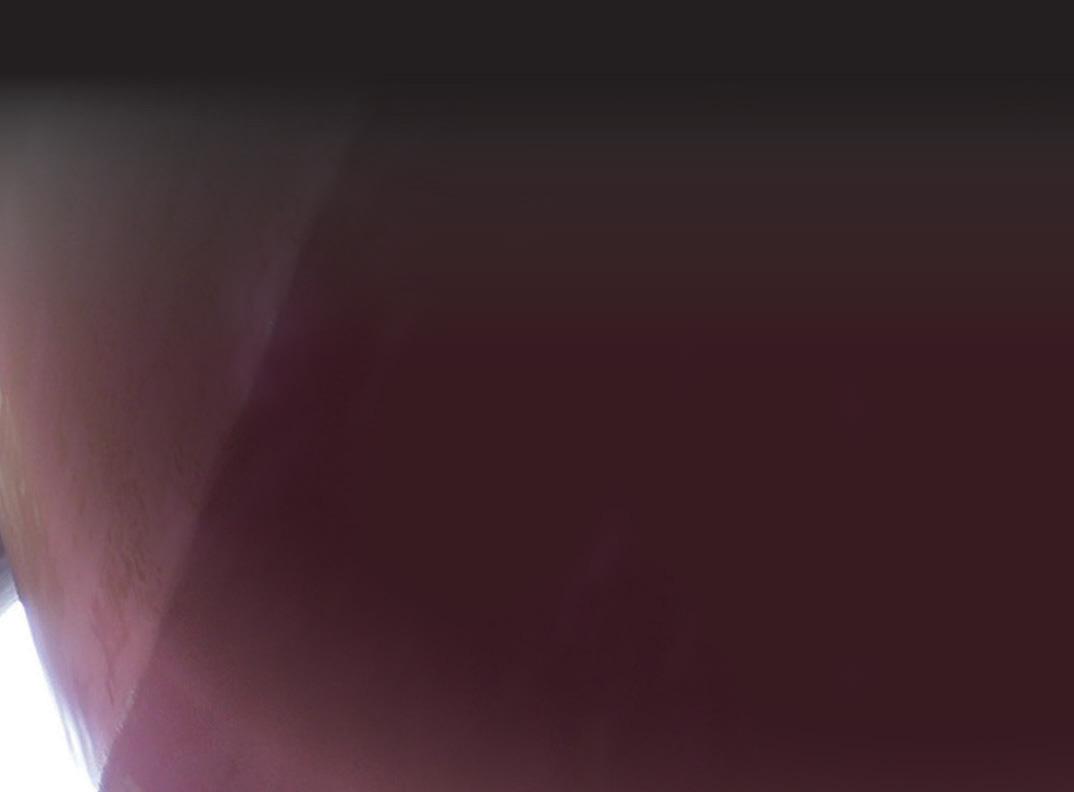
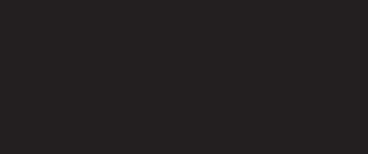
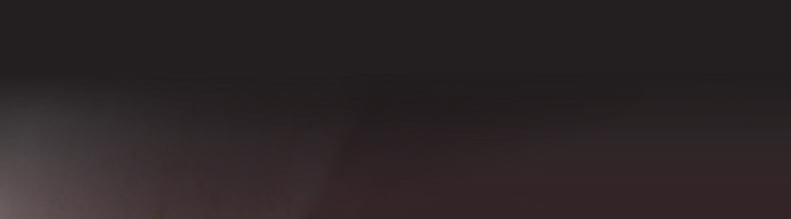

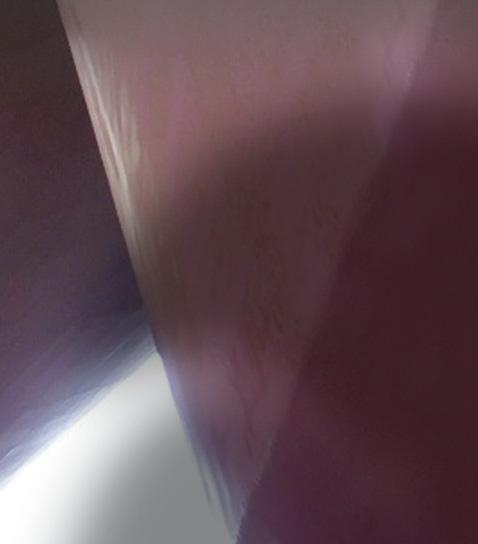



