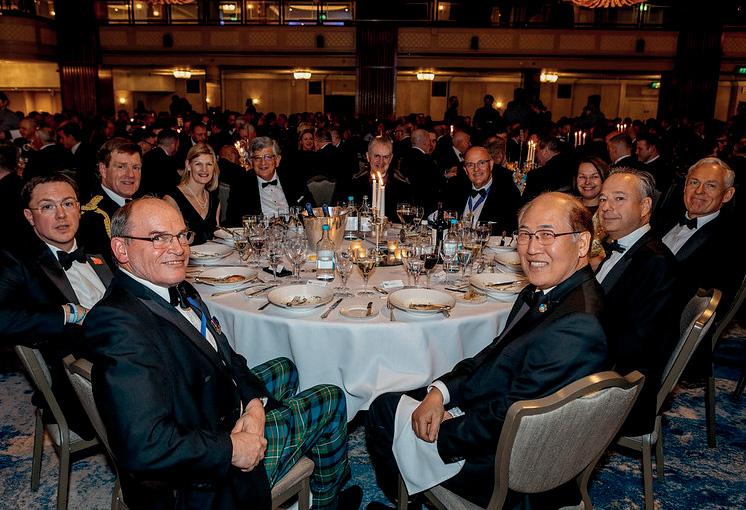
17 minute read
UK consultation on shore power
UK LAUNCHES CONSULTATION ON SHORE POWER
The UK government launched a consultation in February 2022 to form a fully considered cost/benefi t analysis around the proposed introduction of shore power charging in the UK
The announcement by the UK government that it was launching a fresh consultation around the vexed issue of shore power connections in the UK has come as no surprise to market participants. The consultation was originally expected to be launched before the end of 2021.
It is asking the industry to provide detailed submissions around different options outlined below. The consultation will run from 7 February 2022 until 25 April 2022.
The responses to the consultation will help to inform further policy development work, as part of the Clean Maritime Plan. The final actual proposals will form part of the 2023 refresh of the Clean Maritime Plan Mark Simmonds, director of policy and external affairs at the British Ports Association told The Motorship.
CONSULTATION AREAS
There are three broad areas that are being addressed by the consultation. The first covers the potential role of the government in helping to coordinate the development of shore power connections, as well as wider information sharing.
While the Decarbonisation Tool for Ports that was launched by the National Grid in September 2021 has helped to capture the energy demand from some of the UK’s myriad smaller ports, there is still some uncertainty about current and future requirements. Obtaining a more accurate estimate of the cost of grid strengthening to extend higher capacity grid connections to smaller ports is expected to be one of the key deliverables from the consultation.
The second focuses on the potential for the UK to impose requirements for the use of shore power connections, both on ports and vessels calling at UK ports. This could also include a requirement for vessels and ports to report on the usage of shore power.
Critics have warned that introducing requirements for higher standards than competing countries could disadvantage UK shipbuilding and discourage investment in UK-domiciled fleets.
The consultation is intended to obtain detailed information about the scale of vessel emissions at berth, the actual potential of shore power alongside other technologies in reducing emissions, the barriers to the commercial take-up of shore power and the impact of potential solutions to enable the roll out of this technology.
MARKET-BASED MEASURES
However, it is the suggestion that the consultation could see the UK introduce its own market-based measures to incentivise the adoption of shore power by vessel and port operators that has provoked the strongest responses.
The president of the UK Chamber of Shipping, John Denholm, addressed the issue directly in a speech delivered shortly after the launch of the consultation, warning the UK against establishing a national Emission Trading Scheme modelled along the lines of the EU’s regional model.
“A plethora of regional market-based measures would put a terrible burden on our industry, depress trade and would inevitably be inequitable. Instead, we ask you to campaign against nations setting up regional or national market-based measures.”
LOCAL FACTORS
Finally, the consultation document directly addresses a number of local obstacles to the accelerated roll-out of shore-power connections in the UK.
The economics of the use of shore power connections for ship owners and operators remains uncertain at best, and unsupportive at worst. Put simply, electricity prices in the UK are among the highest in Europe. The consultation document notes that ship owners and operators in Norway, by comparison, enjoy some of the lowest prices of electricity for commercial users in Europe.
The current requirement for end-users to directly contribute to the cost of grid strengthening work could potentially be replaced from early 2023, if a proposal by the energy regulator is accepted.
The report identifies supply and demand issues as an obstacle to ports investing in shore power connections more widely, and speculates that the prohibitive cost of shore power retrofits may act as a barrier to adoption.
Up until the present, few port operators in the UK have shown any interest in installing shore power connections in the UK. Commercial installations have until now been limited to Orkney and Southampton.
Natasha Gray, Corporate Communications Manager at Associated British Ports stressed that the shore power facility for cruise ships at the port of Southampton would contribute to lowered emissions at the port. “By introducing the option for cruise ships, with onboard capability, to plug in while alongside, the port could start seeing CO2 emission savings of up to 863 kg in CO2 and 10.5 kg of Nitrogen Oxide (NOx) per vessel call each year,” she concluded.
8 The port of
Orkney installed the UK’s fi rst intermediate voltage shore power connection in 2020
ULSTEIN APPLIES OLD HYBRID APPROACH TO NEW TRAWLER
Norway’s maritime cluster opens a new chapter in the roll-out of greener fi shing following the confi rmation of an order for a hybrid factory trawler combining diesel and electric power
The order for a 73-metre factory trawler at Westcon Shipyard for Blue Wild, an Ålesund-based Norwegian ship owner was confi rmed in early February 2022. The new trawler will primarily be used for prawn and whitefi sh trawling.
The stern trawler has been designed by Ulstein Design & Solutions AS, which based the design on its existing FX101 demersal trawler concept. The new order is expected to usher in a new design segment for Ulstein: the new factory trawler combines a twin skeg propulsion concept with Ulstein’s existing proven hybrid diesel-electric and dieselmechanical propulsion solution.
By combining the diesel-mechanical and diesel-electric systems into one larger hybrid propulsion system, the new system will occupy less space and cost less than a larger diesel-electric system. Compared to similar conventionally propelled vessels, fuel savings of up to 25% are expected, depending on the mode of operation.
The hybrid power and propulsion system, which combines the best features of diesel-electric and diesel-mechanical propulsion, is supported by a 1.1MWh battery pack. The battery pack will recover surplus energy, such as the return energy from the winches, which can be stored in the battery pack, while excess heat from the engines will be recovered and used where desired elsewhere in the ship.
Ulstein noted that it mapped how the vessels use their power system, and identified trawling as the most important mode of operation. It was therefore chosen to install two propellers instead of the traditional solution with one propeller because the increased propeller area increases the vessel’s towing efficiency. The propellers are placed in separate skegs in a twin-skeg hull, which provides great advantages in terms of placement of the propulsion equipment and increases the propeller efficiency.
“Once you go for two propellers, you get new opportunities to operate the vessel in ways you do not have on vessels with only one. By calculation, two propellers use less energy together than one propeller to achieve the same towing power. Also, one of the propellers can be loaded more than the other to steer the vessel. Generally, fishing vessels get a large added resistance when compensating for wind, waves and currents with large rudder angles,” says Erwin Jager, sales manager fisheries at Ulstein Design & Solutions.
The stern trawler has been designed by Ulstein Design & Solutions AS, which based the design on its existing FX101 demersal trawler concept. The new order is expected to usher in a new design segment for Ulstein: the new factory trawler combines a twin skeg propulsion concept with Ulstein’s existing proven hybrid diesel-electric and dieselmechanical propulsion solution.
By combining the diesel-mechanical and diesel-electric systems into one larger hybrid propulsion system, the new system will occupy less space and cost less than a larger diesel-electric system. Compared to similar conventionally propelled vessels, fuel savings of up to 25% are expected, depending on the mode of operation.
The hybrid power and propulsion system, which combines the best features of diesel-electric and diesel-mechanical propulsion, is supported by a 1.1MWh battery pack. The battery pack will recover surplus energy, such as the return energy from the winches, which can be stored in the battery pack, while excess heat from the engines will be recovered and used where desired elsewhere in the ship.
Ulstein noted that it mapped how the vessels use their power system, and identified trawling as the most important mode of operation. It was therefore chosen to install two propellers instead of the traditional solution with one propeller because the increased propeller area increases the vessel’s towing efficiency. The propellers are placed in separate skegs in a twin-skeg hull, which provides great advantages in terms of placement of the propulsion equipment and increases the propeller efficiency.
“Once you go for two propellers, you get new opportunities to operate the vessel in ways you do not have on vessels with only one. By calculation, two propellers use less energy together than one propeller to achieve the same towing power. Also, one of the propellers can be loaded more than the other to steer the vessel. Generally, fishing vessels get a large added resistance when compensating for wind, waves and currents with large rudder angles,” says Erwin Jager, sales manager fisheries at Ulstein Design & Solutions.
“During the most energy-intensive operations, such as shrimp fishing with quadruple trawl, both main engines will be used, mechanically connected to each propeller to be most efficient at high power. But the vessel should also be able to operate efficiently with lighter trawling that requires less engine load, and it has been enabled to do so in diesel-electric mode with only one of the main engines in operation. Operating time between the engines will be reduced, while the operative engine will be allowed to run more optimally. The propellers can then run at a very low speed, which gives very high efficiency during trawling, the vessel will be quieter and little power is needed to operate the ship. In this way, the advantages of both diesel-mechanical and diesel-electric power systems are utilised, while many of the disadvantages will be avoided.
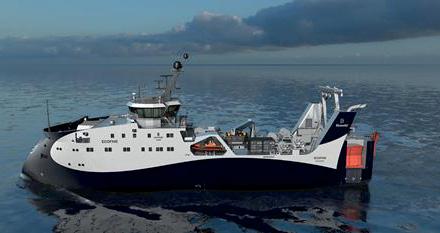
8 Alesund-based
fi shing company Bluewild has contracted a factory trawler from Westcon Yards
NEW BLUE-CHIP REFERENCE FOR METHANOL FUEL
A further milestone in the development of the tanker fl eet controlled by Stena Bulk will be marked by the handover of a methanol-fuelled chemical/product carrier marrying the principle of more ‘sustainable’ shipping with sharper competitiveness
Currently fi tting out in China, the 49,900dwt Stena Pro Patriawill give fi rst form to the IMOIIMeMAX design, the enhanced, dualfuel version of the innovative IMOIIMAX generation delivered between 2015 and 2018, ranking among the most energy effi cient medium-range tankers in existence. The versatile, IMO Type 2 newbuild will also operationally inaugurate the collaboration agreement struck in 2019 between the Swedish company and the Swiss-headquartered energy fi rm Proman, the world’s second largest producer of methanol.
Three such vessels have been ordered from Guangzhou Shipyard International (GSI) by the Stena Proman joint venture, while a further three newbuilds of the class have been booked at the Chinese yard to Proman’s own account.
The IMOIIMeMAX type perpetuates the features and qualities of the IMOIIMAX, but with the addition of methanol dual-fuel power. Stena Teknik and GSI were jointly responsible for drawing up the IMOIIMAX design, subsequently produced as a 13-ship series led by the Stena Impression in January 2015.
IMOIIMAX coupled increased cargo flexibility with reduced fuel consumption resulting from scrutiny of every sphere of energy usage. The aggregate effect of the combination of technical solutions adopted was a 10-20% reduction in energy consumption compared with other vessels of a similar size.
Each of the original series is fitted with a 6S50ME-B9.3 diesel engine, featuring low-load optimisation and exhaust gas bypass. Keeping faith with the marque, and using a similar engine structure and footprint, Stena Bulk and its partner have opted for a new development in dual-fuel powering. In this, the tanker programme provides a further reference for the latest iteration of MAN Energy Solutions’ ME-LGIM dual-fuel two-stroke engine design, the LGIM-W type, which burns a mixture of methanol and water.
Incorporating a special blending system, the addition of water to the methanol fuel achieves Tier III NOx compliance, without needing exhaust gas recirculation (EGR) or selective catalytic reduction (SCR). Methanol is not only a sulphur-free fuel, thereby virtually eliminating SOx emissions, but is also less pollutant in CO2 terms than conventional fuels.
The actual model fitted in the tanker, and as specified for each of the subsequent vessels, is a six-cylinder G50ME-C9.6LGIM-W, to run on methanol while affording the capability to operate on conventional marine fuel, allowing seamless changeovers between fuels. The so-called ‘grey’ methanol that the ship will bunker is produced using natural gas as feedstock, but the engine type provides for future use of ‘green’ methanol derived from renewable sources. The vessel is expected to use some 12,000t of methanol per annum.
The power map for the six-cylinder engine nominated extends from 6,120kW at 79rpm, at the L4 rating point, to a nominal maximum continuous output of 10,320kW at the L1 rating, conferring substantial choice as to the contractual specification. In the case of the preceding IMOIIMAX tankers, the 6S50ME-B9.3 engine had been specified at 7,211kW, although the model’s nominal MCR was 10,680kW.
The Stena Pro Patria’s crosshead engine gives direct drive to a four-bladed propeller, abaft of which is a hub vortex absorbing fin to recover energy losses.
Clean nitrogen produced by a nitrogen generator, rather than ‘traditional’ inert gas and the associated generator, is used to facilitate the tank cleaning process and decrease the time between discharge and loading. Deriving gas for inerting purposes from a nitrogen generator is also claimed to be more efficient compared to an inert gas generator-based supply.
As befits its IMO Type 2 designation, the chemical/product carrier caters to a very wide range of cargoes, including vegetable oils, clean and dirty petroleum products, chemicals and caustic soda. The ship’s 16 cargo tanks and two slop tanks are uniform in filling capacity at 3,000m3, the maximum for Type 2 status. The large number of moderately sized tanks plus the wherewithal for eight segregations allows multiple cargo load configurations, conferring a ‘parcel’ carrying capability.
The handling system is based on 18 individually controlled deepwell pumps, rendering a high throughput rate and flexibility in cargo circulation. The tank cleaning arrangements are such that four tanks can be washed simultaneously using a layout that minimises shadow areas and contributes to expeditious turnaround times.
Stena Pro Patria and the second Stena Proman jointlyowned vessel, Stena ProMare, will enter long-term charter to Proman Shipping. Third-of-class Stena Prosperous will initially be utilised within Stena Bulk’s traded pool, for a period of two or three years, and will therefore be the first methanol dual-fuel tanker traded on the chemicals/clean petroleum products market without an active contract to a methanol producer. Thereafter, she will be engaged on longterm timecharter with Proman Shipping, which is based in Wollerau, Switzerland.
The second trio, for Proman ownership, will be named Provident, Progressive and Promise. The delivery schedule is due to be completed by the end of 2023.
The IMOIIMeMAX generation will transport methanol and other cargoes from Proman’s production hubs in Trinidad & Tobago and the USA to markets around the world, and will maximise the scope to handle a broad variety of products for backhauling. As well as offering a pathway to reduced emissions, methanol is viewed as a cost-competitive fuel available at all major bunkering ports.
PRINCIPAL PARTICULARS - Stena Pro Patria
Length overall 186.0m Breadth, moulded 32.3m Depth, moulded 18.5m Draught, scantling 13.0m Corresp. deadweight 49,900t Draught, design 11.5mW Corresp. deadweight 42,500ts Cargo capacity 54,000m3 Main engine MAN 6G50ME-C9.6-LGIM-W
RELIABILITY COMES INTO FOCUS
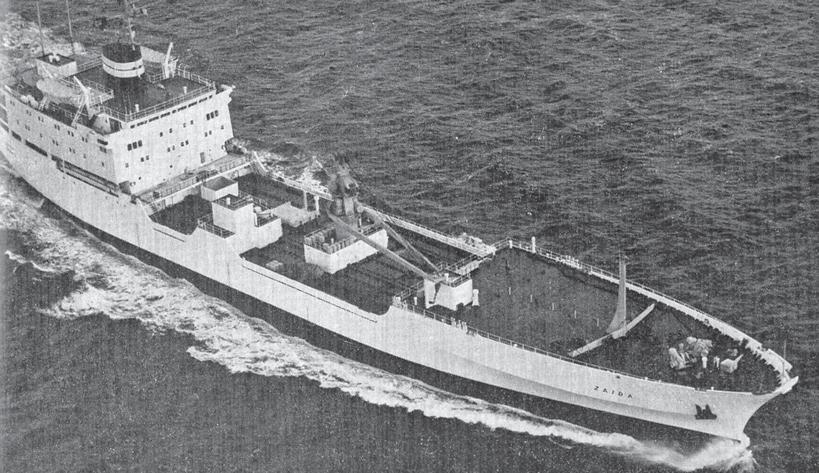
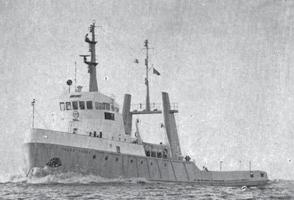
The February 1972 issue of The Motor Ship opened with the news that Great Britain had taken a major step towards joining the European Economic Community.
The reason for this rejoicing was that the move, alongside the revaluation of the Japanese Yen, was seen as offering a boost to British shipyards, which were suffering from a dearth of new orders. The hope was that the EEC could reinstate an investment grant system, which the British government had abandoned some years before. Ironically, similar hopes are still being expressed by British manufacturers following the recent decision to leave the European Union, the successor to the EEC, after over 40 years of membership.
With reefer container ships so common in today’s freight market, it was interesting to see a 132m long, 6,300 dwt, newbuild described as a “revolution in reefer ships”. The Zaida was built for the British India company by Swan Hunter, for use on a service carrying frozen meat between New Zealand and Japan. Lamb carcasses would be carried on special steel pallets loaded, via roller conveyors and a vertical lifts, through two shell doors, rather than the then-normal refrigerated holds with hatch covers. The system could be used too for standard wooden pallets carrying cartooned meat projects and butter. Additionally, 56 20-ft reefer containers could be carried on deck for transporting beef. The cargo system, although based on a previous development for Fred. Olsen vessels, was designed for programmable automatic operation. The automation and monitoring equipment extended to the Sabroe electrically-driven cargo cooling system and the machinery, a 12,000 bhp Doxford main engine supplemented by four 600kW alternators driven by Allen medium speed engines.
Other articles included an “answer to cylinder liner wear” – chromium molybdenum coatings – seen as a solution to a problem that had developed through engine developments such as the lower height of scavenging air ports and the use of high-alkaline
8 Refrigerated vessel Zaida featured a novel cargo
handling system. Inset - Polar Shore, which claimed to be the fi rst icebreaking AHTS vessel
cylinder oil when burning fuel oil with a relatively low sulphur content.
A further area of reliability concern was failure of stern tube seals. This was becoming particularly marked in VLCC vessels where the trend was for lower propeller speeds, necessitating a large diameter tail shaft to transmit the required power. Design and materials of lip seals were proving inadequate, and a long discourse presented several specific case studies and possible solutions. The conclusion was that, although many engineers preferred the simplicity of gravity feeds for stern tube lubrication oil, greater reliability could be obtained from an automated low-pressure oil feed driven by electric pumps, the extra cost of which was more than met by the prevention of delays resulting from emergency repairs.
Improved reliability was the focus too for Fujisan, a 101,000 dwt oil-bulk-ore carrier, the largest ship built by Gotaverken for the Brostroem Group. Using a shaft generator to power the cargo oil pumps offered a significant reduction in maintenance needed for auxiliary engines as well as a smaller steam installation, solely for cargo heating. A further measure was the use of fresh water machinery cooling rather than the normal sea-water system, considerably lessening the pipework needed. The Gotaverken 850mm bore, 9-cylinder, main diesel engine developed 19,800 bhp and was equipped with automatic controls and a monitoring system, to enable the main engine and the two small auxiliary engines to be operated from the bridge. The bridge controls extended to the Kamewa CP propeller, to enable manoeuvring while the engine room was unmanned, as well as to allow the use of the shaft generator for most of the electrical load.
Finally, a feature on British tug construction expressed disappointment about the current order situation, but found several notable new deliveries worthy of comment. The international magazine for senior marine engineers
EDITORIAL & CONTENT
Editor: Nick Edstrom editor@mercatormedia.com
Correspondents
Please contact our correspondents at editor@motorship.com Bill Thomson, David Tinsley, Tom Todd, Stevie Knight, Wendy Laursen
Production
David Blake, Gary Betteridge production@mercatormedia.com
SALES & MARKETING t +44 1329 825335 f +44 1329 550192
Brand manager: Sue Stevens sstevens@mercatormedia.com
Marketing marketing@mercatormedia.com
EXECUTIVE
Chief Executive: Andrew Webster awebster@mercatormedia.com
TMS magazine is published monthly by Mercator Media Limited Spinnaker House, Waterside Gardens, Fareham, Hampshire PO16 8SD, UK
t +44 1329 825335 f +44 1329 550192
info@mercatormedia.com www.mercatormedia.com
Subscriptions
Subscriptions@motorship.com or subscribe online at www.motorship.com Also, sign up to the weekly TMS E-Newsletter 1 year’s magazine subscription Digital Edition: £GBP177.00
© Mercator Media Limited 2022. ISSN 2633-4488 (online). Established 1920. The Motorship is a trade mark of Mercator Media Ltd. All rights reserved. No part of this magazine can be reproduced without the written consent of Mercator Media Ltd. Registered in England Company Number 2427909. Registered offi ce: Spinnaker House, Waterside Gardens, Fareham, Hampshire PO16 8SD, UK