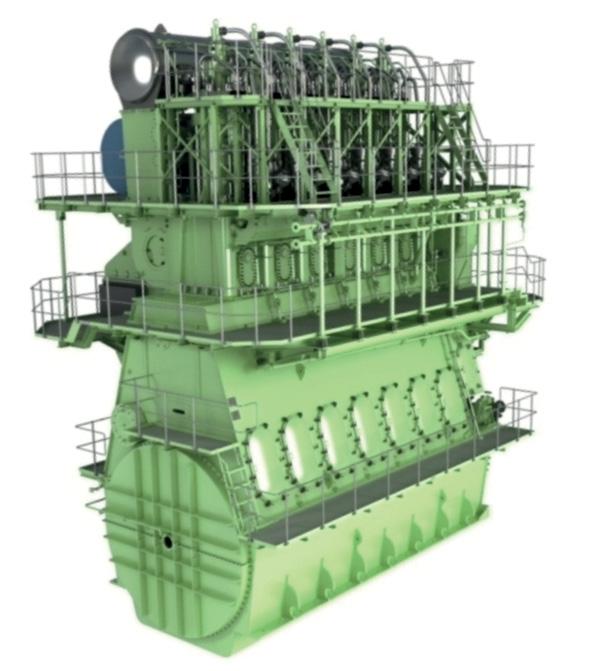
24 minute read
Hurtigruten oks hybrid retrofi ts
solutions to reduce the energy consumption more attractive on large vessels
PEAK SHAVING
The white paper assessed the viability of peak shaving - which keeps the engine load constant while peaks in the required power are supplied by a battery - for a main engine equipped with a PTO/PTI and a battery.
A modelling simulation was carried out using a 6G70ME-C9.5 engine with an SMCR of 15,570 kW at 72 rpm. The mean SFOC was calculated by integrating the total injected fuel mass and the energy delivered by the crankshaft. The integration was performed in an SFOC evaluation window of 100 seconds.
The study assessed that transmission and conversion losses in the electric generator and motor, which were estimated at 10% or around 1% of the overall load, exceeded the 0.4% SOFC savings achieved by peak shaving.
BARRED SPEED RANGE
A separate discussion concerned the potential applicability of energy storage systems to permit passage through the barred speed range. The topic is topical as tankers and bulk carriers are reducing the installed power on board to meet EEDI requirements, reducing the amount of power available to accelerate the shafting and the vessel.
The white paper provides a detailed explanation of the potential applicability of an ESS or auxiliary engine to boost the acceleration of the shafting through the barred speed range. MAN ES notes that the in the case of adverse weather conditions, a battery solution would not be able to keep the operational point of the main engine above the barred speed range for an extended period. An alternative option during adverse weather conditions would be to utilise energy from the auxiliary engines to provide additional torque to the shaft via a PTI.
BENEFITS OF BATTERY HYBRID SYSTEMS IN THE ELECTRIC GRID
The white paper concludes with an overview of the potential application of energy storage systems into the electric grid aboard a deep-sea vessel.
The potential for achieving savings by using a battery as a spinning reserve every time two or more auxiliary engines run at constant low load for safety purposes is identified. This can optimise the fuel consumption of the auxiliary engines by increasing the load on the engine by running only one of them. By operating auxiliary engines closer to their optimal load, it increases their efficiency, reduces their operating costs and lowers maintenance.
Meanwhile, the potential of peak shaving of auxiliary engines (or more) is examined. A battery installed for peak shaving leads to an operating cost reduction from acting as spinning reserve as well, as it will be possible to limit the time during which two auxiliary engines operate simultaneously.
MAN noted that introducing a high-power 217kWh energy storage system capable of operating for 15 minutes (sufficient to avoid blackouts and to restart a tripped auxiliary engine) in addition to three auxiliary engines would cost USD108,500 at current ESS prices, with a payback period of around 6 years. If ESS prices fall to close to USD250/kWh, the cost of the installation would halve, as would the payback period.
By comparison, the commonly assessed solution of replacing an auxiliary engine with a larger capacity ESS would have a higher cost, and a payback period of over 14 years.
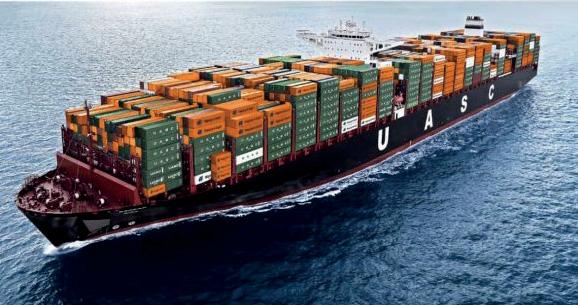
Credit: Hapag-Lloyd AG 8 Supplying
a 20,000 teu container vessel such as the Barzan (pictured) via a shore power connection would require 256MWh of energy per port call
8 The costs of peak
shaving outweighed the benefi ts in modelling of the applicability of ESS systems based on MAN's 70-bore ultra long-stroke G-type engine
Credit: MAN Energy Solutions
NEW MORE ACCURATE PRESSURE SENSOR
The Kistler Group’s new 6041C M8 miniature cylinder pressure sensor represents a new advance for small-size water-cooled cylinder pressure sensors for large marine and stationary engines
It incorporates state-of-the-art PiezoStar crystals and yields precise measurement results thanks to improvements to its design and manufacturing process. This versatile, reliable cylinder pressure sensor is the solution of choice for thermodynamic investigations in the engine development process, where overall accuracy is of highest priority.
Combustion engines are set to maintain a position in future propulsion concepts for many years to come, but new alternative fuels will challenge engine developers. Kistler has launched a portfolio of highly advanced sensors that provide maximum support for the development process in order to meet this challenge.
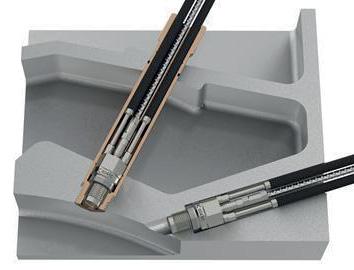
PRECISE AND STABLE MEASUREMENT
The new 6041C miniature cylinder pressure sensor is the third generation of Kistler’s smallest water-cooled sensor (size: M8) and features minimal sensor-to-sensor deviation during combustion pressure measurements. Thanks to the small linearity deviation, engineers are able to yield accurate measurement data at all loads.
Improved thermodynamic behavior creates more stable measurements within the operating temperature range of -20 to 350°C, with the sensor recording a sensitivity shift of under 0.2% 50 ± 30°C, even during thermal changes in the combustion chamber. Moreover, its thermal shock error is minimal, ensuring mean effective pressure (MEP) accuracy under all conditions. The miniature sensor features an optimised cooling flow around the measuring element to enhance its stability over long-term measurements and grants a longer service life without losing thermodynamic accuracy over time.
The use of PiezoStar crystals, which are grown specially by Kistler, also contribute to the pressure sensor’s reliability. They offer exceptional measurement stability and minimal temperature dependence in demanding environments. The sensors function reliably at temperatures of up to 350°C.
A ROBUST SENSOR FOR DIVERSE APPLICATIONS
Compared to uncooled sensors, water-cooled sensors have the advantage that they can be either recessmounted or flush-mounted, even when subjected to high thermal loads. Thanks to an advanced measuring element coupled with improvements to the production process, they provide measurement results with maximum accuracy. These advances also give the 6041C miniature cylinder pressure sensor higher natural frequency and excellent thermal stability so the sensor is optimized for gas exchange analysis tasks.
Like its predecessors, the 6041C cylinder pressure sensor requires only little space and can be mounted in a sleeve or directly into bore holes starting from 12mm diameter. The sensor is compatible for mounting with its predecessors 6041B and 6041A, and the
uncooled variants 6045A, 6045B and 6044A. The sensor comes with a mounted cable, and optional PiezoSmart sensor detection. Kistler notes that flush mounted installation is g element to recommended to avoid pipe oscillations, while a reduction ements and of the thermal load can be achieved with an up to 2 mm losing recessed mounting position. The further recessed mounting, with a small gas channel in front of the rown diaphragm offers excellent thermal-shock ssure protection but can be prone to pipe oscillations. If tional the sensor must be mounted through the water erature jacket of the cylinder head, it is recommended to sensors use a mounting sleeve.
C.
HIGHEST PRECISION FOR ENGINE DEVELOPERS
NS Roger Leutwyler, Product Manager for piezoelectric ensors cylinder pressure sensors at Kistler, comments: ecess- “High sensitivity, high natural frequency, a low ted to thermal shock error and outstanding zero-point suring stability: these advantages make our new 6041C the cylinder pressure sensor deliver measurement ement results with the highest accuracy. As a miniature s also sensor with an M8 mounting thread, it is particularly ensor suitable for compact multi-valve engines where ermal space is limited – and obviously, its benefits also hange come into play whenever precision and long-term stability are critical factors.” essure ounted ng from mounting and the recomme of the th rec mo dia pr the jac us
HI
Ro cy “H th st cy re se su sp co sta
8 The new 6041C cylinder pressure sensor is
compatible with highly advanced combustion engines that require high-performance measurement equipment
8 The new 6041C
cylinder pressure sensor from Kistler off ers engineers various installation options
MAN ENERGY SOLUTIONS INTRODUCES NEW LASER-TECHNOLOGY DRIVE SHAFT RINGS
MAN Energy Solutions has qualified a new high-friction ring for the drive shafts of its large 2- and 4- stroke engines.
The new rings have a surface texture created by a network of 55 micron pits surrounded by mounds of spatter so that the result resembles a uniform hexagonal array of hole saws. The texture is created using nanosecond-pulsed fibre lasers and then hardened using a chromium-based process developed by Denmark-based TRD Surfaces.
“The drive shaft transfers torque from hydraulic pumps to the gear, and the high friction rings perform this function. They are also designed to slip if the torque exceeds a certain level to prevent overload of the gear,” said Dr Jesper Vejlø Carstensen, Senior Research Engineer at MAN Energy Solutions. “The high friction ring ensures this dual functionality but it requires the friction coefficient to be within a certain specific range.”
Previously, the rings were textured using a thermal spray coating. This provided less control of the variation in the coefficient of static friction, which should be at least 0.6. If
the coefficient is too low, unintentional slippage can occur, and if it is too high, excessive torque can be transferred to the drive train, leading to catastrophic damage to the component. In both cases, significant extra cost is involved as the pumps must be shut down while the drive shaft is disassembled and the ring replaced.
After successful laboratory testing, the new rings were mounted on 2 x 3 driveshafts in two different marine engines on ships. The parts performed well, and after 1,500 hours of operation there was no evidence of slipping. “We have achieved a coefficient of static friction of 0.74 (0.6 requirement) and a relative standard deviation of 3–4% as opposed to 13–14% for thermally sprayed samples,” said Carstensen. He anticipates that the new rings will reduce maintenance costs by around 90%.
MAN Energy Solutions has now introduced a set of new, more stringent specifications for the part. The previous requirement that the coefficient of static friction be at least 0.6 has been changed to require the coefficient of static friction to be within a range of 0.7 to 0.9.
Carstensen notes that while the engines that have the rings fitted are huge, weighing up to 2,300 tons and exceeding 23 metres in length, the new design demonstrates that even details at the micrometre level are important. High friction rings elsewhere on MAN Energy Solutions engines will now be evaluated to see if the new technology will be beneficial.
The research behind the development was undertaken by MAN Energy Solutions, Heriot-Watt University in Scotland and TRD Surfaces as part of the SHARK project funded by the European Union’s Horizon 2020 Framework Programme for Research and Innovation. The results were published in Materials..
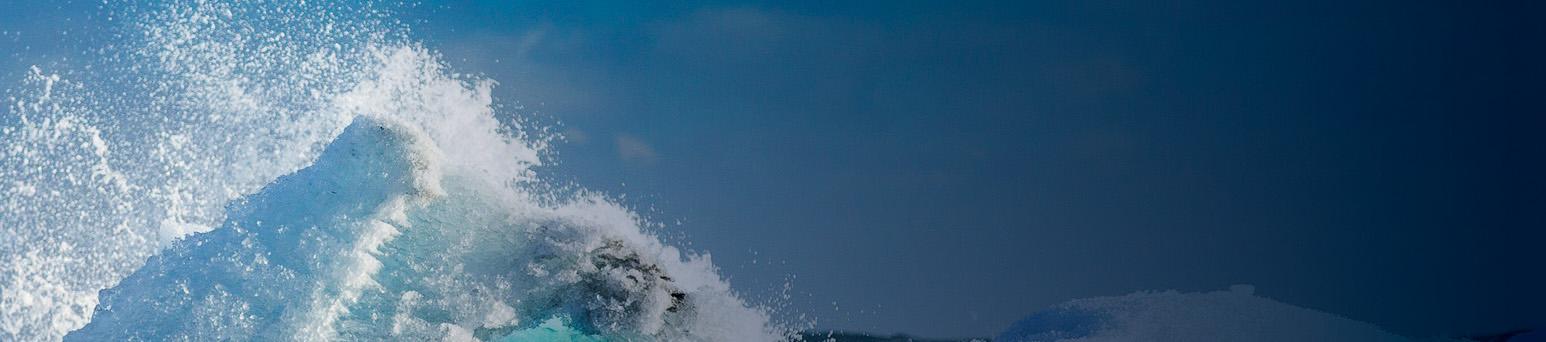
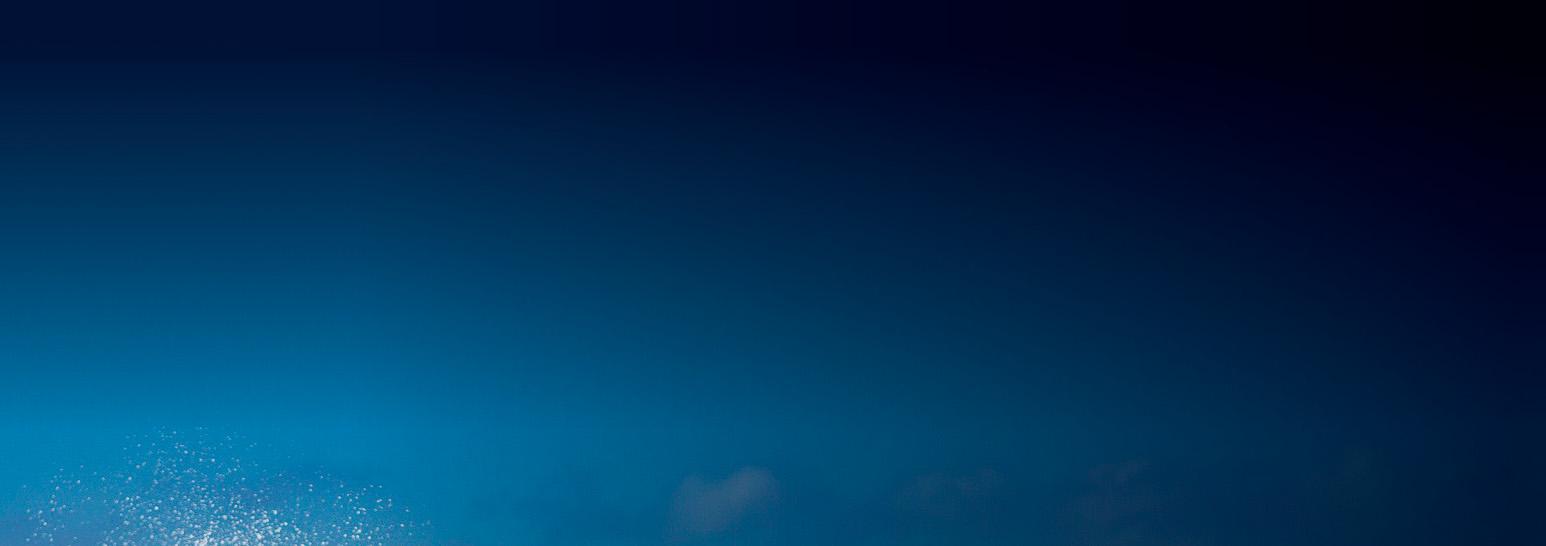
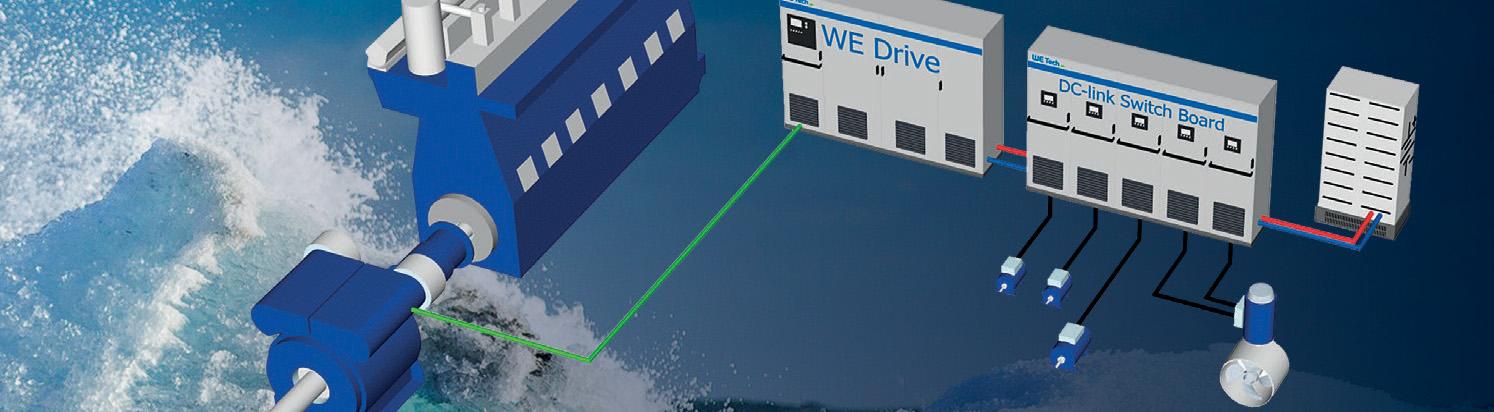
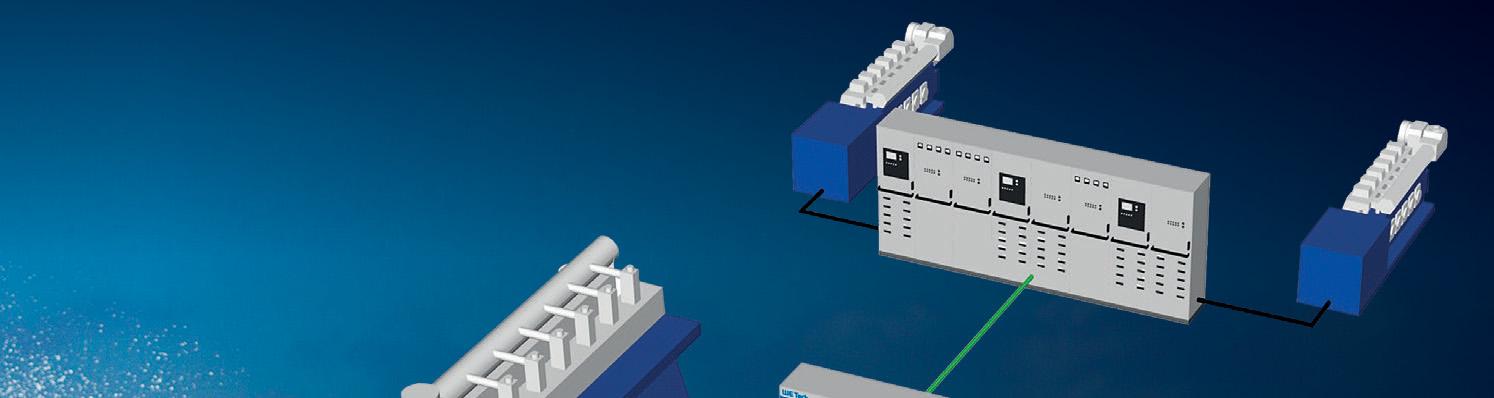
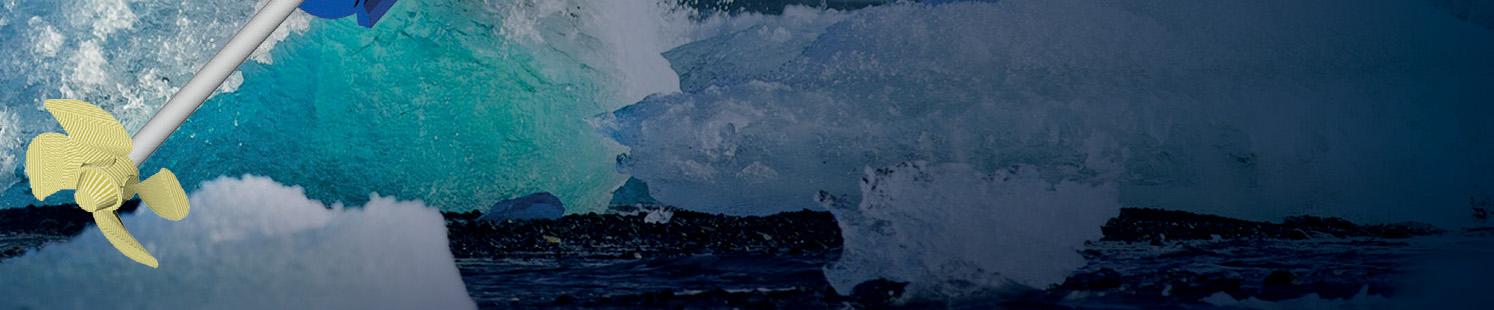
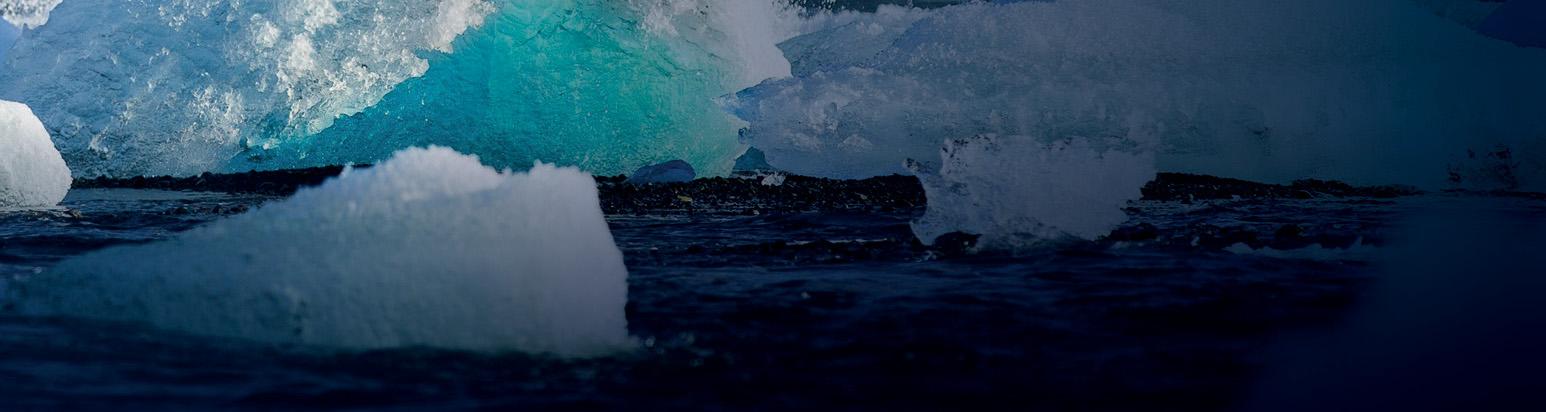
Meet WE Tech at Nor-Shipping Hall D03-43
WORKAROUNDS NEEDED TO COUNTER BWTS SHORTFALLS
The three-year experience-building phase associated with the Ballast Water Management Convention has resulted in data from 35 Member States and seven other stakeholders, relating to approximately 15,000 ships. The data is currently being analysed by the World Maritime University which will submit a report to MEPC 78 in June this year.
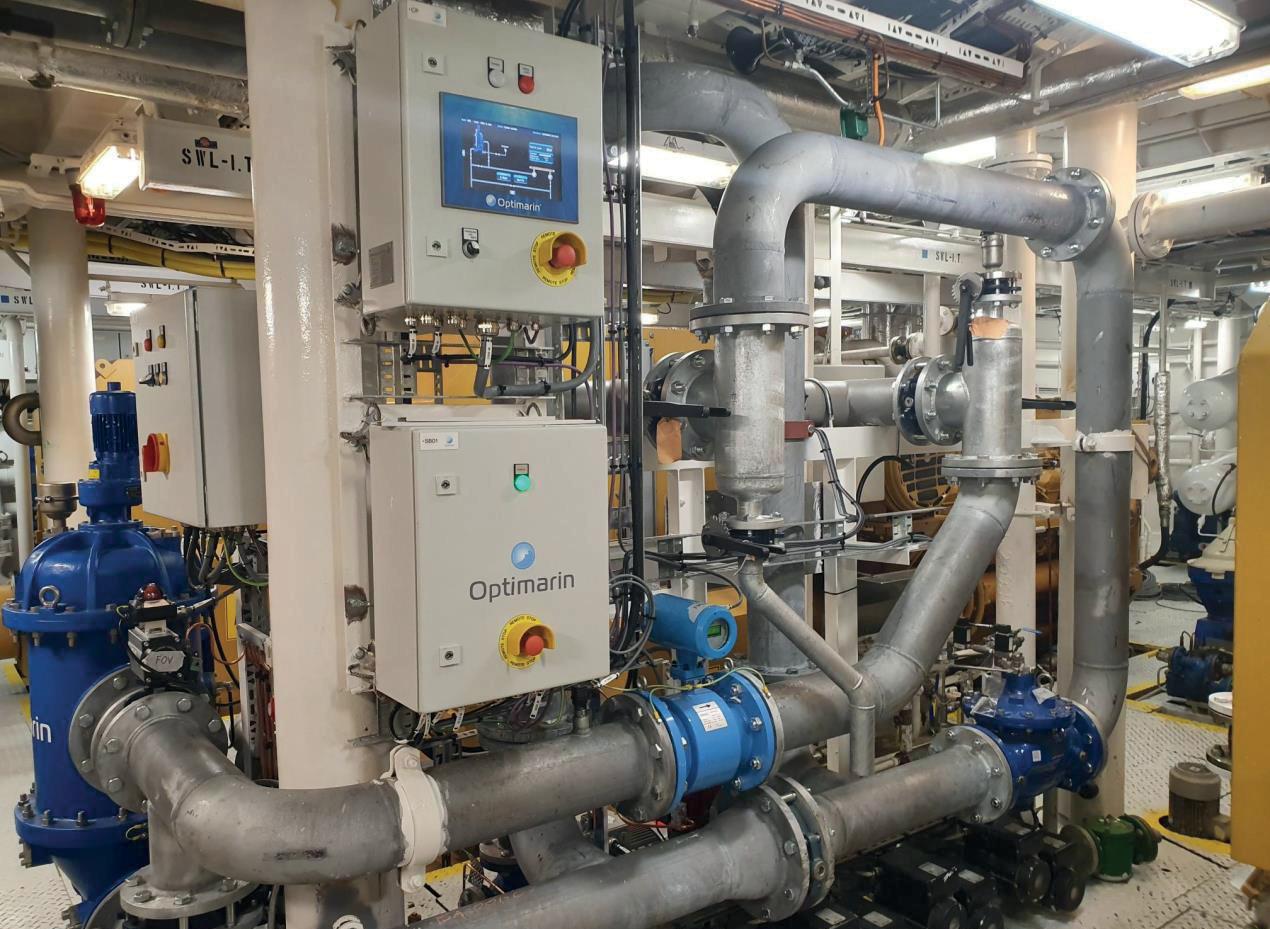
Credit: Optimarin
In a submission to MEPC76, Intertanko reported on its members’ experiences, highlighting reports of 10 ports where treatment systems have been unable to operate at optimal levels: Ohio (17 reports), New Orleans, (10 reports), Thames (nine reports), Brunsbuttel (eight reports), Haldia (eight reports), Alaska (eight reports), Rio Grande (six reports), Emden (six reports), Texas (six reports) and Alabama (six reports).
MEPC 77
Tore Andersen, Executive Vice President Sales & Marketing at Optimarin, notes that MEPC 77 did not agree on the rules that are needed globally to help ship operators manage this situation. Instead, ship operators must devise workarounds that are acceptable to the vessel’s next port of call. This can include avoiding ballasting operations in water known to be rich in sediment or performing ballast water exchange before reaching the next port in combination with ballast water treatment. If the flow rate of treatment systems needs to be slowed down, this can add significant time and needs to be catered for in voyage planning.
“We save all operational data from our systems in the cloud and have gathered information about water quality in different harbours, logging running hours and operation results so that owners can follow their ships and system performance,” says Andersen. “Our OptiLink system helps them to plan operations in the next port and avoid any issues.”
The system can be linked via a vessel’s internet connection or via a 4G antenna. It provides a full overview of the entire fleet for shore-based personnel, with KPIs to compare vessel performance, and it’s ready to be incorporated into thirdparty voyage planning platforms. Additionally, Optimarin can provide use it to provide interactive remote support to vessels reducing the need for physical service jobs.
FILTERLESS
Despite the issues the industry has encountered with sediment-rich waters, some ballast water treatment manufacturers are moving to offer variations of their equipment without filters. For example, Ecochlor’s filterless EcoOne™ and EcoOne™ Hybrid have now recently received United States Coast Guard (USCG) Type Approval.
8 Optimarin has a
fast-track delivery model to expedite ship installations of ballast water treatment systems
Jad Mouawad, CEO of Mouawad Consulting, explains: “Filters are designed to remove large organisms from the ballast water, reducing the need for high UV, high chlorine, high chemical injection concentrations. Removing filters is basically a trade-off. You either keep it and reduce your consumption in the second treatment or remove it and increase your consumption in the second treatment.
“The advantages of having a filter are obvious. It is a mechanical (semi-passive) way of getting rid of most large organisms. It also helps reduce some suspended solids due to an effect called caking, meaning when small particles add up around a pore and block it, even though each one is smaller than the pore itself. But caking is not enough to reduce silt significantly in ballast tanks. Most of it is much smaller than the filter´s mesh size, so it goes right through it.
“The disadvantage of a filter is that it adds another layer of treatment that can go wrong, either by clogging or by somehow malfunctioning. It requires maintenance, and it is an expensive product. It also adds significantly to limiting the maximum water flow that can be treated. So, removing it, if the second treatment is enough, is positive in that sense.”
COMMISSIONING
Commissioning testing will become mandatory prior to using a ballast water management system (BWMS) from the 1 June 2022 in line with BWM.2/Circ.70, rev1 to obtain an International Ballast Water Management Certificate. Dimitrios Tsoulos, Regional Sales Manager EMEA at De Nora said: “We believe that the industry will feel the pressure of this as some systems have struggled to meet compliance standards in real life conditions, and some suppliers have struggled to fully support their customers with installation and training needs. These issues will become more critical as faults in the BWMSs or lack of knowledge leave a vessel non-compliant.”
De Nora welcomes this step forward as without widespread compliance testing. It was previously possible to underinvest in systems and installations that a shipowner merely hoped would comply with the rules. “As this changes, the whole market is starting to see that buying a poor quality BWMS or service means buying twice – with huge costs associated with rectifying mistakes.”
EEXI
Tsoulos says that the biggest and most socially conscious shipowners today are acutely aware that solving one environmental issue in a way that causes another is not a viable option – and the impact of ballast water on a whole vessel’s efficiency will be tightly monitored by every owner as shipping prepares for Energy Efficiency Design Index for existing ships (EEXI) implementation. “This is especially true for larger ships, which is why De Nora’s focus on low energy use and whole life costs for the BALPURE® and Hyde GUARDIAN® systems deliver true value for the environment.”
ONE-WAY TREATMENT
Langh Tech has introduced an option for one-way treatment for its LanghBW system which reduces the operating costs and required treatment time. For this, filtration and UVtreatment of the ballast water is done during ballasting only. Once the required retention time has been achieved (zero hours in IMO areas, 24 hours at USCG areas), the BWMS can be bypassed and ballast water discharged without any further treatment. This treatment regime can be applied in marine waters with salinity greater than 28 PSU.
The one-way treatment option and capability to operate in extremely turbid waters with relatively high flow rate is achieved through Langh Tech’s specially designed UV-C reactor. The company is also investigating the possibility of using LED technology instead of fluorescent lamps to further improve energy efficiency.
PORTSIDE
It’s not just shipowners that are facing challenges. In a submission to MEPC77, Canada described its research which indicated that treated ballast water samples taken by researchers did not consistently meet the D-2 performance standard for organisms greater than 50 microns. They trained inspectors to take samples and found that they still needed additional support and didn’t have time to conduct the testing given the other compliance instruments they had to deal with relating, for example to crew welfare and safety equipment. The testing also resulted in one to three cubic metres of water that couldn’t always be disposed of via the ship’s bilge.
Using indicative testing equipment also required extensive training, and Canada concluded that the devices could only be useful for enforcement in cases of gross non-compliance.
TREATMENT-AS-A-SERVICE
Monstrant Viam and Bawat Technology Services has created a company, Freedom Ballast, to introduce ballast water reception and treatment-as-a-service for US ports. William H. Burroughs, Founder and CEO of Monstrant Viam, highlights that, as well as existing practical and regulatory hurdles, a two-year regulatory development phase is soon to begin under the US Vessel Incidental Discharge Act (VIDA). Importantly, there is no experience building phase for US discharges, he says. The USCG regulations and US EPA 2013 VGP are enforced with no learning curve.
“Our plans are based on the US EPA 2013 VGP and USCG’s regulations (33 CFR 151 Subpart D) that allows discharges to a shore facility or another vessel for the purposes of treatment. The burden for compliance is transferred to the specific US state which issues their permits based
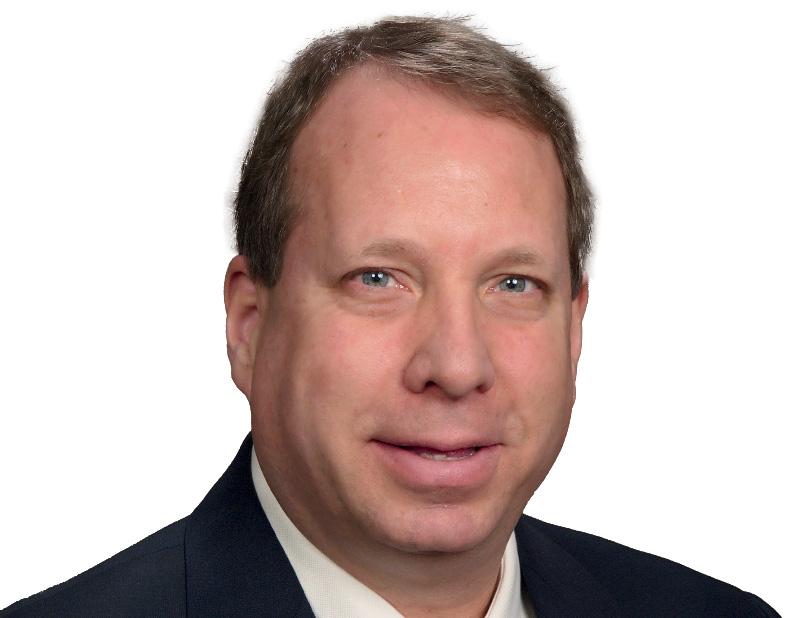
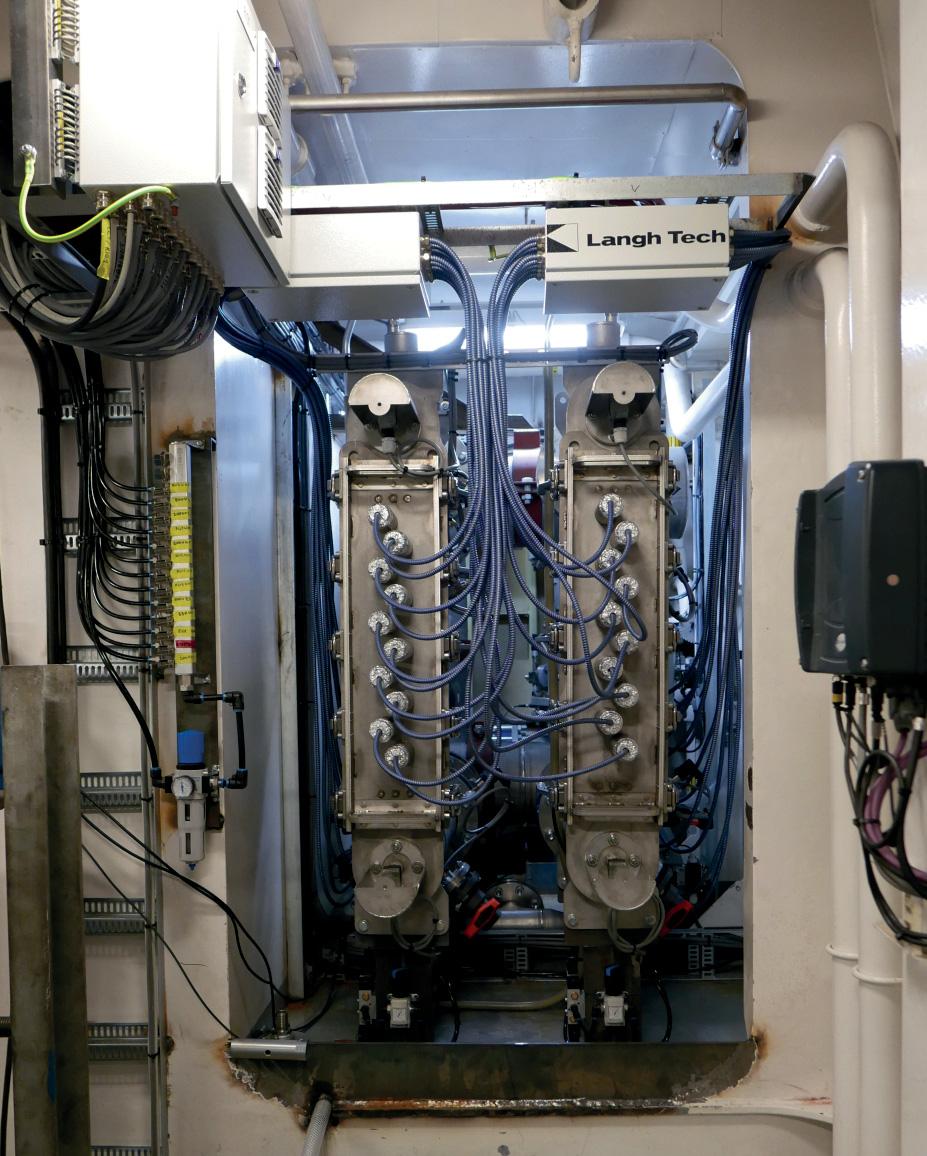
Credit: Langh Tech
xperience building s, he says. The
EPA 2013 VGP ning curve. n the US EPA gulations (33 that allows facility or purposes of r compliance ific US state s based
8 An installation
of Langh Tech’s specially designed UV-C reactor
8 William H.
Burroughs, Founder and CEO of Monstrant Viam
on the EPA’s National Pollutant Discharge Elimination System (NPDES) at the state level.” The Freedom Ballast service offering will start in the Mississippi Delta in Louisiana where an operating permit is pending.
BACKLOGS
Some equipment manufacturers have pointed to the installation backlogs that could impact shipowners’ ability to be compliant with regulations. Kim Tervonen, Product manager for Langh Tech, says one of the greatest challenges at present lies in the interface layer of different industries and actors. “The increasing raw material, manufacturing and logistical costs together with prolonged lead times can make it more difficult for BWMS manufacturers, yards and shipowners together to fulfil the D-2 standard on time before the IOPP renewal of the subject vessel, which may cause some regulatory issues.”
Valve specialist W&O estimates that there are still over 15,000 BWTS installations outstanding, a sizeable proportion of the global fleet. The world’s supply chain sector’s current issues make sourcing parts at short notice challenging, and as owners and operators rush to obtain the required marine valves, actuated valves, pipes and fittings, there is a risk of becoming trapped in a bottleneck, where necessary ship parts cannot be sourced on short notice, says Kristof Adam, General Manager Europe, W&O.
“It is not uncommon for unsuitable parts to be ordered hastily at a low-cost from local or unreliable suppliers, and on an ad hoc as needed basis. Not only does this make the equipment more costly, in doing this, shipowners and operators risk buying improper equipment and ending up with non-compliant assets, unused pipe, valves, and fittings.” A vital supply agreement can aid yards in pitching and completing the backlog of conversions, and combat the demand by ship owners and charterers.
Konstantinos Dimopoulos, International Sales Manager at ERMA FIRST says: “There have been a lot of projects that have been planned and executed well, and the installations have been operating brilliantly for the shipowners concerned. However, as we are progressing now towards the end of the implementation period of the Convention, things are becoming more rushed, and there is a concern that the installations themselves may not be well managed. This can obviously impact the quality of the project.”
IN-TANK SOLUTION
ERMA FIRST has added to its family of ballast water management solutions with oneTANK, the world’s smallest ballast water treatment system. The system’s footprint is 600mm x 600mm two square feet. It is IMO and USCG compliant and is suited to smaller vessels such as superyachts, fishing vessels and workboats, for vessels with limited ballast requirements such as semi-submersibles, and for larger vessels’ aft peak tanks. oneTANK refers to an in-tank, bleach injection treatment process for ballast tanks up to 5,000 cubic meters that is neutralized prior overboard discharge. Specifically, the system treats ballast water within the vessel’s ballast tank(s) and uses an 8.5% or 12.5% sodium hypochlorite (bleach) and 30% sodium thiosulfate solution (neutraliser) – common chemicals that can be purchased from chemical suppliers worldwide.
No 3D laser scans are required to integrate the system as it is typically accommodated in the closest void area to ballast tanks in the engine room, bolting it in place and simply connecting directly to the ballast tank(s). This reduces piping complexity as the system is not dependent on the vessel’s ballast pumps for operation.
RIDING SQUADS
Due to the current spike in freight rates, BIO-UV Group is fielding more enquiries for in-service installations using dedicated BIO-SEA flying squads. Maxime Dedeurwaerder, Business Director – BIO-SEA, says there is a noticeable trend for shipowners looking to work with a limited number of business partners during a retrofit project, and to be fully supported along that process.
Coinciding with the introduction of digital modelling services, BIO-UV Group has also updated all versions of its UV technology-based BIO-SEA systems to ensure compatibility with GPS data acquisition. “This is a new feature we are providing in anticipation of possible future regulatory requirements,” Dedeurwaerder said.
Additionally, BIO-UV has introduced a new reactor design. The previously approved BIO-SEA B-Series incorporates a mono-lamp reactor, and several ‘B’ reactors need to be mounted in parallel to reach high treatment rates. This requires specific manifolds for hydraulic balance, which can take a significant footprint. The new BIO-SEA M-Series, however, is based on multi-lamp reactors, equipped with two-to-seven lamps in a single chamber, allowing a more compact design for the same capacity of treatment. A maximum of two reactors are installed in parallel.
The BIO-SEA M-Series system has been specifically designed to optimise the footprint and installation costs of a medium flow rate ballast water treatment system. Available as a modular or skid system and with fewer piping components, the company says it is available with a short lead time.
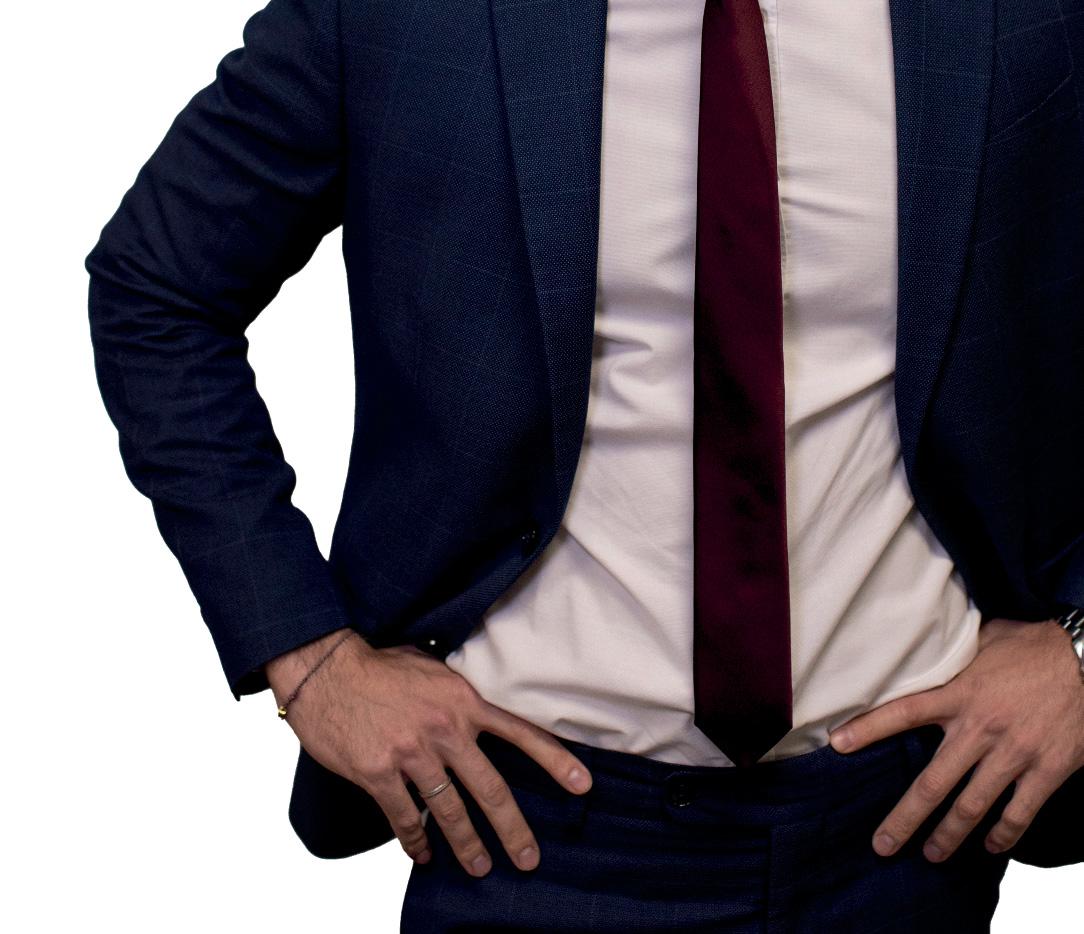
RE-RETROFIT
DESMI Ocean Guard’s order book spans well into 2024. “These are both retrofit and re-retrofit solutions. The latter is the replacement of existing ballast water systems that do not live up to the latest requirements or that can no longer be serviced because the supplier is no longer on the market,” says marine engineer, Bjarne Nørgaard Krogholm, Team Leader at DESMI Ocean Guard.
Regardless of the challenges, the industry must be ready to meet IMO requirements for ballast water treatment by 8 September 2024.
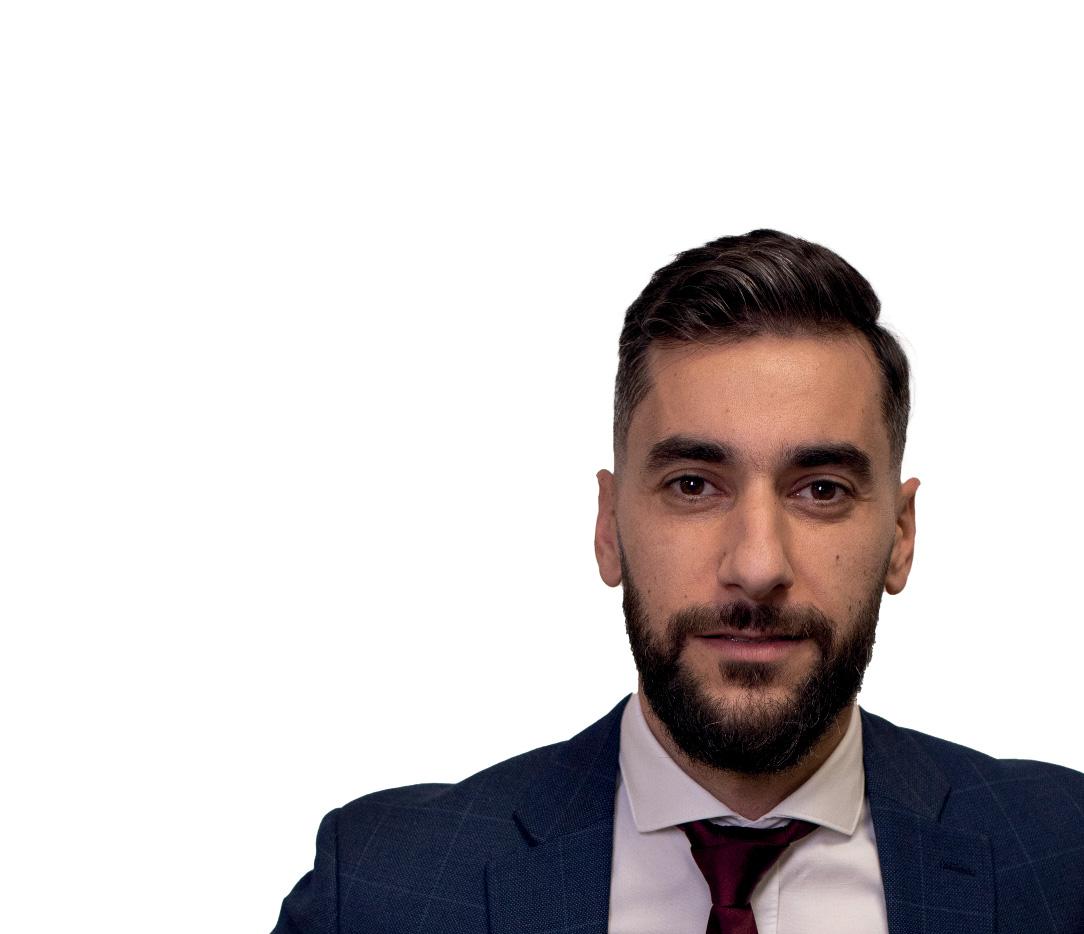
Leader at DESMI Ocean Guard.
Regardless of the challenges, the industry must be ready to meet IMO requirements for ballast water treatment by 8 September 2024.
8 Konstantinos Ko
Dimopoulos, Dimo International Sales Inter Manager at Mana ERMA FIRST ERM
EFFECTIVELY NAVIGATING THE BWMS QUAGMIRE
Shipowners considering ballast water installations in 2022 should beware backlogs at yards, and bear in mind challenging water conditions and Shanghai Test results when making decisions, Mark Riggio, Head of Marine at Filtersafe tells The Motorship
From 8 September 2024, vessels are required to have a ballast water management system (BWMS) that can treat invasive aquatic species consistently and eff ectively. This is in line with the D-2 standard for the implementation of the International Maritime Organization’s (IMO) Ballast Water Management (BWM) Convention. While 2024 might still seem like a long time away, choosing an appropriate BWMS and fi lter for your vessel’s unique operating profi le takes time. Proper planning, installation, certifi cation and training must all be done prior to operations too.
Moreover, with International Oil Pollution Prevention (IOPP) Certificates due this year, and installation and retrofit bottlenecks expected in shipyards, 2022 will be a critical year for BWMS installations. In a recent webinar, using readily available class society data, a marine engineer from Exponent International stated that only about 1/3 of the existing fleet has a BWMS fitted. Therefore, in order to be compliant with BWM Convention regulations, 15,000 systems need to be fitted in 2022. Shipyards simply won’t have capacity for those trying to fit systems at the last minute. Plus, if demand for shipyard spaces exceeds supply, the prices will increase, increasing OPEX costs.
Therefore, it is important to make informed decisions now.
CHALLENGING WATER CONDITIONS
Whether a vessel will encounter sediment-rich waters should influence a BWMS purchaser’s decision. Planning for these conditions will impact the quality of system required and therefore CAPEX costs. While failure to effectively plan for these waters will greatly impact OPEX costs.
Many ship operators are experiencing clogging problems with their BWMS in areas with high levels of total suspended solids (TSS), such as Shanghai or Hamburg. These result in costly disruptions, often damage to the BWMS and filter, and exposure to the substantial risks of regulatory non-compliance.
There have been some cases where operators have decided to retrofit high-quality filters as a pre-filter to their current system. Similarly, there have been interesting cases where filters have retrospectively been added to a filterless system for operations in challenging water conditions. As a result, regulatory compliance is assured while disruption to operations is eliminated. However, this approach is no substitute for fitting an appropriate BWMS with a highperformance filter from the outset, which remains the most cost-efficient option.
NO BLANKET EXCEPTIONS
MEPC 77 merely reinforced the status quo when it comes to ballast water management in ports with ‘challenging water conditions’ and there are no blanket exceptions or bypassing of systems for ships operating in these locations, nor should operators expect them. Exceptions would allow low-quality systems to be by-passed in less-than-ideal ballasting conditions. There is no real basis for this. It’s contrary to the environmental aims of the Ballast Water Management Convention (BWMC). It’s also against the UN Sustainable Development Goal 14 Life Below Water.
Some will try to seek exemptions on a case-by-case basis, which is a risky, short-term approach which will require time spent, and therefore money spent, negotiating with the port on current water quality and compliance. The logical option is to ensure that you are buying an appropriate BWMS and filter from the outset.
There is sufficient technology and equipment available on the market today to meet the operational challenges posed by challenging water conditions. CAPEX costs may be marginally higher, but OPEX costs are much lower. Operational delays and disruption are minimised, maximising trading time and providing a competitive advantage.
THE SHANGHAI TEST
The Shanghai Test was developed to promote an advanced understanding of how a BWMS performs in real waters. Purchasers should look for a BWMS and filter that has not only passed the Shanghai test, but exceeded its requirements, as results show how well a BWMS and filter work in sedimentrich waters.
They should look for three main results. Firstly, the filter’s clog percentage in relation to the TSS load. Secondly, that realistic outlet pressures were used in the test.
Thirdly, that the filter screen cleaning time is efficient. Selfcleaning capabilities can drastically reduce cleaning times and also reduce OPEX costs. Manual cleaning, and stopping operations to do so, takes time, crew attention and opens up compliance issues.
To summarize, 2022 is a critical year for BWMS installations. Challenging water conditions and Shanghai Test results are just two of a myriad of considerations that purchasers must account for. However, when factoring in the additional OPEX costs associated with operational and regulatory issues, the case for a high-quality filter is clear.
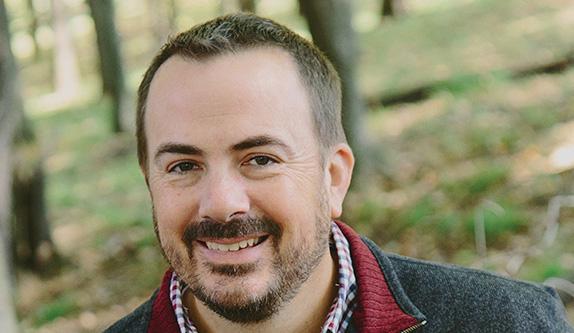
8 Mark Riggio