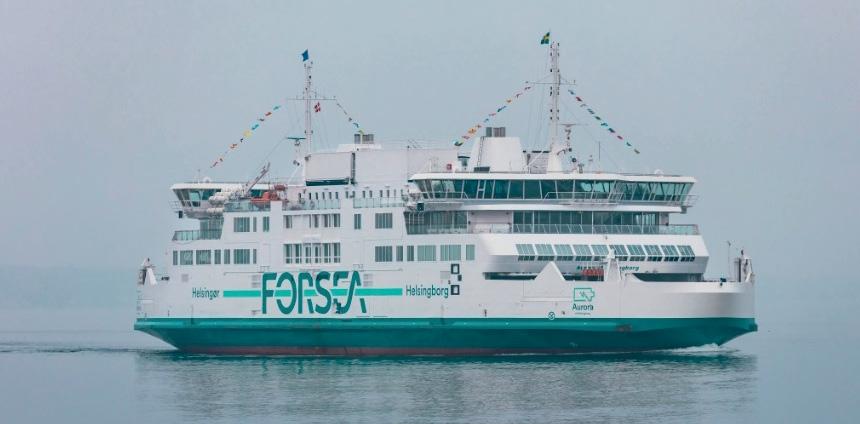
7 minute read
The cost of effi ciency
BATTERY ECONOMICS LIMIT ESS SCOPE FOR DEEP-SEA SHIPPING
MAN Energy Solutions has issued a white paper evaluating battery technology and how it could be applied on board large ocean-going vessels powered by two-stroke engines. The company concludes that, with the exception of short-sea ro-ro shipping, battery-electric propulsion does not present a feasible alternative to conventional 2-stroke powered shipping at present
Pure-electric solutions are considered and quickly dismissed as impractical, from both a weight and volume perspective, for the majority of ship types considered in the white paper. Techno-economic considerations around upfront battery cost diff erentials and the need for the replacement of battery cells after 10 years of operation are recognised.
The white paper acts as a comprehensive introduction to current battery technology, and introduces the main lithiumion chemistries, and explains why Lithium nickel manganese cobalt oxide (LiNiMnCoO2) is currently most favoured for maritime applications.
Some of the main considerations around battery sizing – including the temperature at which the battery system operates, and the effect of charging and discharging patterns on the operational life of the battery are reviewed.
While space considerations mean that some phenomena are not addressed (such as the challenge posed by lithium dendrites), the impact of battery ageing and operational limits on ESS specification requirements is addressed.
BATTERY MANAGEMENT SYSTEM
The white paper introduces the concepts of the battery system, ranging from the individual cell level up to the entire battery level. The differences between power electronics control and the battery management system are outlined, identifying the dual role of the BMS in controlling the charging and discharging of individual cells as well as monitoring the state of charge and system voltage.
The role of the BMS in balancing the system to minimise individual cell-level variations in cell voltage as a result of different self-discharge rates and temperatures is explained. This connects with a discussion of the role of the BMS in handling safety considerations, including the detection of faulty cells. The white paper provides an introduction to the causes and potential remedies to safety failures, including the rare but potentially serious thermal runaway issue.
MARINE APPLICATIONS
Having outlined the composition of battery systems and explained how the BMS system works in practice, the paper touches on a number of different configurations where battery systems are employed.
The pure-electric configuration, such as that seen in the 4.1MWh pure-electric Tycho Brahe passenger ferry, operating between Helsingor in Denmark and Helsingborg in Sweden, is described.
More relevantly from the perspective of operators in the deep-sea market, the paper discusses the potential applicability of battery systems for deep-sea vessels. The differences between a semi-hybrid diesel-mechanical set up and some of the different full-hybrid diesel mechanical set up are introduced.
The white paper notes that the latter arrangement includes a battery in combination with a PTO/PTI attached to a 2-stroke engine. This allows for the battery and auxiliary engines to support the propulsion of the vessel and for the main engine to charge the battery while at sea.
Appraising the different combinations, the white paper concludes that the higher system efficiency offered by a 2-stroke prime move directly coupled to the propeller shaft means diesel-mechanical arrangements remain the most efficient arrangement for large ocean-going vessels.
Credit: ForSea 8 The ForSea
Tycho Brahe and Aurora (pictured) passenger ferries now feature 4,160kWh batteries
By comparison, traditional diesel-electric propulsion is traditionally better suited to vessels with fluctuating load requirements, where the advantages of peak load shaving have the greatest effect.
BATTERY SIZE AND COST FACTORS
The white paper also discusses the impact of the C-rate or the rate at which a battery is discharged relative to its maximum capacity. The smaller the proportion of the total capacity that is charged and discharged in one cycle, the longer the battery life, and as a result the more expensive it will be.
This difference between different applications, and their impact of battery sizing requirements, is illustrated by comparing the example of a high-power, low-capacity battery system used to power thruster operation during manoeuvres, and a high-energy battery used to power a pure-electric harbour ferry.
Aside from the sizing of an individual battery system, MAN Energy Solutions notes that including the weight of cooling, racks, and other ancillary equipment would increase the headline weight and volume of a battery system (see Table 1).
While there are differences between different types of systems, and the requirements for air cooled and watercooled systems vary, it is clear that maritime battery systems have larger insulation requirements than batteries for terrestrial transportation applications. Maritime systems also require the installation of cooling equipment, fire detection and fire-fighting equipment.
This goes some way towards explaining the price differential seen between battery systems for automotive applications and maritime applications. As of early 2022, MAN Energy Solutions notes that a heavy-duty marine battery system (circa USD500/kWh) while an automotive battery would cost close to USD210/kWh.
Looking forward, the white paper challenged the accepted wisdom that a further decline in battery cell prices would lead to substantially lower maritime battery system prices. “Today, the cost of the cells constitutes roughly 40% of the total cost of the battery system… Even if the cell price fell by 75% compared to the current level, this would only correspond to a 30% reduction of the current total system cost.”
MAN ES offered USD250/kWh as a potential lower price scenario by 2030. Although efficiencies of scale are expected to lower the cost of power electronics, battery modules and racks as production volumes increase, MAN ES highlights uncertainties about the future prices of key non-ferrous metal inputs, as well as rare earths.
BATTERY-ELECTRIC DEEP-SEA ENERGY CONSUMPTION
The report then carefully examines the case for batteryelectric installations aboard a variety of deep-sea commercial vessels, including four different types of bulk carrier, ranging from 50,000dwt up to 320,000dwt, three types of container vessel and a 15,000dwt RoRo.
It will come as little surprise to readers that with the exception of the short-sea ro-ro vessel assessed, batteryelectric propulsion does not offer a feasible alternative to ICE-powered shipping at present.
When the 5,000 lane metre RoRo was subjected to closer study, it became clear that replacing an existing vessel with a battery-electric alternative would increase the cost of an individual vessel by between 50% (if ESS prices were to decline to USD250/kWh) and 100%, while the slower operating speed would require the addition of an additional vessel to maintain current service levels.
ENERGY REQUIREMENTS DURING PORT STAYS
While the charging of batteries with a PTO while at sea could allow vessels to operate with emission-free port stays, the advantages decline as the length of the port stay extends. The average stay for bulkers extends from 36 hours up to 72 hours for bulkers of 320,000 dwt or more.
The implications for container vessels are important, given the current proposals under consideration by the European Commission to force container vessels to install battery systems.
The sheer impracticability of pure-electric designs for commercial shipping is comprehensively debunked in the report: the white paper drily notes that a 209,000t battery installation on a 14,000 teu would “exceed the cargo carrying capacity of the vessel”.
However, white paper outlines the energy requirements to enter and leave port, and finds that both bulkers and container vessel hotel load and propulsion requirements are relatively moderate.
The report notes that there are a number of technical issues relating to leaving port on battery power and later engaging the two-stroke main engine. For a typical twostroke engine directly coupled to the propeller, the main engine can be turned/ motored along with the propeller shaft (which MAN estimates would require an estimated 5% of SMCR-power), or the main engine can be decoupled from the propeller shaft.
The paper gives the example of the 500 kW of frictional power required to turn a 10,000kW engine along with the propeller shaft, compared with the 1,300 kW required to propel the 82,000 dwt bulk carrier at 5 knots in calm waters.
The alternative to turning/motoring the main engine is to use a clutch to disengage it from the propeller shaft. There are two main families of clutches, the first of which requires the shaft to be at standstill when the main engine is engaged, whereas a second, more complex type, allows the engine to be engaged while the shaft is spinning.
However, the high Capex costs of clutches can make other
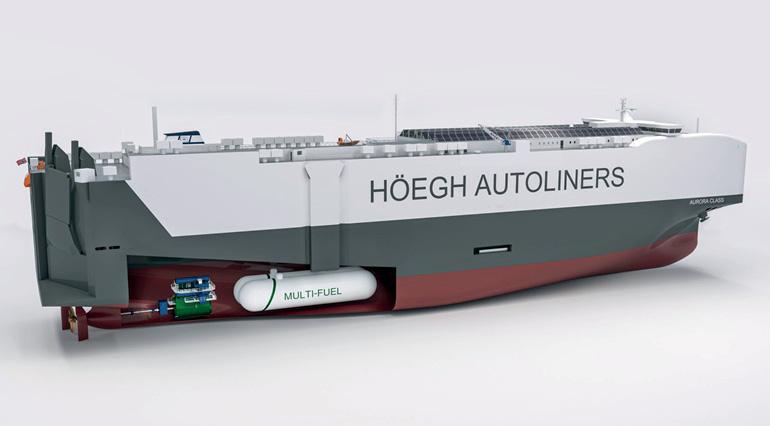
8 Höegh Autoliners’ new Aurora Class-design will feature a
large ESS and an ammonia-ready high-pressure dual-fuel MAN B&W two-stroke engine
Credit: Höegh Autoliners
System level Pack level Module level Cell level
Specific weight [kg/kWh] 11-30 7-28 6-24 6-8 Specific volume [l/kWh] 12-38 10-12 7-10 1.5-2.5 Specific price [USD/kWh] 500 - - 200-250
8 Table 1: Specifi c weight, volume, and price of a large, >1 MWh, heavy-duty marine lithium ion battery as of 2019
8 Container
Vessel Energy consumption during port stay
Vessel type Container Container Container Size 2,500 teu 14,000 teu 20,000 teu
Duration [hours] 18 24 32
Power [kW] 1,200 5,600 8,000 Energy consumption [MWh] 21.6 134 256