

Future of Manufacturing
Building beyond the Industrial Strategy
“The
Mark Goldstone, Policy Manager, Head of
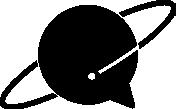
“Manufacturing plays a pivotal role in shaping a stronger, more resilient UK.”
James Selka, Chief Executive Officer, Manufacturing Technologies Association Page 06
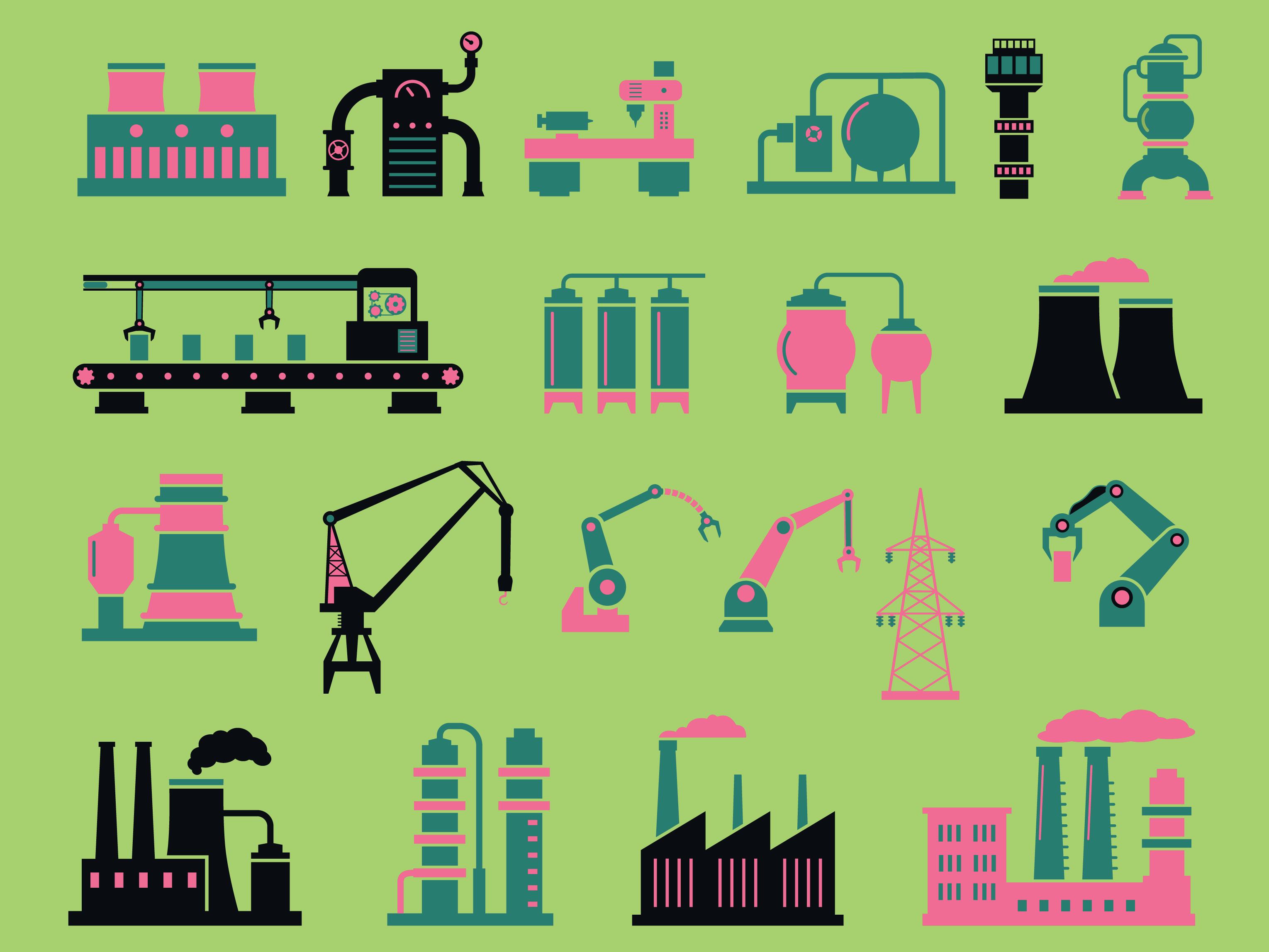
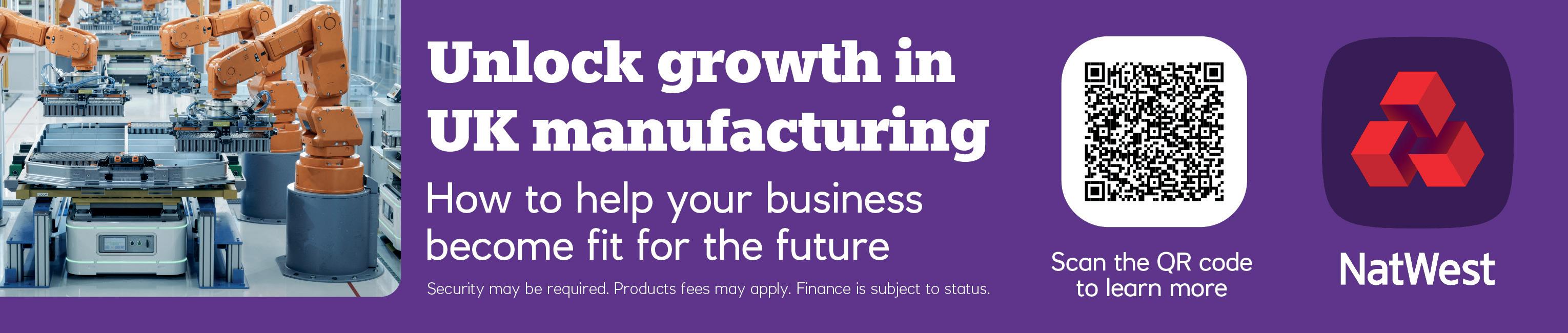
Why supply chain resilience is critical to economic security today
The Government is setting out bold ambitions as part of the forthcoming Invest 2035 industrial strategy, including for the UK to be a global leader in advanced manufacturing.
The resilience of supply chains is a cornerstone of competitive advantage in manufacturing. Recently, the threat of trade disruption has increased pressure on manufacturing supply chains. These shocks have underscored a clear necessity for robust and adaptive systems capable of withstanding, reacting to, and recovering from global challenges.
Supply chain resilience shift
Once optimised solely for cost and efficiency, supply chains are now being reimagined for agility, transparency and robustness. For decades, lean manufacturing and just-in-time logistics ruled the industrial landscape. However, the fragility of these hyper-optimised systems has been exposed, with manufacturers faced with cascading delays, raw material shortages and skyrocketing freight costs. The lesson is clear: efficiency without resilience is a liability.
Key pillars of supply chain resilience
1. Diversification of suppliers and geographies: Relying on a single supplier or region is a recipe for vulnerability; leading manufacturers are adopting multi-sourcing as a default to spread risk and increase flexibility.
2. Digital twin technology: Digital twins (virtual replicas of supply chains) allow manufacturers to simulate disruptions, test responses and optimise operations in real time. This predictive capability is transforming supply chain planning from reactive to proactive.
3. End-to-end visibility: Real-time data sharing across the supply chain enables faster decisionmaking. Internet of Things sensors, blockchain, and AI-powered analytics are helping companies gain granular visibility into inventory, logistics, and supplier performance.
4. Sustainability and circularity: Resilience and sustainability go hand in hand. Circular supply chains that reuse materials and reduce waste are not only environmentally responsible but also less dependent on volatile raw material markets.
5. Workforce agility and collaboration: Human capital remains a critical asset. Cross-functional teams, agile training programmes, and collaborative ecosystems with suppliers and logistics partners are essential for rapid response and innovation.
Looking ahead: the role of AI and automation
Artificial intelligence is poised to become the nervous system of resilient supply chains. From demand forecasting and route optimisation to anomaly detection and autonomous procurement, AI is enabling smarter, faster and more adaptive operations. Meanwhile, automation — from robotic warehouses to drone deliveries — is reducing dependency on human labour in critical nodes.
The future of manufacturing belongs to those who can turn volatility into a strategic advantage. By embedding resilience into the DNA of their supply chains, manufacturers are not just surviving disruption — they’re thriving through it.
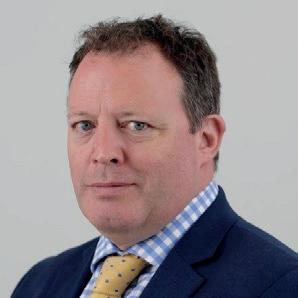
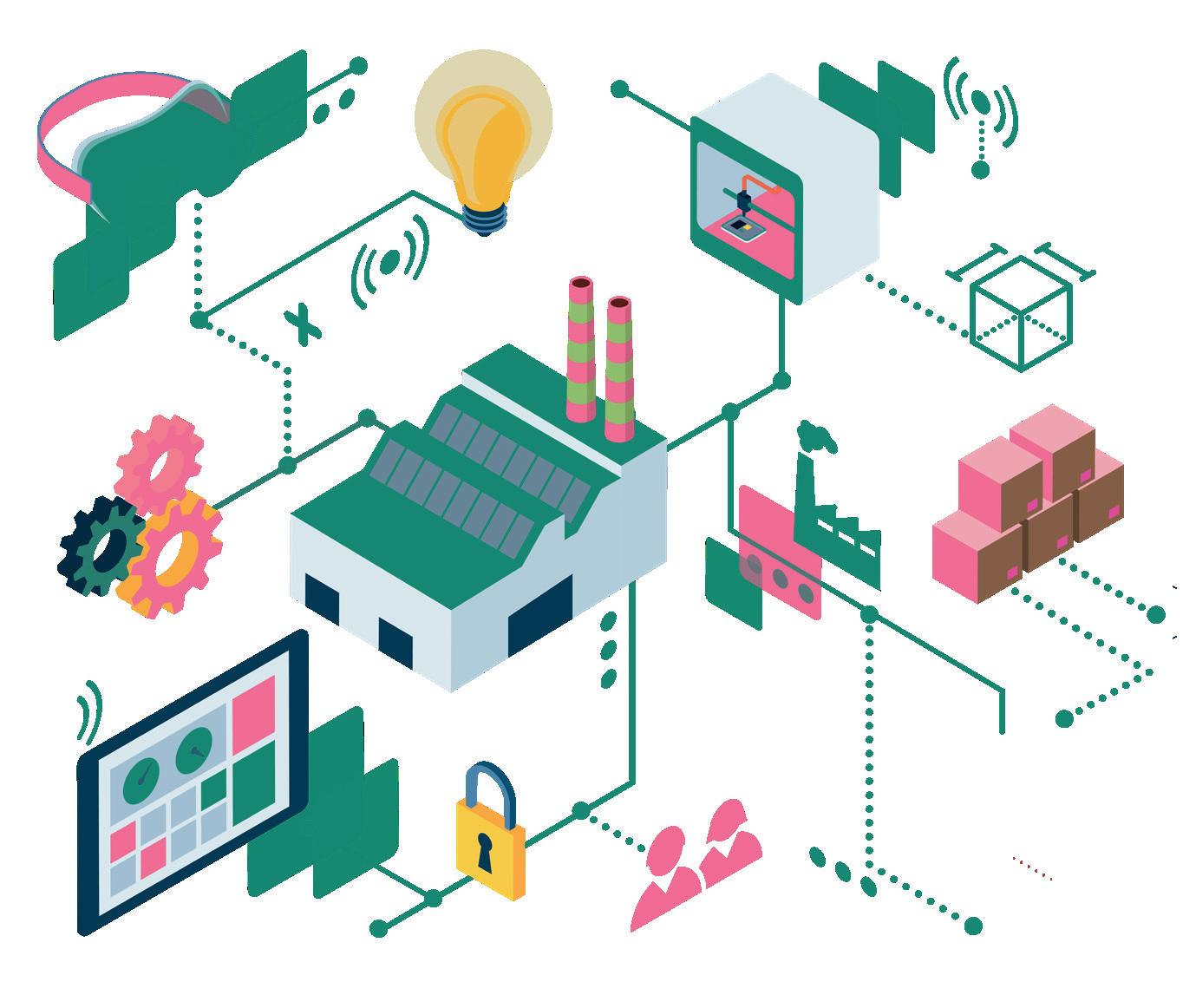
Accelerating automation adoption in UK factories to close productivity gap
In the UK, we are entering a new and exciting digital age that has the potential to bring about numerous benefits to the manufacturing sector.
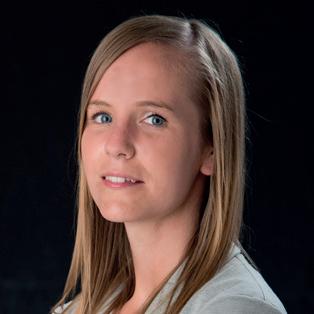
Technologies such as artificial intelligence (AI), machine learning (ML) and large language models (LLMs; generative AI) are transforming industries by automating tasks, optimising production and revolutionising the way we approach problem-solving.
Automation and robotics in manufacturing
As AI, automation and robotics continue to evolve and speed up processes on the factory floor and elsewhere, their potential to drive economic growth and reshape industries is becoming increasingly clear. The manufacturing sector and its factories of the future have a central role to play. The sector brings stability and economic resilience to the economy and provides the jobs and goods needed to ensure that communities across the country thrive.
Productivity and automation adoption lag
However, despite being a major contributor to growth in the UK, the manufacturing sector faces a significant challenge when it comes to productivity and automation adoption. Just 7% of the companies we surveyed as part of our report regarded themselves as ‘very
knowledgeable’ about AI, and we remain behind in many global rankings when it comes to metrics such as robot density.
Multifaceted benefits of tech adoption Yet, there are huge financial gains to be had. For example, the AI industry in the UK is expected to contribute $1 trillion to the economy by 2035. As an economy, and as a manufacturing sector, we have the potential to realise these gains. After all, manufacturing contributes some 47% of all private R&D spending in the UK.
It’s clear that factories could look very different in five, 10 or 20 years’ time, by adopting existing digital technologies to transform them into the factories of the future. This can help boost efficiency and productivity, not just on production lines but also in other areas such as decarbonisation and occupational health and safety.
As the Government moves to develop its industrial strategy, digital technologies and digital skills must be at the heart of it. Two hundred years after the industrial revolution took root, the fourth one is bringing the zero-impact factory within reach.
WRITTEN BY
Verity Davidge Director of Policy, Make UK
Steps that can help upskill the UK manufacturing industry
The Government’s commitment to publishing a modern Industrial Strategy is a welcome step to providing manufacturing businesses with much-needed certainty.
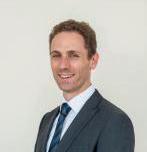
It has been a turbulent decade for the UK’s manufacturing sector. Brexit tore up the rulebook for businesses that sold their goods into the EU, the Covid-19 pandemic disrupted global supply chains, and Russia’s invasion of Ukraine led to a spike in energy costs not seen for a generation.
Addressing skills and modernising manufacturing
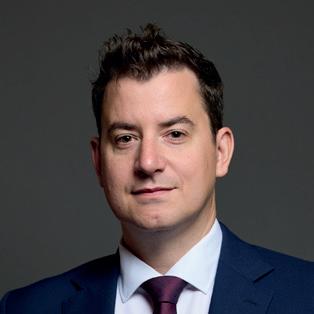
The forthcoming Industrial Strategy aims to drive growth and seize opportunities to lead in new sectors, with highquality, well-paid jobs. UK manufacturing will play a vital role in many of these growth-driving sectors, including clean energy, defence and life sciences. However, growth will not be possible without modernising the manufacturing sector and addressing skills gaps. UK manufacturing has a bigger gap than in almost any other sector, with 55,000 unfilled long-term vacancies nationwide.
Progress in recent years
The introduction of Local Skills Improvement Plans helped ensure post-16 technical education is more responsive to the needs of local employers. The new Government has also created an arm’s-length body, Skills England, which will bring forward strategic oversight of England’s currently fragmented skills system.
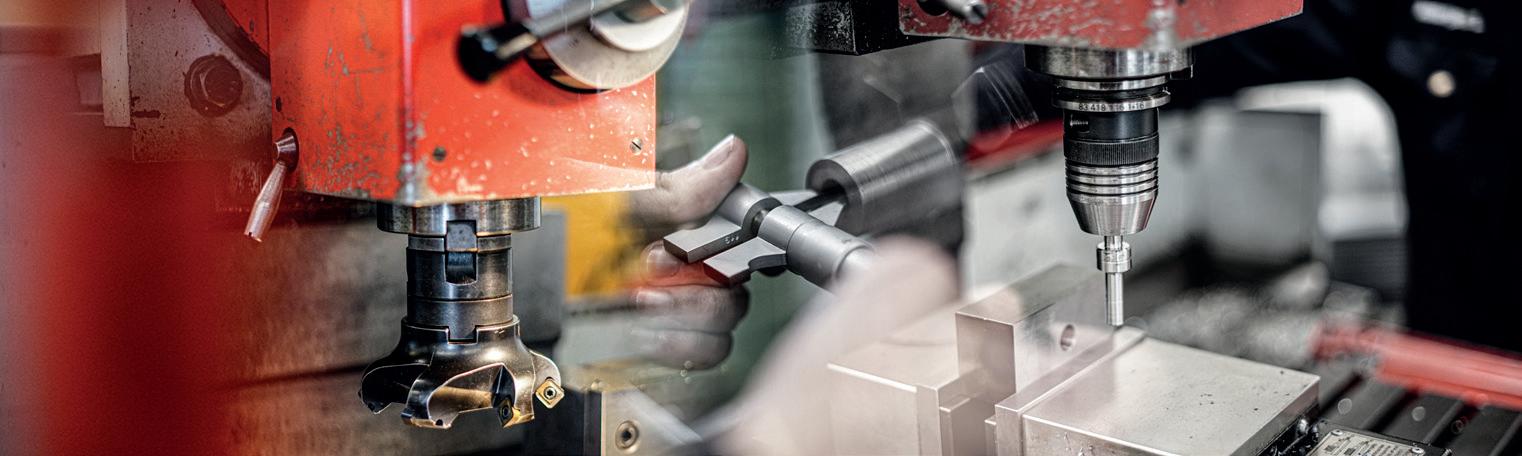
It must be formed with a mandate to focus on delivery, rather than another round of consultation on skills requirements and qualifications. Time is of the essence if we are to see change in this Parliament.
Creating career appeal
Improving the attractiveness of a career in the manufacturing sector requires the industry to modernise. Modern, advanced manufacturing often removes physical, exhausting, low-paid jobs from the sector and instead creates quality digital, engineering-skilled work, which is what jobseekers are crying out for.
However, we still have some way to go if we are to create a sustainable pipeline of talent. This should start with efforts to increase the number of people choosing STEAM subjects and should be supported through increased funding for vocational subjects and better access to careers advice.
Why the stakes are high
The manufacturing sector employs 2.6 million people nationwide and contributes £224 billion GVA (gross value added) to the economy. However, skills gaps throughout the sector are estimated to cost £6 billion annually, and we risk further losses without investment in a skilled workforce capable of meeting the needs of a modern Industrial Strategy.
Closer cross-collaboration and smarter hiring processes to generate new talent for manufacturing
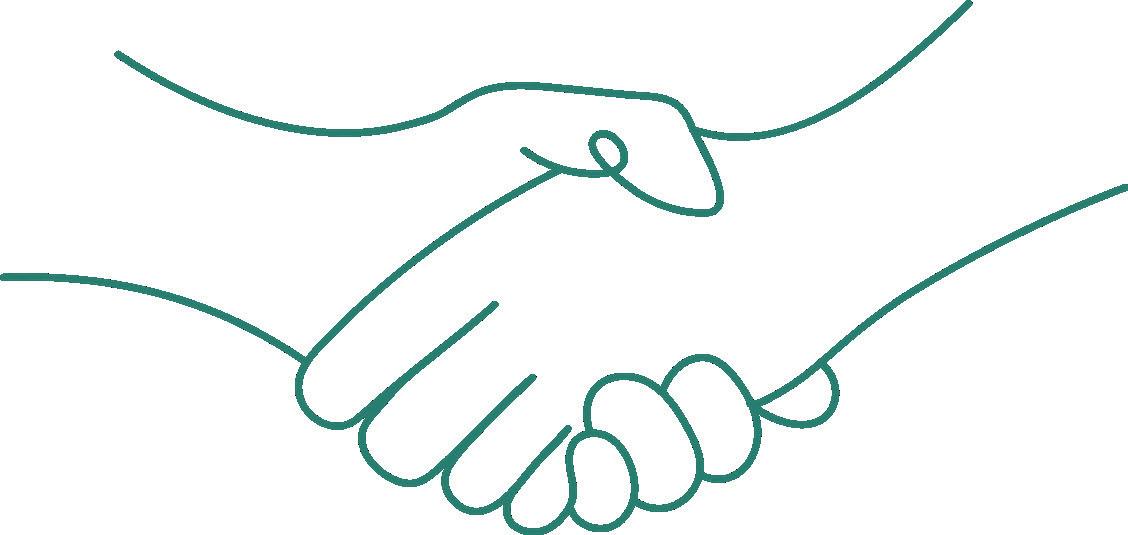
TIndustry needs to partner with government and educational institutions to help grow the workforce.
he manufacturing sector is vital to the UK economy, driving innovation, productivity, and growth. It contributes around £220 billion per year to the economy.1 However, attracting and retaining new talent continues to be a significant challenge.
New talent crucial for the sector to thrive
Apprenticeship starts in the engineering and manufacturing sectors have declined since 2017/18 and have stalled at around 46,000 starts per year (2023/2024).2 This is worrying considering manufacturing employers reporting skills shortages. In 2023, we
ran an inquiry in partnership with Lord Willetts and Lord Knight, to understand the reasons behind the downward trend. These are outlined in our Fit for the Future report which suggests many businesses, particularly smaller firms, are struggling to find the capacity and resources to take on young apprentices. There are concerns too about the quality of training provision and barriers of complying to apprenticeship standards.
Bringing new talent into the manufacturing workforce through apprenticeships is vital. We support efforts by government to find ways to increase the uptake and offer of apprenticeships, particularly for younger people. We welcomed
the announcement of foundation apprenticeships at the end of 2024 but would urge government not to rush into introducing them. It is vital that there is clarity about whom they are for, what problem they look to address, how they fit into the wider system and how and if they can work for the engineering and manufacturing sectors.
Stakeholder collaboration to strengthen diversity
We also need more women and more currently underrepresented groups to join the manufacturing workforce. For this to happen, we need businesses to offer more opportunities and look at their recruitment as well as employment practices, and we need more young people to be aware of the apprenticeship options available to them and how to access them.
Collaboration between industry, government, and educational institutions is crucial for that. For example, partnerships between businesses and schools and colleges can help raise awareness of the opportunities available in the sector and encourage young people to consider a career in manufacturing. By working together, these stakeholders can develop targeted initiatives such as work experience or pre-apprenticeship programmes that address the skills gap and promote careers in manufacturing.
References: 1. MAKE UK. 2024. UK manufacturing: the facts 2024. 2. GOV.UK. 2025. Apprenticeships: Academic year 2024/25.
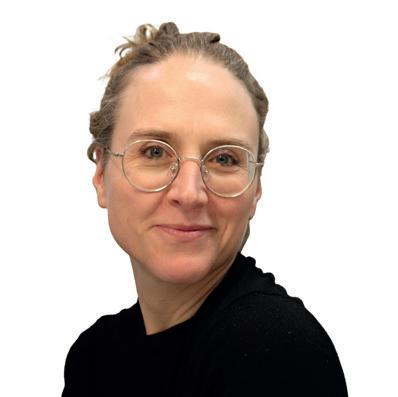
WRITTEN BY Beatrice Barleon Head of Policy and Public Affairs, EngineeringUK
WRITTEN BY
Rob Allen Senior Policy and Research Manager, Policy Connect
WRITTEN BY Mike Reader MP Member of Parliament for Northampton South
Financing the future: unlocking growth and resilience in UK manufacturing
We want to bridge this gap by providing solutions and flexible expertise to help manufacturers scale and grow.
As the Government rolls out its new industrial strategy, the UK manufacturing sector stands at a critical point: securing access to finance will be essential to driving long-term growth.
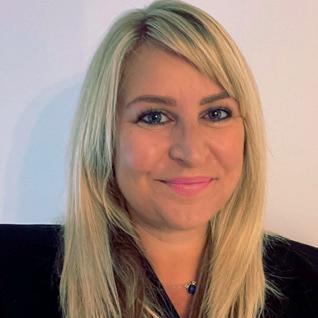
Often regarded as the backbone of Britain’s economy, manufacturing not only contributes over £200 billion annually to the UK’s GDP (according to manufacturing body, Make UK), the sector also provides critical supply-chain capabilities, job creation and training.
Amid global uncertainty, the sector faces unprecedented challenges. Bold investments in new technology, sustainable practices, innovation and human capital could be the key to thriving in a world of rapid change.
At NatWest, we’re committed to pushing Britain’s manufacturing sector forward into a new era of opportunity. We are ready to connect manufacturing businesses with the funding and support they need to capitalise on the government’s industrial strategy — and position themselves for enduring success.
Key factors for future success
The Government’s industrial plan outlines a clear, decadelong vision to future-proof UK industry by encouraging investment in advanced manufacturing processes, clean energy, digital infrastructure and strong supply chains.
The strategies it identifies for future success are:
• Automating processes to boost productivity
• Digital transformation to drive competitiveness
• Sustainable growth to accelerate the transition to net zero
• Workforce agility to adapt to future skills needs
• Supply chain resilience to reduce vulnerability and improve strategic capability
Finance is often crucial for manufacturers looking to invest in new machinery, adopt cleaner tech, expand capacity or improve energy efficiency. However, businesses have cited complexity or lack of awareness as barriers to securing the right financial support.
Backing British manufacturing
NatWest, along with our asset finance division, Lombard, currently works closely with over 50,000 businesses and customers in UK manufacturing, from corporates and PLCs to sole traders and the SMEs, which are the engine of the UK’s manufacturing base.
Our regional relationship managers, sector specialists and enterprise teams are embedded in local economies across the country. This localised approach ensures they understand the specific challenges and opportunities facing manufacturing businesses, from engineering hubs in the Midlands to advanced materials innovators in the Northeast.
“British manufacturers are the lifeblood of our economy, and at NatWest, we’re committed to helping our manufacturing customers navigate the challenges and embrace the opportunities presented by an evolving and changing sector,” says Laura Capper, NatWest’s Head of Manufacturing and Construction.
“We know manufacturing businesses require a bank that understands industry dynamics, and through our sector insight, specialist trained staff and vast network of strategic partners, we support manufacturing businesses with tailored solutions.”
Finance is a key enabler in supporting longerterm strategies. Our recent report with Make UK4 found that 87% of businesses say they will require access to finance to meet their investment plans.
A recent report, published by NatWest and Make UK, found that almost three-quarters of companies said that without access to finance, investments would not take place. This clearly demonstrates the pivotal role finance plays in activating the government’s industrial strategy – and the importance of strong, lasting partnerships between finance providers and businesses.
We are part of a diverse ecosystem of products, services and information sources empowering manufacturers to become Future Fit, offering support across five key growth pillars:
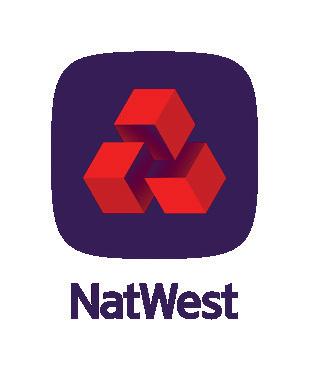
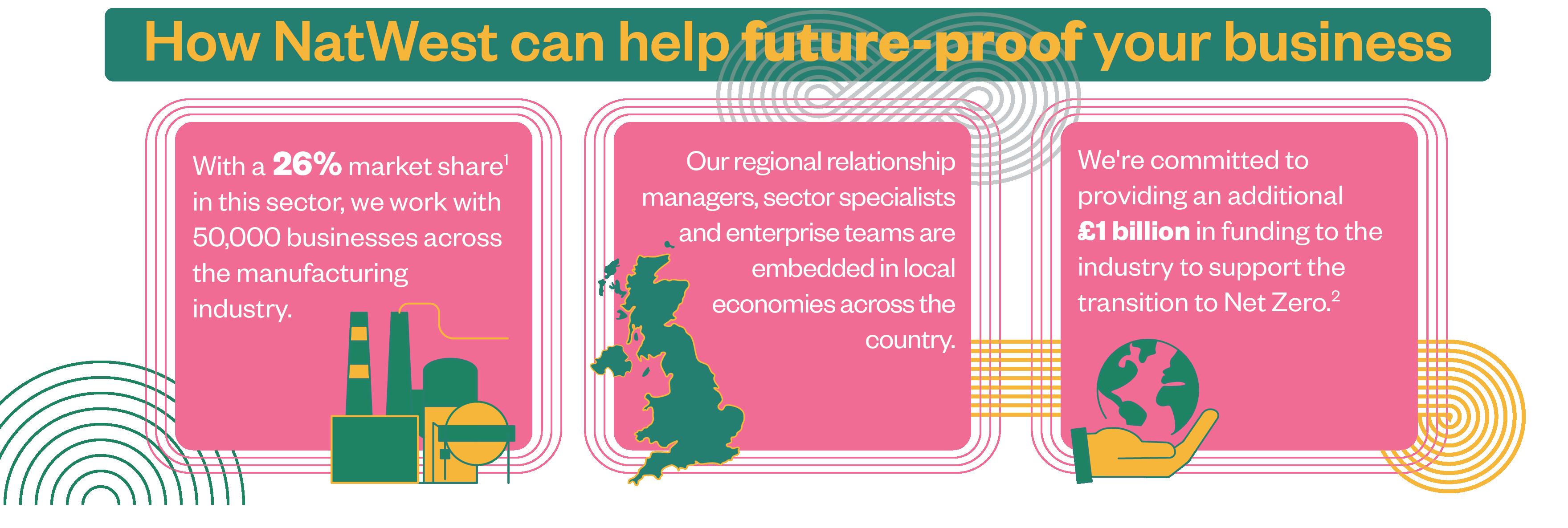
Paid for by NatWest
INTERVIEW WITH Laura Capper Head of Manufacturing and Construction, NatWest
Discover how NatWest and Lombard can support your manufacturing journey at natwest.com/ business/ sectorexpertise/ manufacturing. html and lombard.co.uk. Security may be required. Products fees may apply. Finance is subject to status and for business purposes only.
1. Leveraging automation and asset finance
Rising costs and competition make automation essential for many businesses. However, manufacturers investing in robotics, AI-driven machinery, or advanced data systems often face capital limitations, which can slow progress.
Lombard, the UK’s largest asset finance provider5, enables businesses to acquire cutting-edge equipment without large upfront costs. Through hire purchase, leasing or other flexible funding options, we help manufacturers to increase production and reduce downtime.
2. Driving digital transformation
Digitisation is redefining how manufacturers operate, from predictive maintenance to cloud-based supply chain management. However, integrating these technologies requires investment in infrastructure and training.
NatWest can help support this digital transition through finance as well as strategic partnerships with tech providers and innovation centres. Businesses can also access the NatWest Accelerator Programme, which offers mentoring and development support for scale-ups, driving digital innovation in manufacturing. Through relationships with industry bodies like Make UK and the High Value Manufacturing Catapult, we integrate manufacturers into networks where they can share best practices, access tech pilot schemes and connect with sector specialists.
3. Advancing sustainability for clean growth
As the UK moves towards the Government’s goal of net zero by 2050, sustainable manufacturing needs to be good for business — and good for the planet.
We’re committed to helping businesses in the manufacturing sector transition to net zero through sustainability solutions, ESG advisory services and practical support. In 2023, we pledged £1 billion in additional lending to UK manufacturing to support this transition.
With our Carbon Planner tool, businesses can assess their environmental impact and identify cost-saving opportunities through energy efficiency, circular economy models and investments in clean technology. Lombard complements this with asset finance, helping businesses acquire everything from electric fleet vehicles (EVs) to solar panels and energy-efficient manufacturing equipment.
4. Building a talent pipeline
Technological adoption is only as effective as the workforce behind it. As skills gaps widen in areas like data science, robotics and cybersecurity, manufacturers need agile, future-ready talent.
NatWest can help manufacturing businesses build a value proposition with broad appeal, offering benefits like workplace pensions, salary sacrifice EV schemes and wellbeing programmes.
We also partner with local educators, local enterprise partnerships (LEPs) and innovation hubs to connect businesses with the training, apprenticeships and reskilling programmes needed to attract next-gen talent.
5. Improving supply chain resilience
Supply chain management has been challenging for manufacturers, amplified by the global pandemic and geopolitical events. Manufacturers are simplifying supply chains and reducing dependency on specific countries through strategies such as nearshoring, friendshoring and onshoring.
Our trade specialists support manufacturers in optimising their supply chain relationships, mitigating risks associated with new suppliers, and identifying new markets for export.
Financial support for future growth
Our recent report with Make UK found that 87% of businesses say they will require access to finance to meet their investment plans in the next two years. The research also suggests that 39% of manufacturers could use external finance instead of their own funding to invest and keep their working capital for day-to-day operations.
We are committed to removing barriers to external funding, enabling businesses to grow while maintaining healthy working capital reserves and cash flow.
Accelerating innovation for competitive advantage
Manufacturing is a vital and high-value sector of the UK economy and one of the most rapidly changing. Businesses need financial partners with sector expertise and innovative solutions to gain a competitive edge in the sector.
The industrial strategy ushers in a new era of opportunity for manufacturing businesses, and we’re committed to helping them fully benefit from it. “We continue to evolve our support to UK manufacturers and have many solutions to enable businesses to grow, innovate, improve productivity and become more sustainable,” Capper says. “Our ambition is not just to finance the future of UK manufacturing — but to help shape it.”
References:
1. Experian pH March 2024
2. NatWest Group to provide £1 billion in additional lending to UK manufacturing to support net zero transition | NatWest Group
3. Resetting manufacturing for tomorrow’s opportunities | NatWest business survey of 1,000 UK businesses across 10 sectors in 2024
4. Finance: Opening doors to investment in manufacturing finance for manufacturing: Make UK research highlights | NatWest Business
5. Asset Finance UK Top 50, 2024
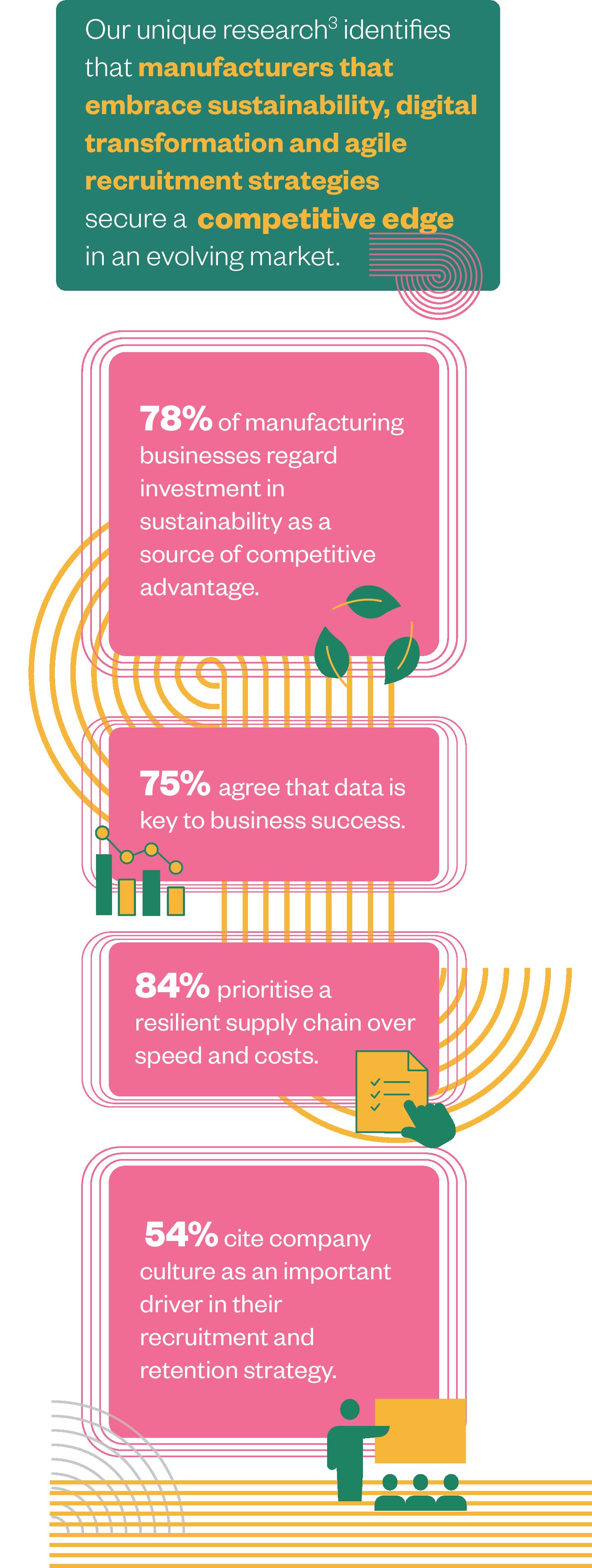
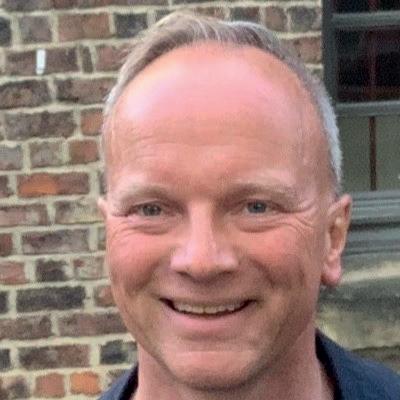
David Grailey Managing Director, Manufacturing Technology Centre (MTC) Training
Empowering the future: skills investment crucial for the industrial strategy
Delivering the UK’s Industrial Strategy relies on a thriving manufacturing industry, but the sector faces significant labour constraints.
While the Strategy emphasises innovation and economic growth, it will fall short without serious investment in skills and enough workers in growth sectors. With growing demand for talent in critical areas such as nuclear and defence, companies struggle to find people with the right skills. Urgent action is needed to attract skilled workers to advanced manufacturing, especially those from other industries.
Supporting apprenticeships and future-proofing the workforce
Investment in skills and training must be a cornerstone of the new Strategy. It needs to support all businesses, particularly SMEs, which often lack the time and resources to focus on training or onboarding apprentices. Financial and other incentives help to manage apprenticeship administration. In addition, pre-skilling apprentices with the fundamentals before employment can remove barriers to growing and upskilling teams. We also need to future-proof our workforce. As technology advances, it is essential that the UK’s workforce can use these effectively. Public funding must be used strategically to maximise investment and drive real outcomes through highly skilled workers. By investing in our workforce, we can fuel innovation, enhance global competitiveness, ensure long-term economic growth, and provide
The technologies powering UK manufacturing’s future
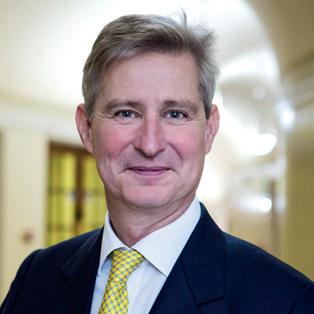
individuals with meaningful career progression in advanced, well-paid technical roles. Companies will also benefit from lower recruitment costs due to higher retention rates and increased employee loyalty.
Focusing on skills is crucial
At the MTC, the focus on skills is happening. MTC leads Innovate UK’s Workforce Foresighting Hub, which identifies skills required for future jobs, ensuring education and training systems meet emerging needs. By gathering insights from the Catapult Network’s technology experts, employers and educators, as well as analysing global and national datasets, the Hub translates foresight into action. Ultimately, it all comes down to skilled and productive people. To have a manufacturing sector that is resilient, productive and future-ready, skills must be at the heart of the conversation. Properly funding and developing a highly skilled workforce ensures UK manufacturing not only keeps up with global change but leads the way. Skills are the foundation for a successful Industrial Strategy.
MTC transforms how commercial products are designed, made and built. Our independent research and technology organisation has delivered pioneering solutions to a variety of industries. We are proud to be part of the High Value Manufacturing Catapult, working in partnership with Innovate UK. For more information visit: the-mtc.org For more information about the Catapult Network, visit: catapult.org.uk
Discover the cutting-edge technologies powering UK manufacturing. Learn how they drive innovation, productivity and sustainability at the heart of industry and national strategy.
Every man-made product starts with a process, and behind that process lies technology. The Manufacturing Technologies Association (MTA) Cluster represents the companies that provide these essential — but often invisible — technologies: the ones that shape, cut, form and assemble raw materials into the products that power our world.
These are the ‘mother technologies’ of manufacturing — essential foundations systems without which modern industry couldn’t function. Today, they are advancing at speed, driven by connectivity, automation and digital transformation. For the first time since the age of Henry Ford, we can manufacture flexibly, efficiently and viably to demand revolutionising productivity and sustainability.
Why manufacturing drives UK excellence
As the Government looks ahead to a new Industrial Strategy, it’s clear that manufacturing plays a pivotal role in shaping a stronger, more resilient UK. From enabling net zero goals and export growth to improving national security, health and food systems, manufacturing technologies are at the heart of solutions for today’s complex global challenges.
Everything starts with our sector. If you want to build anything — whether it’s a satellite, train or turbine — you need the technologies our members provide. At the MTA, we are proud to be the enablers of innovation, productivity and progress.
Efforts to champion UK industrial revolution
The MTA Cluster is the voice of this sector. We champion the innovation, investment and skills needed to keep the UK at the forefront of industrial excellence. We are owned by the industry we serve and are proud to support businesses across every stage of the supply chain.
We also organise MACH 2026, the UK’s only fully live manufacturing exhibition, where advanced technologies can be seen operating as they would in real production environments.
To realise the ambitions of the new strategy, the UK must invest in the technologies that make everything else possible. This is where the future of manufacturing begins.
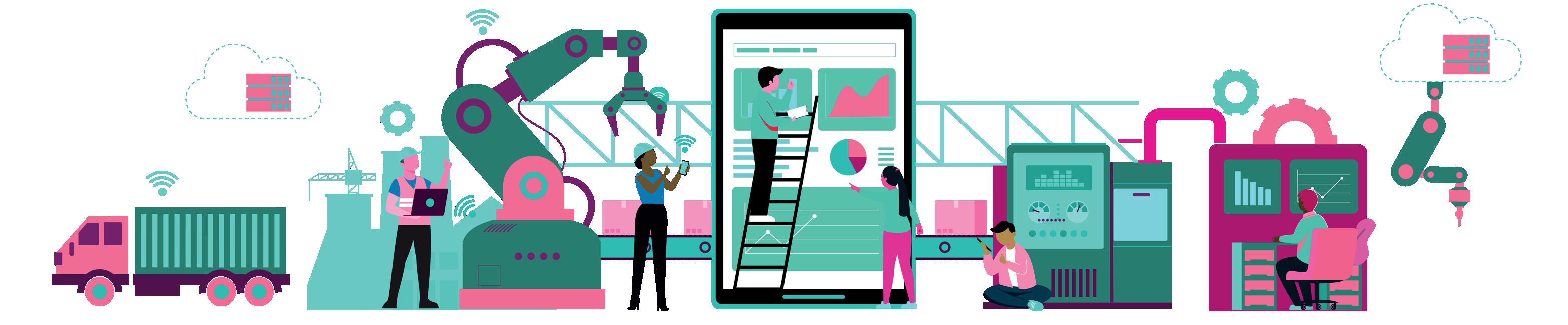
WRITTEN BY
WRITTEN BY James Selka
Chief Executive Officer, Manufacturing Technologies Association
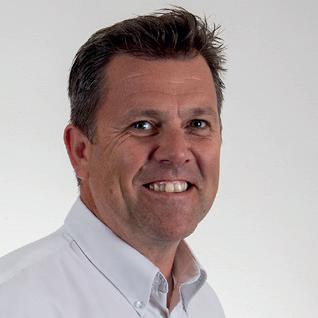
Why people development is a boon for business agility — and growth
Manufacturing companies should recognise the importance of people development. It’s an investment that creates workforce agility and gives businesses a competitive edge.
“All companies must be resilient,” says Malcolm James, CEO of business transformation experts, Sharing in Growth. One way to achieve resilience is through agility. “Agile workforces have the ability to foresee problems, react to them quickly — and, crucially, think of challenges as opportunities to do things better in the future,” he explains.
People development strategies
However, to become truly agile, a business may have to fundamentally change the way it operates. Malcolm argues that the most sustainable and effective transformations occur when a business puts its people first. This includes engaging and motivating them with development strategies to help them reach their full potential.
He says: “People are the most important asset in any business. However, some UK SMEs are unwilling to invest in people at the level and scale that’s required for them to achieve double-digit growth.” For example, if companies in the manufacturing industry pour investment into machinery but forget about people development, it can harm their agility and, ultimately, competitiveness.
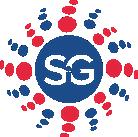
Investing in people to increase confidence and capabilities Sharing in Growth has helped many manufacturing companies build resilience and agility through people
UK life sciences
being held back by lack of institutional investment
UK life sciences lead in R&D, yet lag in funding. Find out how pension reform and investment shifts could unlock £50 billion to drive global health innovation.
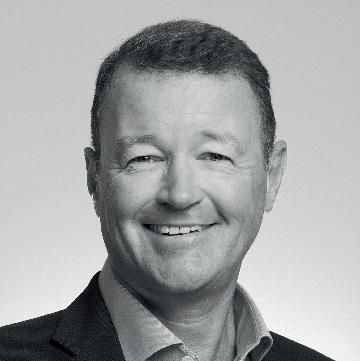
Tdevelopment. Yet, as every business is different, Malcolm warns that this is not a ‘copy and paste’ process. Every transformation programme is unique to that business, as the DNA of the business is created through the Senior Leadership Team’s personalities and behaviours.
“The first thing we do is listen to senior leaders to understand the vision, mission and values of their business and build a three-to-five-year STRAP (Structured Requirements Analysis Planning) strategy,” he says. “When the business’s purpose is clear, the next step is talking to its people, at all levels, about ways they can contribute to it. Once they’re engaged, our transformation coaches work with them to grow their confidence and capabilities.”
Creating change for long-term success Change doesn’t have to be a painful process, although the common perception is that people don’t like it much. “I disagree,” says Malcolm. “People might be fearful of change, but actually, human beings seek creativity and change.”
It’s a two-way street because transforming your business by investing in people with learning and upskilling is a career boost for employees — and helps protect your interests over the long term. Malcolm says: “If your workplace is creative and exciting and your workforce is curious about seeking knowledge and keen to experiment and embrace change, it’s a way to future-proof your business.”
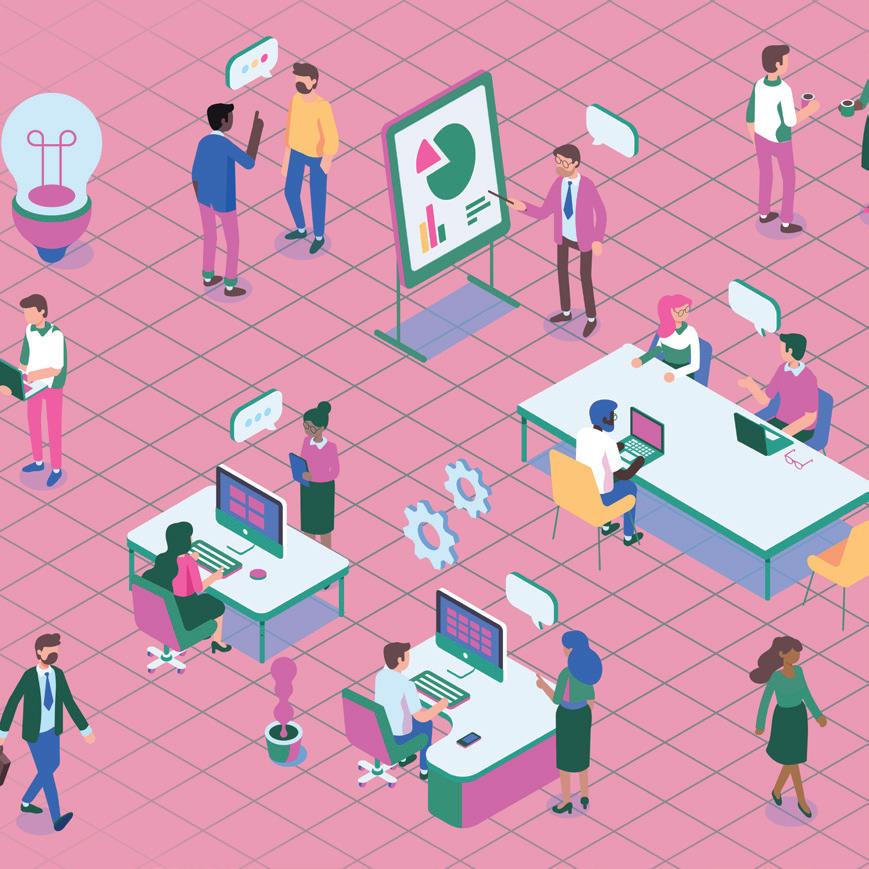
he UK life science sector punches above its weight on the global stage. Our small nation plays host to only 0.8% of the world population but four out of the world’s top 10 universities. It also accounts for 8.2% of the global share of highly cited researchers, making us world leaders per capita in important R&D.
Unlocking venture capital potential
However, we are not very good at investing in that innovative brilliance to make it world-leading commercially. It is widely recognised that our conservative approach to venture capital investment means that the leaders of these bright
companies spend most of their time on the fundraising trail, which stops them from focusing on other important leadership areas like strategy development, people and culture, regulatory and market access. When they do get some cash, it is typically modest amounts, which means they need to start all over again.
Lack of institutional investment in UK
life sciences
The key issue is the lack of institutional (primarily pension fund) investment in UK life sciences. Paradoxically, the Canadian pension industry invests more in UK life sciences than our own pension
industry. The amount of capital that these funds have access to — and decide on the destination of — is significant enough to be truly transformational to UK life sciences.
What’s the solution?
The (previous Conservative) Government created, in conjunction with the pension industry, the Mansion House Compact, which aimed to invest 5% of UK pension funds into unlisted (private) companies by 2030. This voluntary deal has made only very limited progress since it was signed in mid2023. Recently, the Mansion House Accord was signed by 17 pension funds and adds momentum to investing £25 billion into the British economy by 2030.
Will it work?
Life sciences (one of the Government’s eight growth focus areas identified in its Invest 2035 growth plan due in June) could fare favourably in this. If it does, the uptick in material investment could be game-changing. We have done the difficult stuff (spent almost a millennium investing in world-class education to foster innovation). Now, we just need to inject the cash that can make those brilliant ideas fly, turning them into health innovations that transform the lives of you and me.
WRITTEN BY Stuart Rose
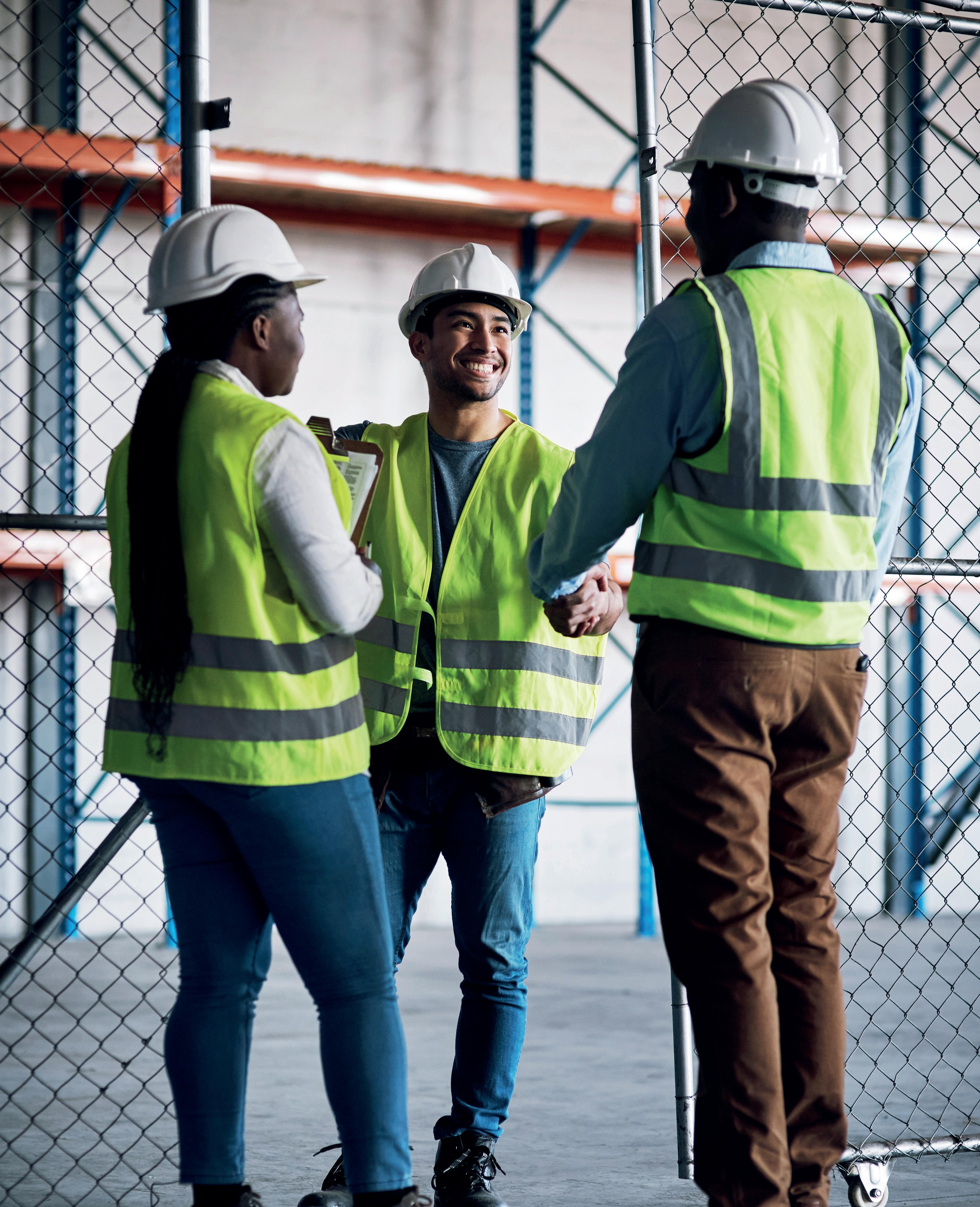
Ultimately, it all comes down to skilled and productive people.
~David Grailey, Managing Director, Manufacturing Technology Centre (MTC) Training