Here's What You Need to Understand About Fiber Opening Machines
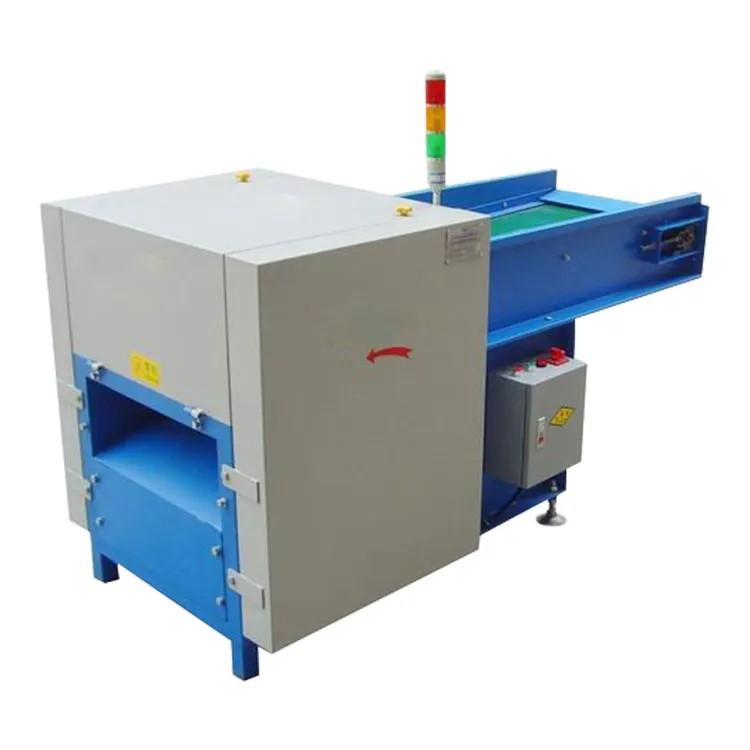
Fiber opening machines are sophisticated pieces of equipment utilized extensively across various industries, especially in textile manufacturing. These machines serve a critical function in the initial stages of fiber processing, where they meticulously handle raw materials such as cotton, wool, polyester, or blends thereof.
At the core of fiber opening machines are intricate mechanisms comprising rollers, beaters, or blades, each meticulously engineered to perform a specific task. As the raw fiber material, often delivered in compacted bales or bundles, is fed into the machine, these components spring into action. They systematically tease apart the fibers,
disentangle any clumps or knots, and effectively "open" them up, thus enhancing their loftiness and fluffiness.
This process of fiber opening holds several key advantages for downstream processing. Firstly, it facilitates the blending of different types of fibers, enabling manufacturers to create custom blends tailored to specific product requirements. By ensuring uniformity in fiber composition, these machines contribute to the consistency and quality of the final textile product, whether it's yarns, fabrics, or nonwoven materials.
Moreover, fiber opening machines significantly contribute to the efficiency and productivity of textile manufacturing operations. By automating the labor-intensive task of fiber preparation, they reduce reliance on manual labor, thereby cutting down on production time and costs. Additionally, the mechanized process minimizes the occurrence of human errors, ensuring a higher degree of precision and reliability in the output.
Beyond these operational benefits, fiber opening machines also play a crucial role in improving the overall sustainability of textile production. By optimizing fiber utilization and minimizing waste, they help companies operate more eco-consciously and in alignment with evolving environmental standards and regulations.
In essence, polyester fiber opening machines represent a cornerstone of modern textile manufacturing, combining precision engineering with practical efficiency to enable the seamless transformation of raw fibers into high-quality, market-ready products. Whether in large-scale spinning mills, specialized non-woven fabric plants, or smaller textile
workshops, these machines continue to drive innovation and progress in the industry.
Fiber opening machines stand as monumental pillars within the vast expanse of industrial infrastructure, commanding attention as the stalwart guardians of the textile manufacturing realm. In the grand tapestry of production processes, these machines wield unparalleled prowess, serving as the linchpin that bridges the chasm between raw fiber and refined textile.
Within the labyrinthine confines of their mechanical architecture lies a symphony of precision-engineered components, meticulously choreographed to orchestrate a dance of transformation. The raw material, often delivered in imposing bales or bundles, undergoes a metamorphosis at the hands of these machines. Guided by a labyrinth of rollers, beaters, and blades, the fibers embark on a journey of liberation, shedding their tightly wound confines to embrace a newfound freedom.
But this liberation is not merely symbolic; it is the very essence of efficiency and productivity. With each fiber unfurled and di sentangled, the machine paves the way for a seamless convergence of diverse materials. Blends are forged, compositions harmonized, and uniformity enshrined. Through this meticulous process of fiber opening, the machine becomes the architect of consistency, ensuring that every strand, every thread, bears the hallmark of excellence.
Yet, beyond the realm of uniformity lies the realm of sustainability. In an era where environmental stewardship reigns supreme, fiber opening machines stand as champions of eco-conscious manufacturing. By optimizing fiber utilization and minimizing waste, they serve as
custodians of finite resources, weaving a tapestry of sustainability that stretches far beyond the confines of the factory floor.
In the grand scheme of textile prod uction, fiber opening machines are not merely cogs in the wheel; they are the very heartbeat of progress. From the towering heights of sprawling spinning mills to the intimate confines of bespoke workshops, their influence reverberates across the industry landscape. As beacons of innovation and efficiency, they illuminate the path forward, guiding manufacturers towards a future defined by excellence, sustainability, and unparalleled quality.
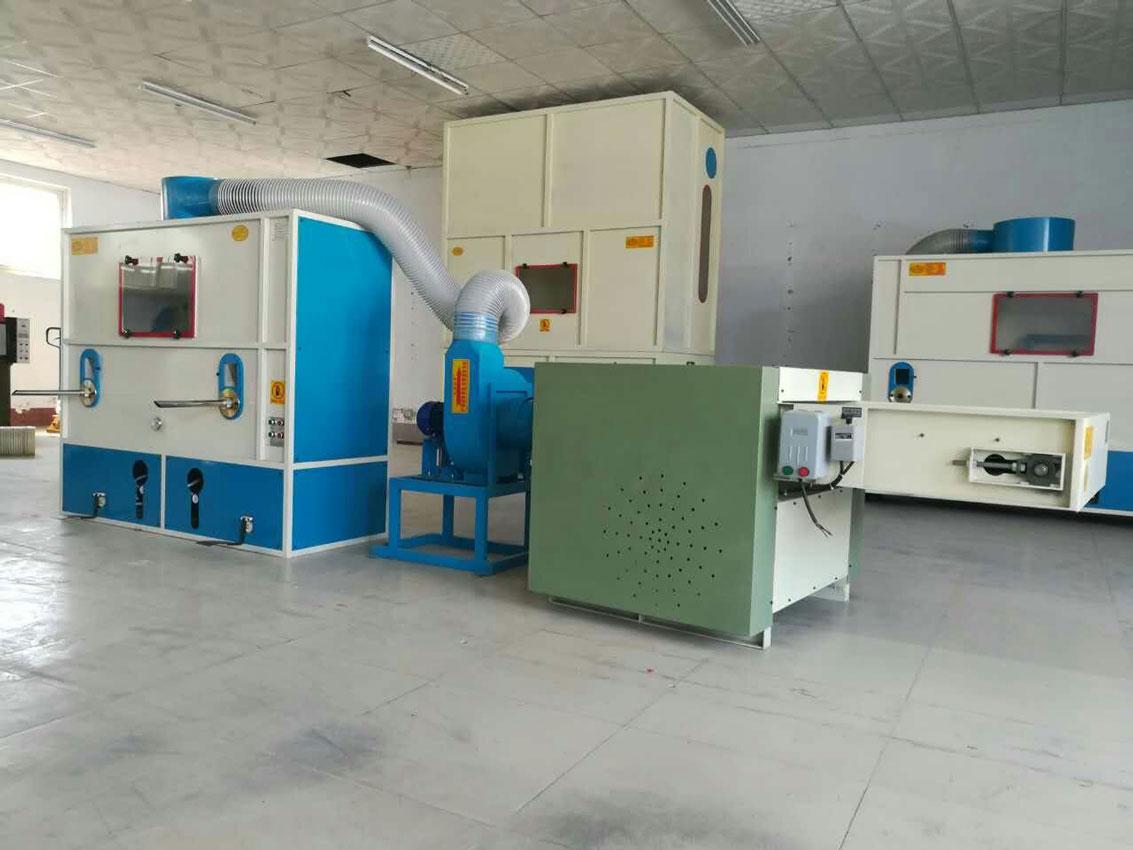
The advantages of integrating polyester fiber opening machines into textile manufacturing processes are monumental, exerting a transformative impact on operational dynamics and industry standards:
1. Revolutionized Production Capacities: Fiber opening machines revolutionize production capacities by enabling the rapid and continuous processing of raw fibers. Their high throughput capabilities facilitate the handling of immense volumes of raw material, empowering manufacturers to scale operations to unprecedented levels.
2. Elevated Product Consistency: These machines uphold an unparalleled standard of product consistency by meticulously refining raw fibers into uniform strands. By mitigating inconsistencies in fiber composition and texture, they foster the creation of textiles renowned for their uniformity and superior quality across batches.
3. Expedited Time-to-Market: With fiber opening machines streamlining fiber preparation, manufacturers experience significantly reduced lead times from raw material acquisition to final product delivery. This accelerated time-to-market not only enhances competitiveness but also enables companies to swiftly respond to dynamic market demands and emerging trends.
4. Empowered Customization Capabilities: The flexibility afforded by polyester fiber opening machines empowers manufacturers to craft bespoke fiber blends tailored to precise specifications. This versatility facilitates the creation of textiles with customizable attributes such as strength, softness, and color, allowing
companies to cater to diverse consumer preferences and niche markets.
5. Optimized Resource Utilization: By minimizing waste and maximizing the utilization of raw materials, fiber opening machines epitomize resource efficiency. Their adept handling of fibers ensures minimal material loss during processing, thereby conserving resources and reducing environmental impact.
6. Heightened Operational Efficiency: Integrating fiber opening machines into production workflows optimizes operational efficiency by streamlining processes and reducing manual labor dependencies. This operational streamlining minimizes bottlenecks, enhances workflow fluidity, and augments overall productivity, thereby elevating operational performance to unprecedented heights.
7. Facilitated Innovation and Adaptability: Fiber opening machines serve as catalysts for innovation, empowering manufacturers to explore new materials and techniques. Their adaptability allows companies to swiftly pivot production in response to market shifts, technological advancements, and evolving consu mer preferences, thus fostering a culture of continuous innovation and market relevance.
8. Augmented Global Competitiveness: Leveraging polyester fiber opening machines equips manufacturers with a competitive edge on the global stage. By delivering superior product quality, expedited production cycles, and enhanced customization capabilities, these machines position companies as leaders in the
fiercely competitive textile industry, driving sustained growth and market dominance.
In essence, the integration of fiber opening machines transcends mere process optimization, ushering in an era of unparalleled efficiency, innovation, and competitiveness in textile manufacturing. As stalwarts of progress, these machines pave the way for industry-wide advancements, shaping the landscape of textile production for generations to come.
The deployment of a pillow filling machine heralds a transformative revolution in the realm of bedding and textile manufacturing, ushering in a new era characterized by unparalleled efficiency, precision, and scale. This colossal piece of industrial machinery stands as a titan among equipment, orchestrating a symphony of processes with remarkable finesse and ingenuity.
At its core, the blow pillow filling machine embodies the pinnacle of engineering innovation, boasting a sophisticated array of components meticulously engineered to optimize every facet of the filling process. From its towering hopper systems, capable of accommodating vast quantities of filling material, to its intricate conveyor belts and rotary mechanisms that seamlessly transport pillow shells through the production line, every element is finely tuned to perfection.
The operation of this behemoth is a marvel of modern automation, a ballet of mechanical precision choreographed to perfection. As pillow shells glide effortlessly along the conveyor belt, they are met with a precise and calculated dosage of filling material, dispensed with unwavering accuracy by the machine's state-of-the-art dispensing
systems. The result is a symphony of efficiency, as pillow after pillow is swiftly and flawlessly filled to exacting specifications.
But the true marvel of the pillow filling machine lies not merely in its ability to fill pillows at an unprecedented rate, but in its capacity to do so with uncompromising quality and consistency. With advanced sensors and monitoring systems working tirelessly in the background, every pillow is meticulously inspected and scrutinized to ensure that it meets the highest standards of quality. From ensuring uniform filling densities to detecting and correcting any imperfections or irregularities, the machine leaves no stone unturned in its quest for perfection.
The benefits of employing such a monumental machine are manifold, extending far beyond mere improvements in production efficiency. By automating the filling process, manufacturers can dramatically reduce labor costs, minimize human error, and achieve levels of consistency and precision that would be unattainable through manual methods alone. Moreover, the sheer scale and throughput of the machine enable manufacturers to meet even the most demanding production requirements with ease, positioning them at the forefront of the industry.
In essence, the blow pillow filling system stands as a testament to human ingenuity and innovation, a towering monument to the relentless pursuit of excellence in manufacturing. As it continues to revolutionize the way pillows are produced, it not only reshape s the landscape of the bedding industry but sets a new standard of efficiency and quality that will endure for generations to come.
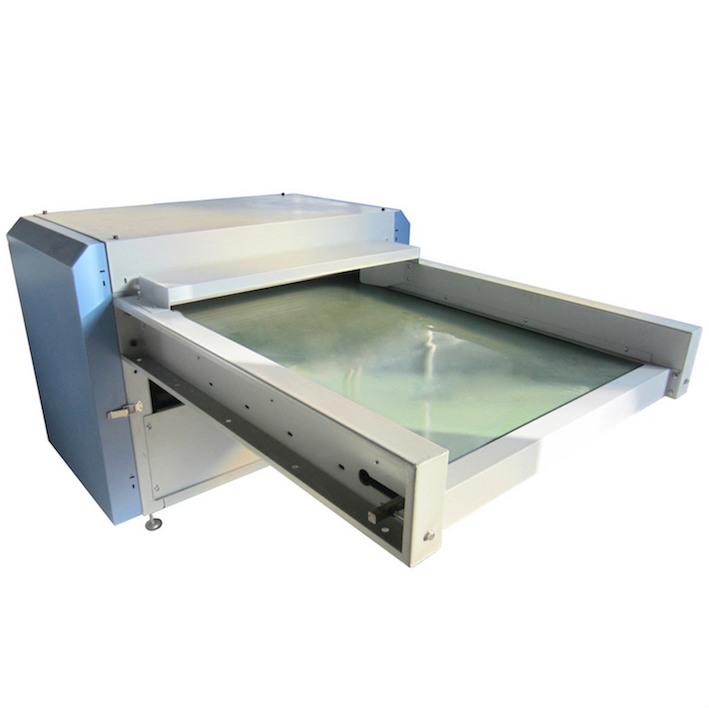
The advantages of utilizing a pillow filling machine in the manufacturing process are monumental and multifaceted, underpinning a transformative shift in efficiency, quality, and profitability within the bedding industry:
1. Unmatched Production Efficiency: The deployment of a pillow filling machine dramatically enhances production efficiency by automating the filling process. These machines boast impressive throughput capacities, enabling the rapid filling of pillows at a rate far surpassing manual methods. As a result, manufacturers can meet high demand volumes while minimizing production time and labor costs.
2. Precision and Consistency: Blow pillow filling machines ensure unparalleled precision and consistency in the filling process. Through advanced dispensing systems and monitoring technologies, they dispense filling material with pinpoint accuracy, resulting in pillows that exhibit uniform density and loftiness across the entire production batch. This consistency elevates product quality and enhances customer satisfaction.
3. Labor Cost Reduction: By automating the filling process, pillow filling machines significantly reduce the need for manual labor, thereby cutting down on labor costs. This cost-saving measure not only improves operational efficiency but also frees up human resources for more specialized tasks, such as quality control or product development.
4. Customization Capabilities: Pillow filling machines offer manufacturers the flexibility to customize pillows according to specific customer preferences and market trends. Whether adjusting filling material types, densities, or pillow sizes, these machines can accommodate a wide range of customization options, enabling manufacturers to cater to diverse consumer demands and niche markets.
5. Streamlined Operations and Scalability: Integrating a pillow filling machine into production workflows streamlines operations by minimizing bottlenecks and optimizing workflow efficiency. This operational streamlining facilitates scalability, allowing manufacturers to ramp up production in response to increased demand or market expansion without compromising product quality or consistency.
6. Enhanced Quality Control: Pillow filling machines incorporate advanced quality control mechanisms to detect and address any irregularities or defects during the filling process. Through realtime monitoring and automated adjustments, these machines ensure that each pillow meets stringent quality standards, reducing product wastage and minimizing the risk of product recalls or returns.
7. Competitive Edge and Market Differentiation: By leveraging the capabilities of blow pillow filling machines, manufacturers can gain a competitive edge in the marketplace. The ability to produce high-quality pillows efficiently and consistently positions companies as leaders in the industry, fostering brand loyalty and driving market differentiation.
In summary, the adoption of a pillow filling machine represents a strategic investment for manufacturers seeking to enhance productivity, quality, and competitiveness in the bedding industry. By harnessing the benefits of automation and precision engineering, these machines propel manufacturers towards greater profitability and success in an increasingly competitive market landscape.
The implementation of a pillow filling machine heralds a seismic shift in the landscape of bedding manufacturing, embodying a colossal leap forward in efficiency, precision, and scalability. This towering behemoth of industrial innovation stands as a monument to progress, its monumental presence reshaping the very foundations of production processes within the textile industry.
At its core, the pillow filling machine epitomizes the pinnacle of engineering ingenuity, boasting a labyrinthine network of components
meticulously designed to optimize every facet of the filling process.
From its towering silos brimming with filling materials to its intricate conveyor systems that deftly maneuver pillow shells through the production line, each element is a testament to human innovation on an unprecedented scale.
The operation of this titan among machines is a symphony of automation, a choreographed dance of mechanical prowess orchestrated with flawless precision. As pillow shells glide seamlessly along the conveyor belt, they are met with a symphony of filling material dispensed with unparalleled accuracy by the machine's sophisticated dispensing mechanisms. The result is a breathtaking spectacle of efficiency, as pillow after pillow emerges from the production line, perfectly filled to exacting standards.
Yet, the true marvel of the pillow filling machine lies not merely in its capacity for mass production, but in its unwavering commitment to quality and consistency. Equipped with advanced sensors and monitoring systems, every pillow undergoes meticulous scrutiny to ensure that it meets the highest standards of excellence. From uniform filling densities to flawlessly sealed seams, each pillow bears the hallmark of craftsmanship and precision.
The benefits of harnessing the power of this industrial titan are nothing short of extraordinary, transcending mere improvements in production efficiency. By automating the filling process, manufacturers can achieve unprecedented levels of scalability, effortlessly meeting the demands of a rapidly evolving market landscape. Moreover, the machine's ability to deliver consistency and quality at scale empowers manufacturers to
establish themselves as leaders in the industry, driving brand loyalty and market differentiation.
In essence, the pillow filling machine stands as a testament to human innovation and ingenuity, a towering symbol of progress in the pursuit of excellence. As it continues to revolutionize the textile industry, it not only reshapes the way pillows are produced but sets a new standard of efficiency, precision, and quality that will endure for generations to come.
The Fiber Carding Machine: Redefining Textile Production Efficiency
The fiber carding machine stands as a monumental pillar in the realm of textile manufacturing, revolutionizing the way raw fibers are processed and transformed into usable materials. This colossal piece of industrial equipment epitomizes innovation, efficiency, and precision, reshaping the very fabric of the industry.
At its core, the polyester fiber carding machine embodies a fusion of cutting-edge engineering and meticulous craftsmanship. Its intricate design comprises a series of precisely calibrated rollers, cylinders, and wire brushes, meticulously arranged to perform a singular task: to align, separate, and clean raw fibers with unparalleled accuracy and speed.
The operation of the fiber carding machine is nothing short of mesmerizing. As raw fibers are fed into the machine's hopper, they embark on a journey through a labyrinth of rotating cylinders and rollers. With each pass, the fibers undergo a transformation, as the machine gently teases them apart, aligns them into a uniform web, and removes any impurities or irregularities.
But it is not merely the efficiency of the fiber carding machine that sets it apart; it is also its capacity for versatility. From natural fibers such as cotton and wool to synthetic materials like polyester and nylon, this machine can process a vast array of raw materials with equal precision and efficacy. This versatility empowers textile manufacturers to explore new materials, experiment with innovative blends, and push the boundaries of creativity and design.
The advantages of employing a polyester fiber carding machine are manifold. Firstly, it dramatically enhances production efficiency, allowing manufacturers to process large volumes of raw fibers in a fraction of the time required by traditional methods. This not only reduces labor costs but also increases overall productivity, enabling companies to meet growing demand and stay ahead of the competition.
Moreover, the fiber carding machine ensures a level of consistency and quality that is virtually impossible to achieve through manual processing. By aligning fibers with pinpoint accuracy and removing impurities, it creates a uniform web that serves as the foundation for high-quality textiles and finished products. This consistency not only enhances product performance but also enhances customer satisfaction and brand reputation.
In conclusion, the fiber carding machine is more than just a piece of equipment; it is a symbol of innovation and progress in the textile industry. With its unparalleled efficiency, precision, and versatility, it is reshaping the way raw fibers are transformed into textiles, paving the way for a future defined by excellence and ingenuity.