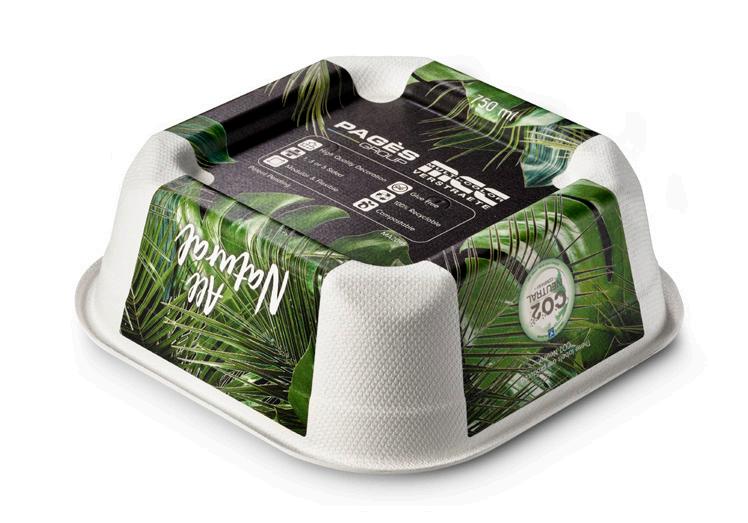
9 minute read
Sustainability Built Into Every Fiber
Innovation Sustainability Built Into Every Fiber
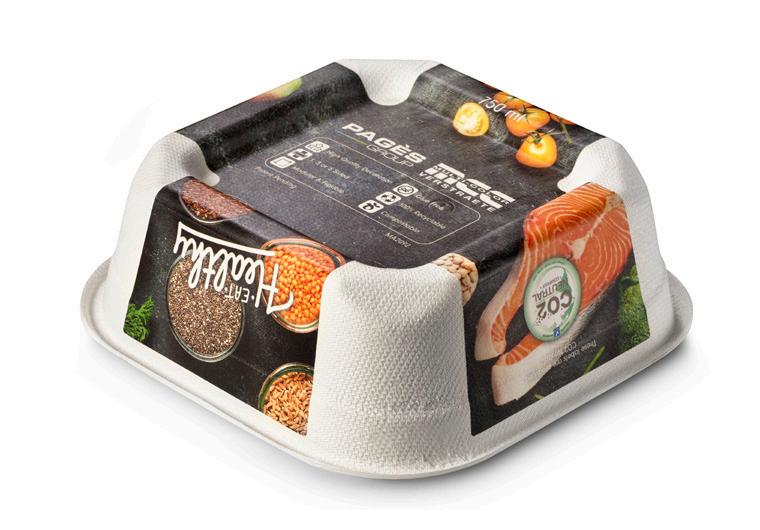
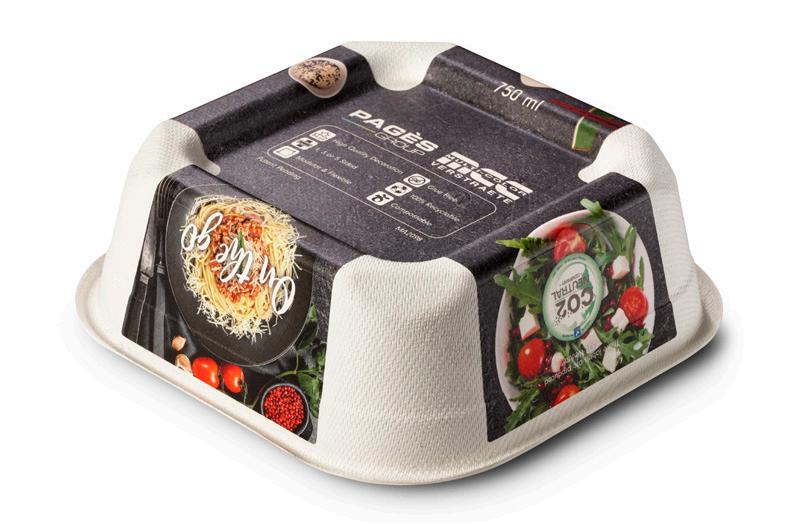
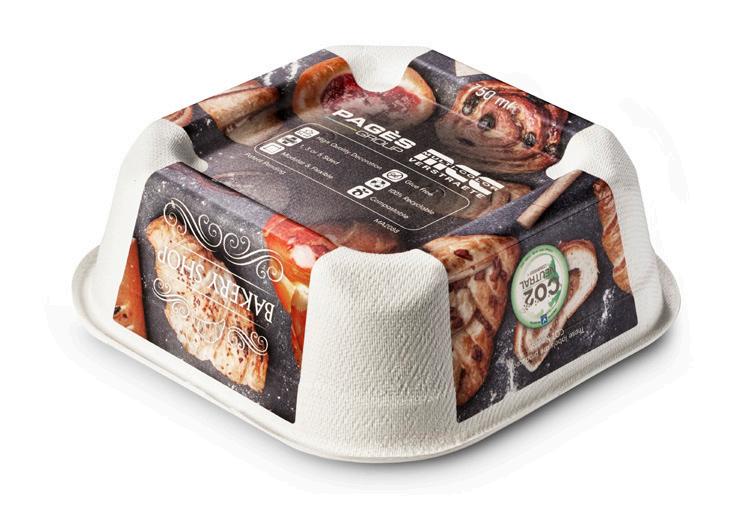
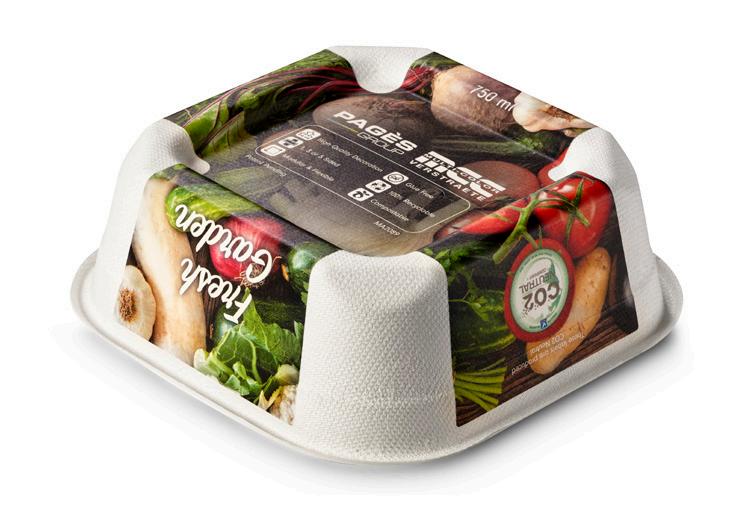
As Molded Fiber Labeling™ (MFL) – a new breakthrough technology for the ultimate in sustainable packaging – prepares to hit the market, we talk to some partners involved in this trailblazing project.
What is your company’s role in the project?
Sanna Fager: PulPac has invented Dry Molded Fiber, a manufacturing method of cellulose molding for producing low-cost, high-performance fiber-based packaging and single-use items. Sanna Fager Chief Commercial Officer This groundbreaking technology at PulPac forms the basis for the MFL™ project. We license it to packaging manufacturer partners, in this case Hébert Group. They set up their own production in cooperation with specialized machine suppliers, and develop applications for their customer. Romain Hervé: We have seen rapid growth in the molded fiber packaging market, and it is an area that we are investing a lot of time and effort in, with new patented decoration technology. Our modular MFL™ machine platform can be configured from a single station for prototyping or pre-production to a full system with multiple stations for high volume production, either as standalone or in-line with the forming machine. The technology ensures perfect fusing of the MFL™ labels to the product surface and is flexible enough to handle many different shapes on the same line. Julien Hébert: Hébert Group introduced the In-Mold-Labeling process early in the 80’s. 40 years later, our team is thrilled to again play a pioneering role by joining forces with our historical partners, Pagès Group and MCC Verstraete, to leverage the full potential of the dry molding technology owned by Pulpac. Through Herpulp, a new and dedicated business unit, we have worked closely with PulPac and are now in the process of setting-up the new PU300 Modula platform for Dry Fiber Molding. It will be combined with an automated Molded Fiber Labeling™ machine from Pagès Group which will apply the printed MFL™ labels from MCC Verstraete, as we ramp up with a full production line to manufacture 100% fiber-based packaging solutions for our customers. Nico Van de Walle: MCC Verstraete has used its unrivaled IML experience and expertise to develop unique paper-based MFL™ labels that can be used to decorate both wet and dry molded fiber packaging. MFL™ labels enable strong fusion with the fiber molded packaging without the use of adhesives, and we print them offset with high resolution graphics to deliver packaging with exceptional shelf standout.
What are the main advantages of MFL™?
Sanna: Brands and consumers want greener options with great look and feel, but they don’t necessarily want to pay extra for them. As PulPac’s Dry Molded Fiber technology is up to 10 times faster than traditional fiber forming methods and makes it possible to fuse the MFL™ label to the product inline in one sequence. Overall, there are some highly competitive economics in the mix, in addition to the crucial sustainability aspect.
Romain: MFL™ offers a winning combination of highquality printing, sustainability, and competitiveness, which will answer many brands’ demands for greener solutions. This world premiere automated solution allows you to decorate fiber molded containers for stunning looking packaging that brand owners will be proud to put on shelf.
Julien: Maximum print quality, recyclability, quick design changeovers and cost efficiency are among the key benefits of the IML technology that is today well established within the plastic industry. And this will be no different with MFL™. Combining each party know-how and technological edge will enable the emergence of MFL™ as a technically new and truly competitive way to decorate paper-based solution that meets both market expectations and environmental regulations.
Nico: Because the packaging with the glue-free MFL™ label consist of compatible fiber materials, the whole pack can be recycled or composted as one unit. The MFL™ labels are able to resist humidity and big temperature fluctuations, making them suitable for all types of food applications, including chilled and frozen. They adhere perfectly to the fiber material, so they are not susceptible to creasing or air bubbles.
How does it compare to other solutions?
Sanna: When focusing on the molding process, our unique and patented technology is based on a dry process. Besides saving significant amounts of water and energy, CO2 emissions are up to 80% lower than
Who is PulPac?
PulPac is based in Sweden, and developes sustainable and cost-effective alternatives to single-use plastics. More precisely, the company is pioneering cellulose molding to help accelerate the global shift away from plastic containers and other plastic products. Their vision is to replace more than 1 million tons of plastics by 2025, that’s around 1% of annual packaging production.
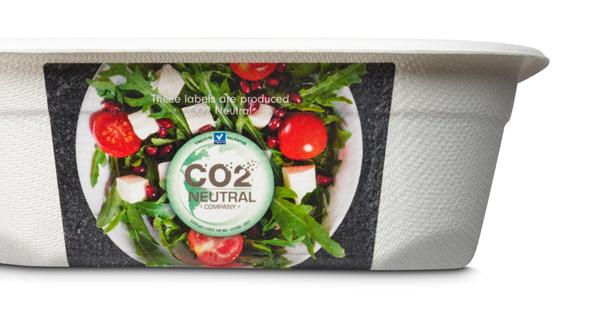
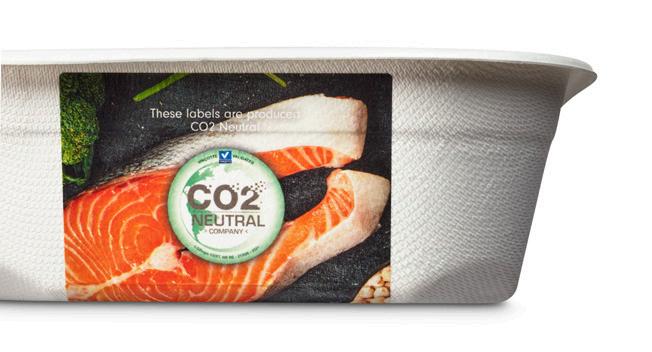
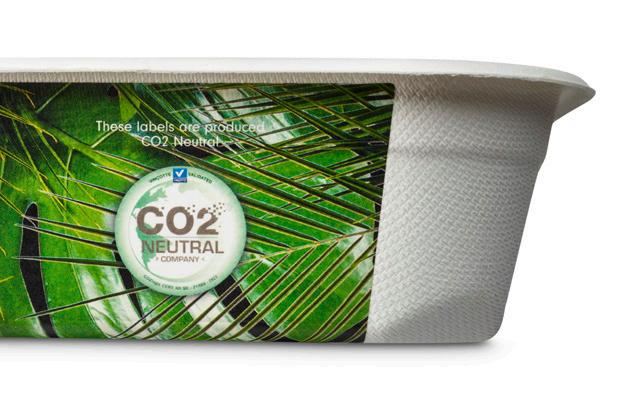
alternatives. In addition, output is up to 10 times faster and matches conventional packs, resulting in very competitive unit economics. That enables replacement of single-use plastics at scale.
Romain: In terms of decoration methods, alternatives would be either direct to object (inkjet) printing or applying self-adhesive labels, which can present problems in regard to print quality, speed of production and sustainability of the packs. Direct to object does not offer the high quality of offset printed IML, and if you introduce adhesive into the construction, the compostability and recyclability are negatively affected.
Julien: Our aim is to offer to the market products that are decoupled from fossil resources and fully recyclable. MFL™ applications can meet both requirements and the fact it is a one-step process makes it more cost effective that many alternatives. We trust that our experience and our technical expertise that have been consolidated through injection molding can now benefit to dry fiber molding, making MFL™ the preferred decoration technique for FMCG companies in the years to come.
Will fiber-based packaging and MFL™ be a success? Sanna: It already is a success, and it is growing fast. In fact, a recent study from Smithers Pira states that by 2040 consumers won’t tolerate a choice between sustainability and convenience, they will expect both
Who is Pagès Group?
Pagès Group is a global innovation leader in machine automation for packaging decoration for the consumer, industrial and medical sectors. The company has provided downstream solutions for the pulp packaging market for many years and has over 30 years of experience in handling in mold labeling, which is their main focus. “ From all the market insights we have gathered, the idea of combining the
Julien Hébert, Technical and Sales Director at Hébert Group
– and that fiber-based packaging will be perceived as the most sustainable solution. We are working with many different partners who share our holistic view on sustainability and efficient use of resources. The end goal is to establish Dry Molded Fiber as a new world standard for fiber-based packaging.
Romain: The reaction from the market is a clear sign that there is an appetite for decorated fiberbased packaging. We have made a fantastic start with MFL™ and are now working on the next level, such as handling and labelling round shapes. We have already made a prototype for round packs and is now building the pilot line. The demand is certainly there, so we continue to innovate in this space.
Julien: The development and the manufacturing of bespoke solutions is our core business. From all the market insights we have gathered, the idea of combining the IML technology with the dry molded fiber one is a promising answer to address some key expectations in terms of sustainability. We believe
Romain Hervé
Business Development Director at Pagès Group
Who is Hébert Group?
Hébert Group is a family-owned company based in France with an expertise in the development and the manufacturing of tailored packaging solutions for the food and cosmetic markets. The company has been supporting key FMCG companies in the large-scale industrialization of some of the most iconic designs in the packaging industry. While injection molding is Herplast specialty, Herpulp has been launched in 2022 and focuses on the molding of fiber-based items. Herplast and Herpulp will operate as two complementary business units.
that our new development has a strong future as it contributes to the circular economy while still being a high quality and cost-effective solution.
Nico: Although I’m also a strong believer in sustainable plastic IML packaging, being sustainable in its own right when recycled responsibly, I do also see a bright future for molded fiber MFL™ packaging. This is mainly driven by the EU single-use plastics directive and by the quest brand owners have to reduce the amount of plastic packaging material they use. Our vision is that the final packaging, decorated with one of our labels, no matter if it’s IML or MFL™ , should stay at all time, recyclable, reusable or compostable. In this spirit and supported with over 30 years of experience in IML, we believe in a bright future for both IML and MFL™ packaging.
Is there scope to take the MFL™ project global?
Sanna: PulPac has aimed to be global from start. Our technology is patented worldwide and made available to converters through licensing to accelerate global spread and make impact at scale. By collaborating with the industry, we can help transform it from within – in just a few years. We are building a community for Dry Molded Fiber, a global value chain of industry leaders within application development, tooling, material, barriers, machinery and know-how, supporting the converters who make the shift. A shift that in the end will help save our planet from plastics.
Romain: Pagès Group operates worldwide and has over 3000+ systems in the market for various industries. We export to over 45 countries and have experts in place globally, meaning we can support local customers no matters where they are based if they want to explore the opportunities in Molded Fiber Labeling™. Nico: MCC Verstraete is part of the global MCC Group and we have four local production units and technical support from five locations around the globe. Having that worldwide presence allows us to respond faster as we don’t have to rely heavily on fragile supply chains. In this instance, it means the MFL™ project can be implemented in other parts of the world, because we can supply labels quickly.
Nico Van de Walle
Product & Circular Economy Manager at MCC Verstraete
How was the experience of working with MCC Verstraete?
Sanna: For this project to be a success, we needed an expert who was willing to push the boundaries of IML technology. MCC Verstraete has been integral to developing MFL™, and they have been very flexible and open to work with.
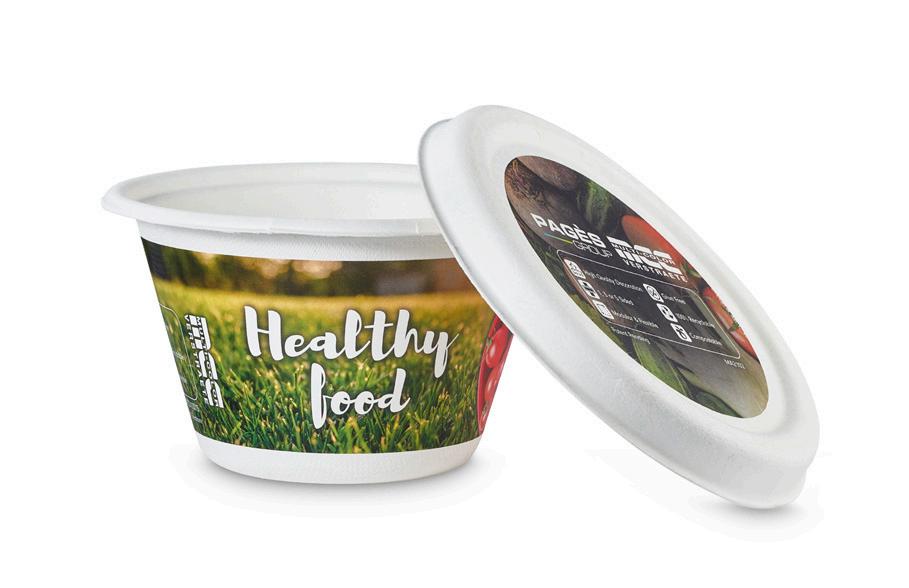
Romain: It was a great collaboration. MCC Verstraete is definitely a very responsive partner, which was crucial for the project to succeed. They were able to deliver new materials for testing on our line very quickly and their technical support was key in the development of the label handling and application.
Julien: Like ourselves, MCC Verstraete has been active in IML since the very beginning, so there is a great synergy and understanding between our companies. This has been very evident throughout the MFL™ project and will be in the future, I’m convinced.