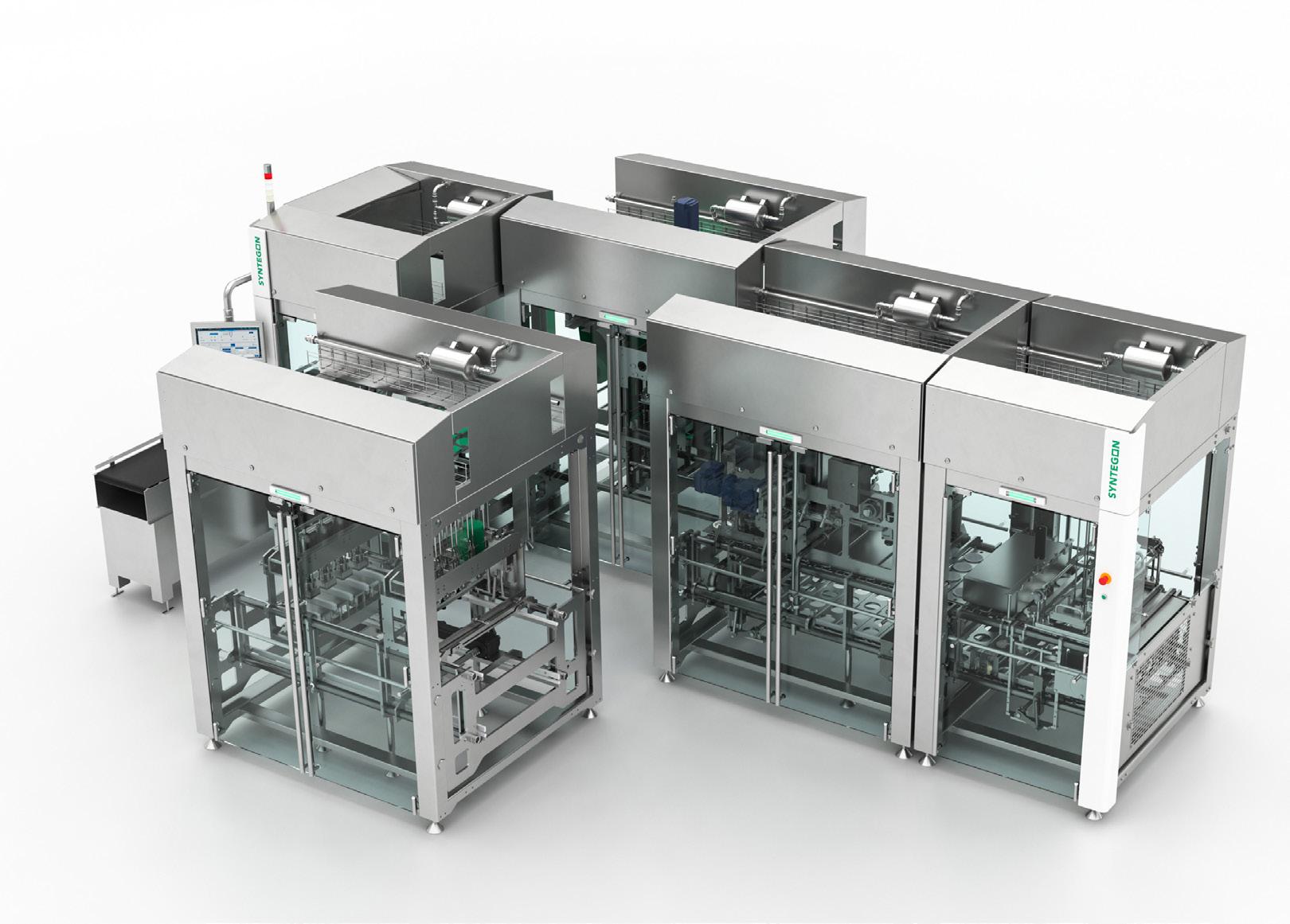
7 minute read
Testimonial Syntegon: Creating sustainable packaging with SealPPeel
Interview Creating sustainable packaging with SealPPeel
Interview with Machinery Manufacturer Syntegon
Syntegon has implemented MCC Verstraete’s SealPPeel die-cut lidding solution on its new LFS filling machines for preformed cups for dairy and other liquid foods. Here, Ilona Junkers, Project Manager for Sustainable Solutions at Syntegon, and Stijn Quintyn, Product Manager for SealPPeel at MCC Verstraete, discuss this innovative project.
What is Syntegon’s vision for sustainable packaging?
Ilona Junkers: Syntegon’s aim is to provide intelligent and sustainable solutions for everyone. We deliver packaging technology that can process eco-friendly materials such as mono-material, paper or biodegradables, bioplastic and other biobased solutions. We focus on minimizing Ilona Junkers resource consumption across the Project Manager for Sustainable board, both for the end application Solutions at Syntegon and in the machines we build. We support customers on their sustainability journey – from design and initial material testing to final machine application and beyond, so they can meet requirements and regulations in the different regions.
What are the main packaging drivers in the dairy industry?
Ilona: There are four main drivers in the dairy packaging industry. First of all, of course costs, because dairy is a very price-sensitive market, so customers are highly conscious of margins and productivity. This is closely connected with the second driver, which is machine efficiency. A third driver is consumer behavior. If the consumer likes the packaging solution, our customers sell more products. We work with them to optimize opportunities. Finally, sustainability, especially if it means that consumers will buy more of the product because of a sustainable look, touch and feel or because it is a real sustainable solution. Stijn Quintyn: By 2025, we should see the impact of Modulated Extended Producer Responsibility (EPR), which will hold the producer accountable for the entire lifecycle of the product, meaning some packaging could be taxed higher or other lower. Do you think this will help in the push towards more real sustainable options instead of greenwashing? Ilona: Yes, regulations are also a driver. If the price increases for unsustainable solutions, total cost of ownership (TCO) will be in favor of more environmentally friendly options.
Could you explain the aim of the project?
Ilona: The aim of the project is to produce a fully recyclable mono-material solution for liquid and viscous foods. Working closely with MCC Verstraete, we set out to create a packaging structure that the consumer can recycle without first having to separate the cup and the lid. By specifying SealPPeel polypropylene (PP) heat seal die-cut lids in combination with PP plastic tubs on our newly launched LFS and FCL UC filling machine, I’m pleased to say that we have achieved our goal and that the new solution is now in the market. With SealPPeel on our new LFS, FCL UC lines and retrofit able old EVO machines, we can now offer a fully recyclable packaging solution as an alternative to aluminum lidding. Stijn: Of course, a lot of the IML labels we produce at MCC Verstraete already end up on a Syntegon filling line at the converter, but now with SealPPeel, our recyclable PP lids for cups are part of the solution applied on Syntegon lines directly. This means the filler is ready to go with a sustainable packaging, and which is more economical, compared to aluminum lidding.
And how was it accomplished?
Ilona: I would say it is the combination of our two innovations that has made this project a great success. Our new LFS and FCL UC filling machine concept, which has been designed for a wide variety of liquid and viscous products for clean and ultra-clean applications works well with the SealPPeel lids and that has opened up a much wider market.
Initially, we sent the construction for evaluation with several recycling companies and it came back with top scores, so that gave us the impetus and also the focus to look into this innovative packaging material.
What are the main advantages of SealPPeel?
Ilona: First of all, the look of the SealPPeel lids themselves. The feedback from our marketing team was incredibly positive, they thought the solution was excellent with great branding opportunities. We love the fact that they can be printed in offset quality without affecting the performance.
Secondly, the silicone sealing technique is very efficient on the production line, and it has good peel force, which is also a crucial part of the innovation. The seal performs much better than other PP mono-material
Ilona Junkers, Project Manager for sustainable solutions at Syntegon
Stijn Quintyn
Product Manager SealPPeel at MCC Verstraete
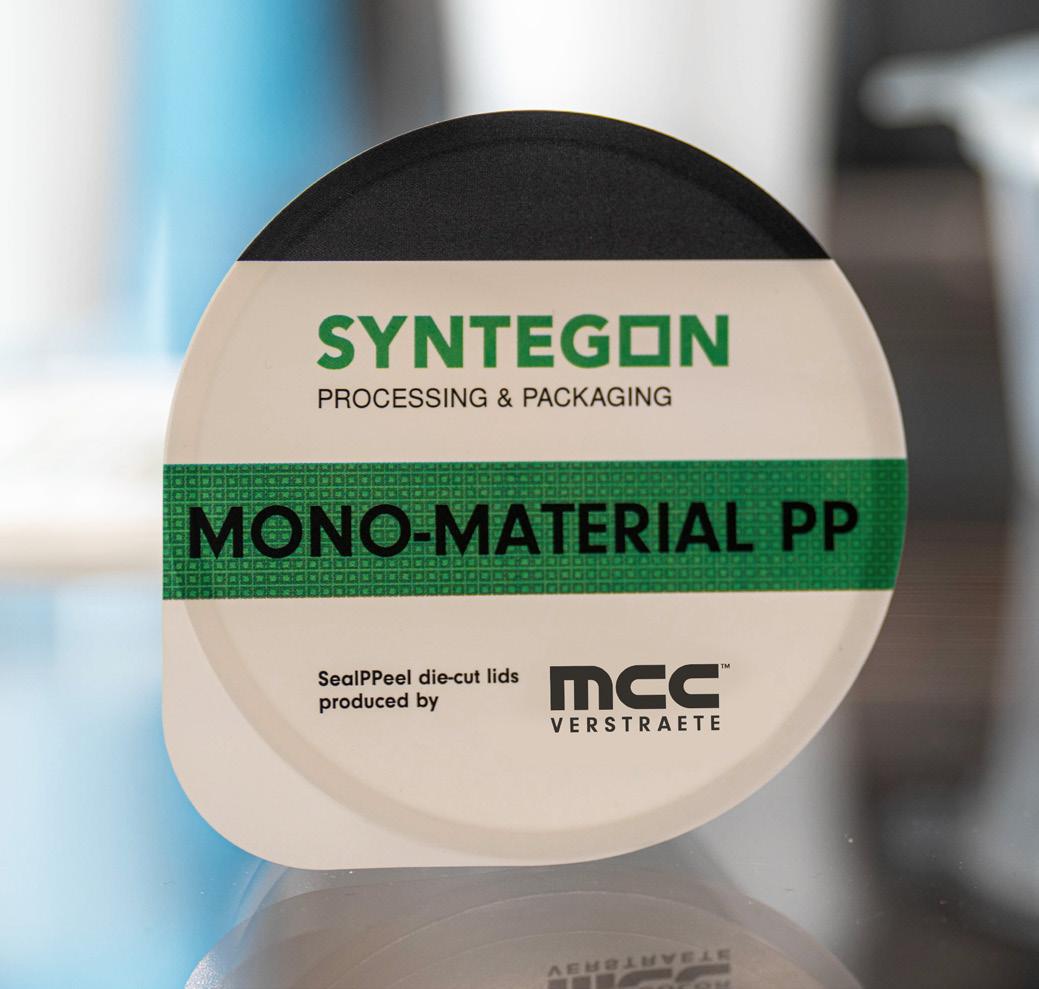
solutions we have investigated, and that benefits consumers directly because of the convenience.
It is very important for us as a machine supplier that we can give our customers the security that if they change from aluminium to PP. The product security is not compromised, and the shelf life is not affected for the products we have produced so far with the new PP lid solution. We have achieved that with this project.
How do you see the future of SealPPeel?
Ilona: I think the future is very bright for SealPPeel because it can help alleviate problems with supply of aluminum – we see a shortage worldwide. As a mono-material solution, it will also enable brands to better comply with existing and new regulations regarding the circular economy. I have no doubt that we will see a growing demand.
There is also a big opportunity for our customers to use the solution in more market segments. The LFS filling machine is suitable for many other products in addition to dairy, such as deli foods, on-the-go and plant-based foods, dips, sauces, soups, etc. With SealPPeel die-cut lids on the machine, we can now address all those markets with a sustainable solution.
Why did Syntegon choose to work with MCC Verstraete?
Ilona: We worked with MCC Verstraete because the company is well known for its IML technique, so we knew the team is experienced in handling PP, which can be a very difficult material to process.
The cooperation during the development has been very close with great communication at every step. Our discussions around what we wanted to accomplish and what was feasible were very productive and we did a lot of testing to come up with the optimal product. Now that SealPPeel is on the market, we continue the close cooperation, especially when dealing with customer queries and new requests.
Is it a benefit that both companies operate globally?
Ilona: Yes, it’s a major benefit for our customers that we are both global players, because they know that we can supply machines and materials locally. For instance, in the US where we expect more growth, we have Osgood Industries in Florida producing machines as a part of Syntegon.
Stijn: For MCC Verstraete it is also a very big benefit, because when you start a SealPPeel project, the partners involved need to work as a trinity with the filler, who needs a lot of information, the filling line manufacturer, so Syntegon in this case, and ourselves, as the lidding producer. Those three parties have to work together very closely, so if they all work in an international context that makes the rollout smoother.
And will there be more joint projects?
Ilona: I certainly think so, because there are so many great solutions coming to market from MCC Verstraete, such as Molded Fiber Labeling™ (MFL), which is another unique sustainability driven project. There is a lot of innovation happening at MCC that fits really well with our strategy.
Stijn: Our companies share the same vision about what sustainable packaging should look like. We are both firm believers in mono-material packaging, and MCC offers both mono-material PP and mono-material fiber solutions, so I think that combination will for sure lead to more cooperation in the future.
Who is Syntegon?
Syntegon has over 160 years of experience in manufacturing machinery for the global pharmaceutical and food industries. As a partner for processing and packaging technology, the company makes individual machines and automated packaging systems and services as well as setting standards in packaging with innovative and tailor-made solutions for reliable production processes and high-quality results.
Become an IML-expert
• All IML knowledge bundled in one place, available 24/7 • Offering all kinds of tools: whitepapers, educational videos, magazines, ... etc.
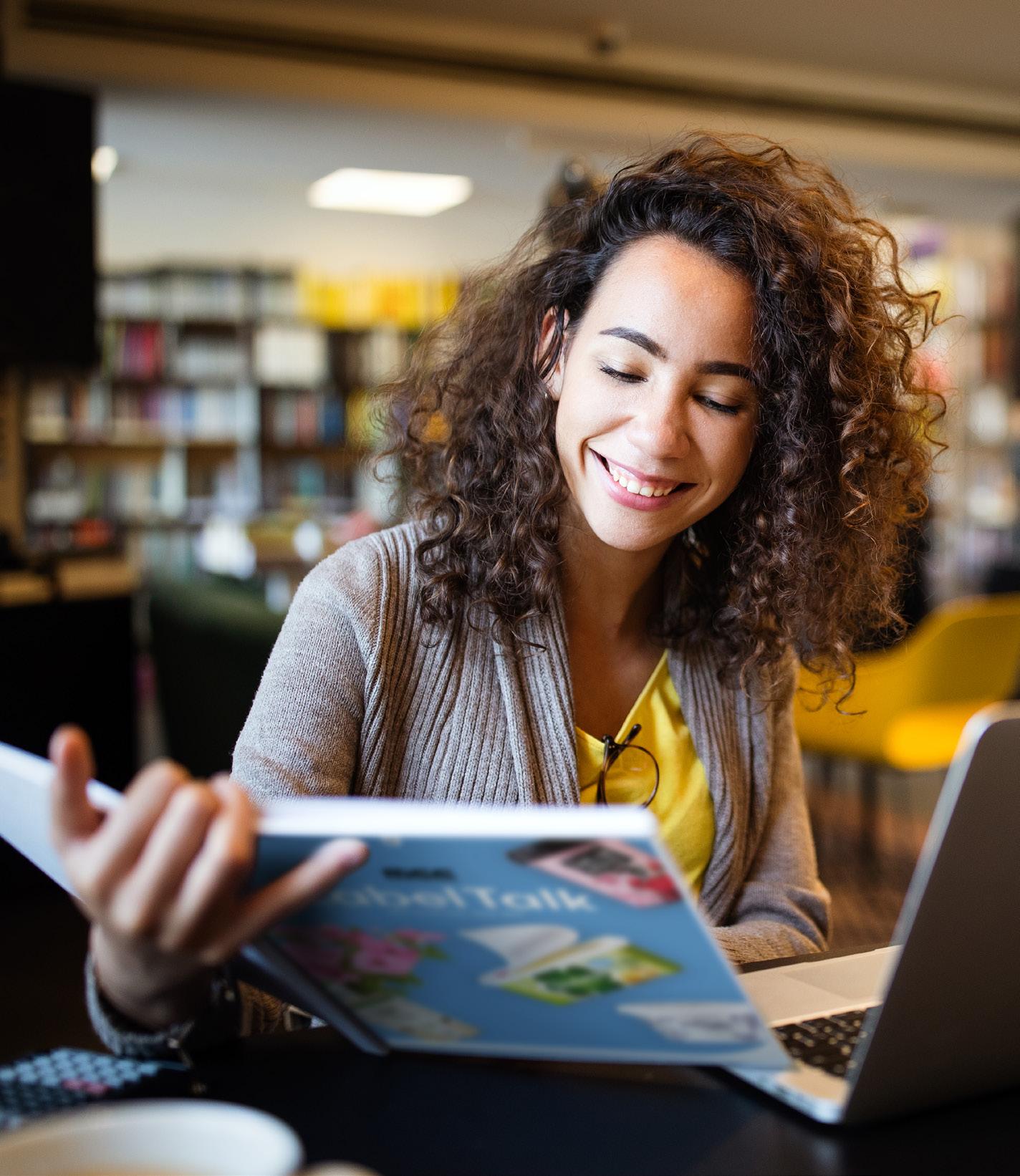