WCM Journey
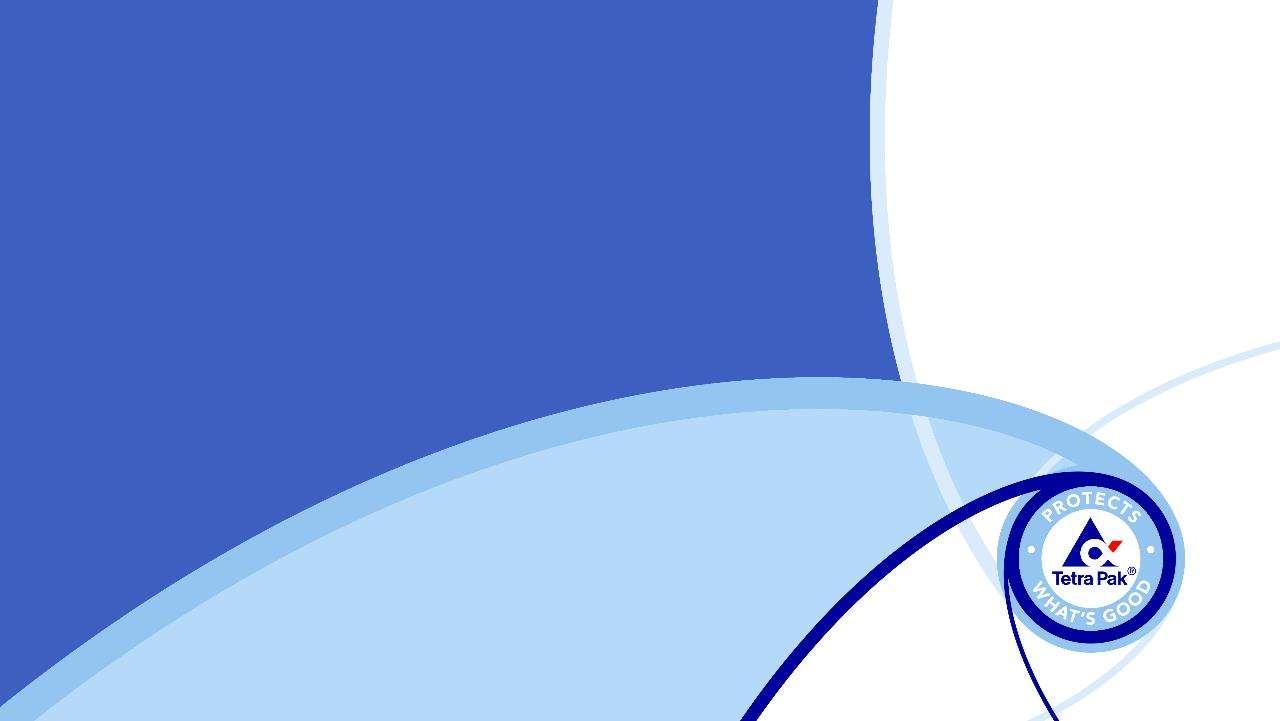
Beograd, Sep 2017
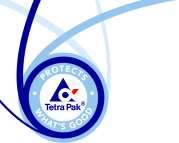
Beograd, Sep 2017
► Svetislav Savic
► WCM & Engineering Manager
► Tetra Pak, Converting Factory Gornji Milanovac
We commit to making food safe and available, everywhere
“A package should save more than it costs”
Converting factories produce printed rolls of packaging material
• a mindset based on a continuous improvement approach
• a systematic approach to achieve maximum organization effectiveness through all employee involvement
WCM has its foundations in the Total Productive Maintenance (TPM) - a maintenance process developed in Japan for improving productivity by making processes more reliable & less wasteful.
TPM started in Tetra Pak – 1999 as WCM Programme
► Top management initiative and support
► Pilot teams in 2 factories
► Investment in time and coaching
Expansion started in other factories 2001 - 2003
► WCM global office established with WCM Champions and Master Pillars
► Extensive training and coaching programme established
Stabilization Phase 2004 – 2009
► WCM Champions moved to Clusters
► Factories start delivering consistent results
Progress and Evolution 2009 – 2014
► Factories delivering breakthrough results
► Teams and factories becoming self driven
► Building on continous improvement to drive innovative solutions
- Zero Defects (Total Quality ) - Zero Breakdowns and unplanned Stops - No touch - JIT
Involvement
Engagement and
Self-fulfillment
► Factory Managers and WCM Managers take on the coaching
► Tackling more losses together
► Benchmarking and sharing between factories
► Expansion in full Supply Chain and Engineering areas
► 2001 - Start of World Class Manufacturing Program – 4 Pillars
► Internal support from advanced Tetra Pak factories
► Big opportunity for the factory to improve and be exposed
► 2 main resources
− People
− Time
► Right implementation of available methodology
► Embraced from top and middle management
► Full involvement of employees
► Empowerment
► Change of mind set of employees
− From individual to team approach
− From receiving to giving and sharing
− From reactive to proactive
− From operator to innovator
► From small factory to standard one
► From outsider to World Class factory
► cross functional team which use specific methodology to achieve defined business objectives (KPI) in a systematic way with total involvement of all members
LOSS ANALYSIS (Deployments, Improvement team launching)
IMPROVEMENT TEAM SUPPORT (Training, Coaching,Auditing)
► “competence centre” supporting the organisation at three levels
► Pillar leaders & WCM Manager & Factory Director – Steering Committee
SYSTEMS DEVELOPMENT (DMS - loss control and loss prevention)
• 30 Kaizen teams each year
• All operators are members of AM teams
Tetra Pak factory in Serbia – World Class Award 2015
First Tetra Pak factory to receive the World Class Award!
Operational Excellence secures the present.
Innovation Excellence secures the future.
Full top management commitment is essential
Willingness to invest time in coaching
Needs involvement at all levels
Does not work overnight – requires persistence
Get the fundamentals right
Things don’t work if they are not simple
Develop and retain WCM talents
Empowered people deliver breakthrough results!
It’s not always easy. Sometimes it’s even painful...but:
It works! It makes the difference! It changes the way you do business!
“If you focus on results, you will never change. If you focus on change, you will get results.”