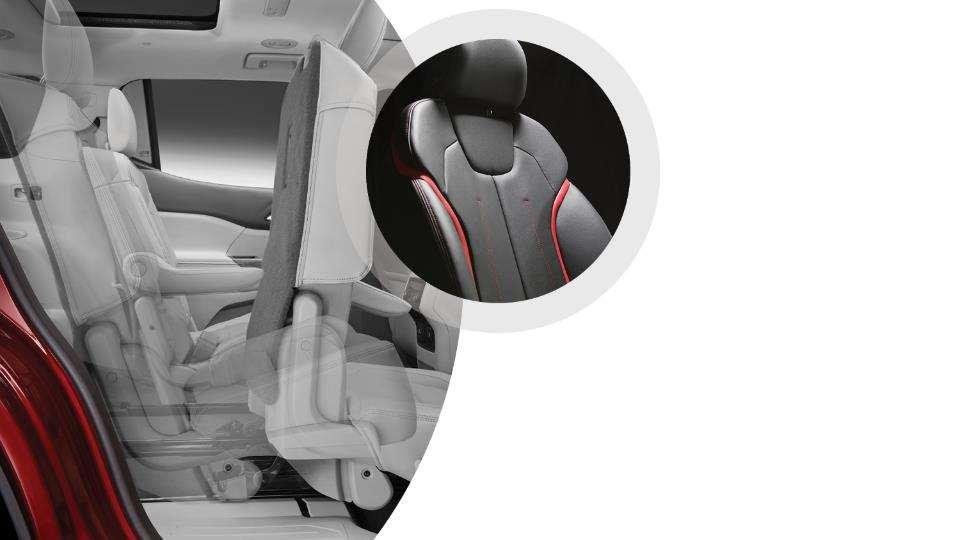
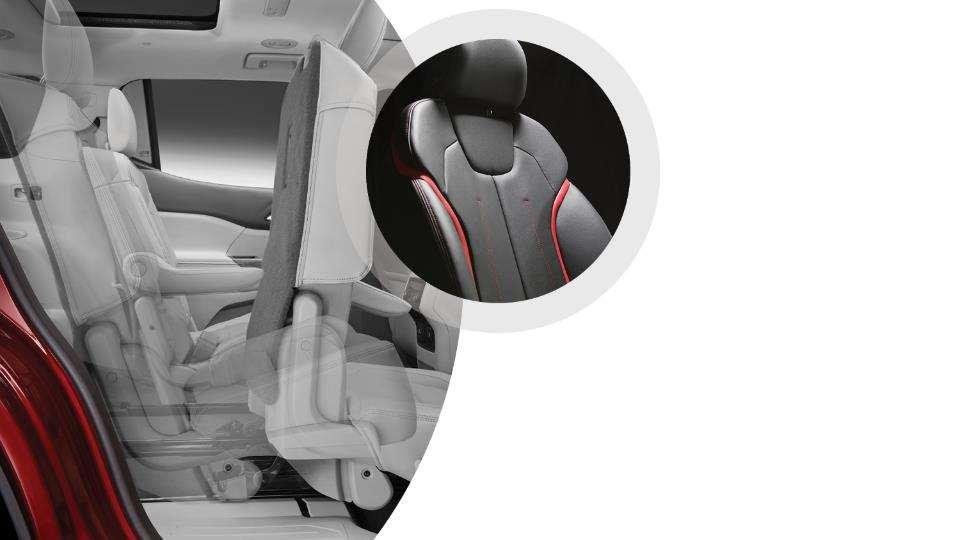
Global Presence
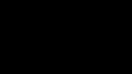
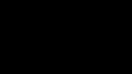
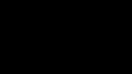
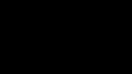
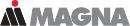
Product Systems
SEATING
Capabilities
• complete seating systems
• seat structures, mechanism & hardware solutions
• specialty mechanism solutions
• foam & trim products
• design & development capabilities
EXTERIORS
Capabilities
• fascia & trim
• liftgate & exterior modules
• front end modules
• active aerodynamics
• lightweight composites
CLOSURES
Capabilities
• latching systems
• door modules
• window systems
• power closure systems
• handle assemblies
• electronics
• engineered glass
• hinges
• wire forming
• sealing & trim
• running boards
• roof racks
• composite products
Global Footprint
• 23,825 employees
• 52 mfg/assy facilities*
• 9 product development/ engineering/ sales centers
*including In Progress Facilities
Global Footprint
• 20,400 employees
• 58 mfg/assy facilities*
• 13 product development/ engineering/ sales centers
*including MinorityJVs
Global Footprint
• 13,300 employees
• 41 mfg/assy facilities*
• 10 product development/ engineering/ sales centers*
*including MinorityJVs
VISION SYSTEMS
Capabilities
• interior mirrors
• exterior mirrors
• actuators
• door handles
• headlamps
• tail lamps
• small lighting
Global Footprint
• 9,650 employees
• 27 mfg/assy facilities
• 8 product development/ engineering/ sales centers
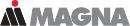
ROOF SYSTEMS
Capabilities
• soft tops
• retractable hard tops
• textile folding roofs
• modular roofs
Global Footprint
• 2,050 employees
• 6 mfg/assy facilities
• 4 product development/ engineering/ sales centers
Product Systems
BODY & CHASSIS
Capabilities
• body systems
• chassis systems
• technology, engineering & tooling systems
POWERTRAIN
Capabilities
• GETRAG transmissions
• driveline systems
• fluid pressure & controls
• metal-forming solutions
• advanced engineering
ELECTRONICS
Capabilities
• automated driving systems
• secure connectivity
• electrification
Global Footprint
• 44,450 employees
• 93 mfg/assy facilities*
• 21 product development/ engineering/ sales centers
* including MinorityJVs & In Progress Facilities
Global Footprint
• 32,275 employees
• 54 mfg/assy facilities
• 30 product development/ engineering/ sales centers
Global Footprint
• 1,925 employees
• 6 mfg/assy facilities
• 11 product development/ engineering/ sales centers
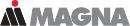
VEHICLE ENG & CONTRACTMFG FUELSYSTEMS
Capabilities
• engineering services – from systems and modules to complete vehicle development
• contract manufacturing – world class flexible solutions from niche to volume production
• fuel systems – energy storage systems made of steel, plastic and aluminum
Global Footprint
• 11,700 employees
• 16 mfg/assy facilities
• 29 product development/ engineering/ sales centers
Global Presence
$36.4 Billion 2016SALES
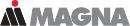
161,000 EMPLOYEES
MANUFACTURING MARKETPOSITION
327 global sites
#1NorthAmerica #3 Globally
Magna Seating Global Presence
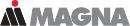
Magna Seating Odžaci

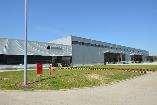

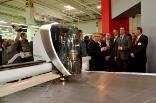

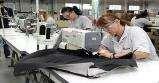
Foundation of MAGNA ODŽACI TRIM PLANT : April 2012
Start of production : October 2013
Space (Production) : 10.103m2 (7.143m2)) , from extension in 2017.
No. of employees : 1288 (September 2017)
• Products
– Cutting and sewing of covers for premium passenger cars and light commercial vehicles
• Capabilities
– Trim covers production (cutting & sewing)
• Technology
– CNC Cutting – fabric, vinyl, sponge
– Standard sewing machines
– Side Airbag machines
– Multi needle machines
• Certified ISO/TS 16949
ISO 14001 EMS
ISO 18001 OHSAS
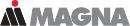
• Projects

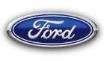

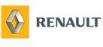

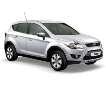

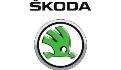

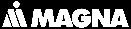
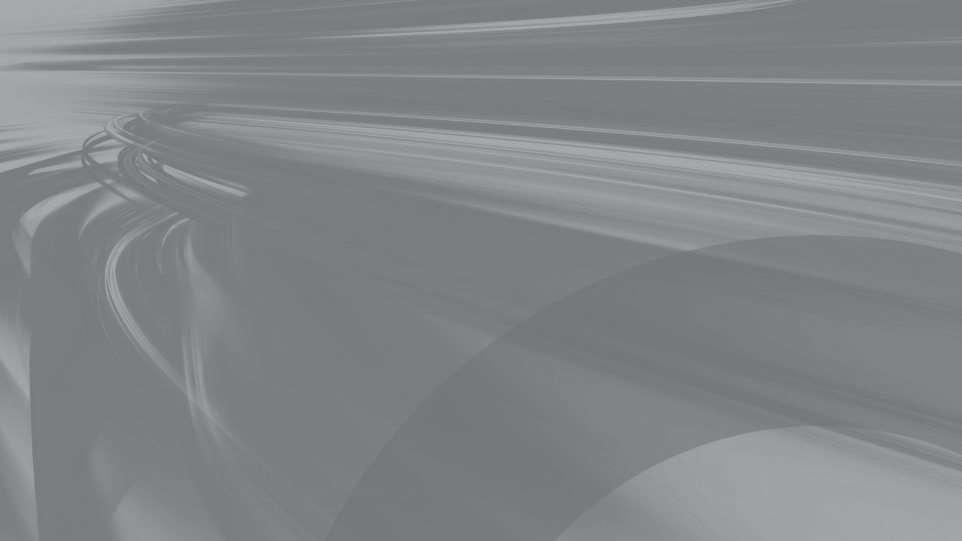
MAGNA Lean concept MAFACT
- Magna Factory Concept
MAFACT - Introduction
• Mafact = Magna Factory Concept
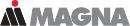
• The purpose of Mafact is to create a common, but unique factory concept for all Magna Divisions globally, where common operating principles are employed to achieve our goal to be world class manufacturers.
• This will enable us to satisfy our Customers, to generate healthy profit margins and to provide employees with a better place to work.
• Mafact makes use of continuous improvement in all our processes to eliminate the 7 types of waste. This is accomplished through the efforts of dedicated teams of capable individuals that are supported by our Leadership teams.
MAFACT - Introduction
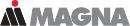
All of our Divisions must reflect the same World Class image and performance to our Customers, Employees and Shareholders. As a minimum, this means that
– each plant should reflect clean, organized work areas,
– with good visual controls at all times. Production targets should be visual with ongoing monitoring of outputs to targets.
– People should be well-trained in their responsibilities and in charge of the operation,
– performing work in a standardized way and everything from product development through purchased components, to the shipping of finished product, should be well controlled.
In essence, each plant should have similar systems in place in order to achieve this.
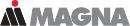
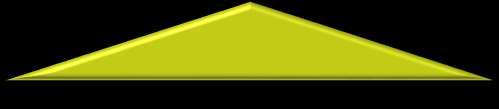
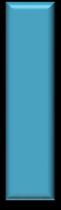
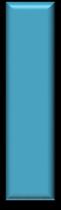
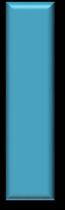
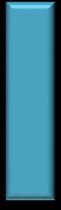
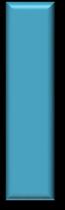
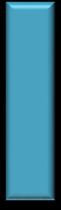
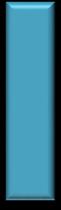
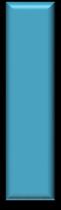
What Mafact Covers
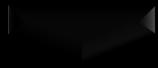
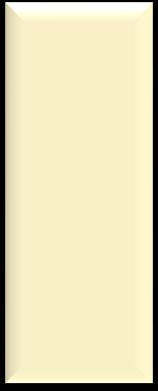
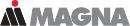
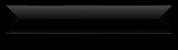




APQP
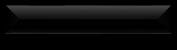
Expectations MAFACT Pillars Objectives Tools and Methods
• Safe Workplace
• Cleanliness and Organization
• Ergonomics
• Environmental Awareness & Compliance
• PreventiveQuality Management
• Effective Problem Solving
• Scrap Reduction
• Supplier Management
• WarrantyReduction
• Reduction of Waste
• Standardized Work / Consistent Set-Ups
• Line Balancing
• QualifiedEmployees
• EfficientProcesses
• EffectiveMaintenance
• Continues Improvement
• Good Material Flow
• Material Identification
• Optimal Stock Rotation
• OptimizedInventoryManagement
• Production Scheduling
• ControllingChanges
• Keeping Records Up-to-Date
• Planning for Product & Process Design
• Meet Business Plan Targets
• ControllingCritical KPI
• Establish Communications& Reporting
• Top ManagementInvolvement
• Openness to Ideas and Suggestions
• ControllingCost
• Tracking Cost Savings
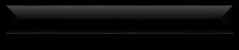
• Safety Mindset
• Personal Protective Equipment
• 5S Methods
• Visualization and Identification
• Ergo Risk Assessments and Actions
• Environmental Systems
• Incident / PPM Tracking (KPI)
• Zero Defect / Fast Response Board
• A3 Problem SolvingMethodology,Quality Tools and Six Sigma
• Scrap Monitoring(KPI)
• Supplier Incident / PPM Tracking (KPI)
• Warranty& Cost Monitoring (KPI)
• 7 Types Of Waste
• Standardized Work Recording / CombinationTable and Chart
• Line Leveling
• On the Job Trainingin Production Processes & Problem Solving
• TPM
• OEE
• Ongoing Continues Improvement& Problem Solving
• Material Movement– Quantities and Frequencies
• Labeling and FIFO
• Min/Max InventoryLevels/ Supermarkets
• Line Supply
• Pull System / Kanban
• DFSS
• FMEA
• Effective Project Management
• Lessons Learned / Benchmarking
• Effective Change Management
• Record Keeping
• Business Planning
• KPI Monitoring& Actions
• Contol & Information Boards
• Daily Operations Meetings
• Process Audits
• MAFACT Approach
• Bill Of Material Reviews
• MCRP
• Cost Of Quality KPI Monitoring
• Purchasing / Engineering / Continues ImprovementCost SavingsKPI
• Recruiting Process
• QualifiedEmployees
• Motivated Employees
• Good Communication& Information
• Employee Leadership Balance
• Employee Involvement
• Trainingfor all Employees
• Employee Performance Appraisals / Employee Opinion Surveys
• Employee Information Systems
• Leadership Methods
• Employee Involvement/ Reward and Recognition
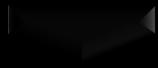





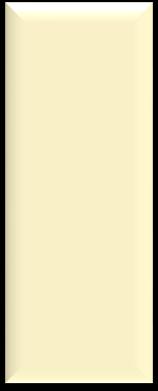
Magna Industry 4.0 - Initiatives
• World Class Manufacturing as one of Magna’s “Top 3 Initiatives”
• Magna implemented the Global Initiative “Agenda 2025”
– High Level Management involvement
– Grouped by Functionality (JIT, Trim, Metals, …)
– Working Levels with individual Tasks
• Magna Seating in liaison with by Magna Steyr regards “Smart Factory”
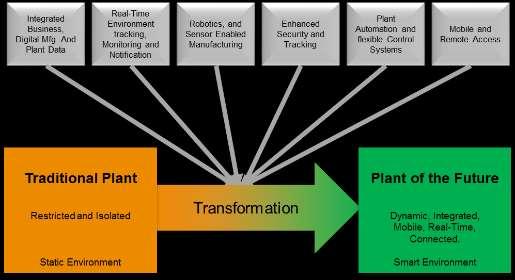
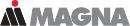
Magna Industry 4.0 - Current Status

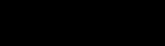
Product Design and Development
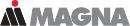
Process Design and Development

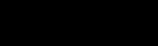



Serial Production
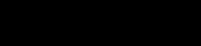
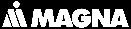
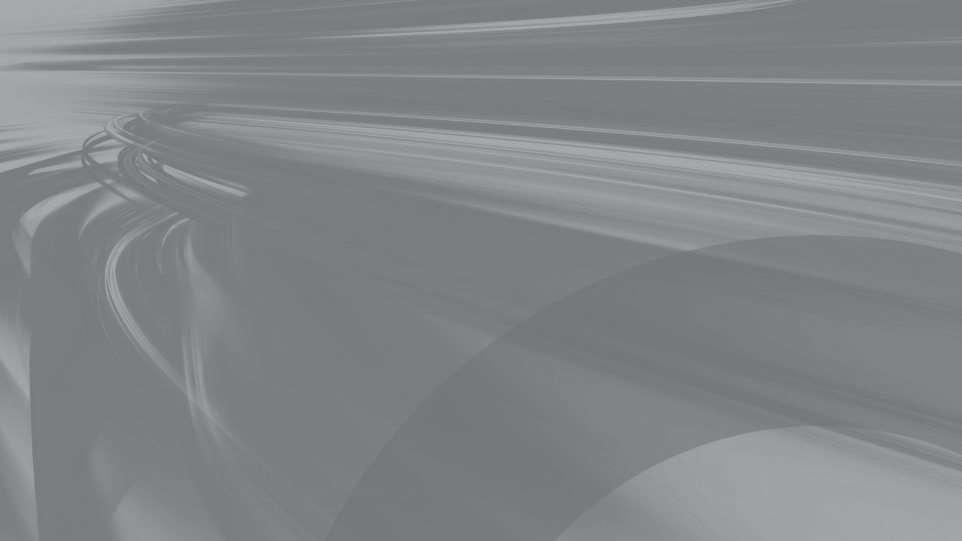
MAGNA ODŽACI
Continuous Improvement
7 Types of Waste
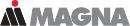
• Waste is anything in the process that is non value added (ie what the customer doesn’t pay for).
• Walking, moving parts, unpacking, reworking, waiting, correcting, scanning.
• In general, lean mfg identifies 7 types of waste (plus 1).
• State some examples of value added, non value added work and waste!

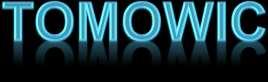
TOP KAIZENS – BROKEN SEAM
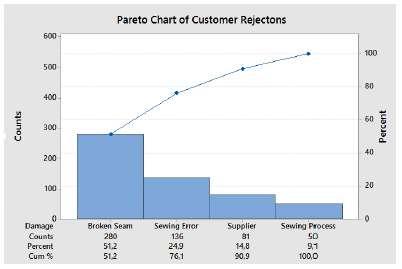
Critical X 1
Critical X 2
Critical X 3
Critical X 4
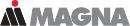
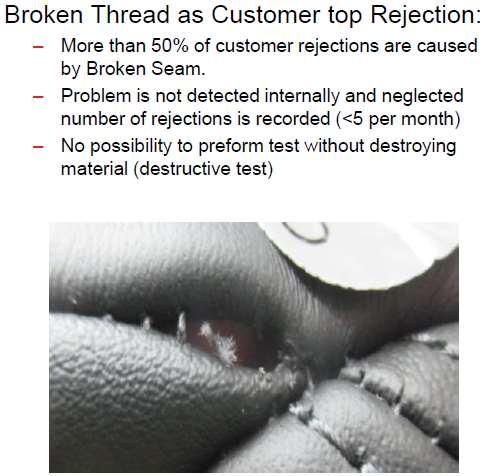
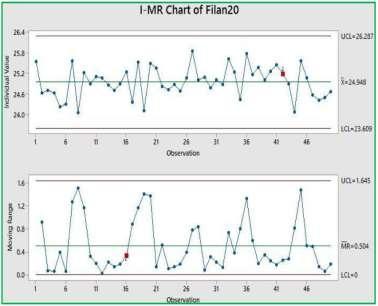

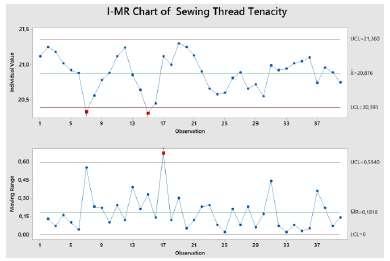
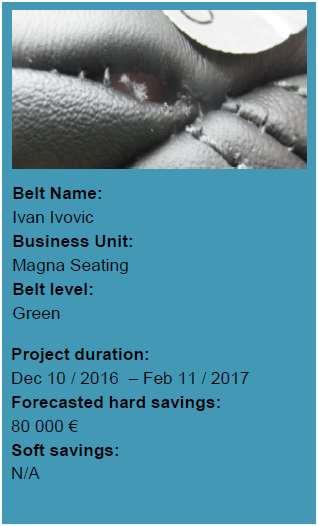
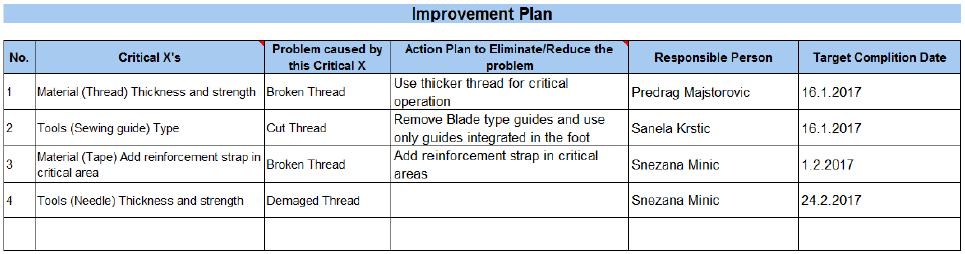
TOP KAIZENS – PRODUCTION BACKLOG
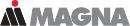
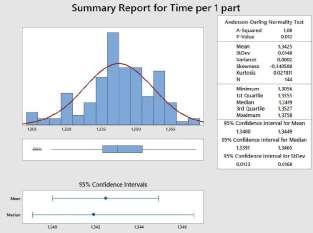
Critical X 1
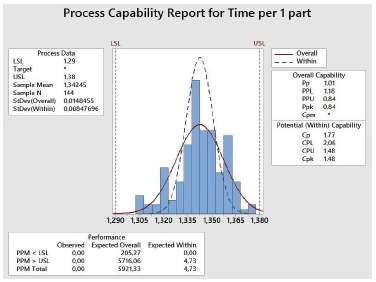
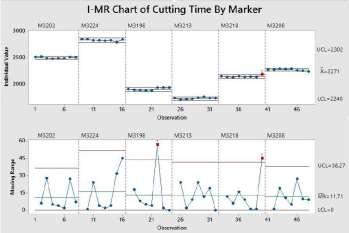
Critical X 2
Critical X 3
Critical X 4
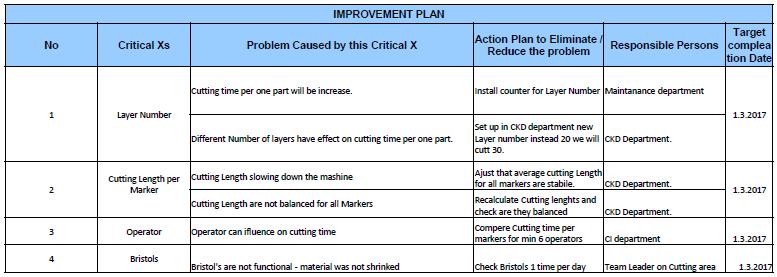

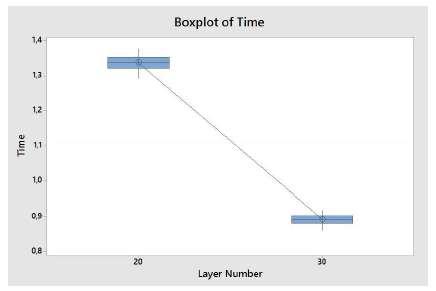
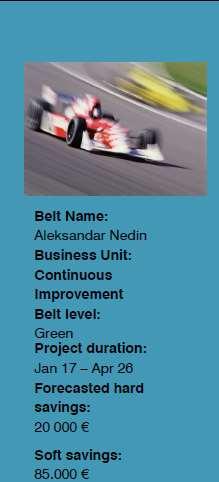
TOP KAIZENS – INVENTORY DISCREPANCIES
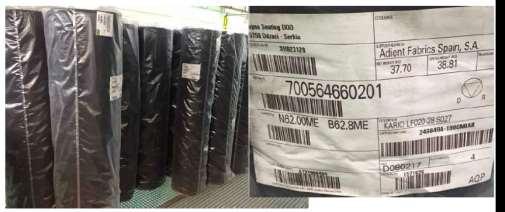

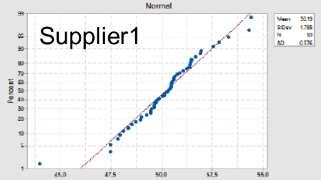
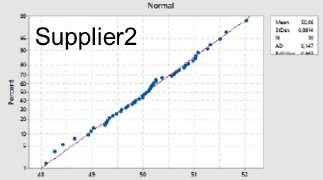
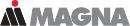
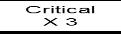

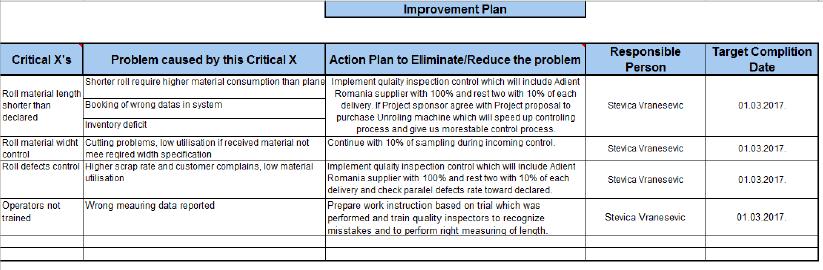

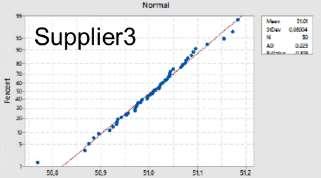
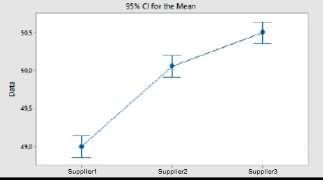
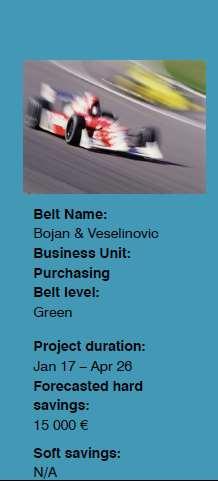
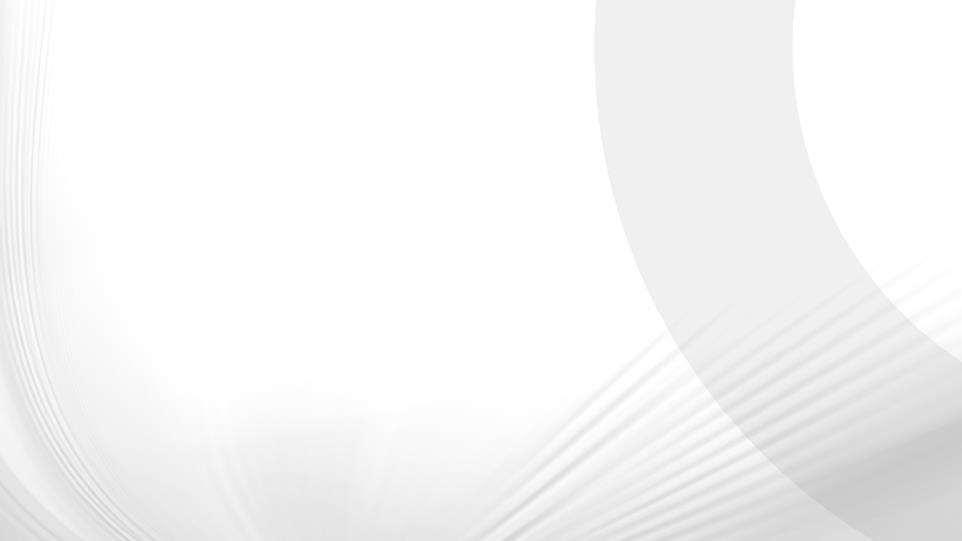
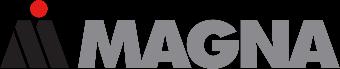
