1st Kaizen Congress
28 September 2017
Belgrade, Serbia
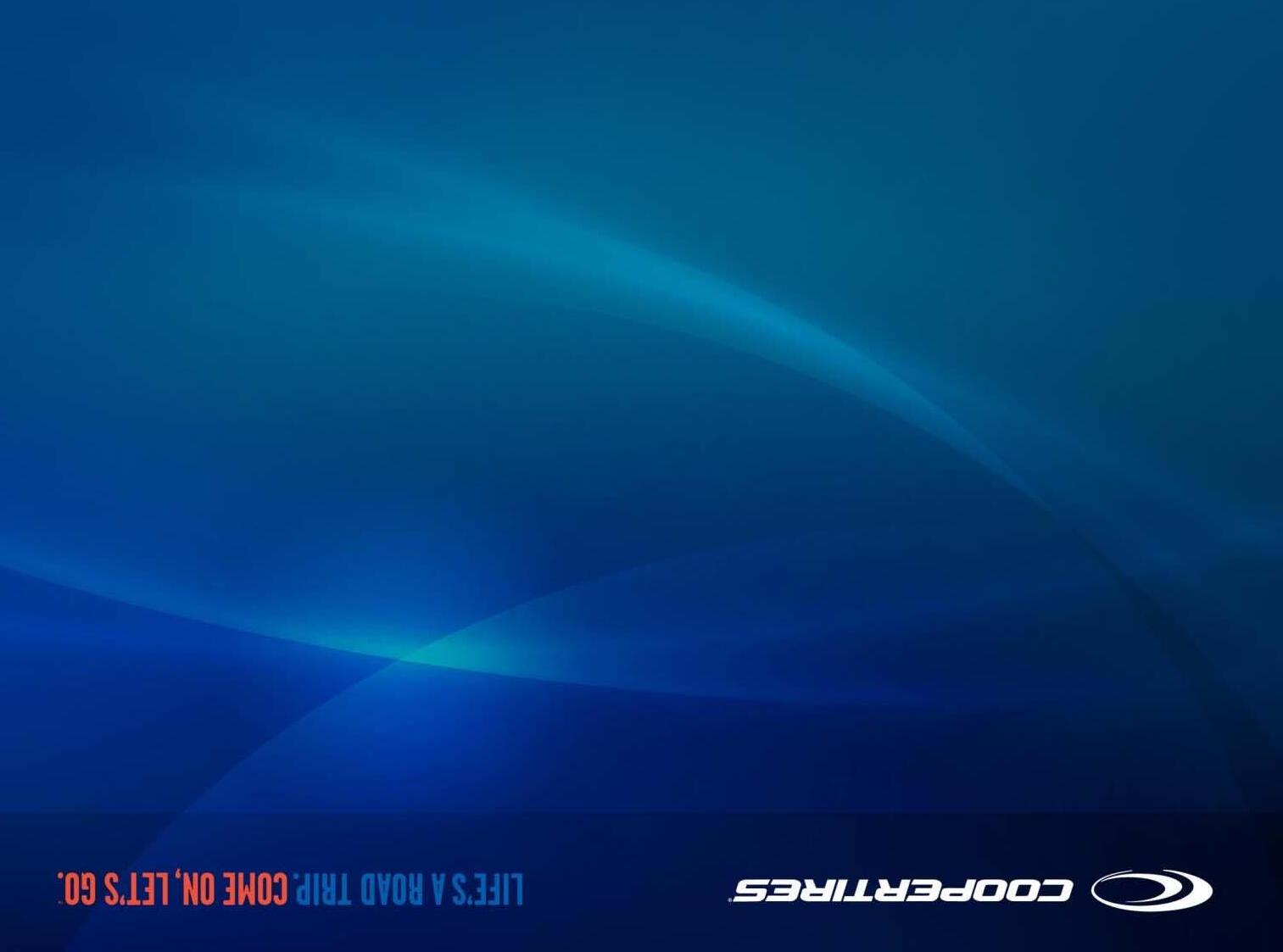

28 September 2017
Belgrade, Serbia
•Reflections and lessons learned
•Not talk about specific tools or techniques
•Rather an approach or perhaps “philosophy,” supported with examples
•Cite LSS concepts/visuals for reinforcement
•Challenge us to consider and think about this when implementing LSS
•Practical perspective, high level
•Notice I didn’t say “instead of”
•Many of us may have Quality backgrounds
•Often pushed for quantity/speed over quality
•Need to turn this around
•Show positive effects of quality versus negative effects of quantity
•What better place than LSS programs!
Message and Focus
•LSS must have management support
•Companies begin, continue, and implement
•Management or business conditions change
•LSS is forgotten, dropped and not supported
•Have experienced this
•Have experienced the opposite
•LSS can become part of strategy
Fundamental, Expected, Assumed
•Not everything is a BB project
•Projects should justify LSS/Belt, not the other way around
•Quality of project, selection and execution reflects the quality of the system
•People make judgements, right or wrong
•Mitigate and manage for success
Weak Belts
Lack of Management Support Poor Project Poor Project Selection
Measurement
•Pick good people
•Not everyone is “cut out” to be a Belt
•It shows in their work, poor quality
•Minimize variation from “outlier” Belts (variation reduction)
•Many times, “Let’s get more belts, train more …”
•What’s wrong with this?
•Answer -end up with quantity
, not quality
•Others see this
•My BBs advised me, and I am learning…
“Don’t compromise the quality of the group”
•Hurts the operation and department
•Is bad for change management
•Reflects on the organization -in perception and results!
•Choose quality over quantity!
•Keep this in mind!
•Weak belts equal Non-Value Added (NVA) waste
•How?
•A Green Belt with minimal interest requires hand holding, multiple discussions, and follow ups from mentoring Black Belts or me
•Projects stall
•May or may not get picked up by other belts
•Wasted and lost time due to poor quality belt
•LEAN: reduce waste…less can be more
•Types of Waste DOTWIMPI: Defects, Overproduction, Transportation, Waiting, Inventory, Motion, overProcessing, Intellect
• Inventory of poor belts produce Waste, but their skills may be better used elsewhere so Intellect is not wasted, Quality added to the process
Quality belts, not quantity, are the foundation ‐ like building a house!
•Train people quickly to get “numbers” because we can’t afford to have them off the job too long
•Few remember what was taught, then something goes wrong … “well, they were trained”
•Then what do we do -retrain everyone
•Never time to do it right the first time, but always money and time to do it again
•5S Reset Moment
•Started slowly, did it right -Quality!
•Got comfortable, so 5S more areas -Quantity!
•Months later, felt we were not as good as before
•Paused progress to reevaluate process
–Training, audits, requirements, expectations
•Fundamentally very sound, but missed some things to help sustain quality
•Perfect?
•No!
•It’s always something, “shift happens”
•Manage and recognize this to minimize it
•Plants that succumb to quantity over quality
•Completed over 100 areas for 5S
•Year later, 5S areas not being sustained
•Management changed, not “supportive”
•Didn’t understand 5S is more than cleaning
•Basically, had to start over from the beginning
•Lessons learned!
•Quality over Quantity allows us to learn as we go
•Speed along highway for vacation -miss a lot
•When we rush, we miss things
•Then we have to go back and “revisit”
•Make it a journey, see and experience a lot!
•Don’t rush, don’t cut corners -it costs
•Sometimes we just need a friendly reminder
Final Thoughts
•It is the right thing to do!
•“Do the right things”, versus doing things right
–approach it in that order
•Easy? No, takes time and effort
•Always exceptions and changes
•Be vigilant and remind ourselves …