Common Warehouse and Trucking Errors—and Proven Fixes
By Matthew Herzberger
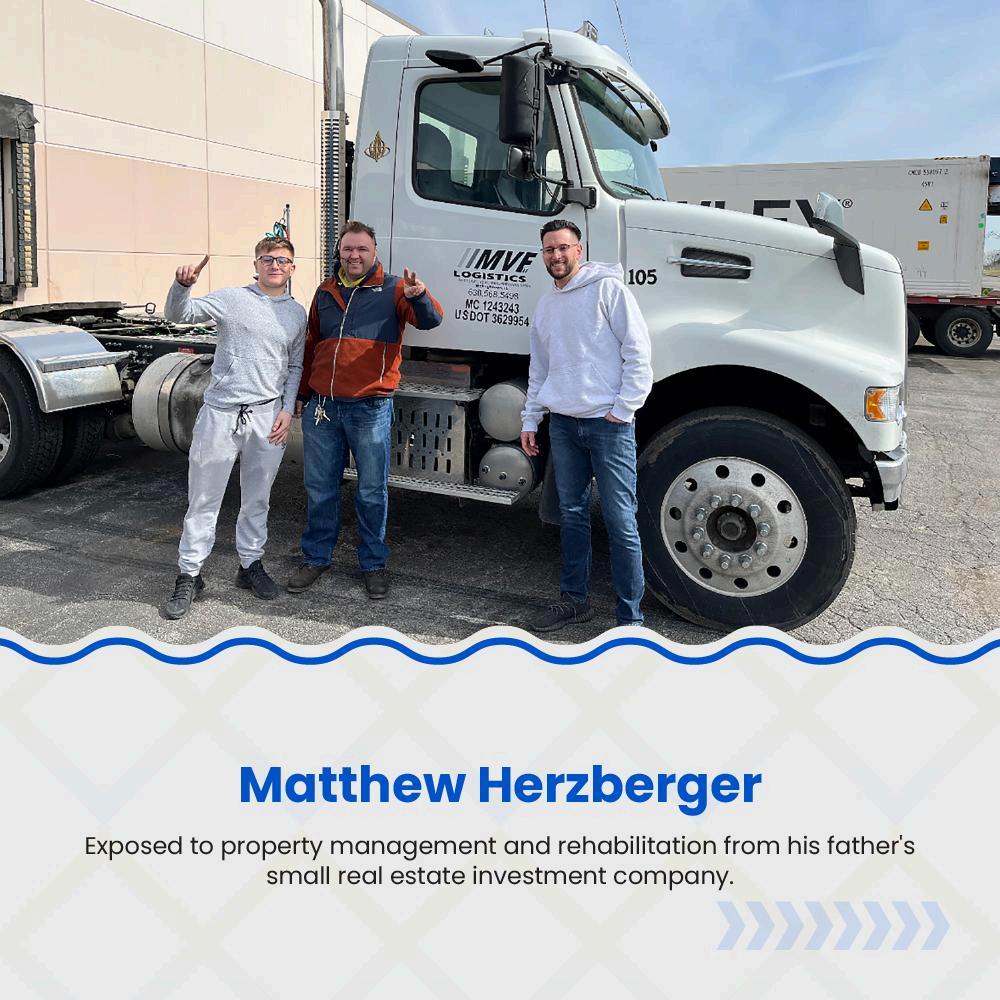
Matthew Herzberger believes that trucking and warehouse operations face constant challenges in the logistics and transportation industries From delays and inefficiencies to safety concerns and rising costs, the errors that occur in these sectors can significantly impact a business's bottom line However, understanding the most common mistakes and implementing
proven fixes can improve efficiency, reduce costs, and enhance productivity In this article, we'll explore some of the most frequent errors in warehousing and trucking and provide actionable solutions to avoid them
Error 1: Poor Inventory Management
In both warehouse and trucking operations, inventory management is a critical function. A standard warehouse error is inaccurate inventory tracking, leading to stock discrepancies, lost goods, and missed orders This error affects customer satisfaction and results in unnecessary costs related to replenishing stock or re-shipping items. Similar issues in trucking can occur when shipments are not tracked accurately, leading to delays or lost freight
Proven Fix: To address poor inventory management, businesses should invest in software that offers real-time tracking and automated updates Using barcode scanners or RFID technology can help ensure that all products are accurately accounted for Additionally, integrating inventory management with a fleet management system allows for better visibility of goods and vehicles, ensuring that products are shipped on time and stock levels are constantly updated accurately Regular cycle counting and audits can also reduce errors and help maintain inventory accuracy.
Error 2: Inadequate Driver Training
Trucking companies often need to pay more attention to proper driver training, which can lead to increased accident rates, fuel inefficiency, and compliance issues Inadequate training endangers the safety of the driver and other road users and leads to costly legal problems, accidents, and insurance claims Drivers who need to be appropriately trained may also need to follow regulations regarding hours of service, cargo securement, or weight limits, which can result in fines and penalties.
Proven Fix: A comprehensive driver training program is essential to improve safety, fuel efficiency, and regulatory compliance. Trucking companies should invest in ongoing driver education that covers road safety, defensive driving techniques, and eco-friendly driving practices such as smooth acceleration and braking. Additionally, ensuring that drivers are up-to-date on industry regulations and certifications is critical Offering incentives for safe driving, such as bonuses for accident-free months or adherence to rules, can further motivate drivers to perform safely and efficiently.
Error 3: Underutilizing Technology
One of the most common errors in trucking and warehousing operations is the failure to leverage technology effectively Many warehouse managers still need to rely on manual processes for sorting, storing, and tracking inventory, which increases the likelihood of human error and inefficiency In trucking, relying on outdated fleet management methods can result in missed delivery deadlines, excessive fuel consumption, and ineffective route planning.
Proven Fix: Integrating modern technology into trucking and warehouse operations can significantly enhance efficiency and reduce errors. Implementing a Warehouse Management System (WMS) in warehousing can automate inventory tracking, optimize storage space, and improve order-picking processes. For trucking companies, fleet management software and GPS tracking tools can help optimize routes, monitor truck performance, and provide real-time tracking updates to customers Additionally, adopting Electronic Logging Devices (ELDs) ensures regulatory compliance by automatically recording drivers' service hours, reducing the risk of violations
Error 4: Inefficient Routing and Scheduling
Inefficient routing and scheduling significantly contribute to delays, excessive fuel consumption, and increased operational costs. In trucking, errors in route planning can lead to longer travel times, missed delivery windows, and wasted fuel Similarly, in warehousing, poor scheduling can cause bottlenecks during loading and unloading, leading to delays and reduced throughput
Proven Fix: To fix routing and scheduling inefficiencies, trucking companies can adopt advanced route optimization software that considers real-time traffic data, weather conditions, and delivery time windows These tools can help determine the most efficient routes, reduce fuel costs, and improve on-time deliveries Implementing a dynamic warehouse scheduling system that aligns delivery and unloading times with available labour and dock space can eliminate bottlenecks and enhance warehouse throughput Automation tools can streamline operations by scheduling tasks based on real-time data, ensuring that inventory is moved and sorted efficiently.
Error 5: Failing to Maintain Proper Safety Standards
Safety is paramount in both trucking and warehousing operations Failing to adhere to safety standards, whether it's regarding equipment maintenance, employee safety, or proper handling of hazardous materials, can lead to accidents, injuries, and legal penalties. Trucking companies may overlook routine truck inspections, while warehouse managers might need to pay more attention to employee safety training or provide proper safety gear.
Proven Fix: Trucking and warehouse operations should have regular safety audits and checks to maintain safety standards. Trucking companies must ensure that drivers conduct pre-trip inspections and that vehicles are maintained regularly, following manufacturer guidelines and regulatory requirements A proactive approach to maintenance, including scheduled repairs and tyre rotations, can prevent breakdowns and accidents. In warehouses, implementing strict safety protocols, such as requiring personal protective equipment (PPE), training employees on proper lifting techniques, and conducting regular safety drills, can reduce the risk of injuries. Creating a safety-first culture emphasizing safety in all training and daily operations can also prevent accidents and improve morale
Error 6: Ignoring Customer Communication
In trucking and warehousing, better communication with customers can lead to satisfaction and a loss of business For trucking companies, failing to provide customers with accurate delivery times or updates on shipment status can cause frustration and distrust Similarly, warehouses that don't communicate stock availability, shipping delays, or issues with orders can damage their relationship with customers
Proven Fix: A commitment to transparent and consistent customer communication is vital for maintaining long-term relationships Trucking companies can improve communication by offering real-time tracking services to customers, allowing them to track shipments at any time. Notifications via email or text can be sent when a delivery is delayed or completed Similarly, warehouse managers should implement systems that allow customers to access live updates on inventory levels, order fulfilment, and shipping status. A dedicated customer service team promptly handling inquiries and complaints can improve satisfaction and loyalty
Error 7: Overlooking Employee Morale and Retention
One of the biggest mistakes warehouse and trucking company owners make is paying attention to the morale and retention of their employees. High turnover rates, especially in the trucking industry, can lead to increased hiring and training costs and a loss of experience and knowledge. In warehouses, low employee morale can result in inefficiencies, slower workflows, and higher rates of workplace accidents
Proven Fix: Investing in employee morale improves productivity and reduces turnover. For trucking companies, offering competitive salaries, benefits, and incentives for safe driving can help attract and retain skilled drivers Regular check-ins and feedback sessions, as well as opportunities for career growth, can make employees feel valued and engaged. In warehouses, offering performance-based bonuses, providing training and skill development opportunities, and fostering a positive, team-oriented work culture can improve employee satisfaction and retention Additionally, ensuring employees access to proper tools, equipment, and a comfortable work environment can increase efficiency and reduce mistakes
Trucking and warehouse operations are complex, and errors can lead to significant inefficiencies and costs However, by understanding the common mistakes in these industries and implementing proven fixes, business owners can improve operational efficiency, reduce risks, and ultimately thrive in a competitive market Investing in technology, optimizing routes, ensuring safety compliance, and maintaining strong customer and employee communication are essential strategies for success. Trucking and warehouse businesses can achieve long-term growth and profitability by addressing these common errors and taking proactive steps to fix them.