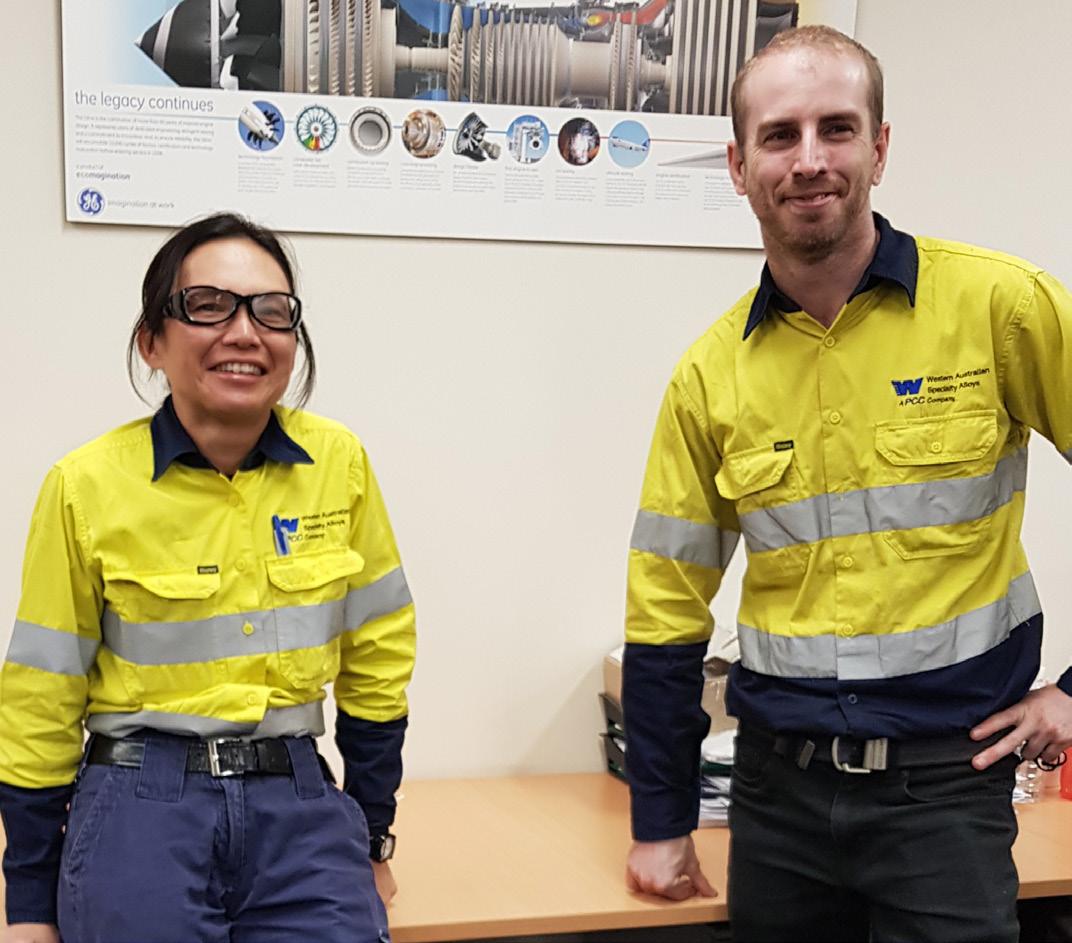
3 minute read
WA Branch Technical Meeting - 11 April 2022
WA Branch Technical Meeting - 11 April 2022 Western Australian Specialty Alloys
Source: Michael Lison-Pick, Operations Manager
The Western Australian Branch held a technical meeting in early April. Michael Lison-Pick, Operations Manager at Western Australian Specialty Alloys (WASA) was the guest speaker. WASA produces superalloy ingot, billet and bar for forging and ring rolling applications for a range of aerospace, power generation and oil and gas applications. Established in 1993 and now part of the Precision CastParts Corporation group, WASA is undoubtedly one of the most unusual local manufacturing operations—its material input is almost entirely imported, and its products are almost entirely exported. WASA’s success has been established on its hard-earned capacity to produce more than 100 highly specialised nickelbased alloys, notably for the most demanding aerospace applications. This capacity is confirmed by client accreditation, often based on ‘fixed process’ agreements. In this rarefied part of the world of metals, alloy grades are only the starting point, as individual clients have extremely tight and differing specifications within grade ranges. These limits can be as low as 0.1 ppm maximum limits on certain elements, such as antimony and selenium. Where a specified element content is demanded, the composition limits may be as tight as 10-20 ppm. The fixed process specification, goes beyond composition to ensure that other variables, notably segregation, are also tightly controlled. Michael Lison-Pick and Seach Hwee Goh led visitors on the tour of WASA’s operation, starting with charge formulation for the vacuum induction furnace. Approximately half the charge is ‘revert’ alloy, mostly returned in-process scrap from customers, with remainder being virgin material, mainly nickel. With such tight limits on impurities, segregation of stored raw materials is critical.
Michael explained that the slowest part of the operation is charging the furnace, which must be done under vacuum. Up to ten charging pans are prepared, and the rate-controlling step in the melting process – introducing each charge pan under vacuum – means that a typical batch time is around eight hours. The analytical facility is critically important in meeting the composition specification. After each pan is loaded and melted, a sample is analysed using a combination of rapid combustion and x-ray techniques, and the make-up of the next charging pan adjusted accordingly. Wet chemical analysis (ICP-MS) for certification of composition. The vacuum induction melting (VIM) has two product types. ‘Little sticks’ (~6 t, 150-200mm diameter ingots) are sawn into small (less than 10kg) billets for melting by customers, in which case the segregation typical of VIM ingots is irrelevant. ‘Big sticks’ (400-600mm diameter, ~15 t ingots) are used internally as feed to the next processes in line: vacuum arc remelting (VAR) and electro-slag refining (ESR). The purpose of vacuum arc remelting (VAR) is to control solidification to the avoid micro-segregation and the formation of laves, sigma and mu phases that cause problems in the forging of nickel superalloys. The VAR process can follow the primary step of vacuum induction melting (VIM) used to produce the alloy (double melting). Vacuum arc remelting can be likened to 'a big DC arc welder in a vacuum', but under highly sophisticated control. A VIM ingot is used as an electrode with an arc struck in the gap between its bottom and a second ingot underneath, which continues to grow as the upper ingot is melted drip-wise through the 10mm vacuum space above it. The remelted ingot typically has a diameter around 50mm larger than that of the original ingot. Ingots destined for forging into rotating machinery parts, such as turbine shafts, require the extra step of ‘triple melting’ in which the VAR ingot is re-processed with ESR. The ESR process can be likened to submerged arc welding, in which droplets of molten alloy fall through a specifically formulated calcium fluoride-based flux pool on top of the growing remelted ingot underneath. This alloys even greater control over impurities. It was interesting to see the changes since the WA branch’s last visit to the WASA operation some years ago. The OPTIMAT system is used for management raw materials and charge control, greater use is made of nickel-based master alloys for additional of minor elements, the VAR and ESR processes are subject to more sophisticated control, and laser surface cleaning is now applied to ingots. One of the most dramatic recent impacts has been the rise in the nickel price, with full VIM charge currently worth around $0.25 million. These changes show that while there are advantages in incumbency, constant innovation is essential to ‘stay in the game’.
(L to R): Seach Hwee Goh, Michael Lison-Pick.