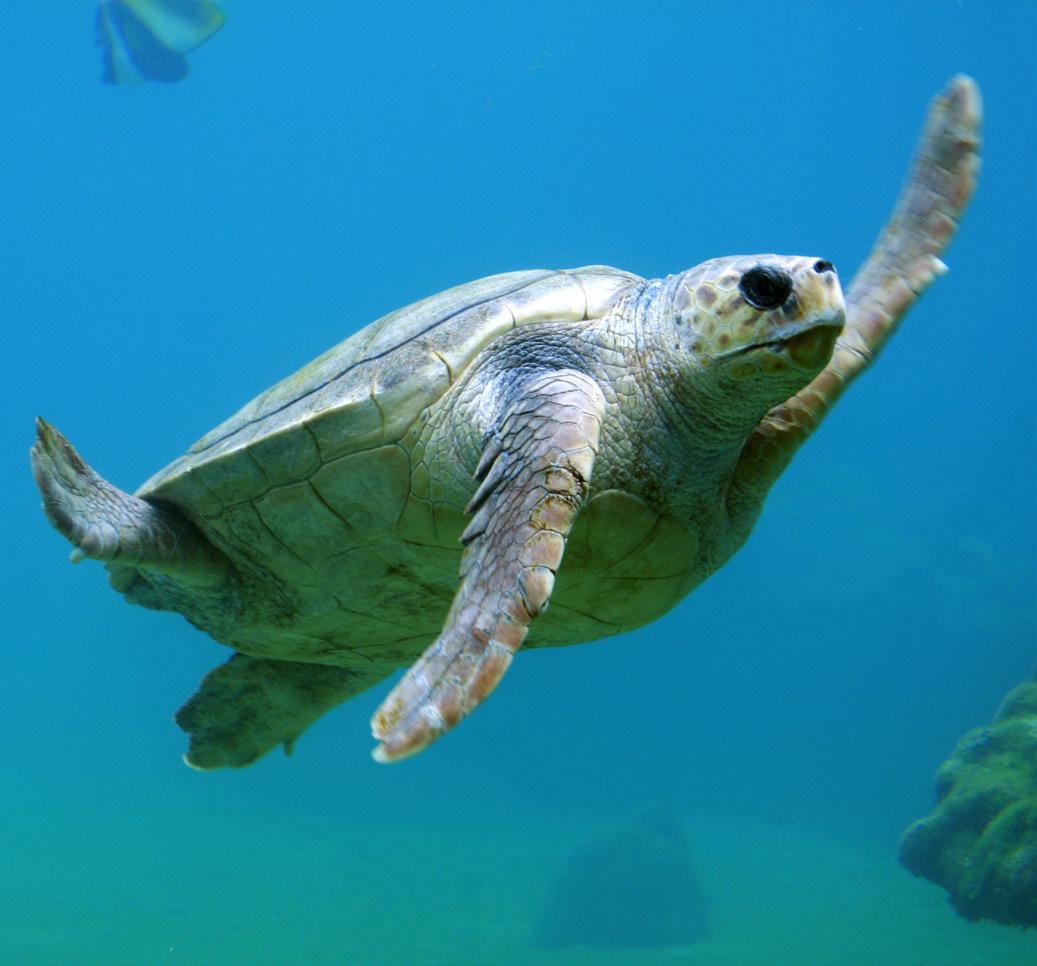
18 minute read
Breaking News
Sustainable Solutions for Ghost Net Waste
A recent report has found solutions in the fight against discarded ‘ghost’ nets and other fishing marine debris in northern Australia.
The research was conducted by the environmental not-forprofit organisation TierraMar and the UNSW SMaRT Centre, who uncovered sustainable methods to detect, collect, transport and responsibly dispose of ghost nets. “Ghost nets are fishing nets that have been lost at sea, abandoned or discarded when they have become damaged,” said Professor Veena Sahajwalla from the UNSW SMaRT Centre.
“Discarded fishing equipment can cause pollution such as microplastics and entangle marine wildlife and damage reefs, silently killing,” she added. Marine debris accumulates in the Gulf of Carpentaria off northern Australia, which is recognised as a global marine debris ‘hot spot.’ “Four of the six marine turtle species found in Australian waters are listed as threatened under Australian environmental legislation and they are regularly found entangled in derelict fishing nets,” Professor Sahajwalla said. Self-sustaining solutions are critical for ghost nets and marine debris in northern Australia.
Meanwhile, reducing the reliance on government support to clean-up and dispose of the debris depends on the ability to create high quality products made from waste. “There is an opportunity to develop a range of high-quality homeware and building products made directly from ghost nets and marine debris coming out of northern Australia,” Professor Sahajwalla said. “The products, such as ceramic tiles, could creatively reflect the unique cultures, artistic values and connections to country by local communities,” she concluded.
Researchers from Monash University recently took another step towards the holy grail of renewable energy: the ability to store it cheaply. Image courtesy of Monash University.
Cheaper, Cleaner, Faster — New Technology for Better Lithium Batteries

Researchers from Monash University recently took another step towards the holy grail of renewable energy: the ability to store it cheaply. The research team created a lithium-sulfur battery interlayer that promotes exceptionally fast lithium transfer and improves the performance and lifetime of the batteries. It is also cheaper, greener and faster, which enables the charge and discharge of batteries, and discharge of energy at a much faster rate than previously offered. “A lithium battery interlayer sits in the middle of the battery and keeps the electrodes apart, it helps lithium get from one side of the battery to the other faster,” said Professor Matthew Hill, who led the research project. “The new interlayer overcomes the slower charge and discharge rates of previous generation lithium-sulfur batteries,” he added. This latest breakthrough continues the world-leading work into lithium battery development by a team from Monash University’s Faculty of Engineering. Lithium-sulfur batteries offer higher energy density and reduced costs compared to the previous generation of lithium-ion batteries.
They can store two-to-five times as much energy by weight than the current generation of lithium-ion batteries, which means a car may only need to be charged once a week. In previous cases, the electrodes in lithium-sulfur batteries deteriorated rapidly and the batteries broke down. “These batteries are not dependent on minerals that are going to lack supply as the electrification revolution proceeds, so this is another step towards cheaper, cleaner and higher performing batteries that could be made within Australia,” Professor Hill said.
SPEE3D Demonstrates World's Fastest Metal 3D Printer at Melbourne Grand Prix
Australian additive manufacturing company, SPEE3D recently showcased its world-leading metal 3D printing technology at the Melbourne Formula One Grand Prix. The company's flagship product, the WarpSPEE3D, is the world's fastest metal 3D printer. It can produce parts up to 1,000 times faster than traditional methods.
SPEE3D teamed up with Gary Rogers Motorsport to bring the high-speed production of aluminium parts for the s5000 open-wheelers to life. The company is based in Melbourne, and provides global racing teams with the opportunity to witness the worldleading technology in action. In recent years, the company has claimed many awards for their technology, and hold the record for the world’s fastest print of a 1kg part. In Melbourne, it was the first time crowds of motor racing enthusiasts were able to see dozens of metal parts printed on demand.
Byron Kennedy (CEO of SPEE3D) said it was a pleasure to highlight the technology to racing fans. “It was exciting to showcase our technology at this fantastic event in Melbourne. SPEE3D’s technology is the world’s fastest way to make metal parts, and what better place to show this off than at the Grand Prix which is all about speed and innovation.” One of the many metal automotive parts featured at the event included an s5000 Support Arm. This 2.4kg aluminium part was printed in only two hours on a WarpSPEE3D metal 3D printer for $180 dollars. SPEE3D focuses on the development, assembly, and distribution of machines and integrated system solutions.
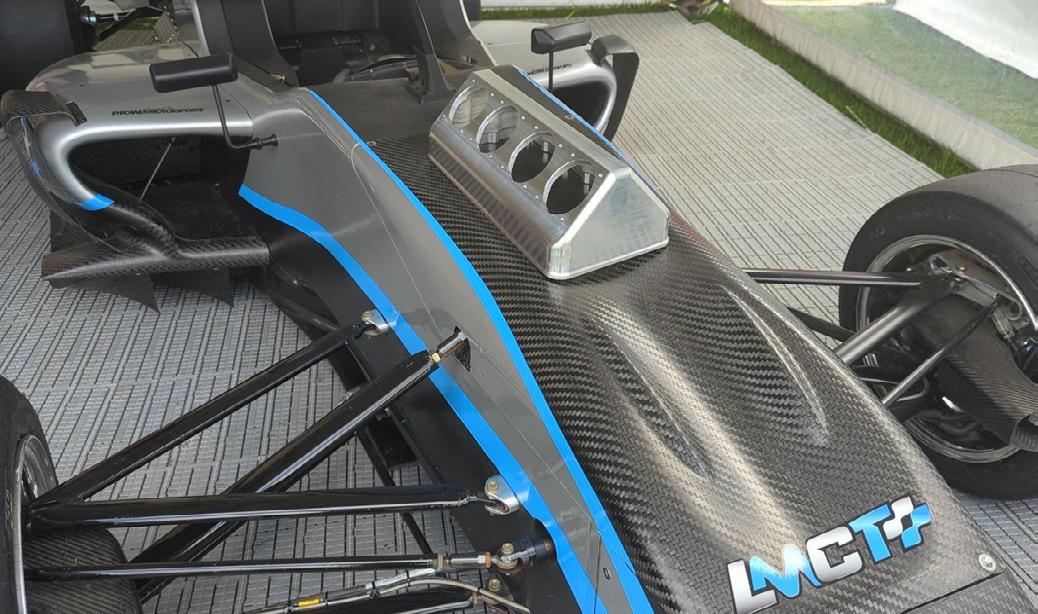
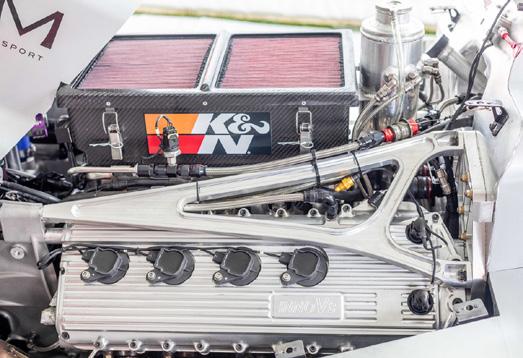

Top left: SPEE3D metal 3D Printed Support Arms on Garry Rogers MotorSport s5000 open-wheeler. Top right: SPEE3D Printed Support Arm installed on s5000 Garry Rogers Motorsport. Above: SPEE3D printed Crest CNC machined Intake Runner Manifold on s5000 open-wheeler Garry Rogers Motorsport.
Liquid Metals, Surface Patterns, And the Romance of The Three Kingdoms
Researchers recently found that a single silver–gallium system can produce distinct patterns such as particles or bundle-like structures of an Ag2Ga compound. The individual Ag2Ga structures that build the patterns are small, with micrometre or nanometre thicknesses, which are tens or hundreds of times smaller than a human hair.
The researchers observed that the patterns divide and unite in a repeated manner. Dr Jianbo Tang from University of New South is the first author of the study who said this came as a surprise. “The first time I saw such cyclic divergent-convergent patterns, it immediately reminded me of the famous opening lines of the Romance of the Three Kingdoms.” Pattern formation is a fundamental yet ubiquitous phenomenon, which has interested and inspired scientists for a long time. In fact, some pattern types are more common than others. Divergent pattern formation, or bifurcation, is frequently seen in nature because the arrangement tends to favour energy conversion or distribution. Bifurcation is evident in river networks, tree branches, lightning pathways, and vascular systems. In comparison, convergent pattern growth, or inverse bifurcation, is encountered less frequently. The cyclic divergent and convergent growth is rare and has not been observed in solidification structures before this piece of work. The researchers observed oscillatory bifurcation patterns on the surface of several liquid alloys after solidification. This suggests this counter-intuitive behaviour is quite general for solidification patterns forming on the surface of liquid metals.

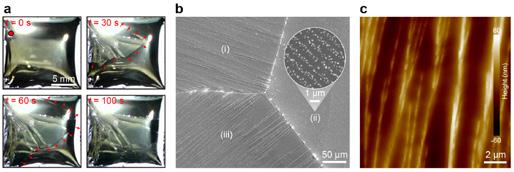
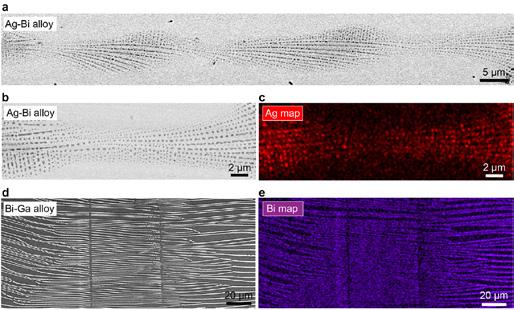
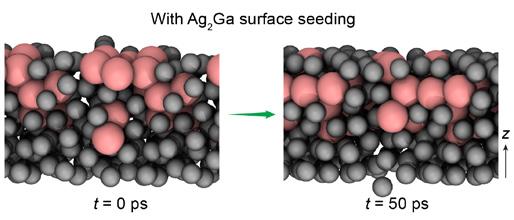
Above left: Divergent surface patterning spreading out from a ‘seed’ (left to right), meeting convergent patterning (right to left). Bottom: oscillatory bifurcation patterns on surface of solidified Ag-Ga alloy (scanning electron microscopy image). Above right: Examples of oscillatory bifurcation patterns observed in (a-c) Ag-Bi alloys and (d,e) Bi-Ga alloys. Scanning electron microscopy (a,b,d) and energy dispersive spectroscopy (c,e) Below left: Left: Time-lapse of the seeded surface solidification process, with arrows indicating the propagating direction of the surface solidification front. Centre: scanning electron microscopy reveals multiple surface subdomains with different patterns. Right: atomic force microscopy of the surface patterns. Below right: Initial and final (50 picoseconds) atomic configurations of the Ag atoms (pink) and Ga atoms (grey) seen in one of the molecular dynamics simulations

Monash University recently launched a world-class robotics research facility. Image courtesy of Monash University.
The Monash University Faculty of Engineering recently launched a world-class robotics research facility to train the next generation of engineers and global innovators. The $6.5 million investment into Monash Robotics drives the emerging artificial intelligence economy. Monash University President Professor Margaret Gardner AC said the launch of the facility is a major step in advancing knowledge and innovation. “Robots are changing and improving the lives of people across the globe every day.” “This investment shows our ongoing commitment to world-leading research and education in this important and dynamic field, and aligns with our goals and ambitions within Monash’s Strategic Plan, Impact 2030, to address the great challenges of our time through innovative and excellent education and research,” she said. The Monash Robotics facility will give researchers the opportunity to support and enhance impactful robotics research. It will bring top researchers together to develop robots that can improve the nation’s economy and wellbeing. “Robotics and artificial intelligence will deliver the next generation of breakthrough technologies and will rapidly change the way we live and work, and help shape our future,” said Professor Elizabeth Croft, who is Monash University’s Dean of the Faculty of Engineering. Robotics deployment across the world is rising rapidly. The International Federation of Robotics reports that three million industrial robots were operating in factories around the world in 2021.
As such, Monash University is taking advantage of the immense research and industry collaboration opportunities. “This is a very exciting step for Monash University,” Professor Croft concluded.
New Hub to Make Diamond-Based Quantum Computers
A joint research and development hub will use the strength of synthetic diamonds to build a new generation of quantum computers. The recently established Research Hub for Diamond Quantum Materials uses the impurities within diamonds— where a carbon atom is swapped out for a nitrogen atom within the crystal—to generate qubits, which are the standard bits within a quantum computer. The German-Australian quantum computing provider, Quantum Brilliance leads the hub, alongside RMIT and La Trobe universities as major research partners. The process results in a microprocessor, which is protected by its diamond casing. Once inside, fragile quantum states that typically survive in a vacuum or at ultra-cold temperatures can interact at room temperature and enable quantum computing. Dr Marcus Doherty is the Chief Scientific Officer of Quantum Brilliance, who said the team's fabrication techniques would enhance the performance of diamond-based quantum computers. “The hub is another example of our collaborative research efforts to advance diamond-based quantum technology and deliver economic benefit to Australia in the years to come,” he said.
The hub is designed to make great strides in developing synthetic diamond accelerators, and create a network of experts in diamond material science. RMIT Deputy Vice-Chancellor for Research and Innovation Professor Calum Drummond said collaborations like these are vital in supporting future industries. “We value this opportunity to support development of new technology, which will in turn grow new businesses here in Victoria,” he said.
All three organisations have world-leading expertise and resources in diamond materials sciences.
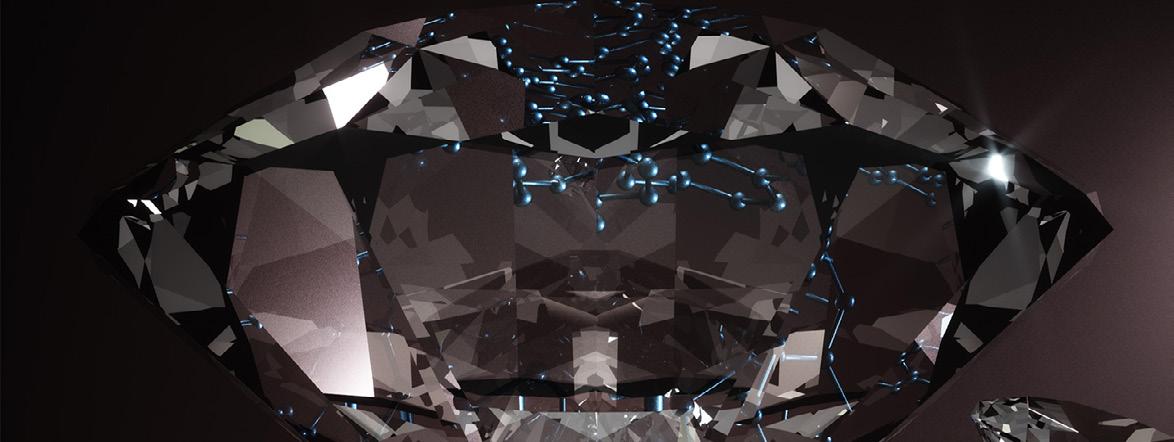
A joint research and development hub will harness the strength of synthetic diamonds to build a new generation of quantum computers. Image courtesy of RMIT University.
Self-Healing 3D Printed Plastic Can Repair Itself... Using Only Light
New research from UNSW demonstrates that special treatment of liquid resin used in 3D printing can cause the material to mend itself if it becomes damaged. Engineers recently demonstrated a way to help 3D printed plastic heal itself at room temperature using only lights. Professor Cyrille Boyer and his team have shown that the addition of a ’special powder’ to the liquid resin, which is used in the printing process, can assist with making quick and easy repairs if the material breaks. The process can be conducted by shining standard LED lights on the printed plastic for one hour. This causes a chemical reaction and fusion of the two broken pieces. The entire process makes the repaired plastic stronger than it was before it was damaged. Researchers hope that further development and commercialisation of the technique will help to reduce chemical waste in the future. “In many places where you use a polymer material, you can use this technology. So, if a component fails, you can repair the material without having to throw it away,” said Dr Nathaniel Corrigan, who also worked on the research project. Researchers used trithiocarbonate, which is known as a reversible addition fragmentation chain transfer agent that was originally developed by CSIRO. The agent enables rearrangement of the nanoscopic network of elements that make up the material and allows the broken pieces to be fused. “There is an obvious environmental benefit because you're not having to re-synthesise a brand-new material every time it gets broken. We are increasing the lifespan of these materials, which is going to reduce plastic waste,” Dr Corrigan said.
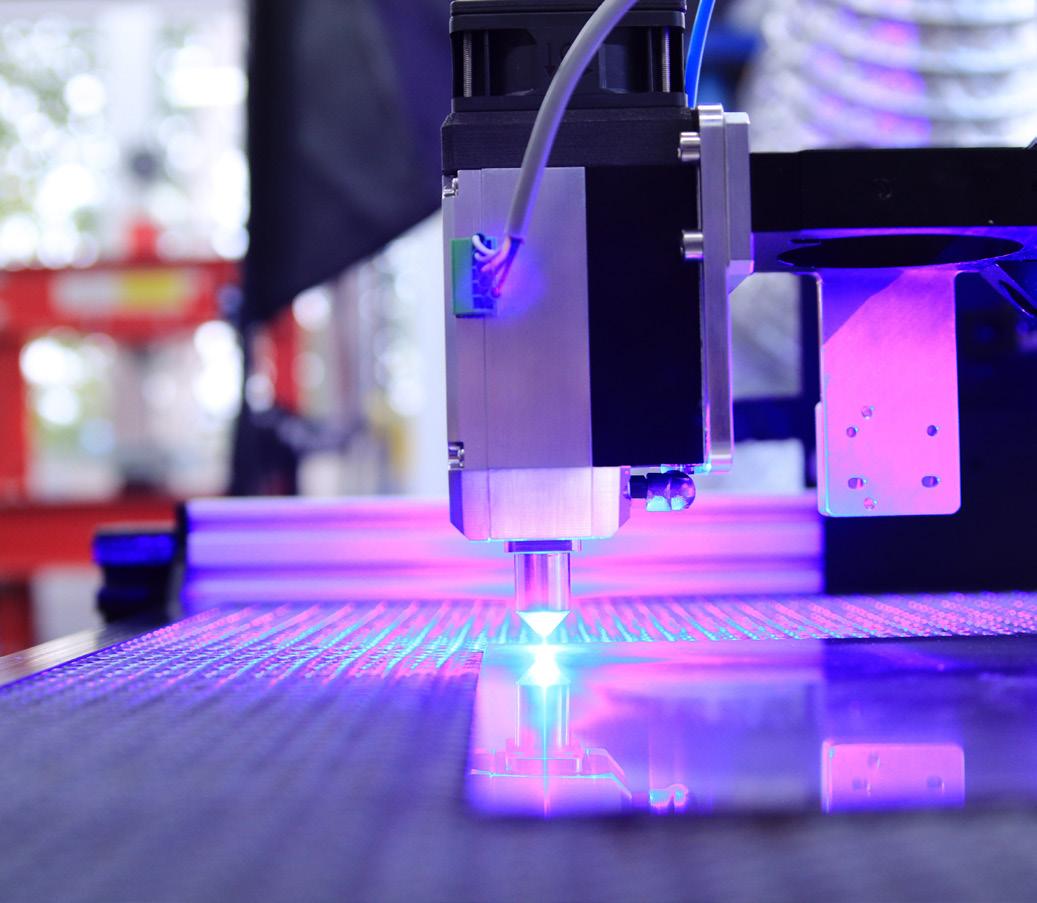
3D printed materials treated with a reversible addition fragmentation chain transfer (RAFT) agent have been shown to selfheal under UV lights. Dr Xiaoqing Li is using benth plants as a transient expression tool to make novel fibres for the cotton industry.
Dr Xiaoqing Li: Taking the Guess Work Out of Sustainable Textiles

Researchers continue to uncover fresh ways to trace the origins of fibres to ensure people can buy sustainable textiles and trust their origins. Dr Xiaoqing Li from CSIRO is a leader in novel fibres for the cotton industry. She is investigating methods to be more sustainable in a growing consumerist society. “Customers are seeking more sustainable products, particularly in the textile industry. Unfortunately, without being able to verify the history of the fibres it’s hard to tell where the material comes from,” she said. “So, traceability is a very good tool to make this happen and to improve the sustainability of the whole supply chain.” Dr Xiaoqing recently developed an engineered cotton germplasm, which produces a protein that is not naturally found in cotton fibres. She believes it could be used to trace cotton back its original source. A 2021 report by the Economist Intelligence Unit found the popularity of Google searches relating to sustainable goods has increased by 71% globally since 2016. Dr Xiaoqing said her research can make a significant impact for the industry. As such, she is exploring a plant-based way of tracing Australian cotton fibres that will make it easier to choose sustainable textiles.
“We hope this work can lead a new direction in developing plant-based tracing technology. If this can happen, we really can make a leap forward.” “If this added protein is stable and we can detect it, we can possibly trace it from the beginning to the end of the life of the fibre,” she concluded.
Surfing At the Atomic Scale: ANSTO Scientists Confirm Experimentally New Fundamental Law for Liquids
The first experimental evidence to validate a universal law that provides insights into the complex energy states for liquids has been discovered. ANSTO researchers used an advanced nuclear technique that has solved the problem of obtaining the distribution of complex energy states for liquids. “One of the most important quantities in the physics of matter is the distribution of the frequencies or vibrational energies of the waves that propagate in the material,” said Professor Alessio Zaccone from the University of Milan. “It is particularly important as it is the starting point for calculating and understanding some fundamental properties of matter, such as specific heat and thermal conductivity, and the light-matter interaction,” he added. The problem with liquids involves other types of vibrational excitations related to low energies of the disordered motion in atoms and molecules— excitations that are almost absent in solids.
“These excitations are typically short-lived and are linked to the dynamic chaos of molecular motions but are nevertheless very numerous and important, especially at low energies,” Professor Zaccone said. The time-of-flight neutron spectrometer Pelican at ANSTO’s Centre for Neutron Scattering was used to measure the vibrational densities of states for several liquid systems including water, liquid metal, and polymer liquids. The instrument has the sensitivity to measure rotational and translational vibrations over short time intervals and at low energies. Researchers confirmed the linear relationship of the vibrational density of states with frequency at low energies. This work was published in the Journal of Physical Chemistry Letters as the editor’s choice and featured on the front cover of the journal.
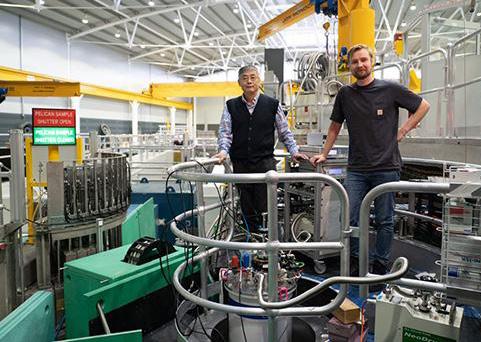
Dr Dehong Yu (left) and PhD candidate Caleb Stamper of the University of Wollongong at the time-of-flight neutron spectrometer Pelican. Not shown: Dr David Cortie. Image courtesy of ANSTO.
Silicon-Carbide Modulator Overcomes Decades Long 'Missing Block'
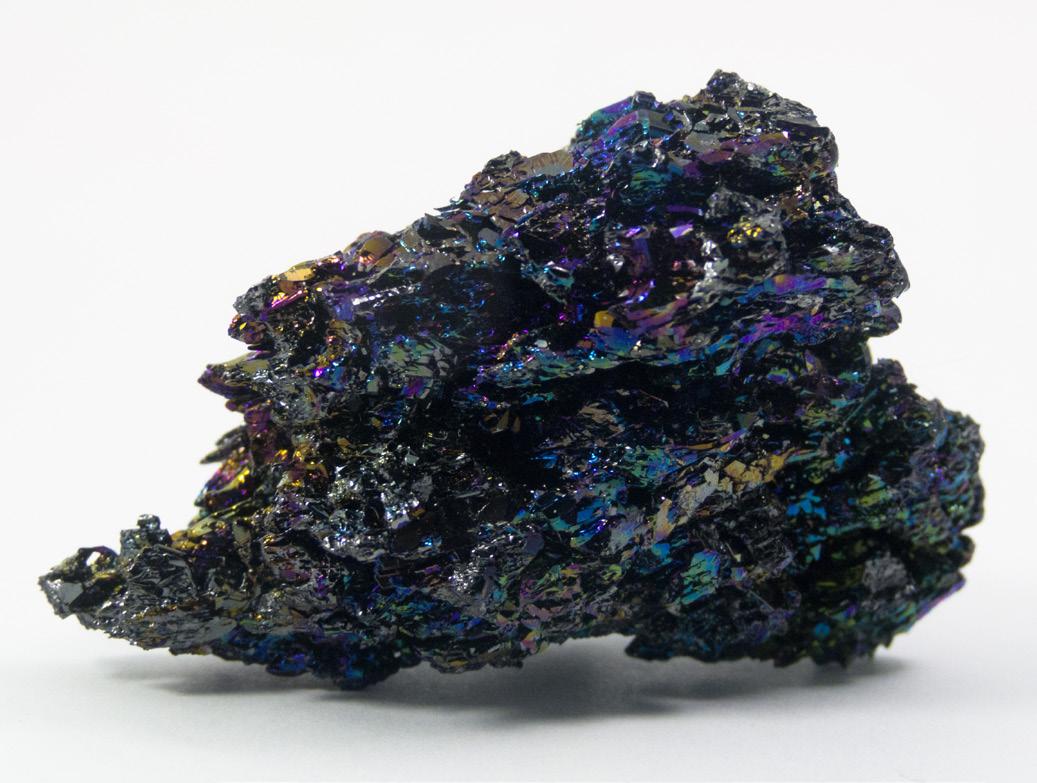
Silicon carbide is known for being difficult to work with, but researchers are now harnessing its unique properties.
A Harvard University collaboration recently led to the development of a new-generation electro-optic modulator that could stamp out its bulky predecessor. The new modulator was made possible by harnessing a ‘difficult’ compound—silicon carbide. This was first recognised as a photonics wonder material more than three decades ago when it was found to display the ‘pockels effect.’ Despite silicon carbide's durability in demanding electrical, mechanical and radiation environments, its use in photonics has been limited. However, researchers believe their technique, which was described in Nature Communications, will advance quantum communications and microwave photonics. Lead researcher from the University of Sydney’s School of Electrical and Information Engineering Professor Xiaoke Yi said this breakthrough had wide implications for industry professionals. “The use of silicon carbide will potentially open up a new chapter of opportunities in photonics for various applications including quantum computing.” Electro-optic modulators encode electrical signals onto an optical carrier. They are essential for the operation of global communication systems and data centres. “Modulators that use the Pockels effect enable low loss, ultrafast and wide-bandwidth data transmission.” “Overcoming the previous unworkability of silicon carbide may allow for unique photonic-integrated circuits to transmit and process wideband and fast-speed signals – as well as for emerging quantum technologies,” Professor Yi said. The University of Sydney and Harvard modulator had no signal degradation, and demonstrated stable operations at high optical intensities. This paves the way for high optical signal-to-noise ratios for modern communications in datacentres, 6G and satellites, and future quantum internet.
A Flash Future of X-Ray Technology Could Come from A Digital Camera
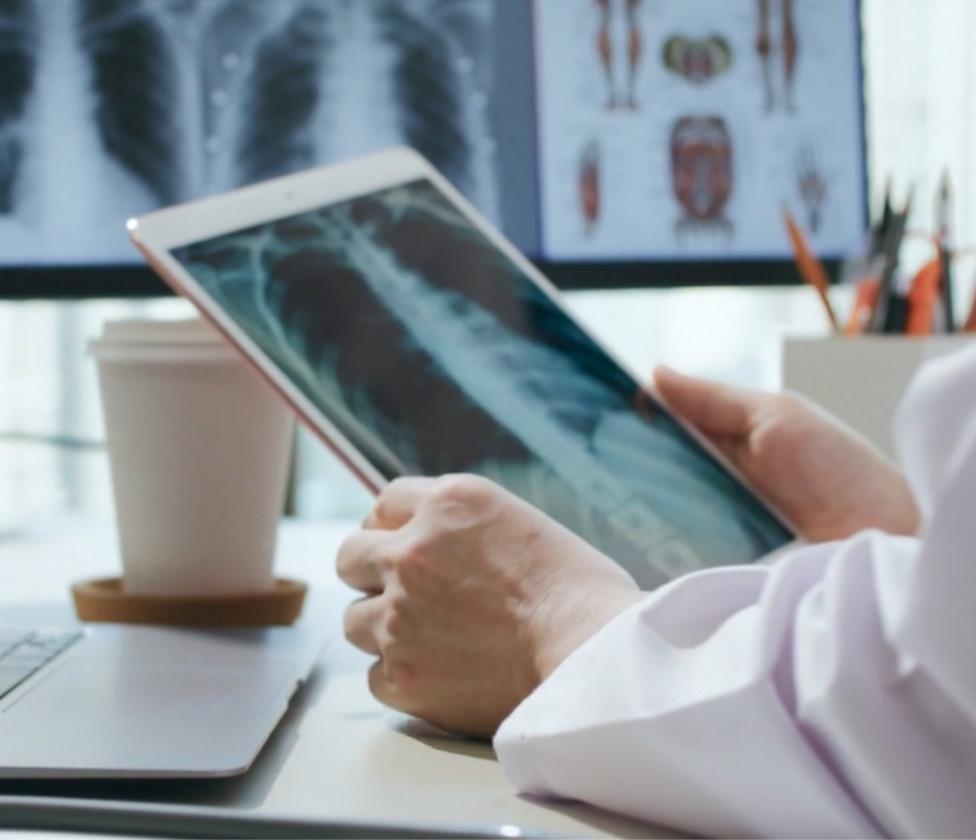
A Curtin University researcher is embarking on an international project to develop a technology that will aim to take x-rays using a standard digital camera. The project is one of eight that successfully secured funding from the Hebrew University of Jerusalem out of 69 applications. Associate Professor Guohua Jia, from Curtin’s School of Molecular and Life Sciences will focus on developing x-ray detectors from metal halide perovskite materials. This is a type of cheaper semiconductor compound that serves as a visualisation tool for x-ray radiography. Together, this enables a very low detection limit, which means they could lower medical expenses and reduce the risk of radiation to patients. “X-ray detection is widely used in medical diagnoses and the non-destructive inspection of luggage and industrial products at airports and other custom entry points.” “This modern x-ray imaging uses scintillator materials such as caesium iodide and gadolinium oxysulfide as photodetectors to convert the high-energy X-rays into visible light.” “The problem with this is that these materials are made of very expensive crystals grown at high temperatures, and they usually show low radioluminescence conversion efficiency,” Dr Jia said. The team is investigating the use of a cheaper metal halide perovskite material made in solution at low temperatures to fabricate X-ray detectors. “Based on these materials, we believe we should be able to detect small doses of X-ray photons, converting them into visible light,” Dr Jia said. The project has been funded for two years with the support of $150,000 for both participating parties per annum.
Cutting Edge Steel to Be Made at Port Kembla
Port Kembla recently became the home of specialist steel manufacturing for armoured vehicles, navy vessels and renewable energy installations. The University of Wollongong (UOW) will lead the Federal Government’s $217 million Advanced Steel Manufacturing Precinct, in partnership with BlueScope Steel. The precinct will include a new facility that will produce plate steel for armoured vehicles and ocean vessels, and the type of steel used to create wind turbine towers and large-scale solar installations. Together, it will reduce the need for overseas imports and secure our sovereign capability in steel fabrication. Dr Phil Commins is the Acting Director at the Facility for Intelligent Fabrication at UOW, who said the involvement of a research partner was vital for the success of the bid by BlueScope Steel. “This is a fabulous example of industry collaborating with the university sector delivering real translational research outcomes.”
“The project is about investing in new capital equipment and processes. BlueScope wants to ensure that it takes full advantage of the modern Industry 4.0 manufacturing principles, which is where our expertise comes in,” he said. UOW will provide support to the project in areas such as manufacturing design, simulation, modelling and pilot scale demonstrations.
“The investments proposed by BlueScope will foster deeper business-to-research collaborations and will likely develop and propagate new skills and industry best practices,” Dr Commins said. More than 200 people will be employed directly in steel manufacturing, with an additional 1,000 workers in adjacent industries. The Facility for Intelligent Fabrication at UOW is part of the School of Mechanical, Materials, Mechatronic and Biomedical Engineering.
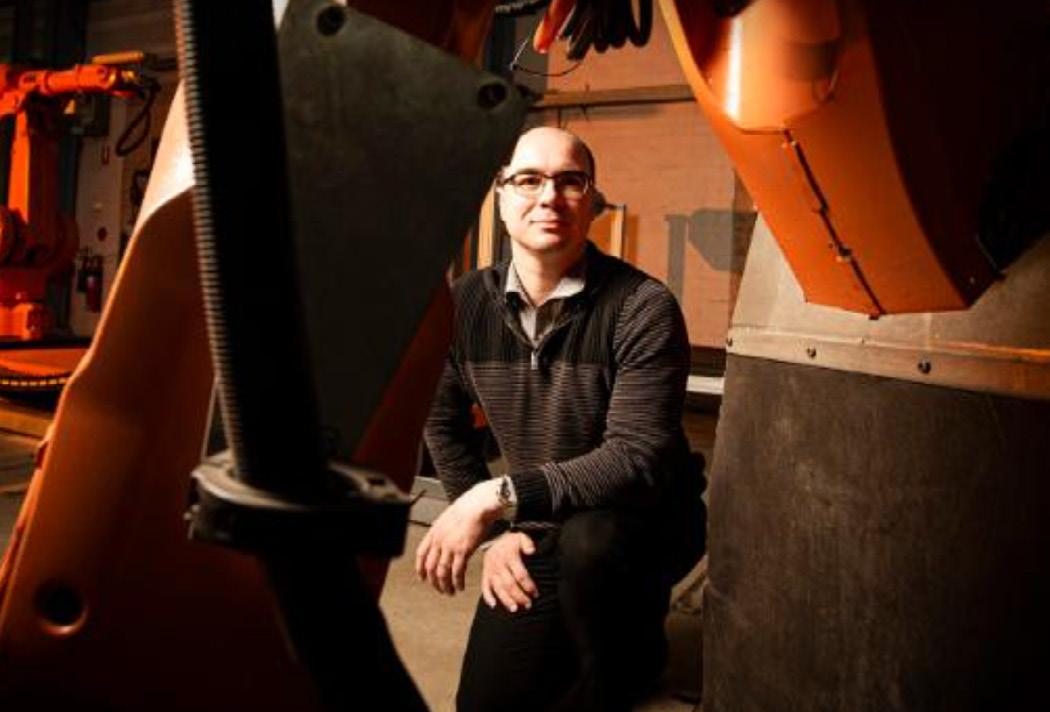
Dr Phil Commins, Acting Director, Facility for Intelligent Fabrication (FIF) at UOW.