
25 minute read
Technology-First Approach For Light Metals Innovation
TechnologyFirst Approach For Light Metals Innovation
Source: Sally Wood
Light metals are a gamechanger in Australia’s renewables future.
These low density and cost-effective alternatives boast a strength-toweight ratio that is not matched by other materials.
They are crucial for a range of engineering solutions in land, sea, air, and space transportation. In fact, researchers have discovered that a 10% weight reduction in today’s vehicles delivers a 6% fuel economy improvement. The average vehicle in North America is estimated to contain around 208kg of aluminium,and approximately 10kg of magnesium. These materials have a long usage history in the automotive sector. However, the next generation of thinkers believe there are a suite of lighter materials for improved performance and reduced costs in the sector.
Similarly, light alloys are critical for the aerospace industry, where approximately 70% of commercial aircraft airframes are made from aluminium alloys. In fact, the Wright brothers used aluminium for the engine parts on their first flight in 1903. This was also the first time that an aluminium alloy had been heat-strengthened. But the jumbo jets of today are flying further and carrying a greater payload, which means they demand more consideration about the materials being used. Even when one kilogram of metal is saved in the design of an aircraft, it can lead to crucial economic savings in terms of weight, construction spending and fuel use. Specifically, aluminium, magnesium, and titanium are light metals with commercial importance for local manufacturers. These metals, and their alloys, are the three most common metals used in industrial systems. They also have a wide range of commercial benefits. For example, aluminium is one of the most versatile materials, while titanium is resistant against corrosion.
Aluminium Alloys
In the world of materials science and manufacturing, aluminium is a proven winner. The metal boasts wide fabrication abilities by forming, machining, or welding. These lightweight, non-ferrous metals also offer corrosion resistance and strength. Aluminium also offers electrical and thermal conductibility, which is a key consideration for researchers and commercial partners alike. Its durability is also met with versatility, as aluminium is present in almost every industrial and commercial device.
However, like many metals, aluminium has a downfall. The metal has a low melting temperature (660°C), which limits the maximum temperature in certain applications.
Magnesium Alloys
When combined with another alloying metal, like copper, zinc, or aluminium, magnesium alloys offer lightweight possibilities that are crucial in the manufacturing sector. Their decent ductility, fair corrosion resistance, and moderate strength means they have been used in several industries and applications like aerospace and marine. Crucially, pure magnesium is highly flammable. Although it is challenging to ignite, this remains a key concern for some sectors. Flame temperatures of magnesium and some magnesium alloys can reach up to 3,100°C.
Titanium Alloys
Titanium alloys are known for their lightweight, resistance to corrosion and their strong capacity to withstand extreme temperatures. Titanium is typically alloyed with tiny amounts (6% and 4%) of aluminium and vanadium—a concoction that has a solid solubility, depending on the temperature. Australia has 51% of the world's known titanium ore deposits, which positions researchers to take advantage of the nation’s vast manufacturing capabilities.
Research and Development
Latrobe Magnesium is an Australian company who are drawing on industryfocussed research to transform brown coal waste into a valuable mineral.
This objective is securing the company as a global manufacturing powerhouse, and positions Australia as an international source of magnesium. China is a dominant player in the global magnesium market. It produces over 85% of the world’s magnesium supply. While the process of making magnesium is energy intensive, the automotive sector relies on this material.
Magnesium is an essential part of aluminium alloys and has become an increasingly popular mineral because aluminium cars are lighter than older vehicles made from steel.
Latrobe Magnesium seeks to draw magnesium metal from fly ash, which is a common waste product when brown coal power is generated. The company is drawing on its research and development initiatives to position Australia as an alternative magnesium supplier. It has patented the ground-breaking technology in every country that has brown coal deposits and has plans to licence the intellectual property to global markets. A $40 million pilot plant will also enhance the company’s standing on the world stage. Specifically, the company is seeking to penetrate the United States and European markets, where there are growing restrictions on vehicle emissions. This is creating a demand for fuel-efficient and environmentally sustainable cars.
Similarly, light materials are also taking to new heights in the aviation sector. Monash University is at the forefront of metallurgical research, which is attracting the attention of some of the world’s biggest companies. Aviation manufactures are on the hunt for materials that are lighter, yet stronger, safer, cheaper, and environmentally sustainable. It is a major challenge for a sector that is experiencing vast competition from new manufacturers in Canada, China, India, Brazil, and Russia. There are also legal and environmental frameworks to meet, like the European Union’s greenhouse reduction targets. Professor Xinhua Wu from Monash University said the research team is working at the atomic level. “In metallurgy, just a few atoms in a million added to an alloy can influence engineering at the macro-scale; how we control the homogeneity of metal sheeting when it is rolled, or the integrity of the metal when it is fabricated into a component." One of the Professor Wu’s projects is an aluminium alloy that will reduce the weight of an average aircraft by 30% to 40%, make it twice as fuel-efficient and still meet structural requirements. "From just a materials research perspective, without worrying about costs, we can make the most wonderful metal and alloy materials.” “But the goal is not just to develop stronger, lighter, more durable and more stable metals. They must also be produced through more efficient and cheaper manufacturing with lower energy consumption, both during construction and during the aircraft's operational life over 25 or more years.” "This is what makes industrial science exciting. Yes, the fundamental science must be good, but it is the industrial science that has to deliver this material, functionally and costeffectively, to industry. And it doesn't stop with developing the material; new manufacturing processes have to be designed for each new material developed,” Professor Wu said. This research was inspired by Professor Wu’s 20 years with RollsRoyce’s aerospace division. She described the experience as learning experience at "a technology-driven company and world leader in materials technology and manufacturing". Professor Wu is also involved in the development of titanium and titanium aluminide alloys. Some of her work has sharpened the approach of manufacturing technologies to produce complex 3D parts from a computer design. This process is expected to reduce material waste by 90%. It will also lower manufacturing costs by 30% to 50%, and the lead time will drop to three months for certain components. It is a win for manufacturers who have pivoted during the COVID-19 pandemic, but do not want to compromise on environmentally conscious choices for their business. Australia’s research hubs and institutions are the backbone of ensuring tailored research meets enduser requirements.
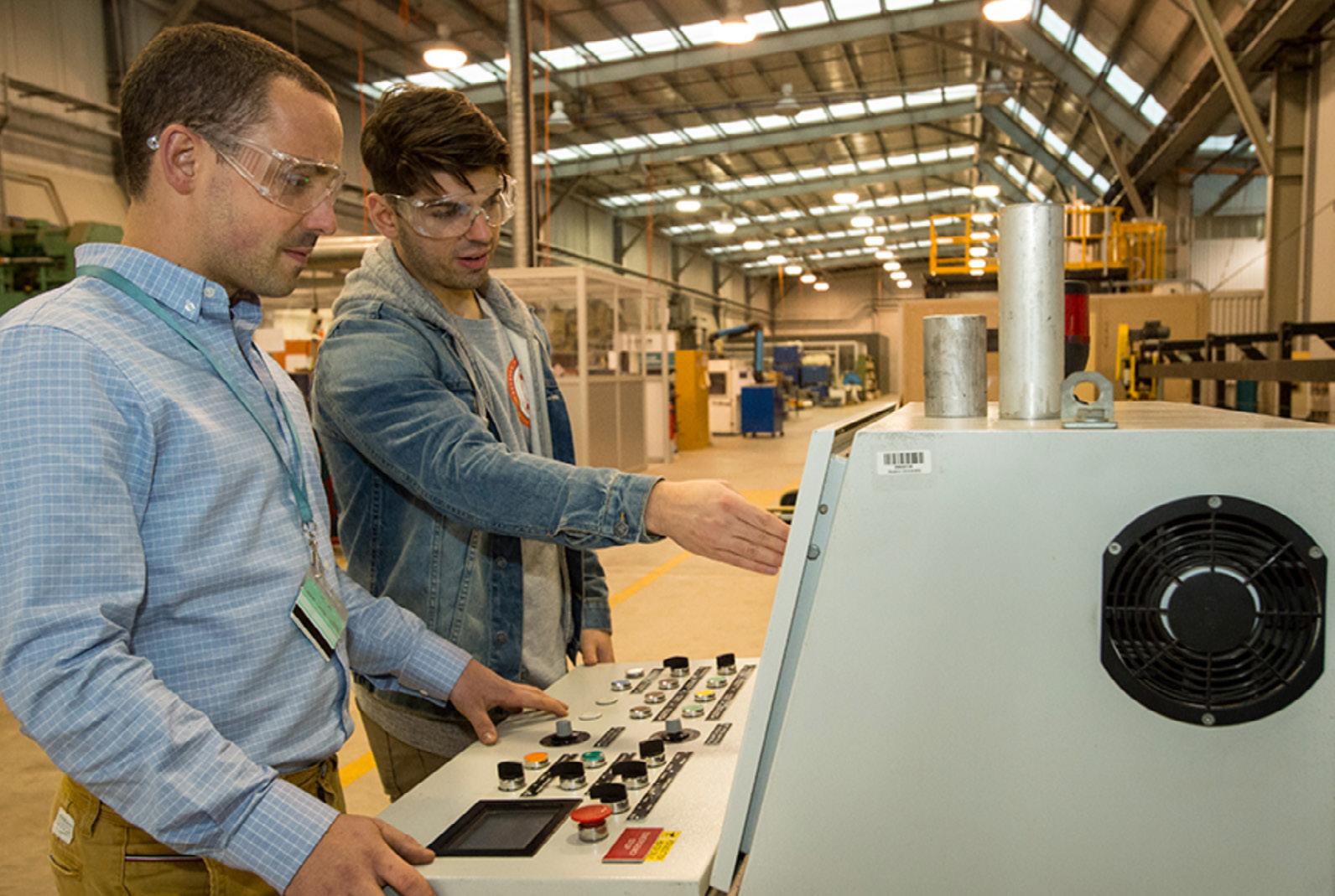
Deakin University
Deakin University’s Institute for Frontier Materials (IFM) is a pioneer in the development of smarter solutions for the future.
IFM’s research areas seek to address material challenges in the energy, mining, environment, health, transport and manufacturing sectors. For example, Dr Thomas Dorin’s research is focussed on renewable solutions for the transport sector, which accounts for around 20% of global greenhouse gas emissions. Dr Dorin believes aluminium could reduce the weight of vehicles and lower emissions.
To make this dream a reality, Dr Dorin has used scandium, a metallic d-block element that can improve the performance of aluminium. His research will determine the interactions between scandium and other alloying elements. He has also pioneered RAPDID—a software that can reduce the production and costs associated with alloy manufacturing. “Traditional alloys are complex systems of up to 15 different elements and the processing route can include up to ten different thermo-mechanical stages.” “This results in an extremely complex system and the best solution is unlikely to be found with traditional trial and error (iterative) methods,” Dr Dorin said.
The software uses adaptive experimental design to ensure the best results under strict time constraints.
Dr Dorin said a nickel super alloy derived from traditional trial and error methods would take around twoand-a-half years. But RAPID produces an alloy with a 13% improvement in properties within six weeks. The researcher was recently the recipient of the prestigious Discovery Early Career Researcher Award from the Australian Research Council.
This award granted Dr Dorin with $407,000 to pursue academic research on new classes of aluminiummagnesium-silicon alloys through the inclusion of scandium. IFM prides itself on end-user driven research. As such, the research hub has partnered with also Callidus Welding Solutions to improve the life of metal components used in mineral processing. Researchers are working together on a $3.9 million Cooperative Research Centre project to create engineering solutions that avoid severe erosion and corrosion in metal reactor components. “The partnership we have developed with Deakin is a true win, I hope for both teams. Innovation although a bit overused today is at the core of our DNA as a company said Gary Lantzke, who is the Chief Executive Officer at Callidus.
The project focusses on the novel component design to double a component’s life, which is poised to save millions of dollars across the industry. IFM believes in a strong pipeline of future research trailblazers. The facility is responsible for graduating more than 30 PhD students each year, and training 80 post-doctoral researchers at any given time.
Australian National University
The Department of Electronic Materials Engineering at the Australian National University is a launchpad into a suite of world-class research underpinned by state-of-the-art facilities
The scope of research is endless: • Light-matter interaction at the nanoscale
• Physics and engineering of photonic, electronic and quantum materials • Integrated and meta-optics • Physics of nanoscale devices • Advanced materials for the energy sector
• Bio and chemical sensing The Research School of Physics undertakes an ambitious research program. Researchers use state-of-the-art facilities like an ultra-high speed laser ablation to modify and create nanoscale ablation products. Some of the outputs include ultra-light carbon foams.
In addition, the school undertakes mechanochemistry research, which generates powders with a unique physical property. Researchers are actively engaged in creating a range of selective nanostructures that are commercially viable.
International Players
Across the ditch, the University of Auckland boasts the Light Metals Research Centre (LMRC). This facility leans into the world of smelter-grade alumina, where researchers have expertise in aluminium smelting. LMRC hosts the world’s first purposebuilt centralised control system that can alter aluminium smelter potline operations. The Gen3 device includes a specific software that creates a controlled and managed research environment. Likewise, the University of Cape Town develops competitive research in light metal alloy products. For example, powder metallurgy processing routes are analysed to form a cheaper supply of titanium metals for local manufacturers.
The team of researchers collaborate with representatives from the transport, medical and chemical industries by drawing on South Africa’s rich energy and mineral resources.
Commercial Partners
Institutions rely on solid end-user arrangements, where research comes to life.
One company, data M, is specialising in sheet metal processing, alongside a range of consulting and engineering services.
Many companies turn to data M for support to assist with insufficient design capacity; resource allocation; time to market solutions; and knowledge of crucial processes. For example, data M tune into the demands of clients who are seeking lightweight construction improvements for their services. The company has pioneered the COPRA software package, which is a roll-forming design tool that plays a
crucial role in the development and validation of high-strength and ultrahigh-strength steels. For over 30 years, data M has developed roll-formed parts for the automotive industry, including cars, commercial vehicles and bespoke trailer components. COPRA offers customised and predefined lightweight outputs, which save time and costs for end-users. The tailor-made approach is essential for meeting respective customer requirements. Similarly, Quickstep is Australia’s largest aerospace and composites organisation. The company was recently awarded a $30 million maintenance contract by Jetstar for its V2500 Engine Nacelle. The airline has 53 Airbus A320 aircraft, which will be serviced by Quickstep Aerospace Services. “In our opinion, the Australian aviation sector should see a strong rebound from the pandemic during 2022.” “Our Tullamarine facility is well placed to offer highly competitive aftermarket solutions both domestically and across the Asia-Pacific region,” said Mark Burgess, who is Quickstep’s Chief Executive Officer
The deal marks the first contract to be awarded to an Australian independent maintenance, repair and overhaul provider.
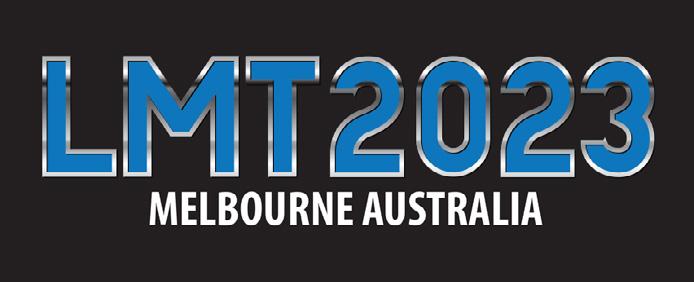
LMT2023 Light Materials Technology Conference
Light materials will be on full display at the LMT2023 Light Materials Technology conference, which is calling for abstracts. The biennial event gives industry professionals and researchers an opportunity to share knowledge and engage in networking across light materials and their applications. The event is curated by Materials Australia and will share success stories and developments from across science and technology linked to aluminium, magnesium and titanium alloys. It will also focus on their translation into commercial products. Delegates will have a front-row seat for interactive presentations that address challenges and opportunities in the light metals industry. LMT2023 is scheduled for 9–12 July 2023 in Melbourne.
For more information, please visit: lmt2022.com
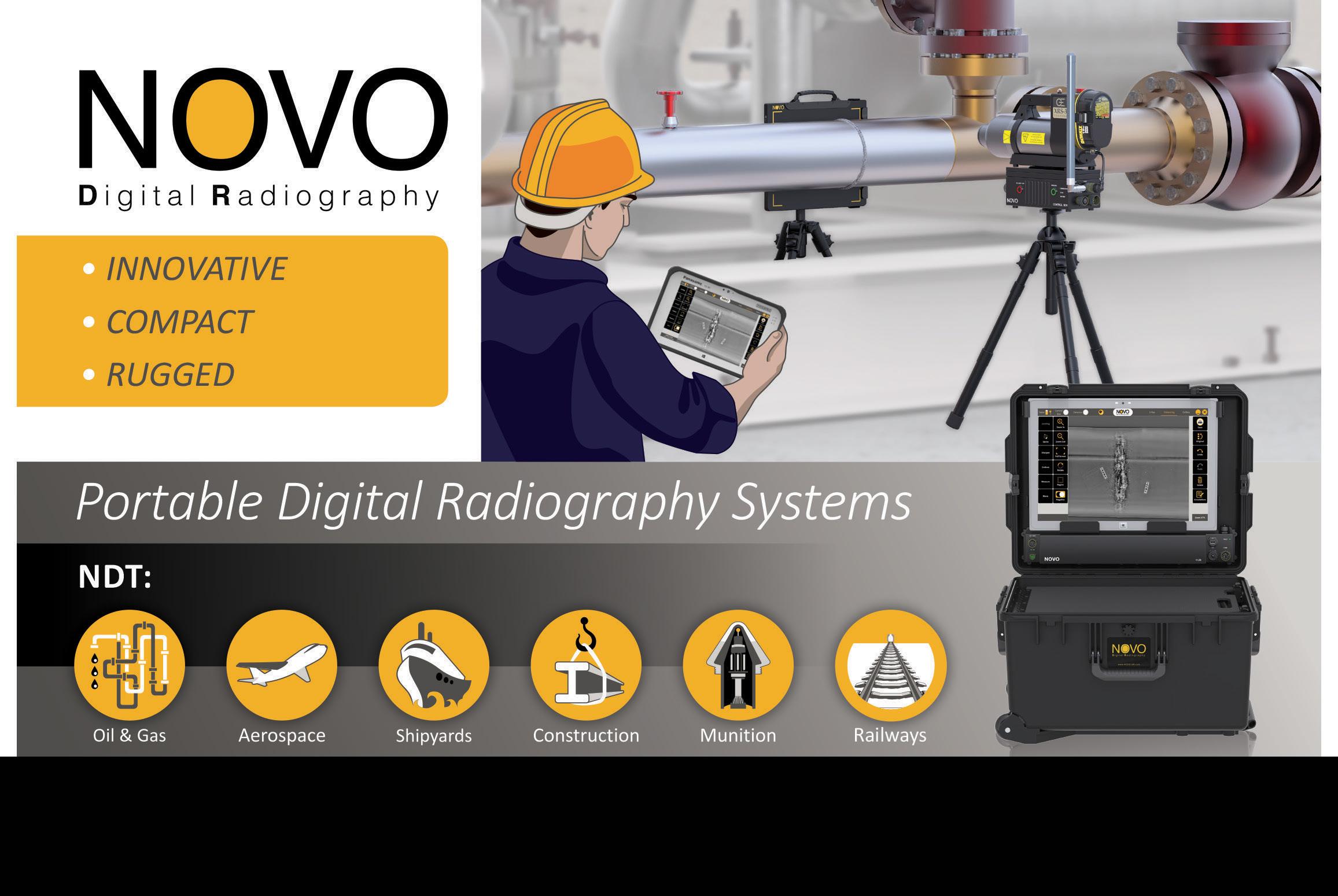
Opening ATLAS To A World Of Opportunity
Source: Sally Wood
From the days of Henry Ford’s Tin Lizzie, commercial vehicles have been primarily made of steel. Despite its cost-effectiveness and durability, steel is a very heavy material.
As such, Australia’s next generation of automotive movers and shakers are at the forefront of ATLAS, where they draw on fresh research initiatives to design and manufacture lightweight structures.
ATLAS, or the ARC Training Centre in Lightweight Automotive Structures, is administered through RMIT University. It brings together expertise from Deakin University, the Australian National University, and lead industry partners under the same roof. In all, there are 12 local and international partner organisations including the CSIRO, who are tasked with addressing Australia’s challenges in light weighting. The centre seeks to develop and design new technologies, manufacturing processes and energy storage designs to reduce Australia’s carbon dioxide emissions in transportation. John Davis is an American Emmy Award winner, and the host of the MotorWeek automotive program. He believes lightweight materials are crucial for the longevity of the automotive sector but there are some challenges. “If we all could afford Bugattis, then carbon fibre would be an easy answer. It’s half the weight of steel and four times stronger. But at $15 per pound, it’s more than three times the cost.”
ATLAS seeks to bridge this gap by developing high-performance materials that can be used by Australian manufacturers in the automotive sector.
For example, the centre works with highly formable metal alloys and carbon-fibre composites that are helping the next generation of manufacturers.
ATLAS boasts four key research themes, which drive its innovation: 1. Lightweight materials 2. Integrated multi-material structures 3. Design and advanced structures 4. Whole of life assessment
The program is run by Professor Stuart Bateman, who also serves as the Director of the ARC Training Centre in Lightweight Automotive Structures. Professor Bateman has vast expertise in polymeric materials for advanced manufacturing across disciplines like additive manufacturing, and biomimetic surfaces and interfaces.
He also believes in the commercialisation of research outcomes.
Lightweight Materials
Lightweight materials are the backbone for modern automobiles. They offer an enhanced fuel economy and environmentally sustainable travel opportunities. They also maintain crucial safety and performance features.
The United States’ Department of Energy believes a 10% reduction in the weight of a vehicle, can lead to a fuel improvement of between 6 and 8%. When lightweight materials are used, like carbon-fibre and polymer composites, it can also reduce a vehicle’s framework by up to 50%. ATLAS undertakes three projects within the lightweight materials research theme:
1. Surface sizing of carbon fibres 2. Rapid cure on-demand resins for automotive composites 3. Influence of heat treatment and chemical composition on the bendability and toughness of 6,000 series aluminium
These projects analyse the structural performance of vehicles by optimising their sizing for thermoplastic composites. They also seek to uncover the relationship between cure chemistry, trigger mechanisms, and material properties, and develop timetemperature transformation curves. In the United States context, lightweight components, alongside high-efficiency engines in around 25% of vehicles is estimated to save over 5 billion gallons of fuel per annum by 2030.
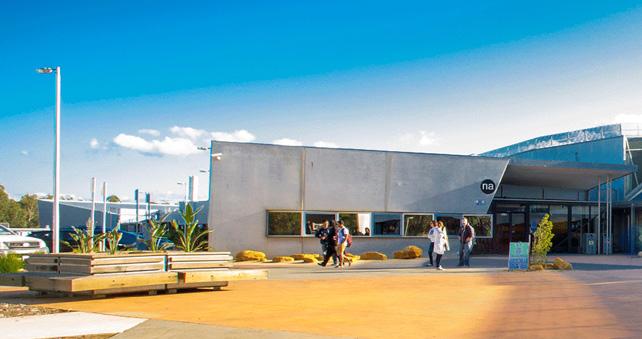
Integrated Multi-Material Structures
ATLAS researchers are focussed on the design and usability of multi-materials structures to power the automotive sector’s next generation of smart vehicles.
The centre undertakes four projects within the lightweight materials research theme:
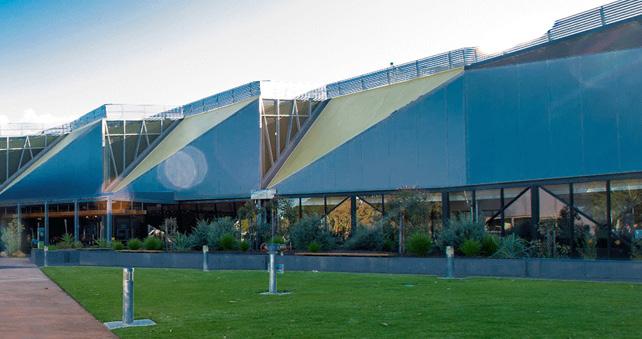
1. Hot stamping light alloys 2. Novel carbon fibre pre-form 3. Additive manufacturing of gradient lattice structure 4. Production of longitudinal components by combining flexible roll forming and free-forming Together, these projects seek to reduce the time and production costs for ATLAS’ industry partners.
Design and Advanced Structures
This research theme considers additive manufacturing, flexible roll forming technologies and multi-material joining techniques to grant a suite of new opportunities for manufacturers. Australia’s manufacturing sector is the backbone of the nation’s economy and requires research to unlock high value products for local and international markets.
Within this research theme, there are four key projects: 1. Multi-materials joining using 3D printed micro-pins 2. Integrated energy storage structure 3. Non-destructive evaluation of laser beam welded and brazed joints 4. Multi-material design solutions In one project, PhD student Simon Inverarity from RMIT University recently developed novel methods for joining composite to aluminium components. His work trialled a series of fresh techniques in composite development, computer simulations and failure analysis. “We will create micro-pins with unique geometric design to minimise the manufacturing time and increase the structural performance of light alloycomposite joints for vehicle assembly,” he said.
This ATLAS research project is a gamechanger for the current methods of composite-to-metal joining. It will also pave the way for a renewed approach for methods like pinned joints, self-piercing rivets and thermoplastic welding. “An adhesive layer can be added and cured as the component goes through the paint oven to further improve the fatigue and crash performance of joints,” Inverarity said.
Whole of Life Assessment
This research theme considers the environmental, economic and societal benefits that the next generation of lightweight materials can offer. Researchers focus on how certain design decisions can impact the overall outcome of a vehicle. These decisions include energy consumption, material selection, and recyclability, which is crucial for a material’s end-of-life plans. “Whether you’re seeking maximum performance or maximum fuel economy of a vehicle, reducing weight is a sure-fire way of achieving meaningful results.” “But striking the ideal balance between light, strong, safe, efficient, and costeffectiveness is a complicated feat of engineering,” said John Davis from MotorWeek.
Paving The Way For Industry Adoption
The ATLAS research training centre relies on its worldwide network to bring knowledge to life. There are also several industry organisations like the Ford Motor Company; Australian Rollforming Manufacturers; Composite Materials Engineering; Quickstep Automotive; Capral Aluminium Centres; M.T.M Pty Ltd; Data M Sheet Metal Solutions; and Shape Corporation. Ford is a trailblazer for putting research into practice. The company is incorporating Dura-Touch—a new sustainable material—into its luxury brand.
The material is expected to be rolled out on its Lincoln Corsair models, as a lighter and more cost-effective alternative.
The Ford Authority, is a hub for enthusiasts of the Ford Motor Company, who said “this material is also more durable, easier to clean, and more stain resistant than real leather.”
World-leading scientists and industrial engineers from 16 organisations across Australia, the United States, United Kingdom and Germany make up the industry-focussed environment at ATLAS.
Project teams work in collaboration with the Imperial College London; University of Bristol; Michigan Technological University; and Friedrich Alexander University Erlangen in Nuremberg.
CSIRO’s Pivot Towards A Future Of 3D Printing
Source: Sally Wood
Australia’s national science agency, CSIRO, has been transforming people’s lives for over a century. Throughout history, the organisation has shifted its operations to better align itself with Australia’s science objectives and focus on emerging opportunities across industry. In its early years, the organisation was tasked with exploring control measures for the prickly pear pest, which was impacting the agricultural sector on Australia’s east coast.
By the 1950s, CSIRO’s research focussed on animal pests and diseases; fuel problems; and the preservation of food.
In 2014, CSIRO simplified its research practices to better connect with industry and shift its attention towards ‘impact science’, which address the nation’s biggest challenges. As such, researchers and scientists began their ‘ore to more’ project, which sought to expand the national value chain.
This approach builds on Australia’s ore reserves and wide-ranging knowledge on additive manufacturing, or 3D printing, and material science, to deliver a more resilient future for industry. Additive manufacturing has a range of benefits: • Waste material reduction • Lower labour costs • Increased speed • Product customisation • Scope to produce complex parts The CSIRO approach works around the pillars of economic viability; environmental; and cost-effectiveness. The metal industries branch seeks to position Australia as a world leader in novel metal production by making additive manufacturing a more costeffective and robust process.
Lab22 Creates Value For Australia’s Manufacturing Industry
Additive manufacturing is the next frontier in Australia’s manufacturing capabilities. It offers a suite of advantages over traditional manufacturing methods and leads to a significant increase in productivity and efficiency. CSIRO understands the importance of connecting research with industry. As such, CSIRO is an active partner and end-user driven organisation, where fresh process in metallic additive manufacturing is passed onto local manufacturing hubs. For example, the Lab22 Innovation Centre works to increase metallic additive manufacturing across Australia.
Since it opened in 2015, the centre has become one of the nation’s frontrunners for metallic additive manufacturing. The metal 3D printing sector is expected to reach a market value of $10 billion by 2030. As such, Lab22 is well-positioned to take advantage of this by linking itself with key players in the aerospace, biomedical, defence, and sports manufacturing sectors. Lab22 offers advanced machining; surface engineering; metallic 3D printing and laser heat treatments to create a range of endless possibilities for industry. Some of the facilities available to researchers include: • Arcam A1 • Concept Laser M2 • Optomec LENS MR-7 • Voxelject VX1000 • Cold Spray Plasma Giken Researchers and industry are able to connect and use the facilities to print materials from sand, titanium and other metals.
The machines can also handle several other ferrous metals and non-ferrous metals. The facility has a patented novel titanium powder production process, which has had commercial success.
For example, ‘Flying Machine’ is a bicycle company based in Perth, who are using Lab22’s innovation in their bespoke products. “CSIRO are the only titanium printer in the southern hemisphere, so for us it not only was cheaper getting it here in Australia than from overseas, but it was also quicker in its turnaround time,” said Sam Froud, who recently designed a bicycle for the company. The bicycles capitalise on the 3D printed titanium frame with a carbon belt drive.
“I’ve just been so stoked to be able to get on it finally and go for a ride.” “I actually went to ride around the block, and then ended up riding right down into the city and back. It’s like the titanium’s just completely blown my mind about how it was going to be,” Froud said.
This Lab22 innovation unlocks the capacity for anyone to own a 3D printed bicycle that is made to fit.
Low-Cost Titanium Wire For Additive Manufacturing
CSIRO has developed an innovative process to transform inexpensive alloy waste into a high value wire product, which is a winner for the additive manufacturing market. This method of producing titanium wire is an Australian first.
“The result is a product that is significantly cheaper than titanium wire made by conventional processes,“ Dr Robert Wilson said.
Researchers used low-cost titanium alloy particulates to produce a wire, which can be used to make a series of 3D printed parts. The global market for titanium wire is estimated to be worth over $200 million.
In this instance, the 2.5mm to 3mm titanium wire can also be used to produce metal powders for 3D printing.

The Chief Executive Officer of Amaero International, Barrie Finnin, said the titanium alloy wire and powders offer a valuable capability for Australia’s growing additive manufacturing sector.
“This technology has the potential to put Australia on the map as a competitive supplier of aerospace grade titanium alloy wire for additive manufacturing and will greatly impact on our global competitiveness,” Mr Finnin said.
Amaero is an additive manufacturing company, which provides an integrated metal 3D printing research, design, and construction program. “Even better, the end product will be comparable to what is currently available overseas, but much cheaper because it is using waste product,” Mr Finnin added.
The patented wire extrusion process is also working to produce 50kg of titanium wire at pilot scale. The challenge for Australia’s additive manufacturing market is onshore processing. However, the Director of the Australasian Wire Industry Association, Richard Newbigin, said this research will bridge that gap. “Currently, Australian additive manufacturers have to source their titanium wire offshore, but this new capability will change that,” he said. Australia is also well represented in other types of wire manufacturing, which grants researchers and industry professionals with a suite of fresh opportunities.
Improving Horse Racing Performance
In a horse racing-first, CSIRO recently produced a 3D printed set of titanium shoes for one Melbourne horse.
A 3D modelling software was used to design and fit a lightweight racing shoe, which is a gamechanger for horse racing. Horse shoes are typically made from aluminium and can weigh upwards of 1kg. But CSIRO’s lightweight solution was able to print four customised shoes within a short timeframe.
John Moloney is a horse trainer, who said the ultimate race shoe should weigh as little as possible. “Any extra weight in the horseshoe will slow the horse down. These titanium shoes could take up to half of the weight off a traditional aluminium shoe, which means a horse could travel at new speeds.” Moloney’s horse has been dubbed ‘Titanium Prints’. The process involved a research team scanning the horse’s hooves with a handheld 3D scanner.
The precision scanning process takes several minutes but its possibilities are endless.
“Naturally, we’re very excited at the prospect of improved performance from these shoes,” he concluded.
Pelvic Organ Prolapse
Source: Zahrina Mardina, Jeffrey Venezuela, Christopher Maher, Zhiming Shi, Matthew S. Dargusch, Andrej Atrens
Pelvic organ prolapse, or POP, is the herniation of pelvic organs such as the bladder, uterus, and rectum due to loss of muscle support. POP affects more than 50% of women in the ageing population—physically demanding activities such as heavy lifting or vaginal labour increase the prevalence of POP. The protruding organs compress the surrounding vaginal nerves, intensify the pain, and reduce women’s life quality. The early treatments of POP are pelvic floor exercises or the insertion of doughnut-shaped polymers, known as pessaries. Pessaries are intended to suspend the prolapsed organs. However, pessaries are hard to fit, prone to bacteria, and inadequate to treat higher grade prolapse. The gold standard for POP treatment is the surgical implantation of pelvic mesh. Pelvic mesh is intended to replace the weakened muscle’s function. The most commonly used material was polypropylene. However, in 2016 the Food and Drug Administration (FDA) reclassified pelvic mesh as high-risk (class III). The reclassification was based on the reported complications as follows: • Exposure: the visibility of the mesh through the vagina epithelium. • Perforation: the tendency of the mesh to come through the entrance of some hollow organs, which could rupture these organs. • Extrusion: the tendency to protrude through an opening such as the vagina. The more generic term erosion is often used rather than the other three terms. The pelvic mesh complications urge the search for alternative materials that could perform better in biocompatibility, mechanical, and degradation behaviour. Our study [2, 3] utilises lightweight, biodegradable metals, namely magnesium alloy, zinc alloy, and iron alloy. The biodegradable metals could be alternative materials for pelvic mesh. The issues with polymer-based mesh are: • Prolonged inflammation response due to its non-degradable nature • uniaxial loading causes pore loosening and hinders tissue integration • Low yield point induces plastic deformation • Susceptibility to creep • Strain hardening of polymeric yarns Biodegradable metals offer advantages over polymer-based meshes. The advantages are: • Completely degrade after the tissue healing is achieved. The degradation obviates the possibility of prolonged inflammation • A bigger pore size provides better resistance to pore loosening, hence promoting integration • A higher yield point ensures elastic deformation during physiological loading • A higher melting point results in better creep resistance Figure 2 provides a schematic of biodegradable metal mesh. One of the most common suspended organs is the uterus. The expected healing time of the supporting tissue is two and a half years. Therefore, given this timeframe, the pelvic mesh should completely degrade into safe ion intakes such as Mg2+, Zn2+, and Fe2+. Some remaining challenges in the use of biodegradable metals are hydrogen production and rapid degradation of magnesium alloys, zinc alloys’ ageing which alters the mechanical properties during storage, and bulky corrosion products and MRI artefacts for ironbased alloy.
References [1] R.U. Margulies, C. Lewicky-Gaupp, D.E. Fenner, E.J. McGuire, J.Q. Clemens, J.O. Delancey, Complications requiring reoperation following vaginal mesh kit procedures for prolapse, Am J Obstet Gynecol, 199 (2008) 678 e671-674. doi:10.1016/j.ajog.2008.07.049 [2] Z. Mardina, J. Venezuela, C. Maher, Z. Shi, M. Dargusch, A. Atrens, Design, mechanical and degradation requirements of biodegradable metal mesh for pelvic floor reconstruction, Biomaterials Science, (2022). doi:10.1039/d2bm00179a [3] Z. Mardina, J. Venezuela, M.S. Dargusch, Z. Shi, A. Atrens, The influence of the protein bovine serum albumin (BSA) on the corrosion of Mg, Zn, and Fe in Zahrina’s simulated interstitial fluid, Corrosion Science, 199 (2022).doi:10.1016/j.corsci.2022.110160
Figure 1. Vaginal inspection indicates (a) pelvic mesh erosion and (b) pelvic mesh exposure. Reproduced from Ref [1] American Journal of Obstetrics and Gynecology, with permission from Elsevier, copyright 2008. Figure 2. Work schematic of the biodegradable metal-based mesh created with BioRender.com
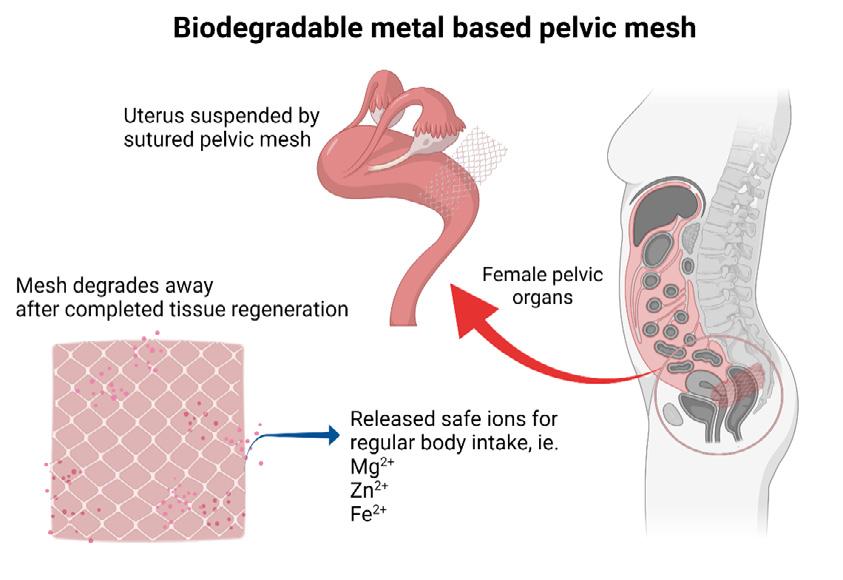