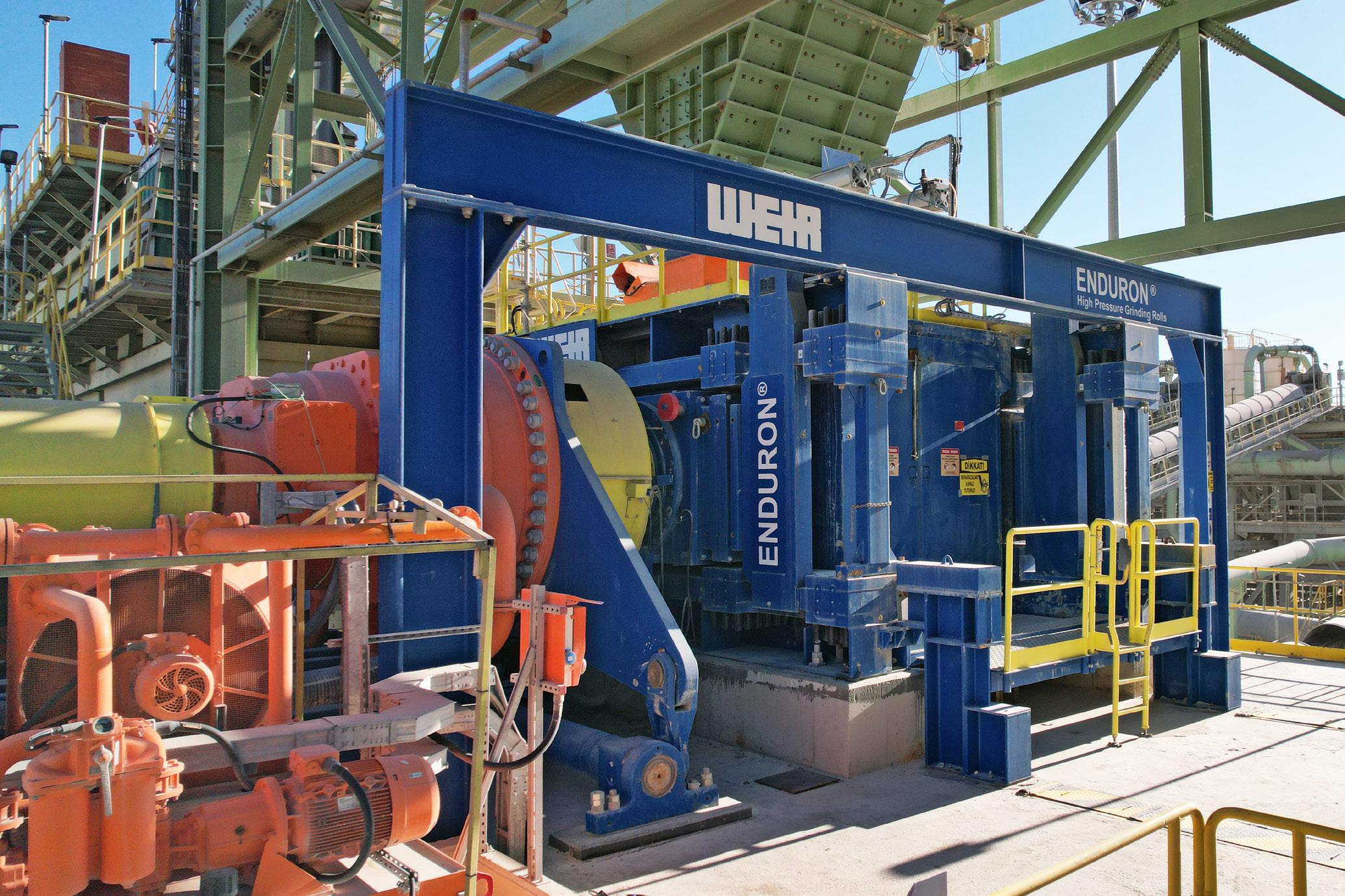
7 minute read
Uutisia alalta: Bjorn Dierx: Replacing conventional technology with innovative solutions can cut energy consumption and carbon emissions in comminution circuits
from Materia 1/2025
There is a growing consensus in the industry that miners need to reduce their carbon, water, and waste footprints. Innovative technologies and partnerships will be integral to ensure that the industry becomes more sustainable in the future.
Every operation has its own challenges, constraints and requirements. Mining takes place in different parts of the world where environmental factors and regulatory frameworks vary greatly. In other words, a one-size-fits-all approach to reduce emissions is neither possible nor preferable.
Weir recently completed a comprehensive study that highlights a significant opportunity to reduce energy use and emissions in comminution by employing a combination of three alternative technologies. The study utilised the World Business Council for Sustainable Development’s (WBCSD) Avoided Emissions Guidance and was independently assured by SLR Consulting Ltd.
Weir’s study demonstrates that there are technologies—and various combinations of technologies—which can be implemented in both greenfield and brownfield operations today to significantly reduce the amount of energy consumed in the comminution circuit.
The alternative technologies were evaluated against a conventional comminution-circuit design for a typical Chilean copper mine processing 1SMtpa. Each circuit was based on a ‘rock-to-recovery’ system boundary, reducing rock directly from the mine to a size that enables mineral recovery.
The four configurations were: 1) conventional comminution circuit based on a semi-autogenous grinding (SAG) mill and ball mill; 2) Weir’s ENDURON high-pressure grinding rolls (HPGR) replacing the
SAG mill at the initial grinding stage; 3) ENDURON HPGR plus vertical stirred mill replacing the ball mill; and 4) the addition of an Eriez Hydro Float coarse particle flotation (CPF) unit.
The study demonstrated that replacing conventional technology with innovative solutions can cut energy use by 40%, while also avoiding 50% of CO2e (carbon dioxide equivalent) emissions. By adopting a system-based approach to technology collaborations, the mining industry can scale up and clean up simultaneously.
Since the study was published, Weir has developed and released further technology to enhance its transformational flowsheet offering. The HPGR discharge can now feed Weir’s ENDURON ELITE screen, allowing miners to reduce their energy consumption even further.
Screening HPGR discharge typically requires a large screen because HPGR circuits operate with up to a 200% recirculation load, resulting in high screen-feed rates. Moreover, because the cut size of typical HPGR screens ranges from 1-4mm, larger screens than those usually employed in typical mining applications are required to ensure optimal performance.
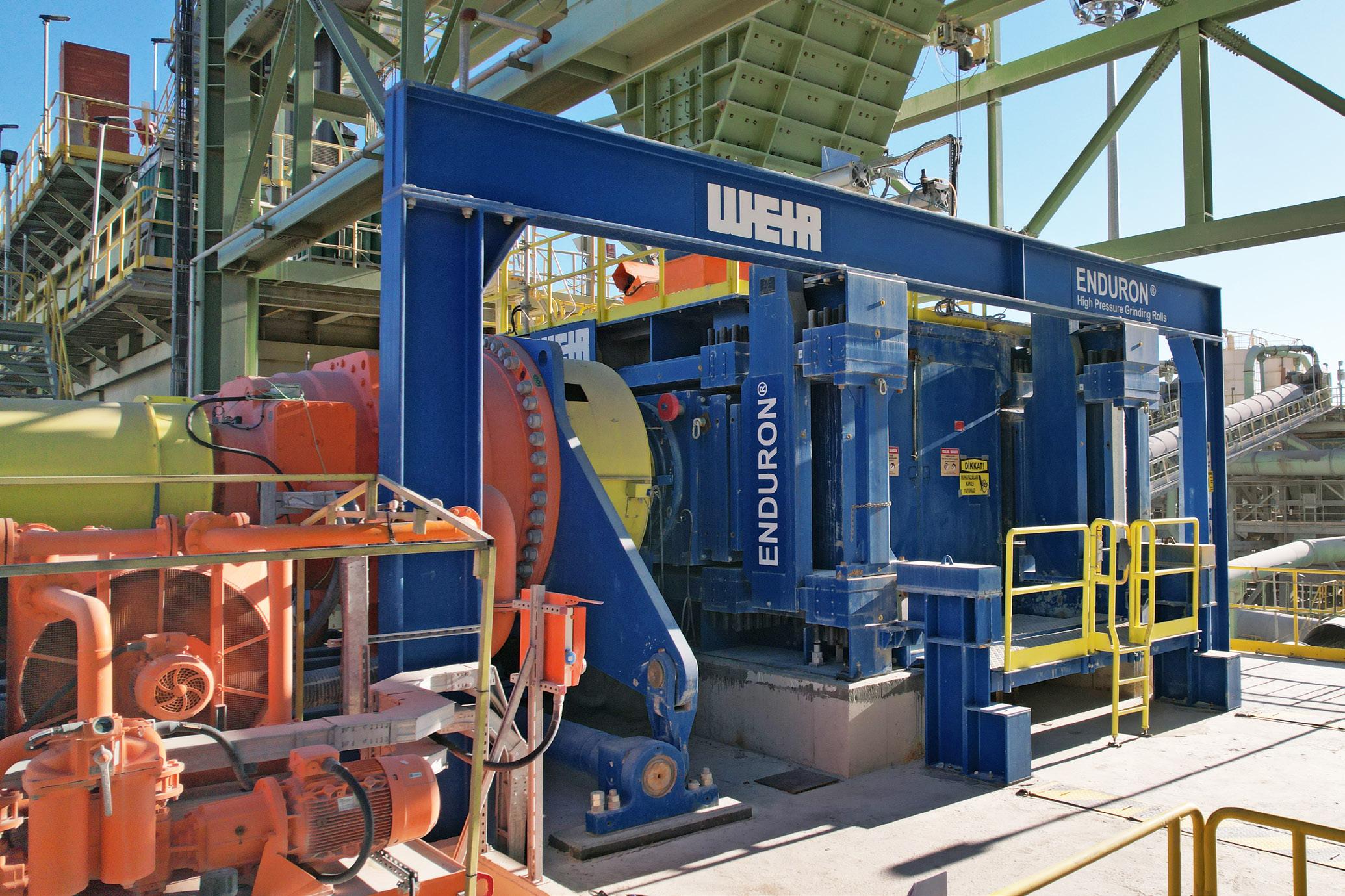
While HPGRs were first utilised in the minerals processing industry over 30 years ago, most concentrators still use tumbling mills for grinding duties. Over the same period, the operating environment has changed significantly, which arises the question: why haven’t flowsheets?
Two of the most notable operational changes are: reduced ore grades and increased ore hardness, and the increased costs in milling consumables, such as power and steel grinding media. These two factors have a direct relationship because processing harder ores requires higher grinding energies, which, when achieved with tumbling mills, typically consumes more steel media, resulting in significantly higher milling costs.
Therefore, to reduce the milling costs, miners can implement more energy-efficient grinding technologies, like HPGRs and vertical stirred mills. Given that grinding power demand is inversely correlated to the final grind size, the ability to recover target metals at a coarser grind size may also significantly reduce operating costs.
ENDURON HPGRs can adapt to changing feeding conditions instantly because the roll speed and grinding force can be changed while in operation. As a result, the most effective, minimal stress-intensity force is applied to the particles to ensure that they break at the given throughput rate.
With grid and energy availability being more heavily scrutinised, comminution equipment that can be swiftly ramped up and down to maximise energy consumption when off-peak energy becomes available during the day can deliver additional cost savings to the owners. There is also a growing demand for vertical stirred mills with higher installed power ratings. The largest mill that has been delivered has 6500kW installed power.
The vertical stirred mill has a vertical mill chamber with grinding rotors (discs with castellations) installed on the central mill shaft. The mill feed is a slurry, pumped through the bottom of the mill and discharging from the top. The mill chamber is filled with ceramic grinding media to approximately 60% of its volume. As the ceramic media is inert, it doesn’t contaminate the recovery plant feed, further improving efficiency.
The grinding media bed moves only in the horizontal plane, which ensures energy isn’t wasted. The vertical mill arrangement, combined with bottom feed entry and top discharge, ensures that the coarse particles don’t short-circuit the mill. The mill shell is internally equipped with shell liners and 360° stator rings between each two grinding rotors, generating numerous consecutive grinding chambers.
The target is that coarser particles, together with the ceramic media, are pushed by centrifugal forces to the periphery of the chamber into the high-intensity grinding zones; while finer particles tend to travel upwards through the centre of the mill, thereby avoiding any unnecessary grinding. This is called selective grinding, where the energy from the mill motor is applied as much as possible to the coarser particles.
Combining these two proven technologies achieves the grinding circuit that delivers the highest recovery and the lowest possible energy consumption. The ENDURON HPGR and screen prepare the feed for the single or double-stage vertical stirred-mill grinding circuit.
Weir’s new ENDURON ELITE screen is our large, high-capacity, double-deck banana screen, featuring Weir’s new ETX exciter technology. With a deck measuring up to 4.3m wide and 10m long, the ENDURON ELITE screen range is designed for screening the high-capacity conglomerated fines created by the HPGR.
The varying slope angles within the screen mean that the feed material is subjected to differing angles of throw throughout its journey along the deck. This benefits the changing PSD on the deck as material gets removed through the apertures. The steep slope angle at the feed end ensures the fine material is rapidly stratified. This creates inter-particle space within the material layer, allowing the fine material to easily reach the deck surface and stratify through the screen media panel apertures.
As the deck angle flattens out towards discharge, the throw angle in relation to the deck becomes more vertical, and the material velocity slows down, which is ideally suited to near-size screening. A typical banana screen will separate most P50 material within the first third of the deck. The second third removes the P80 material, while the last third is used for near-sized screening, which concentrates on the material closest to the cut-size (i.e., P90 and above).
Conventional flotation only achieves high efficiency in a narrow interval in the middle of the range, typically 50 to 130µm. As a result, the tailings of these concentrators are enriched in valuable metal units in both the fine and coarse classes of the size distribution.
Eriez’s Hydro Float CPF represents a major step forward in terms of recovery, by extending flotation efficiency over a size range that is two to three times greater than conventional flotation machines’ limit. CPF produces this result by combining features that facilitate particle collection and mass transfer, including fluidisation water to enhance lift, counter-current contacting, a plug-flow residence time distribution and a zero-order froth.
This amounts to CPF allowing the effective flotation size range for copper to be increased to approximately 400µm. As a result, the P80 is shifted to significantly coarser sizes. This, in turn, reduces the volume of fine feed in the distribution, thereby enhancing overall recovery, reducing energy or allowing increased throughput for the same energy, as well as creating safer, sand-like tailings for disposal. Notably, CPF reduces ball mill energy consumption alone by 30% to 50%.
In conclusion, Weir’s innovative approach and technological advancements provide a viable pathway for the mining industry to significantly reduce energy consumption and carbon emissions. By integrating these solutions, mining operations can achieve greater efficiency and sustainability, paving the way for a sustainable future. ▲
BJORN DIERX, WEIR’S GLOBAL PRODUCT MANAGER OF ENDURON HPGR, AND CORNE KLEYN, GLOBAL PRODUCT MANAGER OF VIBRATING SCREENS