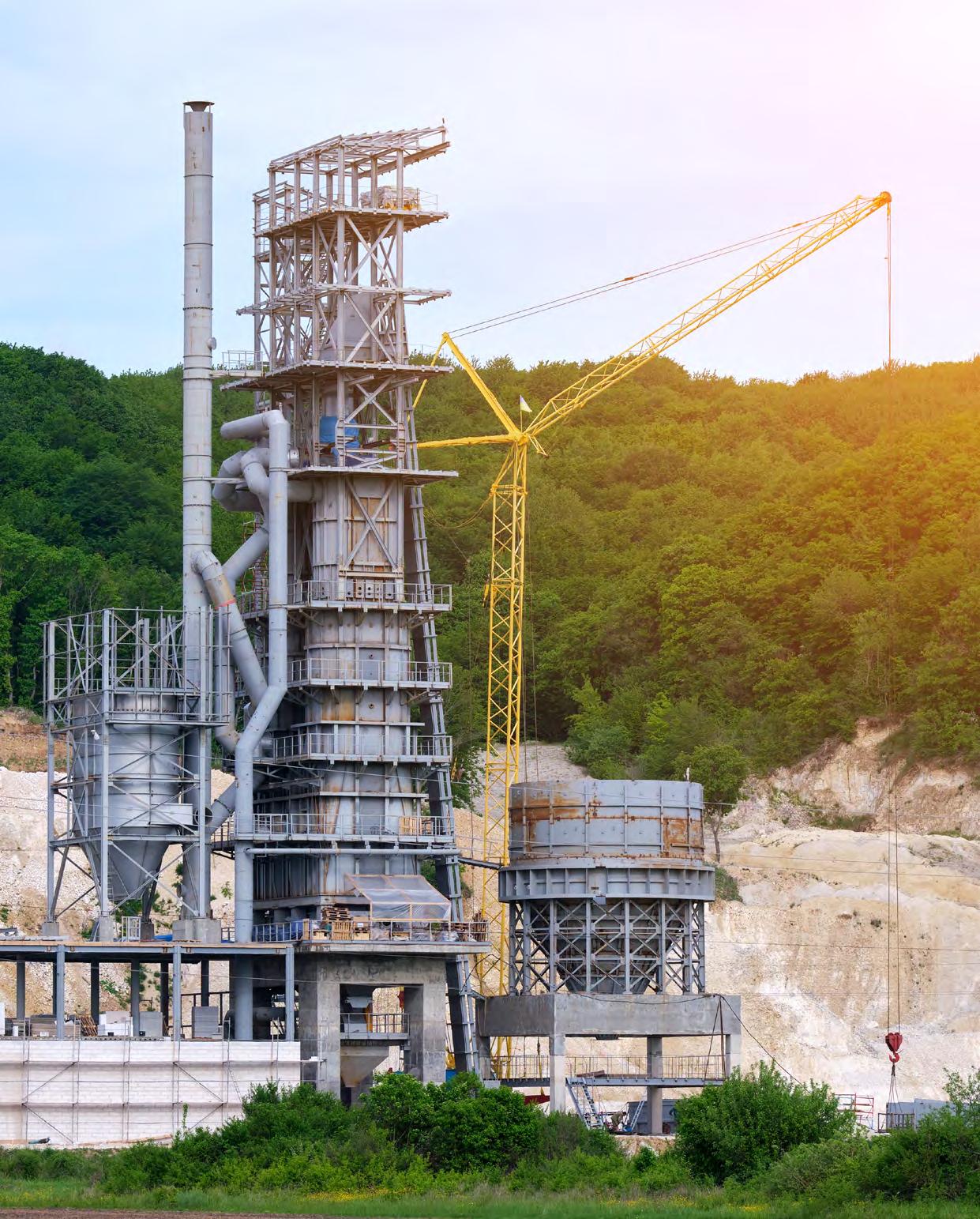
7 minute read
cement
from BTI Winter 2021-22
by Maritime-AMC
GREY MATTERS
With environmental issues top of the agenda for many countries, port equipment that is both efficient and environmentally friendly is increasingly important, particularly when it comes to cement loading and unloading
Obtaining the necessary equipment to improve handling capacity and speed up production is essential at times when financing is tight. Coming up with environmentally friendly solutions is also essential in the current environment.
For example a new ship unloader ordered from Siwertell for use in Kuwait is set to double cement handling capacity at Shuaiba Port.
Bruks Siwertell has won a repeat order from Kuwait Portland Cement for an ST 490-M Siwertell ship unloader, equipped with a new side tilt motion for enhanced through-ship efficiency. It will join another cement handling Siwertell ship unloader in Shuaiba Port, Kuwait City, Kuwait, which has been securing environment-friendly material handling for the operator for over two decades.
“Kuwait Portland Cement has benefited from 20 years of experience using our Siwertell screw-type technology,” says Peter Göransson, sales manager at Bruks Siwertell.
“It knows what our unloaders deliver. Time and again the technology has proven its capabilities, demonstrating reliability, efficiency, and environmental protection in terms of emissions and noise. In fact, the main reason why the operator returned for a second unit is the outstanding operational performance of its original delivery,” he says.
The new unloader, Göransson explains “features a new side tilt motion, which offers an enhanced
reach into the corners of the cargo hold, as well as under the hatch coamings,” he adds. “As a result, less material is left for the clean-up phase, which reduces vessel turnaround times, raising the utilisation rate of the jetty and therefore profitability.
“Also, all Siwertell unloaders offer a layer-by-layer unloading process, which minimises the chance of airborne emissions from avalanches in the cargo hold. The side tilt function adds to this capability,” Göransson notes.
“The new unloader is part of the operator’s long-term vision. It has been designed as a fully assembled, heavy-lift mode delivery, but will actually be transported in break bulk,” he explains. “This enables it to be relocated, fully assembled, to a new location should the customer wish to do so in the future, minimising any transition downtime.”
Planned for delivery to the port in mid-2023, the rail-mounted unit will handle various cement types and deliver a continuous material handling capacity of 800t/h, discharging vessels up 50,000dwt. It will be installed on an existing jetty next to the operator’s older ST 490-F, rail-mounted Siwertell unloader.
Both the current and new unloader will be equipped with a total capacity regulating system, maximising the use of each unit, but ensuring that they do not overfill the downstream conveying system. They can also directly discharge to bulk trucks via a truck loading arrangement underneath the ship unloader’s gantry.
“The new unloader is equipped with two out-loading units,” says Göransson. “This is a great asset, delivering increased redundancy and ensuring that any demurrage costs are kept to a minimum if there is an issue with the downstream conveying system.”
Like its predecessor, the new unloader is also designed to operate in Kuwait’s extreme climate. To accommodate predicted temperature rises in the region, the latest unit can withstand ambient summertime temperatures of up to 55°C.
call for duty
The South Indian Cement Manufacturers’ Association (SICMA) has asked the government to impose higher duty on the import of clinker and cement into India to retaliate against moves by neighbouring countries to implement anti-dumping duties on imports of cement from India.
“South India has excess cement capacity but companies are unable to export to neighbouring countries,” said a pre-budget memorandum submitted by SICMA president, N Srinivasan in December last year. “Meanwhile, India is providing free access to cement from other countries. We therefore request the Finance Minister to impose higher duty for import of cement and clinker from other countries.”
South India – with 180m tonnes per annum capacity – accounts for almost 40% of India’s cement production, although other parts of the country are expected to experience cement shortages going forward.
“We request the government to facilitate movement of cement by providing either telescopic railway freight or some other method,” the memorandum said.
Port investment
Sri Lanka’s Insee Cement has been boosting its activity in recent months, recently signing a memorandum of understanding with the Hambantota International Port Group (HIPG) to supply the Galle cement facility through the port.
The cement company was the first dry bulk customer for the port and the move is a step towards building up its handling of dry bulk cargoes. Chief executive of HIPG Johnson Liu says the port handled a dry bulk volume of over 1m tonnes last year, the first time it has exceeded the 1m figure, with a single customer.
Gustavo Navarro, chief executive of INSEE Cement, says: “Due to the limitation we have experienced in our previous operations, we couldn’t bring bigger vessels with larger volumes. HIPG has been a great business partner for us and the port came up with some creative solutions to get our raw materials delivered efficiently and in a timely manner, which made a positive impact on our operation. This has not only benefited our company, but also the local economy in terms of dollar savings because it reduced freight costs we otherwise paid to foreign vessels.”
INSEE not only helped to develop the dry cargo segment, but brought in a dust controlling mechanism for environmentally friendly operation. The port is going ahead with plans to position itself as a multi-purpose facility.
MacGregor approach
Over the past 60 years, MacGregor cement handling systems have been installed on more than 140 cement carriers sized between 500 and 40,000dwt. Most of these are still in operation.
The system comprises a range of distribution arrangements, both mechanical and pneumatic, which can be combined to deliver the required function and cargo handling rates.
Easily adaptable to any size and shape of vessel, the system is suitable for newbuildings as well as conversions. Overall, the system ensures the reliable and highly-efficient seaborne transportation of cement from producers to consumers all over the world. It is designed for use with a range of different receiving systems and is therefore able to load and unload in many different terminals.
The equipment offers dust-free material handling. MacGregor shipboard solutions for cement carriers are designed with unique screw conveyor technology, which incorporates a totally-enclosed conveying line for environmentally-friendly operation in all weather conditions.
MacGregor screw conveyors are used both for mechanical loading and unloading of cement carriers and for the transfer of cargo between ships and shore based facilities. Screw conveyors are designed to handle powdery cargoes such as cement, fly ash and limestone powder under tough conditions.
BEUMER: SIMPLY OVERCOMING OBSTACLES
COMPANY NEWS
In the mining industry, modern technologies require systems capable of transporting bulk materials efficiently from the quarry to their destination, through rough terrain or populated areas. Beumer Group supplies customised systems such as open troughed belt conveyors and closed pipe conveyors to carry out these essential tasks.
These systems operate quietly and avoid emissions of dust or exhaust gases. Compared to trucks, they are often more energy efficient and can be adjusted to the structure of the premises. They are also able to safely handle steep sloping routes, rivers or road crossings.
The system provider determines the best conveying route and adopts project planning and installation. Beumer Group also ensures that the owner remains sustainably competitive, with cost efficiency aas well as comprehensive customer support.
Essential features
As an essential feature, this technology enables horizontal and vertical curves. Angles of inclination of up to 15° are possible, depending on the characteristics of the material to be transported and the topography, with lengths of several kilometres.
Due to the ability to navigate curves, fewer transfer towers are required – in some cases none are needed at all. This results in substantial cost savings for the customer. The system continuously transports the material even over challenging ascending and descending sections. Furthermore, the open troughed belt conveyors are particularly suitable for high throughputs.
The operator can significantly save energy costs by using belt conveyor systems. This is because electric drives and lowenergy belts are installed. These are less polluting than trucks and also have a positive effect on operating costs.
The engines used in the systems are usually designed to be controllable. This allows the loads to be optimally distributed among the drive units in different operating conditions. If the belt conveyor system is moving downhill, it can operate in regenerative mode. The electrical energy generated from this is then fed back into the public grid via a regenerative unit or can also remain in the system. It is not burned up in braking resistors.
Using Beumer calculation programs, the experts precisely calculate the static and dynamic tractive forces of the belt during the development phase of the system. This is the prerequisite for the safe dimensioning of the curves. Beumer engineers select the type of drive technology and conveyor belts needed on the basis of these calculations, thus ensuring the longevity of the entire system.
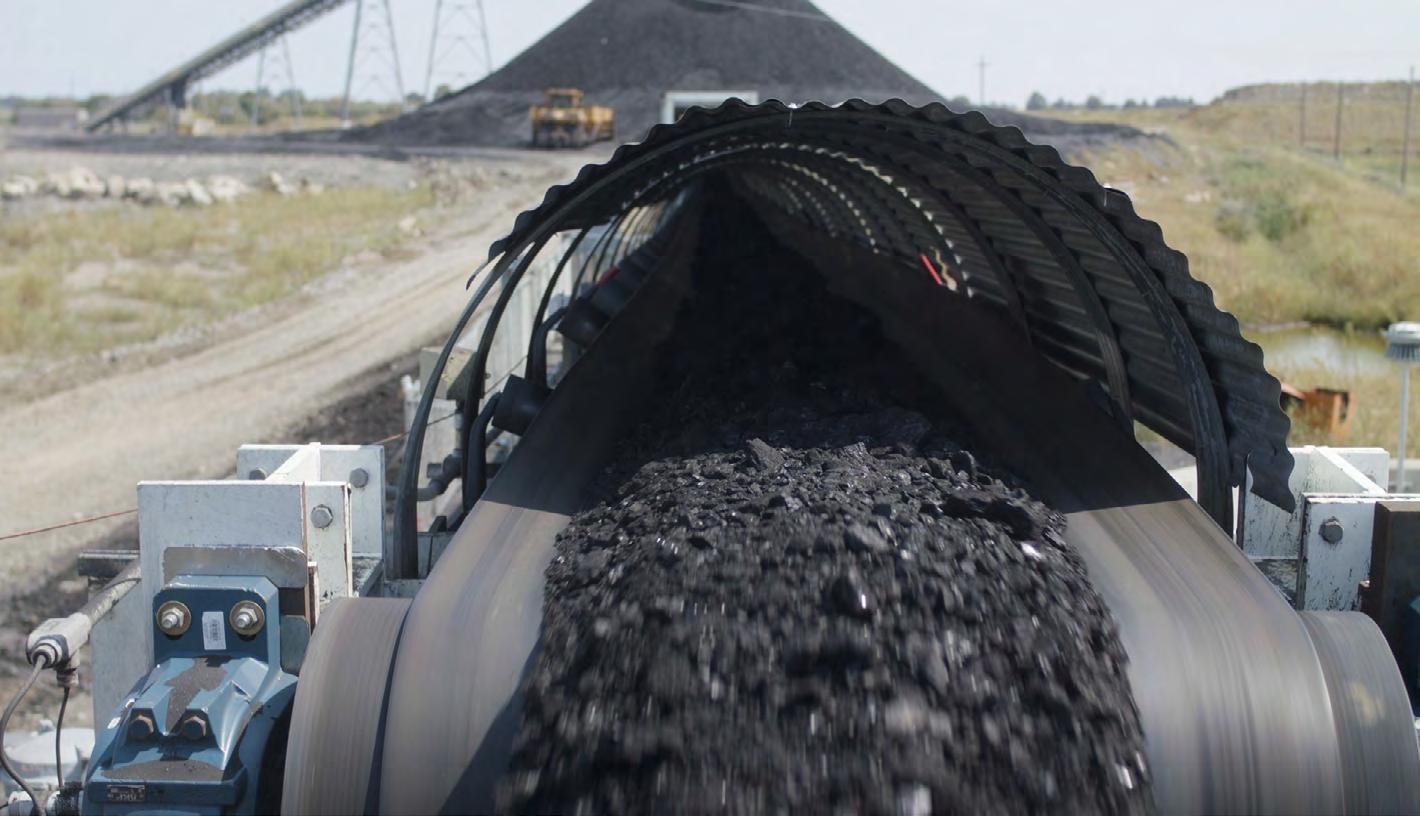
For more information, visit: beumer.com