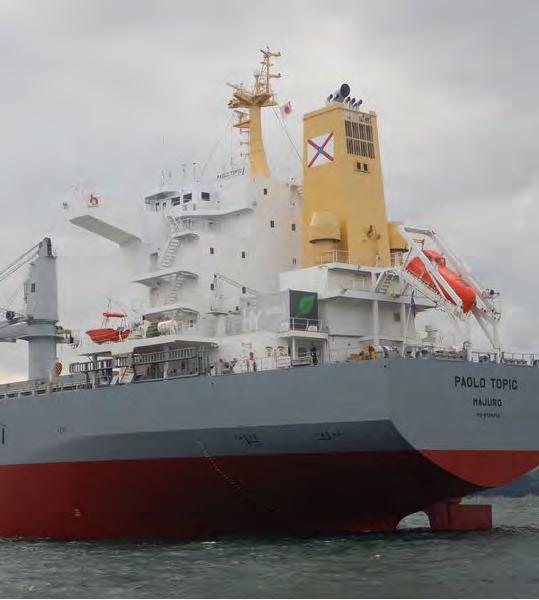
8 minute read
shipbuilding
from BTI Winter 2021-22
by Maritime-AMC
DESIGNS FOR THE FUTURE
As the shipbuilding market remains buoyant, shipbuilders are devising ever-more effective designs that will improve the efficiency, cost effectiveness and environmental friendliness of fleets and overhaul the shipbuilding process
THE COMPACT AND CONTAINERISED WÄRTSILÄ HY MODULE FOR BULKERS INSTALLED ON BOARD THE M/V PAOLO TOPIC © MARFIN There was a strong start to the year in the shipbuilding market with a number of orders, many of them being placed with Chinese yards, emerging during the first few days of the New Year.
There were a lot of orders placed in the gas segment, although a slow start as far as dry bulk orders were concerned, although shipbroker Allied said recently that it expected dry bulk orders to pick up. There were orders from Bocimar for two bulkers and an order by Wisdom Marine for one. There was also activity in the sale and purchase market for dry bulk ships.
Allied said in its weekly assessment that “a modest start took place in the SNP market, given the fair number of units changing hands during the first few days of the year. We already see that buying appetite is firm, while being relatively fairly distributed across the different size segments and age groups. Given that we are only at onset of the year, a lot will depend on how things develop from the side of earnings in the near term.
“To be more precise, as to whether we are about to witness a continuation of the robust momentum, similar to that took place during the previous year or so, or if things are on the verge of a shift.
“On the tanker side, it was a relatively strong start in terms of activity taking place. We have repeatedly mentioned that given the current freight market regime, we can hardly expect any sort of balance in the SNP market as well for the near term (at least). However, given the recent trend noted, we may well being amidst a more sustainable path with an improvement to be noted during the course of the year”.
simulation approach
In a paper produced by Siemens marine industry expert Dejan Radosavljevic, it was revealed that a simulation-driven approach to ship design can reduce costs and speed up design times. As the shipping industry is facing the challenge of reducing emissions and improving vessel efficiency, the greatest impact on meeting these targets “can be made during the ship design phase”, the white paper says.
The paper looks at the simulationdriven design process – “a new approach that moves away from the inefficient ship design spiral and instead makes full use of the digital technology available today. Naval architects can evaluate many more designs and focus on improvements or novel solutions to find the most efficient design.”
According to Radosavljevic: “The traditional ship design process typically starts with a mission statement for the new ship and the process then looks at many different aspects of the design in turn, such as proportions, hull form, general arrangement, structure, ship weight, and so on. Often these evaluation stages are performed by separate teams with no link between the tools they use or the data produced.
“Any changes in requirement or ship design require all aspects to be re-examined, but because of the delay in data transfer, detailed analyses often lag behind the current design. This process increases pressure on profit margins and reduces the time available to create the best possible design.”
The simulation-driven ship design process outlined in the paper rethinks ship design basics. The method uses connected analysis tools and centralised data storage to remove silos and connect all analysis stages to one central master model.
Teams have access to the required data and can always work on the current design. This enables faster design updates and integrated analyses. To find out more, visit: tinyurl.com/SiemensPaper Solar solutions
Technology group Wärtsilä has completed the installation and commissioning of a ground-breaking hybrid power system combined with a PV solar energy system in collaboration with Marfin Management and Solbian, on a bulk carrier, making it one of the most technologically advanced vessel of its type in the global fleet. The installation was carried out on the Paolo Topic, a bulk carrier built in 2016 at the Onomichi Dockyard in Japan and managed by Marfin Management.
The fully integrated Wärtsilä HY Module solution includes an energy management system and batteries that deliver auxiliary power to the grid. When coupled with other sources of energy such as PV panels, the benefits are enhanced. It will address the marine sector’s major challenges to lower operating costs while simultaneously reducing environmental impact.
The solution achieves this through significant reductions in fuel consumption and maintenance needs, while offering cleaner, safer, and more efficient operations. It also contributes to placing the vessel in a positive position regarding the industry’s Energy Efficiency Existing Ship and Carbon Intensity Indicator indexes.
“This is an extremely exciting development that will lead the way to a more sustainable future” says Alex Albertini, chief executive Marfin Management. “We will be able to provide our customers and partners with the most advanced vessel performance and environmental quality, and it is without compromising operational effectiveness or flexibility. We would like to thank all our partners who worked on
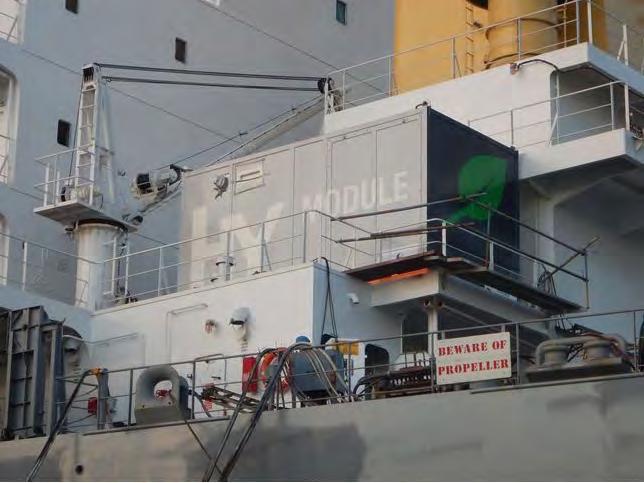
THE COMPACT AND CONTAINERISED WÄRTSILÄ HY MODULE FOR BULKERS INSTALLED ON BOARD THE M/V PAOLO TOPIC © MARFIN THE PV PANELS INSTALLED ON BOARD THE M/V PAOLO TOPIC © MARFIN
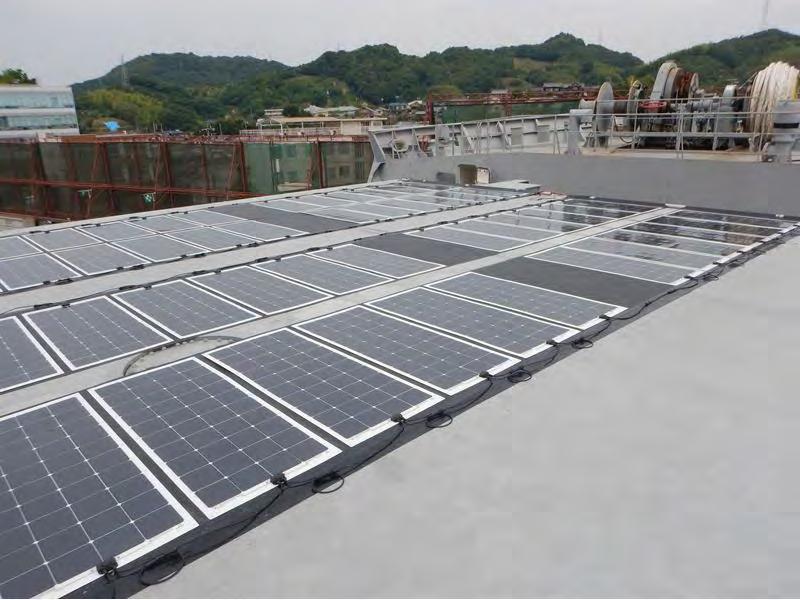
the project for this highly innovative and effective solution.”
“This installation represents a truly significant breakthrough in enabling the bulker fleet to increase both its economic competitiveness and environmental performance. The decarbonisation of shipping is a major priority for stakeholders throughout the maritime sector, and this unique solution helps us take a long step towards reaching this goal,” says Giulio Tirelli, director, business development, Wärtsilä Marine Power.
The Wärtsilä HY Module for bulkers is a compact containerised solution that cuts a vessel’s emissions by optimising the onboard power production, consumption, and management. The HY module gives the possibility to combine and integrate an energy storage system and additional energy sources, such as solar power, with Wärtsilä’s Energy Management System (EMS) to deliver auxiliary power. The EMS has overall control of the engines, batteries, power distribution and, with the installation of solar panels on the weather deck, it is a maritime industry first.
The containerised solution has been placed on the ship’s deck to save space and has been installed without the need for dry-docking.
Steel ship construction
Leading Classification Society ClassNK has released amendments to its Rules and Guidance for the Survey and Construction of Steel Ships. Rules and Guidance revisions reflect the latest results from relevant research and development projects, feedback from damage investigations, requests from the industry as well as changes made to relevant international conventions, International Association of Classification Societies (IACS) unified requirements and national regulations.
More specifically, some of the requirements amended this time are as follows:
In response to industry requests: » Amendment related to the “Material
Marking Methods” In response to changes in international conventions: » Amendment related to the “Ballast
Water Sampling Analysis During
BWMS Commissioning Testing”, the “Bulkhead Valves”, the “Fuel Oil
Sampling Points” and the “Energy
Efficiency of Ships” In response to changes in IACS unified requirements: » Amendment related to the “Welders and Welders Qualification Tests” and the “Anchoring, Towing and
Mooring Equipment”. The PDF files of ClassNK Rules and Guidance are available free of charge via ClassNK’s website at classnk.com for those who have registered for the ClassNK “My Page” service.
Ammonia fuel initiative
Sumitomo Corporation is to launch a full-scale project to design and develop an ammonia-fuelled dry bulk carrier jointly with Oshima Shipbuilding.
In 2018, the International Maritime Organization (IMO) adopted a strategy to reduce greenhouse gas (GHG) emissions from international shipping. In this strategy, the IMO upholds the target of improving the average fuel efficiency of ships used for international shipping by 40% relative to the 2008 level by 2030, and of halving the total GHG emissions from the ships by 2050.
In response, companies in the maritime industry are required to replace the fuels for their ships with ammonia, hydrogen and other substitutes with low environmental impact, and to introduce the equipment that will help them reduce their GHG emissions. As ammonia can be liquefied more easily than hydrogen, the substance is attracting much attention as a substitute fuel for ocean-going ships that navigate a long distance at one time.
Oshima Shipbuilding has been building and selling dry bulk carriers jointly with Sumitomo Corporation since 1973. Sumitomo, jointly with the shipbuilder, will work on the design and development of an ammoniafuelled dry bulk carrier for completion in 2025. After the completion of the bulk carrier, Sumitomo Corporation will own and operate it, thereby helping users of the ship’s transportation service to reduce their GHG emissions across their supply chains.
Sumitomo has been looking at the launch of an ammonia supply business to fuel ships in Singapore. In addition to building an ammonia supply chain, the company, in association with the Singapore government, is putting together operational guidelines and regulations.
Sumitomo is implementing initiatives for the entire ammonia supply chain, including developing an ammoniafuelled ship and making ammonia fuel available at ports, thereby contributing to the decarbonisation of the industry. The company will also speed up its measures to achieve carbon neutrality in 2050 as the long-term target for the mitigation of climate change and to create a sustainable energy cycle.
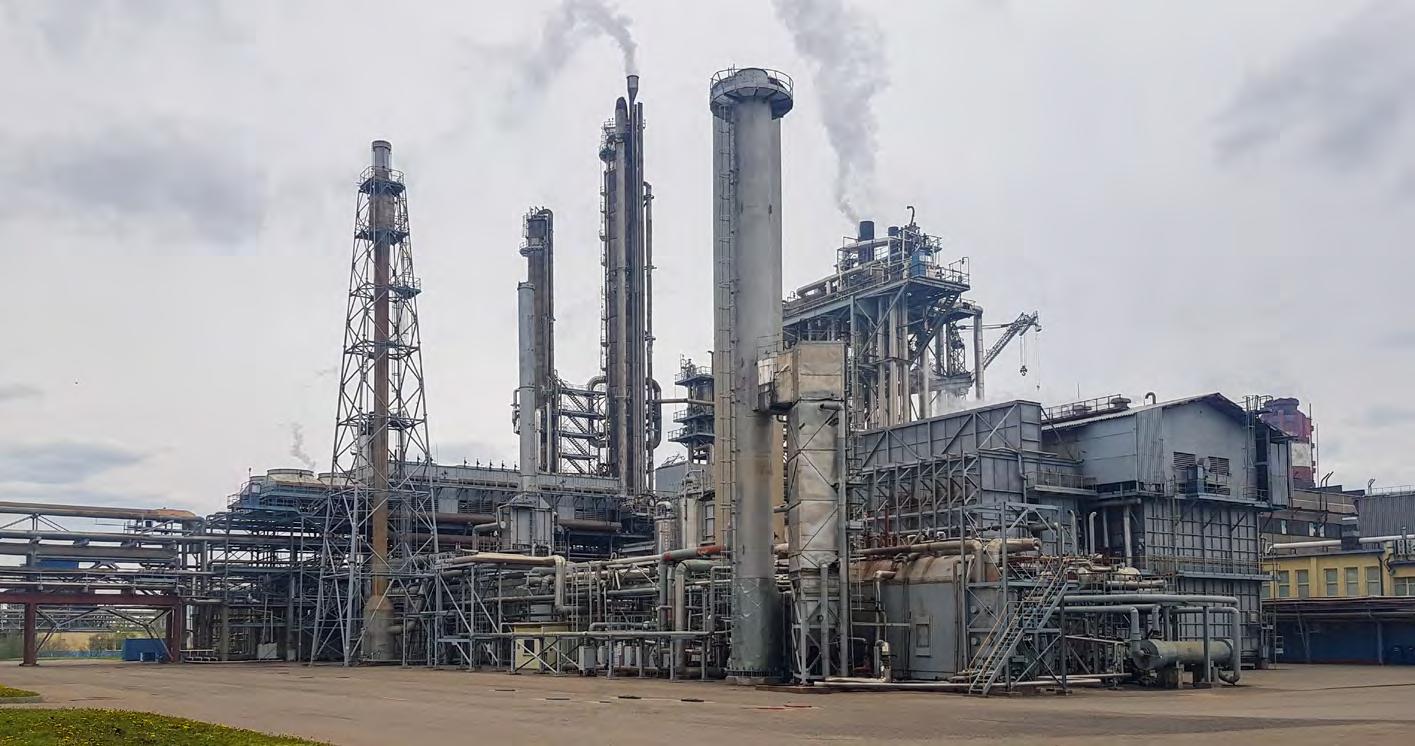