
10 minute read
viewpoint: dust
from BTI Winter 2021-22
by Maritime-AMC
THE LOGISTICS OF PORT DUST CONTROL
Mike Lewis, dust specialist and VP of sales at BossTek, examines the options available to provide an environmentally friendly, efficient dust control solution
It’s early morning and the wind rolls across the water, causing a moderate chop on the surface. It’s a sure sign that any dust generated that day will travel a long way, hopefully just down the port, but possibly further into the nearby community. Operators know it well and hope that any complaint calls come to them instead of the local authorities or Environmental Protection Agency. Community relations is one thing, hosting inspectors and trying to avoid fines is another.
With no natural barriers other than landmasses, port waterways can concentrate winds and raise air speed. Ocean and seaport breezes can be unpredictable and environmental conditions can affect the entire operation, from intake to storage to loading.
PROPER POSITIONING OF DUST CONTROL WHEN LOADING RAW MATERIAL REQUIRES MOBILITY
Port Logistics and Dust
The logistical journey of bulk material at a port begins when it is offloaded to the site up to the moment the material hits the deck or hold of a vessel. Every port is unique, and some can be highly specialised. From a dust control standpoint, flexibility is needed to achieve tailored dust control solutions.
A dedicated system might cater to the standards of a specific industry. Bulk grain, for example, must be kept dry to prevent mould, so an enclosed system of covered conveyors and silos limits the exposure to rain, but can still have dust emission points at unloading and loading. A specialised port without material-specific restrictions such as handling light and dusty petroleum coke (petcoke) might have a completely open system from train to storage to ship, with dust concerns at every logistical stage.
Some ports are generalised as to the type of material they handle from month to month. This introduces its own set of obstacles in preventing particle emissions. For example, a large nearby demolition and construction project can suddenly feed a port tons of scrap and
recycled material from metal to concrete, which can all carry different handling, storage and emissions requirements.
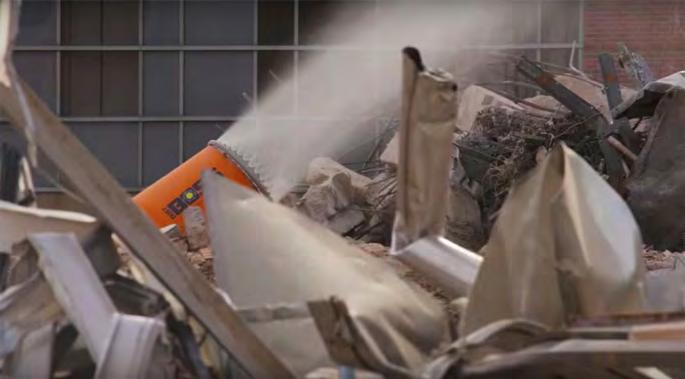
MATERIALS SUCH AS SCRAP METAL AND DEMOLITION WASTE CAN HAVE HIGHLY VARIABLE DUST PROPERTIES
These examples require different dust control solutions and creating a comprehensive dust management plan using modern technology helps mitigate some of the issues around particulate emissions. With the right plan and technology, port managers can enjoy positive relationships with local government, nearby communities and the media over air quality issues.
Automated Dust Solutions
Being able to control when and where dust solutions are operating in response to conditions from a central location is key. One major part of efficient port operation is automation. Ports are often massive, windy open areas and having staff spray down thousands of tons of bulk material stacked in large storage piles to mitigate dust is inefficient and minimally effective. An automated suppression solution is more efficient, safer and cost-effective over time.
There are various technologies for different applications, but many ports are choosing atomised mist technology because its use in shiploading and unloading over nearly two decades has proven its effectiveness in suppressing both airborne and surface particles. Managers prefer atomised mist cannons for their ability to automatically control flow and direction with very little manual labour, using a fraction of the water of hoses and sprinklers.
Working backward from ship to train, some of the options for atomised mist are:
Misting rings – No matter if material is discharged straight off of a conveyor, through a sock or down a metal chute, there is always a gap between the exit and the pile where the material is in a freefall and exposed to wind. This can be mitigated using a stainless-steel misting ring that surrounds the material flow with a curtain of light mist that falls with the material. When wind hits the stream, the mist travels with airborne dust, colliding with particulates and pulling them down, preventing the escape of fugitive material.
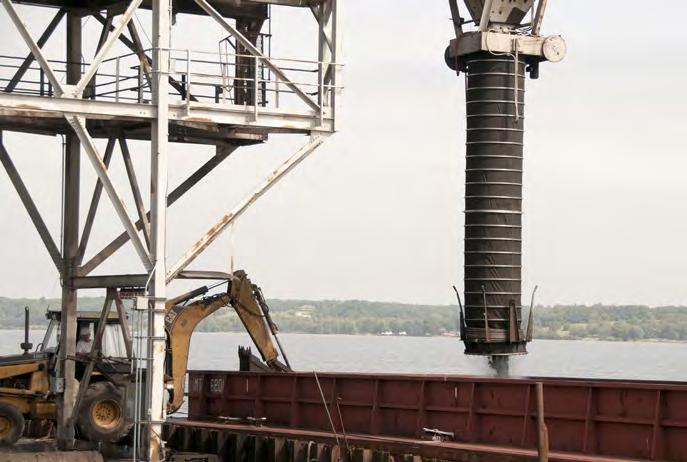
A MISTING RING CAN ENSURE ADEQUATE SURFACE SUPPRESSION WHEN THE MATERIAL LANDS ON THE PILE
Transfer point misting bars – Most operations have several transfer points, particularly when directing material to different sections of the port. During transfer, dropping material separates, offering an excellent opportunity to introduce moisture from strategically placed misting bars or spray heads to prevent downstream dust emissions. Accompanied by a dosing system, operators can introduce dust suppressing surfactants and other additives that promote clumping without saturation. Some units provide data on the volume of surfactants dispersed and chemical levels,.
Tower-mounted dust cannons – Storage areas and stockpiles experience a constant churn of material. Even with natural barriers, wind can lift dust off the piles and carry it long distances. Consistent disruption from front loaders can cause dust to become airborne, eliminating any previous efforts at surface suppression with hoses or sprinklers. To address these conditions, many operators have turned to tower mounted cannon systems. Atomised misting cannons can be positioned around storage areas high enough to reach the entire pile and introduce millions of tiny droplets to the ambient airflow, with the goal of stopping airborne particle emissions before they can travel.
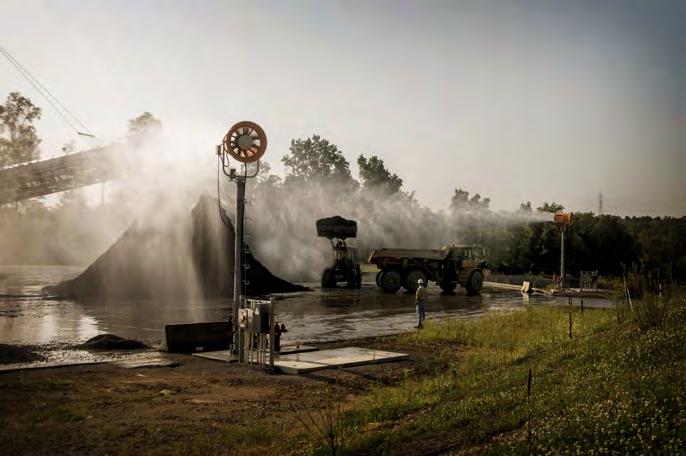
A WELL-APPOINTED STORAGE AREA WITH PROPER DUST SUPPRESSION IMPROVES COMPLIANCE AND EFFICIENCY
Mobile dust control cannons – Whether mounted on trucks or trailers or equipped with a mobile carriage, these cannons can be called upon to suppress dust wherever needed. With a vertical throw angle of 0-50º, based on the maximum ship size allowed by the port, operators can choose models that can reach the height of an empty ship with enough power to stretch across the beam. When not in use on the dock, they can be easily moved to material storage or loading areas. They can also be used for large area cooling on hot days.
Misting heads – In ports handling raw material by train or hopper truck where dozens of cars are unloaded one after the other, atomised misting heads can be cost-effective compared with manual spraying. Since the unloading area doesn’t change, this allows operators to strictly control water output, as the units can be programmed to activate only when material is being unloaded into storage or on to a conveyor.
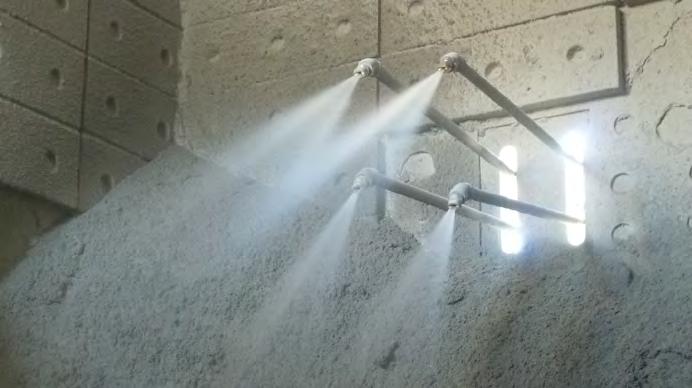
TREATMENT WITH SURFACTANTS IN STORAGE CAN HELP WITH EMISSIONS CAUSED BY DISRUPTION
Case Study 1 Hendricks River Logistics (HRL)
Located on the Mississippi River, a high-volume coal transshipping company handles 1.6 to 1.7m tons of coal per year from the Powder River Basin (PRB) in Wyoming.
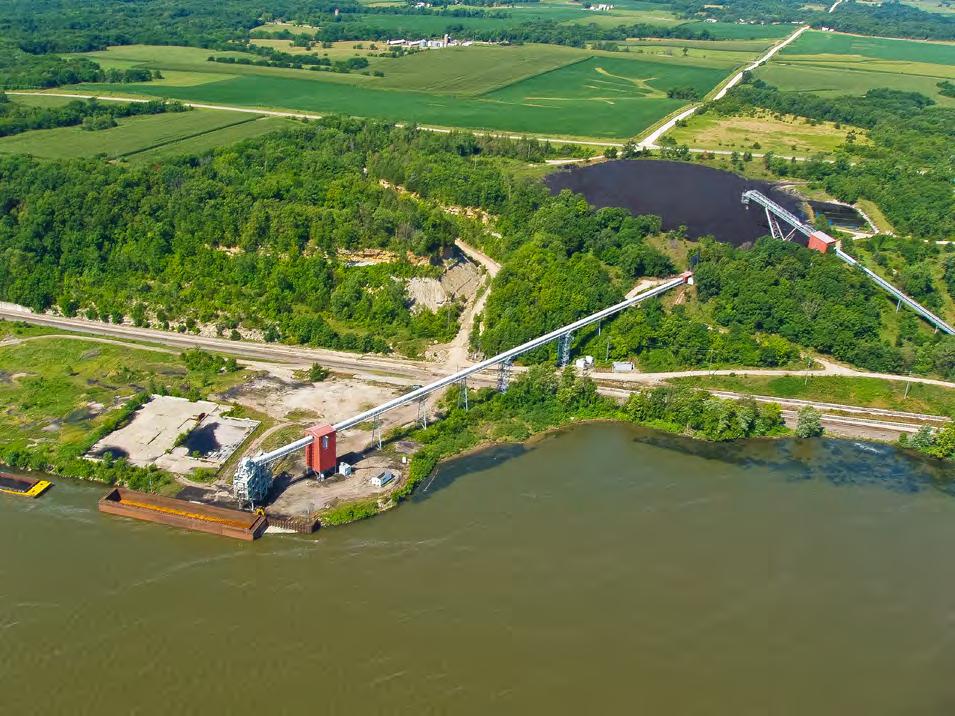
ALTHOUGH THE STORAGE AREA HAS AN ADEQUATE WIND BARRIER, THE DOCK REMAINS EXPOSED
Trains carrying sub-bituminous coal unload approximately 3,175 tonnes per hour into the receiving area, where it’s then conveyed to the storage depot. The main discharge belt travels 304m uphill from the rotary dumper to the supply depot. The conveyor leading from the supply depot to the dock is 335m long, loading barges at a rate of 1,360 tonnes per hour. There, HRL has fleeting for 40 barges.
HRL employs two DustBoss® atomised misting rings at the site, a 1,219mm diameter unit on the smaller loading area and a large 1,828mm ring on the main loading area. The rings are stainless steel circular manifolds that can be fitted with up to 38 misting nozzles. They are mounted on the conveyor 915mm under the discharge point, pumping 90.62 litres per minute of atomised water.
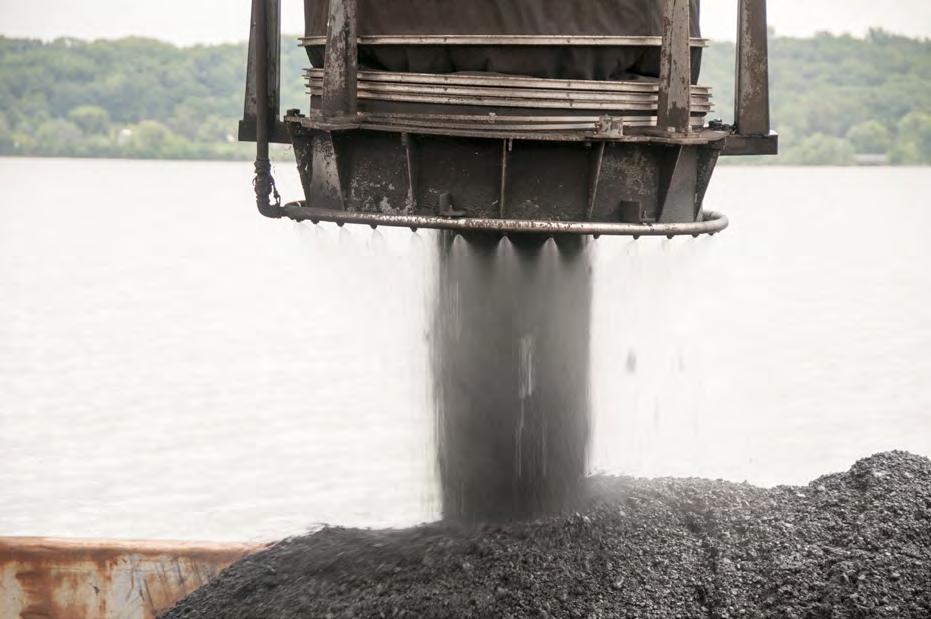
Case Study 2 Servicios Especiales Portuarios (SEPSA)
SEPSA is a leading-edge stevedoring and bulk cargo distribution company based in the Port of Veracruz, Mexico. The firm handles more than a million tonnes of bulk cargo per year, including shredded and structural scrap, pig iron, hot briquette iron, petcoke and fertiliser.
Along with dust emissions from loading raw material on to ships, dust was also being generated by the nearby storage yard. With sudden shifts in wind and weather along the waterway, crews struggled to control dust drifting over the company’s 5-hectare property.
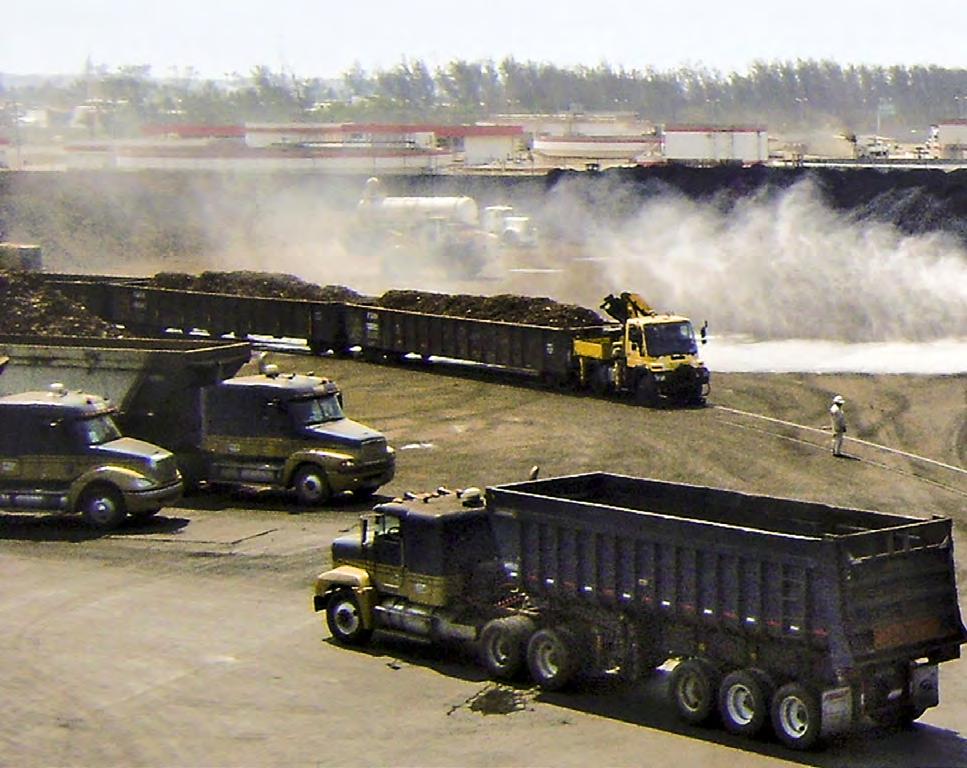
PROPER POSITIONING OF DUST CONTROL WHEN LOADING RAW MATERIAL REQUIRES MOBILITY
With mobility and versatility among its primary needs, SEPSA mounted an atomised mist cannon from BossTek® on a tanker truck that could be easily driven and parked wherever dust suppression was needed. The unit features a manifold with 30 brass nozzles that create millions of water droplets per minute within a range of 50-200 microns, the optimum size for particle attraction and coverage area. It launches the mist with a powerful 18.6KW fan, delivering a range of more than 60m. Equipped with full 359º oscillation, it can cover more than 1.1 hectares with a fine, dust-trapping mist.
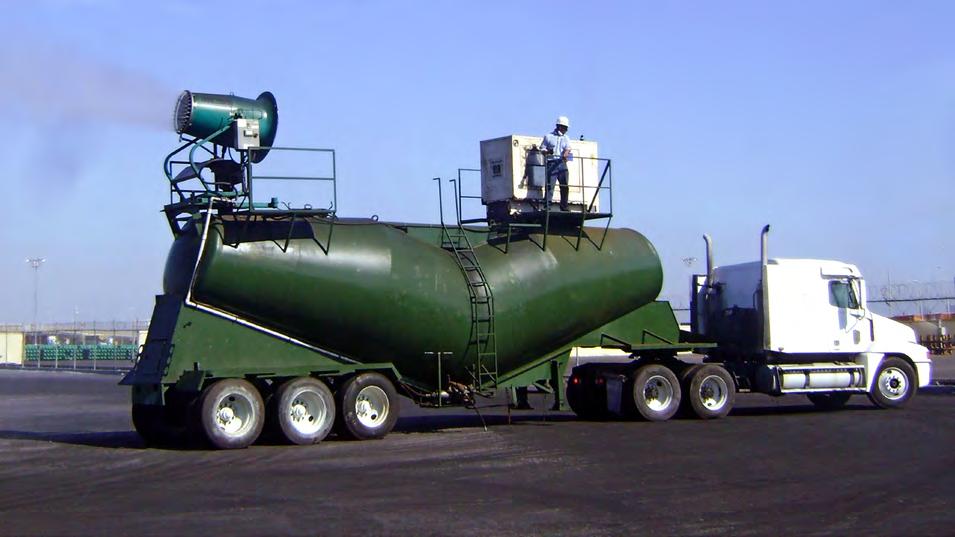
Case Study 3 River Port
A busy port in New England operates a dock and industrial park with bulk material storage. About 40-50 vessels per year arrive from Europe, delivering nearly 30,000 tonnes) per week of clinker. When the ship arrives, large clamshell shovels controlled by tower cranes unload the material from the ship’s cargo hold, over the ship’s deck – up to 36.5m in the air – to a 6m hopper, which discharges into a 36 tonne haul truck. The truck drives the material the short distance to the adjacent industrial park, where it is stored for further transport.
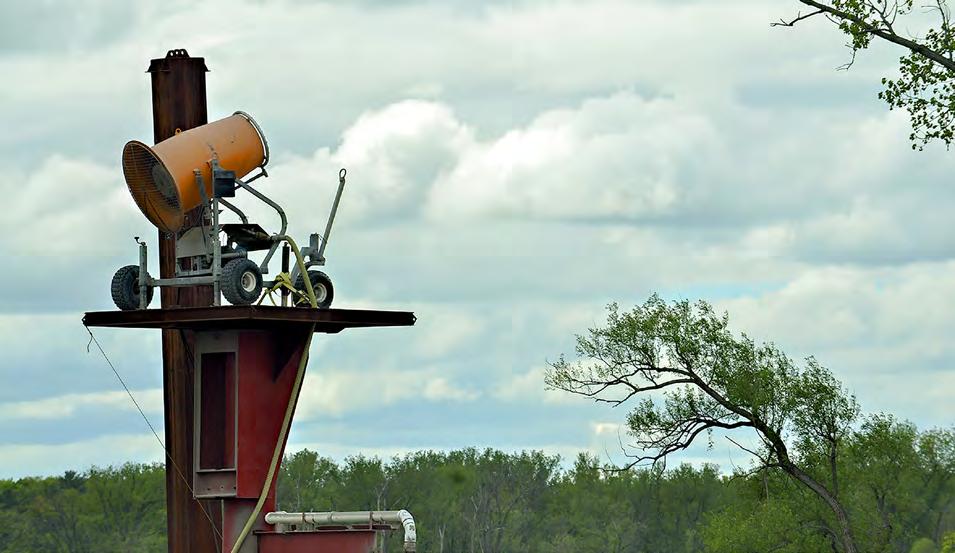
PLACED BY CRANE ON A PLATFORM OVERLOOKING THE SCRAP YARD, THE DUSTBOSS CONTROLS AIRBORNE PARTICULATES
The port purchased two cannons, one for mounting above the scrap yard and one mounted on a wheeled carriage to remain mobile so it can be moved wherever it is needed. Both cannons feature a 18.6KW fan producing 849.5m3 of airflow to propel the engineered mist in a 60m long cone that can reach high over the deck of the ship.
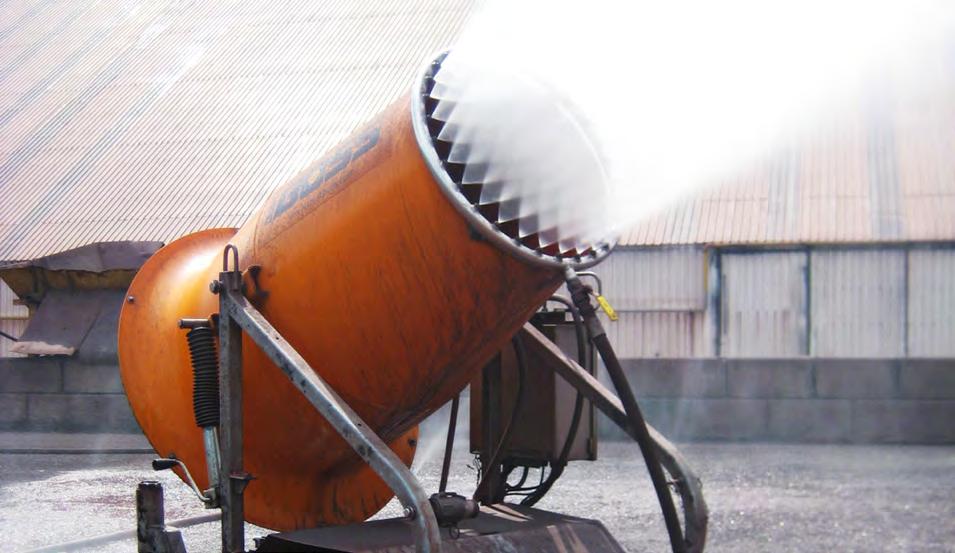
THE MOBILE CARRIAGE ALLOWS THE UNIT TO BE QUICKLY MOVED WHEREVER NEEDED
Operators report that air quality at the port has significantly improved during the unloading of clinker and other dusty materials, and that fugitive dust emissions have not been seen leaving the site since adding the units to the facility’s dust management plan.
Case Study 4 Port Panama City
The Panama City Port Authority in Florida needed a dust suppression system for its wood pellet loading operation to help retain high air quality and prevent negative effects on workers, local residents and manufacturing operations. The facility receives about 30,000 tonnes of pellets each month by rail car, creating stockpiles more than 30m wide, with an enormous potential for dust. Dock workers can load about 1,000 metric tons of material per hour.
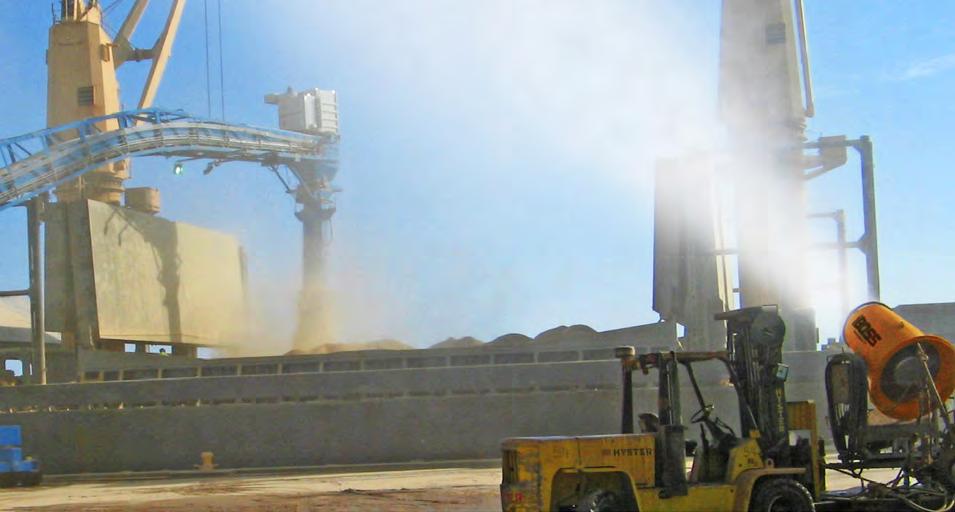
MOBILITY IS KEY TO POSITIONING THE CANNON AND ADJUSTING FOR CHANGING WIND CURRENTS
Operators chose a mid-sized atomised mist cannon. Once crews started working, they aimed the plume of water mist into the dust cloud and it made an immediate difference. Port officials report that the equipment has been very efficient, helping to protect ambient air quality and prevent negative effects on workers, as well as local residents and manufacturing operations.
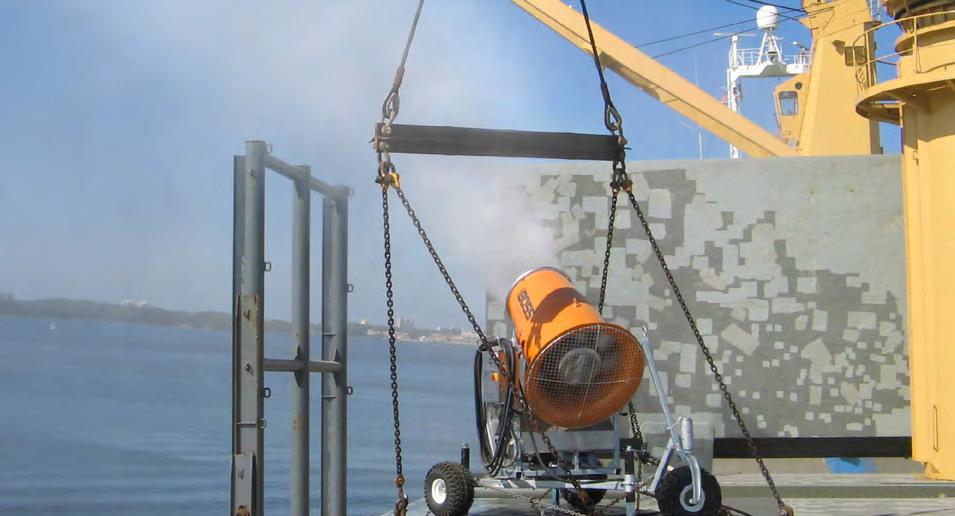
VERSATILITY IS PART OF WHAT ATTRACTED PORT OPERATORS TO ATOMIZED MIST TECHNOLOGY
Conclusion
Ports that create a comprehensive dust management plan are better equipped for clean, sustainable operations. These plans generally involve a thorough assessment of logistical throughput, revealing where dust emissions originate and identifying other potential issues that need to be addressed.
For port operators, changes in weather, varying materials and strict air quality standards can be difficult to traverse, but with the right dust control technology and approach, each unique situation has a solution. Contacting a dust control specialist from a reputable company to help with the dust management plan and customised solution is a good first step.