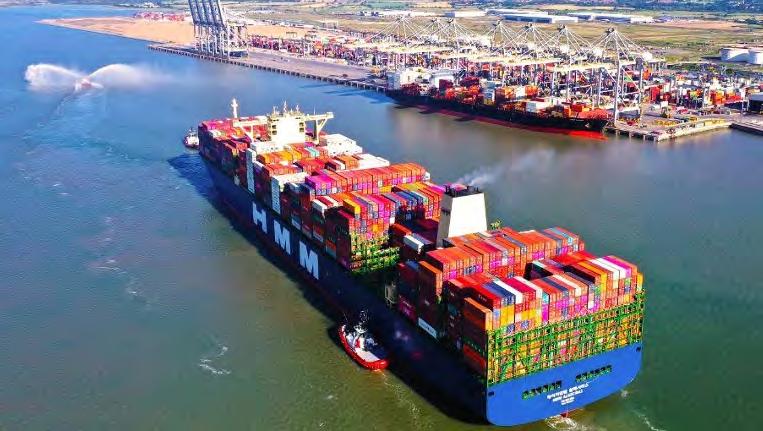
21 minute read
world news round-up
from BTI Winter 2021-22
by Maritime-AMC
Investment is on the up, in spite of the constrictions of the pandemic, but the industry has felt the effects of covid-19 in many other ways
The charter market for multipurpose vessels (MPVs), including both breakbulk and project cargo carriers, is expected to remain strong through 2022, supported by the continued prevalence of covid-19 and the resultant global supply chain disruption, according to consultants Drewry.
However, Drewry says that charter rate inflation will be checked by slowing cargo demand growth and expanding capacity in the competing fleets of dry bulk and containerships from 2023, according to its recently published Multipurpose Shipping Forecaster.
“It is clear that 2021 consolidated our belief that the charter markets for containerships and dry bulk carriers have as much of an effect, and sometimes more, than the pure economics relating to the MPV fleet,” the report says. “Although it was not always clear that weak charter rates pre-2021 were exacerbated by the competing fleets driving them lower, it has been very apparent that the current booming market is underpinned by even higher rates in these other sectors.
“The demand for MPV tonnage, from both breakbulk and project cargo, rose by almost 9% over 2021, following a drop of 2.5% in 2020. Although the majority of this increase is accounted for by stronger global dry cargo demand, a significant element of it is also down to improved market share for the MPV fleet. As the well-documented supply chain problems have caused unprecedented capacity constraints for the container sector, breakbulk cargoes have returned to the MPV fleet as shippers struggled to secure cargo space.”
Capacity constraints are expected to last well into 2022, Drewry adds. “The New Year has started with a number of reports of MPV vessels carrying cargoes usually associated with containers, such as bagged coffee.
“With the Chinese government’s zero tolerance covid-19 policy continuing to put port operations at risk, even as the rest of the world considers the Omicron variant to be less threatening than initially feared, the supply chain issues are far from over.”
There has also been a significant increase in consumer demand over the past 12 months, as public health restrictions have led to a switch of spend from services to consumer goods, the consultant adds.
port boost for libya
US-based The Guidry Group has signed an agreement with Archirodon Construction (Overseas) Company setting the main terms of its co-operation for the design and construction of the US$1.5bn Susah Secure Port in Libya. The Susah Secure Port, conceived as a multi-use port, will be the deepest water port in Libya, the first public-private ownership port project to be undertaken in the country, the first port to be built to a globally competitive and efficient standard and the largest port infrastructure investment by a US company in Libya’s history.
The Susah Secure Port project is critical to the rebuilding of Libya and was recently endorsed by the Libyan Government of National Unity. It will provide a secure means of trade for international companies and governments and become a centre for economic development for Libya. There is an expectation for greater US involvement in the development of Libya, with the Susah Secure Port being the a first step in the right direction.
The Port of Susah is located about 240km east of Benghazi in Eastern Libya. The seaport in Susah serves as the main
artery and entry port for goods into Libya by sea. A natural self-dredging port with a sea depth of 18m, the proposed newly developed Port of Susah will enable ships to offload their containers of goods with ease.
The US$1.5bn port will be constructed in four phases. The total development cost projection of the first phase of the project is approximately US$200m. It will primarily focus on container handling, grain handling and other bulk cargoes, general cargo and as a logistics base.
Competition complaint
The British International Freight Association (BIFA) has written to the UK government asking it to investigate the state of competition within the current deep sea container shipping market.
The UK’s main trade association for freight forwarding and logistics companies says that its members are concerned that certain practices undertaken by the principal container shipping lines, as well as easements and exemptions provided to them under competition law, are distorting the operations of the free market to the detriment of international trade.
In a letter to Robert Courts MP, Parliamentary Under Secretary of State at the Department for Transport, BIFA’s Director General Robert Keen expresses the trade association’s concern that during a period of welldocumented chaos within the container shipping sector, commercial power is becoming increasingly concentrated, resulting in diminished market choice and competition, and distorted market conditions.
Keen says: “BIFA members fully accept that a free market economy is open to all, but are increasingly concerned that the activities of the container shipping lines, and the exemptions from legislation from which they benefit, are distorting the operations of that market to the shipping lines’ advantage, whilst adversely and unfairly affecting their customers, especially freight forwarders and small and medium-sized enterprises.
“The facts speak for themselves. During a period that has seen EU block exemption regulations carried forward into UK law, there has been huge market consolidation.
“In 2015, there were 27 major container shipping lines carrying global containerised trade, with the largest having a 15.3% market share. Today, there are 15 shipping lines, organised into three major alliances carrying that trade, with some analysts observing that the market share of a single alliance on certain key routes could be over 40%.
“The pandemic has highlighted and accelerated this development, which has also contributed to dreadful service levels, and hugely inflated rates, with carriers allocating vessels to the most profitable routes with little regard to the needs of their customers.
“Drewry recently issued a profit forecast of more than USD150bn for 2021 for the main container shipping lines for which financial results are available.
“To put that into perspective, this is more than has been achieved in the previous 20 years combined, and many BIFA members consider it to be a case of blatant profiteering,” Keen concludes.
BIFA is joining a growing number of organisations, including CLECAT and FIATA, the US Federal Maritime Commission, and the Australian Productivity Commission, in calling for governments at a national and pan-national level to give careful consideration to the evolving business arrangements in the container shipping market to see whether they are in breach of competition law.
Derivatives volumes
The freight derivatives market for dry cargo vessels saw increased traded volumes in 2021, according to data released by the Baltic Exchange.
Dry Forward Freight Agreement volumes hit 2,524,271 lots, up 61% on 2020. Options trading in the dry market hit an all-time high of 409,255, up 25% on the previous year. The most heavily traded contract was settled against the Baltic Exchange’s panamax timecharter assessment (PTC) which saw 1,202,432 lots traded in 2021.
Tanker FFA volumes were down 16% on the previous year, reaching 553,535 lots. Middle East Gulf to China was the favoured tanker contract with 304,719 lots changing hands.
One lot is defined as a day’s hire of a vessel or 1000 metric tonnes of ocean transportation of cargo.
Commenting on the figures, Baltic Exchange chief executive Mark Jackson says: “2021 was another impressive year for the Dry FFA market. Underpinning these volumes are volatility, world class clearing, trust in the Baltic Exchange’s settlement data and increased participation by owners, charterers and traders. Our status as a regulated benchmark provider has allowed more hedge funds and banks to enter this mature, liquid market.”
He adds: “Last year, the dry bulk market experienced considerable swings as a result of ongoing supplychain challenges caused by the covid19 pandemic.
“With low freight rates, the tanker FFA market was more subdued 2021 due to a lack of sellers. But there are signs of confidence in the market. Our benchmark Middle East Gulf to China crude oil route (TD3C) has open interest going out five years, which shows the excellent depth of this market.”
Weather routing
Technology company ZeroNorth recently highlighted the changing role of weather routing in the maritime industry, as new technologies shift responsibility for mastering the weather to more individuals within shipping companies and amplify the influence that voyage planning has on commerciality.
Previously the responsibility of multiple, unconnected individuals with different priorities, weather routing through interconnected and integrated data is having an increasing impact on commerciality – and ultimately on the industry’s ability to decarbonise – ZeroNorth argues.
In many cases, today’s services tackle different elements of successful ship operation and offer operators siloed recommendations. While the future of weather routing will continue to enable
masters to fulfil their critical role of vessel and crew safety management, shipping’s data landscape has matured enough through technology platforms, ZeroNorth says, that the benefits of weather data and applications no longer need to be siloed from each other.
New technology advancements enabling optimisations in real time mean that shipping companies will be able to act on voyage planning recommendations with a clear view of their commercial and sustainability impacts. ZeroNorth says that these evolutions mean that vessel routing decisions will become even more closely tied to successful commercial and sustainability performance, above and beyond the critical baseline of ensuring vessel safety.
The positive impact of optimisation with integrated weather routing on commercial performance will only become more important as the industry transitions to cleaner fuels. Revenue upsides will allow the industry to manage its transition to more expensive, low carbon alternative fuels because every ton of fuel saved through weather routing represents more money that the sector can inject into clean fuel adoption.
ZeroNorth is also launching a new 24/7 weather advisory service. The weather advisory team comprises seasoned experts who are available 24/7 to support customers – including operators and masters – to navigate any situation that a vessel might encounter. The team, which includes meteorologists, master mariners, and routing experts, offers advice while in the voyage planning phase, as well as for specific queries during a particular passage.
Shuttle tanker investment
AET, a leading owner and operator of maritime transportation assets and specialised services, took delivery of Eagle Campos, the first of another three Suezmax Dynamic Positioning (DP2) Shuttle Tankers. These are purpose built for long-term charter to Brazil Shipping Limited, which is a wholly owned indirect subsidiary of Shell.
AET’s commitment to moving energy in an increasingly responsible and ecofriendly way led to the agreement with Shell in December 2019 to operate these three Suezmax DP2 shuttle tankers in the international and Brazilian Basin on a long-term charter, with Eagle Campos being the first in this series. She was delivered to AET on 5 January 2022 and will commence her operations in Brazil, joining Eagle Pilar, which AET already operates for Shell.
Eagle Campos’ two sister vessels are currently under construction at Hyundai Heavy Industries (HHI) in Ulsan, South Korea, and are due to be delivered later this year. AET and Eaglestar site teams have been working closely together with the HHI team to ensure all health and safety precautions were in place to safeguard the construction and delivery of the vessels during the ongoing pandemic.
Biosafety initiative
A newly signed project is set to provide pilot projects in developing countries in order to demonstrate technical solutions for biofouling management, address the transfer of invasive aquatic species and help reduce greenhouse gas emissions from ships.
Biofouling is the accumulation of aquatic organisms on wet or immersed surfaces, such as ships and other offshore structures.
The TEST (Transfer of Environmentally Sound Technologies) Biofouling Project will run for four years (2022-2025), following an agreement signed in December by International Maritime Organization (IMO) Secretary-General Kitack Lim and the Norwegian Agency for Development Cooperation (Norad). Norad funding amounts to US$4m.
The project complements the existing Global Environment Facility (GEF)/United Nations Development Programme/IMO GloFouling Partnerships Project, which aims to support its lead partnering and partnering countries to implement IMO’s Biofouling Guidelines.
The TEST Biofouling Project will focus on demonstrating technical solutions in the GloFouling partner countries. TEST Biofouling will feature some of the latest advances in technological solutions for managing biofouling, such as remote operated vehicles for in-water cleaning and underwater cameras for monitoring anti-fouling coating status. Additionally, the project will provide capacity building courses in developing countries.
IMO Secretary-General Lim says: “I am pleased to sign this agreement with Norad for the TEST Biofouling Project. We need to showcase solutions to today’s challenges, including preserving the oceans’ biodiversity and tackling climate change.
“In 2022, IMO’s World Maritime Theme will be ‘New technologies for greener shipping’, so it is particularly pertinent to launch a project which is going to focus on demonstrating just what can be done. This project will work with developing countries, ensuring that they can lead in demonstrating solutions.”
co2 project underway
Equinor, Shell, TotalEnergies, Gassco and classification society DNV announced the kick-off of a new joint industry project (JIP) to develop low-pressure solutions for the transportation of CO2 by ships. The CO2 Efficient Transport via Ocean (CETO) JIP will carry out the technology qualification of a lowpressure ship design and identify solutions to scale CO2 transportation volume, while reducing the associated risks, to support the development of opportunities in CCS.
CETO is funded by the project partners and GASSNOVA through the CLIMIT programme and is expected to be completed in 2023.
SIRE overhaul
The Oil Companies International Marine Forum (OCIMF) is overhauling its Ship Inspection Report Programme (SIRE) by introducing tablet-based inspections, a more comprehensive inspection process, and enhanced policies and procedures from Q2 2022.
The new programme, SIRE 2.0, will facilitate a risk-based approach to assessing the safety and quality of a vessel and its crew on an ongoing basis, but will require a “change in mindset” from industry, OCIMF warns.
Under SIRE 2.0, accredited inspectors will complete a Compiled Vessel Inspection Questionnaire (CVIC) in realtime using a tablet device. Unlike the existing paper-based questionnaire, the SIRE 2.0 CVIQ uses a sophisticated algorithm to select questions from a question library based on the type of vessel, its outfitting and operational history to create a bespoke risk-based inspection questionnaire. This means no two inspections will be the same.
In another significant change to the reporting process, most questions require the inspector to provide responses based on hardware, processes and human factors, with observations graded from not as expected through to exceeds expectation. Observations will also be supported with documentary and photographic evidence, where permitted.
As a result of these enhancements to the programme, each inspection question set is varied, providing vessel operators and crews greater opportunity to demonstrate their best practices, and for the first time both positive and negative observations can be documented.
Enhanced governance processes will ensure greater transparency and control for OCIMF and other parties involved in the programme, with stringent compliance requirements enhancing accountability, creating an altogether more robust and programme that can more easily be adapted to the evolving risk profile of the industry.
Electronic certificates
Classification Society ClassNK will make electronic certificates and reports issued for ships as standard service from 30 January 2022.
ClassNK has been providing an environment in which documents can be used in electronic data upon request since the early 2000s for survey records and since 2017 for class certificate and statutory certificates issued on behalf of flag states.
Electronification has become widespread due to its benefits in reducing the burden of handling papers, preventing loss, damage, and falsification of papers, and facilitating information sharing among stakeholders such as crew and management companies. Especially, electronic certificates have been introduced in major flag states, including Panama, Liberia, Singapore, Marshall Island, Bahamas, Malta, and so on, and accepted by regional port state control.
As the environment has been improved after many years of operation, ClassNK will make the electronic documents as standard service for class/statutory survey records and International Safety Management (including Document of Compliance to a company)/International Ship and Port Facility Security Code/Maritime Labour Convention audit records issued for ships, as well as for certificates of the flag states that authorise electronic certificates from 30 January 2022.
The documents are available by the links sent to the e-mail address registered on “e-Application”, the online application system for ships in service, and on “NK-SHIPS” storing information of ClassNK related ships. Certificates of the flag states that have not authorised electronic certificates yet, and some other certificates continue to be provided in paper form.
THE BPA IS PUBLISHING NEW DATA ON UK PORT INVESTMENT ALONGSIDE ANALYSIS OF NEW Q3 TRADE STATISTICS
british boom
New research published by the British Ports Association (BPA) reveals that UK port investment topped £1bn in 2021, despite continuing pandemic volatility. The figures are being published alongside BPA analysis of new trade data that shows how continued depressed demand for fuel is masking a strong recovery across multiple cargo segments.
Investment in port infrastructure in 2021 stood at over £1bn, swelled by several big projects such as the £300m fourth berth at DP World’s London Gateway, which will raise capacity at the container port by a third.
Significant investment in modernising port machinery, pilot vessels and buildings adds at least another £75m to the total, although this is almost certainly an underestimate as the value or existence much of this investment is not routinely published.
Other notable port infrastructure investments announced this year include: » £25m development of the Port of
Lowestoft’s Eastern Energy Facility » a £50m expansion at the Port of
Cromarty Firth » Teesport’s new £9.2m bulks terminal » the start of a new £60m programme of works to redevelop areas within
Pembroke Port » £40m of investment in the Port of
Leith by Forth Ports Port infrastructure investment remained strong at over £600m despite the pandemic. Notable projects include Harwich Haven’s £120m channel deepening for the Port of Felixstowe, which is currently underway. The Harwich channel deepening will mean that the biggest container ships in the world will be able to access Felixstowe, which handles more than a third of the UK’s containers.
These investment figures follow new data for Q3 2021 that show that most cargo types have returned to prepandemic volumes or are stronger than they have been for years. Weak liquid bulk volumes due to a drop off in transport demand during the pandemic have masked what is shaping up to be a very busy year for many ports.
For more information, visit: tinyurl.com/BPA-PortReport
TT CLUB highlights the risk of theft
Freight insurance specialists TT Club and the supply chain services and solutions team at business improvement and standards company BSI have highlighted the increased risk of theft from storage facilities seen over the past few months in the US. The changes in theft patterns from the same quarter last year highlight a trend away from ‘on the move’ targets to those locations where cargo is temporarily stored and delivered.
These locations include traditional warehouses and depots where containers and trailers are being held awaiting collection, many of which are temporary facilities in port areas without adequate security regimes.
As the report’s diagrammatic comparisons show, the largest rise in the methods and locations for cargo theft was from facilities: the percentage of the total increasing to 25% in the third quarter this year in contrast with just 7% in 2020. At the other extreme, theft of vehicles fell from a dominant 47% in 2020 to a surprisingly low 15%; in addition, hijackings halved from 20% to 10%.
Commenting on some of the more contrasting figures, Mike Yarwood, TT Club’s managing director, Loss Prevention says: “The is little doubt that the problems of supply chain disruption that are currently bedevilling the US freight transport system, particularly that of container congestion at ports and inland hubs, is creating increased opportunities for thieves.
“The static nature of cargo in these circumstances, often stored in temporary and less secure facilities, leads to criminal ingenuity adapting the modus operandi of theft in a typically resourceful way.”
TT is keen to use the insightful data provided by BSI Screen in identifying shifts in cargo theft trends and bring them to the attention of operators in as timely as a fashion as possible. Those concerned with risk management in the supply chain both in the US and throughout the world should be aware of such patterns and hopefully take measures to reduce losses, costs and insurance claims.
TT is committed to providing resources to help supply chain stakeholders to enact such mitigating measures. Yarwood explains: “Whatever the location and means of cargo theft such incidents can often be averted through straightforward due diligence, management processes and employee vetting and training. ”To this end, TT has a webpage dedicated to advice on improving supply chain security. For more information, visit: ttclub.com/loss-prevention/supply-chain-security/?
NEGRINI: ADDING REMOTE ASSETS
COMPANY NEWS
Negrini has introduced a new tool to further enhance its extensive range of electro hydraulic grabs. Remote Control Industria 4.0 is ideal for routine maintenance, as well as to improve the efficiency and operation of customers’ production processes.
state-of-the-art features
» Monitoring and control of processes in electro-hydraulic equipment » Real-time scans and diagnostics » System communication via wi-fi or data sim » Notifications via email, sms or smartphone, tablet and PC » Preliminary production analysis » Routine maintenance alert » Failure prediction » Immediate alarm in case of failure or malfunction

THE SMART GRAB
With Remote Control Industria 4.0 installed, the grab parameters automatically adapt to the type of material being handled without the need for human intervention, therefore maximising production and reducing costs.
In the presence of high-density materials such as mineral, the grab speed is reduced and the hydraulic pressure is increased – parameters that are not suited to lighter materials such as coal or cereals, where we see a change in speed
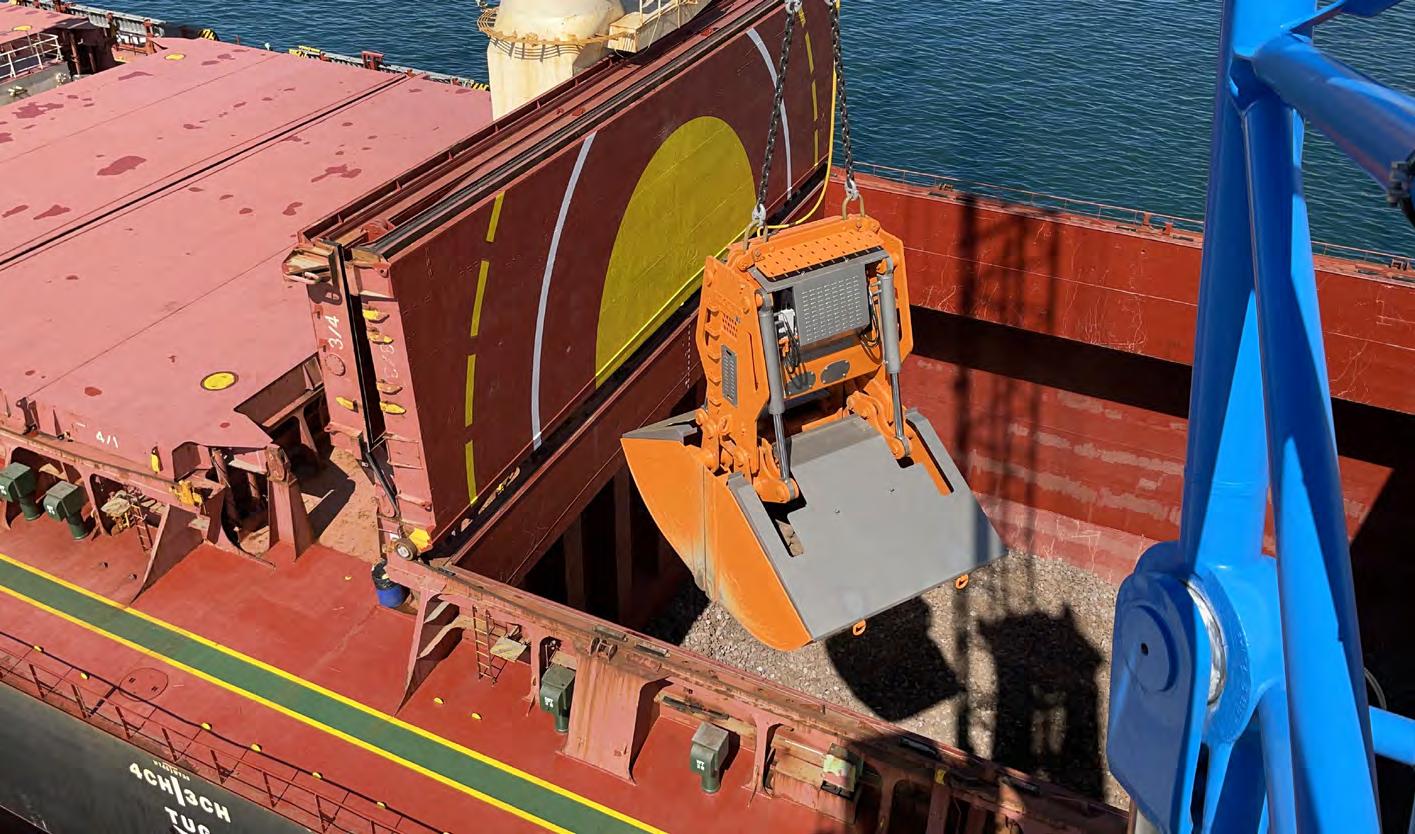
REMOTE MONITORING IS SIMPLE WITH INDUSTRIA 4.0
GRAB SPEEDS ARE EASILY CONTROLLED
and reduction in hydraulic pressure – thereby reducing energy wastage and wear.
The most important advantage offered by the Remote Control Industria 4.0 device installed on Negrini’s equipment concerns the processing of data, thus allowing preliminary production analysis and failure prediction. Notifications are sent via email and sms and each time an event occurs, either an incident, arrest or maintenance request is recorded.
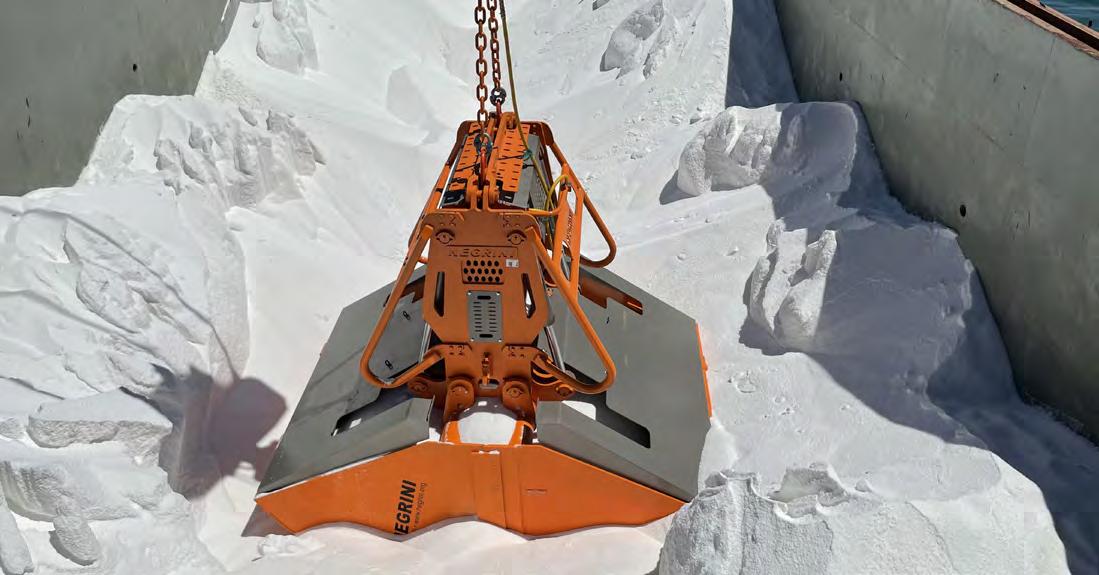
Costly machine downtime is therefore avoided while maximis ing production, reducing periods of non-activity and minimising expenses normally incurred by corrective maintenance works. The client and Negrini Srl have total control over the condition of the equipment via wi-fi or a data sim, using a smartphone, tablet or PC, and will receive all notifications sent by the system so as to always be informed of machine requests and events.
For more information, visit negrini.org
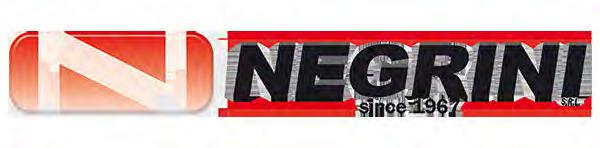
THE GRAB CAN BE EASILY ADJUSTED TO SUIT MATERIALS
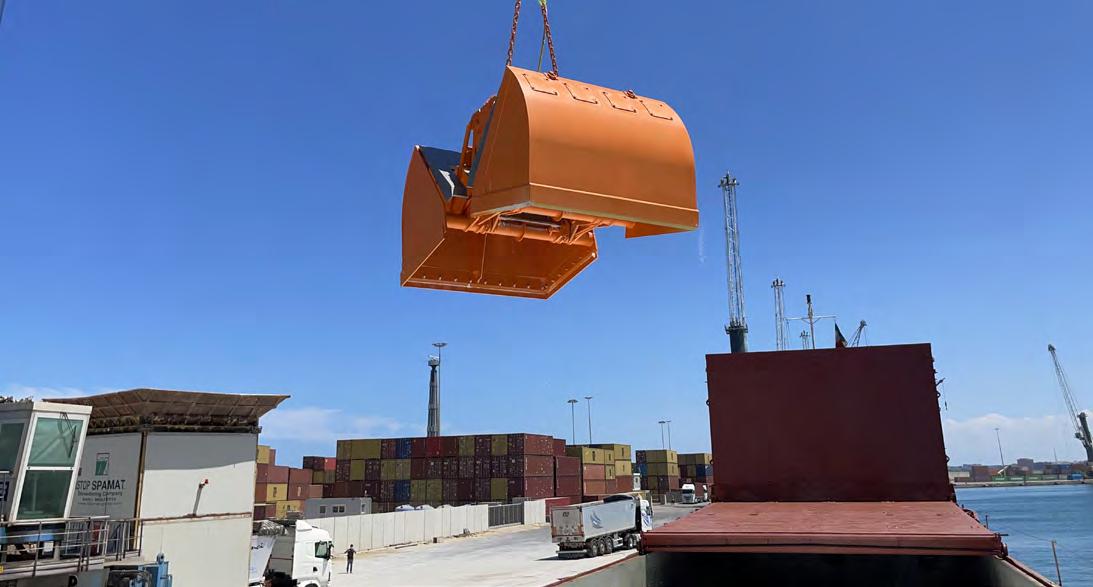




NEUERO: KICKSTARTING INNOVATION
COMPANY NEWS
French agri-food group Soufflet in Rouen recently took delivery of the new Neuero Kiko (kick-in kickout) shiploader, which has a loading capacity of up to 1,200t/h of grain with minimal dust emission. After four successful installations in the region, the Neuero Kiko DSH (dust suppression head) has impressed port operators with its efficient operation and high dust suppression, due to mass flow control.
The shiploader was assembled in Germany and transported using a heavy lift ship to France. The most significant advantage of this means of transport is the short downtime of the terminal. However, such transport is not easy and requires a lot of planning and preparation. Therefore Neuero and Soufflet already agreed on this shipment method at the beginning of the project so that lifting points and lashing points could be integrated into the machine design.
Heavy lift cranes set the shiploader into position at the site and Neuero was able to begin dry testing. The next step was hot commissioning after the site conveyor was ready.
So what is the difference that makes the Kiko DSH operate so efficiently and with the highest environmental standards available today? The answer is a combination of mass flow and pendulum movements. The mass flow allows loading of the cargo at low speeds, reducing dust emission. The shiploader does not eliminate dust completely, but reduces it significantly, therefore avoiding product segregation and slow material discharge speed. Older systems throw the product at boom height and try to stop it at arrival, especially during hatch trimming work where it is needed to fill all gaps.
The pendulum movement that we call Kiko allows the loading head to move simultaneously with the vertical telescope and enclosed system. Additionally, the slewing movement allows all areas of the hold to be reached, including the corners.
For more information, visit: neuero.de/en
READY FOR HOT COMMISSIONING


DEPARTING FROM GERMANY