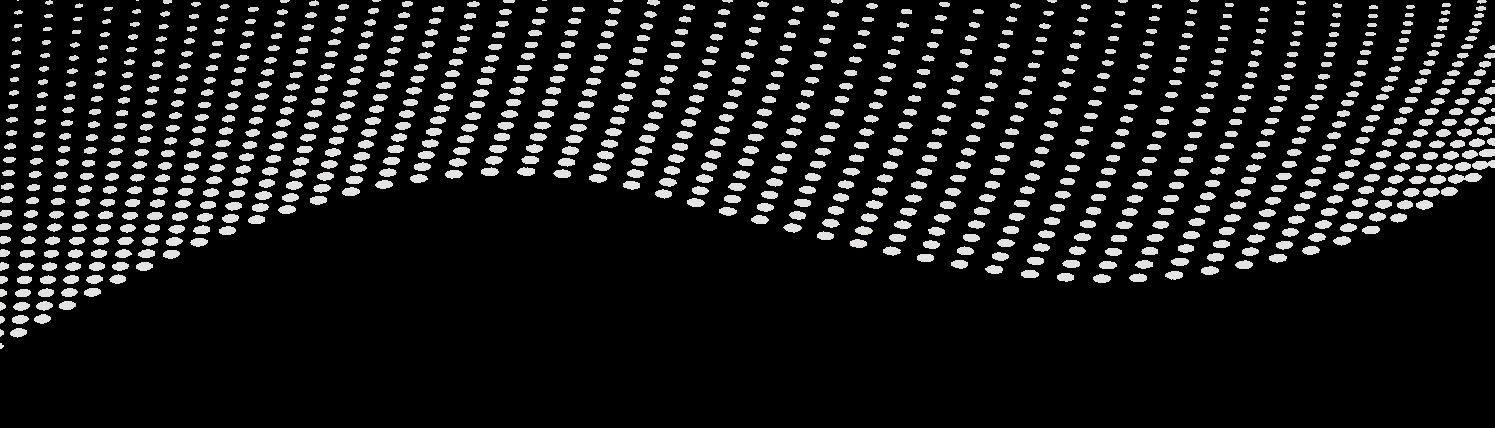
5 minute read
Additive Manufacturing
from Wavelength #80
Technical Additive Manufacturing with 3D printed spare parts revolutionize maritime supply chain
By Christos Chatzigiaksoglou
Advertisement
Additive Manufacturing (AM), also known as 3D printing, is an appropriate name to describe the technologies that produce physical 3D objects by adding layer-upon-layer of material, whether the material is plastic, metal, concrete or any other suitable material using a computer-based 3D design. It is considered one of the nine main pillars (Internet of things, Augmented Reality, Simulation, System Integration, Cloud Computing, Autonomous Systems, Cybersecurity, Big Data Analytics) of the Fourth Industrial Revolution and has improved tremendously in the last decade from primarily being used for prototyping to actual production. The story of Additive Manufacturing starts back in 1981, when a form of AM called Stereolithography (SLA) was first introduced by Dr. Hideo Kodama of the Nagoya Municipal Industrial Research Institute. Unfortunately, Dr. Kodama's patent application was denied because of his failure to file the full patent requirements on time. In 1986 an American inventor named Charles Hull filed the first official patent for SLA, which is the 3D printing technology that we have now become accustomed to.
Main Types of Additive Manufacturing:
1.Vat Photo-polymerization, 2. Material Jetting, 3. Material Extrusion, 4. Binder Jetting, 5. Powder Bed Fusion (3D printing technique mostly used in the marine industry), 6. Sheet Lamination, 7. Directed Energy Deposition. This can be used for repairs, or for adding to an existing object.
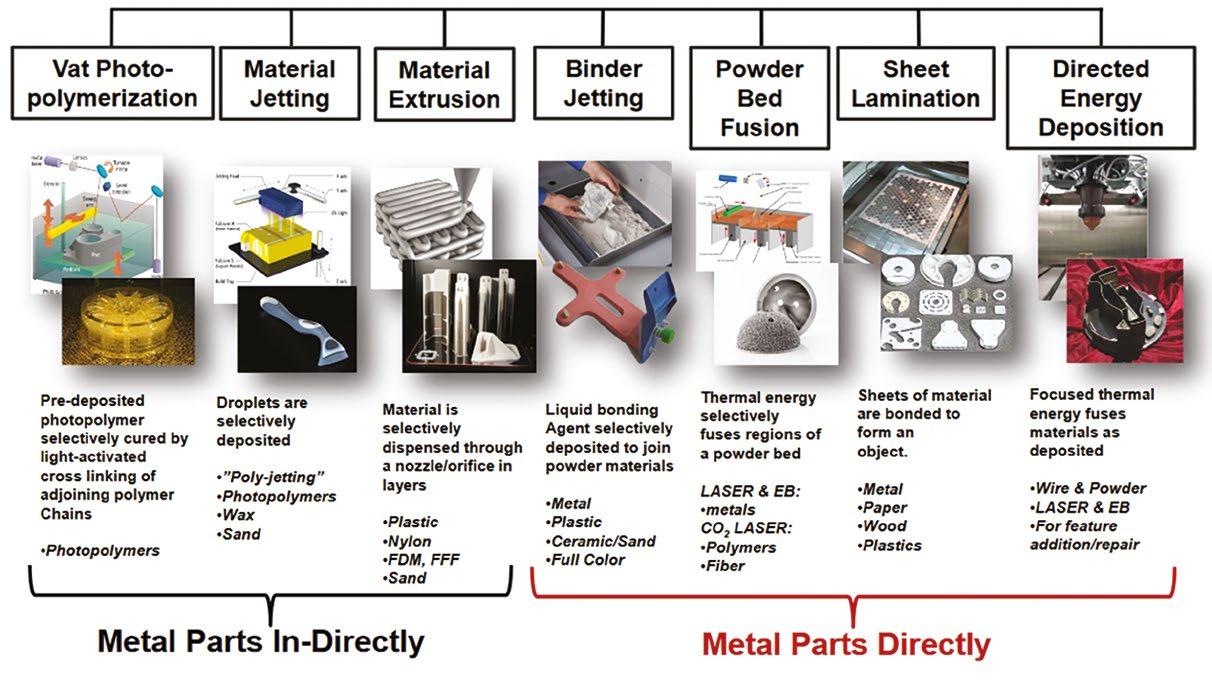
Figure 1: Main Types of additive manufacturing
Over the last decade we have seen Additive Manufacturing (AM), or 3D printing, make its way into the maritime sector – redefining the maritime and offshore spare parts supply chain and the way spare parts are made through its ability to manufacture rapidly and flexibly. The maritime industry spends billions of dollars on spare parts and repairs annually. More than 50% of vessels are over 15 years old, and the need for spare parts increases every year. Moreover, spare parts are limited and finding them can be difficult, timeconsuming, and costly. Certain 3D printing technologies like directed energy deposition (DED) are used not only to build new objects but also to add material onto existing parts. If a certain part is scratched or cracked, 3D printing can be employed to fill those scratches or cracks with a compatible metallic material. This process is relatively cheap and fast, and its capability is beyond the limitations of any traditional process.
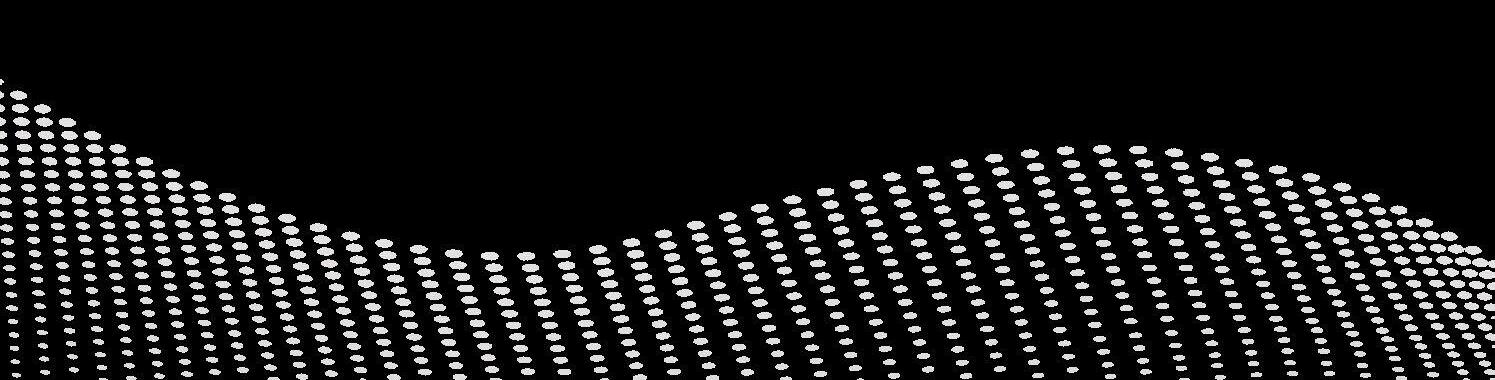
Benefits of Additive Manufacturing
•Reduced costs associated with minimum order quantities and storage (reduced inventory) •Shorter transportation and delivery time •Reduced warehousing and shipping costs •Minimized delays – no more prolonged importing procedures that could result in machine downtime •Typical parts procurement can take months but 3D printing could take just days •Personalized parts according to customer needs •Reduced overall energy waste and smaller carbon footprint
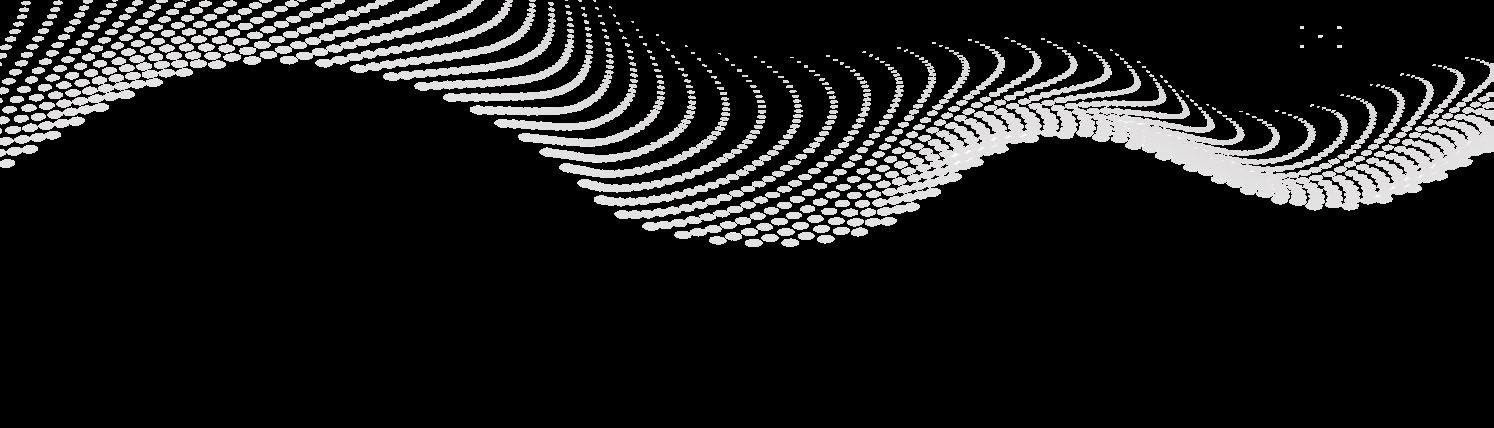
Challenges of Additive Manufacturing
•Technology know-how •Cost of equipment & material feedstock (compared with traditional manufacturing material) •Staff skills •Quality assurance •Difficulty in scaling operations •Availability of regulatory framework
Where are we now?
- In 2020, Wilhelmsen and Thyssenkrupp entered into a collaboration to establish a 3D printing joint venture focused on the maritime industry. The venture will re-examine and optimize the production and delivery process of 3D printed spare parts for the unique demands of the maritime market. Six customers have already signed up for the programme to begin utilizing ondemand 3D printing in order to eliminate physical inventory, storage, and distribution.
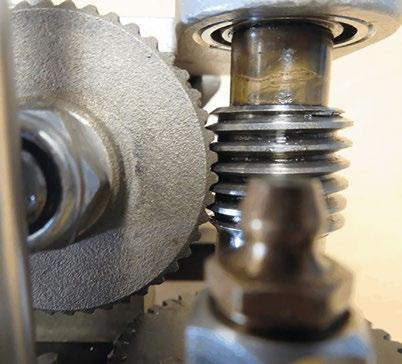
Figure 2: Worm Gear fabricated by binder jetting process enhanced both in functionality and durability through passivation for extra corrosion resistance Figure 3: 3D printed marine spare parts
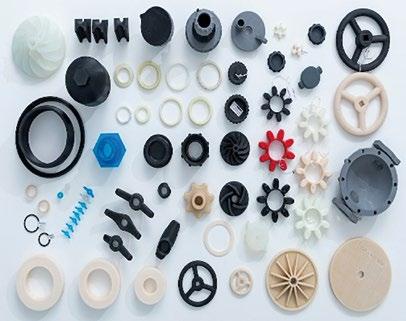
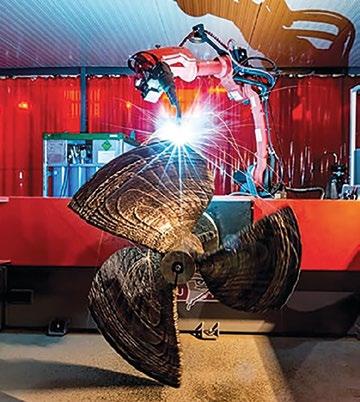
Figure 4: First fully certified marine propeller made by additive manufacturing at RAMLAB
- The Maritime and Port Authority of Singapore (MPA) launched a joint industry programme (JIP) in early 2019 to develop a concept for a future supply chain of AM spare parts. DNV GL was asked to lead the first phase of the project, which included a study into the feasibility of establishing a local additive manufacturing infrastructure able to supply a set of one hundred commonly ordered marine spare parts on demand. - In early February 2020 the bulk carrier Berge Mafadi was one of the world’s first ships to receive a commercial delivery of 3D-printed spare parts, including scupper plugs. - The Port of Rotterdam has opened the Rotterdam Additive Manufacturing Lab (RAMLAB), an on-site facility that includes a pair of six-axis robotic arms, which is capable of additively manufacturing large metal industrial parts. This enables RAMLAB to pursue faster fabrication options – 3D printing large ship components in metal and then finishing the pieces using traditional CNC milling and grinding methods within days. - In 2015, Tru-Marine, a turbocharger specialist, revealed that it had developed a proprietary additive manufacturing process to repair turbocharger nozzle rings to a “like-new” condition in a fraction of the time required by conventional repair methods. - In 2018, DNV issued the first Additive Manufacturing Approval of Manufacturer certificate to Thyssenkrupp Marine Systems, giving Thyssenkrupp TechCenter Additive Manufacturing the status of a DNV-approved supplier for maritime and general industrial applications. - Funded by the Danish Maritime Fund, the Green Ship of the Future Consortium is an independent non-profit organization driven and financed by its members which include Maersk, MAN Diesel & Turbo and DNV GL. One of their projects explored 3D printing in the maritime industry, including on-board printing, large-scale 3D printing, 4D printing or repair, and reconditioning with 3D printing.
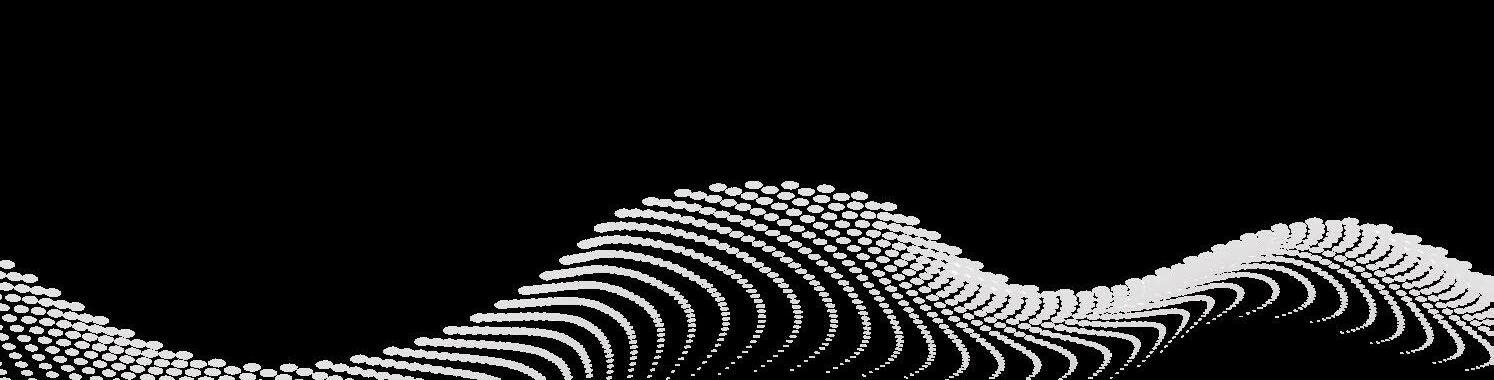
Conclusion
3D printing will have a significant impact on the maritime sector since it has the potential to reduce costs, reduce the carbon footprint of supply chains, to use fewer resources, and increase the efficiency of a ship’s operation. The processes are advancing, and the range of print materials is steadily increasing. Now that major classification societies and several large maritime companies have given their stamp of approval, 3D printing in the maritime industry can only become more widespread as it matures.