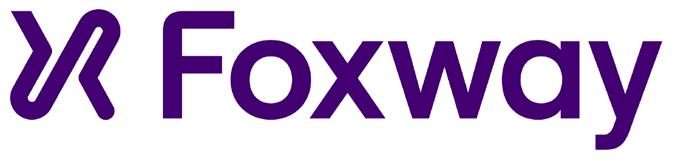
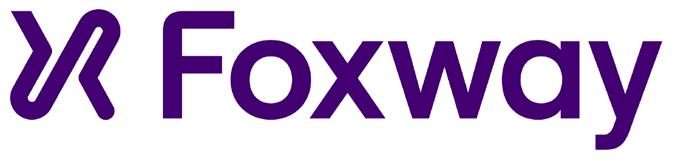
togetherWorkingwith Let’s work together .
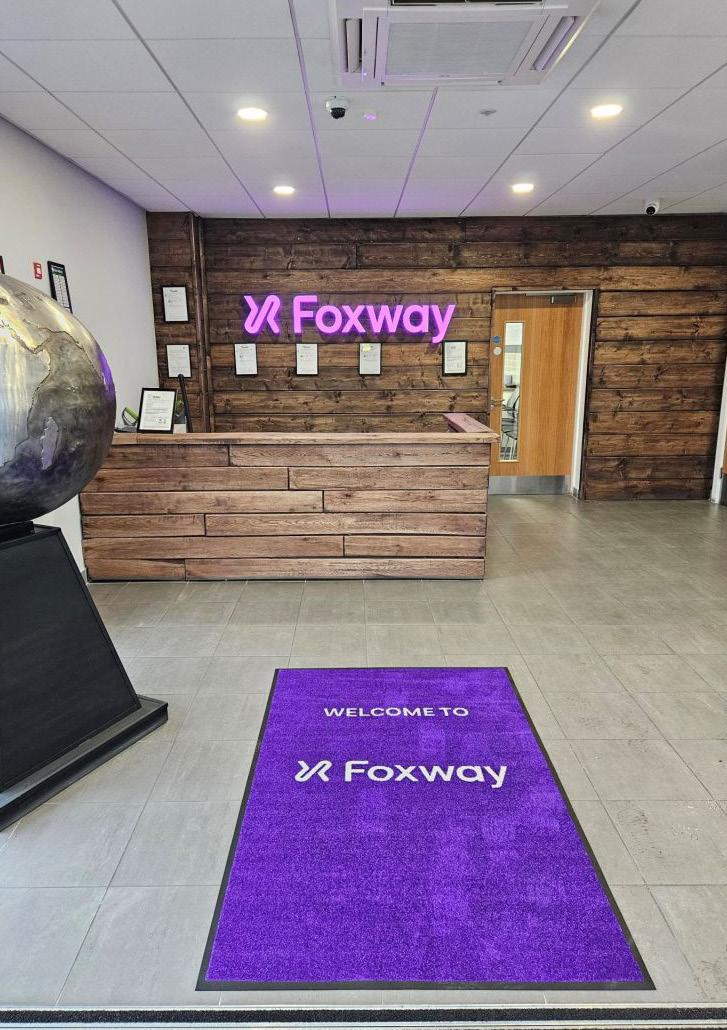

Foxway is a full-service, international resell and reverse logistics business focused on the mobile, IT, and electronics sectors. Foxway partners with the leading manufacturers, carriers, lessors, retailers, resellers, and large corporate accounts to handle their worldwide reverse logistics needs. With state-of-the-art processing centres in Texas (Global Headquarters) and Essex (European Headquarters), Foxway serves as a single-source solution for its partners, offering the full range of reverse logistics capabilities, including takeback, collection, inventory, data sanitization, repair, harvesting, and resell.
www.foxway.com
FIND US HERE
SPRINGWOOD INDUSTRIAL ESTATE
FOXWAY UK
A120 TOWARDS: DUNMOW TAKELY BISHOP’S STORTFORD HARLOW LONDON
A131 TOWARDS: GREAT NOTLEY GREAT LEIGHS CHELMSFORD
LIDL
MARSHALLS PARK
A131 TOWARDS: HALSTEAD EARLS COLNE SUDBURY LONG MELFORD
Foxway UK 4 Bradbury Park, Bradbury Drive, Springwood Industrial Estate, Braintree CM7 2DH
A120 TOWARDS: COGGESHALL STANWAY MARKS TEY COLCHESTER IPSWICH HARWICH
BRAINTREE FREEPORT
A120 TOWARDS: COGGESHALL STANWAY MARKS TEY COLCHESTER IPSWICH HARWICH
BRAINTREE
BRAINTREE VILLAGE
PARKING SPOTS
PARKING (FIRST 4 BAYS)
OFFICES
OFFICES
PARKING (NOT Foxway)
YOU SHOULD KNOW...
Toilet facilities are located on the site map
Breaks (1 hours) can be taken as a full 1 hours or 2 x 15min and 1 x 30min
Please make sure you are aware of your supervisor name
Mobile phones are not allowed to be used while onsite except during break times. Phones are not allowed within the main warehouse at any point.
Make sure you are aware of the fire assembly point, which is indicated on the site map.
Fire Tests – These are completed every Thursday around 10am. Fire evacuations are held randomly throughout the year.
MANUAL HANDLING HEALTH & SAFETY INFO
The health and safety of all its workers is paramount to Top Job Recruitment Limited. Whilst it is the client’s responsibility, under the Health & Safety at Work Act 1974, to provide a safe and healthy working environment, Top Job Recruitment has a duty of care to its temporary workers to ensure that they are aware of health and safety issues.
As a temporary worker your most important responsibilities are:
1
To take reasonable care of your own health and safety.
a. Avoid wearing jewellery or loose clothing and keep long hair tucked out of the way.
b. To take reasonable care not to put other people - fellow employees and members of the public - at risk.
c. To cooperate with your employer, making sure that you get proper training and that you understand and follow the company’s health and safety policy/policies.
2
3
4
Not to interfere with or misuse anything that’s been provided for your health, safety or welfare.
To report any injuries, strains or illnesses you suffer as a result of doing your job.
To tell your employer if something happens that might affect your ability to work (e.g. becoming pregnant or suffering an injury).
5
If you drive or operate machinery, to tell your employer if you take medication that makes you drowsy.
Clients will have their own Health and Safety policies but most of the following general safety rules will be in place and must be observed by all workers
More than a third of all “over-three-day” injuries reported each year to the enforcing authorities are caused by manual handling – the transporting or supporting of loads by hand or by bodily force.
The Manual Handling Operations Regulations 1992 require employers to:
AVOID the need for hazardous manual handling, so far as is reasonably practicable;
ASSESS the risk of injury from any hazardous manual handling that can’t be avoided
REDUCE the risk of injury from hazardous manual handling, so far as is reasonably practicable.
You need to assess the task, load, working environment and individual capacity.
There is no such thing as a completely ‘safe’ manual handling operation, but working within the following guidelines will cut the risk and reduce the likelihood of injury.
Manual handling will be eliminated where possible with the use of mechanical lifting equipment; if not possible the risk of injury will be reduced with the use of handling aids such as pallet trucks, sack barrows and trolleys etc.
Where manual lifting is required, care must be taken especially whilst lifting products over 25kg and assistance must be sought. Assess the weight properly before lifting and where appropriate PPE, gloves are a requirement for this operation.
If you believe that you are at serious risk of an injury then don’t lift, seek guidance and assistance from the supervisor.
Factors that affect likelihood of injury…
Weight of load
Size and shape of load
Posture during manual handling
The distance to lift
Nature of manual handling movement
Frequency of manual handling
Working environment
Capability of the person
Do's
One Stop & think – Take a balanced stance with your feet about shoulderwidth apart.
Two
Three
Four
Five
Position the feet – One foot can be behind the object and the other next to it.
Adopt a good posture – Squat down to lift the object, but keep your heels off the floor. Get as close to the object as you can. Use your palms, (not just your fingers) to get a secure grip on the load.
Get a firm grip & keep close to body – Lift gradually (without jerking) using your leg, abdominal and buttock muscles and keeping the load as close to you as possible. Keep your chin tucked in so as to keep a relatively straight back and neck line.
Stand straight & move feet only – Once you’re standing, change directions by pointing your feet in the direction you want to go and turning your whole body. Avoid twisting at your waist while carrying a load. When you put a load down, use these same guidelines in reverse.
Don'ts
Don’t bend your back
Don’t crouch
Don’t tilt your head
Don’t move your upper body, when moving the load
