SKID MOUNTED LUBE OIL BLENDING PLANT

What is Skid Mounted Lube Oil Blending Plant?
The Skid Based Lube Oil Blending Plant stands as a pinnacle of efficiency and innovation in the lubricant manufacturing industry. This state-of-the-art solution is meticulously designed to streamline the process of blending lube oils with precision and reliability. Mounted on a compact and modular skid, this plant offers a turnkey solution that optimizes space utilization, making it an ideal choice for industries where real estate is a critical consideration.
Equipped with advanced automation, the skid-mounted blending plant minimizes the need for manual intervention. Intelligent sensors, programmable logic controllers (PLCs), and user-friendly interfaces collaborate seamlessly to orchestrate the blending process with precision. This not only enhances the overall efficiency of the manufacturing process but also contributes to the production of consistently high-quality lubricants.
The skid-mounted configuration offers additional advantages, simplifying installation and commissioning. The compact footprint allows for easy integration into existing facilities, reducing both time and costs associated with plant setup. This feature makes the skidmounted lube oil blending plant an attractive choice for both new installations and facility upgrades.
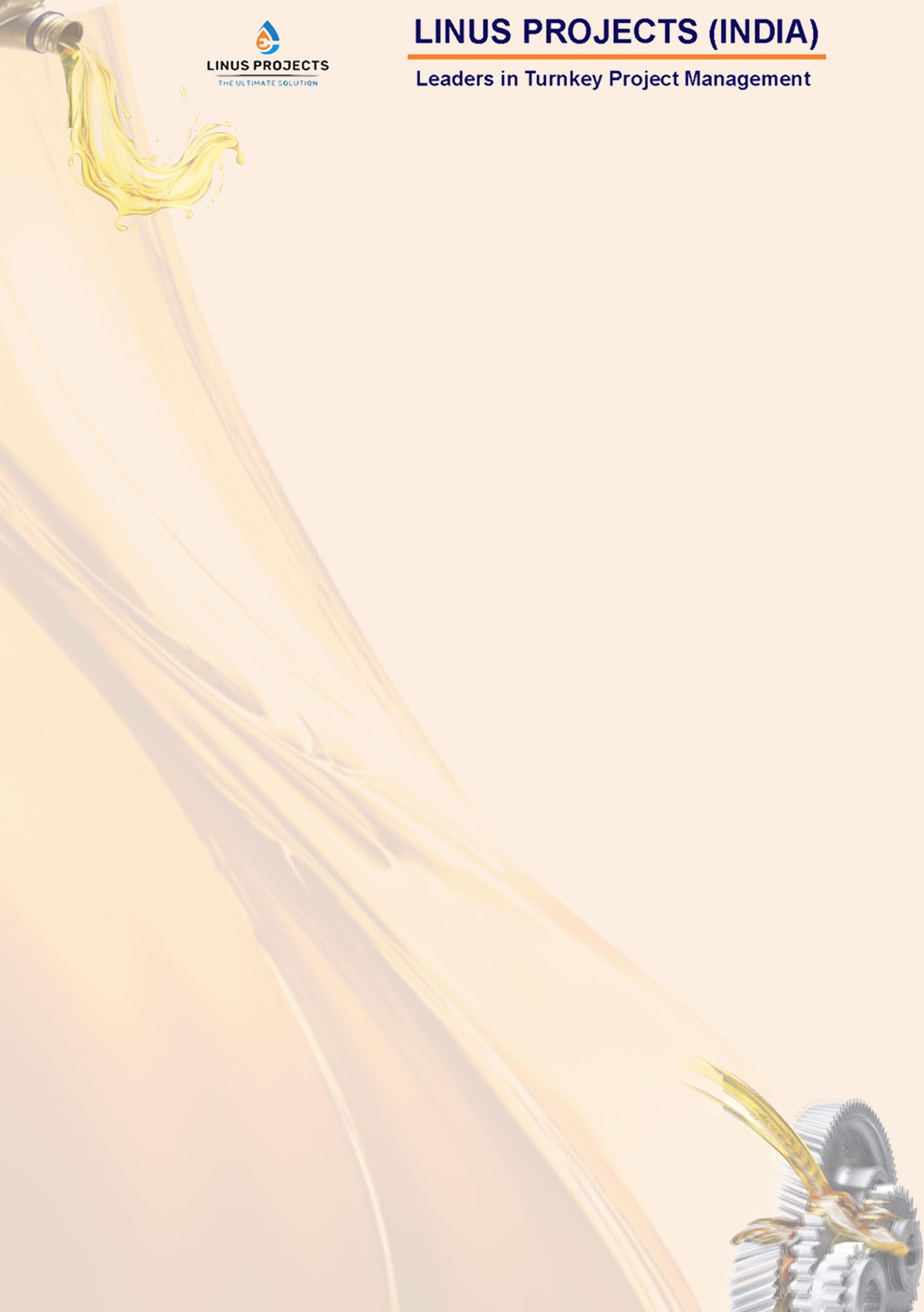

In terms of maintenance and scalability, the skid-mounted system excels. Routine maintenance is streamlined, ensuring minimal downtime and maximizing operational continuity. Moreover, the modular nature of the system facilitates easy scalability. Manufacturers can expand their production capacity by adding additional skids without major disruptions to ongoing operations.
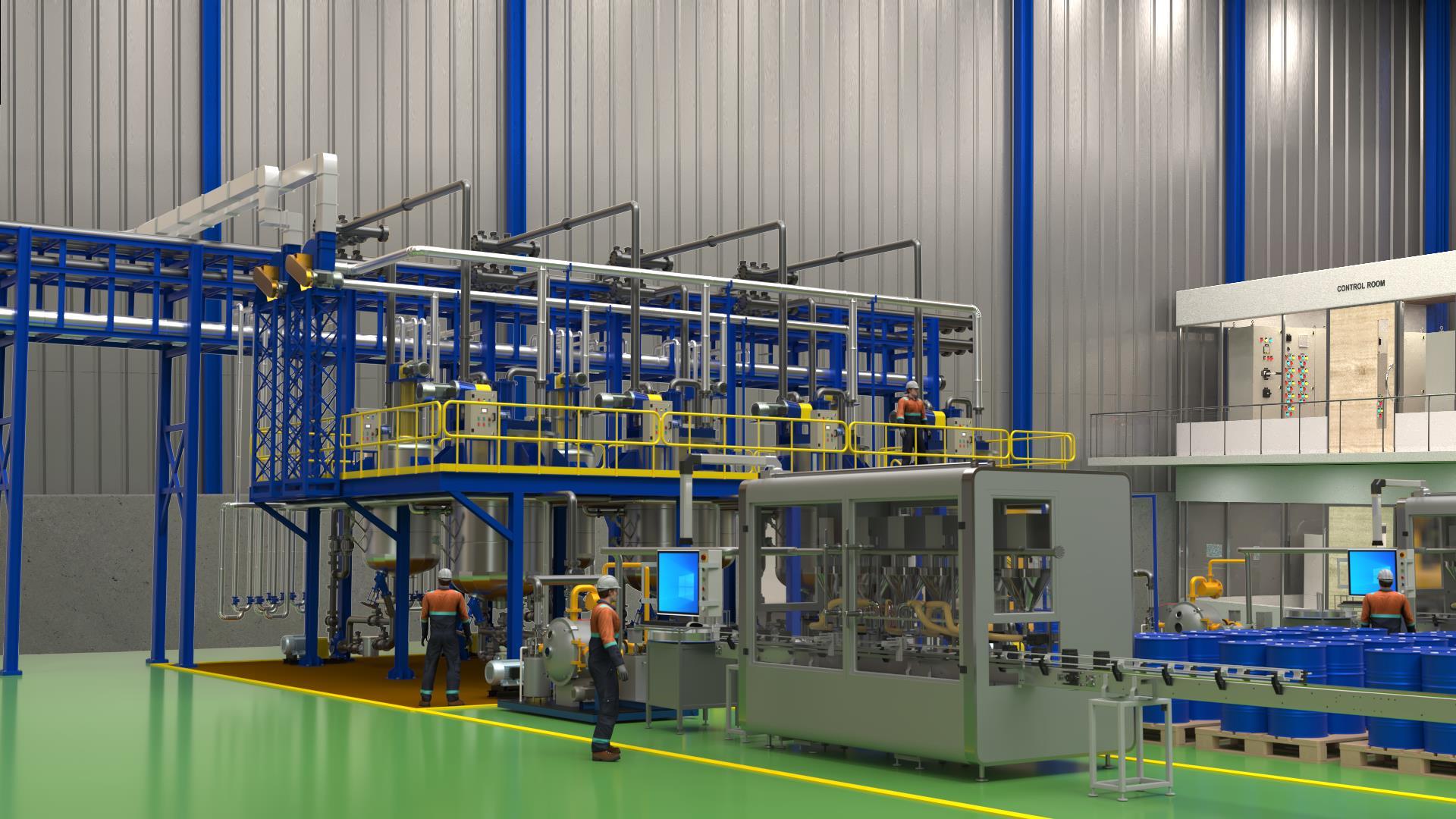
Whether deployed in the automotive, industrial, or aviation lubricant sectors, the Skid based lube oil blending plant offers a comprehensive solution for manufacturers seeking efficiency, flexibility, and reliability in their lubricant production processes. As a testament to technological advancements in the industry, this plant stands as a strategic investment, empowering manufacturers to meet market demands, maintain product quality, and stay at the forefront of the dynamic lubricant market.
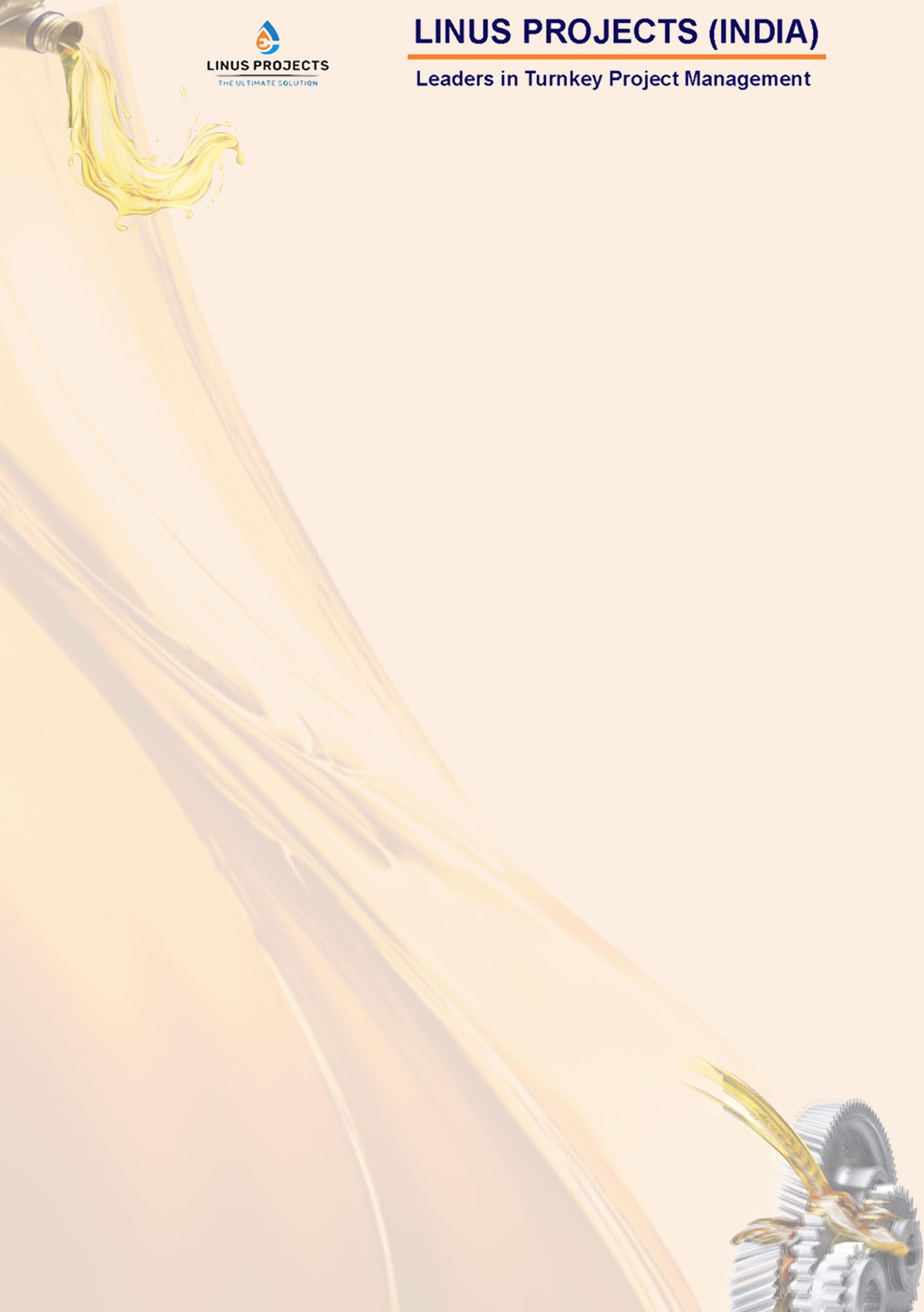
SKID - LUBE BLENDER
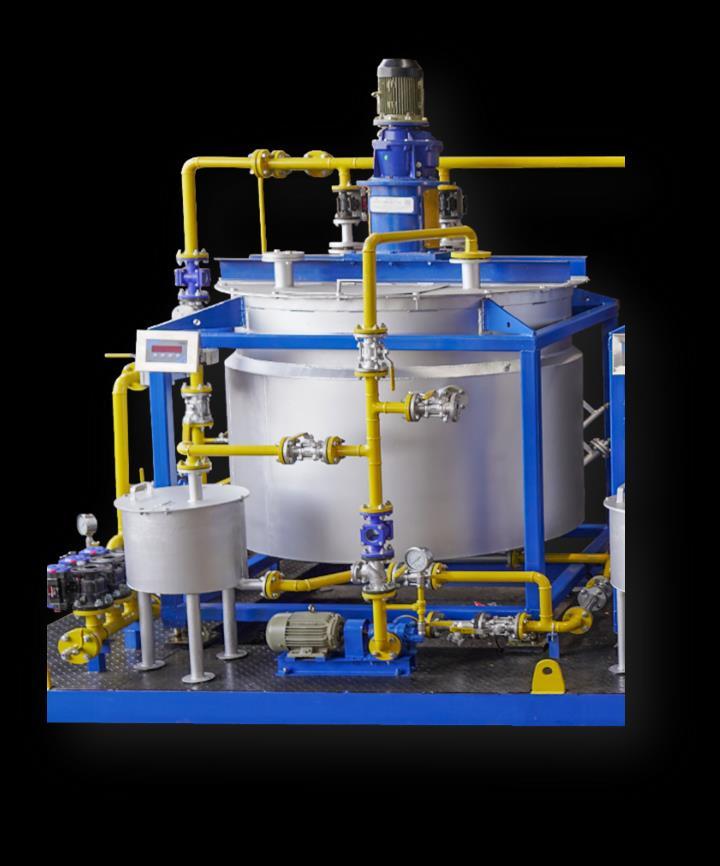
FEATURES:
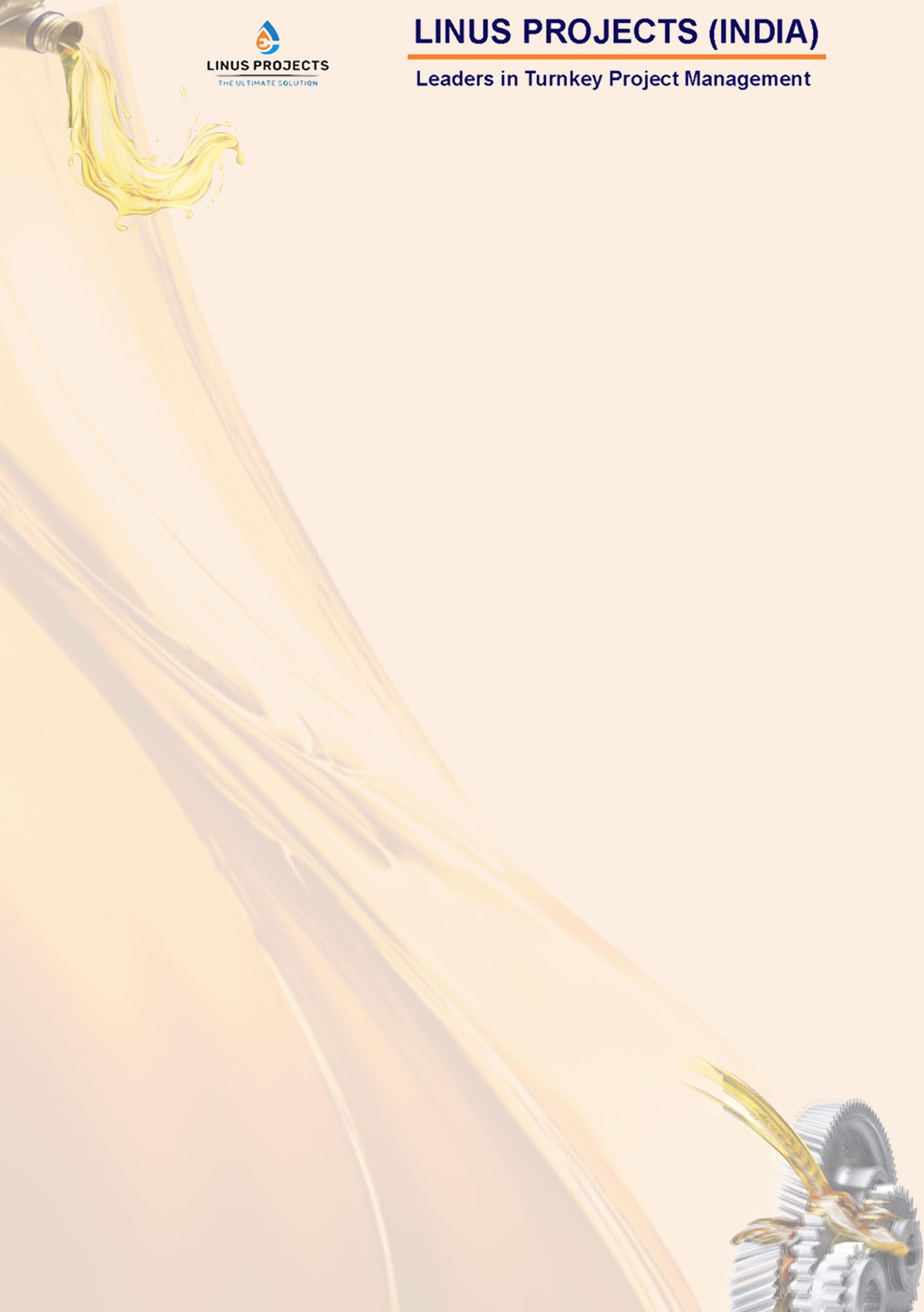
One of the key features of the skid-mounted lube oil blending plant is its versatility. The system accommodates a wide range of base oils and additives, allowing for the formulation of a diverse array of lubricant products tailored to specific industry needs. The modular design ensures flexibility in production, enabling manufacturers to adapt quickly to changing market demands and product specifications.
The Skid Mounted Lube Blender comes equipped with a range of features that collectively enhance its efficiency, flexibility, and usability in lubricant blending processes. These features make it a standout solution for manufacturers seeking precision and adaptability intheir operations.
• The system is mounted on a skid, offering a compact and modular design that simplifies installation and integration into existing facilities.
• The Skid based configuration optimizes space utilization, making it suitable for installations with spatial constraints.
• The blender is designed to accommodate a diverse range of base oils and additives, allowing manufacturers to formulate various lubricant products.
• Versatility in formulation supports applications across different industries, from automotive to industrial and specialty lubricants.
• Equipped with intelligent sensors, the system ensures precise measurement and monitoring of ingredients during the blending process.
• Programmable logic controllers (PLCs) enable automated control of the blending sequence, optimizing consistency and reducing the need for manual intervention.
• Intuitive user interfaces enhance ease of operation and provide real-time monitoring capabilities for operators.
• The system employs efficient mixing mechanisms to ensure thorough blending of base oils and additives, resulting in high-quality lubricant formulations.
• The automated and streamlined blending process reduces processing time, contributing to overall operational efficiency.
• Automated controls and precision in the blending process contribute to consistent and high-quality lubricant formulations.
The system may incorporate traceability features to monitor and record the ingredients used, enhancing quality control.
VI KETTLE:
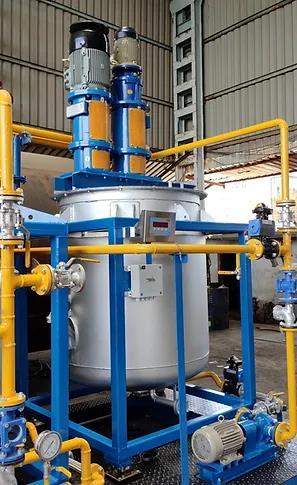
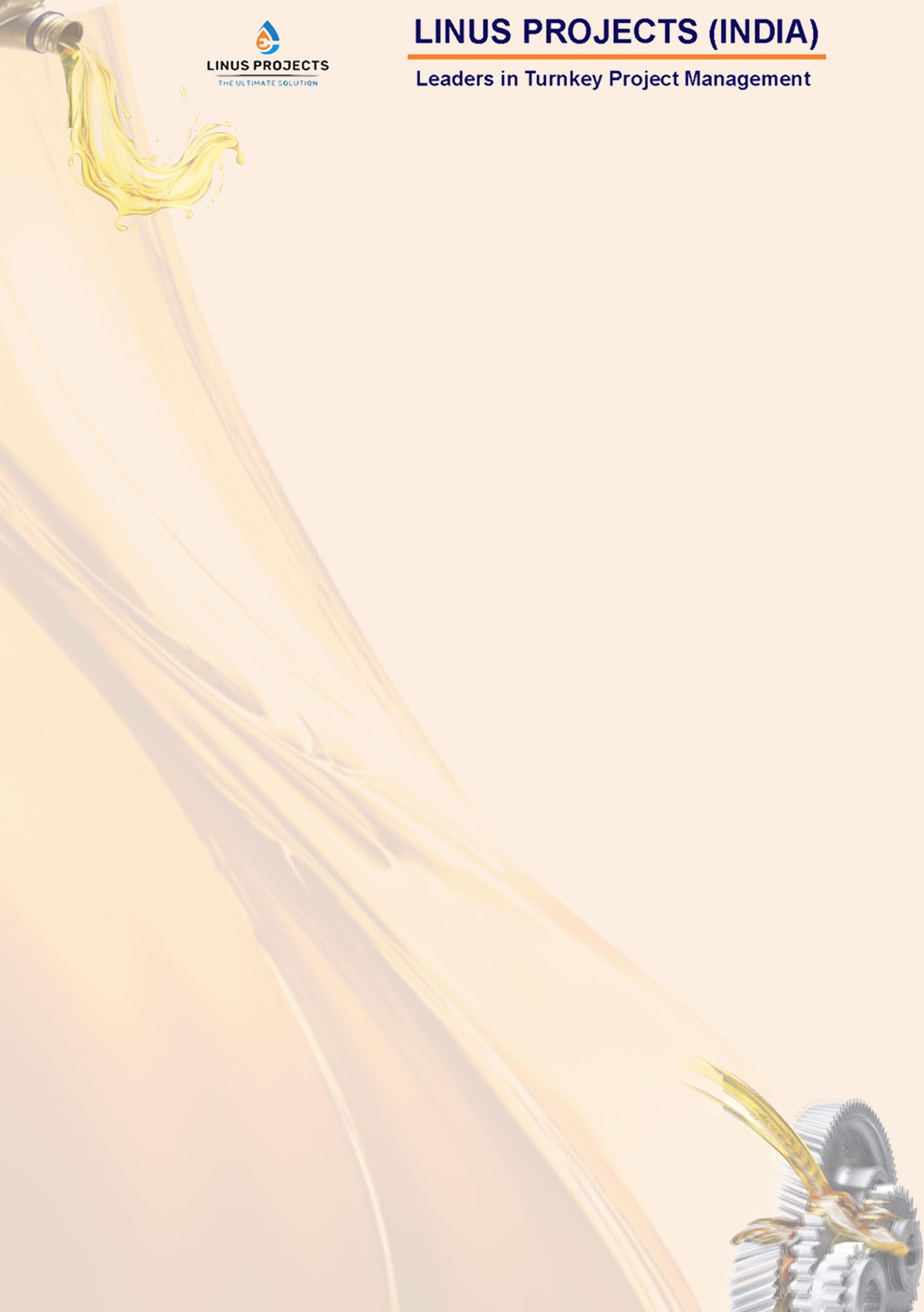
Viscosity index improvers are additives that enhance the viscosity-temperature relationship of lubricating oils, making them more stable across a range of temperatures. The process of blending or incorporating these additives often involves specialized equipment, including kettles or vessels.
Here are some key points regarding a viscosity index improver kettle:
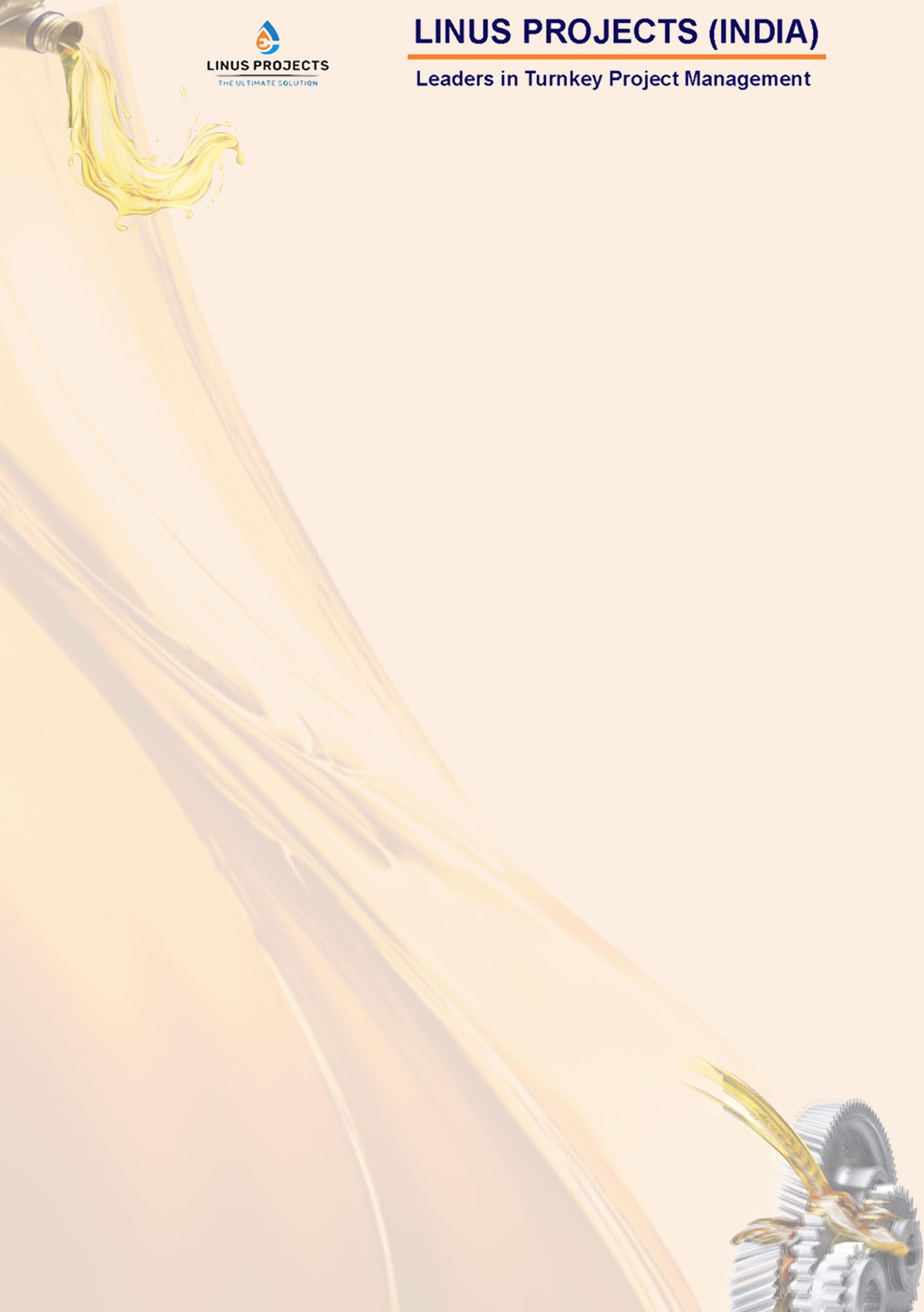
FEATURES:
• The kettle is designed for the controlled blending and incorporation of viscosity index improvers into lubricating oils. It ensures uniform distribution of the additive within the oil blend.
• The kettle is typically constructed from materials that are compatible with the lubricant additives and base oils, ensuring the integrity of the lubricant formulation.
• The kettle often includes a heating mechanism to maintain the lubricant blend at an optimal temperature for effective mixing and incorporation of the viscosity index improver.
• Agitation or mixing mechanisms inside the kettle help homogenize the blend, ensuring the even distribution of the additive.
• Precise temperature control is crucial during the process to prevent degradation of the lubricant components and to facilitate the proper incorporation of the viscosity index improver.
• The kettle may include an additive injection system to introduce the viscosity index improver into the lubricant blend accurately and at the desired rate.
• Safety features such as pressure relief valves, temperature sensors, and emergency shut-off mechanisms may be incorporated to ensure safe and controlled operation.
• The size and capacity of the kettle depend on the production scale and requirements of the lubricant blending facility. Larger facilities may use industrialscale kettles with higher capacities.
• In modern lubricant blending plants, the viscosity index improver kettle is often integrated into the overall automation system. This integration allows for synchronized control with other units in the blending process.
• Kettles used in lubricant blending are designed for ease of cleaning and maintenance. This is essential for preventing cross-contamination between different lubricant formulations.
GEAR PUMP
A Gear pump is a common type of positive displacement pump employed in lube oil blending plants to facilitate the transfer and circulation of lubricant fluids. It plays a crucial role in the movement of base oils, additives, and blended lubricants within the plant. Here are key features and functions associated with the use of a gear pump in a lube oil blending plant:
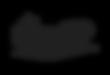
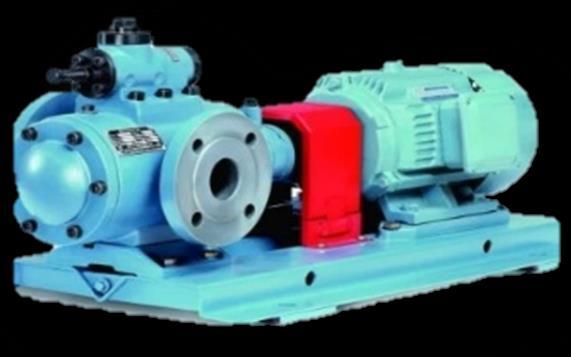
FEATURES:
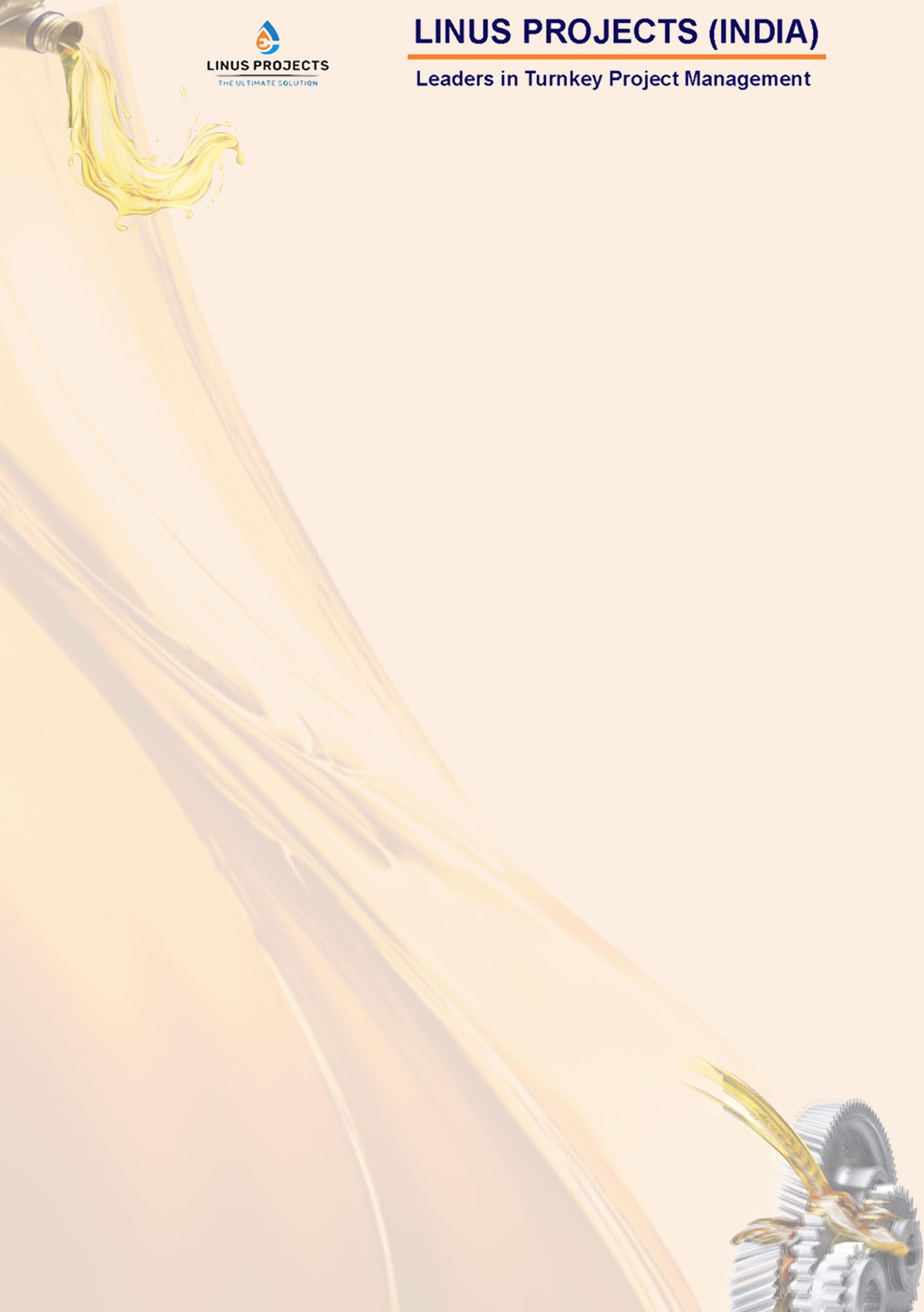
These Gear Pumps is used for the transfer of 4 types of Base oil from the tank farm to ABB blenders SN900, SN150, SN100, SN250 etc.
A gear pump uses the meshing of gears to pump fluid by displacement. They are one of the most common types of pumps for hydraulic fluid power and Lubricant Grease projects.
• The system is mounted on a skid, offering a compact and modular design that simplifies installation and integration into existing facilities.
• The skid-mounted configuration optimizes space utilization, making it suitable for installations with spatial constraints.
• The blender is designed to accommodate a diverse range of base oils and additives, allowing manufacturers to formulate various lubricant products.
• Versatility in formulation supports applications across different industries, from automotive to industrial and specialty lubricants.
• Equipped with intelligent sensors, the system ensures precise measurement and monitoring of ingredients during the blending process.
• Programmable logic controllers (PLCs) enable automated control of the blending sequence, optimizing consistency and reducing the need for manual intervention.
• Intuitive user interfaces enhance ease of operation and provide real-time monitoring capabilities for operators.
• The system employs efficient mixing mechanisms to ensure thorough blending of base oils and additives, resulting in high-quality lubricant formulations.
• The automated and streamlined blending process reduces processing time, contributing to overall operational efficiency.
• Automated controls and precision in the blending process contribute to consistent and high-quality lubricant formulations.
• The system may incorporate traceability features to monitor and record the ingredients used, enhancing quality control measures.
BASKET FILTERS:

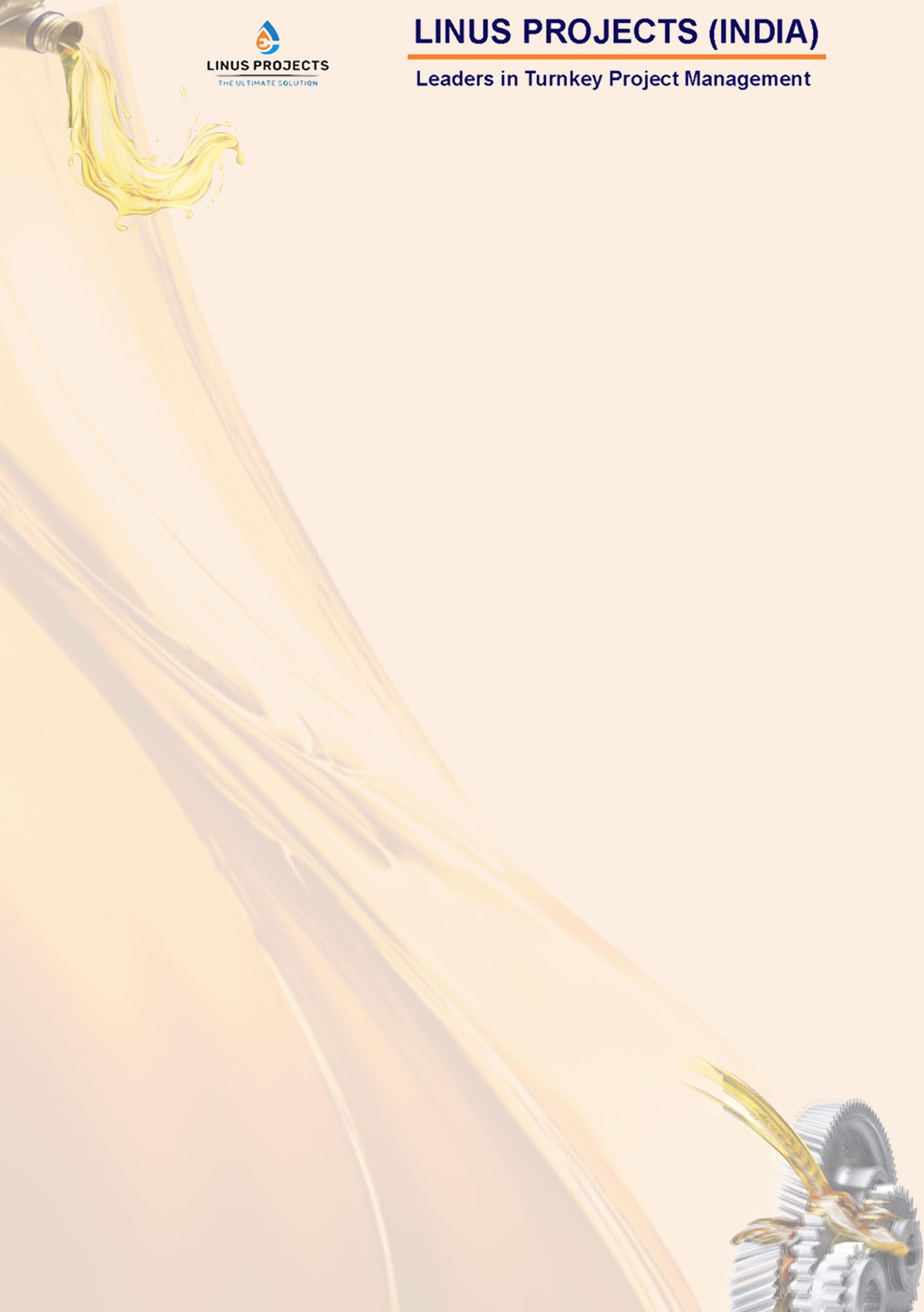
Unfiltered liquid enters the strainer housing and passes down them. Solids are retained inside of strainer mesh which is removed when the unit is serviced. strainers are normally supplied with a spring arrangement at the top of the filter element.
This will ensure any type of bypass & confirm the position of the strainer even in case of reverse flow. Fluid bypass around strainer is prevented by optional “O” ring seal between strainer rim and the housing inside diameter. 200-micron filter as per base oil pump supplying-3 nos.
LOAD CELL:
Load cell required for blending vessel to know exact weight of incoming and outgoing material in blender. Load cell having following advantages
Built in Safety against vessels tilting and build forces, allows vessels expansion & contraction, which Occurs due to thermal effect. Flexible copper earthing strip to protect the load cell from lightening or welding current.
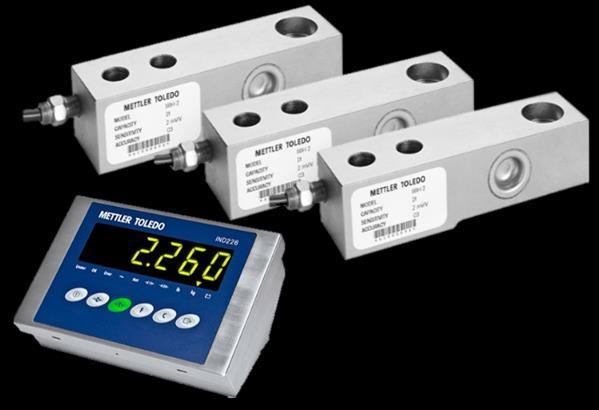
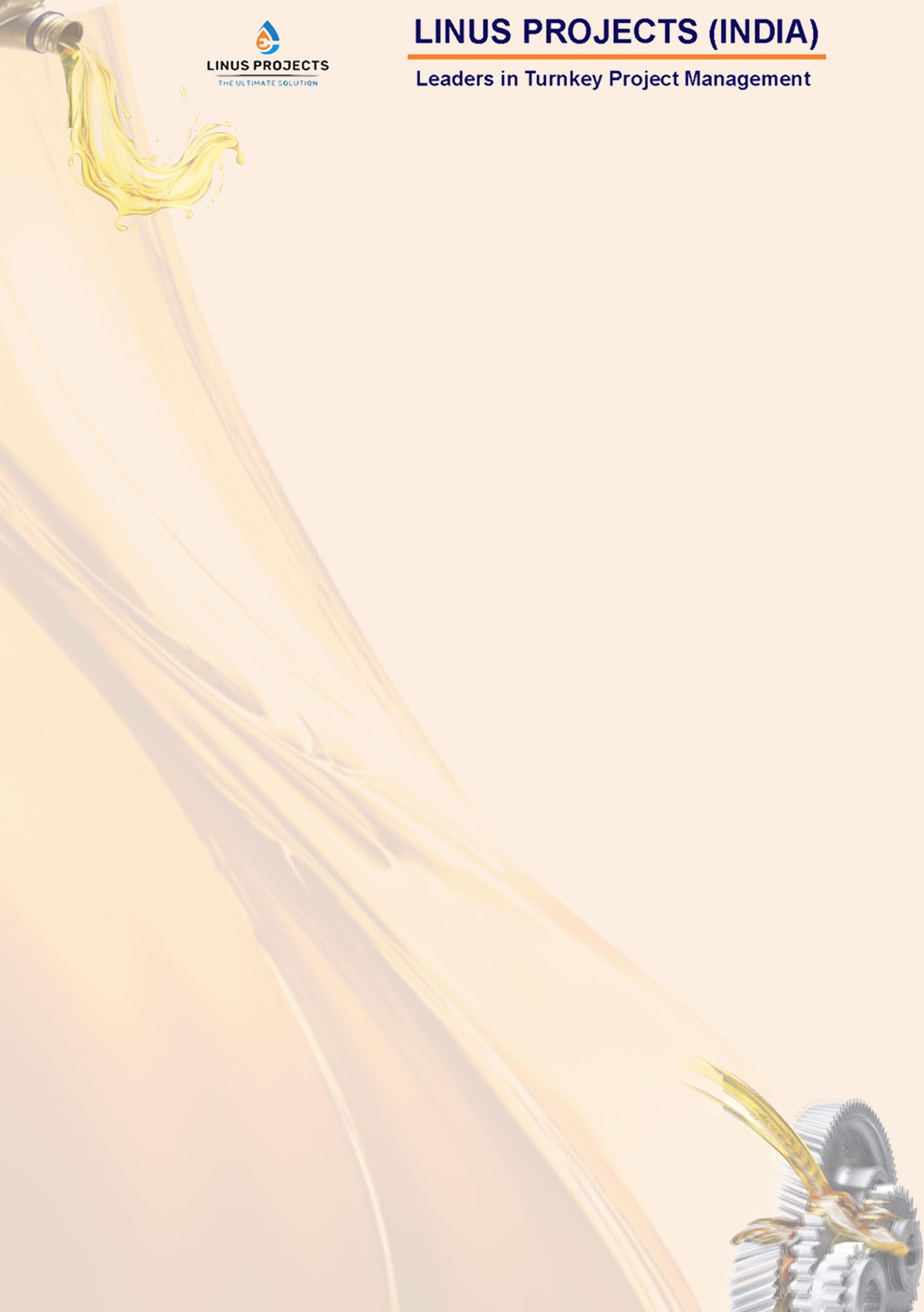
In built Load Cell cable protection plate & Overload protection plate with Heat Insulation Pad
AUTOMATION AND MANUAL VALVE:
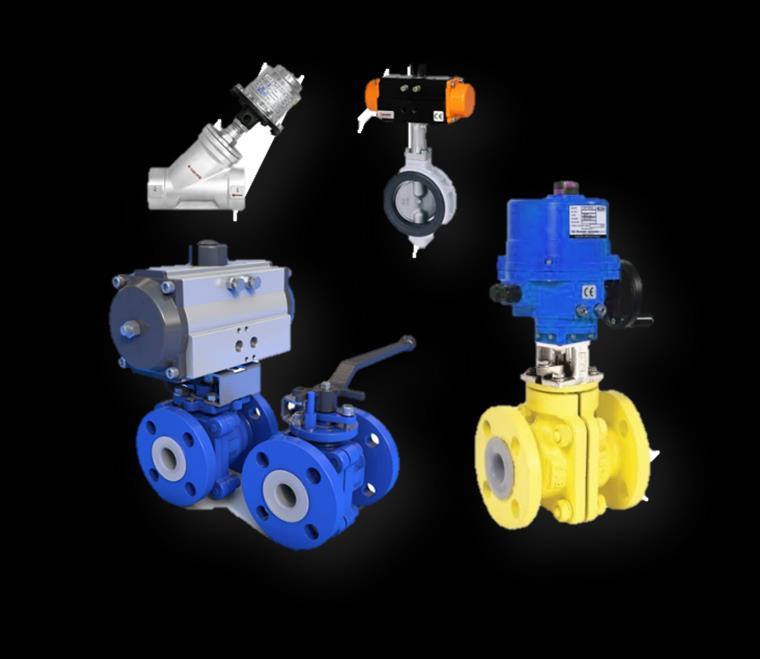
A valve is a device that regulates, directs or controls the flow of a fluid (liquids, fluidized solids, or slurries) by opening, closing, or partially obstructing various passageways. Valves are technically fittings, but are usually discussed as a separate category. In an open valve, fluid flows in a direction from higher pressure to lower pressure. The simplest, and very ancient, valve is simply a freely hinged flap which drops to obstruct fluid (gas or liquid) flow in one direction, but is pushed open by flow in the opposite direction. This is called a check valve, as it prevents or "checks" the flow in one direction. Modern control valves (solenoid valves) may regulate pressure or flow downstream and operate on sophisticated automation systems.
Linus projects Supply high grade cast steel valves that last for decades. Valves are designed as ASME codes.
INSTRUMENTS AND GAUGES:
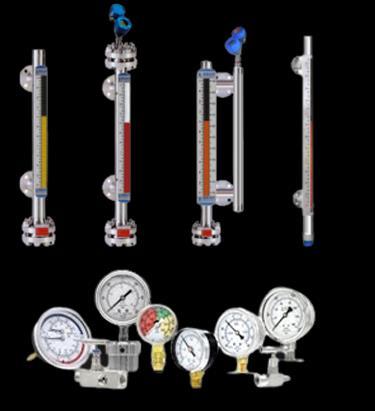
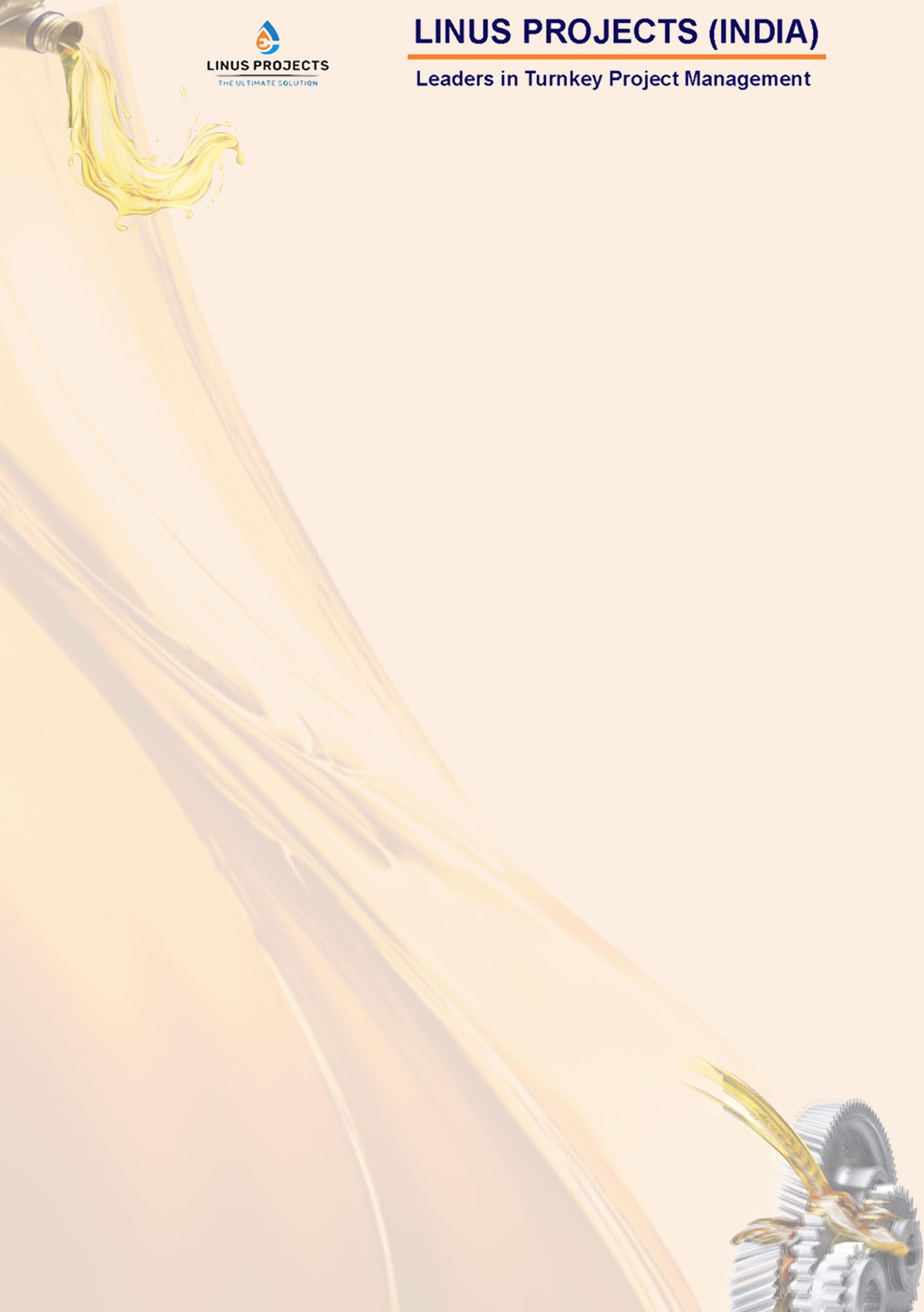
Pressure gauges measure gas and liquid pressure and are available in analog and digital styles. These gauges are typically used in pressure and vacuum applications, including testing, laboratory, process control, and manufacturing. Dial indicating or analog pressure gauges have a needle that is calibrated to respond to fluctuations that occur within a specified parameter.
They are often installed to have direct contact with a liquid or gas and provide local readings based on changes in pressure or vacuum.
PIPE & FITTING FOR PLANT (within factory limit):

The design of process plants is a complex design Linus projects teamwork fabricate all the piping on the platform at the site to avoid welding and fabrication work involvement as per site feasibility.
Linus project supplies high-grade carbon steel pipe, flanges, and fittings as per ASME B16.5 code.
All the pipe is coated with ant rust painting and 2 coats of paint for the long life of the plant.
INSULATION FOR BLENDERS:
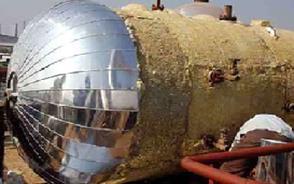
ADDITIVE DOSING TANK:
All insulation shall be done by ROCKWOOL mattress50mm thick as required of Density 100Kg/cu mtr of reputed make and cladded with aluminium / GI sheet 24 gauge. This part of the job shall be done on the site. The material shall be supplied loose and client has to organize the same at site under our guidance. Insulation of pipelines below blenders to filling lines to be done on site.
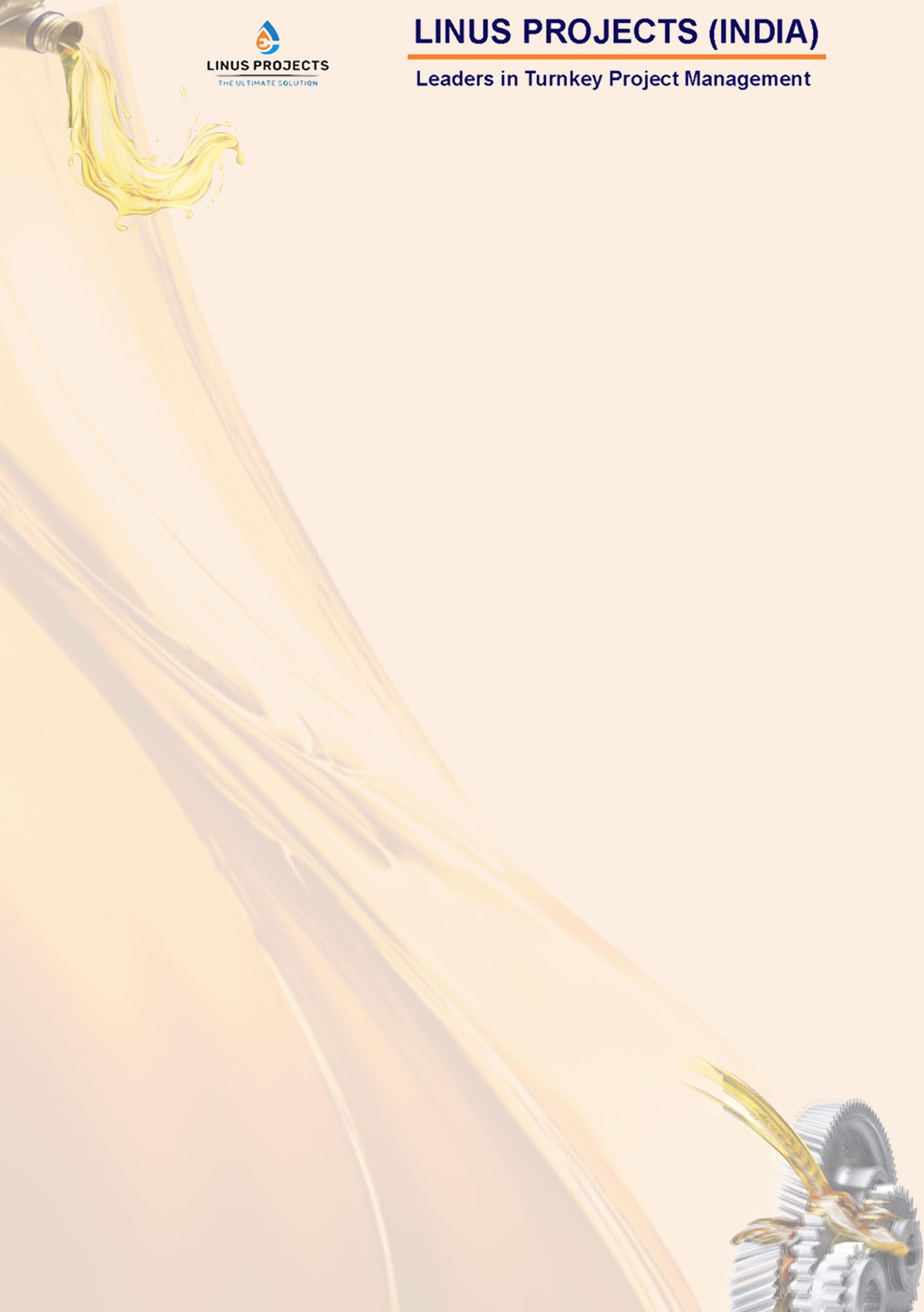
An additive dosing tank in a lube oil blending plant serves as a critical component in the precise formulation of lubricants. This tank is specifically dedicated to the controlled and accurate addition of various additives into the base oil to achieve the desired lubricant properties. Here are key features and functions associated with an additive dosing tank in a lube oil blending plant
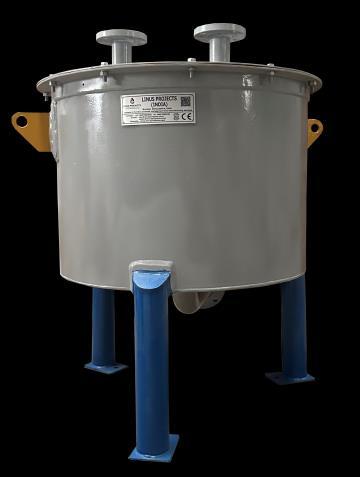
FEATURES:
• The additive dosing tank is equipped with an additive injection system designed for the controlled release of specific additives into the blending process.
• This system ensures a precise and measured dosage of additives, contributing to the consistency and quality of the final lubricant formulation.
• The dosing tank is often designed for modular integration within the overall lube oil blending plant. It seamlessly interfaces with other components, such as base oil tanks and mixing units.
• The tank is versatile and compatible with a wide range of lubricant additives, including anti-wear agents, detergents, dispersants, antioxidants, and viscosity modifiers.
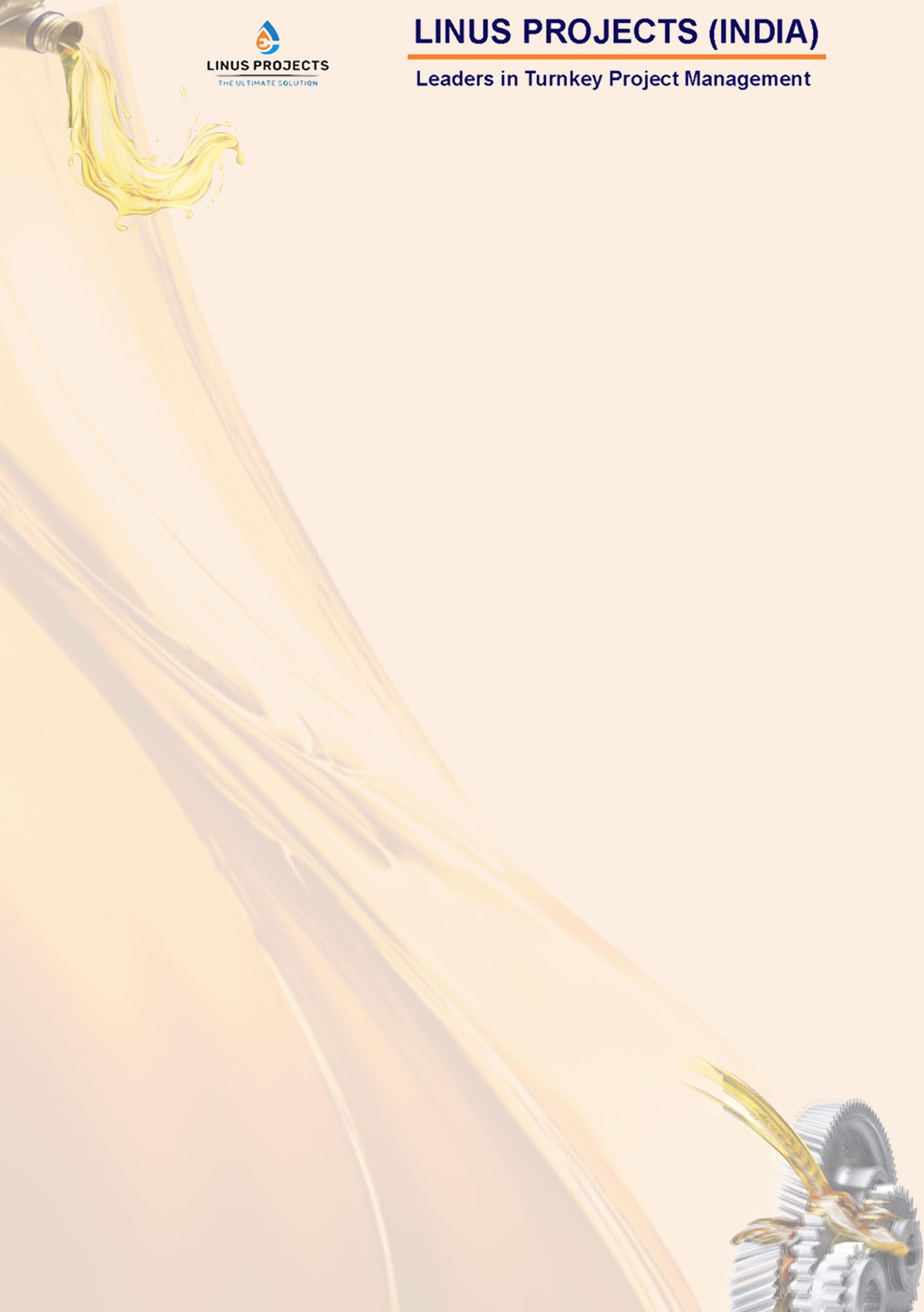
• The dosing tank is designed to be adjustable and flexible to accommodate changes in formulation requirements. Manufacturers can easily adapt the dosages based on variations in base oils or specific product formulations.
• Many additive dosing tanks incorporate a Clean-In-Place (CIP) system. This feature facilitates easy cleaning of the tank between different additive formulations, preventing cross-contamination and maintaining product integrity.
• Safety features, such as leak detection and overflow protection, are often integrated into the additive dosing tank to prevent spills and ensure a safe working environment.
• The system may include features for traceability and documentation. This ensures that dosages are recorded, providing a comprehensive record for quality control and regulatory compliance.
• The additive dosing tank is seamlessly integrated into the overall plant automation system. This allows for coordinated control and synchronization with other units in the blending process.
• This flexibility allows manufacturers to formulate lubricants tailored to specific industry standards and application requirements.
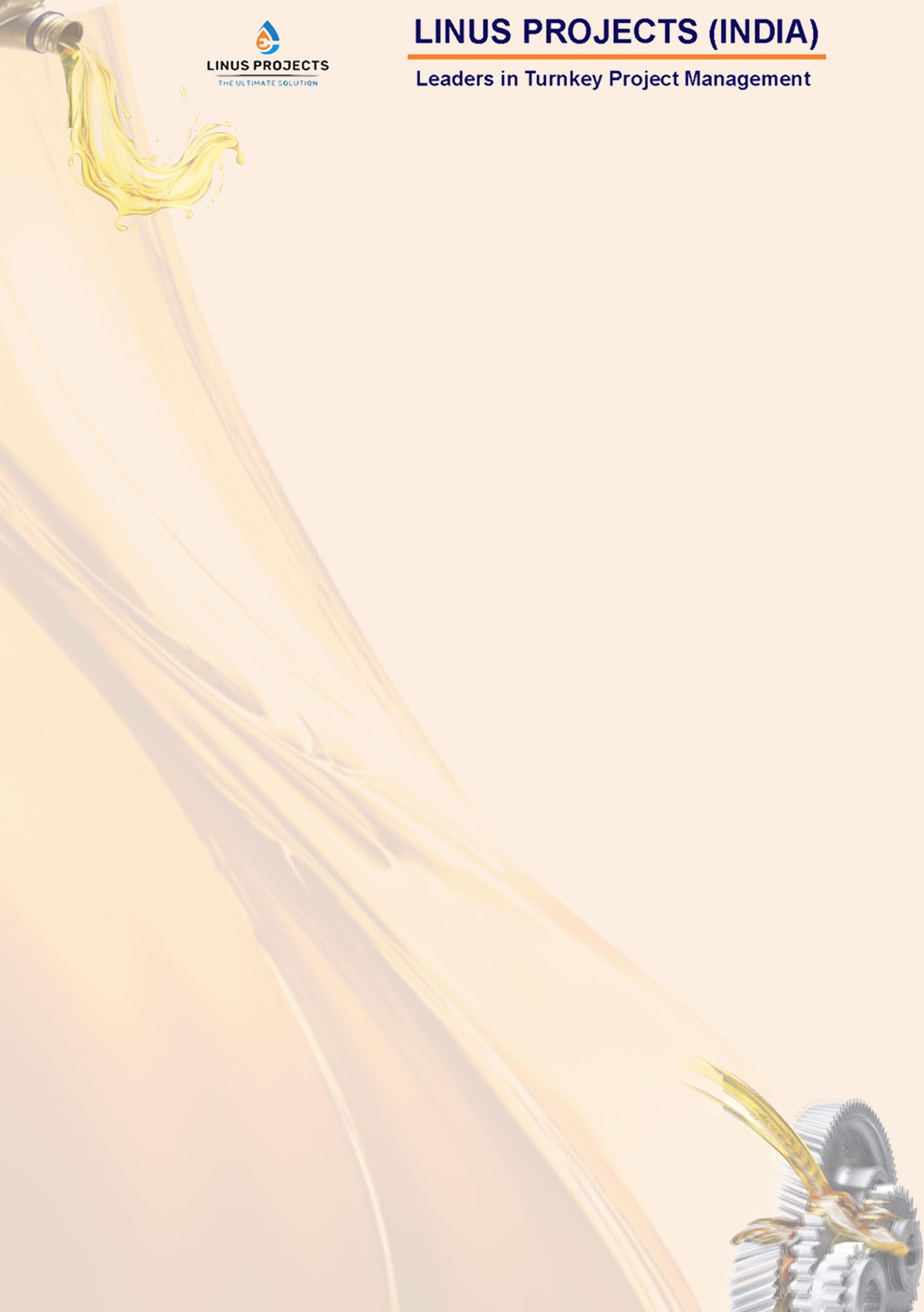
FOUR HEAD FILLING LINE: (RANGE:1 LTR TO 5LTRS):
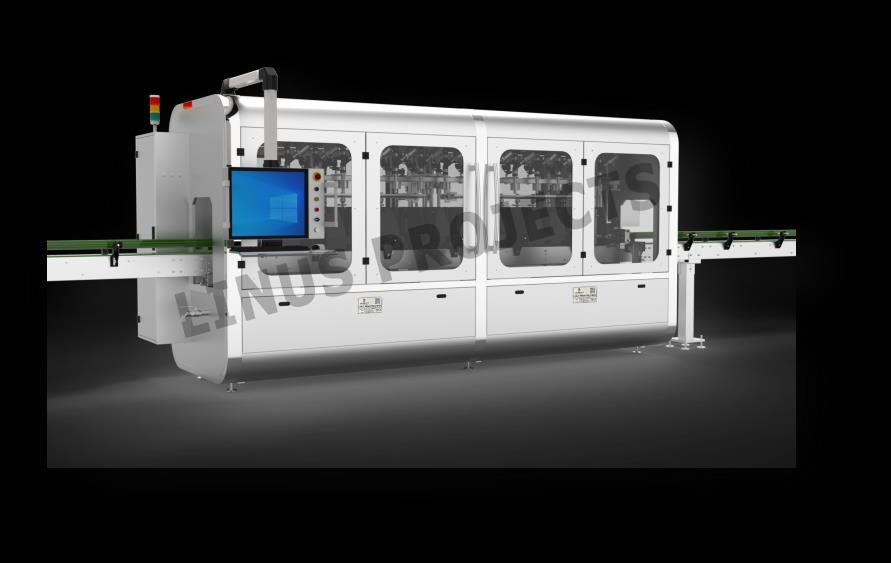
It is volumetric type complete with a 50 Ltrs stainless steel storage hopper. The pump is suitable for filling of coolants in plastic containers from 250ml to 5 Ltrs. A 1 HP electric motor drives the pump. An electronic control panel with volume control setting is provided. The Bottles are to be placed manually on Machine. the nozzles dive into the Bottles and filling take place. The volume adjustment is manual through cam adjustment. The machine is constructed in Stainless steel. Estimated filling speed: 500ml @ 14 Bottles per minute & 1000 ml @ 12 fills per minute.
LINER CAPPING MACHINE:
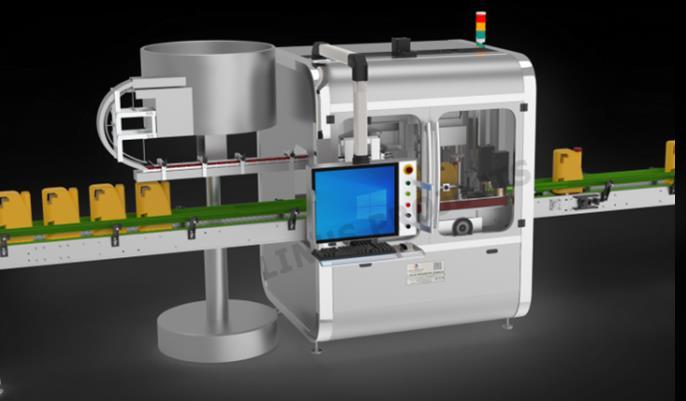
The machine comprises of Cap Vibrator for cap orientation & capping unit. The caps fed in the vibratory hopper are properly oriented here. The properly oriented caps are brought out through chute and supported at the end by spring loaded fingers the containers as it comes out of the filling station moves to the capping unit, where-in it picks up the cap and goes towards the capping head. The caps are subsequently tightened through magnetic clutch system. The capped bottles finally emerge out of the machine through discharge conveyor. The speed can be adjusted through the VFD on the conveyor Necessary Mechanism shall be provided for no bottle – no cap. The torque can be set on the PLC of the filling machine. The capping machines will be supplied with parts for one pack size along with Eight feet long and 150mm wide conveyor. Additional change part will be required for each pack for any change in dimensions of the containers which shall be charged at extra. The machine Power Requirement:3 Phase, 415V Volts AC., 50 Hz. Load: 2 HP
INK-JET PRINTER:
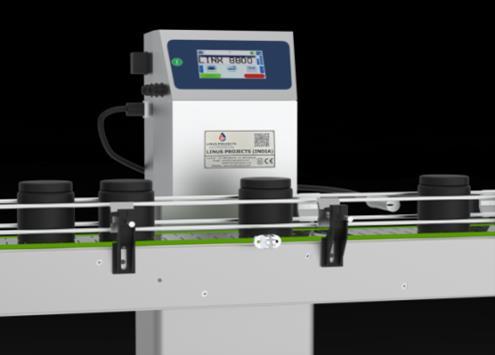
LABELING MACHINE:
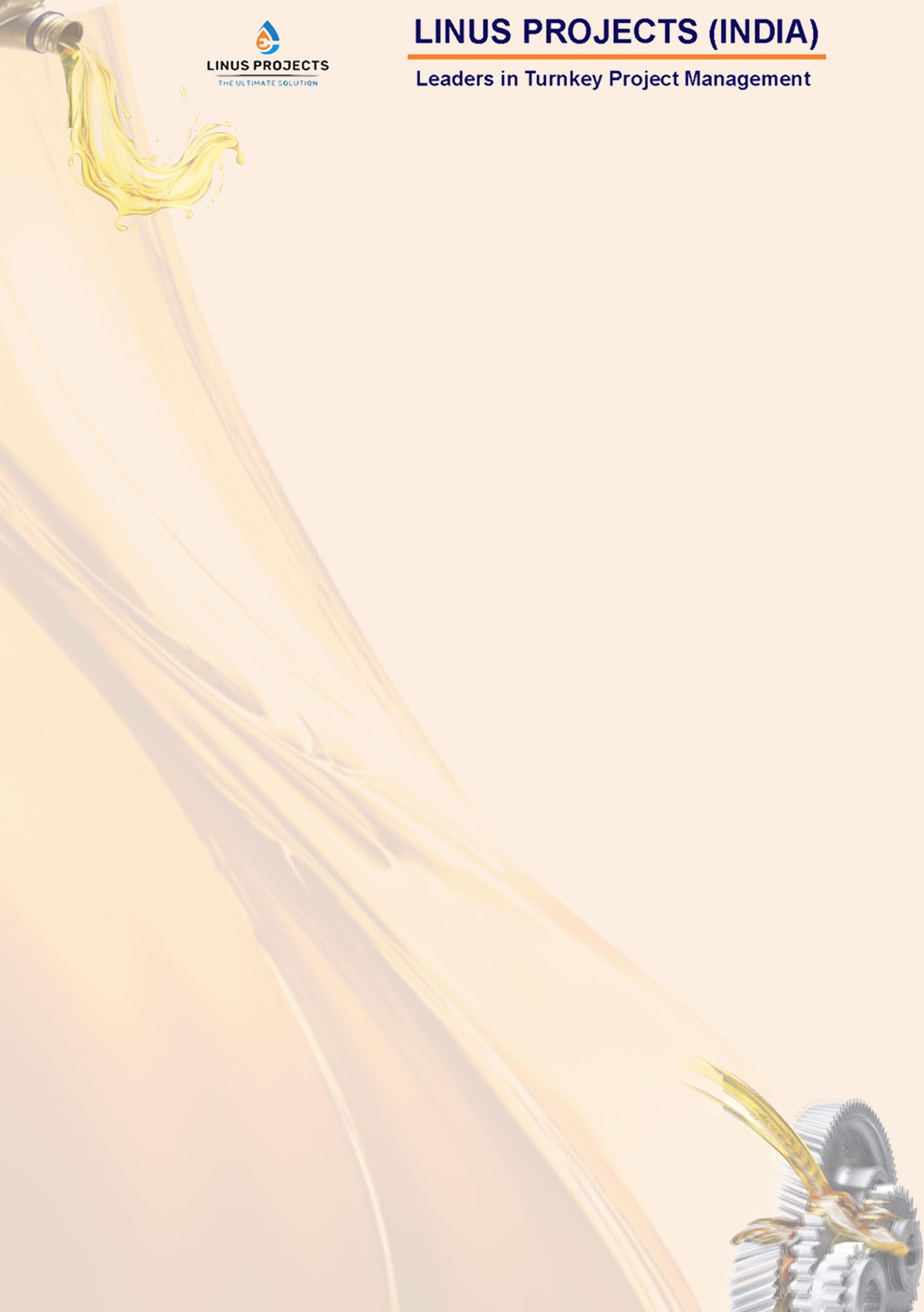
Automatic solution for printing batch identification codes, MRP, best before and packaged dates, plus QR codes onto almost any material, including specialist applications such as food and metals. CIJ coding & marking machines offer high-speed, reliable batch, lot, MRP & date coding for product identification and traceability. Our continuous ink jet batch printing machines can code onto a wide range of materials, even in dusty, hot, and wet environments. Automated Batch code, MRP & Date Coding.
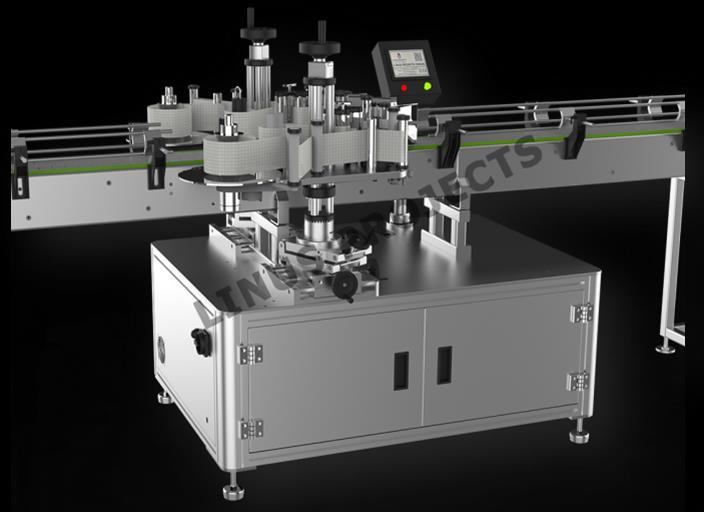
The Automatic Self-Adhesive Sticker Labelling Machine is one of the most users friendly. The machine is used for two sides labelling on the flat surfaces of different sizes of flat containers. It is capable of labelling up to 40 containers per minute depending on products and label size. The automatic model is equipped with a belt spacing device resulting in a simple “No change parts required”. The flat containers are positioned & curate spacing between two containers by the belt spacing device and a belt drive mechanism holds the container from the top of the container for two sides labelling on the flat container at the labelling point, an electronics product sensor sense container & relies on a label from self-adhesive label roll. If the machine is equipped with a batch printing device in that case batch printing device prints the batch no. & another matter on the label during label is stationary means time between the sensing of two labels.
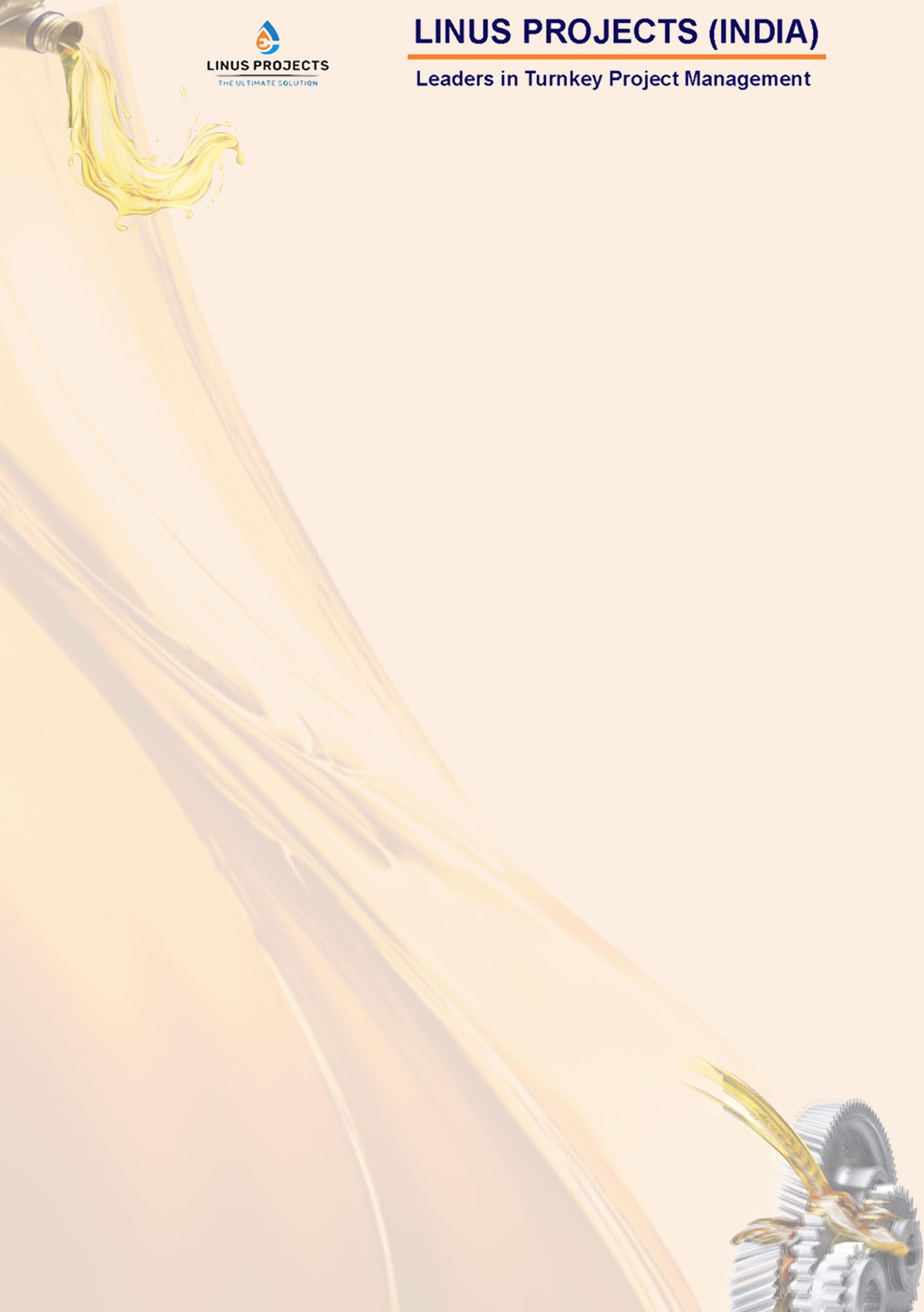
CARTON TAPING MACHINE:
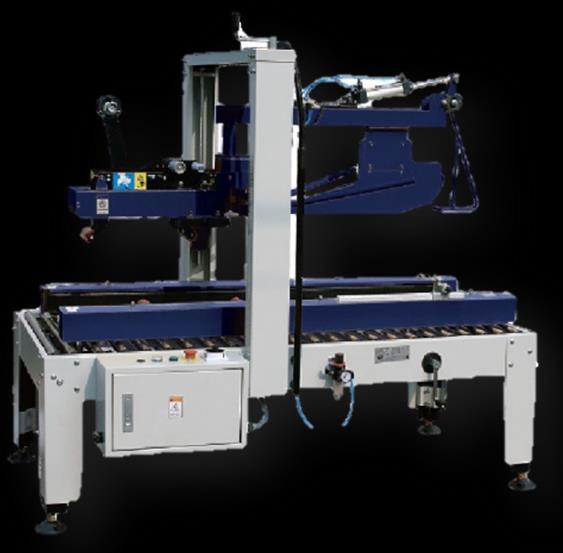
INDUCTION CAP SEALER:

IGBT based power and intelligent controls circuits for maximum efficiency. Built-in monitor circuit ensures safe working parameters (e.g. temperature, water, line voltage drops). In case of malfunction machine shuts off and fault is indicated on the front panel. Efficient sealing head design available in various types e.g. flat head, tunnel head, deep tunnel head, to suit different applications. Potential free contacts provided for alarm circuit in case sealing power drops below present value. Output rating: 2 KW Input Supply: 230V+/- 10% single phase 50Hz. A.C
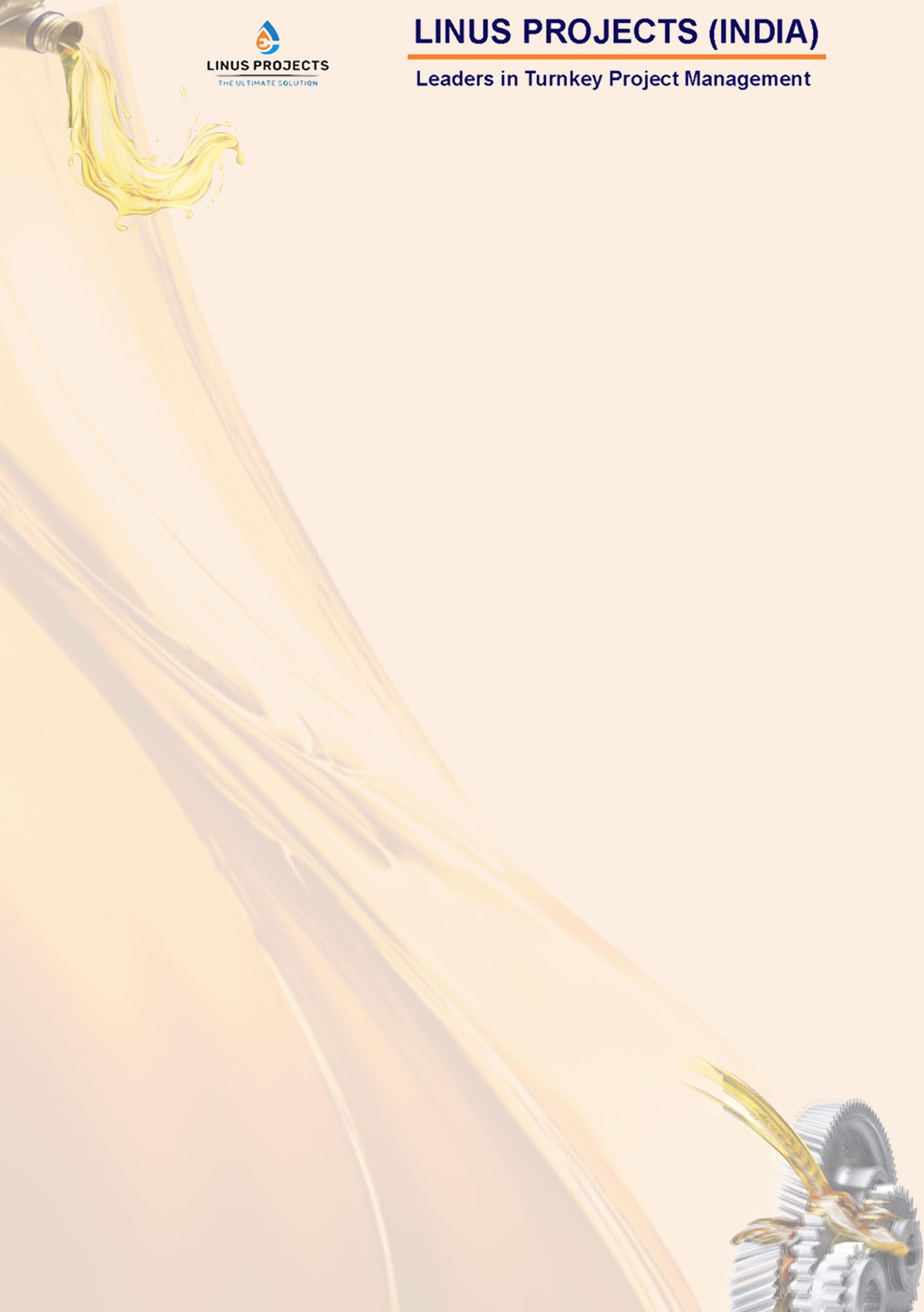
BARREL FILLING MACHINE:
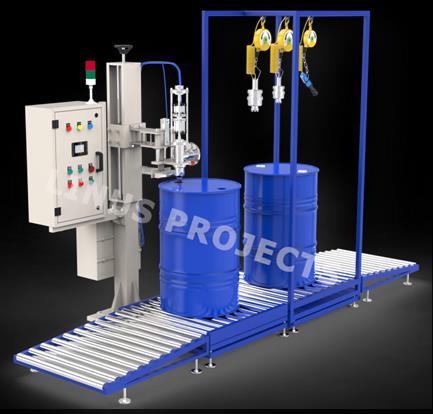
This automatic drum-by-drum filler capper is capable of filling up to 120 drums per hour. It fills drums from 25L to 220L capacity, and can handle plastic or metal bung caps and plastic or metal cap seals. Automatic drum filler is designed to accommodate a broad range of products and applications. One fully automatic drum filling machine is suitable for drums of varying materials and sizes, and can be housed in a cabinet or guard to control the ambient atmosphere. In addition, explosion-proof design makes this machine suitable for filling any liquid type, including petrochemical fuels, lubricants, agrochemicals, paints, coatings and food products.
Benefits of this automatic drum filling machine include:
• Explosion proof design.
• High-speed filling machines.
• The integrated automatic drum filling system allows for simultaneous execution of automatic operations on each station: debugging, filling, bunging, crimping.
• Fast format changeovers.
• Precise positioning of drums during transfers from station-to-station CIP cleaning system.
• Able to fill thousands of drums per day, this drum filling system offers the versatility and safety you need for even the harshest filling applications.
THERMIC BOILER FOR UTILITY PURPOSE:

A thermic boiler, also known as a thermal oil heater, is a specialized industrial heating system designed to efficiently and safely transfer heat to a thermal fluid or oil. This fluid is then circulated to provide indirect heating to various processes, equipment, or spaces within an industrial setting. The use of thermic boilers is widespread in industries where precise and controlled heating is crucial.
Boiler processes of high performance often require high temperature. Thermal oil heating using a special heat transfer fluid (HTF). It offers many advantages compared to other heat sources such as instance heating with low flue and good accuracy. Its time-saving process along with auto start-stop heating Capacity – 200000 kcal/hr. Fuels – LDO. Temperature range 300° C for standard unit Efficiency -Overall efficiency of 88 % (+/-2%) on NCV.
This unit consist of BOILER / EXPANSION TANK / FUEL TANK / CHIMNEY & ACCESSORIES / CENTRIFUGAL PUMP.
• High Efficiency Less Fuel consumption.
• Single Button Start / Stop with Automatic Control with Safety features.
• Noiseless operation with Monoblock Burner
• Quick Heating.
FEATURES:
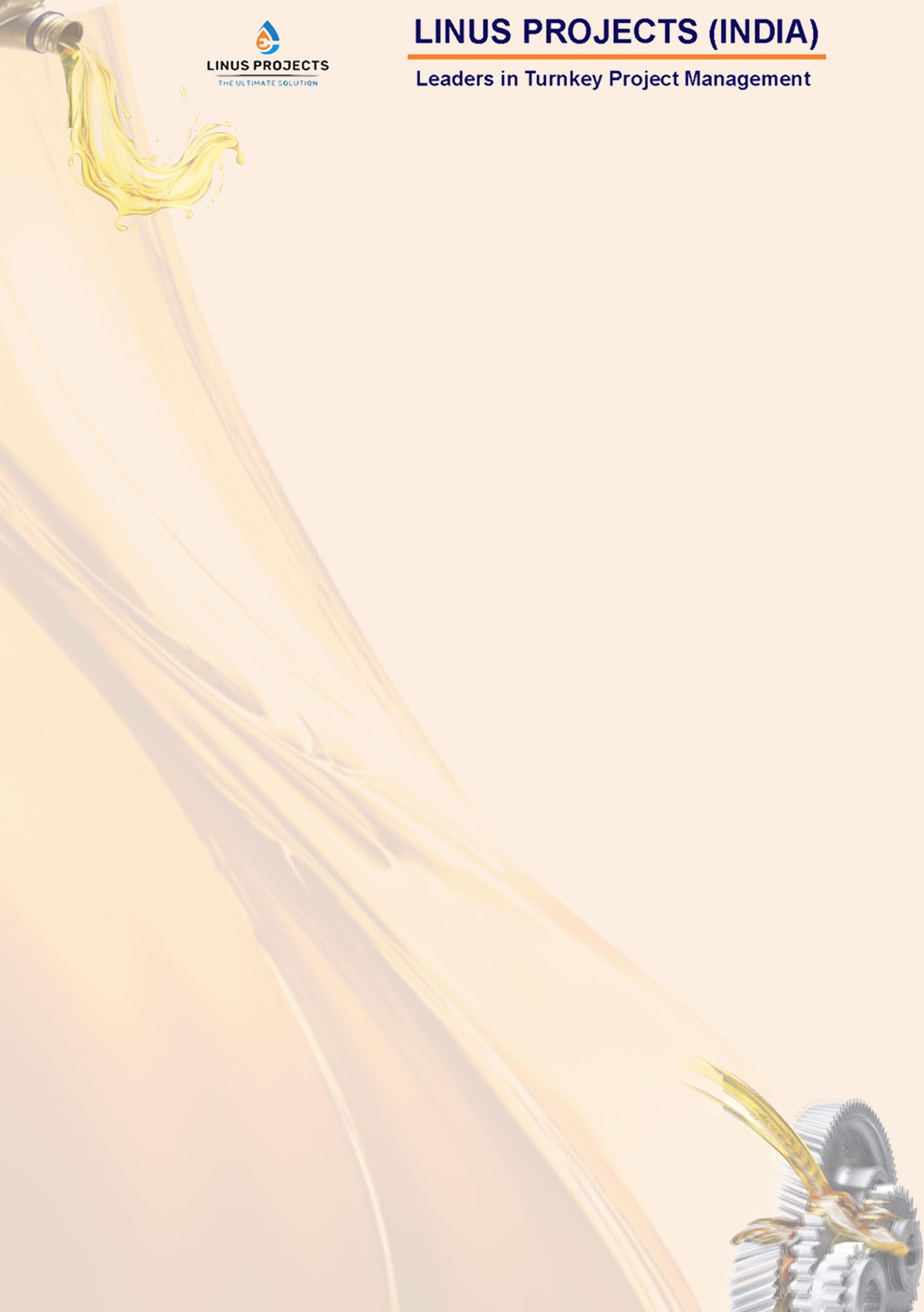
• At the heart of the thermic boiler's prowess lies its ability to facilitate efficient heat transfer. The thermal fluid, carefully selected for its heat-carrying properties, absorbs and transports heat with exceptional efficiency.
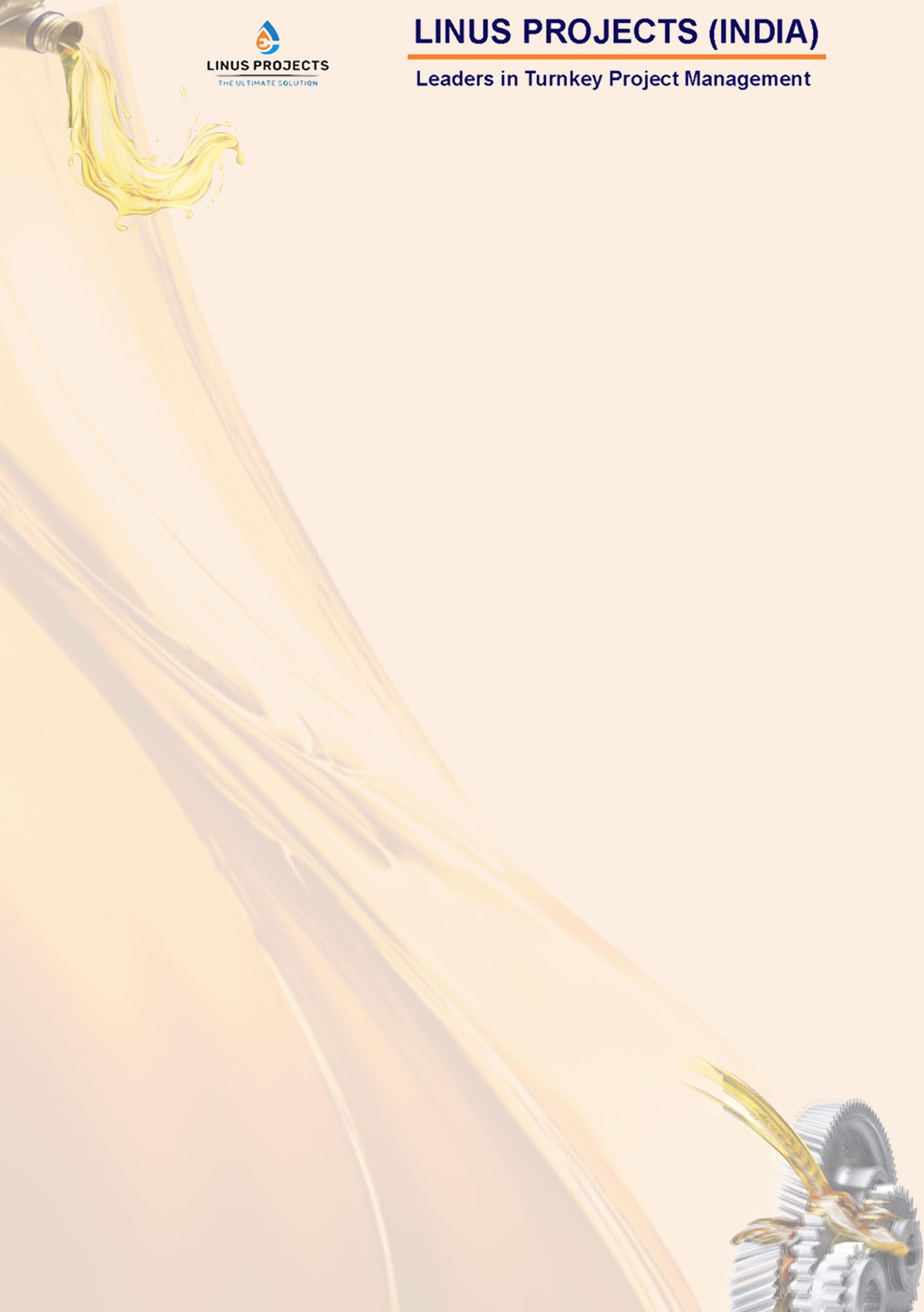
• Thermic boilers excel in delivering precise temperature control. Advanced control systems ensure that the thermal fluid maintains the desired temperature, meeting the exacting requirements of diverse industrial processes.
• The versatility of thermic boilers is a hallmark of their design. From chemical and petrochemical industries to food processing and manufacturing, these boilers find applications in a myriad of sectors where indirect heating is paramount.
• Operating within a closed-loop system, thermic boilers offer enhanced safety and reliability. The thermal fluid circulates without exposure to the atmosphere, minimizing the risk of oxidation and ensuring longevity.
• The compact design of thermic boilers allows for seamless integration into existing industrial setups. This adaptability is particularly advantageous for facilities with space constraints, making them a preferred choice for modern industries.
• Thermic boilers are recognized for their low maintenance requirements. The closed-loop system reduces the likelihood of contamination, contributing to extended operational intervals and minimizing downtime.
• Tailored for high-temperature applications, thermic boilers can operate efficiently at elevated temperatures. This makes them suitable for processes demanding stringent temperature controls.
PLC + MCC ELECTRICAL PANEL:
MCC PANEL: Panel is provided for operating all the electrical motors. The panel is duly pre-wired and enclosed in sheet steel powder coated enclosure. A MCC panel provided with remote push button Station to control the motor. All the motors are controlled through mccpanelIfanythingwronghappenwithmotors,panelwill Triptosavemotorfromdamage. Panel is provided with good brand of switches Like L&T etc.R-Y-B lamps withAmmeter and volt meter digital type is provided.An electrical control panel is provided for operating all the
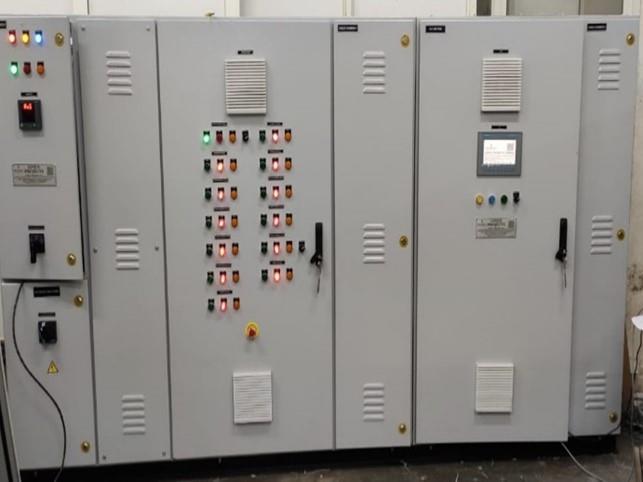
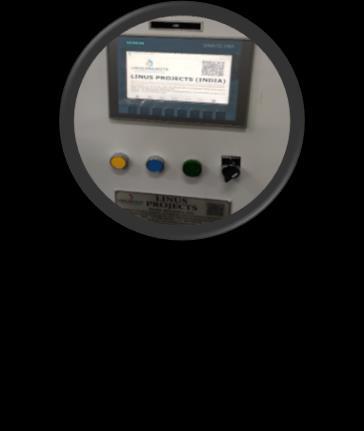
electrical motors. The panel is duly pre wired and enclosed in sheet steel powder coated enclosure.
PLC PANEL (SCADA): Acomplete PLC based HMI is provided for monitoring and controlling the flow of base oils to the Blenders. (Full plant to be controlled from SCADA COMPUTER)
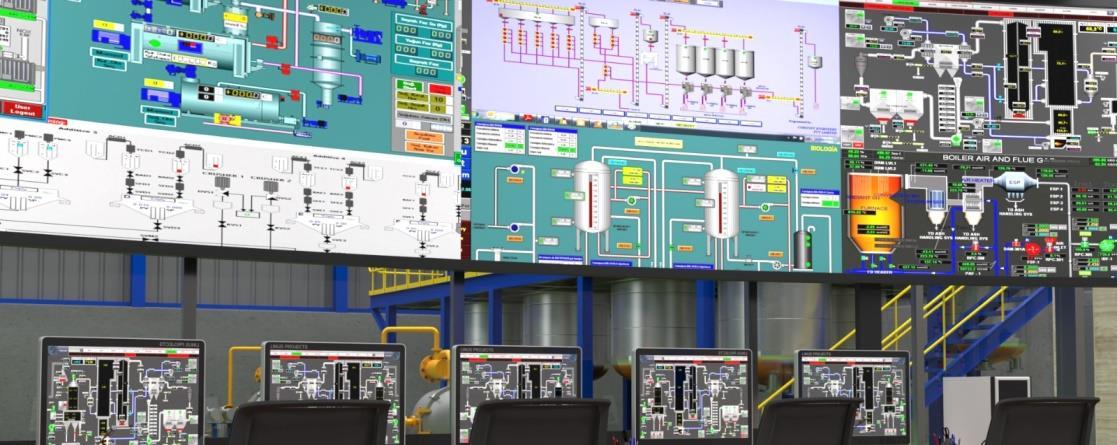
PALLET TRUCK 1T: Manual Pallet Trucks Which Are Supplied in Rounds, Flats N Plates Sections. Hand Pallet Trucks Manual & HydraulicAre Used to By Major Industrial Units Hand.
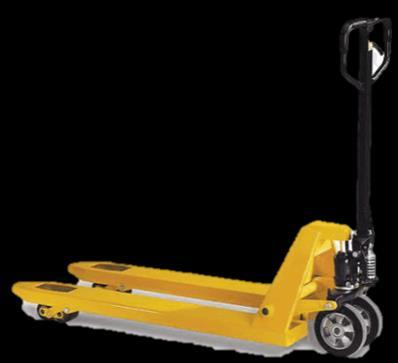
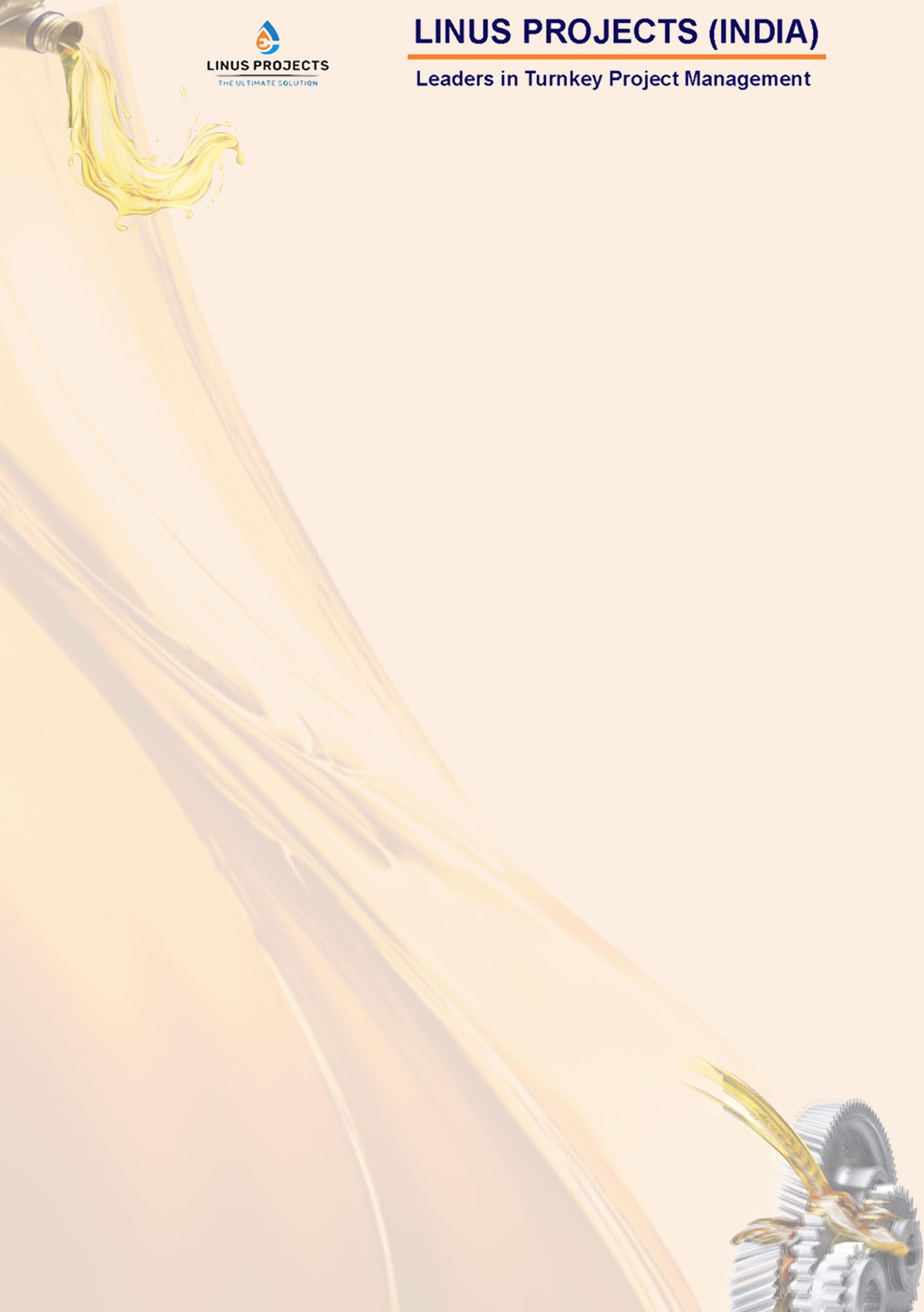
Pallet Trucks Manual & Electric Is Being Supplied to The Consumers.
DRUM TROLLEY:
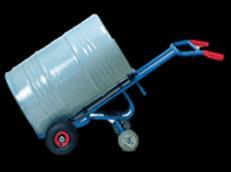
DRUM LIFTER & TILTER:

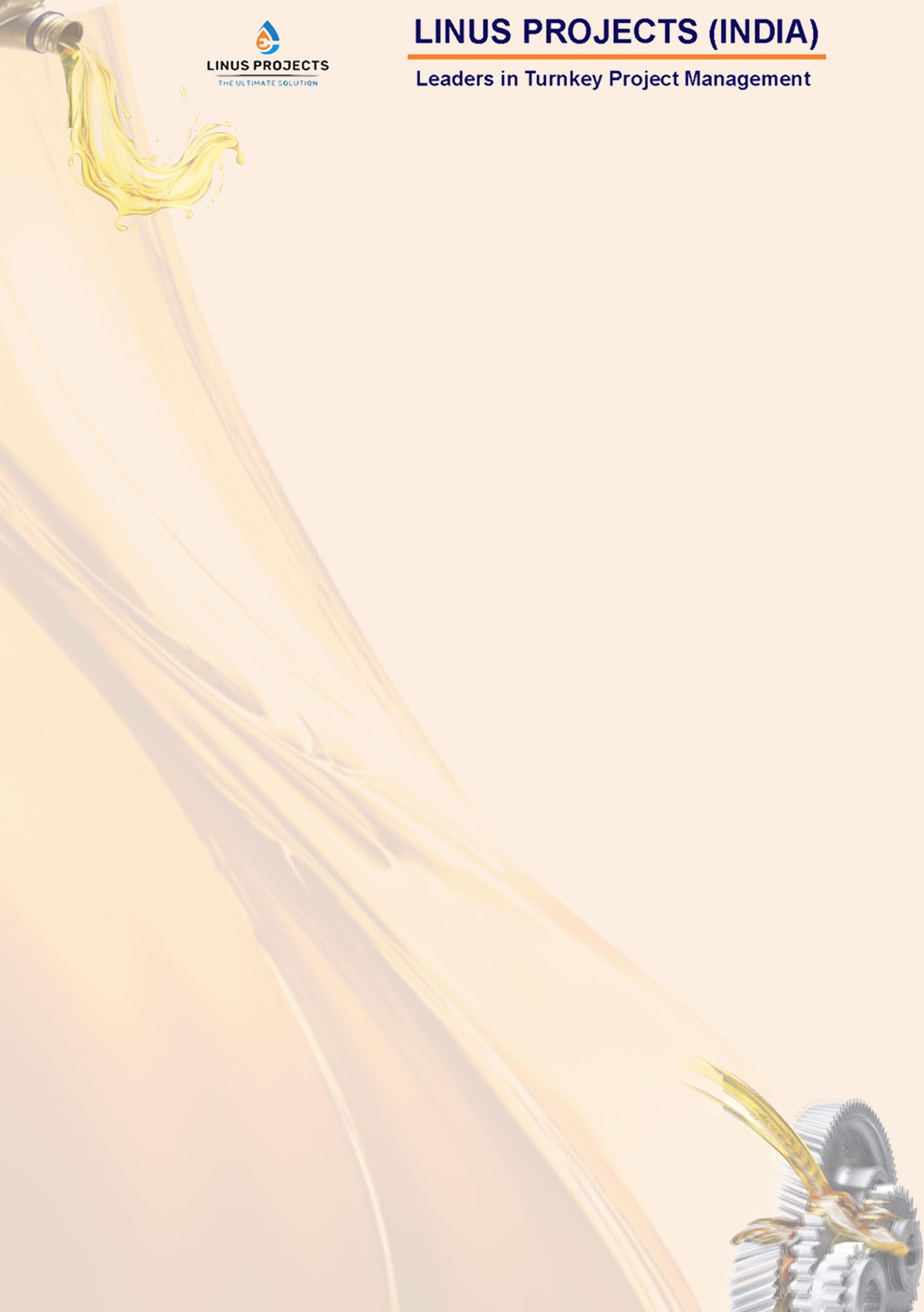
Drum holder: by means of fabricated belt & pipe with positive gripping. Structure: simplex single mast structure made from heavy-duty ‘c’ channel section. It would be supported by heavy-duty deep grooved guide rollers. Forks lifting would be by means of 2nos. Duplex chain & design pulley. Handle: designed for best maneuverability & made of m. S. Pipe. Wheel: 8” x 2” nylon swivel castor wheel with 6204zz double ball bearing Paint: auto-finish paint.
Drum lifter & tilter are very useful in loading / unloading & emptying drum in industries like engineering, lubricant to get proper amount in blender.
It is essential equipment’s were drum handle regularly. It having carriage assembly, Hydraulic system & Hydraulic cylinder.
CLIENT SCOPE
LABORATORY EQUIPMENT:

A) VISCOSITY BATH SUITABLE TO 100 °C & 40°C
B) FLASHPOINT APPARATUS COC
C) POUR POINT 1 CHAMBER AT 51 C
D) HYDROMETER M-50 2 NOS
E) THERMOMETER-IP 51
F) TBN TITRATION APPARATUS
G)MUFFLE FURNACE
H) LAB ANALYTIC SCALE
I) LAB CHEMICALS FOR TBN
GLASS APPARATUS FOR LABORATORY
AIR COMPRESSOR -10 HP:
Model: SSP-hp10
Capacity: 100 CFM
Rated Operating Pressure: 140psiG
Max Discharge Pressure: 143psiG
Max Modulated Pressure: 150pisG
Nominal Drive Motor: 10HP
Total Package Amps: 106
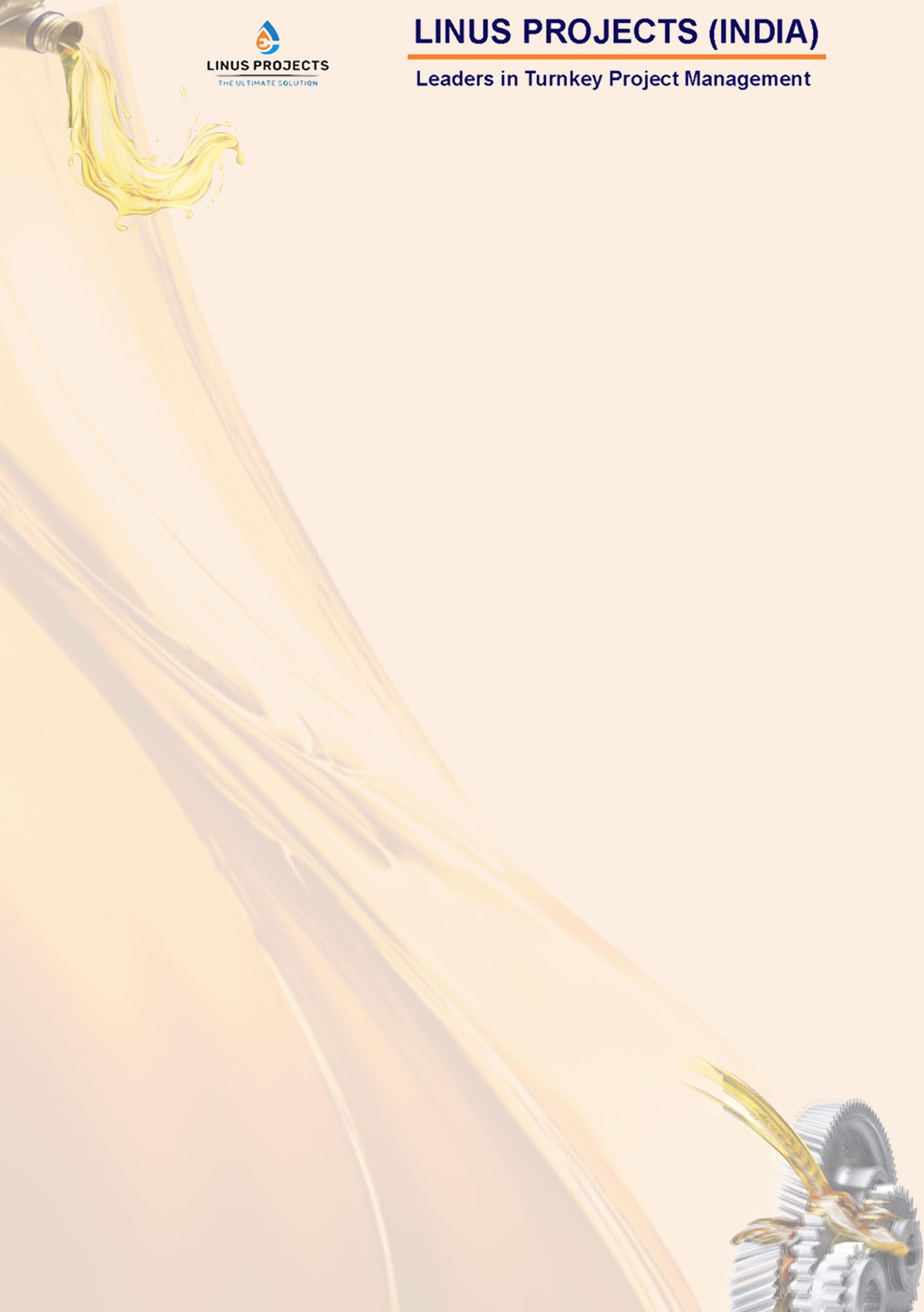
FINISHED PRODUCT TANK:


LUBE OIL storage tank is used for storage of Lube oil after manufacturing inside the blender.

10000 Ltrs x 3NOS.
We will provide you design of storage tank at 5000$. then you will fabricate storage tank at your site.
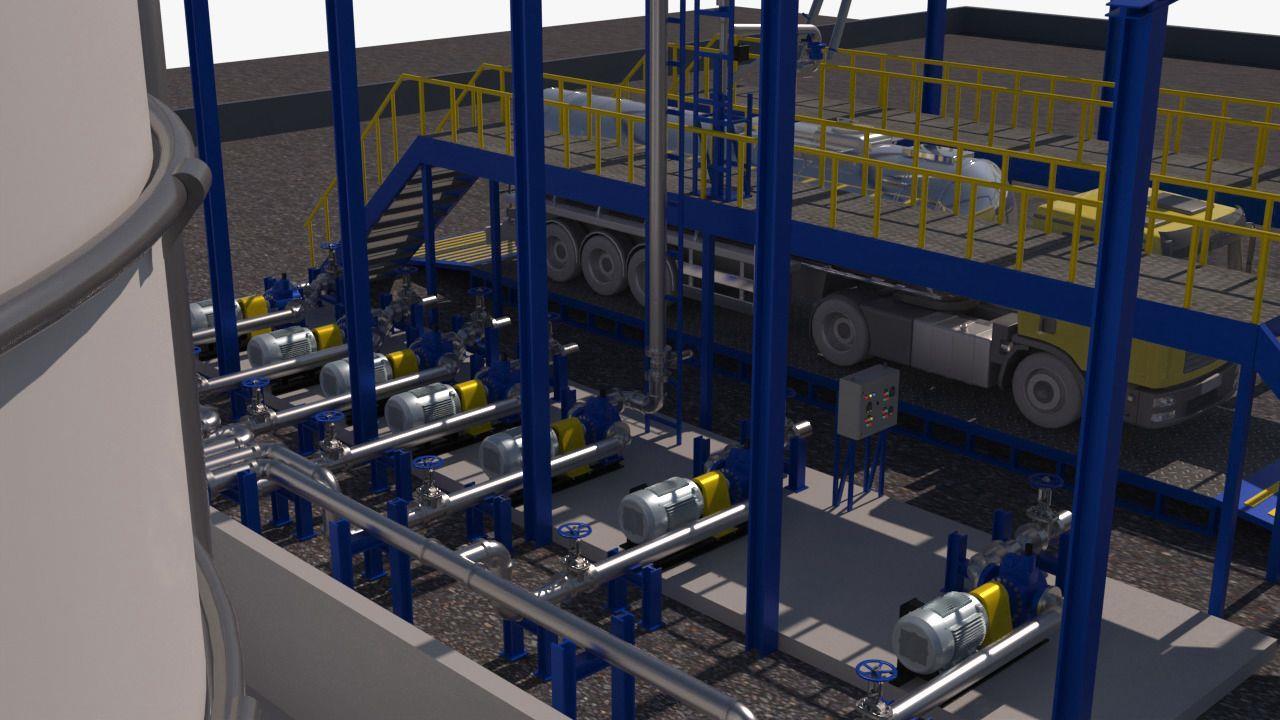

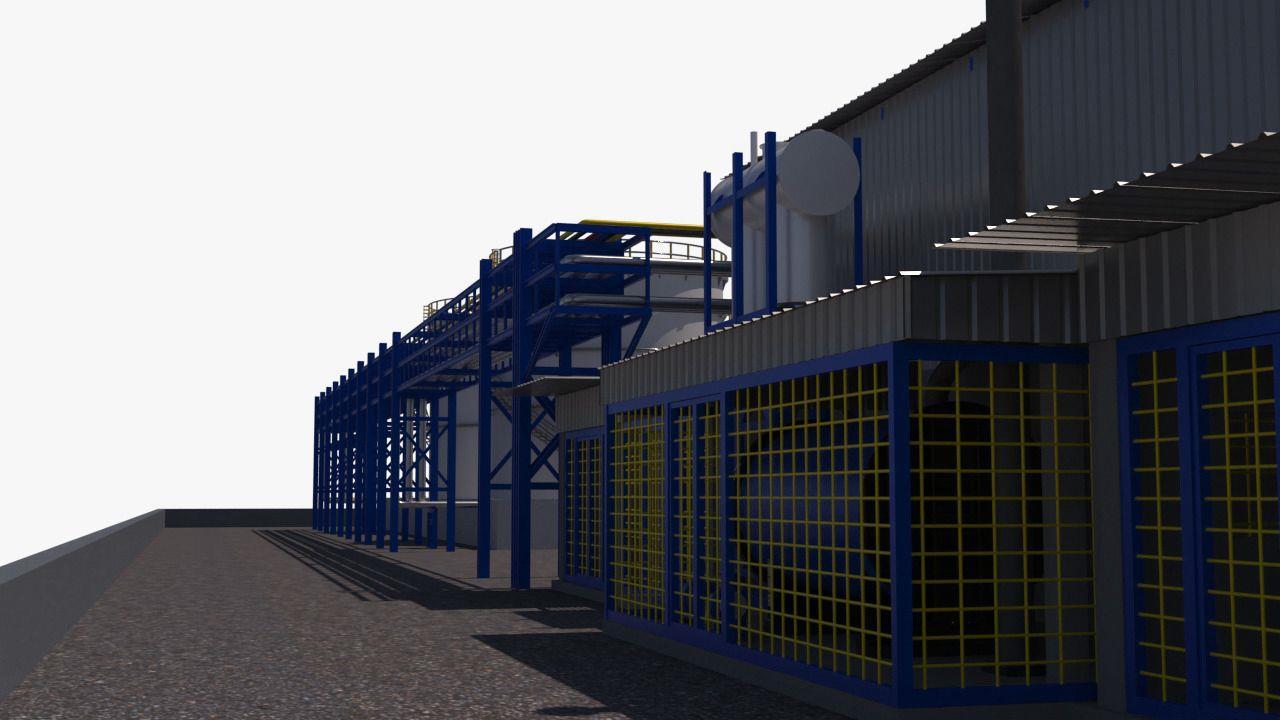
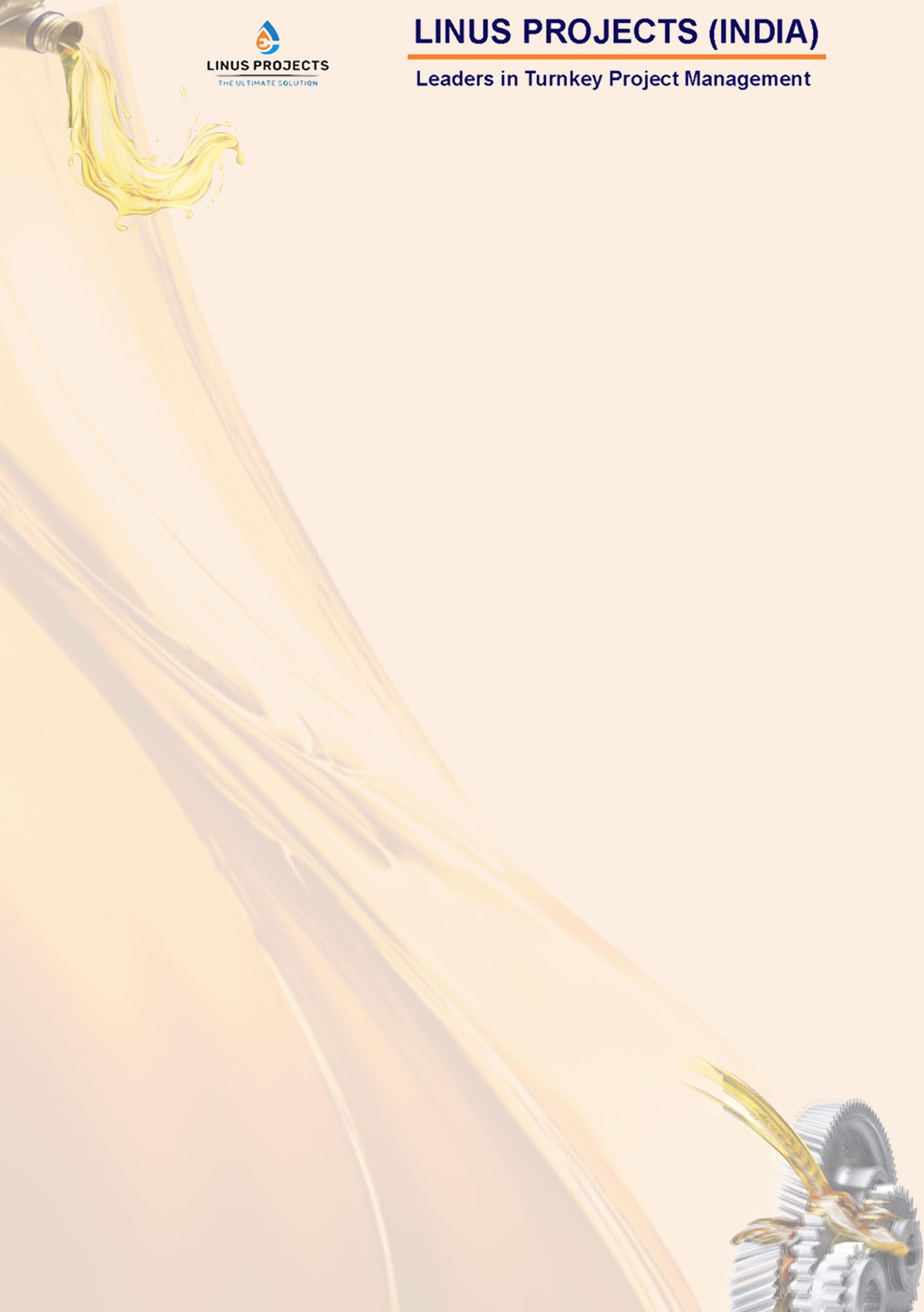
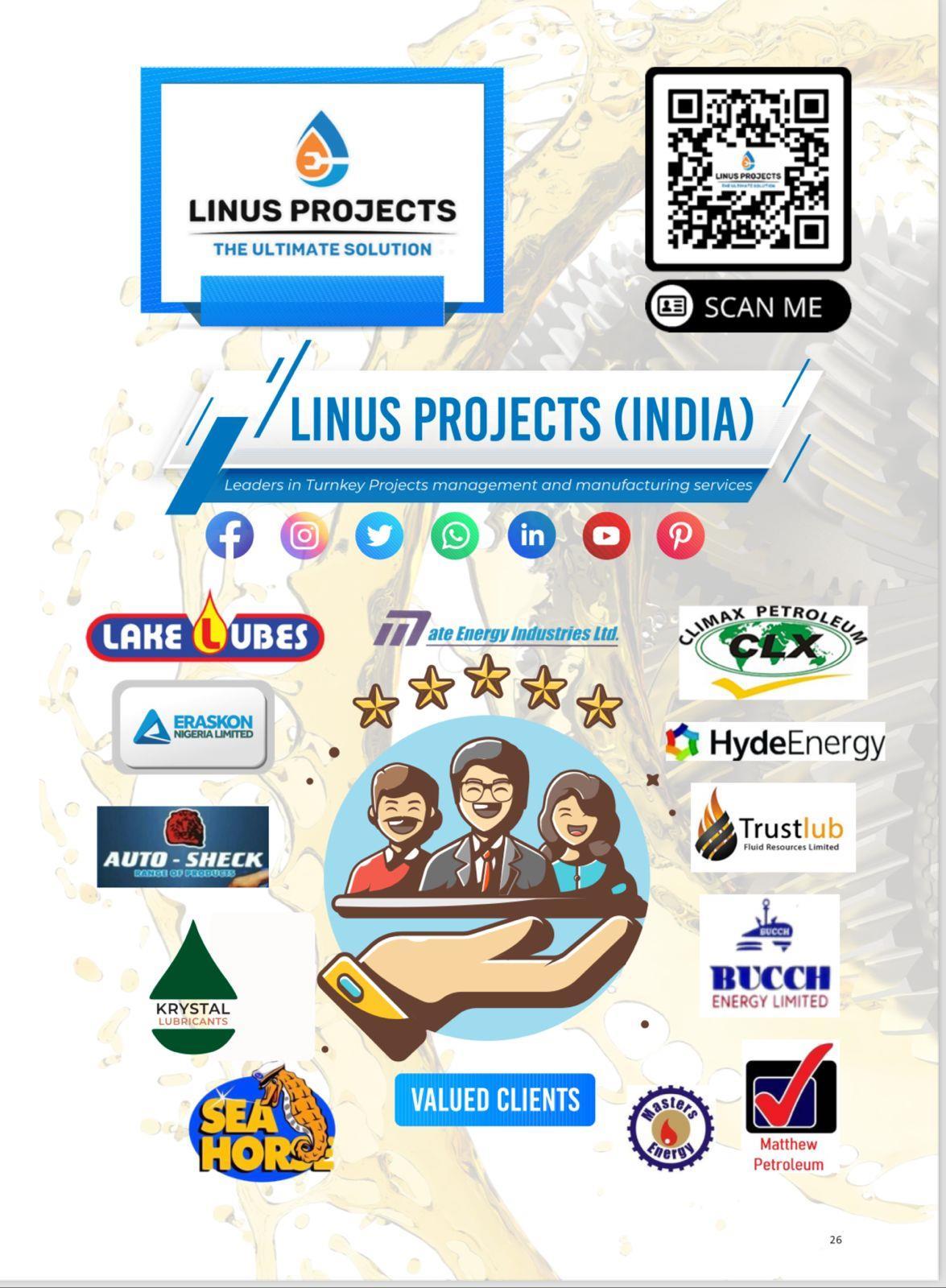
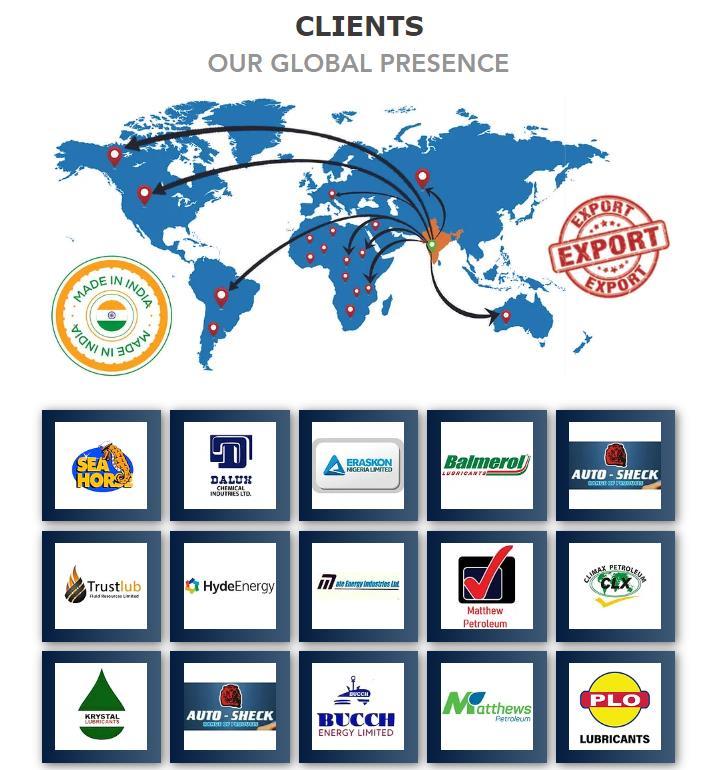
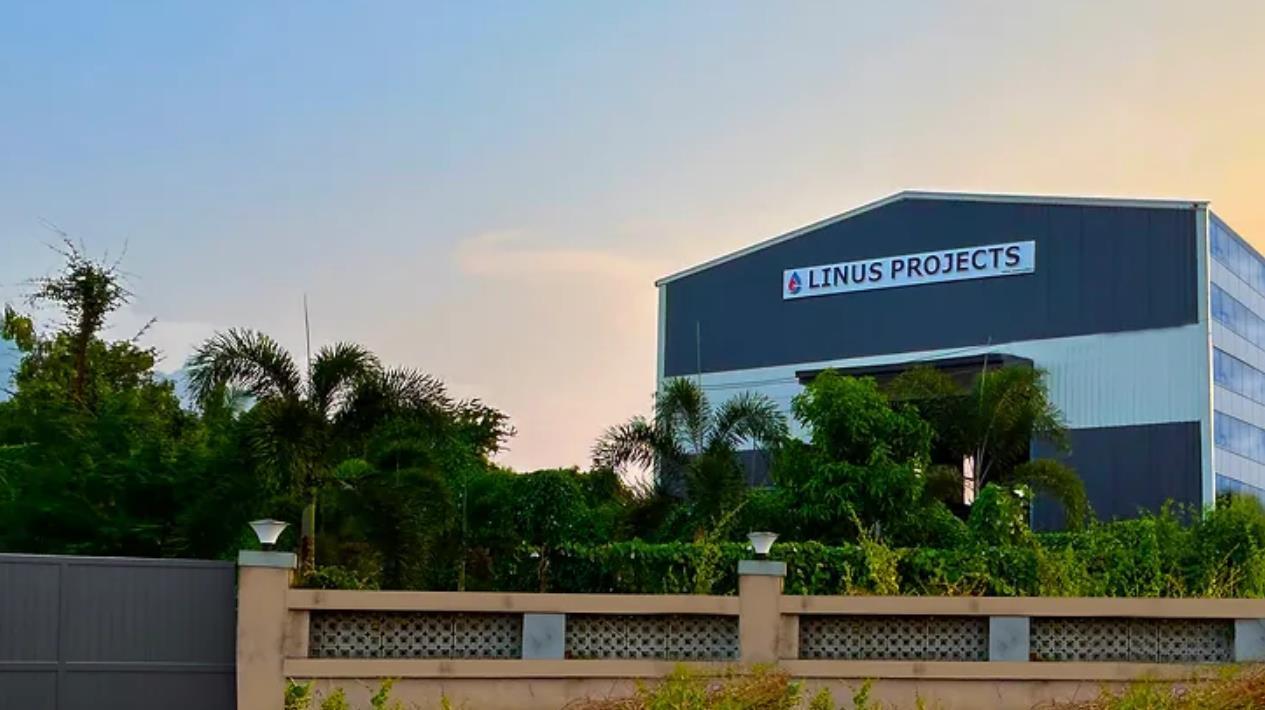

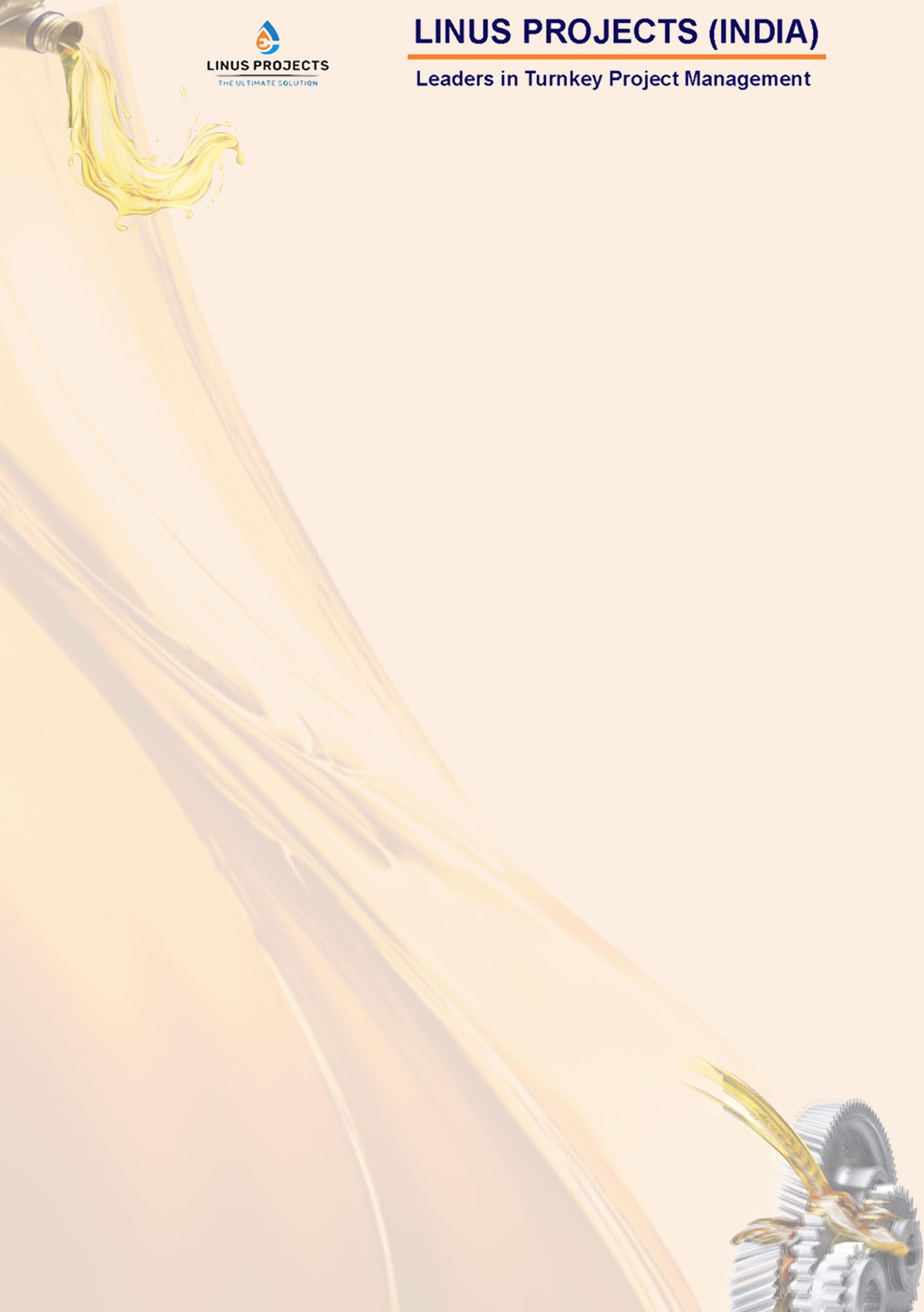

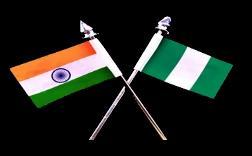


