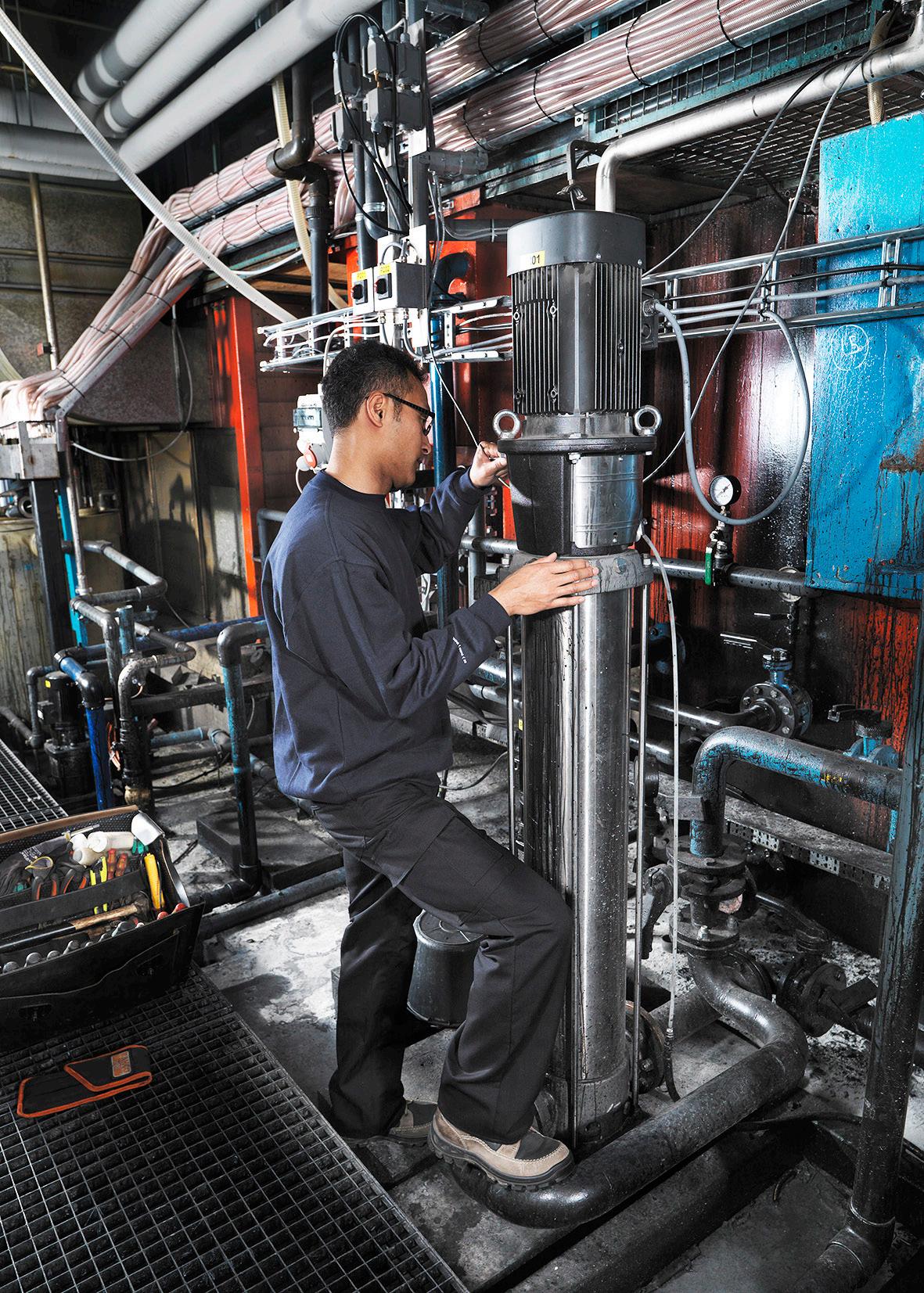
2 minute read
Energy efficient water pumps save costs and planet
Energy costs continue to rise and the pressure is on for the private sector to create a more sustainable, low-carbon economy; what better time for companies to optimise energy usage on their water pumps?
“Original equipment manufacturers like Grundfos have been working hard for many years to make our pumps more energy efficient,” says Nicolette Gomes, senior service sales specialist at Grundfos. “I am still surprised that few pump users take advantage of the opportunity to improve their bottom line by cutting energy costs – at the same time reducing their carbon footprint.” Doing this requires firstly a clear picture of a company’s current energy costs, says Gomes, so Grundfos offers an ‘Energy Check’ service to help establish the foundation for a considered solution. This involves a service engineer visiting the site and collecting data from pumps and motors, as well as basic energy consumption indicators. “From this data, we produce an analytical report that shows where improvements can be made,” she says. “Knowing exactly what our energy-efficient Grundfos systems can achieve, we can compare these expectations to the current situation; in our experience, the savings can be up to 30%.” The information contained in these reports also includes the new system’s lifecycle costs and its return on investment (ROI). She highlights that some customers’ energy savings have paid off the new equipment in less than two years, after which the system provides ongoing and substantial savings in operational costs. “A useful rule of thumb is to look at the age of the pumps in your existing arrangement – and if they are older than six or seven years, then an upgrade invariably makes perfect financial sense,” she says. “Where the capital outlay can be recouped in three years or less, it is usually an easy decision to make.” Where data is more difficult to gather – for instance, where nameplates have been removed or are not legible – Grundfos can also conduct a more intensive Pump Audit. Using a range of equipment from a specialised audit kit, the service engineer will install flow meters and pressure transducers, and measure kilowatt ratings of pumps. “This will log data for five to seven days, to create a detailed load profile for the customer,” she said. “An added benefit is that the cost of this audit is deducted should they decide to go ahead with our Grundfos solution.” This intervention is of particular interest to the head of engineering in a plant or facilities manager in a building, whose key performance indicators (KPIs) are often linked to the cost-effectiveness of their operations – as well as the carbon emissions generated. “With services like our Energy Check and our Energy Audit, we can help key personnel to achieve their KPIs in relation to energy consumption,” she concludes.
Advertisement
