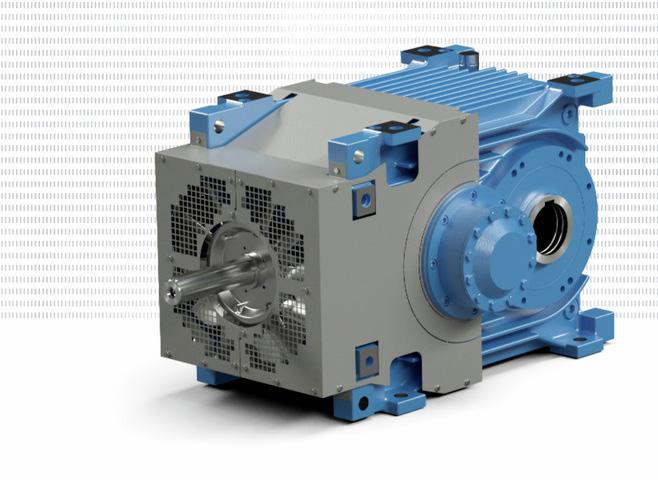
2 minute read
Corner Stone
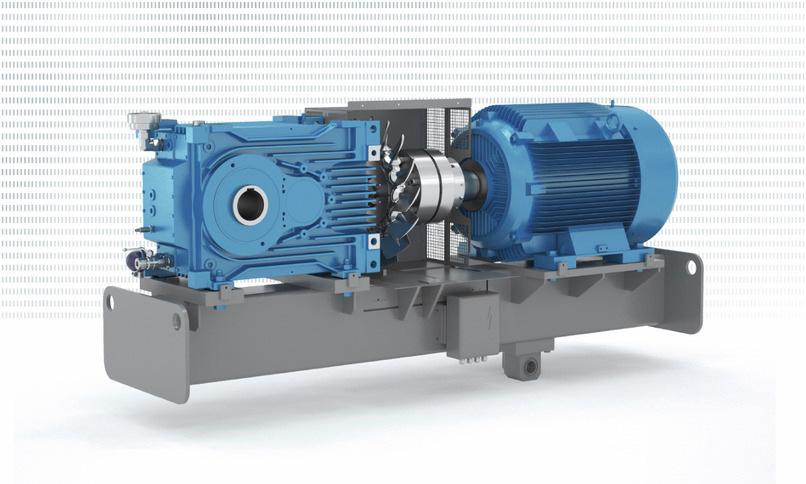
flammable dust in bucket conveyor applications. BMG’s NORD predictive maintenance solutions offer fast, efficient and comprehensive evaluation of analogue and digital data, to enhance the operational efficiency and safety of machines. The intelligent PLC in NORD drive technology forms the basis for condition monitoring and predictive maintenance. BMG specialists use predictive maintenance as a methodical continuation of condition maintenance, with the prime objective of proactively maintaining machinery and equipment and detecting operational changes. NORD status-oriented maintenance system replaces traditional time-based maintenance to enhance the performance of the gear unit, electric motor and frequency inverter, for increased efficiency of the entire plant, as well as reduced downtime. Digitalisation in drive technology boosts the added value our customers derive from drive data. This is especially so in drive systems in demanding production environments, where industrial gear unit installations are usually used in critical applications and their failure could cause severe damage. For example, in mining, wastewater, intralogistics and the food industry, as well as in general heavy-duty applications. An important advantage of this system is it offers dependable data analysis, rather than merely data reading. Results of pre-processing or complete data can be optionally transmitted to an edge device, from which the data of all subsystems is managed and evaluated. This information is then available as pre-selected and edited smart data for further use and clear visualisation. NORD modular drives – designed for reliability, energy-efficiency, low noise levels, extended service life and reduced maintenance - are used in applications where frequently changing speeds are essential and where a specificallydefined sequence of movement is required. These systems are easy to expand or upgrade, using a minimum of different types and sizes of components. Included in BMG’s NORD range are drives suitable for torques from 10 Nm to over 250 kNm, electric motors in the power range from 0,12 kW to 1 000 kW and frequency inverters with the required power electronics up to 160 kW. Inverter solutions are available for conventional control cabinet installations, as well as for decentralised, fully-integrated drive units. NORD’s decentralised technology, which integrates mechanical drive components and electronics components into compact units, provides highly efficient and reliable customised drive solutions that reduce operative and service costs. Decentralised drive technology - an alternative to control cabinet installations - incorporates frequency inverters that are installed close to the motor or mounted directly on the geared motor, to enhance productivity in many applications, including conveyor technology and intralogistics. This stand will be manned by a team of technical experts.
Advertisement
BMG, +27 (0) 21 493 3250, deonc@bmgworld.net, www.bmgworld.net
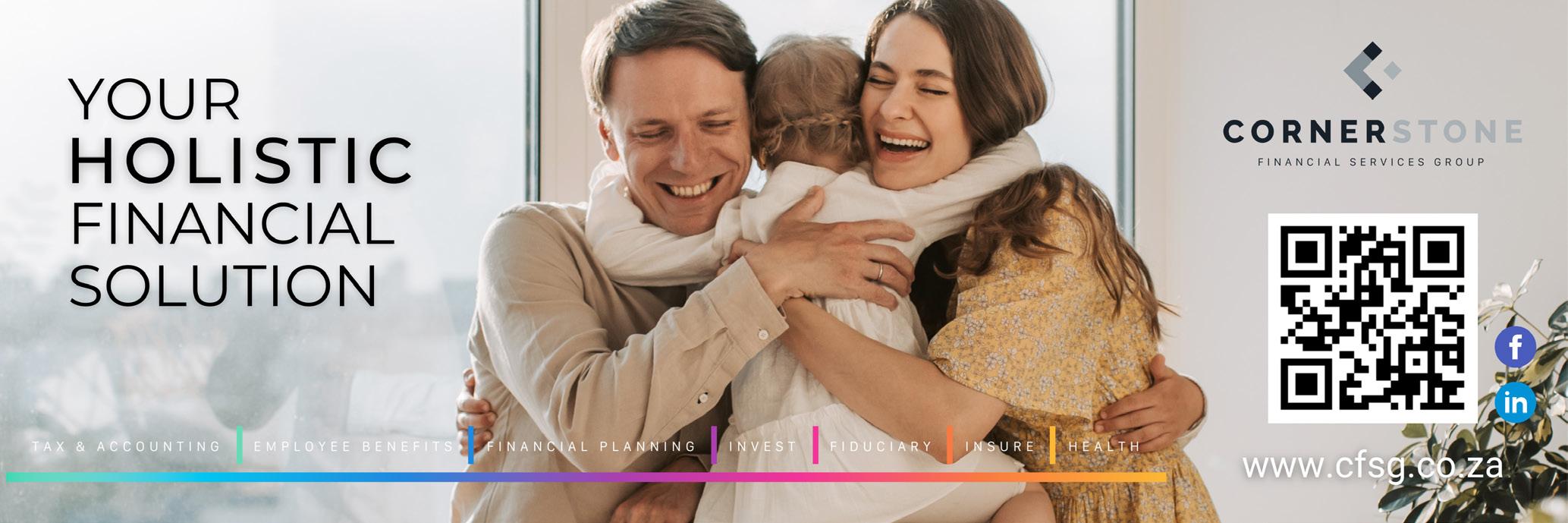