VACUUM PUMPS AND BLOWERS
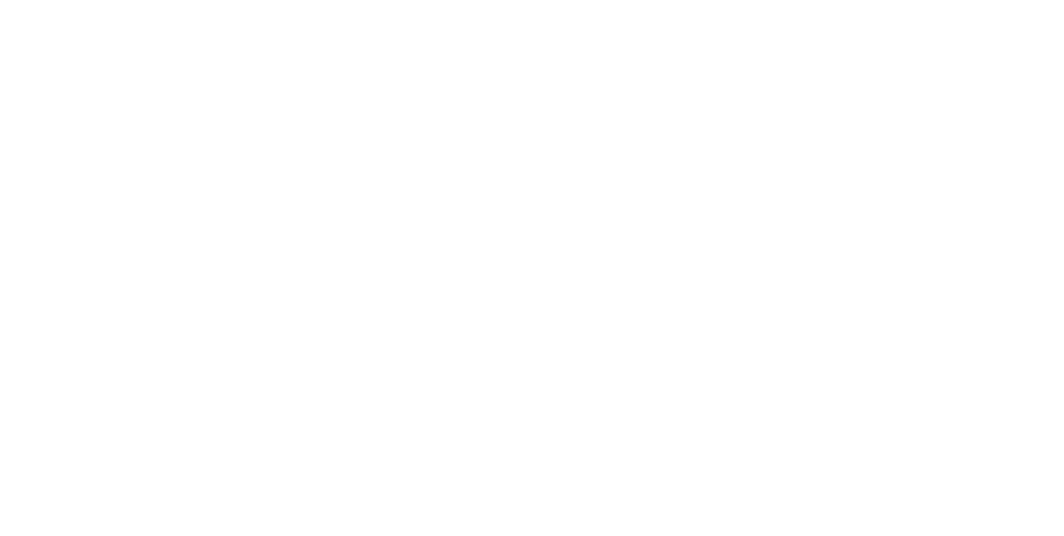
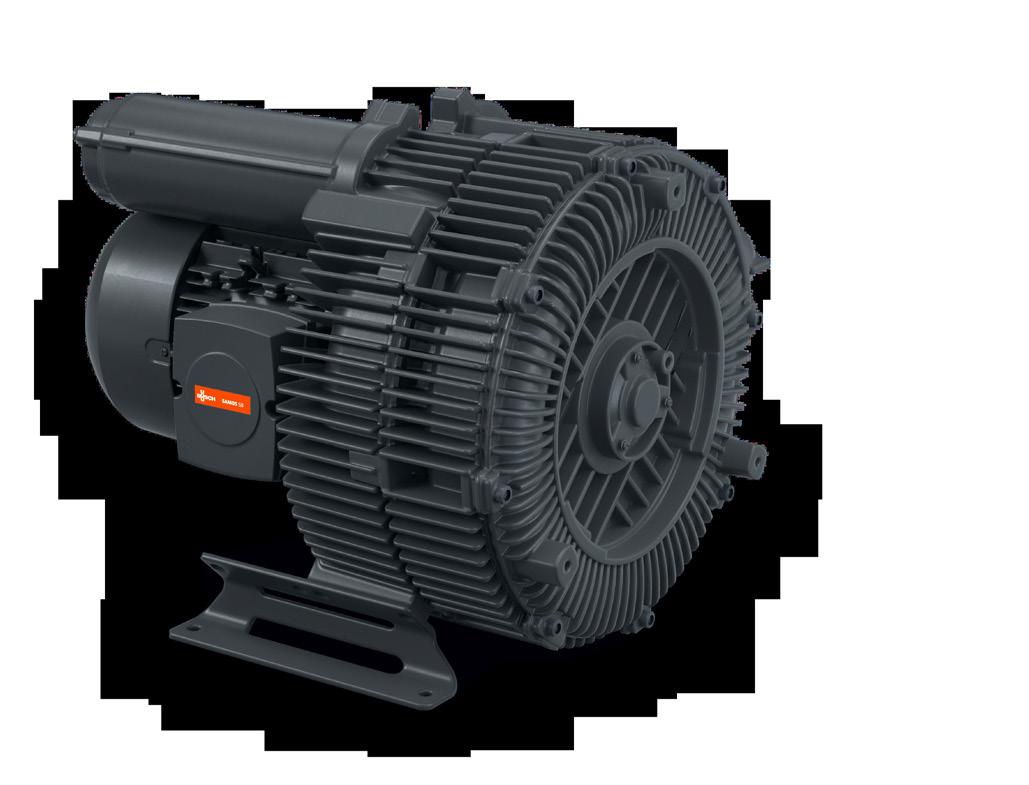

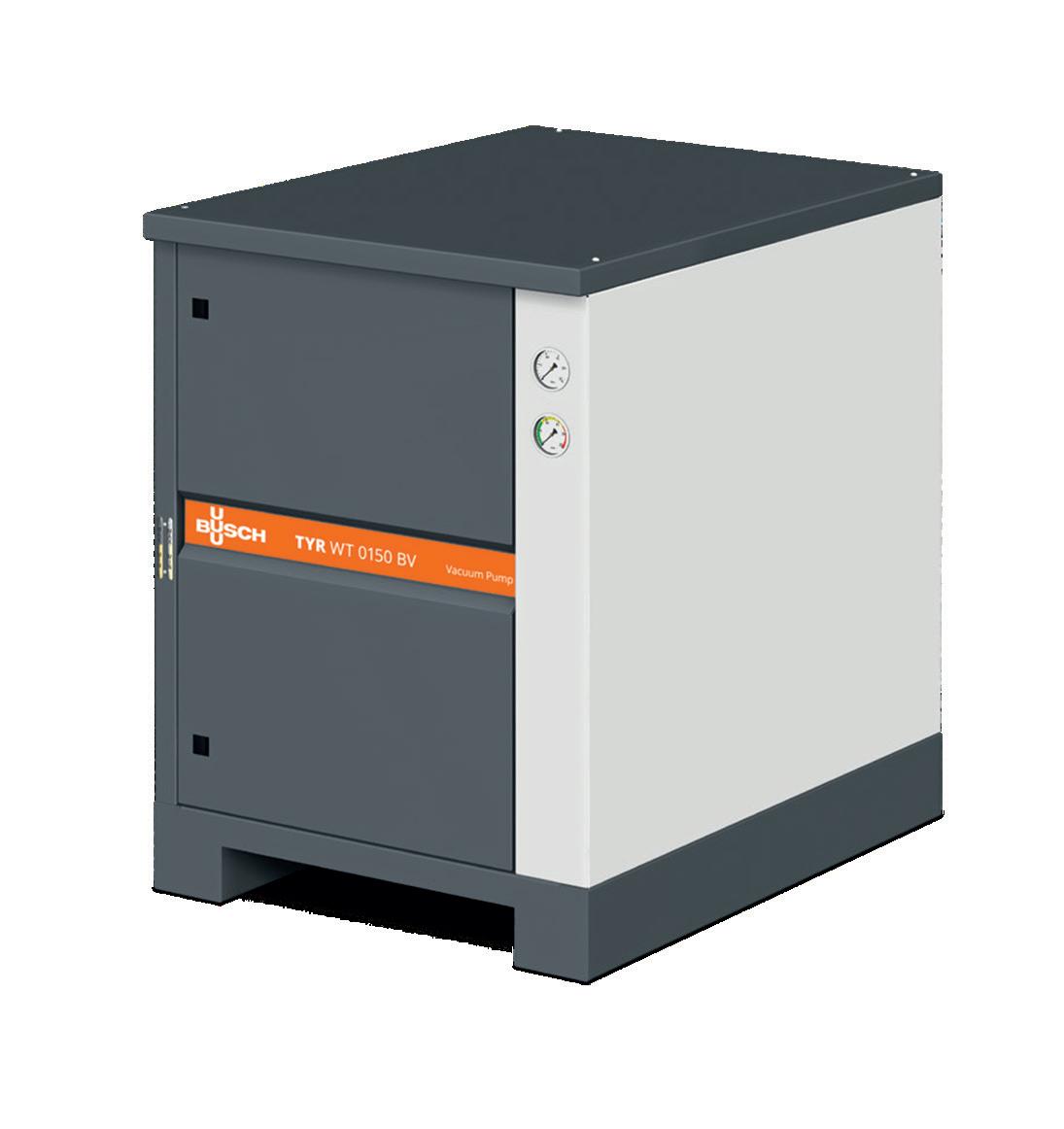
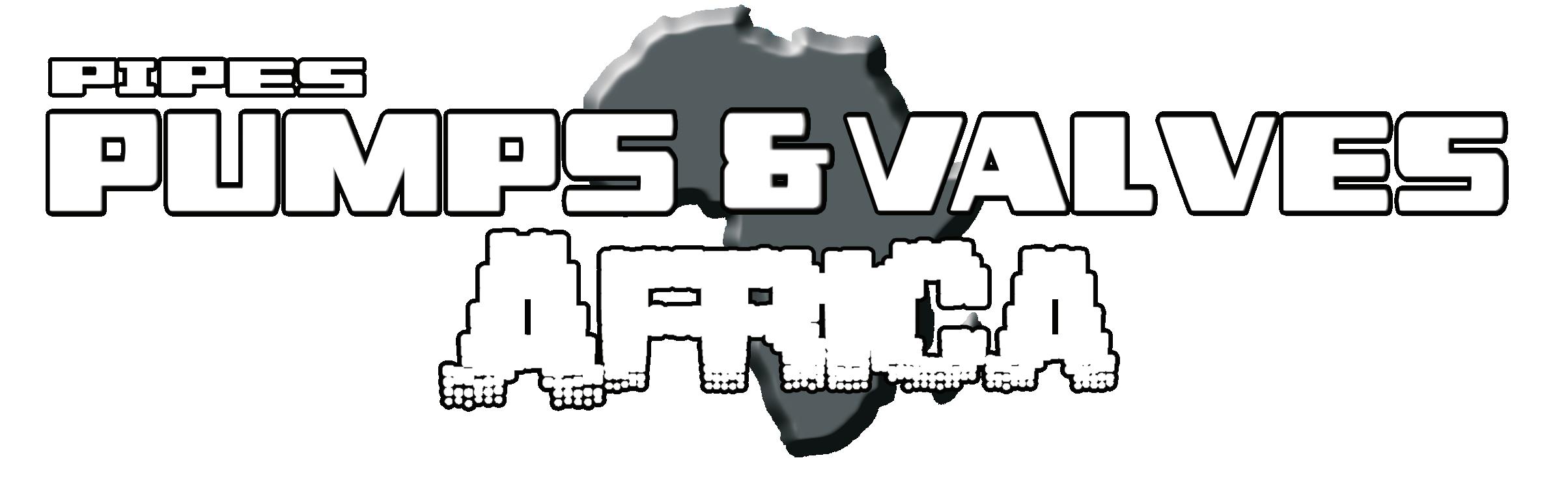
Load shedding adds last straws to looming SA water crisis; but there is hope
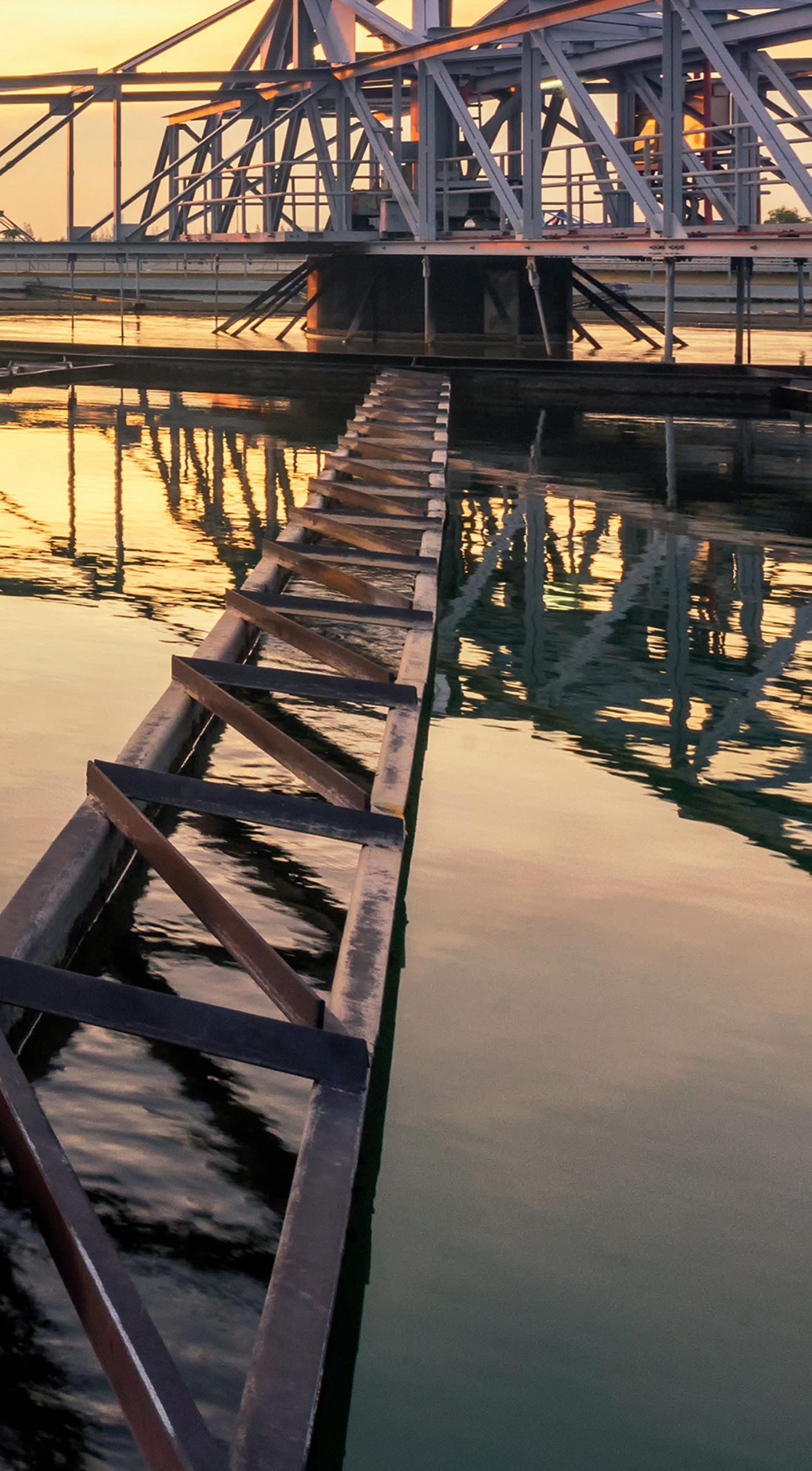
Load shedding adds last straws to looming SA water crisis; but there is hope
Bilfinger Intervalve Africa (Pty) Ltd. is one of the enterprises in Bilfinger Power Africa (Pty) Ltd., the South African subsidiary of German based Bilfinger SE. For years, we have been adding value to the power, mining, paper pulping and broader industry through comprehensive valve supply, valve maintenance and heat treatment solutions. www.intervalve.bilfinger.com
Busch Vacuum Solutions, +27 (0) 11856 0650, info@busch.co.za, www.buschvacuum.com
Pipes, Pumps & Valves Africa
Managing Editor: Surita Marx
Tel: +27 (0) 87 700 9834
Cell: +27 (0) 83 281 5761
Email: info@pumpsandvalves.co.za
Web: www.pumpsandvalves.co.za
Editor: Llewellyn Pronk
Sales: Peter Rametsi
Email: sales@pumpsandvalves.co.za
Production Manager: Xane Roestroff
Busch, a leading provider of vacuum and blower pump solutions, significantly reduces water usage and energy consumption while expanding its footprint in the water and wastewater industry. The company's commitment to cost-saving alternative technologies has garnered attention from customers seeking sustainable solutions. Pipes, Pumps & Valves Africa finds out more.
At Busch, customer centricity is a core value, with ongoing investments to ensure proximity to its customers. Managing director Sean Pieterse highlights that this has been a driving force in the company's expansion strategy. "As a business, we have always been committed to putting the infrastructure and the people on the ground as close as possible to our customers." He says this has always allowed the business to understand local market conditions more intricately and adapt and respond quickly to market needs. With a focus on various industries, the company has specifically been targeting the water and wastewater, medical and food industries as part of its latest growth strategy.
Currently, in the process of building a new 2700 square meter head office in Johannesburg that will house a range of capabilities, Africa remains a top priority for Busch. "Our goal is to be the best backup service provider in the continent's vacuum and blower pump market," he says. The company also has a footprint in Cape Town and Durban with offices and service centres in these cities.
“We are firmly established in South Africa,” says Pieterse. “All offices have workshop service and repair facilities and carry stock of vacuum and overpressure generators to support any industry.” With the aim of becoming the go-to supplier not only in South Africa, but across the continent, has required ongoing investment and expansion, keeping up with market trends and ensuring customers' needs are met consistently and efficiently – something the Busch team prides itself on.
Technical director Reeza Hoosen highlights the company's focus on water and energy savings, mainly through large-scale projects. "We have implemented several initiatives aimed at reducing costs for our customers. By leveraging alternative technologies, we have significantly saved water and energy consumption," says Hoosen. "Moving to
Busch South Africa is a no-brainer for our customers due to the substantial savings we can offer." Says Pieterse, “Our product are designed with a focus on customer piece of mind, offering increased production efficiencies, reduced maintenance costs, and lower energy and water consumption. Compared to many of the older installed vacuum technologies, Busch delivers up to 60% reduction in the total cost of ownership.”
The water and wastewater industry in South Africa has faced several challenges recently, with treatment plants under pressure and often needing to catch up in terms of expansion and delivering drinkable water. However, the private sector's effluent plants and the mining industry have grown robust in water and wastewater. Busch South Africa has been actively engaging with contractors in this market, supplying products and offering integrated solutions to meet the increasing water and wastewater treatment demand. Hoosen notes that the water and wastewater industry will witness a greater need for treatment facilities as the African population grows. "Water and wastewater management is closely tied to population growth, and as Africa's population expands, the demand for effective wastewater treatment will rise. Africa is experiencing significant investment in this sector, with countries like Egypt and West African nations like Nigeria, Ghana, and Ivory Coast witnessing infrastructure growth and numerous projects on the grow."
To cater to the growing demand, Busch has extensively expanded its footprint on the continent over the past few years. The company already has offices in Ghana and Kenya, and by the end of the year, it plans to open a new office in Egypt. The construction of its new head office in Johannesburg is also expected to be completed within the next few months. This facility will be fitted with stateof-the-art equipment and testing facilities. "Having a physical presence in each region is critical for Busch. We are primarily an aftersales driven company, and being close to our customers allows us to provide prompt support
and services," explains Hoosen.
According to Hoosen, in the current global economic environment, there is an increased move to extend the life of products as long as possible. "Clients are far more aligned to repairing equipment until it is no longer possible rather than immediately buying new or replacing it with a refurbished model. With companies under pressure and the ability to replace no longer favoured, it has become critical to address customers' needs quickly."
He says stock and the technical expertise to address product failure need to be on hand far more quickly than ever to reduce downtime and decrease costs.
In addition to maintaining a robust stock profile across Africa, Busch prides itself on the fully-fledged service warehouses in all its branches and its ability to be on the ground no matter where the client might need them on the continent. This enables the company to provide repair services and on-site support, ensuring the extended life of its products. "We offer high-quality products and exceptional after-sales support, ensuring our client's needs are always met," says Pieterse.
He emphasises the company's differentiation as an Original Equipment Manufacturer (OEM) and customer proximity. "Unlike other OEMs whose distribution partners cover the market, Busch is close to the customer. We invest in infrastructure and skilled personnel to effectively cater to the market's needs. Our ability to quickly service customers, maintain substantial stock levels, and provide technical expertise sets us apart." Busch aims to grow its footprint and profile as the partner of choice in the vacuum and blower pump market by focusing on excellent backup services. With plans for increased stock levels, a new factory, and comprehensive servicing capabilities, the company is well on its way to offering its customers a one-stop solution from design and production to commissioning and aftersales service.
Why not look for inspiration to meet water challenges in unexpected places? Inspired by big waves and high pressure pumping in industry, we followed Joana Andrade, one of the world’s best professional big wave riders in her search for challenges beyond the expected.
Joana dares to challenge the big waves at Nazare, Portugal, which peak at 25 to 30 meters.
Our largest CR pump handles pressure up to 40 bar, pushing water to a height of about 400 meters. High pressure pumping meets the challenges of industrial water treatment and processes. Inspired by Joana’s passion for challenging big waves, we will continue to move the limits beyond the expected. Find out more about how the extra-large CR pumps meet water challenges and watch the video to recognize the courage needed to ride big waves.
The CR 255 pump completes the CR range and continues to push the boundaries
The impressive new CR 255 is now available, completing the CR range and continuing to move limits with a flow range up to 320m3/h.
After the last big addition of the CR 185 and CR 215 pumps – with a flow range capacity up to 240 m3/h and 280m3/h respectively – we continue to push the boundaries with this strong addition to the world’s most modular pump range. Our new hydraulic design improves everything from impeller and guide vanes to inlet, discharge port, sleeve and diffuser – giving you world-class energy efficiency and improving pump reliability even more than before.
Our CR range delivers world-class reliability, with pumps that are tested to the absolute limits and beyond to offer optimised operating economy via enhanced hydraulic efficiency. The CR pump range provides literally millions of solutions to fit your every application need.
The CR 255, CR 215 and CR 185 are three new CR pumps that together with the CR range continue to push the boundaries of performance. Find out more below and get a first-hand look at the added value of the new flow range capacities brought to you by the CR 255, CR 215 and CR 185. The pumps have been designed using state-of-the-art simulation-driven processes and have been field-tested around the world – so you can install and operate the range with total confidence.
Grundfos Pumps, +27 (0) 10 248 6000, info_za@grundfos.com, www.grundfos.com
This revolutionary system delivers optimal performance while reducing your total cost of ownership. It also offers unparalleled flexibility and simplicity on a whole new level. You might even say it thinks for itself. We invite you to enter a new era in wastewater pumping with Flygt Concertor.
One powerful solution. Unlimited possibilities .
Jet Park-based pump and dredging specialist IPR has been appointed by Toyo Pumps Europe (TPE) to market the leading Toyo heavy duty slurry pump range in southern Africa.
IPR’s established presence and reputation in the market – as well as its capacity to support customers – was the basis for TPE’s choice of IPR as its official distributor in the region, according to Edoardo Palmisano, Business Development at TPE. Increasing sales in Africa is an important part of TPE’s development strategy, says Palmisano. Based in Belgium, TPE is a subsidiary of Japanese company Toyo Denki Industrial, which manufactures Toyo pumps. TPE manages the distribution of Toyo pumps in Europe, Middle East and Africa.
“South Africa is one of the countries we have decided to focus on,” he says. “We have appointed IPR as our distributor because it is a serious and dynamic company which is a well-known name in the pump rental and sales market.”
He also praised IPR’s “pragmatic and positive approach” – and highlighted the value of IPR not only selling Toyo pumps but also renting them to customers. The Toyo brand is recognised globally due to its high quality, robust construction and efficiency in dealing with abrasive material, offering the largest range in this type of heavy duty slurry pump.
“Africa is a continent with important economic growth potential, and the future market for our pumps is important,” he says. “We are convinced that Toyo pumps can contribute to the development of Africa, so it is time to increase the Toyo pumps presence here.”
He explains that, as one of the most advanced countries on the continent, South Africa’s potential justifies a specific effort. In particular, continued development will require growing investments in mining, construction and other industries, and will include dredging works.
“TPE is mainly present in north, western and central Africa with pumps in applications such as dredging and transporting slurries and other abrasive liquids,” says Palmisano. “We have also been selling Toyo pumps in South Africa, but not through a continuous local distribution channel.”
Ruaan Venter, Rental Development Manager at IPR, highlights the benefit to customers of having access to the Toyo range. These heavy duty slurry pumps are engineered to solids that have settled out of fluid suspension, he explains, a situation where conventional pumps often fail.
“The pumps feature a patented built-in agitator that lifts the sediments and creates a homogenous slurry mixture which enables continuous pumping of slurries with high solids concentrations,” says Venter. “Their quality and reliability, combined with IPR’s application expertise and maintenance capability, ensure a winning partnership that puts customers first.”
IPR, +27 (0) 87 759 8654, admin@pumprental.co.za, www.pumprental.co.za
We cater for all sectors of industry including underground and surface mining, quarrying, construction, wastewater, energy, petrochemical, oil and gas, engineering, agriculture and general industry across Africa.
We are known for our agility with a proven track record of offering customers quick and easy access to a comprehensive range of dewatering pumps, heavy duty slurry handling pumps, dredging and hydro mining solutions either for outright purchase or rental
Our small portable pump sets are lightweight and easy to move on site yet engineered for the toughest applications. Available in petrol, diesel or electric drive.
Submersible pumps are an effective, inexpensive solution for dewatering whether on an opencast mine or quarry site, in an underground mine, on a construction site or anywhere else that dewatering needs to be done.
Our self-priming diesel driven pump sets are suitable for dewatering applications where power is not readily available. Available as standard import or as local custom engineered.
The SlurrySucker Dredging System is suitable for the regular cleaning of process water ponds, return water dams or other water storage areas. It is also ideal for dredging and cleaning water capture areas where silt or slimes is an issue or where water retention and water holding capacity is being threatened.
The locally manufactured SlurryBlaster is purpose-engineered for removal of slurry and sediment accumulation on dam walls and inside dams. It will assist mines with on-going maintenance. It offers mining and plant operations a cost effective cleaning tool for all applications where slurry has become an issue and needs to be washed away.
Heavy duty slurry handling solutions from global supplier, Toyo provide high performance pumping of slurries including those with solids that have settled out of fluid suspension. Toyo heavy duty slurry pumps move material in applications not previously considered pumpable.
Tel: +27 87 759-8654
admin@pumprental.co.za
www.pumprental.co.za
In the mining industry’s drive to conserve energy, a focus on pumps is essential, especially given the sheer scale of pumping equipment required on the average mine and mineral processing plant.
On this score, global minerals process specialist FLSmidth has allowed mines to achieve new levels of efficiency with the initially patented wear ring technology on its KREBS pumps, according to Stephan Kruger, FLSmidth’s Vice President Pumps, Cyclones and Valves for Sub-Saharan Africa, Middle East and South Asia.
Mines have seen significant efficiency gains by using KREBS pumps, explains Kruger, resulting in considerable bottom line impacts when multiplied by the dozens or even hundreds of pumps often employed on a single mine site.
“It is not only the rising cost of electricity that drives mines’ energy strategies, but also their commitment to a low carbon future,” he says. “
FLSmidth’s KREBS pumps directly support these efforts by our mining customers, thanks in great part to our innovative wear ring technology.”
He highlights that two key aspects that reduce efficiency in slurry pumps tend to be suction side recirculation and mechanical grinding between the casing and the impeller.
The wear ring significantly reduces both of these factors, leading to lower power draw and longer pump life.
“Through our case studies, we have seen power draw being cut by 5 to 10% for the same flow and head with the application of KREBS pumps,” he points out. “Similarly, we have measured the impact on pump life, and have shown that the life of wet end parts can be lengthened by one and a half to two times.”
According to Derek Lane, General Manager Operations, conventional products in the market solve only one of these factors through impeller and liner adjustment which may reduce recirculation but simultaneously exacerbates the grinding.
“This leaves the pump user having to compromise on efficiency, which we do not expect our customers to do,” Lane explains.
He says adjusting the wear ring allows the speed of the pump to be maintained as a constant, rather than users having to speed up the pump in response to the impact of
grinding and wear. The wear ring in KREBS pumps can be easily adjusted so that it continues drawing the same power for the required pressure, holding energy consumption to a minimum.
The regular adjustment of KREBS pumps can also be done without shutting down the pump and disrupting operations, says Morne Potgieter, FLSmidth Sales Manager Pumps, Cyclones and Valves for Central and Southern Africa. This is important as it contributes to the general continuity – and hence efficiency – of the whole operation.
“The wear ring can be simply adjusted by hand while the pump is running, and without the use of any special tools,” he notes.
“This allows the gaps to be kept as small as possible to avoid recirculation inside the pump, while maintaining speed and pressure.”
FLSmidth makes the most of this technological innovation through its skilled field service teams and training offerings, which ensure that customers understand and apply the wear ring adjustment to best effect.
Potgieter says the training leaves on-mine operators more comfortable with the task of adjustment, even if many of them may be hesitant about working on rotating machinery.
“We also do extensive technical training with customers on aspects such as pump assemblies, and make sure that we are available when they need us,” he says.
The life of KREBS pumps is further enhanced by the range of materials of construction available to suit the application, says Kruger. “The choice of material is based on the application requirements and in particular minimising wear. There are a number of factors considered which determine the material of construction such as pump size, impeller size and tip speed as well as slurry hardness.”.
Materials used in the construction of slurry pumps are classified into two main types: metals and elastomers. For metal pumps highchrome alloys, hypereutectic alloys, hypoeutectic alloys and stainless steels are commonly used. Elastomers
options vary between natural rubber, polyurethane and synthetics such as neoprene. He emphasises that the application of these materials makes their own contribution to the mining sector’s sustainability agenda, by
reducing the level of scrap produced due to equipment replacement.
FLSmidth, info@flsmidth.com, www.flsmidth.com
For Earth Day 2023, we’re spotlighting 5 ways that Xylem is investing in our planet by reducing our environmental impact. We’re committed to being a responsible corporate steward, advancing sustainability across our company footprint, and through our customer solutions and work to serve communities, as we address the world’s water challenges.
To advance our commitment to reach Net-Zero before 2050, we’re helping our customers decarbonize, and we’re leading by example by reducing the carbon footprint across our own operations.
Seventeen of our 22 major manufacturing sites are now using 100 percent renewable energy, and we are expanding our focus on renewable energy to our smaller locations.
Among the steps we’re taking:
• Decreasing the consumption of energy at our sites
– One way we’re doing this is by conducting “energy treasure hunts,” where Xylem colleagues work to identify opportunities to find and cut energy waste. We’re also changing equipment to conserve energy. For example, in Chihuahua, Mexico, we replaced the compressors in our factory with energy-saving variable frequency equipment.
• Generating our own renewable energy – Our location in Dubai generates almost all the energy they use by solar power, and we also leverage solar power in Buenos Aires, Argentina; Nanjing, China; Weilheim, Germany; Sundbyberg, Sweden; and Cheektowaga, New York.
• Procuring green energy at sites that would otherwise not have access to sources of renewable energy. One example
is our manufacturing site in San Diego, which now runs on 100 percent renewable energy and, in 2022, became the first Xylem site to have this goal externally verified.
Twelve of our major sites are recycling and reusing 100 percent of process water. In 2022, we launched a new water treatment plant at our location in Emmaboda, Sweden. Designed and supplied by Xylem, the system can recycle 20 million liters of water each year.
Our waste reduction strategy centers around working with our suppliers to reduce packaging, segregating waste streams more comprehensively, and implementing increased or new recycling practices or on-site reuse of certain materials considered wastes in the past.
Twelve of our major sites achieved our goal of zero process waste to landfill in 2022, doubling our total from 2021.
One great example is our site in Slaton, Texas, which has established a sand recycling and reuse program that is recovering sand while streamlining production processes. We’ve also started recycling programs for cardboard and wood in our factories in Morton Grove, Illinois, and Auburn, New York.
We’ve committed to transitioning 100 percent of our passenger vehicles to electric or hybrid plug-in solutions and 80 percent of our global fleet, which includes service vans and trucks, to electric or hybrid plug-in solutions. In recognition of our progress, in 2022 our Fleet Procurement Category Manager won the prestigious Fleet Europe award for “European Fleet Procurement Manager of the Year.”
Ensuring safe Water, Sanitation and Hygiene (WASH) across our supply chain is not only an integral part of our mission at Xylem, it’s also a key component of business continuity and supply chain resilience.
The WASH4Work Pledge initiative, which Xylem joined in 2019, has been a great tool to address WASH standards and action on SDG6, within our Supply Chain. Since January 2020, more than 600 Xylem supply partners have committed to the WASH Pledge for the Workplace.
Xylem, makingwaves@xyleminc.com, www.xylem.com
A strategic drive to grow the Grindex dewatering pump footprint in key Southern African markets has already begun to deliver results for local distributor Integrated Pump Technology, with significant take-up in mines where dewatering is mission critical.
Among the countries seeing the most action is the Democratic Republic of Congo (DRC) and Zambia, says Integrated Pump Technology Managing Director Jordan Marsh. With rising global demand for copper in a world pursuing a lower carbon future, mines in the DRC have been growing. “With many of these mines being among the wettest in the world, dewatering is a vital duty that is well served by our quality Grindex pumps,” says Marsh. “Since we established sales and support channels with well-placed distributors in these regions, we have seen sizeable orders coming through for our equipment.” He notes that many copper mines in Southern Africa are expanding and mining deeper, and in countries like the DRC, Zambia and Tanzania this means much more water being encountered in mining operations.
Grindex submersible pumps are now playing an important role in keeping deeper mining areas operational and safe. “It is gratifying to see demand growing for both ends of our pump spectrum – for our smaller pump sizes and the larger units,” he says. “On the smaller side, we see the 3,7 kW and 5,6 kW pumps are popular – and the larger pumps we have supplied include 10 kW, 18 kW, 37 kW, 80 kW and 90 kW units.”
These are supplied mainly in the Grindex H model range –the high head pumps – with a number also being supplied from the Grindex N model range for more flow at lower heads. He highlights that Botswana has also become a focus for Integrated Pump Technology, especially the country’s diamond and copper mines. Progress is being made in proposing efficient dewatering systems using the world class Grindex range.
“So successful have our efforts been in neighbouring countries that last year our export sales just surpassed our local performance,” says Marsh.
“We believe that our cross-border work will continue to be very productive in terms of getting to know new customers and meeting their variety of specific dewatering needs.” With South Africa’s Northern Cape province being an exciting area for mining, the company has recently boosted its sales resources there, he points out. There has also been a strong effort directed into its distributor base around South Africa – including extensive training on various aspects of the Grindex range which has set the foundation for further growth. Integrated Pump Technology has over a dozen distributors in this country alone. “Our business development drive into new African territories continues very strongly,” he emphasised. “This includes countries like Angola, Gabon, Kenya, Malawi, Rwanda, Tanzania and Uganda, and in some of these we are already making exciting progress.”
There’s no way around it: pumps play an essential role in the success of processing industries across the globe. Whether its chemical processing plants, oil fields and refineries or wastewater treatment facilities, pumps allow all these operations to function properly.
- By Edison BritoWhile pumps are versatile pieces of equipment, they also are not impervious to wear, which in turn impacts performance. Over time, consistent and unchecked wear can ruin a pump’s efficiency and functionality. This pathway eventually leads to failure.
While wear is inevitable with industrial equipment, it does not have to undermine a pump’s performance. The best way to keep a process pump operating at its peak throughout its lifespan is with protective and preventive maintenance. By following and maintaining a regular maintenance schedule, operators can ensure prolonged, optimal pump performance. This white paper will highlight the importance of pump maintenance while also revealing the areas to focus on for getting the most out of a process pump. For this white paper, we will focus on the maintenance concerns of centrifugal pumps.
No matter the application or the operating conditions, a defined and routine maintenance program will extend the life of a pump. Well-maintained equipment lasts longer and requires fewer and less-expensive repairs, especially when some pumps have lifespans that extend 15 years or longer.
Regular and efficient maintenance is required to obtain optimum working life from a centrifugal pump. After purchase, the pump manufacturer typically advises the plant operator about the frequency and extent of routine maintenance. The operator, however, has the final say about how his facility’s maintenance routine will function, which could range from less frequent but more major attention to more frequent but simpler servicing. The potential cost of unexpected downtime and lost production is also a significant item when determining the total LCC of a pumping system.
The facility operator should also keep a detailed record of all preventive maintenance and repairs for each pump. This
information allows operators to have an easily accessible record for diagnosing problems and eliminating, or minimizing, any future equipment downtime.
For centrifugal pumps, routine preventive and protective maintenance practices should include, at a minimum, the monitoring of:
• Bearing and lubricant condition. Monitor bearing temperatures, lubricant level and vibration. The lubricant should be clear with no signs of frothing, while changes in bearing temperature may indicate imminent failure.
• Shaft seal condition. The mechanical seals should show no signs of visible leakage. Any packing should leak at a rate of no more than 40 to 60 drops per minute.
• Overall pump vibration. Imminent bearing failure can be preceded by a change in bearing vibration. Unwanted vibration can also occur due to a change in pump alignment, the presence of cavitation or resonances between the pump, its foundation or the valving located in the suction and/or discharge lines.
• Differential pressure. The difference between the readings at the discharge and the pump’s suction will provide the total developed head pressure of the pump. A gradual decrease in the developed head pressure of the pump can indicate that the impeller clearance has widened, which requires adjustments to restore the pump’s intended design performance: impeller clearance adjustment for pumps with semi-open impeller(s) or replacement of the wear ring(s) for pumps with closed impeller(s).
Maintenance and monitoring intervals should be shortened if the pump is used in severe-service conditions, such as with highly corrosive liquids or slurries.
Quarterly Maintenance
• Check the pump’s foundation and hold-down bolts for tightness.
• The oil should be changed after the first 200 hours of operation for a new pump then after every three months or 2,000 operating hours, whichever comes first.
• Regrease bearings every three months or 2,000 operating hours, whichever comes first.
• Check the shaft alignment.
Annual Maintenance
The pump’s performance should be checked and recorded in detail at least once a year. Establishing performance benchmarks should occur during the early stages of a pump’s operation when the parts are new with proper installation adjustments.
This benchmarking data should include:
• The pump’s developed head pressure as measured at the
suction and discharge pressures for three to five conditions should be obtained. A no-flow reading is a good reference and should be included where possible and practical.
• Pump flow rate
• Motor amp draw and voltage, corresponding to the three to five operating conditions mentioned above
• Vibration signature
• Bearing housing temperature
During annual pump performance assessments, any changes in the benchmarks should be noted and used to determine the level of maintenance required to get the pump back to its optimal functionality.
While preventive and protective maintenance will keep a pump operating at its peak efficiency, there is one factor to keep in mind: all pump bearings will eventually fail. Bearing failure typically occurs due to the lubricating medium rather than equipment fatigue. That’s why monitoring bearing lubrication – another form of maintenance – helps maximize bearing longevity and, in turn, pump life.
When opting for oil for bearing lubrication, it’s important to use non-foaming and non-detergent oils. The proper oil level is at the mid-point of the bull’s-eye sight glass on the side of the bearing frame. Over-lubrication must be avoided as it can be just as damaging as under-lubrication. Excess oil will cause a slightly higher horsepower draw and generate additional heat, which can cause oil frothing. When checking the lubricating oil condition, cloudiness can indicate that overall water content – commonly the result of condensation – is higher than 2,000 ppm. If this is the case, the oil needs to be changed immediately.
If the pump is equipped with regreaseable bearings, operators should never mix greases with different properties or consistencies. Shields must be located near the interior of the bearing frame. When regreasing, ensure that the bearing fittings are clean as any contamination will decrease bearing life. Overgreasing must also be avoided as this can cause localized high temperatures in the bearing races and create caked solids. After regreasing, the bearings might run at a slightly higher temperature for one to two hours.
In instances of replacing a part – or several – on a malfunctioning pump, operators should take this opportunity to examine the pump’s other components for signs of fatigue, excessive wear and cracks. At this time, any worn parts should be replaced if they do not meet the following part-specific tolerance standards
• Bearing Frame and Foot — Visually inspect for cracks, roughness, rust or scale. Check machined surfaces for pitting or erosion.
• Bearing Frame — Inspect tapped connections for dirt. Clean and chase threads as necessary. Remove all loose or foreign material. Inspect lubrication passages to be sure that they are open.
• Shaft and Sleeve — Visually inspect for grooves or pitting. Check bearing fits and shaft runout, and replace the shaft and sleeve if worn or if the tolerances are greater than 0.002 inches.
• Casing — Visually inspect for signs of wear, corrosion or pitting. The casing should be replaced if wear exceeds 1/8inch deep. Check gasket surfaces for signs of irregularities.
• Impeller — Visually inspect the impeller for wear, erosion or corrosion damage. If the vanes are worn more than 1/8-inch deep, or if they are bent, the impeller should be replaced.
• Frame Adapter — Visually inspect for cracks, warpage or corrosion damage and replace if any of these conditions are present.
• Bearing Housing — Visually inspect for signs of wear, corrosion, cracks or pits. Replace housings if worn or out of tolerance.
• Seal Chamber/Stuffing Box Cover — Visually check for cracks, pitting, erosion or corrosion, paying special attention to any wear, scoring or grooves on the chamber face. Replace if worn more than 1/8-inch deep.
• Shaft — Check the shaft for any evidence of corrosion or wear. Check the shaft for straightness, noting that the maximum total indicator reading (TIR) at the sleeve journal and coupling journal cannot exceed 0.002 inches.
While routine maintenance might seem daunting, the benefits outweigh the risks of deferring it. A wellmaintained pump keeps operations effective and efficient while extending pump life and avoiding premature pump failure. Letting maintenance lapse or deferring it further and further into the future can lead to costly downtime and expensive repairs. Though it requires great attention to detail and multiple steps, having a robust maintenance plan will keep pumps running and downtime minimal, allowing their operations to thrive now and well into the future.
Griswold, info@griswoldpump.com, www.psgdover.com/griswold
Both pump technologies share strengths and benefits when used in fluid-handing applications. Pumps are an integral part of everyday life. They are machines that move fluids and produce hydraulic energy.
Over time, pump technologies have evolved to allow pumps to process fluids of varying viscosities and properties, such as chemicals, biofuels, crude oil and solvents.
Several pumping technologies are available to operators, offering a wide variety of choices for their processing needs. They can select centrifugal, submersible, piston, or axial pumps and still have several options available. Over time, one pump technology has stood out against the others – positive displacement (PD).
PD technology has endured decades of process challenges and substances, becoming a versatile choice among professionals for its consistent performance and robust nature. PD pumps operate by pulling in fluid, trapping a fixed amount within a chamber and then forcing it out into a discharge pipe. Because of their design, PD pumps tend to have
better flexibility than alternative pumping technologies when handling pressure and flow variations found in continuous or intermittent-type processes. PD pumps also operate at high efficiencies when operating conditions –such as viscosity or pressure – change, allowing them to operate at peak efficiency regardless of the conditions or environment.
Gear and vane pumps are the standouts of the PD pump line, which also includes diaphragm, peristaltic, eccentric disc, and lobe pumps. These two pump variations have served as popular picks for a range of industry applications, such as manufacturing plants, tank trucks, ships, trains, storage tanks and bulk storage facilities. When it comes to these pumps, the toughest choice an operator has is deciding which one will work best in their application. It’s not always a simple choice either, as both technologies offer many of the same benefits and varying advantages.
In this white paper, we’ll take a closer look at gear and
vane pumps, examining the advantages of each and the benefits they share.
Gear pumps create flow by pushing liquid through a mesh of teeth between two rotating gears. A drive shaft moves one gear, and that motion moves the other gear. The rotating gears form a liquid seal inside the casing, creating a vacuum at the inlet as the gear teeth separate. Liquid flows into the space and moves around the outer edge of the gears. Once the teeth meet again by the outlet, the gears force the liquid out.
Gear pumps can be classified in to two main categories –internal or external. External gear pumps use two separate shafts to support two interlocking gears, which form a mesh at the center of the pump to move fluid along. Common gear types include helical, spur or herringbone gears to move liquid through the pump.
A similar principle is used in the internal configuration, but with two interlocking gears of different sizes. The smaller gear rotates within the larger gear, which creates cavities for fluid transfer. An idler pin and a bushing keep the smaller gear, also known as the idler, in an off-center position, allowing it to interlock with the external gear’s cavities. A fixed, crescentshaped spacer serves as a seal between the pump’s ports and fills the void from the smaller gear’s off-center position.
Sliding vane pumps feature a rotor with vanes that slide into and out of it as the rotor turns. This sliding motion creates chambers into which the liquid flows, and as the rotor turns, the liquid is moved to the outlet where it is discharged as the pumping chamber is squeezed down. Each revolution of the rotor displaces a constant volume of fluid with little chance for slippage, which is the very essence of a PD pump. Variances in pumping pressure have little effect on the sliding vane pump’s flow rate, and the open flow profile provides a gentle and shear-sensitive
Regardless of configuration, gear pumps do not have many moving parts. The primary components in an external gear pump include two gears and two shafts. Internal gear pumps consist of a rotor (larger gear) and an idler (smaller gear), as well as an idler pin, bushing and a crescent-
In either setup, the number of components is minimal. Operators don’t have to stockpile extra components in case of failure as there are only so few to evaluate. With few components, operators don’t have to worry about keeping track of multiple moving parts and replacing them on a frequent basis.
Maintenance is also easy to perform on a gear pump. During maintenance shutdowns, gear pump operators only have a few components to evaluate and service. In many cases, service can be performed in place without the need to remove the pump from its service location. Should a component, such as a gear, fail, operators simply have to open the pump, replace the part and put it back online.
This speeds up and simplifies the maintenance process, giving operators more time to focus on other tasks instead of dedicating time to an array of moving parts with different service requirements.
Gear pumps are usually made from cast iron or stainless steel, giving the technology a robust framework to handle a variety of highly abrasive fluids with varying viscosities. They can also be made using composites or alloys, which expands their fluid-handling range.
These gear pump variations can process corrosive liquids, such as sodium hydroxide and sulfuric acid, fluids that can severely damage other material compositions. Ductile iron is another material that can be used to construct gear pumps, an option reserved for reducing costs on larger pumps without sacrificing performance.
Temperature performance is a key attribute for gear pumps. Because of their robust nature, gear pumps can successfully operate in temperatures as low as -112°F (-80°C) and process fluids with temperatures as high as 800°F (425°C).
This type of flexibility means varying temperatures –in fluids (surfactants, soaps, adhesives, asphalt) and atmosphere – won’t hamper the performance of gear pumps. They can operate at peak levels no matter if they are processing fluids in the Artic, the Amazon or anywhere
Gear pumps also don’t suffer when it comes to handling fluids across the viscosity spectrum. The interlocking gears can reliably accept fluids as low as 5 centipoise (cP) or as high as 1,000,000 cP. This is especially beneficial in
process plants as operators don’t have to outfit them with several different pumping technologies for varying fluid proprieties. Gear pumps also come with tight internal clearances, the tightest of which are found in the rotor/ case, rotor/head and rotor/crescent mesh. These tight clearances allow for the successful management of aggressive liquids and dissolved solids, which include paints and coatings, adhesives, sealants, rubbers, epoxy resins, detergents and food-based products like sweeteners and chocolate.
Sliding Through – Advantages of Sliding Vane Pumps
Sustained performance, long-lasting components
Sliding vane pumps leverage non-contacting rotating components that avoid material wear and sustain flow rate capacity.
The contacting elements are dynamically actuated vanes, that self-adjust for wear throughout the life of a pump. This allows a used pump to sustain the same performance achieved by a brand-new pump. Time is a most essential commodity and sliding vane pumps provide operators with a Sliding vane pumps sustain optimal performance throughout their lifetime by using a sliding vane design. As the vanes wear, they slide out of the rotor and continue to stay in contact with the cylinder. This means that even after many years and more than 100 million gallons of transferred liquids, internal slip will not occur, guaranteeing volumetric consistency throughout the life of the pump. This is called flow sustainment. Time is valuable, and vane pumps ensure that process times remain optimized throughout the pump’s life.
Component life is another feature of sliding vane pumps, which have a symmetrical between-bearing support design. This means the hydraulic load is supported equally on both sides, resulting in minimal shaft deflection and the prevention of cyclical deflection and fatigue. The sealing surfaces are also immediately adjacent to the bearings, making them stationary and ensuring longer seal life. The ultimate benefit of the between-the-bearing design is that no uneven loads occur, preventing wear of contacting components.
By their design, sliding vane pumps don’t have metal-onmetal contact. Without this form of contact, sliding vane pumps can run dry without galling or adverse effects on pump life. This means sliding vane pumps can self-prime, even if they start empty. In such a scenario, the pump can still draw a vacuum, compress the air in the piping, push it through the discharge side and draw liquid from the suction source until primed – all without damaging the unit.
The vacuum suction capacity of a sliding vane pump is also noteworthy. The pump has high suction lift to 25 feet (8.3 m), making it well suited for top-offloading, underground storage or berm applications. Because sliding vane pumps can run dry effectively and pull a strong vacuum, the technology also fits well in product-recovery applications. The pump has linestripping capabilities, allowing operators to recover valuable product from piping and hoses. With proper product recovery, operators can save money and waste less product during recovery and cleanup.
Sliding vane pumps don’t require a minimum liquid viscosity because they don’t have metalon-metal contact. This means that these pumps have a liquid-handling range from ultrathin liquids (0.2 cP) all the way up to liquids with a thickness of as much as 22,500 cP, without a drop in performance when handling thin (3-100 cP) or medium-viscosity (100-5,000 cP) liquids.
Vane pumps can also handle liquids with small particulates
up to 40% concentrations. Sliding vane pumps also require no self-lubrication so both lubricating and nonlubricating liquids can be handled equally well. In fact, sliding vane pumps are renowned for operating reliably under continuous cavitation in low net positive suction head (NPSH) applications, where multi-phase vapor/liquid mixtures are expected.
Whether it’s crude oil or condensate, sliding vane pumps can handle them with the same pump, making this technology a champion of ultra-low viscosity and nonlubricating applications, as well as thick crude applications with suspended solids.
Each pump technology’s advantages make them better suited for select applications, depending on the needs of the operators. Still, they have shared features that make both technologies reliable and dependable.
Both gear and sliding vane pumps excel in fluctuating systems, offering significant operational flexibility when compared to centrifugal pumps. Centrifugal pumps have a single optimized best efficiency point (BEP) and fail when operating outside of this narrow range.
Unfortunately for centrifugal pumps, most applications operate across a wide range of conditions, such as fluctuations in pressure, flow rate, tank level, or fluid properties. Gear and sliding vane pumps have wide performance ranges, allowing operators to sustain optimal performance consistently.
Fluid viscosity, thickness, density, vapor phase, and sheer sensitivity are additional areas of advantage for gear and sliding vane pumps. Gear and vane technologies allow for
wide range of properties in each of these areas, providing flexibility for liquid type, ambient conditions, and process parameters unmatched by other pump technologies.
Gear and sliding vane pumps also feature flexible sealing options, available in packed, single seal, double seal, or sealless design (a magnetic-drive).
This seal-less design eliminates dynamic seals and prevents leaks. Both gear and vane are electrically driven, removing the need for compressed air needed by many other sealless pump types.
Other standout features include a vast, consistent, zero-pulsation flow range, the ability to operate at high temperatures, and immunity to changes in the liquid pressure or viscosity.
Gear and sliding vane pumps also have self-priming ability, allowing them to run dry without issue. These pumps can also handle bi-directional pumping, meaning they can process fluids in either direction if required.
The composition of these pumps also serves as an advantage to both. Gear and sliding vane pumps have several options for material construction.
Cast iron, ductile iron and stainless steel are three of many options available to these pump technologies. When it comes to handling difficult substances that require heat retention, such as asphalt or adhesives, both pump technologies can be jacketed across most of their surface area.
Blackmer, mark.pyk@psgdover.com, www.psgdover.com
There are times when a simple pump design and less maintenance are preferred by pump users, especially in messy dirty wastewater applications. Such was the case with one wastewater plant operator in South Africa, which was being called in every couple of weeks to remove, disassemble and clean wastewater pumps at one or other of the facilities that the company maintains.
Aeration pumps float on wastewater treatment dams and ensure that chemical decomposition of the dirty water occurs before the wastewater gets treated further. The pumps ensure that the water remains oxygenated and that there is aerobic decomposition rather than anaerobic decomposition, which usually results in volatile and poisonous gases such as methane.
The pump design that was in place was a standard vertical shaft pump design with an output of between 5 kW and 10 kW.
However, the bearing design was complex and prone to failure before the introduction of Vesconite materials.
The main shaft bearing design consisted of a ball bearing with carbon mechanical seals on either side of it and the ball bearing was lubricated by oil that was pressure fed into the system so the pressure of the oil was higher than the pressure of the water on either side of the carbon seals, describes Vesconite Bearings engineer Petrus Fourie.
The main problem was that the carbon seals would pick up the dirt and grime that was in the naturally abrasive water and would erode. The seals would then fail and the wastewater would enter into the ball bearing.
“Anyone who has worked with ball bearings would know that ball bearings and water are not friends,” describes Fourie.
“If you get water anywhere near them they corrode very fast, especially if it is abrasive water,” he says.
It is this problem that resulted in the pumps seizing or shutting down because the ball bearings failed, and this resulted in the aerator pump company being called out every two to three weeks for pump maintenance.
The maintenance then required fishing the pump out of the wastewater; opening it up; cleaning out all the water and dirt that was trapped inside; and replacing the ball bearings.
The aeration pump company then approached Vesconite Bearings in search of a solution and Vesconite Bearings and the pump original equipment manufacturer (OEM) went through several design iterations before an appropriate and effective design was finalised.
The first design involved the replacement of the ball bearing, two carbon seals and the lubrication system with a no-swell wear-resistant Vesconite Hilube bushing in the existing housing.
The design was a combined thrust bearing and radial guide bearing — a combined main shaft bearing and thrust bearing so it has both axial and radial running faces.
“We proposed a flange bearing design where basically a step on the shaft would sit on the flange,” states Fourie.
“The vertical shaft would sit on top of the flange to absorb the vertical forces, the axial forces, and then you would have the bushing that would absorb lateral forces, or radial forces,” he says.
“In a pump that uses plain bearings from the start, you have a separate thrust washer or wear ring and a main shaft bearing,” Fourie notes.
“But here we hybridised the two parts,” he says noting that, because the ball bearings absorbed the axial force, Vesconite Bearings designed a plain bushing also to take on the axial force.
However, the first design proved inadequate in testing on a test bench with dirty water in the OEM company’s workshop.
None of the water that followed through the pump got to the flange face and this resulted in that particular face overhearing and melting.
“I suggested that the pump company cut some grooves on the flange face to allow the water to flush through,” notes Fourie. “I also suggested that they add a stainless steel collar to the shaft, which would increase the area on to which the axial force applied,” he says, adding
that, if you increase the area, you would decreasing the pressure and decrease the overall load on the bearing so it is less likely that it would overheat.
This second design worked better, but a couple of the grooves got blocked up on the axial face because of the dirty water and, again, that resulted in the bearing overheating. Fourie further altered the design and suggested that the pump OEM switch its bearing material to Vesconite Bearings’ highestgrade bearing material, Vesconite Superlube, which is known for its ultra-low friction and extreme wear resistance.
His design also included additional grooves, increased groove sizes and holes through the stainless steel flange that rests on the axial face of the bearing to allow more water flow through the bearing.
The third design iteration has proven to be a charm and the South African wastewater company is happy with its pump’s performance.
The exact lifetime improvement has yet to be quantified, as the pumps that were installed with the latest bearing design are still operating, having been installed in October 2022.
Other advantages include that the company has reduced oil lubrication which, prior to the introduction of Vesconite Superlube, took place every four to six weeks depending on the water quality and currently takes place between four to six months with Vesconite Superlube, says the wastewater company’s operations director, who adds that the company is still deciding on a final acceptable maintenance schedule for the Vesconite Superlube application.
In addition, Vesconite Bearings’ solution resulted in the elimination of the carbon seals and the ball bearings, making the system much less complex and allowing for fewer problem areas while making the bearing system cheaper due to the reduction in the number of components. The wastewater company’s operations director notes that he estimates that the Vesconite Superlube solution costs two third’s
the cost of the replaced bearings and seals, with additional savings for the end user since they have reduced down time, labour and service costs.
The company increased the bearing lifetime and decreased its running costs. The company has also indicated it is easier to do maintenance because it is simpler to replace a plain bushing than to replace the carbon seals and ball bearings that were present in the earlier design.
“There are much fewer places for the dirt to accumulate so the engineer’s job is a little bit less messy,” states Fourie. Vesconite’s premier bearing material, Vesconite Superlube, is a niche product which is made for niche applications such as this one, which is characterised by extremely abrasive and dirty water.
The material’s low friction, which is lower than virgin PTFE , is directly proportional to the material’s low wear rate.
“The low friction also has the advantage that it generates less heat,” describes Fourie.
“If you have any application that has a tendency to overheat and is wearing too fast, Vesconite Superlube is the ideal replacement because it generates less heat and it wears less quickly,” he adds.
Vesconite Bearings, +27 (0) 11 616 1111, vesconite@vesconite.com, www.vesconite.com
The technical advancement of Weir Minerals’ GEHO® positive displacement pumps has ensured they play a key role in reducing mines’ environmental footprint.
The GEHO® pump range is well known in various pumping applications including tailings, backfill, ore transportation and dewatering. Weir Minerals Global Product Manager for GEHO® positive displacement (PD) pumps, Erik Vlot, highlights the pumps’ ability to pump highly viscous slurry, allowing mines to conserve water. The energy efficiency of pipeline transportation also helps cut energy costs and reduces mines’ carbon footprint.
“The foundation of GEHO pumps’ success is our ongoing attention to technical innovation and improvement,” says Vlot. “This also allowed us to be pioneers in the pumping of very acidic material at high temperatures, such as nickel slurry at more than 200°C at a mine in Madagascar.”
With their high capacity, GEHO® pumps transport bauxite or iron ore over hundreds of kilometres, offering one of the most cost effective and sustainable transfer methods available to the mining industry. These pumps have also played an integral role in the success of a Weir Minerals paste solution at Finland’s largest open pit mine. Yara’s Siilinjärvi mine uses GEHO® pumps to move tailings from the plant, achieving the necessary beach slope on its tailings facility to meet its life-of-mine strategy.
Backfilling is an important method for mining to achieve safety and environmental goals, and GEHO® pumps have been enabling this work. In a North American platinum
operation, the equipment pumps over a thousand litres a minute of this viscous backfill material – measuring 70% solids by weight – back into the mine’s worked out areas. In the context of deep mines, GEHO® pumps provide an efficient and reliable way of dewatering from great depths, instead of using multiple smaller pumps to transfer water to surface.
The powerful GEHO® pump range can do this by pumping from the bottom of a mine to the surface in just one lift –even over kilometres.
“Apart from the cost effectiveness of this solution, an important advantage is that it reduces the risk of one pump in a pumping chain failing, and disrupting the entire dewatering function,” he says. “It also reduces the cost and maintenance requirements of having multiple pumping stations at different levels within the mine.”
The reputation of GEHO® pumps has also been built on their reliability, he explains. This has resulted from Weir Minerals’ ongoing research and development into its pumps’ wear parts. This process is based on an in-depth understanding of the whole pumping system in which the pump operates.
“Taking into account how our pumps interact with these systems, we focus on key aspects of the pumps such as
In an era where innovation and self-sufficiency are paramount, the manufacturing industry adapts to stay ahead of the curve. Invincible Valves has recently moved towards independence by acquiring a machine shop. This bold step eliminates reliance on third parties and paves the way for diversification and long-term business growth. Pipes, Pumps and Valves Africa sat down with Managing Director Pam du Plessis to learn more about this latest development in the company.
At Invincible Valves, there is always something happening. For Du Plessis, this is critical for the future of the company. “We have built a strong foundation for our business, so it makes sense that we continue to develop and grow this even more.”
Having experienced unprecedented growth in the past few years, the company was expanding when the Covidpandemic happened. Not one to let a good challenge go to waste, Du Plessis opted to forge ahead rather than shelve plans to upgrade and expand the facilities. While the pandemic did slow down the process ever so slightly, purchasing a new facility close to the existing Knights, Germiston premises went ahead, and the more than 2000 square meter under-roof facility heralded a new era for Invincible.
“The new factory was welcomed by industry and allowed us to streamline our operations and make our entire process more efficient. Since its opening, it has already undergone an extensive renovation and now boasts an increased range of capabilities.” This includes the addition of a separate rubber lining division, an entire paint bay, and a shot blasting bay. Furthermore, they have invested in a 10-meter autoclave and are purchasing a machine shop. By the time this edition goes to print, this will have been concluded.
technology has developed at a breakneck pace. “If one just considers the impact of 3D printing on manufacturing and how quickly it has evolved, one recognises why it is important to embrace emerging technologies and remain ahead of the game at all stages,” she says. “We are extremely forward-thinking, and this is about ensuring the sustainability of our business. Diversification is of utmost importance for valve manufacturing companies. By expanding our product range and venturing into different sectors, we reduce the reliance on a single market or industry.”
She says that purchasing the machine shop is a strategic move that not only spreads the risk but also opens doors to new opportunities and revenue streams. “In an everchanging business landscape, where market demands and technologies evolve rapidly, diversification allows us to stay ahead of the curve. Moreover, by offering a diverse portfolio of valves tailored to various applications, we can cater to a broader customer base and adapt to shifting market dynamics. Ultimately, diversification enhances our business’s resilience, competitiveness, and long-term sustainability, ensuring its continued growth and success.”
At its core, Invincible Valve’s decision to establish self-sufficiency is driven by the desire to grow the business and provide long-term benefits to its clients. Over the past 15 years, the company has experienced exponential growth, and its commitment to reinvesting in the industry has paid off. By mastering its operations on a larger scale and venturing into manufacturing, the company has established itself as one of South Africa’s top valve reconditioners, providing a variety of local industries and the export market with a full range of new and reconditioned products.
The new shop is set to be equipped with state-of-the-art CNC equipment. This complete setup lays the groundwork for enhanced production efficiency and increased control over the manufacturing process.
Du Plessis says this has become increasingly important as
“We aim to master our new machine shop before starting our next expansion stage. Growing our business will always be our goal, but we are taking our time with the process. We have an obvious strategy to ensure we are never biting off more than we can chew.”
According to Du Plessis, it is of increasing importance to be able to navigate in unforeseen waters. “We are operating in challenging times, and the manufacturing sector remains under pressure. It is with this in mind that we remain determined to achieve self-sufficiency. In doing so, we address some of our big challenges.”
One ongoing challenge for the manufacturing sector is that of load-shedding. Power interruptions and load curtailment disrupt production schedules, leading to increased costs and productivity losses. To combat these challenges, Invincible has explored several alternative energy sources, including generators and renewable power. The company has also implemented a range of contingency plans to minimise downtime.
For Du Plessis, the most significant and crucial aspect of the business is its people. Acknowledging the skills shortage in the industry, Du Plessis says it is critical for companies such as Invincible to actively invest in training and skills development programmes to retain and nurture talent. “Only by prioritising the well-being and growth of our staff can we ensure a robust foundation for future success.”
Asked about the future, Du Plessis said despite the challenges and the current global economic uncertainty, she remained pretty optimistic. “As mining operations continue to expand worldwide, the demand for valves is expected to rise. By leveraging technological advancements and staying informed about global markets, we believe we can navigate the challenges that come our way and continue to grow our business.”
Invincible Valves, +27 (0) 11 822 1777, enquiries@invalve.co.za, www.invalve.co.za
Dewatering pumps are essential in the construction industry for an efficient and speedy transfer of water and other fluids. They are used across a variety of applications and are critical to completing projects on time, meeting quality standards and avoiding costly delays.
The reliability and availability of pumps can make all the difference in ensuring a project runs smoothly without any disruptions to tasks, schedules or workers.
With the U.S. industrial pump market expected to expand at a rate of 5.9% a year over the next decade, according to Global Industry Insights, equipment uptime is gaining increased value. Mike Grant, Tsurumi's portable product and rental market manager, acknowledges that the overall outlook of the construction sector is currently robust.
“Despite some apprehension about high-interest rates affecting residential housing and the deceleration of commercial building and office space projects due to hybrid work schedules, the demand for dewatering equipment has only somewhat decreased. Consequently, infrastructure projects throughout the United States are expected to continue at a strong pace for the next few years.”
Glenn Wieczorek, Tsurumi's managing director, added that the company has undertaken a series of initiatives
to expand its capabilities in recent years. This action is in pursuit of the company’s commitment to establishing itself as a key player in the construction market and supporting the sector’s rapid growth.
“Our company is proud to devote significant efforts to promoting its manufacturing process and maintaining a well-stocked parts inventory,” Wieczorek said.
“Additionally, Tsurumi has expanded its logistical capabilities to ensure that contractors have access to the pumps they need for a wide variety of construction and infrastructure projects, regardless of location or timing.”
Contractor friendly Tsurumi’s HS Series submersible pumps are a favorite among contractors due to their transport ease and impressive ability to resist wear and clogging.
These features are largely due to a built-in shaft-mounted agitator that suspends solids while pumping water containing sand, solids and debris.
Suitable for a wide range of applications requiring the removal of water, this small yet robust trash pump is available in manual or automatic configurations, with 2 or 3-inch side discharge.
The HSE2.4S model features an Automatic Water Level Sensor that enables automatic operation, even in confined spaces where floats are not an option.
As the water level rises to the electrode, an internal 60-second timer starts the pump. Conversely, once the water level falls below the electrode for 60 seconds, the pump will shut off.
“There’s no tougher application for a piece of equipment than construction and rental, and that fact is integrated into every step of our design process to build heavy-duty, reliable equipment,” Grant said.
“Our pumps have a record of dependable, continuous work, which contractors and engineers everywhere appreciate.”
Operation for extended periods
The ability of Tsurumi’s LH Series electric submersible three-phase cast iron drainage pumps to endure extended operation at low water levels has driven their use across a variety of construction sectors.
The top-discharge flow-thru design forcibly cools down the motor, providing extended dry-run capability.
Able to fit inside 8, 12 or 16-inch pipes, with discharge sizes from 2 to 12 inches. Featuring a 4 hp to 150 hp range supporting flow rates from 110 up to 3700 gal/min.
Options include seawater-resistant kits, using special cast iron impellers, high-temperature rewinds, and mining variants where all parts that contact fluid are machined from 316 stainless steel.
These features provide high resistance to corrosive fluids or those with high pH levels.
Slim design to fit into 8-inch pipes
Tsurumi’s LB Series is an electric submersible dewatering option. The portable, easy-handling design enables fitting into 8-inch pipes while efficiently handling up to 110 gal/ min.
Ideal for applications such as well dewatering, river bypass, site dewatering and manholes in tanks, it is offered in outputs from 2/3 hp to 2 hp, with 2 or 3-inch discharge sizes.
LB models offer a level of durability equivalent to threephase drainage pumps with a single-phase design and wear parts made from abrasion-resistant materials.
The LB Series employs all the technical advantages Tsurumi is known for such as anti-wicking power cable sealing and double mechanical seals that protect the electric motor from water intrusion during submergence.
These seals, sporting silicon carbide faces, provide five times the corrosion-, wear-, and heat resistance than the tungsten carbide alternatives. Some LB models are also available in LB-A designation, employing the aforementioned Automatic Water Level Sensor that enables automatic operation.
The feature eliminates dry-running and reduces power consumption by up to 40%.
Tsurumi Pumps Africa, +27 (0) 82 404 4743, enquiries@tsurumipumpsafrica.com, www.tsurumipumpsafrica.com
Every business relies on water. It requires more than 14,0,000 litres of water to produce one car (Automotive World) and 2,700 litres to make a single t-shirt (University of Waterloo).
Daily consumption by offices and their employees is as staggering. Office buildings consume almost half of municipal water supply (Stellenbosch Business School) and large office buildings use an average of 75 litres of water per square foot and 50 litres per employee (Commercial Buildings Energy Consumption Survey). This scope also extends to the external: community relations, environmental concerns, and something as simple as customers needing water to remain economically viable.
South Africans are currently experiencing the ongoing impact of electricity undersupply, which gives us a reasonable expectation of what could happen when water supplies fail to meet demand. But unlike energy or practically any other resource input that businesses rely on, there is a tendency to treat water access as reliable and thus without many nuances in monitoring or risk management.
That attitude has to change because the world is changing. Water sources are under growing stress, weather events are becoming more intense, and urbanisation has already changed general water access and consumption patterns. If we consider that without water, every organisation will soon cease or severely curb operations, managing water risks should be a strategic priority.
What are the water risks we should consider? Here are examples:
Are you spending too much on water? Your water consumption might be a significant cost centre, but only tracking general consumption hides nuances problems such as leaks or other wastage, not to mention old pumps and other legacy equipment moving water around.
Are you assuming a regular supply? Water is a human right, and events such as droughts or demographic changes can rapidly constrain how much water a business could access.
Are you contributing to worse water quality? Whether for Environmental Social Governance (ESG) requirements or impact on surrounding communities, if your actions reduce a region's water quality, you may face backlash and punitive harm.
Are you at risk of water-related damage? Floods, erosion, hail damage and drought can harm infrastructure and supply chains.
Can regulatory changes impact operations? Since water is a public resource, State policies can suddenly and rapidly reduce water access, particularly during droughts.
Is there a reputational risk? Poor water management can hurt your brands or corporate reputation, especially if customers link responsible behaviour to your business. Are you exposed to climate change or urbanisation? Your risks will grow if you operate in regions at growing risk from extreme weather events or high urbanisation rates.
The above are common examples. But water risks are often very specific, relating to a business's physical region, operations and supply chain. Knowing a business consumes X amount of water daily or weekly is insufficient. Companies must understand their reliance on water down to the specifics.
Fortunately, you only need a small group of actions to address the broad church of water risks: Do water foot printing: Understand what types of water your business uses. At the highest level, a water footprint looks at your interactions with green (rain), blue (surface/ underground), grey (usable but unfit for consumption) and black (contaminated) water. Water foot printing can show how much you rely on external sources and what mitigation options you have, such as recycling greywater or capturing rainwater. Contextualise water use: Know where your business uses water, such as consumption, cooling, dust management, or as an integral part of processes (cleaning vegetables, mixing chemicals, etc.). This context helps determine the different priorities water represents to your operations.
Track water more directly: A monthly water bill tells you
nothing about where exactly all that water is going. Once you have a context for your business usage, measure key areas for a clear view of consumption. This is helpful for several reasons, such as knowing how to prioritise supply in the event of water restrictions. Do water life cycle assessments: Water flows in and out of your business and connects it to the outside world. Water life cycle assessments are crucial to understanding surrounding environmental and community impact, and will inform ESG and regulatory decisions. You can conduct assessments that include water with other resources—just be sure water is a priority in those assessments.
These four actions can cover most, if not all, of your water risk insights, and there are several ways to tackle each of them. The World Resources Institute and WWF provide tools covering many regional water concerns. More directly, options such as the Water Alternatives Corporate Water Risks Framework and Xylem Water Loss Management can give direct insight into business water usage. Modern analytics using historical data, smart metres and artificial intelligence can bring significant granularity to water strategies. We mustn't ignore water-related risks to our companies. The more we rely on water to produce goods and services, the more severe the impact when that water supply runs low. But businesses can prepare and put measures in place. Is your business doing that yet?
Xylem, makingwaves@xyleminc.com, www.xylem.com
www.pump-technology.com
more than just a pump complete pumping solutions
Improving the management of an MBBR system and reducing its energy consumption with Robuschi technology. Wastewater treatment is something of a customisation task, where the solution has to be tailor-made for the individual paper mill.
Surely, when the challenge takes the form of limited space and a need to discharge safely into surface water, the answer is a plant design that combines innovative biological technology with a screw compressor. Wastewater treatment in a paper mill can be optimised in a number of ways, but having to adapt an existing system set-up, where there are limits due to the plant configuration, undoubtedly complicates the job. It can always be done though. The secret lies in finding the technological solution that best fits the particular features of the site. That’s what happened in Lucca, at the plant of one of the leading corrugated cardboard manufacturers of the paper industry - Toscopaper. Robuschi, in partnership with Italprogetti (which looked after the engineering side), supplied the waste water treatment technologies, working to offer the best solution for the real system needs in terms of efficiency, reliability and easy maintenance.
The task was to intervene on an existing system that no longer met the development needs of the paper mill. The solution was developed by Italprogetti (www. italprogetti. it), deciding to use a type of technology that it had so far applied only in the field of municipal waste water treatment, adapting it in this case to the specific plant characteristics. We’re talking about an MBBR (Moving Bed Biofilm Reactor). «With this type of biological treatment,» explains Daniele Bacchi, Head of the Waste Water Treatment Sector for Italprogetti, «bacterial colonies - able to clean the water by breaking down the organic matter in it - aren’t free to move around in the water; they remain attached to special plastic supports called ‘carriers’. These, in turn, are kept in motion inside the reactor thanks to the stirring action of the aeration process whose job is to provide the system with the oxygen needed for the treatment, by injecting compressed air. Special grilles installed in the biological reactor prevent the carriers from emerging along with the treated water. This avoids
any risk of biomass loss apart from the excess which, spontaneously detaching itself from the carriers, is then taken away by the biological system.
“We’ve renewed an existing water pre-treatment process with a biological solution that meets the needs of the paper mill, thereby creating an efficient new system” says Daniele Bacchi, Head of Italprogetti’s Wastewater Treatment Dept. This is a decidedly important aspect, especially in the paper industry where the traditional processes with activated sludge with a sedimenter produce sludge flocs that are particularly lightweight and so don’t settle well. The risk of dragging the biomass along with the treated water is considerable. “In these conditions, the use of MBR technology (even in the case of running problems, dosing errors, etc.) ensures the persistence of the bacteria in the tank and therefore the recovery of the system, restoring optimum conditions in a short time and reducing the volumes in question by 2 or 3 times compared with traditional technology”. And that’s not all. The type of effluent also displayed certain distinguishing aspects: a high inlet COD, a high fraction of organic substances with poor biodegradability, and a high concentration of calcium. “These needs called for not only an MBBR system but also the adoption of other technological solutions to prevent the substantial low-biodegradable fraction from invalidating the outlet COD result and to prevent the calcium from falling onto the carriers, limiting their effectiveness”. To resolve the problem, the last of the three MBBR reactors installed in series was given over to the recycling of the activated sludge. “This meant the low-biodegradable fraction of COD could be kept under control, while the calcium level was managed by carefully monitoring the pH in the reactors and dosing a product that prevents it from falling.” The result is a system with capacity rates of 1000m3 per day, with a COD of about 4,500mg/l on the inlet and 80-100mg/l on the outlet - far below the limit value for the authorisation of discharge in surface waters (160mg/l).
The ROBUSCHI RBS range of low-pulse, tri-lobe blowers & exhausters with pressures up to 1bar & vacuum levels to -500mba Flow rates from 240m3/hr up to 10,400m3/hr.
In today’s business climate, where project budgets and schedules are under cost and time pressures (and where installed valve applications must perform reliably under increasingly severe conditions), valve simulations are enabling new capabilities.
This article describes five case studies where a vendor is providing industrial plants and facilities with an array of valve solution simulations to eliminate the need for testing.
Valve testing ensures that valves meet the requirements of an application—as far as plant personnel can estimate. However, in some cases, conditions are not exactly as predicted, and the valve may not perform as expected. In such a case, plant personnel are faced with an expensive decision: Should the valve be removed and sent back to a lab for further testing, or is another solution available?
The alternate solution is simulation. With computational fluid dynamics (CFD), a simulation engineer can develop predictive, physics-based computational models to cover a wide range of tests and situations, including valve flow coefficients, multiphase applications, turbine bypass temperature sensor optimization, and installed valve troubleshooting, among others. With CFD, a simulation engineer can input the design of the valve in question, simulate the installed conditions, identify the problem and develop a solution.
By modeling existing process conditions, CFD helps designers formulate solutions to control valve issues such
as buffeting, vibration, erosion and valve instability.
CFD simulation is already being used by most valve vendors for initial design (e.g., when engineers need to understand a valve’s expected flow performance under certain conditions). While experienced valve designers typically have a sense for how the valve and trim geometries must be shaped to provide the desired flow performance, CFD provides insights and physics-based predictions of the expected performance. Physical flow testing has historically been used to determine valve performance, but CFD simulations are now commonly used to predict flow performance during the design process of new valves, either prior to, or in lieu of, physical flow testing.
Typically, a valve designer will create a valve, use simulation to evaluate concepts and refine the design (FIG. 1), and then have a valve cast. The new valve will then be subjected to flow lab testing. If the valve performs as expected, it can go into production. If not, testing will usually point out areas requiring modification. The valve design simulation model can also be used for future testing, including CFD simulation of valves installed in the field. It is crucial to validate CFD simulations against actual test results in a flow lab, and to involve experienced analysts in the simulation to assist in ensuring the quality of results.
Simulation experts apply best practices with quantified uncertainties developed using data procured in test facilities, coupled with field experience, to provide value in ways only simulation can provide. End-user collaboration is critical for identifying the pain points and understanding where simulation can be of service.
Some simulation capabilities include:
• Fluid dynamics analysis via simulation of capacity, choking, velocities and pressure profiles
• Validation through prototypes and production unit flow tests
• Structural checks using finite element analysis (FEA)
• Validation through digital image correlation and strain gauge hydro tests
• Thermal analysis via computational model thermal profiles
• Validation through prototypes and production unit process temperature tests
• Seismic analysis to computationally predict and exaggerate structural loads
• Validation through prototypes and production unit load tests.
Traditionally, CFD has only been used as an internal resource by valve vendors, primarily for new product development and testing, and has rarely been made
available outside of a vendor’slab. However, some control valve vendors are now providing CFD simulation services to end users to help them cut costs, reduce downtime and make other operational improvements. The following are a few examples.
A major original equipment manufacturer (OEM) of power plant turbines required flow capacity Cv validation on a 32-in. high-performance butterfly control valvea (FIG. 2) installed in a critical bypass application. The traditional solution would have been to physically flow test the valve, but this was deemed unacceptable because of increased costs and negative schedule impacts.
Instead, valve simulation engineers created a CFD model of the butterfly valve to simulate the Cv, then verified to the OEM through a report that the valve would perform as expected. The simulation provided a ±7% confidence band for all flow coefficients.
By using CFD as an acceptable alternative to physical flow testing, the turbine OEM saved more than $100,000, with no delivery schedule interruption.
Thirty years ago, a refinery installed a severe-service (FIG. 3) control valveb in the non-preferred flow-up direction. The refinery was undergoing an expansion project where process conditions required a larger-capacity severeservice control valve. Refinery personnel wanted to replace the valve with another control valve due to its 30-plus yr of proven service; however, they realized that changing the piping to the preferred flow-down orientation would be too costly and would negatively impact the project schedule. The refinery wanted to keep the flow-up orientation, which led to sizing implications, since the valve sizing parameters were flow tested only in the flow-down orientation.
The service was too critical to size the valve by using the process of extrapolating valve sizing parameters to match the application. Instead, a CFD simulation was performed to predict valve flow coefficients and pressure drop ratio factors, allowing for accurate control valve sizing. The new valve was installed and is functioning as required in this severe-service application.
CFD provides value in both front-end engineering design (FEED) and post-installation situations. This CFD application not only solved a problem, but it also provided a model for this end user’s future FEED projects.
Turbine bypass is considered one of the most critical control valve applications in a power plant. Properly selected turbine bypass valves (FIG. 4) are important for keeping a turbine safe and for maintaining the overall power plant heat rate, a common measure of efficiency. In a bypass system, steam is de-superheated by creating a pressure drop, with a control valve used to add the proper amount of water to the steam. CFD was used to predict the ideal location to install temperature transmitters, specifically where the added water is fully evaporated, and where temperature readings would be most accurate. With better-understood requirements for turbine bypass valve temperature transmitter locations, downstream
straightlength piping requirements were reduced from those provided by the sizing tool. This cut installation cost and time.
An undersized actuator
A high-pressure injection pump recycle valve on an offshore platform in the North Sea was experiencing instability issues when trying to control a 3,700-psid seawater pressure drop. The solution for sizing this critical severe- service, multiphase fluid control valve was to utilize CFD to ensure that the control valve and the downstream pressure relief valve were sized correctly. For both valves, CFD simulations were used to predict valve Cv and pressure drop ratio factors, allowing for accurate sizing.
In addition, root cause analysis of an undersized actuator on the control valve was derived using both smart positioner online diagnostics and CFD simulation. This was accomplished without taking the valve apart and causing further interruptions. A new actuator was shipped and installed, solving the problem at minimal cost and disruption to existing operations.
The IEC 60534-2-1 control valve sizing standard covers most control valve applications. However, many applications fall outside its scope, such as outgassing and fluid flows composed of multiple phases.
An OEM for a refinery water treatment skid required CFD analysis on its severe-service, multiple-component fluid control valve application to ensure that the control valve was sized correctly. The OEM did not want an oversized valve because this would negatively affect the sizing of the downstream pressure relief valve. The high pressure drop and the presence of solids required a flow-down, severeservice control valve with erosion- resistant materials, including solid stellite trim with ceramic inserts, and an outlet liner extending beyond the valve outlet.
OEM process engineers provided full fluid composition data, enabling the valve simulation engineers to generate a CFD report and correctly size the control valve. Accurate CFD modeling (FIG. 5) mitigated the OEM’s risk of under- or over-sizing these final control elements—thus providing confidence to the OEM’s customer regarding the performance of due diligence for these critical skid components.
Almost anyone can acquire simulation software and create an attractive rainbow-hued image as in FIG. 1, but it takes an experienced valve designer to set boundary conditions, meshing and material properties to obtain results correlating well to testing.
This is especially the case with the specialized application of using CFD to replace valve testing, where non-expert analysts can create situations with serious consequences
with respect to design decisions. For example, with some control valve designs, seemingly trivial changes to meshing inputs can result in unexpectedly large effects on valve capacity predictions. This sensitivity to small input changes is further magnified by the selection of, and coupling with, an appropriate turbulence model for massively separated and complex recirculating flows.
The proliferation of results generated by using nonvalidated CFD methodologies can have serious consequences on design decisions, which can, consequently, more than offset expected project schedules and cost benefits.
If non-validated CFD methodologies are used early in the design cycle, the expected benefits may not be realized due to unquantified or uncharacterized deficiencies in the method. This is especially applicable to the use of CFD analysis tools, which typically automatically apply modeling and meshing choices without any user involvement or awareness.
CFD simulations can provide insight and value, but not all CFD simulations are equal. End users must be certain that the valve vendor can back up simulations with test data from a flow lab, with experienced valve designers and applications engineers available to interpret results.
When a valve vendor designs a valve by using CFD, and tests the designs in a flow lab, it produces a software model that can be used to predict or diagnose problems with installed valves. CFD simulations are not only being used in new product development, but they are also being provided by valve vendors as a service to end users, thereby saving time and money when diagnosing problems with installed valves.
Emerson Automation Solutions, +27 (0) 11 451 3700, emrsouthafrica@emerson.com, www.emerson.com
Val e man fact rer and pro iders of ater lit ser ices
Are o read to na igate the aters of fl id management ith confidence and ease? Look no f rther than the CLA-VAL Control Val e, the flagship prod ct of the reno ned CLA-VAL brand. Its e cep onal feat res, ad antages, and benefits ill re ol oni e the a o approach fl id control.
Feat res: The CLA-VAL Control Val e boasts an impressi e arra of feat res that set it apart from the compe on. From its precision-engineered press re control capabili es to its ersa le flo control and le el control f nc onali es, this al e is designed to deli er nparalleled performance. With its speciali ed design for p mp control, it ens res smooth and efficient opera ons, e en in the most demanding applica ons.
Ad antages: What sets the CLA-VAL Control Val e apart is not j st its technical pro ess, b t also the e per se of the Seapro SA technical team. With their deep nderstanding of fl id d namics and ears of e perience, the pro ide in al able s pport and g idance thro gho t o r jo rne . Addi onall , the CLA-VAL brand offers an asto nding different config ra ons, gi ing o the freedom to c stomi e the al e to perfectl match o r niq e req irements.
Benefits: B choosing the CLA-VAL Control Val e, o nlock a orld of benefits. E perience smart ater management at its finest as o achie e precise control o er flo rates, maintain op mal press re le els, and ma imi e the efficienc of o r fl id s stems. Not onl does it deli er e cep onal performance, b t it also represents e cellent al e for mone , making it a so nd in estment for o r opera ons. And as an added bon s, Seapro SA pro ides free Link Val e so� are, empo ering o ith ad anced tools for flo , press re, and asset management.
Embark on a jo rne of smooth sailing ith the CLA-VAL Control Val e b Seapro SA. With its c ng-edge feat res, technical e per se, and nmatched al e, it's me to nleash the f ll poten al of o r fl id management s stems. Get read to na igate ith confidence and efficienc like ne er before.
Debbie Henning
Internal Sales Manager
Cell: 074 425 4220
Phone: +27 11 397 1126
debbie@seaprosa.co.za
Sanele Chili a
Internal Sales
Cell: 065 862 3147
Phone: +27 11 397 1126
sanele@seaprosa.co.za
Da id Ke ser
Field Service Manager
Cell: +27 60 915 1945
Phone: +27 11 397 1126
david@seaprosa.co.za
Danie Stander
Project Manager
Cell: 082 453 1775
Phone: +27 11 397 1126
danie@seaprosa.co.za
Ig an Roo en International Sales & Marketing Manager
Cell: + Phone: + ig@seaprosa.co. a
A single al e bod can perform f nc ons sing interchangeable components. Addi onall , an al e bod can be retrofi ed to pgrade to ne er and more ad anced feat res.
South Africa is approaching a water crisis as load shedding adds undue pressure to water and wastewater treatment systems already on the verge of collapse. However, there is still hope that South Africans can work together to find solutions. This is according to water and wastewater treatment experts on the advisory board of the upcoming IFAT Africa trade fair for water, sewage, refuse and recycling in Southern Africa, which will be staged at Gallagher Estate, Johannesburg, from 5 -7 July.
Benoît Le Roy, Environmental, Technology & Project Alchemist, says a lack of cohesion between local and national government in meeting policy objectives such as the NDP 2030, NIP 2050 and 2018 Water & Sanitation Master Plan has exacerbated the problem of decades of crumbling infrastructure. He says: “If leadership is unable to steer the ship, it doesn’t matter what’s happening in the boiler room. We need a catch-up. Billions in funding is needed just to make a dent in the water asset rejuvenation that is needed. We need to put more money into the water sector. Of 1 000 or so sewage plants, 97% do not comply with their licences and are putting water resources at risk. What we are seeing is a disconnect between national and local government and a systemic collapse of our water security. If water systems fail completely, it would be the end of life as we know it.”
The Department of Water and Sanitation (DWS) 2022 Green Drop report noted that sewage spillages and failing wastewater treatment works were a cause of great concern, with many systems achieving scores below 31%. Green Drop Reporting aligns with incentive-based regulation and provides accurate data on the status of wastewater services in South Africa. No Department of Public Works (DPW) region qualified for Green Drop status
and 102 of the 115 DPW systems were identified as being in critical state.
The Blue Drop report for 2022, which assesses water services, found that while 48% of water supply systems are in the low risk category, 18% are at medium risk, 11% are at high risk and 23% are in the critical risk category. Poor water quality compliance results were highlighted as a serious concern to DWS.
South Africa, says the country’s deteriorating water treatment and supply situation is worsened by load shedding. “Long outages cause water shortages because reservoirs only have so much buffer capacity, and areas run out of capacity. Older pumps and drives aren’t made to be suddenly switched off and on as we see in unexpected outages. So, the power crisis is standing tall as a major challenge.”
“On top of that, the latest Blue Drop and Green Drop reports indicated that while there were isolated improvements, overall there is still a lack of maintenance and a deterioration and growing pollution of surface water. There is also a drastic skills shortage of water and wastewater professionals. Municipal process controllers may have the will to properly maintain plants, but they don’t have the funding,” Pretorius says.
Eric Bruggeman, CEO of the SA Capital Equipment Export Council (SACEEC), a 164-member public private partnership between the South African Department of Trade, Industry and Competition and the capital equipment and related services industries, says load shedding is a major problem, but just one of many facing manufacturers in the sector.
“Companies are battling to get parts and material in, water systems are failing, ports and harbours aren’t working and goods must be taken by road, so costs have become higher.”
Despite these challenges, Bruggeman says SACEEC members are enjoying a bumper year.
“The good news is our members that are exporting broke all records this year. China is battling – it can’t deliver, there are not enough containers, and the rand dollar/pound has gone through the roof, so many countries are finding it cheaper to buy from South Africa. Right now, South Africans are making the most of the situation.”
“South Africans are incredibly resilient. We must have some of the best entrepreneurs in the world, because they
are performing against all odds. For every piece of bad news there’s good news and major exporters are smiling at the moment. But for industry to grow and the smaller, newer businesses to survive too we also need reliable electricity, water, roads and infrastructure – and the government needs to come to the party,” he says.
Bruggeman says the infrastructure challenges, along with younger employees driving a green agenda, has seen green manufacturing starting to take off in South Africa.
“A lot of our manufacturers are looking at renewable power, more efficient water usage, greener materials, and lower emissions. They are using more technologies to become more efficient and greener,” he says.
Le Roy believes South Africa has to reindustrialise its water sector to be able to re-establish itself as a regional and continental powerhouse in the water sector.
He also sees opportunities for water reuse, desalination and digitalisation to improve water security.
Pretorius agrees: “For South Africa, desalination offers an important opportunity to mitigate water scarcity. Network management, reducing water loss, management of sewer networks and pump stations will also improve the situation, as will aligning with global trends such as water resource management, surface water monitoring, and
digitalisation of information and making it available from a central point.” IFAT Africa will be co-located with analytica Lab Africa – the only South African trade fair for laboratory technology, analysis, biotechnology and diagnostics.
The co-location brings together the broad and integrated spectrum of science and innovation, laboratory technology, water treatment, waste management and recycling for one-stop access to the interconnected value chains in these sectors.
The market response to co-locating the event with IFAT Africa has been resoundingly positive, with visitors and exhibitors from across Africa and around the world exploring multi-sectoral business opportunities.
IFAT Africa offer access to thousands of industry decision makers from across the African continent and the world. The supporting programme of presentations and workshops will be designed to bring together government, academia, scientists and business to engage, explore solutions and drive the pace of change. Registration to visit the exhibition is open.
www.flsmidth.com
Paltech, the leading South African original equipment manufacturer (OEM) for valves and pumps, is delighted to announce its strategic distribution partnership with Schneider Electric Global, a renowned French multinational company specialising in digital automation and energy management across various sectors.
Effective from 1st May 2022, Paltech has become the sole OEM official distributor of Schneider automation instrumentation in the entire Sub Saharan African region. Paltech's distinction as the only OEM among the four partners demonstrates its commitment to providing exceptional quality and service to its customers. This groundbreaking partnership extends beyond our South African operations to include Paltech's sister companies, Paltech Ghana and Mwendo Engineering based in Mozambique.
Schneider's state-of-the-art automation instrumentation will enable Paltech to integrate automation capabilities into select valves, such as the highly acclaimed Pal-T. By leveraging Schneider's innovative products and instrumentation, Paltech will further enhance its offerings, providing cutting-edge solutions to its clients in South Africa and beyond. As part of this distribution
partnership, Paltech will stock and offer a range of select Schneider products and instrumentation, ensuring customers have access to a comprehensive portfolio of world-class solutions for their automation and energy management needs.
The official launch of the Paltech-Schneider distribution partnership is scheduled for 25th May 2023, at 42 Steel Rd. This milestone event will bring together industry leaders, customers, and stakeholders to celebrate the union of two industry powerhouses and the vast potential it holds for the future.
Paltech, +27 (0) 12 653 1156, sales@paltech.co.za, www.paltech.co.za
Moving industrial fluids from one point to another is essential to the health of the worldwide economy. There are a variety of methods to transfer these fluids, with the most common being by truck and rail. The process of loading and unloading tank trucks and railcars occurs daily thousands of times at industrial sites across the world.
While this is a routine procedure, it also comes with safety and cost challenges. On the safety side, the primary risks associated with fluid transfer include leakage and spillage, both of which can create catastrophic consequences. Hazards from leaks and spills range from widespread pollution to fires.
Regarding expenses, spills and leaks lead to a loss of product. When you consider the frequency of fluid transfers across the world, a small spill or leak during each of those interactions creates substantial product loss, all of which impacts the bottom line to the tune of millions of dollars. Additionally, if leaks or spills occur, then maintenance also becomes an immediate necessity on the pumping equipment, which adds to those costs. Another costly problem comes from shearing when using a nonadapted pumping technology.
Complicating fluid transfer is the fluid itself. Each liquid brings its share of unique challenges when it comes to loading and unloading. In the chart above, are a few examples of liquids that are transported by road or rail. If there is at least one “yes” in the product line, an adapted
pumping technology must be used for loading and unloading applications.
Hazards
Leaks from pumping equipment typically come from the mechanical seal. A truck uses an unloading pump intermittently, meaning that its intervals are not continuous or steady. Those circumstances can prove problematic for products that dry or polymerize when static, especially when a mechanical seal has a leak. Those products will leak rapidly from the compromised seal.
Spillage is nearly impossible to avoid. During those thousands of routine transfers, the hose between the truck tank and the pump must be disconnected. Regardless of the liquid, there will always be some left inside the disconnected segments. This requires recovery protocols and protective measures for staff.
Costs issues
Outside of the high expenses that come from safety issues, the main costs associated with loading and unloading pumps are maintenance, downtime and product loss.
Regarding maintenance, it’s almost inevitable that a mechanical seal will eventually leak. Complications arise even further when considering some applications feature pumps that run continuously, such as with isocyanates. These low-molecular weight chemicals cannot be left in a static state. When they are not moving during loading and unloading functions, they are kept active through continuously running pumps.
Under this scenario, a failed mechanical seal will cause a serious leak, resulting in severe costs, including lost product, maintenance on the seal, product cleanup and halted production. All of these costs accumulate to create an unnecessary and harmful financial burden.
Downtime results from these complications. If liquids cannot be transferred, it amounts to lost time on both ends and also affects the downstream process. The longer the downtime, the more detrimental the costs.
Product loss affects costs because of the expensive nature of the transferred liquids. Whether through a major spill or a slow mechanical seal leak, any product loss will impact expenses. Over time, those expenses become more pronounced and harmful. Additionally, the loss of the product isn’t the only issue. That lost product, especially during spills, needs to be cleaned up, which raises costs.
Mouvex eccentric disc pumps can mitigate all of the challenges that come from liquid transfers. This technology consists of a cylinder and pumping element mounted on an eccentric shaft. As the shaft rotates, the pumping element forms chambers within the cylinder. This increases the size of the cylinder at the intake port and draws fluid into the pumping chamber. The fluid moves to the discharge port, where the pumping chamber size decreases, squeezing out the fluid.
During loading and unloading, this unique design provides the following:
• Line stripping that leaves a minimum amount of product inside the hoses on the suction and discharge sides after transfer, which ensures cleaner and safer operation and reduces the opportunity for product spillage.
This is crucial, especially when transferring a dangerous chemical.
• Self-priming from underground tanks. This is necessary to start the pump and creates a strong vacuum to lift the liquid.
• No mechanical seal, which ensures no maintenance and no leaks, and thus no downtime.
• Limited regular maintenance. The only maintenance needed is a transmission oil change every 24,000 hours, which equates to every 2.7 years. This is for a pump that runs continuously year-round.
• Constant flow rate vs. variable viscosity – Loading and unloading applications are generally located outside with significant ambient temperature variations between winter and summer.
• Constant flow rate vs. variable pressure – When filling a tank from the bottom, the discharge pressure will increase while the level rises.
• Low shear on fragile products.
• Can run dry for up to five minutes even in ATEX zones.
• Up to 300 gpm (70 m3/h).
Mouvex seal-less eccentric pumps have proven their performances and reliability on many loading and unloading applications. A few of those examples include:
Truck loading of polymers emulsions. G-Flo 50 pump.
Problem solved: Seal leakage
Bonus: Product recovery inside the hose
Truck unloading of cream.
SLS36 pump.
Problem solved: Liquid shear
Bonus: Product recovery inside the hose
Truck unloading of fruit concentrate.
SLS36 pump.
Problem solved: Product losses
Truck unloading of Polyethylene glycol.
SLC36 pump
Problem solved: liquid spillage after transfer
Mouvex, paul.cardon@psgdover.com, www.psgdover.com/mouvex
Industrial and mining operations are under increased financial pressure in the current economic and social climate in South Africa. Which means that when businesses make capital investments in new equipment, they need to be sure that the machinery will function optimally for as long as possible.
One of the key ways to ensure this happens is to use the right lubrication and aftermarket reliability solutions. Aftermarket reliability solutions, such as oil level monitors, vibration sensors and breathers, can have a major impact on the lifespan of equipment.
In hard-to-reach or hard-to-see places such as inside gearboxes, problems often arise because the lack of consistent monitoring of what is happening inside the apparatus means that oil levels get too low, seals get
damaged because of the resultant pressure build up, and then the entire gearbox is at risk of failing. Gary Wentzel, Senior Technical Consultant at Lubrication Engineers (LE) South Africa, has seen first-hand how using oil level monitors and breathers can save on maintenance and repair costs.
At a plaster and plasterboard manufacturing client’s company, the addition of sight glasses and oil level monitors in gearboxes has saved hundreds of thousands of rands and had a marked impact on maintenance downtime for the gearboxes.
“Aftermarket reliability solutions have saved on the repairs of the client’s gearboxes because correct lubrication management has stopped leaks happening via the gearbox seals (which are the weakest point). Giving the maintenance engineers visibility has been massive. Many of the gearboxes were previously run to fail and then had to be replaced. At around R35 000 to replace a small gearbox and up to R160 000 for larger ones, this is a big saving. The gearboxes where we used these aftermarket reliability solutions and our Almatek® General Purpose Lubricant have now been running for three years without breakdowns,” says Wentzel.
The Almatek® General Purpose Lubricant can be used in multiple applications, which is useful for plants that have different types of equipment components in use.
The grease has been specifically designed to be tacky and it clings well to metal in elements such as bearings.
Importantly, as in the case of LE’s client’s gearboxes, it is formulated for extended use and reduces maintenance costs by letting equipment run cooler, with less frictional wear.
Maintenance teams are often required to manage large workloads and to monitor many different moving parts in a business’ operations.
Using long-lasting lubrication products is key to help them extend equipment lifespans, but tools that improve their visibility and reduce machine failures (and the resultant repairs) increase their capacity and ability to balance the maintenance needs across a plant.
Lubrication Engineers, +27 (0) 11 464 1735, gavin@lubricationengineers.co.za, www.lubricationengineers.co.za
PUMPS FOUNDRY
Ukuthela Foundry Projects
T: +27 (0) 12 719 8860
E: ukuthela@live.co.za
AIR OPERATED DOUBLE DIAPHRAGM PUMPS
Air & Vacuum Technologies
T: +27 (0) 11 318 3241/2/3/4
C: +27 (0) 82 576 9373
E: burnm@vactech.co.za
W: www.vactech.co.za
Monitor Engineering (Pty) Ltd
T: +27 (0) 11 618 3860
E: info@monitorpumps.co.za
W: www.monitorpumps.co.za
BOREHOLE PUMPS
Ernest Electro Engineering
T: +27 (0) 11 792 9550
E: eeeaman@mweb.co.za
W: www.ernestee.co.za
Stewarts & Lloyds (Pty) Ltd
T: +27 (0) 11 917 0778
F: +27 (0) 11 917 0769
E: peterk@sltrading.co.za
W: www.stewartsandlloyds.co.za
CENTRIFUGAL PUMPS
Atlas Copco
T: +27 (0) 11 821 9854
E: david.stanford@atlascopco.com
W: www.atlascopco.com
Sulzer Pumps (South Africa) (Pty) Ltd
T: +27 (0) 11 820 6000
F: +27 (0) 11 820 6206
E: CSSEnquiries@sulzer.com
W: www.sulzer.com
DEWATERING PUMPS
Sulzer Pumps (South Africa) (Pty) Ltd
T: +27 (0) 11 820 6000
F: +27 (0) 11 820 6206
E: CSSEnquiries@sulzer.com
W: www.sulzer.com
KSB (Pty) Ltd
T: +27 (0) 11 876 5600
F: +27 (0) 11 822 2013
E: info-za@ksb.com
W: www.ksb.com
END SUCTION PUMPS
Aquaplex Pumps
T: +27 (0) 76 476 4084
E: gavin@aquaplexpumps.co.za
FIRE PUMPS
C.R.I Pumps S.A. (Pty) Ltd
T: +27 (0) 11 805 8631
F: +27 (0) 11 805 8630
E: cri-za@crifluidsystems.com
W: www.cripumps.co.za
HIGH PRESSURE PUMPS
KSB (Pty) Ltd
T: +27 (0) 11 876 5600
F: +27 (0) 11 822 2013
E: info-za@ksb.com
W: www.ksb.com
Hawk High Pressure Pumps
T: +27 (0) 31 274 8555
T: +27 (0) 11 822 4039
E: sales@hawkpumps.co.za
W: www.hawkpumps.co.za
HORIZONTAL SPLIT CASE PUMPS
AESPUMP SA
T: +27 (0) 17 631 1003
F: +27 (0) 17 631 1002
E: craigg@aespump.co.za
W: www.aespump.co.za
Integrated Pump Rental
T: +27 (0) 11 894 2906
E: admin@pumprental.co.za
W: www.pumprental.co.za
APE Pumps
T: +27 (0) 11 824 4810
F: +27 (0) 11 824 2770
E: info@apepumps.co.za
W: www.apepumps.co.za
KSB (Pty) Ltd
T: +27 (0) 11 876 5600
F: +27 (0) 11 822 2013
E: info-za@ksb.com
W: www.ksb.com
KSB (Pty) Ltd
T: +27 (0) 11 876 5600
F: +27 (0) 11 822-2013
E: info-za@ksb.com
W: www.ksb.com
Integrated Pump Rental
T: +27 (0) 11 894 2906
E: admin@pumprental.co.za
W: www.pumprental.co.za
KSB (Pty) Ltd
T: +27 (0) 11 876 5600
F: +27 (0) 11 822 2013
E: info-za@ksb.com
W: www.ksb.com
SAM Engineering
T: +27 (0) 11 823 4250
F: +27 (0) 11 823 4943
E: sales@sameng.co.za
W: www.sameng.co.za
Sulzer Pumps (South Africa)
(Pty) Ltd
T: +27 (0) 11 820 6000
F: +27 (0) 11 820 6206
E: CSSEnquiries@sulzer.com
W: www.sulzer.com
MAGNETIC PUMPS
AESPUMP SA
T: +27 (0) 17 631 1003
F: +27 (0) 17 631 1002
E: craigg@aespump.co.za
W: www.aespump.co.za
MULTISTAGE PUMPS
KSB (Pty) Ltd
T: +27 (0) 11 876 5600
F: +27 (0) 11 822 2013
E: info-za@ksb.com
W: www.ksb.com
C.R.I Pumps S.A. (Pty) Ltd
T: +27 (0) 11 805 8631
F: +27 (0) 11 805 8630
E: cri-za@crifluidsystems.com
W: www.cripumps.co.za
SAM Engineering
T: +27 (0) 11 823 4250
F: +27 (0) 11 823 4943
E: sales@sameng.co.za
W: www.sameng.co.za
Monitor Engineering (Pty) Ltd
T: +27 (0) 11 618 3860
E: info@monitorpumps.co.za
W: www.monitorpumps.co.za
Ltd
T: +27 (0) 11 820 6000
F: +27 (0) 11 820 6206
E: CSSEnquiries@sulzer.com
W: www.sulzer.com
SELF PRIMING PUMPS
C.R.I Pumps S.A. (Pty) Ltd
T: +27 (0) 11 805 8631
F: +27 (0) 11 805 8630
E: cri-za@crifluidsystems.com
W: www.cripumps.co.za
Integrated Pump Rental
KSB (Pty) Ltd
T: +27 (0) 11 876 5600
F: +27 (0) 11 822 2013
E: info-za@ksb.com
W: www.ksb.com
VACUUM PUMPS
Umulig Engineering
T: +27 (0) 31 942 0489
E: info@umulig.co.za
W: www.umulig.co.za
PISTON PUMPS
Hawk High Pressure Pumps
T: +27 (0) 31 274 8555
T: +27 (0) 11 822 4039
E: sales@hawkpumps.co.za
W: www.hawkpumps.co.za
PLUNGER PUMPS
Hawk High Pressure Pumps
T: +27 (0) 31 274 8555
T: +27 (0) 11 822 4039
E: sales@hawkpumps.co.za
W: www.hawkpumps.co.za
POSITIVE DISPLACEMENT PUMPS
Monitor Engineering (Pty) Ltd
T: +27 (0) 11 618 3860
E: info@monitorpumps.co.za
W: www.monitorpumps.co.za
T: +27 (0) 11 894 2906
E: admin@pumprental.co.za
W: www.pumprental.co.za
SLURRY PUMPS
Africa Slurry Pump Solutions
T: +27 (0) 79 402 3662
E: pierre@africasps.com
W: www.AfricaSPS.com
KSB (Pty) Ltd
T: +27 (0) 11 876 5600
F: +27 (0) 11 822 2013
E: info-za@ksb.com
W: www.ksb.com
SUBMERSIBLE PUMPS
Africa Slurry Pump Solutions
T: +27 (0) 79 402 3662
E: pierre@africasps.com
W: www.AfricaSPS.com
Air & Vacuum Technologies
T: +27 (0)11 318 3241/2/3/4
C: +27 (0)82 576 9373
E: burnm@vactech.co.za
W: www.vactech.co.za
VERTICAL SPINDLE PUMPS
Walter Meano Engineering
VersaFlo VSE Pumps
T: +27 (0) 11 873 8620
F: +27 (0) 11 825 1401
E: wme@mweb.co.za
W: www.versaflo.co.za
VERTICAL TURBINE PUMPS
KSB (Pty) Ltd
T: +27 (0) 11 876 5600
F: +27 (0) 11 822 2013
E: info-za@ksb.com
W: www.ksb.com
Busch Vacuum Solutions Africa
T: +27 (0) 11 856 0650
C: +27 (0) 63 686 0869
E: reeza.hoosen@busch.co.za
W: www.buschvacuum.com
Sulzer Pumps (South Africa) (Pty) Ltd
T: +27 (0) 11 820 6000
F: +27 (0) 11 820 6206
E: CSSEnquiries@sulzer.com
W: www.sulzer.com
WASTEWATER PUMPS
Unique Engineering
T: +27 (0) 11 826 6111
F: +27 (0) 11 826 6162
E: sales@uniqueeng.co.za
W: www.uniqueeng.co.za
Aquaplex Pumps
T: +27 (0) 76 476 4084
E: gavin@aquaplexpumps.co.za
Integrated Pump Technology
T: +27 (0) 11 824 4810
E: info@pumptechnology.co.za
W: www.pumptechnology.co.za
Pipes, Pumps and Valves Africa - May/Jun 2023
Integrated Pump Technology
T: +27 (0) 11 824 4810
E: info@pumptechnology.co.za
W: www.pumptechnology.co.za
Africa Slurry Pump Solutions
T: +27 (0) 79 402 3662
E: pierre@africasps.com
W: www.AfricaSPS.com
VAC-CENT SERVICES (PTY) LTD
T: +27 (0) 11 827 1536
F: +27 (0) 11 824 3590
E: info@vaccent.co.za
W: www.vaccent.co.za
VERTICAL SUMP PUMPS
KSB (Pty) Ltd
T: +27 (0) 11 876 5600
F: +27 (0) 11 822 2013
E: info-za@ksb.com
W: www.ksb.com
KSB (Pty) Ltd
T: +27 (0) 11 876 5600
F: +27 (0) 11 822 2013
E: info-za@ksb.com
W: www.ksb.com
WELL PUMPS
KSB (Pty) Ltd
T: +27 (0) 11 876 5600
F: +27 (0) 11 822 2013
E: info-za@ksb.com
W: www.ksb.com
BALL VALVES
Pleix-Quip
T: +27 (0) 11 736 4994
C: +27 (0) 83 461 0801
E: tiaans@pleixquip.co.za
W: www.pleixquip.co.za
BUTTERFLY VALVES
Ainsworth Valves
T: +27 (0) 10 020 8388
E: sales@ainsworthvalves.com
W: www.ainsworthvalves.com
CHECK VALVES
Ainsworth Valves
T: +27 (0) 10 020 8388
E: sales@ainsworthvalves.com
W: www.ainsworthvalves.com
Hydromine
T: +27 (0) 11 608 4292
E: sales@hydromine.biz
W: www.hydromine.biz
Invincible Valves (Pty) Ltd
T: +27 (0) 11 822 1777
F: +27 (0) 11 822 3666
E: enquiries@invalve.co.za
Asahi Africa
Boksburg Branch:
T: +27 (0) 11 397 4353
F: +27 (0) 11 397 4368
E: info@asahi-africa.com
W: www.asahi-africa.com
Asahi Africa
Durban Branch:
T: +27 (0) 31 563 3923
F: +27 (0) 31 563 3929
E: joshua@asahi-africa.com
W: www.asahi-africa.com
Bray Controls Africa
T: +27 (0) 10 007 3222
E: sales@bray.com
W: www.bray.com
W: www.invalve.co.za
Macsteel Fluid Control
T: +27 (0) 82 495 2772
C: +27 (0) 11 383 4000
E: Rowan.Blomquist@macfluid.co.za
W: www.macsteel.co.za
Pleix-Quip
T: +27 (0) 11 736 4994
C: +27 (0) 83 461 0801
E: tiaans@pleixquip.co.za
W: www.pleixquip.co.za
Enserve Engineering Services
(Pty) Ltd
T: +27(0) 16 971 3385
F: +27(0) 16 971 3935
E: mail@enserve.co.za
W: www.enserveonline.com
Hydromine
T: +27 (0) 11 608 4292
E: sales@hydromine.biz
W: www.hydromine.biz
Seapro SA
T: +27 (0) 11 397 1126
T: +27 (0) 10 109 2703
E: info@seaprosa.co.za
W: www.seaprosa.co.za
DIAPHRAGM VALVES
Invincible Valves (Pty) Ltd
T: +27 (0) 11 822 1777
F: +27 (0) 11 822 3666
E: enquiries@invalve.co.za
W: www.invalve.co.za
KSB (Pty) Ltd
T: +27 (0) 11 876 5600
F: +27 (0) 11 822 2013
E: info-za@ksb.com
W: www.ksb.com
Hydromine
+27 11 616 1111
KSB (Pty) Ltd
T: +27 (0) 11 876 5600
F: +27 (0) 11 822 2013
E: info-za@ksb.com
W: www.ksb.com
KV Controls (Pty) Ltd
T: +27 (0) 16 100 4592
E: fred@kvcontrols.co.za
W: www.kvcontrols.co.za
Seapro SA
T: +27 (0) 11 397 1126
T: +27 (0) 10 109 2703
E: info@seaprosa.co.za
W: www.seaprosa.co.za
CONTROL VALVES
Bray Controls Africa
T: +27 (0) 10 007 3222
E: sales@bray.com
W: www.bray.com
Asahi Africa
Boksburg Branch:
T: +27 (0) 11 397 4353
F: +27 (0) 11 397 4368
(PTY) LTD
E: info@asahi-africa.com
W: www.asahi-africa.com
Asahi Africa
Durban Branch:
T: +27 (0) 31 563 3923
F: +27 (0) 31 563 3929
E: joshua@asahi-africa.com
W: www.asahi-africa.com
T: +27 (0) 11 608 4292
E: sales@hydromine.biz
W: www.hydromine.biz
Seapro SA
T: +27 (0) 11 397 1126
T: +27 (0) 10 109 2703
E: info@seaprosa.co.za
W: www.seaprosa.co.za
VACSERVE (PTY) LTD
T: +27 (0) 11 827 1536
F: +27 (0) 11 827 3590
E: info@vacserve.co.za
W: www.vacserve.co.za
Ainsworth Valves
T: +27 (0) 10 020 8388
E: sales@ainsworthvalves.com
W: www.ainsworthvalves.com
Invincible Valves (Pty) Ltd
T: +27 (0) 11 822 1777
F: +27 (0) 11 822 3666
E: enquiries@invalve.co.za
W: www.invalve.co.za
Valcon Valve & Controls
T: +27 (0) 11 453 7537
E: valconsa@iafrica.com
W: www.valcon.co.za
KNIFE GATE VALVES
C.R.I Pumps S.A. (Pty) Ltd
T: +27 (0) 11 805 8631
F: +27 (0) 11 805 8630
E: cri-za@crifluidsystems.com
W: www.cripumps.co.za
Mine Track & Tools (Pty) Ltd
T: +27 (0) 11 412 4536/1665
E: info@minetrack.co.za
W: www.minetrack.co.za
PRESSURE REDUCING VALVES
CALAFRICA Hydronic Solutions
T: +27 (0) 11 795 1519
C: +27 (0) 83 303 1437
E: technical@calafrica.co.za
W: www.calafrica.co.za
Hydromine
T: +27 (0) 11 608 4292
E: sales@hydromine.biz
W: www.hydromine.biz
VACSERVE (PTY) LTD
T: +27 (0) 11 827 1536
F: +27 (0) 11 827 3590
E: info@vacserve.co.za
W: www.vacserve.co.za
VALVE RECONDITIONING
Enserve Engineering Services (Pty) Ltd
T: +27(0) 16 971 3385
F: +27(0) 16 971 3935
E: mail@enserve.co.za
W: www.enserveonline.com
Mine Track & Tools (Pty) Ltd
T: +27 (0) 11 412 4536/1665
E: info@minetrack.co.za
W: www.minetrack.co.za
Seapro SA
T: +27 (0) 11 397 1126
T: +27 (0) 10 109 2703
E: info@seaprosa.co.za
W: www.seaprosa.co.za
VALVES FOUNDRY
KEW Foundries
T: +27 (0) 53 841 0474
F: +27 (0) 53 841 0473
E: info@kewfoundries.co.za
W: www.kewfoundries.co.za
Ukuthela Foundry Projects
T: +27 (0) 12 719 8860
Seapro SA
T: +27 (0) 11 397 1126
T: +27 (0) 10 109 2703
E: info@seaprosa.co.za
W: www.seaprosa.co.za
E: ukuthela@live.co.za
Compact Design
Extended Pressure Ratings
Conical Design
One Moving Part
Variable Port Design
Patented Gas Scavenging
Improved Cone Angle
2 Year Warranty
Less Floor Space Required
Flexibility & Easy Maintenance
Ability to handle applications where Backpressure is required
Ability to handle water /partculate sluge/
residuel Gas Compression
Trouble free Start-Up & Operation
Extended Scope of Application
Performance at High Vacuum Levels
Long Term Reliability
Peace of Mind
NASH Vectra XL vacuum pumps and compressors are created to meet exacting performance and design standards. They combine the highest standard of reliability with a new level of ingenuity.
Gardner Denver Nash employs advanced design technologies to achieve optimum performance and unprecedented production efficiencies.
• Market leader in vacuum and overpressure
• Robust technology – built to last
• Most extensive experience in the market