P RT F L
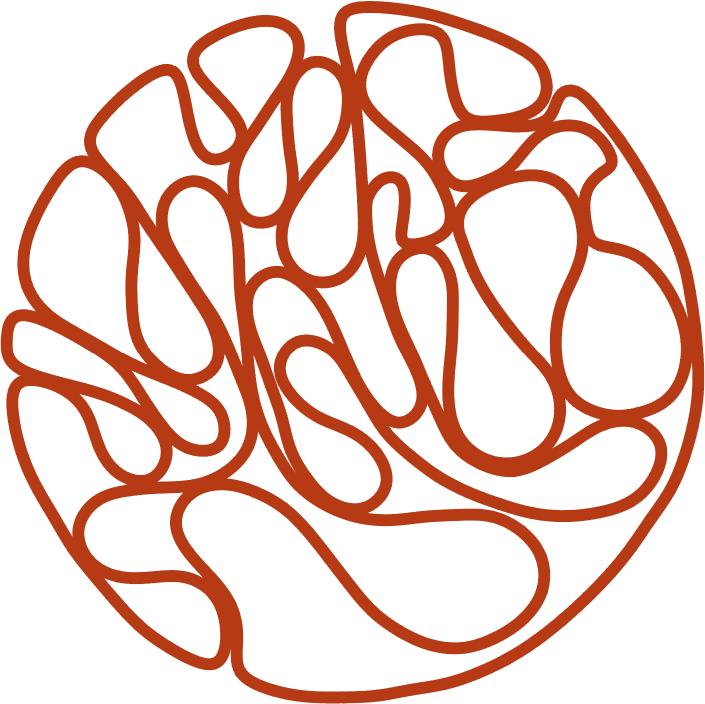




AutoCAD
Rhinoceros+V-Ray
Grasshopper
Adobe InDesign
Adobe Photoshop
Adobe Illustrator
Adobe Premiere
Italian (native speaker)
English C1 (IELTS 7.0)
Spanish (basic)
Chinese (basic)
HOBBIES & INTERESTS
3D printing
Wood work
Hand drawing
Robotics
2020-2023
South East University, Nanjing, China
2019-2023
Politecnico di Milano, Milan, Italy
2021-2022
IaaC - 3DPA, Barcelona, Spain
2018
Bauclassroom, Treviso, Italy
2015-2018
IUAV University, Venice, Italy
2010-2015
High school, Conegliano, Italy
Master degree at South East University, Nanjing
Master degree at Politecnico di Milano, Milan - 110 cum Laude
Postgraduate program in 3D Printing Architecture at IaaC
Architectural Visualization Workshop
Bachelor’s degree at IUAV, Venice - 110/110
High school degree at Liceo scientifico G. Marconi
2023-on going
D+R archittettura, Conegliano, Italy
2022
IaaC, Barcelona, Spain
2020
DesignMorphine, Barcelona, Spain
2019
D+R archittettura, Conegliano, Italy
2018-2019
Studio RAP, Rotterdam, Netherlands
2018
APA Studio, London, UK
Architect at D+R architettura - current occupation
Internship at IaaC - six months traineeship
Robotic Inform workshop with DesignMorphine - three days workshop
Internship at D+R architettura - six months traineeship
Internship at Studio RAP - four months traineeship
Internship at Ashton Porter architects - four months traineeship
arch. Leonardo BinIndividual project Design Morphine workshop 2020
Team project YAC competition 2021
Master thesis project
Individual project
PoliMi, IaaC and Southeast university
2022-2023
Designer(s):
Leonardo Bin
Supervisors:
prof. Valentina Sumini (PoliMi)
prof. Bao Li (Southeast University)
My thesis project arises from the combination of a deep attraction towards Chinese vernacular architecture and a personal interest in the world of 3D printing in architecture.
The result is the reinterpretation of a typical Chinese vernacular building, the Tulou, through the use of a new technology: earth 3D printing. In addition to this, aiming to add a further challenge to the project, a delicate social issue that has been afflicting Chinese society for several years, the plague of left-behind children, was addressed. The new Tulou proposed by this project, in addition to revolutionising its ancient reference both in formal, spatial and dimensional terms, will also have a new function. From a macro-house designed to host and protect entire villages, it will become a co-living space thought to host the left-behind children of rural Chinese villages and the elderly who will be able to take care of them in a healthy and safe place.
The Fujian Tulous are traditional vernacular architectures built in southern Fujian province between XIII and XX century. The etymology of the word (Tù «earth» and Lóu «multi-storey house»), gives us a hint about what essentially a Tulou is. With the term “Tulou”, indeed we can typically refer to collective dwellings built with rammed earth and wood.
Although the mass urbanization of the last 30 years has progressively pushed people towards major urban centres, emptying the small rural villages spread in the Chinese countryside, more than 3000 Tulous have nevertheless survived and, exactly as in the past centuries, many people still live and work inside them. The main victims of this phenomenon are children, who are very often left behind by their own parents, forced to seek better fortune in the city but unable to take their children with them for economic reasons.
LEGEND:
01. Earth 3D printed wall
02. Light mortar 10mm
03. Brick support base 20mm
04. Stone foundation footing
05. Water barrier 2mm
06. Polystyrene panel
07. Lean concrete sub-foundation 150mm
08. Terrain
10. Draining gravel
11. Bed of sand 20mm
12. Rough cut stone tiles
13. Wood profile 110x50mm
14. Wooden flooring slats 16x100mm
15. Double OSB panel 12+12mm
16. Cork thermo-acoustic insulation 110mm
17. Lightweight concrete screed 50mm
18. Concrete substrate with welded mesh 120mm
19. Crawl space with Igloo 450x450mm
20. Lean concrete base 100mm
21. Wood profile 100x50mm
22. Wood profile 150x50mm
23. Wooden finishing slats 12x100mm
24. Plaster ceiling finishing 15mm
25. Wood profile 20x20mm
26. Tiny OSB panel 12mm
27. Roof wooden truss 150x150mm
28. OSB board 12mm
29. Wood profile 100x100mm
30. Sewage plants
31. Wood profile 220x60mm
32. Wood pillar 200x150mm
33. Steel hot-rolled L profile 140x140mm
34. Secondary wood beam 200x100mm
35. Primary wood beam 300x150mm
36. Wooden tablet hosting the primary beam 40mm
37. Steel hot-rolled T profile 100x100mm
38. Wooden ceiling slats 24x150mm
39. Steel hot-rolled T profile 130x130mm
40. Wooden beam supporting the stair step 150x150mm
41. Wooden secondary beam of the stair step 50x50mm
42. Step’s wooden slats 30x100mm
43. Steel hot-rolled L profile 80x80mm
44. Steel plate connecting the primary beams 300x250mm
45. Rain water drainage channel 250x220mm
46. Concrete substrate 260mm
47. Terrain holder element
48. Courtyard terrain
49. Double glass panel 10+10mm
50. Fixing dowel with stud
PROTOTYPE A_01: FLAT OPENING PROTOTYPE A_02: BENT OPENING
The deformation of the wall happens whitin the wall axis, generating a ‘‘curtain shaped’’ opening.
Printer used: ABB IRB 1100
Scale of the prototype: 1:10
Print time: about 6.00h
Here the wall deforms iteself ouside its axis, bending over it towards the inside or the axis and orienting the opening as needed.
Printer used: ABB IRB 1100
Scale of the prototype: 1:20
Print time: about 4.00h
The openings of this prototipe are generated by a gradual transition from a certain orientation of the wall (rotated) to another (alligned).
Printer used: ABB IRB 1100
Scale of the prototype: 1:20
Print time: about 4.00h
This prototype is the terminal portion of the wall of the building used to support the roof trusses. It deforms and opens both inwards and outwards to support the truss elements.
Printer used: KUKA KR 470-2 PA
Scale of the prototype: 1:2
Print time: about 3.5h
IaaC 3DPA program Team project (realized)
IaaC 2022
Designer(s):
Adel Alatassi, Aslinur Taskin, Charles Musyoki, Deena El-Mahdy, Eugene Marais, Hendrik Benz, Juliana Rodriguez Torres, Leonardo Bin, Mariam Arwa, Al-Hachami, Marwa Abdelrahim, Mehdi Harrak, Michelle Bezik, Michelle Antonietta Isoldi Campinho, Mouad Laalou, Nareh, Khaloian Sarnaghi, Nawaal Saksouk, Orestis Pavlidis and Seni Boni Dara.
Supervisors:
TOVA 3D is the first building made with earth and a 3D printer in Spain, a project born from the ongoing research conducted by IAAC Postgraduate program 3DPA to find new ways of facing the social and environmental challenges of the future through advanced construction technologies, such as 3D printing, sustainable materials and computational design.
www.xelplus.com
Edouard Cabay, Alexandre Dubor, Ashkan Foroughi, Eduardo Chamorro Martin, Francesco Polvi, Bruno Ganem Coutinho, Marielena Papandreou and David Skaroupka.
https://shorturl.at/gBJP2 Tulou3D video
https://www.youtube.com/watch?v=17K4KwTJtC8&t=2s Tova video
The construction has been carried out at the Valldaura Labs facilities, on the outskirts of Barcelona. It is a prototype that represents the bridge between the past — vernacular earthen architecture — and the future — large scale 3D printing technology — which will not only serve to change the architecture of the future, but will also be very useful when facing the current climate and housing crisis across the globe. It is the first building of this type in Spain and stands out for being one of the most sustainable and environmentally friendly construction forms that can be applied today.
https://iaac.net/project/3dpa-prototype-2022/ Tova article https://www.youtube.com/watch?v=DitE_e3VDMk
The design of the building takes into account the climatic conditions of the Mediterranean: the volume is compact to protect from the cold in winter, but expandable during the other three seasons of the year, allowing the use of the immediate outdoor surroundings. The walls are made up of a network of cavities that contain airflow and allow great insulation to prevent heat loss in winter and protect from solar radiation in summer.
It is a near-zero emissions project: its shell and the use of an entirely local material allow the reduction of waste, making it a pioneering example of low-carbon building, given that current construction methods are responsible for 36 % of CO2 emissions.
The possible applications of this construction model are endless; from homes, to public spaces, interiors and exteriors. In combination with other construction systems, it can accommodate complex and innovative buildings that would reduce the environmental impact that construction currently entails.
The 3D printer used for the construction of the prototype, the Crane WASP, is a modular system made of three steel trusses (expandible) joint together on the top. One of the axis bears the extruder, a horizontal arm with a maximum radius of 3 meters.
DRY MIX: WET MIX:
EARTH - 85%
CLAY - 15%
FIBERS - 0.1%
The main material used for the construction of the prototype is local earth, which was sourced within a 50 meter radius from the site. The earth was therefore sifted using a a rolling machine able to remove all the impurities such as stones and branches.
WATER - 16%
ENZIMES - 0.03%
Once the material is ready, it is pushed to the extruder through the WASP pump and therefore 3D printed. The average production was within 10-12 layers per day, with a layer height of 2 cm, making it possible to complete the print in about four weeks.
With the walls fully printed and sufficiently dried, the external the surface has been made waterproof using a coating mado of raw extracted materials such as aloe and egg whites, in order to protect the building from the rain water.
The finishing works include: the ceiling realization, the insulation of the building, the wooden wall of the Eastern faced (fabricated on site), the electrical system of the lighting and the floor realization, made of a mixture of earth, sand, water and straw.
The wood structure of the roof is totally integrated in the 3D printed wall, which means that the loads of the roof are transfered by the structure to the structural earthen walls. The structure, fabricated on site, could be assembled only once the walls were dry.
PLYWOOD ROOF
WOODEN TRUSS KEY
PLYWOOD CEILING FOLDAWAY
LOAD BEARING WEST WALL
3D PRINTED LIGHT-FILTRATION SOUTH WALL
PRINTING PROCESS LAYERS PER DAY
VENTILATION SYSTEM
ENTRY FACADE
3D PRINTED EAST WALL
ROOF TRUSS-WALL DETAIL
3D PRINTED VENTILATION CAVITY
PRINTING RADIUS: 3m
GABION FOUNDATION
GEOPOLYMER BEAM
FLOOR SYSTEM
CASTED GEOPOLYMERS FOUNDATION BASE
GEOPOLYMERS SUBSTRATE
Design Morphine workshop
Individual project
Design Morphine
2020
Designer(s):
Leonardo Bin
Supervisors:
Kunaljit Chadha, Eduardo
Chamorro Martin
In recent times industrial robots have been adapted to the architectural world and the design environment in now open to completely new possibilities, both involving the architectural aesthetic output, but also different design approaches, new ways of thinking to the project and more possibilities of using materials.
The workshop ‘‘Robotic Inform’’, promoted by Design Morphine, had the objective to open our mind on these new themes and to give us a very first contact to the numerically informed design through the computation. The use of digital and robotic computation indeed, gives us the possibility to explore innovative geometric languages, a functional integration and new and smart design methodologies able to exploit in the best way these technologies. The workshop gave us the possibilitiy to digitally design and produce our personal 3D printed chair through a generative algorithm able to create the organic profile of the chair.
THE PROCESS:
BORDER DEFINITION
DESIGN_01
DESIGN_02
DESIGN_03
RANDOM FORCES ARE APPLIED
SECTION DEFINITION
FINAL RESULT
After the three days workshop, one prototypes was printed in scale 1:2 using a robotic arm. Once the 3D model was finished, the G-CODE was exported, sent to the robot that was previously set up properly. Two colours have been used: the first and the last three layers are coloured in blue, meanwhile the central body of the chair is in transparent-white, a design choice made to highlight the curvy layout created by the generative algorithm. The final result was incredibly resistant: even if it was half-dimensioned (scale 1:2), it was possible to sit without breaking it, highlighting the great potentialities of this technology applied on the design world.
Printer used: KUKA KR 470-2 PA
Print time: about 50 min.
Total amount of layers: 148
Scale: 1:2
Material used: Plastic (PLA)
YAC competition Team project 2021
Designer(s): Leonardo Bin, Mattia Grigolato, Natalia Estevez, Lorena Rodriguez
Competition jury: Ben van Berkel, Winy Maas, Kazuyo Sejima, Hasan Çalışlar, Nicola Scaranaro, Paolo Cresci, Fedele Canosa, Linna Choi and Chad Oppenheim.
Las Vegas represents in the collective imagination a mirage, a living oasis in one of the most desolate and in some ways most inhospitable places on the planet. Cold and quiet during the day, alive and frantic at night. The Hyperloop Desert Campus will give form and solidity to the mirage itself and will bring to life that same hallucination, so familiar to those who venture into the Mojave Desert.
Like every revolutionary idea, the construction of the Hyperloop has been welcomed with great interest and enthusiasm, for this reason the task of this architecture will be to nourish in the user that sense of astonishment and wonder, of challenge to what is conventionally recognized as impossible. What is the Hyperloop, if not the attempt to challenge one of the fundamental laws of physics, the gravitational law, through electromagnetic gravitation? In the same way, the Campus will result to float between the dunes, forming under it an underworld where the greatest inventions of science will be implemented.
OFFICES
RELAX AND FITNESS AREA
FLEXIBLE DISCUSSION OFFICES
HABITABLE STAIR SPACE CAFE
MUSEUM
MUSEUM CORE -FUTURE OF TRANSPORTATION
MUSEUM ENTRANCE TRANSPORTATION HISTORY
HALL RECEPTION
GRID STRUCTURE
WALKABLE PATH
GYM
GYM POOL
APARTMENTS
WATER ABSORTION GREEN HOUSE
TWO APARTMENTS PER FLOOR
RELAX AREA
LABORATORY
HYPERLOOP TUBE
RESTAURANT ARENA
CHILL AREA
TRAINING CENTER
Flexible laboratory 10 - rooms
Center for model training
TECHNOLOGICAL UNDERGROUND
HYDROPONICS GREEN MOUNTAINS
ACCESS BRIDGE
UNDERGROUND PARKING
As well as Las Vegas, the Desert Campus has a dual nature. On the surface, the roof of the building camouflages itself with the dunes of the desert and is surrounded by Xeriscaping, but under the veil of water you will come across a real temple of science.
Holograms take the place of physical models, digital floors allow the reconfigurability of the space, interactive glass installed on movable partitions walls replace blackboards and water becomes an architectural element itself. Moreover, under the building, the hydroponic farm contributes to the self sufficiency of the Campus. The layer of water that covers it, will form a closed cycle: used minimally for the hydroponic farm, the energy produced by its fall will be transformed into electricity. This strategy will also allow the energy sustenance of the Campus community, which lives in earth 3D printed houses, built from the soil obtained from the excavation.
COMMON
RESTAURANT/ARENA (DOWNSTAIRS)
CHILL
TRAINING
WORKERS VISITORS
PUBLIC PARKING HOUSES STAIRS LANDSCAPE STAIRS STAFF PARKING MAIN ENTRANCE ELEVATORS - SERVICES
MUSEUM OFFICES ARENA APARTMENTS GYM
TRAINING CENTER CHILL AREA RESTAURANT LABORATORIES
STRUCTURAL GRID GLASS ROOF BIPV
COMMON TERRACE
DOUBLE BEDROOM APARTMENT
CENTRAL CORE
SINGLE BEDROOM APARTMENT
COMMON TERRACE
APARTMENTS
COMMON GREENHOUSE ENTRANCE/BASEMENT
WATER COLLECTION
CENTRAL CORE
APARTMENTS
Once the escavation process is over, the crane 3D printer can be installed at the center of the building site. The printer radius is 6 m.
The eath that was previously escavated is now used for the 3D print of the load bearing walls of the staff’s houses.
Once the 3D print is completed, the printer can be easily disassembled and moved to the next printing site.
The finishing works include the slab construction, the central staircaise, the doors, windows and forniture installation.