[Translated from the Japanese]
Academic year 2015
Practice-based Research Report
[Submitted in partial fulfillment of the requirements for the Degree of Master’s Program in Art and Design]
Methodology in Creating Ceramics
MODELLING & DECORATING
Kyoto Saga University of Arts・Graduate School
Master’s Program in Art and Design・Mixed Media
Name: Phuong Nguyen Thanh Le
Student ID: G214007
Roll course: April 1st , 2014 – March 19th , 2016
Chapter I - Research content
To progress my methodology in creating ceramics through a synthesis of coil building - the modelling1 method I began practicing in Japan, and the method of decorating ceramics at a ceramics producing area in the South of Vietnam.
I.1. Coil building – the modelling method that I began practicing in Japan
I.1.1. Why I chose coil building among many other modelling methods
Coil building is a “primitive method of forming pots by coiling long rolls of clay until the desired shape had been attained, after which inside and outside are smoothed by being scraped and smeared. The method was used to make pots of extremely large size, and it is still sometimes employed today by makers of studio pottery”2 .
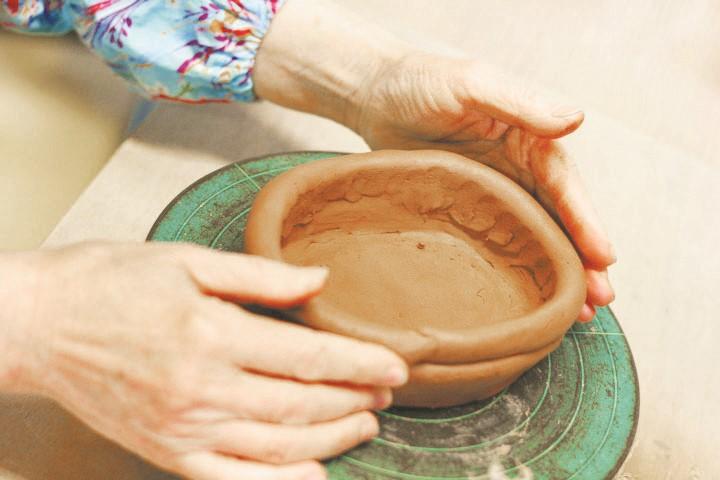
1 ‘Modelling: the process of shaping an original piece of ceramic ware (or the model or maquette from which is made a mould to be used in producing reproductions for sale). Usually the original model of clay or wax is made from a drawing, the modeler seeking to preserve the spirit and details of the designer. The modeler must allow for shrinkage when the clay dries, and again when it is fired; the model is said to be in “clay-size” , and the fired piece is about one-sixth smaller. Some ceramic designers, notably Bustelli at Nymphenburg, produced original models in carved lime-wood instead of in modelled clay, and the moulds were made from these.’ George Savage・Harold Newman (2000) AnIllustratedDictionaryofCeramics, Thames & Hudson, p.195.
2 George Savage ・ Harold Newman (2000) An Illustrated Dictionary of Ceramics, Thames & Hudson, p.81.
The difficulty of this method is that the desired shape has to be kept hollow from the beginning of the modelling process. It is different from making a drawing on which any of the disliked portions may be erased and then redrawn smoothly. For clay, it is necessary to ensure the appropriate wetness in order to be able to accordingly adjust the shape; otherwise fissure will decidedly come out on the surface. A dynamic sculpture is definitely not as simple as a pot shape whose outlook is imaginable at the beginning. A sculpture is more intricate because we have to keep modelling concurrently at various angles. That is a reason why coil building is not an appropriate method for modelling dynamic sculptures Nonetheless, through coil building I feel entirely free when being able to translate my imagination directly into the shape. And to me the freedom while creating is high priority
In the process of making a ceramic piece, the firing3 might be considered the last step but it could decide the quality of the outcome. At the time the kiln is switched on, the ceramist can no longer retouch the product as if it was placed in front of him/her. That is also a reason why making copies of one design is considered a basic practice in the field of ceramics
3 a‘Biscuit firing: a preliminary firing of pottery and porcelain which transforms the ware into the biscuit state. This is followed by glazing and decoration, unless the ware is intended to be left unglazed.’
‘Biscuit: unglazed porcelain or earthenware which has been fired only once. Such ware is sometimes erroneously termed “bisque” in England and the United States…’ George Savage・Harold Newman (2000) AnIllustratedDictionaryofCeramics, Thames & Hudson, p.44.
b- ‘Glost firing: a second firing of ceramic ware for the purpose of fusing the glaze which is applied after the biscuit firing. The requisite temperatures are usually about 1100 Celsius degrees for porcelain and 1050 Celsius degrees for earthenware, but these temperatures can be modified by the addition of a flux to assist fusion. Decoration applied overglaze is fused at a slightly lower temperature which is just sufficient to remelt the surface of the glaze.’ George Savage・ Harold Newman (2000) AnIllustrated DictionaryofCeramics, Thames & Hudson, p.136 – p.137.
ltnph4/40
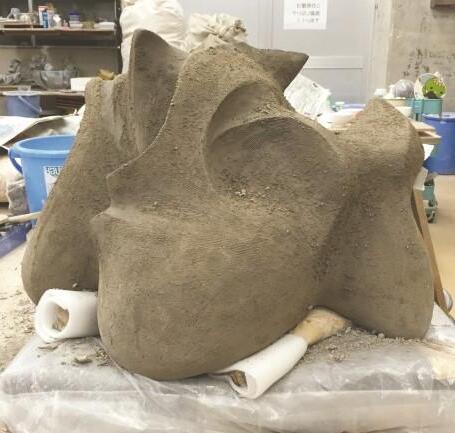
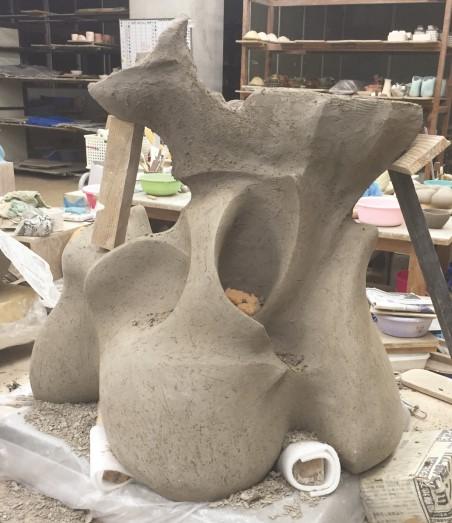
Because it is impossible to produce in mass a ceramic sculpture by the coil building method, I did not practice it during my time of studying the Ceramic Art Specialty in the Department of Industrial Arts at Dong Nai College of Decorative Arts in Vietnam. Being impossible to be adapted to ceramic mass production is a disadvantage of this method. Furthermore, it is difficult to make plaster moulds of complex-surfaced forms, and the increased cost of the firing process makes the coil building method an unsuitable option. As a ceramic designer, I rejected many interesting designs in order to meet the requirements of mass production In case the form continues being adjusted in order to match production conditions, the final design will become far different from the original idea.

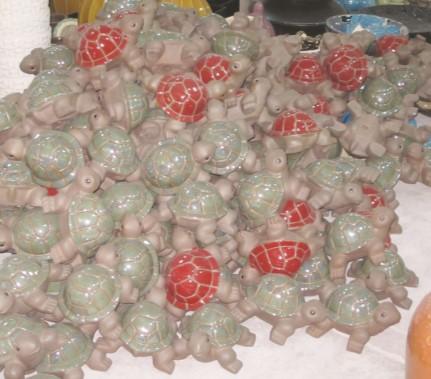
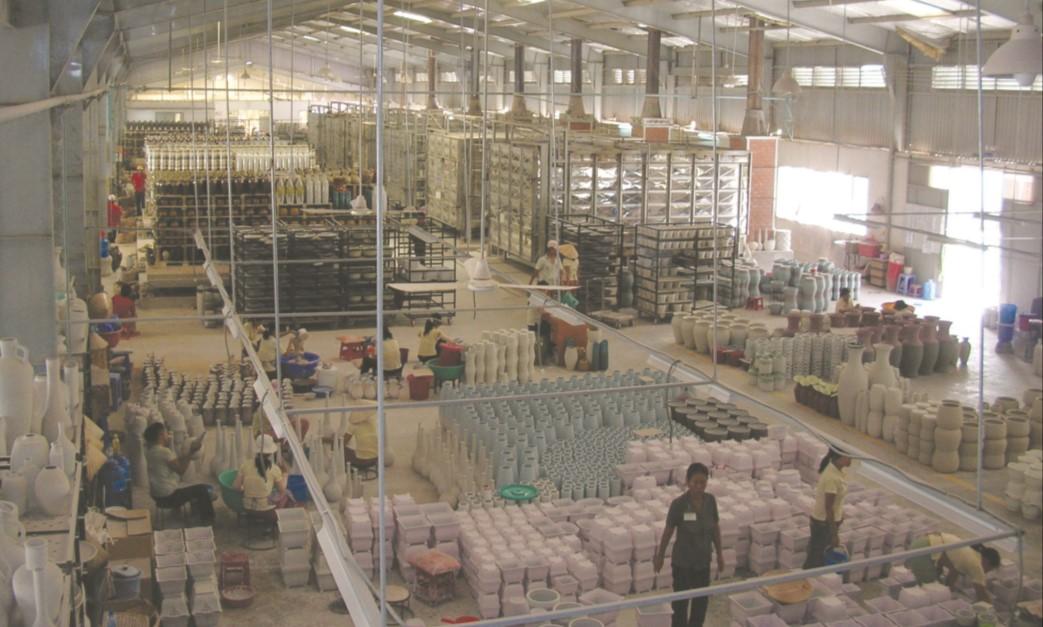
I.1.2 Coil building method synthesized with botanic motifs
In a course named Major Decorative at Dong Nai College of Decorative Arts in the past, I practiced how to create my own decorative patterns from sketching real figures and objects such as the human body, animals and botany. I found the arrangement of botanical motifs very intriguing Perhaps I was influenced by my parents, whose hobby is gardening. During my childhood in Vietnam, our house always had plenty of plants It is an exaggeration to state that I love nature, but observing it has become one of my habits An attractiveness of plants is that they quietly grow day by day whether we are taking care of them or not I am excited by this kind of vitality. Gradually, my involvement in the beauty of botany was raised before I become aware of it
The content of the Major Decorative course was practice in modifying sketches to become decorative patterns. Nonetheless, I had never considered applying these patterns on my ceramic designs in the past. Albeit this is in fact not my hobby, I tend to sketch plants when feeling depressed, and immersing myself into this drawing process gives me back calm and peace of mind. Occasionally, I do the practice. Below are some examples from my sketch book:

I- 5 Example from my sketch book( 1) 2011 – 2014
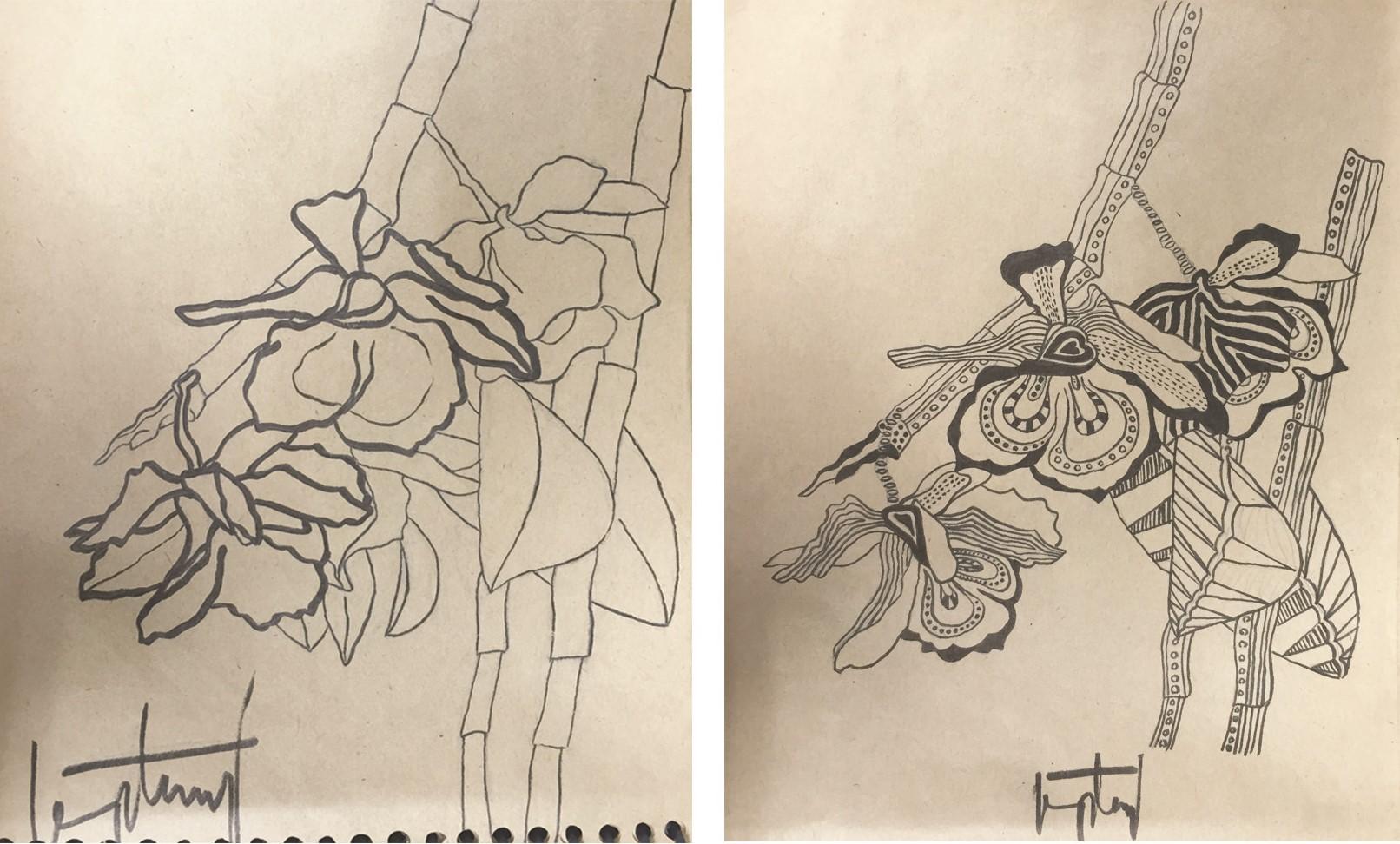
I 6 Example from my sketch book( 2) 2011

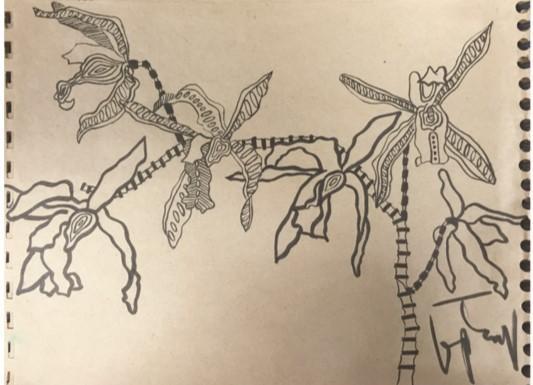
I 7 Example from my sketch book( 3) 2012
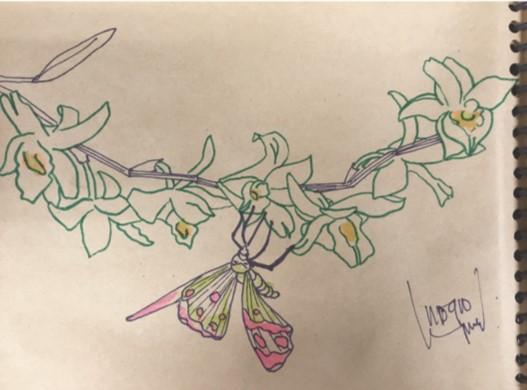

I 8 Example from my sketch book( 4) 2011
When I review my current clay modelling process, I sometimes experience something similar to the process of doing sketches. However, I do not start to model a sculpture from observing a real plant. The shapes just come out from my hands, even though all of the sketches in the past were accomplished in two-dimensional form. The movement of my hand on the drawing during the modifying process from a sketch to a decorative pattern in my memory appears to be replaced by the interaction between my hands and the clay. Merely the first step of the process which is the imitation of the real plant has disappeared
Adapting the coil building method, I am able to translate my imagination into a real clay sculpture at one time (without the repetition of any step within the modelling process) It is similar to holding a brush to draw something on canvas. When the painting is accomplished, the creating process is done I believe the coil building method is a suitable option for modelling my botanic motifs which
might appear more real in an ‘organic shape’. Furthermore, it often requires time to succeed in creating a ceramic sculpture with an acceptable quality. And in that rigid world, coil building brings total freedom in the modelling process.
At present, fissures occasionally appear on my sculpture’s surface because I insistently proceed with the modelling even though I know it could be a too complex-surfaced sculpture to be accomplished perfectly. On the other hand, pursuing the standard has enhanced my awareness concerning the disadvantage of this method. Whether the accomplished sculptures are good or bad, comprehension of how and why the problem occurred is essential in this modelling process.
I.2. The method of decorating ceramics in the South of Vietnam
I.2.1 Introduction of this decorating method
Dong Nai College of Decorative Arts (École Professionnelle de Bienhoa) was established in 1903 in Bien Hoa City in the South of Vietnam This was the French colonial period. The traditional ceramic decorating method which I was taught during my study at the college (2002–2005) looks like that in Figure I-9 below. It was considered to be one of many developments made by Mariette Balick, who was trained at Limoges, a well-known pottery producing area in France. She was assigned as an assistant to the principal, who was as well her husband (Mister Balick), in 1923, when the school was renamed as École d’Art Indigene de Bienhoa by the current French government.
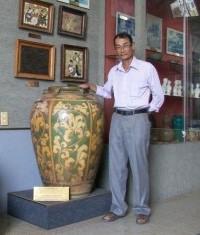
Figure I 9 Urn with six handles, chrysanthemum décor, green and yellow glazes, 1936–1954, Dong Nai Province Museum, Bien Hoa City, South of Vietnam
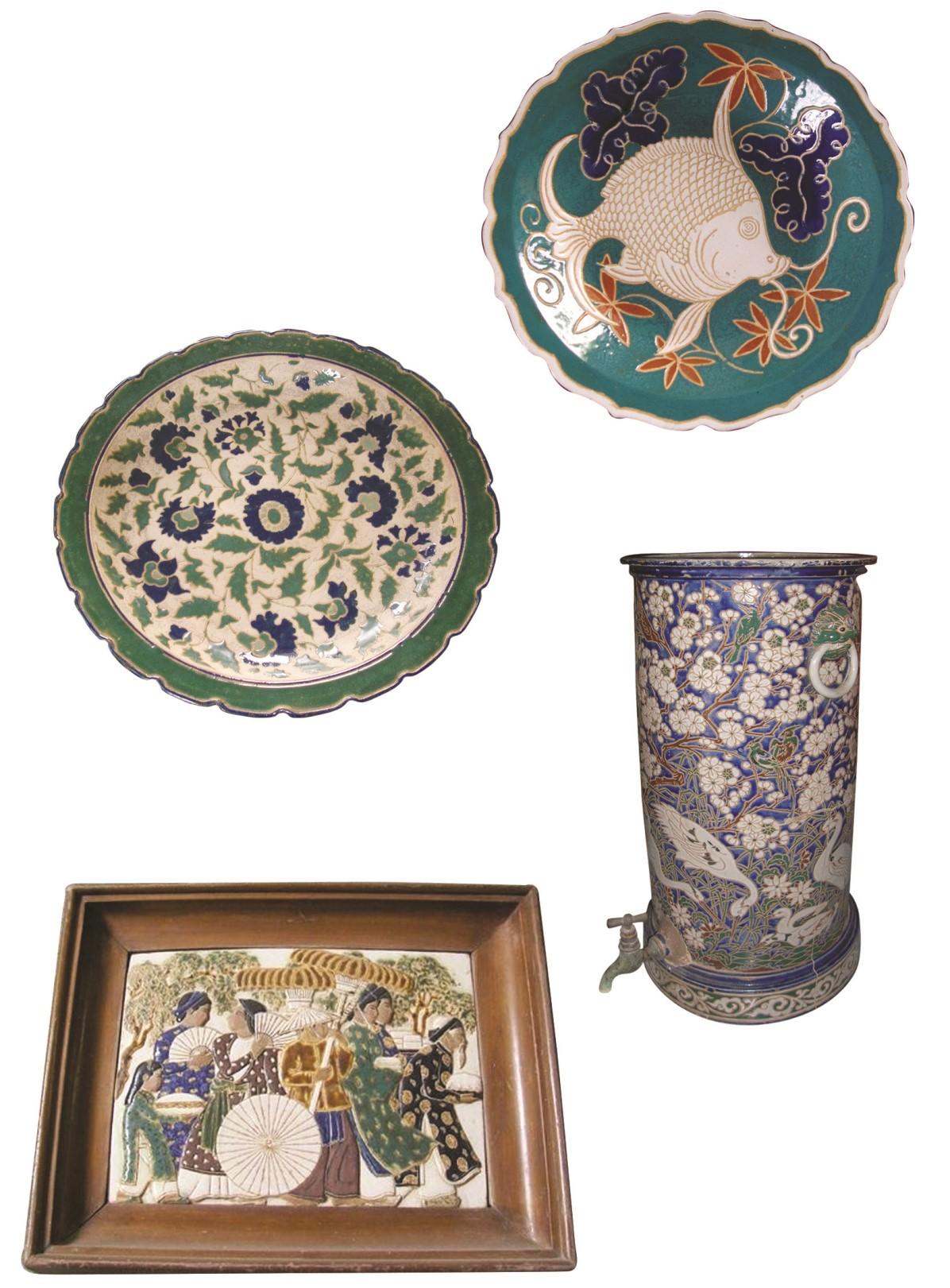