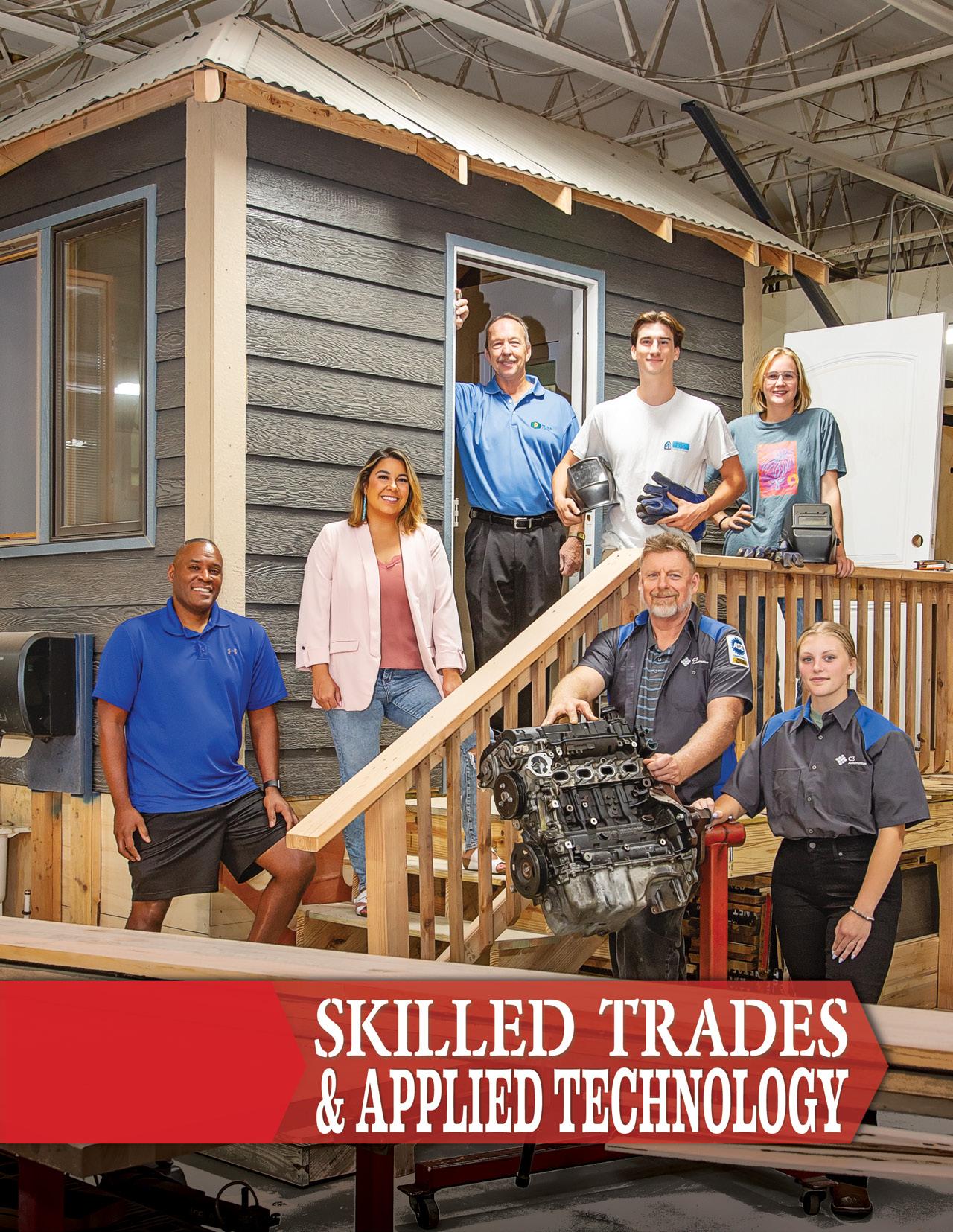
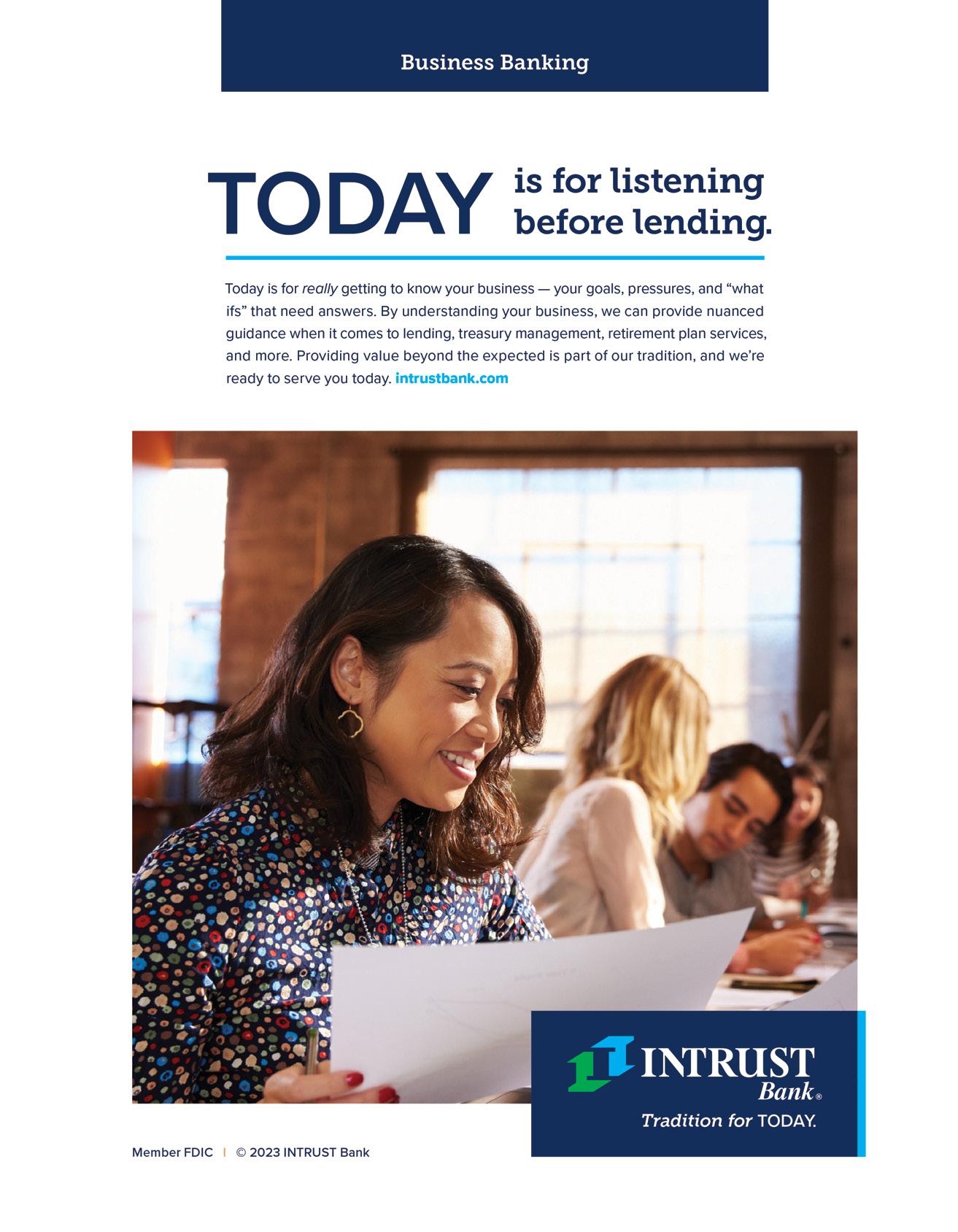
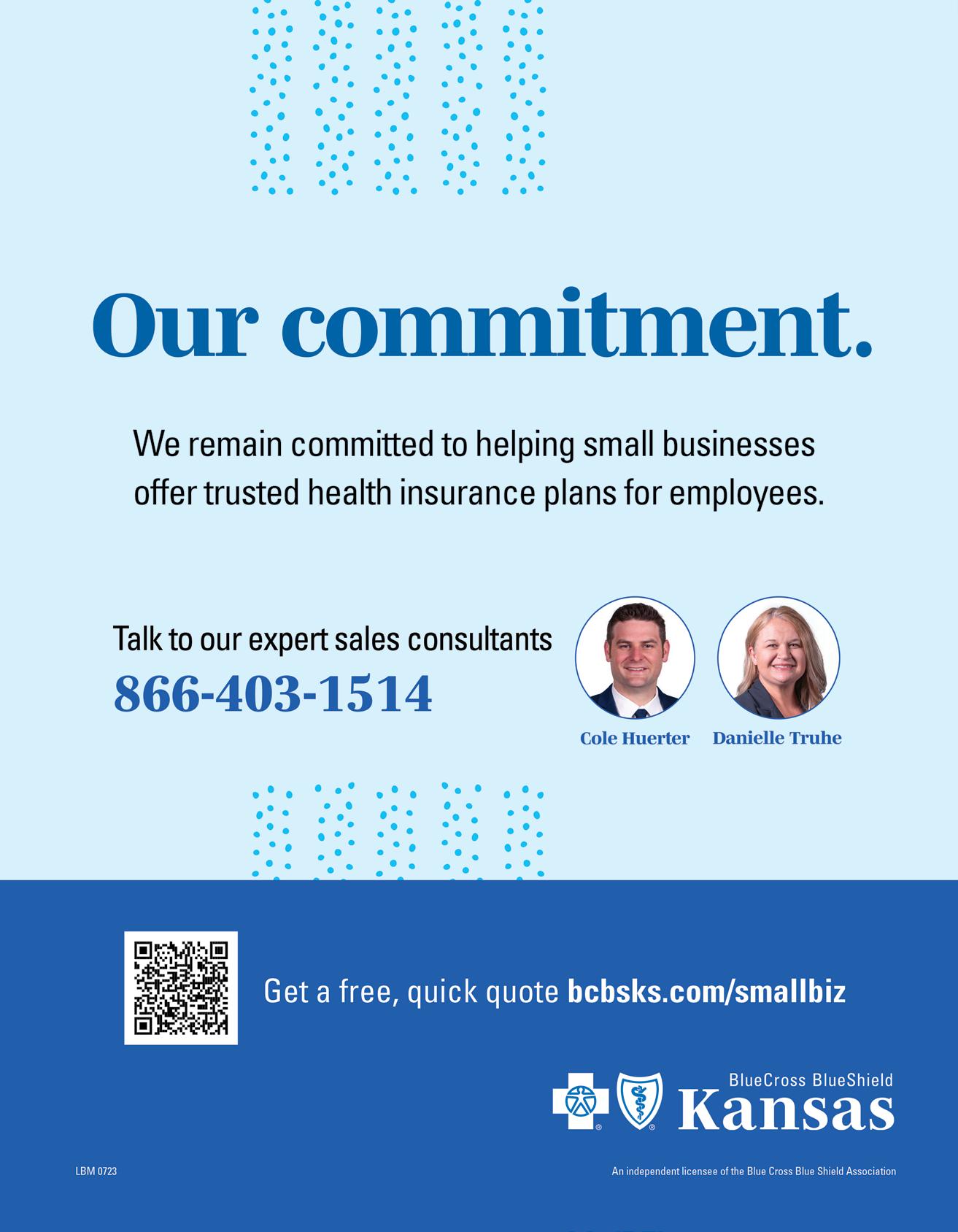
Skilled trades and the training required to excel in them are vital to our thriving community. This wide range of professions includes plumbers, electricians, carpenters, welders, HVAC, robotics, commercial drivers, and mechanics, to name a few. Luckily, we have many of these businesses in Lawrence and the capacity to train for these careers. The significance of these professions goes beyond economic contributions, as they play a fundamental role in shaping the fabric of our local community. Unfortunately, we cannot cover all of the businesses here in Douglas County, but we try to give you an overview of these professions and a little insight into the careers.
Skilled trades offer an alternative educational pathway for community members who may not want to pursue traditional two and four-year college degrees or are looking for a second career. Vocational and technical training programs provide accessible avenues for personal and professional development. When residents are trained and employed in these jobs, it bolsters our local economy. These skilled tradespeople are responsible for building and maintaining critical infrastructure – including our city streets and county roads, bridges, water utilities, constructing homes, schools, healthcare facilities, and local businesses.
Lawrence's Peaslee Tech offers technical training for skilled trades, as well as mentorship and apprenticeship opportunities. The passing down of knowledge and skills from experienced professionals to newcomers is a valuable aspect of community-building. It ensures that expertise is preserved and that younger generations have access to essential skills.
Another key role the skilled trades play is in promoting sustainable practices within Lawrence and the greater community. Electricians install energy-efficient lighting, plumbers implement water-saving technologies, and HVAC technicians optimize heating and cooling systems for energy conservation, reducing resource consumption, which benefits the environment.
Skilled tradespeople are essential for quick and effective responses during emergencies, such as natural disasters or power outages. Electricians, for example, help restore power, while carpenters and construction workers assist in rebuilding damaged structures. Good training in these professions helps ensure that Lawrence stays resilient and better equipped to handle unforeseen challenges.
As you read through this issue, please remember that all our advertisers have a stake in the local economy; we ask you to first consider them before looking to source your needs outside of the community. Try and shop locally as much as possible and avoid the urge to order online. If you find something online – see if one of our local businesses has it. We know they would appreciate the business - our local businesses are at the center of our community.
When we Shop Local - Shop Baldwin, Eudora, Lecompton, and Lawrence (and use Local Services) -we are supporting those businesses, giving back to our community, and building a future together.
Sincerely,
Publisher:
Lawrence Business Magazine, LLC
Ann Frame Hertzog & Steven Hertzog
Editor-in-Chief:
Ann Frame Hertzog
Chief Photographer: Steven Hertzog
Featured Writers: Bob Luder
Patricia A. Michaelis, Ph.D.
Ann Frame Hertzog Editor-in-Chief/Publisher Chief Photographer/Publisherwww.LawrenceBusinessMagazine.com
ON THE COVER - PEASLEE REPRESENTATIVES
(clockwise from left): Nick Marshall - Math Instructor, Adult Education Program (GED); Brittany Hall - Board Member; Dr. Kevin Kelley - CEO; Stephen Huffman - Welding Student; Lina Matthews - Welding Student; Isabella Armstrong - Automotive Technology Student; Kevin Bailey - Automotive Technology Instructor.
Emily Mulligan
Nick Spacek
Tara Trenary
Darin M. White
Copy Editor: Tara Trenary
Contributing Writers: Kade Han
Julie DeYoung
Contributing
Photographers: Thad Powell, McElroy's Inc
INQUIRIES & ADVERTISING
INFORMATION CONTACT: info@LawrenceBusinessMagazine.com
LawrenceBusinessMagazine.com
Lawrence Business Magazine, LLC
3514 Clinton Parkway, Suite A-113 Lawrence, KS 66047
© 2023 Lawrence Business Magazine, LLC
Lawrence Business Magazine, is published quarterly by Lawrence Business Magazine, LLC and is distributed by direct mail to businesses in the Lawrence & Douglas County Community. It is also distributed at key retail locations throughout the area and mailed to individual subscribers. All rights reserved. No part of this publication can be reprinted or reproduced without the publisher’s permission. Lawrence Business Magazine, LLC assumes no responsibility for unsolicited materials. Statements and opinions printed in the Lawrence Business Magazine are the those of the author or advertiser and are not necessarily the opinion of Lawrence Business Magazine.
Although started as a school to assimilate American Indians into white culture, Haskell Indian Nations University transformed into an institution that celebrates indigenous cultures.
by Pat Michaelis, Ph.D., Historical Research & Archival Consulting photos provided by Douglas County Historical Society, Watkins Museum of HistoryHaskell Indian Nations University in Lawrence, Kansas, is a diverse inter-tribal educational institution. Its mission is “to build the leadership capacity of our students by serving as the leading institution of academic excellence, cultural and intellectual prominence, and holistic education that addresses the needs of Indigenous communities.” Approximately 1000 students attend the university where they can receive associate and baccalaureate degrees. The baccalaureate degree programs are Indigenous and American Indian Studies, Elementary Education, Business Administration and Environmental Science.
In the 19th century, the United States government believed industrial training schools were part of the solution to the American Indian “problem.” The government stated that it wanted to assimilate Native Americans into the mainstream (white) society and felt that education of the tribal children was the best way to accomplish this. However, the students spent most of their time doing manual labor. Little time was spent in the classroom.
It is important to understand how the Europeans settling North America viewed Native Americans. They believed they were inferior to the whites and that the Europeans had a right to the land the indigenous people had lived on for generations. As European settlers expanded west, they encroached on land claimed by Native Americans. This led to a government policy of Indian removal and the establishment
of the reservation systems. Tribes were resettled into areas where the environment was extremely different from where they had been living. A report dated June 30, 1885, from the Haskell superintendent James Marvin to the Commissioner of Indian Affair contained the following assessment of the students attending the school:
In every department two points have been made most prominent: First, how to speak the English language; second, how to do any kind of work in hand quickly and well. The difficulties attending instruction can be appreciated best by those who have had the experience with youth who know little or nothing of English and who are entire strangers to all habits of industry and economy. A vague notion that necessity if laid upon them to “learn the white man’s way” is the leading thought with these youth and their friends. They have no conception of the particular subjects of study, nor of the time and effort required. On these points the parents are as ignorant as the children. Aversion to severe manual labor is not only fixed by heredity, but by prejudice, especially on the part of boys. A knowledge of letters without habits of industry cannot save the Indians.
This unfair judgement of the students doesn’t take into account that Native Americans had their own cultures and traditions of educating their youth. It does make it clear that the
intent of education at Haskell and other Indian schools was to “Americanize” the young men and women attending the schools.
Haskell was founded in 1884 as the United States Indian Industrial School on 280 acres of land that was donated by Lawrence residents. When the first students arrived at Haskell, the school hadn’t opened yet and the children spent their time clearing fields, planting orchards and getting the farm and buildings ready for use. The first 22 students attended classes in grades one through five but within a year approximately 400 children lived at the school. The students, some as young as three and four years old, were treated harshly. They couldn’t speak their tribal languages or follow any of their own customs. The students were given crew cuts which ignored the custom of having long hair except when mourning. They couldn’t return home or have any contact with their families.
When Haskell opened, the campus contained three main buildings, two barns, and several other outbuildings. Crops had been planted and corrals had been built to contain the livestock. An orchard of 400 apple, pear, and peach trees had been planted.
Many students had difficulties adjusting to life at Haskell. Several students tried to return home but they received severe punishments if they were caught and returned to the school. While they plans for the school looked good in reports, students in the early years had inadequate food and clothing. The buildings were unheated and poorly ventilated leading to unsanitary living conditions. Two separate petitions from teachers and staff and from students were submitted to the Department of the Interior in 1887 asking them to investigate conditions at the school. They were concerned about the high number of sick students and student deaths occurring at the school.
In addition to the emphasis on learning English, classes focused on manual training related to agriculture and domestic skills. The boys studied tailoring, wagon making, blacksmithing, harness making, painting, shoe making, and farming. Girls studied cooking, sewing and homemaking. Most of the students’ food was produced on the Haskell
farm and students were expected to participate in various industrial duties.
By 1896, Haskell offered two tracks of study—a Normal department that trained students to be teachers with the intent that they would return to their homes and organize schools and a Commerce Department that taught business skills. Haskell was accredited as a high school by the state of Kansas by 1927. The curriculum evolved to include post-secondary classes and by the late 1930s it was considered a post high school, vocational technical institution. The last high school class graduated in 1965 as the secondary education classes had been phased out. It became a junior college in 1970 and in 1992 the name was changed to Haskell Indian Nations University, reflecting its status as a 4-year college.
In 1897, The Indian Leader was introduced. It is the oldest Native American student newspaper still in publication. The first issue stated the mission of the endeavor was to share news of former students and include information about current students and teachers. In addition, the paper hoped to win new friends, to enter the homes of many who know but little of Indians and their capabilities, showing them that though of a different race, many of them are intelligent and progressive; that they have for their motto, “Onward and Upward” and are trying to live up to this.
The goal of learning English was met with the students writing the articles for the paper and industrial training was accomplished by setting type and printing the paper. Students working in the print shop also did job printing for local businesses and the school. The newspaper content included literary essays, updates from the Indian Service about where former teachers and students were working, accounts of the school’s athletic competitions, and news about activities on campus. By 1923, it contained information about a variety of extracurricular activities. One article described a concert by the band at Perry and others described the activities of the campus YMCA and YWCAs. The music students presented a program on American composers. It included brief biographies of the composers and selections of their work. It concluded with the audience joining in the singing. Several literary societies were active as well as other clubs.
In order to learn home making skills, the girls in the domestic science courses had a small cottage that they furnished. It had four kitchens. All the woodwork and the furniture was painted white and white muslin curtains adorned the windows. It had a guest room that contained a set of ivory furniture, a Japanese rug and blue and cream chintz drapes. The girls in the cottage also had a flock of chickens and vegetable and flower gardens.
Letters from former students reporting on their lives were printed frequently. One student who graduated from the commercial department was working as a stenographer at the Indian agency in Fort Washakie, WY. In 1923, he wrote that he appreciated the work that was being done at Haskell. He kept up with what was happening by reading The Indian Leader and felt that the newspaper reflected the improved educational programs when it was compared to the content of the paper ten years ago. A current student wrote a friend in South Dakota about her experiences at the school and it was published in the local newspaper:
Perhaps you would like to know where I am and what I am doing here. My school is situated about 2 miles south of the city of Lawrence. Lawrence is quite a large place itself. There are over 800 students here. They come from Washington, Oregon, California, Idaho, Montana, Wyoming, North Dakota, South Dakota, New Mexico, Oklahoma, Minnesota, Arizona, Michigan, Wisconsin, and Kansas. By this you can see that the states are well represented here. We are given from the lower grades through high school. We are given a chance to take either normal training, commercial training, or home economics course, but this chance does not come until we finish the sophomore year or tenth grade. . .. Next year I intend to continue high school and take the normal course. I am a sophomore just now and if I am lucky enough to be given a choice you can be assured that I will choose to be a teacher.
As these comments from students indicate, some students appreciated the education they received at Haskell. Because the newspaper was overseen by the school’s administrators, only positive comments were published.
A visitor to the Haskell campus can see twelve buildings that have been designated National Historic Landmarks as well as several sculptures and murals. The Haskell Cultural Center and Museum is open to visitors. Several annual events worth noting are the Haskell Indian Art Market each September and a twoday Pow Wow where many graduating students wear traditional dress in conjunction with the spring commencement.
Note: We want to thank Travis Campbell, director of the Cultural Center and Museum for providing digital copies of The Indian Leader. The newspaper was an invaluable resource for writing this article. We also want to thank him for reviewing this article. His feedback helped us include some important Native American perspectives to various aspects of Haskell history. p
The health-care industry offers a diverse array of career paths. It encompasses administrative and clinical positions in multiple specialties and areas of care. The pathway to entering the clinical side of health care does not have to be through a traditional four-year college degree or a doctorate, but rather via on-thejob training, vocational certifications or an associate’s degree.
A phlebotomist is trained to draw blood samples and prepare them to be tested and analyzed. They primarily work in hospitals, labs, clinics and blood-donation centers. Everyday tasks for phlebotomists include:
■ preparing and labeling collection vials
■ preparing patients for blood draws
■ performing blood draws
■ maintaining blood draw instruments and supplies. Individuals who are interested in becoming a phlebotomist can receive on-the-job training or obtain an in-person or online certification. Most LMH Health phlebotomists received on-the-job training after being hired.
“The hardest part about completing my phlebotomy training was being afraid to hurt my patients,” says Nicholina Chronister, LMH Health phlebotomy supervisor.
Chronister, a former wildfire firefighter, was seeking a career change that would allow her to enter the health-care industry. She wanted to get her foot in the door to see if a career in emergency medicine was right for her. Phlebotomy was a great way for her to get hands-on experience without investing time and money in a specialized degree.
“I know of a few people who used phlebotomy as a way to kick-start their career,” she explains. “Some of them have gone on to become registered nurses, therapists or achieve higher levels of education.”
Although one might think a college degree and possibly more are required to work in the medical field, there are many pathways that don’t require that extra time and money.Curtis Weilert and Nicholina Chronister
Chronister began her career with LMH Health in 2011 after she connected with a phlebotomist during an emergency department visit. She received additional training in administrative and laboratory processes, and progressed to become the phlebotomy supervisor in 2019.
“I fell in love with phlebotomy and how important and impactful it is to patient care,” Chronister says. “Our work influences treatment plans, provides answers and gets patients on the road to recovery.”
Think of the health-care industry as a beehive with every position inside it a different bee. Each position has a role that impacts how other health-care professionals respond and work. Chronister likens phlebotomists to the worker bees of the hive, but instead of collecting pollen, they draw blood.
“We are a part of large system, and it is important that we do our tasks in a timely manner so that our lab can do theirs without rushing,” she says.
Phlebotomy is a fast-paced career that has a lot of interaction with patients. A phlebotomist needs to be good with people, pay attention to detail and be self-motivated and driven.
“When we are looking at phlebotomist applications, we aren’t always looking for previous health-care experience,” Chronister explains. “Oftentimes, we are looking for the candidates who have no experience but are willing to learn and adapt on the job.”
Not every position in the health-care industry requires patient contact. Biomedical technicians work behind the scenes to keep hospital and clinic equipment up and running. Depending on the scale of the organization for which they work, these technicians can service more than 2,500 unique pieces of equipment.
Some of the daily tasks of biomedical technicians include:
■ installing, maintaining and repairing medical equipment
■ performing routine tests and inspections of equipment
■ performing preventive maintenance
■ identifying parts and equipment for removal or replacement
■ keeping records of equipment replaced, repaired and maintained.
“You don’t get bored. Every day, there is a new surprise,” says Curtis Weilert, LMH Health biomedical technician. “I often find myself asking, ‘What’s this piece of equipment and what does it do?’ ”
There are two common ways to enter the biomedical field. The first is through an associate’s degree with a focus on computer sciences, engineering or biomedical; and the second is through a military biomedical program.
Weilert earned an associate’s degree in electronics and computer engineering technology from Grantham University. He completed all of his general education credits through a community college to lower the cost, later transferring to a specialized online college for the core electronic credits.
“While working for a wind farm on wind towers, I decided it was time to get out of that business,” Weilert explains. “My experience was in electronics, but I did not know a lot about the biomed aspect. I was able to learn the biomed aspect on the job.”
Individuals interested in pursuing a career as a biomedical technician should have an interest in how and why things work, as well as a basic knowledge of logic and troubleshooting, as well as mechanical sciences.
“Biomed is a hidden gem within health care,” Weilert continues. “You get to move around and get your hands on lots of different equipment.”
Sometimes, the biggest challenge biomedical technicians face in a larger health-care setting is finding the equipment. LMH Health has more than 6,000 pieces of equipment spread across multiple cities and clinics. Because of the number of pieces of equipment and the fact that some only need routine maintenance, LMH Health biomedical technicians may only touch a piece once each year. This results in the techs having to reacquaint and relearn the equipment constantly.
“I had to restart at age 47 after 10 years working with family,” Weilert says. “I turned toward the wind farm and then to biomed. Even at that age, I was able to start over, learn new things, finish my associate’s degree and start a new career. If I can do it, anybody else can.” p
You can’t define it, but you know it when you see it: the difference between an average life and the good life. When your cup is full—with joy, purpose and lifelong health— it shows. At LMH Health, we are all about healthy people, healthy communities and healthy futures, and that makes us your destination for an exceptional career. From flexible work-life harmony to competitive pay and great advancement potential, find everything you’re looking for at LMH Health. We’re looking for you.
Visit lmh.org/careers to apply.
Let's Have a Parade! Those words kick off a Lawrence holiday tradition, the Lawrence Old-Fashioned Christmas Parade, held at 11 a.m the first Saturday in December. This year, on Dec. 2, 2023, it will be for 30th anniversary.
Celebrating the role of horses in history as well as the winter holidays, the Lawrence Christmas Parade is one of the few all-horse parades in the country and is believed to be one of the largest and longest-running.
“We are so honored to continue this tradition for its 30th trip down Massachusetts Street. For both participants and spectators, it has become a special time to kick off the Christmas season with family and friends, and it wouldn’t be possible without the support of the Lawrence business community, and especially downtown Lawrence,” says Marty Kennedy, president of Lawrence Old-Fashioned Christmas Parade Inc., who leads the 501c3 nonprofit board and all-volunteer committee that manages the parade.
Originally named “The Eldridge Hotel Old-Fashioned Christmas Parade,” this event was the brainchild of Robert W. Phillips, a local businessman and general manager of the (at the time) newly renovated Eldridge Hotel. In 1992, Phillips became involved with driving horses and purchased a team and wagon so he could participate in a wagon train that traveled across Kansas on the historic Oregon Trail. Along the route, people came out to see the wagon train, and as it passed through small towns, it turned into a parade. Phillips was struck by the enthusiasm of the crowds. Thus, the idea of a parade hosted by the Eldridge Hotel was born. The first parade was pulled together in just a few months and included 21 horse-drawn vehicles traveling down Massachusetts Street with six cowboy outriders to assist. As news of the event spread, the number of entries increased each year, and the crowds who gathered to watch grew dramatically. The parade has hosted as many as 70 horse-powered vehicles paying tribute to the contribution of the horse in our transportation heritage. Crowds numbering in the tens of thousands throng Downtown Lawrence to experience the sounds of hoof beats and sleigh bells as the horses make their way down Mass.
Phillips created 11 rules to guide the parade’s development, most of which are honored today. Historically authentic, horse-drawn
vehicles and participants in period or holiday dress are central to the parade, as is providing a dinner the night before and complementary hotel rooms for participants traveling from a distance. Sponsors are invited to the Friday dinner to mingle with the participants, and the public is welcome to visit the 100 or more horses stabled at the Douglas County Fairgrounds overnight.
As the parade has grown, the financial support required for a quality event has increased. The Lawrence business community has stepped up during the years and continues to be the financial foundation today. Major sponsors include the City of Lawrence, eXplore Lawrence, The Chamber, Eldridge Hotel, Kennedy Glass and Standard Beverage, and new in 2022 Laser Logic and media sponsors Great Plains Media and Lawrence Business Magazine. Friends of the Parade— individual and business sponsors—and in-kind donors provide substantial funding, as well.
In addition to being a meaningful tradition, the parade is an economic driver for the community. „The Lawrence OldFashioned Christmas Parade is truly an unmistakable event. It draws in participants from across the country and attracts visitors from surrounding communities. It’s a magical way to showcase Lawrence as a destination and share our community,“ says Kim Anspach, director of eXplore Lawrence.
The event fills hotel rooms during off-peak travel season and generates nearly $700,000 in economic impact. Sponsors benefit from visibility on the parade website, social media and parade signage and marketing materials.
As part of the 30th parade celebration, participants in the original parade will be recognized at the Friday night dinner and during the parade. Organizers expect three of the original participants to have wagons in the parade, and those no longer driving will ride as guests in other participant conveyances.
Bonnie Lowe, president and CEO of The Chamber of Lawrence, says, “The Lawrence Old-Fashioned Christmas Parade has become a quintessential part of celebrating the holiday season in our community. All of us at The Chamber are thrilled to be a partner with Marty, Patty and the team on their 30th year of leading these beautiful horses down Mass Street. We look forward to this year’s parade and many more to come!”
For more information about the parade and sponsorship opportunities, visit www.lawrencechristmasparade.org. p
An alternative to traditional college, Peaslee Tech offers programs that teach a trade, apprenticeships while in training and direct access to the workforce upon graduating — all without incurring debt.
The outside of The Dwayne Peaslee Technical Training Center looks like an industrial building straight out of the 1970s, but walk through its front doors, and you’ll find yourself standing in a state-of-the-art facility equipped with technology to train students in transportation, health care, manufacturing and many other skilled trades. It offers more than 800 classes and is guided by demand from Douglas County businesses and organizations.
Walking down the main hall of this 76,000-square-foot space, you pass classrooms made for education and testing, including classes for such things as ESL (English as a second language), real estate licensing and obtaining a GED. Outside these classrooms is a large breakout area where students can gather for breaks and get drinks and snacks. Further down the hall in the woodworking lab, a carpentry instructor works with a group from the Boys & Girls Club of Lawrence building raised flower beds to place outside of the Boys & Girls Club headquarters. A lab a bit further down and across the hall houses Avium, a startup born of University of Kansas (KU) graduates that studies hydrogen as an element for a more sustainable future. Its technology is intended to “accelerate the widespread use and adoption of green hydrogen for energy storage, chemical processing, industrial use, heating and transportation,” according to its website.
Employee offices dot the hall, and upon entering yet another large space, we find a dwelling built by residential carpentry students for Tenants to Homeowners, and local nonprofit
dedicated to providing affordable housing. Electrician students did the wiring, and plumbing students will do some of the plumbing. “We are trying to incorporate as many of our students into that house as we can,” explains Charlie Lauts, M.A., Enrollment Services Coordinator at Peaslee Technical Training Center and retired 30-year industrial arts teacher at Lawrence High School.
This house is meant to be a first step out of homelessness, she continues. “The rent will be affordable. They’ll have to have a job. It’s one bedroom, one bath, so very small,” she says. The dimensions of this house are 11 feet x 35 feet. Tenants must work to save money and then move out so another eligible tenant can move in. The plan right now is to build 10, two a year, Lauts adds. “The first two will go on the same lot. They [the City] have lots throughout Lawrence. The goal is to get people out of homelessness.”
Other large spaces throughout the facility are used for HVAC, auto tech—including engine repair, brakes and suspension, and supported by all five major dealerships in town—electrical, welding, truck driving, construction, robotics, industrial maintenance and electrician training. “Our welding class goes to three different levels. Each level is 14 weeks long, but most of them are hired pretty much when they’re done with the first level,” Lauts says. “Recruiters come to the class and hand out applications, it’s such a high-demand job.” Though welding is not a glamorous job but a dirty one, she says welders are in high demand, especially now with the Panasonic Battery Plant coming to DeSoto to make batteries for electric cars. The $4-billion, 4-million-square-foot plant is slated to begin production in 2025. It will bring more than 4,000 jobs to the area.
Located at 2920 Haskell Ave., Peaslee Tech, as it’s locally known, was named for Dwayne Peaslee, a local pipe fitter who had a passion for educational and vocational training. His goal was to help people see how important the skilled trades are to quality of life. He wanted local citizens who want to work in Lawrence and Douglas County to have an opportunity for a great career.
“I was a friend of Dwayne [Peaslee] since the mid-80s,” says Shirley Martin-Smith, chair of the Peaslee Tech board. “He had a gift about him that made people realize how important technical skills were.” She says watching him talk to people so eloquently about the importance of the technical trade and the great living one can gain was inspiring.
“He was very proud of his work. He really believed that you could have the American dream … even if you didn’t go to college,” she adds. “He affected me, but he affected hundreds of other people in this county to believe in technical training and to realize the importance of it.”
Rep. Mike Amyx, Kansas State Legislature District 45 and former Peaslee Tech board member, agrees. He says he was convinced by Dwayne that this was something that needed to be done, putting together a facility that was going to be able to take care of itself and of its students, and prepare them for their future employment. “He really believed in Lawrence and Douglas County, in making sure we were prepared for whatever the next step was going to be, that we were about job creation and had a workforce that was going to be educated and prepared to move into those new jobs. He’d be pretty proud of the Center and everything that is going on there.”
Since its conception, Peaslee Tech has been a component of Douglas County’s economic development effort, explains Kevin Kelley, CEO. Its role is training local residents for livable-wage jobs. Initially, the training was provided by community colleges from throughout the region, but in November 2017, Peaslee Tech was approved by the Kansas Board of Regents as a post-secondary education provider. Since then, he continues, it has started 18 open-enrollment programs and 14 apprenticeship programs, making Peaslee Tech the largest provider of apprenticeship programs in Kansas. During the same period, it expanded service to local businesses in the form of customized training programs. Peaslee is on track to reach 3,000 enrollments in 2023.
Peaslee Tech currently has 40 employees, five full time and 35 part time. There are 32 instructors, with the remainder of the staff supporting recruitment, administration and facilities. The 2023 budget is approximately $1.6 million, with about 25% from Douglas County, 12.5% from the City of Lawrence, 48% from instructional income and grants, and the majority of the remaining from lease income.
It was formed in cooperation with KU through efforts of the Lawrence Douglas County Economic Development Corporation, Douglas County and the City of Lawrence, Kelley explains. Initial collaborations were in the form of training skilled-trade employees. That has expanded with Peaslee hosting the development of the KU Solar Car project, a group of engineering students developing KU’s first solar-powered car, and more recently, with Avium, located on the Peaslee campus.
Peaslee Tech also works with the Apartment Association of Kansas City, which sends its apartment facilities maintenance people to learn a little bit of everything—from electrical to landscaping to drywall—so they can work on apartments. And it houses The Crunch, a large meeting space and private offices for people who want to start their own business and have nowhere else to work. It’s dedicated to supporting the success of entrepreneurs by providing space, equipment and expertise. Many local groups also use the space, including Leadership Kansas, Leadership Lawrence, 1 Million Cups and local unions. The Crunch is tied to KU’s Small Business Development Center.
In addition to most major local employers, Kelley continues, Peaslee works with Heartland Works, Kansas Vocational Rehabilitation, Kansas Department for Children and Family Services, the Lawrence Branch of the NAACP, Catholic Charities, Tenants to Homeowners and many
others. It also works within the local school district. Enrollment Coordinator Lauts does the educational outreach, meaning she visits all of Douglas County middle and high schools, and conducts tours of the facility for local school kids, as well.
Peaslee is supported by the Lawrence Workforce Center, which offers grants that help with tuition assistance for any program if a student qualifies. The Department for Children and Families and Catholic Charities also send people to Peaslee.
“Our unique focus on the needs of Douglas County organizations versus on the learner benefits both the businesses and the learners. We do not deliver programs that don’t support community needs,” Kelley adds.
According to the American Institute of Medical Science and Education, the top 10 benefits of a technical school are its cost effectiveness; students learning by practice; easier admission requirements; flexibility and convenience; a good investment; students acquiring jobs before graduating; graduates having higher rates of employment; no unnecessary classes required; smaller class sizes providing a more personalized education; and careers being available in lucrative fields.
“I wish this place would’ve been here 30 years ago,” Lauts says. As a former industrial arts teacher, she explains she had so many students who would take her engineering class because they loved problemsolving but didn’t love math and science, so engineering was not in their world. “Being able to send them here to be an HVAC technician or an electrician, or something like that, would’ve been such a perfect fit for so many of my students.”
She says one problem is parents’ expectations that their kids must go to college. “So many parents believe their kids need to go to college, but this is just another way to do that. College is for some kids but not for all kids.” When she started teaching in the 1980s, the mindset was, “You need to go to college, you have to go to college, where are you going to college?” Then, she explains, it became too expensive to go to college for some, and people began to focus on what they were and were not actually getting out of it. “So many of the careers now don’t require a four-year degree, and you still get paid really well without the debt. There’s a lot of parents whose minds just haven’t grabbed on to that yet,” she says.
Lauts explains that in the Peaslee truck-driving program recently, both an 18- and a 19-year-old got their licenses. “It’s a good career for them, and it can lead them a lot of directions.” On the flip side, she adds, a 40-year-old man who’s trying to find a second career might be attracted to Peaslee because of the many programs that offer apprenticeships while students are in school. “They can be working in the industry while they’re taking our classes. So they’re earning while they’re learning. A lot of people take advantage of that.”
Peaslee Tech fills another educational opportunity for those who are getting out of high school or simply looking for a new career in their life, Amyx adds. “It gives them an opportunity to say, ‘I’ve always wanted to do this, and it’s something I’d be good at.’ If the program is offered at Peaslee Tech, they’re able to get in there and handson learn, and know upon completion that they’re going to be able to get out in the community and work. It gives them an opportunity for success.”
The most important challenge of Peaslee Tech and the focus of the board and CEO Kelley right now is permanent funding. Funding from the city, Douglas County, the private sector, income from grants and instructional income is in place, Martin-Smith explains. Peaslee staff has worked with the state legislature and is currently working with the senate to get permission as a county to gain support and hold a public vote for this permanent funding. “We would
like to not have to go to the city or county and ask for money every year,” she adds.
Peaslee was needed in this community for decades, MartinSmith continues. “And when the tipping point finally came, the business community and school district and KU and Haskell all came together and said this is something we should do. It was awesome to see. No arguments, nobody said no. The timing was right.”
She says it’s been interesting to watch how years ago so little was spoken about technical trades and what they can do for a career, and how they can be a great alternative. “But it’s now obvious that you can get training, and you can go out and get a good-paying job without debt. I think it’s been a challenge to help people see how respectable these jobs are.” She believes it’s absolutely critical that we provide the training locally to a diverse community from all ages and career paths.
“We’re training them so they get the skills they want that meet what businesses need in our community,” Martin-Smith continues. “If we don’t keep the skills flowing into the companies, you can’t keep the businesses here.” She says Peaslee’s goal is to provide the training to people from different walks of life and to improve the retention and expansion of the businesses already here. Also, to attract new businesses. “It’s all about retention and employee satisfaction on the job. If a company can take an employee, and Peaslee can help build
their skills, they’re going to stay with that company and make more income. It all works well together,” she adds.
Martin-Smith says she’s amazed at the talent that is attracted to Peaslee Tech. “They are all [Peaslee Tech staff members] so generous with their knowledge and experience, and they’re always excited about sharing what they know. The students are so anxious to learn. They want to be there. It’s fascinating the people who are attracted to Peaslee.”
Kelley, his staff and the board do a good job making sure they understand what the next up-and-coming certification is needed, Amyx explains. “That’s an important part. They make sure we are meeting those opportunities for folks to get certified and go right into the marketplace and get jobs.
“I was convinced by Dwayne that this was something we needed to make sure we were able to do,” he continues, “to put together a facility that was going to be able to take care of itself and take care of the students, and prepare them for their future employment. I think we, as a community and a county, have met those needs and will continue to push and get better and better, and continue to be able to give folks an opportunity to be successful.”
Surely Dwayne Peaslee himself would be pleased. MartinSmith says he used to kid her and say, “ ‘You know, if we don’t train these plumbers, you’re all gonna be doing your own plumbing.’ That always stuck with me, because I don’t want to do my own plumbing.” p
Advancing technology has reinvented the automobile industry and, thus, the requirements of the trade.
The COVID-19 pandemic and ensuing shutdown early in 2020 effectively turned the world of business upside down. Employees were all but confined to home, factories ground to a halt—the world stopped.
The automotive industry was not immune to any of it. Plants overseas that made computer chips now required in evermore-complicated car and truck engines ceased production and closed. Not that new autos were needed now that it seemed most everyone was staying home and off the roads. Even the automotive trades—specifically auto technicians, the modern-day job title of what once were mechanics— suffered from some leaving the workforce along with fewer numbers coming into training programs, leading to the same kind of staff shortages suffered in so many industries today.
It’s been a rough three years. But at least one local expert in the field never had a doubt the automotive service industry and automotive trades would bounce back, and in a big way.
“People have to drive,” says Ginger Lopez, service and parts director at Crown Toyota. “For this industry, that’s it. No matter what else happens, people still need their cars.
“Auto service remains steady,” she adds. Not that there haven’t been challenges. The U.S. Bureau of Labor Statistics forecasts “little to no change” from 2021 to 2031 in the demand for automotive service techs. But change is coming. Car and truck engines are becoming ever more technical and computer driven. It’s widely believed that within 10 years, one-third of all cars and trucks on the road will be all-electric vehicles that require less maintenance.
“It’s changed a lot,” says Lopez, who has 38 years of experience in the industry. “The tech of 30 years ago is hardly interested in working on these cars today.
“Recruiting has been a challenge,” she continues. “Over the last 15 years, the number of applicants is down. More seem to push to (information technology) jobs.”
Despite the challenges, though, Lopez says her team of techs remains fully staffed, with 20 technicians working in 20 service bays in Crown Toyota’s spacious garage, on the south end of Iowa Street.
“We work hard on retention and keeping our people,” she explains, adding that Crown participates in Toyota’s T-Ten Program in Omaha, which allows aspiring techs to pursue a two-year associate’s degree in automobile technology, as well as become fully certified, at no cost to them.
“People’s ears perk up when they find out they can learn on the job without going into debt,” says Jaime Llamas, human resources director at Crown Toyota. “It seems like everything is a bit better now. So many people were affected by COVID. But now, people are getting back to work and getting more comfortable.
“I feel like we’re in a good place, and it’s picking up,” he says.
Twenty years ago, give or take, auto technicians were endearingly often referred to as “grease monkeys.” They’d spend much of their days working power wrenches and wiping equipment down with oil rags.
Today, they might be able to work for NASA. Vehicles have become so sophisticated and advanced, loaded with computers and technology, that having advanced knowledge in programming and computer maintenance is more important than how a carburetor moves gas through an engine or how pistons fire.
Rollie Stallbaumer, service manager for three Laird Noller dealerships in Lawrence, pulls out his smartphone, calls up and shows three full pages listing dozens of computer modules for a 2023 Ford F-150 truck.
“A standard car today has about five miles of wiring,” says Stallbaumer, who has 20 years of experience in automotive technology. “Those three pages of modules in the F-150, that’s just computers.”
Because of the complexity of today’s engines, plus the fact that the technology is always changing, training today’s auto techs is a day-to-day exercise. Stallbaumer says he has two master technicians on-site daily who serve as mentors to all the other techs. There is web-based training every quarter, nine categories in which to be certified and three weeklong courses techs have to pass.
Stallbaumer says there also is EV (electric vehicle) training, which consists of 20 web courses in addition to attending a weeklong training seminar in Chicago.
“They’re training all the time,” he says. “In order to be successful in this business, you have to.”
Lopez similarly keeps her technicians up-to-date at Crown Toyota. She has a Service Quality Specialist, Spencer Hutchens, who keeps up with the newest technology and trains the techs accordingly.
“I’ve gone down to the Plano, Texas, (Toyota) campus and attended classes and seminars (on the latest technology),” Hutchens says. “Also, the manufacturer will send module updates. We do specialized training, a combination of online and hands-on training. And I have a direct line to a Toyota engineer.
“I’ve found it’s actually gotten easier for me,” he continues. “It’s almost gotten second nature.”
Eddie O’Dell, senior master technician at Laird Noller Ford, says, “(Learning is) always going on. If you’ve got five years or 25 years, you’re still learning something new every day. I feel like I’m at a point now where I’m dropping stuff I knew in order to pick up current technology that’s put in these vehicles. It’s a challenge, but it’s exciting at the same time.”
Many, if not most, auto technicians will tell you their love of cars began when they were very young. They helped Dad when he was tinkering with the old family jalopy back in the day and fell in love with engines and what made them tick.
Of course, they didn’t know then they’d have to learn such extensive knowledge of computers and the way they work, and most importantly, interconnect with other modules to make all the systems on today’s autos run smoothly and efficiently.
“It’s a difficult job,” says Zac Carroll, automotive technician at Laird Noller Ford, who grew up working with his dad on his cars and started in the business as a lube tech. “Most people look at it from the outside looking in. I really believe (the job is) more thinking than anything.
“I often make the joke that I’m an electrician, not a mechanic,” he says.
O’Dell adds, “I didn’t think we’d ever be where we are today. A vehicle is a computer talking to other computers in a nanosecond so that everything works.”
Carroll says he’s never thought about going back and doing something else as a trade.
“I’ve been a fan of cars since I was a kid,” he says. “It’s different. I’m looking at a lot of kids my age who are in debt from college loans, and they’re not even finished yet and ready to work. I went to community college and instantly went to work.
“If cars are your passion … I work with my hands,” he continues. “I’m able to single my mind on one task at a time. I honestly think I went down the right path.”
It’s not an entirely rosy picture, however. Carroll points out that in a technology class he once attended, he was just one of two who went on to become automotive technicians.
Stallbaumer says the supply of auto techs since the pandemic has tightened considerably. He currently employs nine techs at the Laird Noller Ford operation and says he could comfortably support 12 to 14. That shortage in techs, in addition to equally tight supplies for parts, leads to longer turnaround times for service and frustrated customers.
“We try to be as efficient as we can with what we have,” he says.
Stallbaumer says he recently spoke to a group of 60 students at a local high school, and only three showed interest in the automotive field.
“Since COVID, it’s changed drastically,” he says. “My opinion is young people today are doing trades, but they’re looking for instant money. In other trades, you can start making money quicker.”
Stallbaumer says he mitigates the tight labor supply by offering starting salaries in the $25- $30-per-hour range with sign-on bonuses, fuel compensation, health care and daycare assistance. He attends career and jobs fairs, and sits on the board at Peaslee Tech.
Although her team at Crown Toyota is fully staffed, Lopez and her team also have had to deal with a post-COVID world where “people are more impatient,” she says.
“We made a commitment to think outside the box to keep the same level of customer service,” she explains. That includes offering more online services as well as sending drivers to pick up and deliver vehicles so that customers can wait from home.
“We wanted people to not avoid service because they were afraid,” Lopez adds.
She’s definitely seen the pool of aspiring auto techs dwindle the last few years. Several decades of the prevailing wisdom being that a four-year college degree can lead to more money is one cause. Car engines becoming so much more complex and technical could be another.
But with the costs of a four-year college education soaring and becoming unattainable for so many, those trends in automotive technician supply could be about to change.
“I think the message is getting out there a lot more now,” says Ryan Wingert, assistant service manager at Crown Toyota. “Most trade schools don’t last more than two years. It’s a great jump-start. If you’re comfortable around vehicles, you can learn at a really fast rate. It’s just a matter of putting in the time and showing you’re committed.”
Wingert points out that industry experts say in 10 years, one-third of all vehicles on roads in the U.S. will be allelectric. That typically means less maintenance since there is no oil moving through lines or pistons chugging through cylinders.
Lopez, for one, doesn’t believe that will lead to marked decreases in demand for service. She points out that even during COVID when people left their cars parked and sheltered at home, vehicles were being brought into the Crown garage constantly suffering from “rodent damage.” That’s right. Mice, squirrels and other rodents climbed into engines underneath the bodies of cars and chewed and damaged wiring, and other auto infrastructure.
“People are still going to need service on brakes,” she says. “They’re going to need air filters, tires rotated. “It’s always changing because of technology. It’s a constant learning environment,” Lopez adds. “But I think the push for trades, including automotive trades, is definitely coming back.”p
Rollie Stallbaumer, Laird Noller service manager, speaking with a clientCollaboration between organizations that employ commercial truck drivers and local tech center keep the community running efficiently.
Douglas County roads carry loads of commercial truck traffic every day. Every single one of those vehicles needs a certified driver at the wheel, so that makes for a lot of local job opportunities that require a commercial driver’s license (CDL).
Standard Beverage Corp. and the City of Lawrence recruit, hire, train and employ dozens of CDL drivers and roll trucks all over the area, day and night. Driving a commercial truck means delivering vital supplies, performing essential jobs and, overall, contributing to improved quality of life for everyone.
Commercial truck driving is the opposite of a desk job—drivers are out and about most of the time and get to know people and places around town. The job requires physical energy and is rewarded with the satisfaction of completing crucial transport for materials and services.
Recent changes to the federal requirements for testing and training for CDLs means that both the City and Standard Beverage have relied heavily on the expertise housed at Peaslee Tech, in Lawrence, to execute and supplement their respective CDL training programs.
It may look like a single vehicle with a driver, but behind and around and all over that vehicle are the efforts of a team—in-house and communitywide.
There are more than 150 positions with the City of Lawrence that require a Class A or B CDL, says Jenny O’Brien, MSO analyst management for the city’s Municipal Services and Operations. Jobs include solid waste operators who drive garbage trucks; water distribution drivers; sanitary sewer collection; streets maintenance crew; traffic maintenance crew; and the garage staff that maintains and repairs all the machines. Many of the jobs have a Monday through Friday work week with varying shifts, but major weather events and other happenings can lead to overnight and weekend work, as well.
Standard Beverage is an alcoholic beverage wholesale distributor across the state of Kansas. The company sells and delivers beer, wine and spirits to licensed customers that include restaurants, liquor stores and bars. About 85 drivers spend either their days or their nights in trucks loaded with cases of beverages, driving routes and unloading their wares at establishments large and small. Daytime drivers deliver the products to stores, while the line-haul drivers take products to bars
Truck and bobcat work together with the City of Lawrenceand restaurants at night, says Carl Wettstein, director of transportation and day operations at Standard Beverage. Drivers work 10-hour shifts, four days or nights per week.
With so many positions to fill and keep filled, both O’Brien and Wettstein are continually in the process of recruiting and training new drivers. As if that isn’t challenging enough, major changes happened at the federal level in 2022 that have forced the City and Standard to outsource portions of their training. Thankfully, Peaslee Tech is here and at the forefront of the changes for these entities and others in the area. Wettstein and O’Brien say they don’t know what they would do without Peaslee as a place to save time and money for up-and-coming CDL drivers.
When the Federal Motor Carrier Safety Administration issued new guidelines for Entry-Level Driver Training (ELDT) in February 2022, that brought watershed change to how new potential drivers had to study for, prepare for and train to take the CDL exams. The new ELDT regulations set a baseline for entry-level drivers getting their Class A or B CDLs for the first time. Potential drivers cannot just show up to take the test; rather, they now must have proper entry-level training and show specific evidence of that training before they can sit for the CDL exam. Peaslee provides the theory class and the behindthe-wheel road-and-range training for the CDL exam, and manages the driver’s information in the federal registry on behalf of the City, Standard Beverage and a roster of other local companies.
Typically, employers provide potential CDL drivers a certain amount of time, usually a couple to a few months, to prepare and train for the exam. Employers will supplement the truck driver training with training specific to their operation, such as learning mechanical aspects of the particular vehicle or general information about the work the company does.
“Working with Peaslee Tech is just amazing. We can send our new hires there for online training, and that covers the registry requirements; plus, Peaslee keeps the registry. They are a third-party evaluator that is certifying that our people have been completely trained. That gives us an extra set of eyes on our training processes,” O’Brien explains.
The full training period for a City driver ranges from six months to a year, depending on the job, so there is extensive effort for and investment in the drivers before they are even working the job on their own.
“Since we have partnered with Peaslee, we send new employees to Peaslee with the truck and trailer for onsite training. We pay for them to obtain their license and medical card. With Peaslee, the drivers don’t have to go to a separate driving school, which can cost them $4,800 to $5,300 out of pocket. We can get a driver trained for $1,000 to $1,500 at Peaslee, and they earn a paycheck and train at the same time,” Wettstein says.
Because there is so much money wrapped up in training and licensing, Wettstein says they typically sign their entry-level CDL drivers to two-year agreements.
In short, commercial trucking jobs are varied, active and important.
“These programs have a high level of trust,” O’Brien says. “Our field crews and solid waste crews are our eyes and ears in our community.”
She says young people regularly report that it matters for them to have importance in the work they do every day; CDL driving serves that purpose. The jobs are also physical jobs that keep people physically fit, and drivers work in teams with tight-knit groups of people and crews that depend on one another for their safety.
One solid waste crew received an award for heroism recently because, while on their route, they spotted a house fire and were able to notify the occupants and get all of them out safely. The City’s commercial drivers may also have additional duties that can strike at any moment thanks to Mother Nature. In the winter, if there is a snow event, O’Brien says all field staff participate in snow removal. If the snowfall is more than 6 inches, it is “all hands on deck,” where all drivers pivot away from their usual duties and help install plows on trucks, load road salt onto distribution vehicles and hit the road in those vehicles.
Kyle Rodecap has been a commercial truck driver for 13 years, the past four of which have been with Standard Beverage. He works as a daytime driver for Standard and previously worked for what is now known as Keurig Dr Pepper, formerly Dr Pepper Snapple Group, in Topeka.
He chose to work for Standard because a friend who works there who told him about the company.
“The big thing for me is that I was driving six days a week at Dr Pepper, but it’s just four days a week at Standard. It’s better for my life with my wife and family—started off at Standard with an extra 104 days off per year [two days times 52 weeks],” he laughs.
Rodecap drives the same routes to the same stores each week, so he likes that he gets to know his customers and see them regularly.
“It’s a good job for me because it’s not the same monotonous thing every day,” he says. “And I like building the relationship and dealing with the same customers. I want them to be like, ‘Oh good, Kyle is here.’ ”
Rodecap likes the team aspect to the work, as well. Drivers help one another out if one driver is running behind on his or her route because of mechanical or other problems. “Even a flat tire can set you back a couple hours,” he says. And knowing that willing help is on the way is a win for everyone.
He also works as a trainer for the drivers at Standard, something he says is satisfying and gives him a lot of pride. “When I get a good driver that goes out and excels, I tell them that I want them to go out and be better than me,” he says.
Wettstein says Standard’s driving positions became fully staffed within the past nine months or so, which he considers “pretty fortunate.” Standard remained operating at full capacity during the pandemic, when demand for alcoholic beverages was high, but he says there was 30-percent turnover during that time. The company will not let up on recruiting efforts, though, because the training pipeline is minimum a couple of months for even experienced drivers. He says they are continually accepting online applications. With competitive pay, the four-day work week and many other incentives and rewards built in, there are lots of reasons to drive for Standard, Wettstein says.
O’Brien says the City has a lot of competition for filling its CDL jobs. With the Kansas City area becoming more and more of a logistics hub, CDL drivers have a lot of options in front of them. Entry-level pay for field operator positions with the City is $20 to 23 per hour, depending on qualifications, she explains. “Our benefits are stellar. People with families get great family benefits,” she adds. And there is ample opportunity for promotions and career advancement.
“These jobs are essential to the community—they are absolutely essential. Our water distribution crews are fixing water mains, and our trash service is about public health. It makes our community livable,” she says. p
Interest in jobs such as welding and carpentry is on an uptick because of job security, the high cost of a college education and the possibility of getting a good-paying job while remaining debt-free.
At the Dwayne Peaslee Technical Training Center, where Kevin Kelley has been CEO the last 5½ years, business is booming. He estimates the training center, best known as simply Peaslee Tech, has 3,000 “duplicated” enrollments (meaning some individuals are enrolled in more than one program) throughout its 31 programs and apprenticeships, which cover everything from the aforementioned welding and carpentry to heating/air conditioning (HVAC), electrician training, robotics and commercial driving. That level, he says, is as high, if not higher, than prepandemic enrollment levels. Many of the training center’s fall classes are already filled.
And interest only seems to be picking up. The high cost of traditional four-year college today and skyrocketing levels of student debt have chipped away at the long-held belief that traditional secondary education is the best way to get ahead and have a prosperous future.
Could it be that trades are the next big thing?
“Since the pandemic, people have realized there are other ways of making a living,” Kelley says. “The thing is, during the pandemic, it was our workers who were essential workers.
“We’ve seen a lot of career changes from the hospitality sector to building trades. The demand is so high for people with skills: pharmacy technicians, medical assistants, court reporters,” he continues. “Electricians, welders, plumbers, HVAC—all are in super-high demand.”
Kelley is quick to point out that Peaslee Tech is not a school but a training center. Because of that distinction, it doesn’t participate in student loan programs. In fact, Kelley says no one gets turned away because they don’t have money to pay for a course, which on average runs around $2,500. Peaslee Tech relies on private donors, government grants and other gift programs to cover costs for students of limited means. Therefore, students can’t leave there with debt.
photos by Steven Hertzog“The beauty of our model is, we don’t give grades,” Kelley says. “We teach people what they need to know and let outside parties (certification organizations) validate the teaching and learning.”
What Peaslee Tech is doing appears to be working, he adds, as those achieving successful certifications after completing programs is well greater than 90 percent.
Kelley says he has one electronics program that runs four years. In contrast, there is a pharmacy technician program that runs four weeks. Most students work while attending classes. If one is enrolled in an apprenticeship, they’re required to be a fulltime employee.
The most popular trade program, by far, Kelley says is the commercial driver’s license (CDL), which provides individuals certification to drive big-rig trucks—18-wheelers. The course consists of 160 hours of training, including 90 behind the wheel. What makes Peaslee Tech’s program special, he adds, is that each student is assigned one instructor and one truck from which to learn. Peaslee Tech has six big rigs available for training.
“Like most of our programs, it’s a performance-based program, so students can complete it in less time if they meet the benchmarks,” he explains.
Bryson Korir, a native of Kenya, says it took him “about five weeks” to complete his commercial driving license and was all smiles knowing he’d taken an important step in securing a better and more prosperous future for himself and his family.
“I’ve been driving a box truck for two years,” Korir says. “I saw this program (at Peaslee Tech) and saw where I can advance. It’s becoming an in-demand profession. The pay is good. You get to move around while you do your work and get paid.”
He says his dream is to one day own his own truck and operate his own business. And that, Kelley says, is what Peaslee Tech is all about, giving people the needed skills to one day realize their dreams in whatever field or trade they choose.
Along with CDL, some of the most popular trades people are choosing these days include HVAC, welding, carpentry and robotics.
Perhaps it’s more than coincidence that an instructor in heating and air-conditioning describes interest in the program as running “hot and cold.” But Riq Quinteros, who’s worked in construction and with machinery most of his adult life, thinks the field in which he teaches could be about to blow up.
“A lot of people of modern generations don’t seem to be mechanically minded,” says Quinteros, who learned to teach trades in a four-year program at Pittsburg State University. “A lot of them don’t understand that there are trades and what different trades do.
“But once they find out, they’re all in,” he adds.
Quinteros says his program consists of 40 weeks, with many nine-hour days—one hour of lecture and the rest lab time, where students take apart and rebuild heating and AC units, learning the ins and outs of the mechanisms.
“They’ll have a completion exercise and then a second-party certification,” he explains. “There are some who come to us who already know a lot and some who don’t.
“The ones that stick around will be great techs,” Quinteros says.
Eighteen-year-old Chris Howard recently received training in Quinteros’ HVAC class while concurrently honing his skills in his full-time job with Dunco Heating and Cooling. While many of his peers are wondering what to do after high school or sinking money into college, Howard says it’s been nice to be earning good, full-time pay at such a young age.
“At first, I wasn’t into trades,” he says. “I’d always been lazy. But I knew they pay well. Now I love it. I like all the guys I work with. It’s busy, but I’m helping people.”
Much like the automotive tech industry, HVAC and plumbing are trades that constantly are evolving and changing, forcing technicians to constantly learn and adapt.
“Nothing in my class is done for nothing,” Quinteros explains. “Everything is done with a purpose.
“HVAC is not just a job. It’s a way of thinking. But if you take care of the trade, the trade will take care of you,” he says.
Kelley need only glance at the enrollment trends in Peaslee Tech’s welding courses during the last year to know it is one of the hottest trades in the marketplace.
“We doubled our numbers over the last year in welding,” he says.
David Youmans, who works full-time for a scrap metal company in the Kansas City area and is an adjunct welding instructor at Peaslee, agrees that the current trend in demand for welders is up.
“From what I’ve been told, in the early 1970s, community colleges and trade schools were full,” Youmans says. “Then it started to drop. Schools started pushing more four-year college tracks. While that’s fine for some people, it’s not for everybody.
“Now more people are coming back into it,” he continues. “I work with industrial accounts every day, and every day I hear companies say everybody needs welders. There are a lot of jobs, and a lion’s share pay well.”
Youmans says entry-level salaries for welders typically range from $17 to $22 per hour, while an experienced welder can make $26 to $28. Welders also typically can work a lot of overtime and receive production bonuses.
Peaslee Tech’s beginning welding course runs 14 weeks, meeting for four hours on Tuesday nights. On a recent summer evening, Youmans lectured seven students on topics ranging from LASER (Light, Amplification by Stimulated Emission of Radiation) welding, water pressure welding and push versus pull beads.
“I try not to spend more than 30 minutes at a time in the classroom,” he says, before moving to the shop where students don their protective masks and practice making welding beads. “They’re usually chomping at the bit to arc and spark.”
One of Youmans’ students, Bryce Phillips, grew up on a nearby farm, where he was introduced to welding at a young age.
“I just thought I’d try it out,” says Phillips, who drives a forklift for a local plastics company. “I enjoy it. I’ve definitely learned a lot more about it here.”
Youmans says he’s seen a uptick in interest in welding among women in recent months. He’s had two females in each of his last two terms.
“My dad used to be a welder,” says LeStat Wilson, a student in Youmans’ class this summer. “I’d see him working in his shop when I was about 9. Ever since I saw that, I’ve had an interest in welding. I started welding when I was about 12.
“It’s a good alternative (for a trade), especially when you have family helping and a job helping pay for this,” she adds.
Wilson says it will take her three class terms to complete her training, but she should be ready for a fulltime welding job by the end of the year.
“Knowing that I’m more marketable … ,” she says. “It’s a good feeling knowing that a lot of people need welders.”
In fact, Youmans says if welders can’t land a job in the current economy, it’s because they don’t want one.
“This is a great option if you don’t want to go to college or go into debt,” he says. “There are plenty of jobs. If you’re a trained and skilled worker, and not working in this economy, it’s probably because you don’t want to work.”
It probably should come as no surprise that trends in the job market for anything relating to automation are on the upswing. It only makes sense that, as more and more of people’s daily lives become connected to automation at some level, demand for such services and those who provide them would increase.
Ed Keating, who’s taught the last six-plus years in manufacturing automation systems at Peaslee Tech, has seen this demand skyrocket in recent years. As a result, he says interest in his automation and robotics courses, at Johnson County Community College as well as Peaslee Tech, have increased dramatically, as well.
“Everything is getting more technical,” Keating says. “You need more people to support that.”
He says U.S. manufacturing is on the rise because of political instability in foreign countries, inability to control quality at remote locations and logistic delays, which will lead to increases in employment. At the same time, manufacturing here is growing more complex, driven by the need for real-time production data (inventory management, maintenance management), the need to coordinate real-time scheduling across multiple manufacturing plants and the need to integrate data from the plant floor to corporate planning systems.
Because of that, Keating says much of the training he provides at Peaslee Tech revolves around integration of various automation systems—becoming a proverbial jack of all trades. The more one knows, and the more flexible one can be moving from one system to another, the better.
“In automation, there’s a lot of integration,” he says. “You take an IT (information technology) person and make them electricians or take an electrician and make them an IT person. Lately, it’s been the latter.”
Keating says his programs typically contain about 40 hours of basic training with programmable logic controllers (PLCs), another 40 hours with an advanced controller, learning to go into a system and change code, 24 hours with a variable frequency drive, 25 hours on integration and 15 hours on an operator interface terminal.
“Peaslee is directed more to plant electricians, the more practical side,” he explains. “I have a teaching philosophy that I’m going to have every student come out of class with a basic working knowledge.”
Keating says he expects the field to continue to grow.
“People are realizing a four-year degree doesn’t guarantee financial security,” he says. “You can make as much (in an automation systems trade) and not go into debt while doing so.
“I see it as a growing field,” he adds. “The needs are going to keep growing as technology continues evolving.”
Jay Hundley says the supply of students coming to his classes wanting to learn to be carpenters and woodworkers runs hot and cold, and he should know. Before retiring and taking a job as a carpentry/woodworking instructor at Peaslee Tech, he worked as a high school woodshop teacher for 33 years, the last 21 at Lawrence High School.
“Overall, it’s stayed about the same,” Hundley says regarding interest in the trade. “Sometimes, you fill a class easily, but then only about half actually show up to take the class. Some sign up and are gophers on construction sites, and they don’t realize the time it takes and don’t last.
“A lot of students are older men and women trying to get remodeling skills so they can complete work around their houses. It runs the gamut,” he explains.
Anytime there’s a new technology that pops up, Hundley says older, traditional trades such as carpentry take a hit. After all, he says, carpentry is more physically laborious and often pays less than newer trade jobs like IT. Work is often done outdoors in poor conditions like rain or excessive heat or cold.
“Woodshop just is not sexy,” Hundley says. “Everyone knows what it takes. Physically, you’re going to live longer if you don’t do it. Construction is hard on you.”
That doesn’t mean Hundley is giving up on the trade that’s made his working life. Far from it. He says he combats negative perceptions of carpentry “one student at a time.” In the meantime, he instructs his Peaslee classes, which he says number 14 to 16 students to start, five to 9 by the end, with basic knowledge in rough framing, wood studs, installation of doors and windows, siding, building stairs, roofing and Sheetrock.
His last class in the spring built a tiny home inside the spacious woodshop at Peaslee. Once complete, the house will be moved onto a trailer and transported to a nearby Lawrence neighborhood to serve as low-cost housing.
Hundley says his class this fall will build the same thing and will use high school students from all around Douglas County.
“We have one or two already signed up,” he says. “I hope to get eight to 12, maybe even 15.”
Hundley says 90 percent of his courses take place in the shop. There’s very little in the way of classroom lectures. “Most students in my class hate sitting in a chair and listening to a lecture,” he says. “I want to get them out working in the shop as soon as possible.”
That way, he says, students will gain basic skills that always will be in demand no matter where technology takes us next.
“There’s always going to be a need for carpenters,” Hundley adds. p
Though many skilled trades such as plumbing are taken for granted in our daily lives, when something goes wrong, you bet you’re going to be begging for a plumber’s help.
Picture this: The time is 11:43 p.m. on a Sunday evening. The family has been in bed for an hour and a half. Suddenly, everyone is woken by a scream. After discovering the human alarm was triggered by the pipes backing up, you realize there is nothing you can do. Who do you call? If you answered the plumber, you answered correctly. What would we do if we lived in a world without plumbing and plumbers? It would certainly be a different landscape. These hidden internal systems most of us take for granted in our daily lives are convenient and keep us comfortable while bringing one of the most important resources straight into our homes and businesses.
Skilled trades such as plumbing, while seemingly simplistic and many times overlooked, can be a serious challenge. As long as plumbing and pipe systems exist, we will need skilled tradespeople in plumbing and pipe fitting. Plumbing is the network of pipes and other elements like tanks for holding and connections that bring our water supply into our homes, schools and businesses for heating, sanitation and drinking. Paul Bost, owner of Jim Bost Plumbing, explains: “Pipe fitting are things that are threaded together, like gas lines, boiler systems, high-pressure systems and industrial/commercial.”
While many of today’s careers may vanish in the years or decades ahead, talented tradespeople will always be in demand wherever you go, explains Dan Beal, president of McElroy’s Inc. For many years, there has been a decline in skilled labor for occupations such as plumbing and pipe fitting. One reason for this is the focus placed on going to college instead.
Freedom to get the best seats for the show.
WE LISTEN TO YOUR DREAMS and then find ways to minimize the burden of wealth management, bestowing the freedom to enjoy everything else. Visit us at tckansas.com.
Recently, there has been a push to encourage people to reconsider applied technologies and skilledtrade positions. From a purely practical standpoint, communities need skilled labor. This, of course, does not diminish the need for higher education through colleges. Beal, who has a master’s degree in mechanical engineering from The University of Kansas, states, “I understand there will always be careers that require a college degree. Even so, more and more educators are realizing the trades offer outstanding careers for young people who like working with their hands and who enjoy making things people need and depend upon.”
McElroy’s is developing strong ties with area high schools to help students discover the valuable opportunities that best suit their desires, he adds. “Considering that tradespeople get paid to learn on the job from skilled mentors, careers in the trades make a lot of financial sense, too.”
There are many reasons for individuals to get involved in the trades. Joe Bradshaw, owner of Blue Duck Plumbing, says one way to get involved as a plumber is to create a résumé and apply to a plumbing company directly. “Another way to better your chances of being sought by a plumbing company,” he says, “is to go to a technical school, and while you are going to school, start applying.”
When he was starting out, Bradshaw worked in a variety of trades, including as a maintenance man, engineer and teacher, before settling on plumbing. “Several things attracted me to plumbing: the challenge and adventure of the work, the stability of the field, and the pay is good,” he says. He also acknowledges that, “College costs in time and money, whereas in plumbing, you are paid while you learn. In Kansas, it takes about two years to go from an apprentice to qualify to test for journeyman status.”
He says in recent years, he has seen the quality of candidates for plumbing im prove significantly. And Bradshaw be lieves in vocational training in education. “This is a great opportunity for the com munity to prepare many of its younger citi zens for successful careers. I am pleased with Peaslee Tech and have hired several people from their classes. We need more such help in the area of vocational train ing.”
Bost agrees that Peaslee Tech is a good local school. The focus of high schools to send kids to college has caused the trades to be “grossly understaffed.” He says he believes the easiest way to get into the plumbing business is to call plumbing contractors and see if they’re hiring. “A lot of business owners would rather hire a person that has no experience so they can be trained how that particular contractor likes to plumb.”
Bost’s path to plumbing was generation al. His father started Jim Bost Plumbing in 1983, and he grew up with a tool belt and “spent summers on job sites.” When asked about changes in plumbing, he explains, “The plumbing industry has changed a lot in the last 50 years. Safer practices, better materials and technology always help advance the trades. Technology is really the leading factor in making plumbing systems more energy efficient, better for the environment and easier to install; but sometimes, technology gets in the way and makes some things more difficult to repair.”
Blue Duck’s Bradshaw agrees that technology has drastically changed the plumbing profession. He points to how different pipe materials have come along and replaced old materials. “Cast iron was replaced with PVC; Copper with PEX (cross-linked polyethylene); PEX with Type A expansion PEX; pipe-bursting sewer line replacement to replace sewers with just two pits using butt welded HDPE; CIPP (cured-in-place pipe) lining of sewer lines.” He says about new tools and their uses, “Sewer cameras, location tools that allow one to tell on top of the ground where the camera is in the sewer pipe and how deep it is; thermal-imaging equipment to find leaks under slaps; com-
pression tools that replace soldering; flex shafts and jetting machines to clear sewer lines—the list goes on. It is amazing how many new plumbing inventions have been developed in the last couple of decades. It is exciting to see what will be invented next.”
Matthew Wingert, who represents the Plumbers and Pipefitters Union Local 441, also had a family connection for a career in plumbing. He says, “I am a fourth-generation union pipefitter. So going into apprenticeship straight out of high school is what I considered normal. But speaking generally, I don’t know that there is a specific path for anybody interested in the pipe trades.” He says all are welcome to apply to the apprenticeship program then move forward to the math testing and interview process. The “barrier,” in his opinion, would be potential apprentices and members not being aware of the option of being a union tradesperson and the benefits that come along with it.
Wingert explains the benefits of being involved in skilled trades through the union are substantial. “Many adults are carrying some form of student loan debt. Whereas a person out of high school becomes a union apprentice and graduates five years later with no student debt and making around $85,000 annually at today’s wage rate. A message I always try to convey to young and/or new apprentices and potential future members is: Work hard, and you are guaranteed to go far. It is very simple. You get out what you put in.” And if you can manage that, you will be assured of three things: an excellent hourly wage, provided health coverage and the ability to retire with dignity, he adds. “A common theme amongst all unions regardless of trade.”
Wingert also points to the union as leading the way for fair wages. “[Unions] typically set the prevailing wage/DavisBacon wage rates for the state, which means unions set the bar for wages in their respective markets.” Another benefit through the apprenticeship programs is called “transferring,” which allows a journeyman to travel for work or transfer to another local if he or she were to move to another state. Not only can they pick up where they left off in another state, but “the benefit package would kick in upon the transfer and starting work in the members new local, all the while still contributing to the same national pension plan,” he says.
McElroy’s has been in business for more than 70 years and is a union contractor. President Beal says, “We hire union technicians who take great pride in the quality of their craftsmanship and their dedication to serving the customer. We
do our best to treat all of our team members like family, making them feel seen, appreciated and valued. As a result, we have employees who have stayed with us for 10, 20, 40 years and more.” He says McElroy’s has hired many technicians who have developed skills at area trade schools like Peaslee Tech in Lawrence and Washburn Tech in Topeka. Area high schools often help students connect with technical college classes as juniors and seniors, which is a great time to learn whether a trade career is right for you. Tech school skills increase a person’s odds of getting hired and can make their path through union apprenticeship easier.
Whether a plumber is a part of the union or are independent, it seems there are many overlapping reasons a person would choose the path of applied technologies or skilled trades. Jim Bost Plumbing owner Bost says, “... college is not for everybody. You can make a very good living and provide a very good life if you enjoy working with your hands and fixing things. And that doesn’t have to be plumbing.” He explains that it could be HVAC, a mechanic, an electrician, anything that takes a skill set. “But you have to be willing to work for it and take pride in what you do.”
There’s going to be a point in the very near future, he continues, when tradesmen who are skilled and do high-quality work will be able to “write their own check,” meaning the workforce will not be there. “They will be able to pick and choose what they want to do, and be able to charge whatever amount they want, because there won’t be the workforce to support competition, and that’s kind of scary.”
If you are hard-working, enjoy working with your hands and have the willingness to learn, applied technologies or skilled trades may well be a career path for you to consider. Beal says, “... plumbing and pipe fitting is a very satisfying career. When a homeowner or business owner has a plumbing crisis, a service plumber can save their day.” Plumbers and pipe fitters working in new construction have the satisfaction of helping build the plumbing and piping systems that homes and businesses rely upon, he continues. McElroy’s does a lot of work in the medical and science fields, and in those environments, the complicated piping systems skilled craftspeople create can actually save lives. However, if plumbing and pipefitting don’t describe your interests or skills, we can be thankful that many others are making this choice. “When the pipes are backed up, the sink is dripping or another plumbing issue unfolds, we have the ability to make a call to our local plumber and get the situation corrected quickly.” p
Speaking with anyone in the electrical business, you’ll soon discover that whether their focus is on residential, commercial or industrial, the people running the businesses and working for them have a sense of curiosity and a desire to learn. While the basics, such as running cable, haven’t changed much over the decades, the technology has evolved quite a bit, and it’s a constant circuit of learning about new things, learning how to implement those things and then getting them implemented.
“One of the interesting things about being in the electrical trade, in my opinion, is there’s always a new product that could more benefit our customers in some way, whether it’s greater utility or use, or better cost savings for them without compromising on quality or safety,” says Malcolm Proudfit, CEO of Good Energy Solutions (GES). “You’re constantly having to learn and evolve, and keep up and go to trade shows, and communicate with vendor reps and this and that. This doesn’t stop.”
Good Energy Solutions was started in 2007 by owner Kevin Good, with the business’ focus on solar and renewable energy. During the course of those 15 years, they’ve been in the business of installing solar systems for both residential and commercial properties—churches, homes and businesses— along with having been contracted by Evergy to install solar farms on its grid.
Seven years ago, Good Energy Solutions acquired electrical contracting firm JJ’s Electric, along with the expertise of the company’s owner, JJ Willems. It’s now grown into the second division of Good Energy and has a team of 16, as well as multiple millions of dollars in annual revenue. The Good Energy Solutions’ total employee count is about 45.
“We’re glad to have them on board,” Proudfit says of Willems, explaining that solar and electrical contracting work go hand in hand. “Sometimes we have customers that want to get a solar system, but solar feeds into your main breaker panel through a breaker. If you don’t have the room on your panel—if it’s only 100 amps—you got to get a 200-amp panel. Then our solar team will actually have the electrical division do that main panel upgrade, because they’re so much better at it. There’s a lot of complementary skills there.”
Spacek, photos by Steven HertzogThose complementary skills aren’t just between divisions in one company but can be found within singular people, as Patrick Brooks, president of Brooks Electric, explains from his view of the electrical industry after 40 years in the field.
Brooks Electric been in business for 25 years, and it specializes in commercial and industrial wiring, along with a small amount of residential service work. Along with Brooks and his wife, Susan, with whom he co-owns the business, the company has 11 employees.
“Technology has gotten a lot better, and those are things that we have to learn as we go,” Brooks explains. “But being an electrician, you got to learn as you go anyway, because the rules change every three years. Materials change. People’s understanding of how materials have changed to install has also changed. Speed on computer cabling has increased. It’s all changed.”
Keeping up with those changes means that for those who run these businesses, they must remain up-to-date on the latest industry news, while also hiring people who are of the same mindset. GES’s Proudfit sums up what the electrical business needs in an employee: “It’s an industry for people who love to stretch their brain and give themselves a challenge on purpose,” he says. “We, as humans, tend to just take the easy road most of the time, and that’s not the way of the electrician or the plumber, or any tradesman.”
Brooks agrees, saying those who are looking into joining the industry might want to know they’ll be working in heat and cold, hanging from a ladder and required to do a lot of math.
“A lot of math, a lot of math,” he muses. “It’s not just A plus B-type stuff. You got to know a little bit of trig and algebra a little bit. Takes quite a bit of science.”
Brooks says recently, the company was searching for why some LED lights were flickering, and they finally noticed there were surges every time the air-conditioners came on. “It surges the electrical wiring, which makes the lights flicker. That’s science. You gotta know what’s happening, and you learn that by being observant and aware of a lot of different things. It’s a really neat occupation, and it takes a lot of thought, especially if you’re troubleshooting.”
Given the sheer number of electronic devices out there these days and the number of kids being raised on them, one would
businesses grow for over 80 years.
▸ High Yield Business Savings
▸ Real Estate & Construction Loans
▸ Commercial Lending Team
assume there’d be a healthy number of young people looking to take over from those looking to retire. But that’s unfortunately not the case. According to an NPR “Your Money” story from January 2023, “The application rate for young people seeking technical jobs—like plumbing, building and electrical work—dropped by 49% in 2022 compared to 2020, according to data from online recruiting platform Handshake.”
“I’m just shocked by how few students are going through that type of program,” Proudfit laments. “I’ve sat on the advisory board over at Johnson County Community College for a while in their electrical technology school, and they probably put 40 or 50 students through that program annually.”
He compares this to when he was going through business school when there were a thousand students in his economic program graduating in any given year, with the same number in his master’s program.
“There’s just not enough focus on becoming a tradesman or learning a valuable skill like that,” the GES CEO continues. “It’s not like you couldn’t go out into the field knowing how to be a plumber or an electrician, or anything like that and make six figures. You certainly could, and people do it every day, all the time. I think that’s a stigma that still needs to get resolved in the minds of young high school graduates.”
As Brooks explains, being an electrician is a solidly stable career choice. “I’ve never been out without a job for one day. Even if you aren’t working for just a short time period, somebody’s always looking for a little extra work.”
Both Brooks Electric and Good Energy Solutions draw from schools such as Peaslee Tech, Johnson County Community College and Washburn Tech, and both Brooks and Proudfit recommend those interested in the trades take a few classes as a good baseline before considering applying for jobs. That being said, it’s not just something that appeals to those just out of high school, and there’s a glimmer of hope in that, Proudfit says .
“Initially, when I was making hires in my first year or two here at Good Energy Solutions, it was mainly folks straight out of an electrical technology program or someone coming from another firm with that experience that we were looking for,” he explains. “But we’ve always been happy to train if we were going to hire someone who’s a blank slate, so to speak. We’ll train you up if you’re willing to put in the work.”
In the last year or two, many people have come in to apply looking to reinvent themselves or make an industry change, Proudfit continues. From car salesmen to concrete workers, and graphic design artists to videographers, they’ve all come in to try something new. And what they bring to the industry is a can-do attitude and a fresh perspective. One of those folks is Good Energy Solutions’ Joe Cottin.
Cottin grew up working in his parents’ store, Cottin’s Hardware & Rental, 1832 Massachusetts St., in Lawrence. After high school, he decided on food services as a career for the next two decades. During those 20 years, he worked for KU Dining, Free State Brewing Co. and most of what he refers to as the “high-volume restaurants in Lawrence.” He went from line cook to shift manager to sous chef.
“I’ve never been a head chef or an executive chef, but that would’ve been the final step as far as my career would’ve gone,” Cottin reflects of his career in that industry. A couple years ago, he came to a point where he needed to make the decision whether he could—or even wanted to—become either an owner/operator or partner of someone who wanted to open up a restaurant, he continues.
“It started making less and less sense to invest all my time and effort into it,” Cottin laments. “The effort that I would have to put in and the amount of financial backing required to get to that highest level of earning, it just seemed unfeasible to me to try, because most restaurants do fail.”
Most of the head chefs and executive chefs for whom Cottin worked in the past sacrificed everything in their lives to be successful. But with Cottin at the point where that was not going to meet his definition of success, the now-electrician looked at other industries he felt capable of entering, which had a much higher ceiling as far as effort versus reward.
“I had always been interested in the trades,” Cottin says of his eventual choice of new career. “My dad, as I was growing up, he would buy a house that was all run down and, while we lived there, he would gut it and repair room by room. When I was little, it would be like, ‘OK, go into this crawl space and pull these wires.’ And he showed me when I was 12 or something how to wire a receptacle. I had that entry-level understanding and confidence in my abilities to do it.”
In addition to not wanting a desk job, he was particularly interested in the green elements of the electrical trade. In his mind, the future of energy was going to be more about technology and sustainability, so it seemed to him like a field that would just keep growing and expanding.
“I’m 39 now, and starting a new career at 38 was definitely not something I thought I would be doing,” Cottin explains. “It just seemed like a really interesting field to me and something that I had enough basic understanding of to think that, even in my later-in-life point, it seemed to be within my capabilities.”
While Cottin’s time in kitchens did not prepare him for the day-to-day activities of electrical work, the soft skills and intangibles of his prior career path certainly put him at an advantage. Working in high-pressure situations, uncomfortable temperatures and somewhat dangerous environments where one has to be very conscious of his or her surroundings were all things with which he was quite familiar.
“No one needed to be looking over my shoulder to make sure I didn’t mess something up,” he explains. “It just became a point where all I had to do was show up to work and absorb as much knowledge as I could from the master electricians and the journeymen.”
Once they saw that Cottin was willing to learn, it became very much a case of, “Here’s how you do this. Now let me see you do it,” he says. “At 38, I’m not trying to go to community college at night while I’m doing this, so it’s something that I have to spend a lot of time outside of work training myself, learning the code book and researching different techniques and different safety precautions, and things like that.”
The mentor/mentee relationship is an important one in whatever career path someone might choose, but it’s especially
important within the electrical industry, says Robert Bausch, business manager for the International Brotherhood of Electrical Workers (IBEW) Local Union 226.
“With our apprenticeship programs, you’re underneath a journeyman at all times,” Bausch says. “In other words, they’re responsible for training you, teaching you and keeping you safe. Obviously as you get farther into your apprenticeship, you’re given more responsibilities, but you’ve got a mentor there every day that you’re at work.”
From there, he says, you pass it along. Bausch has even taught some continuing education classes along the way, explaining that the concept of mentorship and being there to answer questions continues even after you’ve gotten off work. He reconfirms what Brooks, Cottin and Proudfit have all said thus far: Learning is key to being a successful electrician.
“I sit on the board of Washburn Tech … and it’s good beginning training,” he explains. “But again, the trade’s so diverse, one year’s just not enough for those guys to pick up enough to be proficient at all of it—or any of it, for that matter. Just enough to kind of get their feet wet.”
When Bausch topped out of his apprenticeship, he traveled, going to California and Illinois and Massachusetts, some of it by choice and some of it out of necessity. But the thing he points to is that thanks to a solid apprenticeship through the IBEW, no matter where he went, the training he received made it so there was nothing he couldn’t do.
“You can’t see it all, right?” Bausch says. “The trade is so vast that you’re never going to master all of it, but you master enough to know that you can work yourself through any part of the trade that maybe you haven’t seen.”
That’s why the IBEW matters, too, he continues. It’s harnessing the power of the group to make the individual’s position and standing stronger than it would be on his or her own.
“This is probably more of a broader spectrum of labor and construction labor, but would you have a voice?” posits Bausch about the absence of a union, pointing to the fact that there are trade organizations for the companies that employ the electricians and represent those companies, and make their collective voice heard all the way up to the legislative level.
“As workers, we don’t have that unless we have a union to do that,” he explains. “Whereas with a group voice, we have much more power—at least at the table—to talk about the issues that affect us on a daily basis, whether it’s safety or having a job that just can’t let you go because they didn’t like the color of the shirt that you wore that day.”
When job safety is ensured, then electricians can concentrate on learning and expanding their knowledge, which makes them happier better at that job.
“I do enjoy showing up to work and getting to learn a lot, which is something that started falling off in my previous career,” Good Energy’s Cottin says. “I got into the mode of, ‘I know pretty much everything I can learn,’ and just showing up and doing the routine became very draining. … I didn’t see a great future in it.”
With electrical, there’s always new stuff to learn, he adds. There’s always new technology coming out, and if he gets bored doing residential, he can switch over to commercial or start installing security systems.
“There’s always a different avenue to go down and learn and advance in, and I don’t really see that dying off anytime soon,” the former kitchen employee says. “I’ve learned so much in the last year doing it that I feel like I’m just scratching the surface, honestly.”
While Cottin’s only been at it a little over a year, the 40-year veteran president of Brooks Electric agrees.
“It’s fun for me to try to figure something out and make it work and make the lights go on or the airconditioning come on in the summer,” Brooks jokes. “People really like you when you bring the air-conditioner back on. You’re very popular.” p
The City of Lawrence is pleased to announce the recipients of the 2023 Phoenix Awards. The Phoenix Awards recognize outstanding artistic achievements in the Lawrence community. Biennially, the Cultural Arts Commission asks for nominations from the community to recognize exceptional achievements in the arts. Due to the pandemic, this is the first year since 2019 that the Phoenix Awards program has been implemented.
This year, the Cultural Arts Commission recognized the following six awardees:
• Cider Gallery, awarded for Creative Spaces in the Arts - Nominated by Tiffany Hall, Lawrence Chamber of Commerce
• Indigenous Community Center, awarded for Creative Spaces in the ArtsNominated by Felice Lavergne for Lawrence Transit
• Heidi Gluck, awarded for Musical ArtsNominated by Brad Allen
• Mike Jones, awarded for Musical Arts Educator - Nominated by Tim Metz
• Regana "Rita" Rials, awarded for Social Justice in the Arts - Nominated by Derek Kwan
• Richard Renner, awarded for Performing Arts - Nominated by Larry Carter
The Cultural Arts Commission received many qualified nominations for this year's awards and was honored to select this year’s awardees as exemplary representatives of the Lawrence arts community.
The Phoenix Awards will be presented by Mayor Lisa Larsen at the 2023 Phoenix Awards reception and ceremony, which will be held at 4 p.m. on Sunday, October 15 at Theatre Lawrence. The event is free and all are welcome to attend. Curtis Young, the new director of the Kansas Creative Arts Industries Commission, will provide keynote remarks.
All of this year's awardees will receive awards created by local artist Toni Brou.