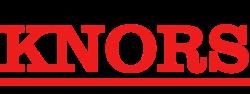
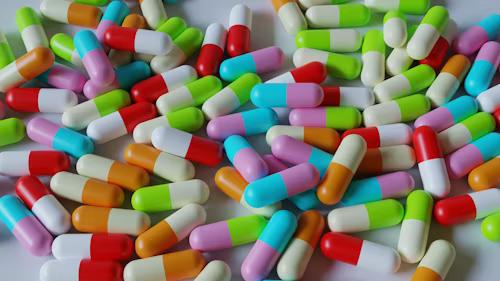
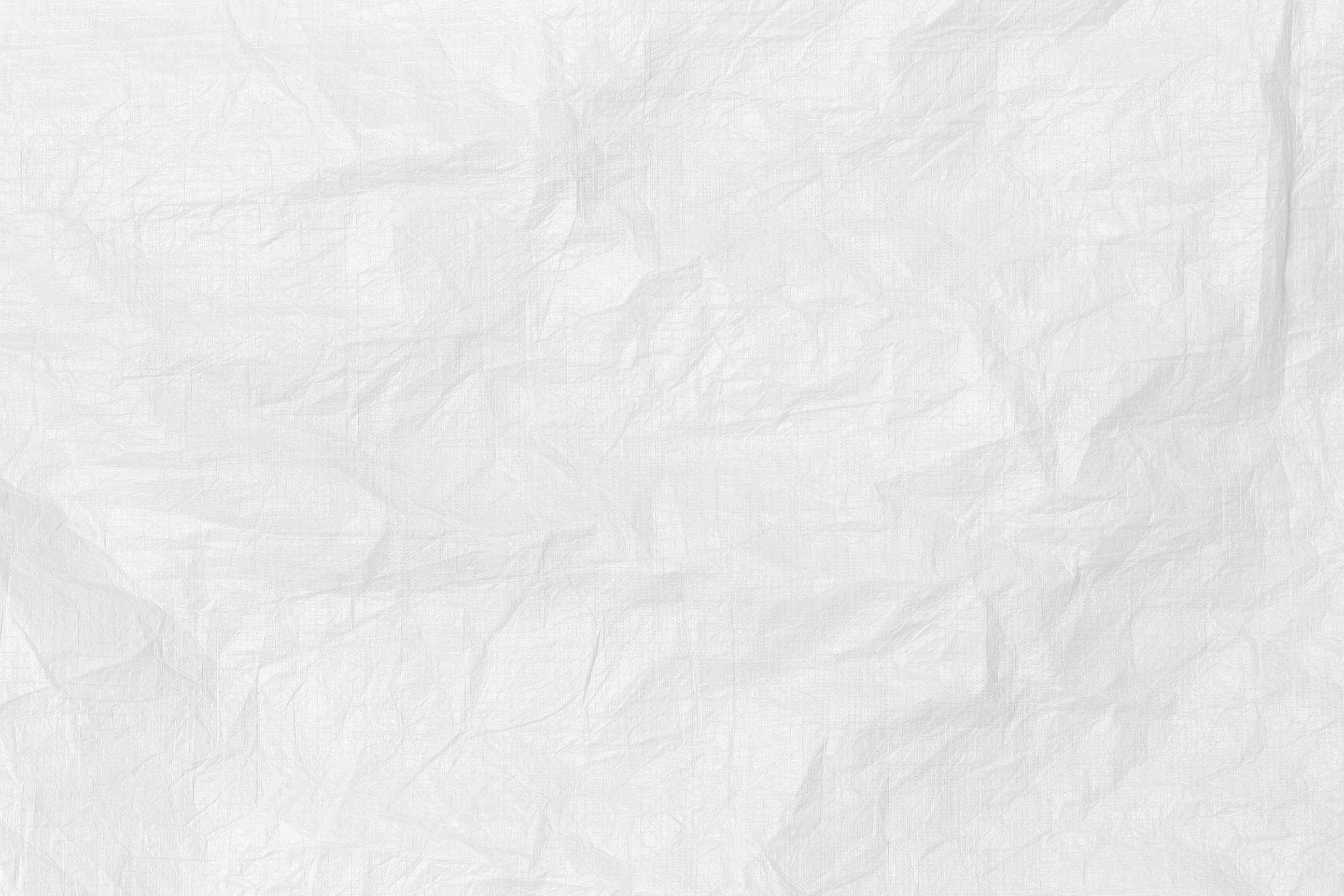
MACO (Maximum Allowable Carryover) is a critical concept in pharmaceutical cleaning validation. It determines the maximum residue from a previously manufactured product that can be carried over into the next product without causing harm to patients.
MACO (Maximum Allowable Carryover) calculation plays a crucial role in cleaning validation in the pharmaceutical industry. It ensures that drug manufacturing processes are safe, compliant, and efficient.
1. Prevents Cross-Contamination
Ensures that residues from one product do not transfer to the next batch.
Critical for multi-product manufacturing facilities.
2. Ensures Patient Safety
Reduces the risk of adverse drug interactions caused by contamination.
Helps maintain drug purity and efficacy.
3. Regulatory Compliance
Meets international standards set by FDA, WHO, EMA, MHRA, PIC/S, etc.
Avoids regulatory penalties, product recalls, and audit failures.
4. Enhances Product Quality
Ensures that each batch meets strict purity and safety standards.
Prevents batch rejection and financial losses due to contamination.
5. Improves Manufacturing Efficiency
Reduces downtime between batch changes by implementing effective cleaning protocols.
Increases production output and minimizes resource wastage.
MACO= TDD×SF×MBS
Where:
TDD (Therapeutic Daily Dose) = The daily dose of the previous product (mg).
SF (Safety Factor) = Typically 1/1000 for potent drugs to add a margin of safety.
MBS (Minimum Batch Size) = The smallest batch size of the next product (mg).
LDD (Lowest Daily Dose) = The lowest daily dose of the next product (mg).
Knors Pharma Solutions LLP specializes in p pharmaceutical solutions, including third-pa compliance assessments for manufacturers pre by regulatory agencies such as the USFDA, MH Their expertise encompasses cleaning valida
Allowable Carryover (MACO) calculations, ensur between batches to prevent cross-contamin product safety.