Translation of the original instruction
List of models:
Change history:
Date Change
2017-11-01 Various updates
2018-01-01
2018-03-01
2018-05-25
Change description
Periodic maintenance, page 6 - 5 Updated maintenance list.
General, page 13 - 23
List of error codes, page 7 - 11
Changed to block 1 as standard.
Clarified truck behaviour, 3:587 updated
Emergency release of the parking brake, page 11 - 6 Updated the transport screws.
Overview, page 11 - 2
Programming PIN codes, page 13 - 24
PIN code defaults, page 13 - 26
New dust seal
PIN code at delivery, page 13 - 25 [New information]
PreOpCheck, page 17 - 4 [New information]
Parameter list, page 4 - 2 1142 added, 311/ 329 new value
Weighing system, page 13 - 28 New setting
Parameter list, page 4 - 2 Added configurable optional functions
Overview steering servo, page 12 - 45 New bracket
Technical data, page 8 - 43
Technical data, page 8 - 43
Technical data, page 8 - 42
Technical data, page 8 - 42
Technical data, page 8 - 43
Technical data, page 8 - 42
Technical data, page 8 - 44
Truck data
Suspension/PT cylinder
Suspension/PT cylinder
Suspension/PT cylinder
Suspension/PT cylinder
Suspension/PT cylinder
Suspension/PT cylinder
Suspension/PT cylinder
Added LPE340BE
1 General introduction
1.1 Images and other information
Images and other information used in this manual may differ from your truck depending on model or optional equipment.
1.2 Warning levels and symbols
The following warning levels and symbols are used in the repair manual:
DANGER
Indicates a dangerous situation that – if not avoided – will cause death or serious bodily injury.
WARNING
Indicates a dangerous situation that – if not avoided – could possibly cause death or serious bodily injury.
CAUTION
Indicates a dangerous situation that – if not avoided – will cause a slight or minor bodily injury.
NOTICE
Used in connection with actions that can cause material damage but not bodily injury.
Used to attract attention and to give information about various actions.
1.3 Pictograms
Visual inspection of condition, wear and loose connections.
Component replacement. Cleaning
Checks for leaks.
Listening for noise.
Check of functions.
An example of another type of pictogram is “Cut cable ties”:
Measurement
Check that screws, nuts, etc. are tightened to torque.
Lubrication, application.
1 General introduction
Additionalinformationunderthepictogramcan,forexample,indicatethenumberofcabletiestobecut.
1.4 Abbreviations
Abbreviation Meaning
Explanation
ACC Alternate Current Combi Motor control, hydraulics and drive.
ACH Alternate Current Hydraulic Motor control, hydraulics.
ACT Alternate Current Traction Motor control, drive.
ADU Automation Display Unit Display used for automated applications for control inputs and visual feedback from the automatic system.
ACU Automation Camera Unit Camera equipment used for automatic applications in order to identify empty places in racking, etc.
ACP Automation Control Panel Control panel used for automated applications for control inputs and visual feedback from the automatic system.
AUX Auxiliary Outside equipment
BCU Onboard system
BDI Battery Discharge Indicator Unit indicating the state of battery charge.
BMS Battery Management System
CAN Controller Area Network
A interface for battery to truck communication.
A standardised interface that enable communication between different electrical units.
CID Central Information Display Display with menu-based information system that is used as the primary communication tool between operator and truck.
DHU Data Handling Unit
DX Duplex Mast with two sections.
EPS Electronic Power Steering Complete steering servo with its own motor control.
ESO Emergency Switch Off Emergency stop switch.
FCM Fuse Central Module Fuse panel.
FCU Fork Control Unit Unit for fork functions.
GFU General Function Unit Unit for general functions.
HPS Height Pre-Select
ICH Integrated Control Handle
Height pre-selection
IPM Intelligent Power Module Power control unit
LID Load Information Display Display that provides the operator information such as lift height, load weight and height preselection.
LGU Laser Guidance Unit
LSU Laser Scanner Unit
Laser guidance unit
Laser scanner that detects objects.
MC Main Contactor Main contactor
MCU Main Control Unit Main control unit.
MLD Multi Load Detection Sensor for automatic detection of loads, etc.
PDA Personal Digital Assistant
PPS Personal Protection System
A compact, portable handheld computer.
Personal protection system.
PTC Positive Temperature Coefficient Electrical property that causes resistance to increase with temperature.
SAU Secondary Automation Unit Device used for automatic control in order to have enough I/O.
Abbreviation
Meaning
Explanation
SCU Secondary Control Unit Secondary control unit
SEU Spider Expansion Unit Expansion unit
SF Shuttle Forks Telescoping fork unit.
SR Safety Relay Relay to disconnect power to certain components in order to stop all movements.
SPLC Safety PLC
Device used in automation applications for control with SR and UAC.
SSU Shock Sensor Unit Shock sensor that registers any collision.
TBD To Be Defined Means that the instruction/chapter will be added at a later date.
TCS Truck Control System The truck control system that communicates with units.
TH Turret Head Turret head fork unit
I-Site Toyota Wireless Information System Wireless communication.
TX Triplex
UAC Unit for Automation Control
Mast with three sections.
Device used for automated control of an operator-less truck. UAC will build an extra CAN and a power system for automation by itself
VNA Very Narrow Aisle Narrow aisles
VRE Very narrow aisle Rider Electric
10 Transmission/Drive gear C2000
Drive unit, final gear C2500
10 Transmission/Drive gear C2000
10.1 Drive unit, final gear C2500
10.1.1 Drive unit/gear C2550
10.1.1.1 Overview
Part number: 7540136 7525837 7530286
Pos. Designation
a Transmission housing
b Motor bearing and packing box
c Steering bearings
d Seal and cover ring
e Stud M12X1.5
10.1.1.2
Overview
Part number: 7525839 7540133
10.1.1.3 Description
10.1.1.3.1
Design
Pos. Designation
a Seal and cover ring
b Transmission housing
c Motor bearing and packing box
d Steering bearings
e Stud M14X1.5
The drive gear is a two-stage angle gear that is integrated with the motor and brake assembly in a complete drive unit. The drive gear is bolted to the chassis. At the top edge of the gear, the steering bearing and a gear ring for the steering motor (option) are fitted.
A complete reconditioning of the drive gear must be performed in the workshop by trained technicians.
10.1.1.3.2
Technical data
Part number: 7525839 7540133 Description
Description Value Oil type See Lubricants specification, page 22 - 2
10.1.1.3.3 Technical data
Part number: 7540136 7525837 7530286 Description Value Type Two-stage angle gear Gear ratio 18.39 Oil quality 0.9 litres Drive wheel Ø 230 Oil type See Lubricants specification, page 22 - 2
10.1.1.4 Check the drive gear's attachment
1. Check the drive gear's attachment. Tighten the screws if necessary. 23 N·m
10.1.1.5 Checking for leaks in the drive gear
1. Check the drive gear for leaks. If there are any leaks, change the oil seal, see Replacing the wheel hub seal , page 10 - 7
10.1.1.6 Checking for noise in the drive gear
1. Listen for any abnormal noise in the drive gear bearings
In case of noise:
Check if the oil level is up to the bottom edge of the filler hole, see Lubricants specification, page 22 - 2.
Replace the steering bearing. Replacing the drive gear steering bearing , page 10 - 13
10.1.1.7 Replacing the drive gear
10.1.1.7.1 Removing the drive gear
Preparations
Removing the platform, page 8 - 78
Removing the platform [Fixed side guards], page 8 - 81
1. Turn the drive wheel as much as possible in one direction.
2. Switch off the truck and disconnect the battery connector.
WARNING Risk of personal injury and material and property damage
For trucks with power steering, the truck battery must be disconnected when working on the drive gear/drive wheel.
► The drive wheel will automatically return to the original position when the truck is started.
Removing the drive motor [M1], page 9 - 19, Removing the drive motor [M1], page 9 - 21, Removing the drive motor [M1], page 9 - 23
3. Undo and remove the screws to the drive gear.
4. Lift the truck 100 mm and support it on trestles.
WARNING Risk of crushing under the truck
Risk of crushing since a poorly supported truck could fall down.
► Secure the truck in a safe manner.
5. Remove the gear from the truck.
6. Mark the position of the steering bearing.
10.1.1.7.2 Installing the drive gear
1. Lift the drive gear in place. Turn the wheel towards you (rearwards) to facilitate the lift.
2. Rotate the steering bearing to the right position; see marking.
3. Lower the truck and position the gear in place.
4. Fit the drive gear. Remember to tighten the screws crosswise
Resetting
Installing the drive motor [M1], page 9 - 25
Installing the drive motor [M1], page 9 - 27
Installing the drive motor [M1], page 9 - 29
Installing the platform, page 8 - 81
Fitting the platform [Fixed side guards], page 8 - 83
10.1.1.8 Replacing the wheel hub seal
10.1.1.8.1 Removing the wheel hub seal
Disassembling the drive wheel, page 11 - 17
10.1.1.8.2 Installing the wheel hub seal
Installing a drive wheel, page 11 - 18
10.1.1.9 Drive gear oil change
2. Fit the cover ring. Tap it lightly into place.
1. Empty the oil from the drive gear. Empty the drive gear oil, page 10 - 10, Empty the drive gear oil, page 10 - 11
2. Fill oil into the drive gear. Filling oil in the drive gear, page 10 - 12, Filling oil in the drive gear, page 10 - 13
10.1.1.9.1 Empty the drive gear oil
1. Undo and remove the oil plug on the lower part of the gear housing.
2. Drain all old oil into a suitable receptacle.
3. Clean away dirt and metal shavings from the oil plug.
4. Install the oil plug, tighten to 20 N·m
10.1.1.9.2 Empty the drive gear oil
1. Undo and remove the oil plug on the lower part of the gear housing.
2. Drain all old oil into a suitable receptacle.
3. Clean the oil plug of any dirt and shavings. Refit the oil plug, tighten to 20 N·m
10.1.1.9.3 Filling oil in the drive gear
1. Remove the oil filler plug on the upper part of the gear housing.
2. Top up with oil up to the lower edge of the hole to reach the correct level, Lubricants specification, page 22 - 2
Screw in the plug.
10.1.1.9.4 Filling oil in the drive gear
1. Remove the oil filler plug on the upper part of the gear housing.
2. Top up with oil up to the lower edge of the hole to reach the correct level, Lubricants specification, page 22 - 2
10.1.1.10 Replacing the drive gear steering bearing
10.1.1.10.1 Removing the drive gear steering bearing
Part number: 7525839 7540133
Removing the drive gear, page 10 - 4
Thank you very much for your reading. Please Click Here. Then Get COMPLETE MANUAL.NOWAITING
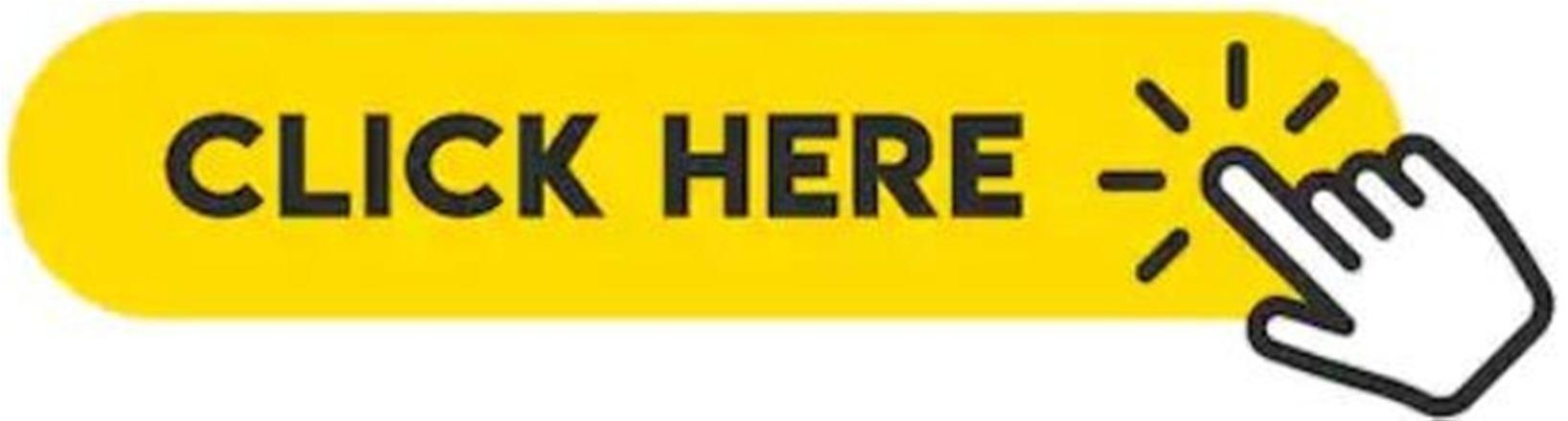
NOTE:
If there is no response to click on the link above, please download the PDF document first and then clickonit.
10.1.1.10.2 Removing the drive gear steering bearing
Part number: 7540136 7525837
Removing the drive gear, page 10 - 4
2. Lift away the steering bearing.
10.1.1.10.3 Installing the drive gear steering bearing
Part number: 7525839 7540133
1. Install the steering bearing. Check that the bearing rotates before fitting it in the truck.
10.1.1.10.4 Installing the drive gear steering bearing
Part number: 7540136 7525837
1. Install the steering bearing. Check that the bearing rotates before fitting it in the truck.
Installing the drive gear, page 10 - 6
10.1.1.11 Stud replacement
10.1.1.11.1 Removing a stud
Disassembling the drive wheel, page 11 - 17