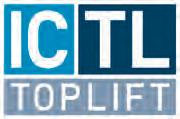
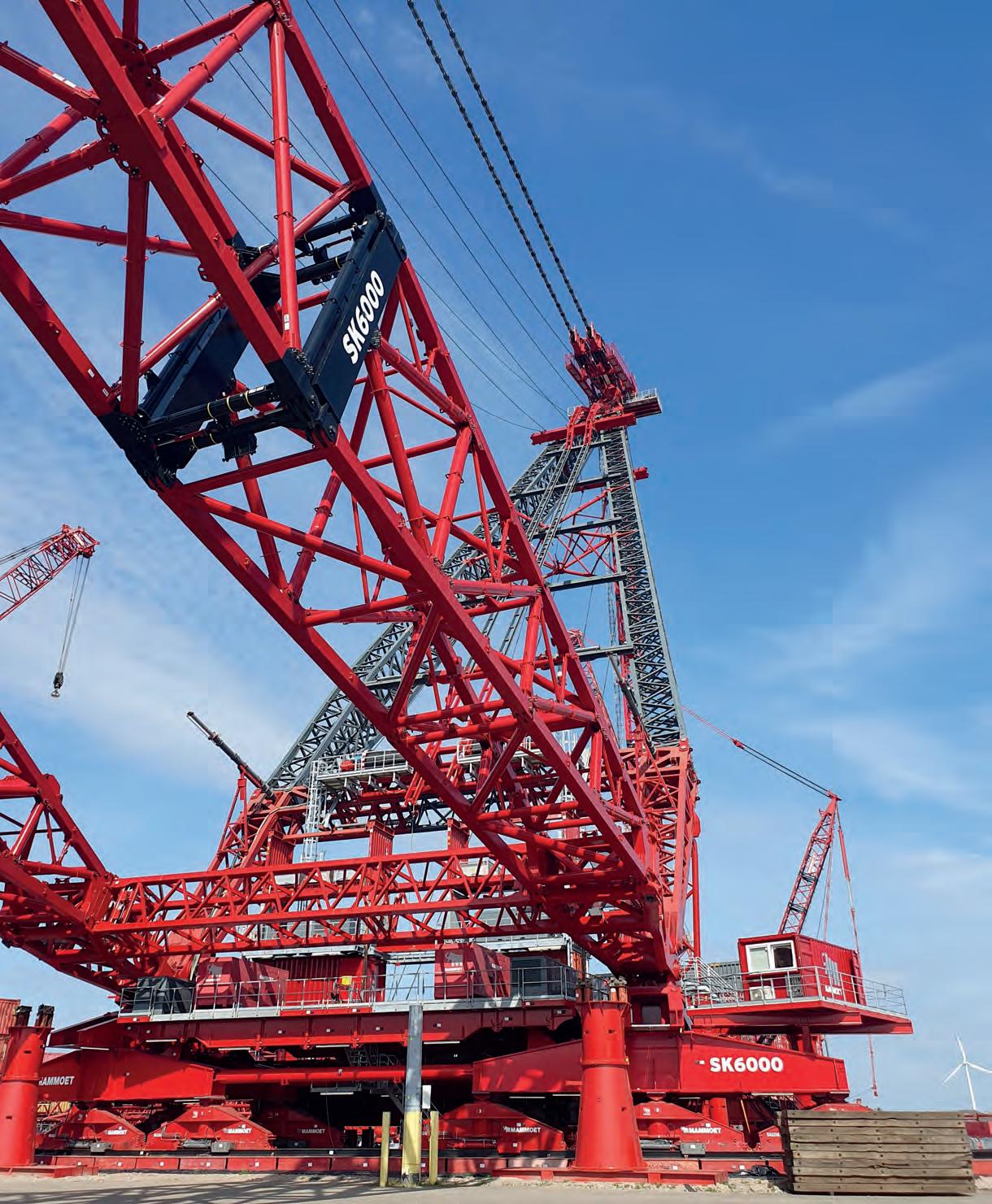
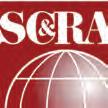

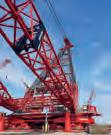
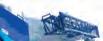

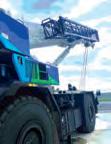
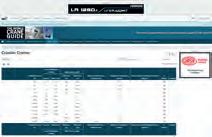
By the time you read this I hope you may well have seen the new daily Crane and Transport Briefing (CTB). Our new email of the latest news and analysis on the industry launched on 3 September.
It is produced five days a week by the editorial team you might be familiar with from the Crane and Transport Briefing website with its frequent updates of news and features, plus the regular International Cranes and Specialized Transport and American Cranes & Transport printed and digital publications.
CTB is from a stable that also includes the unique IC100 and other toplists, the weekly World Crane Week email newsletter, plus our social media channels, events such as the World Crane and Transport Summit and more –the full gamut. All are intended to help you in your business, by keeping you abreast of the latest industry developments, informing and sharing best practice but some things are just simply interesting.
You'll likely see news first in our online channels but sometimes you’ll see stories in one or both the magazines before they appear online, other times something might be published only online, maybe as a brief summary, in bite size chunks in the magazines, or various other combinations thereof. We want to make all the information is available to you on whatever platform or in whichever format best suits you. At the same time, variety is the spice of life, as they say, so it is worth having a look at a range of these outlets of ours whenever you can.
Being part of the KHL Group means via our crane and transport information channels you can also access a wider but often relevant and interesting range of information from our other construction and power industry-related channels and publications.
If you haven’t already you can sign up for free to receive the new briefing at our craneandtransportbriefing.com homepage under the e-newsletters tab. Please do let me know what you think of it and I’d be pleased to hear any constructive suggestions for improvement. In the meantime, enjoy this issue of the magazine.
ALEX DAHM Editor
1 & 2 October 2024, Dubai
& 4 June 2025,
Correspondence is welcome and should be sent to: The editor, International Cranes and Specialized Transport Southfields, South View Road, Wadhurst, East Sussex TN5 6TP, UK
Beijing Representative Office, Room 769, Poly Plaza, No.14, South Dong Zhi Men Street, Dong Cheng District, Beijing, PR China 100027. +86 10 6553 6676 | cathy.yao@khl.com
USA/CANADA PLUS AUSTRIA/EASTERN EUROPE/ GERMANY/IRELAND/KOREA/RUSSIA/ SPAIN/ SWITZERLAND/UAE
Matt Burk, Vice president sales
+1 312 4963314 | matt.burk@khl.com UK/SCANDINAVIA
John Austin, Marketplace/Classified advertising
+44 (0)1892 786245 | john.austin@khl.com
DACH & IBERIA Simon Battersby +44 1892 786223 | simon.battersby@khl.com
THE NETHERLANDS/LUXEMBOURG
Arthur Schavemaker
+31 (0)547 275005 | arthur@kenter.nl
FRANCE/BELGIUM Hamilton Pearman
+33 (0)1 45930858 | hpearman@wanadoo.fr
ITALY Fabio Potestà
+39 010 5704948 | info@mediapointsrl.it
TURKEY Emre Apa
+90 532 2343616 | emre.apa@apayayincilik.com.tr
CHINA Cathy Yao
+86 (0)10 65536676 | cathy.yao@khl.com
JAPAN Michihiro Kawahara
+81 (0)3 32123671 | kawahara@rayden.jp
USA/CANADA Bev O’Dell
+1 816 8861858 | bev.odell@khl.com
VP GLOBAL SALES Alister Williams +1 843 637 4127 | alister.williams@khl.com
Max. Lifting Capacity : 75t x 3.0m
Boom Length : 10.0m to 30.1m
Side Deflection-Resistant Fully Powered Boom for All Lifting
Tough 4-plate box boom structure with special welding quality standards, but lightweight
A Superstructure Designed to Take on Tough Jobs
The upper frame is designed to be durable for winch operation with high line pull.
The vertical layout of the main & aux. winches helps achieve a compact design and efficient weight balance.
Engine Output
Chosen as the official magazine of the SC&RA (Specialized Carriers & Rigging Association)
Approved media partner for:
To subscribe to International Cranes and Specialized Transport or any of the magazines in the KHL portfolio go to: www.khl.com/free-subscription or call +44 (0)1892 784088 for details.
International Cranes and Specialized Transport is a monthly publication with a worldwide circulation. The annual airmail subscription rate is US$301, €258, £215. This issue of International Cranes and Specialized Transport is mailed on 16 September 2024. Material published in International Cranes and Specialized Transport is protected under international copyright law and may not be reproduced without prior permission from the publisher.
International Cranes and Specialized Transport (USPS 017 158) is published monthly by KHL Group and distributed in the US by DSW, 75 Aberdeen Road, Emigsville, PA 17318-0437. Periodicals postage paid at Emigsville, PA. Postmaster: Send address changes to International Cranes and Specialized Transport, c/o PO Box 437, Emigsville, PA 17318-0437.
Heavy lifting giant Mammoet has launched its biggest crane to date, the SK6000. Niamh Marriott went to see it.
Casey Savlov at Vita Industrial explains how technology can be used to improve safety in lifting. ICST reports.
A roundup of alternative lifts and news from around the world. Niamh Marriott reports.
EDITOR & EDITORIAL MANAGER Alex Dahm
alex.dahm@khl.com | +44 (0)1892 786206
DEPUTY EDITOR Niamh Marriott niamh.marriott@khl.com | +44 (0)1892 786208
EDITORIAL DIRECTOR Murray Pollok
NEWS WRITER Leila Steed
GROUP EDITORS Lindsey Anderson
Andy Brown Catrin Jones D.Ann Shiffler
Leila Steed, Euan Youdale
WORLDWIDE CONTRIBUTORS John Bowman, Australia; Graham Brent, USA; Marco van Daal Aruba; Heinz-Gert Kessel, Germany; Richard Krabbendam, Netherlands; Tim Maughan, Japan; Brent Stacey, Australia; David Weston, UK
Long heavy loads, a cellar and limited space were among the challenges on this job in Alex Dahm reports.
Opportunities to evolve in a consistent market. Hannah Sundermeyer reports.
Presenting ten spectacular lifting projects carefully selected from the last 12 months. Have a look and then submit your vote for your favourite one. ICST reports.
SC&RA CORRESPONDENT
Mike Chalmers
SALES MANAGER Matt Burk matt.burk@khl.com | +1 312 496 3314
MARKETPLACE SALES John Austin john.austin@khl.com | +44 1892 786245
CLIENT SUCCESS & DELIVERY MANAGER
Charlotte Kemp | charlotte.kemp@khl.com
CLIENT SUCCESS & DELIVERY TEAM Alex Thomson | alex.thomson@khl.com
Olivia Radcliffe | olivia.radcliffe@khl.com
GROUP DESIGN MANAGER Jeff
| alison.filtness@khl.com FINANCE MANAGER Yasmin Toumi | yasmin.toumi@khl.com
CREDIT CONTROL Carole Couzens carole.couzens@khl.com | +44 (0)1892
The company’s first GMK3060L-1 handling maintenance work at the Palau de la Música in Barcelona
Spanish crane rental company Grúas del Vallés has taken delivery of two new 60 tonne capacity Grove GMK3060L-1 all terrain cranes.
This latest order follows its purchase of another GMK3060L-1, delivered in 2022.
The three axle crane has a 48 metre boom and was chosen for its compact size and ease of transport. It can drive with up to 7.5 tonne counterweight within 12 tonnes per axle.
Commenting on this latest order, Marc Gelabert, Grúas del Vallés manager, said, “The cranes are ideal for the jobs we focus on, and we get great support from our local dealer Rexma which always provides swift and responsive service.”
Finnish crane maker
Konecranes is establishing the necessary supplier network and infrastructure to begin building port cranes in the USA.
The move follows US President Joe Biden’s introduction in mid-May of 25 per cent tariffs on imports of such cranes and similar rates on other goods from China.
Konecranes has developed an expanding network of steel structure providers and subcontractors for the Build
» LIEBHERR USA is expanding its presence in the USA with a new spare parts warehouse for mobile and crawler cranes in Kansas City. The 12,000 square foot (1,115 square metre) warehouse holds around 2,300 line items, with more than 5,000 expected to be stocked once the facility is fully converted.
» MANITEX INTERNATIONAL announced a North American dealership agreement with BRUCKNER’S TRUCK & EQUIPMENT to sell and support the full line of Manitex equipment, including PM articulating cranes. in selected markets through their network of 40 support centres.
» A new public transport monorail line in São Paulo, Brazil, moved closer to completion with the help of a large number of cranes, among them were wheeled mobiles from the Mongel company.
Construction of the overhead monorail line started in 2012. It was originally intended to be finished in time for the 2014 football World Cup but progress is now being made again.
Mongel used its fleet of all terrain cranes from Sany in China. Largest was the 700 tonne SAC7000S. Others were the 600 tonne SAC6000C8 and a 250 tonner.
America Buy America (BABA) Act of 2021.
As part of the Infrastructure Investment and Jobs Act, BABA established a domestic content procurement preference for all Federal financial assistance obligated for infrastructure projects after 14 May 2022.
The domestic content procurement preference requires all iron, steel, manufactured products and construction materials used in covered infrastructure projects to be produced in the United States, according to the US Government Office of Acquisition Management.
In a Whitehouse Briefing Room statement the move was described as “a combination of Finnish expertise and American industrial capacity.”
Konecranes said it can now manufacture a full range of domestic manufacturingcompliant port cranes in the USA, including ship to shore (STS) container cranes.
KHL Group, publisher of this magazine, has launched Crane and Transport Briefing (CTB), a daily newsletter to provide high quality information and analysis on the global crane and specialized transport industry.
The Briefing focuses on one piece of exclusive journalism, providing insight, news and analysis. It will be supplemented with a selection of other relevant stories.
CTB is edited by Alex Dahm, editor of International Cranes and Specialized Transport, with support from D.Ann Shiffler and Hannah Sundermeyer, both from American Cranes & Transport, and Niamh Marriott on International Cranes and Specialized Transport magazine.
The Briefing joins KHL’s three existing daily newsletters –Construction Briefing, Rental Briefing, Power Briefing – all launched in the last 18 months.
“We are excited to be providing this new service for our audience, building on the existing magazines, our website and the weekly World Crane Week newsletter”, said Dahm.
“Every day the team – myself, D.Ann, Niamh and Hannah –will provide reporting to inform and entertain, showcasing the most interesting stories impacting our industry.
“The lead piece in each Briefing could be a report on an important new crane, a spectacular lift or transport report, analysis of legislation or market trends impacting our industry.”
The existing weekly crane and transport newsletter, World Crane Week, which is a round-up of weekly industry news, will continue. The official partner for the new briefing is Specialized Carriers & Rigging Association (SC&RA).
If you have a story you’d like to share for CTB, please contact Alex Dahm: alex.dahm@khl.com or any of the rest of the team.
Crane and Transport Briefing will carry exclusive news and analysis on the crane and transport industry
Japanese crane maker Tadano has posted a rise in net sales of 6.1 per cent to a total of JPY 141,381 million (US$ 979.3 million) for the first half of 2024. It is up by JPY 8,114 million ($56.2 million) on the JPY 133,267 million ($923.6 million) total for the first half of 2023.
Also up was the operating income, at JPY 12,283 million ($85 million) or 8.7 %, over the JPY 8,797 million ($61 million) or 6.6 % in the first half of 2023. Tadano attributed this JPY 3.4 billion ($23.6 million) rise to improved selling prices and the effects of foreign currency exchange rates. Note this increase was achieved despite higher prices for raw materials.
Net sales were up in all segments. Mobile crane sales were up 4.3 %, truck mounted loader cranes by 3.6 %. While mobile cranes saw the largest increase in value, at JPY 4,031 million ($27.9 million), percentage-wise aerial work platforms were up the most, by 39.3 %, or JPY 2,861 million ($19.8 million).
Looking more closely at mobile cranes, outside Japan there was an 8.1 %, JPY 5,597 million ($38.8 million) increase to JPY 74,627 million ($517.3 million) while domestic sales were down 6.3 %. Total market demand for mobile cranes was up 10.2 %, the company said. The most active markets were reported as being Latin America, the Middle East, North America and Europe.
» A Manitowoc MLC650 crawler crane owned by W.O. GRUBB assisted in the turnaround of a tunnel boring machine (TBM) known as Mary in the USA. Mary completed the first tunnel on the US$ 9.3 billion Hampton Roads Bridge Tunnel Expansion (HRTAC) project, the largest highway construction project
in Virginia’s history. Completion is due in early 2027. Construction crews were on hand to see Mary emerge, busting through the barrier with its rotating cutter. After emerging into a receiving pit at North Island, the crews used nitrogen tables to raise, slide and turn Mary 180 degrees ready for its next run.
» CAPITAL CITY GROUP in the USA has acquired cranes and equipment from Midwest Equipment Company. Bay Crane Companies subsidiary Capital City expands its presence in the Cleveland area with the acquisition at Garfield Heights, Ohio. The premises will become the Capital City Cleveland branch.
Capital City Group has been operating in the Midwest and MidAtlantic for nearly 30 years. Its fleet includes specialized transport equipment and more than 500 cranes, including crawlers over 1,000 tonnes capacity, all terrain cranes up to 900 US tons and and rough terrain up to 160 US tons.
Barnhart continues its expansion in the south western United States
In its fifth acquisition of the year Barnhart Crane and Rigging has purchased Mountain States Crane of New Mexico, USA.
The deal includes Mountain States’ operated crane rental service, personnel and equipment. It is Barnhart’s first foray into New Mexico.
“Over a period of more than 25 years, Mountain States Crane has earned a reputation for superior service in crane, rigging and heavy haul by focusing on safety and customer satisfaction,” said Chris Howe, Barnhart
VP and southwest regional director. “They are known in the industry for their highlytrained and experienced operators and riggers as well as a comprehensive and well-maintained fleet. Mountain States’ focus on providing crane and rigging service within a 400 mile radius of central New Mexico complements our branch in Arizona as we expand further into the Southwest.”
Tennessee-based Barnhart is a leading lifting and logistics contractor in North America with more than 60 facilities.
Acquisitions are continually being announced this year. In late August 2024, Denzai KK acquired fellow lifting and transport specialist Kurogane Corporation in Japan. Kurogane has a 77 year history in Kyushu and it is Denzai’s first foray into the region.
Commenting on the deal Kohki Uemura, Denzai president and CEO, said, “Kurogane Corporation is a long-established major company with a [strong] track record in Kitakyushu City, which has been selected as a base port for offshore wind power generation. It has been providing services to Nippon Steel Corporation’s Kyushu Works in the Yahata and Oita as an onsite subcontractor, and is highly trusted by the company.”
USA-based Kito Crosby has entered into an agreement to acquire eepos and its subsidiaries, makers of aluminium light crane systems. The acquisition is expected to be finalised in the third quarter of 2024.
» Azerbaijani construction company Azinvest purchased two used Potain MC 120B tower cranes for construction of a wellness center in Karabagh. Reliability and cost-effectiveness were vital and the cranes were refurbished ahead of delivery. The cabins were refitted essential components were replaced, including power cables and ropes. “Reliability and performance are going to be crucial on a project like this, so it made sense to choose Potain. Azinvest has already used tower cranes on several jobsites,” said Kamran Amiraslan, lifting equipment department manager at Manitowoc dealer AS Texnika.
Founded in 2006 in Wiehl, Germany, eepos offers lifting solutions for workplaces and has a global presence including subsidiaries in the US, Mexico, Brazil, Hungary, Turkey, France, South Africa, China, and India.
Ten kilometres off the Normandy coast in the English Channel, workers are busy drilling foundations for what will be France’s fourth offshore wind farm. The Calvados offshore wind farm, expected to be commissioned in the third quarter of 2025, will be 64 wind turbines with a total capacity of 450 MW – enough electricity for 630,000 people.
As demand for wind power increases around the world, manufacturers are building bigger and bigger turbines. Like most wind farms under construction at the moment, turbines at the Calvados site will have a hub height of 100 metres, a massive increase on the 37.5 metre hub heights seen on the first off shore sites in the 1990s. As turbines get bigger, the heavy lifting and transport companies have to adapt. Technology and engineering company Saipem is delivering the huge steel monopile foundations, each one weighing around 1,000 tonnes.
Saipem contracted Italian specialist Fagioli to mastermind the heavy lifting, relocation, transport and storage of the components at the BOW Terminal in Vlissingen, Netherlands. Fagioli provided a 120,000 square metre marshalling yard to offload, store and reload the cargo delivered by German manufacturer EEW, alongside another 64 transition pieces, each weighing up to 600
tonnes, They connect the turbine tower to its foundation.
Fagioli's lifting and storage solutions include building sets of gravel dunes to store the monopiles and setting out more than 1,400 concrete blocks to store the transition pieces.
it also moved loads on and off the vessels using two crawler cranes – a 1,350 tonne capacity Liebherr LR 11350 and a 1,250 tonne Demag CC 6800 – and more than 100 lines of self propelled modular transporter.
In tandem the crawler cranes lifted each huge steel monopile cylinder horizontally onto the SPMT and carefully placed it between the specially constructed gravel dunes.
Intelligent counterweight system, slabs interchangeable for all CC cranes. The right crane for the job
Boom extensions, luffing jib, Boom Booster Kit, and other modules can be added as needed.
IC-1 Remote gives you access to advanced real-time diagnostics and much more.
Quick-connection system allows superstructure to be installed or removed in less than 15 minutes.
When the job demands something unusually
powerful and
a Tadano lattice boom crawler crane is the perfect solution. They have excellent capacities up to 3,200 t and maintain outstanding maneuverability under heavy load.
Despite their size, Tadano lattice boom crawler cranes are easy to transport and quickly rigged on the job site. Innovative solutions provide you with the right crane for every application. Learn
Specialist heavy lift giant Mammoet has launched its SK6000 which it claims as the world’s strongest land-based crane. NIAMH MARRIOTT went to see it
Visible from well over 10 kilometres away from the Westdorpe, Netherlands site due to its impressive size, the 6,000 tonne capacity super heavy lift ring crane, the SK6000, has now been fully assembled for testing.
Mammoet used its own cranes for the assembly, which began in June 2024, including a 250 tonne capacity crawler crane and a 140 tonne Gottwald mobile harbour crane.
The SK6000 can lift 3,000 tonnes to a height of 220 metres and will allow the use of new construction techniques for offshore wind projects and onshore new build projects like nuclear plants.
Assembled and ready for testing at Mammoet's yard in Westdorpe, NL
Some
The company said it can be used in a range of different industries and applications but its fully battery powered options offer green opportunities for eco-conscious sites. It can also be powered using traditional diesel engines.
Maximum capacity is achieved with 4,200 tonnes of ballast and the crane can be transported using 300 shipping containers to any location in the world.
The crane is undergoing testing at Westdorpe, ready for deployment on its first project later in the year. The company said it will be transported to a client’s site in Asia.
Gavin Kerr, Mammoet director of global services, said, “This crane is truly a world record feat of engineering, with a production schedule to match.
“The basis of the starting point was to build a 6,000 tonne crane,” he explained. “We wanted that to be a solution, not for tomorrow or even one year. We really wanted to ensure that it would be relatively future proof, flexible and scalable. Sustainability was at the heart of the design – re-using existing components as much as we possibly could and to have forward and backwards compatibility with the existing SK family of systems.
“The back mast is actually the main mast of the SK 350. The main mast is this new construction, which can also be used as a gantry system. So it has dual purpose capabilities.
“We wanted to ensure that we would be fully electric, that we would have the capability of operating the crane on electric power. And together with our electric SPMTs, we imagine the future of where we can give a full carbon free solution.”
“We had to do additional training for the operators”, says Erik Visser, senior lead engineer for the SK6000. Visser worked on the crane from its inception.
“We are training them here on-site. As
we were setting up the system, we are directly training the operators. The set up is in line with the previous SK series. It’s more like a continuation of the range. Some of the screens and buttons and functions are still the same as were in the smaller cranes so that helps a lot with training. Once we complete the module in the control system, the operators will be trained to work with that.
"It’s not the design engineer who pulls up the main parts, it’s actually the operators. When it leaves this test yard, they are capable of breaking down the machine too. The full training takes a couple of weeks. It will be a dedicated crew who stay with the crane the whole time. Training was going on at the same time as building the crane and setting it up for testing. The team have been here for a few months, getting all the details from assembly up to operation and control.”
Maximum flexibility
Up to 57 m boom length, 15 m folding jib inclusive
Telescoping under load
Work on up to 4° incline*
Moving under load
Powerful Full Power Boom for pick & carry with up to 100 % load
Effective transport
With or without crawler tracks
Innovative self-assembly system
*with reduced load charts
For further information sennebogen.com/683
Bernhard Kraus
SENNEBOGEN
Maschinenfabrik GmbH
94315 Straubing, Germany bernhard.kraus@sennebogen.de
starting from 0 % interest, 0 % down payment
CASEY SAVLOV, executive vice president at Vita Industrial, explained how technology can be used to improve safety in lifting operations
ICST reports
Vita Industrial started out as an aerospace company for the US armed forces.
“There’s an issue when you rescue people with evacuation helicopters, you lower a litter basket and those baskets swing, right? Our founder, [Caleb Carr] was doing a mission off a mountain medical evacuation with his mentor, [who] had heart problems. They called a helicopter to evacuate him but [could not do it] fast enough because the baskets were spinning so much. Unfortunately, the mentor went into cardiac arrest and died.”
After this, Carr began work on systems for the US military at university, developing technology to stabilise baskets under helicopters and he decided to try and develop the same thing for loads on construction cranes.
For the construction industry, the use of cranes and heavy lifting equipment is both essential and fraught with risk. Traditional methods, which often involve workers managing taglines and operating
close to heavy loads, have historically presented significant safety challenges. Recent advances in technology, however, are changing how these operations are conducted, dramatically improving both safety and productivity, Savlov claims.
“Managing loads is not easy, it’s very costly, it’s very risky. We have a standard of using taglines to manage these loads. And let me be very clear, I am not, nor is our company, suggesting that you don’t use taglines. We just believe with the advancement in technology there could be safer, faster, smarter ways than just only having a tagline."
Savlov provides an overview of how Vita’s technology is reshaping crane operations.
Showing a slide of a tower crane disassembly he says, “This is how you dismantle a tower crane. Now what you’ll notice there’s this little device at the top... you’ll notice there are no 400- or 500-foot taglines. There’s nobody running around this congested site risking a slip, trip or fall.”
The technology in question is a unit
CASEY SAVLOV, Vita Industrial executive VP
“I’ve never seen anything that’s made me safer and faster. Safety is big but also productivity is a big one.”
Maintaining or altering load position in the air for tower crane sssembly
suspended from the crane that eliminates the need for traditional taglines (ropes used to stabilise loads). By removing these, the risks of slips, trips and falls – common hazards on congested construction sites –are significantly reduced.
One example Savlov discusses involves the dismantling of a tower crane at a congested site in California, USA. Here, a single operator using a remote control was able to manoeuvre the load with precision, bringing it down between two buildings without the need for multiple workers handling taglines.
Savlov notes, “There’s one guy... using a remote control, which will automatically rotate this load between those two buildings and bring that down in less than nine minutes.” This not only enhanced safety but also reduced the time needed for the operation, Savlov explains.
The ability to keep loads stable during lifts is another significant safety improvement offered by modern crane technology.
Savlov describes a project in Minneapolis, USA, where his product kept a crane’s load “completely stable,” so the operator could move faster and more efficiently.
“The load’s completely stable, it’s not going to rotate,” he says. This stability is crucial, especially in environments where precision is essential, such as when placing large forms in narrow spaces.
At this site workers previously spent 18 to 21 minutes completing tasks that now take just 4 to 6 minutes thanks to the technology. “They now drop those forms in minutes,” Savlov says. This not only accelerates project timelines but also minimises the time workers spend near potentially dangerous loads, thereby
reducing the likelihood of accidents.
Wind is a notorious challenge in crane operations, often forcing work to halt due to safety concerns. New technologies like Vita’s, however, are helping to mitigate these issues. Savlov recounts a project on San Francisco, USA’s Treasure Island, where high winds regularly posed a challenge.
Despite being rated for winds up to 35 miles per hour (57 km/h), the crane operator would typically stop work at around 16 or 17 mph (26 to 28 km/h) due to safety concerns. After implementing the new load control technology, however, the operator found he could continue working even in higher winds, due to the load’s increased stability.
As Savlov describes, “As those winds are howling, that load is completely locked into position as he is rotating it to where he needs to go.” This technology reduces downtime and prevents accidents that could occur if taglines were used in high wind conditions. The result is a safer, more efficient operation that keeps projects on schedule even in challenging weather.
While safety is the primary benefit, the economic advantages of using this technology are also significant. Savlov shares a story about a construction site in London, where two identical cranes were operating under different conditions. One crane, equipped with the technology, could »
continue working despite adverse weather, while the other had to be shut down for safety. “The safety team said you cannot use that second crane. It’s too dangerous today with the weather, but that crane that has the technology you can use all day long,” Savlov explains.
This difference in operational capability not only improves safety but also increases productivity, as work can continue uninterrupted. For contractors, this means more efficient use of equipment and labour, leading to cost savings and higher profit.
Remotely controlled load stabilisation technology for tower crane assembly
to mobile cranes, and used in various construction scenarios.
As the construction industry continues to embrace these innovations, Savlov says the potential for even greater safety improvement is enormous. He concludes with a forward-looking statement, “This is just the beginning of what we’re doing. In another month or so, we’ll have some more exciting announcements of what we’re going to bring to the market.”
uncontrollably, which can lead to costly damage. “A lot of their panels get damaged from the tagline smacking them in some of the conditions,” Savlov notes. By stabilising the load and controlling its movement with precision, the technology minimises these risks, leading to fewer claims and lower insurance costs.
Integrating advanced technology in crane operations is a game-changer for the construction industry. By enhancing stability, reducing the need for taglines, and allowing for safe operation in challenging conditions, these innovations are significantly improving safety on construction sites.
As Savlov puts it, the ultimate goal is to ensure workers go home safely to their families every day. With these technological advancements, that goal is increasingly within reach. ■
EQUIPMENT USER: Sarens
EQUIPMENT USED: SGC-250 ring crane
LOCATION: England
Sarens’ 5,000 tonne capacity crane known as Big Carl was used to install a polar crane weighing 750 tonnes at the Hinkley Point C nuclear power station construction project in the UK, one of the heaviest lifts made on the project to date.
Big Carl has been on the Hinkley Point C site since 2019.
EQUIPMENT USER: Mammoet
EQUIPMENT USED: PTC 210 DS ring crane
LOCATION: Scotland
Offshore wind projects are challenged by tidal changes, delaying loading and unloading at quaysides. Mammoet solved it using a PTC 210 DS ring crane at the Port of Nigg in Scotland for the Seagreen offshore wind farm. This solution allowed continuous lifting, avoided delays from tidal shifts and doubled operational efficiency.
Our annual TopLift competition returns with the top ten lifts reported from the last 12 months. Now we hand over
EQUIPMENT USER: BMS
EQUIPMENT USED: Huisman ring crane
LOCATION: Denmark
Lifting specialist BMS set up its new 3,000 tonne capacity ring crane in Denmark, with a 1,530 tonne test lift planned. The crane, standing 245 metres tall, can lift 1,200 tonnes at a 200 metre hook height. Its low ground pressure, electric winches, and high accuracy make it ideal for complex projects, including future wind farm work, BMS said.
EQUIPMENT USER: Vanguard
EQUIPMENT USED: Bespoke hydraulic gantry lifting systems
LOCATION: South Africa
Specialist heavy lift contractor Vanguard up-righted the bark Europa, a 650 tonne, 112-year-old sailing ship, after it tipped over in dry dock at Cape Town’s Victoria and Alfred waterfront in South Africa. Lacking space for a crane, Vanguard engineered a custom solution using telescopic hydraulic gantries and strand jacks, completing the operation with precision and control.
EQUIPMENT USER: XCMG
EQUIPMENT USED: XCA3000 all terrain crane LOCATION: China
The 3,000 tonne capacity XCA3000, claimed as the world’s highest capacity all terrain crane, was put to work for the first time, in making this lift. The flagship model of Chinese manufacturer XCMG completed assembly of a wind turbine in Liaoning Province, China. Site of the landmark lift was the Dashiqiao Xintai New Energy 200 MW wind park in Yingkou.
to you, our readers, to choose your favourite lift and select your vote for the winner. NIAMH MARRIOTT reports
EQUIPMENT USER: Autokrane Schares
EQUIPMENT USED: LTM 1650-8.1, LTM 1450-8.1 all terrain cranes
LOCATION: Germany
In Wuppertal, Germany, two Liebherr mobile telescopic cranes worked in tandem to install a new bridge over the Wupper River. Space constraints required an unusual rigging setup, with cranes positioned on each bank. They lifted eight precast concrete beams, each weighing 85 tonnes, using a 160 tonne capacity triangular cross beam, completing the installation in two days.
EQUIPMENT USER: Allelys
EQUIPMENT USER: MJ Van Riel
EQUIPMENT USED: 16x wheeled mobile telescopic cranes
LOCATION: The Netherlands
Sixteen cranes were used by Van Riel’s team to move a 352 metre section of heat pipeline during a drilling operation under the busy Erasmusplein in The Hague, a solution that allowed trees and bushes along the route to be spared.
EQUIPMENT USED: LG 1550 all terrain crane
LOCATION: England
UK-based heavy transport and lifting specialist Allelys minimised site disruption by using a crane to install a 160 tonne turbine and a 96 tonne generator through the roof of a 22.3 metre high turbine hall in the UK. The components were transported 33 miles (53 km) on specialized trailers and lifted into place by a Liebherr LG 1550 crane, overcoming structural challenges and space restrictions.
EQUIPMENT USER: Sancho Toro Sur
EQUIPMENT USED: 2x 420 EC-H 16 tower cranes
LOCATION: Spain
Sancho Toro Sur deployed two Liebherr 420 EC-H 16 Litronic tower cranes for a 110 metre high lift for the Puente Quinto Centenario bridge renovation in Seville. The cranes were mounted to pylons, navigating the bridge’s stay cables. They lifted 7.5 tonne pylon reinforcements to add an extra lane, enhancing traffic flow.
EQUIPMENT USER: Roll Group
EQUIPMENT USED: RMG modular gantry crane system, Tadano CC 68.1250-1 crawler
LOCATION: Indonesia
Heavy lift, transport and installation specialist Roll Group completed two 1,000 tonne lifts at a petrochemical plant in Cilegon, Indonesia, using its new RMG modular gantry crane system. The system, capable of lifting 3,000 tonnes to heights above 120 metres, proved effective and efficient.
The
India-based JM Baxi Heavy completed the load-in of a 963 tonne bridge module for McDermott Asia Pacific’s ONGC KG-DWN-98/2 gas field project at Krishnapatnam Port, in Andhra Pradesh, on India's east coast.
The heavy transport specialist loaded the bridge at Rohini Yard, near Raigad, back in April 2024, before setting sail for the east coast of India.
The bridge was intended for installation in the KG Basin as part of the project scheduled for May 2024. However, due to adverse weather conditions, the installation had to be postponed, requiring the relocation of the bridge on land. It remains there until the next available installation window, in December 2024.
This delay prompted JM Baxi Heavy to reassess the load-in feasibility, as the
major loading structures used for the bridge were no longer available for load distribution, load-in, and stowage due to the monsoon. To address this, JM Baxi Heavy started engineering modifications a month in advance, considering the challenging weather conditions.
To ensure a smooth load-in, JM Baxi Heavy re-engineered the load-out steel structures. Various locations were evaluated for the load-in, including Krishnapatnam Port, Visag Port, Hindustan Shipyard Jetty (Visag), and the possibility of returning the barge to Rohini Yard.
After careful consideration of costs and timelines, Krishnapatnam Port was selected for the load-in operation.
Following the completion of an engineering study, the engineering team visited Krishnapatnam Port to assess
UK-based transport and lifting specialist Allelys has purchased heavy equipment to expand its capability and meet increased UK market demand.
Included are multiple girder frame trailers, a range of modular axles and heavy ballast trucks, including UK designed and built Trojans.
Some has already joined the existing fleet, with the remainder completing within the coming months.
“We’re excited for the new equipment to join our existing fleet and for our client base to experience the added value that this will provide. With both our capability and capacity increased, our service offering continues to expand, which will only have a positive impact for our clients,” said Richard Beardmore, chief commercial officer at Allelys.
The equipment purchase deal included Trojan heavy haul tractors, girder frame trailers and modular axles
feasibility and prepare for the operation.
Triton 330 barge, which had been on standby at Krishnapatnam anchorage since June 2024, was permitted to berth on 4 July 2024. The load-in operation, which required meticulous timing and co-ordination, was carried out on 8 July 2024. n
Bennett On-Site Services, (BOSS Crane & Rigging) and subsidiary, BOSS Heavy Haul, has opened a new location just south of Atlanta, Georgia, USA. There is a 4-acre yard and office space. It will enhance BOSS’s ability to provide specialized heavy haul and heavy lift services across the south east.
The new branch will allow BOSS to expand its geographical footprint, showcasing its collective capabilities to offer specialized transportation, specialized rigging and rail services to crane services all under one umbrella, said Richard Miller, BOSS president.
Transporting a 34 tonne transformer was the first project from the new Georgia yard
Eliminate paper and bring in a scaled jobsite with touch of button
Rigging Designer
Create and save simple or complex rigging for any lift equipment 3D LiftPlan App
Place your operators and/or customers in the seat “virtually” in any 3D Lift Plan you create!
Alternative lifting solutions use specialized equipment and techniques to move heavy loads in situations where traditional cranes may not be feasible or efficient. This includes devices like gantry systems, strand jacks, hydraulic skidding systems, and other customised lifting solutions designed for unique challenges, such as limited space, irregular load shapes, or extreme weight.
These alternative lifting methods are increasingly important in complex industrial projects, providing innovative ways to safely and effectively manage heavy lifting tasks in diverse environments.
Heavy lift, transport and installation specialist Roll Group recently made two lifts, each of more than 1,000 tonnes, at a petrochemical plant in Cilegon, Indonesia. It used its new RMG modular gantry crane equipment for both lifts. The work was part of Roll Group’s combined scope,
Roll Lift using its unguyed heavy lift gantry and a 1,250 tonne crawler to upend a column
A round up of alternative lifts and equipment news from around the world. NIAMH MARRIOTT reports
also using its fleet of self propelled modular transporter (SPMT) and cranes.
To move the C3 lower splitter column prior to uprighting, Roll Group used two sets of 24 axle lines of SPMT, one set
Roll Group’s heavy lift RMG gantry crane system at work
Handing over the new SBL600 gantry to Schmidbauer at Enerpac’s customer experience day
under each end of the column. It was 79.6 metres long by 9.36 metres wide and 9.95 metres tall. Weight was 1,042.7 tonnes. The 2400Te gantry system was erected to a total height of 97 metres. As the gantry system uprighted the C3 column it was tailed by a 1,250 tonne capacity Terex Demag CC 6800 crawler crane, a model now designated Tadano CC 68.1250-1. Implementation of the new heavy gantry crane system on this job proved the ability to install heavy loads Roll Group says. The system can handle loads weighing as much as 3,000 tonnes, lifting to heights exceeding 120 metres. A distinguishing feature of this system is that it can operate without needing guy lines, thereby minimising disruption to the surrounding area, increasing efficiency and occupying minimal space.
In addition to the gantry lifts, Roll Group’s scope included discharging vessels, transporting all cargo and lifting it into position. It meant the company offered the total solution, including engineering, project management, SPMT and five crawler cranes. The heavy gantry crane system proved itself on these two lifts and two more made »
in the Middle East, where it will stay for the next two years.
Demand is such for the new gantry system, Roll Group has started fabricating another, ready to go to work by the end of 2024. This one will boast “enhanced capacity and capabilities, ensuring Roll Group remains at the forefront of the evolving market landscape,” the company says.
A new tunnel section was installed using battery-powered jacking and skidding equipment in an emissions-free operation in Belgium.
Stadsbader Contractors approached Netherlands-headquartered international heavy lift and transport specialist Mammoet to lift and skid an 850 tonne concrete tunnel section 40 metres underneath railway lines. Mammoet determined that this job could be done without pollution and its engineers worked to combine conventional skidding tech with new battery-powered equipment.
Accurate calculations and precise implementation were needed to lift and skid the 850 tonne concrete tunnel. It was 25 x 8.5 metres and had to be moved 40 metres below a railway track near Brussels. Mammoet used its own tunnel adaptors and a skidding system with a batteryelectric hydraulic power pack. Prior to skidding the load was lifted using hydraulic jacks. When there was enough ground clearance, hydraulic cylinders pushed the tunnel section along the 40 metre skid
Enerpac completed the factory acceptance testing on a new system for
520 cable drums. Each weighs 95 tonnes. The SBL600 will be set up at several sites to lift the drums from road trailers, hold them and then lower them on to self propelled modular transporter (SPMT) for onward delivery to the point of use off road. The gantry’s side shift will help speed up the positioning and accurate placement.
This SBL is Schmidbauer’s first hydraulic telescopic gantry system. Commenting on the move Philipp Verges, sales manager for global projects at Schmidbauer Group, says, “The SBL600 is ideal for the cable reel handling project, and we were especially attracted by the ease of deploying the gantry to site. We’ve invested in six, hard top, standard 20 metre containers which will allow us to easily transport the SBL600 by road, rail and sea to projects worldwide.”
tracks with their polytetrafluoroethylene (PTFE) pads to minimise friction.
With everything ready the skidding took less than an hour and it came out 2.5 hours ahead of the estimated schedule.
Lifting and specialized transport contractor Schmidbauer has added new equipment to its fleet for a contract that will see it handle 50,000 tonnes of electrical power cable.
The company bought a 600 tonne capacity Enerpac SBL600 telescopic hydraulic lifting gantry to use on a German power transmission infrastructure project.
Over the next four years Schmidbauer will co-ordinate the handling and storage of
Mammoet used electro hydraulic jacking and skidding equipment for a zero-emission bridge move project
Enerpac’s SBL600 lifts 612 tonnes and offers a 10.6 metre maximum lifting height.
Enerpac has completed the factory acceptance testing (FAT) on a new system for German customer Lastro Heavylift.
The JS-250 hydraulic jack up lifting system was tested at the factory in Hengelo, the Netherlands by lifting a 660 tonne load to a height of 15 metres. Capacity of the JS-250, configured with four lifting towers, is 1,400 tonnes to a height of 5 metres and 1,000 tonnes to 10 metres.
The new system for Lastro has a bracing kit to triangulate the structure and help resist side loading. It includes four specially designed mid barrels, four adjustable braces and eight diagonal tension bars. The mid barrels are added to the tower and the braces and tension bars are fitted at ground level. As more barrels are added the bracing rises synchronously.
In addition to the JS-250, Lastro has also added Enerpac strand jacks and an SCJSeries 100 cube lifting system.
Enerpac gantries are proving popular in other parts of the world too. USA-based Engineered Rigging recently expanded its rental fleet with an additional SBL500 hydraulic gantry system.
Christopher Cox, founder and president at Engineered Rigging says, “We expect bidding on large infrastructure projects to increase in 2024, and we stand ready to assist customers with equipment rentals.”■
– lifting capacity from 85 to 180 tons
Long heavy loads, a cellar and limited space were among the challenges met by crane specialist Haslach on a factory project in Austria. ALEX DAHM reports
A pair of large wheeled mobile cranes was the chosen solution to install a series of large and heavy concrete beams at the factory in Austria. (Inset) The 300 tonne crane lifting one end of one of the 98 tonne beams off its trailer
Tandem lifting with a pair of large wheeled mobile cranes was the chosen solution to install a series of large and heavy concrete beams at the factory in Bludenz. The pre-stressed concrete trusses each weighed 98 tonnes and were 42 metres long.
Haslach was constructing a new hall at
the Getzner textile factory. This new building had a full cellar running underneath it and there was limited space to place the cranes. The ten new concrete trusses formed the roof structure for the new factory building.
A further challenge for the crane company was that deliveries had to be able to continue throughout the works.
Commenting on the job Tobias Haslach, Kranverleih Haslach owner, said, “After extensive planning and many detailed calculations, we were able to come up with a solution for the installation work in conjunction with the other companies involved. We stabilised the cellar ceiling from underneath with ceiling supports in order to achieve the support strength required to allow our [Liebherr] LTM 13006.3 to work on this cellar ceiling.” In addition to the 6-axle mobile crane, the specialized transports carrying the trusses also drove over the cellar to unload.
In addition to the 300 tonne capacity crane Haslach used a 230 tonne LTM 1230-5.1 as the second crane for the tandem lifts. Haslach takes up the story, “We set up »
the 5-axle vehicle on a specially filled embankment outside the hall. Due to the positioning behind a concrete wall, we were only able to co-ordinate with the work team via radiotelephones. The truss also had to be guided around the LTM 1300-6.3.”
To get the truss of the delivery truck each crane lifted 51 tonnes at radii of 13 and
Off the special trailer and straight into position with one crane inside and the larger one outside the new factory wall
A series of supports in the basement allowed crane operation to take place above
15 metres, respectively. The beams alone were big enough but, loaded for the delivery by road, they made a total of 148 tonnes, needing a special permit and they could only travel at night.
Following the installation of each beam, both cranes were moved, retaining all their equipment and ballast, into new positions ready for the next lift.
“The co-operation on the construction site was excellent. Operations at the Getzner textile factory continued virtually undisturbed. Our two crane operators were also delighted with the collaboration of everyone involved on site,” said Tobias Haslach.
Family-run Kranverleih Haslach is based in Wertach, southern Germany. Its entire mobile crane fleet is Liebherr cranes. ■
10th Edition
25-27 September 2025 - Piacenza (Italy)
25-27 September 2025 Piacenza (Italy)
25-27 September 2025 - Piacenza (Italy)
While the market for telescopic crawler cranes is consistent, there are plenty of opportunities to evolve. HANNAH SUNDERMEYER from ICST sister title ACT reports
Telescopic crawler cranes are known for their versatility, ease of transport and ability to mobilise quickly and work on various terrains. They are popular for highway and bridge jobs, performing powerline work and as assist cranes on wind farms. The market for this type is strong and manufacturers see potential for even more business.
Telescopic crawlers are becoming a fleet favourite because they are easy to mobilise and operate. Manufacturers offering tele crawler cranes include LinkBelt, Liebherr, Grove, Tadano and Sany. ICST’s sister publication American Cranes and Transport reached out to those five for their insight into the current market and their latest models.
The market for telescopic crawlers has been consistent with some modest growth expected year over year, according to LinkBelt. This is expected to continue through the remainder of 2024.
“Demand is highest for our larger-class models, the 120 US ton [109 metric tonne] cranes and up,” says Brian Elkins, product manager, lattice and telescopic crawler cranes, Link-Belt Cranes. “This includes our 120 ton TCC-1200, 140 ton [127 tonne] TCC1400, and 250 ton [227 tonne] TCC-2500. The lower-tonnage classes are still a popular option for smaller projects but they’re just not as high in demand as the larger models. TCCs continue to replace traditional lattice boom crawlers in bridge construction, as they can handle the needs of larger fixtures and bridge beams at greater radius with better efficiency.”
The TCC-800 is a staple in rental fleets for pick-and-carry tasks in general construction and is also favoured by foundation contractors, Elkins says. Telecrawlers are ideal as a support crane, handling rebar cages
LIFTING CAPACITY: 110 tonnes
MAIN BOOM: 12.2 to 45.7 metres
FIXED JIB: 10.7 to 17.7 metres
MAXIMUM BOOM AND JIB: 63.4 metres
COUNTERWEIGHT: 37.2 tonnes
and for other applications where clearance is tight and mobility is limited.
“Since their introduction in 2017, large-capacity telescopic crawler cranes like the TCC-2500 have consistently demonstrated their value,” Elkins adds.
“From the outset, customers recognised the advantages of models like the TCC-1400 and the TCC-2500. These larger cranes have played a crucial role in the green energy sector, particularly in wind projects, making
to 68 metres 11 metres
MAXIMUM BOOM AND 88.1 metres
COUNTERWEIGHT: 65 tonnes
LIFTING CAPACITY: 150 tonnes
MAIN BOOM: 52 metres
FIXED JIB: 18.9 metre folding jib and-or 2.9 metre assembly jib
MAXIMUM BOOM AND JIB: 85 metres
COUNTERWEIGHT: 22 tonnes, plus superstructure counterweight: 41 tonnes
them an essential part of the industry.”
When purchasing telescopic crawlers, Link-Belt customers are always looking for versatility. Elkins says. In general construction customers regularly need to move underneath bridge overpasses. The ability to retract the boom, travel below and extend the boom to be back to lifting mode in just minutes is a huge advantage over a traditional lattice boom crawler.
While Link-Belt is expecting this sector to remain mostly consistent, there is also certainly room for growth. “As more and more contractors, crane rental houses and owners and operators see the value of it, they start finding more uses,” concludes Elkins. “Telecrawlers cover a lot of ground and add an extremely versatile crane to any fleet. Ground preparation, for example, is much less of a concern than with a traditional outrigger crane.”
Elkins says Link-Belt’s smaller capacity telecrawlers are still in demand, particularly the 55 ton (50 tonne) TCC-550 and the 80 ton (73 tonne) TCC-800, with the TCC-800 being especially popular. »
The market is a diverse one covering many applications, including wind, road and bridge, petrochemical, tilt wall construction and more.
“We see a strong push in multiple markets within the USA including green energy, infrastructure, data centres and distribution centres,” says Beau Pocock, business development manager, rough terrain cranes, and product specialist all terrain and telecrawler cranes in the mobile and crawler crane division at Liebherr USA. “Within these various sectors the market demand continues to grow for a more flexible, compact machine with a strong chart and easy transport such as the newly developed Liebherr LTR 1150.”
Liebherr offers its VarioBase feature to provide greater safety for telescopic mobile cranes, and allows for significantly higher load capacities, especially for lifts directly over the supports. The LTR 1150 is the first telescopic crawler crane to have this system, which determines the optimum load capacity in real time, depending on the fixed track width and the variable rotation angle. The greatest advantages in terms of load capacity are achieved when performing lifts over the corners of the tracks, especially on reduced track widths. The maximum track width of 5.8 metres, a reduced width of 5 metres and a narrow 3.5 metre track width are available.
“For the first time for Liebherr telescopic crawler cranes, we have also calculated WindSpeed load charts for the new LTR 1150, making it possible to work safely and flexibly even at high wind speeds,” says Pocock.
Manitowoc will begin shipping its largest Grove hydraulic crawler (GHC) telecrawler crane – the new GHC200 – to customers later in 2024. Featuring a 200 ton (181 tonne) capacity and 56.4 metre main boom, the new model is said to deliver heavy-duty lifting power in applications that require high capacity at various radii in tough job site conditions, such as swampy and mountainous terrain.
The GHC200 was unveiled to dealers and customers at Manitowoc’s Crane Days event in May at the company’s factory in Shady Grove, Pennsylvania, USA.
“We have seen substantial growth
within our telecrawler offerings, and our new model launches continue to contribute to this success,” says JJ Grace, product manager for GHC cranes at Manitowoc. “One market trend we have seen is the growth and demand for larger telecrawlers. To meet this demand, the GHC200 is our latest and largest telecrawler offering.”
Typical applications for Grove telescopic crawlers include utility work or lifting work on infrastructure projects, Grace says. “Users really like how our GHC cranes combine the advantages of a fast telescopic boom that would typically feature on a wheeled mobile crane, with the stability of a crawler crane and the ability to cover rough ground,” adds Grace.
Grove’s GHC series is for customers who need a compact, manoeuvrable crane designed to withstand the rigours of merciless terrain. With minimal transport requirements, 100 per cent pick-and-carry ability, and a telescoping boom, these cranes have proven nimble in both getting to and navigating jobsites, says Grace.
When it comes to unique applications, Manitowoc has seen its telecrawlers assist with barge work (barge charts are standard), pile driving and foundation jobs.
“One of the latest is an assist crane on a wind farm to build some of our Manitowoc
LIFTING CAPACITY: 160 tonnes
MAIN BOOM: 13.1 to 61 metres
FIXED JIB: 18 metres
MAXIMUM BOOM AND JIB: 93 metres
COUNTERWEIGHT: 31.8 tonnes
LIFTING CAPACITY: 145.1 tonnes
MAIN BOOM: 12.9 to 59.9 metres
FIXED JIB: 3 to 15.5 metres
MAXIMUM BOOM AND JIB: 59.9 metres + 15.5 metres
COUNTERWEIGHT: 36 tonnes, plus carbody: 10 tonnes
MLC product,” says Grace. “Then, they stayed on the job to do pick and carry work or even used a tailing crane.”
While the market has been growing with a shift to the larger capacity models, the Tadano GTC-1600 and GTC-2000 (145 and 181 tonne capacities, respectively) are immensely popular, the company says. The smaller capacity telecrawlers in the Tadano line also see steady demand.
“Our customers like the telecrawlers for their ease of operation, transportability and pick-and-carry capabilities,” says Allen Kadow, product manager, telescopic and lattice crawler cranes at Tadano America.
“We believe the market will continue to strengthen as customers discover the many applications that these cranes perform perfectly in.”
Regarding replacement, the telescopic crawler is less of a commodity crane than RTs and smaller lattice products. These cranes and their quality tend to stand the test of time and remain working in fleets for a number of years, according to Tadano.
This crane family has really found its footing in foundation work, bridge and heavy civil, commercial projects and powerline construction and maintenance, Kadow said. They also perform well in the wind industry, supporting the large lattice crawler cranes used for turbine erection, as well as in marine and railroad applications. ■
CATME speaker Andrei Geikalo, CEO of MYCRANE, the first global platform for online crane rental, on the tangible benefits of digitalization
As we prepare to meet many of our friends and partners at Cranes and Transport Middle East (CATME), the wellregarded KHL event taking place on October 1-2 in MYCRANE’s home city of Dubai, we wanted to share some of our latest developments from around the world.
For those who aren’t yet familiar with our mission to bring digitalization to the construction industry, you should know that MYCRANE has developed the first global platform for online crane rental.
But how do we help our users? Simply, you can save valuable time, energy and money by putting our platform to work for you. Digitalization means it’s no longer necessary to spend hours chasing multiple service providers by phone or email. Would you still pick up the phone to book a taxi? Probably unlikely…
Fortunately, there is a much more efficient way to source the lifting equipment you need. After registering for free at MYCRANE, you will be able to add an enquiry and you’ll soon hear from our crane rental partners. All responses and commercial offers are standardized, meaning the different quotations you’ll receive will be directly comparable.
Our service is just as valuable for crane owners, who can optimize their fleet utilization, and grow their business with MYCRANE.
As a company, we made a strategic decision to pay particular attention to the key markets where we see significant construction activity and therefore the potential to make the biggest impact – these include the Kingdom of Saudi Arabia, India and the USA.
In KSA, we’ve recently expanded our team by appointing Syed Ahmed Salman as VP sales, Middle East, and Zulnoon Bukhari, who joins as business development director, KSA.
Our new team members have a combined 45 years of experience and have hit the ground running, recently
registering a large number of crane rental companies, as well as industrial clients including Shibh Al Jazira Contracting, ALEC Contracting and Saudi Pan Kingdom Co. (SAPAC).
Meanwhile, our team in India has seen a surge in new client registrations and project enquiries, working with leading industrial names such as Larsen & Toubro (L&T), Tata Projects and KEC International.
KEC’s Amit Khurana, a MYCRANE registered customer, says it best when he describes the benefits we offer. “We particularly appreciate not having to manually contact different equipment providers with the same request, as MYCRANE allows us to conveniently post our requirements in one place, then receive a broad range of quotes in a standardized format, with all the information we need. This encourages efficiency and improves our business processes.”
MYCRANE India has been further bolstered by the appointment of two experienced external advisors.
Completing the trio of our focus countries is the USA, where the platform’s director of business development, Olga Dubinok, recently attended the SC&RA annual conference in Austin, Texas, where she enjoyed networking with the industry and spreading the word about MYCRANE.
As our minds begin to focus on CATME, we look forward to meeting and talking to KHL readers about the benefits of digitalization. ●
MYCRANE is the lunch sponsor of CATME. If you would like to arrange a meeting with the MYCRANE team virtually, in person, or at CATME, email info@my-crane.com
For free registration as a client or crane rental company, visit:
Getting your workforce to embrace new ways of working when everything seems to be changing can be a challenge but it is crucial for maintaining productivity, morale and long-term success.
This involves not only adapting to change, but empowering employees to thrive in a rapidly evolving environment. While that sounds logical, still, around half of today’s employees in a recent PwC study of 56,000 workers in 50 countries and regions, reported feeling too much change happening at once, with many admitting to being nervous about job security or adjusting the way they work. And that apprehension isn’t just stemming from broad changes sweeping across an industry; it’s rooted in the day-to-day … i.e., bigger workloads, new tech to learn, new teams to navigate.
that the bigger the changes buffeting your company, the more important it is to get your people on board, and to understand what’s helping and hindering them. It starts with communicating vision and purpose. Reach out to your workforce and clearly explain the reasons behind any changes impacting your company, and how they align with the organisation’s goals.
Employees are more likely to embrace new ways of working if they understand the bigger picture. Maintain consistent communication across all levels. Ensure leaders and managers are delivering the same messages to avoid confusion and build trust.
Adding to the disruption, executives and management teams are managing enormous change themselves, up to and including fullscale business model reinvention.
Amid these pressures, however, it is important to keep in mind
CHAIRMAN
Scott Bragg
Bragg Companies, Long Beach, California, USA
PRESIDENT J Rozum
MSA Delivery Service, Canton, Michigan, USA
VICE PRESIDENT
Jim Sever
PSC Crane & Rigging, Piqua, Ohio, USA
TREASURER
Michael Vlaming
Vlaming & Associates, Vallejo, California, USA
ASSISTANT TREASURER
Harry Fry
Harry Fry & Associates, West Newbury, Massachusetts, USA
ALLIED INDUSTRIES GROUP
Mike Walsh
Dearborn Companies, Bridgeview, Illinois, USA
CRANE & RIGGING
Randy Sever
PSC Crane & Rigging, Piqua, Ohio, USA
TRANSPORTATION GROUP
David Yarbrough
Yarbrough Transfer
Winston-Salem, North Carolina, USA
PRESIDENT
Jennifer Gabel
JK Crane, Kenvil, New Jersey, USA
VICE PRESIDENT
Kate Landry
Deep South Crane & Rigging, Baton Rouge, Louisiana, USA
TREASURER
Stephanie Bragg
Employee buy-in is critical, so involve them in the change process as much as you can. Seek their input and feedback – which helps identify potential issues early on and gives employees a sense of ownership over the changes. It also allows workers to experience the changes firsthand and provides an opportunity to make adjustments based on their feedback.
If we know anything about the modern workforce, particularly younger workers, it is that learning and development is a high priority. Thus we owe it to ourselves as leaders to embrace upskilling and reskilling within our companies and organisations.
As technology and market demands evolve, so too must the skills of your workforce. Offering regular training programmes, certification and opportunities for skills development ensures employees stay relevant, competitive and committed.
Further still, encourage a culture where learning is valued and supported. This could involve creating platforms for knowledge sharing, offering mentorship programmes or even incentivising self-directed learning. It also cultivates agility and flexibility – key components of the modern workplace – and will likely calm any anxiety employees have about their employment future.
Finally, do your consistent best to be a forward-facing company. Align your workforce strategy with the overall business goals –which involves forecasting future skills needs, identifying gaps and planning for recruitment, development and retention accordingly.
Establish clear metrics to assess the effectiveness of workforce initiatives. Regularly evaluate the metrics to ensure the workforce strategy remains aligned with the organisation’s evolving goals.
Leaders who embrace this type of thinking and approach will not only find the complexities of constant transformation easier to navigate but also harness the full potential of their workforce to drive innovation, growth and long-term success. ■
Bragg Companies, Long Beach, California, USA. CHIEF EXECUTIVE
SC&RA has long been known for offering a robust platform of networking, education and advocacy opportunities to its membership around the world.
Accordingly, one of the most valuable yet sometimes overlooked benefits of an Association membership is its suite of affinity programmes.
From insurance programmes that can offer solutions to help mitigate the risks inherent in heavy lifting or transport operations to travel discounts that ease the logistical and financial burdens of managing a mobile workforce, SC&RA’s affinity programmes are a strategic asset for companies of all sizes.
These offerings not only help members reduce operational costs but also enable them to reinvest savings into other critical areas of their business, fostering growth and resilience in a competitive market.
Moreover, these programmes mark an SC&RA membership as not just another professional affiliation, but a strategic business decision. “Many of our affinity programmes are longstanding, and specifically designed to cover so many
facets of member business,” explained Jason Bell, SC&RA director, membership.
“If you’re not looking at them, you might just be wasting money.”
Currently boasting seven programmes, the Association’s affinity offerings include: property and casualty insurance, a 401K programme, Enterprise and National car rental, publications (KHL), FedEx shipping, Milwaukee Tool and CrownSource’s discounted products marketplace.
“It really is a one-stop-shop,” added Bell, “and, uniquely, this suite of programmes, as well as their offered solutions, are always being updated, or added upon, to their members' benefit.”
A prime example, he pointed out, would be the CrownSource programme. “It was once primarily a way for members to save a lot of money on tyres across a variety of market-leading brands, but now, SC&RA members have access to five million products through this programme. There are discounts on fuel, oil and coolant, toll management, warehousing, computers, even mattresses. Just about anything you could want for your fleet, your office, or your business.”
“Access is a word right now that I think plenty of members are thinking about when considering the current insurance market.”
JASON BELl, SC&RA director, membership
Along similar lines, SC&RA recently established the Milwaukee Tool Heavy Duty Alliance partnership, which provides benefits ranging from trade-in support to annual rebates alongside a host of promotions, customised incentives, their Red Tote service programme and tiered rebates.
“This one is really exciting for us as an Association because it directly helps members to be at their best,” said Bell. “Imagine you’re a carrier or a crane rental company – you need tools for equipment repair and maintenance. This relationship
Members can benefit from
these companies in the affinity programme
with Milwaukee Tool doesn’t just provide rebates, it helps you to determine your best options through your local rep and builds out a rebate programme accordingly. It’s designed to address those needs across the entirety of your business and establish a high-value equivalency across all that purchasing.”
Bell emphasised that with each of SC&RA’s affinity programmes, members have free access. “And access is a word right now that I think plenty of members are thinking about when considering the current insurance market,” he noted.
Within the Association’s Property & Casualty Insurance Program – which includes two endorsed market partners and four preferred producers – options are exactly what SC&RA is offering up. “Insurance costs have skyrocketed,” indicated Bell, “so we ask what can we do to help out in planning – how can we work to make sure our members are prepared, don’t get caught off guard and are able to make better, educated business decisions. Because at the end of the day, we’re looking to work alongside our members in navigating this landscape – align them with partners who are working to make the industry better and ultimately help manage those insurance costs.”
To that end, planning is a cornerstone principle within SC&RA’s 401K Program –through a partnership with One Retirement Source. Through this programme, members
gain access to a retirement plan as an employer, said Bell, in terms of pricing and fiduciary services, that they may not be able to obtain individually on their own –especially smaller member companies.
“And now with the retirement mandates, it won’t be long before all fifty states will be requiring companies to provide some type of retirement plan for their employees,” he explained. “Getting out in front of that is critical – again, especially for the smaller companies. But also, working with someone who knows the industry and is working with other SC&RA members to offer benefits that are applicable and competitive. This programme specifically helps members to understand the market, look for a programme and plug one in that makes sense, quickly and efficiently.”
As for day-to-day operations, Bell spotlighted SC&RA’s Enterprise and National and FedEx affinity programmes as longstanding options for members that offer notable savings that could positively impact the bottom line.
“The Enterprise and National rental car programme not only supports members when they’re travelling to our meetings in a particular city but wherever they are –the jobsite, visiting customers or even last-minute business or personal travel,” he confirmed. “SC&RA members are entitled to discounts of up to twenty per cent off rates. It’s another example of – if you don’t have a preferred relationship with a rental car
company, this is one to align yourself with immediately to save yourself some serious money.”
The FedEx programme is no different, insisted Bell – where SC&RA member companies who have registered are saving up to 27 per cent on all shipments through the FedEx agreement with PartnerShip. “We’re coming up on ConExpo and Bauma –we do have a freight programme within this FedEx offering,” he acknowledged. “Savings on ground shipments, overnight, express –this is another one of these programmes where you could potentially be saving double digits on your shipping.
“And if you’re sending documents, contracts, components, hard mail –effectively anything – through FedEx without any type of a discount, you’re missing out. This is one of our longeststanding affinity programmes where we see roughly six or seven per cent of the Association’s membership actively using it and saving money.”
Savings, planning and preparation being what they are, recognised Bell, the Association’s affiliation with KHL is a partnership as much as it is an affinity programme. “With ACT and ICST magazines, and online through Crane and Transport Briefing, KHL helps us broaden our reach and inform members of what’s going on across industry sectors with new products and services. Overall, access to information is a key component to our value proposition for SC&RA members worldwide.”
At the end of the day, added Bell, it stands to reason that the publications piece is at or near the top of SC&RA affinity benefits – just based on the value of information across the board.
“Absolutely, there’s no sense in trying to navigate these extremely complicated times and markets blindfolded. But indeed, all of these programmes, especially in conjunction with each other, point to so many unquantifiable dollars saved – be it through product and service discounts and rebates, retirement and insurance planning, or simply being as educated and informed as much as possible while endeavouring to succeed within this industry.” ■
For more information on SC&RA’s Affinity Partners, visit scranet.org/partners
WHEN
3 June 2025:
Join other industry leaders at the 9th International Tower Cranes conference in Rome. Bringing the industry together to further develop knowledge on safety, innovation, trends and best practice.
WHERE
Cardo Roma, Autograph Collection
Viale Del Pattinaggio, 100 Rome 00144, Italy
Off-site tour TBC followed by a welcome networking drinks reception.
4 June 2025:
Full day conference and post-event farewell drinks reception.
BRONZE SPONSOR
Atrio of ship to shore container cranes at Port Liberty (formerly Global Container Terminals) in New York, USA, have been future-proofed as part of a major upgrade programme.
STS cranes in ports can be upgraded to handle larger vessels by being made taller and given more outreach. That is what Liebherr’s Transform division did to three of the four STS cranes at Port Liberty, with the fourth to follow.
Liebherr engineers increased the lifting height of the STS cranes by 8.6 metres and added 5 metres to the outreach. To increase the height Liebherr used a patented jacking
system, where the STS crane’s end carriage is used as a base for jacking.
A benefit of this method is that less additional equipment is needed. An important element of this type of project is for it to not intrude on the normal operation of the port. Being able to work faster also minimises the downtime.
The Liebherr Transform division at the port crane factory in Ireland offers an upgrade and modification service with the aim of making cranes “stronger, faster, smarter, greener, and ultimately better.”
■ For more information see: www.liebherr.com
Instead of simple time-based maintenance for a hoist winch, scheduling it according to the amount of work done is a better approach. That is according to European abnormal transport and mobile crane association ESTA which has just published a new guide on the subject.
The new guide is available on ESTA’s website in the Knowledge Base section. It sits alongside a calculation tool to help crane owners calculate remaining hours of use based on its usage and the related wear and tear.
Supporters believe the new proposals could both improve safety and even save
money. It is a vital safety consideration because if the crane winch gearbox fails the crane’s load can come down.
As it stands a major overhaul is required after ten years to check the condition. Experts argue that the ten-year threshold is an arbitrary deadline and does not reflect the equipment’s actual usage.
Industry experts, including crane owners, wrote the guide in consultation with winch manufacturers. A maintenance regime based on technical analysis will provide detailed information for other inspections. This can improve safety by
Kito Crosby has announced a new dynamometer to help in lifting situations where close proximity load monitoring is needed.
The Crosby Straightpoint Self Indicating Dynamometer (SID) replaces mechanical products. It is a 6.5 tonne capacity dynamic self-indicating version of the Crosby Straightpoint Bluelink.
Applications include operating lever or chain hoists at height or lifting motors in vehicles. Rigged with compact shackles allows minimal loss of
Liebherr’s Transform division offers a modification and upgrade service for ship to shore container cranes catching unexpected problems earlier. It might also save money by extending the use of the winches beyond current time frames.
Following a poll of its members, SC&RA’s Tower Crane Committee assembled a taskforce from the industry and produced the Guide to Tower Crane Procedures covering tower crane assembly, disassembly and climbing procedures.
It contains best practice to plan, communicate, mitigate risk and identify roles and responsibilities that align with the manufacturer’s recommendations for tower crane assembly, reconfiguration, climbing (changing the tower height), tiebacks, foundation design and disassembly procedures.
The final document was also written and designed to be easy to understand for individuals who are not overly experienced with tower cranes.
■ For more information see: www.scranet.org
■ For more information see: https://estaeurope.eu
headroom. It is 156 mm from eye to eye.
Aluminium construction contributes to it being 30 per cent lighter than competing units, Kito Crosby said. It offers a 6 to 1 safety factor and has a 6-digit LCD screen. Functions include tare, imperial or metric units, and an audible alarm.
Battery life is 80 hours of continuous operation.
■ For more information see: www.kitocrosby.com
No visit to Paris, France, is complete without going to see the cranes helping to reconstruct the world famous Notre-Dame Cathedral following a devastating fire there in April 2019. Here, in unexpected rain (mid-August 2024), is a Potain MDT 809 tower crane owned by Uperio and a large Liebherr wheeled mobile crane owned by crane rental and transport firm Dartus Levage.
IAA TRANSPORTATION
16 to 22 September 2024 Hannover, Germany www.iaa-transportation. com/en
SC&RA CRANE & RIGGING WORKSHOP
24 to 26 September 2024 Arizona, USA www.scranet.org
CRANES & TRANSPORT MIDDLE EAST (CATME)
1 and 2 October 2024 Dubai, UAE www.khl-catme.com
POWER PROGRESS SUMMIT & AWARDS 2024
1 and 2 October 2024 Chicago, USA www.dieselprogress summit.com
TCUBE (COMMERCIAL VEHICLE INDUSTRY)
17 to 19 October 2024 Piacenza, Italy www.tcube-expo.it/en
WORLD DEMOLITION SUMMIT
6 and 7 November 2024 Stockholm, Sweden www.demolitionsummit.com
BAUMA CHINA
26 to 29 November 2024 Shanghai, China www.bauma-china.com/en
Long-time crane industry leader
STEVE FILIPOV has taken up a new position outside the crane industry. Filipov is part of an international consortium that has acquired Metalliance, a French designer and manufacturer of underground vehicles, specialist materials handling machinery and other equipment for the road and rail industries. Filipov also takes the role of chief executive officer at the company that will retain its existing name.
Announcing his move on LinkedIn Filipov said, “I am excited to share that I have accepted the role of CEO at Metalliance… Our focus on innovation, sustainability, and global expansion will reshape Metalliance’s trajectory in the tunnelling industry and electric vehicles sector.”
Over the last three decades in the crane industry Filipov held leadership positions at manufacturers Terex, Demag and Manitex. The Metalliance factory is in St Vallier, eastern France.
FRANK BARDONARO has been appointed chief executive officer at scaffolding provider
The Brock Group in the USA. He joins from Yak Access where he was CEO. Before that he was president and COO at Maxim Crane, the largest crane rental company in North America. He began working with Platinum Equity in 2012, when he joined Maxim. His primary responsibility was to lead the growth, acquisition strategy and margin improvements for the business during Platinum’s ownership of Maxim. Bardonaro has held executive leadership positions in the industry, at AmQuip Crane, Terex Corporation and most recently, ArborWorks.
Bardonaro commented, “It is with great pride that I’m joining the Brock Group, a company known for its unwavering commitment to safety, people, and performance. Having collaborated closely with Brock over the years, I am thrilled to now be a part of the team as we embark on this new chapter together.”
Kobelco Construction Machinery USA has promoted JIMMY HODGES to general manager of Kobelco Cranes. Hodges is a graduate of Texas A&M University and joined Kobelco more than seven years ago. As general manager, he is responsible for all aspects of the Kobelco crane business: parts, service and sales.
After 24 years in the crane and aerial platform industry, RANDY HOOVER has joined CraneWorks in the USA as the company’s new boom truck and sign crane product manager. Most recently, Hoover was regional business manager at Manitowoc. At CraneWorks Hoover’s remit is to collaborate closely with the sales team, driving strategic initiatives to expand and optimise the boom truck and sign crane market. CraneWorks is a North American dealer of new and used truck-mounted and related mobile cranes.
n Please send picture of the month entries and all other back page-related information to The editor, International Cranes and Specialized Transport, KHL Group, Southfields, South View Road, Wadhurst, East Sussex TN5 6TP, United Kingdom, or by email to alex.dahm@khl.com. Entries for Picture of the month should include: the month and year taken, the place, type of crane, owner and project, plus any other relevant information.
■ Market size, development and five-year forecasts
■ Analysis by crane size class
■ Market shares of leading suppliers
■ Detailed production analysis
International Cranes and Specialized Transport's Marketplace is designed to help readers find the products and services they need. The Marketplace is divided into colour coded sections to help you quickly find what you need.
Operational aids, communication systems, components, controls, software, crane mats and outrigger pads, crane repair, hydraulics, jacks, attachments, personnel baskets, rigging hardware, rollers, slings and chains, tires, winches, wire rope, batteries, braking systems, and new, used and refurbished parts.
Training, insurance, inspections, financing, consulting and safety equipment.
Transportation permits, freight forwarding, heavy haul, pilot car services, trailers, wheels and tyres. CAREER OPPORTUNITIES
Employee recruitment and job postings.
To advertise in the International Cranes and Specialized Transport Marketplace, please contact: JOHN AUSTIN on: Tel: +44 (0)1892 786245 e-mail: john.austin@khl.com
Your Global Partner for Used Mobile Crane Parts
•Large Inventory: Over 50,000 parts in stock, ready to ship
•Trusted Brands: Tadano, Liebherr, Spierings, Grove, Faun, Demag, PPM and more
•Worldwide Shipping: Experience in delivering to over 140 countries
•Sustainability: Reduce your carbon footprint by choosing used parts
Wide variety of Cabins: Liebherr , Grove, Tadano, Demag, Spierings and more Big selection of Engines: Mercedes, Volvo, Scania, Liebherr , Deutz and more
CRANES AND EQUIPMENT FOR SALE OR RENT • CRANES AND EQUIPMENT FOR SALE OR RENT • CRANES AND EQUIPMENT FOR SALE OR RENT • CRANES AND EQUIPMENT FOR SALE OR RENT
The D10 is a 10-ton drop test hook that enables you to drop the load into the air safely and from a distance when the order is given, using the Elebia’s remote control. No need to climb, use of ropes or cables to drop the load. Release the load effortlessly, from a safe distance. Experience the convenience of our quick drop system, making your workflow seamless and secure. Introducing the D10. Safely drop loads in
Stevedore, windpower, steel mills, mining, aeronautics, nuclear, construction… No matter what your industry is elebia will boost the safety and productivity of your cranes.